Berker RMD 75314013 Guide

Shutter actuator 4gang 6A 230V manual
RMD
75314013
Technical
Documentation
© Gebr. Berker 2005 Version: 10.05.2005 Page: 1 / 17
(Subject to prior change) 75314013.doc Part 7
Application:
Depending on EIB telegrams received, the shutter actuator switches up to four independent output
channels, one for each motor (4-channel operation). The number of output channels can also be reduced
to two so that up to two blind/shutter motors can be controlled per channel (2 x 2-channel operation).
The shutter actuator is equipped with a manual control feature permitting bus-independent operation of
the individual outputs in a permanent or temporary mode.
On reception of a storm warning, the actuator can, for instance, move the shutter into a predefined safety
position and lock them there. Each output can be independently parameterized for individual moving
times.
Illustration: Controls:
A3 A 4
NA1 A 2
A1 A2 A3 A4
OFF
L
L
L
L
L
L
Dimensions:
Width: 4 modules, 72 mm
Height: 90 mm
Depth: 64 mm
1 programming button
1 programming LED (red)
Manual controls:
1 " " key for manual control mode
activation (select key)
1 "OFF" key (ALL stop)
1 "
" key for manual UP movement
1 "
" key for manual DOWN movement
Status indicators:
8 LEDs (red) to indicate the movement
direction of the individual outputs or of the
manually selected output
1 LED (red) to indicate the "permanent
manual mode"
1 LED (red) to indicate the "UP" movement of
the manually selected output
1 LED (red) to indicate the "DOWN"
movement of the manually selected output
(For further information on controls and status
indicators cf. "Manual control")
Degree of protection: IP 20
Mark of approval: KNX / EIB
Ambient temperature: -5 °C ... +45 °C
Storage temperature: -25 °C ... +70 °C (reduced lifetime when stored abo ve +45°C)
Fitting position: any
Minimum distances: none
Type of fixing: snap-fastening on DIN rail (no data rail required)
instabus EIB supply
Voltage: 21 – 32 V DC (SELV)
Power consumption: max. 150 mW
Connection: instabus connecting and branching terminal
External supply
Voltage: 110 V (-10 %) - 240 V (+10 %) AC; 50 / 60 Hz (no DC)
Total power dissipation: min. 0.3 W up to max. 1.8 W (no load connected)
Connection: screw terminals:
0.5 – 4 mm² single wire and stranded without ferrule
0.5 – 2.5 mm² stranded wire with ferrule

Shutter actuator 4gang 6A 230V manual
RMD
75314013
Technical
Documentation
© Gebr. Berker 2005 Version: 10.05.2005 Page: 2 / 17
(Subject to prior change) 75314013.doc Part 7
Response to voltage failure (see also "Bus and mains voltage")
Bus voltage only: parameter-dependent ("Response to bus voltage failure")
Mains voltage only: All outputs switch off (stop); manual control not possible.
Bus and mains voltage: All outputs switch off (stop); manual control not possible.
Response on reactivation: (see also "Bus and mains voltage")
Bus voltage only: Mains voltage not available:
Outputs are off (stop); bus communication is possible, i.e. safety
functions can be activated
Mains voltage available:
parameter-dependent ("Response to bus voltage return")
Mains voltage only: Bus voltage not available:
parameter-dependent ("Response to bus voltage failure ")
Manual control is possible.
Bus voltage available:
All outputs switch off or remain off (stop) until a new bus telegram
is received and until the switching state changes.
Exception: The actuator automatically reactivates the safety
function(s) for the outputs assigned if the safety objects were
activated before or during the mains failure. The parameterized
"response at the beginning of the safety function" is repeated. A
safety function activated before and deactivated during the mains
failure does not launch a new movement on return of the mains
voltage. If a safety function was at first activated and then
deactivated again during the mains failure, the actuator launches
a new movement for the outputs assigned after return of the
mains as parameterized for "at the end of a safety function". In
any case, the outputs assigned are re-enabled after safety
deactivation.
Manual control is possible.
Bus and mains voltage: parameter-dependent ("Response on return of bus voltage"
(cf. "Bus voltage only" / "Mains voltage only")
Input ---
Output
Type of switching contact: 1 make contact and 1 change-over contact per output,
monostable
(movement directions mechanically interlocked.)
Number of outputs: 4
Switching voltage: 110 V – 240 V AC +/- 10 % 50 / 60Hz (no DC)
Max. switching current: 6 A at 230 V AC : non inductive or low-inductance loads
(e.g. condenser-type motors)
Connection: Screw terminals:
0.5 – 4 mm² single wire and stranded without ferrule
0.5 – 2.5 mm² stranded wire with ferrule

Shutter actuator 4gang 6A 230V manual
RMD
75314013
Technical
Documentation
© Gebr. Berker 2005 Version: 10.05.2005 Page: 3 / 17
(Subject to prior change) 75314013.doc Part 7
Connection diagram: Assignment of terminals:
L1
L2
L3
N
A3 A 4
NA1 A 2
M1 M2
A1 A2 A3 A4
OFF
L
L
L
L
L
L
redblack
instabus-
wire
Hardware information:
•The supply voltage (mains voltage) is connected to terminals N and L beside the terminals of output A1.
Output A1 and thus motor M1 are then supplied at the same time.
The supply of outputs A2 thru A4 requires an additional phase conductor connected to the respective L
terminals.
It is not necessary to connect a motor to output A1. For proper functioning of the device, connection of
the mains voltage (terminals N and L) is, however, necessary.
•Connection of different phase conductors is possible.
•If motors are to be connected in parallel to an output, it is absolutely indispensable to observe the
corresponding instructions of the motor manufacturers to avoid irreparable damage to the motors. If
necessary, use supplementary isolating relays.
•Use only shutters with end position limit switches (mechanical or electronic). The limit switches of the
motors connected must be checked for correct adjustment.
•Activation of the manual control mode stops all output channels. In this case, bus communication has no
longer any effect on the relay switching states. Safety movements will be aborted. A safety function will
be subsequently executed on leaving the manual control mode, if still active. In the manual control
mode, only long operation (MOVE) (long depression of key) and the stop command (brief depression of
key) are available.

Shutter actuator 4gang 6A 230V manual
RMD
75314013
Technical
Documentation
© Gebr. Berker 2005 Version: 10.05.2005 Page: 4 / 17
(Subject to prior change) 75314013.doc Part 7
Software description
Shutter actuator 4gang 230V manual RMD
ETS symbol:
4
AST-Type 01
Hex
1
Dez
reserved
Applications:
No. Brief description: Name: Version:
1 Shutter with safety monitoring Shutter 207401 0.1
Application note:
1. Shutter 207401
Executable from mask version: 1.1 onwards
Number of addresses (max): 32 dynamic table management Yes No
Number of assignments (max): 32 maximum length of table 64
Communication objects: 10
Object
Name Function Type Flag
Mode of operation "4–channel operation"
0 Output 1 Step operation 1 Bit C, W, (R*)
1 Output 2 Step operation 1 Bit C, W, (R*)
2 Output 3 Step operation 1 Bit C, W, (R*)
3 Output 4 Step operation 1 Bit C, W, (R*)
4 Output 1 Move operation 1 Bit C, W, (R*)
5 Output 2 Move operation 1 Bit C, W, (R*)
6 Output 3 Move operation 1 Bit C, W, (R*)
7 Output 4 Move operation 1 Bit C, W, (R*)
Mode of operation "2 x 2-channel operation"
0 Output 1/3 Step operation 1 Bit C, W, (R*)
1 Output 2/4 Step operation 1 Bit C, W, (R*)
4 Output 1/3 Move operation 1 Bit C, W, (R*)
5 Output 2/4 Move operation 1 Bit C, W, (R*)
16
Safety 1 Safety 1 Bit C, W, (R*)
17
Safety 2 Safety 1 Bit C, W, (R*)
*: For objects marked (R), the current object status can be read out (set "R" flag).

Shutter actuator 4gang 6A 230V manual
RMD
75314013
Technical
Documentation
© Gebr. Berker 2005 Version: 10.05.2005 Page: 5 / 17
(Subject to prior change) 75314013.doc Part 7
Description of objects (dynamic object structure):
0 - 3 Step operation:
1-bit object for step operation of a shutter
4 - 7 Move operation: 1-bit object for move operation of a shutter
16 - 17 Safety: 1-bit object for reception of an alarm resp. safety message
(polarity can be parameterized)
Scope of functions
•Mode of operation: 4-channel operation or 2 x 2-channel parameterizable:
- in 4-channel operation, 4 independent output channels, each for one shutter motor or for similar
systems,
- in 2 x 2-channel operation, reduction of output channels, so that two output terminals can be used in
common for two motors per output channel.
•Short operation (STEP) or long operation (MOVE) presettable independently for each output channel
(long operation (MOVE) also infinitely).
•Switch-over delay at change of running direction independently presettable for each output.
•Automatic moving time extension (3 %) for the adaptation of different moving times to upper limit stop
(dependent on drive unit). This is useful since shutters are slower during UP movements.
•Two safety functions separately assignable to shutter channels and common cyclical monitoring:
Movement into a parameterized limit position on activation and deactivation of the safety function(s). The
polarity of the safety objects is adjustable.
•Response after failure and return of bus voltage presettable.
•Manual control of the output channels is possible even without bus voltage. The manual control mode
can be inhibited.

Shutter actuator 4gang 6A 230V manual
RMD
75314013
Technical
Documentation
© Gebr. Berker 2005 Version: 10.05.2005 Page: 6 / 17
(Subject to prior change) 75314013.doc Part 7
Description of functions
Moving times / short operation (STEP) / long operation (MOVE) / switch-over delay / moving time
extension
The shutter actuator can be adapted to the sometimes different moving times of the shutters used. For
such adaptation, the different times must be determined during commissioning of the device and
incorporated in the ETS.
Determination of short operation (STEP)
The short operation mode (STEP) is needed, for instance, for the adjustment of the 'gap width' of a roller
shutter. In most cases, the short operation (STEP) is effected by depressing a shutter push button
permitting manual intervention into the shutter control cycle. When the actuator receives a STEP
command while the shutter is in motion, the movement is stopped immediately by the shutter actuator.
With the "Short operation (STEP) base" and "Short operation (STEP) factor" parameters, it is possible to
fix the time of short operation (STEP) independently for each output channel. The time fixed should
correspond to
ca. ¼ of the complete moving time needed for opening the shutter segments in case of a roller shutter.
If the factor is set to "0", the reception of a STEP command will only result in a stop when the shutter is in
motion. There is no reaction in this case, when the shutter is stationary.
Determination of long operation (MOVE)
The long operation mode (move) is needed for the adjustment of the shutter height. In most cases, the
long operation (MOVE), too, is initiated by a long press on a shutter touch sensor or by a superordinate
time control. The long operation mode can always be stopped by an incoming STEP command. An
uninterrupted long operation moves the shutter into the limit positions (completely open or completely
closed).
With the "Long operation (MOVE)" parameter, the time for long operation (MOVE) can be fixed
independently for each output channel. The following two settings must be considered:
•"Time base * time factor + 20 %":
Long operation (MOVE) is adjusted with the "Long operation time base" and the "Long operation time
factor" parameter. The moving time must be adjusted in such a way that it corresponds to the actual
time required to move the shutter from the upper limit position into the lower limit position.
To ensure that the shutter is in any case in one of the limit positions after the end of the long operation
(MOVE), an 'extra time' amounting to 20 % of the moving time parameterized is automatically added.
As shutters are slower when moving upwards due to gravity effects or other physical influences (e.g.
temperature wind, etc.), the actuator always automatically extends the time set for long operation
(MOVE) into the upper limit position by the fix "Time extension" of 3 % (cf. "Moving time extension") to
ensure that the upper limit position is always reached even in the event of uninterrupted long operation
movements towards this position.
Depending on movement direction, an uninterrupted long operation (MOVE) is always performed with
the long operation moving time regardless of the position occupied by the shutter.
Important:
- The long operation time must not be chosen shorter than the actual time required to move the shutter
from the upper into the lower limit position!
-A long operation (MOVE) can be retriggered by an incoming new long (MOVE) command.
•"Infinite":
In this setting, the corresponding output channels are permanently energized during a long operation
(MOVE) depending on the direction of movement. This setting may be required for certain types of
drives (please observe the instructions of the motor manufacturers).
Even an 'infinite' long operation (MOVE) can be interrupted by a STEP command.

Shutter actuator 4gang 6A 230V manual
RMD
75314013
Technical
Documentation
© Gebr. Berker 2005 Version: 10.05.2005 Page: 7 / 17
(Subject to prior change) 75314013.doc Part 7
Change-over time:
To protect the motor drives against irreparable damage, a fixed break during each change of the moving
direction can be parameterized for each output channel. During the break, no moving direction is activated
(stop). The "Break during change of moving direction" parameter can be set for change-over interruptions
of 0.5 s, 1 s (default), 2 s and 5 s. The required parameter setting can be found in the technical
documentation of the drive motor installed.
The change-over time is taken into account also for bus voltage failures and the manual control mode.
In the unprogrammed state of the actuator, all output channels are preset for a change-over time of 1 s.
Moving time extension:
Due to their weight or to external physical influences (e.g. temperature, wind, etc.), shutters move more
slowly when travelling upwards.
During each upward movement (long operation (MOVE)), the shutter actuator therefore takes a fix moving
time extension into account. The extension is taken as a percentage of the moving time computed and is
adjusted to 3%.
Safety function
The shutter actuator has two safety functions with separate assignment to the shutter channels. The
safety functions can be activated or deactivated by separate objects. The priority of the objects can be
parameterized.
Safety reaction
The reaction of the assigned output channels at the beginning and at the end of a safety function can be
preset.
Response at the beginning of a safety function
The actuator moves the shutters alternatively into one of the limit stop position, if the response at safety is
parameterized for "Moving up" or "Moving down". With these settings, the shutters are locked up in the
limit position after the end of the safety movement. If the response at safety at the beginning of the safety
function is parameterized for "No reaction", no movement is started and the output channels are locked in
the actual position.
With respect to all other bus-controllable functions of the actuator, the safety function has the highest
priority. This means that all functions in progress for the outputs (e.g. step or move operations) will be
aborted and the safety reaction is executed. The safety function can be interrupted only by manual control
on the device itself.
Response at the end of a safety function
At the end of a safety function, the actuator immediately re-enables the output channels concerned when
the setting is "moving up" or "moving down" and approaches the corresponding limit stop positions. If the
response at the end of a safety function is parameterized for "No reaction", the corresponding outputs are
enabled without starting a new movement. If enabling by "No reaction" occurs during a safety movement
still in progress, the outputs are enabled without interrupting the movement.

Shutter actuator 4gang 6A 230V manual
RMD
75314013
Technical
Documentation
© Gebr. Berker 2005 Version: 10.05.2005 Page: 8 / 17
(Subject to prior change) 75314013.doc Part 7
Safety assignment
Each output channel can be assigned separately to safety functions 1 or 2 or alternatively to both safety
functions. If a channel is intended to respond to both functions, the safety objects resp. the functions are
combined by a logic OR. This means that the corresponding output channel goes into the safety lock state
as soon as one of the objects is active. In this case, the channel will be re-enabled only if both objects are
deactivated. Only then can a position follow-up be performed at the end of the safety lock of a channel
assigned to both functions!
If the setting is "No assignment", the safety function for this output channel is deactivated.
Manual control and safety function
Compared to all other bus-controllable function of the actuator, the safety functions have the highest
priority. The safety functions can be interrupted only by manual control on the device itself.
After a manual control, the actuator automatically reactivates the safety function(s) for the outputs
assigned, if the safety objects had been activated before or during a manual control. The parameterized
"Response at the beginning of the safety function" is then re-executed.
If a safety function was deactivated during manual control, (object update "Not active"), the parameterized
"Response at the beginning of the safety function" is re-executed after the end of manual control. It is
assumed that the safety function was activated before or during manual control.
Cyclical monitoring
Both safety objects can be cyclically monitored for the reception of telegrams.
When monitoring is enabled, the actuator expects a telegram update to both safety objects. If no
telegrams are received during the monitoring time, the safety function corresponding to the missing
telegram will be activated.
The safety function can be deactivated again when a safety unlock command is received.
The cycle time of the transmitters should be shorter than the monitoring time parameterized in the shutter
actuator in order to ensure that at least one telegram can be received during the monitoring time.
Safety function information:
•The time needed by an output for a safety movement into the limit stop positions is determined by the
"Long operation (MOVE)" parameter on the "Output X" cards. For this reason, the safety movement can
be as long as the parameterized extended moving time (downward movement: parameterized moving
time + 20 %; upward movement: parameterized moving time + 20 % + fixed moving time extension of
3 %) or also 'infinitely' long. Safety movements cannot be retriggered.
•After return of bus voltage, the safety functions are always deactivated. In the event of a safety lock with
object value "0", an object update ("0" telegram) must first be made after bus voltage return before the
safety function is activated.
•An object update of the safety objects ("ON" after "ON" resp. "OFF" after "OFF") yields no reaction.
•Move-step or step-step commands during an active safety function will be rejected.

Shutter actuator 4gang 6A 230V manual
RMD
75314013
Technical
Documentation
© Gebr. Berker 2005 Version: 10.05.2005 Page: 9 / 17
(Subject to prior change) 75314013.doc Part 7
Bus and mains voltage / programming procedure
Response in case of bus voltage failure:
The response in case of bus voltage failure is predefined by the "Response to bus voltage failure"
parameter on the "General" card. The following actions can be parameterized: shutter moving into upper
limit stop position ("Moving up"), shutter moving to lower limit stop position ("Moving down"), movements
in progress being stopped ("Stop") or no reaction taking place ("No reaction" / movements still in progress
will be accomplished). Manual control is possible depending on the "Manual control during bus voltage
failure" on the "Manual control" card.
Response to mains voltage failure:
The actuator needs a mains voltage supply for operation. In the event of mains voltage failure, all outputs
switch off (stop). Manual control is then no longer possible. Safety functions activated via the bus remain
active.
Response to bus and mains voltage failure:
As in a normal mains failure, all outputs switch off (stop). Manual control is then no longer possible. Safety
functions activated via the bus are rejected.
Response on return of bus voltage:
The response depends on whether mains voltage is present or not when the bus voltage returns.
If the mains is present on return of bus voltage, the reaction is fixed by the "Response on return of bus
voltage" parameter on the "General" card. The following actions can be parameterized: shutter moving to
upper limit position ("Moving up"), shutter moving to lower limit position ("Moving down"), movements in
progress being stopped ("Stop"). Manual control – if activated – will be terminated. In an unprogrammed
actuator, the reaction after bus voltage return is factory-adjusted to "Stop".
If there is no mains voltage on return of bus voltage, all output channels remain off (Stop). Bus
communication is, however, possible, i.e. the safety functions can be activated. Short- or long operation
commands are rejected.
A safety function – if activated – will be executed when the mains voltage returns later on. If no safety
function has been activated during the mains failure (bus voltage available), the actuator executes the
parameterized "Response on bus voltage return" when the mains is restored later on. Manual control is
not possible.

Shutter actuator 4gang 6A 230V manual
RMD
75314013
Technical
Documentation
© Gebr. Berker 2005 Version: 10.05.2005 Page: 10 / 17
(Subject to prior change) 75314013.doc Part 7
Response to mains voltage return:
The response depends on whether bus voltage is available or not when the mains voltage returns.
If bus voltage is available, all outputs are being shut off or remain off (stop) until a new bus telegram is
received and the switching state changes.
Exception: The actuator automatically reactivates the safety function(s) in the outputs assigned, if the
safety objects were activated before or during the mains failure. The parameterized "Response at the
beginning of the safety function" is re-executed. A safety function activated before the mains failure and
deactivated during the failure does not start a new movement on return of mains voltage. If, during mains
failure, a safety function was activated and then deactivated again, the actuator starts a new movement
for the outputs assigned after mains voltage return as parameterized for "End of the safety function". The
outputs concerned are in any case re-enabled after safety deactivation.
If the bus voltage is not present on return of mains voltage, the parameterized "Response on bus voltage
failure" is started ("Stop" is factory-adjusted in unprogrammed actuators).
Manual control is possible again.
Response to bus and mains voltage return:
The parameterized "Response on bus voltage return" is started. Manual control in this case is possible.
(Cf. also "Response on bus voltage return" / "Response on mains voltage return")
Programming procedure:
After the end of programming by the ETS or after a bus reset (bus voltage return), the parameterized
"Response on bus voltage return" is executed. After programming, the manual control mode is terminated.
Manual control depending on bus and mains voltage:
Manual control is only possible when mains voltage is available. Depending on the "Manual control on bus
voltage failure" parameter on the "Manual control" card, manual control with no bus voltage applied is
possible. An activated manual control mode ends on return of bus voltage.

Shutter actuator 4gang 6A 230V manual
RMD
75314013
Technical
Documentation
© Gebr. Berker 2005 Version: 10.05.2005 Page: 11 / 17
(Subject to prior change) 75314013.doc Part 7
Manual control
The actuator as delivered has the manual control mode already enabled. The four keys on the device front
panel permit comfortable local operation of the up to 4 output channels also without bus voltage being
present. The different operating states are indicated by up to 11 red LEDs. For manual control, the mains
supply must be on.
A1 A2 A3 A4
OFF
Activation of manual control and operation:
The manual control mode can be activated temporarily or permanently.
Permanent manual control:
Activation: 1. Press the " " key for at least 5 seconds.
2. The red LED beside the " " key lights up statically. The actuator is now permanently
in the manual control mode, control via the EIB is disabled and all output channels are
stopped.
Operation: A short press (< 1 second) on the " " key selects the output channel which is to be
operated by manual control. The two status LEDs (
) of the output selected in the
LED array start flashing. Pressing the select key repeatedly permits switching between the
outputs (A1 →A2 →A3 →A4 →A1 →...). If the actuator works in 2x2-channel
operation, the outputs are automatically combined and controlled in common. (A1 / A3→
A2 / A4 →A1 / A3 →A2 / A4 →A1 / A3 →...).
The "
" and "
" keys can be used to control the selected output channel and to modify
the switching status and the sense of movement. The LEDs beside the keys indicate the
switching state of the selected channel. The switching states of non selected outputs are
indicated as for 'normal' bus operation by means of the LEDs of outputs A1 thru A4 in the
LED array.
Deactivation: - by pressing the " " key for at least 5 secs. until the corresponding LED goes out or
- by bus reset or reapplication of bus voltage (return of bus voltage), or
- by switching off the mains voltage.
Master stop function:
When the actuator is in the permanent manual control mode, all output channels can be shut off at the
same time (stop).
A press on the "OFF" key executes the stop function. All relays are switched off immediately.
The master stop function is available in the permanent manual control mode only!

Shutter actuator 4gang 6A 230V manual
RMD
75314013
Technical
Documentation
© Gebr. Berker 2005 Version: 10.05.2005 Page: 12 / 17
(Subject to prior change) 75314013.doc Part 7
Temporary manual control mode:
Activation: 1. The " " select key must be pressed briefly (< 1 sec.).
2. The red LED(s) of output channel 1 (4-channel operation) resp. 1/3 (2x2-channel
operation) in the LED array start flashing. The actuator is now temporarily in the
manual control mode, control from the EIB is disabled and all output channels are
stopped. The red LED beside the select key is off!
Operation: A short press (< 1 sec.) of the " " key selects the output channel which is to be
controlled manually. The two status LEDs (
) of the output selected in the LED array
start flashing. Pressing the select key repeatedly permits switching between the outputs
and terminating the temporary manual control mode (A1 →A2 →A3 →A4 →End). If the
actuator works in the 2x2-channel mode, the outputs are combined automatically and
controlled in common. (A1 / A3→A2 / A4 →End). After termination of the manual control
mode, the actuator goes back to 'normal' bus operation. The "
" and "
" keys can be
used to control the selected output channel and to modify the switching status and the
sense of movement. The LEDs beside the keys indicate the switching state of the
selected channel. The switching states of non selected outputs are indicated as for
'normal' bus operation by means of the LEDs of outputs A1 thru A4 in the LED array.
Deactivation: - if no further key is pressed after more than 5 seconds, or
- - when the select key is pressed once again after all outputs channels have been selected
once with the key, or
- - by bus reset or reapplication of bus voltage (bus voltage return) or
- - by switching off the mains voltage.
If the " " key is pressed in the temporary manual control mode for at leat 5 seconds, the actuator
changes over to permanent manual control. Pressing the "OFF" key in the temporary manual control
mode yields no reaction!
On activation of the temporary or permanent manual control mode, all output channels are generally
stopped and active safety functions are aborted. Output channel control via the bus is disabled.
Safety functions are reactivated after deactivation of the manual control mode, if they have not been
cancelled (cf. "Safety function").
Manual control mode enable:
The manual control mode is available only when mains voltage is present. The manual control mode
generally can be disabled by selecting the parameter "Manual control = disabled" on the "Manual control"
card. Depending on the "Manual control on bus voltage failure" parameter, it is possible to specify in
addition (with manual control generally disabled) whether a manual control is to be permitted even in the
event of bus voltage failure. An activated manual control mode is terminated on return of bus voltage.
Manual control mode information:
•The parameterized "Break during change of movement direction" is taken into account also for the
manual control mode.
•In the manual control mode, only long operation (MOVE) (long depression of key) and a stop command
(short depression of key) are possible. When delivered ex factory (actuator not yet programmed), the
long operation (MOVE) is factory-adjusted to 'infinite'. After programming of the device with the ETS, the
moving time parameterized for each output channel under "Long operation (MOVE)" is applicable.

Shutter actuator 4gang 6A 230V manual
RMD
75314013
Technical
Documentation
© Gebr. Berker 2005 Version: 10.05.2005 Page: 13 / 17
(Subject to prior change) 75314013.doc Part 7
Settings of the actuator when delivered ex factory
When delivered ex factory, the actuator is factory-adjusted as follows:
•Mode of operation: 4-channel operation
•Long operation (MOVE): infinite
•Short operation (STEP): only stop
•Break during change of movement direction: 1 second
•Response after bus voltage failure: stop
•Response on return of bus voltage: stop
•Manual control: fully enabled

Shutter actuator 4gang 6A 230V manual
RMD
75314013
Technical
Documentation
© Gebr. Berker 2005 Version: 10.05.2005 Page: 14 / 17
(Subject to prior change) 75314013.doc Part 7
Parameters
Description: Values: Comment:
General
Mode of operation
4-channel operation
2 x 2-channel operation
4 output channels working independently of
each other or 2 x 2 channels working in
combination.
All four channels working independently of
each other.
2 channels consisting of 2 connected
channels each.
Response after bus voltage
failure
Stop
Moving up
Moving down
No reaction
Defines the response of the acutator on
bus voltage failure.
The shutter stops on bus voltage failure.
The shutter moves up on bus voltage
failure.
The shutter moves down on bus voltage
failure.
No reaction. Travel movement unchanged.
Response on return of bus
voltage
Stop
Moving up
Moving down
Defines the response of the acutator on
return of bus voltage.
The shutter stops on bus voltage return.
The shutter moves up again on bus voltage
return.
The shutter moves down again on bus
voltage return.

Shutter actuator 4gang 6A 230V manual
RMD
75314013
Technical
Documentation
© Gebr. Berker 2005 Version: 10.05.2005 Page: 15 / 17
(Subject to prior change) 75314013.doc Part 7
Output 1 in "Mode of operation = 4-channel operation" resp.
Output 1/3 in "Mode of operation = 2 x 2-channel operation"
Step operation
Time base
8 ms
130 ms
2.1 s
33 s
Definition of time base for short operation
(STEP).
Step time = time factor ⋅time base
Step operation
Time factor
(0...255) (0...100)
(0 = nur Stop)
0 bis 255, 64
with bases:
8 ms, 130 ms, 2.1 s
0 to 100, 64
with base: 33 s
Definition of time factor for short operation
(STEP).
Step time = time factor ⋅time base
Preset: 8 ms 64 = 512 ms
Move operation
Time base * time factor +
20 %
Infinite
Definition of long operation (MOVE).
Long operation (MOVE) as parameterized
long operation moving time with an
automatic extension by 20 %.
Long operation (MOVE) infinite, i.e. the
relays are not automatically de-energized
after reaching the limit position. The relay
state is changed only by a new short
command or other actions influencing the
travel movement.
Move operation
Time base 8 ms
130 ms
2.1 s
33 s
Definition of time base for long operation
moving time.
Moving time = time factor ⋅time base
Not visible with 'infinite' long operation
(MOVE)!
Move operation
Time factor
(125...255)
(8...255)
(3...255)
(3...100)
125 to 255, 125
with base: 8 ms
8 to 255, 30
with base: 130 ms
3 up to 255, 30
with base: 2.1 s
3 bis 100, 30
with base: 33 s
Definition of time factor for long operation
moving time.
Moving time = time factor ⋅time base
Preset: 2.1 s 30 = 63 s
Not visible with 'infinite' long operation
(MOVE).
The moving times must be determined with
precision.
Break during change of
direction 0.5 s
1 s
2 s
5 s
Defines the break during a change of
moving direction (change-over time).
Output 2 to 4 in "Mode of operation = 4-channel operation" resp.
Output 2/4 in "Mode of operation = 2 x 2-channel operation" see output 1!

Shutter actuator 4gang 6A 230V manual
RMD
75314013
Technical
Documentation
© Gebr. Berker 2005 Version: 10.05.2005 Page: 16 / 17
(Subject to prior change) 75314013.doc Part 7
Safety
Cyclical monitoring time for
safety 1 and 2
none
1; 2; 3; 4; 5; 6; 7; 8 min.
10; 11; 12; 20; 40 min.
1; 2 Std.
Setting of monitoring time for both safety
objects.
Cyclical monitoring deactivated when
setting is "none".
Safety lock with object value
for safety 1 0 (safety unlock = 1)
1 (safety unlock = 0)
Defines the polarity of safety object 1.
Safety lock with object value
for safety 2 0 (safety unlock = 1)
1 (safety unlock = 0)
Defines the polarity of safety object 2.
Assignment output 1
resp. output 1/3
No assignment
Safety 1
Safety 2
Safety 1 OR
safety 2
Defines te assignment of output 1 resp. of
outputs 1/3 to the safety functions.
Each output channel can be separately
assigned to safety functions 1 or 2 or
alternatively to both safety functions.
The safety function is deactivated for te
output.
The output responds only to safety function
1.
The output responds only to safety function
2.
The output responds to both safety
functions; the safety objects resp. functions
are combined by logic OR. This means that
the respective channel is safety-locked as
soon as one of the objects is active. In this
case, the output channel is enabled only
after both objects are deactivated. Only in
this case is a position follow-up for a
channel assigned to both functions
possible after the end of a safety lock.
Response at the beginning
and end, output 1 resp.
output 1/3
Beginning
no reaction
no reaction
no reaction
moving up
moving up
moving up
moving down
moving down
moving down
End
no reaction
moving up
moving down
no reaction
moving up
moving down
no reaction
moving up
moving down
Defines the reaction of output 1 resp. of
outputs 1/3 at the beginning resp. at the
end of an active safety lock.
If the position is to be followed up and can
also be followed up at the end of a safety
function, the actions parameterized "at the
end" will not be executed.
Assignment, outputs 2 to 4
resp. output 2/4
see output 1
Response at the beginning
and end, outputs 2 to 4
resp. output 2/4
see output 1

Shutter actuator 4gang 6A 230V manual
RMD
75314013
Technical
Documentation
© Gebr. Berker 2005 Version: 10.05.2005 Page: 17 / 17
(Subject to prior change) 75314013.doc Part 7
Manual control
Manual control
enabled
disabled
In the manual control mode it is possible to
operate the output channels manually.
Manual control works only when mains
voltage is available.
Manual control can on principle be
activated.
The manual control mode cannot be
activated when bus voltage is available.
Manual control on bus
voltage failure
enabled
disabled
Manual control can additionally be
permitted in the event of bus voltage
failure.
The manual control mode can only be
activated in the event of bus voltage failure.
Manual control can, on principle, not be
activated.
Only with "Manual control" = "Inhibited"!
Software information
•This type of actuator does not permit read-out of bus voltage by the ETS!
Other Berker Controllers manuals
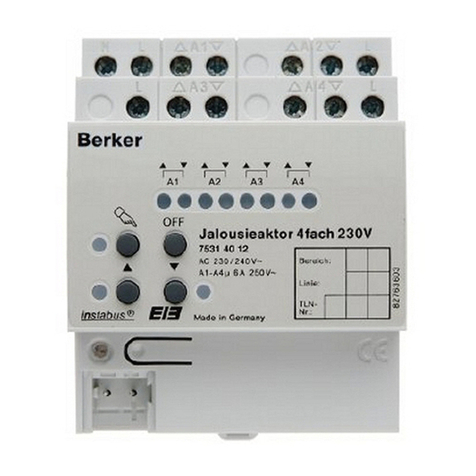
Berker
Berker 7531 40 13 User manual

Berker
Berker 7531 40 15 User manual

Berker
Berker 7531 80 03 User manual
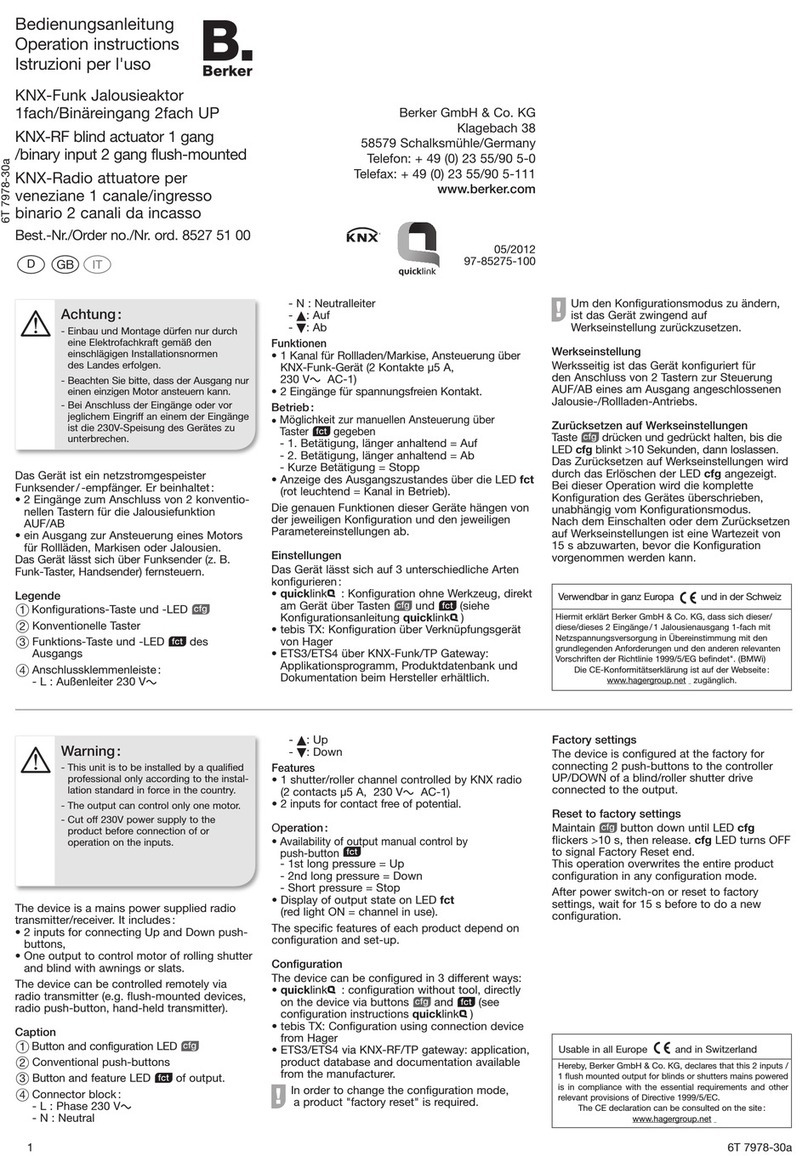
Berker
Berker KNX-RF User manual

Berker
Berker 7574 01 01 Product guide

Berker
Berker 8536 52 00 User manual
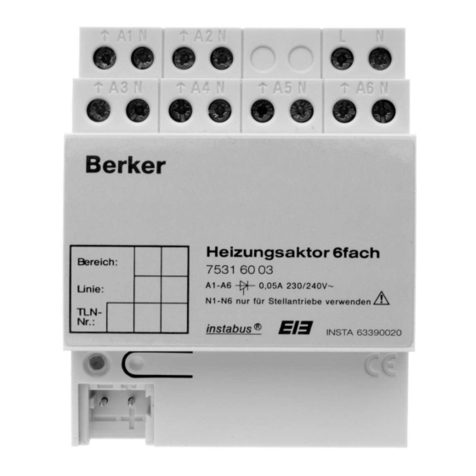
Berker
Berker 7531 60 03 User manual
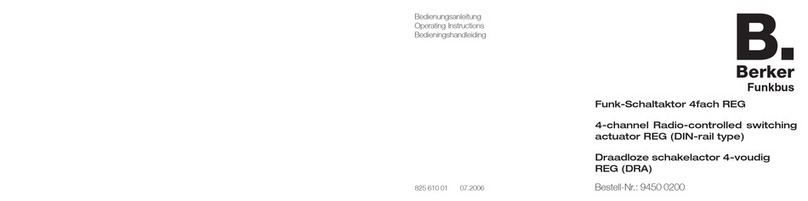
Berker
Berker 9450 0200 User manual

Berker
Berker 7531 31 07 Product guide
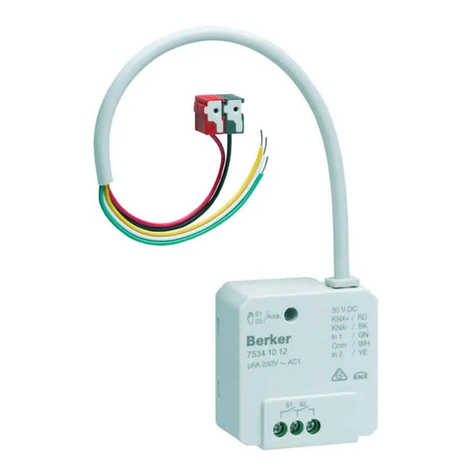
Berker
Berker 7534 10 12 User manual
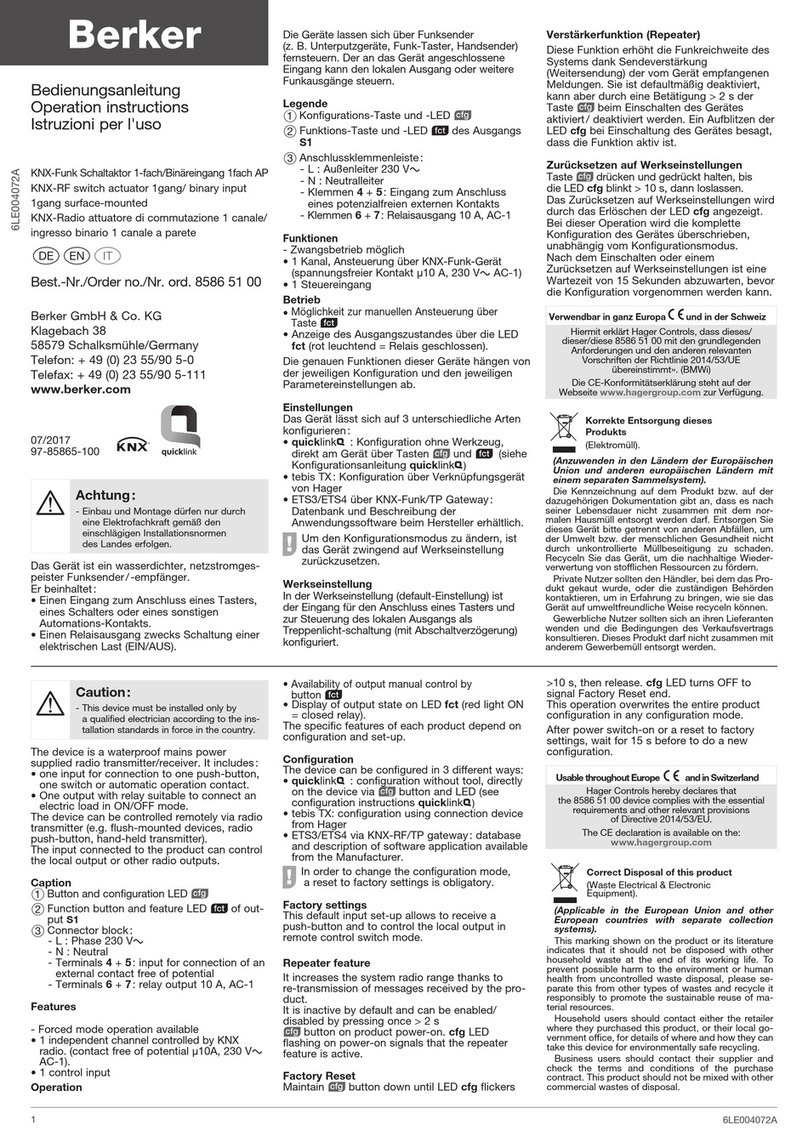
Berker
Berker 85865100 User manual
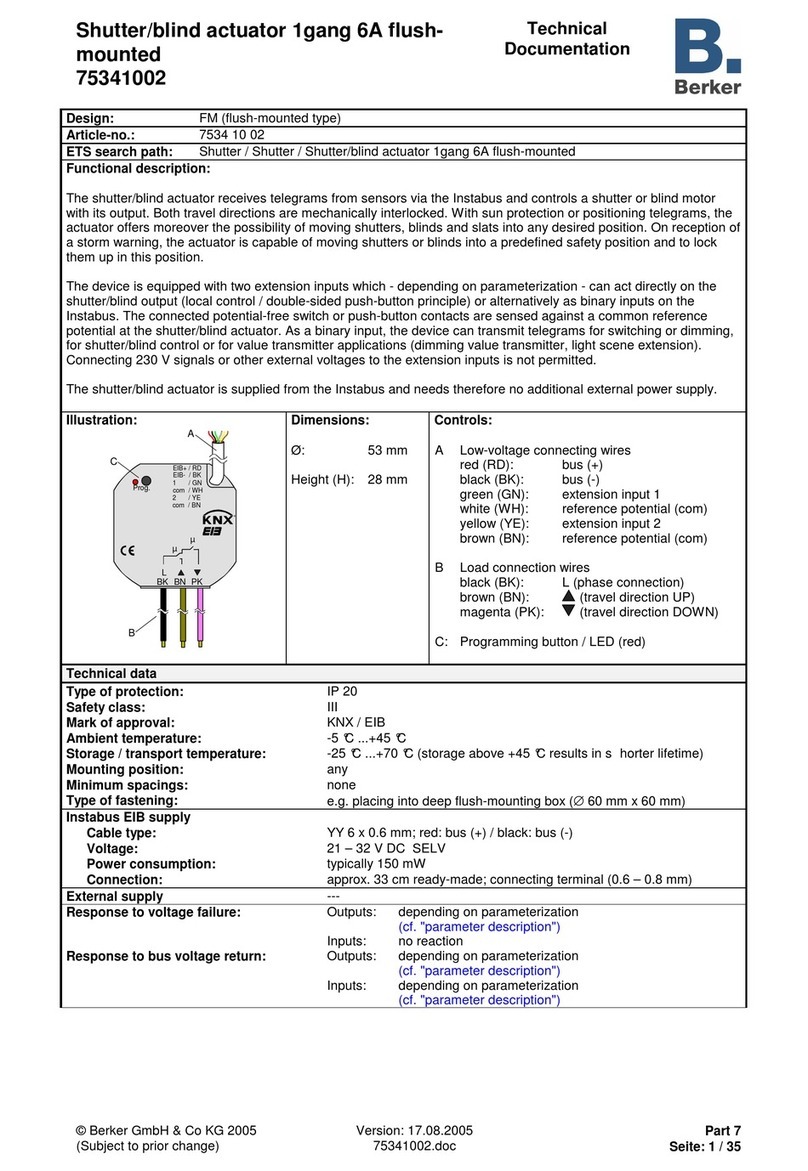
Berker
Berker 75341002 Guide
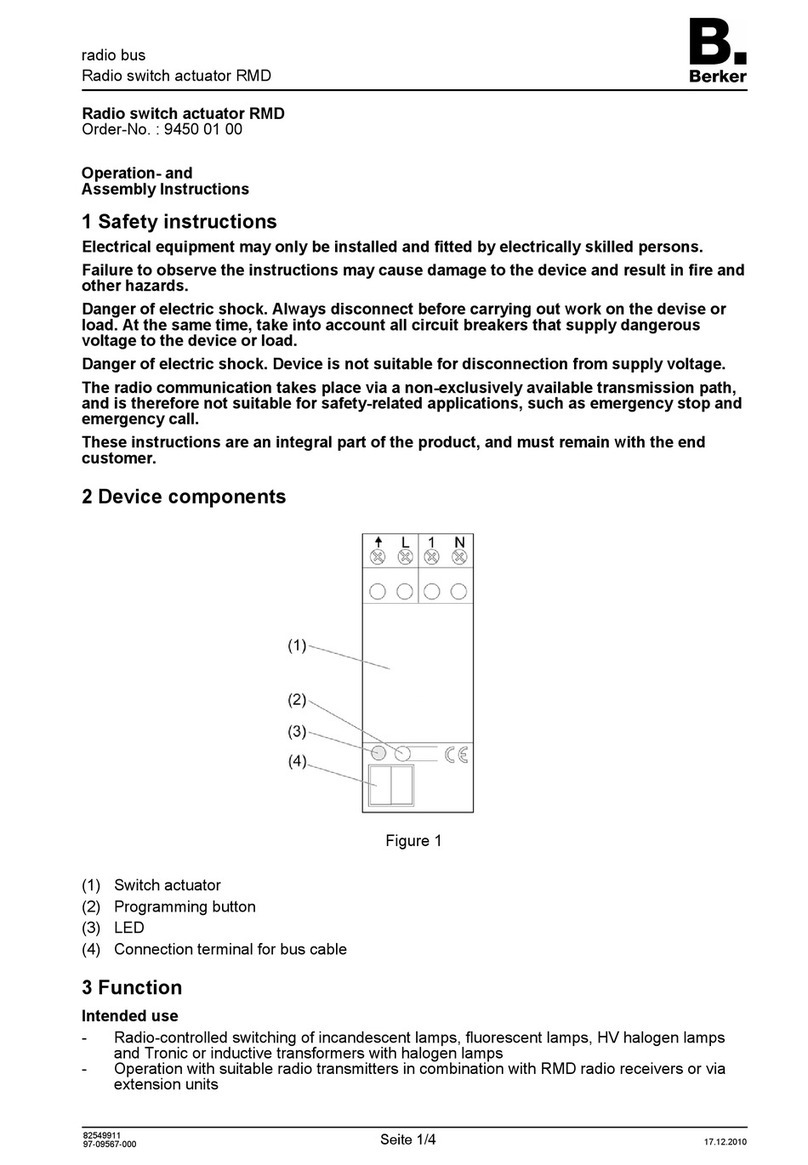
Berker
Berker 9450 01 00 Service manual
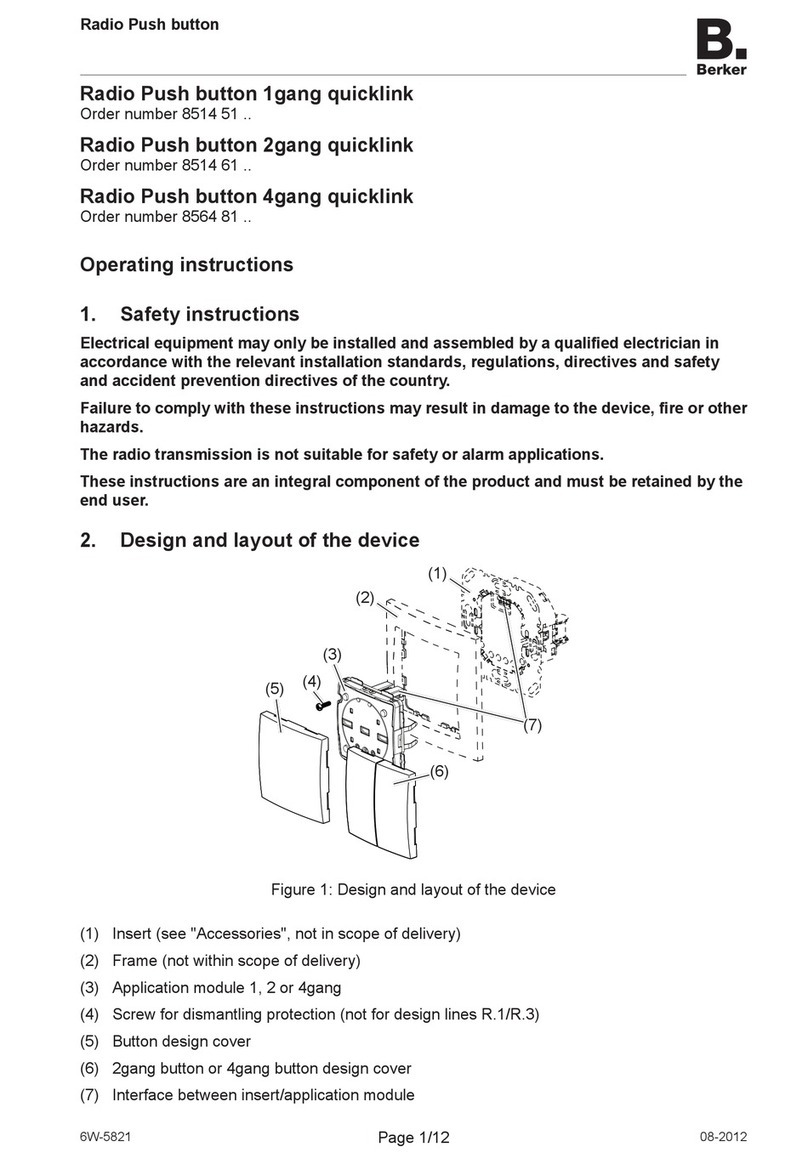
Berker
Berker Radio Push button 1gang quicklink User manual
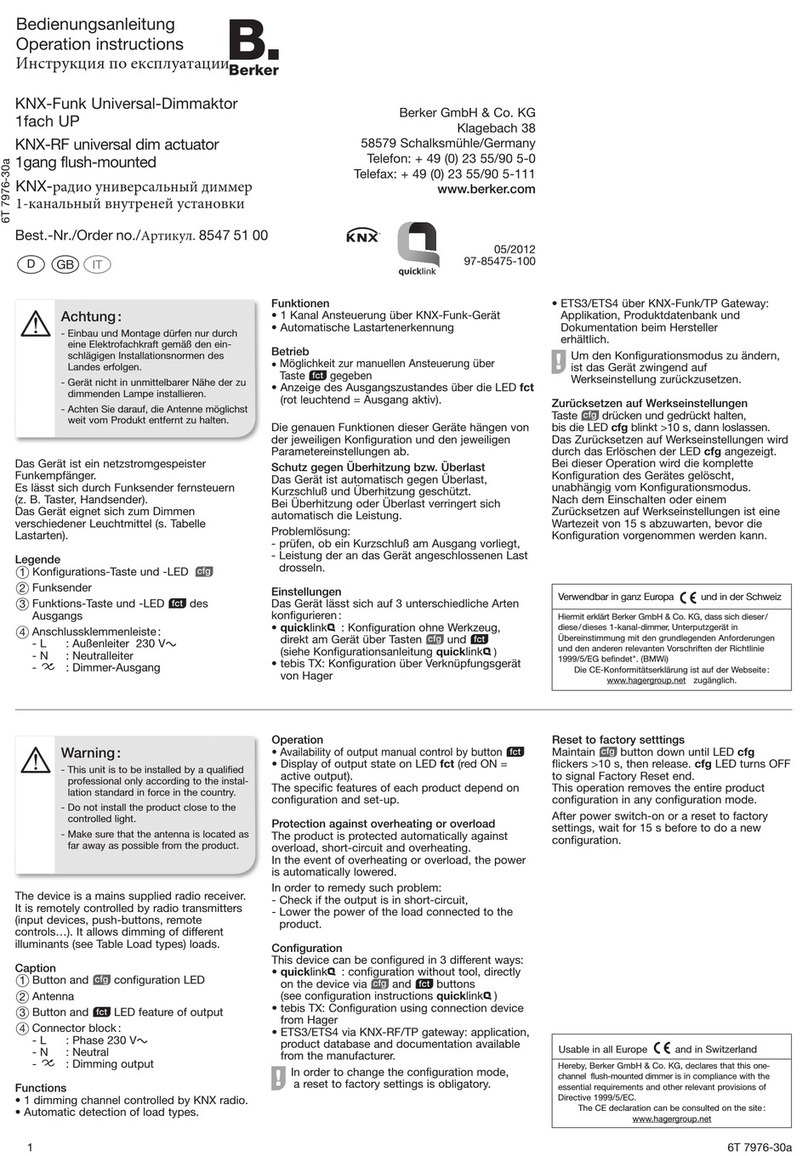
Berker
Berker 85475100 User manual
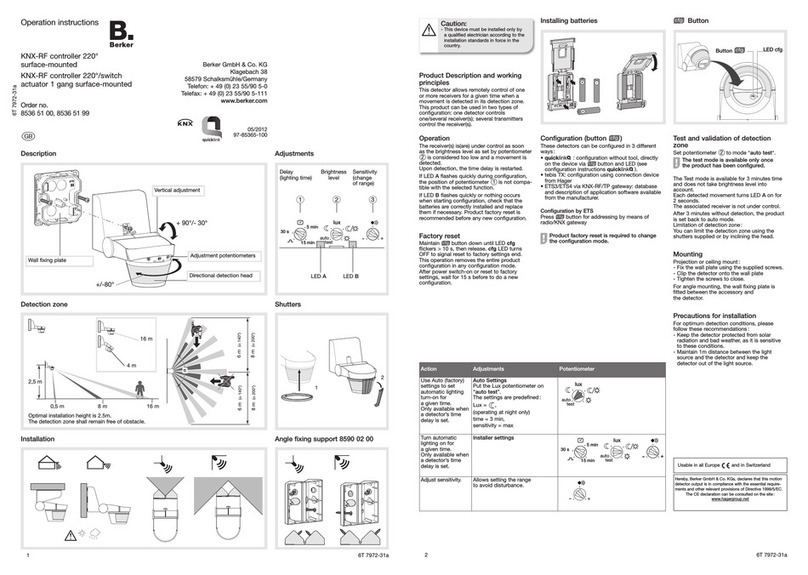
Berker
Berker KNX-RF User manual
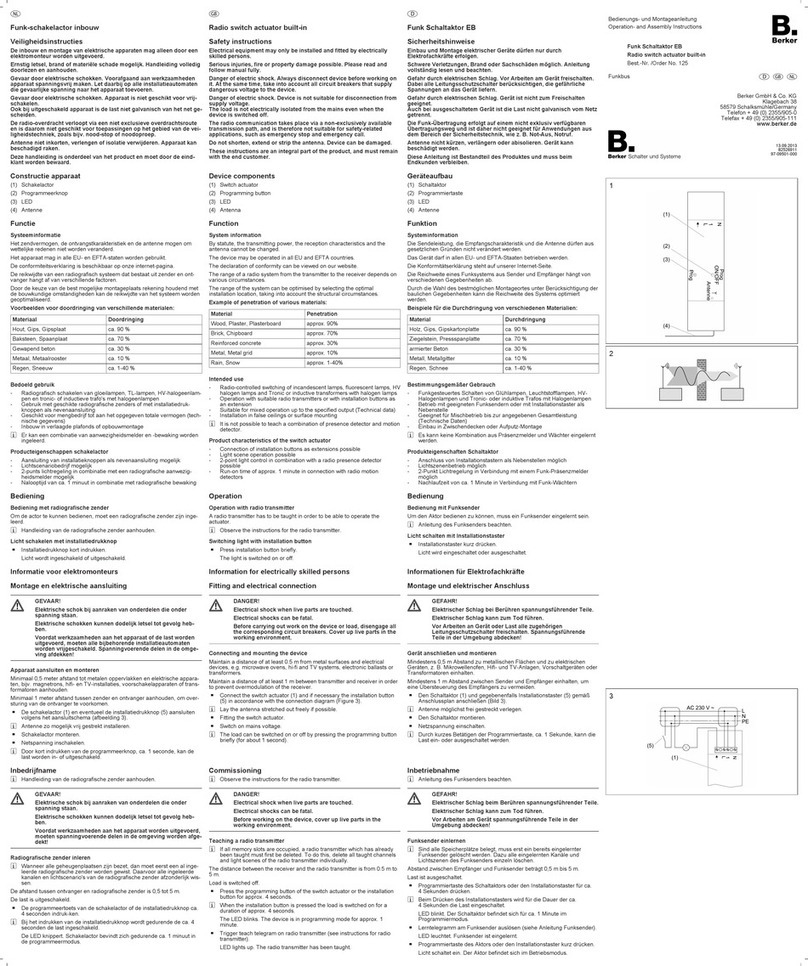
Berker
Berker 125 Service manual

Berker
Berker KNX-RF 8547 51 00 User manual
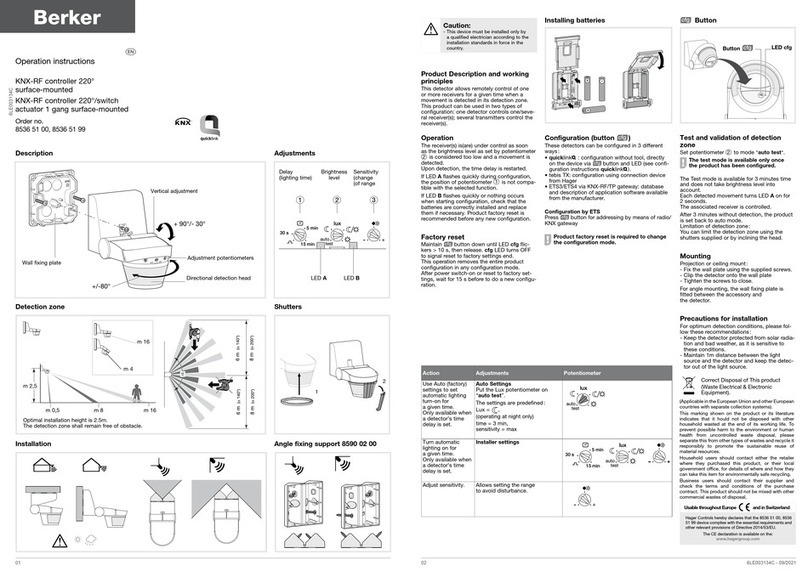
Berker
Berker 8536 51 00 User manual
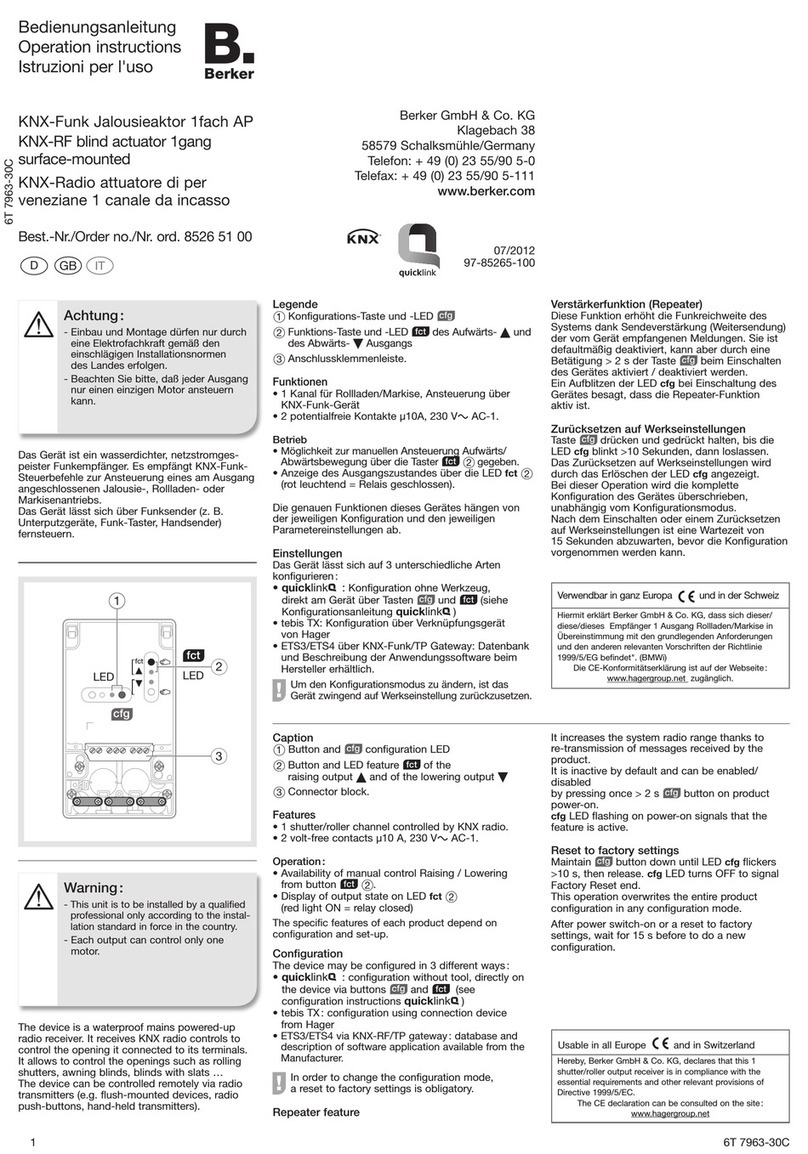
Berker
Berker 8526 51 00 User manual