Oce CS6407 User manual

Océ Technologies B.V.
Océ CS640
7
Océ CS6407

2
Select the language of messages used for LCD.
#LANGUAGE
>ENGLISH
<Parameter (choice input)>
ENGLISH
The LCD message is displayed in English.
FRENCH
The LCD message is displayed in French.
ITALIAN
The LCD message is displayed in Italian.
GERMAN
The LCD message is displayed in German.
SPANISH
The LCD message is displayed in Spanish.
PORTUGUESE
The LCD message is displayed in Portuguese.
Table of Contents
Appearance / Name and function of each part 3
Printer front (takeup side) 3
Printer rear (supply side) 4
Printer heater unit 5
Operation panel 5
Media installation and removal ……………… 7
Roll media installation procedure 7
Procedure to install general roll media to the take-up reel
unit 11
Procedure to remove media from the printer 13
Setting media advance correction values 15
Ink pack installation and replacement ……… 16
Ink pack installation/replacement procedure 16
Waste ink bottle installation and replacement 17
Procedure when the waste ink bottle becomes full 17
Procedure when no waste ink bottle is installed 17
Replacing the wiper blade …………………… 18
Correcting the edge sensor position ………… 19
Adjusting tension bar length ………………… 20
Print head cleaning …………………………… 20
Feeding the media [Feed] …………………… 21
Backfeeding the media [Backfeed] …………… 22
How to use the pressure control knob ……… 22
How to use the head up/down mechanism … 23
How to use media edge guards ……………… 23
Periodic maintenance ………………………… 24
Menu Tree ……………………………………… 28
Setting items …………………………………… 29
Troubleshooting ……………………………… 32
When an error message is displayed ………… 33
Service call errors 33
Operator call errors 33
When a warning message is displayed ……… 34
Ç
PRINTER SETUP
È
Å
ADJUST HEATER
Æ
Océ CS6407
Quick Reference Guide
ENGLISH

3
ENGLISH
Appearance / Name and function of each part
This section shows the printer appearance and describes the name and function of each component.
Printer front (takeup side)
Unlock
(OFF)
Lock
(ON)
>
@
Operation panel Provided with LEDS and LCD to display printer status and keys to set functions.
Ink box cover An inlet to set ink (Note: Displayed as “INK COVER” on the LCD.)
Tension bar guide The guide of bar to apply tension to the media
Caster Unlocked to move the printer and locked to immobilize it.
Pressure control knob A knob to switch the media press force
Front cover Must be closed during printing.
Waste ink bottle unit A unit to contain a waste ink bottle
Cap cover Opened when cleaning the capping unit or replacing the wiper blade.
Wipe cover Opened when maintaining the print head (replacement/height adjustment).
Take-up direction switch A switch to select media takeup direction
Media feed switch
Take-up reel switch
A switch to feed media automatically
A switch to wind media automatically
@Media dryer fan A fan to dry ink after printing.
>Protection bar A bar to protect media surface just after the print.

4
Printer rear (supply side)
[
W
[
SGY
T
V
K
K
K
K
K
K
K
K
K
K
K
K
Q
Q
Q
Q
Q
Q
Q
Q
Q
Q
Q
R
R
R
R
R
R
R
R
R
R
SPrinter power inlet
YPrinter power switch
GHeater power inlet
THeater power switch
VUSB connector Connected to the printer server.
[Subcartridge An auxiliary ink for printing even during replacement of ink
WTake-up reel switch
Media feed switch (P.43)
KPressure control knob (P.55)
QScroller ange (P.40)
RPeel roller (P.43)

5
ENGLISH
Operation panel
The keys, LEDs and LCD are laid on the operation panel of the printer as shown below. In addition, the operation panel is also
equipped with a buzzer function for attention in case an error occurs or an invalid input is entered.
LCD Indicates printer status and menus.
B
Power switch
A
D
C
E
OK
MENU ONLINE
HEATER CANCEL
Printer heater unit
This printer is equipped with three heaters for ink fusing and image quality stabilization.
Media
Head
Supply side
(rear) Takeup side
(front)
LEDs
Indicate printer status with ON, OFF,
and blinking.
Keys
Used for menu operation and other
purposes of the printer.
Buzzer
Preheater (rear)
Preheats media.
Print heater (front)
Penetrates ink into media to fuse the ink.
Afterheater (nishing)
Dries ink to stabilize print quality.
- These three heaters are controlled independently.
The temperature of each heater can be controlled from
the operation panel and the host PC (RIP).
WARNING
-Do not touch these heaters to avoid burn as they
become hot.
B
A

6
Name and function of LCD, LEDs, and keys
No. / Classication
Name Function
LED
AData LED
(Green)
Indicates data reception state.
-Blink: Receiving data from the host computer.
-OFF: No receiving data from the host computer.
BError LED (Orange)
Indicates whether an error has occurred.
-ON: An error has occurred.
-Blink: Warning state.
-OFF: Normal (no error)
CInk LED
(Green)
Indicates whether ink is remaining.
-ON: Ink of all colors is present.
-Blink: Ink near-end (Ink of any color is little.)
-OFF: No ink.
DMedia LED (Green)
Indicates whether media is remaining.
-ON: Media is present (Either roll media or cut-sheet media is
loaded.)
-Blink: Take-up reel unit's operation was suspended.
-OFF:
No media (Neither roll media nor cut-sheet media is loaded.)
EONLINE LED (Green)
Indicates online or oine state of the printer.
-ON: Online
-Blink: Online pause mode
-OFF: Oine
Key
ONLINE key Used to select online or oine of the printer.
MENU key Used for auxiliary parameter input (switching menu layer display).
CANCEL key Used to cancel entered parameters.
OK key Used to x the selected menu and parameters.
HEATER key Used to enter heater control menu.
key
Used to select a menu group and switch menu (selection,
increment/decrement of value)
key
key
key
Power switch Power switch Used to turn on or o the power of the printer.
LCD LCD
Displays messages and status of the printer in alphanumeric characters,
KANA characters and symbols (20 characters × 2 lines). The menu
adopts a layered structure. Each menu can be accessed with the S, T,
W, and Xkeys.
Buzzer Buzzer Sounds when an error occurs or when invalid key operation is made or
when the print head is not capped in the daily maintenance.

7
ENGLISH
Media installation and removal
1
Put the media on the table.
If you want to use a dolly, contact us. We have a
recommend product.
2
Insert the scroller shafts into the paper tube.
Scroller shaft
Roll spacer
Note
-Adjust the position of the roller shaft so that the roll
spacer is positioned at the center of the media roll.
3
Install the scroller ange into each end of the
media roll.
(1) Insert the scroller ange into each edge of the paper
tube.
Scroller ange
Roll media installation procedure
The installation method of the scroller ange varies with the type, weight and take-up direction of the media. See the tables
below to install the scroller ange correctly.
General media Vinyl chloride media
Flange spacer Required Not required
(2) Insert the ange spacer between the scroller ange
and the media roll.
Flange spacer
(3) Push the scroller ange until it stops and turn the handle
clockwise until the ange is xed to the paper tube.
Scroller ange Handle
(4) Remove the ange spacers.

8
4
Attach the scroller shaft clip.
(1) Slip the scroller shaft clip on the scroller shaft.
(2) Turn the knob to x the scroller shaft.
Knob
Scroller shaft clip
r
oll
l
l
ll
2
1
5
Install the media roll tted with the scroller
anges into the printer roller groove properly.
gy
Printer rear (supply side)
P
rinter rea
Flange support
Scroller ange
6
Cap side Wiper side
Install the ange holders.
7
Remove the protection bar and open the front
cover. Front cover
Protection bar
8
Move the media edge guards to each side so
that they are not under the media.
Media edge guards
9
Rotate the pressure control knob clockwise to
raise the pressure roller.
Takeup side Supply side
or
Pressure control knobs
10
Insert the media end into the paper feeder
while smoothing out the media by hand to
prevent wrinkles.
Printer rear
Paper feeder
If it is hard to insert the media end into the paper
feeder due to a curl of the media, interpose an interleaf
and insert the media end under the interleaf as shown
in the gure.
-Up curl - Down curl

9
ENGLISH
11
Feed the media until the media end almost
reaches the oor.
In this state, smooth out the media toward the both
sides on the platen to make the media center tense.
Platen
Note
-If the media is set with a distortion or wrinkles, this may cause a
media jam or skew.
12
Feed back the media to the top of the front
paper guide. Front paper guide
Feed back the media while pressing the center of
the media gently at the supply side.
-Step 12 is important to set the media properly.
13
Takeup side Supply side
or
Pressure control knobs
Rotate the pressure control knob
counterclockwise to lower the pressure roller.
14
Set the media edge guards and close the front
cover.
CHECK EDGE GUARD
*OK?
Check that the media edge guards are not under the
media or thick media is not caught by inserting it
forcibly. After conrming visually that the media edge
guards are properly set, press the key.
15
Select roll media or cut-sheet media.
ROLL/SHEET:SHEET
SELECT MEDIA
ROLL/SHEET:ROLL
Either [roll] or [sheet] can be selected with the key
or key.
Here, select [roll] and press the key.
(To return to the media selection, press the CANCEL
key.)
16
Select the type of media.
Select the registered type of media with the and
keys and press the key.
MEDIA:TYPE02
SELECT MEDIA
MEDIA:TYPE02
To register new media
[NEW MEDIA ENTRY] is displayed at the end of the registered
media.
Press the key to enter MEDIA REG MENU.
The media registration procedure is the same as the
registration from the registration menu.
Press the key to return from the media registration menu
to the media type selection menu.
To return to the value before input, press the CANCEL key.
MEDIA:TYPE02
SELECT MEDIA
MEDIA:TYPE02
(The registered media is displayed.)
SELECT MEDIA
NEW MEDIA ENTRY
(Enter the media registration menu.)

10
17
Enter the remaining media.
Enter the remaining roll media loaded on the printer.
SET REMAINING MEDIA
*XXXm
Note
-After installing the media, check whether the media on the
platen has no oat or wrinkles.
18
This sign is displayed when the slack is
insucient.
-In case of use of sheet media, this message is not
displayed.
-If the media slackness is insucient, the next
operation will not be started.
CHECK
SLACKEN MEDIA
19
Press the tension bar to the peel roller’s upper
part. Then create a slack between the platen
and the peel roller, by carrying the tension
bar to the rear side of the peel roller with a
supply-side feed switch.
Switch Tension bar
Tension bar
Adjust the tension bar length and decide whether to
attach a ange or not, depending on the type and
width of the media.
Examples of tension bar combinations
Size used Tension bar length
L 48 inches (123 cm)
L, S 64 inches (164 cm)
L, S, S 80 inches (204 cm)
<General media in TENSION winding mode>
Put a tension bar suitable for the media width.
Usually put a tension bar suitable for the media width with a
few exceptions.
<General media without take-up reel unit>
Put a tension bar which is half the width of the media.
<Vinyl chloride media>
Put an S size tension bar (without a ange) on the center of
the slack.
Peel roller
Scroller ange
Supply-side slack sensor
S
S
r
Slacken o to a level lower than the supply-side slack sensor.
When the slack reaches the sensor detection area, the
operation panel blips.
Note
-Be sure to rotate the panel with the supply-side feed switch.
Do not rotate the peel roller manually, or the printer may be
damaged.
20
Check the media setting.
Press the key.
SET MEDIA
*OK?
PREPARING MEDIA
PLEASE WAIT
Note
-Rewind the printer's media completely at the end of the day. The
PVC media installed and left for a night on the printer may cause
media jam.

11
ENGLISH
Procedure to install general roll media to the take-up reel unit
1
Prepare a paper tube and attach it to the
scroller anges.
(1) Insert a scroller anges into each edge of the paper
tube.
Scroller ange
Paper tube
(2) Insert the ange spacer between the scroller ange
and the media roll.
Note
-When PVC media is used, push the scroller ange until it
stops without inserting the ange spacer.
-The ange spacer should be inserted to the position
indicated by the line B.
Be careful not to deform it by applying too much force.
A
B
(3) Push the scroller ange until it stops and turn the
handle clockwise until the ange is xed to the paper
tube.
Scroller ange
Handle
(4) Remove the ange spacers.
2
Set the take-up direction switch to OFF.
Note
-If the printer processing proceeds to the next step with the take-
up direction switch set to ON, your hand may be caught as the
scroller is not secured.
Take-up direction switch
uOuter take-up
- OFF
vInner take-up
3
Attach the scroller ange by tting it with the
roll groove of the printer.
Scroller ange
Roll groove
Note
-Hook the tension bar to the tension bar hook beforehand.
Tension bar hook
Tension bar
4
Feed the media with the FORM FEED MENU on
the operation panel to an extent where it can
be taken up.
OFF

12
5
Paper tube
Tape
Install the drawn media to the paper tube.
(1) Check the take-up direction, remove the slack of the
media, and then make sure that the media is not
deviated on the supply side and the takeup side.
(2) With tape hold the media straight at the center, and
then at the rest six positions in the direction from the
media center to the media edge.
Inner take-up:
Media is taken up
with its print surface
comes inside.
Outer take-up:
Media is taken up
with its print surface
comes outside.
Note
-Be careful of the tape axing direction on the takeup side.
-If the media is not installed straight to the paper tube, a skew of
media may occur.
6
Set the take-up direction switch according to
the take-up direction.
Take-up direction switch
uOuter take-up
- OFF
vInner take-up
7
Advance the media with the FORM FEED MENU
on the operation panel to wind it around the
paper tube by one turn. Then set the take-up
direction switch to OFF.
Note
-If the tension bar is attached without winding the media by
one turn, the tape will peel o.
8
Advance the media with the FORM FEED
MENU on the operation panel to an extent
where a slack can be created.
Be sure to create a sucient slack so that the tension
bar is placed at the bottom of the tension bar guide.
9
Open the tension bar guide’s cover.
10
Place the tension bar at the bottom of the
tension bar guide.
Note
-When the tension bar does not reach the tension bar guide’s
bottom, feed the media with the operation panel’s FEED menu.
Conrm that tension bar was placed securely at the tension bar
guide’s bottom.
11
Close the tension bar guide’s cover.
12
Press the take-up direction switch according to
the take-up direction. Take-up direction switch
uOuter take-up
- OFF
vInner take-up
Note
-If the media slack is secured excessively, the take-up reel unit may
keep winding the media for more than the prescribed time, and a
take-up timeout error occurs. In such a case, turn o the take-up
direction switch, and then press the switch again.
OFF
OFF

13
ENGLISH
<Media at the take-up side>
1
Turn o the take-up direction switch.
Take-up direction switch
uOuter take-up
- OFF
vInner take-up
2
Open the tension bar guide’s cover.
3
Place the tension bar at the tension bar hook.
Detach the tension bar at the take-up sides.
In case of vinyl chloride media, this procedure is not
necessary at the take-up side, because no tension bar is
used there.
4
Open the front cover, and then cut the media.
Set the cutter to the cutter groove, and cut the media
along the grove.
Platen
Paper guide
Note
-A net is spread out on the feeding side and take-up side
paper guides, respectively so that the media will not
adhere to the guides.
Do not remove these nets.
-When cutting the media, be careful not to damage the
paper guide net.
-Pay attention not to drop the used media so as to avoid
messing up the oor.
Procedure to remove media from the printer
5
Set the printer to the oine state by pressing
the ONLINE key.
Ç
INK MEDIA REG
È
Å
MEDIA M.ADV
Æ
6
Press the key.
The TUR’s take-up switch is activated by selecting
media and setting the take-up direction switch to ON.
7
Rotate the scroller the wind switch at the
supply side to take up the media.
Take-up reel switch
8
Detach the protection bar.
Protection bar
9
Loosen the right and left knob screws next to
the movable media dryer fan.
Media dryer fan
Knob screw
w
10
Pull the media dryer fan toward you and turn
it upward 90 degrees.
Media dryer fan
Note
-When the media dryer fan is turned upward, it slightly goes down
and is xed.To return the fan to its original position, pull it up and
turn it toward you, and then push it and secure it with the knob
screws.
-Turn the media dryer fan carefully so that the pressure control
knob and surrounding sheet metals do not get hung up on the
media dryer fan connecting cable.
OFF

14
11
Remove the tension bar from the tension bar
hook.
12
Loosen the knob screw of each tension bar
hook and extend it laterally.
Knob screw
Tension bar hook
13
Recommended dolly
Media
Set a dolly under the media and lift the media
to remove it.
<Media at the supply side>
1
Set the printer to the oine state by pressing
the ONLINE key.
Ç
INK MEDIA REG
È
Å
MEDIA M.ADV
Æ
2
Press the key.
The TUR’s take-up switch is activated by selecting
media.
3
Lift the slackened part and remove the tension
bar at the supply side.
Peel roller
Scroller
<Media in general>
Tension bar
<Vinyl chloride media>
Printer rear (supply side)
Peel roller
Tension bar
S size tension bar
n b
n
n
a
Switch
Caution
-Do not ratate the peel roller, or the printer may be
damaged.
4
Rotate the pressure control knob clockwise to
raise the pressure roller.
Takeup side Supply side
or
Pressure control knobs
5
Rotate the scroller ange manually to take up
the media.
6
Remove the scroller ange of the printer.
Printer rear (supply side)
Scroller ange
P
rinter rear
e

15
ENGLISH
-The factors that change the media advance correction
values are as follows.
• Change of print mode
• Pressure change using the pressure control knob
• Use/not use of take-up reel unit
• Type of media
• Dierence in media feed route
1
Set media longer than 4 m.
Find the rough media advance correction value in
[ROUGH] and determine the media advance correction
value in [DETAIL]. Both [ROUGH] print and [DETAIL]
print need paper of about 90 cm in length for one-time
print. (To cancel printing of media advance correction
pattern, press the CANCEL key.
2
Set the printer to the oine mode.
(Press the ONLINE key.)
Ç
INK MEDIA REG
È
Å
MEDIA M.ADV
Æ
3
Press the key and then key to display the
media advance correction pattern.
#MEDIA ADV PRINT
>ROUGH(NORMAL1)
Select the print mode to be used normally for the
media to set the media advance value.
Note
-To obtain the media advance correction value in DENSITY2 mode,
apply the media advance correction patterns, ROUGH(QUALITY)
or DETAIL(QUALITY).
4
Select the rough print mode with the and
keys, and press the key.
#MEDIA ADV PRINT
*OK?
5
Press the
key. Then the media advance
correction pattern [ROUGH] is printed in the
selected print mode.
#MEDIA ADV PRINT
*EXECUTING
6
Select a rough media advance correction value
from the print result.
Nine patterns are printed with 0.5% increments within
a range of 99.00% to 101.00%. Select a rough media
advance correction value from them.
7
Press the key and then the key to display
the media advance correction value.
#MEDIA ADV VALUE
>01:099.80%
8
Enter the media advance correction value and
press the key.
Align the digit with the and keys and set the
value with the and keys.
9
Press the key and then the key to display
the media advance correction pattern.
#MEDIA ADV PRINT
>ROUGH(NORMAL1)
10
Select the detail print mode with the and
keys.
Select the same print mode as for [ROUGH].
#MEDIA ADV PRINT
>DETAIL(NORMAL1)
11
Press the key twice to print the media
advance correction pattern [DETAIL].
#MEDIA ADV PRINT
*EXECUTING
12
Select the detail media advance correction
value from the print result.
Five patterns are printed for the entered rough media
advance correction value with 0.1% increments within
a range of -0.20% to +0.20%. Select an appropriate
media advance correction value from them.
13
Press the key and then the key to
display the media advance correction value.
#MEDIA ADV VALUE
>01:099.80%
14
Enter the determined media advance
correction value and press the key.
Align the digit with the and keys and set the
value with the and keys.
15
Press the key to return to the oine state.
Setting media advance correction values

16
Ink pack installation and replacement
1
Push the knob of the ink box cover to open the
ink box.
Knob
Ink box cover
2
Conrm the color of the ink pack to be replaced,
and pull the ink tray out of the printer.
Ink tray
3
Take the empty ink pack out of the ink tray.
If ink is not installed, go to step 4.
Push the two claws at the lower part of the plate of the
ink pack, and pull up the plate . Then remove the ink
pack from the hook of the ink tray .
1
2
Plate
Hook
Push two claws
Ink pack
Ink tray
P
h
l
a
a
te
t
t
t
t
Ink pack installation/replacement procedure
4
Take a new ink pack out of the box and set it in
the ink tray.
Hook the two holes at the end of the ink pack on
the ink tray's two protrusion. Then insert the plate into
the ink tray until a click is heard .
2
1
New ink pack
Plate
Protrusion
Ink tray
5
Insert the ink tray into the slot of the printer.
Note
-Insert the ink tray as far as it will go.
-The location of ink tray is determined by color. Be sure to insert
each ink tray into the specied slot.
Ink tray
6
Close the ink box cover.
Ink box cover
o
x
c
7
Conrm that the ink pack replacement was
completed.
-When the replacement is successfully completed, the
printer returns to the online or oine state.
-If the replacement is not completed, an error message
appears. Retry the replacement procedure beginning
with step 1.
-While ink is remaining in the subcartridge even during
replacement of ink, print operation is performed.
Ink tray
Ink pack

17
ENGLISH
Waste ink bottle installation and replacement
Note
-Replace the waste ink bottle carefully not to bump your head on
the printer upper part.
1
Slide the lever up and lift the whole cap.
Tube
Lever
Waste ink bottle
2
The ink drips from the tube. Leave it for a while.
3
Remove the full waste ink bottle from the unit
paying attention not to spill the waste ink. Then
cap it and replace it with a new one.
4
Wipe o the spilt ink in the waste ink bottle unit.
5
Slide the lever up and install a new waste ink
bottle.
6
Lower the lever.
Tube
Lever
Waste ink bottle
Note
-Do not hit the external cover's upper part, or the waste ink
may spill.
7
The message to select the waste ink counter
reset (clear) is displayed.
#BOTTLE EMPTY?
*NO
,
#BOTTLE EMPTY?
*YES
8
Select "BOTTLE EMPTY? *YES" and press the
key.
Procedure when the waste ink bottle becomes full
Procedure when no waste ink bottle is installed
1
Conrm that the printer recognizes no waste ink
bottle with the guidance message is displayed.
BOTTLE OUT
INSTALL BOTTLE
2
Install a new waste ink bottle.
Refer to [Procedure when the waste ink bottle
becomes full].
3
Conrm the message to select the waste ink
counter reset (clear) is displayed.
#BOTTLE EMPTY?
*NO
,
#BOTTLE EMPTY?
*YES
4
Select "BOTTLE EMPTY? *YES" and press the
key.

18
Replacing the wiper blade
The following describes the wiper blade replacement procedure.
Replace the wiper blade when the replacement message appears or scratches are found in the daily inspection. Prepare the
tweezers supplied in the daily maintenance kit before replacing the wiper blade.
1
Open the front cover and wipe cover.
2
Nip the bottom edge of the wiper blade with
tweezers and release the hook of the plastic
projection.
3
Remove the wiper blade upward.
4
Nip the rubber of the new wiper blade with the
tweezers and insert it straight downward, and
install it by hooking the hole in the rubber to the
plastic projection.
Note
-When handling the wiper blade, do not touch its upper part by
hand or nip it with tweezers because the upper part directly
contacts with the print head.
5
Close the wipe cover and front cover.
Upper part
Rubber part

19
ENGLISH
Correcting the edge sensor position
Print out the edge sensor adjustment pattern, and correct the edge sensor position.
After printing, measure the distance and specify the parameter.
1
Hold down the MENU key until the
[ADJUST] menu appears.
Ç
PRINTER SETUP
È
Å
ADJUST HEATER
Æ
2
Press the key to enter the [ADJUST] menu.
#TEST PRINTS
>NOZZLE PRINT
3
Press the key.
4
Hold down the key until the [CHECK EDGE
SENSOR] menu appears.
#TEST PRINTS
>CHECK EDGE SENSOR
5
Press the key.
#TEST PRINTS
*OK?
6
Press the key.
#TEST PRINTS
*EXECUTING
7
Judge the printing results.
Measure the margin of the printing result with a square,
and obtain a dierence between the measured margin
and the value (15mm) shown in the specications.
If the dierence is 15mm, complate this procedure.
If not, follow the prcedure below to correct the value.
508nozzles
(Blankbythe
evennumber
ofheads)
508nozzles
(Allnozzles)
15mm
8
Press the key to enter the [ADJUST] menu.
#EDGE SENSOR ADJ VAL
>±Y.Ymm
9
Press the key to display the [EDGE SENSOR
ADJ VAL] menu, and press the key.
10
Based on the printed sensor adjustment
pattern, enter the correction value of the edge
sensor position.
#EDGE SENSOR ADJ VAL
>±Y.Y mm
Y.Y
11
Press the key to decide the entered value.
#EDGE SENSOR ADJ VAL
>+0.0mm
12
Press the key to return to the higher-level
menu.
To obtain the correction value:
Obtain the correction value by measuring the margin
setting the reference value to 15 mm.
<Example>
The margin is 14 mm: The correction value is -1.0 mm.
The margin is 16 mm: The correction value is +1.0 mm.

20
Adjusting tension bar length
A set of tension bars for the supply side includes the
following parts. Use suitable ones depending on the width
and type of the media.
Coupling tension bars (supply side)
Tension bars can be connected to each other by screwing. The
bar's length is 72 inches when an L-size bar is connected to an
M-size bar. The L-size tension bar whose both ends are convex
is always used. M-size and S-size tension bars whose one end
is concave are coupled with the L-size tension bar.
-In case of vinyl chloride media, use only one S size
tension bar (16 inches) (about 41cm).
Print head cleaning
The following two types of print head cleaning are provided. Use the suitable one.
Type of cleaning Usage
NORMAL ALL Recovery from nozzle-out
STRONG ALL Recovery from nozzle-out that is not rectied by [NORMAL ALL]
1
Set the printer to the oine state.
(Press the ONLINE key.)
Ç
INK MEDIA REG
È
Å
MEDIA M.ADV
Æ
2
Press the MENU key to display PH.REC
MENU.
Ç
INK MEDIA REG
È
Å
MEDIA M.ADV
Æ
MENU
Ç
REWIND FORM FEED
È
Å
PH.REC PH.MAIN
Æ
3
Press the key to enter the head cleaning
menu.
#PH RECOVERY
>NORMAL
Note
-If ink lling from the ink tray is not yet completed, the ink supply
menu is displayed instead of the cleaning menu.
-Prepare an ink pack and perform ink supply operation.
4
To change the parameter, press the key.
#PH RECOVERY
>NORMAL
5
Select the option for cleaning with the and
keys.
>STRONG
#PH RECOVERY
>NORMAL
6
Press the key.
#PH RECOVERY
*BOTTLE OK?
7
Select head numbers with the key or the
key, and reverse (display or non-display) the
selected head numbers with the key or the
key.
#SELECT:87654321 FB
*BOTTLE OK?
Note
-The indicated head numbers denote the heads to be cleaned.
L size (48 inches) (123 cm): 1 piece
M size (24 inches) (61 cm): 1 piece
S size (16 inches) (41 cm): 2 pieces
Other manuals for CS6407
1
Table of contents
Languages:
Other Oce Printer manuals
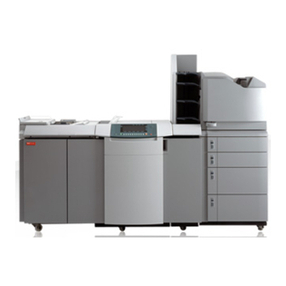
Oce
Oce VarioPrint 2090 User manual
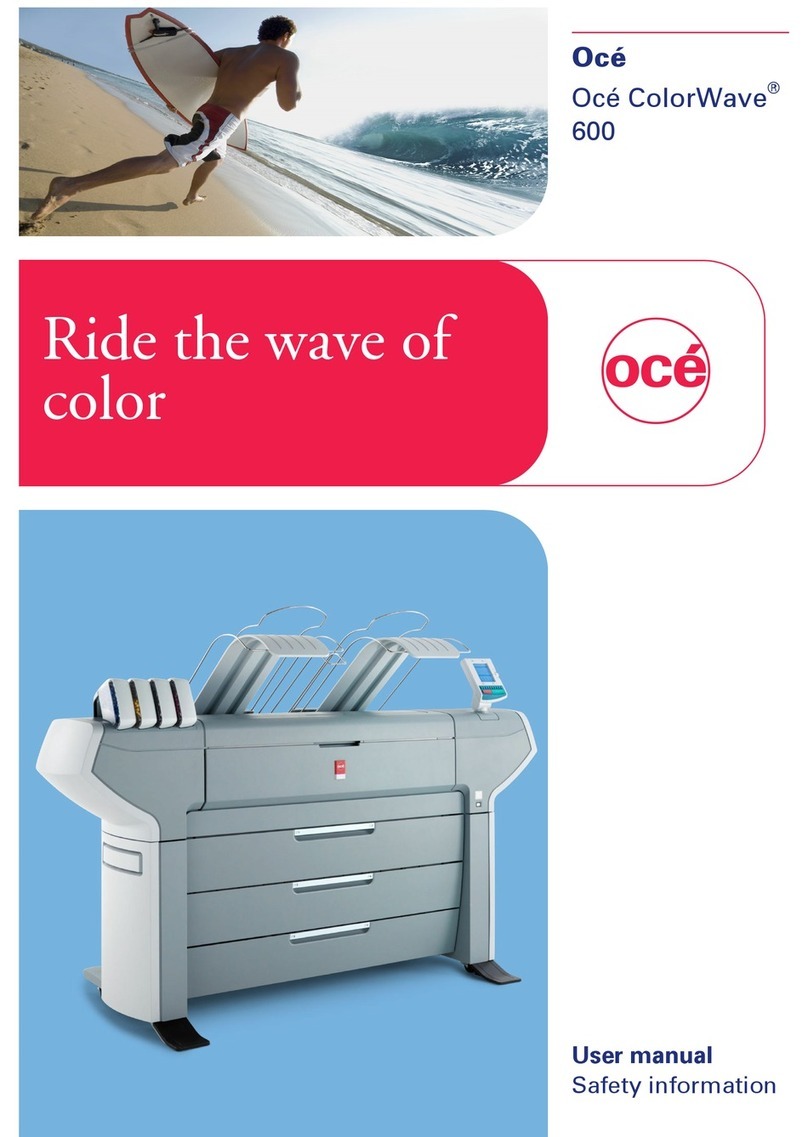
Oce
Oce ColorWave 600 User manual
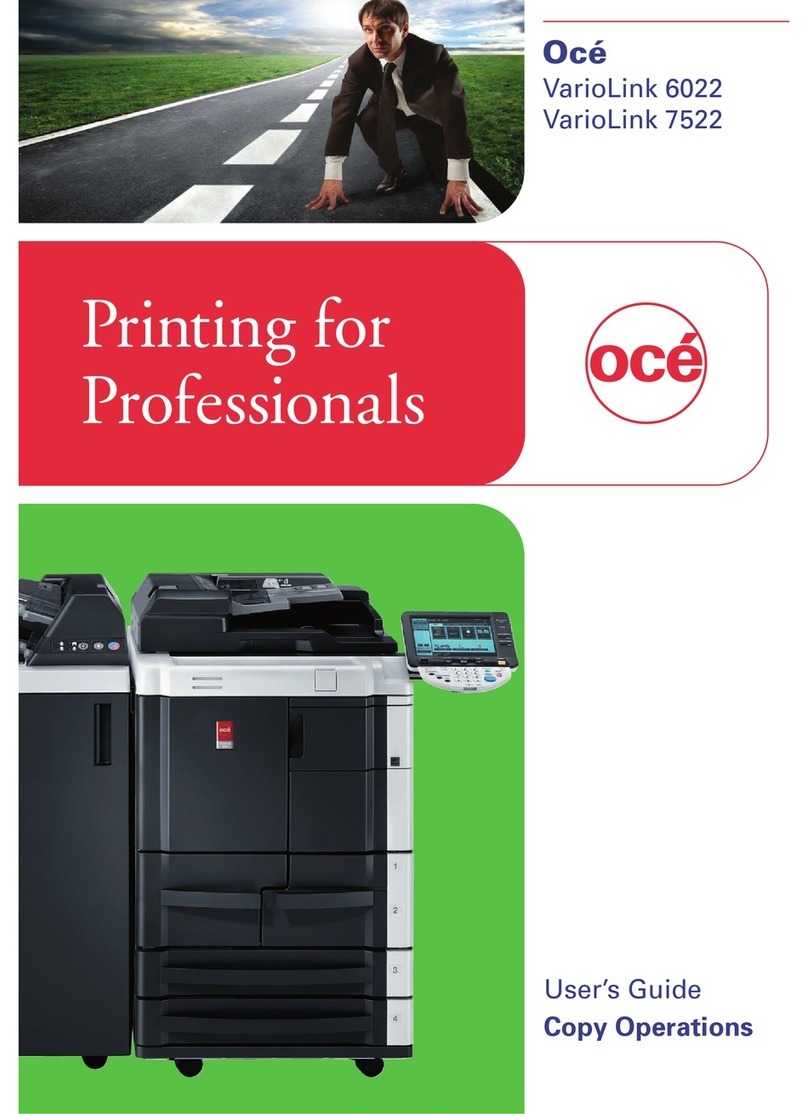
Oce
Oce VarioLink 6022 User manual
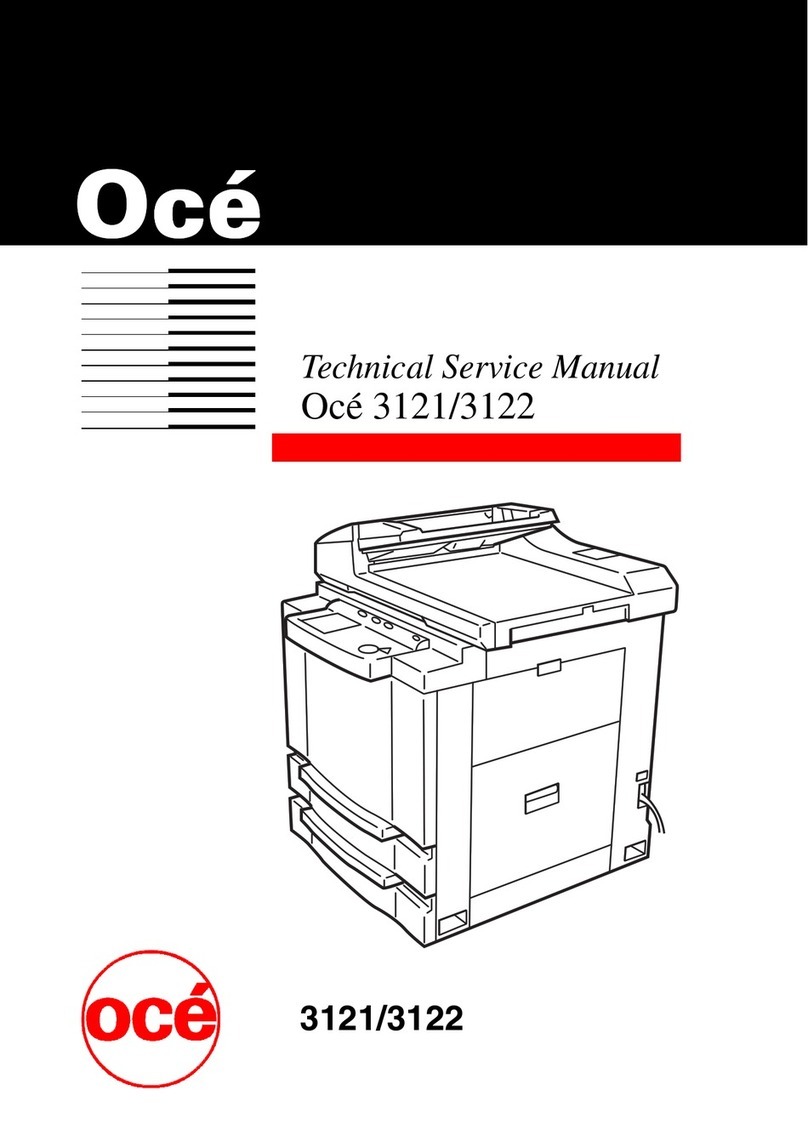
Oce
Oce 3121 Operating manual
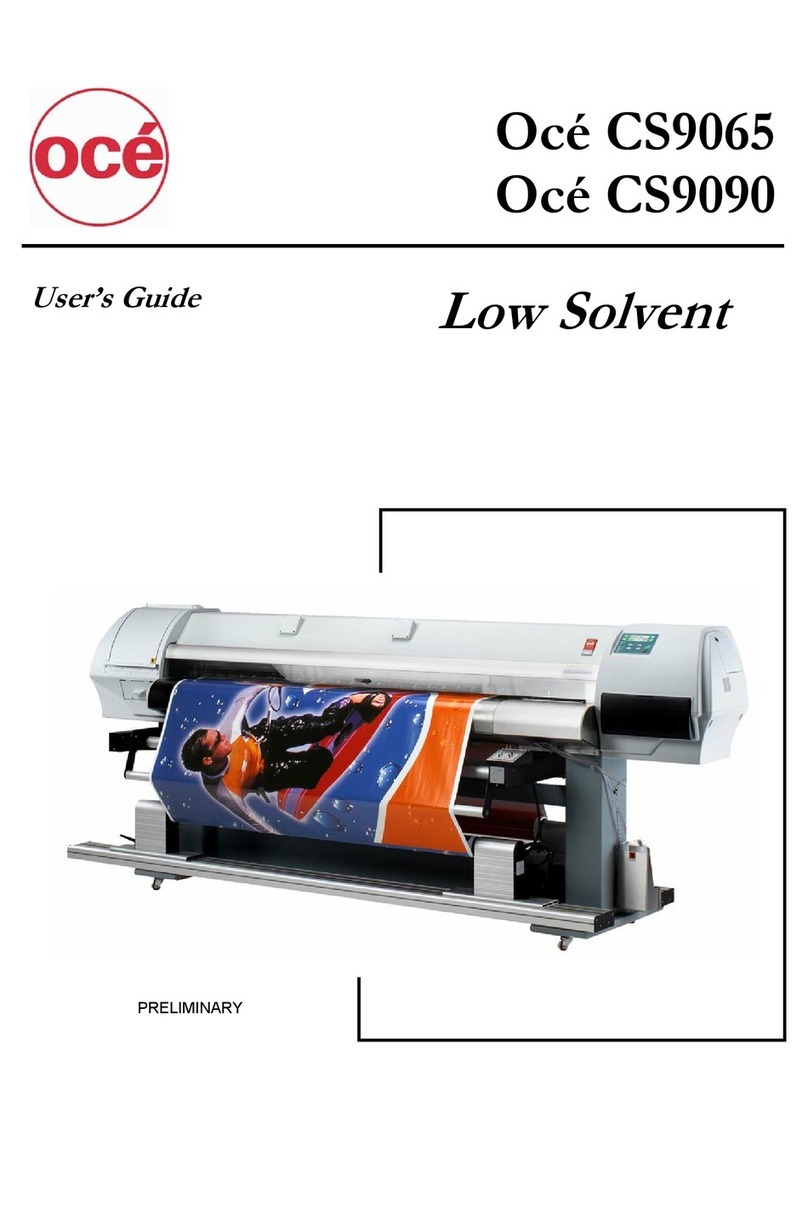
Oce
Oce CS9090 User manual
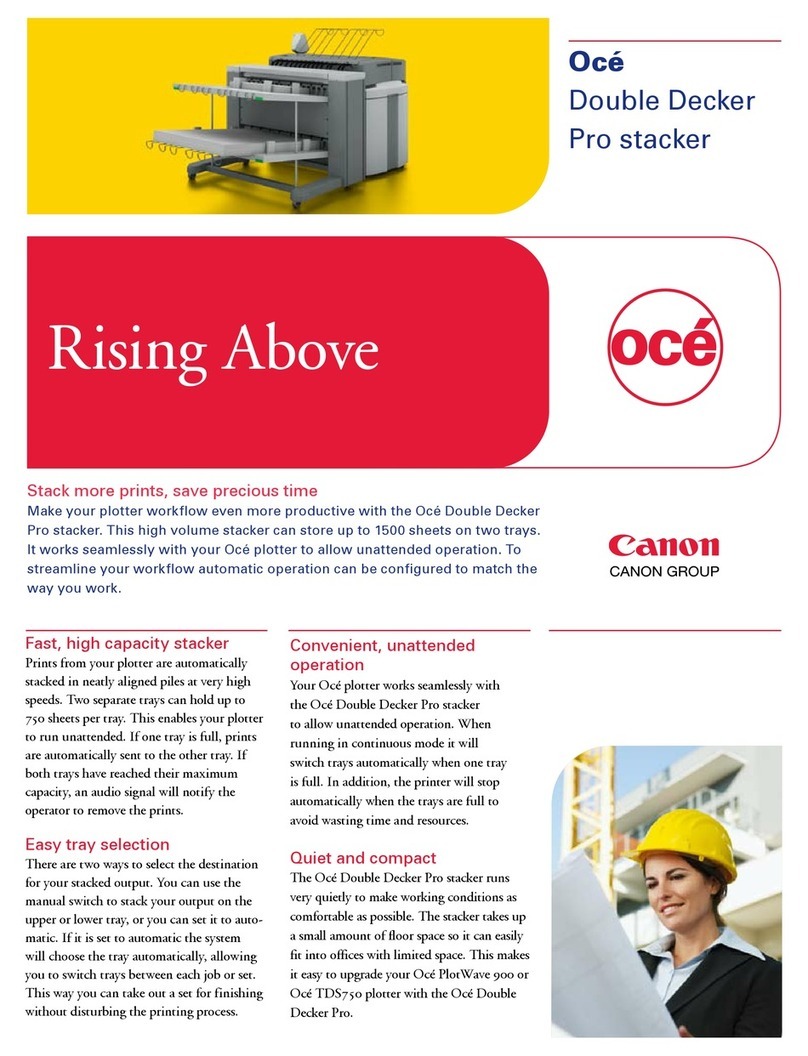
Oce
Oce PlotWave 900 User manual
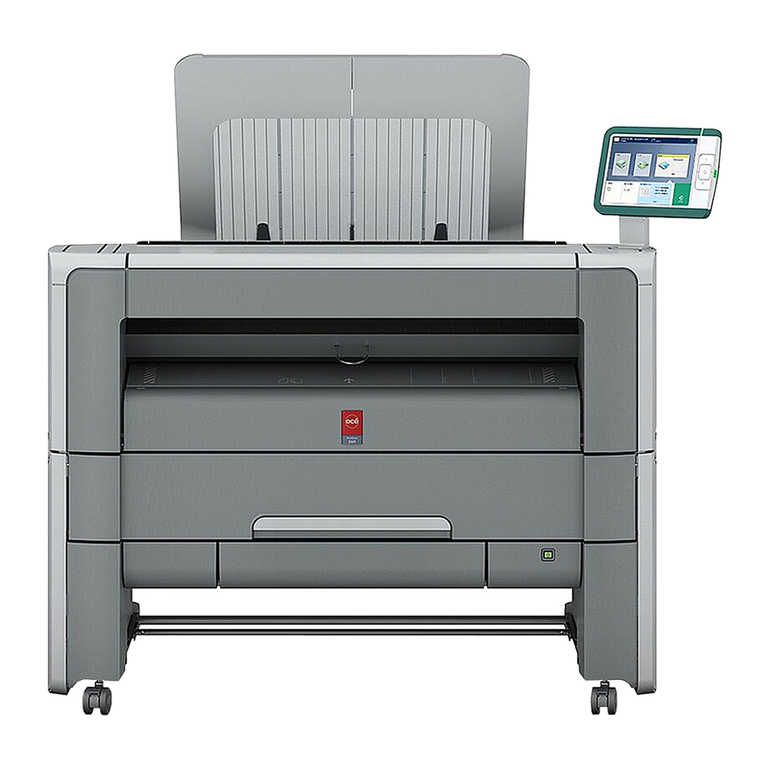
Oce
Oce PlotWave 340 User manual

Oce
Oce Arizona T220 User guide
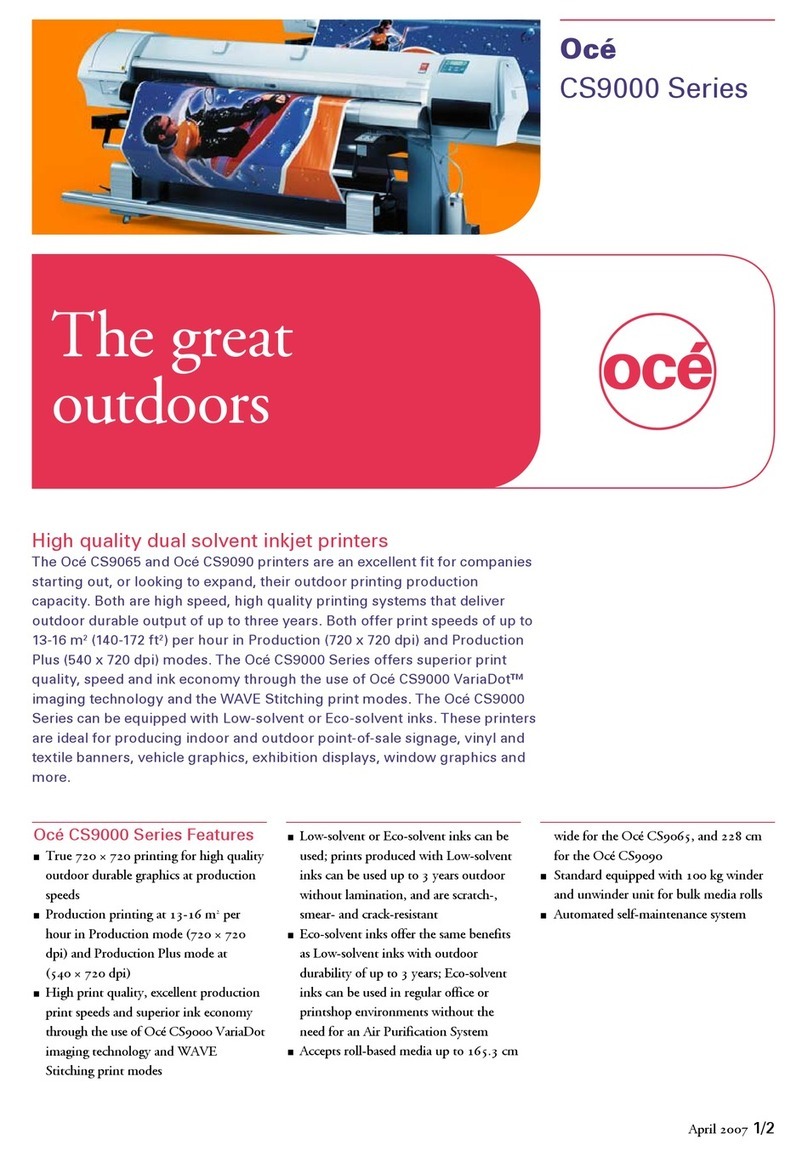
Oce
Oce CS9065 Installation and operation manual
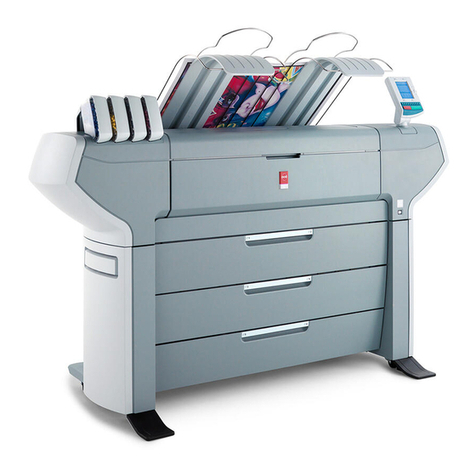
Oce
Oce ColorWave 650 User manual