Krom Schroder VGBF 15R User manual

2.1.1.8 Edition 04.11
DK S N P GR
➔ www.docuthek.com
D GB F NL I E
TR CZ PL RUS H
© 2008 – 2011 Elster GmbH
Please read and keep in a safe place
Please read through these instructions
carefully before installing or operating. Following the
installation, pass the instructions on to the opera-
tor. This unit must be installed and commissioned in
accordance with the regulations in force. These in-
structions can also be found at www.docuthek.com.
Explanation of symbols
• , 1 , 2 , ... = Action
= Instruction
Liability
We will not be held liable for damages resulting
from non-observance of the instructions and non-
compliant use.
Safety instructions
Information that is relevant for safety is indicated in
the instructions as follows:
DANGER
Indicates potentially fatal situations.
WARNING
Indicates possible danger to life and limb.
CAUTION
Indicates possible material damage.
All interventions may only be carried out by qualified
gas technicians. Electrical interventions may only be
carried out by qualified electricians.
Conversion, spare parts
All technical changes are prohibited. Only use OEM
spare parts.
Transport
On receipt of the product, check that the delivery is
complete (see Part designations). Report any trans-
port damage immediately.
Storage
Store the product in a dry place. Ambient tempera-
ture: see Technical data.
Operating instructions
Translation from the German
D
GB
F
NL
I
E
GB-1
Safety
Contents
Gas pressure regulators VGBF
Gas pressure regulators VGBF . . . . . . . . . . . . 1
Contents ..............................1
Safety.................................1
Checking the usage. . . . . . . . . . . . . . . . . . . . . 2
Intended use ...........................2
Type code..............................2
Part designations........................2
Installation ............................2
Installing the impulse line . . . . . . . . . . . . . . . .
Tightness test .........................
Changing the outlet pressure pa ..........4
Maintenance...........................4
Replacing the spring . . . . . . . . . . . . . . . . . . . . 4
Technical data..........................5
Declaration of conformity . . . . . . . . . . . . . . . . 6
Spring table............................6
Contact ...............................6

GB-2
D
GB
F
NL
I
E
Checking the usage
Intended use
The gas pressure regulator VGBF serves to maintain
a constant outlet pressure pa despite changing gas
flow rates and inlet pressures pe in gas pipelines.
This function is only guaranteed when used within
the specified fields of application – see [Technical
data – p.5].
Any other use is considered as non-compliant.
Type code
Code Description
VGBF Gas pressure regulator
15 – 150 Nominal size
R
F
Rp internal thread
Flange to ISO 7005
05
10
40
pe max. 500 mbar
pe max. 1 bar
pe max. 4 bar
-1
-
Screw plug at the inlet
Screw plug at the inlet and outlet
L
V
For air only (without approval)
Medium: aggressive gases (check
suitability), rubber parts coming into
contact with gas made of Viton
(without approval)
Part designations
VGBF..FVGBF..R
10
11
2
3
3
44
5
6
6
77
8
8
99
2
1Cover cap and adjusting screw
2Breather screw
Impulse line connection (not on VGBF..05)
4Outlet
5Outlet (pa) measuring connection
6Arrow of direction of flow
7Inlet (pe) measuring connection
8Inlet
9Type label
10
Damping valve for VGBF 40 – 100..40
Inlet pressure pe, outlet pressure pa and ambient
temperature: see type label.
Vor dem Öffnen Feder
entspannen!
Release spring
before opening!
Avant d'ouvrir le dôme,
détendre le ressort!
VGBF
CE: 0063AQ0973
Installation
CAUTION
Please observe the following to ensure that the
gas pressure regulator is not damaged during the
installation:
Install the unit free of mechanical stress.
Sealing material, cuttings and other impurities must
not be allowed to get into the regulator housing.
The installation location must be dry. Do not install
the unit in the open air.
Installation in the vertical or horizontal position,
never upside down.
The outlet pressure pa is set at the factory with
the spring dome pointing vertically upwards. If
the VGBF is installed with the spring dome in the
horizontal position, check and adjust the outlet
pressure pa (see [Changing the outlet pressure
pa – p.4]).
1 Install a filter upstream of the unit, in order to
protect it against impurities in the pipeline.
VGBF..F
>20
mm
42 3
5
VGBF..R
>20
mm
42 3
65

GB-3
D
GB
F
NL
I
E
Installing the impulse line
VGBF 40 – 150..05 for 500 mbar
No external impulse line required. VGBF..05 fea-
tures an internal feedback function.
VGBF 40 – 100..40 for 4 bar
In order to avoid possible oscillations, a damp-
ing valve should be fitted. The damping valve is
secured to the spring dome with an adhesive
strip on delivery.
Impulse line: 12.5 × 1.5 mm.
VGBF 40 – 100
31 2
54 Push union
nut and
compression
fitting onto
the impulse
line.
VGBF 15 – 100..10 for 1 bar and
VGBF 15 – 100..40 for 4 bar
6 Install the impulse line and seal with an approved
sealing material.
VGBF 15 – 25R
Rp 1/4
5xDN
VGBF 40 – 150
5xDN
Rp 3/8
Tightness test
Also after maintenance.
1 Block the pipeline at the inlet and outlet.
2 Slowly apply inlet pressure pe.
(pe ≤ 1.5 × pe max., see type label)
Slowly apply outlet pressure pa.
(pa ≤ 1.5 × pa, see type table)
CAUTION
First apply the inlet pressure p
e
– then the outlet
pressure pa.
The inlet pressure pe must always be equal to or
higher than the outlet pressure pa.
In the event of non-compliance with the sequence,
the compensation diaphragm will reverse.
1. 2.
pepa
2. 1.
pepa
54
76
98
1110
12 Relieve the outlet pressure pa.
1 Relieve the inlet pressure pe.

GB-4
D
GB
F
NL
I
E
Changing the outlet pressure pa
The outlet pressure pa is set at the factory with
the spring dome pointing vertically upwards. If
the VGBF is installed with the spring dome in the
horizontal position, check and adjust the outlet
pressure pa.
Use the test points on the unit only for measure-
ments of zero flow or very slight flow.
− +
0
pa
6 mm
21
43
5 Clearly mark the adjusted value of the outlet pres-
sure pa on the type label.
Maintenance
In order to ensure smooth operation: check the func-
tion annually, or every six months if operated with
biologically produced methane.
1 Request different outputs on the burner in order
to change the flow rate.
2 Close the manual valve at the inlet a little in order
to change the inlet pressure pe.
Despite changing flow rates and inlet pressures p
e
(within the capacity range of the VGBF), the outlet
pressure pa must remain constant (±10–15%).
Reduce the capacity to low-fire rate and close
the valve downstream of the VGBF.
Approx. 30 seconds after the valve has been
closed, the outlet pressure p
a
should not increase
significantly.
Check the tightness of the VGBF during operation
to detect possible leaks due to hardened rubber
materials.
54
6 If a leak is found, replace the rubber materials –
see spare parts DVD, “PartDetective”.
7 Then check for tightness once again.
Replacing the spring
1 Choose a spring according to the outlet pressure
range (see [Spring table – p.6]).
2 Remove the cover cap.
WARNING
The taut spring can pop out when opening the
spring dome and lead to injury. Therefore, decom-
press the spring as far as it will go before open-
ing. Then turn back 5 × to relax the spring counter
bearing.
6 mm 5x
53 4
7 86
VGBF 15 – 50
9 Turn down the spring counter bearing slightly.
10 11
12 Ensure that the guide grooves and bars engage
in each other.
VGBF 65 – 150
9 Turn down the spring counter bearing slightly.
10 11
12 Ensure that the guide groove and the cylinder
engage in each other.
VGBF 15 – 150
− +
0
pa
6 mm
1413
15 Screw on cover cap.
16 After inserting the spring, take the spring’s label
from the packaging and stick it below the type
label on the pressure regulator.
17 Clearly mark the adjusted value of the outlet pres-
sure pa on the type label.

GB-5
D
GB
F
NL
I
E
Technical data
Gas type: natural gas, town gas, LPG (gaseous)
and biologically produced methane, VGBF..L for air.
Outlet pressure ranges:
The outlet pressure range is reached through
the use of different springs (see [Spring table –
p.6]). The regulators are pre-set at the factory to
20mbar (red spring).
Rp 1/4 connection for test points or even for a
pilot gas line:
at the inlet: VGBF 15 and 25,
at inlet and outlet: VGBF 40 – 150.
Ambient temperature: -15 to +60°C,
VGBF..V: 0 – 60°C.
Strainers that are possibly fitted serve as flow
conditioners.
Housing: aluminium,
diaphragms: Perbunan or Viton,
valve seat: aluminium,
valve stem: aluminium,
valve disc: vulcanized Perbunan or Viton seal.
Internal thread: Rp to ISO 7-1,
flanged connection: PN 16 to ISO 7005,
see T12.2.3 brochure for special version,
DN 15 – 50 with NPT thread,
DN 50 – 100 available with ANSI flange.
Impulse line connections: NPT.
Weight [kg]:
Type Weight Type Weight
VGBF 15R 0.9 VGBF 65F 12.0
VGBF 25R 1.9 VGBF 80F 16.1
VGBF 40R 2.9 VGBF 100F 26.0
VGBF 40F 4.8 VGBF 150F 46.5
VGBF 50F 7.7
VGBF..10
Max. inlet pressure pe max.: 1 bar.
Feedback via impulse line:
Rp 1/4 connection for DN 15 and 25,
Rp 3/8 connection for DN 40 – 150.
EN 334, Accuracy Class AC 10, Lock up pressure
class SG 30.
VGBF..40
Max. inlet pressure pe max.: 4 bar.
Feedback via impulse line:
Rp 1/4 connection for DN 15 and 25,
Rp 3/8 connection for DN 40 – 150.
EN 334, Accuracy Class AC 10, Lock up pressure
class SG 30.
VGBF..05
Max. inlet pressure pe max.: 500 mbar.
Internal feedback.
EN 88, Class A, Group 2.
Service life
The Pressure Equipment Directive (PED) and the
Energy Performance of Buildings Directive (EPBD)
demand regular checks on and maintenance of heat-
ing systems, in order to ensure a high level of use
in the long term, a clean method of operation and
safe function.
The service life on which the construction is based,
hereinafter referred to simply as the “service life”, is
compiled from the relevant standards. You can find
further explanations in the applicable rules and regu-
lations and on the afecor website (www.afecor.org).
This information on service life is based on using
the product in accordance with these operat-
ing instructions. The product must be serviced at
regular intervals. Once the specified service life has
been reached, the safety-related functions must be
checked in accordance with the section entitled
[Maintenance – p.4].
If the product passes the aforementioned function
tests, you can continue to use it until the next sched-
uled maintenance operation. At this point, these tests
must be repeated.
If the product fails one of the aforementioned tests,
it must be replaced immediately.
This procedure applies to heating systems. For ther-
moprocessing equipment, observe national regula-
tions.
Service life (based on date of manufacture) in accord-
ance with EN 13611 and EN 88 for VGBF: 15 years.
Long-term use in the upper ambient temperature
range accelerates the ageing of the elastomer ma-
terials and reduces the service life (please contact
manufacturer).

Elster GmbH
Postfach 28 09, D-49018 Osnabrück
Strotheweg 1, D-49504 Lotte (Büren)
T +49 541 1214-0
F +49 541 1214-370
GB-6
D
GB
F
NL
I
E
If you have any technical questions, please contact
your local branch office/agent. The addresses are
available on the Internet or from ElsterGmbH.
We reserve the right to make technical modifications
in the interests of progress. info@kromschroeder.com, www.kromschroeder.com
Contact
Spring table
Outlet pressure
pa [mbar]
Order No. Marking
VGBF 15 VGBF 25 VGBF 40 VGBF 50
5 – 12.5 75421911 75421961 75421961 75422031 –
10 – 30** 75421921 75421971 75421971 75422041 red
25 – 45 75421931 75421980 75421980 75422051 yellow
40 – 60 75421941 75421990 75421990 75422061 green
55 – 75 75421951 75422000 75422000 75422071 blue
70 – 90 75442046 75422010 75422010 75422081 black
85 – 105 75442047 75422020 75422020 75422091 white
100 – 160 75442048 75438978 75438978 75438981 black/red
150 – 230 75442049 75438979 75438979 75438982 black/yellow
220 – 350 75442050 75438980 75438980 75438983* black/green
Outlet pressure
pa [mbar]
Order No. Marking
VGBF 65 VGBF 80 VGBF 100 VGBF 150
5 – 12.5 75426160 75426230 75426310 75426450 –
10 – 30** 75426170 75426240 75426320 75426460 red
25 – 45 75426180 75426250 75426330 75426470 yellow
40 – 60 75426190 75426260 75426340 75426480 green
55 – 75 75426200 75426270 75426350 75426490 blue
70 – 90 75426210 75426280 75426360 75426500 black
85 – 105 75426220 75426290 75426370 75426510 white
100 – 160 75426329 75438984 75438987 75438990 black/red
150 – 230 – 75438985 75438988 – black/yellow
220 – 350 – 75428986 75438989 – black/green
* Spring set comprising two springs.
** Standard spring
Mark the new outlet pressure on the type label – adhesive label supplied.
Declaration of conformity
We, the manufacturer, hereby declare that the
product VGBF, marked with product ID No. CE:
0085AQ0973, complies with the requirements of
the listed Directives and Standards.
VGBF 15 to VGBF 150:
Directives:
– 90/396/EEC
– 97/23/EC
Standards:
– DIN EN 88
– DIN 3380
– DIN EN 334
The relevant product corresponds to the type tested
by the notified body 0063.
The production is subject to the surveillance pro-
cedure pursuant to DIN EN ISO 9001 according to
annex II, paragraph 3 of Directive 90/396/EEC.
Elster GmbH
Scan of the Declaration of conformity (D, GB) – see
www.docuthek.com
Approval for Russia
Certified by Gosstandart pursuant to GOST-R.
Approved by Rostekhnadzor (RTN).
This manual suits for next models
9
Table of contents
Other Krom Schroder Controllers manuals
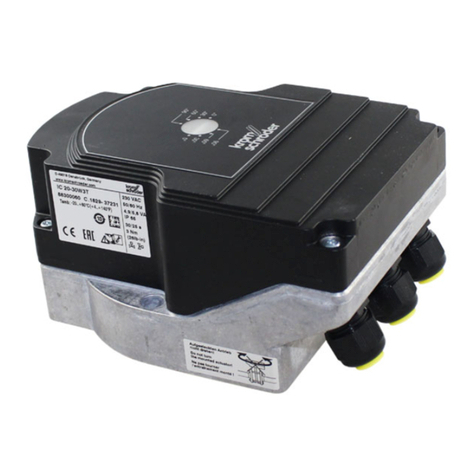
Krom Schroder
Krom Schroder IC 20 User manual
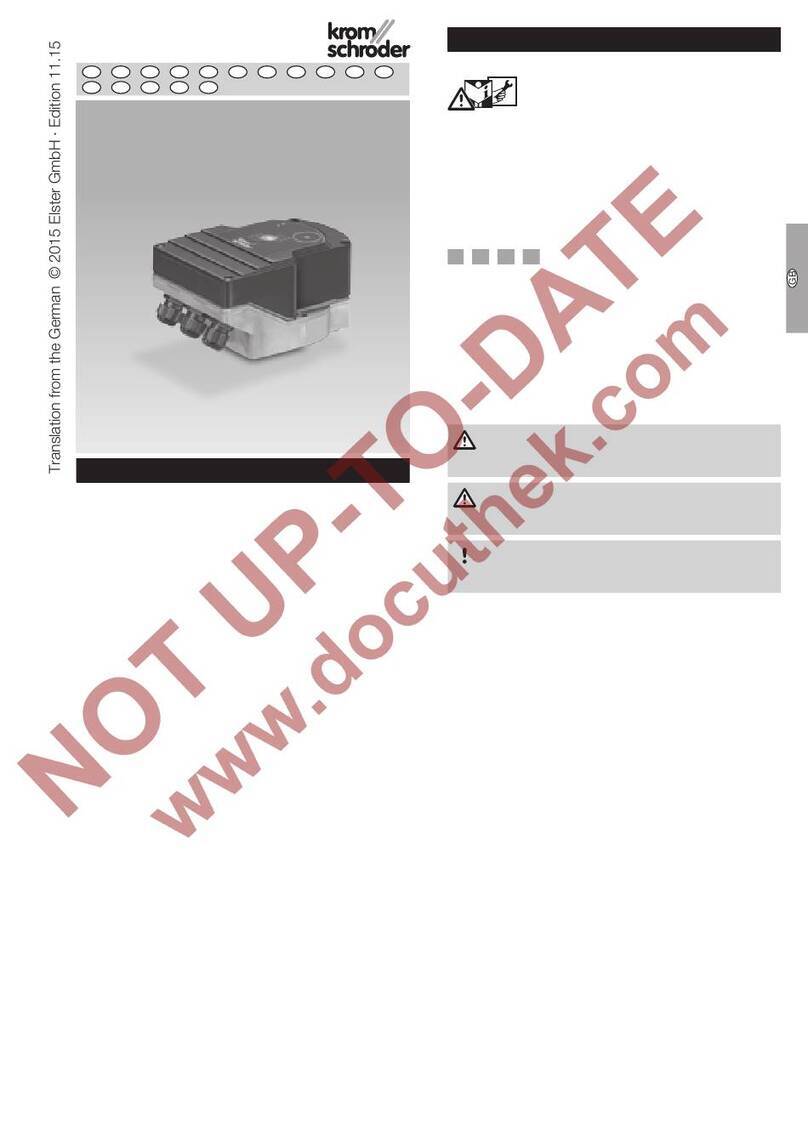
Krom Schroder
Krom Schroder IC 40 User manual

Krom Schroder
Krom Schroder IC 20 User manual
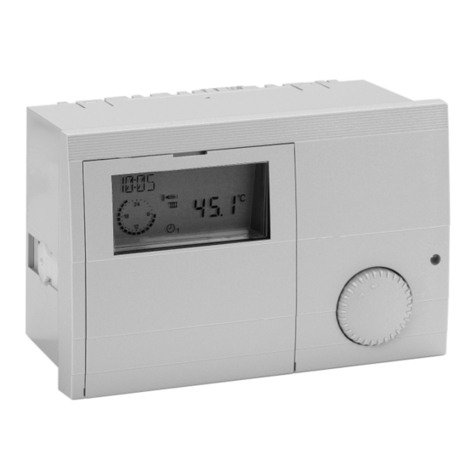
Krom Schroder
Krom Schroder E8.5064 V1 User manual
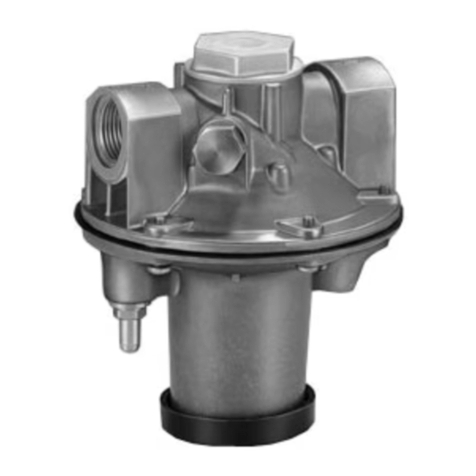
Krom Schroder
Krom Schroder GIK Series Manual
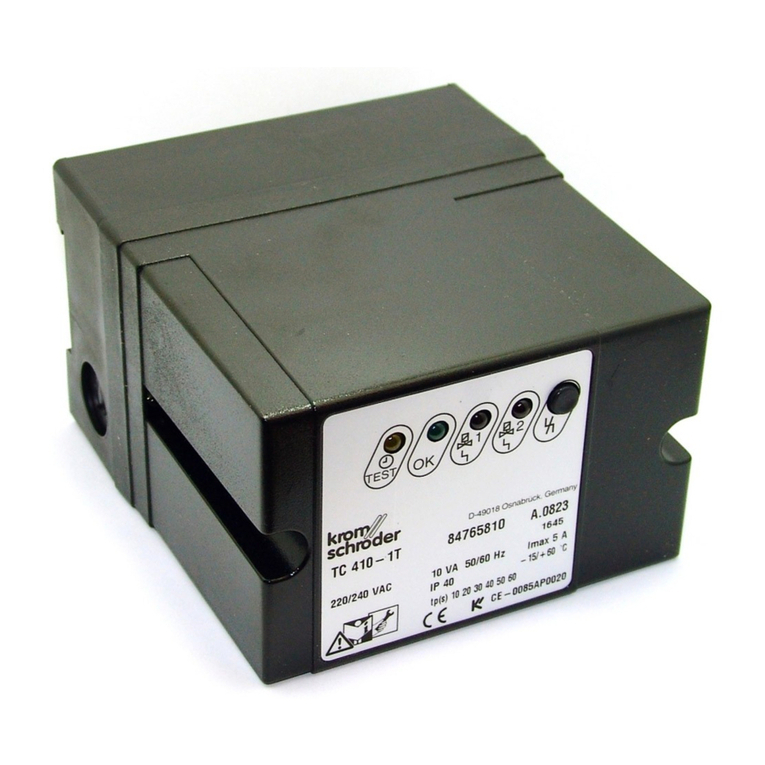
Krom Schroder
Krom Schroder TC 410 User manual
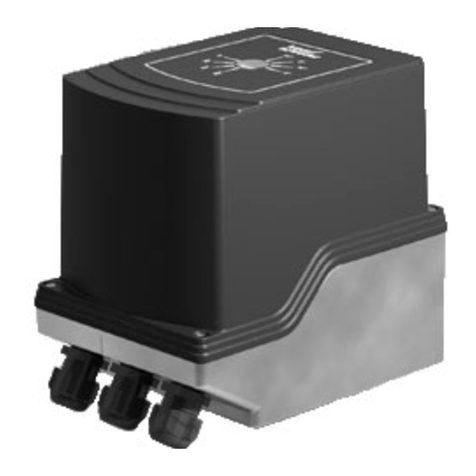
Krom Schroder
Krom Schroder IC 50 Series User manual
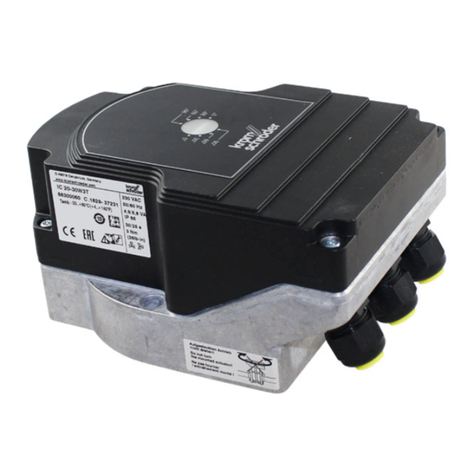
Krom Schroder
Krom Schroder IC 20 User manual
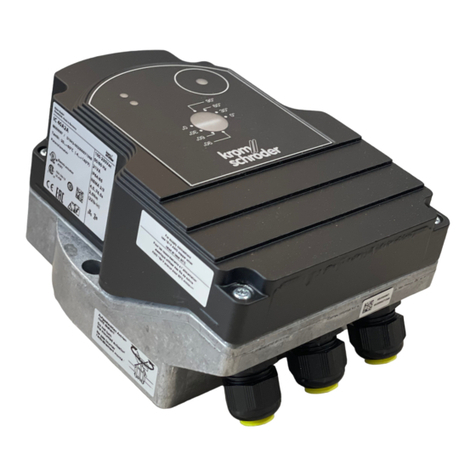
Krom Schroder
Krom Schroder IC 40 User manual

Krom Schroder
Krom Schroder IC 50 User manual