Omron TL4019 Series User manual

Electrical Connection
When choosing the insulation material and wire
for the connections, pay attention to the over-
temperature in the housing (depending on the
operating conditions)!
Only switching contacts marked with the
positively driven NC contact symbol are to
be used for the safety circuit.
For switching elements with four positively
driven NC contacts only the contacts 21-22
and 41-42 are actuated on activating and
deactivating the guard locking. In applications
with potentially hazardous states (e.g.
overtravelling movements), contact 21-22
and/or 41-42 must always be integrated into
the safety circuit.
For TP without plug connector:
:
For use and applications as per the requirements
of , copper wire 60/75° C is to be used.
The operating voltage for the interlocking solenoid
must match the value on the rating plate (e.g. US =
AC/DC 24 V).
Cable entry M20x1.5
Break out the required entry opening.
Fit the cable gland with the appropriate degree
of protection.
For pin assignment see Figure 3.
Tighten the screws with a torque of 0.5 Nm.
Check that the cable entry is sealed.
Close the cover and screw in position.
Functional Check
Warning! Danger of fatal injury as a result of
faults in installation and functional check.
Before carrying out the functional check, make
sure that there are no persons in the danger
area. Observe the valid accident prevention
regulations.
After installation and any fault, the safety function
must be fully checked. Proceed as follows:
Mechanical function test
Electrical function test
1.Switch on operating voltage.
2.Close all safety guards.
Guard locking by solenoid force: Activate
guard locking.
The machine must not start automatically.
It must not be possible to open the safety guard.
3.Enable operation in the control system.
It must not be possible to deactivate the guard
locking as long as operation is enabled.
4.Disable operation in the control system and
deactivate guard locking.
The safety guard must remain locked until there
is no longer any risk of injury.
It must not be possible to start the machine as
long as the guard locking is deactivated.
Repeat steps 2 - 4 for each safety guard.
Inspection and Service
No servicing is required, but
of the following is necessary to ensure trouble-free
long-term operation:
correct switching function
secure mounting of components
dirt and wear
sealing of cable entry
loose cable connections or plug connectors.
Note:The year of manufacture can be seen in the
bottom, right corner of the rating plate.
Exclusion of Liability under the Following
Conditions
if the unit is not used for its intended purpose
non-compliance with safety regulations
non-compliance with safety regulations
failure to perform functional checks.
Technical Data
Parameters Value
Housing material Reinforced thermoplastic
Degree of protection according to IEC 60529
Cable entry IP67
Mechanical life 1 x 106operating cycles
Ambient temperature -20 ... +55°C
Degree of contamination (external, according to EN 60947-1)
3 (industrial)
Installation position Any
Approach speed, max. 20 m/min
Actuating force, max. at 20°C 10 N
Extraction force 20 N
Retention force 10 N
Locking force Fmax
All TL4019 except TL4019-5 1,300 N
TL4019-5 800 N
Actuation frequency 1,200/h
Switching principle Slow-action switching contact
Contact material Silver alloy, gold flashed
Connection type Screw terminal with cable entry
Conductor cross-section (rigid/flexible)
0.34 ... 1.5 mm²
Rated insulation voltage i
U = 250 V
Rated impulse withstand voltage imp
Rated short-circuit current 100 A
Switching voltage, min. at 10 mA 12 V
Utilization category to EN 60947-5-1
AC-15 4 A 230 V
DC-13 4 A 24 V
Switching current, min., at 24 V1 mA
Short circuit protection to IEC 60269-1
4 A gG
Conv. thermal current Ith 4 A
Solenoid operating voltage/solenoid power consumption
AC/DC 24 V (+10%/-15%)8 W
110AC 110 V (+10%/-15%)10 W
Duty cycle 100 %
Reliability figures according to EN ISO 13849-1
B10d 3 x 10 6
TL4019
Operating Instructions for TL4019 Series Safety Switches
EC declaration of conformity
The manufacturer named below herewith declares
that the product fulfills the provisions of the
directive(s) listed below and that the related
standards have been applied.
Directives applied:
Machinery directive 2006/42/EC
Standards applied:
EN 60947-5-1:2010
GS-ET 19:2015
U = 2.5 kV
Locking force FZh in accordance with test principles
(FZh = Fmax) = 1,000 N
1,3
All TL4019 except TL4019-5
GS-ET-19
The actuator must slide easily into the actuating head.
Close the safety guard several times to check the
function. The function of any manual releases (except
for the mechanical release) must also be tested.
If damage or wear is found, the complete switch
and actuator assembly must be replaced.
Replacement of individual parts or assemblies is
not permitted!
Check the device for proper function at regular
intervals and after every fault. For information
about possible time intervals, refer to EN ISO
14119:2013, section 8.2
The Declaration of Conformity is part of the operating
instructions, and it is included as a separate sheet with
the unit.
Hank Liu
Quality Representative and Authorized Signatory
OMRON Robotics and Safety Technologies, Inc.
Pleasanton, CA, U.S.A.
Representative in EU: J.J.P.W. Vogelaar
European Quality & Environment Operations Manager
Omron Europe B.V.
Zilverenberg 2, 5234 GM, ‘s-Hertogenbosch
The Netherlands

Safety Precautions
Fig. 1: Changing the actuating direction
TL4019
Safety,
Technology
& Innovation
Operating Instructions for TL4019 Series Safety Switches
Correct Use
Safety switches series TL4019 are electromagnetic
interlock devices with guard locking solenoid (separate
actuator). The actuator has a low coding level.
In combination with a separating safety guard and the
machine control, this safety component prevents the
safety guard from being opened while a dangerous
machine movement is being performed.
For the control system, this means that starting
commands which cause hazardous situations must
become active only when the safety guard is in
protective position and the guard locking is in locked
position.
The locked position of the guard locking must be
released only when the hazardous situation is no
longer present.
Closing and locking a safety guard must not cause
automatic starting of a dangerous machine function. A
separate start command must be issued. For
exceptions, refer to EN ISO 12100 or relevant
C-standards.
Before safety switches are used, a risk assessment must
be performed on the machine in accordance with
EN ISO 13849-1, Safety of machinery. Safety related
parts of control systems. General principles for design
EN ISO 12100, Safety of machinery – Risk
assessment and risk reduction.
IEC 62061, Safety of machinery – Functional safety of
safety-related electrical, electronic and programmable
electronic control systems.
Correct use includes compliance with the relevant
requirements for installation and operation, particularly
EN ISO 13849-1, Safety of machinery. Safety related
parts of control systems. General principles for design
EN ISO 14119, Safety of machinery. Interlocking
devices associated with guards. Principles for design
and selection
EN 60204-1, electrical equipment of machines
Important:
The user is responsible for safe integration of the device
in a safe overall system. For this purpose the overall
system must be validated, e.g. in accordance with EN
ISO 13849-2. If the simplified method according to section
6.3 EN ISO 13849-1:2015 is used for validation, the
Performance Level (PL) may be reduced if several
devices are connected one after the other.
Logical series connection of safe contacts is possible up
to PL d in certain circumstances. More information about
this is available in ISO TR 24119.
If a product data sheet is included with the product, the
information on the data sheet applies in case of
discrepancies with the operating instructions.
Safety switches fulfill a personal protection
function. Incorrect installation or tampering can
lead to severe injuries to personnel.
Safety components must not be bypassed
(bridging of contacts), turned away, removed or
otherwise rendered ineffective.
On this topic pay attention in particular to the
measures for reducing the possibility of bypassing
according to EN ISO 14119:2013, section 7.
The switching operation may only be triggered
by actuators specially provided for this
purpose which are permanently connected to
the protective guard.
Mounting, electrical connection and setup only
by authorized personnel.
Function
The safety switch permits the locking of movable
safety guards.
In the switch head there is a rotating cam that is
blocked/released by the guard locking pin. The
guard locking pin is moved on the insertion /
removal of the actuator and on the activation /
deactivation of the guard locking. During this
process the switching contacts are actuated.
If the cam is blocked, the actuator cannot be pulled
out of the switch head guard locking active.
Version TL4019-1, TL4019-3 and TL4019-5
(Guard locking by spring force)
The guard locking pin is held in the locked position by
spring force and unlocked by electromagnetic actuation.
The spring interlock guard locking functions in
accordance with the closed-circuit current principle. The
safety guard cannot be opened immediately in the event
of interruption of the solenoid power supply.
Versions TL4019-2 and TL4019-4
(Guard locking by solenoid force)
This type must be used only in special cases after
strict assessment of the accident risk! The safety
guard can be opened immediately in the event of
interruption of the solenoid power supply!
The guard locking pin is held in the locked position by
electromagnetic force and released by spring force. The
guard locking operates in accordance with the
open-circuit current principle.
Close safety guard and activate guard locking
The guard locking pin is released by insertion of the
actuator into the safety switch.
TL4019-1, TL4019-3 and TL4019-5: The guard
locking pin is moved to locked position by spring force.
TL4019-2 and TL4019-4: The guard locking pin is
moved to locked position when the solenoid operating
voltage is applied.
The safety contacts are closed.
Deactivate guard locking, open safety guard
TL40191/TL4019-5: The guard locking pin releases
the cam when the solenoid operating voltage is applied.
For switching function see Figure 3 column 2 Door
closed and not locked. The actuator can be
removed.
TL4019-2: The guard locking pin releases the cam
when the solenoid operating voltage is switched off.
For switching function see Figure 3 column 2 Door
closed and not locked.
The actuator can be removed.
TL4019-3 (with door monitoring contact): The guard
locking pin releases the cam when the solenoid operating
voltage is applied. For switching function see Figure 3
column 2 Door closed and not locked.
The actuator can be removed.
On the removal of the actuator, the door monitoring
contact switches and signals that the safety guard is
open (see Figure 3 column 3, Door open ).
TL4019-4 (with door monitoring contact): The guard
locking pin releases the cam when the solenoid operating
voltage is switched off.
For switching function see Figure 3 column 2 Door
closed and not locked.
The actuator can be removed.
On the removal of the actuator, the door monitoring
contact switches and signals that the safety guard is
open (see Figure 3 column 3, Door open).
Door request (TL4019-5)
When the actuator is in the locked state positively driven
contact 21-22 is opened by pulling the safety guard (6
mm actuator stroke) as a result of which a signal is
forwarded to the higher-order control system. Depending
on the control concept, the safety guard can be unlocked
automatically - when machine components which were
still running have stopped.
Mechanical Release
In the event of malfunctions, the guard locking can be deactivated
using the mechanical release, irrespective of the state of the solenoid
(see Figure 2).
Unscrew locking screw.
Using a screwdriver, turn the mechanical release by approx.
180° in the direction of the arrow.
The mechanical release or the mechanical key release must
be returned to its original position and sealed after use (for
example with sealing lacquer or using wire).
Please observe the supplied dimension drawing in the case of
key release.
Lock and Escape Release
On the actuation of the lock or the escape release, the actuator
must not be under tension.
The contacts 21-22 and 41-42 are opened and the switch
mechanically unlocked. The state of contacts 1x-1x and 3x-3x can
vary.
Mounting
Safety switches and actuators must not be used as an
end stop.
Mount the safety switch only in assembled condition!
Caution! Risk of burns due to high surface temperature at
ambient temperatures above 40°C! Protect switch against
touching by personnel or contact with inflammable material.
Assemble the safety switch so that
access to the switch is difficult for operating personnel
when the safety guard is open.
it is possible to operate the mechanical release and check
and replace the safety switch.
the escape release can be actuated from the hazard area.
Fit an additional end stop for the movable part of the safety
guard.
Insert the actuator in the actuating head.
Mount the safety switch positively.
Permanently connect the actuator to the safety guard so that
it cannot be detached, e.g. using the enclosed non-remova-
ble screws, rivets or welding.
Changing the Actuating Direction
Remove the screws from the actuating head.
Set the required direction.
Tighten the screws with a torque of 0.6 Nm.
Cover the unused actuating slot with the enclosed slot cover.
Protection Against Environmental Influences
A lasting and correct safety function requires that the
actuating head must be protected against the penetration
of foreign bodies such as swarf, sand, blasting shot etc.
Cover the actuating slot, the actuator and the rating plate
during painting work.
The safety switch is designed so that fault exclusions
for internal faults in accordance with EN ISO
13849-2:2013, Table A4, can be assumed.

Figure 3e: With mechanical key releaseFigure 3d: With rare release
76,5
20,5
19
39
61,5
74,7
5,76
53
63
4
4
M
41
20
31
locked
unlocked
Short axle
Long axle
locked
unlocked
Flex 2 Actuator
12
26
20
35
28
+2
R> 90
R> 100
TL4019
Subject to technical modifications.
Manual P/N 99926-0010 Rev.E
Drawing number 095299-07-01/20
Safety,
Technology
& Innovation
Original Instructions
Actuator Removed
Switching position:
Unlocked Opened
Type
TL4019-1-..1
TL4019-2-..1
41 42
3433 22
1413
21 14
22
34
42
21
13
33
41
14
22
34
42
21
13
33
41
41
33
11
21
42
34
22
12
41
33
11
21
42
34
22
12
21
11 12
22
33 34
4241
41
31
13
21
42
32
22
14
41
31
13
21
42
32
22
14
21
13 14
22
31 32
4241
41
33
13
21
42
34
22
14
41
33
13
21
42
34
22
14
21
13 14
22
33 34
4241
E2
E1
31
13
21 32
22
14
31
13
21 32
22
14
21
13 14
22
31 32
E1
E2 E1
E2
E1 E2E2
E1
14
22
32
21
13
31
TL4019-3-..1
TL4019-4-..1
TL4019-3-..2
TL4019-4-..2
TL4019-3-..3
TL4019-4-..3
Completely
Inserted
Closed Request Unlocked
Type
TL4019-5-..1
53
,3 5
30
40
441
291
31
22
16
42
61
34
8,5
3,5
h
v
Auxiliary unlocking
mechanism
M = 0.5 Nm
for M5 > 35 mm
ISO 1207 (DIN84)
ISO 4762 (DIN 912)
M = 1.4 Nm
M = 0.6 Nm
Locking screw
Fig. 2: Switching elements and functions
Fig. 3: Minimum travel + overtravel
Fig. 4: Dimension drawing
Approached direction Standard actuator
horizontal (H)
vertical (V)
28 + 2
29.5 + 1.5
28 + 7
–
Operating Instructions for TL4019 Series Safety Switches
Inserted
Locked
Inserted
E1 E1
E2 E2
Actuator
Switching position:
Completely
Removed
Opened
Overtravel actuator
Flex 1 Actuator
Figure 4: Min. door radii
Actuator type Door radius min. [mm]
Flex 2 90
Flex 1 100
90 Degree 1000
Flat 1000
OMRON Robotics and Safety Technologies, Inc.
4225 Hacienda Drive, Pleasanton, CA 94588 USA
www.omron247.com
©2020 Omron Robotics and Safety Technologies, Inc.
All rights reserved.
This manual suits for next models
8
Other Omron Switch manuals
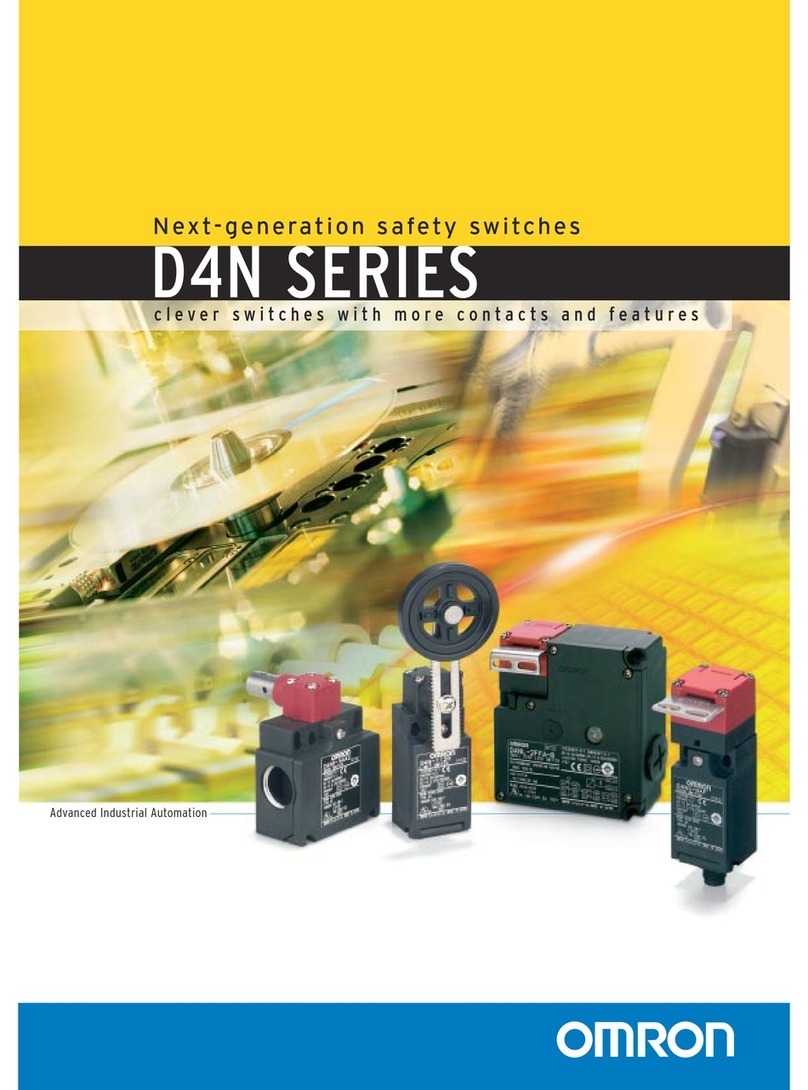
Omron
Omron D4N Series User manual
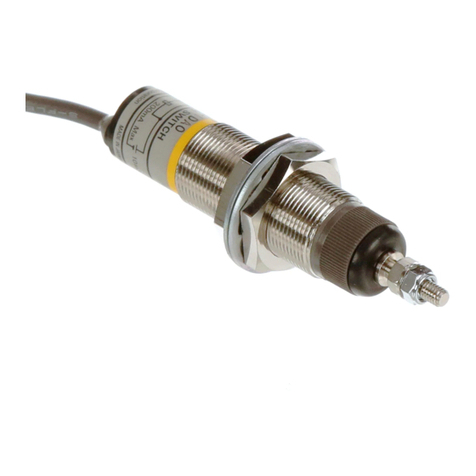
Omron
Omron D5C Series User manual

Omron
Omron D4BL - User manual
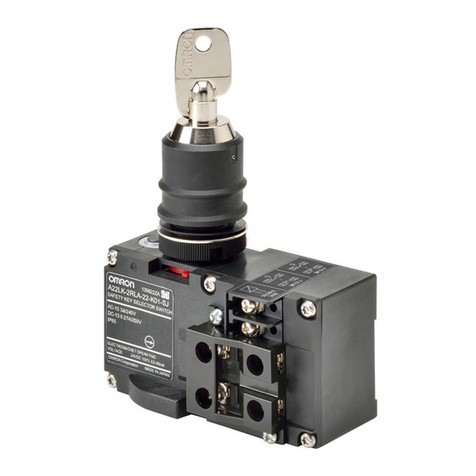
Omron
Omron A22LK Series User manual
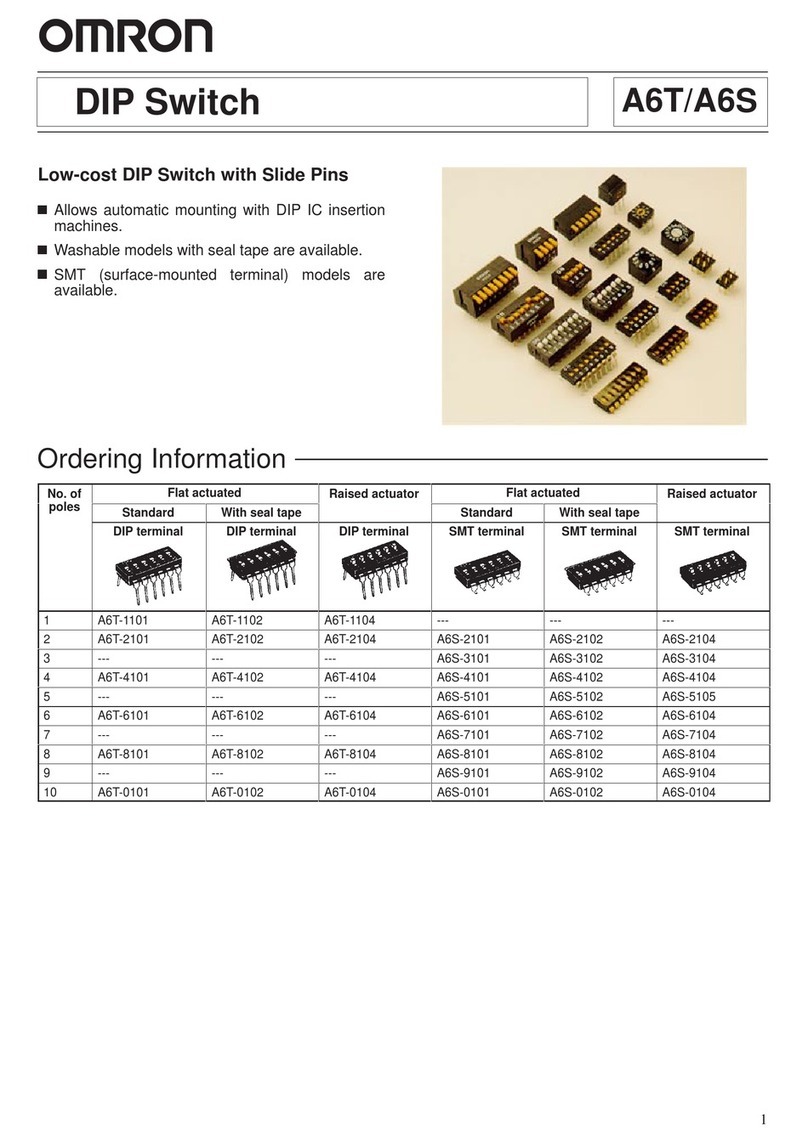
Omron
Omron A6T Series User manual
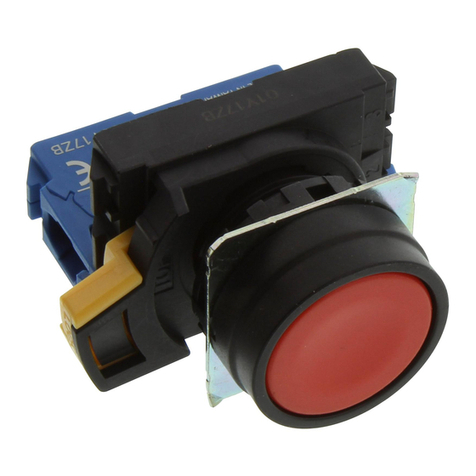
Omron
Omron A22NN User manual
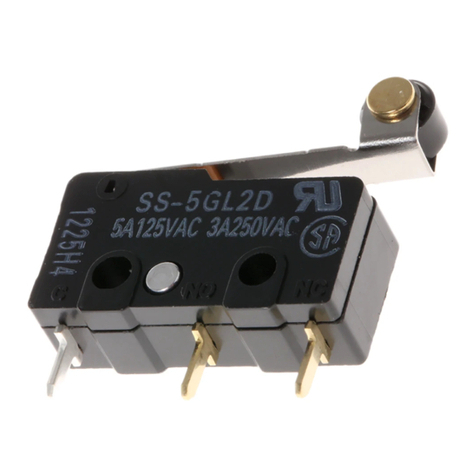
Omron
Omron SS Series User manual
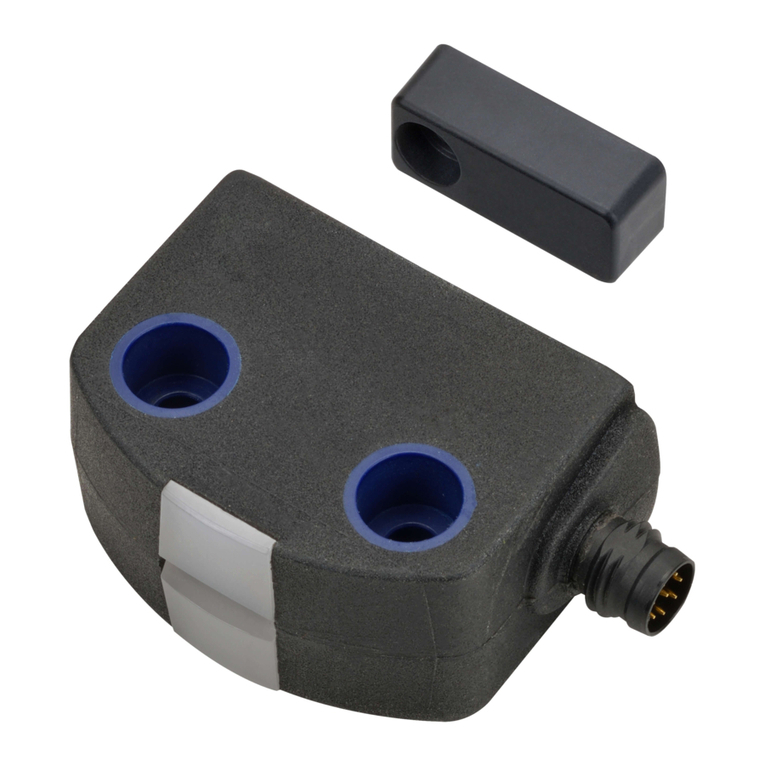
Omron
Omron D41D User manual
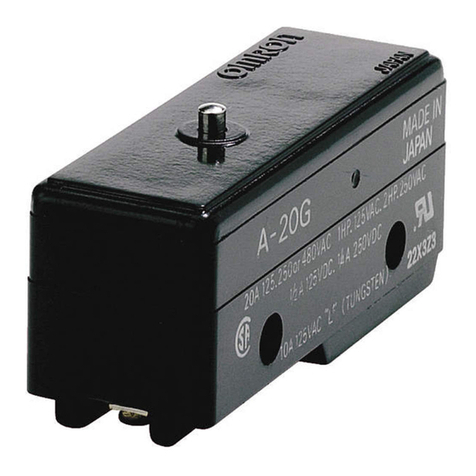
Omron
Omron A User manual
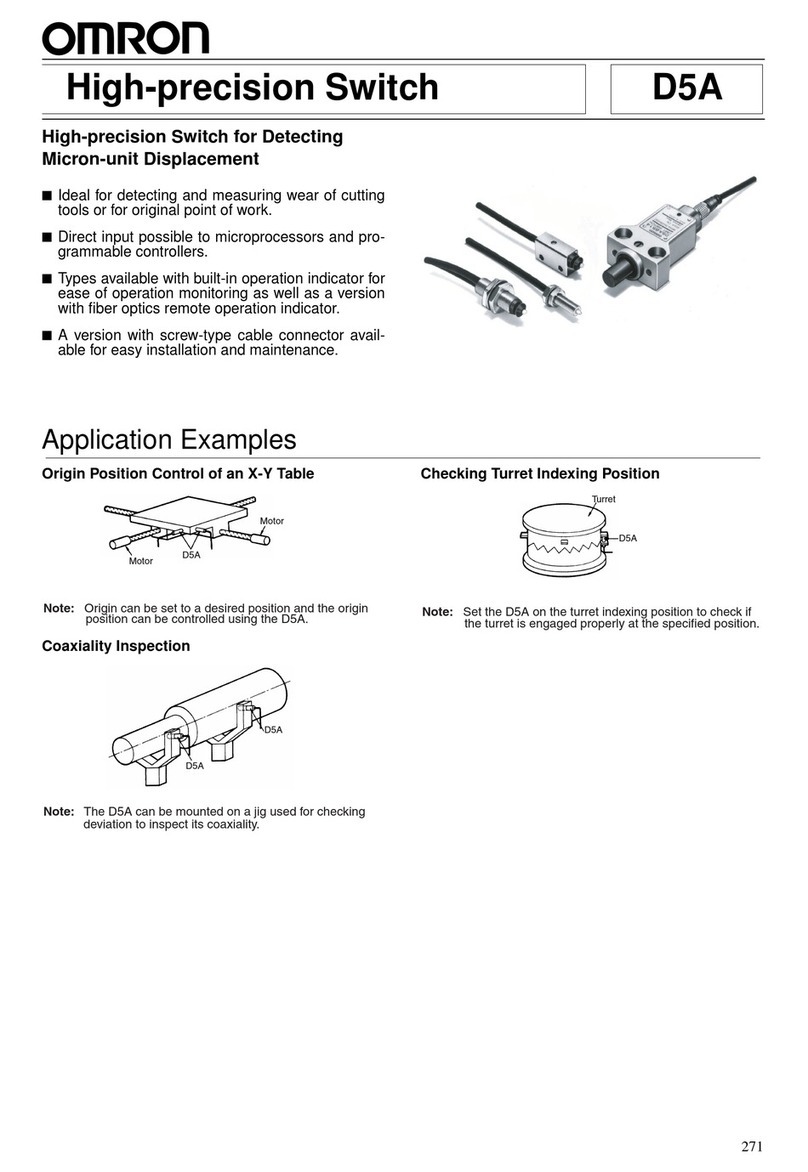
Omron
Omron D5A - User manual
Popular Switch manuals by other brands
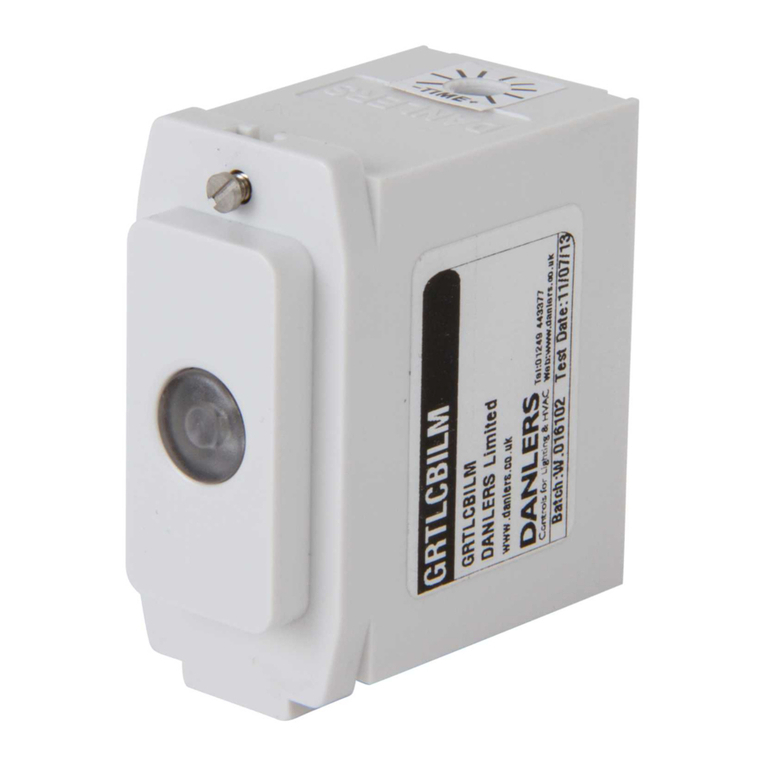
DANLERS
DANLERS GRTL MK Installation notes
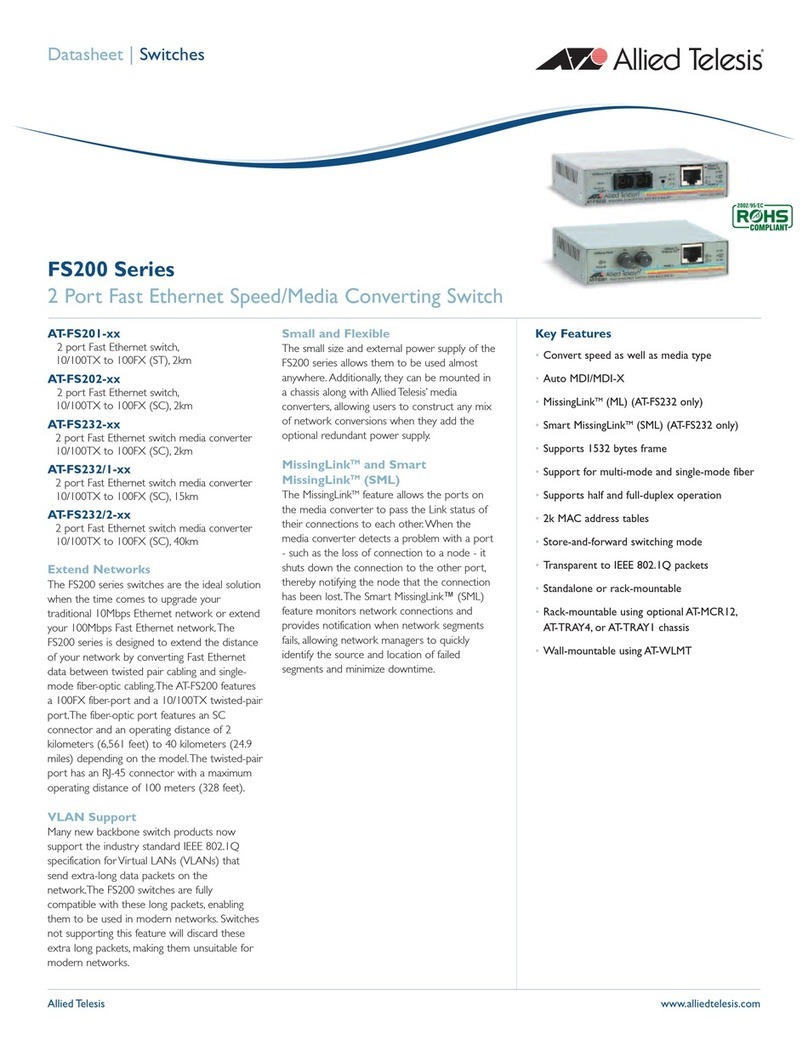
Allied Telesis
Allied Telesis AT-FS201 Series datasheet
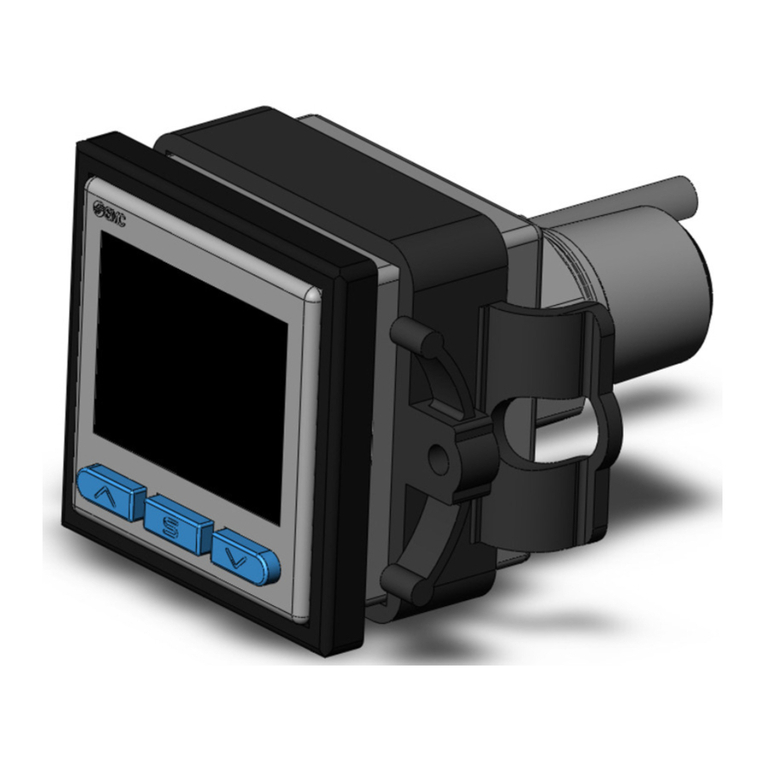
SMC Networks
SMC Networks ZSE20C Series user manual

Cooper Bussmann
Cooper Bussmann H79-2 quick start guide
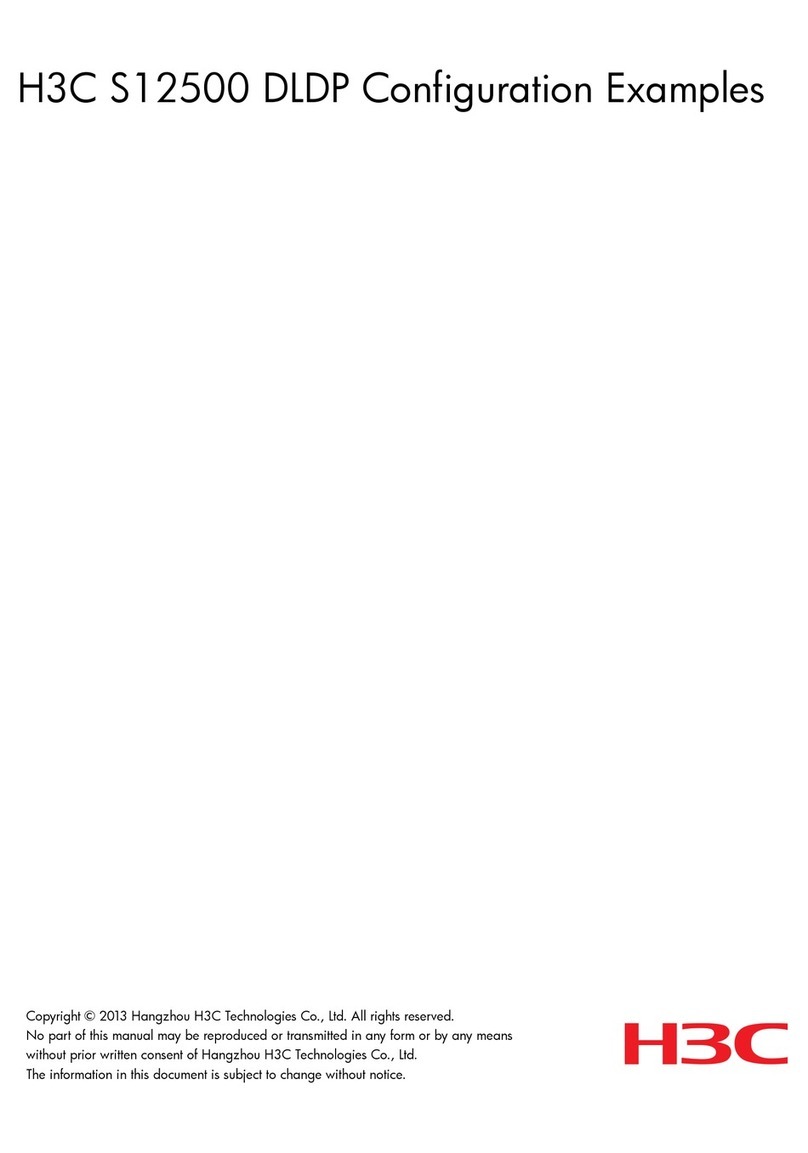
H3C
H3C S12500 Series Configuration Examples
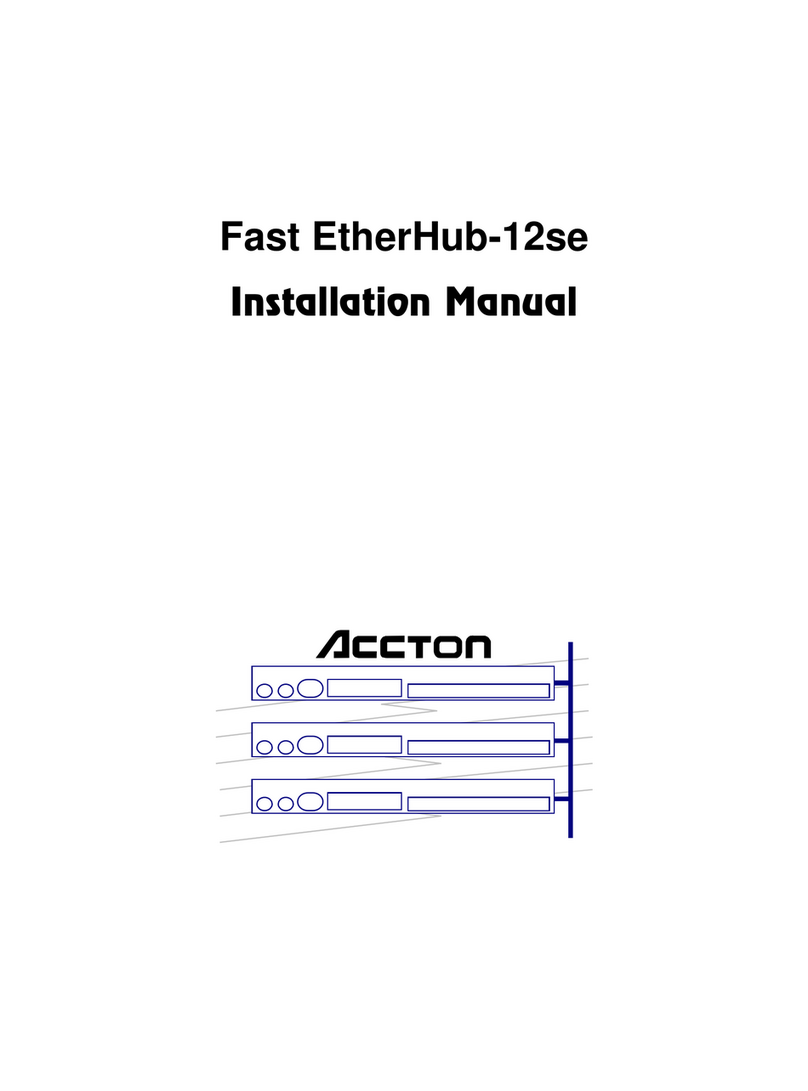
Accton Technology
Accton Technology Fast EtherHub-12se installation manual