GE IAC User manual

GEK
-
86054
CONTENTS
PAGE
DESCRIPTION
APPLICATION
RATINGS
.
3
3
4
INDUCTION
UNIT
STANDARD
INSTANTANEOUS
UNIT
CHARACTERISTICS
INDUCTION
UNIT
STANDARD
INSTANTANEOUS
UNIT
CONSTRUCTION
RECEIVING
,
HANDLING
AND
STORAGE
ACCEPTANCE
TESTS
VISUAL
INSPECTION
MECHANICAL
INSPECTION
ELECTRICAL
TESTS
DRAWOUT
RELAYS
,
GENERAL
POWER
REQUIREMENTS
,
GENERAL
.
.
.
TIME
-
OVERCURRENT
UNIT
Time
Setting
Pickup
Test
Time
Test
INSTANTANEOUS
UNIT
Setting
the
Instantaneous
Unit
Pickup
Test
TARGET
AND
SEAL
-
IN
UNIT
Pickup
and
Dropout
Test
.
.
.
4
5
6
6
8
8
9
9
9
10
10
10
10
11
11
11
12
12
12
12
12
13
13
INSTALLATION
TIME
-
OVERCURRENT
UNIT
TARGET
AND
SEAL
-
IN
UNIT
INSTANTANEOUS
UNIT
PERIODIC
CHECKS
AND
ROUTINE
MAINTENANCE
TIME
-
OVERCURRENT
UNIT
INSTANTANEOUS
UNIT
TARGET
AND
SEAL
-
IN
UNIT
CONTACT
CLEANING
SYSTEM
TEST
SERVICING
TIME
-
OVERCURRENT
UNIT
Pickup
Tests
Time
Tests
INSTANTANEOUS
UNIT
TARGET
AND
SEAL
-
IN
UNIT
RENEWAL
PARTS
LIST
OF
FIGURES
13
13
14
14
14
14
14
14
15
15
15
15
16
16
16
17
18
2
Courtesy of NationalSwitchgear.com

GEK
-
86054
TIME
OVERCURRENT
RELAYS
TYPES
:
IAC
66
A
,
IAC
66
B
,
IAC
66
C
DESCRIPTION
a
long
time
induction
overcurrent
unit
,
an
The
relays
contain
three
units
:
instantaneous
overcurrent
unit
,
and
a
target
and
seal
-
in
unit
.
APPLICATION
The
IAC
66
A
,
B
,
and
C
relays
are
used
to
protect
a
motor
against
two
abnormal
conditions
.
The
time
induction
overcurrent
unit
(
51
/
TOC
)
protects
against
motor
overloads
.
The
unit
has
a
long
-
time
inverse
characteristic
which
is
designed
to
coordinate
with
the
motor
heating
characteristic
,
coordination
to
insure
against
false
tripping
on
motor
starting
currents
,
and
yet
still
provide
adequate
protection
against
motor
overloads
.
The
usual
setting
for
pickup
is
125
to
150
%
of
the
motor
rating
.
The
instantaneous
overcurrent
unit
(
50
/
I
0
C
-
A
)
provides
fault
protection
,
pickup
of
this
unit
must
be
set
higher
than
the
maximum
momentary
motor
inrush
current
,
with
an
adequate
margin
,
such
as
50
%
or
more
.
Typical
pickup
settings
for
the
two
overcurrent
units
are
as
below
:
Application
requires
The
TABLE
I
PICKUP
SETTING
(
MULTIPLES
OF
MOTOR
FULL
LOAD
CURRENT
)
UNIT
1.15
to
1.4
51
/
TOC
Time
overcurrent
unit
Normal
Dropout
Instanta
-
neous
Overcurrent
Unit
8
to
15
50
/
I
0
C
-
A
The
IAC
66
C
relay
is
similar
to
the
IAC
66
A
and
IAC
66
B
relays
except
that
the
time
unit
and
instantaneous
unit
contacts
are
brought
out
separately
.
These
instructions
do
not
purport
to
cover
all
details
or
variations
in
equipment
nor
provide
for
every
possible
contingency
to
be
met
in
connection
with
installation
,
operation
or
maintenance
.
Should
further
information
be
desired
or
should
particular
problems
arise
which
are
not
covered
sufficiently
for
the
purchaser
’
s
purposes
,
the
matter
should
be
referred
to
the
General
Electric
Company
.
To
the
extent
required
the
products
described
herein
meet
applicable
ANSI
,
IEEE
and
NEMA
standards
;
but
no
such
assurance
is
given
with
respect
to
local
codes
and
ordinances
because
they
vary
greatly
.
3
Courtesy of NationalSwitchgear.com

GEK
-
86054
The
internal
connections
are
:
TABLE
II
Drawing
No
.
Figure
Relay
6209658
0257
A
8339
6209961
0285
A
6667
6375694
0285
A
6747
IAC
66
A
IAC
66
A
,
Forms
51
and
up
IAC
66
B
IAC
66
B
,
Forms
51
and
up
IAC
66
C
IAC
66
C
,
Forms
51
and
up
2
A
2
B
3
A
3
B
4
A
4
B
The
outline
and
panel
drilling
dimensions
are
shown
in
Figure
5
.
RATINGS
INDUCTION
UNIT
The
induction
unit
coll
is
available
in
several
ranges
of
pickup
current
.
Table
III
lists
ranges
,
tap
values
,
continuous
-
current
ratings
and
short
time
current
ratings
of
the
induction
unit
coil
.
The
induction
unit
contacts
will
close
30
amperes
for
voltages
not
exceeding
250
volts
.
The
current
carrying
ratings
are
affected
by
the
tap
selected
on
the
target
and
seal
-
1
n
coll
,
as
Indicated
1
n
Table
IV
.
If
the
tripping
current
exceeds
30
amperes
,
use
an
auxiliary
relay
that
is
connected
such
that
the
tripping
current
does
not
pass
through
either
the
contacts
or
the
target
and
seal
-
in
coils
of
the
protective
relay
.
TABLE
III
INDUCTION
UNIT
COIL
RATINGS
(
FORMS
51
AND
UP
)
SHORT
TIME
(
ONE
SECOND
)
RATING
(
AMPS
)
CONTINUOUS
CURRENT
(
AMPS
)
PICKUP
RANGE
(
AMPS
)
TAP
VALUES
(
AMPS
)
75
0.6
,
0.8
,
1.0
,
1.2
,
1.4
,
1.6
,
3
0.6
/
1.8
1.8
200
1.5
,
2
,
2.5
,
3
,
3.5
,
4
,
4.5
1.5
/
4.5
5
300
2.5
,
3
,
3.5
4
,
5
,
6
,
7.5
5
2.5
/
7.5
10
400
4.0
/
12
4
,
5
,
6
,
7
,
8
,
10
,
12
Two
taps
are
required
to
select
pickup
for
IAC
66
relays
having
forms
51
and
up
.
The
two
taps
required
for
the
values
shown
1
n
Table
III
are
(
from
the
lowest
to
highest
pickup
)
:
A
/
L
,
B
/
K
,
C
/
J
,
D
/
H
,
D
/
G
,
E
/
G
and
F
/
G
,
respectively
,
as
labelled
on
4
Courtesy of NationalSwitchgear.com

GEK
-
86054
To
obtain
a
tap
value
of
4.0
amps
on
the
2.5
/
7.5
amp
relay
,
use
taps
the
tap
block
.
D
/
H
.
TABLE
IV
RATINGS
OF
TARGET
AND
SEAL
-
IN
COIL
DUAL
-
RATED
0
,
2
/
2.0
AMP
0.2
AMP
TAP
2.0
AMP
TAP
CURRENT
OPERATED
(
seconds
)
(
seconds
)
(
amperes
)
(
amperes
)
(
amperes
)
(
ohms
)
(
ohms
)
(
ohms
)
Carry
30
amps
for
Carry
10
amps
for
Carry
continuously
Minimum
operating
Minimum
dropout
DC
resistance
60
hertz
impedance
50
hertz
impedance
2.2
0.05
0.45
2.0
0.37
2.3
2.0
0.2
0.05
0.5
8.3
0.24
0.65
50
42
0.54
STANDARD
INSTANTANEOUS
UNIT
Table
V
lists
the
The
instantaneous
unit
is
designed
to
use
one
of
several
coils
,
pickup
range
,
continuous
current
ratings
and
short
time
rating
of
each
of
these
coils
for
forms
1
through
50
.
TABLE
V
STANDARD
INSTANTANEOUS
UNIT
COIL
RATINGS
CONTINUOUS
CURRENT
(
AMPS
)
SHORT
TIME
(
ONE
SECOND
)
RATING
(
AMPS
)
PICKUP
RANGE
(
AMPS
)
12
0.5
-
2
0.75
1.5
25
1
4
51
3.0
2
8
127
16
6.0
4
15.0
10
205
40
326
30.0
20
80
326
40
-
160
60.0
5
Courtesy of NationalSwitchgear.com

GEK
-
86054
For
forms
51
and
up
,
the
standard
instantaneous
unit
has
the
following
ratings
,
listed
in
Table
VI
:
TABLE
VI
STANDARD
INSTANTANEOUS
UNIT
COIL
RATINGS
-
FORMS
51
AND
UP
CfTDTCC
flD
PARALLEL
CONTINUOUS
RATINGS
ONE
SECOND
ft
RANGE
Series
Parallel
0.75
25.0
0.5
-
1.0
-
2.0
0.5
-
4.0
1.5
4.0
50.0
130.0
260.0
3.0
2.0
-
16.0
8.0
Series
Parallel
2.0
-
4.0
-
6.0
16.0
15.0
10.0
-
80.0
10.0
-
20.0
-
Series
Parallel
400.0
600.0
40.0
25.0
80.0
600.0
600.0
20.0
-
160.0
Series
Parallel
25.0
20.0
-
40.0
-
160.0
80.0
25.0
ft
Higher
currents
(
I
)
may
be
applied
for
shorter
lengths
of
time
(
T
)
in
accordance
with
the
formula
:
/
K
I
=
V
-
K
—
constant
T
The
current
-
closing
rating
of
the
contacts
is
30
amperes
for
voltages
not
exceeding
250
volts
.
CHARACTERISTICS
INDUCTION
UNIT
The
induction
unit
consists
of
a
conducting
disk
that
passes
through
the
poles
of
a
permanent
magnet
and
an
electromagnet
.
The
disk
is
free
to
rotate
with
a
vertically
suspended
shaft
,
but
is
restrained
in
one
direction
by
a
spring
.
When
energized
with
an
alternating
current
of
proper
magnitude
(
set
by
the
tap
position
)
,
the
electromagnet
produces
out
of
phase
fluxes
at
its
pole
faces
.
These
fluxes
interact
with
induced
currents
in
the
disk
to
produce
a
torque
on
the
disk
.
When
this
torque
exceeds
the
restraining
force
of
the
spring
,
the
disk
begins
to
rotate
at
a
speed
determined
by
the
magnetic
dragging
action
of
the
permanent
magnet
.
A
post
attached
to
the
rotating
shaft
travels
a
specific
distance
(
set
by
the
time
dial
)
,
and
makes
electrical
contact
with
a
fixed
member
.
Figure
6
gives
the
time
for
the
induction
unit
to
close
its
contacts
for
various
multiples
of
pickup
current
and
time
dial
settings
.
The
time
required
for
this
unit
to
reset
from
contact
closure
to
the
Number
10
time
dial
position
is
approximately
60
seconds
.
Burden
data
for
induction
unit
coils
is
listed
in
Table
VII
.
The
impedance
values
are
for
the
minimum
tap
.
The
impedance
for
other
taps
at
pickup
current
(
tap
6
Courtesy of NationalSwitchgear.com

GEK
-
86054
rating
)
varies
(
approximately
)
inversely
to
the
square
of
the
current
rating
,
following
equation
illustrates
this
:
The
Impedance
of
Any
Tap
at
Tap
Amps
/
Minimum
Tap
Amps
\
2
x
/
Impedance
at
\
Tap
Amps
^
Minimum
Tap
TABLE
VII
BURDENS
OF
INDUCTION
UNIT
COILS
VOLT
-
AMPS
AT
FIVE
AMPS
CALCULATED
FROM
INPUT
AT
MINIMUM
PICKUP
(
I
?
Z
1
PICKUP
RANGE
(
AMPS
1
FREQ
.
(
Hz
)
TAP
POWER
FACTOR
WATTS
1.0
-
3.0
60
1
118.4
15.2
0.13
50
1
98.6
12.7
0.13
1.5
-
4.5
60
1.5
52.5
6.7
0.13
50
1.5
43.7
5.6
0.13
2.5
-
7.5
60
2.5
18.8
2.5
0.13
50
2.5
15.7
2.1
0.13
4.0
-
12
60
4
7.4
0.95
0.13
50
4
6.2
0.79
0.13
For
forms
51
and
up
,
the
burden
of
the
induction
unit
is
as
shown
in
Table
VIII
:
TABLE
VIII
BURDENS
OF
INDUCTION
UNIT
COILS
-
FORMS
51
AND
UP
PICKUP
RANGE
(
AMPS
'
)
VOLT
-
AMPS
AT
FIVE
AMPS
CALCULATED
FROM
INPUT
AT
MINIMUM
PICKUP
(
I
^
Zl
FREQ
.
IMP
.
POWER
FACTOR
(
Hz
)
TAP
OHMS
0.6
-
1.8
60
0.6
110.75
4.43
0.32
0.33
50
0.6
48.0
1.92
1.5
-
4.5
60
1.5
17.75
0.71
0.35
50
1.5
11.5
0.46
0.37
2.5
-
7.5
60
2.5
6.75
0.27
0.44
50
2.5
5.75
0.23
0.47
4.0
-
12
60
4.0
4.48
0.18
0.52
0.47
50
4.0
4.05
0.16
7
Courtesy of NationalSwitchgear.com

GEK
-
86054
STANDARD
INSTANTANEOUS
UNIT
The
standard
instantaneous
unit
is
an
electromagnet
that
attracts
a
hinged
armature
when
sufficient
current
is
applied
,
contact
that
bridges
two
stationary
contacts
when
the
coil
is
energized
.
A
target
is
displayed
when
the
unit
operates
.
Pressing
the
button
in
the
lower
left
corner
of
the
relay
cover
resets
the
target
.
The
armature
carries
a
"
T
"
shaped
moving
The
pickup
range
can
be
adjusted
continuously
over
a
four
to
one
range
by
using
the
adjustable
pole
piece
.
When
the
top
of
the
core
is
lined
up
with
the
calibration
stampings
,
an
approximate
value
of
pickup
can
be
determined
.
Dropout
is
about
40
to
50
%
of
pickup
.
Figure
7
shows
the
variation
of
operating
time
with
applied
current
for
this
unit
.
Burden
data
of
the
standard
instantaneous
unit
is
tabulated
in
Table
IX
.
TABLE
IX
BURDEN
OF
STANDARD
INSTANTANEOUS
UNIT
IMPEDANCE
(
OHMS
)
POWER
FACTOR
VOLT
-
AMPStt
FREQ
PICKUP
RANGE
(
AMPS
)
(
HZ
)
AMPS
12.4
310
0.84
0.5
-
2
50
5
13.2
0.78
330
60
5
0.77
94
3.75
1
50
5
4
0.71
100
4.0
60
5
0.77
23
0.94
8
50
5
2
0.71
1.0
25
60
5
0.23
0.77
16
5
5.8
50
4
0.71
6.2
0.25
5
60
0.77
0.9
0.04
10
5
50
40
0.71
1.0
0.04
5
60
0.01
0.77
0.23
50
5
20
80
0.71
0.01
0.25
60
5
0.71
0.003
0.003
0.07
40
-
160
5
50
0.71
0.07
60
5
ft
Volt
-
amperes
at
5
amps
calculated
from
input
at
minimum
pickup
(
I
2
Z
)
.
CONSTRUCTION
The
IAC
66
A
,
B
,
and
C
relays
are
mounted
in
an
SI
case
(
that
does
not
have
an
upper
contact
block
)
.
The
case
is
suitable
for
either
semi
-
flush
or
surface
mounting
on
panels
up
to
two
inches
thick
.
Hardware
is
available
for
all
panel
thicknesses
.
To
be
sure
that
the
proper
hardware
will
be
provided
,
panel
thickness
should
be
specified
on
the
order
for
the
relay
.
Outline
and
panel
drilling
dimensions
are
shown
in
Figure
5
.
8
Courtesy of NationalSwitchgear.com

GEK
-
86054
The
relay
components
are
mounted
on
a
cradle
assembly
that
can
easily
be
removed
from
the
relay
case
.
The
cradle
is
locked
in
the
case
by
latches
at
the
top
and
bottom
.
Electrical
connections
between
case
and
cradle
blocks
are
completed
through
removable
connection
plugs
.
Separate
testing
plugs
can
be
inserted
in
place
of
the
connection
plugs
to
test
the
relay
in
its
case
.
The
cover
is
attached
to
the
case
from
the
front
,
and
includes
an
interlock
arm
that
prevents
the
cover
from
being
replaced
until
the
connection
plug
has
been
inserted
.
The
induction
unit
,
consisting
of
a
U
-
magnet
,
drag
magnet
and
a
disk
assembly
,
is
mounted
on
a
metal
frame
.
The
pickup
of
the
induction
unit
is
set
by
a
tap
block
located
near
the
top
of
the
relay
.
The
time
delay
is
adjusted
by
turning
the
molded
time
dial
,
located
just
below
the
tap
block
.
The
standard
instantaneous
unit
is
mounted
just
above
the
drag
magnet
on
the
right
hand
side
.
The
adjustable
core
can
be
raised
or
lowered
to
change
the
pickup
of
the
unit
.
The
unit
just
above
the
drag
magnet
on
the
left
is
a
target
seal
-
in
unit
for
the
induction
unit
.
This
seal
in
unit
does
not
have
an
adjustable
core
,
but
tap
screws
located
on
the
right
side
of
the
unit
can
be
used
to
change
pickup
.
Relay
construction
is
illustrated
in
Figures
1
A
and
IB
.
RECEIVING
,
HANDLING
AND
STORAGE
This
relay
,
when
not
included
as
part
of
a
control
panel
,
will
be
shipped
in
a
carton
designed
to
protect
it
against
damage
.
Upon
receipt
,
immediately
examine
the
relay
for
any
damage
sustained
in
transit
,
evident
,
file
a
damage
claim
at
once
with
the
transportation
company
,
and
promptly
notify
the
nearest
General
Electric
Sales
Office
.
If
the
equipment
is
not
to
be
installed
immediately
,
it
should
be
stored
indoors
in
a
location
that
is
dry
and
protected
from
dust
,
metallic
chips
and
severe
atmospheric
contaminants
.
If
damage
from
rough
handling
is
ACCEPTANCE
TESTS
Immediately
upon
receipt
of
the
relay
an
INSPECTION
AND
ACCEPTANCE
TEST
should
be
made
to
make
sure
that
no
damage
has
been
sustained
in
shipment
and
that
the
relay
calibrations
have
not
been
disturbed
,
that
readjustment
is
necessary
,
refer
to
the
section
on
SERVICING
.
These
tests
may
be
performed
as
part
of
the
installation
or
as
acceptance
tests
,
at
the
discretion
of
the
user
.
If
the
examination
or
test
indicates
Since
most
operating
companies
use
different
procedures
for
acceptance
and
for
installation
tests
,
the
following
section
includes
all
applicable
tests
that
may
be
performed
on
these
relays
.
VISUAL
INSPECTION
Check
the
nameplate
stamping
to
make
sure
that
the
model
number
and
rating
of
the
relay
agree
with
the
requisition
.
9
Courtesy of NationalSwitchgear.com

GEK
-
86054
Remove
the
relay
from
its
case
and
check
that
there
are
no
broken
or
cracked
molded
parts
or
other
signs
of
physical
damage
,
and
that
all
screws
are
tight
.
MECHANICAL
INSPECTION
There
should
be
no
noticeable
friction
when
the
disk
is
rotated
slowly
clockwise
.
The
disk
should
return
by
itself
to
its
rest
position
.
1
.
Make
sure
the
control
spring
is
not
deformed
,
nor
its
convolutions
tangled
or
touching
.
2
.
The
armature
and
contacts
of
the
seal
-
in
unit
,
as
well
as
the
armature
and
contacts
of
the
instantaneous
unit
,
should
move
freely
when
operated
by
hand
;
there
should
be
at
least
1
/
32
"
wipe
on
the
seal
-
in
contacts
.
3
.
The
targets
in
the
seal
-
in
unit
and
in
the
instantaneous
unit
must
come
into
view
and
latch
when
the
armatures
are
operated
by
hand
,
and
should
unlatch
when
the
target
release
lever
is
operated
.
Make
sure
that
the
fingers
and
shorting
bars
agree
with
the
internal
-
connections
diagram
.
4
.
5
.
CAUTION
Every
circuit
in
the
drawout
case
has
an
auxiliary
brush
.
It
is
especially
important
on
current
circuits
and
other
circuits
with
shorting
bars
that
the
auxiliary
brush
be
bent
high
enough
to
engage
the
connecting
plug
or
test
plug
before
the
main
brushes
do
.
This
will
prevent
Current
Transformer
(
CT
)
secondary
circuits
from
being
opened
.
See
Figure
1
.
ELECTRICAL
TESTS
DRAWOUT
RELAYS
,
GENERAL
Since
all
drawout
relays
in
service
operate
in
their
cases
,
it
is
recommended
that
they
be
tested
in
their
cases
or
an
equivalent
steel
case
.
In
this
way
,
any
magnetic
effects
of
the
enclosure
will
be
accurately
duplicated
during
testing
.
A
relay
may
be
tested
without
removing
it
from
the
panel
by
using
a
12
XLA
13
A
test
plug
.
This
plug
makes
connections
only
with
the
relay
and
does
not
disturb
any
shorting
bars
in
the
case
.
The
12
XLA
12
A
test
plug
may
also
be
used
.
Although
this
test
plug
allows
greater
testing
flexibility
,
it
requires
C
.
T
.
shorting
jumpers
and
the
exercise
of
greater
care
,
since
connections
are
made
to
both
the
relay
and
the
external
circuitry
.
POWER
REQUIREMENTS
,
GENERAL
All
devices
operating
on
alternating
current
(
AC
)
are
affected
by
frequency
.
Since
non
-
sinusoidal
waveforms
can
be
analyzed
as
a
fundamental
frequency
plus
harmonics
of
that
fundamental
frequency
,
it
follows
that
alternating
-
current
devices
(
relays
)
will
be
affected
by
applied
waveforms
.
AC
relays
(
and
AC
devices
in
general
)
are
significantly
affected
by
the
application
of
non
-
sinusoidal
waveforms
.
10
Courtesy of NationalSwitchgear.com

GEK
-
86054
Therefore
,
in
order
to
test
AC
relays
properly
it
is
essential
to
use
a
test
voltage
and
/
or
current
waveform
that
is
sinusoidal
.
The
purity
of
the
sine
wave
(
i
.
e
.
,
its
freedom
from
harmonics
)
cannot
be
expressed
as
a
finite
number
for
any
particular
relay
;
however
,
any
relay
using
tuned
circuits
,
RL
or
RC
networks
,
or
saturating
electromagnets
(
such
as
time
-
overcurrent
relays
)
would
be
especially
affected
by
non
-
sinusoidal
wave
forms
.
TIME
-
OVERCURRENT
UNIT
Rotate
the
time
dial
slowly
and
check
,
by
means
of
a
lamp
in
the
circuit
,
that
the
contacts
just
close
at
the
zero
(
0
)
time
-
dial
setting
.
The
point
at
which
the
contacts
just
close
can
be
adjusted
by
running
the
stationary
contact
brush
in
or
out
by
means
of
its
adjusting
screw
.
This
screw
should
be
held
securely
in
its
support
.
With
the
contacts
just
closing
at
No
.
0
time
-
dial
setting
,
there
should
be
sufficient
gap
between
the
stationary
contact
brush
and
its
metal
backing
strip
to
ensure
approximately
1
/
32
"
wipe
.
The
minimum
current
at
which
the
contacts
will
just
close
is
determined
by
the
position
of
the
tap
screw
in
the
tap
block
at
the
top
of
the
relay
.
When
changing
the
current
setting
with
the
relay
in
its
case
,
remove
the
connection
plug
,
to
short
the
current
-
transformer
secondary
circuit
.
Next
,
screw
the
tap
screws
into
the
tap
marked
for
the
desired
current
,
and
then
replace
the
connection
plug
.
The
pickup
of
the
unit
for
any
current
tap
is
adjusted
by
means
of
a
spring
-
adjusting
ring
just
above
the
control
spring
.
See
Figure
IB
.
The
ring
may
be
turned
by
inserting
a
screw
driver
in
the
notches
around
the
edge
.
By
turning
the
ring
,
the
operating
current
of
the
unit
may
be
brought
into
agreement
with
the
tap
setting
employed
if
,
for
some
reason
,
this
adjustment
has
been
disturbed
.
This
adjustment
also
permits
any
desired
setting
intermediate
between
the
various
tap
settings
to
be
obtained
.
The
unit
is
adjusted
at
the
factory
to
close
its
contacts
from
any
time
-
dial
position
at
a
minimum
current
within
five
percent
(
5
%
)
of
the
tap
plug
setting
.
The
unit
resets
at
90
%
of
the
minimum
closing
value
.
Time
Setting
The
setting
of
the
time
dial
determines
the
length
of
time
the
unit
requires
to
close
its
contacts
when
the
current
reaches
a
predetermined
value
.
The
contacts
are
just
closed
when
the
dial
is
set
on
0
.
When
the
dial
is
set
on
10
,
the
disk
must
travel
the
maximum
amount
to
close
the
contacts
;
therefore
this
setting
gives
the
maximum
time
setting
.
The
primary
adjustment
for
the
time
of
operation
of
the
unit
is
made
by
means
of
the
time
dial
.
However
,
further
adjustment
is
obtained
by
moving
the
permanent
magnet
along
its
supporting
shelf
;
moving
the
magnet
toward
the
disk
shaft
decreases
the
time
,
while
moving
it
away
increases
the
time
.
Pickup
Test
Use
rated
frequency
for
both
the
pickup
and
time
tests
.
Set
the
relay
at
the
0.5
time
-
dial
position
and
2.0
ampere
tap
.
Using
the
test
connections
in
Figure
9
,
the
main
unit
should
close
its
contacts
within
±
2.0
%
11
Courtesy of NationalSwitchgear.com

GEK
-
86054
All
other
tap
positions
should
pick
up
at
tap
value
±
5
%
of
of
tap
value
current
,
tap
value
.
Time
Test
Set
the
relay
at
No
.
5
time
-
dial
setting
and
minimum
amp
tap
.
Using
the
test
connection
in
Figure
9
,
apply
five
times
(
5
x
)
tap
current
to
the
relay
.
The
relay
should
operate
in
18.6
seconds
±
0.9
second
.
All
other
tap
,
time
-
dial
and
multiples
of
pickup
combinations
should
agree
with
the
time
-
curve
value
±
7
%
.
INSTANTANEOUS
UNIT
Make
sure
that
the
instantaneous
unit
is
wired
for
the
range
in
which
it
is
to
4
)
and
connected
as
operate
(
see
Internal
-
Connections
Diagram
,
Figures
2
indicated
in
test
circuit
Figure
9
.
Whenever
possible
,
use
the
higher
range
,
since
the
higher
range
has
a
higher
continuous
rating
.
Setting
the
Instantaneous
Unit
Loosen
the
locknut
and
turn
the
pole
piece
toward
the
desired
setting
.
See
Figure
1
A
.
Turning
the
pole
piece
up
increases
the
pickup
;
turning
the
pole
piece
down
decreases
the
pickup
.
Bring
up
the
current
slowly
until
the
unit
picks
up
.
It
may
be
necessary
to
repeat
this
operation
until
the
desired
pickup
value
is
obtained
.
Once
the
desired
pickup
value
is
reached
,
tighten
the
locknut
.
CAUTION
The
instantaneous
unit
is
rated
1.5
times
minimum
pick
up
.
test
current
on
too
long
,
as
it
may
damage
the
unit
.
Do
not
leave
the
Pickup
Test
With
the
unit
connected
for
high
-
range
operation
(
parallel
connections
)
and
the
target
in
the
"
Down
"
position
,
check
the
pickup
at
the
maximum
calibration
mark
;
the
pickup
should
be
within
the
limits
in
Table
X
.
TABLE
X
MAXIMUM
AMPERES
UNIT
RANGE
AMPERES
MINIMUM
AMPERES
CALIBRATION
AMPERES
3.6
4.0
0.5
-
4.0
4.5
2.0
-
16.0
16.0
17.7
14.4
10.0
-
80.0
80.0
89.0
72.0
177.0
20.0
-
160.0
144.0
160.0
TARGET
AND
SEAL
-
IN
UNIT
The
target
and
seal
-
in
unit
has
an
operating
coil
tapped
at
0.2
and
2.0
The
relay
is
shipped
from
the
factory
with
the
tap
screw
in
the
lower
-
The
tap
screw
is
the
screw
holding
the
right
-
hand
stationary
To
change
the
tap
setting
,
first
remove
one
screw
from
the
left
-
hand
amperes
,
ampere
position
,
contact
.
12
Courtesy of NationalSwitchgear.com

GEK
-
86054
Next
,
remove
the
screw
from
stationary
contact
and
place
it
in
the
desired
tap
.
the
first
,
undesired
,
tap
and
place
it
on
the
left
hand
stationary
contact
where
the
first
screw
was
removed
.
prevent
the
right
-
hand
stationary
contact
from
getting
out
of
adjustment
,
should
never
be
left
in
both
taps
at
the
same
time
.
This
procedure
is
necessary
to
Screws
See
Figure
1
A
.
Pickup
and
Dropout
Test
Connect
relay
studs
1
and
2
(
See
Internal
-
Connections
Diagram
)
to
a
DC
source
,
ammeter
and
load
box
so
that
the
current
can
be
controlled
over
a
range
of
0.1
to
2.0
amperes
.
1
.
Turn
the
time
dial
to
the
ZERO
(
0
)
TIME
DIAL
position
.
2
.
See
Table
XI
.
Increase
the
current
slowly
until
the
seal
-
in
unit
picks
up
.
3
.
Move
the
time
dial
away
from
the
ZERO
TIME
-
DIAL
position
;
the
seal
-
in
unit
should
remain
in
the
picked
-
up
position
.
4
.
Decrease
the
current
slowly
until
the
seal
-
in
unit
drops
out
.
See
Table
XI
.
5
.
TABLE
XI
DROPOUT
CURRENT
PICK
-
UP
CURRENT
TAP
0.15
-
0.195
1.50
-
1.95
.
050
OR
MORE
.
55
OR
MORE
0.2
2.0
INSTALLATION
The
following
tests
are
to
be
performed
at
the
time
of
installation
.
TIME
-
OVERCURRENT
UNIT
Using
the
test
circuit
in
Figure
9
,
Reduce
the
This
Set
the
tap
screw
in
the
desired
tap
.
apply
approximately
twice
tap
value
until
contacts
just
close
,
current
until
the
light
in
series
with
the
contacts
begins
to
flicker
,
value
of
current
is
defined
as
pickup
,
and
should
be
within
5
%
of
tap
value
.
1
.
Check
the
operating
time
at
some
multiple
of
tap
value
.
This
multiple
of
tap
value
may
be
five
times
(
5
x
)
the
tap
rating
,
or
the
maximum
fault
current
for
which
the
relay
must
coordinate
.
The
value
used
is
left
to
the
discretion
of
the
user
.
The
operating
time
should
be
the
time
shown
on
the
time
-
current
curve
±
7
%
.
2
.
TARGET
AND
SEAL
-
IN
UNIT
Make
sure
that
the
tap
screw
is
in
the
desired
tap
.
Perform
pickup
and
dropout
tests
,
as
outlined
in
the
ACCEPTANCE
TESTS
section
.
1
.
2
.
13
Courtesy of NationalSwitchgear.com

GEK
-
86054
INSTANTANEOUS
UNIT
1
.
Select
the
desired
range
by
making
the
proper
connections
at
the
rear
of
the
relay
(
See
Internal
-
Connections
Diagram
)
.
select
the
higher
range
since
it
has
a
higher
continuous
rating
.
Whenever
possible
,
be
sure
to
2
.
Set
the
instantaneous
unit
to
pick
up
at
the
desired
current
level
.
SETTING
THE
INSTANTANEOUS
UNIT
in
the
ACCEPTANCE
TESTS
section
.
See
All
the
tests
described
above
under
Installation
Tests
must
be
performed
at
In
addition
,
if
those
tests
described
under
the
ACCEPTANCE
TESTS
section
were
not
performed
prior
to
installation
,
it
is
recommended
they
be
performed
at
this
time
.
the
time
of
installation
.
PERIODIC
CHECKS
AND
ROUTINE
MAINTENANCE
In
view
of
the
vital
role
of
protective
relays
in
the
operation
of
a
power
system
,
it
is
important
that
a
periodic
test
program
be
followed
.
It
is
recognized
that
the
interval
between
periodic
checks
will
vary
depending
upon
environment
,
type
of
relay
and
the
user
'
s
experience
with
periodic
testing
.
Until
the
user
has
accumulated
enough
experience
to
select
the
test
interval
best
suited
to
his
individual
requirements
,
it
is
suggested
that
the
points
listed
below
be
checked
at
an
interval
of
from
one
to
two
years
.
These
tests
are
intended
to
make
sure
that
the
relays
have
not
deviated
from
their
original
setting
.
If
deviations
are
encountered
,
the
relay
must
be
retested
and
serviced
as
described
in
this
manual
.
TIME
-
OVERCURRENT
UNIT
1
.
Perform
Pickup
Test
as
described
in
the
ACCEPTANCE
TESTS
section
for
the
tap
in
service
.
2
.
Perform
the
Time
Test
as
described
in
the
ACCEPTANCE
TESTS
section
.
INSTANTANEOUS
UNIT
1
.
Check
that
the
instantaneous
unit
picks
up
at
the
desired
current
level
,
as
outlined
in
the
ACCEPTANCE
TESTS
section
.
TARGET
AND
SEAL
-
IN
UNIT
1
.
Check
that
the
unit
picks
up
at
the
values
shown
in
table
XI
.
Check
that
the
unit
drops
out
at
30
%
or
more
of
tap
value
.
2
.
CONTACT
CLEANING
For
cleaning
relay
contacts
,
a
flexible
burnishing
tool
should
be
used
.
This
consists
of
a
flexible
strip
of
metal
with
an
etch
-
roughened
surface
,
resembling
in
effect
a
superfine
file
.
The
polishing
action
is
so
delicate
that
no
scratches
are
left
,
yet
it
will
clean
off
any
corrosion
thoroughly
and
rapidly
.
Its
flexibility
ensures
the
cleaning
of
the
actual
points
of
contact
.
Do
not
use
knives
,
files
,
abrasive
paper
or
cloth
of
any
kind
to
clean
relay
contacts
.
14
Courtesy of NationalSwitchgear.com

GEK
-
86054
SYSTEM
TEST
Although
this
Instruction
Book
is
primarily
written
to
check
and
set
the
IAC
relay
,
overall
functional
tests
to
check
the
system
operation
are
recommended
at
intervals
based
on
the
customer
'
s
experience
.
SERVICING
TIME
-
OVERCURRENT
UNIT
If
it
is
found
during
installation
or
periodic
testing
that
the
time
-
overcurrent
unit
is
out
of
limits
,
the
unit
may
be
recalibrated
as
follows
:
Pickup
Tests
:
The
pickup
of
the
unit
for
any
current
tap
is
adjusted
by
means
of
a
spring
-
adjusting
ring
.
The
ring
may
be
turned
by
inserting
a
screw
driver
in
the
notches
around
the
edge
.
By
turning
the
ring
,
the
operating
current
of
the
unit
may
be
brought
into
agreement
with
the
tap
setting
employed
if
,
for
some
reason
,
this
adjustment
has
been
disturbed
.
This
adjustment
also
permits
any
desired
setting
intermediate
between
the
various
tap
settings
to
be
obtained
.
The
unit
is
adjusted
at
the
factory
to
close
its
contacts
from
any
time
-
dial
position
at
a
minimum
current
within
five
percent
(
5
%
)
of
the
tap
plug
setting
.
The
unit
resets
at
90
%
of
the
minimum
closing
value
.
Rotate
the
time
dial
to
the
No
.
0
time
-
dial
setting
and
check
,
by
means
of
a
lamp
in
the
circuit
,
that
the
contacts
just
close
.
The
point
at
which
the
contacts
just
close
can
be
adjusted
by
running
the
This
screw
stationary
contact
brush
in
or
out
by
means
of
its
adjusting
screw
,
should
be
held
securely
in
its
support
.
With
the
contacts
just
closing
at
No
.
0
time
-
dial
setting
,
there
should
be
sufficient
gap
between
the
stationary
contact
brush
and
its
metal
backing
strip
to
ensure
approximately
1
/
32
"
wipe
.
Connect
the
operating
-
coil
terminals
to
a
source
of
the
proper
frequency
and
good
wave
form
,
having
a
voltage
of
120
or
more
,
with
pure
resistance
load
boxes
for
setting
the
current
.
See
Test
-
Circuit
Figure
9
.
With
the
tap
plug
in
the
minimum
amp
tap
and
the
time
dial
set
where
contacts
are
just
open
,
adjust
the
control
spring
to
just
close
the
contacts
within
the
limits
given
below
,
which
are
plus
and
minus
2
percent
(
±
2
%
)
of
tap
amps
.
It
should
never
be
necessary
to
wind
up
the
control
-
spring
adjuster
more
than
30
°
(
one
notch
)
or
unwind
it
more
than
90
°
(
three
notches
)
from
the
factory
setting
to
obtain
the
above
pick
up
setting
.
With
the
tap
plug
in
the
minimum
amp
tap
and
the
time
dial
at
No
.
10
time
setting
,
check
the
current
required
to
just
move
the
disk
away
from
the
stop
arm
.
This
current
should
be
within
±
10
%
of
tap
amperes
.
If
the
disk
moves
at
the
lower
limit
,
check
that
the
movement
is
not
over
one
-
half
inch
(
1
/
2
"
)
measured
along
the
perimeter
of
the
disk
.
15
Courtesy of NationalSwitchgear.com

GEK
-
86054
Time
Tests
With
the
tap
plug
in
the
minimum
amp
tap
and
the
time
dial
at
No
.
5
time
setting
,
apply
five
times
(
5
x
)
tap
current
to
the
relay
.
Adjust
the
drag
magnet
to
obtain
a
closing
time
as
near
as
possible
to
18.6
The
magnet
should
be
seconds
,
but
at
least
between
17.7
and
19.5
seconds
,
approximately
in
the
middle
of
its
travel
.
The
magnet
is
adjusted
by
loosening
the
nut
under
the
magnet
shelf
.
Moving
the
magnet
in
decreases
the
time
.
Moving
the
magnet
out
increases
the
time
.
When
adjusting
the
drag
magnet
,
be
sure
the
outer
edge
of
the
magnet
never
extends
out
beyond
the
cutout
in
the
disk
.
Be
sure
the
screw
clamping
the
drag
magnet
to
its
supporting
shelf
is
tight
before
proceeding
with
other
time
checks
.
Make
sure
the
drag
magnet
does
not
hit
the
counterweight
at
any
position
of
the
disk
.
With
the
tap
plug
in
the
minimum
amp
tap
and
the
time
dial
at
the
No
.
5
time
setting
,
check
the
contact
closings
at
2
and
10
times
tap
value
.
These
closing
times
must
be
within
the
limits
shown
on
Table
XII
.
TABLE
XII
60
HZ
MIN
SEC
.
MAX
SEC
.
2
x
Tap
42.6
49.0
12.3
10
x
Tap
10.7
INSTANTANEOUS
UNIT
1
.
Both
contacts
should
close
at
the
same
time
.
The
backing
strip
should
be
so
formed
that
the
forked
end
(
front
)
bears
against
the
molded
strip
under
the
armature
.
2
.
With
the
armature
against
the
pole
piece
,
the
cross
member
of
the
"
T
"
spring
should
be
in
a
horizontal
plane
and
there
should
be
at
least
1
/
32
inch
wipe
on
the
contacts
.
front
half
of
the
shaded
pole
and
the
armature
,
with
the
armature
held
closed
.
The
contacts
should
close
with
the
feeler
gage
in
place
.
3
.
Check
this
by
inserting
a
0.012
inch
feeler
gage
between
the
TARGET
AND
SEAL
-
IN
UNIT
Check
steps
1
and
2
as
described
under
INSTANTANEOUS
UNIT
above
.
To
check
the
wipe
of
the
seal
-
in
unit
,
insert
a
0.012
inch
feeler
gage
between
the
plastic
residual
of
the
armature
and
the
pole
piece
,
with
the
armature
held
closed
.
The
contacts
should
close
with
the
feeler
gage
in
place
.
16
Courtesy of NationalSwitchgear.com

GEK
-
86054
RENEWAL
PARTS
It
is
recommended
that
sufficient
quantities
of
renewal
parts
be
carried
in
stock
to
enable
the
prompt
replacement
of
any
that
are
worn
,
broken
,
or
damaged
.
When
ordering
renewal
parts
,
address
the
nearest
Sales
Office
of
the
General
Electric
Company
,
specify
the
quantity
required
and
the
name
of
the
part
wanted
,
and
the
complete
model
number
of
the
relay
for
which
the
part
is
required
.
Since
the
last
edition
,
changes
have
been
made
1
n
Table
III
and
the
Immediately
following
text
,
and
in
Figure
3
A
.
17
Courtesy of NationalSwitchgear.com

GEK
-
86054
LIST
OF
FIGURES
PAGE
FIGURE
Photograph
:
Type
IAC
66
B
Relay
Out
of
Case
(
3
/
4
Front
View
)
Photograph
:
Type
IAC
66
B
Relay
Out
of
Case
(
Rear
View
)
.
.
Internal
Connections
Diagram
,
Type
IAC
66
A
Relay
Internal
Connections
Diagram
Type
IAC
66
A
,
Forms
51
and
up
19
1
A
19
IB
20
2
A
21
2
B
22
Internal
Connections
Diagram
Type
IAC
66
B
Internal
Connections
Diagram
Type
IAC
66
B
,
Forms
51
and
up
.
..
Internal
Connections
Diagram
for
Type
IAC
66
C
Relay
(
Front
View
)
Internal
Connections
Diagram
Type
IAC
66
C
,
Forms
51
and
up
..
.
Outline
and
Panel
Drilling
Diagram
,
Type
IAC
66
Relays
Time
Current
Curve
for
the
Long
-
time
Overcurrent
Unit
Operating
Time
Versus
Current
for
the
Standard
Instantaneous
Unit
Photograph
:
Cross
Section
of
Drawout
Case
Showing
Position
.
.
of
Auxiliary
Brushes
Test
connections
for
Testing
Pickup
&
Time
Curve
of
IAC
Relays
3
A
23
3
B
24
4
A
25
4
B
26
5
27
6
28
7
29
8
30
9
18
Courtesy of NationalSwitchgear.com

GEK
4
SDM
HOCK
U
*
WTMJT
-
in
UHrt
£
£
lh
ti
#
t
\
ASibniuiE
tOH
1
»
VrDIwO
LlJfcfr
,
SftlijlF
W
L
-
^
i
tSll
1
*
4
I
HSU
IN
«
JCK
1
»
S
das
*
l
-
Kfct
tl
"
l
yNJV
WMF
t
CHl
^
d
#
i
IIM
1
i
-
gpl
il
I
h
1
I
-
SrI
i
I
,
"
-
M
i
li
I
-
iiillill
'
id
"
[
ilTiil
iiijifi
l
?
•
i
.
PM
l
ciuki
-
iJIICMi
Figure
1
A
{
8
Q
39
J
70
)
Photographs
Type
IAC
66
B
Relay
Quit
of
Case
(
3
/
4
‘
Front
VI
«
r
)
CONtiCL
—
H
PIlNB
INDUCTION
UNIT
?
sv
,
a
,
CONliDL
KJSr
DitC
U
-
MlCh
[
T
Figure
IB
(
fl
03
Mfll
)
Photograph
;
rype
IAC
66
Q
Relgj
Out
of
Case
(
Rear
Viev
)
w
T
9
Courtesy of NationalSwitchgear.com
This manual suits for next models
3
Other GE Relay manuals
Popular Relay manuals by other brands
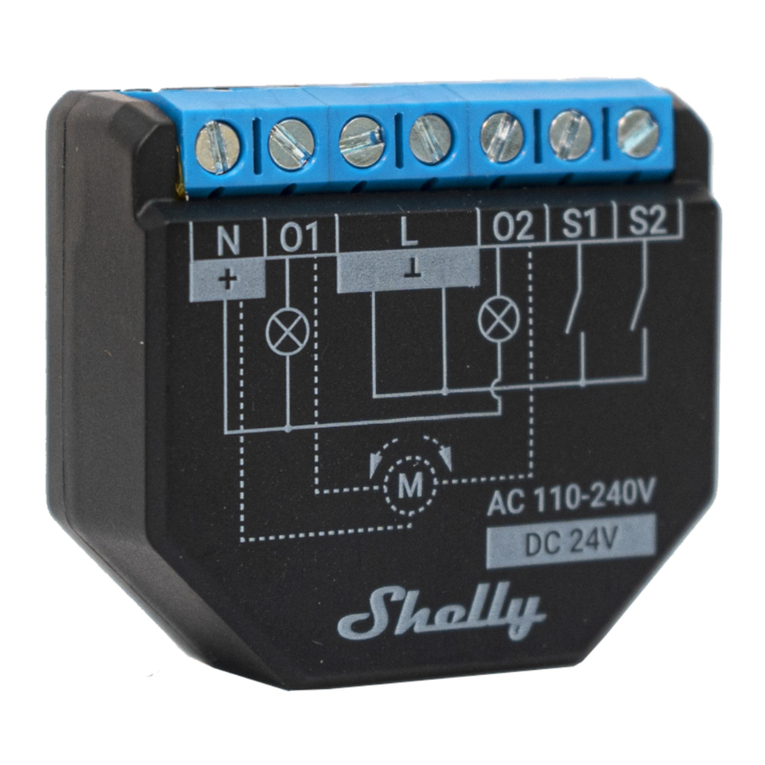
Shelly
Shelly Plus 2PM user manual
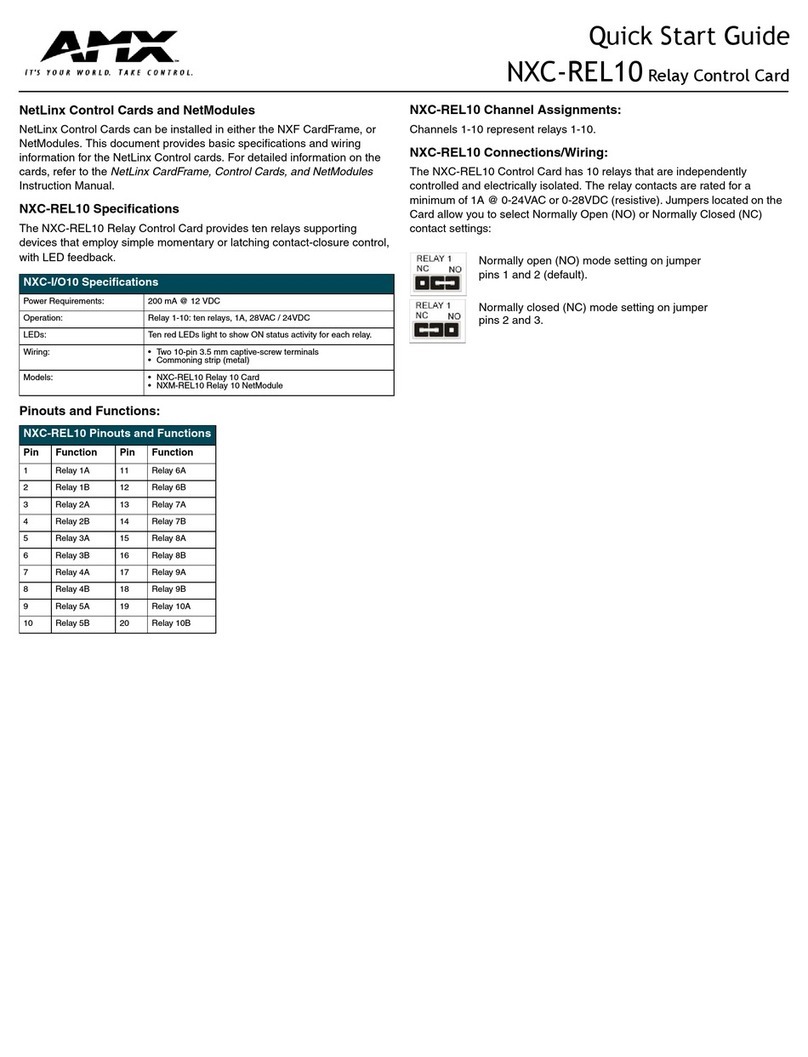
AMX
AMX netlinx NXC-REL10 quick start guide
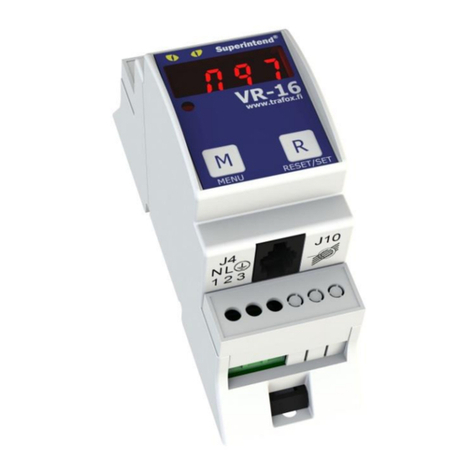
Muuntosahko
Muuntosahko Superintend Trafox VR-16 Short Operating Manual
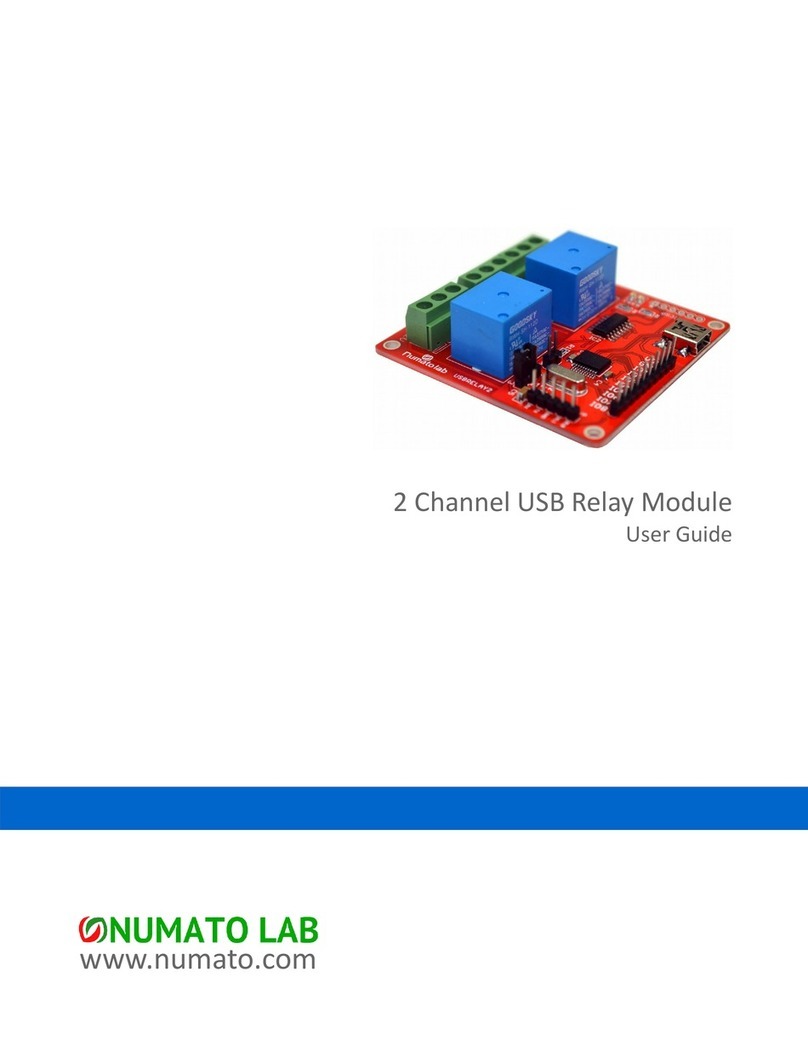
Numato
Numato 2 Channel USB Relay Module user guide
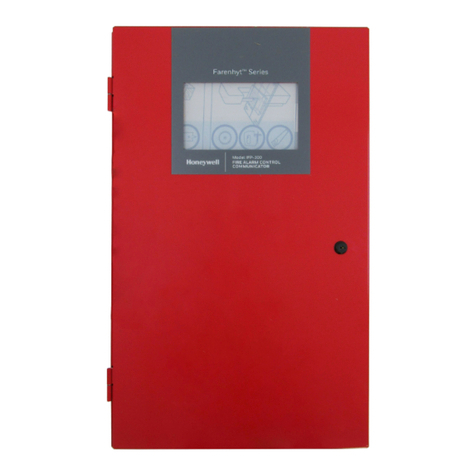
Honeywell
Honeywell Farenhyt Series Installation and maintenance instructions
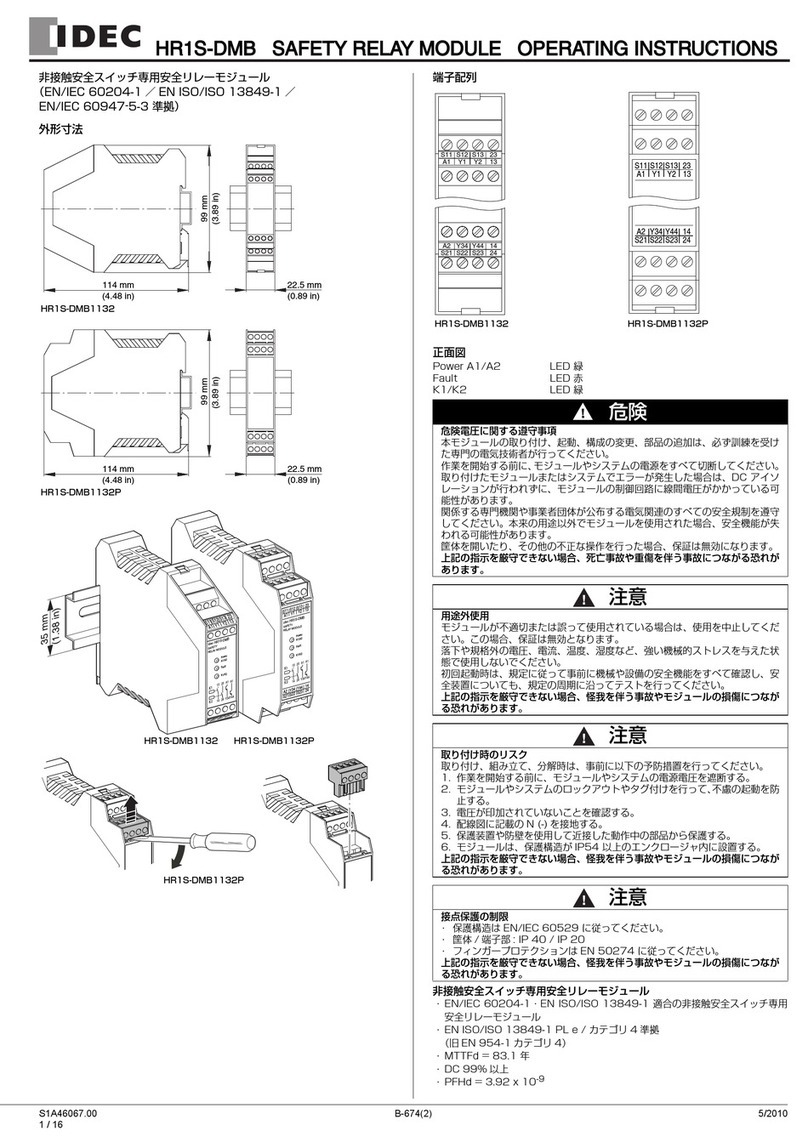
IDEC
IDEC HR1S-DMB Series operating instructions