NIVELCO NIVOPOINT User manual

3/1
mra105en2112h
Thank you for choosing a NIVELCO instrument.
We are convinced that you will be satisfied with our product!
1. INTRODUCTION
The interaction of the magnetic float and the reed relays (incorporated in the protection tube) is the basis of the
NIVOPOINT magnetic float level switch series operation. They are suitable for level indication of normal and
explosive liquids and can be used for level control tasks. The protecting tube contains a max. of 5 relays. Parts
of the instrument are a probe tube with magnetic float and a housing containing the connection terminal.
The magnetic float moves alongside the protection tube tracking the level of the liquid and activating the reed
relays. As the float passes a relay it changes the output state of the relay which retains this state latching until
the level decreases and the float moves again along the respective relay to switch its state back.
2. TECHNICAL DATA
2.1. GENERAL DATA
TYPE MR- MP- MR--7Ex MR--8Ex
Insertion length 0.25…3 m (0.85…10 ft)
Material of wetted parts
Material of probe rod Stainless steel
(DIN 1.4571 / BS 316Ti) PFA / PP coated Stainless steel
(DIN 1.4571 / BS 316Ti)
Material of float 1.4404 PVDF, PP 1.4404
Float sizes (standard
included)*
53.5 × 60 mm
(2.1" × 2.36")
76 × 87 mm
(3" × 3.42")
53.5 × 60 mm
(2.1" × 2.36")
Max. process pressure
2.5 MPa (25 bar)
[363 psig]
at +20 C (68 F)
0.6 MPa (6 bar)
[88 psig]
at +20 C (68 F)
2.5 MPa (25 bar)
[363 psig]
at +20 C (68 F)
Medium-density
(Specific gravity) min. 0.8 kg/dm3 min. 0.7 kg/dm3min. 0.8 kg/dm3
Medium temperature –40…+150 °C
(–40…+302 °F)
–40…+80 °C
(–40…+176 °F) See: Temperature limit data for Ex
approved models table
Ambient temperature –40…+95 °C
(–40…+203 °F)
Output 1…5 × reed-switches, connecting one side of each, NO/NC
Switching rate 120 W / VA, 250 V AC/DC, 3 A /reed relay, summary max. 9 A
Switching differential <10 mm (0.4")
Distance between reed-
switches min. 110 mm (4.35")
Electrical connection
M20x1.5 6…12 for cables
(0.25…0.5")
M20x1.5
7…12 for
cables
(0.28…0.47")
without cable gland
**
terminal, wire cross section: 0.5…2.5 mm2(AWG20…AWG14)
Process connection
1", 1½", 2" BSP
1", 1½", 2" NPT
1", 1½", 2½", 3", 4" TriClamp
PP flange
DN80, DN100
1", 1½", 2" BSP
1", 1½", 2" NPT
1", 1½", 2½", 3", 4" TriClamp
Sealing material Klingerit for BSP — Klingerit for BSP
Electrical protection Class I, Protecting cable 4 mm2(AWG25)
Ingress protection IP67 (as per MSZ EN 60529:2015)
Dimension of the housing 116 × 80 × 65 mm
(4.56 × 3.15 × 2.56")
124 × 80 × 65 mm
(4.9 × 3.15 × 2.56")
Mass 0.4 kg + 0.3 kg/m (0.88 lb + 0.2 lb/ft) 0.45 kg + 0.3 kg/m (1 lb + 0.2 lb/ft)
* For details of non-standard floats, see 2.6. Float selection
** Note: the device must be installed with Ex d IIC certified explosion-proof cable gland.
2.3. ACCESSORIES
User’s Manual,
Warrant Card,
EU declaration of Conformity,
1 × Gasket (for threaded versions)
2.2. EXPLOSION PROTECTION,EX MARKINGS,EX LIMIT DATA
2.2.1 ATEX CERTIFICATE NO.: EXNB 17 ATEX 0003 X/1 2.2.2 TEMPERATURE LIMIT DATA FOR EX APPROVED MODELS
TYPE With cable gland
MR--7Ex
Without cable gland
MR--8Ex
Class T6 T5 T4 T3
Ex marking (ATEX) II 1/2 G Ex db IIC T6...T3 Ga/Gb Max. ambient temperature
from –40 °C (–40 °F)
+80 °C
(176 °F)
+95 °C
(203 °F)
+95 °C
(203 °F)
+95 °C
(203 °F)
Reference document
number mra1053m0600h_12 Max. medium temperature
from –40 °C (–40 °F)
+80 °C
(176 °F)
+95 °C
(203 °F)
+130 °C
(266 °F)
+150 °C
(302 °F)

3/2
mra105en2112h
2.4. ORDER CODE (NOT ALL COMBINATIONS POSSIBLE!)
NIVOPOINT M R – – *
PROCESS CONNECTION CODE
SWITCHING
POINTS CODE
PROBE
LENGTH** CODE
PROBE
LENGTH** CODE
CERTIFICATE CODE
1" BSP A 1 × NO/NC 1
0 m 0 0 m 0 Standard 3
2" BSP C 2 × NO/NC 2
1 m 1 0.1 m 1 Ex 7
1" NPT D 3 × NO/NC 3
2 m 2 : : Ex without cable gland 8
2" NPT G 4 × NO/NC 4
3 m 3 0.8 m 8
1½" BSP B 5 × NO/NC 5
4 m 4 0.9 m 9
1½" NPT E
1" TriClamp F
1½" TriClamp T
2½" TriClamp O Notes:
3" TriClamp P *The order code of an Ex-version should end in ’Ex’
4" TriClamp R ** For Ex version, max. probe length up to 3 m (9.84 ft)!
NIVOPOINT M P – –
PROCESS CONNECTION CODE
SWITCHING
POINTS CODE
PROBE
LENGTH CODE
PROBE
LENGTH CODE
FLOAT /CERTIFICATE CODE
DIN DN80, PN16 P 1 × NO/NC 1
0 m 0 0 m 0 76 PVDF or PP/ 3
DIN DN100, PN16 R 2 × NO/NC 2
1 m 1 0.1 m 1 standard
3 × NO/NC 3
2 m 2 : :
4 × NO/NC 4
3 m 3 0.8 m 8
5 × NO/NC 5
0.9 m 9
Notes: The type of float should be specified in the text part of the order.
2.5. DIMENSIONS
STANDARD VERSION MR- STANDARD VERSION MR- TERMINAL BOX
EX VERSION MR--7M EX VERSION MR--8M STANDARD VERSION MP-

3/3
mra105en2112h
2.6. FLOAT SELECTION
TYPE MRC-106-7M-900-00 MRC-105-7M-900-00 MRC-105-7M-600-00 MRC-105-7M-700-00 MRC-105-7M-800-00 MPP-105-3M-200-00 MPP-105-3M-900-00
Dimensions
Standard type ■■■■――
Plastic co. type ――――■■
Ex type ■■■■――
Medium-density
(Specific gravity)
min.
0.45 kg/dm30.55 kg/dm30.8 kg/dm30.55 kg/dm30.4 kg/dm30.7 kg/dm30.4 kg/dm3
Material Titanium 1.4404 1.4435 1.4401 PVDF PP
Med. pressure 2 MPa (20 bar)
[290 psi]
2.5 MPa (25 bar)
[363 psi]
0.6 MPa (6 bar)
[87 psi]
0.3 MPa (3 bar)
[43.5 psi]
3. INSTALLATION
For mounting the unit 1", 1½", 2" BSP or NPT threads or 1", 1½", 2½", 3", 4"
TriClamp can be used. Minimal gap diameter for the float is 55 mm
(2.16").
Use the M20×1.5 cable gland for electrical connection.
If a protection tube is used the minimum tube diameter should be 75 mm
(2.95") (for insertion length < 1.5 m and 95 mm (3.74") for insertion
length > 1.5m). When using a 96 mm (3.8") float the tube diameter should
be min. 130 mm (5.1").
WARNING!
Do not loosen the gland nut that ensures a ±25 mm (±0.98") adjustment of the
sensors in a pressurized container!
The unit should be mounted in vertical position via its process connection and
handled with care to avoid any damage or bend of the protection tube during
transportation or installation!
4. SET UP, ADJUSTMENT
After screwing in and before tightening the sliding sleeve the direction of the
cable gland and the position of the reed-relay set can be adjusted. an open-end
wrench should be used when loosening or screwing tight the sliding sleeve!
The position of the reed-relay set can be vertically adjusted by a max. of
±25 mm (±0.98").
5. WIRING
Depending on the grounding system either the inner or the outer grounding
terminal should be connected to the EP network.
Standard version
Remove the cover. Feed the electrical cables through the cable gland and
connect them in accordance with the sketch on the cover where the (NO/NC)
states of the relays are marked. The terminal of the lowest switch point has to
be number 1.
“C” is common terminal.
The cross section of the connecting cable has to be between 0.5 and 2.5 mm2
(AWG20…AWG14). After connecting, secure the cable with the cable gland,
check and screw the cover back on with at least 25 Nm of torque.
Ex version
Remove the safety clamp and screw the cover off. Feed the electrical cables
through the cable gland and connect them in accordance with the sketch on the
cover where the (NO/NC) states of the relays are marked.
After connecting, secure the cable with the cable gland, check and screw the
cover back on with at least 25 Nm of torque. Fasten the safety clamp by setting
it into one of the notches of the cover.
6. SPECIAL CONDITIONS OF SAFE USE
Make sure the installation is complete with no visible defects before turning
on the device.
The device may only be used within the limitations specified in the technical
specifications.
The installation of the device must be carried out in a way that the IP20 ingress
protection is maintained throughout the installation!
The thermal resistance of the connection cable insulation must correspond to
the permissible ambient temperature at the place of application.
The metal housing of the device must be connected to the EP (equipotential)
network!
WARNING!
Use exclusively Ex d IIC cable entry for devices with “Ex d” flameproof
protection!
The plastic protective cap should be removed before installing NIVOPOINT
MR☐☐☐☐8Ex, and the device must be equipped with a properly
assembled and sealed and cable gland with “Ex d” protection type.
The housing and measuring tube must be protected against mechanical
impact! The location and method of installation must be such that they are
protected against external mechanical influences during operation!
The aluminum content of the metal die-cast housing exceeds the threshold;
which require protection of the equipment against any possible sources of
spark or ignition resulted by impact or friction!
Devices with order code MR☐☐☐☐7Ex may only be installed with wiring
and cable ducts that complies with MSZ EN 60079-14: 2014 standard
10.6.2. b!
7. MAINTENANCE, REPAIR
The unit does not require regular maintenance. In some instances, however,
the probe may need occasional cleaning to remove surface deposits. This
must be carried out gently, without harming the probe.
All repairs will be carried out at the manufacturer’s premises.
Before returning the device for repairs, it must be cleaned carefully, the parts
in contact with the medium that might contain harmful substances must be
decontaminated. Our official form (Returned Equipment Handling Form) must
be enclosed. Download it from our website www.nivelco.com. The device must
be sent with a declaration of decontamination. Please provide a statement in
the declaration that the decontamination process is completed, the device is
clean and free from harmful materials, and there are no hazardous substances
on it.
8. STORAGE CONDITIONS
Ambient temperature: –20… +60 °C (–4…+140 °F)
mra105en2112h
April 2021.
NIVELCO reserves the right to change technical data without notice!
Other NIVELCO Switch manuals
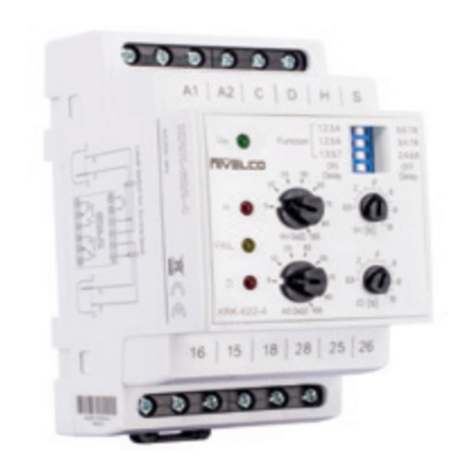
NIVELCO
NIVELCO NIVOCONT K User manual
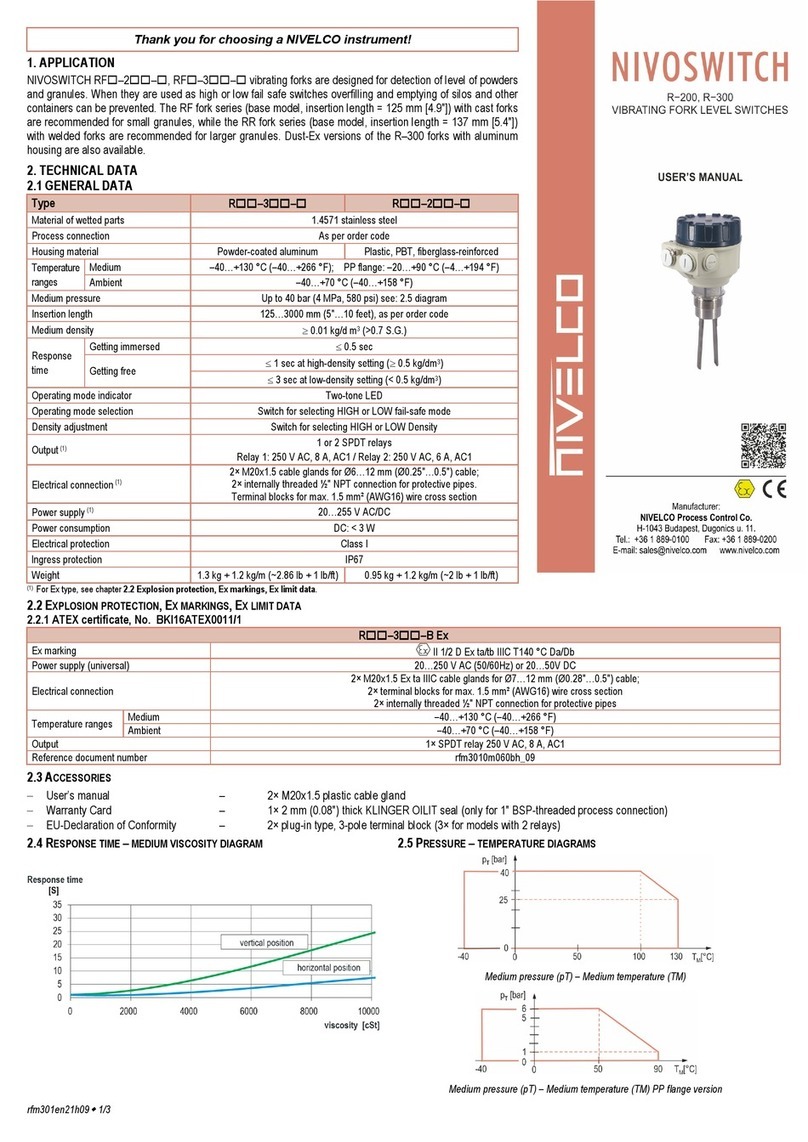
NIVELCO
NIVELCO NIVOSWITCH R-2 Series User manual

NIVELCO
NIVELCO NIVOSWITCH R-400 Series User manual
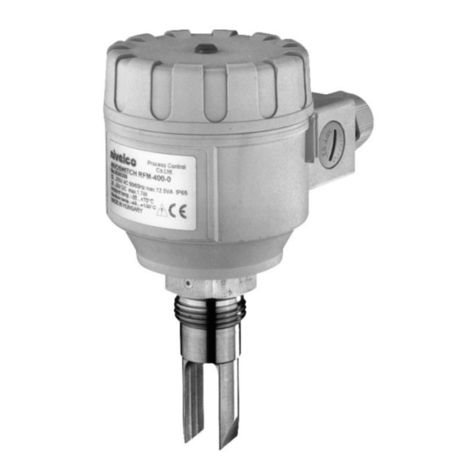
NIVELCO
NIVELCO NIVOSWITCH R-400 Series User manual
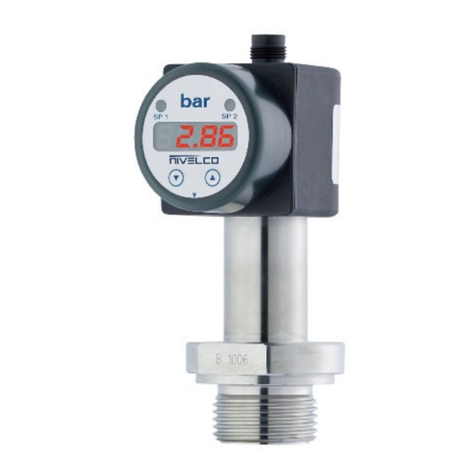
NIVELCO
NIVELCO NIPRESS DK-300 Assembly instructions
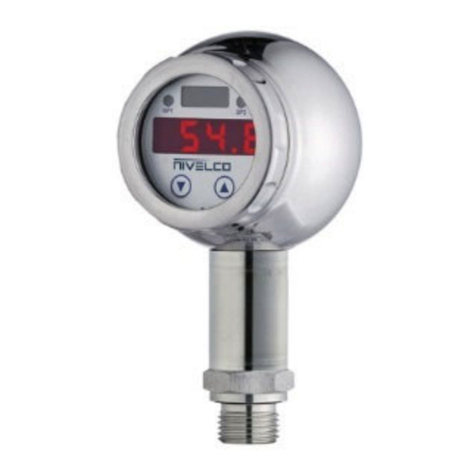
NIVELCO
NIVELCO NIPRESS DK-500 Assembly instructions
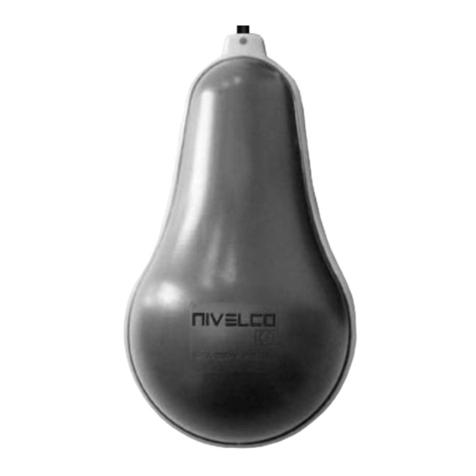
NIVELCO
NIVELCO NIVOFLOAT NW-100 Series User manual

NIVELCO
NIVELCO NIVOMAG MK-21 Series User manual
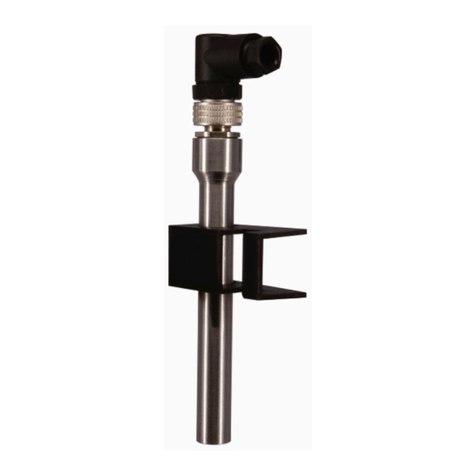
NIVELCO
NIVELCO NIVOFLIP MAK-200 User manual

NIVELCO
NIVELCO NIVOSWITCH R-400 User manual