HBM AD105D User manual

Operating Manual | Bedienungsanleitung
English Deutsch
AD105D

Hottinger Brüel & Kjaer GmbH
Im Tiefen See 45
D-64293 Darmstadt
Tel. +49 6151 803-0
Fax +49 6151 803-9100
www.hbm.com
Mat.:
DVS: A05569_01_X00_00 HBM: public
05.2021
EHottinger Baldwin Messtechnik
Subject to modifications.
All product descriptions are for general information only.
They are not to be understood as a guarantee of quality or
durability.
Änderungen vorbehalten.
Alle Angaben beschreiben unsere Produkte in allgemeiner
Form. Sie stellen keine Beschaffenheits- oder Haltbarkeits
garantie dar.

Operating Manual | Bedienungsanleitung
English Deutsch
AD105D

2A05569_01_X00_00 HBM: public AD105D
English
1 Safety Instructions 3........................................
2 Markings used 6............................................
3 Structure and mode of operation 7...........................
3.1 Structure of the electronics 8..................................
3.2 Signal conditioning 9.........................................
3.3 Adaptive interference suppression 10............................
3.4 Digital output 10..............................................
4 Mechanical installation 12....................................
5 Electrical connection 13......................................
5.1 Transducer connection 14.....................................
5.2 Bus connection 15............................................
6 Interfaces 16................................................
6.1 RS-485 2-wire interface 16.....................................
6.2 CANopen interface 17.........................................
7 Operation via software 20....................................
8 Waste disposal and environmental protection 20..............

Safety Instructions
AD105D A05569_01_X00_00 HBM: public 3
1 Safety Instructions
Intended use
The AD105D digital transducer electronics must only be used for measurement
tasks and directly related control tasks within the application limits detailed in
the specifications. Any other use is not the intended use.
Any person instructed to carry out installation, startup or operation of the de
vice must have read and understood the operating manual and in particular the
technical safety instructions.
In the interests of safety, the device should only be operated by qualified per
sonnel and as described in the Operating Manual.
The AD105D is not intended for use as a safety component. Please also refer
to the “Additional safety precautions” section. Proper and safe operation re
quires proper transportation, correct storage, siting and mounting, and careful
operation.
Operating conditions
SPlease observe the maximum permissible values stated in the specifica
tions for:
- Max. supply voltage
- Max. voltage for the input and output
- Max. current of the output
- Temperature limits
SYou must install the AD105D in an enclosed housing to meet the EMC
guidelines.
SThe safety requirements of EN61010 must be observed1.
SThe design or safety engineering of the device must not be modified without
our express consent. In particular, any repair or soldering work on compo
nents is prohibited.
1) Safety requirements for electrical measurement, control, regulatory, and laboratory equipment

Safety Instructions
4A05569_01_X00_00 HBM: public AD105D
Qualified personnel
Qualified persons are individuals entrusted with the installation, fitting, startup
and operation of the product and with the relevant qualifications for their work.
This includes people who meet at least one of the three following criteria:
SThey have knowledge of the safety equipment and procedures of measure
ment and automation systems, and are familiar with them as project per
sonnel.
SThey are operating personnel of measurement or automation systems and
have been instructed on how to handle the machinery. They are familiar
with the operation of the equipment and technologies described in this doc
ument.
SAs a commissioning or service engineer, they have successfully completed
training on the repair of automation plants. Moreover, they are authorized to
start up, ground and label circuits and equipment in accordance with safety
engineering standards.
Working safely
SThe device must not be directly connected to the power supply system. The
supply voltage must be between 7 and 30VDC.
SError messages should only be acknowledged once the cause of the error
has been eradicated and there is no further danger.
SAutomation equipment and devices must be designed to ensure adequate
protection or locking against inadvertent actuation (e.g. access control,
password protection, etc.).
SFor devices operating in networks, safety precautions must be taken in
terms of both hardware and software, so that an open circuit or other inter
ruptions to signal transmission do not result in undefined states or loss of
data in the automation device.
SFollowing work on settings or password-protected activities, make sure that
any controls that may be connected remain in a safe condition until the
switching behavior of the device has been tested.

Safety Instructions
AD105D A05569_01_X00_00 HBM: public 5
Additional safety precautions
Additional safety precautions may need to be taken in plants where malfunc
tions could cause major damage, loss of data or even personal injury.
The performance and scope of supply of the device cover only a small propor
tion of test and measuring equipment. Therefore, before starting up the device
in a plant, first perform a project planning and risk analysis, taking into account
all the safety aspects of measurement and automation engineering, so that
residual dangers are kept to a minimum. This particularly concerns personal
and machine protection. In the event of a fault, appropriate precautions must
produce safe operating conditions.
General dangers of failing to follow the safety instructions
This is a state-of-the-art device that is safe to operate. However, there may be
residual risks if the device is installed or operated incorrectly.

Markings used
6A05569_01_X00_00 HBM: public AD105D
2 Markings used
Icon Meaning
Note This marking draws your attention to a situation in
which failure to comply with safety requirements
could lead to property damage.
Important
This marking draws your attention to important
information about the product or about handling the
product.
Emphasis
See …
Italics are used to emphasize and highlight text and
identify references to sections of the manual,
diagrams, or external documents and files.

Structure and mode of operation
AD105D A05569_01_X00_00 HBM: public 7
3 Structure and mode of operation
The AD105D digital transducer electronics are part of the range of electronics
developed by HBM for static and dynamic weighing processes. They record
the measurement signals of connected sensors with strain gages. The trans
ducer electronics digitally condition the signals and deliver a fully-filtered,
scaled and digitized output signal for direct connection to bus systems or PCs
via the RS‐485 interface or CANopen. The transducer electronics can simply
and quickly be adjusted to the relevant system via various parameters.
The AD105D forms a unit with the transducer and cannot be replaced sepa
rately without recalibrating the system (SZA/SFA command). Loads cells or
force transducers, that are temperature compensated and for which the zero
value is set, can be used as transducers.
The PanelX software is available as a free download from the HBM website for
setting all the parameters in full, for realizing dynamic measurement signals,
and for frequency analysis of the dynamic system: www.hbm.com → Services
& Support → Downloads → Firmware & Software → PanelX.
Analog strain
gage transducer
AD105D with HBM command set Configuration/control system
PLC
Fig. 3.1 Digitizing analog transducer signals with AD105D
Special features
S4-wire connection of transducers in full bridge circuit, maximum measuring
range of ±2.4mV/V.
SSeparate calibration of transducer and application scaling.
SAutomatic zero tracking device (1d/s, ±2%) and zero adjustment upon acti
vation (±2% to ±20%).

Structure and mode of operation
8A05569_01_X00_00 HBM: public AD105D
SDigital filtering, adjustable speed of measurement output.
SLimit switch with hysteresis (open collector output).
Information
This part of the operating manual describes the hardware and the functions of
the transducer electronics. The communication commands and detailed config
uration instructions for various applications are included in the online documen
tation of the PanelX program.
3.1 Structure of the electronics
Voltage
control
Interface
I/O
Supply
voltage UB/GND
Interface
RS-485/CANopen
IO
EEPROM
Linearization
Serial number
Digital filter
Sample rate
Sensitivity
Zero value
μP
A
D
AD105D
Fig. 3.2 Block diagram
The analog transducer signal is first amplified, then analog filtered, and digi
tized in the A/D converter. This signal is processed in the microprocessor and
can be transmitted over the interface. All of the parameters can be stored
power failsafe way. The transducer electronics is adjusted ex works to a mea
suring range of 0 to 2mV/V.

Structure and mode of operation
AD105D A05569_01_X00_00 HBM: public 9
3.2 Signal conditioning
FMD
ASF ICR
SZA
SFA
NOV, RSN
LDW, LWT LIC TAV, TAS
Net
measured
value
Gross
measured
value
Digital
input
Digital
output
Sample
rate
Factory
calibration
Filter Tare
A
D
User-defined
scaling
Lineari-
zation
IN
OUT
TAR
ZTR, ZSE
Fig. 3.3 Signal conditioning
Digitization is followed by filtering, using digital filters adjusted by the software
(FMD, ASF). The ICR command changes the output rate (measured values
per second).
In the working standard calibration of the transducer electronics (as-delivered
condition), 0mV/V corresponds to zero and the maximum capacity is either
1,000,000digits (NOV≠0), or 5,120,000digits (NOV=0). The two parameters
LDW and LWT enable you to adapt the characteristic curve to your require
ments (scale curve) and you can use the NOV command to standardize the
measured values to the required scaling value (e.g. 3000d). Detailed informa
tion can be found in the command documentation in the Online Help for the
PanelX program.
You also have the opportunity to
Sswitch from gross to net signals,
Sactivate an automatic zero on start up function,
Sactivate an automatic zero tracking function,
Slinearize the input signal with a third order polynomial,
Sactivate various digital filters. Filters with cut-off frequencies below 1Hz,
fast-settling filters for dynamic measurements, notch filters, and mean value
filters are available.

Structure and mode of operation
10 A05569_01_X00_00 HBM: public AD105D
Read out the current measured value via MSV?. The format of the measured
value (ASCII or binary) is set with the COF command. You can also use the
COF command to activate the automatic measurement output. The measured
values are transmitted in the following format, depending on the COF com
mand:
Output format Input signal Output when NOV=0 Output when
NOV>0
Binary, 2 chars. (INT) 0 …maximum
capacity
0 …20,000 digits 0 …NOV
Binary, 4 chars. (LONG) 0 …maximum
capacity
0 …5,120,000 digits 0 …NOV
ASCII 0 …maximum
capacity
0 …1,000,000 digits 0 …NOV
3.3 Adaptive interference suppression
Regardless of the mode of operation, you can use the ADF command to acti
vate automatic interference suppression with adaptive filters. Interference fre
quencies are automatically found during the measurement and suppressed by
comb filters and averaging. The maximum filter settling time can be limited with
the TMA command.
3.4 Digital output
Use the digital output as a limit switch, for example. The gross or net value is
monitored depending on the parameters for the LIV command.
Gross or net value≥switching threshold: low output voltage (≤1V)
Gross or net value<switching threshold: high output voltage (≥6V)
You can also use the POR command if you deactivate the limit value function
(LIV1,0;):
POR0; Low output voltage (≤1V)
POR1; High output voltage (≥6V)
POR,0; LED OFF
POR,1; LED ON

Structure and mode of operation
AD105D A05569_01_X00_00 HBM: public 11
The voltages relate to the GND potential. The maximum power loss of the
switching transistor is 250mW. In the default settings, the LED function is ac
tive and indicates whether the power supply is present.

Mechanical installation
12 A05569_01_X00_00 HBM: public AD105D
4 Mechanical installation
You can install the AD105D in a transducer by mounting the motherboard on
the side of a transducer, for example. Ask HBK for a suitable shielding plate, if
necessary.
You must use a shielded housing and shielded cable if you do not mount the
AD105D within a closed (electrically conductive) transducer housing.
Notice
The AD105D is not protected against electrostatic discharges (ESD). Static
discharges can destroy the electronics.
Therefore ensure you have discharged any static charges before touching the
motherboard parts or connections.
Important
Before installing several transducer electronics modules in a plant with a bus
system, please note the following:
Before establishing a connection to the bus system, connect the transducer
electronics individually to a PC to set different addresses.
Dimensions
Dimensions in mm
41.7
2x ∅2.5
3.3
3.3
19.2
45
22.5
Height of motherboard
including equipment:
7mm

Electrical connection
AD105D A05569_01_X00_00 HBM: public 13
5 Electrical connection
Notice
The AD105D is not protected against electrostatic discharges (ESD). Static
discharges can destroy the electronics.
Therefore ensure you have discharged any static charges before touching the
motherboard parts or connections.
Housing
AD105D
Measurement signal -
Measurement signal +
Sense lead -
Bridge excitation voltage-
Bridge excitation voltage+
Sense lead +
Transducer
1
2
3
4
5
6
>300W
Sense leads are optional
Fig. 5.1 Connections to the solder tabs including indicated shielding
Connection to a bus system
Right connection in
Fig. 5.1
AD105D-RS4
(RS-485, 2-wire)
AD105D-CAN
(CAN bus)
1 GND GND
2 Ub: 7to30V Ub: 7to30V
3 T/RB CAN Low
4 T/RA CAN High
5Open collector output Open collector output
6Digital input Digital input

Electrical connection
14 A05569_01_X00_00 HBM: public AD105D
Important
The AD105D is an unshielded motherboard and is thus not EMC-tested. Either
install the electronics in a closed (electrically conductive) transducer housing or
in a separate EMC-tested housing.
Connect the transducer, AD105D housing, and cable shields to a joint ground
to realize effective shielding against electromagnetic interferences. The elec
tronics is protected against interferences with filters on the interfaces and exci
tation voltage.
5.1 Transducer connection
A 4-wire shielded cable is sufficient for connecting the transducer. If the trans
ducer has a 6-wire cable, the bridge excitation voltage and sense lead must be
connected as illustrated in Fig. 5.1. The connection should be as short as pos
sible. Depending on the bridge resistance of the transducer being used and the
length and cross-section of the transducer cable, there may be voltage drops
that can reduce the bridge excitation voltage. The voltage drop on the connec
tion cable is also dependent on the temperature (copper changes its resistance
with the temperature). The output signal of the transducer changes proportion
ally with the changing bridge excitation voltage. The 4-wire circuit used here
will result in measurement errors if temperatures fluctuate. This is caused by
the temperature-dependent cable resistance.
When establishing a measurement chain where the electronics are positioned
outside the transducer, ensure that the AD105D uses a rectangular carrier fre
quency for the bridge excitation. The cable length between AD105D and the
transducer should therefore be limited to max. 100cm. A max. length of 30cm
should not be exceeded for precision applications (≥3000d).

Electrical connection
AD105D A05569_01_X00_00 HBM: public 15
5.2 Bus connection
Important
Before installing several transducer electronics modules in a plant with a bus
system, please note the following:
Before establishing a connection to the bus system, connect the transducer
electronics individually to a PC to set different addresses.
The transducer electronics are supplied with an RS‐485 or CAN bus interface
(CANopen standard CiA DS301). The interface of the transducer electronics
relates to the GND, while the interfaces of the bus nodes must also relate to
the GND.
Use a shielded cable as the interface cable. The shield should always be con
nected to the ground potential at both ends.
Details of the procedure for setting up the transducer electronics and an expla
nation of the various settings, including for the interfaces, as well as the rele
vant commands, can be found in the online help of HBM's PanelX program,
which you can download free of charge from the HBM website: www.hbm.com
→ Services & Support → Downloads → Firmware & Software → PanelX.
For the interfaces, read the sections relating to your interface in the chapter
headed "Communication via one of the interfaces".

Interfaces
16 A05569_01_X00_00 HBM: public AD105D
6 Interfaces
6.1 RS-485 2-wire interface
You can either connect a single transducer electronics module via the RS-485
interface or, by configuring a bus system, connect up to 32 transducer elec
tronics modules to one RS-485 interface. In this, all the electronics modules
are connected in parallel on one line. The total length of the line may be up to
500 m. The software uses the different addresses to differentiate between the
transducer electronics modules. If the control computer only has an RS-232 or
USB interface, an interface converter is required.
T/RA
T/RB
Control computer Node 1 Node X
TxD RxD
TB TA
TR
RB RA
TxD RxD
TB TA
TR
RB RA
TxD RxD
TB TA
TR
RB RA
...
Fig. 6.1 Connection of several electronics to a PC via RS‐485
The interface signals T/RA and T/RB are switched in parallel for all AD105Ds
and the control computer. The transducer electronics already include the nec
essary bus termination resistors (termination resistor) that can be activated
with the STR software command. So no additional bus termination resistors
are needed on the electronics end. The ground reference for all of the interface
signals is based on the supply voltage ground (GND).
Address range
An address is necessary to be able to identify the nodes in the bus system un
ambiguously. The address may be between 0 and 89. The factory setting for
the address is 31. Set a different address with the ADR command.

Interfaces
AD105D A05569_01_X00_00 HBM: public 17
Baud rate
You can set baud rates from 9600 to 115,200baud with the BDR command.
The factory setting is 9600 baud.
Saving settings
To complete the settings, save all of the parameters to the non-volatile mem
ory of the transducer electronics with the TDD1 command.
6.2 CANopen interface
The CANopen interface operates according to the CiA DS301 standard (CAN
in Automation) - see also ISO 11898. Communication runs via two lines with
CAN HIGH and CAN LOW.
The level of all lines is relative to GND. The GND (0V) of the supply voltage
must therefore also be connected, but you must not connect GND to the
shield. Use a separate line to connect the digital ground of the nodes with the
GND (0V) of the power supply.
Important
You must connect bus termination resistors (each 120W) at the start and end
of the bus. The transducer electronics modules do not contain a bus termina
tion resistor for CANopen. You can only connect the resistors at the ends of
the bus system. If you are using more than two terminating resistors, or they
are not located at the ends, communication will be limited (bus errors) or will
not work at all.

Interfaces
18 A05569_01_X00_00 HBM: public AD105D
CAN H
CAN L
Control computer Node 1 Node X
...
120 W120 W
IN
OUT
IN
OUT
IN
OUT
Bus termination Bus termination
Fig. 6.2 CAN bus wiring
Use a cable with a characteristic impedance of approximately 120Ω, e.g. HBM
cable 1-KAB173.
Maximum cable length subject to bit rate
Bit rate in kBit/s 10 20 50 125 250 500 800 1000
Max. cable length
in m
5000 2500 1000 500 250 100 50 25
The maximum cable length is the total line length, calculated from the length of
all the stub lines for each bus node and the line length between the nodes. The
length of the stub lines per node is limited and depends on the bit rate being
used.
Bit rate
The bit rate factory setting is 125kBit/s. To change the bit rate use the PanelX
program or a configuration tool for CANopen. The transducer electronics sup
port the LSS protocol as defined by CiA DS305. So you can change the bit rate
and address with the PanelX program or a CANopen configuration tool. Gener
ally the change can only be made for one node. If necessary disconnect the
node from the bus system or deactivate the other nodes.
Table of contents
Languages:
Other HBM Control Unit manuals
Popular Control Unit manuals by other brands

Piratelogic
Piratelogic EVE Construction manual
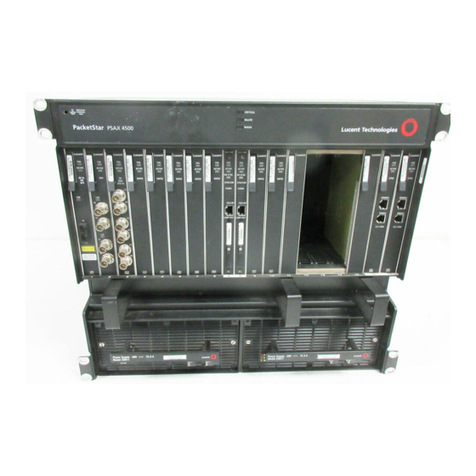
Lucent Technologies
Lucent Technologies PacketStar PSAX 1000 user guide

Parker
Parker DINCon II Installation, operating, & maintenance instructions
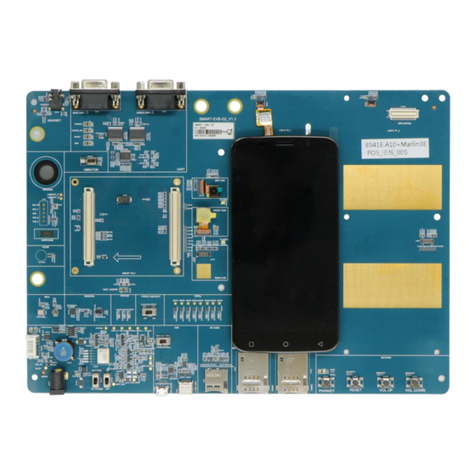
Quectel
Quectel Smart EVB G5 user guide
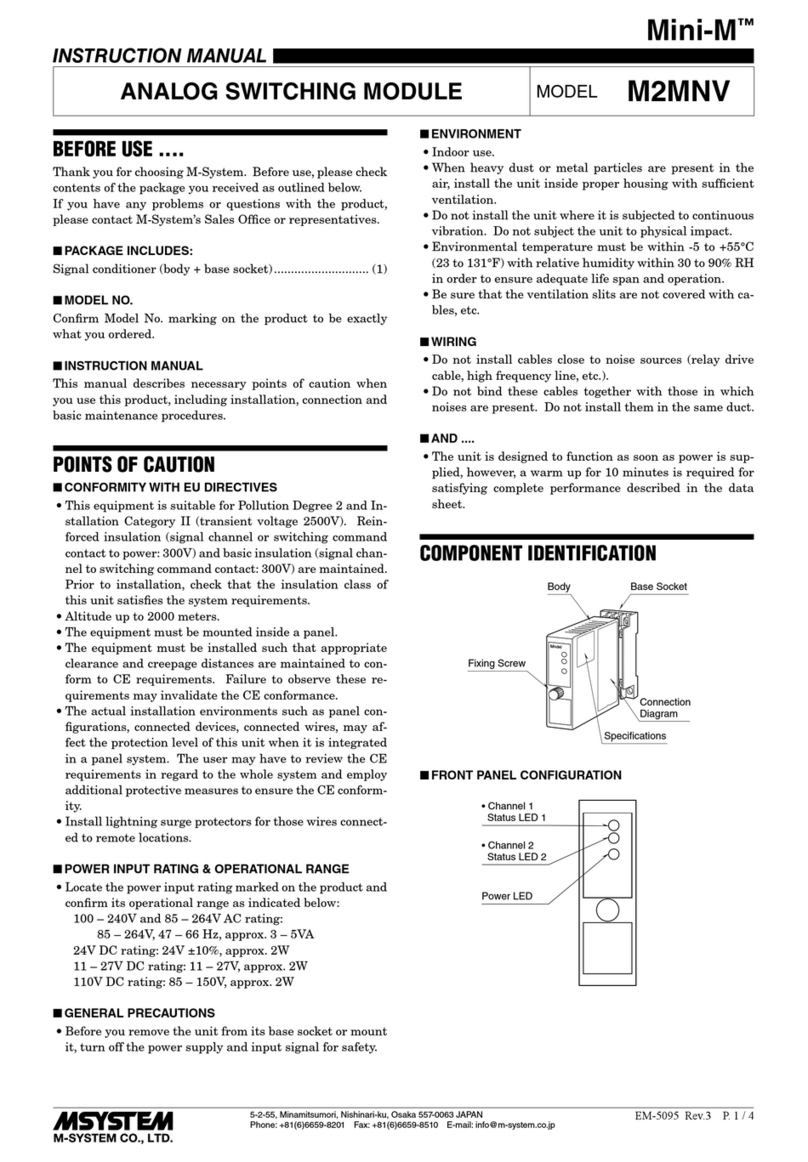
M-system
M-system Mini-M M2MNV instruction manual
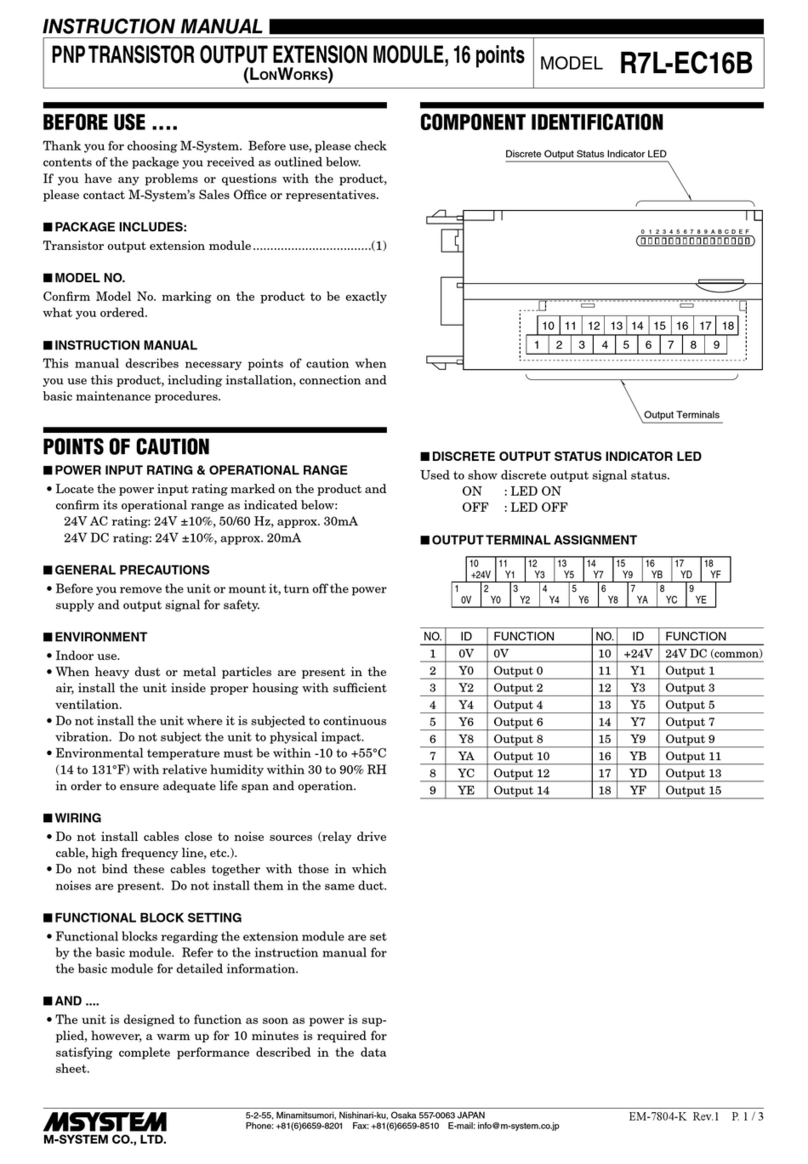
M-system
M-system R7L-EC16B instruction manual