GE PACSystems* RX3i User manual

GE
Intelligent Platforms
Programmable Control Products
PACSystems* RX3i
Power Sync and Measurement
System
User’s Manual, GFK-2749
February 2013

GFL-002
Warnings, Cautions and Notes
as Used in this Publication
Warning
Warning notices are used in this publication to emphasize that hazardous voltages,
currents, temperatures, or other conditions that could cause personal injury exist in this
equipment or may be associated with its use.
In situations where inattention could cause either personal injury or damage to equipment,
a Warning notice is used.
Caution
Caution notices are used where equipment might be damaged if care is not taken.
Note: Notes merely call attention to information that is especially significant to
understanding and operating the equipment.
This document is based on information available at the time of its publication. While efforts
have been made to be accurate, the information contained herein does not purport to cover all
details or variations in hardware or software, nor to provide for every possible contingency in
connection with installation, operation, or maintenance. Features may be described herein
which are not present in all hardware and software systems. GE Intelligent Platforms assumes
no obligation of notice to holders of this document with respect to changes subsequently made.
GE Intelligent Platforms makes no representation or warranty, expressed, implied, or statutory
with respect to, and assumes no responsibility for the accuracy, completeness, sufficiency, or
usefulness of the information contained herein. No warranties of merchantability or fitness for
purpose shall apply.
* indicates a trademark of GE Intelligent Platforms, Inc. and/or its affiliates. All other
trademarks are the property of their respective owners.
©Copyright 2013 GE Intelligent Platforms, Inc.
All Rights Reserved

Contact Information
iii PACSystems* RX3iPower Sync and Measurement System –February 2013 GFK-2749
If you purchased this product through an Authorized Channel Partner, please contact the seller
directly.
General Contact Information
Online technical support and
GlobalCare
http://support.ge-ip.com
Additional information
http://www.ge-ip.com/
Solution Provider
Technical Support
If you have technical problems that cannot be resolved with the information in this guide, please
contact us by telephone or email, or on the web at http://support.ge-ip.com
Americas
Online Technical Support
http://support.ge-ip.com
Phone
1-800-433-2682
International Americas Direct Dial
1-780-420-2010 (if toll free 800 option is unavailable)
Technical Support Email
Customer Care Email
Primary language of support
English
Europe, the Middle East, and Africa
Online Technical Support
http://support.ge-ip.com
Phone
+800-1-433-2682
EMEA Direct Dial
+420-23-901-5850 (if toll free 800 option is unavailable or
dialing from a mobile telephone)
Technical Support Email
Customer Care Email
Primary languages of support
English, French, German, Italian, Czech, Spanish
Asia Pacific
Online Technical Support
http://support.ge-ip.com
Phone
+86-400-820-8208
+86-21-3217-4826 (India, Indonesia, and Pakistan)
Technical Support Email
Customer Care Email


Contents
GFK-2749 v
PSM Module Description and Specifications .....................................................................1-1
PSM Module ..................................................................................................................... 1-2
Terminal Assembly ........................................................................................................... 1-3
Connectors........................................................................................................................ 1-3
User-Supplied Equipment.............................................................................................................. 1-4
PSM Part Numbers........................................................................................................................ 1-4
Specifications................................................................................................................................. 1-5
System Operation.......................................................................................................................... 1-7
Autonomous Operation..................................................................................................... 1-7
Frequency Measurement.................................................................................................. 1-8
ANSI Functions Supported............................................................................................................ 1-9
ANSI Functions for GRID 1 (Public Grid/Load) Protection............................................... 1-9
ANSI Functions for GRID 2 (Generator/Generator Grid) Protection .............................. 1-11
Installation.......................................................................................................................2-1
General Warnings/Cautions........................................................................................................... 2-2
Enclosures..................................................................................................................................... 2-3
Installing the PSM Module............................................................................................................. 2-3
Installing the Terminal Assembly................................................................................................... 2-3
Connector and Cabling Information............................................................................................... 2-4
Basic PSM System Connections...................................................................................... 2-4
Overview of PSM System Connection to Public Grid and Generator............................... 2-5
Power System Connections.............................................................................................. 2-6
Relay Connector for Sync Contacts.................................................................................. 2-9
Wiring........................................................................................................................................... 2-10
General Wiring Notes ..................................................................................................... 2-11
Terminal Assembly Frame Ground Connection ............................................................. 2-11
Wiring Diagrams ............................................................................................................. 2-12
Scaling for PT and CT Ratios...................................................................................................... 2-19
Configuration and Data Transfer .................................................................................3-1
Configuration Parameters.............................................................................................................. 3-2
PSM001 Settings Parameters .......................................................................................... 3-2
Grid1 and Grid2 Parameters............................................................................................. 3-3
ANSI Protection Parameters............................................................................................. 3-6
Power Consumption.......................................................................................................... 3-9
Terminals.......................................................................................................................... 3-9
Data Transfer............................................................................................................................... 3-10
PSM Status Flags........................................................................................................... 3-10
PSM Signal Input Data ................................................................................................... 3-14
Data Sent from the Host Controller to the PSM Module................................................. 3-19

Contents
vi PACSystems* RX3i Power Sync and Measurement System–February 2013 GFK-2749
Mode Control Bits Sent to PSM module......................................................................... 3-19
Parameters sent to PSM Module.................................................................................... 3-22
Example Configurations............................................................................................................... 3-25
Configuration for 120/240 VAC Single Phase System................................................... 3-26
Configuration for 600VAC Single Phase System ........................................................... 3-29
Configuration for 120/208 WYE Three-Phase Four-Wire System.................................. 3-32
Configuration for 120/208 3-Wire Delta system with Two PTs (Two Wattmeter Method),
B-Common...................................................................................................................... 3-35
Configuration for 120/208 3-Wire Delta system with Two PTs (Two Wattmeter Method),
C-Common...................................................................................................................... 3-38
Configuration for 120/208 4-Wire WYE Synchro/Power Control Connection................ 3-41
Configuration for 480V 4-Wire WYE Synchro/Power Control Connection ..................... 3-44
Diagnostics....................................................................................................................4-1
PSM Module LED Indicators.......................................................................................................... 4-1
PSM Module Health Status............................................................................................................ 4-1
Point Faults.................................................................................................................................... 4-2
Fault and No-Fault Contacts.......................................................................................................... 4-3
Product Certifications and Installation Guidelines for Conformance .....................A-1
Agency Approvals ...............................................................................................................................A-1
Environmental Specifications.........................................................................................................A-2
Government Regulations...............................................................................................................A-3

GFK-2749 1-1
PSM Module Description and Specifications
The Power Sync and Measurement (PSM) system monitors two independent three-phase
power grids. It incorporates advanced digital signal processor (DSP) technology to
continuously process three voltage inputs and four current inputs for each grid.
Measurements include RMS voltages, RMS currents, RMS power, frequency, and phase
relationship between the phase voltages of both grids.
The PSM module performs calculations on each captured waveform, with the DSP
processing the data in less than two-thirds of a power line cycle. The PSM module can be
used with wye or delta type three-phase power systems or with single-phase power
systems.
The PSM system can be used for applications such as:
Electrical power consumption monitoring and reporting
Fault monitoring
Generator control features for generator to power grid synchronization
Demand penalty cost reduction/load shedding
The PSM system consists of:
PSM module –A standard IC694 module that mounts in an RX3i main rack. The
PSM module provides the DSP capability.
Terminal Assembly –A panel-mounted unit that provides the interface between the
PSM module and the input transformers.
Interface cables –Provide the GRID 1 and GRID 2 connections between the PSM
module and the Terminal Assembly.
PSM System Features
Uses standard, user-supplied current transformers (CTs) and potential transformers
(PTs) as its input devices.
Accurately measures RMS voltage and current, power, power factor, frequency,
energy, and total, three-phase, 15-minute power demand.
Provides two isolated relays that close when the voltage phase relationships
between the two monitored grids are within the specified ANSI 25 limits provided by
the RX3i host controller. These contacts can be used for general-purpose, lamp duty
or pilot duty loads. Voltage and current ratings for these load types are provided on
page 1-5.
Provides a cable monitoring function that indicates when the cables linking the PSM
module and Terminal Assembly are correctly installed.
Can be easily calibrated using the Proficy* Machine Edition (PME) software to enter
calibration constants for the PSM module and Terminal Assembly.
The PSM001 module supports hot swap (removal and replacement in an RX3i rack
that is under power).
1
Chapter

1-2 PACSystems* RX3i Power Sync and Measurement System –February 2013 GFK-2749
1
PSM Module
In addition to configuring the PSM module upon project
download from PME, the RX3i CPU can control the PSM module
by updating configuration data from the RX3i in the form of %AQ
data words and %Q mode control bits during each sweep.
The PSM module provides calculated data to the CPU in the
form of %AI data words and %I status bits each sweep. The
information sent by the PSM module includes power system
measurements and discrete fault status.
Connectors
The PSM module provides two Mini-D 20-pin connectors that
accept the GRID 1 and GRID 2 voltage and current signals from
the Terminal Assembly.
Indicators
Four LEDs provide status indications for the PSM system.
RUN
Green
The module is operating correctly and
communicating with the RX3i.
Red
The module is operating without
backplane communication.
Off
The module is not operating.
FLT
Green,
blinking
During the period when GREEN is ON,
Grid 2 can be connected to Grid 1.
Green,
steady
Grid 1 and Grid 2 can be connected and
there are no faults.
Red
The module has detected a fault
condition.
Off
The module has not detected a fault and
the grids are not synchronized.
GRID 1
Green
Indicates a voltage signal has been
detected on Grid 1.
Red
A frequency out-of-range condition has
been detected on Grid 1.
Off
No zero crossing signal of Grid 1 has
been detected during the last 250 ms
time period.
GRID 2
Green
Indicates a voltage signal has been
detected on Grid 2
Red
A frequency out-of-range condition has
been detected on Grid 2.
Off
No zero crossing signal of Grid 2 has
been detected during the last 250 ms
time period.
RUN
PSM001
GRID 2
GRID 1
FLT
GRID 1
2
CAL
CAL
Module Offset: -2
Module Gain: 4000H
Module Offset: -2
Module Gain: 4000H

GFK-2749 Chapter 1PSM Module Description and Specifications 1-3
1
Terminal Assembly
The Terminal Assembly accepts three voltage inputs and four current inputs for each of
two grids. The Terminal Assembly translates the 0–5 A current signals and the
45–690 VAC RMS voltage signals to low voltage signals for use by the PSM module.
Voltage inputs are connected through external, user-supplied potential transformers (PT).
External, appropriately-sized current transformers (CT) are used to translate grid or load
currents down to the 0–5 A range required by the Terminal Assembly.
Connectors The Terminal Assembly provides two terminal blocks, each with 12 screw terminals, for
the voltage and current inputs from the grids. The terminals accept up to 10 AWG wire
commonly used in power utility applications.
The Terminal Assembly provides two pairs of Mini-D 20-pin connectors for connection to
the PSM module using the interface cables. The 45–120 VAC or 120–690 VAC range is
selected by connecting the interface cables to the corresponding pair of Mini-D
connectors.
When the cables are connected to the correct grid and matching voltage ranges, the PSM
module provides an indication that the cables are correctly attached to the unit.
A four-pin pluggable connector provides two isolated solid state relay contacts that close
when the correct voltage, phase, and relative frequency differences match the configured
criteria for synchronization of the GRID1 and GRID2 signals.
Note: The Terminal Assembly is not equipped with CT shorting-bars. These must be
provided separately by the user.
COM2
VA2
VB2
VC2
IA2+
IA2-
IB2+
IB2-
IC2+
IC2-
IN2+
IN2-
COM1
VA1
VB1
VC1
IA1+
IA1-
IB1+
IB1-
IC1+
IC1-
IN1+
IN1-
RELAY
1A 1B 2A 2B
GRID 1
120VAC
600VAC GRID 2
120VAC
600VAC
120V GRID 2
GRID 2
Terminal Block
Plastic finger guard
600V GRID 1
600V GRID 2
120V GRID 1
Grounding stud
GRID 1
Terminal Block
Grounding stud

1-4 PACSystems* RX3i Power Sync and Measurement System –February 2013 GFK-2749
1
User-Supplied Equipment
The user must supply the following components depending upon the application. This
equipment includes:
Current transformers, 5 Amps
Potential transformers
Fuses (1 Amp each) for each voltage lead connected to the Terminal Assembly.
A fuse (1 Amp) for the common or return line for the voltage lead on the
Terminal Assembly.
A CT shorting block for each current transformer (CT) connection used on the
Terminal Assembly when used with external CTs.
PSM Part Numbers
IC694PSK001
PSM System. Includes a PSM module, a Terminal Assembly and two interface
cables
IC694PSM001
Replacement PSM module
IC694ACC200
Replacement Terminal Assembly
IC694CBL200
One replacement 2m (6.56 ft.) interface cable
IC694ACC201
PSM replacement parts:
two finger guards
four thumb screws
one relay connector
two grounding lug nuts

GFK-2749 Chapter 1PSM Module Description and Specifications 1-5
1
Specifications
PSM Module Power Requirements
Backplane Power Consumption
400 mA max. at 5 VDC
Total Power Dissipation
2.0 W max.
Isolation from Backplane
1500 VDC
Host Controller Compatibility
RX3i CPUs
For specific versions supported, refer to “Functional
Compatibility” in the Important Product Information
document, GFK-2748.
Maximum number of PSM modules per
RX3i system
No restrictions, as long as the power supply has
sufficient capacity
Sync Relay contacts
Two isolated relay outputs
General purpose:
125 VAC / 125 VDC maximum at 1 amp
Lamp duty:
125 VAC / 125 VDC maximum at 1 amp
Pilot duty:
125 VAC / 125 VDC maximum at 0.35 amp
Switching speeds
Turn-on time
Turn-off time
20ms
5ms
Measurement Specifications
Three voltage inputs per grid
All voltage data is scaled in 0.1 VAC units.
Impedance
>1 MΩ
Range
Low range
High range
45–150 VAC RMS (120VAC nominal)
120–690 VAC RMS (600VAC CAT IV; 690 VAC CAT III)
Frequency
40–70 Hz
Four current inputs per grid
All current data is scaled in 0.001 Amp units.
Impedance
<5 milliohms
Range
0–5 A RMS (5 A nominal)
Frequency
40–70 Hz
Phase difference between grids:
±180O
Measurement Accuracy 1
Voltage
0.2% of Full Scale (see page 3-20)
Current
0.2% of Full Scale (see page 3-20)
kW, kVAR, kVA
0.4%
kWH, kVARH, kVAH
0.4%
Power factor
1%
Frequency
0.01 Hz
Phase angle
0.1O
1
In the presence of severe RF interference (IEC 61000-4-6, 10 volts), accuracy could be degraded
by ±2% of full scale.

1-6 PACSystems* RX3i Power Sync and Measurement System –February 2013 GFK-2749
1
Terminal Assembly Input Terminal Ratings
Current
15 Amps continuous maximum
Voltage
690 VAC RMS
Sync Relay contacts
150 VAC/VDC at 1 Amp Resistive, maximum
Note: Actual contact ratings depend on load type.
See “Sync Relay contacts” on page 1-5.
RX3i CPU Memory Requirement for Automatic Data Exchange
%I
80 bits
%Q
32 bits
%AI
64 words
%AQ
2 words
Data Exchange Time Between RX3i CPU and PSM
A complete data exchange between the PSM and RX3i occurs during each controller scan.
Minimum scan time is 3.5ms per PSM module in the backplane. Minimum data update rate is one
power line period. See “System Operation” on page 1-7 and “PSM Status Flags” in chapter 3.
ANSI Protective Functions
ANSI 25 –Generator and Public Grid Synchronization
ANSI 27 –Under-voltage Protection
ANSI 32 –Reverse Power Protection
ANSI 47 –Voltage Phase Sequence Protection
ANSI 50 –Instantaneous Over-current Protection
ANSI 59 –Over-voltage Protection
ANSI 60 –Voltage (Current) Imbalance Protection
ANSI 81U –Under-frequency Protection
ANSI 81O –Over-frequency Protection
Power Measurement Configurations
Four-wire three phase wye systems: 3 PTs and 3 CTs plus Neutral CT (optional)
Three-wire three phase delta systems: 2 PTs and 2 CTs
Three independent single phase systems: 1 PT and 1 CT for each phase
Three-wire single phase systems: 120/240 (2 PTs and 2 CTs)
Operating Environment
Enclosure mounting
Required. PSM module and Terminal Assembly must be
installed in a NEMA/UL Type 1 enclosure or an IP20
rating providing at least a pollution
degree 2 environment.
When this system is installed in an area designated as
Class 1 Zone 2 in Europe, compliance with the ATEX
Directive requires an enclosure with a minimum rating
of IP54.

GFK-2749 Chapter 1PSM Module Description and Specifications 1-7
1
System Operation
The PSM digitizes the voltage and current input waveforms from Grid 1 and Grid 2, storing
the results into internal memory buffers. Data is updated every power line cycle.
Therefore, the data is updated every 20ms on a 50Hz power grid, or every 16.67ms on a
60Hz power grid.
While background processes analyze a set of waveforms stored in one memory buffer,
the next set of waveforms is captured and stored in another buffer. In this way,
calculations are performed on each waveform with the DSP processing the data in about
two-thirds of a power line cycle.
Autonomous Operation
The PSM is a semi-autonomous module running on the RX3i backplane. If the PLC goes
to Stop Mode, or the CPU is lost due to over temperature or a watchdog timeout, the PSM
continues to operate with the last directive received from the CPU. If the CPU had
requested the synchronization of Grid 1 and Grid 2, when all sync parameters are met, the
PSM will assert RelayCloseOK and close its relay output contacts, even when the PLC is
in Stop Mode. Care must be taken to leave the Sync request in a known state when
transitioning to stop mode.
When Grid 1 and Grid 2 are synchronized, the PSM cannot be reset or cleared, and it
will not accept a new hardware configuration from the CPU. Once synchronized, the PSM
can only be cleared in preparation for receiving a new configuration by first commanding
the PSM to release the grid synchronization (simultaneously set %Q offset 16 to 1, and
clear %Q offset 32 to 0), or by removing power from the PSM module. Mission Critical
applications must have a redundant PSM system to take over the grid synchronization
from the Primary PSM if the primary controller can no longer perform its function.

1-8 PACSystems* RX3i Power Sync and Measurement System –February 2013 GFK-2749
1
Frequency Measurement
Healthy three-phase power systems produce three almost identical sinusoidal voltage
waveforms that swing from positive to negative voltage at a frequency of either 50 or 60
times per second (50–60Hz).
The PSM determines the frequency of the power line by looking for the zero crossings,
which are places where the voltage crosses zero volts going from positive to negative or
from negative to positive. Only phase A voltages are used for the zero-crossing detection,
so phase A must be always present on one or the other grid.
Voltage
Zero-Crossings
Time
Frequency Measurement Notes
PSM preferentially chooses Grid 1 VA zero crossing as the reference for signal
sampling.
In the absence of Grid 1 VA, PSM uses Grid 2 VA zero crossing.
In the absence of either VA signal, grid frequencies will be reported as 0Hz, and the
remaining inputs will be sampled at a rate of 128 samples per 25ms. New data will
be updated at 25ms intervals. This may create sporadic looking individual readings,
but a 10 cycle average will be fairly steady and accurate.
When the difference in frequency between Grid 1 and Grid 2 is large, the Grid 2
RMS readings will vary from cycle to cycle, however a 10 cycle average will be fairly
steady and accurate.

GFK-2749 Chapter 1PSM Module Description and Specifications 1-9
1
ANSI Functions Supported
The Grid 1 and Grid 2 functions are similar, but with differences in implementation. Grid 1
is assumed to be the most stable power source, such a utility. Grid 2 is assumed to be a
less stable power source, such as a back-up generator. Either or both grids can be
connected for load monitoring, such as motors, lighting, HVAC or server room power.
ANSI Functions for GRID 1 (Public Grid/Load) Protection
ANSI 27 –Under-voltage Protection
Under-voltage Protection monitors voltages to protect motors against voltage sags. The
PSM monitors the phase-to-phase voltage in a delta power system, or phase-to-neutral
voltage in a wye power system, as a percentage of the Nominal Voltage parameter. An
alarm will be triggered if any voltage falls below the specified UNDER_VOLT_THR value
for a time period longer than UNDER_VOLT_DELAY. The alarm is cleared when the grid
voltage rises above the UNDER_VOLT_THR value for a time period longer than
UNDER_VOLT_DELAY. The UNDER_VOLT_THR is a percentage of the nominal voltage.
ANSI 32 –Reverse Power Protection
Reverse Power Protection provides protection from excessive reverse active power
produced by motors running as generators (supplying power). An alarm will be triggered if
a circuit’s active power exceeds the REV_PWR_THR for a time period longer than
REV_PWR_DELAY. The Alarm will be cleared when the active power exceeds the
REV_PWR_THR for a time period longer than REV_PWR_DELAY. The REV_PWR_THR
is a percentage of the nominal power, which in a 3-phase system, is three times the
nominal voltage multiplied by the nominal current.
ANSI 47 –Voltage Phase Sequence Protection
This function monitors the sequence of the phase A, B and C voltages. Detection of a
wrong sequence (A, C, B for example) triggers an alarm.
An entire cycle of waveforms is required to make this Phase Sequence determination.
There is no user settable delay parameter, so the moment a Phase Sequence error is
detected, the alarm is set. In both systems (Delta and WYE), the signal at the VA terminal
is expected to lead the signal at the VB terminal by 120 degrees. The signal at the VB
terminal is expected to lead the signal on the VC terminal by 120 degrees. Unused
“reconstructed” signal inputs are ignored for Phase Sequence detection. The current
signals are not monitored for Phase Sequence.
ANSI 50 –Instantaneous Over-current Protection
This function provides three-phase protection against overloads and phase-to-phase
short-circuits. An alarm will be triggered if any phase current exceeds the specified
OVER_CURR_ THR value for a time period longer than OVER_CURR_DELAY. This
alarm is cleared when the current value stays below the OVER_CURR_THR value for a
time period longer than OVER_CURR_DELAY. The OVER_CURR_THR is a percentage
of the nominal current.

1-10 PACSystems* RX3i Power Sync and Measurement System –February 2013 GFK-2749
1
ANSI 59 –Over-voltage Protection
This function provides detection of abnormally high phase voltage. It works with
phase-to-phase voltage in delta power systems, or phase-to-neutral voltage in wye power
systems. Each voltage is monitored separately. An alarm will be triggered if any voltage
exceeds the specified OVER_VOLT_THR value, as a percentage of the Nominal Voltage
parameter, for a time period longer than OVER_VOLT_DELAY. This alarm is cleared
when the voltage drops below the OVER_VOLT_THR value for a time period longer than
the OVER_VOLT_DELAY. The OVER_VOLT_THR is a percentage of the nominal
voltage.
ANSI 60 –Voltage (Current) Imbalance Protection
An alarm will be triggered if any phase voltage or current reading varies from the average
of all three phases by more than VI_IMBALANCE_THR for a time period longer than
VI_IMBALANCE_DELAY. The alarm is cleared when the imbalance condition is corrected
for a time period longer than VI_IMBALANCE_DELAY. IV_IMBALANCE_THR is a
percentage of the average of the three phase voltages (for voltage imbalance) or the three
phase currents (for current imbalance) on a given grid. It works with phase-to-phase
voltage in Delta power systems, or phase-to-neutral voltage in WYE Power systems. No
comparison is performed between the two grids. Neutral current is not monitored for
imbalance.
ANSI 81U –Under-frequency Protection
Detection of abnormally low frequency compared to the nominal frequency, to monitor
power supply quality. An alarm will be triggered if a circuit’s frequency falls below the
nominal frequency minus the UNDER_FRQ_THR for a time period longer than
UNDER_FRQ_DELAY. The alarm is cleared when the frequency rises above the nominal
frequency minus UNDER_FRQ_THR for a time period longer than UNDER_FRQ_DELAY.
UNDER_FREQ_THR is an absolute frequency, in Hz, that is subtracted from the nominal
frequency to determine the lowest acceptable frequency for the grid.
ANSI 81O –Over-frequency Protection
Detection of abnormally high frequency compared to the nominal frequency, to monitor
power supply quality. The alarm will be triggered if a circuit’s frequency is above the
nominal frequency plus OVER_FRQ_THR for a time period longer than
OVER_FRQ_DELAY. The alarm will be cleared when a circuit’s frequency falls below the
nominal frequency plus OVER_FRQ_THR for a time period longer than
OVER_FRQ_DELAY. OVER_FREQ_THR is an absolute frequency, in Hz, that is added
to the nominal frequency to determine the highest acceptable frequency for the grid.

GFK-2749 Chapter 1PSM Module Description and Specifications 1-11
1
ANSI Functions for GRID 2 (Generator/Generator Grid) Protection
Warning
It is the responsibility of the user to verify that the system has
sufficient frequency stability to maintain the current phase trend
during the synchronization process. This requirement is especially
true for long breaker delays. Failure to maintain frequency stability
during synchronization may result in personal injury, equipment
damage, or both.
ANSI 25 –Generator & Public Grid Synchronization
The PSM module can synchronize two sources from either a static phase angle or a
rotating phase angle.
In static phase angle synchronization, the overall PLC control system holds the two grids
at the same amplitudes, frequencies and phase angles, and then requests that the PSM
module synchronize the grids. To select this mode, set the Breaker Delay parameter
to 0ms.
In rotating phase angle synchronization, the overall PLC control system holds the two
grids at the same amplitudes while keeping the frequencies at slightly different values so
the two grids gradually go in and out of phase. The PLC then requests that the PSM
module synchronize the grids whenever it is safe to do so. To select this mode, set the
Breaker Delay parameter to the non-zero value that corresponds to the time required for
the synchronization contacts to close. See “ANSI Protection Parameters” in chapter 3for
more details on setting the breaker delay.
For safe synchronizing (i.e. connecting the generator grid with the public grid), in addition
to having no faults in either the public or generator grids, the following three parameters
must be within their specified limits:
voltage matching (Delta Voltage between public grid and generator grid, all
measured phase voltages considered)
frequency difference (Delta Frequency between public grid and generator grid)
angle (Phase Shift between public grid and generator grid —using phase A
voltages)
Voltage Matching
For synchronization, the Grid 2 RMS voltage must be within ±DELTA_VOLT_THR of the
Grid 1 RMS voltage. DELTA_VOLT_THR is a percentage of the measured Grid 1 voltage.
There is no delay for setting or clearing this DeltaVoltOK status bit.
Frequency Difference
For synchronization, the Grid 2 frequency must be within ±DELTA_FREQ_THR of the
Grid 1 frequency. DELTA_FREQ_THR is an absolute frequency difference in Hz.

1-12 PACSystems* RX3i Power Sync and Measurement System –February 2013 GFK-2749
1
Phase Angle
For synchronization, the two grids must be connected when the phase angle difference
between the grids is in the range of ±PHASE_SHIFT_THR, and ideally at the point when
the two grids are exactly in phase. The phase shift threshold represents an angle window
in electrical degrees (usually ±10°) around the 0° value, where it is safe to connect the two
grids. The phase shift between the grids can be a rapidly changing value in a rotating
system.
Additionally, the breaker delay can be significant (hundreds of milliseconds). Therefore, in
rotating phase synchronization, the moment for commanding the sync relay to close must
shift forward to compensate for the time it takes for the contacts to close. For example, the
window of opportunity for commanding relay closure could happen between 25° and 15°,
in order for the contacts to close when the grids are truly in-phase. This angle offset is a
function of the frequency difference (and therefore the rate of change of the phase shift)
and the breaker delay.
Once the CloseRelayOK bit is set, it remains set until either the breaker delay + 24 power
cycles passes, or the phase shift enters and then leaves the ±Phase_Shift_Thr window.
This gives the contacts time to settle, and the two grids time to stabilize into
synchronization.
Angle Delay
Angle Delay is a value, in degrees, that accounts for both the rate of change of the phase
shift between the grids and the breaker delay. Angle Delay is the angle through which the
synchroscope needle travels between the moment the PSM sets the CloseRelayOK bit to
close the IC694ACC200 relay contacts, and when the physical contacts on the sync relay
actually close: Angle Delay = (360⁰x ΔF x Bdly)
Where:
ΔF = Grid 2 Frequency –Grid 1 Frequency
Bdly = breaker delay in seconds
The Breaker Delay PSM configuration parameter must include all the delays introduced
between the PSM module and the synchronizing contacts. For example, the
IC694ACC200 Terminal Assembly relay outputs have a turn on time of 20ms (see
“Specifications”on page 1-5), and a given contactor has a published closing time of 80ms.
The Breaker Delay parameter should be set to the sum of all delays, or 100ms in this
example. Ideally, the actual breaker delay time will be measured during installation
commissioning and used in the application to compensate for component variations.

GFK-2749 Chapter 1PSM Module Description and Specifications 1-13
1
Slow Rotating Phase Angles
In rotating phase angle synchronization, the PSM sets and clears the PhaseShiftOK
status bit based on the Angle Delay value. In slowly rotating phase angles where
Angle Delay ≤ (Phase_Shift_Thr - 2º)/2, noise-induced jitter in the zero-crossing detection
can make the phase angle difference from one power line cycle to the next appear to
change direction. For this reason, 2º of hysteresis is added to the trailing edge of the
PhaseShiftOK window:
PhaseShiftOK = On @ Angle Delay
PhaseShiftOK = Off @ –(Angle Delay+2º)
SYNCHROSCOPE
0º -Phase_Shift_Thr
FAST
SLOW
Slow Rotation: Angle Delay ≤ (Phase_Shift_Thr - 2º)/2
If the request to sync is on, or received by the PSM module at any time in the green
region (while PhaseShiftOK = on), the CloseRelayOK status bit will be set and the
IC694ACC200 output contacts will close.
Once CloseRelayOK is on and the IC694ACC200 output contacts are closed, they remain
on and closed, regardless of grid alarms, until after the breaker delay plus 24 power line
cycles pass, to allow the newly synchronized grids to settle. After the settling time, all
ANSI protections are reinstated and the PSM monitors the Delta Frequency, Delta Voltage
and Phase Shift status bits again.
In the absence of other alarms, the phase shift is allowed to drift within the phase shift
threshold (the yellow region) indefinitely as the PSM waits for the physical contacts to
synchronize the grids.

1-14 PACSystems* RX3i Power Sync and Measurement System –February 2013 GFK-2749
1
Example: Angle Delay ≤ (Phase_Shift_Thr - 2º)/2
Phase_Shift_Thr = 10º
Breaker Delay = 200ms
Grid 1 Frequency = 60.00Hz
Grid 2 Frequency = 60.01Hz
ΔF (slip frequency) = 0.01Hz
Angle Delay = (360º x 0.01Hz x 0.200sec) = 0.72º
PhaseShiftOK = On @ 0.72º {Angle Delay}
PhaseShiftOK = Off @ -2.72º {-(Angle Delay + 2º)}
If Sync is requested while PhaseShiftOK = On, then CloseRelayOK will be set to On
for the Angle Delay + 24 cycles. At ΔF = 0.01HZ and 60Hz, the PhaseShiftOK window
is 200ms (0.72⁰) + 400ms = 600ms.
Other manuals for PACSystems* RX3i
9
Table of contents
Other GE Controllers manuals
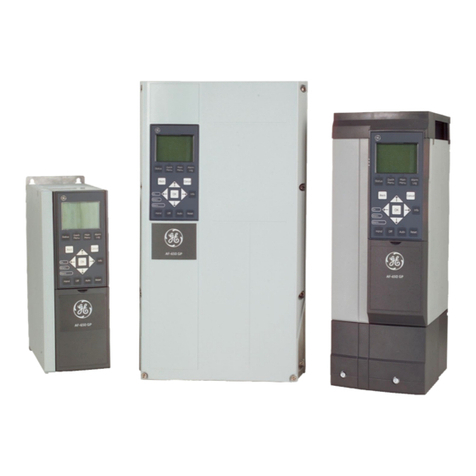
GE
GE AF-650 GP Series User manual
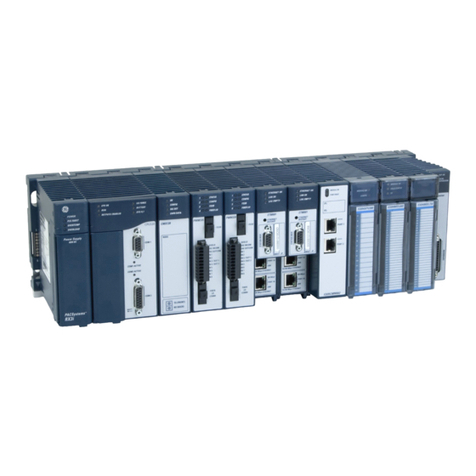
GE
GE PACSystems* RX3i User manual

GE
GE VersaMax User manual
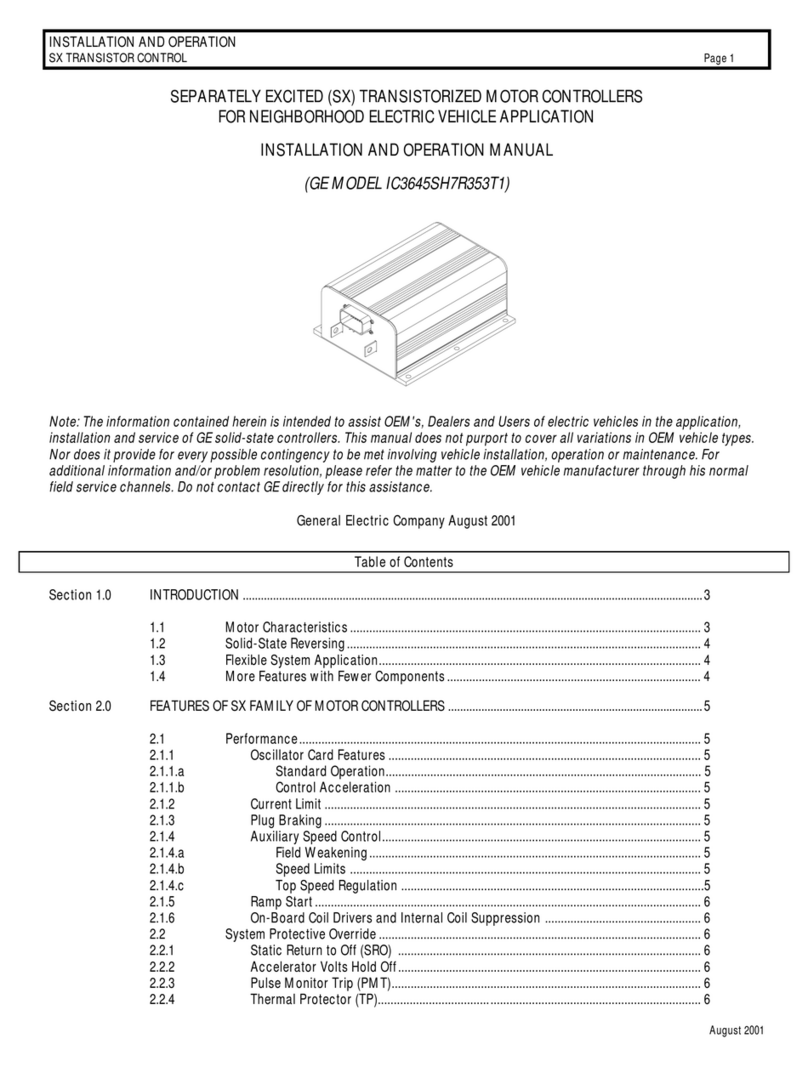
GE
GE IC3645SH7R353T1 User manual
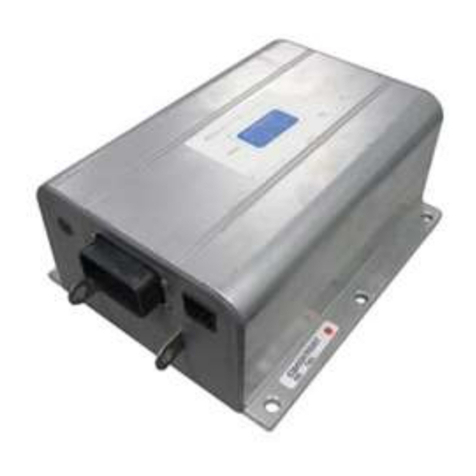
GE
GE IC3645SR4R333AS2 User manual
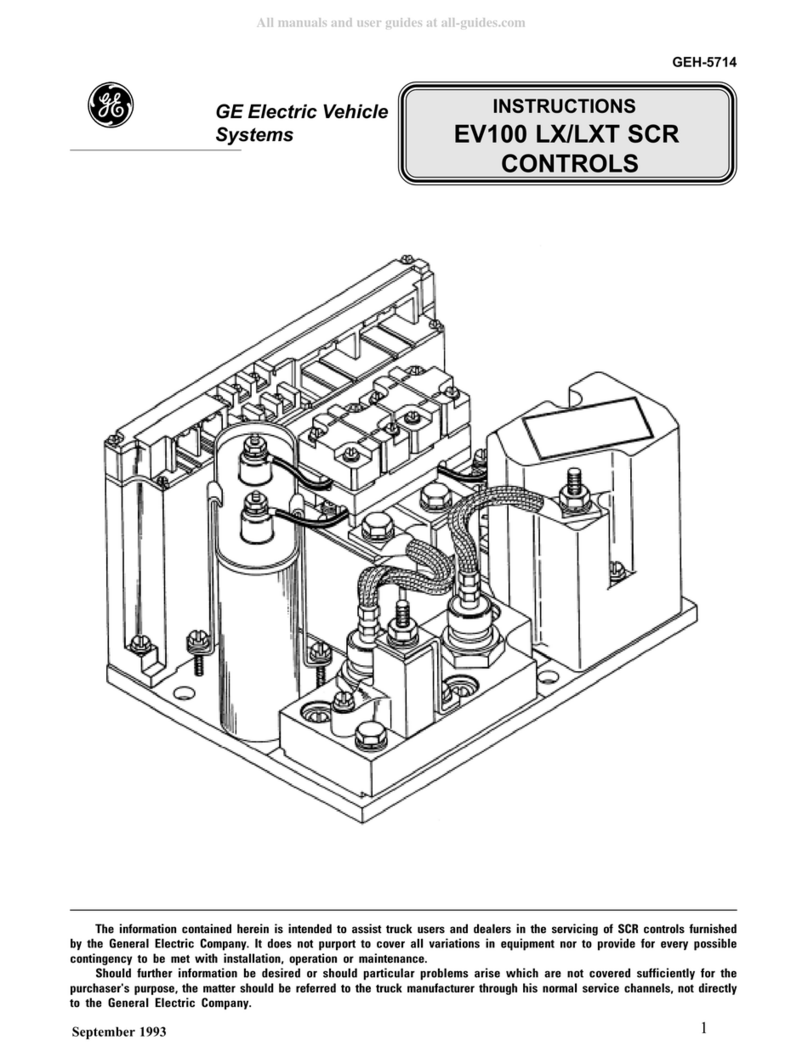
GE
GE EV100 LX User manual
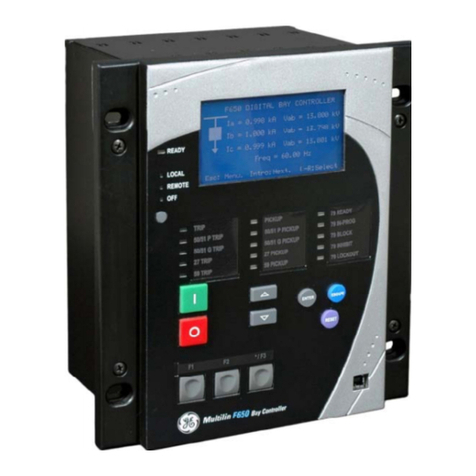
GE
GE Multilin F650 User manual
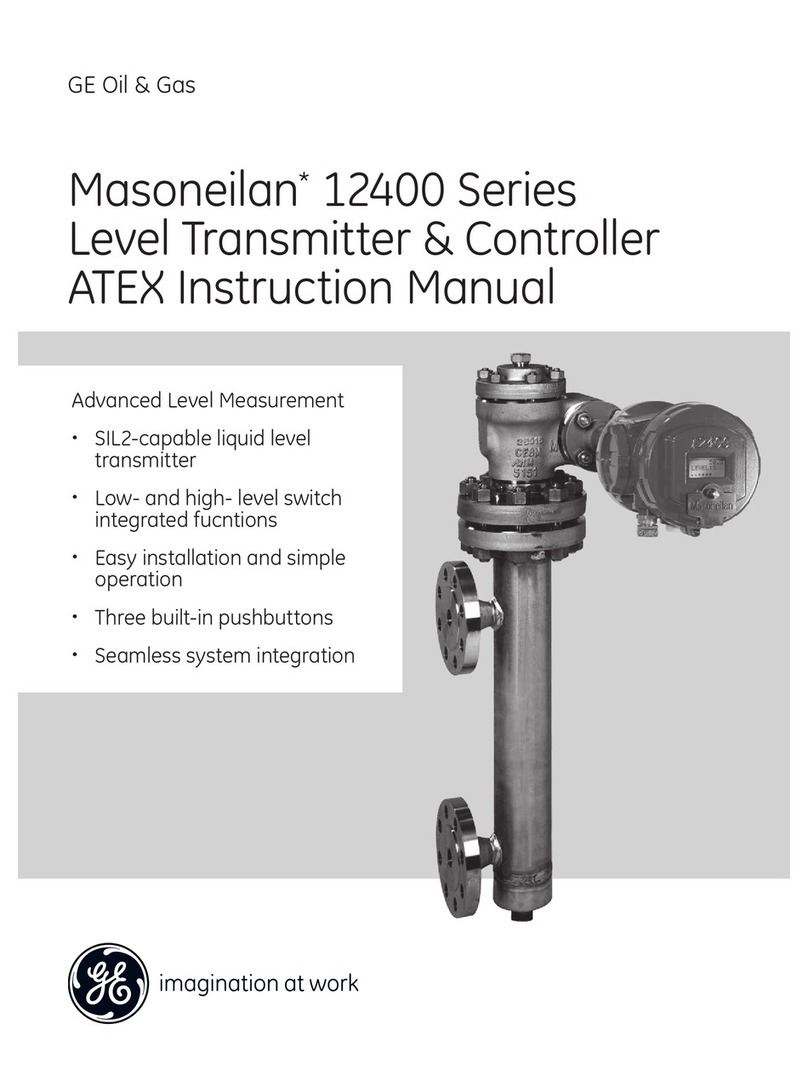
GE
GE Masoneilan 12400 Series User manual
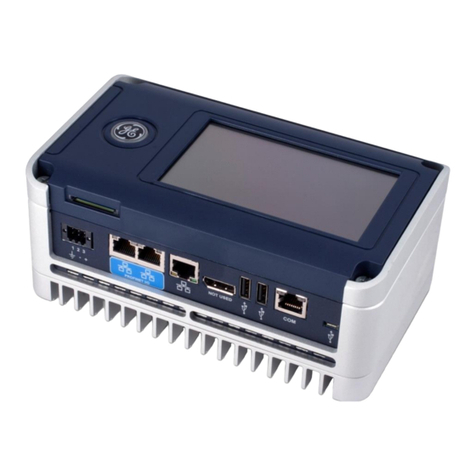
GE
GE PACSystems RXi User manual

GE
GE Multilin GEK-113000T User manual
Popular Controllers manuals by other brands

Oriental motor
Oriental motor LIMO EZS Series user manual
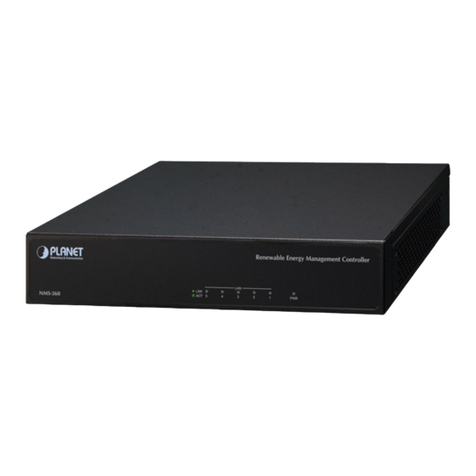
Planet
Planet NMS-360 Quick installation guide
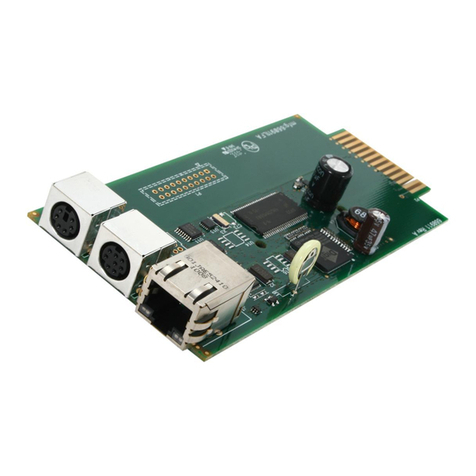
Tripp Lite
Tripp Lite SNMPWEBCARD installation instructions
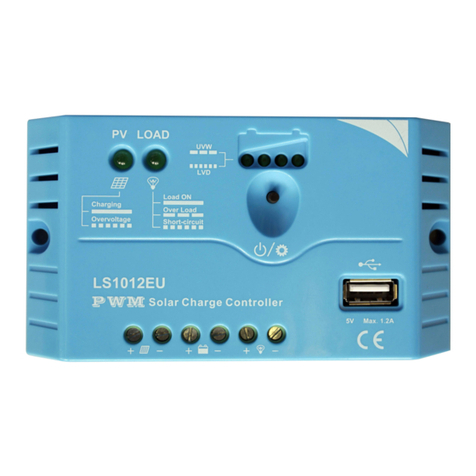
EP Solar
EP Solar LandStar LS-EU Series user manual
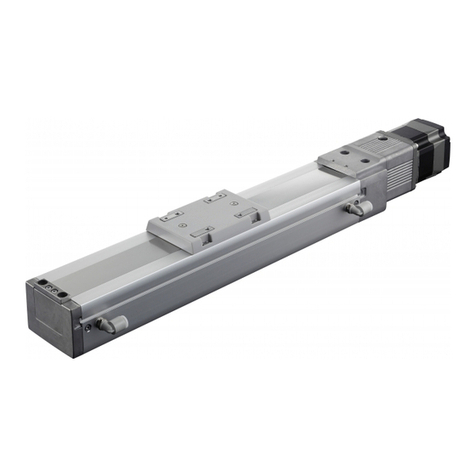
Oriental motor
Oriental motor EZS Series operating manual
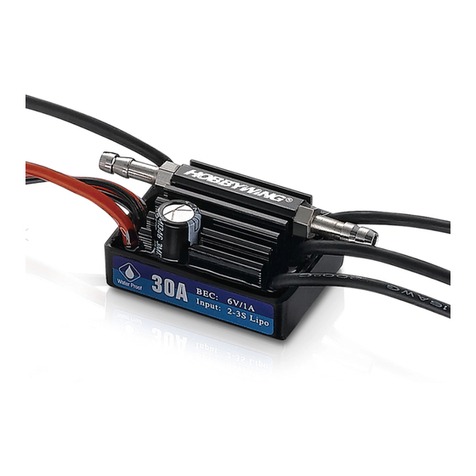
Hobby-Wing
Hobby-Wing SEAKING V3 RTR Series user manual