FUTABA PCM1024H User manual

Futaba
DIGITAL PROPORTIONAL
RADIO CONTROL
PCM1024H
PULSECODEMODULATIONSYSTEM
D60914

Thankyou for purchasing a FUTABA
digitalproportionalradiocontrolset
Please read this manual carefully before using your set
The last page of this manual
isathree-partfoldout
Refertothisfoldoutwhenreadingthemanual.
TABLE OF CONTENTS
FEATURES
.......................1~2
SET CONTENTS..................... 3
RATINGS ......................... 3
RECEIVER
AND
SERVOS
.............
4~5
Nicd
BATTERY CHARGING
.............
6
BASIC TRANSMITTER T9VHP CONTROL . . . 7~9
OPERATING INSTRUCTIONS
TIMER ....................... 10-11
TACHOMETER .....................12
LOW BATTERYWARNING ..............
12
BACK-UPWARNING ..................13
<SYSTEM PROGRAMMING>
EDIT PROGRAM KEY
.................
13
REVERSE
........................
14
FAIL SAFE (F/S) ................. 14-15
ADJUSTABLE TRAVEL VOLUME (ATV) ..... 16
ADJUSTABLE FUNCTION RATE
(AFR)
......
17
DUAL RATE (D/R) ................ 18-19
END SOFT KEY ..................... 19
EXPONENTIAL
(EXP)
..............
20-21
MIXING .......................... 22
PROGRAMMABLE
MIXING
...........
23-27
PITCH
PITCH CURVE
..................
28-30
HOVERING PITCH/PITCH TRIM .........31
HOVERING OFFSET .................
32
RUDDER MIXING (ROTOR DIRECTION,
REVOLUTION MIX, ACCELERATION MIX,
RUDDER
OFFSET)
................
33-34
SWASH MODE
...................
35-37
THROTTLE MIXING
...............
37-39
THROTTLE CURVE
...............
38-39
HOVERING THROTTLE
.............
38-39
IDLE-UP 1, 2 ....................
40-41
THROTTLE
HOLD
(AUTO ROTATION)
.
. .
42-43
RUDDER TO THROTTLE
(RUDDER^THROTTLE MIX) ............
43
TRIM
(CROSS
TRIM, TRIM MEMORY)
....
44-45
PARAMETERS (SERVO TEST, MIXING MODE.
PCM/PPM, D/R SW DIR. COMBI SW)......... 46
MODEL SELECTION .................. 47
MODEL COPY ...................... 48
NAME . .........................49
SERVO (TEST
MODE)
.................
50
RESET
..........................
50
SPLINED HORNS .................... 51
SOFT MAP
1
....................
52-53
T9VHP TRANSMITTER CONTROLS
.....
54-55
SOFT MAP 2
.......................
56
SERVO EXPLODED VIEW
..............
57
WARNING:
The FUTABA PCM1024H system has numerous operating features and is designed for serious and experienced radio con-
trol
hobbyists. Newcomers
to
the
hobby
should
seek
advice
and
assistance
in operating this
set.
Improper
operation can
result in property damage and/or serious personal injury. Radio control model helicopters and airplanes are not toys. If
you are new to the hobby, it is recommended that you contact your local hobby dealer regarding clubs and individuals
offering advice and assistance to beginners.

•FEATURES
The PCM1024H was specially-developed to meet the needs of the serious and demanding
R/C Helicopter hobbyist. Numerous features make this system adaptable to a wide variety
of complex radio control helicopters and stunt and scale aircraft. This is the most advanced
system available for FAI R/C Helicopter (F3C) competition. The built-in microprocessor
utilizing PCM (Pulse Code Modulation) makes this set very versatile and extremely noise and
deadpoint resistant.
Please read this manual carefully before using your set.
TRANSMITTER FP-T9VHP
• Programming data is displayed pictorially and
graphically on a large, easy-to-read
LCD
(Liquid Crystal Display) panel. Programming
and Cursor keys allow convenient adjustment
of aircraft functions.
•"1024"
Channel Resolution: New 1024 PCM
encoder format provides unexcelled servo reso-
lution and response time.
•RF
module uses a narrow
band modulation
circuit and PCM transmission.
• Precise control is made possible by three dif-
ferent endpoint adjustment functions: Adjust-
able Travel Volume (ATV), Adjustable Func-
tion Rate (AFR), and Adjustable Trim Rate.
• Dual Rates, Exponential, and Variable Trace
Rate (VTR) functions provide unlimited flexi-
bility
in
"fine
tuning"
aircraft
control
response.
• There are many functions for collective pitch,
throttle, and rudder, including four adjustable
pitch and throttle curves (plus inverted pro-
gram). Precise and convenient adjustments
enable optimum helicopter performance.
• Four programmable mixing circuits allow many
diverse applications for the control of complex
helicopters and fixed-wingaircraft.
• Four kinds of "swash plate mixing" are avail-
able for direct control and mixing of cyclic and
collective pitch functions (CCPM).
•Programming for up to 6 different models (in-
cluding model name) can be stored in the trans-
mitter memory. Memorized
data is protected
by a 5 year lithium battery.
• Accessory "Sub-Trimmers" are provided on the
transmitter front for convenient field adjust-
ment of frequently-used functions.
•Trim
positions
for
each
model
can be memo-
rized by the Trim Memory Function, allowing
the
trim
levers
and sub-trimmers
to
be returned
to neutral. Neutral positions can be reproduced
in the future, or copied onto another model
program
if desired.
• The Tachometer function measures engine rpm
by means of a built-in sensor.
• Speed (rpm)
can be measured for 1 to 5 bladed
propellers.
• Digital alarm/timer has
Up, Down,
and Rhyth-
mic timing modes.
• Integrating (Total
Timer) timer monitors total
transmitter
ON
time.
• Ball bearing open gimbal sticks, angled switches,
and "human-engineered" transmitter case en-
hance the feeling of comfort and precision in
transmitter operation.
• "Quick Change" Nicd battery pack is easily
accessable by means of a convenient panel
on
the transmitter back.
• Power Off function turns off the transmitter
power automatically if the controls are not
operated for 30 minutes.
• PCM or standard PPM operation can be se-
lected. (Allows operation of standard FM
receivers on the same frequency.)
• DSC (Direct Servo Control): The
DSC
cord
allows
operation
of
all
servos
without
turning
on the transmitter. The voltage of the trans-
mitter and receiver Nicd batteries can also be
read simultaneously using the cord.
• Servo reversing is available on all channels.
•Auto
Dual Rate:
If
desired, aileron, elevator,
and rudder dual rate can be turned ON and
OFF automatically, according to throttle stick
position.
• Stick length and angle is easily adjusted.
• Knobs and levers are conveniently located for
adjustments of Idle-Up functions. Revolution
Mixing, Hovering Throttle and Pitch, etc.
[1]

RECEIVER FP-R129DP
• Extremely quick response, high resolution, and
high reliability are achieved with a newly-
developed, low voltage PCM decoder.
• RF amplifier and monolithic IF amp designed
for high sensitivity.
• Dual conversion
"1991"
design with ultra
narrow-band ceramic filter is immune to ad-
jacent band interference (cross modulation
interference, mutual modulation interference)
and spark noise.
• Fail Safe and Battery Fail Safe functions
provide greater safety and reliability.
•Servo Hold function eliminates "glitches"
during momentary signal losses or strong inter-
ference.
• Gold-plated connector pins provide positive
contact.
• DSC System: Operation of all servos is possible
without turning on the transmitter by connect-
ing the accessory cord directly to the C termi-
nal of the receiver.
SERVO FP-S9201
•High
torque
and high speed water-and dust-
•Fiberglass
reinforced PBT
(polybutylene
proof
servo
with
highest-quality
coreless
motor,
terephthalate)
molded
servo
case
is
mechanical-
Output torque 5 kg-cm (69.5 oz.-in.). Operat- ly strong and invulnerable to glow fuel.
ing speed 0.22 sec/60 . • Strong polyacetal resin, ultra precision servo
• New indirect drive potentiometer improves gears ensure smooth operation, positive neu-
vibration and shock resistance and neutral tral, and minimal backlash.
precision tremendously. • Fiberglass reinforced epoxy resin PC board
• Futaba custom 1C provides high starting with thru-the-hole plating improves reliability
torque, narrow dead band, and excellent against shock and vibration.
trackability. Neutral holding force is also im- • Seven special adjustable splined output arms.
proved substantially.

•SETCONTENTS
Model
Transmitter
Receiver
Servos
Switch
Nicd Battery
Misc.
PP-9VHP
FP-T9VHP x 1
FP-R-129DPx 1
FP-S9201 x 5
SSW-J x 1
NR-4LBx 1
Battery charger, extension cord, DSC cord, CHG adaptor, DSC-CHG cord,
frequency flag,
spare
output
arms, neck strap,
screws
•RATINGS
Transmitter FP-T9VHP Servo FP-S9201
Operating System : Two-stick, 9 Channel, PCM
TransmittingFrequency: 72MHzCH.12—CH.56,
53MHz, and 50MHz
Modulation : FM-PCM/PPM selectable.
Power Requirement : 9.6 volt (8/500mAH) internal
Nicd battery
Current Drain : 230mA
Receiver FP-R-129DP
Control System + pulse width control
1520)iSneutral
Operating Angle Each direction from neutral —
45° or greater (including trim)
Power Requirement 4.8 volt Nicd battery (shared
w/receiver)
Current Drain 8mA at 4.8V (at idle)
Output Torque 5 kg-cm (69.5 oz.-in.)
Operating Speed 0.22 sec/60°
Dimensions 40.5 x 20 x
35.5mm
Weight 50g(1.8oz.)
Receiving Frequencies 72MHz, 53MHz, and 50MHz
Intermediate Frequency 1st IF : 10.7MHz
2nd IF:455kHz
Power Requirement 4.8 volt Nicd battery (shared
w/servos)
Current Drain 35mA (4.8V reception)
Dimensions 60.3x37.8x24.1mm
Weight 45g(1.6oz.)
Receiving Range 500m (1,500 ft.) ground
1,000m (3,000ft.) air
(WhenFP-T9VHPusedunder
best radiowave conditions)
Voltage : 4.8V 1,000mA
Dimensions : 56 x 67 x 14.8mm
Weight : 1 20g (4.2 oz.)
Receiver and Servo
Nicd
Battery Pack NR-4LB
Charger FBC-6B (2)
Input Voltage : 1 20VAC, 60Hz, 4W
Output Voltage : TX side 9.6V, 50mA
RXside 4.8V. 100mA
(Specifications are subject to change without prior notice.)

PIT Pitch
(Collective)
AUX1 Accessory 1
AUX2 Accessory 2
CH9 Channel 9
•RECEIVERAND
SERVOS
Receiver, servo, switch, and battery connections
The channel order is:
AIL Aileron
ELV Elevator
THR Throttle
RUD Rudder
(Tail rotor)
GER Retract gear
(Rate gyro
output
switching)
PRECAUTIONS
•Connect
the
receiver,
servos,
switch
harness,
etc. as shown in the figure. Extend the trans-
mitter and receiver antennas to their full
length. Turn on the transmitter power switch,
then turn on the receiver power switch. The
servos will go to their neutral position. Move
the transmitter sticks one at a time to check
that each servo follows its control stick move-
ment.
•Connect pushrods and linkages to the servos
and check that the direction of travel of each
servo matches the direction of movement of its
control stick. If a servo does not move in the
proper direction, use the servo reversing func-
tion
(See
page
14).
•
Operate
each
servo
to
its
full
extent,
and check
for binding and/or excess slop in the linkage or
pushrod. Unreasonable force on the servo arm
may damage
the
servo and
will
drain
the
bat-
teries very quickly.
• Adjust servo output arms and aircraft control
linkage as necessary so that each servo moves
smoothly throughout its full range of travel,
even when the control stick and trim lever are
operated simultaneously in the same direction.
•
Be
alert for possible sources of electrical noise.
This set is noise-resistant,
but the use of noise-
less
parts
is
recommended.
•When
installing
the
switch
harness,
make sure
that the switch can move smoothly, to its full
extent in each direction without binding.
Install the switch where it will not be exposed
to engine oil, dust, dirt, etc. The switch can be
installed inside the fuselage and operated from
the outside with a piece of wire.
•
Do NOT shorten the
receiver
antenna or
fold
it
back along its length.
•When installing the servos, tighten the mount-
ing screws so that the rubber grommets
are
compressed
slightly.
If
the
screws
are
too
tight,
the vibration-dampening
effect of the grommets
will be lost and servo
damage may occur.
• The crystal can be changed
without opening the receiver
case. Always use a Futaba
matchedTX/RXcrystalset
to change frequencies.
• Extra servo output arms are
supplied.Usethem as needed.
• Use extension cords where necessary. RF
"chokes" are not required with the PCM
receiver.
• Wrap the receiver and the airborne battery
pack separately in foam padding. Padding
should be wrapped loosely for maximum vibra-
tion
protection.
Place
each
inside
a
waterproof
plastic bag and secure the end of the bag with a
rubber band.
• Use the rubber bands wrapped around the
receiver to hold the servo and switch leads.
•After installation and adjustments are com-
plete, perform a range check by collapsing the
transmitter antenna and extending the receiver
to its full length and operating the transmitter
from a distance of 60 to 90 feet from the
receiver (aircraft). The system should operate
normally at this range.
[4]

5 servos
supplied as
standard
Servo Neutral Trimmer
(rudder servo for
helicopter)
(This trimmer is
operative even when
the gyro control box
power switch is
turnedOFF.)
Gyro output
reversing switch
Gyro
sensitivity
adjustment
trimmers
Gyro
Gyro Control Box
Jumper Connector
Connector for 6V pack of five batteries
Motor Regulator Power Supply
(Insertthejumper connectorwhen
power supply shared w/ RX.)
Control Amplifier
Gear
(Rate Gyro
Output Switching)
Extension
cord
Aileron
Servo
Elevator Servo
Throttle Servo
Rudder (Tail rotor)
Servo
Pitch Servo
(Collective)
Pay careful
attention to connector polarity

BATTERY
CHARGING
INSTRUCTIONS
(Transmitter
and
Receiver
Nicd
Batteries)
Before operating your system, recharge the Nicd batteries as follows:
•Connect the DIN connector of the FBC-6B (2)
battery charger to the transmitter charging
socket, and connect the 3P connector to the
airborne NR-4LB Nicd battery pack and plug
the battery charger into a 120VAC outlet as
shown in the figure.
•The
TX
and
RX
LEDs
light
to
show
that bat-
teries are being charged. The Nicd batteries can
also be charged through the DSC-CHG cord by
connecting the CHG adaptor to the charger as
shown in the figure. This allows the NR-4LB
airborne Nicd pack to be charged without
removing it from the model.
•Normally recharge the battery for about 15
hours. If it has not been used for some time,
discharge and recharge it two or three times,
,TX (transmitter)
then charge it a full 15 hours.
• The amount of operating time before the bat-
teries must be recharged can be estimated by
checking the integrated timer at the moment
the TX battery alarm sounds (antenna ex-
tended).
• Leaving batteries in the discharged state for a
long time will adversely affect their capacity
and life.
• The TX and RX Nicd batteries can be charged
simultaneously or independently.
• A fully-charged TX battery can be used for
about 10 flights of 10 minutes each. The air-
borne NR-4LB Nicd battery pack can be used
for about 7 flights when 5 servos are used.
Make this connection
when using the DSC.
DSCcord
Charging
socket
and
DSC
connector
Male
Female
CHG
Adaptor
Male
the aircraft fuselage
to use the charging
and DSC socket.
Female
Male
Cut here.
or during contests, etc.
•When the DIN connector of the
DSC cord is connected to the DSC
socket, the power to the encoder of
the transmitter is turned ON auto-
matically. The transmitter power
switch is left OFF.
• When not using the DSC, discon-
nect the DIN connector to reduce
battery drain.
• To operate the servos, turn on the
airborne switch, (only)
NR-4J
• The DSC (Direct Servo Controller)
system connects the signals from
the transmitter directly to terminal
C of the receiver through the DSC
cord and controls the servos with-
out transmitting radio waves. It is
extremely convenient when other
flyers are on the same frequency,
AC-120V
Charger FBC-6B (2)
RX (receiver)
Female
Receiver
Female
DSC-CHGcord
Female
Install the accessory
DSC-CHG cord
(connectorwithtab)
to the side of
Female
• When the
DSC
cord
is connected, the receiver
power supply voltage
is measured
(no load).
The voltage is displayed
bv "Ex" on the lower
right
side
of the
initial
LCD screen.
[6]

•BASIC TRANSMITTER T9VHP CONTROLS
Refer to the fold-out illustration at the back of the manual.
Aileron Control (Right and Left Cyclic on
helicopter)
Elevator Control (Fore and Aft Cyclic on
helicopter)
Throttle Control (Throttle and Collective
Pitch (T/C)onhelicopter)
Rudder Control (Tail rotor on helicopter)
CH5 Switch Multiple uses depending on pro-
gramming by modeler.
• Landing Gear (fixed wing aircraft)
• Rate gyro output sensitivity switching (heli-
copter)
•COMBI Switch - Rudder offset, Idle-Up.
and Dual rate can be turned ON and
OFF.
• Inverted flight switch
Hovering Pitch
Lever — left side of transmitter
CH6 Control Lever (In BASIC mixing mode)
AileronDual RateON/OFFSwitch
Elevator Dual Rate ON/OFF Switch
Rudder Dual Rate ON/OFF Switch
NOTE: Functions of the D/R switches can
be selected, combined, ON/OFF directions
changed, etc. (See
page 46)
Revolution Mixing (Pitch ->• Rudder Mixing)
UPSide Knob
Revolution Mixing (Pitch -> Rudder Mixing)
DOWN Side Knob
Idle-up1ON/OFFSwitch
Idle-up 1 Knob
Idle-up2ON/OFFSwitch
Idle-up 2 Knob
Hovering Throttle Trim Knob
Throttle Hold Switch
Pitch control servo
total travel
Throw can be adjusted within this range
with the lever when the throttle stick is in
the neutral position.
CH7 Control Knob Pitch Trim Knob (If func-
tion
activated)
CH8 Control Switch COMBI Switch (if se-
lected) - RUD offset, Idle-Up, and D/R ON/
OFF
Aileron Trim Lever
Elevator Trim Lever
Throttle (ATL) Trim Lever
LOW
HIGH
Servo travel by
throttle trimming
— right side of trans-
12 RudderTrim Lever
13 High Pitch
Trim
Lever
mitter
Non-Slip Adjustable Control Sticks
The length of the control sticks can be ad-
justed to suit operator preference.
Unlock
Parts
A
andB
by turning them in op-
posite directions as indicated by the arrows,
and adjust the control stick to the most com-
fortable length.
Adjustable Stick Angle
The horizontal angle of the control sticks
can be adjusted.
Phillips
Screwdriver
Turn this screwwith a
Phillips screwdriver.
The open gimbal stick angle
can be adjusted from about
3° to the inside to 4.5° to
the outside by turning the
adjusting screw as shown.
Adjust the control stick to
the most comfortable angle.
[7]

Transmitter RF Module
Transmitter crystal.
To
switch a frequency in
the same band, change
this crystal.
72MHz Band
53MHz Band
50MHz Band
To remove the module, pull
the module outward while
pushing tabs toward the
center.
Transmitter Battery Pack Replacement
and Spare Crystal Holder
Remove
the
battery
box
cover.
Lift
out
the
Nicd battery pack and disconnect the con-
nector.
Spare crystal holders
A temperature
rise in the RF module during
useisnormal.
NOTE: Be careful not to drop the Nicd battery
pack.
Opening Trimmer Panel and Key Cover
Mini Stand
Use this fold-out Mini Stand as shown when
laying the transmitter down. This makes
operation easier and protects the transmitter
and module.
NOTE: Flip up at both sides with your
fingers. Do not try to open the
panel at the center. The cover may
be damaged.
Flipupwiththetab
[8]

Screen contrast adjustment
Adjust the screen contrast with the special
screwdriver provided. The contrast increases
when the adjusting screw is turned clock-
wise.
Functions of Sub-Trimmers
Sub-trimmers are located on the front panel to
allow convenient trimming of programmed set-
tings on the field or during flight. Master the
computer functions before using them.
T
H. HOLD Throttle hold (TH. servo)
position adjustment
RUD.OFFSET Rudder offset adjustment
NOR.PI.LO
Normal pitch low side ad-
justment
IDL.UP1PI.LO Idle-up 1 low pitch adjust-
ment
IDL.UP2PI.LO Idle-up 2 low pitch adjust-
ment
HOLD Pl.LO.
Hold pitch low side adjust-
ment
RUD. -> THR. Rudder -> throttle mixing
adjustment
HOLD.PI.HI. Hold pitch high side adjust-
ment
Monitor Lamps Sub-trimmers do not operate unless the pertinent
function is set to
The POWER Lamp lights when the transmit-
ter power is turned ON.
The ALARM LED Lamp at the right:
• Blinks off once per
minute during Fail
Safe data transmission.
• Blinks on and off when an activated mix-
ing switch is ON (T. Hold, Idle-up, Invert)
• Lights steadily at all other times.
[9]

ADJUSTMENTS AND FLIGHT TECHNIQUES
•OPERATING INSTRUCTIONS.
• When adjusting and setting the transmitter functions, connect the receiver and servos, and
make the adjustments while observing the operation of the servos.
• Alternatively, when studying the operation of transmitter functions, remove the transmit-
ter RF module (to reduce battery drain). The effects of adjustments can be viewed on the
SRV program screen (See page 50).
•Set the power switch to the ON position. The standard screen shown below appears on the
LCDdisplay.
TACHOMETER
TIMER RESET KEYS
Pressing both keyssimultaneously,
resets the integrating timer.
Display will read 0:00:00.
Integrating Timer display
•Tx 10.1V Transmitter Voltage
• Ex 0.0V The receiver battery voltage can be measured by using the DSC cord supplied.
TIMER
The TIMER function can be used to monitor flying time, fuel consumption, at contests,
etc. Four different timing functions are available: Up Timer, Down Timer, Rhythmic Timer,
and Total (Integrating) Timer.
Timer Functions
1) Up Timer This timer counts up from zero in
1 second steps. Its maximum count is 59:59.
When the alarm time is set, a buzzer begins to
sound 10 seconds before the set time is up.
The buzzer also sounds at each 1 minute
interval. When the time reaches 59:59, timing
restartsfrom00:00.
2) Down Timer This timer counts down from
the set time in 1 second steps. Operation is
otherwise the same as the Up Timer.
3) Rhythmic Timer This is a 0.1 second cyclic
timer. A buzzer sounds at each set alarm
interval. When the set alarm interval elapses,
the counting automatically restarts.
4) Total (Integrating) Timer This timer records
the total transmitter ON time. It is very useful
for estimating remaining Nicd battery capac-
ity and monitoring total flying time. Maxi-
mum count is 59:59:59.
[10]

Setting Instructions
1) Display the standard screen.
2) Reset the Total Timer by pressing the two
RES
program keys simultaneously.
3)
Press
the
TIM
key. The TIMER program
screen
will
appear on the display. The
Up
Timer
will
be dis-
played first.
4) Select the UP (Up), DN (Down), or RYT (Rhythmic) timer mode by pressing the
program key. The example shown is for the Up Timer.
5) To set the alarm time, switch to the TIMER SET display by pressing the SET key. Move the cursor to
the timer mode to be set usinq the cursor keys. Pressing the
keywill
Set the alarm time with the programkeys.
When time and alarm setting is complete, return to the TIMER display by pressing the program key.
6) To start the timer, press the STA program key. The program key characters change to .When
the key is pressed, the timer stops.
7) When the program key is pressed, the display returns to the standard screen.
Timer Counting Range 1. UP/DN Timers 55min.59sec.
2. Total Timer 55 hrs. 59 min. 59 sec.
3. Rhythmic Timer 0.5sec. to 59.9 sec. interval
[11]

ADJUSTMENTS AND FLIGHT TECHNIQUES
TACHO METER
Tachometer
The tachometer function is used to measure the speed on one to five-bladed propellers, etc.
Speed (rpm) is measured up to a maximum of 50,000 rpm fin 20 rpm increments).
Setting Method
1) Display the standard screen, and press the
program key.
2) Press program key to to select the
number of blades.
Ex: for a two-bladed propeller.
3)
Measure
the speed by pointing
the
built-in
sensor on the transmitter (center of the left
side panel) at the front or rear of the propeller
disc from a distance of 8 to 12 inches. Be sure
the model is restrained by an assistant, and be
very careful of the rotating propeller.
Allow a few seconds for the display to stabi-
lize, then read the measured value. Maximum
speed range is 50,000 rpm.
LowBatteryWarning
This function operates when the transmitter
Nicd battery voltage drops below 8.5 volts. The
characters "LOW BATTERY" blink on the
screen, and a buzzer sounds. When this occurs,
land immediately and recharge or replace the
Nicd battery pack.
[12]

Back Up Warning
When the stored data is lost, the characters
"BACK UP" blink on the screen and a buzzer
sounds. When the power switch is turned on
again, the error display disappears and all the
settings return to the factory-set values. When a
Back Up error occurs, the back-up lithium bat-
tery is probably dead, or there is trouble in the
system. To locate the cause, call your Futaba
service center. The back up lithium battery life
depends on the usage state, but is about 5 years.
SYSTEM PROGRAMMING
Press the EDIT program key of the standard screen.
Reversing
Fail Safe
Adjustable
Travel Volume
Dual Rate
System functions are programmed
and adjusted by using the LCD
display screen, the five DATA
INPUT (Program) keys, and the
four CURSOR keys.
Adjustable
Function Rate
End
(Returns to
preceding screen)
Pressing the (EDIT) program key of the
standard
screen
will
display the
EDIT
or
"Menu"
screen. The cursorkeyscanbeand
used to move the cursor bar to Line 1, 2, or 3 of
the screen. The program keys are used to select
the desired programminq screen to be displayed.
NOTE: At all times, pressing the program
key will return the display to the next previous
screen. To return to the standard screen, just
keep pressing the key.
[13]

ADJUSTMENTSANDFLIGHT TECHNIQUES
REVERSE
ServoReversing
This
function
is
used
to
change
the
direction
of
servo
operation
in
relation
to control
stick
or /ever movement.
Setting Method
1) Select the EDIT screen, the select the RE-
VERSE screen by pressing the
program
pressing the or program key.
In the display example, (Rudder) is set
key. to REVERSE.
2) Select the desired channel with the
cursorkeys. 4) Return to the EDIT screen by pressing the
program key.
and
3) Select NORMAL or REVERSE operation by
FAIL SAFE
Fail Safe
Fail Safe and Hold Functions
The HOLD (Hold) and F/S (Failsafe) functions
are designed to allow the aircraft or helicopter to
"fly
through"
a
momentary
loss
of
signal
or very
strong interference, rather than experiencing the
familiar
"glitch"
as
the
servos
react
violently
to
the unwanted signal. These functions cannot be
expected to prevent a crash however, if the
normal signal interruption is of sufficient dura-
tion.
The HOLD function stops the servo at the posi-
tion held just before the normal signal is lost.
When a normal signal is again received, the Hold
function is released.
The FAILSAFE
function
will
move
a
servo
to
neutral or a pre-set position when the normal
signal is interrupted for 1 second or longer (The
system will remain in HOLD for the first 1
second of signal loss). When a normal signal
resumes, FAILSAFE is released.
BFS (Battery Fail Safe) Function
The BFS function moves the throttle (CH3)
servo to the pre-set Fail Safe position when the
airborne power supply is nearly exhausted. If no
Fail Safe position has been set, the throttle servo
will move to medium slow (neutral).
BFS can be released by lowering the throttle
Stick
past the
release
point
(adjustable),
or
with
the CH9 switch. Throttle control is then regained
for about 30 seconds. At the end of 30 seconds,
BFS
will
re-engage
and
the
throttle
will
again
move to the Fail Safe position. Whenever BFS
engages, land the aircraft as quickly as possible
and recharge or replace the Nicd battery pack.
[14]

Fail Safe and Hold General Instructions
Fail Safe
• F/S or HOLD can be selected for each channel
(1
to
8).
•Channels
selected
for
HOLD
will
remain
in
HOLD until a normal signal resumes. Those
selected for F/S will move to their pre-set posi-
tions after 1 second of signal interruption.
• F/S SET simultaneously stores the desired Fail
Safe position in the transmitter memory and
sends it to the receiver.
•The
F/S data
is
automatically
sent
to
the
receiver when the transmitter is first turned ON
and at one minute intervals as long as the trans-
mitter is left on.
• The F/S position can be checked with the
program key.
• Only the Throttle channel (CH3) can be set for
Battery Fail Safe.
Fail Safe Setting
1) Display the EDIT screen, then select the
FAILSAFE screen by pressing the pro-
gram key.
2) Move the cursor to the desired channel with
the and cursor keys and select
HOLD
or F/S for each channel by pressing the
or program key. When Failsafe is
selected, the number 50 will appear below the
appropriate channel on the POSI-(%) line of
the FAILSAFE screen.
3) Store the Failsafe positions in the transmitter
memory by pressing the key while hold-
Battery Fail Safe Setting
1) Set the Failsafe position on the throttle chan-
nel
(CH3) as described above. A position
slightly above the minimum engine idle
speed
is recommended.
2) BFS Release Point Setting (When
THR
is
designated as the release channel)
• Move the cursor to the B/FS-RESET line of
the FAILSAFE screen with the or
cursor key.
•
Select the BFS
release
channel
with
the
or program key.
•Set the throttle stick to the desired BFS
release
point
and
press
the program
key. This designates CH3 (Throttle) as the
release
channel and
sets
the
stick
release
point simultaneously.
3) To release BFS by the CH9 switch, press the
program key.
• BFS can be released by the CH9 switch only
when the switch is moved to the upper
position. If the CH9 switch is in the lower
position, BFScannot be released.
• In the BFS release state, the characters 0%-
RESET are displayed on the B/FS-RESET
line of the FAILSAFE screen.
4) If Battery Fail Safe is not desired, press the
program key (when the cursor is on the
B/FS-RESET line).
The
BFS
function
will
then be disabled.
In the example below, (Throttle) was set to
Fail Safe and Battery Fail Safe.
ing the stick or lever of the channel being set
in the desired Failsafe position. Simultaneous-
ly, the data is also transmitted to the receiver
and is automatically re-transmitted at one
minute intervals.
[15]

ADJUSTMENTS ANDFLIGHT TECHNIQUES
ADJUSTABLE TRAVEL VOLUME
• The ATV function is used to adjust servo travel limits. Servo travel can be adjusted independently in each
direction from neutral. Adjustment from 30% to 110% of normal full travel (throw) is possible.
•
NOTE:
When
servo
travel
is
changed
by
ATV,
the limits of
trim
throw
and the Dual
Rate
ON
(Low
Rate)
limits are increased or reduced by the same percentage.
• ATV limits are displayed by a bar graph and numbers. The point at which the cursor moves from left to
right, as the stick or lever is moved, is the electrical neutral point of that channel.
Setting Method
1) Select the EDIT screen, then select the ATV
program screen by pressing the program
key.
2) Rate data (endpoint limits) for Channels 1 to
4 is displayed on the screen. To display and
adjust Channels 5 to 8, press the program
key. Rate data for Channels 5 to 8 will be
displayed.
3) Select the channel to be set with the and
cursor keys.
extent in the desired direction. The cursor will
automatically move to the left or right con-
firming the direction to be set.
5) Servo endpoint limits can be set by pressing
the and program keys while holding
the appropriate stick or lever in the same
direction.
Pressing
the program key
will
return the set limit to 100%.
6) When you are finished, press the key to
return to the EDIT screen.
4) Operate the control stick, lever, or switch of
the channel to be adjusted to its maximum
In the example shown, the CH1 (Aileron) right throw is reduced to 90%.
100%
RIGHT
NEUTRAL
LEFT
50%
100%
ATV Limit= 50%
TRIM Limit
D/R Limit = 70% of Full
Throw
Normal (Full) Throw = 100%
In the bar graph illustration below, the right
hand throw is reduced to 50% of normal, while
the left hand throw is set to 100%. Note that on
the right side. Dual Rate ON (Low Rate) and
Trim throw limits are also reduced to 50% of
normal.
D/R Limit= 70% ofATV
Limit
TRIM Limit
50%
[16]

ADJUSTABLE FUNCTION RATE
AFR is a servo endpoint limiting function, similar to ATV with one exception:
AFR limits only the Dual Rate OFF (High-Rate) servo travel. Trim throw/and Dual Rate
ON (Low Rate) limits are unaffected (unless AFR is reduced below the D/R ON limit).
SettingMethod
1) The setting method for AFR is the same as for ATV (See page 16).
2) Select the EDIT screen and press the AFR program key.
In
the bar graph illustration below, the right
hand throw is reduced to 70% of normal throw
by AFR. Note that the Dual Rate ON (Low
Rate) limit and Trim throw limits remain the
same
on
both
sides
(Compare
with the ATV
illustration on page 16).
RIGHT
NEUTRAL
LEFT
AFR Limit= 70%
D/R Limit = 50% of Full
Throw
TRIM Limit
TRIM Limit
D/R Limit = 50%
Normal (Full) Throw = 100%
NOTE: Trim Limits and D/R Limits same in both directions.
[17]

ADJUSTMENTSANDFLIGHT TECHNIQUES
DUAL RATE
Dual Rate functions allow the modeler to switch servo travel limits in flight, thus varying
the control sensitivity for different flight conditions or maneuvers.
• Dual Rate functions are available on CH1 (Aileron), CH2 (Elevator), and CH4 (Rudder/Tail Rotor).
• Dual Rate ON (Low Rate) limits can be adjusted from 30%to 100% offull throw.
•
If
servo
travel
is
reduced by ATV, the D/R ON throw will
be
30%
to
100% of the
limit
set
by
ATV
(in
D/R OFF). If AFR is used, the D/R ON limit is unaffected, and will be 30% to 110% of normal (full)
throw.
• Dual Rate ON limits can be adjusted independently in each direction from neutral.
•There
are
three D/R ON/OFF
Switches.
Control of the
three
D/R functions
can
be
assigned
to
these
switches in any combination the modeler desires, or D/R functions can be switched ON and OFF auto-
matically according to the position of the Throttle/Collective stick.
•The
ON/OFF directions
of
the D/R switches
can
be
reversed
using the PARAMETERS program
screen
(See page 46).
• In the AUTO D/R mode, the D/R functions can be turned ON and OFF according to the position
(adjustable) of the T/C stick.
Settinq Method
1) Select the EDIT screen, then select the DUAL
RATE screen with the programkey.
2) Select the channel to be set with the or
cursor key.
3) Move the cursor to the position with the
or cursor key and press the or
program key to activate or deactivate the
D/R function for that channel.
4)
When
the
key
is
pressed,
"ON"or
"OFF"
will be displayed in the "INH" position, de-
pending upon the position of the pertinent
D/R ON/OFF Switch.
5) Using the and
cursor keys, move the
,or programkey.
The D/R ON/OFF Switches are designated by
numbers as follows:
1 ... Aileron D/R
As designated on the
transmitter front.
2 ... Elevator D/R
3... Rudder D/R
Each switch may be used to control one, two, or
all three D/R functions as desired.
7) D/R may also be switched ON and OFF in
conjunction with other functions (Idle-up,
etc.) using the COMBI SW function of the
PARAMETER program screen (See page 46).
cursor to the L/D or R/U position and set
the desired D/R ON throw with the or
program keys.Pressing the program
key will returen the set limit to 100%.
6) Select the desired ON/OFF Switch for each
D/R function by moving the cursor to the
"sw" position with the
keyandor
selecting Switch No.
1, 2, or 3 with the
[18]
Table of contents
Other FUTABA Remote Control manuals
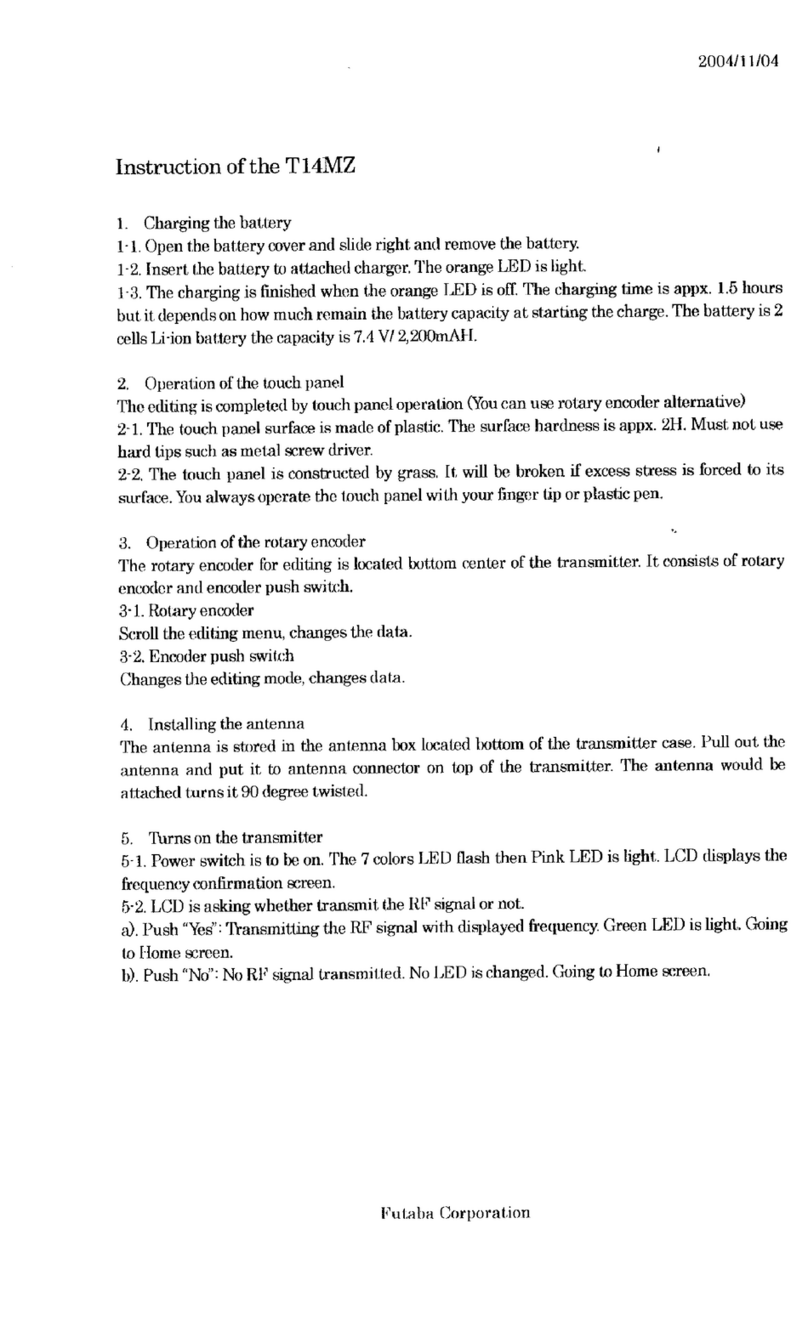
FUTABA
FUTABA T14MZ User manual

FUTABA
FUTABA T12Z Technical manual
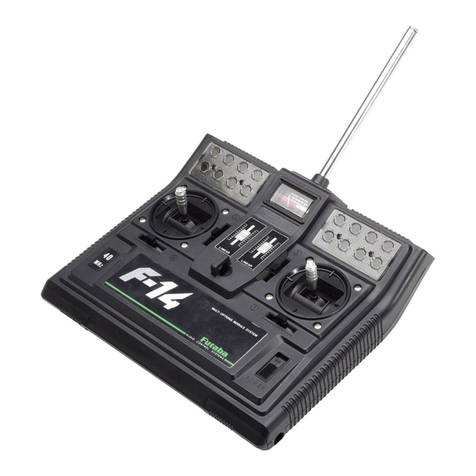
FUTABA
FUTABA F-14 Navy User manual
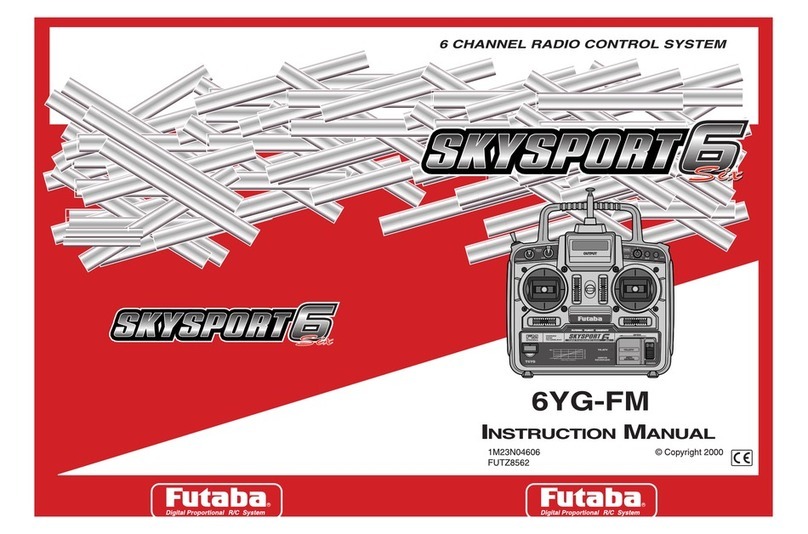
FUTABA
FUTABA 6YG-FM User manual
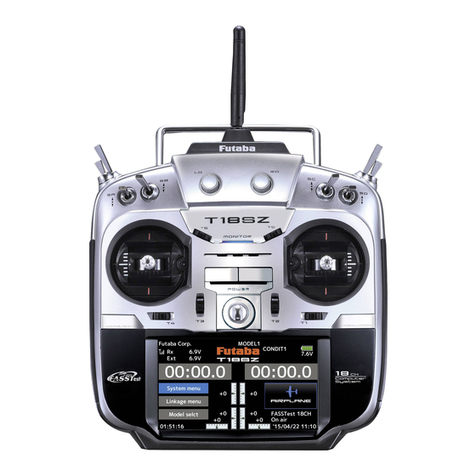
FUTABA
FUTABA T18SZ User manual
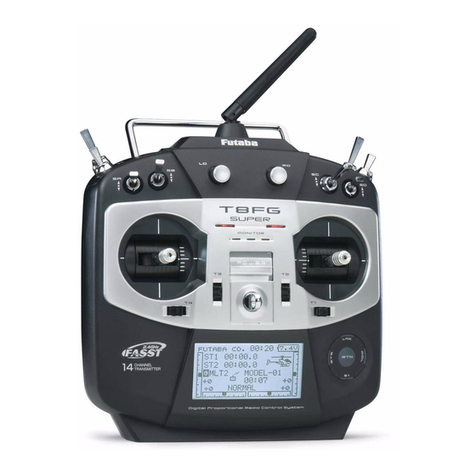
FUTABA
FUTABA T8FG User manual
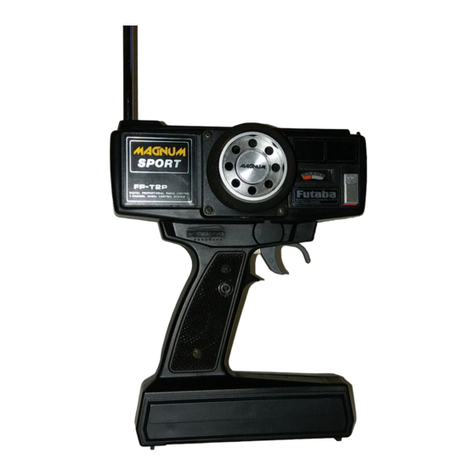
FUTABA
FUTABA Magnum Sport FP-S148 User manual
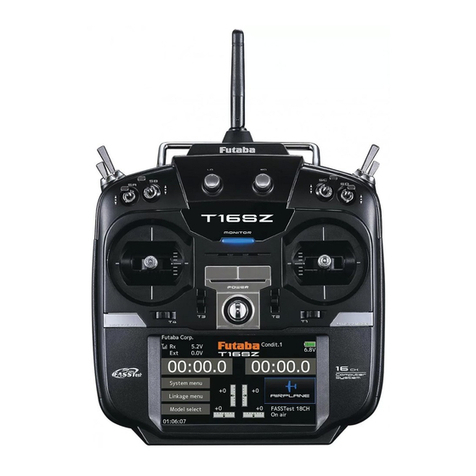
FUTABA
FUTABA FASSTest-2.4GHz T16SZ Series User manual

FUTABA
FUTABA FP-G132 User manual
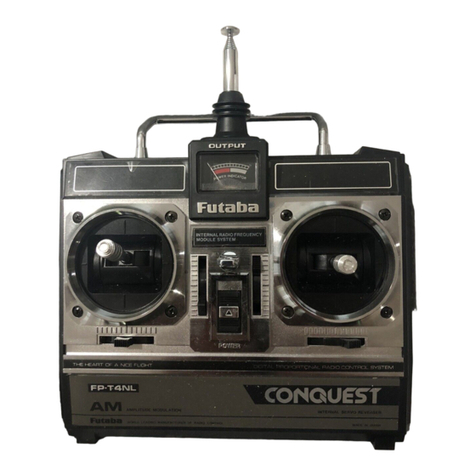
FUTABA
FUTABA CONQUEST User manual
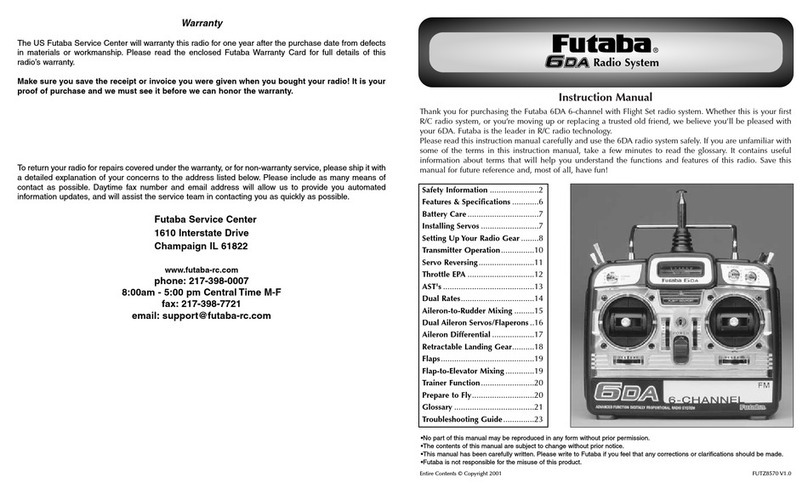
FUTABA
FUTABA 6DA User manual
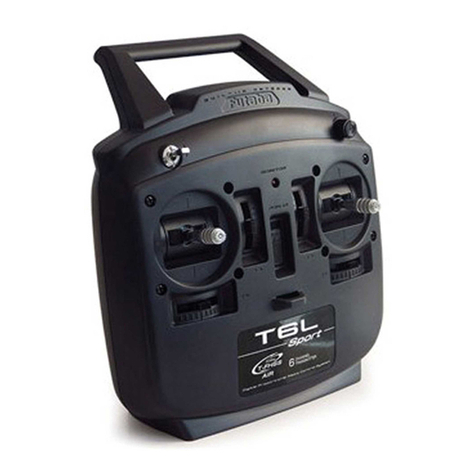
FUTABA
FUTABA T6L SPORT User manual
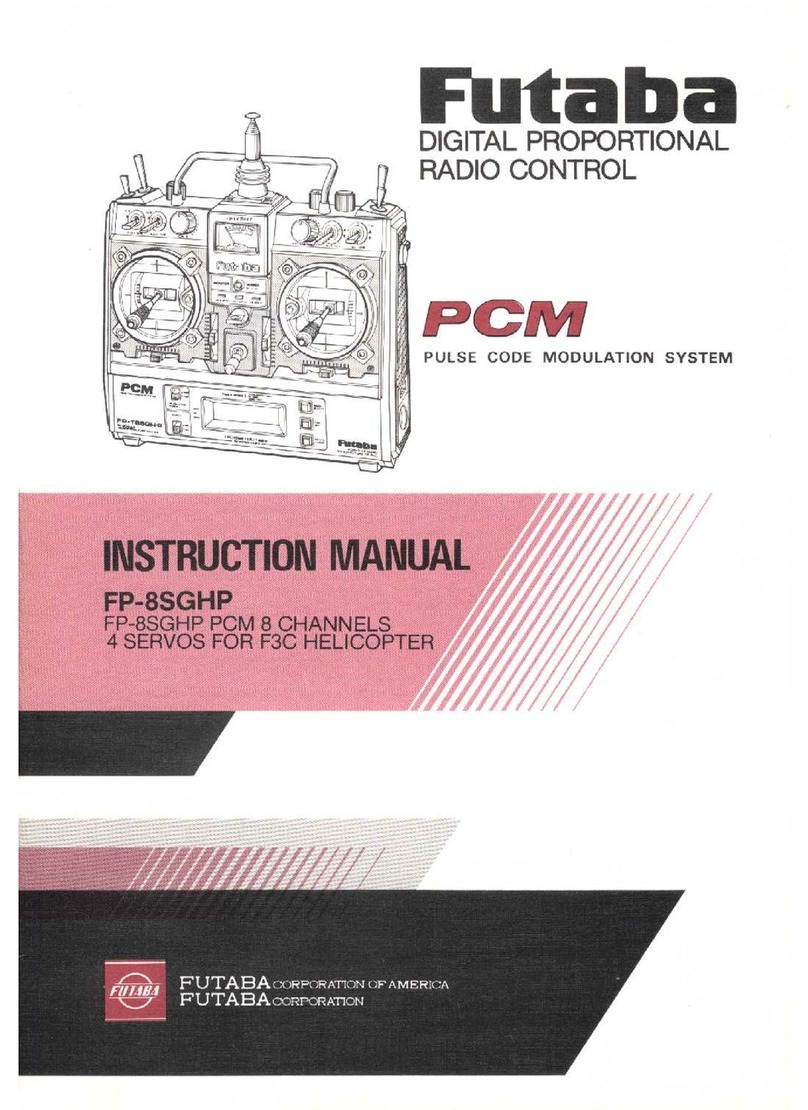
FUTABA
FUTABA FP-8GHP User manual
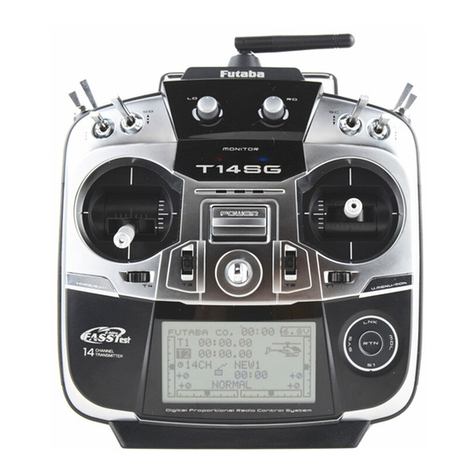
FUTABA
FUTABA T14SG Technical manual
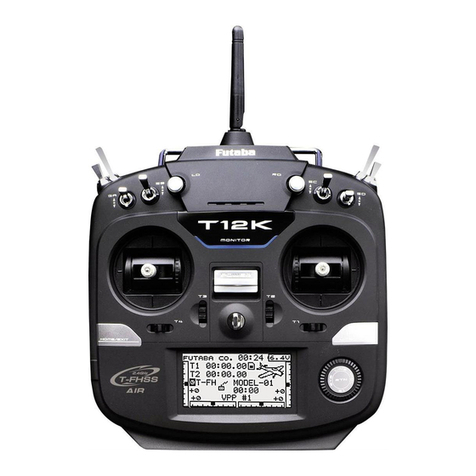
FUTABA
FUTABA 12K User manual

FUTABA
FUTABA T32MZ User manual

FUTABA
FUTABA R334SBS Technical manual

FUTABA
FUTABA Attack FP-R2GS User manual
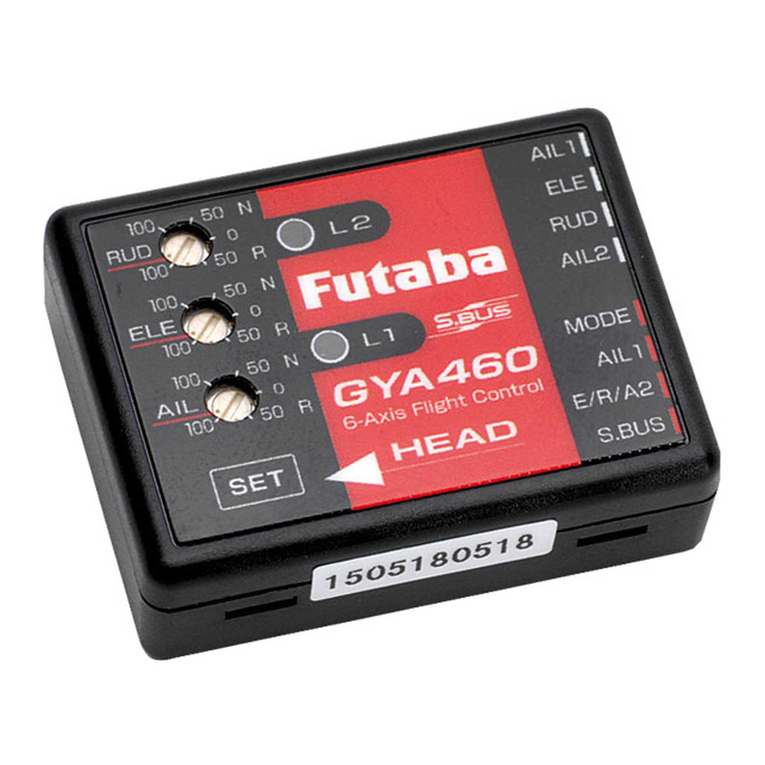
FUTABA
FUTABA GYA460 User manual
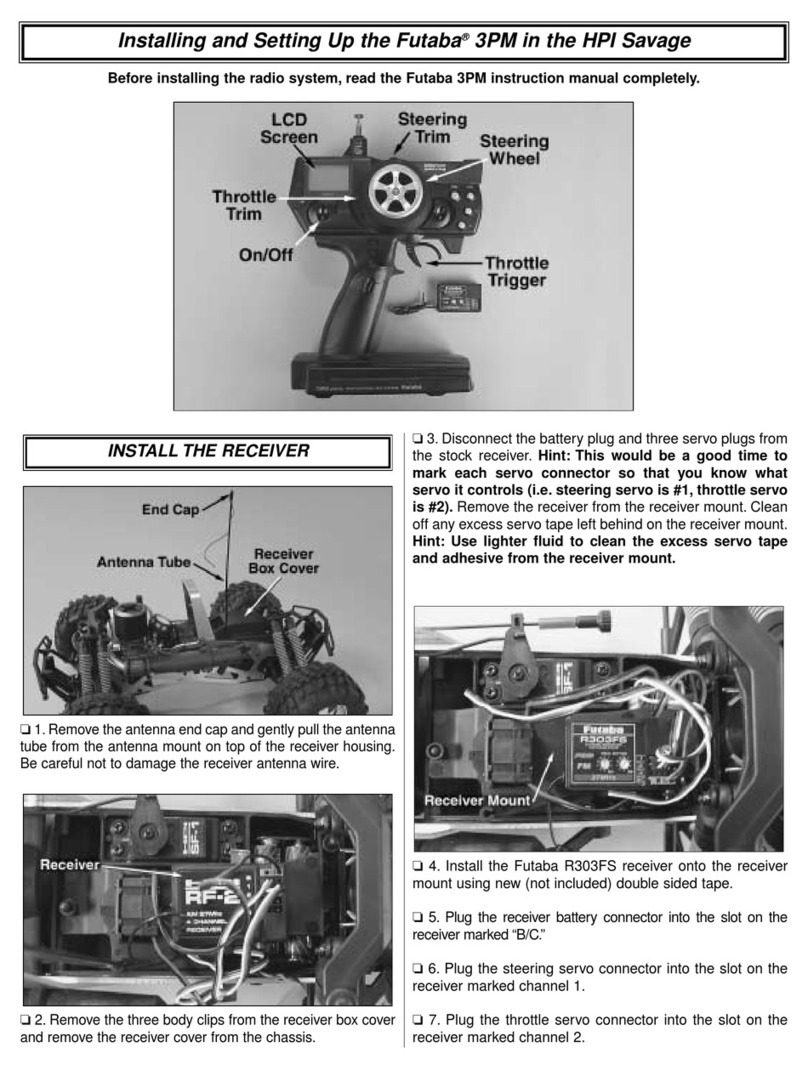
FUTABA
FUTABA 3PM Instruction Manual