Festo YJKP Series Assembly instructions

8095980
YJKP
Servo Press Kit
8095980
2019-01e
[8095982]
Instructions|
Assembly, Installation

Translation of the original instructions
CANopen®, EtherNet/IP®, MODBUS®, OPCUA®, PI PROFIBUS PROFINET® are registered trademarks of
the respective trademark owners in certain countries.
2 Festo — YJKP — 2019-01e

3Festo — YJKP — 2019-01e
1 About this document................................................................................................... 4
1.1 Applicable documents.................................................................................................. 4
2 Safety........................................................................................................................... 5
2.1 Intended use................................................................................................................ 5
2.2 Foreseeable misuse...................................................................................................... 5
2.3 Training of qualified personnel..................................................................................... 5
3 Further information..................................................................................................... 5
4 Service..........................................................................................................................6
5 Product overview......................................................................................................... 7
6 Transport..................................................................................................................... 8
7 Mounting..................................................................................................................... 9
7.1 Preparation................................................................................................................... 9
7.2 Assembly...................................................................................................................... 9
8 Installation.................................................................................................................. 11
8.1 Safety............................................................................................................................ 11
8.2 Electrical installation - cables....................................................................................... 12
8.3 Electrical installation CECC-X-M1-YS............................................................................. 16
8.4 Electrical installation CMMP-AS.................................................................................... 23
8.5 I/O interface for STO [X40]............................................................................................ 26
9 Commissioning............................................................................................................ 27
10 Maintenance................................................................................................................ 29
10.1 Safety............................................................................................................................ 29
10.2 Maintenance work........................................................................................................ 29
10.3 Cleaning....................................................................................................................... 29
11 Repair........................................................................................................................... 29
12 Dismounting................................................................................................................ 30
13 Disposal........................................................................................................................30
14 Technical data............................................................................................................. 30
Table of contents

1 About this document
1.1 Applicable documents
All available documents for the product èwww.festo.com/pk.
User documentation
Name, type Link, contents
Sensor SKDA-...-AB (operating instructions) èwww.festo.com/sp
Electric drive ESBF-BS (operating instructions) èwww.festo.com/sp
Axial kit EAMM-A (assembly instructions) èwww.festo.com/sp
Parallel kit EAMM-U (assembly instructions) èwww.festo.com/sp
Servo motor EMMS-AS-55 (operating instruc-
tions)
èwww.festo.com/sp
Servo motor EMMS-AS-70 (operating instruc-
tions)
èwww.festo.com/sp
Servo motor EMMS-AS-100 (operating instruc-
tions)
èwww.festo.com/sp
Servo motor EMMS-AS-140 (operating instruc-
tions)
èwww.festo.com/sp
Motor controller CMMP-AS-...-M0 (user docu-
mentation)
èwww.festo.com/sp
Controller CECC-X-M1 (user documentation) èwww.festo.com/sp
Encoder cable NEBM-M (assembly instructions) èwww.festo.com/sp
Encoder cable NEBM-T1G8 (assembly instruc-
tions)
èwww.festo.com/sp
Motor cable NEBM-M23G8 (assembly instruc-
tions)
èwww.festo.com/sp
Motor cable NEBM-T1G8 (assembly instructions) èwww.festo.com/sp
Connecting cable NEBS-M12G5-ES-...-LE5
(assembly instructions)
èwww.festo.com/sp
Connecting cable NEBC-S1WA9-P-1.5-N-BB-L2G4
(assembly instructions)
èwww.festo.com/sp
Connecting cable NEBC-S1G25-P-1.5-N-LE6
(assembly instructions)
èwww.festo.com/sp
Tab. 1 Further applicable documents on the Servo Press Kit
About this document
Festo — YJKP — 2019-01e4

Additional media
Name, type Contents
Web Help YJKP Operation of the software for Servo Press Kit
YJKP
Application note Application examples for connection and com-
missioning
èwww.festo.com/sp
Tab. 2 Additional media on the Servo Press Kit
The range of application and certifications of the individual components of the kit are described in
separate documents èwww.festo.com/sp.
2 Safety
2.1 Intended use
This product is a module for execution of joining tasks with monitoring of the joining process. The
module can be used within machines or automated systems with a higher-order controller.
Use the product only as follows:
– in perfect technical condition
– in its original condition, without unauthorised modifications
– Within the limits of the product defined by the technical data
– in an industrial environment
– permanently mounted
2.2 Foreseeable misuse
Construction of presses with manual loading or unloading in accordance with EC Machinery Directive
2006/42/EC Attachment IV Sec. 9 without further protective measures.
Never use the product as follows:
– With unauthorised modifications or alterations to the product
– With load limits exceeded
– In an invalid mounting position
2.3 Training of qualified personnel
Installation, commissioning, maintenance and disassembly should only be conducted by qualified per-
sonnel.
The personnel must be familiar with the installation of mechatronic control systems.
3 Further information
– Accessories èwww.festo.com/catalogue.
– Spare parts èwww.festo.com/spareparts.
Safety
5Festo — YJKP — 2019-01e

5 Product overview
1Servo motor EMMS-AS
2Axial/parallel kit EAMM-A/U
3Electric drive ESBF-BS
4Sensor SKDA-...-AB
5Connecting cable NEBS-M12G5-ES-...-LE5
6Encoder cable NEBM
7Motor cable NEBM
8LAN cable (not in scope of delivery)
9Connecting cable NEBC-S1WA9-P-1.5-N-BB-
L2G4
10 Controller CECC-X-M1-YS
11 Memory card
12 Motor controller CMMP-AS
13 Connecting cable NEBC-S1G25-P-1.5-N-LE6
14 Higher-order controller (not in scope of
delivery)
15 Switch (not in scope of delivery)
16 Laptop (not in scope of delivery)
Fig. 1 Product overview
Product overview
7Festo — YJKP — 2019-01e

6 Transport
Sequence of transport and unpackaging
NOTICE!
Damage to the product due to incorrect transport.
• Observe the transport labelling and information on the packaging.
1. Transport the product to the installation/storage location in its packaging and set it down on a
firm and flat base.
2. When storing: Pay attention to the storage conditions è 14 Technical data.
NOTICE!
Damage to the product due to incorrect unpacking.
• Observe the labelling and information on unpacking shown on the packaging.
• Unpack the product with at least 2 persons present.
• Use appropriate tools.
• Parts of the packaging are large and heavy:
– Do not let any parts fall onto the product.
– Use suitable aids to raise and lower the product (e.g. crane).
3. Remove the packaging in accordance with the printed sequence.
Restraints in the packaging
Transport restraints prevent uncontrolled movement of the product in the packaging during transport
and installation. The product is provided with the following designated transport restraints:
Fig. 2 Transport screws
Transport
8 Festo — YJKP — 2019-01e

Fig. 3 Cable ties
7 Mounting
7.1 Preparation
Fitting space
The fitting space required for the product depends on the selected size of the Servo Press Kit and the
following factors:
– Stroke of the electric cylinder èwww.festo.com/catalogue
– Attachment position and type of motor
Unintentional lowering of the piston rod is possible at any time. The axis cannot be pushed back
manually. If necessary, the electric cylinder may need to be dismantled.
Mounting surface
The mounting surface must exhibit the following characteristics:
– torsionally rigid
– free of stress
– sufficient strength to absorb the maximum forces
– sufficient evenness
7.2 Assembly
WARNING!
Risk of injury due to lowering piston rod.
• Before working on the product: Secure the piston rod to prevent it from lowering.
CAUTION!
Risk of injury due to falling product.
• Make sure the mounting surface is sufficiently strong to absorb the maximum forces.
• Only use the supplied mounting components.
• Secure the screw connections.
Mounting
9Festo — YJKP — 2019-01e

In the Servo Press Kit, the electric drive, axial or parallel kit and servo motor can be pre-assembled.
With individual components, the following assembly steps are required.
Assemble the motor mounting kit
Depending on the configuration, an axial or parallel kit can be assembled.
Assemble the axial kit EAMM-A
Fig. 4 Axial kit EAMM-A
èPay attention to the accompanying documentation: Axial kit EAMM-A (assembly instructions)
èwww.festo.com/sp
• Assemble the axial kit EAMM-A
Assemble the parallel kit EAMM-U
Fig. 5 Parallel kit EAMM-U
èPay attention to the accompanying documentation for EAMM-U.
èwww.festo.com/sp
• Assemble the parallel kit EAMM-U.
Mount the drive unit on the frame
èPay attention to the accompanying documentation for ESBF.
èwww.festo.com/sp
• Mount the complete unit consisting of axis, axial/parallel kit and motor on the customer-provided
frame so that it is tension-free.
Mounting
10 Festo — YJKP — 2019-01e

Assemble the sensor SKDA
Fig. 6 Sensor SKDA
èPay attention to the accompanying documentation for SKDA.
èwww.festo.com/sp
1. Do not screw the lock nut up to the stop on the ESBF-BS.
2. Screw the sensor on the ESBF-BS.
3. Apply the lock nut to secure the sensor.
Additional steps
1. Insert the memory card (microSD card) into the CECC-X-M1-YS.
2. Assemble the CECC-X-M1-YS.
èPay attention to the accompanying documentation for the CECC-X-M1-YS.
èwww.festo.com/sp
3. Assemble the CMMP-AS.
èAccompanying documentation for the CMMP-AS.
èwww.festo.com/sp
Up-to-date information on the accessories èwww.festo.com/catalogue.
8 Installation
8.1 Safety
WARNING!
Risk of injury due to lowering piston rod.
• Before working on the product: Secure the piston rod to prevent it from lowering.
WARNING!
Risk of injury due to unexpected movement of the product.
Electrical energy can cause unexpected movement of the product.
• Before working on the product: Switch off the power supply, ensure that it is off and secure it
against being switched on again.
Installation
11Festo — YJKP — 2019-01e

NOTICE!
Material damage as a result of using the wrong connections.
In accordance with intended use, all unnamed connections must not be used.
Details on handling the individual components of the kit are described in separate documents
èwww.festo.com/sp.
8.2 Electrical installation - cables
Connecting cable NEBS-M12G5-ES-...-LE5
The connecting cable connects the sensor on the electric drive with the analogue input [X19] on the
controller.
The accompanying plug must be assembled on the open cable ends.
Sensor SKDA Controller CECC-X-M1-YS
Connection Pin Wire colour1) Use Pin Connection [X19]
1 BN 24VDC
Power supply for
sensor
X19.0.1
2 WH Not used
3 BU Input 4…20mA
Evaluation of the
sensor signal
through servo
press software
X19.0.2
4 BK Not used
5 GY Not used
Braided screen Apply braided
screen in direct
proximity of con-
troller and sensor
with a large sur-
face area
1) Colour code in accordance with IEC 60757:1983-01
Tab. 3 Sensor connecting cable - analogue inputs [X19]
1. Connect connecting cable to the sensor.
2. Place the open cable ends in the plug provided in accordance with the table.
Installation
12 Festo — YJKP — 2019-01e

Fig. 7 Screening clamp, controller side
Fig. 8 Screening clamp, sensor side
3. Partially remove the cable sheath on both sides and apply the braided screen across a large sur-
face area with screening clamps 1. Provide strain relief with cable binders 2 over the cable outer
sheath.
4. Insert the plug into the connection [X19.0] of the controller.
Connecting cable NEBC-S1WA9-P-1.5-N-BB-L2G4
The connecting cable connects the CANopen interface [X4] of the motor controller with the CANopen
interface [X18] of the controller.
The cable is readily assembled.
1. Insert the plug into the connection [X4] of the motor controller.
2. Insert the plug into the connection [X18] of the controller.
Connecting cable NEBC-S1G25-P-1.5-N-LE6
The connecting cable is used to provide power to the digital controller interface [X1] of the motor con-
troller.
The circuitry should be carried out in accordance with the following table.
Installation
13Festo — YJKP — 2019-01e

Motor controller
CMMP-AS-...-M0
Provided by the customer
Connection [X1] Pin Wire colour1) Use Type
YJKP
Connection
0.8/
1.5/4
GND7 BN Fieldbus: offset
node number bit1
7/ 12/ 1-
7
+24VDC
8 YE Fieldbus: offset
node number bit3
All GND
9 GY Controller enable All +24VDC
0.8/ 1.5-
/ 7/ 12
GND19 WH Fieldbus: offset
node number bit 0
4/ 17 +24VDC
20 GN Fieldbus: offset
node number bit 2
All GND
21 PK Output stage
enable
All +24VDC
1) Colour code in accordance with IEC 60757:1983-01
Tab. 4 Connecting cable wiring, digital control interface [X1]
1. Insert plug into the connection [X1] of the motor controller.
2. Place the open cable ends in accordance with the table.
If a customer-specific connecting cable is used, the following PIN must also be laid:
Motor controller
CMMP-AS-...-M0
Provided by the cus-
tomer
Connection [X1] Pin Wire colour1) Use Connection
3, 11,
14
- - GND
16, 23 - - +24VDC
1) Colour code in accordance with IEC 60757:1983-01
Tab. 5 Connecting cable wiring, digital control interface [X1] - customer-specific
1. Insert plug into the connection [X1] of the motor controller.
2. Place the additional open cable ends in accordance with the table also.
Motor cable NEBM-M23G8-E-...-Q9N-LE8; NEBM-T1G8-E-...-Q7N-LE8
The motor cable connects the connection [X6] on the servo motor with the connection [X6] on the
motor controller. The circuitry should be carried out in accordance with the following table.
The circuitry should be carried out in accordance with the following table.
Installation
14 Festo — YJKP — 2019-01e

Servo motor EMMS-AS Motor controller CMMP-AS
Connection [X6] Pin Wire colour1) Use Pin Connection [X6]
BK 2 Motor power sup-
ply
8 V
BK 3 Motor power sup-
ply
7 W
BK 1 Motor power sup-
ply
9 U
GNYE Motor power sup-
ply
6 PE
BN Temperature
sensor
5 +MTdig
WH Temperature
sensor
4 -MTdig
GN Brake (optional) 2 BR+
YE Brake (optional) 1 BR-
1) Colour code in accordance with IEC 60757:1983-01
Tab. 6 Motor cable
1. Insert the plug into the connection [X6] of the servo motor.
2. Place the open cable ends in accordance with the table in the connection [X6] of the motor control-
ler.
Encoder cable NEBM-M12W8-E-...-N-S1G15; NEBM-T1G8-E-...-N-G1G15
The encoder cable connects the connection [X2] on the servo motor with the connection [X2B] on the
motor controller.
The cable is readily assembled.
NOTICE!
Restart single-turn encoder.
Loss of the reference position.
• Homing is required at the restart of the encoder.
1. Insert the plug into the connection [X2] of the servo motor.
2. Insert the plug into the connection [X2B] of the motor controller.
Installation
15Festo — YJKP — 2019-01e

8.3 Electrical installation CECC-X-M1-YS
Overview of interfaces
1Ethernet interface [X8]
2USB interface [X9]
3Functional earth connection
4I/O interfaces [X2, X3, X4]
5Power supply [X1]
Fig. 9 Interfaces, front
6Status LEDs
7Memory card
8Power supply [X5] for digital outputs
9CANopen interface [X18]
10 Digital outputs [X20]
11 Digital inputs [X17]
12 Analogue inputs [X19]
Fig. 10 Interfaces, lower
NOTICE!
Material damage as a result of using the wrong connections.
In accordance with intended use, all unnamed connections must not be used.
The status LEDs show the operating status of the controller.
Status LED Meaning
[Run] Application status
[Error] Error
[Net] Device detected
Installation
16 Festo — YJKP — 2019-01e

Status LED Meaning
[Mod] Reserved
Tab. 7 Status LEDs
Overview of connection and plug/cable: CECC-X-M1-YS
Connection Plug/cable Purpose
[X1] NECC-L2G4-C11) Power supply for device
[X5] NECC-L2G2-C11) Power supply for digital outputs
[X2] NECC-L2G8-C11)
[X3] NECC-L2G6-C11)
[X4] NECC-L2G4-C11)
I/O interface
[X8] Standard LAN patch cable2) Ethernet interface
[X9] USB port
[X17] 2x NECC-L2G6-C11) Digital inputs
[X18] NECC-L2G4-C1 CANopen interface
[X20] NECC-L2G2-C11) Digital outputs
1) Plug for customer-provided cable
2) not included in the scope of delivery of the kit
Tab. 8 Connection and plug
Power supply [X1]
WARNING!
Risk of injury due to electric shock.
• For the electric power supply, use only PELV circuits that ensure a reliable electric disconnection
from the mains network.
• Observe IEC60204-1/EN60204-1.
– Power supply for device, digital and analogue inputs
–Resultant current for all supplied ports: £750mA
–Of which intrinsic current consumption: £200mA
– Use an external overload protection for the power supply of the device.
Terminal Connection Use
X1.1 24 24 V DC
X1.2 0 0 V DC
X1.3 Functional earth
X1.4 Not assigned –
Tab. 9 Power supply connection for device, digital and analogue inputs
Installation
17Festo — YJKP — 2019-01e

1. Supply the device with power.
2. Place the open cable ends in the plug provided in accordance with the table.
3. Insert the plug into the connection [X1] of the controller.
Power supply [X5]
– Power supply for digital outputs.
–Resultant current for all supplied ports: £5A
Terminal Connection Use
X5.1 24 24VDC
X5.2 0 0VDC
Tab. 10 Connection, power supply for digital outputs
1. Supply the device with power.
2. Place the open cable ends in the plug provided in accordance with the table.
3. Insert the plug into the connection [X5] of the controller.
I/O interface [X2, X3, X4]
Terminal Connection Use
X2.0…X2.7 8 digital inputs Configurable as step enabling
condition in the sequencer of
the press process: DI1…DI81)
X3.0 Start the press process1)
Manual operating mode: plot
the reference curve
Automatic operating mode:
start the press process
X3.1 "Manual" operating mode1)
X3.2 "Automatic B" operating
mode1)
X3.3 Start homing1)
X3.4 Acknowledge errors1)
X3.5
6 digital inputs
Terminate press process 1)2)
X4.0…X4.3 4 digital outputs Configurable as output signals
in the sequencer of the press
process: DO1…DO41)
24VDC output set by the soft-
ware as soon as certain event
occurs (position reached, force
reached).
Installation
18 Festo — YJKP — 2019-01e

Terminal Connection Use
X4.4…X4.7 Not assigned –
1) For details, see online help
2) Process termination if input = FALSE.
Tab. 11 I/O interface connection
Ethernet interface [X8]
The Ethernet interface is designed as an RJ45 socket and supports gigabit LAN.
The following protocols are supported:
– EtherNet/IP (Server)
– ModbusTCP (Server)
– Ethernet TCP/IP
– PROFINET IO
– OPCUA (Only possible with the optional software extension package.)
The interface [X10] of the controller is not supported. The controller cannot be used as a switch.
The Ethernet interface is used to configure and parameterise the system through a PC/tablet connec-
ted to the network. After the mechanical and electrical installation, the servo press kit can be commis-
sioned with a web browser. Control and process data can be exchanged with a higher-order controller
through this interface during the run-time of the system.
A requirement for this is integration of the CECC-X-M1-YS in the local network.
Minimum requirements for a PC/tablet
– Web browser with Java Script and support of HTML5 Canvas, e.g. Firefox, Chrome, Internet
Explorer ³ Version9
– Screen resolution 1024 x 768 pixels
Access is through entry in the address line: http://<<IP address>>:8080/servo_press_kit.htm
Example: http://192.168.4.2:8080/servo_press_kit.htm
NOTICE!
Unauthorised access to the device can cause damage or malfunctions.
When connecting the device to a network, protect the network from unauthorised access.
Measures to protect the network include:
• Firewall
• Intrusion Prevention System (IPS)
• Network segmentation
• Virtual LAN (VLAN)
• Virtual Private Network (VPN)
• Security at physical access level (Port Security)
USB interface [X9]
The controller offers the option of connecting the USB memory stick up to 32GB to the USB interface
[X9] and saving the press results.
Installation
19Festo — YJKP — 2019-01e

The USB interface is compatible with the USB 3.0 and USB 2.0 standards. It is suitable for USB plug
type A.
Digital inputs [X17]
The digital inputs, configured in 3-wire connection technology, are not galvanically separated. The
ground potential for all inputs relates to GND of the power supply [X1].
For connecting additional sensors (e.g. external cylinder limit switches, workpiece inspection) with
3-wire connection technology: Use 3 adjacent terminals each.
NOTICE!
Material damage or loss of function due to incorrect I/O circuitry.
• All digital inputs/outputs are designed as PNP. Use only corresponding circuitry.
Terminal Connection Use
X17.0.1 24VDC Power supply 24VDC for pro-
gram selection bit 01)
X17.0.2 Input DI9 Program selection bit 0
X17.0.3 GND logic Power supply GND sensor for
program selection bit 0
X17.1.1 24VDC Power supply 24VDC sensor
for program selection bit 1
X17.1.2 Input DI10 Program selection bit 1
X17.1.3 GND logic Power supply GND sensor for
program selection bit 1
X17.2.1 24VDC Power supply 24VDC sensor
for program selection bit 2
X17.2.2 Input DI11 Program selection bit 2
X17.2.3 GND logic Power supply GND sensor for
program selection bit 2
X17.3.1 24VDC Power supply 24VDC sensor
for program selection bit 3
X17.3.2 Input DI12 Program selection bit 3
X17.3.3 GND logic Power supply GND sensor for
program selection bit 3
X17.4.1 24VDC Power supply 24VDC2)
X17.4.2 Servo press activation Release of motor controller out-
put stage via controller
CECC-X-M1-YS
X17.4.3 GND logic Power supply GND2)
Installation
20 Festo — YJKP — 2019-01e
This manual suits for next models
6
Table of contents
Other Festo Power Tools manuals

Festo
Festo BV-50- 40 User manual
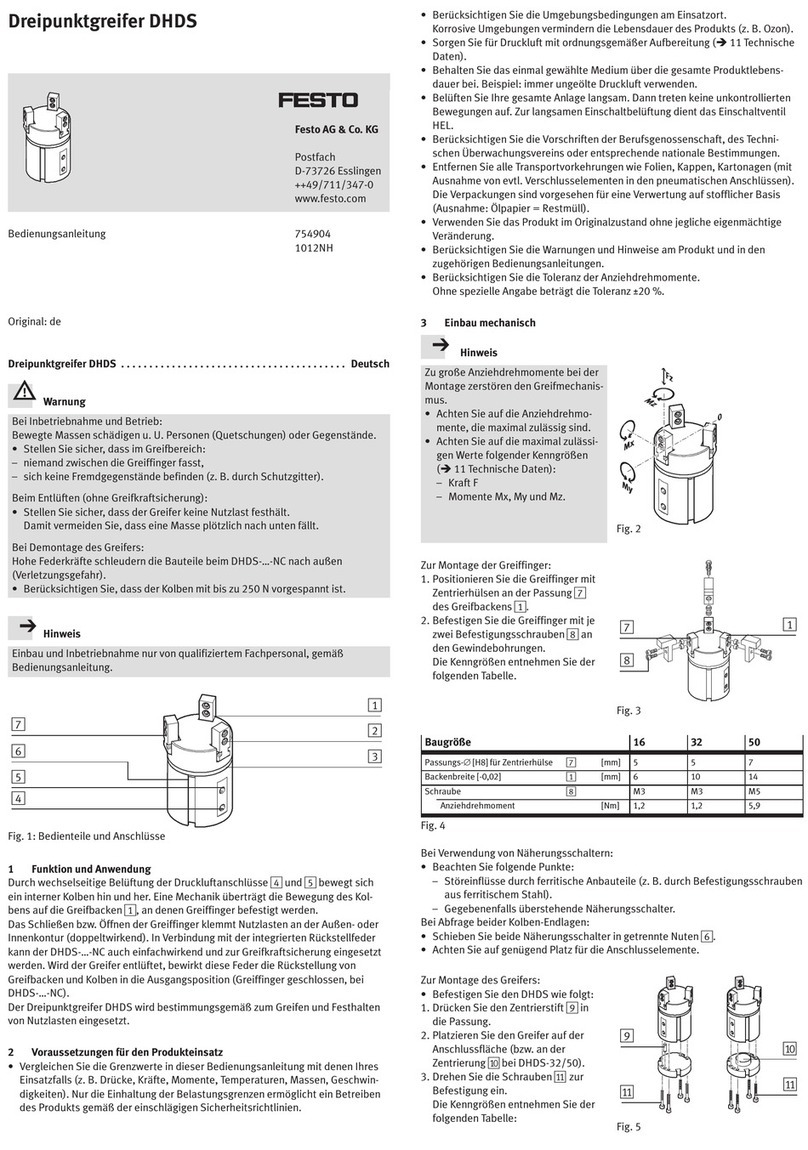
Festo
Festo DHDS User manual
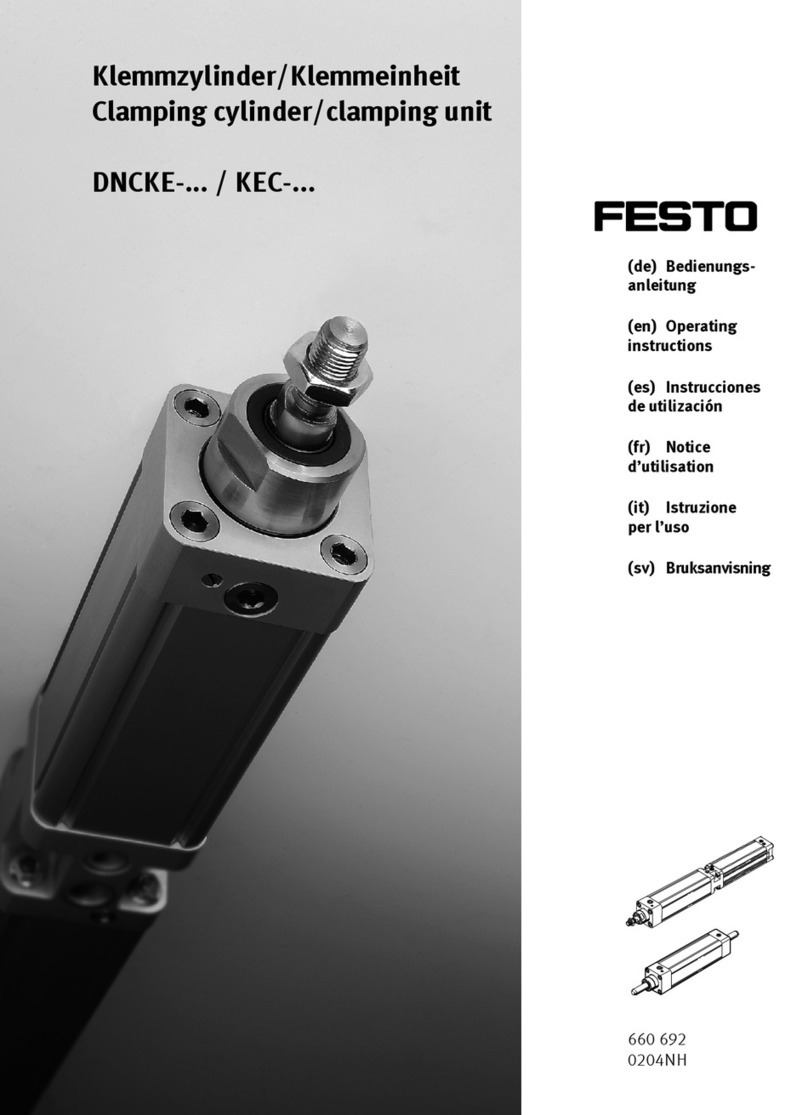
Festo
Festo DNCKE Series User manual

Festo
Festo DRQD-8 Product guide
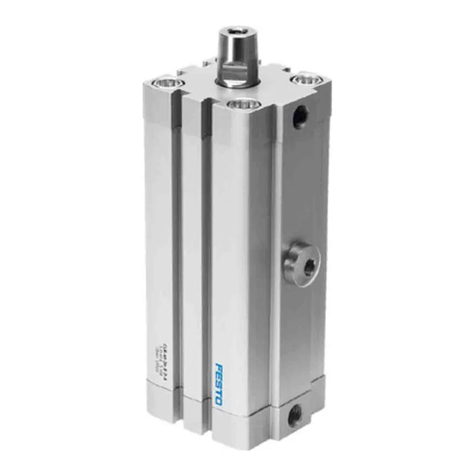
Festo
Festo CLR Series User manual
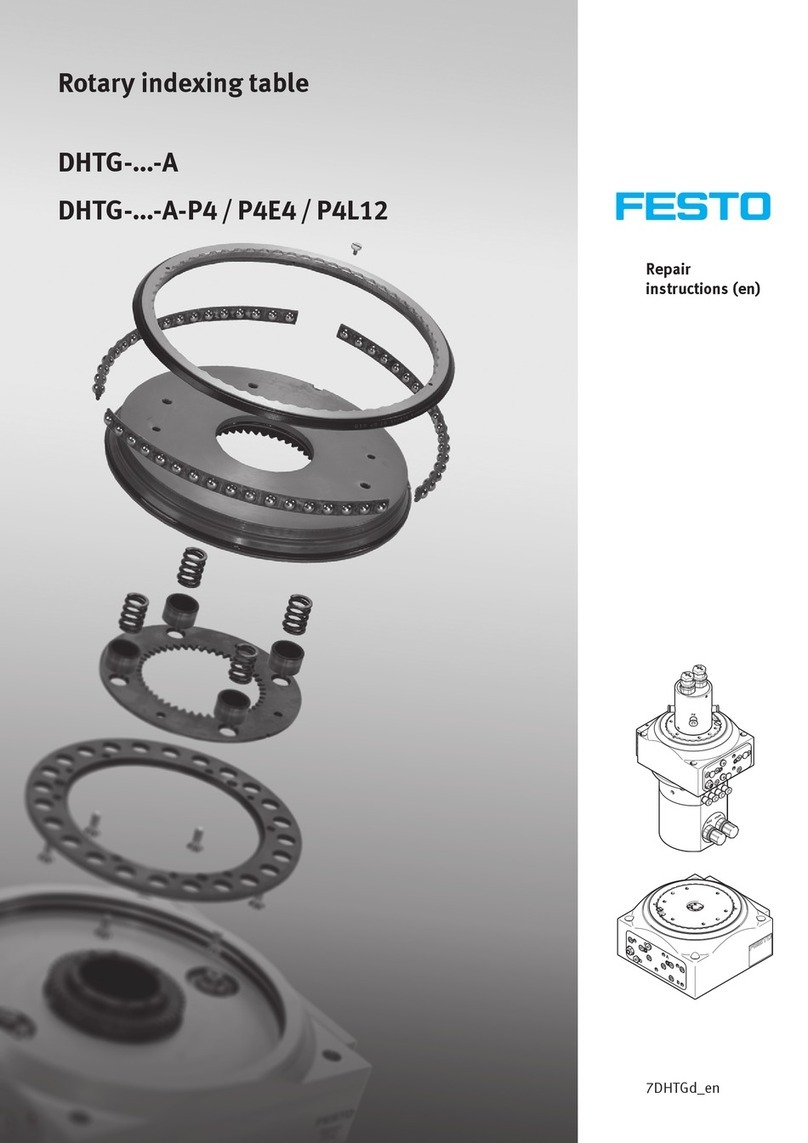
Festo
Festo DHTG A Series Setup guide
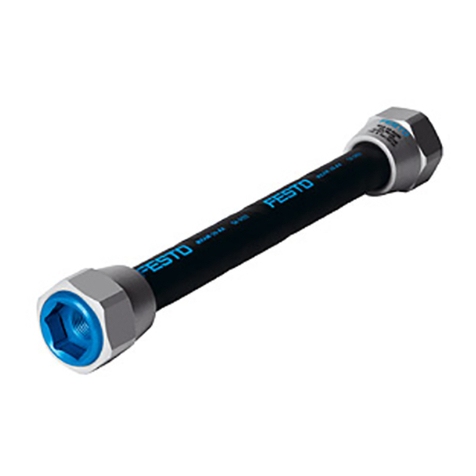
Festo
Festo MAS Series User manual
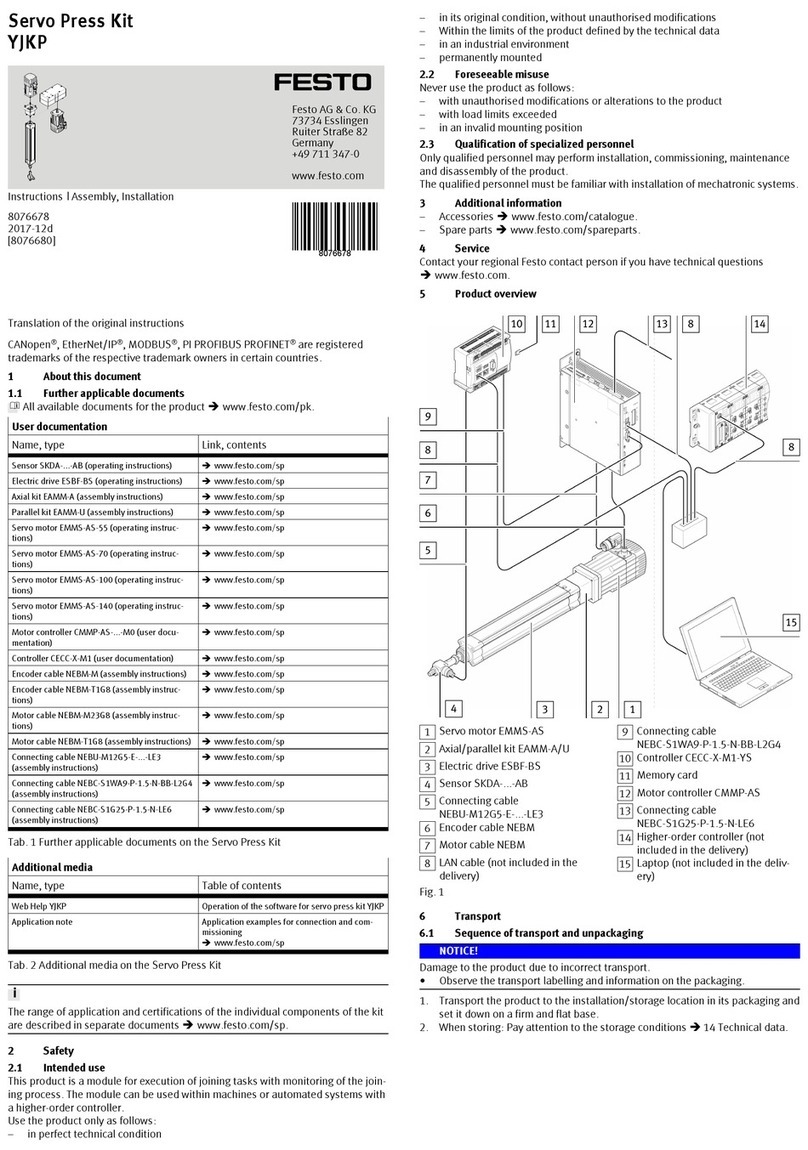
Festo
Festo YJKP Assembly instructions
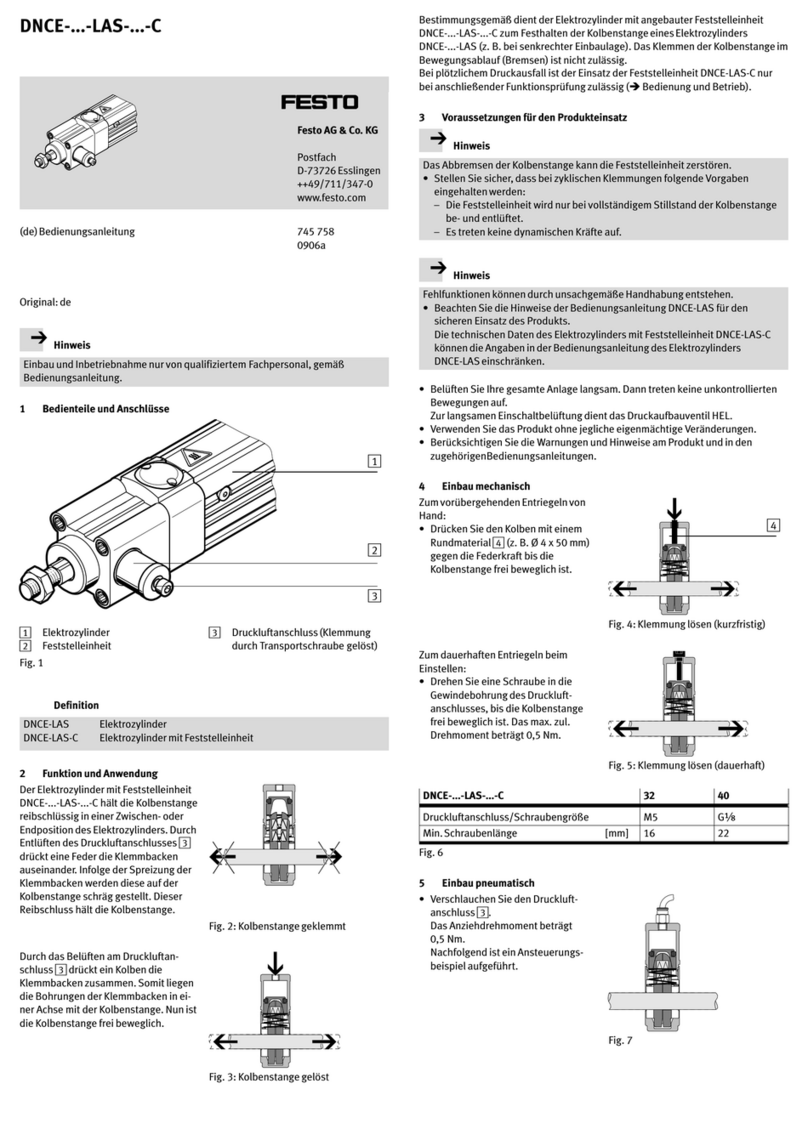
Festo
Festo DNCE-...-LAS-...-C Series User manual
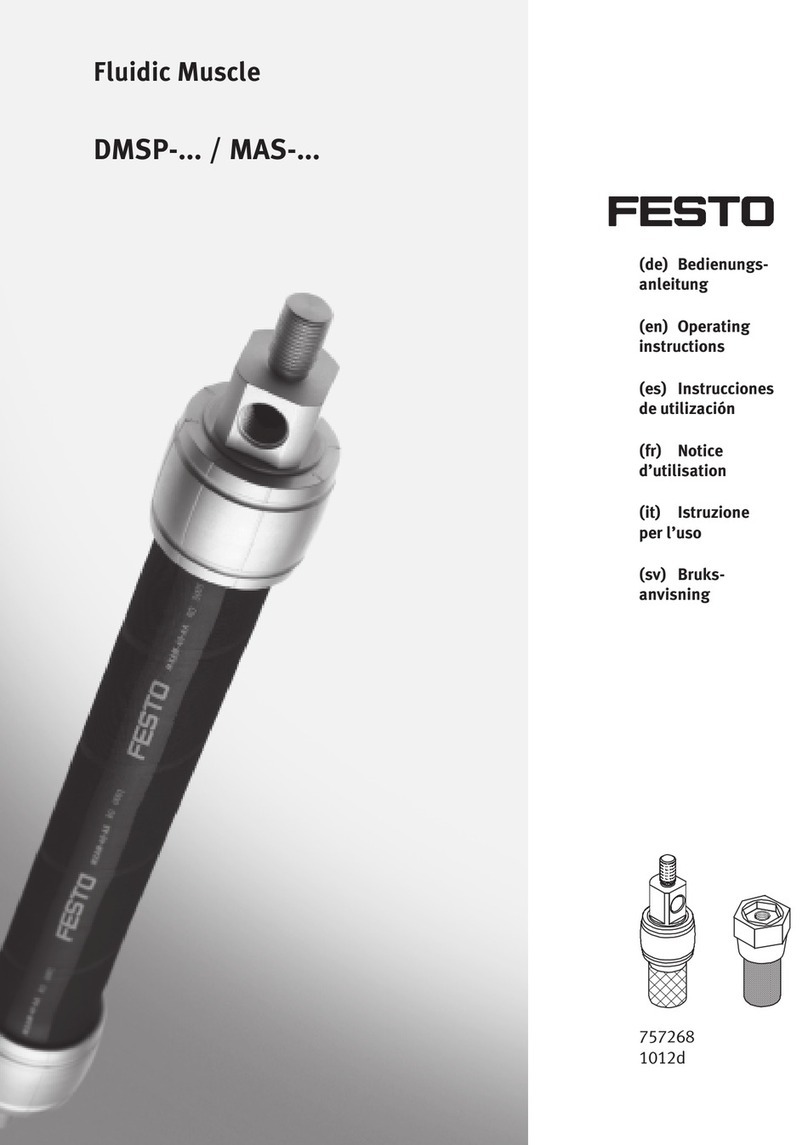
Festo
Festo DMSP Series User manual