PVA FC100-CF User manual

Film Coat Dispense Valve
FC100-CF
Operation Manual
Revision B
INNOVATION. PRECISION. EXCELLENCE.

FC100-CF Manual
Revision B /February 2022 Page 2 of 23
This document is based on information available at the time of its publication. While efforts
have been made to ensure the contents of this manual are accurate, the information
contained herein does not purport to cover all specific details or variations in hardware, or
to provide for every possible contingency in connection with installation, operation, or
maintenance. Features may be described herein which are not present in all hardware and
software systems. Precision Valve and Automation, Inc. assumes no obligation of notice to
holders of this document with respect to changes subsequently made.
Precision Valve and Automation, Inc. makes no representation or warranty, expressed,
implied, or statutory with respect to, and assumes no responsibility for the accuracy,
completeness, sufficiency, or usefulness of the information contained herein. No warranties
of merchantability or fitness for purpose shall apply.
This document, including the information contained herein, is the property of
Precision Valve and Automation, Inc. and is considered confidential and proprietary
information. It is delivered on the express condition that it not be used, disclosed, or
reproduced, in whole or in part, for any reason without prior written consent of
Precision Valve and Automation, Inc.
Copyright © 2021
Precision Valve and Automation, Inc.
All Rights Reserved.

FC100-CF Manual
Revision B /February 2022 Page 3 of 23
Table of Contents
PVA Contact Information........................................................................................................4
Document History.....................................................................................................................4
System Description ..................................................................................................................5
Nozzle Options...........................................................................................................................6
Tool Kit.........................................................................................................................................9
Operation ..................................................................................................................................10
Periodic Maintenance ............................................................................................................10
Routine Cleaning and Disassembly......................................................................................11
Assembly Instructions...........................................................................................................13
General ..............................................................................................................................13
Air Section ........................................................................................................................13
Fluid Section ....................................................................................................................14
Assemble Section ...........................................................................................................14
Spare Parts...............................................................................................................................15
Drawings...................................................................................................................................16
Bill of Materials ........................................................................................................................19

FC100-CF Manual
Revision B /February 2022 Page 4 of 23
Introduction
Before you operate this valve, read the operation and setup manual. This will help you to
become familiar with the product and ensure successful operation.
If any questions or problems arise, contact PVA’s Technical Support department.
PVA Contact Information
Main Office PVA
Six Corporate Drive
Halfmoon, NY 12065
Tel +1-518-371-2684
Fax +1-518-371-2688
Website: http://www.pva.net
Email: info@pva.net
Technical Support
Tel +1-844-734-0209
Email: cs@pva.net
Document History
Revision
Revision Date
Reason for Changes
B
December 2021
Updated Bill of Materials and Drawings
A
Initial Release
Note: All photographs and CAD model representations in this document are a
“general representation” of the system and its components. The actual appearance
of the system and its components can differ based upon customer specific
configuration.

FC100-CF Manual
Revision B /February 2022 Page 5 of 23
System Description
The FC100-CF is a front closing stainless steel film coat dispense valve designed to apply
fluids in a non-atomized method to deliver transfer efficiency greater than 99%. This valve
is typically used for low viscosity coatings.
The FC100-CF has a divorced design comprising of two major sections. These include:
1. Air section (red anodized portion)
2. Fluid section (stainless steel portion)
The air section is an aluminum body with a simple piston/cylinder combination used to
open and close the valve. A micrometer adjustment, Figure 9: Micrometer Adjustment
Breakdown, in the upper air body controls how far the piston and needle assembly can
retract thus regulating the rate of fluid flow. The micrometer will display a distance that the
piston and needle will travel.
The fluid section is a stainless steel body, which includes a needle and seat combination to
control fluid flow. Fluid dispenses as the needle retracts out of the seat, then stops as the
needle moves back into the seat. The micrometer adjustment regulates the distance that
the needle can retract out of the seat, thus controlling the orifice size and the rate of fluid
flow. A film tip nozzle at the end of the valve will fan the liquid outward without the need
for atomizing air to apply thin ribbon coating patterns. Fluids typically include solvent
based or low viscosity conformal coatings.
Wetted parts on the FC100-CF include:
•303, 304 stainless steel
•Teflon
•Kalrez

FC100-CF Manual
Revision B /February 2022 Page 6 of 23
Nozzle Options
The FC100-CF valve is available with a variety of film coat nozzles. All nozzles have a
different orifice to allow for a maximum flow rate and a slit to create a fan shaped flow
pattern. The width of the fan pattern is determined by the distance from the valve nozzle
to the substrate. Different nozzles are easily interchangeable to the valve by removing the
nozzle cap (5).
Nozzle sizes are selected based on the viscosity of the coating fluid and desired coating
thickness. PVA’s application engineers can help you select the best nozzle for your valve.
Valves are supplied from the factory with one nozzle included.
Below is a chart showing the part numbers that are used to specify the nozzle that is
supplied with a valve and the available orifices, flow rates, and fan widths, for each
individual nozzle.
Nozzle Part Number
Flow Rate
Fan Width
P1150013-A 0.05 gpm @ 500psi. 8.0-9.99 mm @ 0.5 in distance
P1150013-B 0.05 gpm @ 500psi. 10.0-10.99 mm @ 0.5 in distance
P1150013-C 0.05 gpm @ 500psi. 11.0-12.50 mm @ 0.5 in distance
Figure 1: Nozzle Options

FC100-CF Manual
Revision B /February 2022 Page 7 of 23
Safety
Due to material contents being under pressure eye protection is required for operators.
Refer to MSDS sheets on material being dispensed for other precautions.

FC100-CF Manual
Revision B /February 2022 Page 8 of 23
Setup
The FC100-CF requires a 2-position, 4-way air solenoid valve to actuate the air section.
The valve should be operated with clean, dry air between 60-100 psi. Two #10-32 threaded
air ports are located on the air section of the valve. The port located furthest from the
midsection of the valve is air to close the valve. The port located closest to the mid-section
of the valve is air to open the valve. Quick connect air fittings are typically supplied with
the FC100-CF to fit 5/32 in tubing.
Note: The valve should normally be in the closed position.
Fluid is supplied to the FC100-CF through the 1/8 in fnpt port located on the stainless steel
fluid section of the valve.
Figure 2: Solenoid Valve

FC100-CF Manual
Revision B /February 2022 Page 9 of 23
Tool Kit
PVA offers standard tool kits for all dispensing valves. The tool kit for the FC100-CF
includes all necessary tools and lubricating grease to perform maintenance on this
dispense valve.
Quantity
Part Number
Description
2 0266244 8 in Adjustable Wrench
2 26563 3/32 in Allen Key
1 26561 5/64 in Allen Key
1 26559 1/16 in Allen Key
1 5516A18 Tweezers
1 B62-0752 2.5cc Mineral Oil Lubrication Kit
1 B62-2048 2.5cc Silicone Lubricant
1 9570K71 Hook and Pick Set
1 0266255 Pliers
2 53085A61 Soft Plastic Cover for Pliers
1 PB135/2 Micrometer Screw Driver, #2
1 PT17184 Micrometer Adjustment Wrench
1 MM115 Removable Thread Locker
Figure 3: B12-1986 Tool Kit

FC100-CF Manual
Revision B /February 2022 Page 10 of 23
Operation
Refer to Figure 8: FC100-CF Cross Section for part reference numbers.
1. Plumb up the valve as outlined above in the Setup procedures.
2. Regulate the air pressure operating the valve between 60-100 psi.
3. Ensuring the valve is not aimed toward anyone, cycle the valve several times. When
the valve is cycling, the piston can be heard hitting the micrometer adjustment, and
the needle (2) can be seen going up and down in the center.
Note: If the valve is not cycling properly, refer to the Troubleshooting section.
4. When the fluid delivery system is connected to the valve, pressurize the material to
be dispensed.
5. Once again, cycle the valve open to purge. Fluid should begin to dispense from the
for tip nozzle of the valve, continue dispensing until all air is removed.
6. Check the fluid connection and the packing nut (17) for leaks.
Note: If the valve is leaking, refer to the Troubleshooting section.
7. Turn the micrometer adjustment head (6) until the desired flow rate is achieved.
Turning the adjustment clockwise toward zero will decrease the material flow rate
and counterclockwise will increase the material flow rate. If the micrometer
adjustment is turned all the way down to zero, it will stop fluid flow entirely.
8. Once the micrometer setting is determined, the collar (Figure 9, Part E) on the
micrometer head (6) can be turned clockwise to lock the adjustment.
Periodic Maintenance
Refer to Figure 7: FC100-CF Cross Section and Figure 8 for location of parts referenced in
the following procedures.
1. Lubricate the packing (16) on the FC100-CF valve every 200 hrs by placing a few
drops of mineral oil or other light oil inside the packing nut.
2. The packing nut (17) may require occasional tightening, as wear occurs in order to
prevent leaks through the packing.
Note: PVA offers a 2.5cc mineral oil lubrication kit; Part#: B62-0752

FC100-CF Manual
Revision B /February 2022 Page 11 of 23
Routine Cleaning and Disassembly
Cleaning and rebuilding the valve will be required from time to time. A spare parts kit,
Figure 4: FC1-C4-SP Spare Parts Kit, is available with all the normal wear parts included.
1. Begin disassembly by removing air and fluid pressure from the valve.
2. Remove all the pneumatic tubing and fluid delivery fittings, hoses, etc. from the
valve.
3. Using the tip of a 3/32 in Allen key, loosen the packing nut (17).
4. Using the same 3/32 in Allen key, evenly remove the two machine screws (9) that
are located on the same corners as the fluid section standoffs (4).
Note: During removal there is a spring (11) forcing the air section away from the fluid
section.
5. Pull the air section (red anodized portion) away from the fluid section (stainless
steel portion).
6. Clean off the tip of the stainless steel needle (2).
7. From the fluid section of the valve, unthread and remove the packing nut (17), and
the packing (16).
8. Using an adjustable wrench, unthread and remove the nozzle cap (5) from the
nozzle adapter (1) to remove the film coat nozzle.
9. Remove the 006 Kalrez O-ring (19) from the nozzle adapter (1). Then using an
adjustable wrench, unthread and remove the nozzle adapter (1) from the fluid
section (4).
10. Using pliers, pull the seat (15) out of the fluid section (4) and remove the 006 Kalrez
O-ring (19) from the seat.
Note: If the seat is stuck, it can be pushed through from the opposite side of the fluid
section.
11. Clean all wetted parts thoroughly with an appropriate solvent.
12. On the air section, use a standard 3/32 in Allen key to evenly remove the final two
machine screws (8) that thread into the end cap (12).

FC100-CF Manual
Revision B /February 2022 Page 12 of 23
Note: During removal, the spring (11) will force the air section apart.
13. Separate the upper air body (3) from the lower air body (13) to remove the spring
(11) then slide the end cap (12) off the needle (2).
14. Holding the lower air body (13) in one hand, grab the needle (2) and push the needle
and piston (14) assembly out of the lower air body.
15. Remove the 004 Buna O-ring (18) from the lower air body (13).
16. Hold the piston (14) with an adjustable wrench then using the 5/64 in Allen key
unthread and remove the set screw (10) to remove the needle (2) and remove the
014 Buna O-ring (21) from the piston (14).
17. Remove the 014 Buna O-ring (21) from the upper air body (3) then use a 1/16 in
Allen key to remove the set screw (7).
18. Using pliers grip the collar (Figure 9, Part E) or body (Figure 9, Part D) of the
micrometer head (6) and turn counterclockwise to loosen then unthread and
remove from the upper air body (3) by hand.
19. Remove the 007 Buna O-ring (20) from the micrometer head (6).
20. Replace components with spares provided in the spare parts kit shown in Figure 4.

FC100-CF Manual
Revision B /February 2022 Page 13 of 23
Assembly Instructions
General
•Lubricate all O-rings with a small amount of silicone grease.
•Apply a small amount of removable thread locker to the set screw (10).
•Assemble the air section and fluid section separately prior to connecting the
assemblies.
Air Section
1. Mount one 007 Buna O-ring (20) on the end (Figure 9, Part F) of the micrometer (6)
and slide it up to the threads.
2. Thread the micrometer head (6) into the upper air body (3) hand tight.
3. Holding the collar (Figure 9, Part E) of the micrometer head (6), turn the dial (Figure
9, Part C) counterclockwise until the number 5 can be seen on the gauge (Figure 9,
Part D).
4. Using pliers, grab the gauge section of the micrometer (Figure 9, Part D) and turn
clockwise to snug it onto the upper air body (3).
5. Use a 1/16 in Allen key to assemble the set screw (7) into the upper air section (3)
securing the micrometer head (6) in place.
6. Mount one 014 Buna O-ring (21) on the end of the upper air body (3).
7. Drop the needle (2) into the piston (14) and assemble with the set screw (10) using
an adjustable wrench and 5/64 in Allen key to tighten.
8. Mount the 014 Buna O-ring (21) onto the piston (14).
9. Apply a small amount of silicone grease to the inside of the lower air body (13) then
drop in the piston and needle assembly.
10. Mount the 004 Buna O-ring (18) on the end of the needle and slide it down into the
groove in the end of the lower air body (13).
11. Slide the end cap (12) onto the needle up to the lower air body (13), place the spring
(11) on top of the piston (14), and assemble the two air bodies using two machine
screws (8) tightening with a 3/32 in Allen key. Ensure the air holes are lined up on
the same face.

FC100-CF Manual
Revision B /February 2022 Page 14 of 23
Fluid Section
1. Drop the packing (16) into the fluid section (4), and screw in the packing nut (17),
leaving finger tight until assembled with the air section.
2. Mount one 006 Kalrez O-ring (19) on the seat (15) and push the seat into the bottom
of the fluid section (4). When inserting the seat, work the O-ring into the fluid body
with a finger to prevent shearing of the edge of the O-ring.
3. Thread the nozzle adapter (1) onto the fluid body (4) and tighten with an adjustable
wrench.
4. Place one 006 Kalrez O-ring (19) into the groove of the nozzle adapter (1).
5. Drop the film coat nozzle into the bottom groove of the nozzle cap (5) and thread
the assembly onto the nozzle adapter (1).
Assemble Section
1. Ensure the micrometer adjustment head (6) is backed out far enough so at least the
number 1 can be seen on the gauge (Figure 9, Part D).
2. Apply a small amount of silicone grease to the end of the needle (2) and insert it into
the packing nut (17). Connect the sections using the two machine screws (9),
tightening them down evenly using a 3/32 in Allen key.
3. Using the tip of a 3/32 in Allen key, tighten the packing nut (17).

FC100-CF Manual
Revision B /February 2022 Page 15 of 23
Spare Parts
PVA offers standard spare parts kits for all dispensing valves. These kits are stocked for
immediate shipment and allow replacement of all wearable parts of the valve.
The spare parts kit for the FC100-CF, product number FC1-C4-SP, includes the following
components:
Quantity
Part Number
Description
1
V302
Seat
1
114-5247
Needle
1
V305
Packing, Teflon
2
VLV-014B
O-ring, Buna
1
VLV-007B
O-ring, Buna
2
VLV-006K
O-ring, Kalrez
1
VLV-004B
O-ring, Buna
1
PT17184
Micrometer Adjust Wrench
Figure 4: FC1-C4-SP Spare Parts Kit

FC100-CF Manual
Revision B /February 2022 Page 16 of 23
Drawings
Figure 5: FC100-CF Dimensions

FC100-CF Manual
Revision B /February 2022 Page 17 of 23
Figure 6: FC100-CF Flow Pattern
Figure 7: FC100-CF Cross Section

FC100-CF Manual
Revision B /February 2022 Page 18 of 23
Figure 8: FC100-CF Cross Section
Figure 9: Micrometer Adjustment Breakdown

FC100-CF Manual
Revision B /February 2022 Page 19 of 23
Bill of Materials
Item and Part Number
Description
Quantity
1. 114-1658
Nozzletech Adapter
1
2. 114-5247
FC100 Needle
1
3. 114-6556
Upper Air Body
1
4. 114-6933
Fluid Body
1
5. 114-8053
Nozzle Cap
1
6. 01423 Micrometer Head 1
7. 01469 Set Screw, #5 – 40 in x 3/16 in 1
8. SHCS #5 – 40 in x 1 ¾ in Socket Head Cap Screw 2
9. SHCS #5 – 40 in x 2 in
Socket Head Cap Screw
2
10. V001
Set Screw
1
11. V050
Spring
1
12. V200
End Cap
1
13. V201
Lower Air Body
1
14. V202
Piston
1
15. V302
Seat
1
16. V305
Packing
1
17. V306 Packing Nut 1
18. VLV-004B O-Ring, -004, Buna-N 1
19. VLV-006K
O-Ring, -006, Kalrez
2
20. VLV-007B
O-Ring, -007, Buna-N
1
21. VLV-014B
O-Ring, -014, Buna-N
2

FC100-CF Manual
Revision B /February 2022 Page 20 of 23
Troubleshooting
Troubleshooting Problem
Possible Cause
Corrective Action
Valve does not cycle
Air pressure to the air section
is too low
Increase the air pressure to
60-100 psi
Packing nut is too tight
Loosen the packing nut
until valve begins to cycle;
retighten the packing nut
Micrometer adjustment bolt
has bottomed out
Back out the micrometer
adjustment bolt by turning
it counterclockwise
Material is cured in the valve
Disassemble and clean the
valve
Valve was assembled without
lubricating the O-ring seals
Disassemble the valve,
lubricate the seals, and
re-assemble the valve
Material leaks from the
valve tip
Packing nut is too tight
Loosen the packing nut
Needle and/or seal are worn
Replace the parts as
necessary
Air bubble trapped in fluid
body or in nozzle adapter
Flip the valve upside down
and cycle until the air
bubbles are removed
O-ring is worn or missing the
nozzle extension
Replace the O-ring
Valve leaks from the
mid-section
Packing nut is loose
Tighten the packing nut
until it is snug
Packing is worn
Replace the packing
Valve does not dispense
anything
Fluid pressure is too low
Increase the fluid pressure
Material cured in fluid section Disassemble the valve and
clean
Micrometer adjustment bolt is
set too close to zero
Back out the micrometer
adjustment bolt by turning
it counterclockwise
Air bubbles in fluid
Valve is not properly purged
Flip the valve upside down
and cycle until the air
bubbles are removed
Problem with the fluid
delivery system
Diagnose and repair
Dispense rate is too fast
The micrometer adjustment
bolt is set too far from the
zero mark
Turn the micrometer
adjustment bolt clockwise
toward the zero mark
Table of contents
Other PVA Control Unit manuals
Popular Control Unit manuals by other brands

Aprimatic
Aprimatic ROLL 500S installation instructions

Brooks Instrument
Brooks Instrument PC100 Series Installation and operation manual
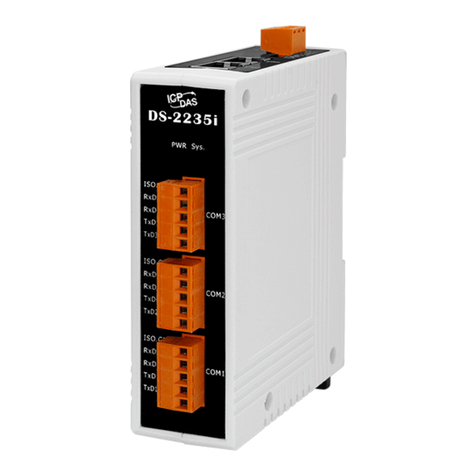
ICP DAS USA
ICP DAS USA DS-2200 Series quick start
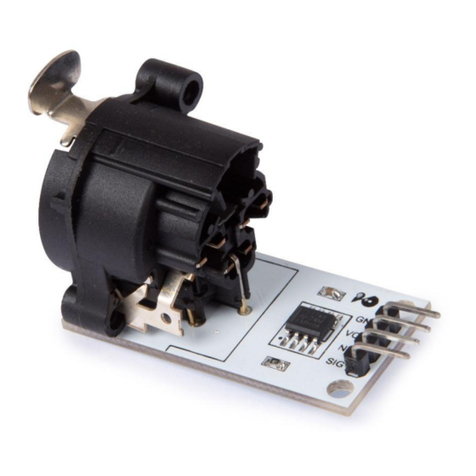
Velleman
Velleman VMA432 user manual

Schmalz
Schmalz 10.02.02.02795 operating instructions
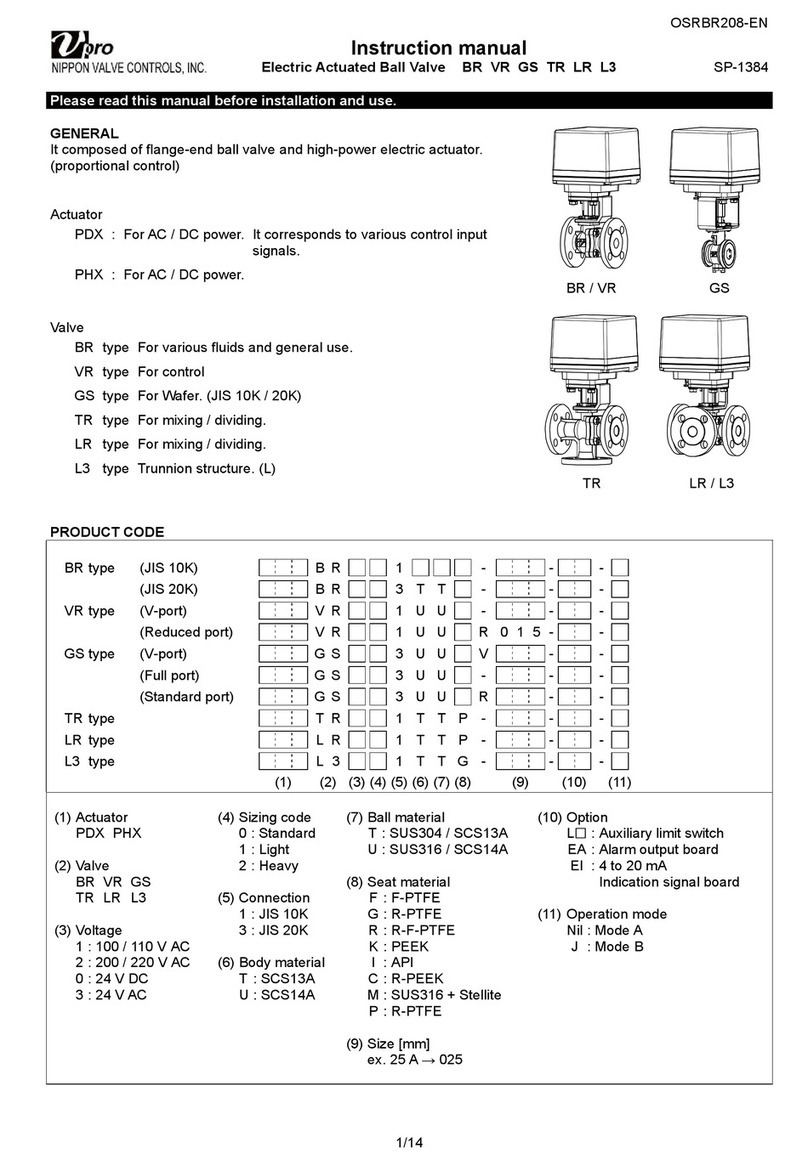
VPro
VPro BR Series instruction manual