Mec Mast Series Guide

Service & Parts Manual
Part # 95568
May 2021
MME20 Serial Number Range 17200000 - Up
MME25 Serial Number Range 17300000 - Up
Mast Series
Art_5671

Page i Mast Series - Service & Parts Manual
May 2021
Revision History
Date Reason for Update
May 2021 New Release
1401 S. Madera Avenue, Kerman, CA93630 USA
Toll Free: 1 - 877 - 632 - 5438
Phone: 1 - 559 - 842 - 1500
Fax: 1 - 559 - 842 - 1520
www.MECawp.com
MEC Aerial Work Platforms

Page ii Mast Series - Service & Parts Manual
May 2021
Table of Contents
Chapter 1 - Service . . . . . . . . . . . . . 1
Service Introduction.................1
Section 1 - MEC Operator Policy .............2
MEC Operator Policy . . . . . . . . . . . . . . . . . . . 2
Section 2 - Safety Symbols & General Safety Tips . . . . . . . . 3
Safety Symbols & General Safety Tips . . . . . . . . . . . . . . 3
Section 3 - Specifications . . . . . . . . . . . . . . . 4
Specifications.....................4
Section 4 - Torque Specifications . . . . . . . . . . . . . 5
Bolt Torque Specification - American Standard . . . . . . . . . . . . 5
Bolt Torque Specification - Metric Standard . . . . . . . . . . . . . 6
Hydraulic Components Torque Table . . . . . . . . . . . . . . . 7
Section 5 - Maintenance Safety. . . . . . . . . . . . . . 8
Maintenance Safety . . . . . . . . . . . . . . . . . . . 8
Section 6 - Hydraulic, Electrical and Total System . . . . . . . . 9
Hydraulic, Electrical and Total System . . . . . . . . . . . . . . 9
Section 7 - Machine Components . . . . . . . . . . . . . 10
Machine Components . . . . . . . . . . . . . . . . . . . 10
Section 8 - Emergency Systems and Procedures. . . . . . . . . 11
Emergency Systems and Procedures . . . . . . . . . . . . . . . 11
Section 9 - Transport and Lifting Instructions. . . . . . . . . . 12
Brake Release Instructions . . . . . . . . . . . . . . . . . 12
Transport and Lifting Instructions . . . . . . . . . . . . . . . . 13
Crane Lifting Instructions . . . . . . . . . . . . . . . . . . 14
Section 10 - Maintenance . . . . . . . . . . . . . . . 15
General Machine Maintenance . . . . . . . . . . . . . . . . 15
Pre-start Inspection Report . . . . . . . . . . . . . . . . . 16
Maintenance.....................17
Pre-delivery Preparation Report . . . . . . . . . . . . . . . . 18
Daily Inspections . . . . . . . . . . . . . . . . . . . . 19
Quarterly Inspections . . . . . . . . . . . . . . . . . . . 21
Semi-annually Inspections. . . . . . . . . . . . . . . . . . 31
Yearly Inspections . . . . . . . . . . . . . . . . . . . . 33
Section 11 - Control System . . . . . . . . . . . . . . 35
Control Component Locations. . . . . . . . . . . . . . . . . 35
FaultCodes.....................36
Error Indicator Readout . . . . . . . . . . . . . . . . . . 37

Page iii Mast Series - Service & Parts Manual
May 2021
Section 12 - Schematics . . . . . . . . . . . . . . . 40
Electrical Schematic . . . . . . . . . . . . . . . . . . . 40
Hydraulic Schematic . . . . . . . . . . . . . . . . . . . 41
Section 13 - Calibrations . . . . . . . . . . . . . . . 42
Calibration Instructions . . . . . . . . . . . . . . . . . . 42
Section 14 - Parameter Adjustments . . . . . . . . . . . . 44
Parameter Adjustment. . . . . . . . . . . . . . . . . . . 44
Chapter 2 - Parts . . . . . . . . . . . . . . 48
Parts Introduction .................48
Section 15 - Chassis.................49
Cover Installation . . . . . . . . . . . . . . . . . . . . 49
Steer Linkage and Wheels Assembly . . . . . . . . . . . . . . . 51
Rear Wheel Assembly . . . . . . . . . . . . . . . . . . . 53
Pothole Protection Assembly . . . . . . . . . . . . . . . . . 55
Electrical Component Installation . . . . . . . . . . . . . . . . 57
Ground Control Box Assembly . . . . . . . . . . . . . . . . 59
Motor Controller Assembly . . . . . . . . . . . . . . . . . 61
Hydraulic Component Installation . . . . . . . . . . . . . . . . 63
Hydraulic Tank Assembly . . . . . . . . . . . . . . . . . . 65
Section 16 - Mast . . . . . . . . . . . . . . . . . 67
Mast and Chassis Installation . . . . . . . . . . . . . . . . . 67
Mast Assembly (MME20) . . . . . . . . . . . . . . . . . . 69
Mast Assembly (MME25) . . . . . . . . . . . . . . . . . . 71
Lifting Chain Assembly (MME20) . . . . . . . . . . . . . . . . 75
Lifting Chain Assembly (MME25) . . . . . . . . . . . . . . . . 77
Pulley Assembly, 5-7 Mast (MME20) . . . . . . . . . . . . . . . 79
Pulley Assembly, 2-4 Mast. . . . . . . . . . . . . . . . . . 81
Pulley Assembly, 1-3 Mast. . . . . . . . . . . . . . . . . . 83
Pulley Assembly, 4-6 Mast (MME25) . . . . . . . . . . . . . . . 85
Pulley Assembly, 3-5 Mast. . . . . . . . . . . . . . . . . . 87
Sequencing Cable Assembly (MME2). . . . . . . . . . . . . . . 89
Sequencing Cable Assembly (MME25) . . . . . . . . . . . . . . 91
Section 17 - Platform . . . . . . . . . . . . . . . . 93
Platform and Mast Installation . . . . . . . . . . . . . . . . . 93
Platform Assembly. . . . . . . . . . . . . . . . . . . . 95
Platform Control Box Assembly . . . . . . . . . . . . . . . . 97
Section 18 - Hydraulic System . . . . . . . . . . . . . . 99
Lift Cylinder Assembly . . . . . . . . . . . . . . . . . . . 99
Function Manifold Assembly . . . . . . . . . . . . . . . . 101
Hydraulic Hoses and Fittings . . . . . . . . . . . . . . . . 103
Section 19 - Electrical System . . . . . . . . . . . . . . 105
Electrical Harness . . . . . . . . . . . . . . . . . . . 105

Page 1 Mast Series - Service & Parts Manual
May 2021
Service Introduction
This Service section is designed to provide you, the customer, with the instructions needed to
properly maintain the MEC self-propelled aerial work platform. When used in conjunction with the
illustrated Parts section in this manual and the Operator’s Manual (provided separately), this manual
will assist you in making necessary adjustments and repairs, and identifying and ordering the correct
replacement parts.
All parts represented here are manufactured and supplied in accordance with MEC quality
standards. We recommend that you use genuine MEC parts to ensure proper operation and reliable
performance.
To obtain maximum benefits from your MEC Aerial Work Platforms, always follow the proper
operating and maintenance procedures. Only trained authorized personnel should be allowed to
operate or service this machine. Service personnel should read and study the Operator’s, and the
Service and Parts Manuals in order to gain a thorough understanding of the unit prior to making any
repairs.
Chapter 1 - Service

Page 2 Mast Series - Service & Parts Manual
May 2021
MEC Operator Policy
Note: The best method to protect yourself and others from injury or death is to use common sense.
If you are unsure of any operation, don’t start until you are satisfied that it is safe to proceed
and have discussed the situation with your supervisor.
Service personnel and machine operators must understand and comply with all warnings and
instructional decals on the body of the machine, at the ground controls, and platform control console.
MODIFICATIONS OF THIS MACHINE FROM THE ORIGINAL DESIGN AND
SPECIFICATIONS WITHOUT WRITTEN PERMISSION FROM MEC ARE
STRICTLY FORBIDDEN. A MODIFICATION MAY COMPROMISE THE
SAFETY OF THE MACHINE, SUBJECTING OPERATOR(S) TO SERIOUS
INJURY OR DEATH.
MEC’s policies and procedures demonstrate our commitment to Quality and our relentless ongoing
efforts towards Continuous Improvement, due to which product specifications are subject to change
without notice.
Any procedures not found within this manual must be evaluated by the individual to assure oneself
that they are “proper and safe.”
Your MEC Aerial Work Platform has been designed, built, and tested to provide many years of safe,
dependable service. Only trained, authorized personnel should be allowed to operate or service the
machine.
MEC, as manufacturer, has no direct control over machine application and operation. Proper safety
practices are the responsibility of the user and all operating personnel.
If there is a question on application and/or operation, contact MEC Aerial Work Platforms:
1401 S. Madera Avenue, Kerman, CA93630 USA
Toll Free: 1 - 877 - 632 - 5438
Phone: 1 - 559 - 842 - 1500
Fax: 1 - 559 - 842 - 1520
www.MECawp.com
MEC Aerial Work Platforms
MEC Operator Policy
Section 1 - MEC Operator Policy

Page 3 Mast Series - Service & Parts Manual
May 2021
Safety Symbols & General Safety Tips
MEC manuals and decals use symbols, colors and signal words to help you recognize important
safety, operation and maintenance information.
RED and the word DANGER – Indicates an imminently hazardous
situation which, if not avoided, will result in death or serious injury.
ORANGE and the word WARNING – Indicates a potentially hazardous
situation which, if not avoided, could result in death or serious injury.
YELLOW with alert symbol and the word CAUTION – Indicates a
potentially hazardous situation which, if not avoided, may result in minor
or moderate injury.
YELLOW without alert symbol and the word CAUTION – Indicates a
potentially hazardous situation which, if not avoided, may result in
property damage.
GREEN and the word NOTICE – Indicates operation or maintenance
information.
Regular inspection and constant maintenance is the key to efficient economical operation of your
aerial work platform. It will help to assure that your equipment will perform satisfactorily with a
minimum of service and repair.
The actual operating environment of the machine governs the inspection schedule. Correct lubrication
is an essential part of the preventative maintenance to minimize wear on working parts and ensure
against premature failure. By maintaining correct lubrication, the possibility of mechanical failure and
resulting downtime is reduced to a minimum.
Never leave hydraulic components or hoses open. They must be protected from contamination
(including rain) at all times.
Never open a hydraulic system when there are contaminants in the air.
Always clean the surrounding area before opening hydraulic systems.
Use only recommended lubricants. Improper lubricants or incompatible lubricants may be as
harmful as no lubrication.
Watch for makeshift “fixes” which can jeopardize safety as well as lead to more costly repair.
•
•
•
•
•
Safety Symbols & General Safety Tips
Section 2 - Safety Symbols & General Safety Tips

Page 4 Mast Series - Service & Parts Manual
May 2021
Specifications
MME20 MME25
Height, Working Maximum* Indoor 26 ft 8.0 m 31 ft 9.5 m
Outdoor 22 ft 6.8 m 26 ft 8.0 m
Height, Platform Maximum Indoor 20 ft 6.0 m 25 ft 7.5 m
Outdoor 16 ft 4.8 m 20 ft 6.0 m
Height - Stowed 78.35 in 1.99 m 78.35 in 1.99 m
Width 30 in 0.76 m 31.50 in 0.80 m
Length 54.7 in 1.39 m 56.7 in 1.44 m
Platform Dimensions - Retracted
Platform Length × Width 29.5×28.5 in 0.75×0.72 m 29.5×28.5 in 0.75×0.72 m
Platform Dimensions - Extended
Platform Length × Width 50.5×28.5 in 1.28×0.72 m 50.5×28.5 in 1.28×0.72 m
Maximum Load Capacity 350 lbs 159 kg 350 lbs 159 kg
Rated Persons Indoor 1 1
Outdoor 1 1
Maximum Wind Speed Indoor 0 mph 0 m/s 0 mph 0 m/s
Outdoor 28 mph 12.5 m/s 28 mph 12.5 m/s
Wheelbase 44 in 1.12 m 44 in 1.12 m
Turning Radius Outside 61 in 1.55 m 62.2 in 1.58 m
Inside 0 in 0 m 0 in 0 m
Ground Clearance 2.36 in 6 cm 2.36 in 6 cm
Ground clearance
Pothole guards deployed 0.55 in 1.4 cm 0.55 in 1.4 cm
Weight ** 2,740 lbs 1,243 kg 3,310 lbs 1,501 kg
Power Source 2×12V 115Ah 2×12V 115Ah
Controls Proportional Proportional
AC Outlet In Platform Standard Standard
Maximum Hydraulic Pressure (Functions) 2,610 psi 180 bar 2,610 psi 180 bar
System Voltage 24V 24V
Driving Wheels 12.7×3.9 in 323×100 mm 12.7×3.9 in 323×100 mm
Airborne Noise Emissions <70 dB; Maximum sound level at normal operating workstations (A-weighted)
Vibration Value Does Not Exceed 2.5 m/s22.5 m/s2
Maximum Slope Rating
Stowed Position - Fore/Aft 25% 25%
Maximum Side Slope Rating
Stowed position 10% 10%
Note: Slope rating is subject to ground conditions and adequate traction.
Maximum Working Slope 1.5° side-to-side, 3.0° in-line
Drive speeds
Stowed, Maximum 2.5 mph 4.0 km/h 2.5 mph 4.0 km/h
Platform Raised, Maximum 0.7 mph 1.1 km/h 0.7 mph 1.1 km/h
Floor Loading Information
Tire Load, Maximum 937 lbs 425 kg 1,102 lbs 500 kg
Tire Contact Pressure - Max Load 115 psi / 8.1 kg/cm2793.8 k Pa 149 psi / 10.5 kg/cm21,028.0 kPa
Occupied Floor Pressure 235 psf / 1,150 kg/m211.27 kPa 267 psf / 1,304 kg/m212.8 kPa
Meets requirements of ANSI 92.20-2020 and CSA B354.6-2019.
Floor loading information is approximate and does not incorporate different option configurations.
It should be used only with adequate safety factors.
*Working Height adds 6 feet (2 m) to platform height.
**Weight may increase with certain options.
Section 3 - Specifications Specifications

Page 5 Mast Series - Service & Parts Manual
May 2021
Bolt Torque Specification - American Standard
Fasteners
Use the following values to apply torque unless a specific torque value is called out for the part being
used.
American Standard Cap Screws
SAE Grade 5 8
Cap Screw
Size (inches) Torque Torque
Ft. Lbs Nm Ft. Lbs Nm
Min Max Min Max Min Max Min Max
1/4 - 20 6.25 7.25 8.5 10 8.25 9.5 11 13
1/4 - 28 8 9 11 12 10.5 12 14 16
5/16 - 18 14 15 19 20 18.5 20 25 27
5/16 - 24 17.5 19 12 26 23 25 31 34
3/8 - 16 26 28 35 38 35 37 47.5 50
3/8 - 24 31 34 42 46 41 45 55.5 61
7/16- 14 41 45 55.5 61 55 60 74.5 81
7/16 - 20 51 55 69 74.5 68 75 92 102
1/2 - 13 65 72 88 97.5 86 96 116 130
1/2 - 20 76 84 103 114 102 112 138 152
9/16 - 12 95 105 129 142 127 140 172 190
9/16 - 18 111 123 150 167 148 164 200 222
5/8 - 11 126 139 171 188 168 185 228 251
5/8 - 18 152 168 206 228 203 224 275 304
3/4 - 10 238 262 322 255 318 350 431 474
3/4 - 16 274 302 371 409 365 402 495 544
7/8 - 9 350 386 474 523 466 515 631 698
7/8 - 14 407 448 551 607 543 597 736 809
1- 8 537 592 728 802 716 790 970 1070
1 - 14 670 740 908 1003 894 987 1211 1137
Torque values apply to fasteners as received from the supplier, dry or when lubricated with
normal engine oil.
If special graphite grease, molydisulphide grease, or other extreme pressure lubricants are
used, these torque values do not apply.
Section 4 - Torque Specifications
Bolt Torque Specification - American Standard

Page 6 Mast Series - Service & Parts Manual
May 2021Section 4 - Torque Specifications
Bolt Torque Specification - Metric Standard
Fasteners
Use the following values to apply torque unless a specific torque value is called out for the part being
used
Metric Cap Screws
Metric Grade 8.8 10.9
Cap Screw Size
(Millimeters)
8.8
9.01
Torque Torque
Ft. Lbs Nm Ft. Lbs Nm
Min Max Min Max Min Max Min Max
M6 × 1.00 6 8 8 11 9 11 12 15
M8 × 1.25 16 20 21.5 27 23 27 31 36.5
M10 × 1.50 29 35 39 47 42 52 57 70
M12 × 1.75 52 62 70 84 75 91 102 123
M14 × 2.00 85 103 115 139 120 146 163 198
M16 × 2.50 130 158 176 214 176 216 238 293
M18 × 2.50 172 210 233 284 240 294 325 398
M20 × 2.50 247 301 335 408 343 426 465 577
M22 × 2.50 332 404 450 547 472 576 639 780
M24 × 3.00 423 517 573 700 599 732 812 992
M27 × 3.00 637 779 863 1055 898 1098 1217 1488
M30 × 3.00 872 1066 1181 1444 1224 1496 1658 2027
Torque values apply to fasteners as received from the supplier, dry or when lubricated with
normal engine oil.
If special graphite grease, molydisulphide grease, or other extreme pressure lubricants are
used, these torque values do not apply.

Page 7 Mast Series - Service & Parts Manual
May 2021Section 4 - Torque Specifications
Hydraulic Components Torque Table
Note: Always lubricate threads with clean hydraulic fluid prior to installation.
Use the following values to torque hydraulic components when a specific value is not available.
Always check for torque values in the following places before relying on the Hydraulic Components
Torque Table.
Parts drawings and service instructions in this manual.
Packaging and instruction sheets provided with new parts.
Instruction manuals provided by the manufacturer of the component being serviced.
Type: SAE Port Series Cartridge Poppet Fittings Hoses
Ft. lbs Nm Ft. lbs Nm In. lbs Nm
#4 N/A N/A N/A N/A 135 - 145 15 - 16
#6 N/A N/A 10 - 20 14 - 27 215 - 245 24 - 28
#8 25 - 30 31 - 41 25 - 30 34 - 41 430 - 470 49 - 53
#10 35 - 40 47 - 54 35 - 40 47 - 54 680 - 750 77 - 85
#12 85 - 90 115 - 122 85 - 90 115 - 122 950 - 1050 107 - 119
#16 130 - 140 176 - 190 130 - 140 176 - 190 1300 - 1368 147 - 155
•
•
•

Page 8 Mast Series - Service & Parts Manual
May 2021
Maintenance Safety
Make sure the chock is in place during maintenance!
When the work platform of a Mast Series needs to be raised for routine
servicing purposes, a captive chock shall be used to enable the
extending structure to be held in the required position to prevent the
work platform from falling!
NEVER perform work or inspection on the machine with the platform elevated without first supporting
the platform with either a forklift or a crane. Alternatively, use a 2”×4” or recommended a 4”×4” piece
of wood to support the mast section that is attached to the platform.
Section 5 - Maintenance Safety Maintenance Safety

Page 9 Mast Series - Service & Parts Manual
May 2021
Hydraulic, Electrical and Total System
Hydraulic System
HYDRAULIC FLUID UNDER PRESSURE CAN PENETRATE AND BURN
SKIN, DAMAGE EYES, AND MAY CAUSE SERIOUS INJURY, BLINDNESS,
AND EVEN DEATH.
CORRECT LEAKS IMMEDIATELY.
Hydraulic fluid leaks under pressure may not always be visible. Check for
pin hole leaks with a piece of cardboard, not your hand.
Electrical System
Prevent damage to battery and/or electrical system;
Always disconnect the negative battery cable first.
Always connect the positive battery cable last.
•
•
When the negative cable is installed, a spark will occur if contact is made between the positive side
of the battery and a metal surface on the machine. This can cause damage to the electrical system,
battery explosion, and personal injury.
Total System
FAILURE TO PERFORM PREVENTIVE MAINTENANCE AT
RECOMMENDED INTERVALS MAY RESULT IN THE UNIT BEING
OPERATED WITH A DEFECT THAT COULD RESULT IN INJURY OR
DEATH OF THE OPERATOR.
IMMEDIATELY REPORT TO YOUR SUPERVISOR ANY DEFECT OR
MALFUNCTION. ANY DEFECT SHALL BE REPAIRED PRIOR TO
CONTINUED USE OF THE AERIAL WORK PLATFORM.
INSPECTION AND MAINTENANCE SHOULD BE PERFORMED BY
QUALIFIED PERSONNEL FAMILIAR WITH THE EQUIPMENT.
Hydraulic, Electrical and Total System
Section 6 - Hydraulic, Electrical and Total System

Page 10 Mast Series - Service & Parts Manual
May 2021
Machine Components
Platform
Controller
Platform
Extension
Platform
Entry
Gate
Manual
Storage
Container
Platform
Guard
Rails
Main Platform
Front
Wheel
Rear
Wheel
Covers
Covers Open To Show Interior
Masts
Assembly
Emergency
Lowering
Knob
Ground
Control
Panel
Main
Power
Switch
Batteries
Charger
Chassis
Tie-Down
Points
Forklift
Pockets
Batteries
Hydraulic Unit
Motor Controller
Pothole
Protection
Device
Art_5671A
Machine Components
Section 7 - Machine Components

Page 11 Mast Series - Service & Parts Manual
May 2021
Emergency Systems and Procedures
IF THE CONTROL SYSTEM FAILS WHILE THE PLATFORM IS ELEVATED,
HAVE AN EXPERIENCED OPERATOR USE THE EMERGENCY LOWERING
PROCEDURE TO SAFELY LOWER THE PLATFORM.
DO NOT ATTEMPT TO CLIMB DOWN ELEVATING ASSEMBLY.
Emergency Stop
The machine is equipped with an EMERGENCY STOP switch at the base
controls and the platform control box.
Press the EMERGENCY STOP switch at any time to stop all machine
functions.
Pull switch to reset.
Either switch will stop all machine functions.
Both switches must be reset or machine will not operate.
•
•
•
•
ART_3353
Emergency Lowering
To lower the platform, pull the Emergency Lowering Knob, located near the bottom of the front of the
machine where the Base Control panel is located. The Emergency Lowering Knob location has a
yellow decal border.
Art_5782
Emergency
Lowering
Knob
Emergency Systems and Procedures
Section 8 - Emergency Systems and Procedures

Page 12 Mast Series - Service & Parts Manual
May 2021
Brake Release Instructions
Observe and Obey:
Common sense and planning must be applied to control the movement of the machine when
lifting it with a crane or forklift.
Only qualified aerial lift operators should move the machine on or off the truck.
The transport vehicle must be parked on a level surface.
The transport vehicle must be secured to prevent rolling while the machine is being loaded.
Be sure the vehicle capacity, loading surfaces and chains or straps are sufficient to withstand the
machine weight. See the serial label for the machine weight.
The machine must be on a level surface or secured before releasing the brakes.
Only qualified forklift operators should lift the machine with a forklift.
Be sure the crane capacity, loading surfaces and straps or lines are sufficient to withstand the
machine weight. See the serial plate for the machine weight.
Brake Release Operation
Chock the wheels to prevent the machine from rolling.
Pull out the red Emergency Stop button on both the ground and platform controls to the ON
position.
Press and hold lift switch to “DOWN” position in ground control, meanwhile turn on the key
switch to the Ground position. The brake will be released afterAlarm alerts.
If you want to apply the brakes, just turn off the key switch or push the Emergency stop buttons.
Push the red Emergency stop button on both the ground and platform controls to the OFF
position.
When the machine is towed, do not exceed 2.5 mph / 4.0 km/h.
•
•
•
•
•
•
•
•
1.
2.
3.
4.
5.
Brake Release Instructions
Section 9 - Transport and Lifting Instructions

Page 13 Mast Series - Service & Parts Manual
May 2021Section 9 - Transport and Lifting Instructions
Transport and Lifting Instructions
Securing to Truck or Trailer for Transit
Always chock the machine wheels in preparation for transport.
Retract and secure the extension deck.
Turn the key switch to the OFF position and remove the key
before transporting.
Inspect the entire machine for loose or unsecured items.
Use the tie-down points on the chassis for anchoring down to
the transport surface.
Use a minimum of four chains or straps. Use chains or straps
of ample load capacity.
Do not overtighen chain binders.
Lifting the Machine with a Forklift
Be sure the extension deck, controls and component trays are
secure. Remove all loose items on the machine.
Fully lower the platform. The platform must remain lowered
during all loading and transport procedures.
Art_5671B
Use the forklift pockets located at the rear of the machine.
Position the forklift forks in position with the forklift pockets.
Drive forward to the full extent of the forks.
Raise the machine 6 in / 15 cm and then tilt the forks back slightly to keep the machine secure.
Be sure the machine is level when lowering the forks.
Lifting the machine from the side can result in component damage.

Page 14 Mast Series - Service & Parts Manual
May 2021Section 9 - Transport and Lifting Instructions
Crane Lifting Instructions
Only qualified riggers should rig and lift the machine.
Ensure that the crane, loading surfaces, cables, chains and straps are of
sufficient capacity to withstand the machine weight. See the serial plate
for the machine weight.
Fully lower the platform. Be sure the extension deck, control box and component trays are secure.
Remove all loose items on the machine.
Make sure the platform and chassis E-stops are depressed.
Use the lifting eye mounted on the rear mast column.
Make sure the mast is fully lowered.
Inspect the entire machine and remove any loose or unsecured items.
Adjust the rigging to prevent damage to the machine.
Lift the machine slowly to prevent rocking.
ART_5741

Page 15 Mast Series - Service & Parts Manual
May 2021
General Machine Maintenance
Instructions in this portion of the manual are to be used in conjunction with the Pre-Start, Frequent
and Annual Inspection checklists found in this machine’s Operator’s Manual.
IMPORTANT:Scheduled maintenance inspection checklists are included in the Operator’s
Manual for use only by qualified service technicians. Only qualified service
technicians may perform repairs to the machine. After repairs are completed,
the operator must perform a Pre-Start Inspection before proceeding to the
Functions Test.
HYDRAULIC FLUID UNDER PRESSURE CAN PENETRATE AND BURN
SKIN, DAMAGE EYES, AND MAY CAUSE SERIOUS INJURY, BLINDNESS,
AND DEATH. REPAIR LEAKS IMMEDIATELY. FLUID LEAKS UNDER
PRESSURE MAY NOT ALWAYS BE VISIBLE. CHECK FOR PIN HOLE
LEAKS WITH A PIECE OF CARDBOARD, NOT YOUR HAND.
NEVER PERFORM WORK OR INSPECTION ON THE MACHINE WITH
THE PLATFORM ELEVATED WITHOUT FIRST BLOCKING THE SCISSOR
ASSEMBLY WITH THE MAINTENANCE LOCK (SEE THE INTRODUCTION
PORTION OF THIS MANUAL).
PERFORM SCHEDULED MAINTENANCE AT RECOMMENDED INTERVALS.
FAILURE TO PERFORM SCHEDULED MAINTENANCE AT RECOMMENDED
INTERVALS MAY RESULT IN A DEFECTIVE OR MALFUNCTIONING
MACHINE AND MAY RESULT IN INJURY OR DEATH OF THE OPERATOR.
KEEP MAINTENANCE RECORDS CURRENT AND ACCURATE.
IMMEDIATELY REPORT ANY DAMAGE, DEFECT, UNAUTHORIZED
MODIFICATION OR MALFUNCTION TO YOUR SUPERVISOR. ANY DEFECT
MUST BE REPAIRED PRIOR TO CONTINUED USE. DO NOT USE A
DAMAGED, MODIFIED OR MALFUNCTIONING MACHINE.
Never leave hydraulic components or hoses open. Plug all hoses and
fitting immediately after disassembly to protect the system from outside
contamination (including rain).
Never open a hydraulic system when there are contaminants in the air.
Always clean the surrounding area before opening hydraulic systems.
Use only recommended lubricants. Improper lubricants or incompatible
lubricants may cause as much damage as no lubrication.
Watch for makeshift “fixes” which can jeopardize safety as well as lead to
more costly repair.
Inspection and maintenance should be performed by qualified personnel
familiar with the equipment.
Section 10 - Maintenance General Machine Maintenance
Other manuals for Mast Series
1
This manual suits for next models
2
Table of contents
Other Mec Lifting System manuals
Popular Lifting System manuals by other brands

Terex
Terex Genie SX-150 Service and repair manual

Affordable Wheelchair Lifts
Affordable Wheelchair Lifts KCSPM3648 owner's manual

Hy-Brid Lifts
Hy-Brid Lifts HB-830 Maintenance and troubleshooting manual

Norco
Norco 72674 Setup, operating, maintenance instructions
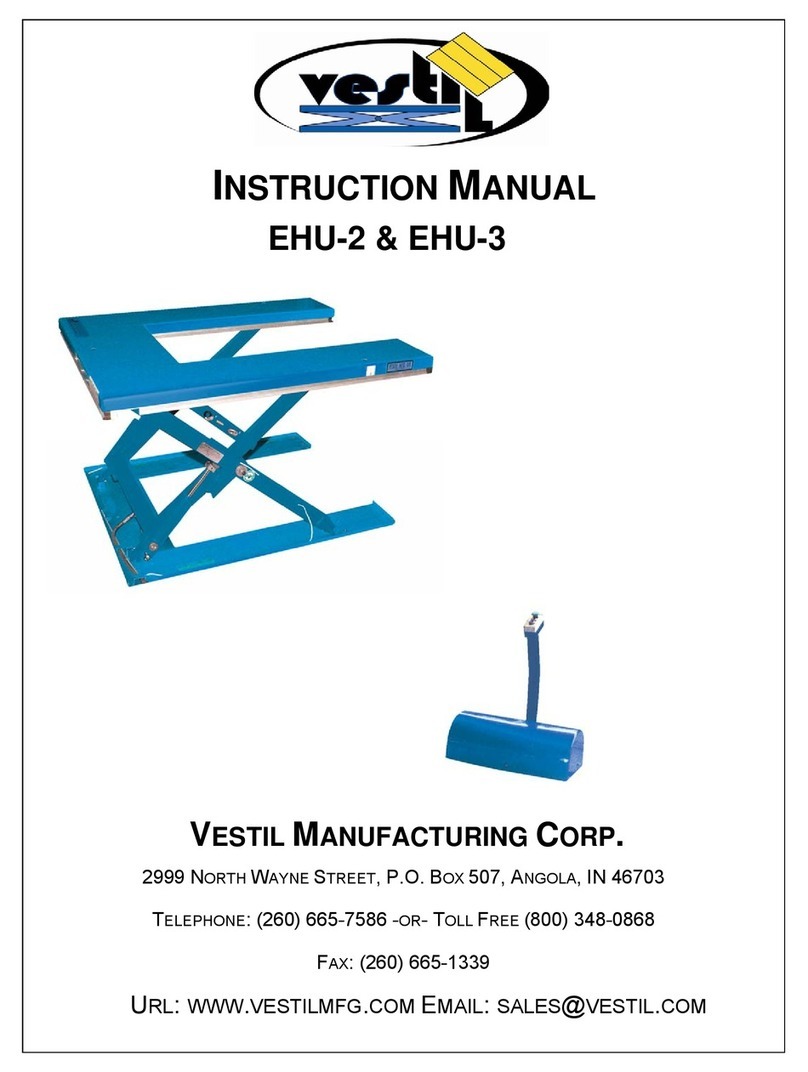
Vestil
Vestil EHU-2 instruction manual
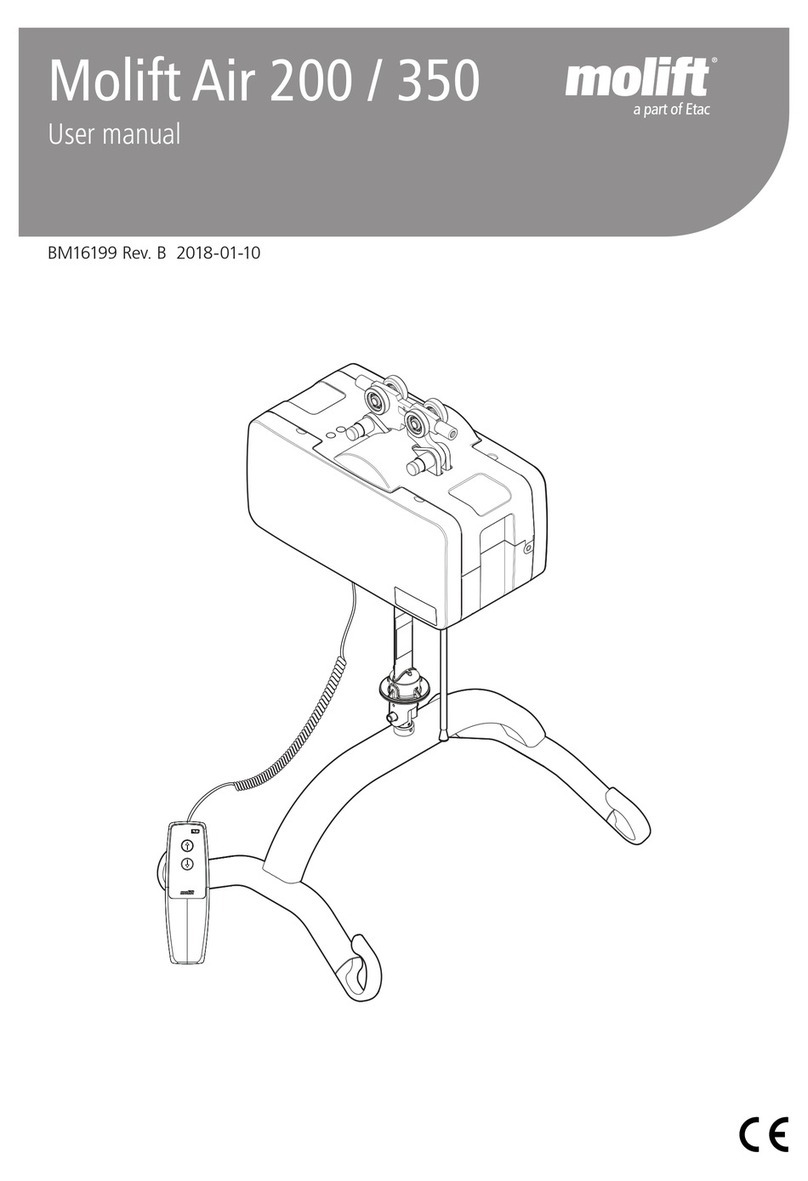
Molift
Molift Air 200 user manual