GE XV-5A Manual

AUG
Book
No.
SPECIFICATION
NO.
124
INSTALLATION,
OPERATION
AND
o
MAINTENANCE
INSTRUCTIONS
r
FOR
X353-5B
AND
X376
FANS
,4
LIFT
FAN
FLIG
lACK
Al
FT
GRAM
CONTRACT
NUMBER
DA44-177-TC-715
WIIT
UTIN,
NFV
$ECTIOIE"
09RWCEN 1
,;..*
lIR.............................
..............
.
....................
G
E
N
E
R
A
L
E
LE
C
T
R
IC
iI
''-"
i R1I
I IMAR
E3d

DDC
AVAILABILITY
NOTICES
1.
Distribution
of
this
document
is
unlimited.
2.
This
document
is
subject
to
special
export
controls
and
each
trans-
mittal
to
foreign
governments
or
foreign
nationals may
be
made
only
with
prior
approval
of
US
Army
Aviation
Materiel
Laboratories,
Fort
Eustip,
Virginia
23604.
3. In
addition
to
security
requirements
which
must
be
met,
this
docu-
ment
is
subject
to
special
export
controls and
each
transmittal
to
foreign
governments
or
foreign
nationals may
be
made
only
with
prior
approval
of
USAAVLABS,
Fort Eustis,
Virginia
23604.
4.
Each
transmittal
of
this
document outside
the
agencies of
the
US
Government
mt~st
have
prior
approval
of
US
Army
Aviation Materiel
Laboratories,
Fort
Eustis,
Virginia
23604.
5. In
addition
to
security
requirements
which
apply
to
this
document
and
must
be
met,
each
transmittal
outside
the
agencies
of
the
US Government
must
have
prior
approval
of
US
Army
Aviation Materiel
Laboratories,
Fort
Eustis,
Virginia
23604.
6.
Each
transmittal
of
this
document outside
the
Department
of
Defense
must have prior
approval
of
US
Army
Aviation Materiel
Laboratories,
Fort
Eustis,
Virginia.
23604.
7. In
addition
to
security
requirements
which
apply
to
this
document
and
must
be
met, each
transmittal
outside
the
Department
of
Defense must have
prior
approval
of
US
Army
Aviation Materiel
Laboratories,
Fort
Eustis,
Virginia
23604.
8.
This document
may
be
further
distributed
by
any
holder
only
with
specific
prior
approval
of
US
Army
Aviation
Materiel
Laboratories,
Fort
Eustis,
Virginia
23604.
9.
In
addition
to
security
requirements
which
apply
to
this
document
and
must
be
met,
it
may
be further
distributed
by
the
holder
only
with
specific
prior
approval
of
US
Army
Aviation Materiel
Laboratories,
Fort
Eustis,
Virginia
23604.
DISCLAIMER
The findings
in
this
report
are
not
to
be
construed
as
an
official
Dep-ment
of
the
Army
position
unless
so
designated
by
other
authorized
documents.
When
Government drawings, specifications,
or
other
data
are
used
for
au
n
se
other
than
in
connedtion
with
a
definitely
related
Government
procurement operation,
the
United
States
Government
thereby incurs
no
responsi-
bility
nor
any
obligation whatsoever;
and
the fact
that
the
Government
may
have formulated, furnished,
or in
any
way
supplied
the
said
drawings,
speci-
fications,
or
other
data
is
nvL
to
be
regarded
by
implication
or
otherwise
as

+*
---__ -....
*
,,1
TALE
OF
CONTENTS
PAGE
SECTION
1.
INTRODUCTION
................... 1
1.1
GENERAL
................
.. .. ... *.................... .
-i
1.2
SCOPE
.....
..
....................
... .......... .
.....
.. -1,1
1.3
REPLACEMENT
OF
PARTS
....................... .......
I-.1
SECTION
2.
SYSTEM DESCRIPTION
............................. .....
1-2.1
2
1
GENERAL
,
.. . . ..........
.*
.......... .
1-2.
1
2.2
BASIC
FAN
DESCRIPTION
.......................... * ... .......
1-2.1
2.3
SYSTEM ORIENTATION
.......................
.....
#
............
1-2.3
2.4
ROTOR
COMPONENT
DESCRIPTION
...............................
1-2.4
2.5
Shaft
and
Disc ...................
0
,
..... ...... .. ......
1-2.4
2.6
Blade Retainer
Rings
.....................
o
............
1-2.4
2.7
Rotor
Blades
.......................
..
....
....
...
1-2.4
2.8
Blade Platforms .................................
o
........
.
1-2.5
2.9
Torque
Band
Segments
..--.................
.....
..
1-2.5
2.10
Carrier
Segment
Seal
.....................................
1-2.5
2.11
Blade Shroud
Cover ........................................
1-2.6
2.12
.3lade
Carrier
Pins.
...................................
..
1-2.5
2.13
Lock
Pin
..................................................
..
1-2.6
2.14
Lock
Strip
...........
#.......
............
0...........
0........
1-2.6
2.15
Turbine
Bucket Carrier
Assembly
.........................
1-2.7
2.16
Turbine Buckets
...................... .........
#
......
1-2.7
2.17
Bucket Tip Shrouds
................... ............. ........
1-2.7
2.18
Bucket Caryier
...
. ...................
...
1-2.7
2.19
Bucket
Carrier
Tabs
.................................
.....
1-2.8
2.20
Balance
Weight
.
........
...
..................
1-2.8
2.21
Tie
Bolts,
Washers and
Nuts
.... ... ................
1-2.8
2.22
FRONT
FRAME
DESCRIPTION
.. ...... ......... ..................
1-2.9
2.23
Hub
............................... .....
....
...
..
......
1-2.9
2.24
Housing
-
Roller Bearing
....... o....... o.....
pit*
... .i-2.10
2.25
Bearing
System
.............. o
......... ......... o....
1-2.10
I-i

PAGE
2.26
Grease
Seals ..................................
*9*9
9 1-211
2.7I
-2.
1
2.27
Retainer
Seal
-
Ball
Bearing.......121
2.28
Grease
Shield
-
Ball
Bearing
.......
1-2.11
2.29
Retiiner-
Roller
Bearing
1-2.12
2.30
Grease Shield- Roller
Bearing
.....
........
-2.12
2.31
Boss-
Speed
Picek-up
Sensor
1 - 2 . 1 2
2.32
Magnetic
Rotor
Speed
Pick-up
Sensor
..........
.....
1-2.12
2.33
Struts
I.................
................ ...............
1-2.12
2.34
Bellmouth
...........
.
.....
... ....
.................
1-2.14
2.35
Pin
-
Support
Beam
........................................
1-2.15
2.36
Clevis
-
Scroll
Mounting..................................
1-2.15
2.37
Shoulder
Bolt
-
Scroll
Mounting...........................
1-2.15
2.38
Shim
-
Scroll
Mounting
Clevis
......
1-2.15
2.39
Forward Compressor
Seal
....
1-2.16
2.40
Insulation
Blanket
........... .
so,
1-2.16
2.41
INLET
VANE
DESCRIPTION
......
I....o....
1-2.17
2.42
SCROLL DESCRIPTION
99.99.99.... o
...
.......
-2.19
2.43
REAR
FRAME
.........
.....
@
....
...............
#
...
1-2.22
2.44
HONEYCOMB AIR
SEALS
................ * ... .............
1-2.24
2.45
TURNBUCKLE
-
REAR
FRAME
TO
SCROLL
1-2.25
2.46
INSULATION
BLANKET
-
INNER
............. *9
.....
99
.....
o *
*
1-2.25
2.47
INSULATION
BLANKET
-
OUTER
I
.. ....
9
1-2.25
2.48
EXIT LOUVER SYSTEM
.......... ...
T-2.25
249
Exit
Louvers
..................
*so
.......
*
..
99999.994.9
1-2.26
2.50
Actuator
Linkage
I...
.. ... *9 499999
999*
.......
1-2.27
2.51
DIVERTER
VALVE
DESCRIPTION
1-2.41
SECTION
3.
SPECIAL TOOLS
I..........
...999 ...
1-3.1
3
.1
GENERAL
I
-3.1
3.2
BEARING,
BALL,
INNER
RACE
........
.
1-3.1
3.3
BEARING,
BALL,
OUTER
RACE
.99999999999
1-3.1
3
.4
BEARING,
ROLLER,
INNER
RACE
...... ........ .
1-3
.2
3.5
BEARING,
ROLLER,
OUTER
RACE
I.............
...............
1-3.2
I-i
i

PAGE
3.6
EXIT
LOUVERS
......................
1-3.2
3.7
FRONT
FRAME
AND
SCROLL
.I..*..................*.......
1-3.2
3.8
LIFT
FAN
........
...................................
1-3.2
3
9
REAR
FRAm,
............
#
........
.
.............
.. . .*.
I-3
2
3.10
ROTOR...............
..
.............
1-3.3
3.11
TURBINE
BUCKET
CARRIER SEGMENT
.
.......................
1-3.3
3.12
NUMERICAL TOOL LIST
.. .
..
......
.................
1-3.4
SECTION
4.
ASSEMBLY
OF
X353-5B
........................
....
1-4.1
4.1
GENERAL
ASSEMBLY
PROCEDURE
.... .........
#
..............
1-4
.1
4.2
Scope
.I..... ...
......
.....*..
.....
..... .
*.
1-4.1
4.3
ASSEMBLY
TOOLING
....................
.... ....
1-4.1
4.4
ROTOR
ASSEMBLY
(REFERENCE FIGURE
4.2)
.................
1-4.2
4.5
Disc
and
Shaft Assembly.
0.0.0
..
1-4.2
4.8
Assembly
of
Rear
Blade
Retainer Ring
......................
1-4.4
4.9
Assembly
of
Blade
Platforms
.......
I......0..............
1-4.4
4.10
Assembly
of
Torque
Band
Segments ..........................
1-4.4
-.
4.11
Assembly
of
Carrier
Seals
...............................
1-4.5
4.12
Assembly
of
Bucket Carrier Segments
...................
1-4.6
4.13
BAI.ANCE
PROCEDURE
I..............o...
1-4.8
4.14
TOhOUINGPROCEDURE
.............
... ..
*.
.............
.o..
1-4.9
4.15
.9
1ADIAL
INSPECTION
..................
I-4.11
4.16
FRONT
FRAMZ
ASSEMBLY
..........
. .
.........
.
1-4.11
4
J7
ORIENTATION
.................
t....
* o.,
.........
1-4.11
4.18
ASSEMBLE
INSULATION
BLANKET
I.......................
1-4.11
4.19
ASSEMBLY
OF
810
SCROLL
MOUNTS
..........................
1-4.12
4.20
SCROLL
ASSEMBLY
...................
. ... ..
to
1-4.13
4.21
Inspection
and
Adjustment
of
the
Scroll
to
the
Front
Frame
............. ..........
-4.15
4.22
Assembly
of
Scroll
Finger
Seals
I....................
1-4.16
4.23
Assembly
of
Scroll
Insulation
.......................
1-4.17
4.24 Final
Assembly
of
Scroll
to
Front Frame
...................
1-4.17
4.25
Assemble Scroll
Seals and
Air
Seal
Supports
...............
1-4.17
'-iii

PAGE
4.26
Assemble Honeycomb
Air
Seal
.........
........
1-4.18
4.27
Assembly
of
Thrust
Bearing
Outer
Race .....................
1-4.18
4.28
Assemble
Rear
Frame
Insulation
Blankets
...................
1-4.19
4.29
Assembly
of
Rear
Frame
Air
Seal
Segments
..................
1-4.20
4.30
Assemble Rotor
to
Front
Frame and
Scroll
..........
1.......
-4.21
4.31
Assemble
Bearing
Inner
Races
to
Rotor
Shaft
...............
1-4.21
4.32
Assemble
the
Rotor
to
the
Thrust
Bearing
..................
1-4.22
4.33
Assemble
the
Roller
Bearing
.........................
1-4.23
4.34
Clearance Inspection
Prior
to
Assembly
of
Rear
Frame
......
1-4.24
4.35
Assembly
of
Rear
Frame
to
Front
Frame
.....................
1-4.25
4.36
Clearance
Inspection
after
Assembly
of
Rear
Frame
.........
1-4.26
4.37
Assemble
and
Adjust
Magnetic
Speed
Pickup
.........
00#......
1-4.27
4.38
Setting
of
Nozzle
Area
Adjustment
Vanes ...................
1-4.27
4.39
EXIT
LOUVER
ASSEMBLY
.
1-4.28
4.40
Orientation
of
the
Exit
Louver
Push
Rods
..................
1-4.28
4.41
Assembly
of
Exit
Louver
Push
Pods
1-4.29
4.42
Assemble
Bushings
to
Supports
......................
1-4.29
4.43
Assemble
Louver Port
Bushing
to
Strut
.....................
1-4.29
4.44
Assemble
the
Lever
Arms
to
Louvers
................
.....
1-4.30
4.45
Assemble
Exit
Louver
#14
...................
..
1-4.30
4.46
Assemble
Louver
#38
.... ..
&
.......
..... ...
1-4.31
4.47
Assemble
Louver
#13
...............
. ....
......
.
1-4.31
4.48
Assemble Louver
#15
.................
...........
.
1-4.31
4.49
Assembly
of
Remaining
Louvers
........................
1-4.31
4.50
ASSEMBLY
OF
CIRCULAR
VANE
...............
.....
..
........
1-4.32
4.51
DIVERTER VALVE ASSEMBLY
....................................
1-4.107
4.52
GENERAL
.................................... #.......#........
1-4.107
4.53
ASSEMBLE INSULATION
BLANKET
...............................
1-4.107
4.54
ASSEMBLE
DOORS
............
.
.......... .
..
................
1-4.107
4.55
Assemble
Seals
Springs,
Seal
Segments
and
Tube
Seals
......
1-4.107
4.56
Assemble
Doors
to
Valve
Body
..............................
1-4.108
4.57
ASSEMBLE
DIFFUSER
CONE
................
*
.................
1-4.109
4.58 INSPECTION
...............
.....
.........
1-4.109
I-iv

PAGE
4.9
AO-4
4.59
ASSEMBLE ACTUATOR
LINKAGE
...........
..........
1-4.109
4
60ASSEMBLE
ACTUATOR
IU*~**~*******~*******
-4.110
4.61
ASSEMBLE
DOOR
LIMIT
SWITCHES
..............................
1-4.111
4.62
Assemble
Diverter
Valve
to
J85-5
1ngine
...................
1-4.112
4.63
Disassembly
of
Actuator
.....................
.. ......
1-4.113
4.64
Assembly
.. . ....... . . .o. . Ioo.
... . . .
-4.113
4.65
Actuator
Pressure Test
..................... .............
1-4.114
4.66
Diverter
Valve
Coupling
Description
I...............
1-4.114
4.67
Divertor
Valve
Splined
Torque
Shaft
Assmnbly
.............
1-4.115
4.68
Diverter
Valve
Coupling Assembly
o..............
.. 1-4.115
SECTION
5.
INSTALLATION
....
o
....
o.
......
................
1-5.1
5.1
INDUCTION
SYSTEM
...........
... ........ .. . ... ..o. ...
1-5.1
5.2
General
.. . . .. . . . . . .. .I0. . .0. . -5.1
5.3
Inlet
Closure
.... o.............
......
.....
**... ..
1-5.1
5.4
Inlet
Seal
.
1-5.2
5o5
Inlet
Connection
.. I....
...
.....
~o....
-5.2
SECTION
6.
X353-5B
LIFT
FAN DISASSEMBLY
1-6.1
6.1
PREPARATION
FOR
TEARDOWN
. ......... o.............. o.
....
1-6.1
6.2
REMOVE REAR FRAME
........... . ... .s
.o. . .
...
1-6.1
6.3
REMOVE
ROTOR FROM FRONT
FRAME...........................
I-6.1
6.4
REMOVE
SCROLL
FROM
FRONT
FRAME
.................
*..so.....
1-6.2
6.5
DISASSEMBLE
FRONT
FRAME
......................
1-6.2
6.6
Remove Circular
Vane
o.. . . . ... ............
1-6.2
6.7
Remove
Thrust Bearing Outer
Race
...
1-6.2
6.8
Remove
the
Roller Bearing
.............. I..............6.
1-6.3
6.9
Remove
the
Insulation
Blanket
I...............
1-6.3
6.10
Remove
Scroll
End
Clevises
..........
I..0.
...
0....
...
1-6.3
6.11
Remove
Speed Pick-up Bushing
.....
I.so
.......
...... I-6.3
6.12
DISASSEMBLE
ROTOR
o.......... ......... ,....
1-6.3
6.13
Remove
Carrier
Segments
.....
. .. . . .o. ....... ......
1-6.3
I-V

PAGE
6.14
Disassemble
Blades
........................................
...
......
1-6.4
6.15
Disassemble Bearings
..............
..............
1-6.4
6.16
DISASSEMBLE
REAR
FRAME
.............. ...
*.
................
...
1-6.4
6.17
Remove Exit
Louvers
............................ ...........
1-6.4
6.18
Remove
Push
Rods
................. 0. ............... .
....
1-6.5
6.19
Remove Insulation
Blanket ................................
1-6.5
6.20
Remcve
Air
Seals
..............................
...
1-6.5
6.21
DISASSEMBLE
DIVERTER
VALVE
.......
...........
1-6.6
6.22
Actuation
Removal
............................
....... .
1-6.6
6.23
Door
Removal
.............................
.........
.
... .
1-6.6
6.24
Insulation
Blanket
Removal
..............
...
........
1-6.6
6.25
Diffuser
Removal
....................
....
...
..........
1-6.6
SECTION
7.
INSPECTION,
REPAIR
AND
REPLACEMENT
...................
1-7.1
7.1
GENERAL .......................................
..........
1-7.1
7.2
CLEANING
AND
INSPECTION
...................... ........
1-7.1
7.3
Cleaning
of
Bearings
....
................
,
.................
1-7.1
7.4
Fluorescent-Penetrant Method
of
Inspection
(Zyglo)
........
1-7.3
7.5
General
.............................. ....................
1-7.3
7.6
Cleaning Prior
to
Application
of
Fluoreqcent-Penetrant
....
1-7.3
7.7
Application
of
Fluorescent-Penetrant
(,il
..................
1-7.3
7.8
Application
of
Developer
.................................
1-7.3
7.9
BLADE TANG
AND
BLADE/DISC
DOVETAIL
COATING
................
1-7.4
7.10
PERIODIC
INSPECTION
REQUIREMENTS
..........................
1-7.32
7.11
LIFT
FAN
SERIAL
NUMBERS
................................
1-7.33
SECTION
8.
TESTING AFTER OVERHAUL
OR
MAINTENANCE
................
1-8.1
8.1
GENERAL
.........
.............. .
.........
..
............
1-8.1
SECTION
9.
OPERATION
OF
X353-5B PROPULSION SYSTEM
..........
1-9.1
9.1
GENERAL
............................. .......... ...
....
.
I-9.1
I-vi

LIST
OF
ILLUSTRATIONS
FIGURE
TITLE PAGE
1.1
X353-5B
Propulsion
System...............
1-1.2
2.1
Typical
Fan-In-Wing
X353-5B
Installation
............... 1-2.28
2.2
Major
Components
of
X353-SB
Lift
Fan
System
............
1-2.29
2.3
System Orientation
.................... ........
..
1-2.30
2.4
Lift
Fan Rotor
Component
..........
1-2.31
2.5
Lift
Fan
Front
Frame
............................
.
1-2.32
2.6
Lift
Fan
Assembly
Showing
Inlet
Vane
..............
t....
1-2.33
2.7
Lift Fan Scroll,
View
of
Inlet
.....................
1-2.34
2.8
Lift
Fan
Scroll,
View
of.Nozzle
............
....
1-2.35
2.9
Lift
Fan
Scroll,
ToP
View
...................
1-2.36
2.10
Sketch
of
Turbine
Nozzle
Partitions
..................
1-2.37
2.11
Scroll
Area
Adjustment
Mechanism
1-2.38
2.12
Lift
Fan
Rear
Fra:ae
............... .. ..o... ......... 1-
2.39
2.13
Exit
Louver
System
i.
.......
-2.40
2.14
Diverter
Valve
Asse~nb
.............
1-2.45
2.15
Diverter
Valve
Actuation
System......
I-2.46
2.16
Sketch
of
Actuation Linkage
in
Straight-Through
and
Diverted
Positions
I...
1-2.47
3.1
Rotor Balance
Arbor
1-3.5
3.2
Rotor Turnover
Dolly
.
I-3.5
3.3
Front
Frame,
Scroll
and-Fan
Turnover
Dolly
.....
*
......
1-3.6
3.4
Ball
Bearing
Inner
Race
Puller
1-3.6
3.5
Rotor
Vertical
Lift Fixture
...... ....
1-3.7
3.6
Roller
Bearing
Inner
Race
Puller
1-3.7
3.7
Spanner
Wrench
.............................
......
1-3
.8
3.8
Ball
Bearing
Outer
Race
Puller
1-3.8
3.9
Roller
Bearing
Outer
Race
Puller
..................
1-3.9
3.10
Tab
Bender,
Front
Frame and
Bearing
Assembly
...........
1-3.9
3.11
Lift
Fan
Shipping
Container
..
1-3.10
3.12
Lift
Fan
Transportation
Dolly
..........................
1-3.10
3.13
Front
Frame
and Scroll
Lift
Fixture
...................
1-3.11
0
I-vi

FIGURE
TITLE
PAGE
3.14
Rotor Support
Stand
.....
* .......
..........
1-3.11
3.15
Rotor
Balance
and Inspection Stand
...........
1-3.12
3.16
Front Frame Air
Seal
Grinding
(lift)
and
Inspection (Right) Fixtures
............................
1-3.12
,3.17
Carrier Retaining
Pin
Inserting
and
Removal
Tool
(Tool
for
Left Hand
Carriers
on
Left;
Tool
for
Right Hand
Carriers
on
Right)
*.........................
1-3.13
3:18 Exit Louver
Protractor
................................
13.13
3.19
Bearing
Cage
Support
...................................
1-3.13
3.20
Exit Louver
Template
.....
.....
*
........
*..
I-S.14
4.0
Balance
Plot
-Top
Looking
Down........................
1-4.9
4.1
Lift
Fan Basic Assembly Drawing
(Left) "..
......
14.49
4.2
Lift Fan
Rotor
Assembly
Drawing
(Left)
.................
1-4.53
4.1A Lift Fan
Basic
Assembly
Drawing
(Right)
.................
1-4.71
4.2A Lift Fan
Rotor
Assembly
Drawing
(Right)
................ 1-4.75
4.2B
X353-5B
Lift Fan
Configuration
(left)
.................
1-4.76
4.2C
X353-5B
Lift
Fan
Installation
.................
1-4.79
4.3
Rotor
Tie
Bolt
Torquing
Procedure
.....................
1-4.83
4,4
Rotor Air
Seal
and
Tip
Seal
Inspection
................
1-4.84
4.5
Front
Frame Insulation
Blanket
Inspection
..............
1-4.85
4.6
Inspection
and
Adjustment
of
Scroll
to
Front
Frame
.....
1-4.96
4.7
Insepction
of
Scroll
to
Front Frame
............
0.......
1-4.87
4.8
Inspection and
Adjustment
of
Scroll
Center
Mount
Uniba!
Slot
.................... . . . I-4.88
4.9
Inspection and
Adjustment
of
Scroll
Seal
Overlap
.... ,..
1-4.89
4.10
Honeycomb
Ar
Seal
Attachment
.............
1-4.90
4.11
Honeycomb
Seal
Grinding
Instructions
and
Inspections
... 1-4.91
4.12
Rear Frame
Assembly
Drawing (Left Hand)
................
1-4.93
4.12A
Rear
Frame
Assembly Drawing
(Right
Hand)
............... 1-4.95
4.13
Inspection
of
Rear
Frame
Insulation
Blanket
Radius
.....
1-4.97
4.14
Assembly
of
Bearing
Retaining Nut Tabwasher
............
1-4.98
4.15
Inspection
of
Rotor
Axial
Clearances
.......
1-4.99
4.16A
Reference
Sketch
for
Final
Inspection
of
Assembly
......
1-4.1n
4.16B Rotor
Bearing
and
Speed
Sensor Clearance
Inspection
....
1-4.101
I-viii

FIGURE TITLE
PAGE
.4.16C
Rotor
Running Clearance
Inspection
............
....
1-4.102
4.17
Assembly
of
Adjustment
Lever
to
Louver
End
............
1-4.103
4.18
Inspection
of
Louver
Angle
Settings
............
1-4.104
4.19A
Torquing
Procedure
for
Torque
Band
Bolts,
(Right
H
and
Fan)
.. ..................................
1-4.105
4.19B
TorquiLng
Procedure
for
Torque
Band
Bolts,
(Left
H
and
Fan).................................
...........
1-4.106
4.20
Assembly
Drawing,
LeftHand
Diverter Valve
........
1-4.123
4.20A
Assembly
Drawing,
Right
Hand
Diverter
Valve...............1-4.131
4.21
Assembly
D
awing,
Diverter
Valve
Actuation
System.........1-4.133
4.21A
X353-5B Diverter
Valve
Installation.......................1-4.135
4.22
Diverter
Valve
Actuator...................................1-4.137
4.23
Exit
Louver
Actuation
Limits............................
1-4.138
4.24
Assembly
Drawing,
Coupled Diverter
Valves
(401200).
-
915)...........................................
1-4.139
.1Exit
Louver
System
................................
1-5.4
5.2
X353-5B
Fan Exit
Louver
Interference.................
1-5.5
5.3
X353-5B
Left
Hand
Fan
Mount
Reactions
..............
1-5.6
9.1
X353-5B
System
Installation
.....................
1-9.3
I-ix

SECTION
1.
INTRODUCTION
1.1
GENERAL
a.
This
publication,
prepared
by
the
General
Electric Company
in-
cludes
installation,
operation
and
maintenance
instructions
for
the
X353-5B
convertible
V/STOL propulsion
system.
This
propulsion
system
is
designed
and
manufactured
by the
General
Electric
Company,
Advanced
Engine
and
Technology
Department,
Evendale,
Ohio.
1.2
SCOPE
a.
The
X353-5B
propulsion
system
(Figure
l.l!consists
of
a
J85-GE-5
turbojet engine
(less
afterburner)
used
as
a
gas
generator,
a
diverter
valve
to
direct
the
gas
flow, and
an
X353-5B
lift fan
equipped
with
vectorable
dis-
charge
louvers.
Reference
to
the
J85
in
this
publication
will
be
limited
to
special
requirements
of
the
X353-5B
propulsion system.
Additional information
on
the
J85
engine
can
be
obtained
from
the
Small
Aircraft
Engine Department,
General
Electric
Company, Lynn,
Massachusetts.
1.3
REPLACEMENT
OF.
PARTS
a.
Only
General
Electric
Class
I,
Ia,
II
or
Ha
parts
are
acceptable
Ifor
use
in
any
X353-5B
propulsion
system.
Replacement parts
can
be
obtained
only
through
the
General
Electric
Company.
Inquiries
should
be
directed
to:
General
Electric
Company
Advanced Engine
and
Technology
Department
•Lift'Fan
Systems
Operation
Building
501
Cincinnati,
Ohio
45215
I-1.1
R-1

FIGURE
1.1
X353-5B PROPULSION
SYSTM

SECTION
2.
SYSTEM
DESCRIPTION
2.1
GENERAL
a.
The
X353-5B
lift
fan
is
designed
for
installation
in
the
wings
of
an
airplane
(Figure
2.1)
and
combines
desirable
VTOL
features
of
high
thrust,
low
sfc,
low
exhaust
velocities,
low
noise
levels and
low
weight.
It
is
a
convertible system
which
augments
the
thrust
of
a
turbojet
engine
for
vertical
takeoff
and
landing.
b.
The
J85
turbojet
engine
and
the lift fan
are
pneumatically
coupled
by
the
diverter valve
and
additional
ducting
as
may
be
required
for
a
specific
installation.
For
vertical
flight,
the
diverter
valve
deflects
exhaust gases
from
the
turbojet
into
a
tip
turbine
which
drives
the lift
fan.
During transition
from
hover
to
horizontal
flight,
louvers located
on
the
lower
surface of
the
fan
vector
the fan
exhaust
rearward
to
provide
horizontal
thrust
for
forward
acceleration.
Once
the
aircraft
has
reached
a
speed sufficient
for
wing
supported
flight,
the
diverter
valve
is
moved
to
the
straight-through position,
the
exit
louvers
and
the
wing
surface
over
the fan
inlet
are
closed
and
the
J85
turbojet
operates
in
a
conventional
manner.
2.2
BASIC
FAN
DESCRIPTION
a.
The
X353-5B
is
a
light-weight,
high-performance,
compact
V/STOL
lift
fan
propulsion system. The
major components
(Figure
2.2)
include
a
diverter
valve,
a
single-stage
axial
flow
fan,
a
power turbine
attached
to
the fan
blade
tips,
a
front
frame
with
an
inlet
guide
vane
assembly,
a
rear frame
containing
the
fan
and
turbine
exit
stator,
a
scroll
which
con-
tains
the
partial
admission
turbine
nozzle,
and
exit
louvers
supported
irom
the
rear
frame.
The
leading
system particulars
are
listed
in
Table
2.1.
1-2.1
R-2

TABLE
2.
1
X353-5B
LEADING
PARTICULARS
I.
LIFT
FAN
Type
Tip
turbine
lift
fan
Type
of
compressor Single-stage,
co-axial
flow
Type
of
Turbine
Single-stage,
impulse, partial
admission.
Fastened
to
blades
of
co-axial
fan.
Direction
of
rotation Clockwise
or
counter-clockwise.
Rotor
speed
(maximum)
2719
RPM
(103%)
Installed dimension:
Distance
between
82.5
inches
(cold)
wing
spar
centerline
Overall
dimension
89.1
inches
(cold)
(spanwise)
Fan
tip
diameter
62.5
inches
Depth
at
hub
18.2
inches
Depth
at
edge
14.40
inches
maximum
Weight
(maximum)
915
pounds (includes
instrumentation)
Center
of
gravity
The
lift
fan
C.G.
is
located
5.3"
from
fan
rotating
axis
on
minor
strut
centerline
and
vertically
0.62"
above
rotor
centerline.
Mounting
Three
Point.
At
leading
edge,
trailing
edge and
inboard
between
scroll
inlets.
2.
DIVERTER VALVE
Type
Tee,
with
double
"butterfly"
doors
Basic
length
34.8 inches
Basic
width
18
inches
between mounts,
16.5
inches
I.D.
Weight
(maximum)
91
pounds (includes
instrumentation)
Center
of
gravity
2.7
inches
forward
of
main
mounts,
4
inches
below
centerline.
Mounting
Integral with
gas
generator
1-2.2
R-2

TABLE
2.1
(Continued)
X353-SB LEADING
SYSTEM
PARTICULARS
3.
LUBRICATION
Fan
bearing grease
Texaco
Unitemp
500
oz
equivalent.
Grease
capacity
Ball
thrust
bearing
60
grams
Roller bearing
40
grams
Bearing temperatures
3500F
maximum
4.
ACCESSORIES
RPM
indicating
Magnetic reluctance
RPM
transmitter
RPM
to
DC
converter
5-1/4"
x 9"
5-3/4"
transistorized
instrument
package.
24-28
V.
DC,
2a.
Diverter
valve
position Terminal
position micro
switches.
transmitters
28
V.
DC
5
Amp.
resistive
2
Amp.
inductive
Diverter
valve
actuator
Two-position,
dual
piston.
Hydraulic
fluid
MIL-H-5606,
3000
psi,
2.7
gpm
(150
strokes/min.).
Design
stroke
3.85
in.,
max.
temperature
3000F.
2.3
SYSTEM
ORIENTATION
a.
Location
references
used
in
this
text
are
shown
in
Figure
2.3.
Similar
components
located
on
a
common
diameter around
the fan
are
numbered
clockwise starting from
the
12
o'clock
position.
The
12
o'clock position
is
the
forward point
of the fan
in
relation
to
the
nose
of the
aircraft;
this
point
remains
12
o'clock
regardless
of
the
direction
of
fan
rotation.
The direction
of
fan
may
be
either right
(clockwise)
or
left
(counter-
clockwise)
when viewing
the
rotor
from
the
top
looking
down.
The
symbol
L
(left)
or
R
(right)
after
the
fan
assembly
serial
number
identifies
the
direction
of
rotation.
References
to
the
forward
end
of
the lift
fan
pertain
to
the
inlet
or
top
side;
references
to
the aft end
of
the lift fan
pertain
to
the
exit
or
bottom
side.
1-2.3
R-2

-.. ... ._
_ _ _ _ _ _
_
__....... .
_
__.....
. . .. .. .. -----
2.4
ROTOR
COMPONENT
DESCRIPTION
a.
The
fan
rotor
component
(Figure
2.4)
is
a
single-stage,
axial
flow
compressor
which
pumps
air
downward
to
produce
lift.
The
rotor
consists
of
a
shaft
and
disc,
retainer
rings,
blades, blade
platforms,
torque
band
seals,
blade
shroud
covers,
blade
carrier pins,
a
carrier
assembly
which
includes
turbine
buckets,
and
carrier
tabs.
2.5
Shaft
and
Disc
a.
The
rotor
shaft
and
disc
(Figure
2.4)
are
made
of
SAE
4340
steel.
The
hollow
rotor
shaft
and
each
of
the
two
cones
that
make
up
the
disc
are
machined
from
individual
forgings
to
a
0.030"
-
0.060"
envelope,
heat
treated,
and
final
machined
except
for
surfaces
affecting
final
assembly
tolerances.
The
two
cones
are
bolted
together
with
36
tie
bolts
at
the
outside
diameter
to
form
the
rim
of
the
disc.
The
cones
are
shrink-
fitted
to
the
shaft
to
form
a
permanent disc-shaft assembly.
Final
machining
of
assembly
surfaces
and
broaching
of
the
blade
dovetail
slots
completes
the
disc-shaft assembly.
2.6
Blade
Retainer Rings
a.
Each
rotor
assembly
has
two
blade retainer
rings
(Figure
2.4).
The
rings
are
bolted
one
to
each
side
of
the
disc
rim; they
prevent
axial
translation
of
the
blade
dovetails
and
provide
attachment
for
the
blade platforms. The rings
are
formed
of
0.045"
17-7
PH
sheet and
contain
36
holes around
the
circumference
to
accommodate
the tie
bolts.
Thirty-six
equally
spaced
tabs
(stamped
from
0.022"
17-7
PH
sheet) are
spot
welded
to
each
ring;
an
anchor
nut
is
spot
welded
to
each
tab
to
provide
an
attachment
for the
blade
platforms.
2.7
Rotor
Blades
a.
The
rotor
has
36
blades
(Figure
2.4)
which
pump
the air
downward
to
produce
lift.
The
blades
have
a
constant
section airfoil
and
are
made
without
platforms.
Each
blade
is
rough
machined
from
either
an
oversized
1-2.4
)
R-1

forging
or
a
hot
rolled
bar
of heat
treated
PH
14-4
Mo,
stress
relieved,
and
final
machined.
The
dovetail
and
shank
are
milled
and
ground
to
final
dimensions.
A
tang
machined
on
the
blade
tip
provides
a
hole
for
a
pin
attachment
to
the
turbine
bucket
carrier
assembly.
2.8
Blade
Platforms
a.
The rotor
has
3U
blade
platforms (Figure
2.4)
which
form
the
inner
aerodynamic
flow
path
througt
the
fan.
The platforms
and
the
stiffening
braces
are
formed
of
0.028"
61S
aluminum.
The assembly
is
spot
welded,
brazed,
and heat
treated.
Two
bolt
hole
grommets
and
washers
(AMS
5510
stainless
steel)
are
swaged
to
th
platform
assembly.
The
platform
assemblies
are
bolted
to
the
tabs
on
the
recaiLner
rings.
2.9
Torque
Band
Segments
a.
Each
rotor
assembly has
two
sets
of
torque
band
segments
(Figure
2.4),
one
set is
located
on
each
side
of
the
rotor (inlet
and
-xit)
between
the
blade
tips and
the
turbine
bucket
carrier
assembly.
The
segments
transmit
torque
from
the
active
part
of
the
turbine
to
the
blades
which
are out
of
the
partial admission
arc.
Each
torque
band
has
six
segments
formed
of
R41
stainless
steel.
Six
ears
project from
each
segment;
three
of
the ears
contain
two
holes,
the
remaining
three
ears
contain one
hole.
A
grommet,
machined
from
R41
stainless
steel,
is
press-fitted
into
the
single-hole
ear
and
is
positioned
at
the
center
of
each
carrier;
the
bolted
connection
at
this
point establishes rotor
spacing
and transmits
the
torque.
The
two-hole
ears
join
the
ends of
the
carrier segments
and
restrict
axial
displacement;
the
bolt
3izes
and
torquing
standards
allow circumferential
growth
of
the
rotor.
2.10
Carrier
Segment
Seal
a.
The
carrier
segment
seal
(Figure
2.4)
forms
part of
the
outer
[
flow
path
through
the
fan.
The
seal
is
formed
in
two
parts
from
0.045"
R41 stainless
steel.
The
halves
are
welded
together
and
slotted
to
accommodate
two
blade
tip
tangs
and
cover
stands.
The
seals
are
bolted
Z-2.5
R-1

to
the
carrier through
ears
mntching
those
in
the
torque
bands. These
same
bolts
provide
the
means
for
assembly
of
the
carrier,
seal,
cover,
carrier
tab
and
torque
band. The
grommet
used
to
align
the
torque
band
extends
into
the
center
hole
of
each
seal
segment
to
establish location.
2.11
Blade
Shroud
Cover
a.
The
36
blade
shroud covers
(Figure
2.4)
form
the
remainder
of
the
aerodynamic
flow
path
at
the
comprecsor
blade
tips,
provide
an
emergency
torque
transmission
system,
and
carry
self-locking
nuts
to
attach
the
shroud covers
and
the
torque bands
and
seals
to
the
turbine
bucket
carrier.
The blade
shroud covers
are
formed from
0.015"
17-7
PH
sheet,
stress
relieved,
spot
welded
and
heat
treated.
2.12
Blade
Carrier
Pins
a.
The blade
carrier pins
attach
the
blade
tip
tang
to
the
turbine
bucket
carrier.
The
pins are
assembled
by
select
fit
and
are
manufactured
in
five
different
sizes
ranging
from
0.3899"
to
0.3914"
in
increments
of
0.0003". The
pins
(36
to
each
rotor)
are
centerless
ground
to
the
finished
dimensions from
R41
stainless
steel
age
hardened
to
Rc
35
to
43.
A
portion
of
the
diameter
of
the
pin
is
contoured
to
prevent
tang
fretting.
The
blade
carrier
pin
is
drilled
to
receive
a
small
radial
lock
pin.
2.13
Lock
Pin
a.
The
lock
pin
prevents
translation
or
rotation
of
the
blade-carrier
pin
during
fan
operation. The
lock
pin
is
machined
to
a
0.115"
to
0.120"
diameter from
403
sta.nless
steel,
Rc
20 to 26
hardness.
2.14
Lock
Strip
a.
The
lock
strip
secures
the
lock
pin
and
holds
it
in
place
during
fan
operation.
The
lock
strip
is
made
of
0.015"
321
stainless
steel sheet
and
has
a
hole
to
receive
the
lock
pin.
1-2.6

2.15
Turbine
Bucket
Carrier
Assembly
a.
The
rotor
assembly
includes
18
turbine
bucket
carrier
assemblies
(Figure
2.4).
Each
turbine bucket
carrier
assembly
(or
segment)
consists
of
18
turbine
buckets,
18
tip
shrouds,
and
a
carrier
brazed
to
form
a
permanent assembly.
2.16
Turbine
Buckets
a.
The
turbine
buckets
are
hollow
shells
formed
to
aerodynamic
shape
fromn
seamless
cylinders
of
0.015"
:nconel
X
stainless
steel.
Each
bucket contains
one
stiffener
rib
running
the
full
length
of the
airfoil
at
mid-chord,
and
two
inserts (one
at
the
leading
edge
and one
at
the
trailing
edge),
and
three
bulkhead
panels
at
the
root
of
the
turbine
bucket.
These
components
are
tweezer
welded
into
a
sub-assembly
and
brazed
prior
to
final
assembly
to
the
turbine bucket
carrier.
2.17
Bucket Tip Shrouds
a.
The
bucket
tip
shrouds limit
tangential
displacement
of
the
bucket
tip,
act
as
a
bucket vibration
damper,
provide
a
radial
seal
against
hot
gas
leakage across
the
bucket
tip
and
form
the
outer
flow
path
for
hot
gas
passing
through
the
turbine.
The
shrouds
are.stamped
from 0.010"
Inconel
X-sheet
ard
are
pierced
with
slots
to
accommodate
the
bucket
tip
airfoil
profile.
The
shrouds
are
brazed
to
the
bucket
tip
during
the
final
brazing
of
the
bucket-carrier
assembly.
2.18
Bucket
Carrier
a.
The
bucket carrier
forms
the
inner
flow
path
through
the
turbine,
supports
the
turbine
buckets
and
provides
the
means
of
attaching
the
tip
turbine,
fen
blades, torque bands,
and
seals.
The
carrier
assembly consists
of
two
side
plates,
a
c.-oss
beam,
a
yoke,
and
a
platform.
b.
The
side
plates
are
the
primary
members
of the
carrier
structure.
They
are
machined
from
Inconel
X
stainless
steel
bar and
have
a
channel
shape
with
tapered
flanges.
1-2.7
This manual suits for next models
2
Table of contents
Other GE Fan manuals
Popular Fan manuals by other brands

Ruck Ventilatoren
Ruck Ventilatoren DVA ECP31 Series Assembly instruction

Yoer
Yoer FHH01W MISTO manual

Cata
Cata E Glass instruction manual
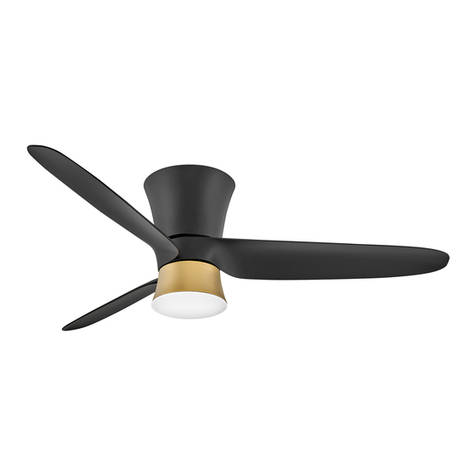
Hinkley
Hinkley NEO 905452FMW-LDD instruction manual
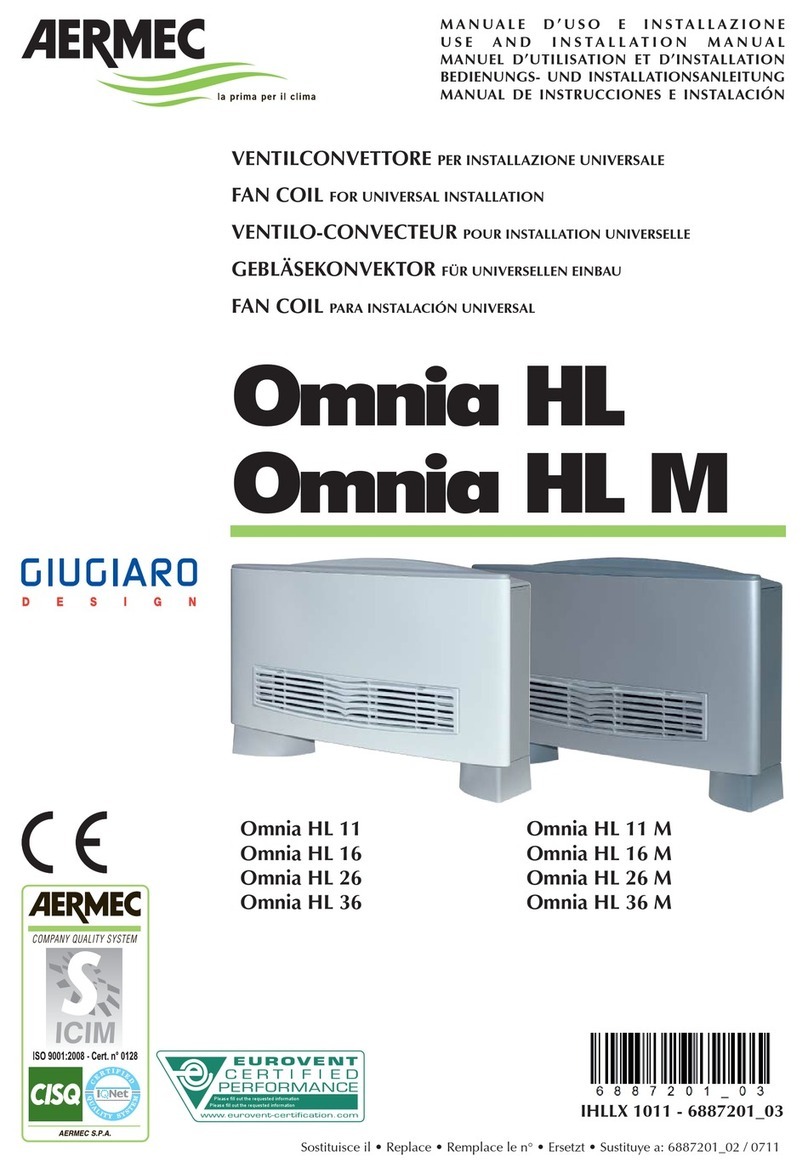
AERMEC
AERMEC Omnia HL M Use and installation manual
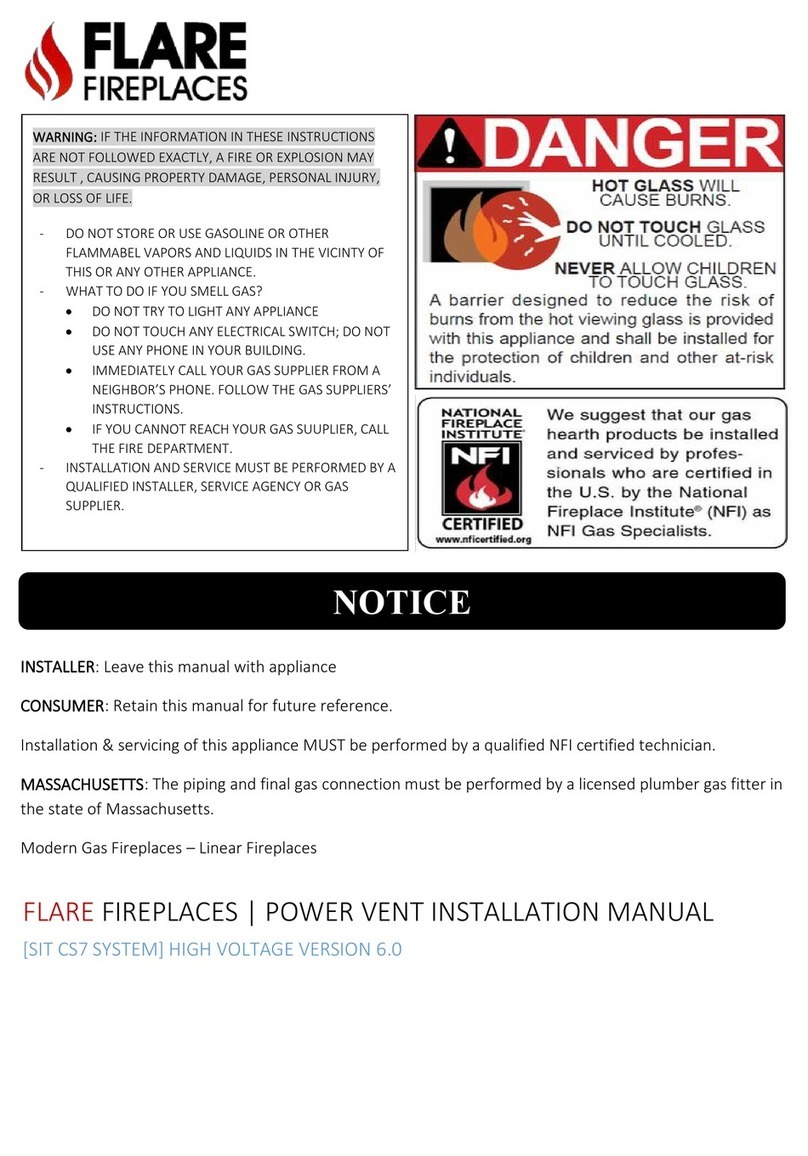
Flare Fireplaces
Flare Fireplaces Flare Front 30-100" installation manual