GEM 343 eSyDrive User manual

GEMÜ 343 eSyDrive
Motorized multi-port globe valve
Operating instructions
EN

All rights including copyrights or industrial property rights are expressly reserved.
Keep the document for future reference.
© GEMÜ Gebr. Müller Apparatebau GmbH & Co. KG
27.04.2021
www.gemu-group.com2 / 31GEMÜ 343 eSyDrive

Contents
1 General information ................................................... 4
1.1 Information ......................................................... 4
1.2 Symbols used ..................................................... 4
1.3 LED symbols ....................................................... 4
1.4 Definition of terms ............................................. 4
1.5 Warning notes .................................................... 4
2 Safety information .................................................... 5
3 Product description ................................................... 5
4 GEMÜ CONEXO ......................................................... 8
5 Correct use ................................................................ 8
6 Order data ................................................................. 9
7 Technical data ........................................................... 11
8 Dimensions ............................................................... 17
8.1 Actuator dimensions .......................................... 17
8.2 Body dimensions ................................................ 18
8.2.1 Flange, connection code 8, 11 .............. 18
8.2.2 Threaded socket .................................... 19
9 Delivery ..................................................................... 20
10 Transport .................................................................. 20
11 Storage ..................................................................... 20
12 Installation in piping .................................................. 20
12.1 Preparing for installation ................................... 20
12.2 Installation position ........................................... 21
12.3 Installation with flanged connection ................. 21
13 Electrical connection ................................................. 22
14 Network connection .................................................. 23
14.1 Network settings ................................................ 23
14.2 Connecting the network ..................................... 23
14.3 Resetting the network settings ......................... 23
15 Commissioning ......................................................... 23
16 Operation .................................................................. 23
16.1 Operation on the device ..................................... 23
16.2 Operation via the web server ............................. 23
16.3 Manual override .................................................. 23
17 Inspection and maintenance ...................................... 25
17.1 Spare parts ......................................................... 25
18 Troubleshooting ........................................................ 26
19 Removal from piping ................................................. 27
20 Disposal .................................................................... 27
21 Returns ..................................................................... 27
22 Declaration of Incorporation according to 2006/42/
EC (Machinery Directive) ........................................... 28
23 Declaration of conformity according to 2014/68/EU
(Pressure Equipment Directive) ................................. 29
24 Declaration of conformity according to 2014/30/EU
(EMC Directive) ......................................................... 30
GEMÜ 343 eSyDrivewww.gemu-group.com 3 / 31

www.gemu-group.com4 / 31GEMÜ 343 eSyDrive
1 General information
1 General information
1.1 Information
•The descriptions and instructions apply to the standard
versions. For special versions not described in this docu-
ment the basic information contained herein applies in
combination with any additional special documentation.
•Correct installation, operation, maintenance and repair
work ensure faultless operation of the product.
•Should there be any doubts or misunderstandings, the Ger-
man version is the authoritative document.
•Contact us at the address on the last page for staff training
information.
1.2 Symbols used
The following symbols are used in this document:
Symbol Meaning
Tasks to be performed
Response(s) to tasks
– Lists
1.3 LED symbols
The following LED symbols are used in the documentation:
Symbol LED conditions
Off
Lit (on)
Flashing
1.4 Definition of terms
Working medium
The medium that flows through the GEMÜ product.
1.5 Warning notes
Wherever possible, warning notes are organised according to
the following scheme:
SIGNAL WORD
Type and source of the danger
Possible
symbol for the
specific
danger
Possible consequences of non-observance.
Measures for avoiding danger.
Warning notes are always marked with a signal word and
sometimes also with a symbol for the specific danger.
The following signal words and danger levels are used:
DANGER
Imminent danger!
▶Non-observance can cause death or
severe injury.
WARNING
Potentially dangerous situation!
▶Non-observance can cause death or
severe injury.
CAUTION
Potentially dangerous situation!
▶Non-observance can cause moderate
to light injury.
NOTICE
Potentially dangerous situation!
▶Non-observance can cause damage to
property.
The following symbols for the specific dangers can be used
within a warning note:
Symbol Meaning
Danger of explosion
Corrosive chemicals!
Hot plant components!
Hot actuator parts!
Rotating cover!
Replacement of spare parts

www.gemu-group.com 5 / 31 GEMÜ 343 eSyDrive
2 Safety information
The safety information in this document refers only to an in-
dividual product. Potentially dangerous conditions can arise
in combination with other plant components, which need to
be considered on the basis of a risk analysis. The operator is
responsible for the production of the risk analysis and for
compliance with the resulting precautionary measures and
regional safety regulations.
The document contains fundamental safety information that
must be observed during commissioning, operation and
maintenance. Non-compliance with these instructions may
cause:
•Personal hazard due to electrical, mechanical and chemical
effects.
•Hazard to nearby equipment.
•Failure of important functions.
•Hazard to the environment due to the leakage of dangerous
materials.
The safety information does not take into account:
•Unexpected incidents and events, which may occur during
installation, operation and maintenance.
•Local safety regulations which must be adhered to by the
operator and by any additional installation personnel.
Prior to commissioning:
1. Transport and store the product correctly.
2. Do not paint the bolts and plastic parts of the product.
3. Carry out installation and commissioning using trained
personnel.
4. Provide adequate training for installation and operating
personnel.
5. Ensure that the contents of the document have been fully
understood by the responsible personnel.
6. Define the areas of responsibility.
7. Observe the safety data sheets.
8. Observe the safety regulations for the media used.
During operation:
9. Keep this document available at the place of use.
10. Observe the safety information.
11. Operate the product in accordance with this document.
12. Operate the product in accordance with the specifica-
tions.
13. Maintain the product correctly.
14. Do not carry out any maintenance work and repairs not
described in this document without consulting the manu-
facturer first.
In cases of uncertainty:
15. Consult the nearest GEMÜ sales office.
3 Product description
3.1 Construction
1
2
3
4
5
6
7
Item Name Materials
1 O-rings EPDM
2 Electrical connections
3 Actuator base 1.4301
4 Distance piece with leak
detection hole
1.4408
5 Valve body 1.4408, cast bronze
6 Optical position indicator PESU
7 Cover with high visibility
LED, manual override and
on-site control
PESU
3 Product description

www.gemu-group.com6 / 31GEMÜ 343 eSyDrive
3 Product description
3.2 Buttons for on-site control
8
9
10
Fig.1: Position of the buttons
Item Name Function
8 DIP switch, "ON-
site" control
Switches the on-site
control on the device
on or off
9 "OPEN" button Moves actuator to
the open position
Resets the network
settings
10 "INIT/CLOSE" but-
ton
Moves actuator to
the closed position
Starting initialisation
3.3 LED displays
3.3.1 On-site status LEDs
LED MODE LED PWR
Fig.2: Position of the status LEDs
The user checks the following conditions directly on-site at
the valve using LED MODE and LED PWR:
Function LED MODE LED PWR
Yellow Blue Green Red
Automatic oper-
ation
Manual opera-
tion
Actuator
switched off
(OFF mode)
Manual opera-
tion (on-site)
Software update
alternating
On-site initial-
isation (buttons)
Remote initial-
isation (via Di-
gIn)

www.gemu-group.com 7 / 31 GEMÜ 343 eSyDrive
Function LED MODE LED PWR
Yellow Blue Green Red
Operation via
emergency
power supply
module
3.3.2 High visibility LEDs
11
11 11
11 11
11
Fig.3: Position of the high visibility LEDs
Item Name
11 High visibility LEDs
Function High visibility LED
Green Orange
OPEN position Position indicator
LEDs,
standard
OPEN position Position indicator
LEDs,
inversed
CLOSED position Position indicator
LEDs,
standard
CLOSED position Position indicator
LEDs,
inversed
Position unknown (e.g. 50%)
Initialisation
alternating
Function High visibility LED
Green Orange
Location function
3.4 Description
The GEMÜ 343 is a motorized 3/2-way globe valve with a
hollow shaft electric actuator. The eSyDrive hollow shaft ac-
tuator can be operated as ON/OFF or with integrated posi-
tioner or process controller. The valve spindle is sealed by a
self-adjusting gland packing providing low maintenance and
reliable valve spindle sealing even after a long service life. A
wiper ring fitted in front of the gland packing protects the
seal against contamination and damage. An integral optical
and electrical position indicator is standard.
3.5 Function
The product controls or regulates (depending on version) a
flowing medium by being closed or opened by a motorized
actuator.
The product has an optical position indicator as standard.
The optical position indicator indicates the OPEN and
CLOSED positions.
3.5.1 Functions
Flange - Distribution Threaded socket - Distribu-
tion
A
AB
B
R
A
P
Flange - Mixing Threaded socket - Mixing
A
AB
B
R
A
P
3 Product description

www.gemu-group.com8 / 31GEMÜ 343 eSyDrive
4 GEMÜ CONEXO
3.6 Regulating cone/regulating cage
Regulating cone Regulating cage
Regulating cone: DN 15 - 50 Regulating cage: DN 65 - 100
4 GEMÜ CONEXO
Order with CONEXO
GEMÜ CONEXO must be ordered separately with the ordering
option "CONEXO" (see order data).
For electronic identification purposes, each replaceable com-
ponent contained in the product is equipped with an RFID
chip (1). Where you can find the RFID chip differs from
product to product.
1
The CONEXO pen helps read out information stored in these
RFID chips. The CONEXO app or CONEXO portal is required to
view this information.
5 Correct use
DANGER
Danger of explosion
▶Risk of death or severe injury.
●Do not use the product in potentially
explosive zones.
WARNING
Improper use of the product
▶Risk of severe injury or death.
▶Manufacturer liability and guarantee will be void.
●Only use the product in accordance with the operating
conditions specified in the contract documentation and
in this document.
The product is designed for installation in piping systems
and for controlling a working medium.
The product is not intended for use in potentially explosive
areas.
●Use the product in accordance with the technical data.

6 Order data
The order data provide an overview of standard configurations.
Please check the availability before ordering. Other configurations available on request.
Order codes
1 Type Code
Multi-port globe valve, motorized,
electro-mechanical hollow shaft actuator,
body with flanged connection,
eSyDrive
343
2 DN Code
DN 15 15
DN 20 20
DN 25 25
DN 32 32
DN 40 40
DN 50 50
DN 65 65
DN 80 80
DN 100 100
3 Body configuration Code
Multi-port version M
4 Connection type Code
Threaded socket DIN ISO 228 1
Flange EN 1092, PN 16, form B,
face-to-face dimension FTF EN 558 series 1, ISO
5752, basic series 1
8
Flange EN 1092, PN 40, form B,
face-to-face dimension FTF EN 558 series 1, ISO
5752, basic series 1
11
5 Valve body material Code
CC499K, cast bronze 9
1.4408, investment casting 37
6 Seat seal Code
PTFE 5
PTFE, glass fibre reinforced 5G
7 Voltage/frequency Code
24 V DC C1
8 Control module Code
OPEN/CLOSE, positioner and process controller L0
9 Regulating cone Code
Please find the number of the optional regulating
cone (R-No.) for the linear or equal-percentage
modified regulating cone in the Kv value table.
R….
10 Actuator version Code
Actuator size 0 0A
Actuator size 1 1A
Actuator size 2 2A
11 Special version Code
Special version for oxygen,
maximum medium temperature: 60°C,
media wetted seal materials and auxiliary materi-
als with BAM testing
S
12 CONEXO Code
Without
Integrated RFID chip for electronic identification
and traceability
C
6 Order data
www.gemu-group.com 9 / 31 GEMÜ 343 eSyDrive

Order example
Order option Code Description
1 Type 343 Multi-port globe valve, motorized,
electro-mechanical hollow shaft actuator,
body with flanged connection,
eSyDrive
2 DN 40 DN 40
3 Body configuration M Multi-port version
4 Connection type 11 Flange EN 1092, PN 40, form B,
face-to-face dimension FTF EN 558 series 1, ISO 5752, basic series 1
5 Valve body material 37 1.4408, investment casting
6 Seat seal 5 PTFE
7 Voltage/frequency C1 24 V DC
8 Control module L0 OPEN/CLOSE, positioner and process controller
9 Regulating cone RS916 60 m³/h - mod.EQ
10 Actuator version 2A Actuator size 2
11 Special version S Special version for oxygen,
maximum medium temperature: 60°C,
media wetted seal materials and auxiliary materials with BAM testing
12 CONEXO Without
6 Order data
www.gemu-group.com10 / 31GEMÜ 343 eSyDrive

7 Technical data
7.1 Medium
Working medium: Corrosive, inert, gaseous and liquid media which have no negative impact on the physical and
chemical properties of the body and seal material.
Max. permissible viscos-
ity:
600 mm²/s (cSt)
Other versions for lower/higher temperatures and higher viscosities on request.
7.2 Temperature
Media temperature: -10 — 180 °C
Ambient temperature: -10 — 60 °C
7.3 Pressure
Operating pressure: B – AB / AB - A
DN Actuator version
0A
Flange
0A
Threaded
socket
1A
Flange
1A
Threaded
socket
2A
Flange
2A
Threaded
socket
15 32 16 - - - -
20 20 16 40 16 - -
25 16 - 32 16 - -
32 - - 20 16 - -
40 - - 12 12 25 16
50 - - 8 8 16 16
65 - - 5 - 10 -
80 - - 4 - 6 -
100 - - - - 4 -
Pressures in bar
All pressures are gauge pressures.
For max. operating pressures the pressure / temperature correlation must be observed.
Leakage rate: Open/Close valve
Seat seal Standard Test procedure Leakage rate Test medium
PTFE DIN EN 12266-1 P12 A Air
Control valve
Seat seal Standard Test procedure Leakage rate Test medium
FKM, PTFE DIN EN 60534-4 1 VI Air
GEMÜ 343 eSyDrivewww.gemu-group.com 11 / 31
7 Technical data

Pressure/temperature
correlation: Connection
types
code 1)
Material
code 2)
Max. allowable operating pressures in bar at temperature in °C
RT 100 150 200
1 9 16.0 16.0 16.0 13.5
8 37 16.0 16.0 14.5 13.4
11 37 40.0 40.0 36.3 33.7
All pressures are gauge pressures.
The valves may be used to -10 °C
RT = room temperature
1) Connection type
Code 1: Threaded socket DIN ISO 228
Code 8: Flange EN 1092, PN 16, form B, face-to-face dimension FTF EN 558 series 1, ISO 5752, basic series
1
Code 11: Flange EN 1092, PN 40, form B, face-to-face dimension FTF EN 558 series 1, ISO 5752, basic
series 1
2) Valve body material
Code 9: CC499K, cast bronze
Code 37: 1.4408, investment casting
Kv values: Open/Close valve
Flange Threaded socket
DN AB - A B - AB A - R P - A
15 4.1 5.4 2.5 3.6
20 7.5 11.6 3.3 5.5
25 12.0 17.6 7.3 10.6
32 18.8 27.0 10.4 18.0
40 30.7 46.7 20.9 31.0
50 42.0 67.1 33.7 47.0
65 71.9 119.9 - -
80 107.6 174.4 - -
100 157.1 250.7 - -
Kv values in m³/h
Kv values determined in accordance with DIN EN 60534. The Kv value specifications refer to the largest actu-
ator for the respective nominal size. The Kv values for other product configurations (e.g. other connections or
body materials) may differ.
Control valve - Flange
DN Flange
AG 0 AG 1 AG 2 Kv value
15 RS190 - - 4.0
20 RS191 RS193 - 6.3
25 RS192 RS194 - 10.0
32 - RS195 - 14.0
40 - RS196 RS200 20.0
50 - RS197 RS231 32.0
65 - RS198 RS232 63.0
80 - RS199 RS233 90.0
100 - - RS234 140.0
Kv values in m³/h
Kv values refer to the flow direction A-AB and B-AB.
www.gemu-group.com12 / 31GEMÜ 343 eSyDrive
7 Technical data

Kv values: Control valve - Threaded socket
DN Threaded socket
AG 0 AG 1 AG 2 Kv value
15 RS180 - - 1.6
20 RS181 RS183 - 2.5
25 RS182 RS184 - 6.3
32 - RS185 - 10.0
40 - RS186 RS188 16.0
50 - RS187 RS189 25.0
Kv values in m³/h
Kv values refer to the flow direction A-AB and B-AB.
7.4 Product compliance
Pressure Equipment Dir-
ective:
2014/68/EU
Machinery Directive: 2006/42/EU
7.5 Mechanical data
Protection class: IP 65 acc. to EN 60529
Weight: Actuator
Actuator version 0A 1.8 kg
Actuator version 1A 3.0 kg
Actuator version 2A 9.0 kg
Body
DN Flange Threaded socket
15 3.4 0.6
20 4.9 0.7
25 5.7 1.1
32 8.5 1.8
40 9.7 2.3
50 15.8 3.4
65 19.4 -
80 24.6 -
100 32.8 -
Weights in kg
Operating time: Actuator version 0A adjustable, max. 6 mm/s
Actuator version 1A adjustable, max. 6 mm/s
Actuator version 2A adjustable, max. 4 mm/s
GEMÜ 343 eSyDrivewww.gemu-group.com 13 / 31
7 Technical data

7.6 Electrical data
Supply voltage: Actuator size 0 Actuator size 1 Actuator size 2
Voltage Uv = 24 V DC ± 10%
Rating Max. 28 W Max. 65 W Max. 120 W
Operating mode
(OPEN/CLOSE opera-
tion)
Continuous duty
Operating mode (con-
trol operation)
Class C acc. to EN 15714-2
Reverse battery protec-
tion
Yes
7.6.1 Analogue input signals
7.6.1.1 Set value
Input signal: 0/4 - 20 mA; 0 – 10 V DC (selectable using software)
Input type: passive
Input resistance: 250 Ω
Accuracy/linearity: ≤ ±0.3% of full flow
Temperature drift: ≤ ±0.1% / 10°K
Resolution: 12 bit
Reverse battery protec-
tion:
No
Overload proof: Yes (up to ± 24 V DC)
7.6.1.2 Process actual value
Input signal: 0/4 - 20 mA; 0 – 10 V DC (selectable using software)
Input type: passive
Input resistance: 250 Ω
Accuracy/linearity: ≤ ±0.3% of full flow
Temperature drift: ≤ ±0.1% / 10°K
Resolution: 12 bit
Reverse battery protec-
tion:
No
Overload proof: Yes (up to ± 24 V DC)
www.gemu-group.com14 / 31GEMÜ 343 eSyDrive
7 Technical data

7.6.2 Digital input signals
Digital inputs: 3
Function: selectable using software
Voltage: 24 V DC
Logic level "1": >14 V DC
Logic level "0": < 8 V DC
Input current: typ. 2.5 mA (at 24 V DC)
7.6.3 Analogue output signals
7.6.3.1 Actual value
Output signal: 0/4 - 20 mA; 0 – 10 V DC (selectable using software)
Output type: Active (AD5412)
Accuracy: ≤ ±1% of full flow
Temperature drift: ≤ ±0.1% / 10°K
Load resistor: ≤ 750 kΩ
Resolution: 10 bit
Overload proof: Yes (up to ± 24 V DC)
Short-circuit proof: Yes
7.6.4 Digital output signals
7.6.4.1 Switching outputs 1 and 2
Design: 2x change-over contact, potential-free
Switch rating: 125 V AC / 2 A
48 V DC / 2 A
Switch points: Adjustable 0 - 100 %
7.6.4.2 Switching output 3
Function: Signal fault
Type of contact: Push-Pull
Switching voltage: Supply voltage
Switching current: ≤ 0.1 A
Drop voltage: Max. 2.5 V DC at 0.1 A
Overload proof: Yes (up to ± 24 V DC)
Short-circuit proof: Yes
Pull-Down resistance: 120 kΩ
GEMÜ 343 eSyDrivewww.gemu-group.com 15 / 31
7 Technical data

7.6.5 Communication
Interface: Ethernet
Function: Parameterisation via web browser
IP address: 192.168.2.1 alterable via web browser
Subnet screen: 255.255.252.0 alterable via web browser
The actuator and the PC must be in the same network to use the web server. The IP address of the actuator is entered in the
web browser and the actuator can then be parametrised. In order to use more than one actuator, a definitive IP address must
be assigned to each actuator in the same network.
www.gemu-group.com16 / 31GEMÜ 343 eSyDrive
7 Technical data

8 Dimensions
8.1 Actuator dimensions
B
B1
B2
B3
A1
Actuator
version
A1 B B1 B2 B3
0A 45.0 68.0 126.0 160.0 193.0
1A 86.0 82.0 132.0 172.0 252.0
2A 121.0 129.0 157.0 224.0 304.0
GEMÜ 343 eSyDrivewww.gemu-group.com 17 / 31
8 Dimensions

8.2 Body dimensions
8.2.1 Flange, connection code 8, 11
ØD
H2
FTF
Ød1
ØL
Øk
C
A
B
AB
DN Connection types code 1)
8 11
Material code 37 2)
FTF H2 ø D ø L c ø K n FTF H2 ø D ø L c ø K n
15 - - - - - - - 130.0 97.0 95.0 14.0 16.0 65.0 4
20 - - - - - - - 150.0 112.0 105.0 14.0 18.0 75.0 4
25 - - - - - - - 160.0 118.0 115.0 14.0 18.0 85.0 4
32 - - - - - - - 180.0 143.0 140.0 18.0 18.0 100.0 4
40 - - - - - - - 200.0 147.0 150.0 18.0 18.0 110.0 4
50 230.0 - 165.0 18.0 - 125.0 - 230.0 167.0 165.0 18.0 20.0 125.0 4
65 290.0 183.0 185.0 18.0 20.0 145.0 4 - - - - - - -
80 310.0 204.0 200.0 18.0 22.0 160.0 8 - - - - - - -
100 350.0 236.0 220.0 18.0 24.0 180.0 8 - - - - - - -
Dimensions in mm, n = number of bolts
1) Connection type
Code 8: Flange EN 1092, PN 16, form B, face-to-face dimension FTF EN 558 series 1, ISO 5752, basic series 1
Code 11: Flange EN 1092, PN 40, form B, face-to-face dimension FTF EN 558 series 1, ISO 5752, basic series 1
2) Valve body material
Code 37: 1.4408, investment casting
www.gemu-group.com18 / 31GEMÜ 343 eSyDrive
8 Dimensions

8.2.2 Threaded socket
L
H2
R
R
RSW 2
R
A
P
DN Connection types code 1 1)
Material code 9 2)
R L SW1 SW2 H2 CT Actu-
ator 1
CT1 Ac-
tuator 1
CT Actu-
ator 2
CT1 Ac-
tuator 2
15 G 1/2 75 36 27 41 192 88 - -
20 G 3/4 87 36 32 46 196 92 - -
25 G 1 107 41 41 47 196 92 - -
32 G 1¼ 123 55 50 66 200 96 277 125
40 G 1½ 147 55 58 68 200 96 277 125
50 G 2 171 55 70 74 204 100 281 125
Dimensions in mm
1) Connection type
Code 1: Threaded socket DIN ISO 228
2) Valve body material
Code 9: CC499K, cast bronze
GEMÜ 343 eSyDrivewww.gemu-group.com 19 / 31
8 Dimensions

www.gemu-group.com20 / 31GEMÜ 343 eSyDrive
9 Delivery
9 Delivery
●Check that all parts are present and check for any dam-
age immediately upon receipt.
The product's performance is tested at the factory. The
scope of delivery is apparent from the dispatch documents
and the design from the order number.
10 Transport
1. Only transport the product by suitable means. Do not
drop. Handle carefully.
2. After the installation dispose of transport packaging ma-
terial according to relevant local or national disposal reg-
ulations / environmental protection laws.
11 Storage
1. Store the product free from dust and moisture in its ori-
ginal packaging.
2. Avoid UV rays and direct sunlight.
3. Do not exceed the maximum storage temperature (see
chapter "Technical data").
4. Do not store solvents, chemicals, acids, fuels or similar
fluids in the same room as GEMÜ products and their
spare parts.
12 Installation in piping
12.1 Preparing for installation
WARNING
The equipment is subject to pressure!
▶Risk of severe injury or death.
●Depressurize the plant.
●Completely drain the plant.
WARNING
Corrosive chemicals!
▶Risk of caustic burns.
●Wear suitable protective gear.
●Completely drain the plant.
CAUTION
Hot plant components!
▶Risk of burns.
●Only work on plant that has cooled
down.
CAUTION
Exceeding the maximum permissible pressure.
▶Damage to the product.
●Provide precautionary measures against exceeding the
maximum permitted pressures caused by pressure
surges (water hammer).
CAUTION
Use as step.
▶Damage to the product.
▶Risk of slipping-off.
●Choose the installation location so that the product can-
not be used as a foothold.
●Do not use the product as a step or a foothold.
NOTICE
Suitability of the product!
▶The product must be appropriate for the piping system
operating conditions (medium, medium concentration,
temperature and pressure) and the prevailing ambient
conditions.
Other manuals for 343 eSyDrive
1
Table of contents
Other GEM Control Unit manuals
Popular Control Unit manuals by other brands
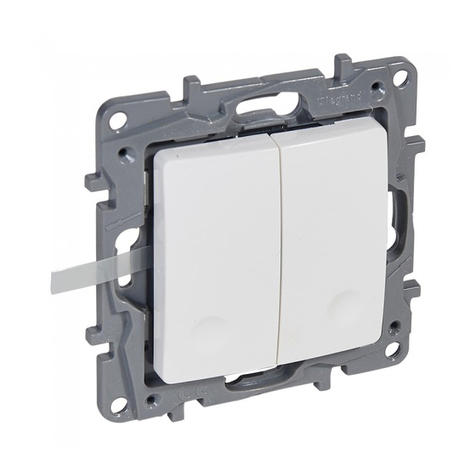
LEGRAND
LEGRAND 0 746 85 manual

Toshiba
Toshiba V Series Operation manual
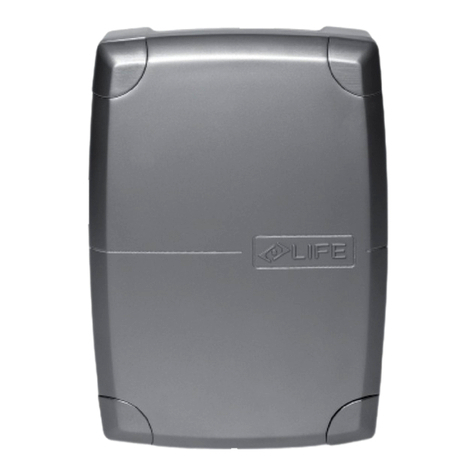
LIFE home integration
LIFE home integration GENIUS GE 224 Instructions and indications for installation, use and maintenance
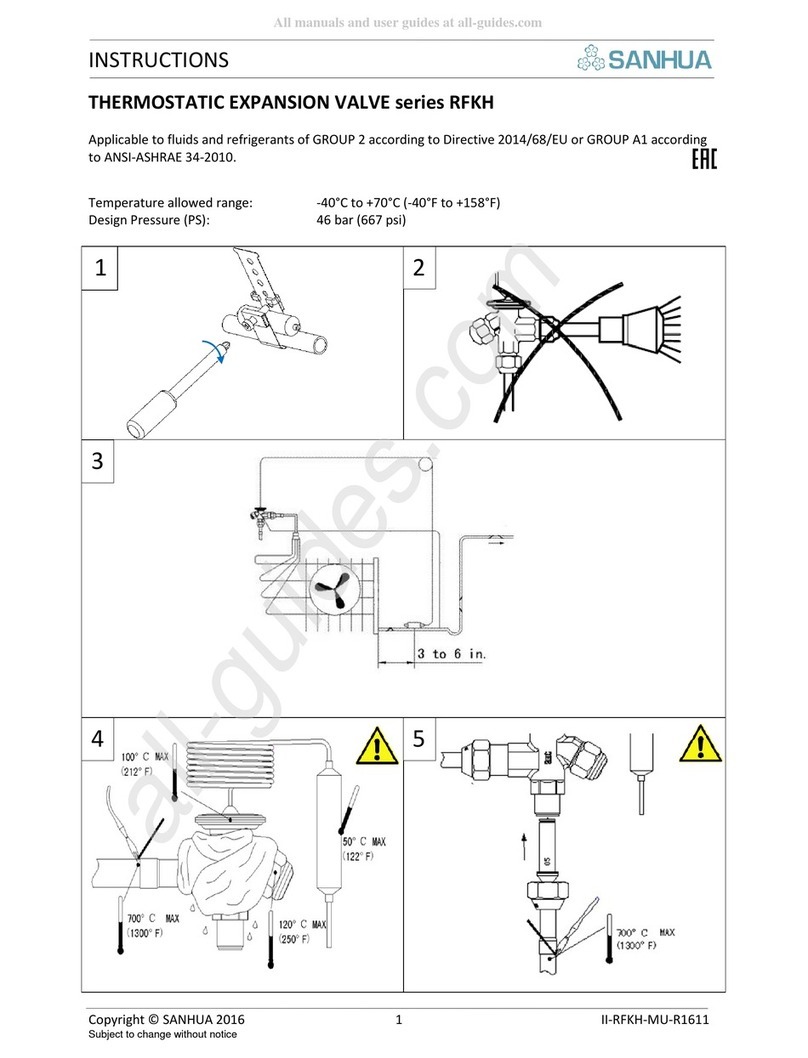
Sanhua
Sanhua RFKH Series instructions

Viessmann
Viessmann VITOTRONIC 300 Technical data manual
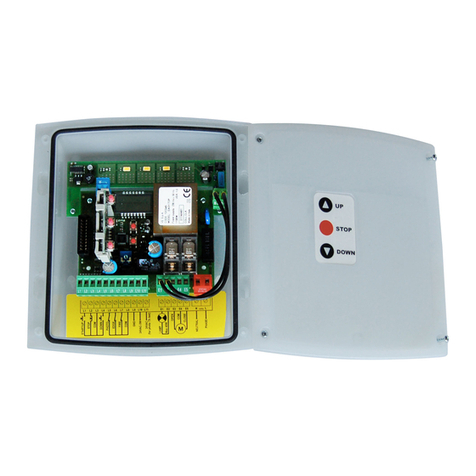
V2
V2 Easy 3 manual