YASKAWA CP 341 User manual

CP | 341-1CH01 | Manual
HB130 | CP | 341-1CH01 | en | 18-40
VIPA System 300S
CP 341 RS422/485
www.vipa.com/en/service-support/manuals

341-1CH01_000_CP 341 RS422/485,1,EN - © 2018
VIPA GmbH
Ohmstr. 4
91074 Herzogenaurach
Telephone: +49 9132 744-0
Fax: +49 9132 744-1864
Email: [email protected]
Internet: www.vipa.com

Table of contents
1 General.................................................................................................................... 5
1.1 Copyright © VIPA GmbH ................................................................................. 5
1.2 About this manual............................................................................................. 6
1.3 Safety information............................................................................................. 7
2 Basics...................................................................................................................... 8
2.1 Safety information for users.............................................................................. 8
2.2 Basics - ISO/OSI reference model................................................................... 9
2.3 CP 341-1CH01............................................................................................... 10
2.4 General data................................................................................................... 11
3 Assembly and installation guidelines................................................................ 13
3.1 Installation dimensions................................................................................... 13
3.2 Assembly standard bus.................................................................................. 14
3.3 Installation guidelines..................................................................................... 16
4 Hardware description........................................................................................... 18
4.1 Properties....................................................................................................... 18
4.2 Structure......................................................................................................... 19
4.3 Technical data................................................................................................. 23
5 Deployment........................................................................................................... 26
5.1 Fast introduction............................................................................................. 26
5.2 Hardware configuration.................................................................................. 28
5.2.1 Properties.................................................................................................... 29
5.3 Communication with the user program........................................................... 31
5.4 Firmware update............................................................................................. 33
5.4.1 Firmware update with Siemens parameterization tool................................. 33
5.4.2 Firmware update at deployment of a SPEED7 CPU................................... 34
5.4.3 Show CP firmware version.......................................................................... 35
6 Communication protocols................................................................................... 36
6.1 Overview......................................................................................................... 36
6.2 ASCII.............................................................................................................. 37
6.2.1 ASCII - Parameter....................................................................................... 38
6.3 3964(R) .......................................................................................................... 42
6.3.1 Basics 3964(R)............................................................................................ 42
6.3.2 Proceeding.................................................................................................. 43
6.3.3 3964(R) - Parameter ................................................................................... 44
6.4 Modbus........................................................................................................... 48
6.4.1 Basics Modbus............................................................................................ 48
6.4.2 Modbus Master - Parameter........................................................................ 49
6.4.3 Modbus Master - Functionality.................................................................... 55
6.4.4 Modbus Master - Function codes................................................................ 58
6.4.5 Modbus Slave - Parameter.......................................................................... 66
6.4.6 Modbus Slave - Functionality...................................................................... 70
6.4.7 Modbus Slave - Communication with the user program.............................. 73
6.4.8 Modbus Slave - Function codes.................................................................. 79
7 Diagnostics and error behavior.......................................................................... 92
7.1 Diagnostics functions overview...................................................................... 92
7.2 Diagnostics via FB STATUS........................................................................... 93
VIPA System 300S Table of contents
HB130 | CP | 341-1CH01 | en | 18-40 3

7.3 Diagnostics via diagnostic buffer.................................................................. 103
7.4 Diagnostics by diagnostics interrupt............................................................. 104
VIPA System 300S
Table of contents
HB130 | CP | 341-1CH01 | en | 18-40 4

1 General
1.1 Copyright © VIPA GmbH
This document contains proprietary information of VIPA and is not to be disclosed or used
except in accordance with applicable agreements.
This material is protected by the copyright laws. It may not be reproduced, distributed, or
altered in any fashion by any entity (either internal or external to VIPA), except in accord-
ance with applicable agreements, contracts or licensing, without the express written con-
sent of VIPA and the business management owner of the material.
For permission to reproduce or distribute, please contact: VIPA, Gesellschaft für Visuali-
sierung und Prozessautomatisierung mbH Ohmstraße 4, D-91074 Herzogenaurach, Ger-
many
Tel.: +49 9132 744 -0
Fax.: +49 9132 744-1864
EMail: [email protected]
http://www.vipa.com
Every effort has been made to ensure that the information contained in
this document was complete and accurate at the time of publishing. Nev-
ertheless, the authors retain the right to modify the information.
This customer document describes all the hardware units and functions
known at the present time. Descriptions may be included for units which
are not present at the customer site. The exact scope of delivery is
described in the respective purchase contract.
Hereby, VIPA GmbH declares that the products and systems are in compliance with the
essential requirements and other relevant provisions. Conformity is indicated by the CE
marking affixed to the product.
For more information regarding CE marking and Declaration of Conformity (DoC), please
contact your local VIPA customer service organization.
VIPA, SLIO, System 100V, System 200V, System 300V, System 300S, System 400V,
System 500S and Commander Compact are registered trademarks of VIPA Gesellschaft
für Visualisierung und Prozessautomatisierung mbH.
SPEED7 is a registered trademark of profichip GmbH.
SIMATIC, STEP, SINEC, TIA Portal, S7-300, S7-400 and S7-1500 are registered trade-
marks of Siemens AG.
Microsoft and Windows are registered trademarks of Microsoft Inc., USA.
Portable Document Format (PDF) and Postscript are registered trademarks of Adobe
Systems, Inc.
All other trademarks, logos and service or product marks specified herein are owned by
their respective companies.
All Rights Reserved
CE Conformity Declaration
Conformity Information
Trademarks
VIPA System 300S General
Copyright © VIPA GmbH
HB130 | CP | 341-1CH01 | en | 18-40 5

Contact your local VIPA Customer Service Organization representative if you wish to
report errors or questions regarding the contents of this document. If you are unable to
locate a customer service centre, contact VIPA as follows:
VIPA GmbH, Ohmstraße 4, 91074 Herzogenaurach, Germany
Telefax: +49 9132 744-1204
EMail: [email protected]
Contact your local VIPA Customer Service Organization representative if you encounter
problems with the product or have questions regarding the product. If you are unable to
locate a customer service centre, contact VIPA as follows:
VIPA GmbH, Ohmstraße 4, 91074 Herzogenaurach, Germany
Tel.: +49 9132 744-1150 (Hotline)
EMail: [email protected]
1.2 About this manual
This manual describes the CP 341-1CH01 of the System 300S from VIPA. It contains a
description of the construction, project implementation and usage.
Product Order number as of state:
CP-HW CP-FW
CP 341 RS422/485 341-1CH01 01 V1.3.1
The manual is targeted at users who have a background in automation technology.
The manual consists of chapters. Every chapter provides a self-contained description of a
specific topic.
The following guides are available in the manual:
nAn overall table of contents at the beginning of the manual
nReferences with page numbers
The manual is available in:
nprinted form, on paper
nin electronic form as PDF-file (Adobe Acrobat Reader)
Important passages in the text are highlighted by following icons and headings:
DANGER!
Immediate or likely danger. Personal injury is possible.
Information product sup-
port
Technical support
Objective and contents
Target audience
Structure of the manual
Guide to the document
Availability
Icons Headings
VIPA System 300S
General
About this manual
HB130 | CP | 341-1CH01 | en | 18-40 6

CAUTION!
Damages to property is likely if these warnings are not heeded.
Supplementary information and useful tips.
1.3 Safety information
The system is constructed and produced for:
ncommunication and process control
ngeneral control and automation tasks
nindustrial applications
noperation within the environmental conditions specified in the technical data
ninstallation into a cubicle
DANGER!
This device is not certified for applications in
– in explosive environments (EX-zone)
The manual must be available to all personnel in the
nproject design department
ninstallation department
ncommissioning
noperation
CAUTION!
The following conditions must be met before using or commis-
sioning the components described in this manual:
– Hardware modifications to the process control system should only be
carried out when the system has been disconnected from power!
– Installation and hardware modifications only by properly trained per-
sonnel.
– The national rules and regulations of the respective country must be
satisfied (installation, safety, EMC ...)
National rules and regulations apply to the disposal of the unit!
Applications conforming
with specifications
Documentation
Disposal
VIPA System 300S General
Safety information
HB130 | CP | 341-1CH01 | en | 18-40 7

2 Basics
2.1 Safety information for users
VIPA modules make use of highly integrated components in MOS-Technology. These
components are extremely sensitive to over-voltages that can occur during electrostatic
discharges. The following symbol is attached to modules that can be destroyed by elec-
trostatic discharges.
The Symbol is located on the module, the module rack or on packing material and it indi-
cates the presence of electrostatic sensitive equipment. It is possible that electrostatic
sensitive equipment is destroyed by energies and voltages that are far less than the
human threshold of perception. These voltages can occur where persons do not dis-
charge themselves before handling electrostatic sensitive modules and they can damage
components thereby, causing the module to become inoperable or unusable. Modules
that have been damaged by electrostatic discharges can fail after a temperature change,
mechanical shock or changes in the electrical load. Only the consequent implementation
of protection devices and meticulous attention to the applicable rules and regulations for
handling the respective equipment can prevent failures of electrostatic sensitive modules.
Modules must be shipped in the original packing material.
When you are conducting measurements on electrostatic sensitive modules you should
take the following precautions:
nFloating instruments must be discharged before use.
nInstruments must be grounded.
Modifying electrostatic sensitive modules you should only use soldering irons with
grounded tips.
CAUTION!
Personnel and instruments should be grounded when working on electro-
static sensitive modules.
Handling of electrostatic
sensitive modules
Shipping of modules
Measurements and altera-
tions on electrostatic sen-
sitive modules
VIPA System 300S
Basics
Safety information for users
HB130 | CP | 341-1CH01 | en | 18-40 8

2.2 Basics - ISO/OSI reference model
The ISO/OSI reference model is based on a proposal that was developed by the Interna-
tional Standards Organization (ISO). This represents the first step towards an interna-
tional standard for the different protocols. It is referred to as the ISO-OSI layer model. OSI
is the abbreviation for Open System Interconnection, the communication between open
systems. The ISO/OSI reference model does not represent a network architecture as it
does not define the services and protocols used by the different layers. The model simply
specifies the tasks that the different layers must perform. All current communication sys-
tems are based on the ISO/OSI reference model, which is defined by the ISO 7498
standard. The reference model structures communication systems into 7 layers that cover
different communication tasks. In this manner the complexity of the communication
between different systems is divided amongst different layers to simplify the task.
The following layers have been defined:
nLayer 7 - Application Layer
nLayer 6 - Presentation Layer
nLayer 5 - Session Layer
nLayer 4 - Transport Layer
nLayer 3 - Network Layer
nLayer 2 - Data Link Layer
nLayer 1- Physical Layer
Depending on the complexity and the requirements of the communication mechanisms a
communication system may use a subset of these layers.
The bit communication layer (physical layer) is concerned with the transfer of data bits via
the communication channel. This layer is therefore responsible for the mechanical, elec-
trical and the procedural interfaces and the physical communication medium located
below the bit communication layer:
nWhich voltage represents a logical 0 or a 1?
nThe minimum time the voltage is present to be recognized as a bit.
nThe pin assignment of the respective interface.
This layer performs error-checking functions for bit strings transferred between two com-
municating partners. This includes the recognition and correction or flagging of communi-
cation errors and flow control functions. The security layer (data link layer) converts raw
communication data into a sequence of frames. This is where frame limits are inserted on
the transmitting side and where the receiving side detects them. These limits consist of
special bit patterns that are inserted at the beginning and at the end of every frame. The
security layer often also incorporates flow control and error detection functions. The data
security layer is divided into two sub-levels, the LLC and the MAC level. The MAC (Media
Access Control) is the lower level and controls how senders are sharing a single transmit
channel. The LLC (Logical Link Control) is the upper level that establishes the connection
for transferring the data frames from one device into the other.
The network layer is an agency layer. Business of this layer is to control the exchange of
binary data between stations that are not directly connected. It is responsible for the log-
ical connections of layer 2 communications. Layer 3 supports the identification of the
single network addresses and the establishing and disconnecting of logical communica-
tion channels. Additionally, layer 3 manages the prior transfer of data and the error pro-
cessing of data packets. IP (Internet Protocol) is based on Layer 3.
Layer 4 connects the network structures with the structures of the higher levels by
dividing the messages of higher layers into segments and passes them on to the network
layer. Hereby, the transport layer converts the transport addresses into network
addresses. Common transport protocols are: TCP, SPX, NWLink and NetBEUI.
Overview
Layer 1 - Bit communica-
tion layer (physical layer)
Layer 2 - Security layer
(data link layer)
Layer 3 - Network layer
Layer 4 - Transport layer
VIPA System 300S Basics
Basics - ISO/OSI reference model
HB130 | CP | 341-1CH01 | en | 18-40 9

The session layer is also called the communication control layer. It relieves the communi-
cation between service deliverer and the requestor by establishing and holding the con-
nection if the transport system has a short time fail out. At this layer, logical users may
communicate via several connections at the same time. If the transport system fails, a
new connection is established if needed. Additionally this layer provides methods for con-
trol and synchronization tasks.
This layer manages the presentation of the messages, when different network systems
are using different representations of data. Layer 6 converts the data into a format that is
acceptable for both communication partners. Here compression/decompression and
encrypting/decrypting tasks are processed. This layer is also called interpreter. A typical
use of this layer is the terminal emulation.
The application layer is the link between the user application and the network. The tasks
of the application layer include the network services like file, print, message, data base
and application services as well as the according rules. This layer is composed from a
series of protocols that are permanently expanded following the increasing needs of the
user.
2.3 CP 341-1CH01
Dimensions of the basic enclosure:
n1tier width: (WxHxD) in mm: 40x125x120
nThe CP 341-1CH01 is compatible to the Siemens CP 341 (6ES7 341-1CH01-0AE0).
nThe CP is configured in the Siemens SIMATIC Manager.
Layer 5 - Session layer
Layer 6 - Presentation
layer
Layer 7 - Application layer
Dimensions/ Weight
Compatibility
VIPA System 300S
Basics
CP 341-1CH01
HB130 | CP | 341-1CH01 | en | 18-40 10

2.4 General data
Conformity and approval
Conformity
CE 2014/35/EU Low-voltage directive
2014/30/EU EMC directive
Approval
UL Refer to Technical data
others
RoHS 2011/65/EU Restriction of the use of certain hazardous substances in
electrical and electronic equipment
Protection of persons and device protection
Type of protection - IP20
Electrical isolation
to the field bus - electrically isolated
to the process level - electrically isolated
Insulation resistance -
Insulation voltage to reference earth
Inputs / outputs - AC / DC 50V, test voltage AC 500V
Protective measures - against short circuit
Environmental conditions to EN 61131-2
Climatic
Storage / transport EN 60068-2-14 -25…+70°C
Operation
Horizontal installation hanging EN 61131-2 0…+60°C
Horizontal installation lying EN 61131-2 0…+40°C
Vertical installation EN 61131-2 0…+40°C
Air humidity EN 60068-2-30 RH1 (without condensation, rel. humidity 10…95%)
Pollution EN 61131-2 Degree of pollution 2
Installation altitude max. - 2000m
Mechanical
Oscillation EN 60068-2-6 1g, 9Hz ... 150Hz
Shock EN 60068-2-27 15g, 11ms
VIPA System 300S Basics
General data
HB130 | CP | 341-1CH01 | en | 18-40 11

Mounting conditions
Mounting place - In the control cabinet
Mounting position - Horizontal and vertical
EMC Standard Comment
Emitted interference EN 61000-6-4 Class A (Industrial area)
Noise immunity
zone B
EN 61000-6-2 Industrial area
EN 61000-4-2 ESD
8kV at air discharge (degree of severity 3),
4kV at contact discharge (degree of severity 2)
EN 61000-4-3 HF field immunity (casing)
80MHz … 1000MHz, 10V/m, 80% AM (1kHz)
1.4GHz ... 2.0GHz, 3V/m, 80% AM (1kHz)
2GHz ... 2.7GHz, 1V/m, 80% AM (1kHz)
EN 61000-4-6 HF conducted
150kHz … 80MHz, 10V, 80% AM (1kHz)
EN 61000-4-4 Burst, degree of severity 3
EN 61000-4-5 Surge, degree of severity 3 *
*) Due to the high-energetic single pulses with Surge an appropriate external protective circuit with lightning protection
elements like conductors for lightning and overvoltage is necessary.
VIPA System 300S
Basics
General data
HB130 | CP | 341-1CH01 | en | 18-40 12

3 Assembly and installation guidelines
3.1 Installation dimensions
1tier width (WxHxD) in mm: 40 x 125 x 120Dimensions Basic enclo-
sure
Dimensions
Installation dimensions
VIPA System 300S Assembly and installation guidelines
Installation dimensions
HB130 | CP | 341-1CH01 | en | 18-40 13

3.2 Assembly standard bus
The single modules are directly installed on a profile rail and connected via the backplane
bus connector. Before installing the modules you have to clip the backplane bus con-
nector to the module from the backside. The backplane bus connector is delivered
together with the peripheral modules.
Order number A B C
390-1AB60 160 140 10
390-1AE80 482 466 8.3
390-1AF30 530 500 15
390-1AJ30 830 800 15
390-9BC00* 2000 Drillings only left 15
*) Unit pack: 10 pieces
Measures in mm
For the communication between the modules the System 300S uses a backplane bus
connector. Backplane bus connectors are included in the delivering of the peripheral
modules and are clipped at the module from the backside before installing it to the profile
rail.
General
Profile rail
Bus connector
VIPA System 300S
Assembly and installation guidelines
Assembly standard bus
HB130 | CP | 341-1CH01 | en | 18-40 14

Please regard the allowed environment temperatures:
1 horizontal assembly: from 0 to 60°C
2 vertical assembly: from 0 to 40°C
3 lying assembly: from 0 to 40°C
If you do not deploy SPEED-Bus modules, the assembly happens with the following
approach:
1. Bolt the profile rail with the background (screw size: M6), so that you still have min-
imum 65mm space above and 40mm below the profile rail.
2. If the background is a grounded metal or device plate, please look for a low-impe-
dance connection between profile rail and background.
3. Connect the profile rail with the protected earth conductor. For this purpose there is
a bolt with M6-thread.
4. The minimum cross-section of the cable to the protected earth conductor has to be
10mm2.
5. Stick the power supply to the profile rail and pull it to the left side to the grounding
bolt of the profile rail.
6. Fix the power supply by screwing.
7. Take a backplane bus connector and click it at the CPU from the backside like
shown in the picture.
8. Stick the CPU to the profile rail right from the power supply and pull it to the power
supply.
9. Click the CPU downwards and bolt it like shown.
10. Repeat this procedure with the peripheral modules, by clicking a backplane bus
connector, stick the module right from the modules you've already fixed, click it
downwards and connect it with the backplane bus connector of the last module and
bolt it.
Assembly possibilities
Approach
VIPA System 300S Assembly and installation guidelines
Assembly standard bus
HB130 | CP | 341-1CH01 | en | 18-40 15

3.3 Installation guidelines
The installation guidelines contain information about the interference free deployment of a
PLC system. There is the description of the ways, interference may occur in your PLC,
how you can make sure the electromagnetic compatibility (EMC), and how you manage
the isolation.
Electromagnetic compatibility (EMC) means the ability of an electrical device, to function
error free in an electromagnetic environment without being interfered respectively without
interfering the environment.
The components of VIPA are developed for the deployment in industrial environments
and meets high demands on the EMC. Nevertheless you should project an EMC planning
before installing the components and take conceivable interference causes into account.
Electromagnetic interferences may interfere your control via different ways:
nElectromagnetic fields (RF coupling)
nMagnetic fields with power frequency
nBus system
nPower supply
nProtected earth conductor
Depending on the spreading medium (lead bound or lead free) and the distance to the
interference cause, interferences to your control occur by means of different coupling
mechanisms.
There are:
ngalvanic coupling
ncapacitive coupling
ninductive coupling
nradiant coupling
In the most times it is enough to take care of some elementary rules to guarantee the
EMC. Please regard the following basic rules when installing your PLC.
nTake care of a correct area-wide grounding of the inactive metal parts when installing
your components.
– Install a central connection between the ground and the protected earth conductor
system.
– Connect all inactive metal extensive and impedance-low.
– Please try not to use aluminium parts. Aluminium is easily oxidizing and is there-
fore less suitable for grounding.
nWhen cabling, take care of the correct line routing.
– Organize your cabling in line groups (high voltage, current supply, signal and data
lines).
– Always lay your high voltage lines and signal respectively data lines in separate
channels or bundles.
– Route the signal and data lines as near as possible beside ground areas (e.g.
suspension bars, metal rails, tin cabinet).
General
What does EMC mean?
Possible interference
causes
Basic rules for EMC
VIPA System 300S
Assembly and installation guidelines
Installation guidelines
HB130 | CP | 341-1CH01 | en | 18-40 16

nProof the correct fixing of the lead isolation.
– Data lines must be laid isolated.
– Analog lines must be laid isolated. When transmitting signals with small ampli-
tudes the one sided laying of the isolation may be favourable.
– Lay the line isolation extensively on an isolation/protected earth conductor rail
directly after the cabinet entry and fix the isolation with cable clamps.
– Make sure that the isolation/protected earth conductor rail is connected impe-
dance-low with the cabinet.
– Use metallic or metallised plug cases for isolated data lines.
nIn special use cases you should appoint special EMC actions.
– Consider to wire all inductivities with erase links.
– Please consider luminescent lamps can influence signal lines.
nCreate a homogeneous reference potential and ground all electrical operating sup-
plies when possible.
– Please take care for the targeted employment of the grounding actions. The
grounding of the PLC serves for protection and functionality activity.
– Connect installation parts and cabinets with your PLC in star topology with the
isolation/protected earth conductor system. So you avoid ground loops.
– If there are potential differences between installation parts and cabinets, lay suffi-
ciently dimensioned potential compensation lines.
Electrical, magnetically and electromagnetic interference fields are weakened by means
of an isolation, one talks of absorption. Via the isolation rail, that is connected conductive
with the rack, interference currents are shunt via cable isolation to the ground. Here you
have to make sure, that the connection to the protected earth conductor is impedance-
low, because otherwise the interference currents may appear as interference cause.
When isolating cables you have to regard the following:
nIf possible, use only cables with isolation tangle.
nThe hiding power of the isolation should be higher than 80%.
nNormally you should always lay the isolation of cables on both sides. Only by means
of the both-sided connection of the isolation you achieve high quality interference
suppression in the higher frequency area. Only as exception you may also lay the iso-
lation one-sided. Then you only achieve the absorption of the lower frequencies. A
one-sided isolation connection may be convenient, if:
– the conduction of a potential compensating line is not possible.
– analog signals (some mV respectively µA) are transferred.
– foil isolations (static isolations) are used.
nWith data lines always use metallic or metallised plugs for serial couplings. Fix the
isolation of the data line at the plug rack. Do not lay the isolation on the PIN 1 of the
plug bar!
nAt stationary operation it is convenient to strip the insulated cable interruption free
and lay it on the isolation/protected earth conductor line.
nTo fix the isolation tangles use cable clamps out of metal. The clamps must clasp the
isolation extensively and have well contact.
nLay the isolation on an isolation rail directly after the entry of the cable in the cabinet.
Lead the isolation further on to your PLC and don't lay it on there again!
CAUTION!
Please regard at installation!
At potential differences between the grounding points, there may be a
compensation current via the isolation connected at both sides.
Remedy: Potential compensation line
Isolation of conductors
VIPA System 300S Assembly and installation guidelines
Installation guidelines
HB130 | CP | 341-1CH01 | en | 18-40 17

4 Hardware description
4.1 Properties
nRS422/485 interface isolated to back plane bus
nFunction compatibility to Siemens CP 341 (6ES7 341-1CH01-0AE0)
nThe following protocols are supported:
– ASCII
– 3964(R)
– Modbus Master ASCII / RTU (no hardware dongle necessary)
– Modbus Slave RTU (no hardware dongle necessary)
nParameterization CP 341 via the parameterization package from Siemens
– CP 341: Point-to-Point is parameterized as of V 5.0
nUp to 250 telegrams within the 1024byte sized receive and send buffer
nBaud rate parameterizable up to 76.8kbit/s
nPower supply via back plane bus
Type Order No Description
CP 341 RS422/485 341-1CH01 CP 341 with RS422/485 interface
Protocols: ASCII, 3964(R), Modbus Master (ASCII / RTU),
Modbus Slave (RTU)
CP 341 RS422/485
Order data
VIPA System 300S
Hardware description
Properties
HB130 | CP | 341-1CH01 | en | 18-40 18

4.2 Structure
1 LED status indicators
The following components are under the front flap
2 RS422/485 interface
nPin compatible to Siemens CP 341 (6ES7 341-1CH01-0AE0)
nLogical conditions as voltage difference between 2 twisted lines
nSerial bus connection
– Full-duplex: Four-wire operation (RS422)
– Half-duplex: Two-wire operation (RS485)
nLine length:
– 1200m at 19.2kbit/s
– 500m at 38.4kbit/s
– 250m at 76.8kbit/s
nData transfer rate up to 76.8kbit/s
CP 341-1CH01
RS422/485 interface
VIPA System 300S Hardware description
Structure
HB130 | CP | 341-1CH01 | en | 18-40 19

Pin Designation Input/Output Description
1 n.c. ---
2 T(B)+ Output Send data (four-wire)
3 R(B)+ Input Receive data (four-wire)
R(B)+ / T(B)+ Input/Output Receive/Send data (two-wire)
4 RTS Output nRequest to send:
– RTS "ON": CP ready to send
– RTS "OFF": CP is not
sending
5 M5V (GND_ISO) Output Ground isolated
6 P5V (+5V_ISO) Output 5V isolated
7 T(A)- Output Send data (four-wire)
8 R(A)- Input/Output Receive data (four-wire)
R(A)- / T(A)- Input/Output Receive/Send data (two-wire)
9 n.c. ---
Never connect the shield of the cable with GND_ISO, as this could
destroy the interface!
Pin 6 (P5V) of the isolated interfaces carries the isolated 5V supply with the respective
ground GND on pin 5 (M5V). You may use this isolated voltage to provide defined static
voltage levels on the signaling lines by means of resistors and ensure that reflections are
reduced to a minimum.
X2: 9pin D-type jack
Isolated voltages P5V,
M5V
VIPA System 300S
Hardware description
Structure
HB130 | CP | 341-1CH01 | en | 18-40 20
This manual suits for next models
1
Table of contents
Other YASKAWA Control System manuals
Popular Control System manuals by other brands
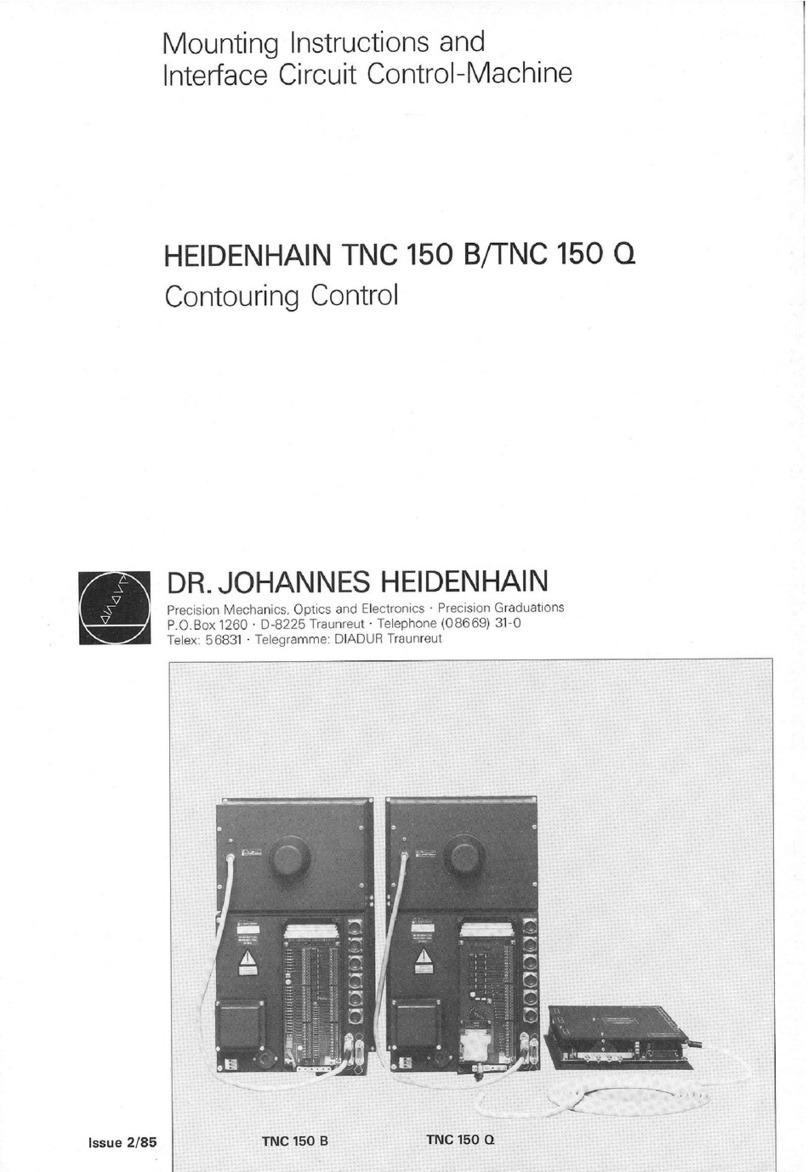
HEIDENHAIN
HEIDENHAIN TNC 150 B Mounting instructions
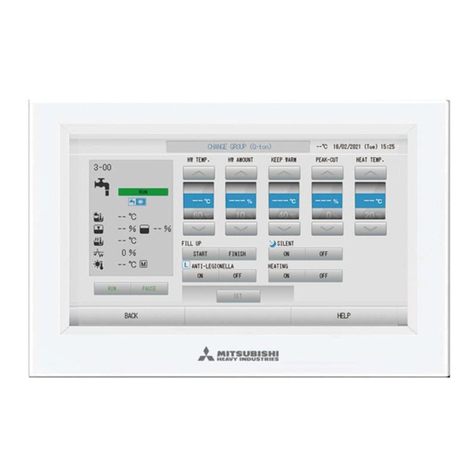
Mitsubishi Heavy Industries
Mitsubishi Heavy Industries SC-SL4-AE2 Technical manual
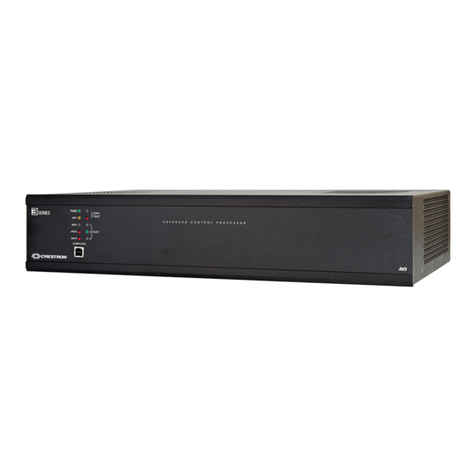
Crestron
Crestron 3 Series reference guide
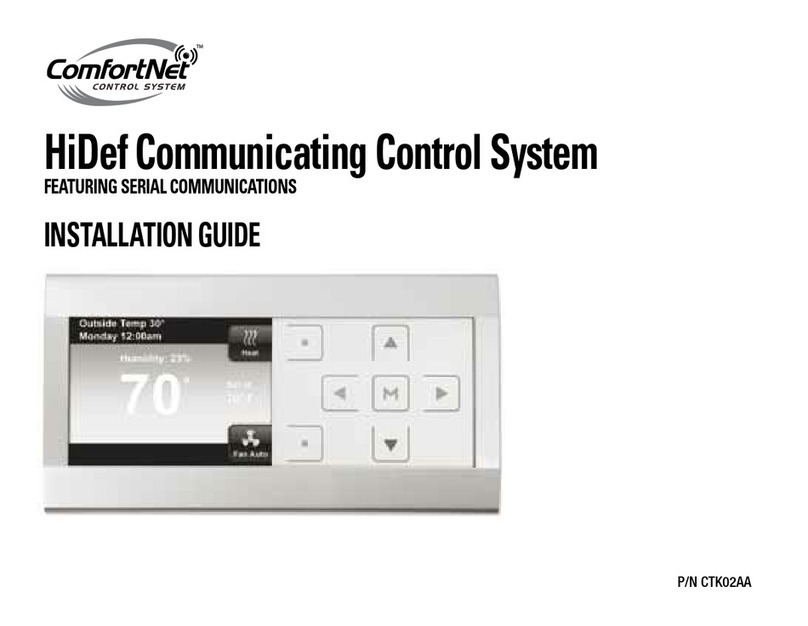
ComfortNET
ComfortNET CTK02AA installation guide
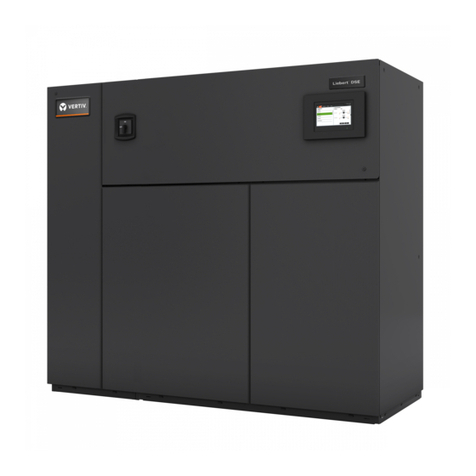
Vertiv
Vertiv Liebert DSE Installer/user guide
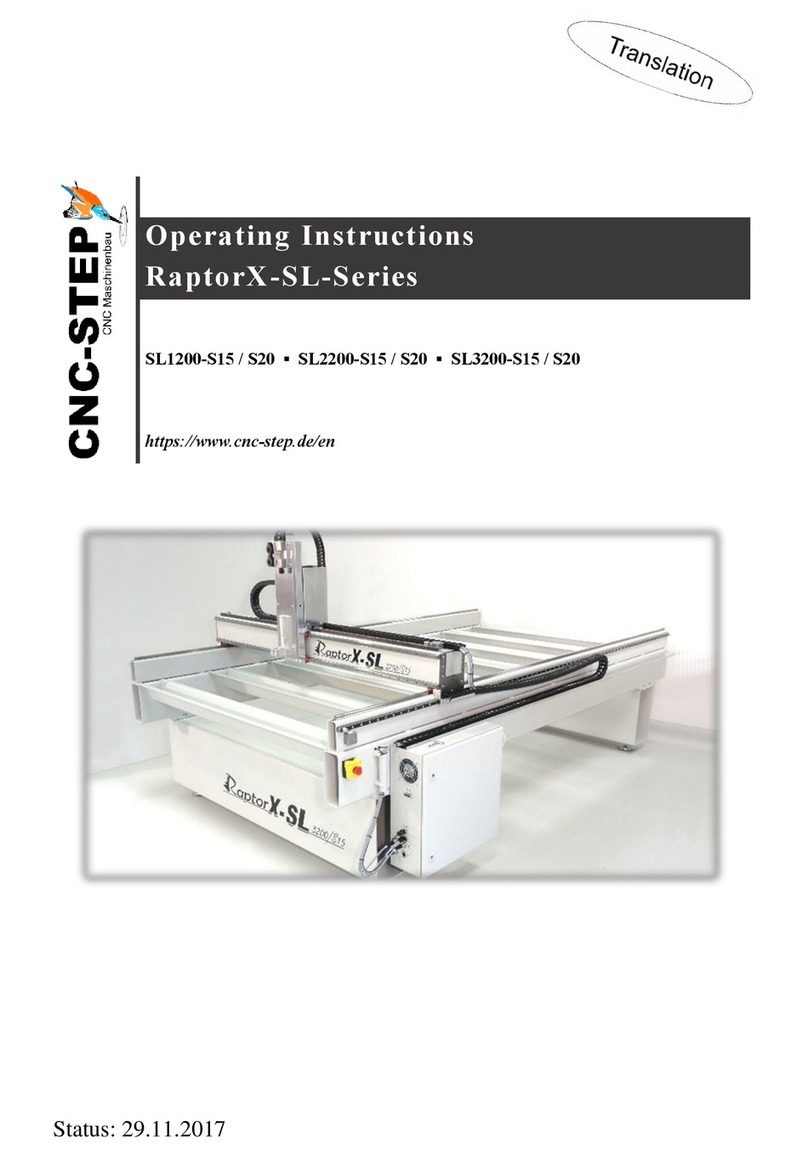
CNC-Step
CNC-Step RaptorX-SL1200-S15 operating instructions