Biobase BBS-H1300 User manual

Horizontal Laminar Flow Cabinet
BBS-H1300/H1800
User Manual
BIOBASE GROUP
Version 2021.12

1
Preface
Thank you very much for purchasing our horizontal laminar flow cabinet.
Please read the “Operating Instructions” and “Warranty” carefully before operating this unit to assure
proper operation. After reading these documents, be sure to store them securely together with the
“Warranty” within reach for future reference.
Warning: Before operating the unit, be sure to read carefully and fully understand important
warnings in the operating instructions.

2
Content
Preface.................................................................................................................................................... 1
Content................................................................................................................................................... 2
1. Unpacking, Installation and Debugging.............................................................................................4
1.1 Unpacking................................................................................................................................. 4
1.2 Accessories Checking................................................................................................................6
1.3 Installation Conditions and Operating Environment.................................................................7
1.4 Installation................................................................................................................................. 7
1.5 Checking after installation.......................................................................................................10
2. User Instructions...............................................................................................................................11
2.1 Functions................................................................................................................................. 11
2.1.1 Product Concept............................................................................................................ 11
2.1.2 Operating Principle/Air flow Pattern............................................................................ 11
2.1.3 Protected Objects...........................................................................................................11
2.1.4 Technical Parameters.................................................................................................... 12
2.2 Product Structure.....................................................................................................................13
2.2.1 Structural Composition of BBS-H1300/BBS-H1800....................................................13
2.3 Instructions of Operation.........................................................................................................16
2.3.1 Normal Operation Notice.............................................................................................. 16
2.3.2 Operation Process..........................................................................................................17
2.4. Daily Maintenance................................................................................................................. 17
2.4.1 Clean the Cabinet Surface............................................................................................. 17
2.4.2 Clean the external surface and front window................................................................18
2.4.3 Overall maintenance period........................................................................................18
2.4.4 Maintenance methods.................................................................................................18
2.4.5 Storage conditions...................................................................................................... 18
2.5 Replacement Parts List............................................................................................................19
2.6 Wiring Diagram (Picture 12)...................................................................................................21
3. Trouble Shooting and Solution.........................................................................................................22

3
3.1 Common Failures and Solutions............................................................................................. 22
3.2 Replace the fuse.......................................................................................................................23
3.3 Replace LED lamp.................................................................................................................. 24
3.4 Replace the UV lamp.............................................................................................................. 25
3.5 Label Description (Picture 15)................................................................................................ 26
4. Warranty...........................................................................................................................................26

4
1. Unpacking, Installation and Debugging
Please firstly check if the packing box is in good condition. If the packing box is damaged, please
take photos.
1.1 Unpacking
Choose proper tools and unpacking method as shown in the below picture.
For wooden box:
1) Method 1 Necessary tools for unpacking: Electric drill with hexagon dead M8(Picture 1)
Picture 1

5
2) Method 2 Use M8 Wrench to unpack(Picture 2)
Picture 2
The following diagram demonstrates quick unpacking procedures (Picture 3). Remove the screws as
shown in the below diagram, then remove the wooden sheet to right and left of the wooden box
Picture 3

6
1.2 Accessories Checking
Refer to the packing list and check the accessories.
BBS-H1300 Packing list
Items
Quantity
Position
Main body
1unit
Wood packaging
Base stand
1unit
Paper (Behind the cabinet)
Power Cord
1pc
Bags(Behind the cabinet)
Fuse (10A)
1pc
Bags(Behind the cabinet)
UV Lamp(T6 30W)
1pc
Paper(Behind the cabinet)
Gas Tap SAN-3102
1pc
Paper(Behind the cabinet)
Water Tap SAN-2102
1pc
Paper(Behind the cabinet)
BBS-H1300 User Manual
1pc
Envelope(Behind the cabinet)
Test report
1pc
Envelope(Behind the cabinet)
Quality certification card
1pc
Envelope(Behind the cabinet)
Warranty Card
1pc
Envelope(Behind the cabinet)
Hexagon cylinder head bolt
M10*55
3 sets
Bags(Behind the cabinet)
flat washer 10+ Spring washer
10
3 sets
Bags(Behind the cabinet)
Allen wrench
1pc
Bags(Behind the cabinet)
BBS-H1800 Packing list
Items
Quantity
Position
BBS-H1800 Main body
1unit
Wood packaging
BBS-H1800 Base stand
1unit
Paper (Behind the cabinet)
Power Line
1pc
Bags(Behind the cabinet)
Fuse (10A)
1pc
Bags(Behind the cabinet)
UV Lamp(T6 30W)
1pc
Paper(Behind the cabinet)

7
Gas Tap SAN-3102
1pc
Paper(Behind the cabinet)
BBS-H1800 User Manual
1pc
Envelope(Behind the cabinet)
Test report
1pc
Envelope(Behind the cabinet)
Quality certification card
1pc
Envelope(Behind the cabinet)
Warranty Card
1pc
Envelope(Behind the cabinet)
Hexagon cylinder head bolt M10*55
3 sets
Bags(Behind the cabinet)
flat washer 10+ Spring washer 10
3 sets
Bags(Behind the cabinet)
Allen wrench
1pc
Bags(Behind the cabinet)
1.3 Installation Conditions and Operating Environment
Laminar Flow Cabinet shall be placed in the protective area of an air stream, and the working area of
the Laminar Flow Cabinet can not be near to the door or window, and should be away from the air
outlet to prevent the air flow from the ventilation system, air conditioning, door, window and
personnel.
At least 300mm gap must be kept in the side and back side of the Laminar Air Flow for clean
operating and for inspection.
Working environment:
a. Only applicable for indoor operation;
b. Ambient temperature: 15° C ~35° C
c. Relative Humidity: ≤75%;
d. Atmospheric pressure range: 70KPa~106KPa;
e. Electrical parameters: Adequate power supply to the laminar flow cabinet(See 2.1.4 Technical
Parameters);
f. Power supply need to be grounded; (Judging method: test the live wire and the neutral wire of the
socket with multimeter. The voltage between live and ground should equal to the voltage of local
electrical grid, and the voltage between neutral and ground should equal to 0. Otherwise the power
supply is not grounded correctly);
1.4 Installation
a. Remove all the packing materials;
b. Check the surface of main body to make sure there is no scratch, deformation or foreign bodies;
c. Confirm the complement of accessories according to the list.
d. Before removing the packing material, move the entire equipment to the place where it is going to
be installed.
The base stand will be packed at back of main body, please take it out before installation.
DO NOT INVERT, DISASSEMBLE OR TILT THE CABINET during transportation.
e. Assemble the base stand with main body as shown in the picture.

8
Please connect the base stand with the main body referring to Picture 4
Picture 4
Removing Hexagon cylinder head bolt on both side lateral brace and T frame, the bottom of T frame,
assemble referring to the picture, fasten the screw and Cap nut on the both side of base stand.
Foot height can be adjusted. Clockwise rotation of feet, when feet height is less than casters, the
cabinet can be (or base stand) moved; anticlockwise rotation of feet, when feet height is greater than
casters, then play a fixed role in preventing the cabinet (or base stand) from moving.
If you have any questions please contact engineers for commissioning
f. connecting main body and base stand.
Please connect main body and base stand refer to Picture 5 .
Leveling Feet
caster
The cabinet is connected
with the positioning bolt
Locating bolt

9
Picture5
First, keep the main body above the base stand. (picture 5), then align the bolt of base stand.
Mounting holes of the Main body at both sides, using Hexagon head bolt M10*55, flat washer 10,
Spring washer 10 insert through base stand and the side panel and make them stable.
g. Pick up the gas (water) tap from accessory kit, first, unscrew the tap and nut, find the Mounting
holes at the both side of cabinet glass. The Tap needs to be fixed as shown in the picture. The water
mouth of the Tap should be inside the cabinet’s operating zone, refer Picture 6, The other end of the
Tap which is having threading on the pipe should be inserted through the glass hole, the threaded
pipe should be fastened with washer and nut outside the glass and need to be tightened with a wrench.
Please refer the below picture to carry out the tap fixing to the cabinet. See picture 6 and 7.
Picture 6
Hex cylinder head
bolt M10×55+ flat
washer10+spring
washer 10

10
Picture 7
h. After the above steps, move cabinet to the right cabinet position slightly, remove the power cord,
check the power cord is intact.
1.5 Checking after installation
First, make sure the voltage and frequency to be same as nameplate showing, and then check the
follows items with power on:
Checking Items
Normal working status
Fan motor
Running normally
LED lamp
Lamp lights up after pressing button
UV Lamp
Lamp lights up after pressing button
Display screen buttons
All buttons can be used
Socket
Use multimeter to test voltage output after
pressing the socket button
If you have any questions please contact engineers to commissioning, Debugging methods
in the service manual
Gas Tap
Water Tap

11
2. User Instructions
2.1 Functions
2.1.1 Product Concept
Laminar Flow Cabinet – is used only for sample protection.
Laminar Flow Cabinet is a work bench or similar enclosure, which creates a particle-free working
environment by taking air through a filtration system and exhausting it across a work surface in a
laminar or unidirectional air stream.
It is widely divided into vertical and horizontal laminar airflow type.
This series is for horizontal type.
2.1.2 Operating Principle/Air flow Pattern
Picture 8
2.1.3 Protected Objects
Laminar flow cabinet is to protect the experimental material, to create a local high cleanliness air
environment, the main role is to ensure the accuracy of the operating area of the experiment, but for
the environment and operators can’t afford protection.

12
2.1.4 Technical Parameters
Model
Parameters
BBS-H1300
BBS-H1800
External Size
(W*D*H)
1300*820*2040 mm
1800*820*2070 mm
Internal
Size(W*D*H)
1200*500*570 mm
1700*500*570 mm
Power Supply
AC 220V±10% AC 110V±10%
Frequency
50 Hz 60Hz
Consumption
400W
500 W
Airflow velocity
0.3~0.5m/s
UV Lamp
Consumption
30W*1
30W*1
LED lamp
Consumption
12W (LED)*1
16W (LED)*2
HEPA Filter
99.999% efficiency at 0.3 um
Noise
≤65dB
Notes: Biobase reserves the rights to make changes in future product design, without reservation and
without notification to its users.
1) Vibration amplitude
The net vibration amplitude, at a range of frequency from 10Hz to 10KHz, would not exceed 5 μ
m .
2) Illumination
The average illumination is more than 350 lux
3) Electrical properties
The cabinet would not breakdown in 5s when the voltage increases by 1390V (AC) within 5s.
Grounding resistance ≤0.1Ω

13
2.2 Product Structure
2.2.1 Structural Composition of BBS-H1300/BBS-H1800
Picture 9
1.Glass door
8. Water, gas tap
2. Power socket
9. Side window
3.Ground terminal
10. Work table
4.Control panel
11. Base Stand
5.Power switch
12. Support foot
6. UV lamp
13.Footmaster caster
7. LED light

14
2.2.2 Structure Introduction
1) Driving system of front window
Driving system consists of tubular motor, front window, hauling mechanism and limit switch.
2) Air filtration system
Air Filtration System is the most important system. It consists of blower and HEPA filter. The
function of Air Filtration System is transferring filtered air to work area, ensure air flow velocity, and
keep Class 100 cleanness of work area.
3) UV lamp
The UV lamp located at the top of the work zone effectively disinfects the entire work zone by
emitting a wavelength of 253.7nm
4) LED light
The laminar flow cabinet is equipped with LED light, which ensures the standard requirement of
average illumination is met.
5) Control Panel
Picture 10
1. Blower
6. Front window Up Status
2. LED Lamp
7. Front window Down Status
3. UV lamp
8. Air volume decreases
4. Power
9. Air volume increases
5. Socket
a. Gear Display
You can know working wind speed by gear display.
b. Soft touch buttons.
The main operation of the device can be carried out by touching button
(1) : The power button
1
2
3
4
5
6
7
8
9

15
(2) : To control blower working status. Blower has memory function, next boot blower gear
shows the last shut down, to avoid each boot need to adjust the fan, (It will not work when front
window is fully closed.)
(3) :To control LED lamp
(4) :To control UV lamp(UV lamp, blower, LED lamp and front window interlock, it won’t
work when LED lamp, blower, front window open )
(5) : To control socket power status.
(6) : Press Down button, front window will fall down. Each time you press, the buzzer will
sound once; hold this key, the front window will continue to decline; release the button, the front
window will stop declining.
(7) : Press UP button, front window will raise. Each time you press, the buzzer will sound once;
hold this key, the front window will continue to rise; release the button, the front window will stop
rising.
(8) :To control blower speed down. When blower is working, if ▊number is More than 1, Each
time you press, wind speed can down a gear, and the buzzer rings once.
(9) :To control blower speed increase. When blower is working, if ▊number is less than 9, Each
time you press, wind speed can increase a gear, and the buzzer rings once.
(10) LCD display: When powered on, from top to bottom is ▊▊▊▊▊▊▊▊▊FAN, It indicates
the strength of blower wind speed, Shown below is the current state of the Winds; The right of the
display is time; UV TIME, UV lamp working time; WORK TIME: HEPA filter working time.
(11) Under standby status, press the LED lamp button and then press and hold the power button for 5
seconds. The clock could be adjusted after a buzz alarm.
Press UP and DOWN to adjust the number and press mute button to switch from minute to hour.
After setting the time correctly, press LED lamp button and then press and hold the power button for
5 seconds. A buzz alarm indicates that the time has been saved).
(12) UV lamp timing:In standby mode, when the front window is lowered to a minimum, please pre
ss UV lamp control button , then the UV lamp is opened. After opening the UV lamp, the display
will show the current status of the UV lamp timing: By pressing blower speed down button , the set
ting time will be reduced one minute each time; by pressing blower speed up button , the setting ti
me will get be increased one minute each time. You can set the time as needed (UV lamp timing rang
e is 0-90 min, and the max factory setting is 90 min)
6)Water proof Socket
Waterproof socket is arranged in the operating area, to within the operating area of the power supply

16
equipment and in the lighting lamp installing the front side plate (Picture 11) and need to use a
socket, open the power supply equipment, press the display of the socket button (Picture 10), the
waterproof socket open cover, access to electricity source plug.
(1) Please make sure the total load of sockets should be ≤ 500W;
(2) Waterproof socket only when the front cover down to the waterproof, the front cover is
opened, the socket can not be considered waterproof socket.
Picture11
7) Fuse
The equipment is equipped with main power fuse, They are located near the power cord’s outlet.
Fuse label is corresponding to the relevant specifications.
8) Control of Front Window
Front window is motorized
9) Structure
a) Cabinet body is built up of 1.2mm cold-rolled steel with anti-powder coating. Strong and steady.
b) Work table is fully made up of 304 stainless steel which looks beautiful and with corrosion
resistance performance.
c) Base stand is made up of cold-rolled steel with anti-powder coating.
d) Soft touch type control panel, easy to handle and beautiful appearance.
2.3 Instructions of Operation
2.3.1 Normal Operation Notice
(1)Make sure input voltage is correct and stable. The rated load of main power socket should be
higher than cabinet consumption. Plug must be well grounded.
(2)Moving principles of different samples inside cabinet: When two or more samples need to be
moved, be sure that low-polluting samples move to high-polluting samples. Movement of
items should also follow the principles moving slowly and stably.
(3)The weight of items placed in the cabinet should not be more than 23Kg/25×25cm2;
(4)Avoid vibration: avoid using vibration equipment (eg centrifuges, vortex oscillator, etc.)
Water
proof
socket
et

17
inside the cabinet. Vibration would cause lower cleanliness of operating area and affect
operator protection.
(5)No flame: No flame is allowed inside the cabinet. Using of fire will lead to airflow disorder,
and filter damage. If sterilization is required during the experiment, infrared sterilizer is
highly recommended.
(6)HEPA filter life: With the usage time increasing, dust and bacteria accumulate inside HEPA
filter. Filter Resistance is getting bigger, when it reaches the maximum point, the speed
requirements can’t be met. Then need contact BIOBASE service department to get a new one.
The used filter should be processed as medical waste.
(7)The steel plate is under fan, which is sealed strictly in the factory. The operator is not allowed
to remove or loose screws of those parts. If necessary, please contact service personal.
(8)The maximum storage period is one year. If the period is more than one year, performance
test should be done .
Serious declaration: BIOBASE will take no responsibility for risks caused by improper
operation and man-made damages!
2.3.2 Operation Process
a. Connect to a suitable power supply
b. Press the relevant key functions (related keys, function and operation of the 2.2.2 in the
description); check the function keys and the operation results are consistent, and according to the
above clean table technical parameters of the test whether the normal start and wind speed is up to
the standard requirements, lighting and ultraviolet lamp is normal work.
c. The cabinet should be sterilized by UV lamp for at least 30 minutes with the window fully closed
before any experiment.
(1) For safety of eyes and skin, people should leave the room during the UV sterilization.
(2) UV lamp should be checked regularly. It should be replaced when either the total working
time reaches 600 hours or the intensity is lower than the requirement.
d. Please move up the front window at the suitable height above the work table and turn on the fan.
Make sure the experiment should be started after fan working for at least 30 minutes..
For operating safety, please place the experiment materials inside the cabinet before
experiment start.
After finishing the experiment, please fully close the front window and make sure to sterilize the
cabinet by UV lamp for 30 minutes before turning off the cabinet.
2.4. Daily Maintenance
Preparations before maintenance: removal of items in the equipment
Preparation of goods: cotton or towel, concentrated soap, hot water, water, medical alcohol or other
disinfectants, etc.
2.4.1 Clean the Cabinet Surface
Clean the surface of working zone
Wipe the entire surface with a soft cotton cloth which has been soaked with concentrated liquid soap.
Afterwards, wipe off the foam with another cotton cloth or towel which has been soaked with clean

18
hot/warm water. At the end, wipe the entire surface with a dry cotton cloth or towel rapidly.
For the contaminated or dirty work surface and sump, use 70% rubbing alcohol or other disinfectant
to wipe.
Disinfectants used for wiping should not damage the 304 stainless steel.
2.4.2 Clean the external surface and front window.
Use a piece of soft cotton cloth or towel to wipe the surface with non-abrasive household cleanser.
2.4.3 Overall maintenance period
The recommended interval period for comprehensive maintenance is either one year or 1000
working hours.
2.4.4 Maintenance methods
1) Weekly or daily maintenance
a. Disinfect and clean the operating area;
b. Clean the external surface and front window around the operating area (Reference 2.4.1
instruction);
c. Check the various functions of the cabinet (Reference 2.4.2 instruction);
d. Record down the maintenance result
2) Monthly maintenance
a. Clean the the external surface and front window (Reference 2.4.2 instruction).
b. Use towel with 70% rubbing alcohol or 1:100 dilution of household bleach to wipe the working
table, the inner face of front window and the inner wall surface of the working area(exclude the
top wind grid). Use another towel with sterile water to wipe those area to erase the remain of
chlorine.
c. Check the various functions of the cabinet;
d. Record down the maintenance result;
3) Annual maintenance
a. Check the two lifting belt of the front window tubular motor, make sure both of them are well
connected to the motor with same tightness.
b. Check the UV lamp and LED light.
c. Apply for overall performance test of the cabinet annually to ensure that the safety meets
requirements. User is responsible for testing costs.
d. Record down the maintenance result.
When doing maintenance, please pay attention to cut off the power, so as to avoid electric
shock!
2.4.5 Storage conditions
Laminar flow cabinet should be stored in a warehouse with relative humidity not more than 75% and
temperature lower than 40°C. The warehouse should have good ventilation performance without acid,
alkali or other corrosive gases. Storage period shall not exceed one year. Laminar flow cabinet stored
for more than one year needs to be unpacked and checked before selling and using. Only the tested
and qualified laminar flow cabinet could be sold.

19
2.5 Replacement Parts List
BBS-H1300 replacement parts list
Number
Name
Specification
BR-01
Fuse
10A
BR-02
Lamp holder T8
LG13-01A
BR-03
UV Lamp
T6 30W
BR-04
LED T5 stand
T5 12W
BR-05
UV lamp ballast
1*TL8-30W
BR-06
HEPA filter
1223*570*69
BR-07
Fan
FH320A
BR-08
Control panel
LCD Control panel
BR-09
Front window
1223*640*5
BR-10
Left Side window
539*405*5
BR-11
Right Side window
539*405*5(has hole)
BR-12
Single wall gas tap
SAN-3102
BR-13
Tubular motor
TMN45-10/17
This manual suits for next models
1
Table of contents
Other Biobase Laboratory Equipment manuals
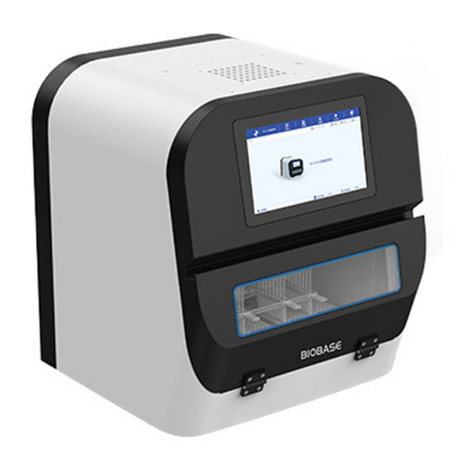
Biobase
Biobase BK-HS32 User manual

Biobase
Biobase BCI-I User manual
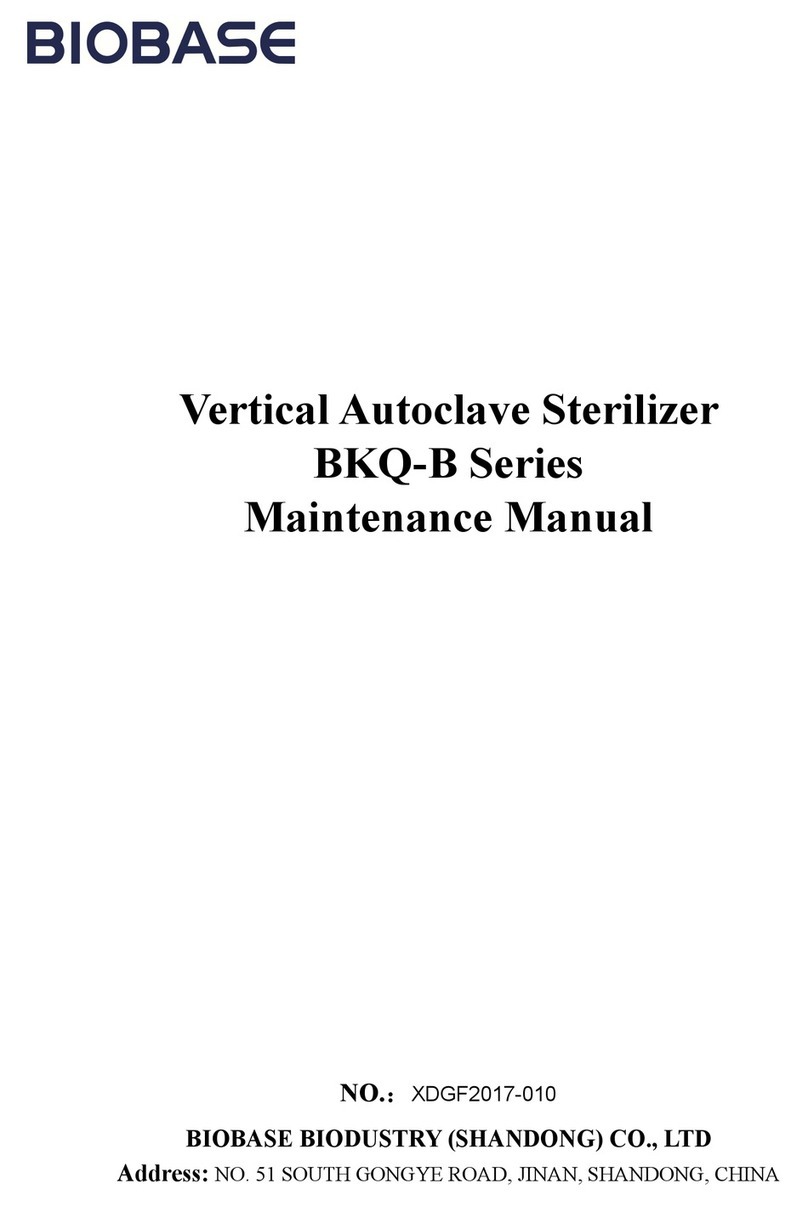
Biobase
Biobase BKQ-B Series User manual
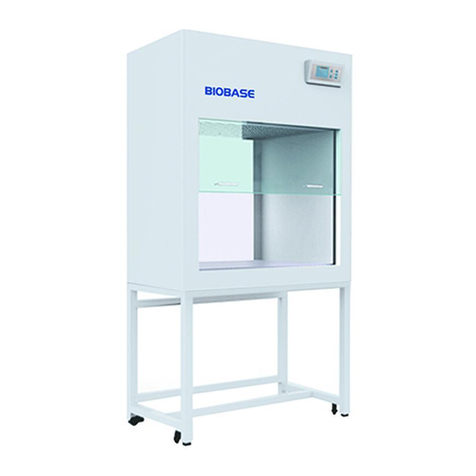
Biobase
Biobase BBS-V800 User manual

Biobase
Biobase BSC-3FA2-HA User manual

Biobase
Biobase BK-AutoHS96 User manual
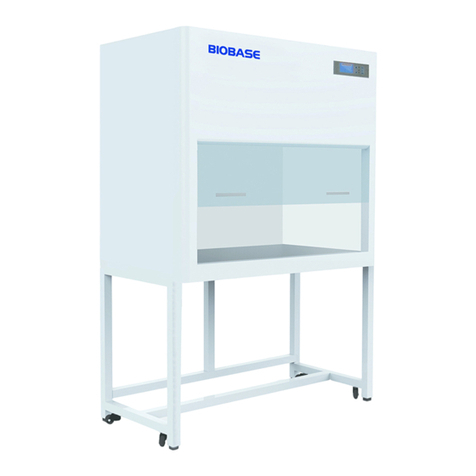
Biobase
Biobase BBS-DDC User manual
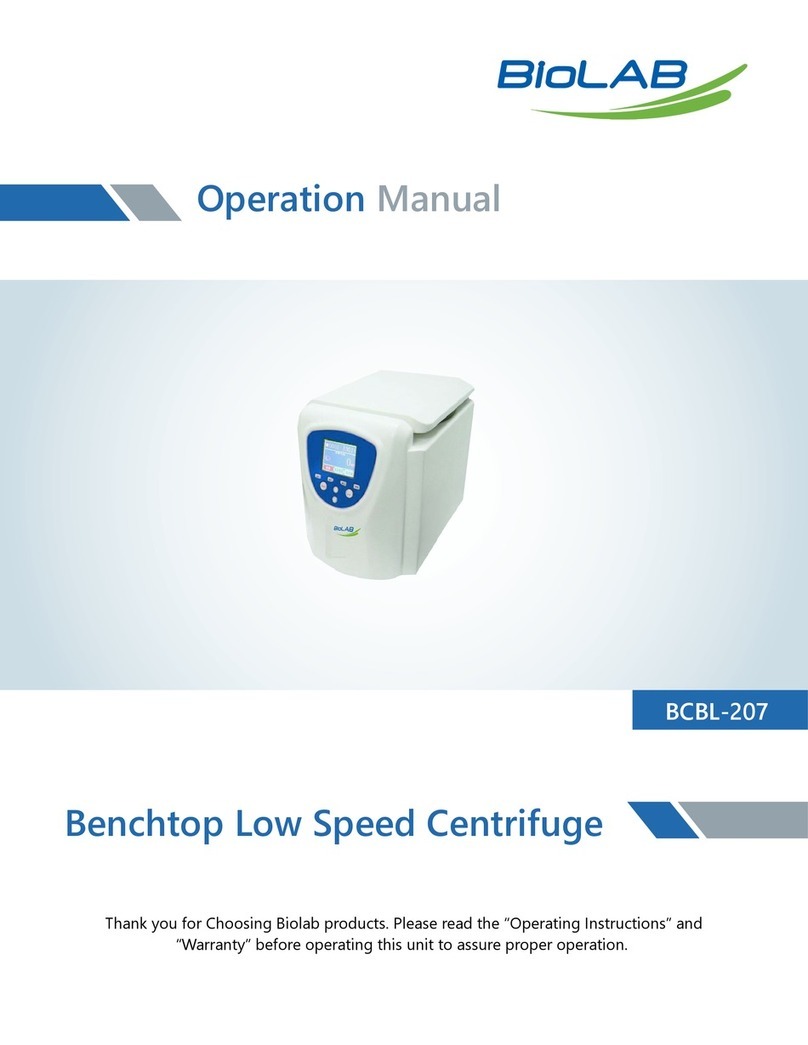
Biobase
Biobase BCBL-207 User manual
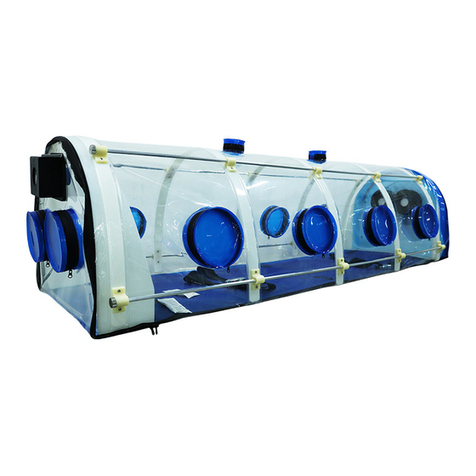
Biobase
Biobase BFG Series User manual

Biobase
Biobase BOV-V30F User manual