Siemens SINUMERIK 840D Instruction sheet




















Other manuals for SINUMERIK 840D
18
This manual suits for next models
1
Other Siemens Control Unit manuals
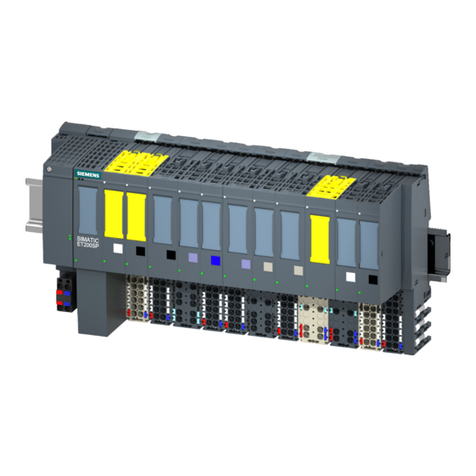
Siemens
Siemens SIMATIC ET 200SP User manual

Siemens
Siemens SIRIUS 8WD4428-0BF User manual
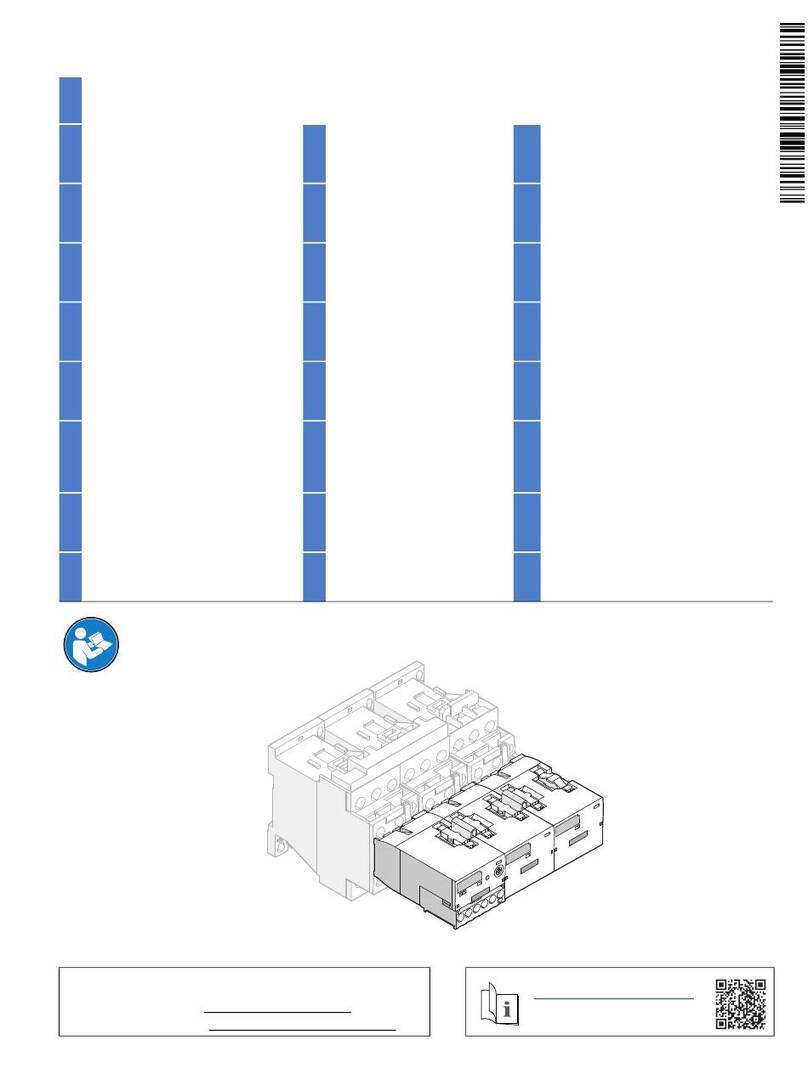
Siemens
Siemens SIRIUS 3RA2711-0DB00 User manual
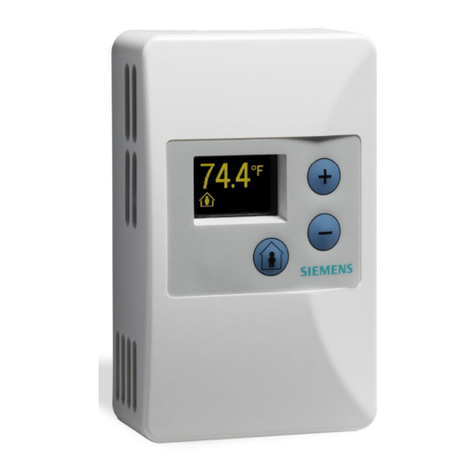
Siemens
Siemens QPA228.FWNC Series User manual
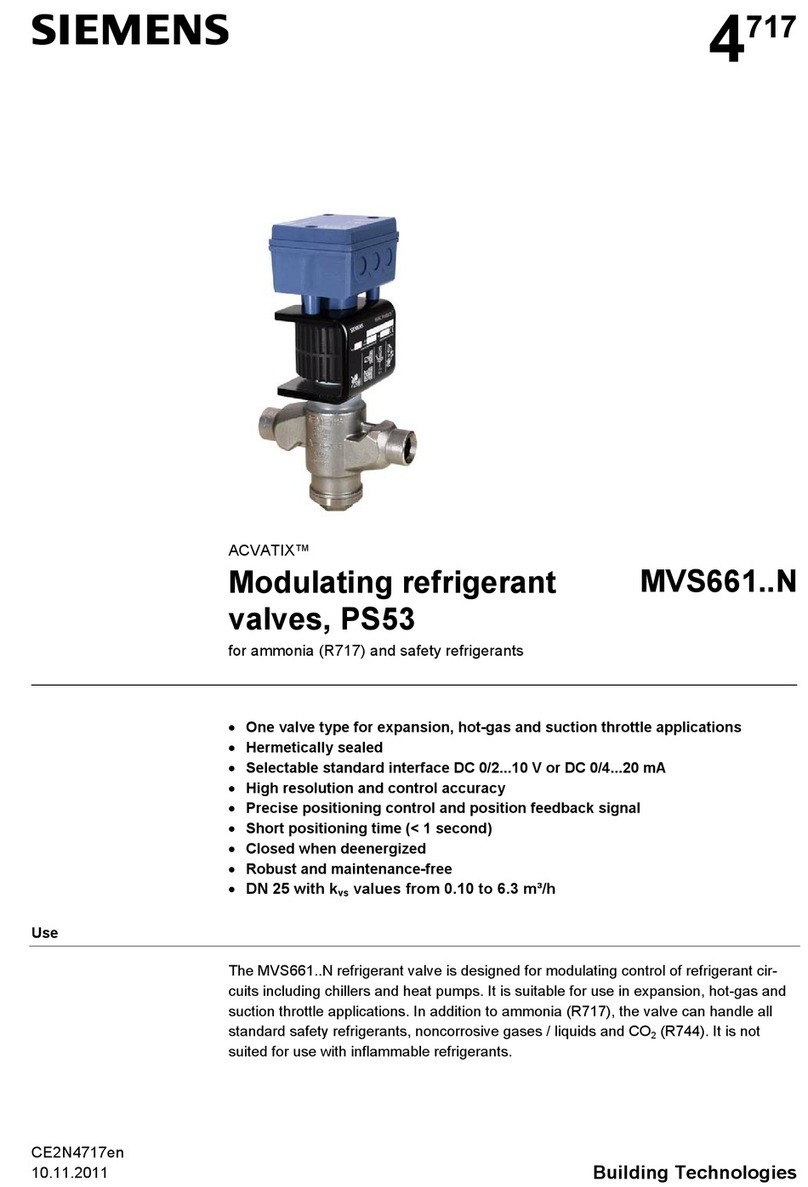
Siemens
Siemens ACVATIX PS53 User manual
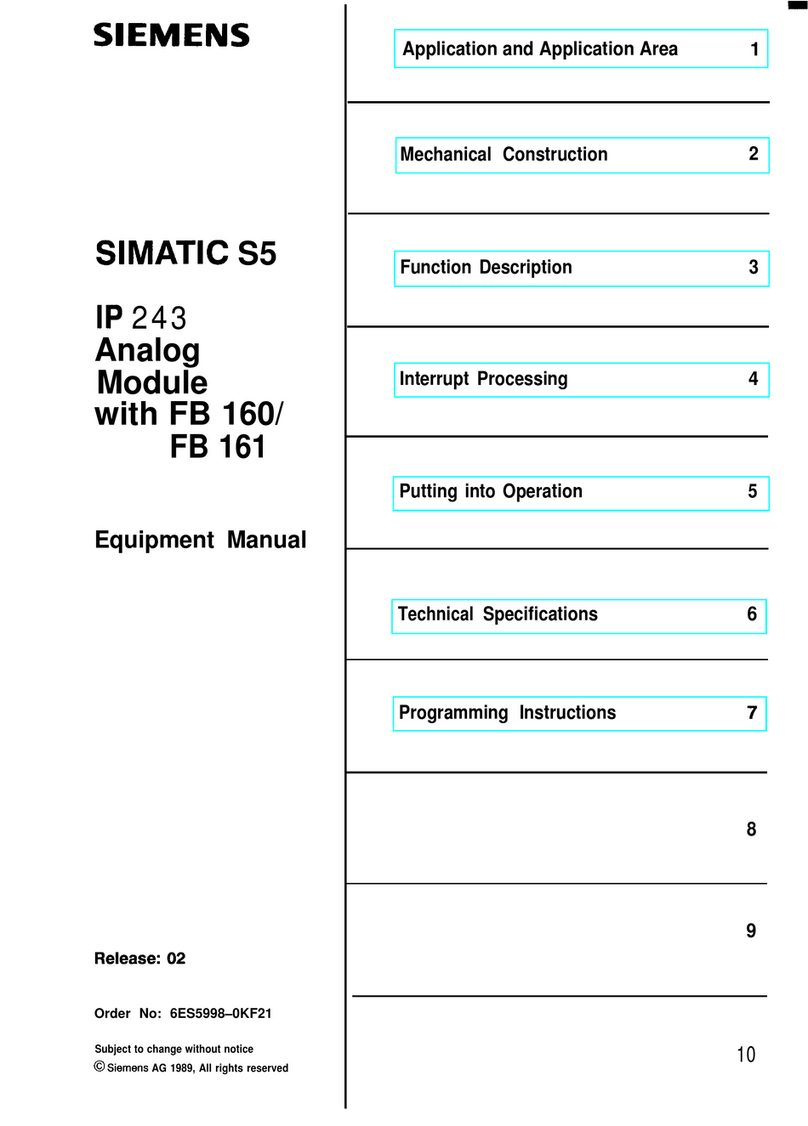
Siemens
Siemens SIMATIC S5 1P 243 Technical Document
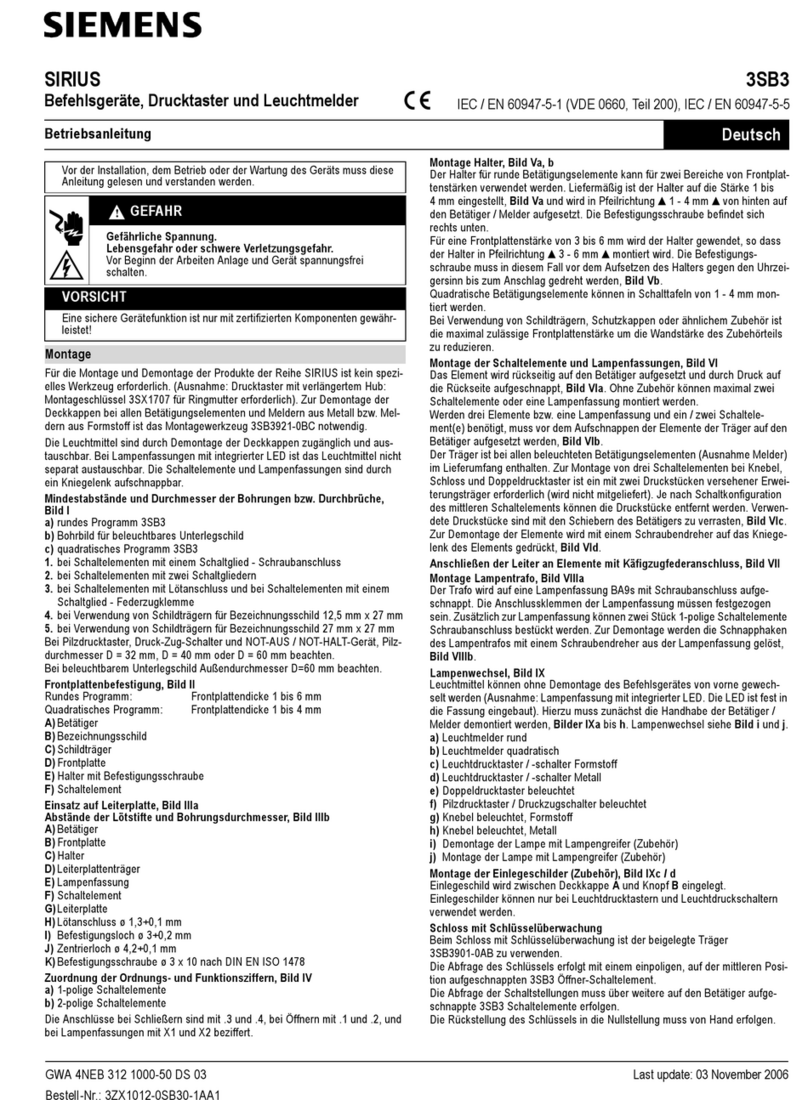
Siemens
Siemens SIRIUS 3SB3 User manual
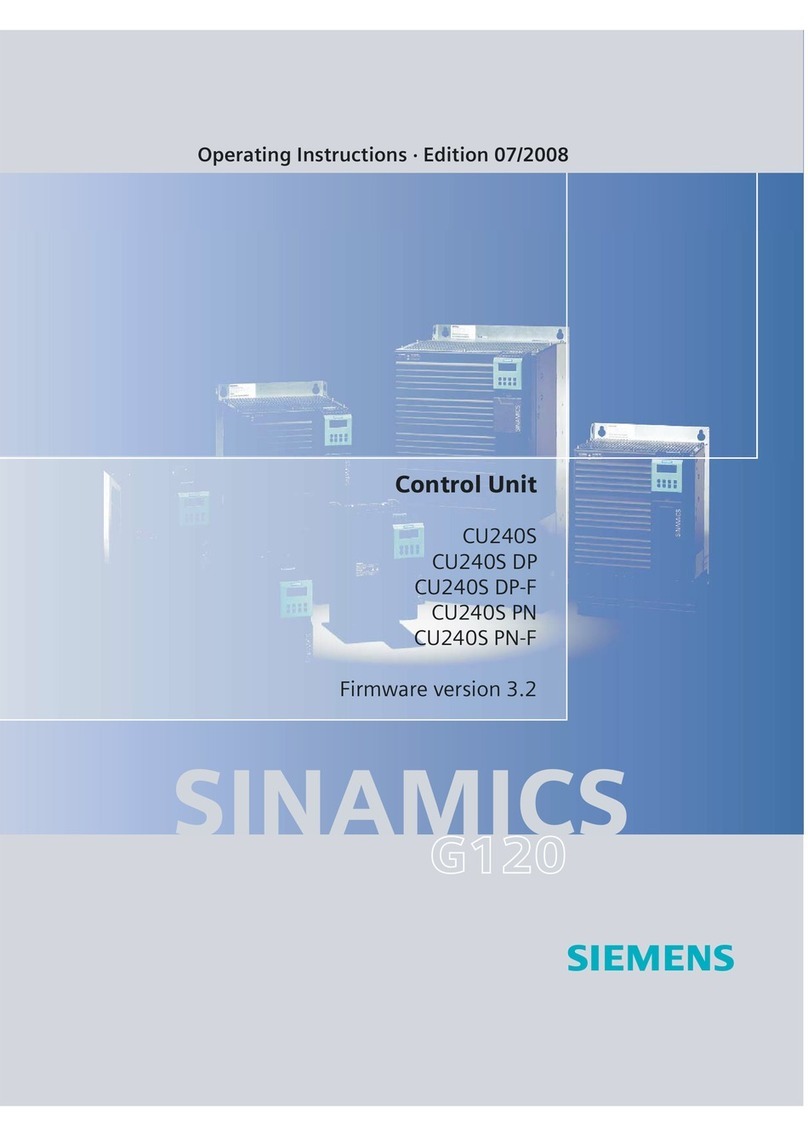
Siemens
Siemens CU240S DP-F User manual
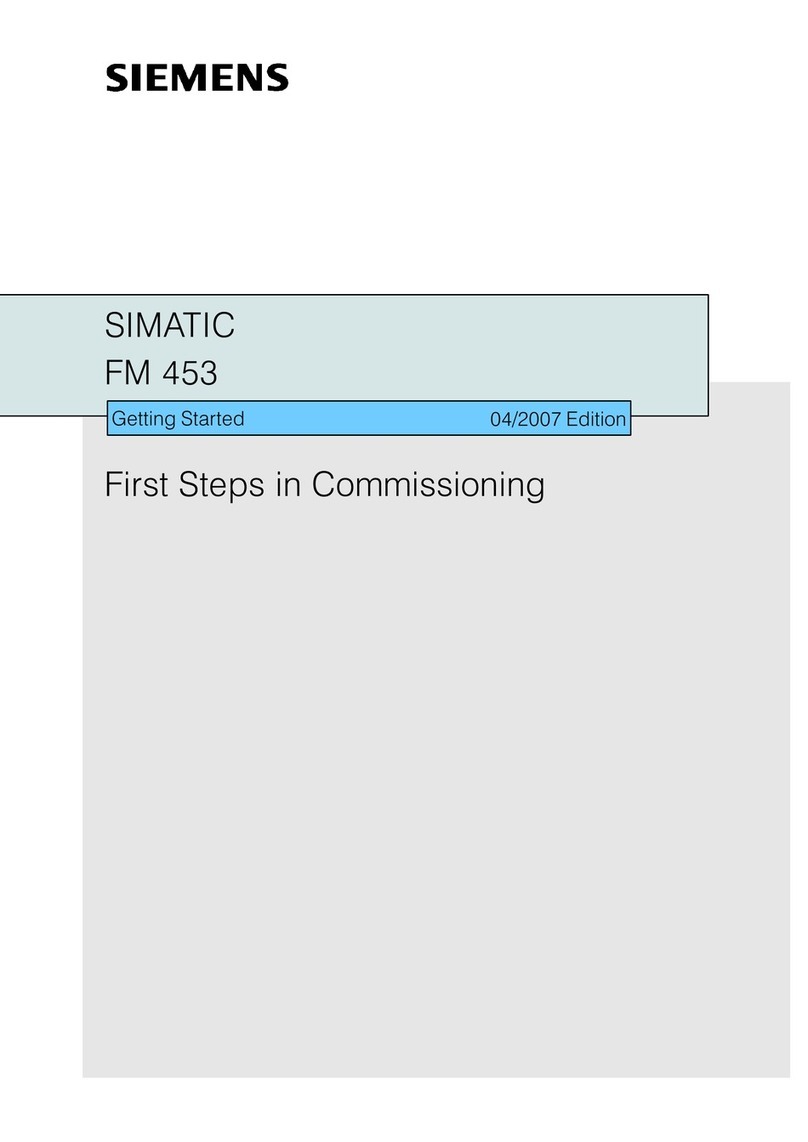
Siemens
Siemens SIMATIC FM 453 User manual
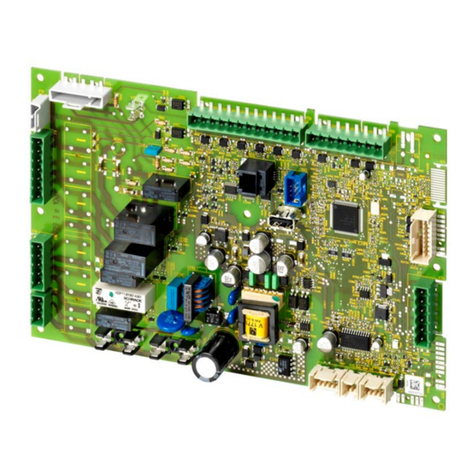
Siemens
Siemens LMS14 User manual
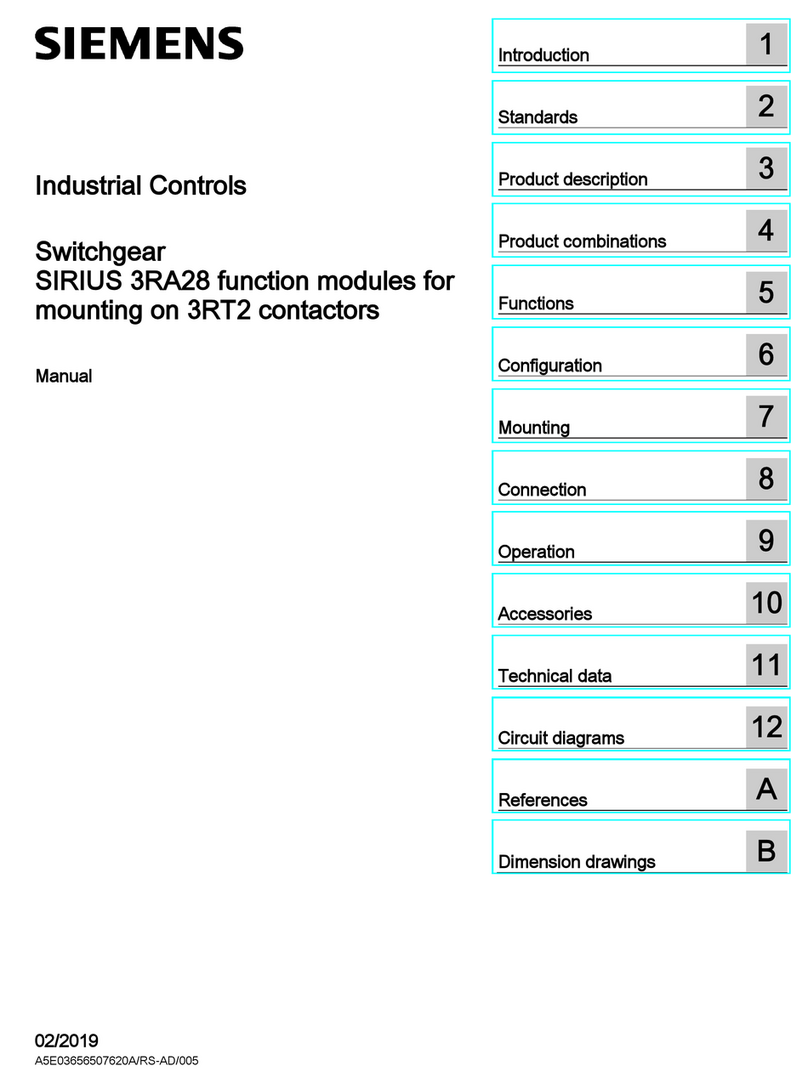
Siemens
Siemens SIRIUS 3RT2 User manual
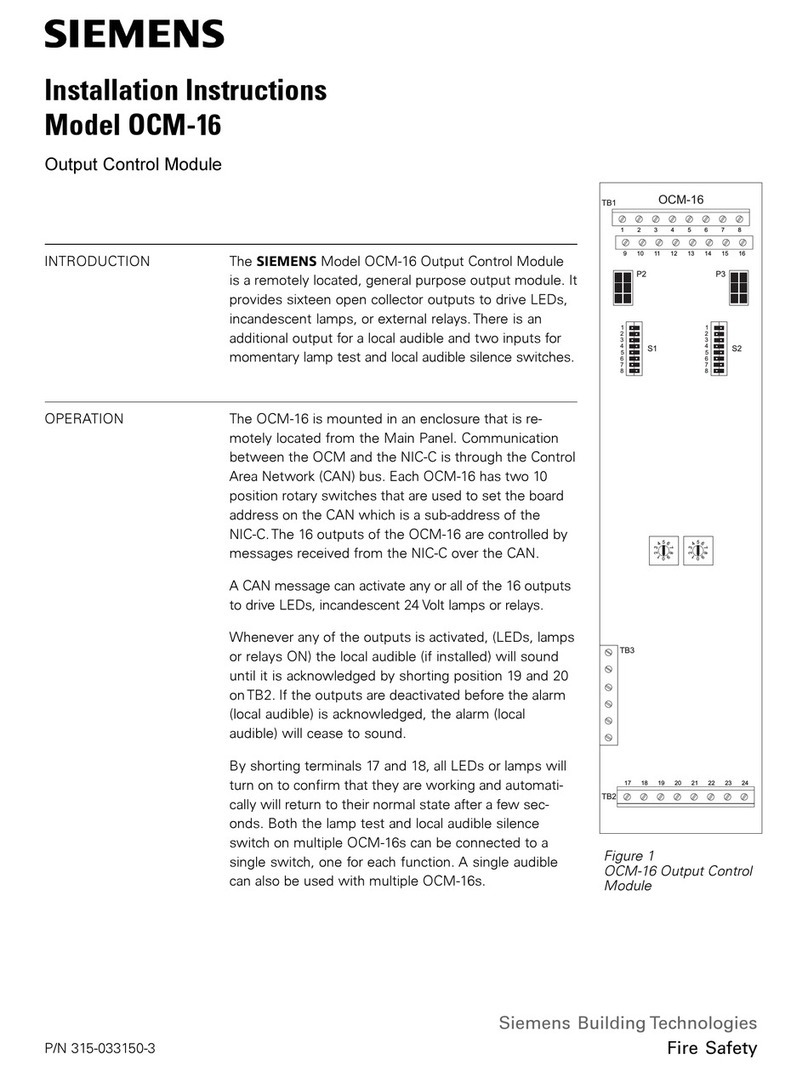
Siemens
Siemens OCM-16 User manual
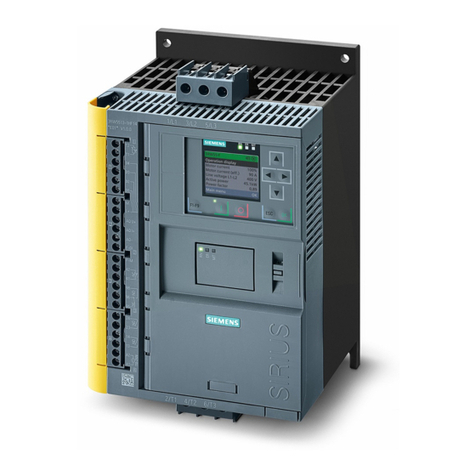
Siemens
Siemens SIRIUS 3RW5 series Technical Document

Siemens
Siemens SIRIUS ACT 3SU18 N Series User manual

Siemens
Siemens MM7000 Series User manual

Siemens
Siemens XC1001-A Manual
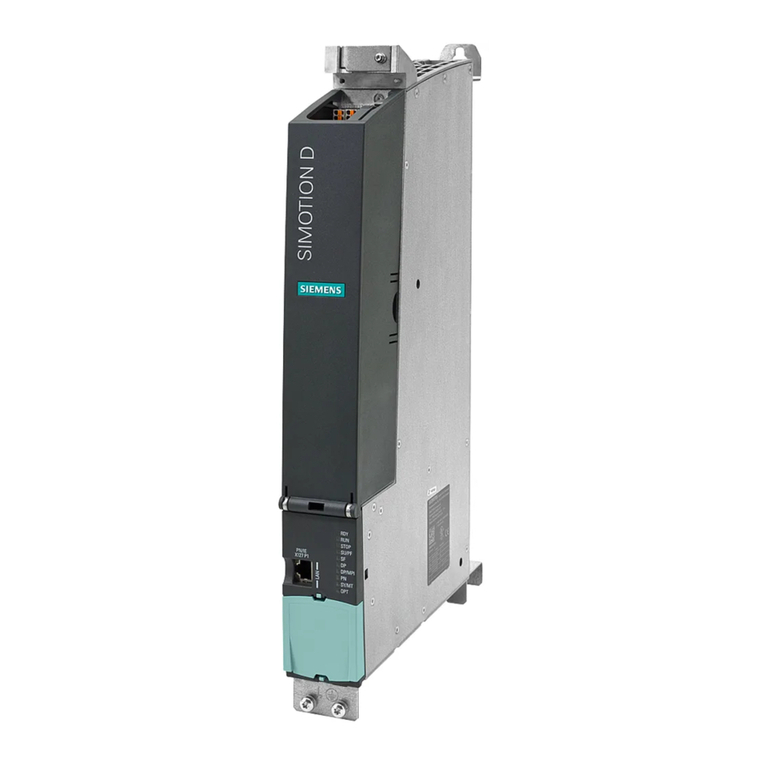
Siemens
Siemens SIMOTION D4 5-2 Series User manual

Siemens
Siemens Synco RMZ792 Operator's manual
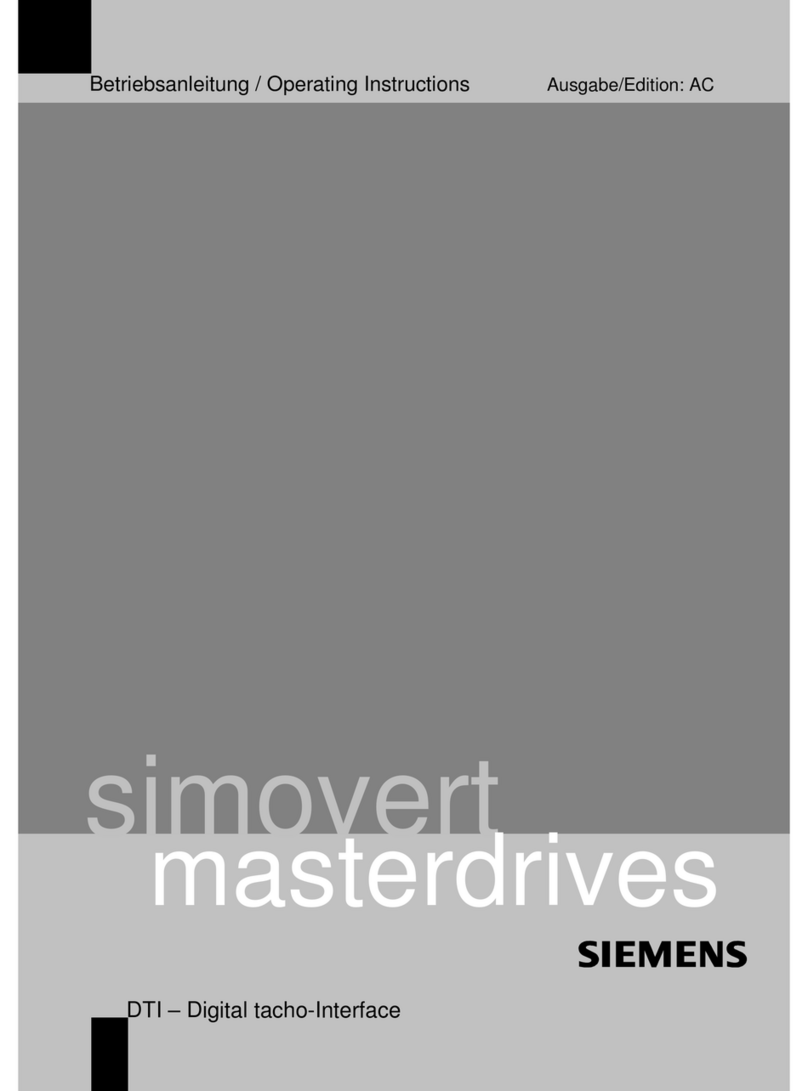
Siemens
Siemens simovert masterdrives User manual
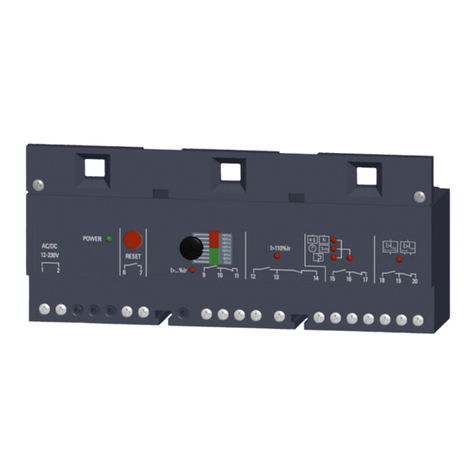
Siemens
Siemens 3VT9500-6AE00 User manual