micro-trak MT-3405 FTW User manual

REFERENCE MANUAL
MTMT
--
33
44
00
55
FTWFTW
™
LR
AUTOMATICSPRAYRATECONTROLLER*
*For sprayers equipped with a single
flowmeter and three-way shut-off valves.

1305 Stadium Road
Mankato, MN 56001-5355
© Copyright 2000
Micro-Trak Systems, Inc.
Printed in the U.S.A.
The MT-3405 FTW is an electronic monitoring and control system that can help you achieve maximum yields and operate more
cost-effectively by providing the information you need to maintain proper application rates of liquid chemicals and fertilizer.
The MT-3405 FTW has been designed for easy installation and operation. However, since each installation will vary depending
on your equipment, please take time to familiarize yourself with this manual and the actual components before beginning.
Following the procedures described in this manual will ensure proper performance and help avoid problems or questions
once you are in the field. PLEASE NOTE: This controller is NOT for use with two-way boom shut-off valves, NH3 application or
dry product application.
This manual is written for the MT-3405 FTW Model MT34F-00-FTW, which may be used for either English or Metric measure-
ment. Please read the manual carefully and follow the instructions as they apply to your usage.
If you do encounter a problem that cannot be corrected by reviewing this manual, consult your dealer or distributor, or contact
a Micro-Trak technician for assistance.
2
MTMT
--
33
44
00
55
FTWFTW
™
LR
AUTOMATIC SPRAY RATE CONTROLLER*
REFERENCE MANUAL
Toll Free in U.S. or Canada: (800) 328-9613 or (507) 257-3600

3
Micro-Trak®Warranty
Micro-Trak (herein “Seller”) warrants to the original purchaser (herein “Buyer”) that, if any product or part of the product
(herein “part”) proves to be defective in material or workmanship, upon inspection and examination by Seller, within one (1)
year from the original date-of-purchase, and is returned to Seller with dated proof-of-purchase, transportation prepaid, within
thirty (30) days after such defect is discovered, Seller will, at their option and sole discretion, either repair or replace said part,
except that the warranty for expendable parts, including but not limited to, light bulbs and batteries shall be thirty (30) days
from the original date-of-purchase. Said warranty is valid only when the part has been installed, operated and maintained in
strict accordance with the procedures outlined in the manual. Any damage or failure to said part resulting from abuse, misuse,
neglect, accidental or improper installation or maintenance, unauthorized modification, use with other products or attributable
to acts of God, as determined solely by the Seller, will invalidate the warranty. Said part will not be considered defective if it
substantially fulfills the performance specification. Buyer shall be responsible for all maintenance services, if any, all in strict
accordance with the procedures outlined in the manual. The warranty does not include labor, installation, replacement parts
or repairs, delivery of replacement parts or repairs or time and travel. Said warranty is nontransferable.
THEFOREGOINGWARRANTYISEXCLUSIVEANDINLIEUOFALLOTHERWARRANTIESOFMERCHANTABILITY,FITNESSFOR
PURPOSE AND OF ANY OTHER TYPE, WHETHER EXPRESS OR IMPLIED. The Seller’s liability, whether in contract, in tort, under
any warranty, in negligence or otherwise, shall not exceed the return of the amount of the purchase price paid by the Buyer,
and under no circumstance shall the Seller be liable for special, indirect or consequential damages. Seller neither assumes nor
authorizes anyone to assume for it any other obligation or liability in connection with said part. No action, regardless of form,
arising out of the transactions under this agreement may be brought by the Buyer more than one (1) year after the cause of
action has occurred.
Seller agrees to extend the term of the foregoing warranty period should the Buyer return completed warranty registration
information, with dated proof-of-purchase, to the Seller within one (1) year from the original date-of-purchase. All conditions
and limitations of said foregoing warranty, except the term of said foregoing warranty, shall apply. Said term shall be extended
to a total of three (3) years from the original date-of purchase on display consoles and network communication modules, as
defined by Seller, and said term shall be extended to a total of two (2) years from the original date-of-purchase on all other
parts, except that the warranty for expendable parts, including but not limited to, light bulbs and batteries shall be thirty (30)
days from the original date-of-purchase, and except that the warranty for parts manufactured by someone other than the
Seller, including but not limited to, shut-off and control valves, DGPS receivers, memory cards and drives, mapping software,
flowmeters and pressure sensors shall be one (1) year from the original date-of-purchase.
Buyer accepts these terms and warranty limitations unless the product is returned to Seller, via proper distribution channels
and approved return authorization, with dated proof-of-purchase, transportation prepaid, within fifteen (15) days from the
date-of-purchase for refund of the purchase price.
Units under warranty should be sent prepaid, with dated proof-of-purchase, within 30 days of discovering defect, to the
address below:
MAIL AND UPS:
Micro-Trak Systems, Inc.
ATTN: Service Department
1305 Stadium Road
Mankato, MN 56001-5355
At Micro-Trak Systems, we believe a product that delivers quality and performance at a low cost is what is needed to help
today’s operator and the operator of the future compete in the world market.
It is our goal to provide operators with a line of electronic equipment that will help build and maintain an efficient and
profitable operation that can be passed on to future generations.
We thank you for your purchase and hope that we can be of service to you in the future.
Micro-Trak Systems, Inc.
Extended Warranty Option
It’s simple! Just complete the enclosed registration card(s) for this
product and mail it in and we’ll extend your warranty for up to three years*, at no additional charge.
MAIL IN YOUR REGISTRATION CARD(S) TODAY!
Registration Card information is for internal use only.
* Some limitations apply. See warranty statement for details.

4
Table of Contents
Warranty..................................................................................................................................................................................................3
Table of Contents ............................................................................................................................................................................ 4-5
Basic Overview of Typical Installation ..............................................................................................................................................6
Component Parts and Assembly Hardware................................................................................................................................. 7-8
Introduction to the MT-3405 FTW .....................................................................................................................................................9
Installation........................................................................................................................................................................................9-15
Mounting the Display Console................................................................................................................................................................................9
Electrical Installation ...................................................................................................................................................................................................9
Speed Sensor Installation.................................................................................................................................................................................10-11
Magnets....................................................................................................................................................................................................................10
Attaching Magnets............................................................................................................................................................................................... 11
Connecting the Speed Sensor Cable............................................................................................................................................................. 11
Speed Sensor Options............................................................................................................................................................................................. 12
Mounting and Plumbing Flowmeter ................................................................................................................................................................. 12
Installing Flow Sensor Cable................................................................................................................................................................................. 13
Pressure Relief Valve ................................................................................................................................................................................................13
Servo, Throttling Valves.......................................................................................................................................................................................... 13
Relief Valves................................................................................................................................................................................................................. 14
Boom Shut-off Valves ..............................................................................................................................................................................................14
Remote Run/Hold......................................................................................................................................................................................................15
MT-3405 FTW Console Functions.....................................................................................................................................................16
Calibration ......................................................................................................................................................................................17-26
English or Metric?......................................................................................................................................................................................................17
Entering Calibration .................................................................................................................................................................................................17
Entering Calibration Values.............................................................................................................................................................................18-21
Target Rate, Adjust Rate, Test Speed, Boom Select, Width................................................................................................................... 18
Setting Individual Boom Width....................................................................................................................................................................... 18
Banding Application Calibration, Circ........................................................................................................................................................... 19
Determining Wheel Circumference............................................................................................................................................................... 19
Drive Shaft Speed Sensor Calibration, Min Flow ...................................................................................................................................... 20
Flow Cal....................................................................................................................................................................................................................21
Exiting Calibration................................................................................................................................................................................................21
Care and Maintenance of your MT-3405 FTW....................................................................................................................................................21
Plumbing Overview Diagrams .......................................................................................................................................................................22-23
Fine Tuning Speed/Distance Calibration Value ............................................................................................................................................. 24
Fine Tuning Flowmeter Calibration....................................................................................................................................................................25
Test Speed....................................................................................................................................................................................................................28
Pre-Field System Checkout.................................................................................................................................................................................... 26
Operation........................................................................................................................................................................................27-28
Console, Power Switch, Run/Hold Switch, Boom Switches, Auto/Man Button .................................................................................27
Cal Button, “+” and “-” Buttons, Rotary Switch, App. Rate, Area/Hour, Speed................................................................................... 27
Total Area, Sub Area, Distance, Flow Rate, Total Flow, Warning Device ..............................................................................................27
On-the-go “Delta” Rate Adjustments (Adjust Rate)......................................................................................................................................28
Resetting System Counters ................................................................................................................................................................................... 28

5
Table of Contents (cont)
Troubleshooting............................................................................................................................................................................29-34
General..........................................................................................................................................................................................................................29
Console Appears Dead, Speed is Always Zero or Erratic, Area Count is Inaccurate.................................................................... 29
Distance Count is Inaccurate, No Readout of Gallons (liters), or Gallons (liters) Per Minute ................................................... 29
Total Liquid Used is Inaccurate, 6553.5 Message Displayed, Console is Erratic in Operation .................................................29
Displayed Measurements Do Not Make Sense, Display Reads “OFL”..............................................................................................29
Checking Individual Components ...................................................................................................................................................................... 30
Console, Harness, Electrical Interference, Power, Accessory Power.................................................................................................. 30
Run/Hold Hall-effect Sensor, Run/Hold Jumper Dust Cover................................................................................................................30
Magnetic Hall-effect Speed and Flow Sensors .......................................................................................................................................... 30
Trak-Star Ultrasonic Speed Sensor .................................................................................................................................................................30
Console Inputs............................................................................................................................................................................................................31
Speed Input, Flow Input, Remote Run/Hold Input .................................................................................................................................. 31
Flowmeter ...............................................................................................................................................................................................................31
Electric Boom Valves, Servo Valve Control Signal, Servo Valve........................................................................................................... 31
Plumbing .................................................................................................................................................................................................................31
Plumbing Troubleshooting Chart ....................................................................................................................................................................... 32
Flowmeter Cleaning and Assembly....................................................................................................................................................................33
MT-3405 FTW Wiring Diagram .............................................................................................................................................................................34
Plumbing Guidelines ....................................................................................................................................................................35-36
General, Pump Inlet, Agitation, Servo, Flowmeter, Pump..................................................................................................................... 35
Valve Purpose and Adjustments.....................................................................................................................................................................36
Appendices.....................................................................................................................................................................................37-44
Appendix A: Optional Speed Sensor Mounting Installation...............................................................................................................38-39
Implement Wheels, Front Tractor Wheel, ATV Wheels...........................................................................................................................38
Mounting on Drive Shaft ...................................................................................................................................................................................39
Appendix B: Various Ball Valve Configurations.............................................................................................................................................. 40
Appendix C: 12-Volt Servo Valve (Control Valve) Calibration................................................................................................................... 41
Appendix D: Adjusting By-pass Valves.............................................................................................................................................................. 42
Appendix E: Conversion Chart ............................................................................................................................................................................. 43
Appendix F: Replacement Parts List...................................................................................................................................................................44
Notes ...............................................................................................................................................................................................45-46

6
MT-3405 FTW Basic Overview of Typical Installation
Hall-eect Speed Sensor
Magnets on Hub of
Non-driven Wheel
MT-3405 FTW Console Remote Run/Hold
Harness Connection
Battery
Agitation Shot-o Valve *
Stainer *
Pump *
Servo
Main Harness Hitch Connectors
Trottle Valve *
Flowmeter installed after
the agitation/return line,
pressure regulator and lter,
but before the boom valve
* Items NOT Included with the MT-3405 FTW
Boom Shut-o Valves *

7
Component Parts and Assembly Hardware
Before beginning installation, check the carton contents for the following items:
Terminal Kit
P/N 13270
Speed Sensor Kit P/N 01531
Including items A-G, below:
C. 15’ 3-Pin Extension Cable
M/P 150 P/N 13207
F. Magnet Clips (6)
P/N 10080
G. Hardware Bag
P/N 13251
D. Speed Sensor
Mounting Bracket
P/N 10013
E. Magnets (6)
P/N 12069
(2 in hardware bag)
MT-3405 FTW Console
P/N 13887
10’ 10-Pin M/P Extension Cable (3)
P/N 13221
5’ 3-Pin W/P Extension Cable
P/N 10450 1” Electric
Servo Valve
P/N 11218
20’ 3-Pin M/P Power Harness
P/N 13092
14” Nylon Cable Ties
P/N 12910
B: 14” Nylon Cable Ties
P/N 12910
5’ Shut-off Cables (5)
P/N 13115
FM750 GFN
Flowmeter
P/N 11501
Console Mount Kit
P/N 13774
5’ Hall-effect Flow Sensor Cable
with threaded sensor
P/N 13096
A: 5’ Hall-effect Flow Sensor Cable
with threaded sensor
P/N 13096
Reference Manual
P/N 13895
REFERENCE MANUAL
MT
-
3
4
0
5
FTW
™
LR
AUTOMATIC SPRAY RATE CONTROLLER*
*For sprayers equipped with a single
owmeter and three-way shut-o valves.
C B A
B A

A B
4 3
C B A
A B C
C B A
C B A
A B C D E
Run/Hold
(Gray Tie)
Flow
(Green Tie)
Boom 1
(Brown Tie)
Servo
(No Tie)
Red Tie
A B
4 3
E D C B A
A B
A B
Relief
(No Tie)
White
(Natural) Tie
Boom 3
(Orange Tie )
Boom 2
(Red Tie)
A B
4 3
A B
C B A
A B C D E
Boom 4
(Yellow Tie)
Blue Tie
Boom 5
(Green Tie)
Speed
(Yellow Tie)
8
Component Parts and Assembly Hardware (cont)
10’ Relief,
Booms 2&3 Harness
P/N 13762
10’ Speed,
Booms 4&5 Harness
P/N 13763
10’ Flow, Run/hold, Servo,
Boom 1 Harness
P/N 13083

9
Introduction
MT-3405 FTW
Select a mounting location which seems most workable,
and that best fits your needs. It should be convenient to
reach and highly visible to the operator. DO NOT INSTALL
IN A POSITION THAT OBSTRUCTS THE VIEW OF THE ROAD
OR WORK AREA. Whenever possible, avoid locations that
expose the console to direct sunlight, high temperature,
strong chemicals or rain.
Place the mounting bracket in the selected location, mark
holes, drill 1/4” (7mm) holes and mount bracket with bolts,
lockwashers and nuts provided. (If bolts are not practical, use
self-tapping screws.) See Illustration 1.
Insert the console in the “U” bracket and install the console
knobs through the bracket, placing a rubber washer over the
threaded stud. Position console to proper viewing angle and
tighten the knobs securely.
Illustration 1
Tools Needed to Install MT-3405 FTW
• Screwdrivers • Pliers
• Set of Wrenches • Wire Cutter
• Electric Drill and Bits • Hammer
• 12-Volt Test Light • Hacksaw
• Center Punch • Bench Vise
The MT-3405 FTW is a flow-based control system which is
designed to be used on sprayers with diverting (three-way)
boom valves.
Using typical boom valves and a Micro-Trak flow-based rate
control system, when one of more of the boom sections are
turned off, the flow of liquid is discontinued to that boom
section, and flow is adjusted through the remaining boom
sections so that application rate (when in automatic) is not
affected.
Using the diverting (three-way) valve and the MT-3405 FTW
flow-based control system, liquid is actually diverted or
by-passed back to the tank. With the special “FTW” software,
the MT-3405 FTW counts only the liquid that has been
sprayed.
The MT-3405 FTW system uses individually entered boom
widths to determine which portion of the total liquid is being
by-passed rather than sprayed from the boom section. For
this reason, it is extremely important to adjust and verify
the amount of liquid that is diverted by the three-way valve
when a boom is shut off. Please read your sprayer’s operating
manual for details, or see Appendix C for basic instructions.
Installation
Mounting the Display Console
WIDTHBOOM
SELECT
TEST
SPEED
ADJUST
RATE
TARGET
RATE
CIRC
MIN
FLOW
FLOW
CAL
SPEED DISTANCE
FLOW
RATE
TOTAL AREA
APP. RATE TOTAL FLOW
SUB AREA
ON
OFF
12345
B O O M S
RUN
HOL
AREA
HOUR
CAL
AUTO
MAN
RESET
MT-3405
™F
AUTOMATIC RATE CONTROLLER
MANAUTO
CALHOLD
V 1 2 3 4 5
AUTOMATIC SPRAY RATE CONTROLLER
Electrical Installation
The MT-3405 FTW must be connected to a 12-volt DC elec-
trical system. Power is connected directly to the battery. The
MT-3405 FTW has an ON/OFF switch on the console to turn
the power off when the system is not being used.
Locate the power cable harness and connect to the mating
connector on the console. Connect the blue chassis ground
wire to a good frame ground. See Illustration 2. Make sure
there is good metal-to-metal contact. Route the power cable
from the console to the battery. Cut off excess length. In
routing cable to battery, avoid areas where the cable may
be subjected to abrasion or excessive heat. Install the in-line
fuse provided with the kit on the white wire, as illustrated,
to protect the circuit. Connect the WHITE wire (hot) to the
positive battery terminal. Attach the BLACK wire (ground) to
a screw or bolt on the equipment frame. See Illustration 2. Be
sure there is good metal-to-metal contact.
Your MT-3405 FTW is equipped with an advanced electronic
memory which does not require a constant supply of pow-
er to retain daily totals or calibration values. The advantage
Hot
(WHITE)
20-Amp In-line
Fuse Required
Chassis Ground
(BLACK)
Ground
Illustration 2
NOTE: For negative ground systems ONLY.
with this type of memory is that it conserves battery power
and will not discharge the vehicle’s battery when equipment
is not in use.

10
PLEASE NOTE: If you have purchased a Trak-Star speed
sensor, disregard the section on magnetic speed sensors
and install the Trak-Star as described in the instructions
packed with the unit.
Locations where the sensor may be installed:
1. Non-driven wheel on tractor, vehicle or implement. This
is less susceptible to errors resulting from wheel slip.
2. Tractor, vehicle or planter drive shaft. This type of
mounting is recommended for trucks, four-wheel drive
tractors or other equipment that has poor or no access
to a non-driven wheel.
Installation (cont)
Speed Sensor Installation
Locate the Following Parts:
• Speed Sensor Cable
• Mounting “L” Bracket
• Magnet Clips
• Magnets
• Cable Ties
Magnets
Please read the following information about magnet spacing
and polarity.
The number of magnets that must be used depends on
where you mount the sensor. The general rule for tractor
or implement wheels is one magnet for each wheel bolt
(minimum of two, and always use an even number). For drive
shafts or small wheels (ATV’s), a minimum of two magnets
are required.
The magnets provided by Micro-Trak are marked with
a dashed line on the SOUTH pole side of the magnet.
See Illustration 3A.
Always use an even number of magnets, and always alternate
the polarities of the magnets as you go around the wheel
hub or drive shaft.
To install, mount the first magnet with the SOUTH pole side
(dashed line) facing toward the hub or shaft. Mount the
second magnet with the NORTH pole side facing toward the
hub or shaft. See Illustration 3B.
For proper operation, the magnets must be evenly spaced
around the wheel or drive shaft. The magnets must be at
least 1” apart. See Illustration 3C.
Illustration 3A
Illustration 3C
Illustration 3B
S
N
North
North
North
South
South
South
1
2
43
5
6
Test magnet
should alternately
attract and repel.
1” Minimum

11
Attaching Magnets
Refer to the following diagram for general mounting
instructions. For specific mounting instructions, refer to
Appendix A in the back of this manual.
NOTE: Magnets may be attached mechanically as shown or
adhered with epoxy or other high quality adhesive. When
using adhesive, thoroughly clean the area of dirt and oil.
The magnets are attached to a wheel hub or drive shaft and
the speed sensor is mounted directly over the magnet. When
the wheel or drive shaft begins turning, a speed impulse
is sent to the MT-3405 FTW console every time a magnet
passes by the tip of the speed sensor. For the speed sensor
to operate properly, the spacing between the magnets and
the tip of the sensor must always remain constant. Before
permanently mounting any parts, be sure that the location
you have selected will meet the following requirements.
See Illustration 4.
Installation (cont)
Speed Sensor Installation (cont)
Illustration 4
45° max
Sensor
(Green body)
Magnet
3/8” nuts
Bracket must
be rigidly
mounted
Sensor assembly must not
be mounted more than
45° from perpendicular
¼” to ½” air gap
Drill lug bolt hole
and bend to fit hub.
Magnet
Connecting the Speed Sensor Cable
The speed sensor cable has a GREEN sensor body and mates
with the main harness cable having a YELLOW cable tie near
the 3-pin M/P connector. Make certain that you install the
correct sensor cable and connect it to the correct connector
on the main harness. The speed sensor and the flow sensor
are identical, but must be connected to the proper harness
connector. The speed sensor always connects to the main
harness lead with the YELLOW tie and flow sensor always
connects to the main harness lead with the GREEN tie.
See Illustration 5.
INSTALLATION NOTE: The main harness provides two
connection points for the speed sensor. For speed sensor
installations in the cab or near the control console, it
may be more practical to use the local access connector
(YELLOW tie) on the control console pigtail exiting the rear
of the console. Using this connection point will disable
the connection point on the end of the main harness. For
speed sensor installations on implements, it may be more
practical to use the speed connector on the end of the
main harness. When using this connection point, make
certain that the local access connector for speed/distance
is mated together.
The Run/hold sensor, which plugs into the other main
harness cable, also uses the same type of connector as the
speed and flow sensors. However, the Run/hold sensor has a
GRAY tie near the 3-pin connector, the sensor body is BLACK,
and it always connects to the main harness lead with the
GRAY tie.
Illustration 5
SENSOR IDENTIFICATION CHART
SENSOR SENSOR BODY COLOR MAIN HARNESS TIE COLOR
Speed Green Yellow
Flow Green Green
BOOM FIVE
DISTANCE
RED
ORG
YEL
GRN
BLU
VIO
N/C
N/C
BLK
BRN A
B
C
D
E
F
G
H
J
K
10-PIN METRI-PACK TOWER
A
B
C
D
E
F
G
H
J
K
10-PIN METRI-PACK SHROUD
A
B
C
3-PIN
M/P 150
TOWER
LOCAL ACCESS SPEED CONNECTOR
BOOM FOUR
MT 3405 FTW CONSOLE
REMOVE JUMPER WIRE
TO CONFIGURE FOR BALL VALVES.
YELLOW TIE
A
B
C
3-PIN
M/P 150
SHROUD
A
B
2-PIN
M/P 150
SHROUD
A
B
2-PIN
M/P 150
TOWER
BRN
RED
ORG
YEL
GRN
BLU
VIO
GRY
WHT
BLK
A
B
C
D
E
F
G
H
J
K
A
B
C
D
E
F
G
H
J
K
10-PIN METRI-PACK TOWER
10-PIN METRI-PACK SHROUD
N/C
RED
BLK
RED
WHT
BLK
BLK
N/C
N/C
RED
3-PIN
M/P 150
SHROUD
A
B
C
YELLOW TIE
2-PIN
M/P 150
SHROUD
A
B
BLACK TIE
YELLOW TIE
GREEN TIE
A
B
A
B
A
B
2-PIN
M/P 150
TOWER
2-PIN
M/P 150
TOWER
2-PIN
M/P 150
SHROUD
3-PIN
M/P 150
TOWER
A
B
C
RED
BLK
RED
BLK
RED
WHT
BLK
FEMALE .250 QD
FEMALE .250 QD
FEMALE .250 QD
FEMALE .250 QD

12
Installation (cont)
Speed Sensor Options
Vansco Radar Speed Sensor
Contact a Micro-Trak sales representative for details on any of these products,
or call Micro-Trak Systems, Inc. at 1-800-328-9613.
Astro II GPS Speed Sensor
In addition to the standard Hall-effect magnetic speed
sensor, the MT-3405 FTW may be interfaced with a variety of
other speed sensing equipment. Several options are listed
below.
ASTROSERIESOROTHERGPSSPEEDSENSORINTERFACES
The MT-9000 may also be used with most GPS speed sensors
that output a pulsed signal, such as the Micro-Trak Astro
II and 5, SkyTrak or Dickey-John GPS speed sensors. An
adapter cable may be required.
VANSCO™RADAR SPEED SENSOR
The Vansco radar speed sensor uses a microwave (radar)
signal to deliver a reliable, accurate speed signal for electronic
equipment. It features state-of-the-art electronic design/
manufacturing, rugged aluminum housing and complete
testing and certification.
RADAR INTERFACE
The MT-9000 may also be interfaced with most popular
radar ground speed sensors. An adapter cable is required for
proper interface.
SEE APPENDIX H FOR LIST OF ADAPTER CABLES FOR RADAR.
GPS SPEED SENSOR INTERFACE
The MT-9000 may also be used with most GPS speed sensors
that output a pulsed signal, such as SkyTrak or Dickey-John
GPS speed sensors. An adapter cable may be required.
The Flowmeter must be installed in the boom supply line
after any strainers, return lines, or valves, but before the
boom shut-off valves. Securely mount flowmeter (hardware
not supplied) in a vertical position in an area away from
intense vibration. DO NOT install flowmeter closer than 12”
to the servo valve or the boom shut-off valves. (The flow-
meter may need periodic cleaning, so it should be easy to
remove). The flow meter is a bidirectional meter (exception:
Polmac’s 1 1/2” - 3”). Liquid can flow in either direction, but
up is preferred. Make connections using 3/4” fittings without
the use of reducers, elbows or sharp bends for a minimum of
six inches (15 cm) either side of meter. See Illustration 6.
NOTE: Save plastic plugs to protect flowmeter during
storage.
Illustration 6
Sprayer Line*
Locknut
Sensor
(green body)
Flowmeter
* NOT SUPPLIED
“L” Bracket*
Hose Clamps*
¾” NPT Male Fitting*
Hose Clamps*
Hose Clamps*
Mounting and Plumbing Flowmeter

13
With the flowmeter in place, install the flow sensor cable
(GREEN body).
Screw sensor all the way into hole of flowmeter. Tighten 3/8”
jam nut to lock sensor in place.
Uncoil flow sensor cable and carefully route it to meet the
main harness flow connector marked with GREEN tie. Align
connectors and press firmly together until locking tab clicks
into place. Secure cable with ties provided. See Illustration 7.
Connect flow sensor cable to green-tie console cable.
Installation (cont)
Installing Flow Sensor Cable
Illustration 7
A B C
C B A
Flow Sensor
Cable Connector
Main Harness
Flow Connector
Green Tie
Pressure Relief Valve
If you have a positive displacement pump or a centrifugal
pump capable of generating excessive pressure, you must
install a pressure relief valve and adjust it to a safe maxi-
mum pressure. If a positive displacement pump is operated
without a pressure relief valve, damage may result to pump
or other plumbing component. See Illustration 8.
For Positive Displacement Pump
Illustration 8
Tee “C”
Tee “A”
Pressure
Relief Valve
Servo, Throttling Valves
The servo valve installs in an unrestricted return line to the
inlet of the pump or directly into the tank. DO NOT install the
servo valve closer than 12” to the flowmeter. The servo valve
has a flow direction decal on it. Make certain that the actual
flow direction matches the decal on the servo valve. DO NOT
install the servo valve in the agitation line. Slow response
time and marginal operation may result. The return line
should tee from the main line just after the throttling valve.
See Illustration 9. The throttling valve is used to limit the
output (set maximum output) of the pump to the flowmeter
and servo valve. The throttling valve is adjusted to put
the servo valve in its optimal operating range. Please refer
to Pre-Field System Checkout for proper valve adjustment
procedure.
The servo valve connects directly to the main harness 3-pin
W/P cable lead. If more length is required, use a 3-pin W/P
extension cable of the appropriate length. If using a Braglia
Illustration 9
Return to pump
inlet or unrestricted
return to tank
Servo Valve Cable
From Pump Throttling Valve
To Flowmeter
Servo Valve
or other 12-volt control valve, please refer to 12-Volt Control
Valve Calibration on page 39.
NOTE: The servo valve may be installed in the main spray
line. For in-line installations, you will need to cut the servo
cable and reverse the wires. Connect the RED wire to the
BLACK wire and vice versa. Failure to reverse the wires will
result in the servo valve operating backwards.

14
The relief valve is used to “dump” pressure when all boom
valves are turned off. Whenever all the boom control
switches are turned off, or when HOLD is selected with the
master switch, the relief valve should be open. Use this
plumbing illustration (See Illustration 10) as your pattern
for proper installation if your relief valve has a flow-through
port. DO NOT install the relief valve closer than 12” to the
flowmeter. Locate a 2-pin solenoid cable and connect it to
the relief valve using an appropriate method. Connect a
2-pin M/P connector to the module cable with no colored tie.
Be careful not to connect the relief valve cable to one of the
boom shut-off leads. All of the boom shut-off leads have a
colored tie near the 3-pin M/P connector. the relief solenoid
lead does not.
If all valves are NOT the same type (all solenoid or all ball
valves), refer to Appendix B for wiring instructions.
If your relief valve does not have flow-through port, you must
add a “T” fitting. See Illustration 11.
NOTE: To assure a good connection and avoid corrosion,
coat electrical connections with silicone grease.
Installation (cont)
Relief Valves
Illustration 11
Illustration 10
RELIEF SOLENOID
“T” Fitting
Servo
Valve
Relief
Solenoid
Boom Shut-off Valves
Locate the boom shut-off cables. Crimp the insulated female
spade terminals provided with the cables to both wires. (If
valves have wires, crimp terminals on those wires). Attach
the cables to the terminals on the boom valves. Normally,
wires connect red to red and black to black. If valves operate
backwards, reverse connections. Apply silicone grease to the
terminal connections to help prevent corrosion and insure a
good electrical connection.
Locate the colored cable ties included with the boom shut-off
cables. Attach a BROWN tie near the 2-pin M/P connector on
the boom one (1) cable. Attach a RED tie near the 2-pin M/P
connector on the boom two (2) cable. Attach an ORANGE tie
near the 2-pin M/P connector on the boom three (3) cable.
Attach a YELLOW tie near the 2-pin M/P connector on the
boom four (4) cable. Attach a GREEN tie near the 2-pin M/P
connector on the boom five (5) cable.
Connect the 2-pin M/P connectors to the mating connectors
on the main harness. Boom one (1) connects to the mating
connector with the BROWN cable tie near the connector.
Boom two (2) connects to the mating connector with the
RED cable tie near the connector. Boom three (3) connects
to the mating connector with the ORANGE cable tie near the
connector. Boom four (4) connects to the mating connector
with the YELLOW cable tie near the connector. Boom five (5)
connects to the mating connector with the GREEN cable tie
near the connector. See Illustration 12.
Illustration 12
Boom 1
(Brn Tie)
Boom 2
(Red Tie)
Boom 2
(Org Tie) Boom 2
(Yel Tie)

15
Lift Wheel Mounting
Hydraulic Cylinder Mounting
Remote Run sensor on hydraulic cylinder. Magnet and sensor
are in line when equipment is lowered and operating.
The run/hold sensor cable has a black body and a GRAY tie
near the 3-pin M/P connector and mates with the main har-
ness cable having a GRAY cable tie near the 3-pin M/P con-
nector. Make certain that you install the correct sensor cable
and connect it to the correct connector on the main harness.
The run/hold sensor has a BLACK body. DO NOT use a speed/
flow sensor (GREEN body). See Illustration 13.
• Attach a magnet to a lever or some part of the equipment
that moves when the implement is raised and lowered.
The Hall-effect run/hold sensor is sensitive only to the
south pole (side with dashed line) of the magnet. Check
the polarity of the magnet by bringing it near the run/
hold sensor with the console turned on. Note and mark
the face of the magnet that is toward the sensor when
the console does not indicate “HOLD.” When the magnet
is away from the sensor, the console will be in HOLD and
will shut off the boom valves and stop counting acres.
NOTE: The run/hold kit includes a 5’ sensor cable
and 10’ extension. You may require additional
extension cables which are available in 5 ft. (1.5
m), 10 ft. (3 m), 15 ft. (4.5 m), 20 ft. (6 m) and 25 ft.
(7.6 m) lengths.
• You may also use a toggle or other type switch. Simply
cut the blue jumper wire in the dust cover and splice on
an appropriate length of wire to reach your switch.
When switch is closed, console is in RUN. When the switch is
open, the console is in HOLD.
INSTALLATION NOTE: The main harness provides two
connection points for the run/hold. For Run/Hold installa-
tions in the cab or near the control console, it may be more
practical to use the local access connector on the control
console pigtail (GRAY tie) exiting the rear of the console.
Using this connection point will disable the connection
point on the end of the main harness. For run/hold sensor
installations on implements, it may be more practical
to use the run/hold connector on the end of the main
harness. When using this connection point, make certain
that the local access connector is mated together.
Illustration 13
BLACK TIE
GREEN TIE
FLOW
SERVO
BOOM ONE
RUN/HOLD
BRN
RED
ORG
YEL
GRN
BLU
VIO
GRY
WHT
BLK
A
B
C
D
E
F
G
H
J
K
10-PIN METRI-PACK TOWER
A
B
C
D
E
F
G
H
J
K
10-PIN METRI-PACK SHROUD
A
B
C
A
B
C
3-PIN
M/P 150
TOWER
LOCAL ACCESS RUN/HOLD CONNECTOR
BROWN TIE
RED TIE
GRAY TIE
GRAY TIE
MT 3405 FTW CONSOLE
3-PIN
M/P 150
SHROUD
BRN
RED
ORG
YEL
GRN
BLU
VIO
GRY
WHT
BLK
A
B
C
D
E
F
G
H
J
K
A
B
C
D
E
F
G
H
J
K
A
B
C
D
E
F
G
H
J
K
10-PIN METRI-PACK TOWER
10-PIN METRI-PACK SHROUD
RED
WHT
BLK
RED
WHT
BLK
RED
BLK
RED
BLK
3-PIN
M/P 150
SHROUD
A
B
C
A
B
C
A
B
C
A
B
C
A
B
C
A
B
C
3-PIN
M/P 150
SHROUD
3-PIN
M/P 150
TOWER
3-PIN
M/P 150
TOWER
3-PIN
W/P 150
TOWER
3-PIN
W/P 150
SHROUD
2-PIN
M/P 150
SHROUD
2-PIN
M/P 150
TOWER
A
B
A
B
RED
WHT
BLK
RED
WHT
BLK
RED
WHT
BLK
RED
BLK
A
B
C
3-PIN
W/P 150
SHROUD
FEMALE .250 QD
FEMALE .250 QD
Installation (cont)
Remote Run/Hold
1/8”to 3/8 “ (6 mm to 13 mm)
space when equipment is
down and operating
Sensor Cable
(black body)
Magnet
South
North
Run Position
Hold
Position
Sensor (Black body)
1/8” to 3/8”
(6 mm to 13 mm)
when wheels are up
Magnet
South
North
Run
Position Hold
Position
Sensor
(Black body)
Magnet
North
South
Rockshaft Control Lever Mounting

16
MT-3405 FTW Console Functions
The MT-3405 FTW features a large, easy-to-read liquid crystal display, lighted Brite-Knob™rotary dial
and lighted panel for night use.
TOTAL AREA: Keeps a running count of the total acres
(hectares) worked. May be reset.
SPEED: Displays ground speed in miles per hour (kilometers
per hour).
AREA/HOUR: Displays
current work rate.
APPLICATION RATE:
Displays gallons (liters)
of liquid applied per
acre (hectare).
TEST SPEED: Used in calibration mode to simulate ground
speed for pre-field checkout.
ADJUST RATE:Used in calibration mode to enter an amount
of change for on-the-go adjustments to the target rate.
TARGET RATE: Used in calibration mode to enter the target
application rate (GPA/LPH).
SUB AREA: Counts acres (hectares) worked. Can be used to
measure individual fields or to perform periodic checks. May
be reset.
DISTANCE: Displays
distance traveled in
feet (meters). May be
reset.
FLOW RATE:
Displays number of
gallons (liters) of liquid
applied per minute.
WIDTH: Used in calibration mode to enter the working
width of your sprayer booms or other equipment.
TOTAL FLOW:
Displays total number
of gallons (liters)
applied. May be
reset.
CIRC: Used in calibration mode to enter the circumference of
the wheel that is equipped with the magnetic speed sensor.
Also used to calibrate Trak-Star or radar speed sensors.
MIN FLOW: Used in the calibration mode to enter the
minimum flow rate (GPM/LPM) of the spray boom.
FLOW CAL: Used in calibration mode to enter the calibration
value assigned to your flowmeter (see flowmeter tag.)
AUTO/MAN: Key which
changes operation from
automatic to manual
control mode.
CAL: This key is used to
enter and exit the
calibration mode.
Key Functions:
PROGRAM KEYS: Used
to calibrate the system.
• RESET clears the
counters when held for
three seconds and not in
CAL.
• The “+” key increases
the figure displayed in
the readout, while “-”
decreases it when in CAL.
IMPORTANT: To reset the Distance, Total Flow or Area
counters, turn the BriteKnob™rotary dial to the appropriate
item, place the system in HOLD and depress “RESET” key for
approximately three seconds.
BOOM SELECT: Used in calibration mode to select an active
boom for calibrating boom width.
WARNING LIGHT: Indicates over or
under application of plus or minus
10% from the Target Rate. Also lit
when in CAL.
Calibration Positions
CAL
AUTO
MAN
RESET

17
The MT-3405 FTW is capable of displaying information in
American English or standard Metric measurement.
• To activate the English mode, turn power OFF and place
the rotary switch at “TOTAL AREA.” Hold down both the
“CAL” and “-” keys and turn power ON. See Illustration
14. The console will display English measurements. Once
powered up, release the two keys. To “lock-in” English
mode you must enter calibration. Press and hold the
CAL key until “CAL” lights on the display. The console
is now in calibration and English mode is locked-in. Exit
CAL by pressing and holding the “CAL” key until CAL
disappears from the display (approximately 3 seconds).
You must be in HOLD to enter Cal.
• To activate the Metric mode, turn power OFF and place
the rotary switch at “SUB AREA.” Hold down both the
“CAL” and “-” keys and turn power ON. See Illustration
14. The console will display Metric measurements. Once
powered up, release the two keys. To “lock-in” Metric
mode you must enter calibration. Press and hold the
CAL key until “CAL” lights on the display. The console
is now in calibration and Metric mode is locked-in. Exit
CAL by pressing and holding the “CAL” key until CAL
disappears from the display (approximately 3 seconds).
You must be in HOLD to enter Cal.
Entering Calibration
In all calibration operations:
1. Place the console in HOLD.
2. Press and hold the “CAL” key for three seconds to
select the calibration mode. The console dis-
play will read “CAL”, and the red warning light will
turn on.
3. Turn the rotary dial to the desired “CAL” position. Then
use the “+” and “-” keys to adjust the displayed value
up or down as needed. Adjust ALL necessary values.
See Illustration 15.
4. Hold the “CAL” key again for three seconds to exit
calibration. “CAL” will disappear from the display.
NOTE: The display will flash alternately between
distance and wheel circumference when in the CIRC posi-
tion, or total flow and flowmeter calibration when in
the FLOW CAL position. When “+” or “-” is pressed, the
display will “hold” the item that was displayed when that
key was pressed. The display will resume alternations
after 64 seconds of no key being depressed. Please refer
to “Entering Calibration Values,” “DISTANCE/ CIRC” or
“TOTAL FLOW/FLOW CAL” for details.
NOTE: In metric, the width will have a decimal point, in
English there is no decimal point. Also, changing from
English to Metric mode may change or alter any previously
entered calibration values. After switching measurement
modes, confirm that all calibration values are correct.
Press to enter or exit
calibration mode.
Press to increase or
decrease values.
Red warning light will
be lit when in CAL.
WIDTHBOOM
SELECT
TEST
SPEED
ADJUST
RATE
TARGET
RATE
CIRC
MIN
FLOW
FLOW
CAL
SPEED DISTANCE
FLOW
RATE
TOTAL AREA
APP. RATE TOTAL FLOW
SUB AREA
ON
OFF
ON
OFF
12345
B O O M S
RUN
HOLD
AREA
HOUR
CAL
AUTO
MAN RESET
MT-3405 ™F
AUTOMATIC RATE CONTROLLER
MANAUTO
CALHOLD
V 1 2 3 4 5
Illustration 14
Illustration 15
WIDTHBOOM
SELECT
TEST
SPEED
ADJUST
RATE
TARGET
RATE
CIRC
MIN
FLOW
FLOW
CAL
SPEED DISTANCE
FLOW
RATE
TOTAL AREA
APP. RATE TOTAL FLOW
SUB AREA
ON
OFF
ON
OFF
12345
B O O M S
RUN
HOLD
AREA
HOUR
CAL
AUTO
MAN RESET
MT-3405 ™F
AUTOMATIC RATE CONTROLLER
MANAUTO
CALHOLD
V 1 2 3 4 5
CAL
Calibration
English or Metric?

18
To enter or change any of the system’s calibration values,
you must enter calibration mode. To enter calibration mode,
STOP the vehicle, place the run/hold switch on the front
panel in HOLD and press and hold the CAL button until “CAL”
lights up (approximately three seconds). (NOTE: Calibration
may be entered while moving, but it is not recommend-
ed to attempt calibration while the vehicle is moving).
The console will remain in calibration mode, with the RED
warning light illuminated until you exit calibration or turn
power OFF.
Once in calibration mode, you may change any one, all or
none of the values, in any order.* To select a calibration
position, simply turn the rotary selector to the desired
position. Calibration positions are identified with white
lettering inside boxes that are outlined in GREEN, on each
side of the rotary selector. All values are entered and
adjusted using the “+” and “-” buttons on the front panel.
*Test speed must be last.
TARGET RATE: Enter the value for the
desired target application rate in gallons per
acre (liters per hectare). This is the applica-
tion rate that the control console will lock
onto when operating in
AUTO.
ADJUST RATE: Enter the value for the desired amount
of change in gallons per acre (liters per
hectare) to be used for making on-the-go
rate adjustments when
operating in AUTO. For
example, if a value “1.0” is
entered, you will be able
to increase and decrease your application rate in one-gallon
(liter) increments during operation in AUTO. To disable this
feature, simply enter “.0” for a value.
TEST SPEED: Enter the value to be used for simulating
speed for performing Pre-Field System Checkout. The
console will use this
speed for simulating
spraying operations. The
test speed value is only
used while in calibration mode. Once CAL is
exited, the Test Speed value is reset to zero.
DO NOT ENTER A TEST SPEED UNTIL ALL OTHER VALUES
ARE PROPERLY ADJUSTED. Please refer to Pre-Field System
Checkout for details.
BOOM SEL: This position is used to select the boom
section to be calibrated. With the rotary switch in this posi-
tion, the display will show
the active boom section
number. Use the “+” and
“-” buttons to select the
boom section to be calibrated. Once the
desired boom section has been selected, turn
the rotary selector to width to enter the effec-
tive working width for that boom section.
Repeat this procedure for each boom section.
Setting Individual Boom Width
In order to accurately measure the number of gallons (liters)
applied per acre (hectare) it is important to determine the
correct “working” width. The “working” width is the width
of ground being affected by any operation. This should be
measured to the nearest inch (thousandth of a meter).
Your “working” width will vary depending on the type of
equipment you are using and the method of application.
For example, if you are broadcast applying chemicals your
“working” width will be the number of nozzles times the
nozzle spacing in inches (mm). For example, if you have 20
nozzles spaced at 20 inches, the working width is 400 inches.
See Illustration 16.
Working Width
WIDTH: Enter the effective working width, in inches (milli-
meters) for the boom sec-
tion currently shown on
the display. Repeat this
procedure for each boom
section. Enter a value of “0” (.000) for any
unused boom sections.
Calibration (cont)
Entering Calibration Values
TARGET
RATE APP. RATE
ADJUST
RATE
AREA
HOUR
TEST
SPEED SPEED
BOOM
SELECT TOTAL AREA
WIDTH
SUB AREA
Illustration 16

19
CIRC: This position is used to calibrate the speed sensor
for accurate speed and distance measurement. When this
position is selected, the display will alternately show, every
three seconds, the wheel
circumference value and
the distance value. The
wheelcircumferencevalue
is the number shown along with “CAL” on the
display. See Illustration 17B. The distance
value is the number shown when “CAL” is not shown on the
display. Either one may be selected to calibrate for speed
and distance measurement. Select by pressing the “+” or “-”
button when the desired value is being displayed.
Working Width
Banding Application Calibration
In banding applications, you will still need to enter the total
width of each boom section so that area counts correctly, but
you must also calculate the percentage of your total width
the band is covering and reduce your target rate to match.
For example, if you are planting with an eight-row planter
with 30-inch spacing, your total working width, regardless
of the width of bands, is 240 inches (8 x 30 inches). Now, for
purposes of this example, you have eight 12” bands. Your
total band coverage is 96 inches (8 x 12 inches). Based on
that, your band is covering 40 percent of your total width
(96 divided by 240). If you want to apply 20 GPA in the
band, enter 8 GPA as your target rate (40 percent of 20 GPA).
See Illustration 17A.
To determine circumference, measure the
distance of one complete wheel revolution
and divide by the number of magnets installed .
Determining Wheel Circumference
For the console to calculate the correct number of acres
(hectares), both the circumference of the sensor-equipped
wheel and the implement width must be entered. Determine
the circumference of the sensor-mounted wheel to the
nearest tenth of an inch (thousandth of a meter) with the
following method:
METHOD
Mark tire with a piece of chalk and measure distance traveled
on the ground for one complete revolution. See Illustration 19.
For accuracy, measure the wheel revolution several times and
take the average. Divide that value by the number of magnets
installed on the wheel hub to get your starting wheel circum-
ference (CIRC) calibration value.
Illustration 17A
Illustration 17B
Illustration 18
Calibration (cont)
Entering Calibration Values (cont)
+
+
+
+
+
+
+
+
+
+
+
+
+
+
=
WIDTHBOOM
SELECT
TEST
SPEED
ADJUST
RATE
TARGET
RATE
CIRC
MIN
FLOW
FLOW
CAL
SPEED DISTANCE
FLOW
RATE
TOTAL AREA
APP. RATE TOTAL FLOW
SUB AREA
ON
OFF
ON
OFF
12345
B O O M S
RUN
HOLD
AREA
HOUR
CAL
AUTO
MAN RESET
MT-3405 ™F
AUTOMATIC RATE CONTROLLER
MANAUTO
CALHOLD
V 1 2 3 4 5
CIRC
DISTANCE

MIN FLOW: The purpose of this calibration parameter is to
prevent the system from applying below the recommended
minimum rate for the nozzles. Enter the minimum flow rate
in gallons per minute (liters per minute) based
on the nozzles being used, for the entire boom
on the sprayer. DO NOT
enter the actual flow rate
of your spray application.
For example, if the mini-
mum flow rate for the nozzle you are using is .22 GPM at their
minimum recommended pressure and your boom has 20
nozzles, enter 4.4 as the MIN FLOW value (.22 x 20 = 4.4). The
system WILL NOT apply at a rate lower than this value when
spraying in AUTO. This value should be checked/changed for
each different nozzle that you use.
APPLICATION NOTE: In certain situations, your ground
speed may be slow enough to result in over application. In
other words, based on ground speed, the actual flow rate
has dropped to the calibrated minimum flow rate.
20
Drive Shaft Speed Sensor Calibration
NOTE: If you have mounted the magnetic speed sensor on
a wheel, skip this step and go on to Fine Tuning Speed/
Distance Calibration Values.
Because of the difference in wheel-to-drive shaft ratios, it is
difficult to determine a calibration value for installation on
a drive shaft by measuring a wheel. You must start with an
estimated calibration value and then fine-tune the calibra-
tion.
1. Place the console in HOLD.
2. Press and hold the “CAL” key for three seconds to
enter the calibration mode. Turn the dial to “CIRC”
position. The display will alternate between the wheel
circumference (CIRC) and distance values at about three-
second intervals. (When the word “CAL” appears, the
number displayed is the wheel circumference (CIRC)
value. When “CAL” does not appear, this is the distance
value.)
3. When the display shows wheel circumference (“CAL” is
displayed) , use the “+” or “-” key to adjust the displayed
value to any number between 10 and 15 (255mm to
380mm). When the number shown on the display
matches the desired value, you have arrived at the
estimated calibration value. Exit “CAL” by pressing and
holding the “CAL” key for three seconds.
NOTE: If you let go of the “+” and “-” keys while you are
adjusting the CIRC value, the console will wait to make
sure you are finished. After 64 seconds, the display will
start alternating between the wheel circumference (CIRC)
and distance values again. Make sure you know which
value you are adjusting.
NOTE: For fine-tuning the wheel circumference (CIRC) value,
turn to page 26.
Calibration (cont)
Entering Calibration Values (cont)
MIN
FLOW
FLOW
RATE
Table of contents
Other micro-trak Controllers manuals
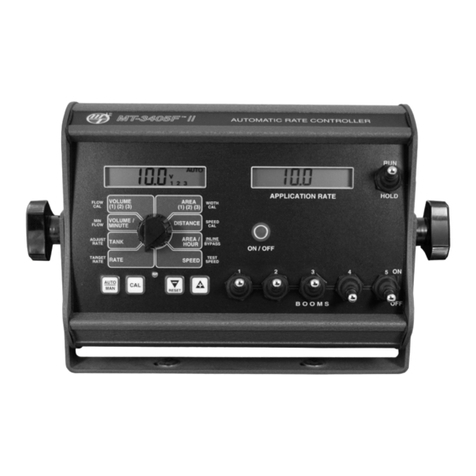
micro-trak
micro-trak MT-3405F II User manual
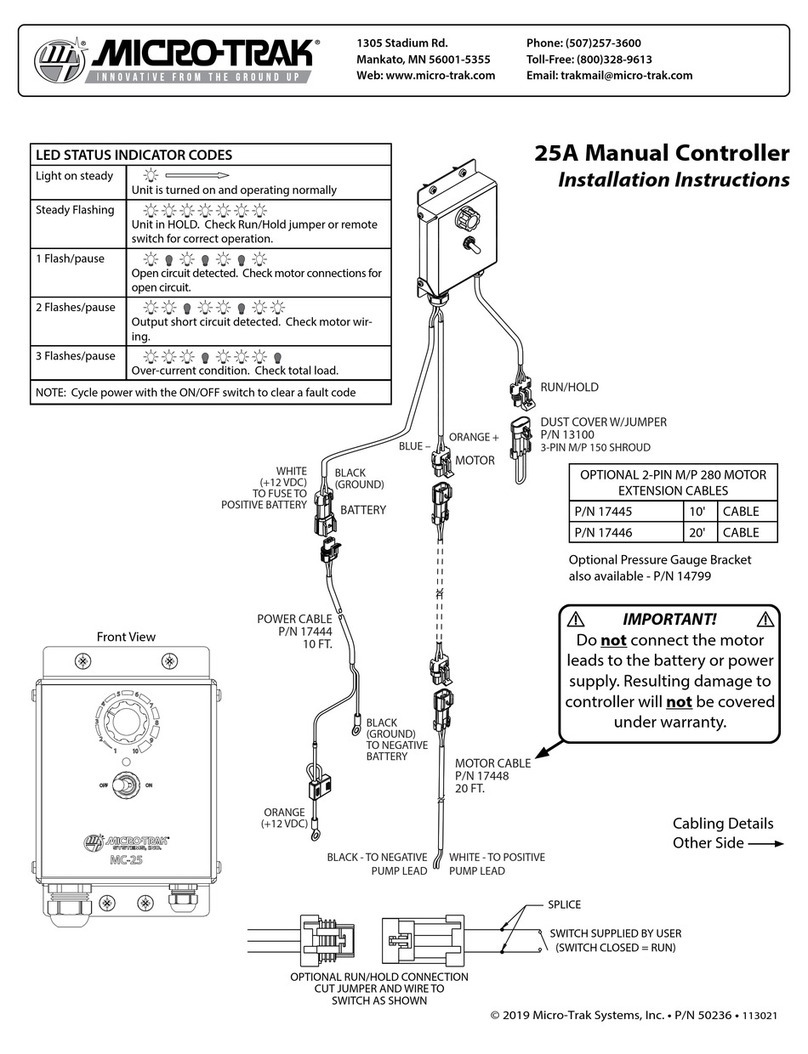
micro-trak
micro-trak 17445 User manual
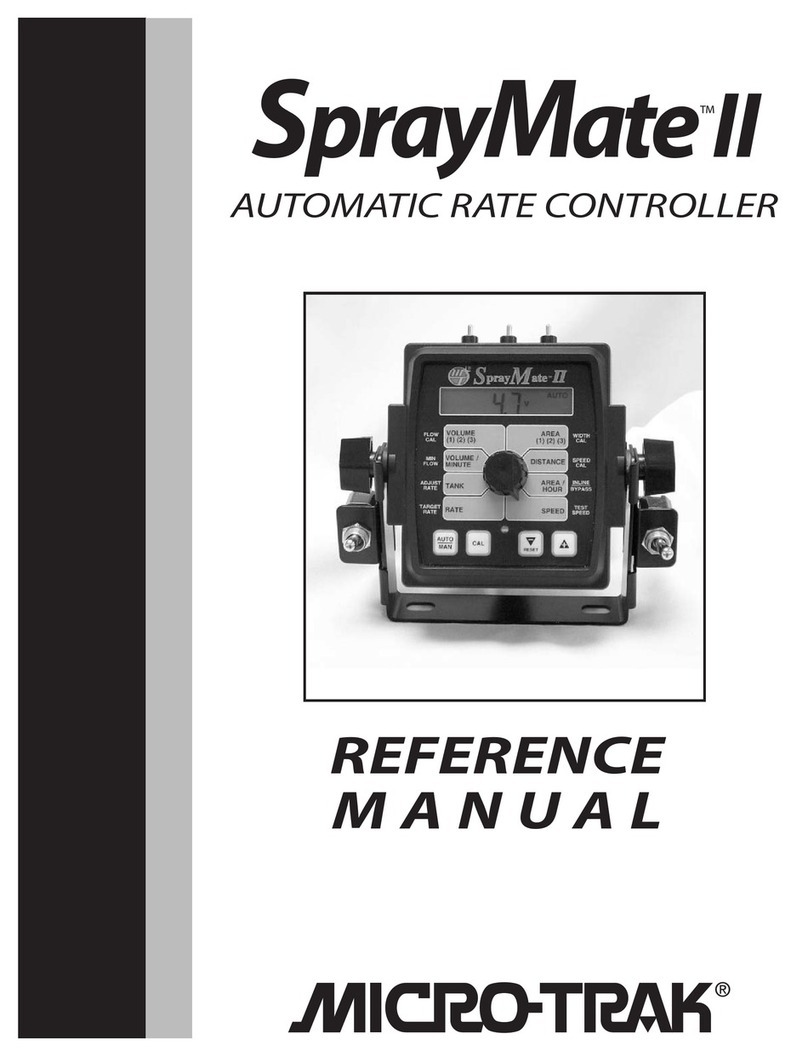
micro-trak
micro-trak SprayMate II User manual
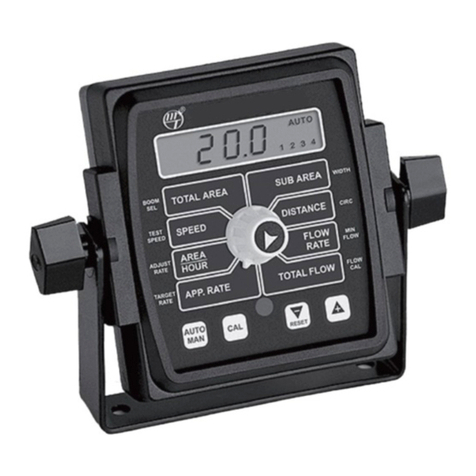
micro-trak
micro-trak MT-2405 FTW User manual
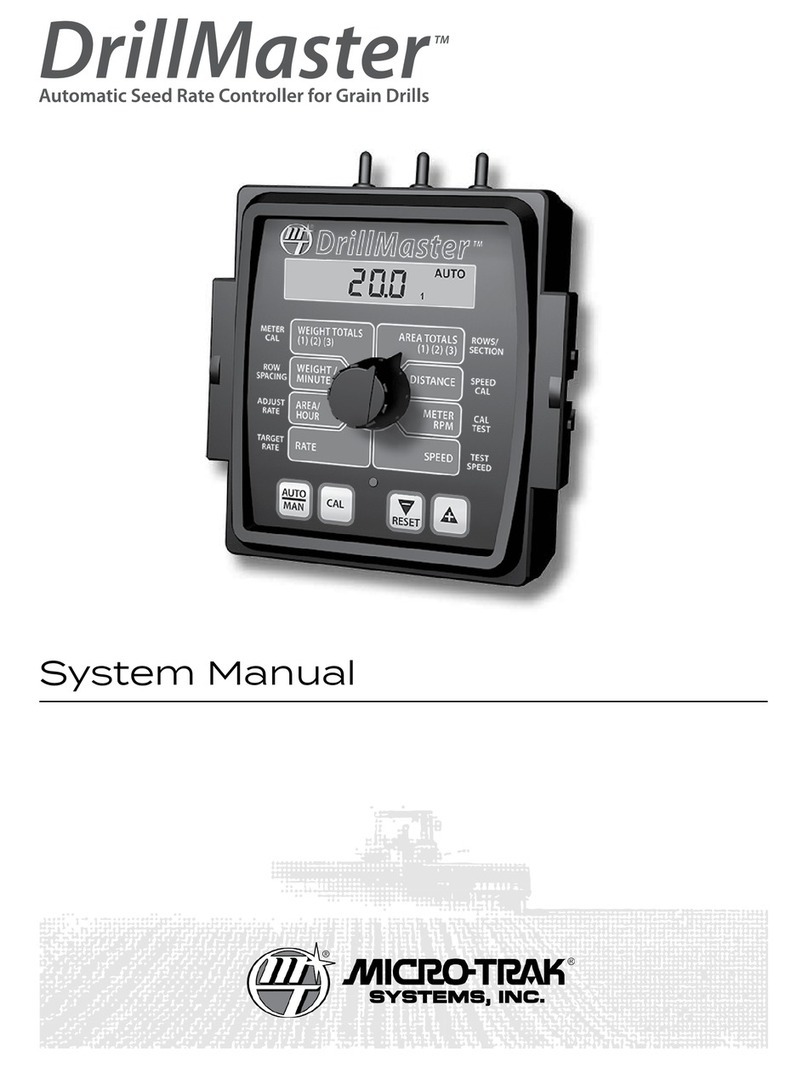
micro-trak
micro-trak DrillMaster User guide
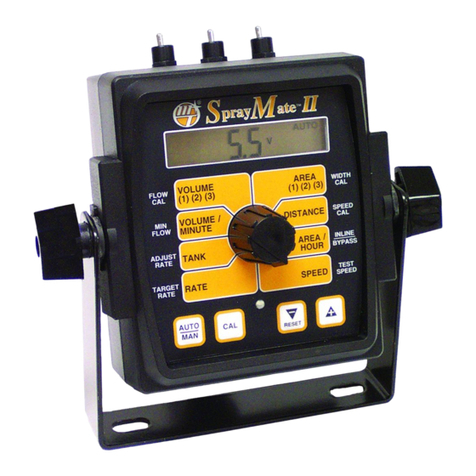
micro-trak
micro-trak SprayMate II User manual
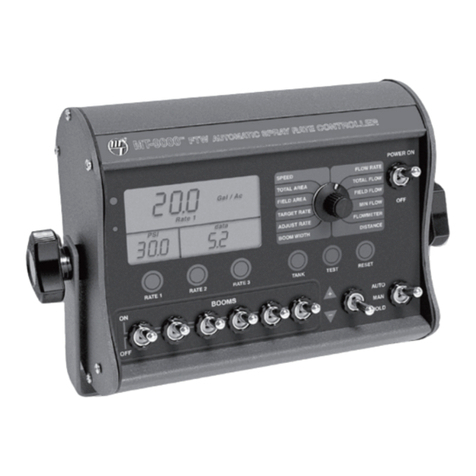
micro-trak
micro-trak MT-9000 FTW User manual
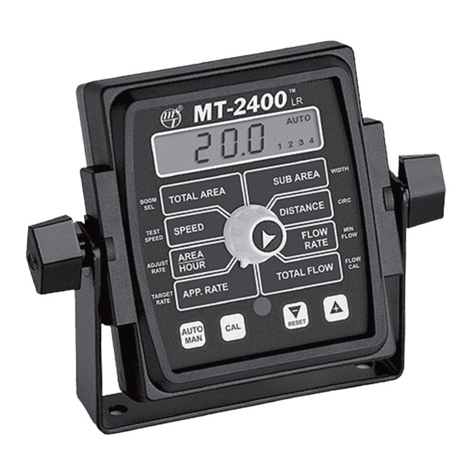
micro-trak
micro-trak MT-2400 LR User manual
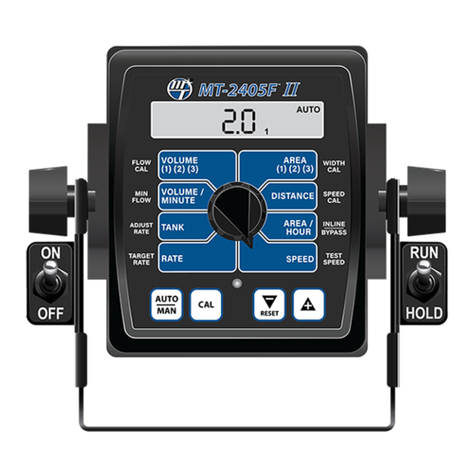
micro-trak
micro-trak MT-2405FTW II User manual
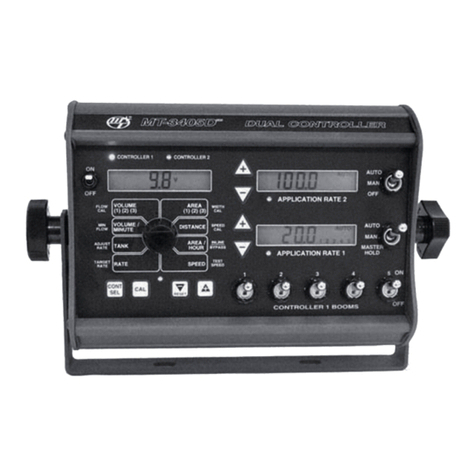
micro-trak
micro-trak DUAL CONTROL MT-3405D User manual