IKA HS 260 Basic User manual

Page
Declaration of conformity 2
Guarantee 2
Safety instructions 19
Proper use 20
Unpacking 20
Useful facts 21
Commissioning 21
Switching on 21
Display 22
Operating modes 22
Setting the agitation time 26
Setting the speed 27
Attachments 28
Supported weight (load) 28
Error codes 29
Interface and outputs 30
Communication between laboratory instrument and PC
32
Motor protection / safety device 33
Maintenance and cleaning 33
Accessories 34
Technical data 34
List of spare parts basic / control 52
Spare parts diagram (control) 54/55
In order to be able to use the appliance properly and safely, every user
must first read the operating instructions and observe the safety instruc-
tions contained therein. Take care of these operating instructions and
keep them in a place where they can be accessed by everyone.
Only staff who have been trained accordingly, know the appliance and
are authorised to carry out work in this field should use this appliance.
The machine may only be opened by trained specialists - even during
repairs. The machine is to be unplugged from the mains before opening.
Live parts inside the machine may still be live for some time after unplug-
ging from the mains.
NOTE ! Covering or parts that are capable of being removed
from the unit without accessory equipment have to be reat-
tached to the unit for safe operation in order to prevent, for
example, the ingress of fluids, foreign matter, etc. .
When working with the shaking unit, the user must select and wear his
personal protective equipment according to the mixing hazard category.
Defective or inadequate protective equipment can expose the user to
the risk of spurting liquids, projectile parts or being pulled in at the sha-
king table or support. Never touch moving parts (risk of crushing, impact
and cutting, see fig. 1: Danger zones).
Ensure that parts of the body,
hair or items of clothing cannot
be trapped by the motion parts.
Please follow the relevant safety
instructions and guidelines, and
occupational health and safety
regulations for use in the labo-
ratory.
Beware of the high dead weight
of the appliance when transpor-
ting. Ensure that your fingers do
not get crushed when setting
down the appliance.
Always install the appliance
on a flat, stable non-slip base.
Before use, please ensure that
the knob for setting the shaking
rate is at the left stop as the
appliance starts up at the last sha-
king rate which was set. Pay attention to the vessels on the shaking table
when setting the shaking rate. This will prevent any of the medium to be
shaken from spurting out of the sample vessels.
All accessories and vessels in place for the shaking process must be
19
Contens
Contens
fig. 1 danger zones

firmly secured.
Shaking vessels which are not properly secured could get damaged or
be projected out, thus causing injury. It is essential to regularly check
that the vessels to be shaken and the attachments are firmly secured,
especially before using the appliance again.
If you notice that the device is not running smoothly, the speed must
always be reduced until no more uneveness occurs in the operation.
Because of improper loading and the position of the center of gravity,
dynamic forces may arise during the agitation process that cause the
shaker to move about on the table. For limits on the load or the weight
placed on the agitation table at high shaking frequencies, please refer
to the diagram in the section “ Weight placed on the table“ (just before
the list of spare parts).
After an interruption in the power supply during an agitation procedu-
re, the device will not start running again by itself.
Additional hazards to the user may occur if inflammable materials are
used during the shaking operation.
Furthermore, the shaking unit may only be used to stir those materials or
material mixtures that the user knows will not react dangerously to the
extra energy produced by the stirring. This also applies to extra energy
by means of solar radiation during the shaking procedure.
The shaker may not been used in explosive atmospheres, for mixing
dangerous substances or under water.
Accessories may only be assembled once the plug has been disconnec-
ted.
The safety of the user cannot be guaranteed if the appliance is ope-
rated with accessories that are not supplied or recommended by the
manufacturer or if the appliance is operated improperly, contrary to the
manufacturer’s specifications.
The original
IKA
®
cable layout must be restored following servicing!
If the target value of the speed is changed too rapidly, the machine
(HS/KS 260 basic) will turn itself off automatically. Avoid allowing
objects to push or strike the agitation table.
Even small undetectable damage may result in serious damage to the
motor bearing. Careful handling will guarantee safe work and a long
service life of the machine.
The HS/KS260basic and HS/KS260control are suitable for usage in
various attachments for mixing liquids in bottles, flasks, test tubes and
bowls for a maximum supported weight of 7,5 kg.
It is designed for use in laboratories. The motion of the agitation table
or of the containers placed on it is circular or horizontal.
For usage in accordance with requirements, the machine must be
standing on a stable, even surface that is as slip-free as passible. In
addition, care must be taken that qbjects in the vicinty are a sufficient
distance away from the agitator and that they will not come too close
to the agitator while it is in operation.
Please unpack the equipment carefully and check for any damages. It
is important that any damages which may have arisen during transport
are ascertained when unpacking. If applicable a fact report must be
sent immediately (post, rail or forwarder).
The delivery scope covers:
A HS/KS 260 basic or HS/KS 260 control, for attachment screws, a
single-head spanner, a connection cable and operating instructions.
20
Proper use
Unpacking

21
With the purchase of this device, you have acquired a high-quality
product. The design of the unit and its special shape ensure ease
of handing and problem-free work. the materials used and an exact
designation of them will significantly facilitate and simplify recycling
and reuse of parts.
The speed-controlled external rotor asynchronous motor allows for
infinitie speed adjustment in the range from 0 to 500 rpm (KS) and 0
to 300 rpm (HS). Electronic motor control holds the set speed constant
even if the weight of the material on the surface increases. The heat
given off by the motor can be used to heat up the holding surface for
the agitation containers.
The Control variant of the device is equipped with a locking device. This
makes it possible to fasten the agitation table in a defined position.
For
example the device can be integrated into a system or screwed
with a table. In addition, the rubber feet must be unscrewed from
the base plate so that the exposed threaded hole (M6) can be
used to secure the device.
Make certain that the maximum depth of
5 mm for inserting the screws is not exceeded.
The Control variant of the device can be delivered with a reverse opera-
ting mode (clockwise / counterclockwise motion) for the vibration table
on request. However, the reverse operation mode can only be used by
means of the serial interface in combination with a PC (for example
with labworldsoft®). If the device is not operated on a serial interface,
it behaves like a Control device without reverse operation mode.
It is easy to exchange the various attachments.
The Control device variant is equipped with a serial interface that
makes it possible to control the device through the PC (for example
with labworldsoft®.
Check whether the voltage specified on the type plate matches the
mains voltage available. The power socket used must be earthed
(protective earth conductor contact). If these conditions are met, the
device is ready to operate after plugging in the mains plug. If these
procedures are not followed, safe operation cannot be guaranteed
and/or the equipment may be damaged.
Observe the ambient conditions (temperature, humidity, etc.) listed
under Technical Data.
When you turn on the basic device variant, the turn button for the time
setting must be in the middle setting (not activated).
If the mounting surface is not even, you can improve the safety level
of the device in reference to how it stands with the adjustable feet. To
do this, turn the appropriate device foot downward with the wrench
(included with delivery) until the device is standing securely on the
surface.
To prevent the foot of
the device from coming
loose by itself, hold
down the foot with one
hand and tighten the
oppsite hexagonal nut
with the other hand until
it is finger tight.
The device can be turned with the flip switch Aon the front side of the
unit. After you have turned on the power switch to position I, all light
diodes of the basic variant will light up for a brief time in the display
windows as a self-test that follows. The red light diode in the TIME LED
line and the OFF mode of the device light (audio signal).
All elements of the display will flash using the control unit and the
self test operation will be shown on the display. All important safety
functions will be tested. The appliance is operable after this check.
Useful facts
Commissioning
IKA R
1/min
minTime
basicHS 250
OFF
ON 10515
Mot 60
30 90
2520 30 35 4540 50
210120 150 180 270240 300
A
Switching on

22
Description of the LED-Display - HS/KS 260 basic
The basic model of the device can be used in continuous or timed
mode depending on the option you select. The ride turn button is used
to make the setting..
Continuous operation:
The device does not interrupt the agitation
sequence (On-LED is lit).
Time operation:
The device interrupts the agitation process
after a set amount of time (max. 50 minutes).
The speed required for the agitation process can be adjusted before
ore after the operating mode is selected.
The HS/KS 260 basic is adjusted so that after you press the power
switch, the agitation process (speed) and time mode is turned off
(Off-LED lights up).
Description of the LCD-Display - HS/KS 260 control
Settingthe operation mode (control model only)
The Control device model can be operated in the modes described
below:
Operation mode A:
The HS/KS 260 control is switched into operating mode Awhen it
leaves the factory. After the device is turned on with the power switch
(flip switch), the agitation and time expiration functions are turned
off. The set target values are stored and are displayed digitally. They
are adopted when the corresponding functions are turned on. the set
target values can be varied. After the power has been turned off and
Display
50 100 150 200 250
Mot 1/min
Time min
300 350 400 450 500
On Off 40 45 50
35302010 15525
Display element for the setting speed
Display element for
the setting agitation time
Continuous
operation
Standstill
Real value Rated value
e.g. phys. unit,
mode of operation,
error code
Mode of operation A: Star out
Mode of operation B: Star on
Mode of operation C: Star flash
SV = Set Value
(Rated value) PV = Processt Value
(Real value)
Operating modes
== Locking

23
back on, both functions must be started again. The upper speed limit
can only be set or changed in operating mode A. You can recognice
operating mode Aby the fact that no star is displayed in the menu bar
display of the time setting.
After the power has been interrupted, the device will no longer auto-
matically start up in operating mode Aby itself any more.
After you have selected the operating mode and turned on the device,
the following process will be shown on the display.
a.) All display elements in the digital displays are activated for about 2
seconds.
b.) The device type (left display) and operating mode (right display) are
displayed for about 2 seconds.
c.) After this, the set (ore stored) upper speed limit of the agitator
is shown in the left display with SAFE, the unit of measure rpm and
flashing SV for about 2 seconds. As long as the display is flashing
with SV , it is possible to change the upper speed limit by pressing
the turn button and turning at the same time.
d.) If the upper speed limit is fixed, the unit 1/min in the left display
changes to OK. The new time target value that is set or stored in the
right display (for example 3:58) is displayed with an indication of h
min and a flashing SV .
e.) The new speed target value that has been set or stored in the left
display (for example 130) is then shown with the unit 1/min and
flashing SV .
f.) By pressing the left or the right turn button, you can place the agi-
tator in operation with the stored value or the one that has just been
set. The actual speed and time values are then shown in large format
on the display. The actual value of the time setting must be understood
from this point onward as the time remaining for the agitation process.
If zhe remaining has reached zero, the agitator stops its motion.
Operating mode B:
When the device is turned on, target values for speed and time setting
are adopted before the device is turned off (power OFF). The upper
speed limit that has been set is taken over from operating mode A
when this operating mode is selected and cannot be modified.
When you turn on the device with the power switch, a Bis shown on
260
KS A
230
SAFE
SV
I
min
/
A
230
SAFE
minn
i
358
:
SV
SV
OK
I30
I
min
/
SV
minn
i
358
:
SV
I30
I30
I
min
/
PV PV
minn
i
356
.
358
:

24
the display for operating mode Balong with * in the right display.
After the power has been turned off,the device will no longer auto-
matically start up in operating mode Bby itself.
After you have selected operating the mode and turned on the device,
the following process will be shown on the display.
a.) All display elements in the digital displays are activated for about 2
seconds.
b.) The device type (left display) and operating mode (right display)
displayed for about 2 seconds.
c.) After this, the set (or stored) upper speed limit of the agitator is
shown in the left display with SAFE and OK for about 2 seconds. As
long as the upper speed limit is being displayed, it is not possible ti
change the upper speed limit. The stored time target value or the one
that has just been set (for example 3:58) is shown in the right display
with the indication h min and a flashing SV . The user can recognize
that operating mode Bis active by the star *in the display for the
time setting.
d.) The new speed target value has been set or just stored in the left
display (for example 130) is the shown in the unit 1/min and flashing
SV .
e.) By pressing the left or right turn button, you can place the agitator
in operation with the stored value or the one that has just been set.
The speed and time values are then shown in large format on the
display. In addition, the text PV is shown on the display instead of
SV . The actual value of the time setting must be understood from
this point onward as the time remaining for the agitation process. If
the time remaining has reached zero, the agitator stops its motion.
Operating mode C:
The upper speed limit that has been sett is taken over from operating
mode Awhen this operating mode is selected and cannot be modi-
fied. The target values from operating mode A oder B are adopted for
speed and time and cannot be modified. When you turn on the device
with the power switch, a Cis shown on the display for operating mode
Calong with *in the display.
After the power has been turned off, the device will auto-
matically start up in operating mode Cby itself.
After you have selected operating the mode and turned on the device,
the folling process will be shown on the display.
260
KS A
230
SAFE
minn
i
358
:
SV
OK
4
I30 I30
Imin
/
PV PV
minn
i
356
.358
:
4
I30
I
min
/
SV
minn
i
358
:
SV 4

25
a.) All display elements in the digital displays are activated for about 2
seconds.
b.) The device type (left display) and operating mode (right display) are
displayed for about 2 seconds.
c.) IThe set time target value (for example 3:58) is displayed with
the indication h min and SV .The set (or stored) upper speed limit
from operating mode Ais displayed with SAFE and OK for about 2
seconds. The display upper speed limit cannot be modified by pressing
and turning the turn button.
d.) The new speed target value that has been set or just stored in the
left display (for example 130) from operating mode Aor Bis then
shown with the unit 1/min and flashing SV .
e.) by pressing the left or right turn button, you can place the agitator
in operation. the speed and time values are then shown in large format
on the display. In addition, the text PV is shown on the display
instead of SV .
The actual value of the time setting must be understood from this
point onward as the time remaining for the agitation process. If the
time remaining has reached zero, the agitator stops its motion.
Switching the operation mode:
The following steps are required to switch the operating mode:
a.) Turn off the device with the power switch.
b.) Hold down both turn buttons and turn on the device with the
power switch. After about 1 second, you can let go of the turn
buttons.
c.) It is not possible to switch between operating modes A, B
and Cin any order. Instead, you can only switch by repeating
the steps above A- step a.) + b.) >B- step a.) + b.) >C- step
a.) + b.) >A- step a.) + b.) >
Setting the audio time expiration signal
The following steps are required to activate the audio time expiration
signal:
a.) Turn off the device with the power switch.
b.) Hold down the right turn button
and turn on the device with the
power switch. Let go of the turn
button after about 5 seconds.
c.) You can activate (SOUND ON) or
deactivate (SOUND OFF) the
audio signal indicating that time
has expired by pressing the right
turn button.
260
KS C
4
230
SAFE
minn
i
358
:
SV
OK
4
I30
I
min
/
SV
minn
i
358
:
SV 4
I30
I30
I
min
/
PV PV
minn
i
356
.
358
:
4
SV
SV
SV

26
ATTENTION! After a power failure, the unlocked
(freely movable) agitation table will continue to perform
a circular motion until the lock function can fasten the
agitation table in place.
Basic model
The amount of time required for the agitation process can be set with
the aid of the right turn button. A distinction is made for the agitation
time setting between timed mode and continuous operation. If conti-
nuous mode is selected (On LED is lit), the agitator can continue its agi-
tation function for any amount of time with the previously set speed.
If timed mode is selected, the agitation process can last for a maximum
of 50 min. The set time is displayed by the LED line. The flashing LED
shows the amount of time currently remaining After all LED’s have
gone out in timed mode, the device switches off into the Off operating
mode and the agitation process comes to an end.
Note: The curently set time can be modified at any time. If the time
setting is set to the right beyond 50 minutes, the LED bar
goes out
and the LED in the On operating state (continuous
mode) starts to
light up. If you continue to hold down the turn button, the device first
jumps to the Off operating mode (standstill) and then back into timed
operation. The same applies in the opposite order if the turn button
is held down beyond a certain amount of time and moved to the left.
After the power failed, the set time (timed mode or continuous
mode) is erased and the device switches into Offline operating mode
(standstill).
Note: If the time expiration signal has been activated, expiration of the
set time is indicated by a sequence of signals (3 times 5 short tons at
intervals of about 10 seconds).
Adjusting the lock function
Note: All devices with the abbreviation „NOL“ in the model name
(power rating plate) do not have a lock function.
The lock function of the agitation table can be activated or deac-
tivated with a direct connection to the setting of the audio time
expiration signal.
The following steps are required to acti-
vate or deactivate the function:
a.) Turn off the device with the
power switch.
b.) Hold down the right turn
button and turn on the devi-
ce with the power switch.
Let go of the turn button
after about 5 seconds. After
you have run through the
Sound On/Off routine, it is
possible to activate or deac-
tivate the lock function.
c.) You can activate (Lock On) or
deactivate (Lock Off) the lock-
function by pressing the right turnbutton.
The activated lock function is displayed by the = icon in the
right display. If you cannot see the = icon in the right display,
the lock function of the agitation table is turned off.
Setting the agitation time

27
tion or for several agitation processes in timed mode.
NOTE: After the power has failed, the set time is erased and the
device switches into Offline operating mode (standstill). The set speed
stays adjusted.
Control model
The target speed
and upper speed
limit (HS max.
300 rpm and
KS max. 500 rpm
)
required for the
agitation pro-
cess can be set
with the aid of
the left turn
button and are
shown on the
right display.
Continuous
mode is activa-
ted by presing the
left turn button. If a target time is set in the right display in continuous
mode or is saved from previous agitation processes, the agitation pro-
cess can be continued in continuous mode by pressing the right turn
button. The agitation process can be terminated by pressing the left
or the right turn button.
ATTENTION! After a power failure, the device will not
automatically start up in operating mode Aor Bby itself.
In operating mode C, the device automatically starts up
by itself.
Control model
The amount
of time requi-
red for the agi-
tation process
can be adjusted
with aid of the
right turn but-
ton and is
shown on the
right display.
Ist eine Sollzeit
If a target time
(max. 9 h 59 min)
is set in the right
display or has
been saved from previous agitation
processes, you can activate or terminate the agitation process with the
left turn button while setting the target speed.
You can exit timed mode and interrupt the agitation process by pres-
sing on the right turn button.
ATTENTION! After a power failure, the device will not
automatically start up in operating mode Aor Bby itself.
In operating mode C, the devive automatically starts up
by itself.
Basic model
You can adjusted the speed (HS max. 300 rpm and KS max. 500 rpm)
by turning the left turn button. When you do this, you should note
that the agitator does not begin to run until continuous mode or time
mode is active. For the user this means that it is possible to set a speed
in the Off operating mode that will be required for continuous opera-
345345
I
min
/
PV PV
minn
i
959
.959
:
345345
I
min
/
PV PV
minn
i
959
:
345
I
min
/
PV PV
minn
i
959
:
Time mode in mode of operation A
Continuous mode in mode of operation A
Display after power failure
in mode of operation A
Setting the speed
345345
I
min
/
PV PV
minn
i
959
.959
:
345345
I
min
/
PV PV
minn
i
959
:
345
I
min
/
PV PV
minn
i
959
:
Time mode in mode of operation A
Continuous mode in mode of operation A
Display after power failure
in mode of operation A

28
Attachments recommended by
IKA
®
must be connected to the agita-
tion table to ensure safe and secure operation. in addition , the usable
weight and speed ranges shown in the diagrams (hatched areas) must
not be exceeded.
AS 260.1 Universal attachment
Universal, steplessly adjustable clamping cylinders make it posible to
adjust to any container shape.
The universal attachment consists of:
AS 1.60 basic suspension 1x Dimension WxHxD
AS 1.5 fastening screw 8x in mm
AS 1.61 clamping cylinder 4x 425 x 135 x 334
ATTENTION: The base suspension of the universal attachment is
secured in place by four lateral clamping screwson the agitation table.
AS 260.2 Holding bracket adapter
With additional holding brackets (AS2.1, AS2.2, AS2.3, AS2.4 and
AS2.5) the holding bracket adapter is suitable foe working with round
flasks, measuring flasks and Erlenmeyer flasks.
Recommended / maximum fitting
AS 2.1 Holding bracket 12 / 12 Dimension WxHxD
AS 2.2 Holding bracket 8 / 9 in mm
AS 2.3 Holding bracket 5 / 8 330 x 24 x 334
AS 2.4 Holding bracket 4 / 4
AS 2.5 Holding bracket 2 / 4
ATTENTION! The holding bracket adapter is secured in place by four
lateral clamping screws on the agitation table.
AS 260.3 Dish attachment
For gentle agitation at low speed, for example for Petri dishes or
culture flasks. The dish attachments is equipped with an anti-slip
sheet that prevents the dish from moving around during the agitation
process.0
Dimension WxHxD
in mm
410 x 33 x 370
ATTENTION! The dish attachment is secured in place by four lateral
clamping screws on the agitation table.
AS 260.5 Separating funnel attachment
For intensive agitation of sparating funnels.
Max. fitting: Dimension WxHxD
6 x 50 ml Separating funnel in mm
5 x 100 ml Separating funnel 228 x 95 x 234
3 x 250 ml Separating funnel
3 x 500 ml Separating funnel
ATTENTION! The separating funnel attachment is secured in place
by four lateral clamping screws on the agitation table.
In order to ensure safe and secure operation, the agitator must only be
operated within the range of usable weight and speed (see diagram -
hatched area). Please make certain that the holding surface on which
the agitator is placed is clean and level. Otherwise the working range
shown in the diagram (the hatched area) cannot be used.
If the agitator is screwed together with an adjacent piece of equipment
(i.e. if it is integrated into a system) it should be noted during opera-
tion that dynamic forces may arise as a result of unfavorable loading
circumstances and the position of the center of gravity. This may cause
the adjacent equipment to vibrate or may cause the table to vibrate
uncontrollably. If you notice that the device is running unevenly, the
speed must in any case be reduced until the running irregularities no
longer occur.
Make certain that individual agitation vessels are placed in the middle
of the agitation table and multiple agitation vessels are place evenly on
the agitation table, and that all vessels are securely fastened in place.
Attachments
Supported weight (load)

29
AS 260.1 Universal attachment
AS 260.5 Separating funnel attachment
Basic error codes:
ATTENTION! If an error code is encountered, an audio warning
signal is generated and the red Off signal light goes on in the display
field. First, please try to continue operation by turning the device off
and back on again.If it is still not possible to eliminate an error after
an extended wait, please contact our service department. If you do so,
you should always tell us what error code has been encountered. This
simplifies the process of tracking down the error and makes it possible
to form a preliminary opinion.
Error code
Error Cause of the error
Off - LED (red) The potentiometer for -
Too rapid a change in the
1x flash / the speed is not assig- speed target value
2 sec pause ning any target value -Internal device error
Off - LED (red) Permissible motor tem- -Permissible supported
2x flash / peratur exceeded weight exceeded
2 sec pause -Permissible ambient
temperature exceeded
Motor locked -Agitation table is being
hindered in this stroke mo-
tion by an outside effect
Read fork signal not -Internal device error
available
Off - LED (red) Maximum adjustable -Resonance behavior of
3x flash / speed of the device the experiment setup
2 sec pause exceeded
Off - LED (red) Motor standstill for de- -When turning on the
4x flash / vice switch-on proce- device, you must ensure
2 sec pause dure (safety confirma- that the motor is not
tion not ensured performing any rational
motion
Off - LED (red) Safety relay cannot -Internal device error
5x flash / be activated
2 sec pause
Off - LED (red) The switch for the TIME -Internal device error
6x flash / function is not assigning
2 sec pause any target value
Off - LED (red) Problem with the power -The device is beeing
7x flash / supply operating with under vol-
2 sec pause tage or overvoltage (for
permissible voltage range,
see technical data)
Off - LED (red) Triac cannot be activated -Internal device error
8x flash /
2 sec pause
HS 260
KS 260
1/min
g
0 100 150 200 250 300 350 400 450 50050
0
8000
7000
6000
5000
4000
3000
2000
1000
Error codes
g
1/min
HS 260 KS 260
0 100 150 200 250 300 350 400 450 50050
0
8000
7000
6000
5000
4000
3000
2000
1000

30
Control error codes:
ATTENTION! If an error code is encountered, an audio warning
signal is generated and the red Off signal light goes on in the display
field. First, please try to continue operating by turning the device off
and back on again. If it is still not possible to eliminate an errorafter
an extended wait, please contact our service department. If you do so,
you should always tell us what error code has been encountered. This
simlifies the process of tracking down the error and makes it possible
to form a preliminary opinion.
Error code
Error Cause of the error
Er 2 No communication bet- -Interface not connected
ween PC and control de- -PC is not sending any
vice in remote operation data within the amount
with active watchdog func-
of time set by the watch-
tion in Mode 1 dog
Er 3 Internal device tempe- -Permissible ambient
rature too high temperature exceeded
Er 4 Motor locked or over- -Agitator table is being
loaded, Problem with
hindered in its stroke motion
read fork signal
-Internal device error
Er 9
Error while reading
-BLP Logik
stored values.
Er 41 Triac defective -Internal device error
Er 42 Safety relay defective -Internal device error
WD No communication bet- -Interface not connected
ween PC and contol de- -PC is not sending any
vice in remote operation data within the amount
with active watchdog func-
of time set by the watch-
tion in Mode 1 dog
(HS/KS 260 control version only)
The HS/KS 260 control is equipped with a 15-pin SUB-D connector on the rear
side of the device. The pins are assigned in operatin with analog and serial signals.
Analog autput
Voltage values for the speed measurement quantify
are present on the analog pins.
(10) Analog GND
(15)
Speed measurement value
100mVDC / 100 1/min
RS 232 C serial interface
The serial assignment of the socket can be used to control
the device externally by means of a PC and a suitable
applikation program.
Configuration of the serial RS 232 C interface
• The function of the interface line between the laboratory
device and the automation system is a selection of the
signals specified in EIA Standard RS 232 C, corresponding to
DIN 66020 Part 1. For the assignment of the signals, please
refer to the illustration.
• Standard RS 232 C applies to the elctronic proerties of the
interfaces and the assignment of signal states in accordance
with DIN 66259 Part1.
• Transmission procedure: Asynchronous character
transmission in start-stop
mode
• Type of transmission: full duplex
• Character format:: Character creation according to the data format
in DIN 66022 for start-stop mode. 1start bit;
7character bits; 1parity bit (even); 1stopbit.
• Transmission speed: 9600 baud
• Data flow conrol: RTS/CTS hardware handshake
Interface and outputs
5
10
15
1
6
11
Analog GND
100mV = 100 1/min
5
10
15
1
6
11
Analog GND
RS232_GND
TxD
RxD
RTS
CTS
100mV = 100 1/min

31
• RTS: (Pin 7) LOW (positive tension)
/ PC may send
• RTS: (Pin 7) HIGH (negative tension)
/ PC may not send
• CTS: (Pin 8) LOW (positive tension)
/ PC recipient
• CTS: (PIN 8) HIGH (negative tension)
/ PC not recipient
• Access method: Data communication from laboratory instrument to
processor is only possible on demand of the processor.
Instruction Syntax
Here applies the following:
• The instructions are generally sent from the processor (master) to the laboratory
instrument (slave).
• The laboratory instrument exclusively sends on demand of the processor. Even
error codes cannot be spontaneously communicated from the laboratory instru-
ment to the processor (automatic system).
• Instructions and parameters as well as subsequent parameters are separated by
at least one blank. (Code: hex 0x20)
• Each individual instruction including parameters and data as well as each reply
are terminated with CR LF (Code: hex 0x0D and 0x0A) and have a maximum lenght
of 80 characters.
• The decimal separator in a floating point number is the point (Code: hex 0x2E).
The above statements largely correspond with the recommendations of the
NAMUR-Association. (NAMUR-recommendations for the desing of electric plug
connections for the analog and digital signaltransmission to laboratory- MSR
individual units. Rev. 1.1)
Overview of the NAMUR-Instructions
(KS 130 control version only)
Abbreviations:
X,y = numbering parameter (integer number)
M = value of variable, integer number
n = value of variable, floating point number
X = 4 speed
X = 6 speed range limit (“safety“ speed)
NAMUR Instructions Function Display
additional
IN_PV_X X=4 Reading the real-value
OUT_SP_Xn X=4
Setting the actual value to n
up to a maximum of the set
upper speed limit
IN_SP_X X=4; 6 Reading the set rated value
START_X X=4 Starting the instrument’s
Remote
(remote) function
STOP_X X=4 Switching off the instrument
Remote
function. Variables set with
OUT_SP_X are maintained. Con-
tains the instruction MP_STOP
RESET Switching off the instrument
function
STATUS Display of status
1*: A mode of operation
2*: B mode of operation
3*: C mode of operation
*0: manual operation without
fault
*1: automatic operation Start
(without fault)
*2: automatic operation Stop
(without fault)
<0: error code: (-1)
-2: Er2 / WD
-3: Er3
-4: Er4
-9: Er9
-41: Er41
-42: Er42
-83: wrong parity
-84: unknown instruction
-85: wrong instruction
sequence
-86: invalid rated value

32
-87: not sufficient storage
space
RMP_IN_X X=4 Reading the real segment
number of ramp. With ramp
not started: 0
RMP_IN_X_y X=4 Reading the accumulated value
and the ramp segment duration
(hh;mm:ss) of ramp segment y.
RMP_OUT_y n
hh:mm:ss
X=4 Setting the accumulated value (n)
and the ramp segment duration
(hh:mm:ss) for ramp segment y
RMP_START_X X=4
Starting the ramp function, begin-
ning
with ramp segment No. 1.
(Only possible after prior
START_X.) After RMP_STOP_X
START_X is not necessary.
RMP_STOP_X X=4
Switching off ramp function.
Rated value=0 (Ramp is main-
tained, that means , ramp can be
restarted with
RMP_START_X.
RMP_PAUSE_X X=4 Stopping the ramp function.
Freezing of real rated value and
real ramp segment time
RMP_CONT_X X=4 Continuation of ramp function
(After prior RMP_PAUSE_X).
RMP_RESET_X Switching off ramp functions
and deleting of all set ramp
segments
RMP_LOOP_SET_X X=4 To work off the ramps in one
loop
RMP_LOOP_RESET_X X=4 Ending of ramp loop
IN_TYPE Requiring identification of
laboratory instrument
IN_NAME Requiring the designation name
OUT_NAME
name
Output of
designation name
(max.6 characters, default:
IKA
®
_S-)
OUT_WD1@m Watchdog mode 1: If the WD1
result occurs, the agitation pro-
cess is turned off and Er2 is dis-
played. The watchdog time is set
to m (10...1800) sec with echo of
the
watchdog time.
This command starts the watch-
dog function and must always be
sent within the time set by the
watchdog.
OUT_WD2@m Watchdog mode 2: If the WD2
result occurs, the target speed
is set to the WD target safety
speed that has already been set.
The warning WD is displayed.
The WD2 result can be reset
with OUT_WD2@0.
The watchdog time is set to m
(10...18000) sec with echo of
the watchdog time. This com-
mand starts the watchdog func-
tion and must always be sent
within the time set by the
watchdog.
OUT_SP_42@n Sets the WD target speed with WD
echo of the value set.
(HS/KS 260 control version only)
PC 5.1 Adapter
IKA
®
- Control
The Adaptor PC 5.1 splits the analog and serial signals. The analog
output signals are alotted to a 7-polar coupling according to the
Namur-recommendation; the serial signals to a 9-polar Sub-D-bushing
plug (RS 232 C).
Communication between laboratory
instrument and PC

33
The HS/KS260basic and HS/KS260control are maintenace-free. It is
subject only to the natural wear and tear of components and their
statistical failure rate.
When ordering spare parts, please give the manufacturing
number shown on the type plate, the machine type and the
name of the spare part.
Use only cleansing agents which have been appro-
ved by IKA®to clean IKA®devices. To remove use:
Dyes isopropyl alcohol
Construction materials water containing tenside / iso
propyl alcohol
Cosmetics water containing tenside / iso
propyl alcohol
Foodstuffs water containing tenside
Fuels water containing tenside
For materials which are not listed, please request information from
IKA®. Wear the proper protective gloves during cleaning of the
devices.
Electrical devices may not be placed in the cleansing agent for the
purpose of cleaning.
Before using another than the recommended method for cleaning or
decontamination, the user must ascertain with the manufacturer that
this method does not destroy the instrument.
Repairs:
Please only send devices in for repair that have been cleaned
and are free of materials which might present health hazards.
For this, use the “certificate of compliance” form which you can
obtain from IKA®or can download a version for printing from the
IKA®website at www.ika.com.
If your appliance requires repair, return it in its original packaging.
Storage packaging is not sufficient when sending the device - also use
appropriate transport packaging.
PC 1.5 Cable
This cable is required to connect the 7-pin connector to a PC (25-pin
connector).
PC 2.1 Cable
This cable is required to connect the 9-pin connector to a PC.
PC 1.2 Adaptor
This adaptor is required to connect the 9-pin connector to an 8-way
serial interface (25-pin plug).
AK 2.1 Cable
This cable is required to connect the 7-pin connector to a chart recor-
der (4mm pin plug).
AK 2.2 Cable
This cable is required to connect the 15-pin connector to a chart
recorder (4mm pin plug).
If the motor is locked or if a load is placed on it resulting in a higher
temperature than is permitted, the device is turned off automatically
by the safety circuit and the control light flashes. To eliminate the
error, the weight of the material must be reduced. Allow the device
to cool off.
The device must be turned off and backon again.
The motor is turned off immediately in the event of a malfunction by
a safety circuit. Amalfunction occurs if the safe and secure functiona-
lity of the device cannot be guaranteed. A malfunction is displayed
for the Basic model by the red Off signal light coming on and flas-
hing, and for the Control model by the error message being shown
on the display of the speed indicator (see the section
“
Error Codes“.
Motor protection / safety device
Maintenance and cleaning

34
AS 260.1 Universal attachment
AS 260.2 Holding bracket adapter
AS 260.3 Dish attachment
AS 260.5 Separating funnel attachment
STICKMAX
Adhesive mat
(HS/KS 260 control version only)
PC 5.1 Adapter
IKA
®
- Control
PC 1.5 Cable
PC 2.1 Cable AK 2.1 Cable
PC 1.2 Adapter AK 2.2 Cable
Design voltage: VAC 230±10%
or VAC 115±10%
Design frequency: Hz 50/60
Input power: W45
Speed range: HS rpm 0 - 300
Speed range: KS rpm 0 - 500
Perm. duration of operation: %100
Perm. ambient temperature: °C +5 to +50
Perm. relative humidity: %80
Protection class acc. to DIN 40 050: IP 21
Protection class: I
Overvoltage category: II
Contamination level: 2
Operation at a terrestrial
altitude: m
max. 2000 above sea level
Drive: Speedcontrol asyn-
chronous motor
Protection at overloaded: Temperature sensor
in motor winding
Fuses on apparatus plug: A
2x T1A 250V
Shaking motion: mm KS - Ø10 orbital
mm HS - 20 to and fro
Max. load: kg 7,5
Dimensions: (B x H x T) mm 360 x 97 x 420
Weight: kg 8,1 (basic)
kg 8,8 (control)
HS/KS 260 basic
Speed setting: Analog (infinitely variable)
Rotary knob on front side left
Speed display: 10 LED’s with scale-in
30 rpm steps (HS) und 50
rpm steps (KS)
Max. speed deviation from idle: %±10
Time setting: three indexing positions /
Rotary knob on the front side right:
key button 10 steps from
5 - 50 min in 5 min steps
Time display: 10 LED’s with scale in
5 min steps
Max. time deviation from idle: %±1
HS/KS 260 control
Speed setting: Digital
Rotary knob on the front side left
(1 step = 10 rpm)
Speed display: LCD - Display
Max. speed deviation from idle: %±1
Time setting: Digital
Rotary knob on the front side right (1 step = 1 min)
Time display: LCD - Display
max. 9h 59min
Max. time deviation from idle: %±1
Interface: RS 232 C / analog
Subject to technical changes!
Accessories
Technical data
Other manuals for HS 260 Basic
2
This manual suits for next models
5
Table of contents
Other IKA Paint Sprayer manuals
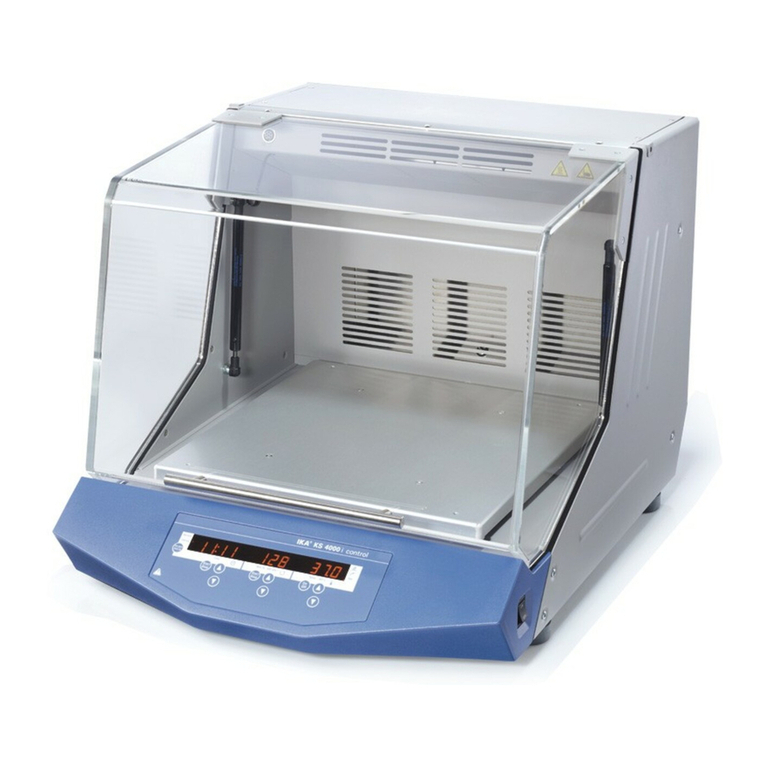
IKA
IKA KS 4000 i control User manual
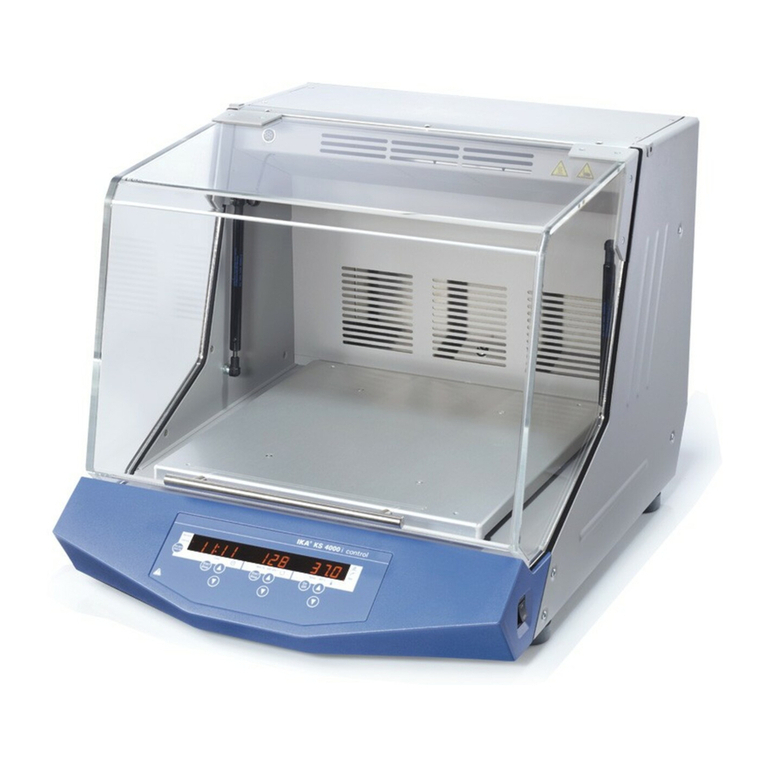
IKA
IKA KS 4000 i control User manual
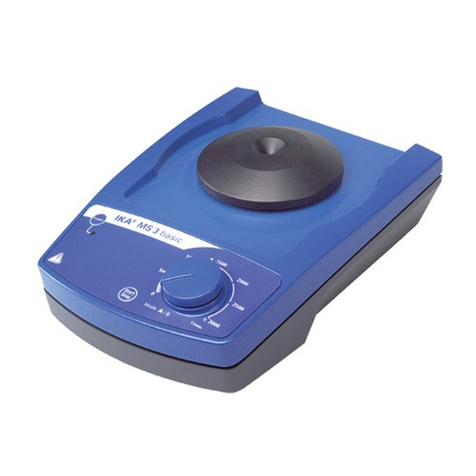
IKA
IKA MS 3 basic User manual
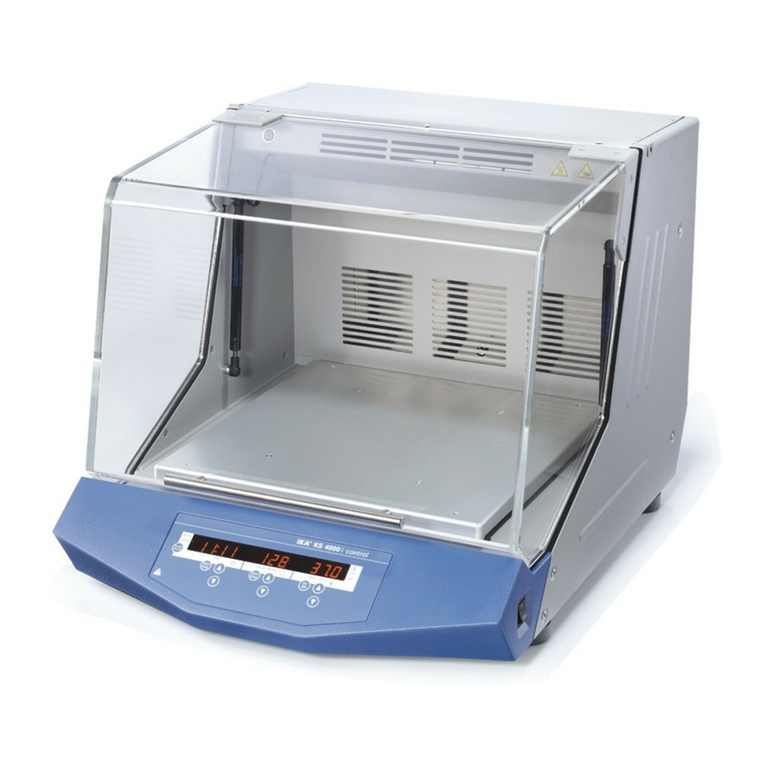
IKA
IKA KS 4000 i control User manual
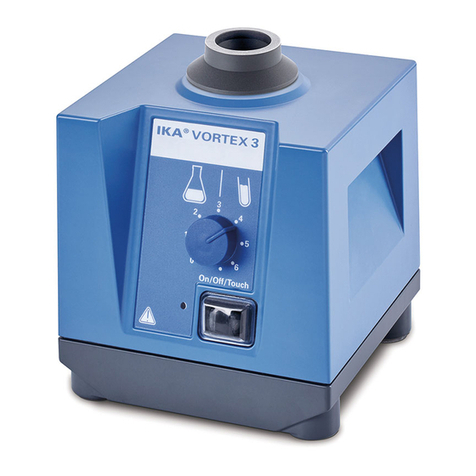
IKA
IKA Vortex 3 User manual
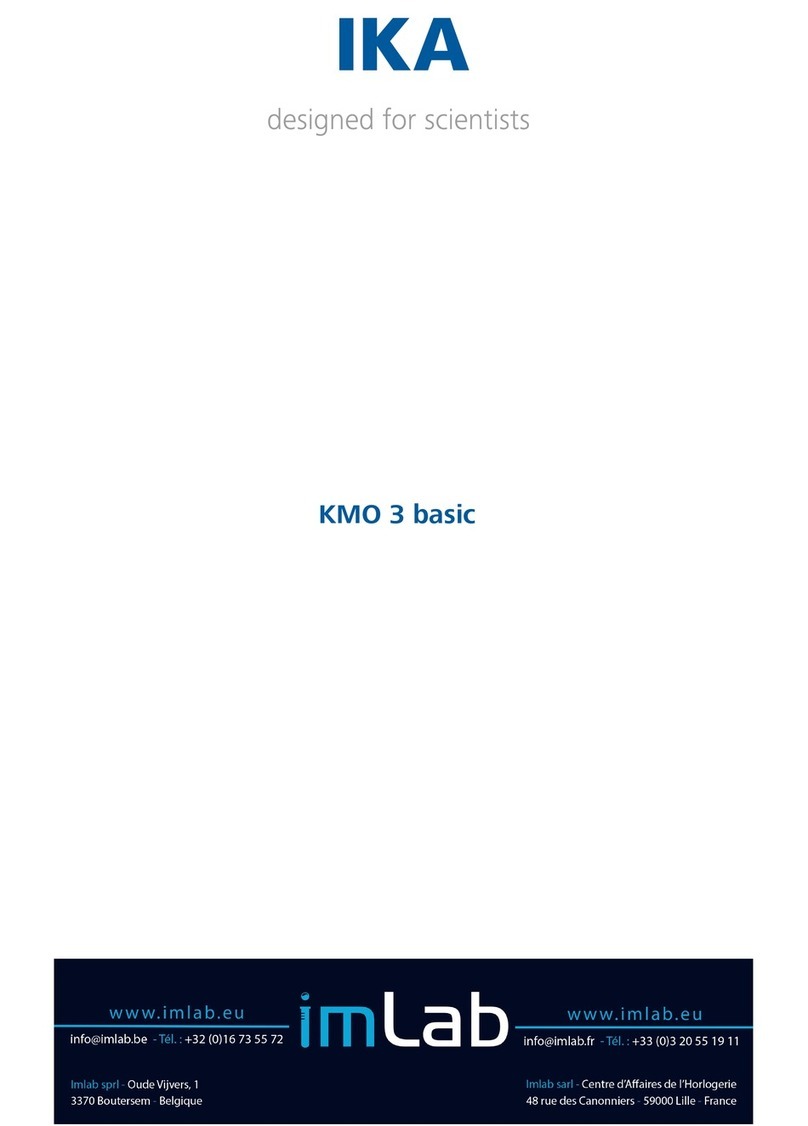
IKA
IKA KMO 3 basic User manual
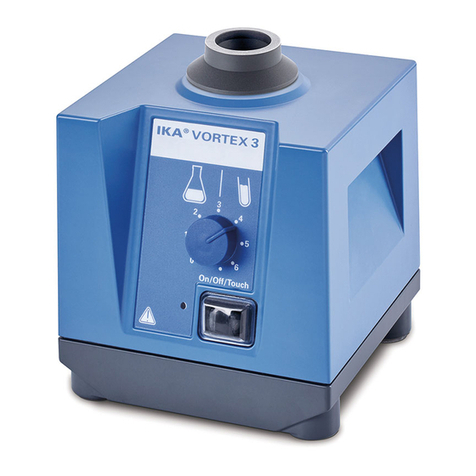
IKA
IKA Vortex 3 User manual
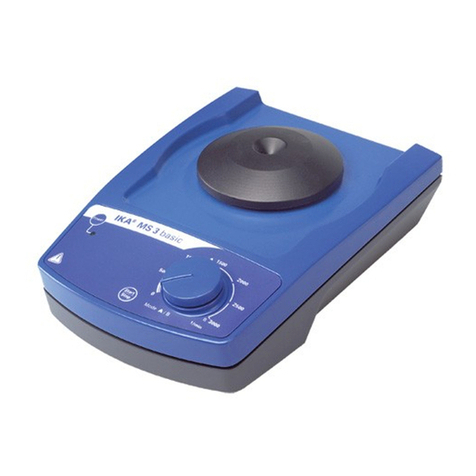
IKA
IKA MS 3 basic User manual
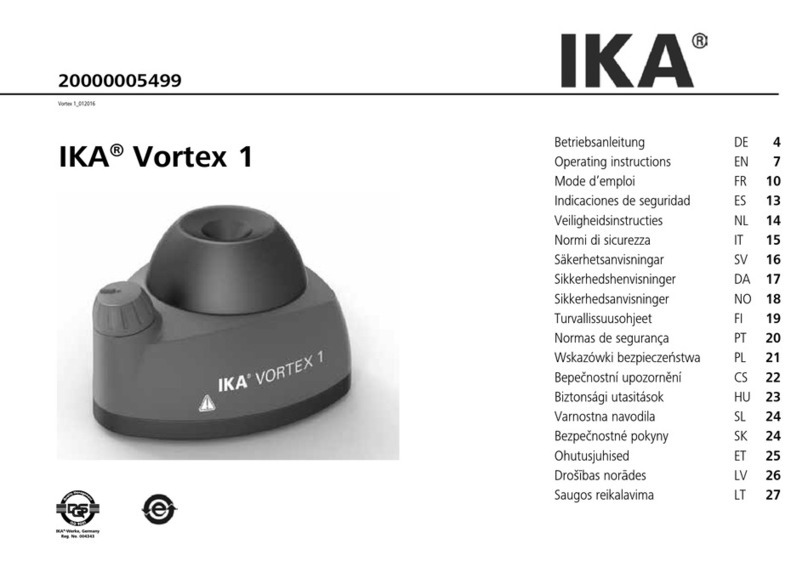
IKA
IKA Vortex 1 User manual
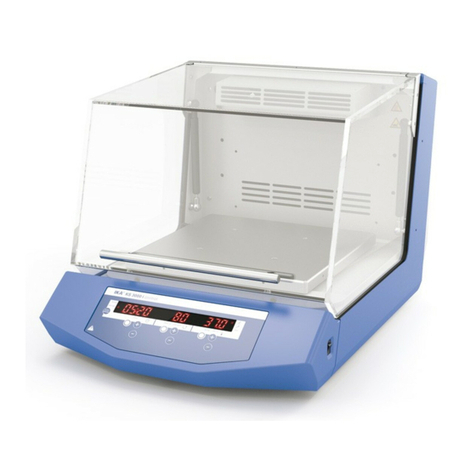
IKA
IKA KS 3000 i control User manual