CKD ER300 User manual

SM−276677−A
INSTRUCTION MANUAL
PARECT
ELECTRO−PNEUMATIC
REGULATOR
ER300
●Please read this instruction manual
carefully before using this product,
particularly the section describing
safety.
●Retain this instruction manual with
the product for further consultation
whenever necessary.
Discontinue

[SM‑276677‑A]−1−
For Safety Use
To use this product safety, basic knowledge of pneumatic equipment,
including materials, piping, electrical system and mechanism, is re-
quired (to the level pursuant to JIS B 8370 Pneumatic System Rules).
We do not bear any responsibility for accidents caused by any person
without such knowledge or arising from improper operation.
Our customers use this product for a very wide range of applications,
and we cannot keep track of all of them. Depending on operating condi-
tions, the product may fail to operate to maximum performance, or
cause an accident. Thus, before placing an order, examine whether the
product meets your application, requirements, and how to use it.
This product incorporates many functions and mechanisms to ensure
safety. However, improper operation could result in an accident. To pre-
vent such accidents, read this operation manual carefully for proper
operation.
Observe the cautions on handling described in this manual, as well as
the following instructions:
Failure to pay attention to DANGER notices may cause a
situation that results in a fatality or serious injury and that
requires urgent addressing.
Failure to pay attention to WARNING notices may result in a
fatality or serious injury.
Failure to pay attention to WARNING notices may result in injury
or damage to equipment or facilities.
※1)IS0 4414 :Pneumatic fluid power・・・Recommendationsfor the application
of equipment to transmission and control systems.
※2)JIS B 8370:General rule for pneumatic systems
DANGER:!
WARNING:
!
CAUTION:!
Discontinue

[SM‑276677‑A] −2−
DESIGN AND SELECTION
1)Inferior quality air will deteriorate the product characteristics and affect its
durability badly. Use an air dryer, filter and sub micron filter to eliminate solid
material, moisture and tar and thus provide clean air from the pressure source.
In the case where the secondary side air pressure is reduced, the secondary side
air flows through the model ER300 and will be discharged from the exhaust port.
The inside of the secondary piping and that of the load side should be kept clean.
Otherwise, similar conditions such as deteriorated product characteristics result.
2)The products response capability will be affected by the working pressure and load
volume. When a stable response is required, regulate the working pressure.
3)When the product is used with the secondary side being opened to the atmosphere
as in the case of air blowing, air pressure may vary depending on conditions of
piping and air blowing. In such a case, be sure to test the product under actual
using conditions or contact us in advance.
4)Select only the dryer, air filter, oil mist filter and regulator having the flow rate
higher than that used for PARECT units.
Recommended air circuit
Air filter
5μ m
Regulator
Pressure
switch
Oil mist filter
Air dryer
Pneumatic
equipment
ER300
Fig1
!
CAUTION
Discontinue

[SM‑276677‑A]−3−
MOUNTING, INSTALLATION AND ADJUSTMENT
1)Be sure to follow the instructions provided below. Failure to follow these
instructions may hamper normal pressure control.
*Never adjust the primary pressure to less than that of the secondary pressure
+0.049MPa while the input signal is on.
*Never send an input signal (this includes the power supply with the voltage
input type) when the primary pressure is at atmospheric level.
*Install a pressure switch capable of detecting the ER300 primary pressure and
turning off input signals (this includes the power supply with the voltage input
type) to the ER300 when pressure is reduced.
Reference:
The pressure switch setting must be the maximum set pressure +0.049MPa or
more, at the ER300.
*Never connect the power supply and input signal groundingline to the ER300
body.
2)The best measures against noise such as of solenoid valve etc. is through surge
protection with CR, Diode (DC) etc.
The following measures are also acceptable:
* Separate the power line from the ER300 signal cable.
* Connect the ER300 signal cable with the shield cable. *1
* Install a line filter in the ER300 source power supply (for example, when using
the DC power supply pack, install in the DC power supply pack AC side).
Warning:
When the above precautions are not provided, normal pressure control cannot
be guaranteed.
Important: * Connect the shield to the GND.
* For the connection between the V, S, and M terminals, divide
the
shield cable.
*When only the 2-core shield cable is available mate V-C, S-C,
and M-C.
3)The monitor output signal voltage differs with the device type, and varies
individually in the certainrange among the products.
When using the function, confirm the output voltage.
Monitoring accuracy will not differ at either output voltage level.
When connecting various types of detector devices to the monitor output, use
those with an input impedance of over 1MΩ.
USAGE AND MAINTENANCE
1)When the primary side pressure is applied to the unit, do not loosen the screw
securing the orifice. Otherwise, the orifice will fly out.
2)Do not disassemble the unit because it will fail. Operations of the disassembled
unit will not be guaranteed.
!
CAUTION
!WARNING
Discontinue

[SM‑276677‑A] −4−
INDEX
ER300 Series
PARECT Electronic Regulator
INSTRUCTION MANUAL No.SM‑276677‑A
1. PRODUCTS
1.1 Specifications ・・・・・・・・・・・・・・・・・・・・・・・・・・・・・・・・・・・・・・・・・・5
1.2 Dimensions・・・・・・・・・・・・・・・・・・・・・・・・・・・・・・・・・・・・・・・・・・・・6
2. WIRING
2.1 Terminal Box・・・・・・・・・・・・・・・・・・・・・・・・・・・・・・・・・・・・・・・・・・・7
2.2 Connection・・・・・・・・・・・・・・・・・・・・・・・・・・・・・・・・・・・・・・・・・・・・7
3. PRODUCT OPERATION
3.1 Adjustment・・・・・・・・・・・・・・・・・・・・・・・・・・・・・・・・・・・・・・・・・・・10
4. HOW TO ORDER・・・・・・・・・・・・・・・・・・・・・・・・・・・・・・・・・・・・・・・・11
DEC.01.1999
Discontinue

[SM‑276677‑A]−5−
1.PRODUCTS
1.1 Specifications
Model
Item ER310 ER350 ER380
Media (Refer to CAUTION) Cleaned air
Working pressure range 150kPa ‑ 200kPa 0.54Mpa ‑ 0.59MPa
0.83Mpa ‑ 0.88MPa
Pressure control range 0kPa ‑ 98kPa 0Mpa ‑ 0.49MPa 0Mpa ‑ 0.78MPa
Input Voltage rate
0VDC ‑ 10VDC .0VDC ‑ 5VDCVoltage
3‑wire type
Input impedance 10kΩ
Input current rate
4mA ‑ 20mA(No power supply required)
Input
Signal
Current
2‑wire type
Input impedance 500Ω or less
Power supply voltage DC11V ‑ DC16V
(Stadilized power supply with a ripple rate of 1%or less)
Consumption current ※4 10mA or less(three wire type)
Hysteresis 1%F.S. or less ※1
Linearlity ±0.5%F.S. or less ※1
Maximum flow rate ※2 700L/min(ANR) 2000L/min(ANR) 2500L/min(ANR)
Step response ※3 2sec or less(no load)
Air comsumption rale (ANR) 3L/min or less
Withstanding vibration 39m/s2(30Hz)
Working temperature range 5℃‑ 50℃
Monitor output ※4 1±0.3V ‑ 3.5±0.6V 1±0.3V ‑ 3.5±0.6V
1±0.3V ‑ 3.0±0.6V
Dimensions See to 1.2 Dimensions
Port size Rc1/4、3/8
Mass 0.9kg
※1.This specification is when the conotrol pressure range is between 10%F.S. and 100%F.S..
It is also assumed that secondary side circuit constitute a closed circuit. If the
product is used for such purposes as blowing, for example, a pressure fluctuation may
occur.
※2.Working pressure : Max. working pressure.
Control pressure : Max. control pressure.
※3.Working pressure : Max. working pressure, step rate :0%F.S.→100%F.S.
※4.Voltage input signal type only.
PRODUCTS
1
Discontinue

[SM‑276677‑A] −6−
1.2 Dimensions
Port size(D)
Rc3/8
Rc1/4
Fig2 Dimensions
PRODUCTS
1
Discontinue

[SM‑276677‑A]−7−
2. WIRING
2.1Terminal Box
To open the terminal box cap, ①remove the M3pan head screw, ②pull the cap lower part until the
lower claw disengages, and ③push the entire cap diagonally upward (refer to Fig3)
Fig3.Terminal Box
2.2 Connection
The connections are for power supply, for the input signal line, and for the pressure monitor line output.
The input connection differs in the voltage input type (3 line system) or the current input type (2 line
system).
1).Voltage Input Type (3 line system) Connection.
Use the 6mm external diameter, 3-core shield cable 0.5 -1.5mm2for a device controlled with
input signal of 0VDC -10VDC or 0VDC -5VDC voltage.
To avoid a malfunction caused by noise, the shield cable must be connected to Ground (Common)
at the operation side (Fig4). When used in an poor environment, power supply noise must be
eliminated with the line filter and the serge killer.
As Figure4 indicates, connect to the respective terminals as indicated in Fig5.
For the power supply, 11VDC ‑ 16VDC rated voltage (ripple rate less than 1%) can
be used. However, we particularly recommend the 12VDC±0.5% stabilized power supply.
Fig4.3-line Input Cable
WIRING
2
Discontinue

[SM‑276677‑A] −8−
Fig5.Voltage Input(3-Line System)Connection Diagram
2) Current Input Type (2-Line System) Connection
Use the 6mm external diameter, 2-core shield cable 0.5-1 5mm2for a device controlled with input
signal of 4mA -20mA current. To avoid connected to a malfunction caused by noise, the shield cable
must be connected to Ground at the operation side as same as at the Voltage Input Type.
As Figure4 indicates, connect to the respective terminals as indicated in Fig7.
Fig6.2-line Input Cable
WIRING
2
Discontinue

[SM‑276677‑A]−9−
3) Pressure Monitor Output Connection
*The pressure monitoring function which the output pressure status is output as an electric signal can
be used only for the Voltage Input Type (3-Line System) device. It cannot be used for the Current
lnput Type (2-Line System).
*Connect to the terminals as indicated in Figure5, with the 6mm external diameter, 0.5-1.5mm22-core
shield cable as indicated in Fig8
Fig7.Current Input (2-line System) Connection Diagram
Fig8.Monitor Output Cable
WIRING
2
Discontinue

[SM‑276677‑A] −10−
3. PRODUCT OPERATION
3.1Adjustment
The Parect Electronic regulator’s zero point and span point are factory adjusted at the time of shipment.
Zero and Span adjustment at factory
Model Zero(MPa) Span(MPa)
ER310 0 0.098
ER350 0 0.49
ER380 0 0.78
If necessary, in accordance with the following procedures after mounting a pressure gage of
accuracy commensurating with the accuracy expected on the secondary side.
Procedure−1 Adjust operational pressure.(primary side).
Procedure−2 Zero point adjustment
First, turn on the power and set the signal to 0 V (4mA for the current input type). Then, set the
pressure to 0MPa by turning the zero point adjustment trimmer either clockwise or counterclockwise.
(Clockwise turn of the trimmer increases the pressure and counterclockwise turn of the trimmer decreases
the pressure.)
Procedure−3 Span adjustment
First, turn on the power and apply the rated voltage or current (10 VDC, 5 VDC, or 20mADC
(depending on the model)). Then, turn the span adjustment trimmer either clockwise or
counterclockwise to obtain the rated output. (Clockwise turn of the trimmer increases the
pressure and counterclockwise turn of the trimmer decreases the pressure.)
Note1.As zero point adjustment and span point adjustment affect the setting of each other, be sure to
perform these adjustments alternately in order to effect the correct settings.
Note 2. Since adjustment trimmers are highly sensitive, output pressure will varies greatly with only a
slight change in trimmer settings, and great care is required when making the adjustment.
Specially the zero point adjustment responds with a time lag, any adjustments must be mad
slowly.
PRODUCT
OPERATION
3
Discontinue

[SM‑276677‑A]−11−
4.HOW TO ORDER
ER3 A 0−B C −D
Symbol Optional blacket
No symbol
Nothing
BBlacket attached
Symbol
Port size
08 Rc1/4
10 Rc3/8
Symbol Input signal
00VDC ‑10VDC
10VDC –5VDC
24mADC ‑20mADC
Symbol Pressure control range
10kPa –98kPa
50MPa ‑0.49MPa
80MPa ‑0.78MPa
MODEL
4
Discontinue
Table of contents
Other CKD Controllers manuals
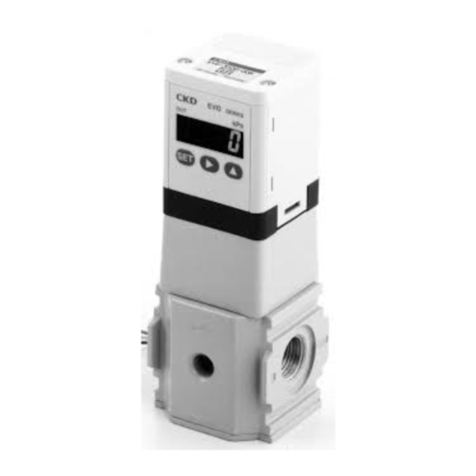
CKD
CKD EVD Series User manual

CKD
CKD ECS Series User manual
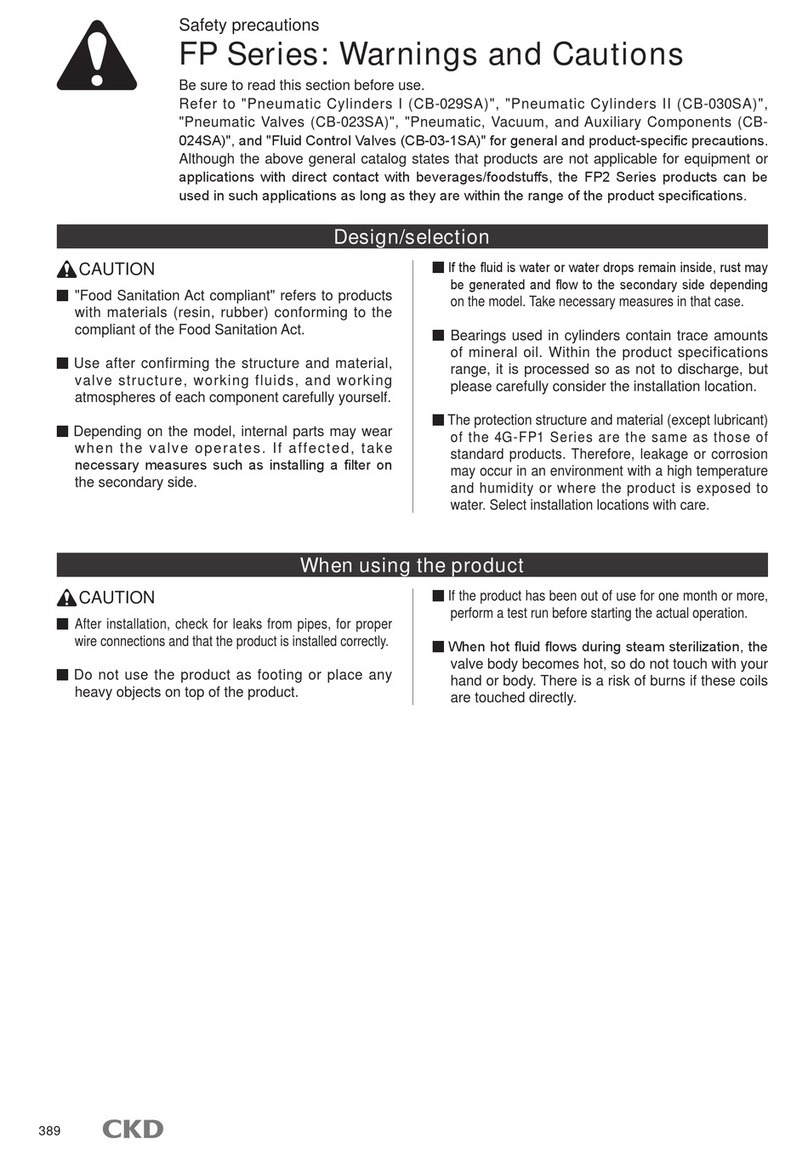
CKD
CKD FP Series User manual
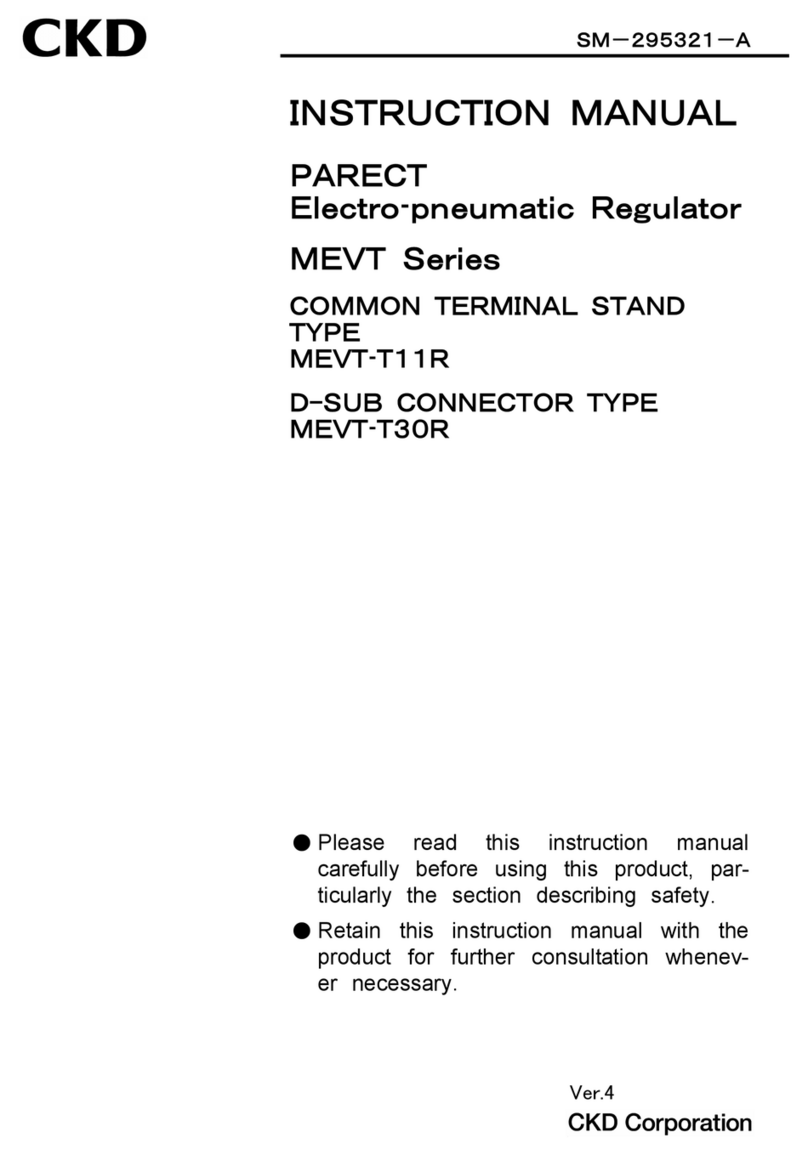
CKD
CKD PARECT MEVT Series User manual
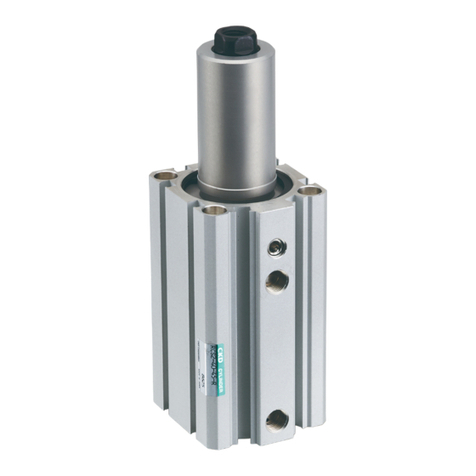
CKD
CKD RCS2 Series User manual
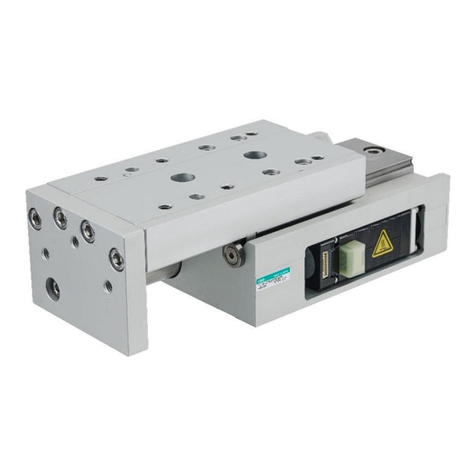
CKD
CKD FLCR-G Series User manual
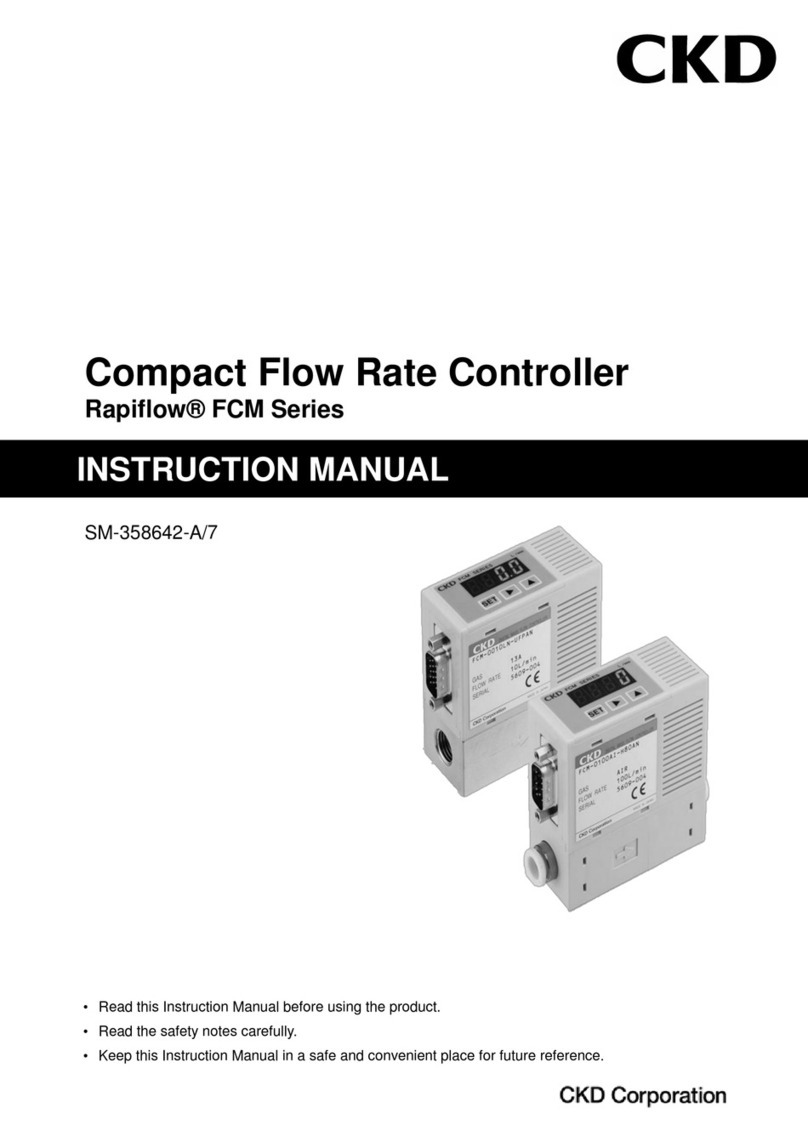
CKD
CKD Rapiflow FCM Series User manual
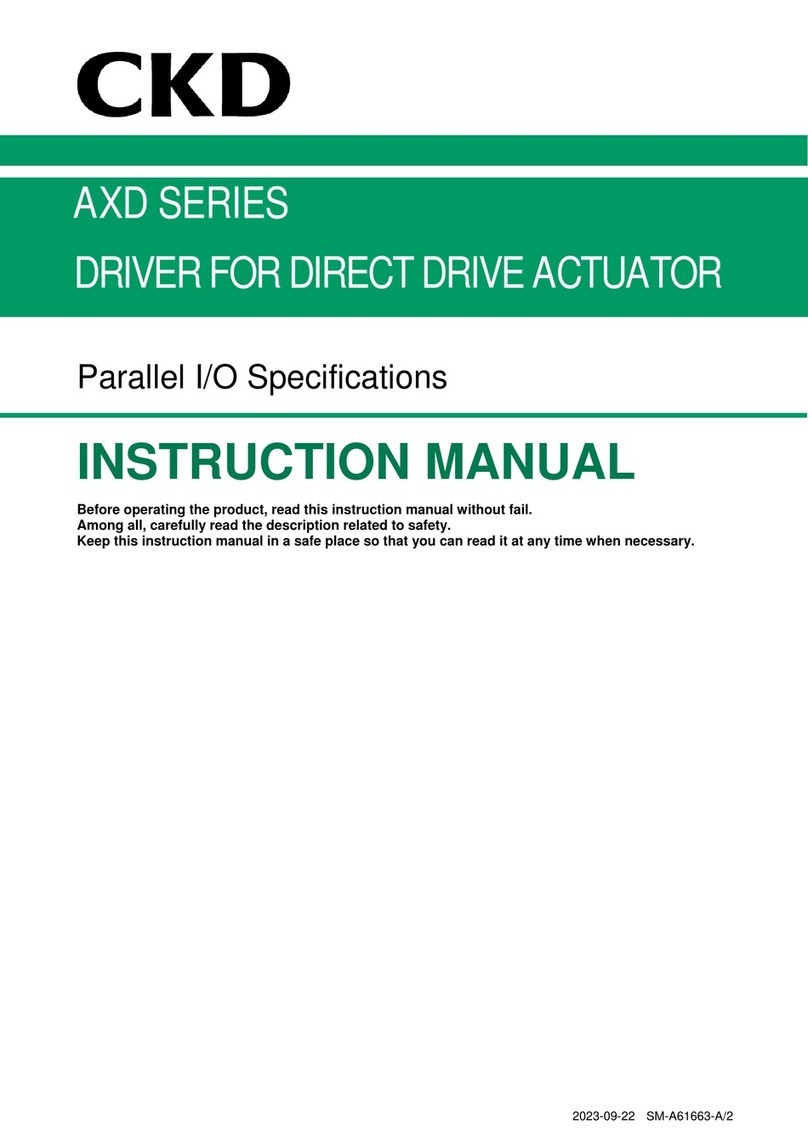
CKD
CKD AXD Series User manual
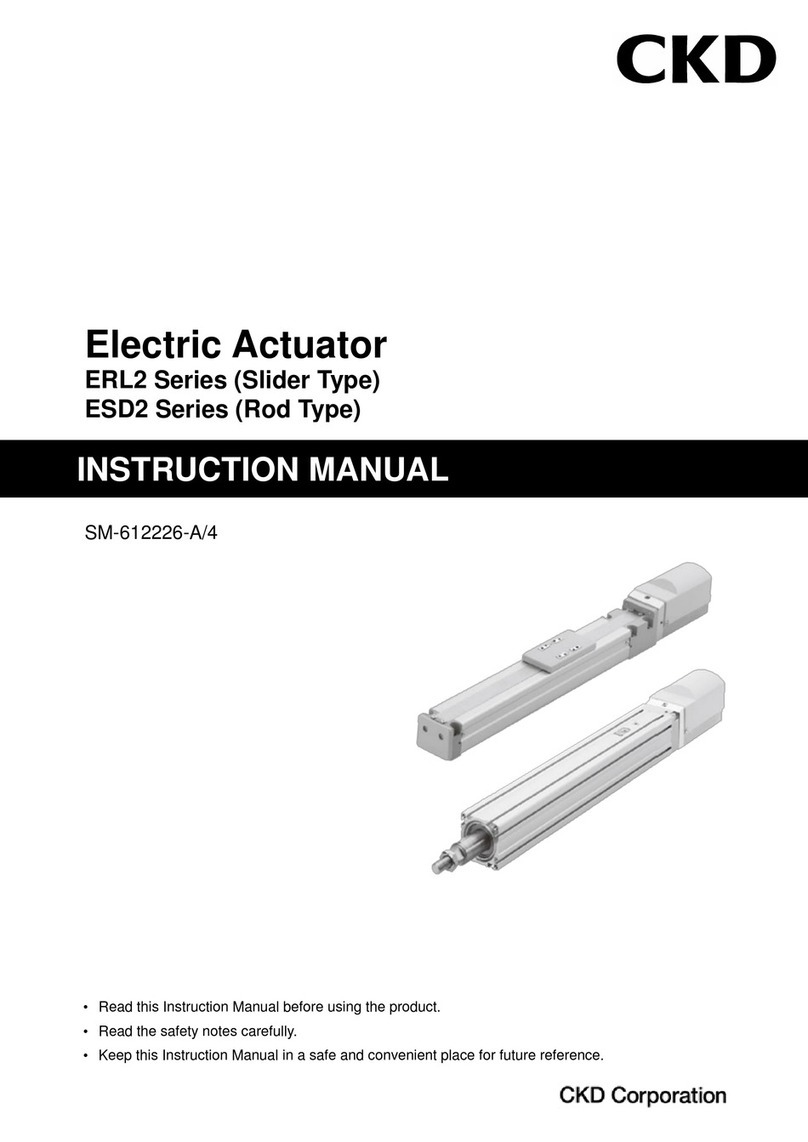
CKD
CKD ERL2 Series User manual
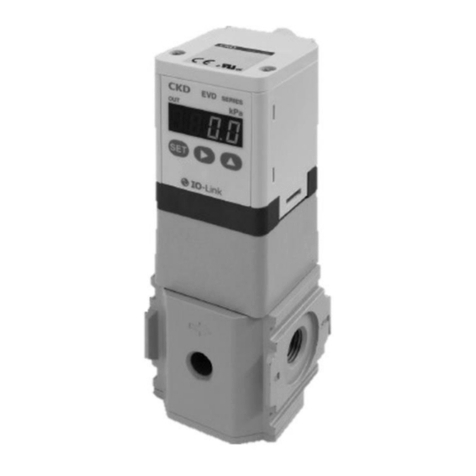
CKD
CKD EVD-1000 Series User manual
Popular Controllers manuals by other brands

Emerson
Emerson Bettis RGS Q-Series Installation, operation and maintenance manual
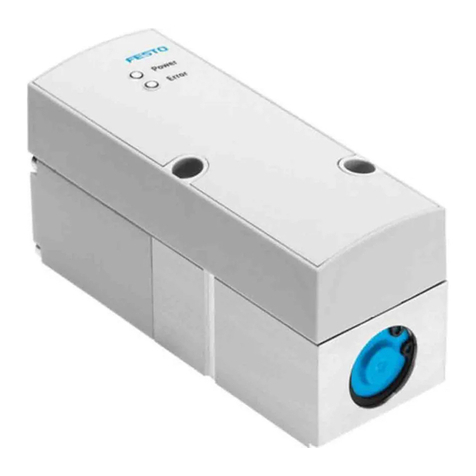
Festo
Festo VPPM-6TA-L-1-F-0L10H Assembly instructions
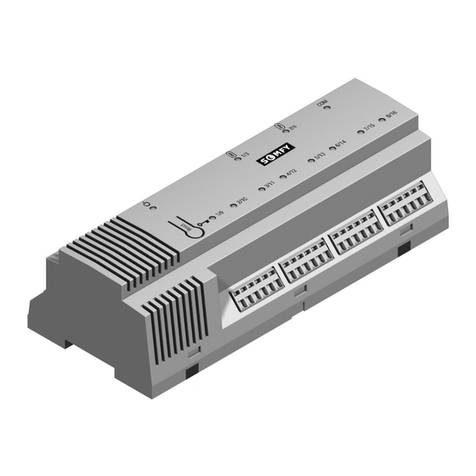
SOMFY
SOMFY animeo IB+ 9001614 installation guide
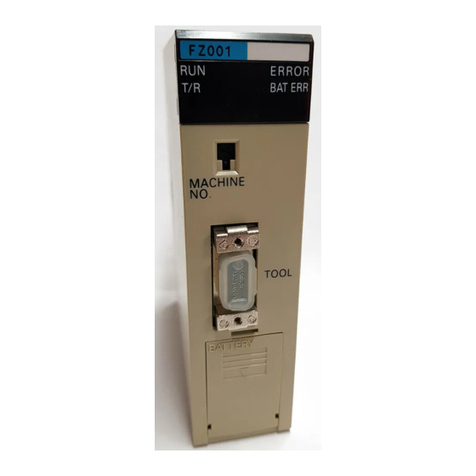
Omron
Omron SYSMAC C200H-FZ001 Operation manual
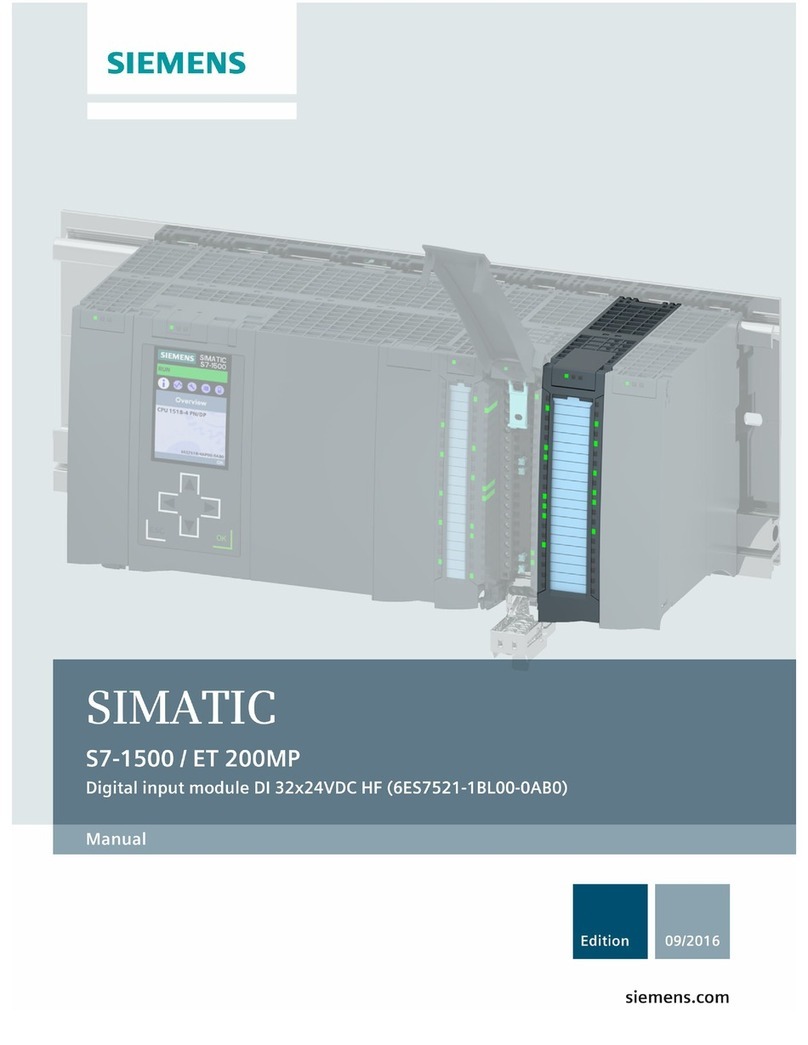
Siemens
Siemens simatic ET 200MP manual
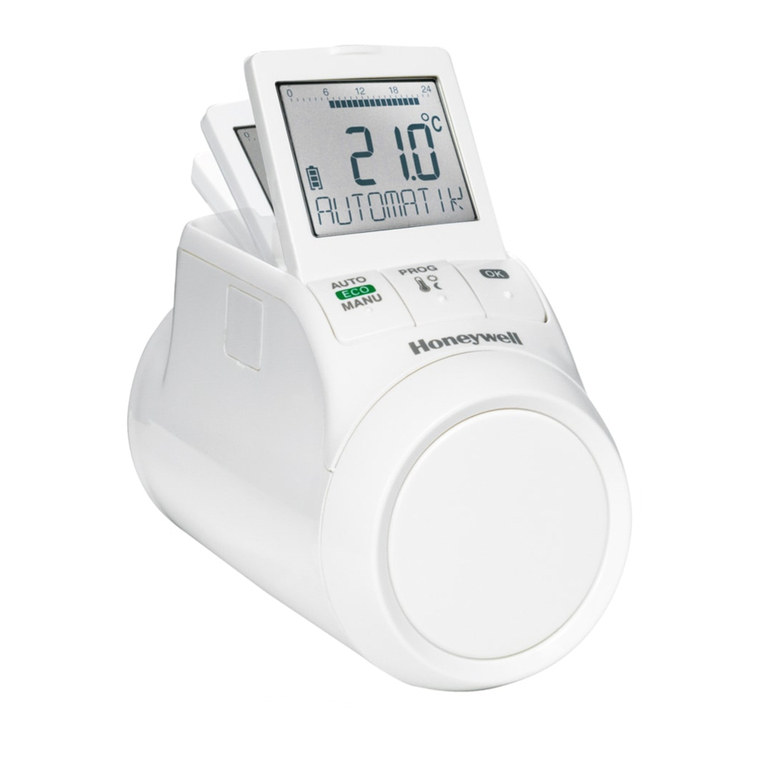
Honeywell Home
Honeywell Home TheraPro HR90 owner's guide