Moog DS2020 Installation manual

THISDOCUMENTDESCRIBESTHE INSTALLATION
ANDSTARTUP FOR THE DS2020 SYSTEM
INSTALLATIONANDSTARTUP
SINGLE AXIS DIGITAL
SERVO SYSTEM
DS2020 TECHNOLOGY
www.moog.com
PN: L-MAS2-E-221, Rev. April 2022

PN: L-MAS2-E-221, Rev. April 2022
Page 2 of 171

Table Of Contents
Table Of Contents 3
List of Figures 9
Foreword 10
About Moog 10
Document Version 10
Revision Record 10
Reader Instructions 11
1 Introduction 13
1.1 Contents 14
1.2 Related Documents 14
1.3 Package Contents 14
1.4 Required Qualifications of Personnel 15
1.5 Applicable Laws 15
1.6 Getting Started 16
2 Safety Information 17
2.1 Safety and Usage Guidelines 18
2.2 Qualified Personnel 18
2.3 Electrical Hazards 19
2.3.1 Voltage Arcs and High Voltage 19
2.3.2 General Hazards and Safeguards 20
2.4 Thermal Hazards 20
2.5 Mechanical Hazards 20
2.6 STO Safety Feature 21
2.6.1 Description 21
2.6.2 Directives on Safety 21
2.7 Safe Use of the DS2020 System 22
2.7.1 Risk Assessment 22
2.7.2 Electrical Connections 22
2.7.3 Motor Selection 22
2.7.4 Power Supply 22
2.7.5 Prohibited Use 23
Moog Casella DS2020 Installation and Startup Guide Table Of Contents
PN: L-MAS2-E-221, Rev. April 2022
Page 3 of 171

2.8 Risk Assessment 24
2.8.1 Installation Risk Assessment 24
2.8.2 General Machine/System Safeguards Information 25
2.8.3 Safeguards Related to SCRF 25
3 System Overview 27
3.1 Product Structure 28
3.1.1 Product Description 28
3.1.2 Storage and Working Conditions 30
3.1.3 DS2020 Standard Models 31
3.1.4 Model Codes 32
3.1.5 Connector Kits 33
3.2 Features and Component Details 34
3.2.1 Electrical Data 34
3.2.2 Mechanical Data 34
3.2.3 Transducers 38
3.2.4 Connectors 39
3.2.4.1 Connector Layout 41
3.2.5 Power Line Filters 50
3.2.6 Braking Resistor 52
3.2.7 Line Inductors 53
3.3 Motors 53
3.3.1 Selecting a Moog Motor 53
3.3.2 Selecting a Non-Moog Motor 53
3.4 Cables 54
4 Certifications 57
4.1 CE Certificate 58
4.2 Safe Torque Off (STO) 60
4.3 Certification Compliant System Installation Requirements 63
4.3.1 Environmental Ratings 63
4.3.2 Short Circuit Protection 64
4.3.3 Primary Circuit Overvoltage Protection 65
4.3.4 Dynamic Brake Unit Ratings 66
5 Electrical and Mechanical Installation 67
5.1 Tools and Equipment 69
5.1.1 Tools 69
5.1.2 Electronic Equipment 69
Moog Casella DS2020 Installation and Startup Guide Table Of Contents
PN: L-MAS2-E-221, Rev. April 2022
Page 4 of 171

5.2 Mechanical Installation 69
5.2.1 Assembly of System Components 69
5.2.1.1 Drive Installation 69
5.2.1.2 Power Line Filter Installation 69
5.2.1.3 Braking Resistor Positioning 70
5.3 Electrical Installation and Thermal Rating 71
5.3.1 Safety and General Instructions 71
5.3.2 Electrical Installation 72
5.3.3 Thermal Rating of the Electrical Panel 74
5.3.3.1 Drive Axis Power Dissipation 75
5.3.3.2 Thermal Dissipation of Accessories 75
5.3.4 Control Power Requirements 76
5.3.5 ACMains Power/Ground Connection 77
5.3.5.1 Types of Earthing (Grounding) Systems 77
5.3.5.2 Protection Components 78
5.3.5.3 Ground Connection 79
5.3.5.4 Ground Stud 79
5.3.6 Drive Wiring 81
5.3.6.1 Grounding 81
5.3.6.2 Power Cord Connection 81
5.3.6.3 Braking Resistor Connection 83
5.3.6.4 Control Power Connection 83
5.3.6.5 Signal Connection 84
5.3.6.6 Motor Cable Connection Details 84
5.3.6.7 Brake Cable Connection 85
5.3.6.8 I/O Signal Connection 87
5.3.6.9 STO Signals Connection 87
5.3.6.10 Transducer Connection 89
5.3.6.11 Connecting the Fieldbus - X8, X9, X10 Connectors 90
6 Commissioning with Dx2020 Software 91
6.1 Safety 93
6.2 Dx2020 GUI 94
6.2.1 Overview 94
6.2.2 Minimum PCRequirements 94
6.2.3 Dx2020 GUI Installation 95
6.2.4 GUI Drive Connection 96
6.2.5 Layout 98
Moog Casella DS2020 Installation and Startup Guide Table Of Contents
PN: L-MAS2-E-221, Rev. April 2022
Page 5 of 171

6.2.6 Firmware Update (BootLoader) 100
6.2.7 Accessing the Dx2020 GUI online help 101
6.3 Activate Power 101
6.4 System Configuration 102
6.4.1 Axis Identification 102
6.4.2 Motor Parameter Configuration 102
6.4.3 Transducer Configuration 104
6.4.3.1 Sensorless 105
6.4.4 I/O Configuration 106
6.4.4.1 Details of Possible Configurations 107
6.4.4.2 Programming Analog and Digital I/O Connector X5 108
6.4.5 Control Loops Configuration 109
6.4.5.1 Control mode configuration 109
6.4.5.2 Torque loop parameter configuration 110
6.4.5.3 Speed loop parameter configuration 110
Filter configuration 111
6.4.5.4 Configuration of the position loop parameters 113
6.4.6 Fault Configuration 114
6.4.7 Application Parameters Configuration 115
6.4.8 Commands and Modes Configuration 116
119
122
122
124
DS2020 State Machine
6.5 STOActivation
6.6 Auto-Phasing Procedure
6.7 Drive (Axis) Enable and Limit Switch Enable/Disable
6.8 Oscilloscope Function and Log File (.UCX) 125
6.8.1 Log Configuration 125
6.8.2 Start Logging 125
6.8.3 View Logs 126
6.8.4 UCX File Management 127
6.9 Using the GUI in Offline Mode 128
6.10 Contextual Help For Parameter Management 129
6.11 Decommissioning Procedure 130
7 Shipment and Storage 132
7.1 Receiving and Checking the Shipment 132
7.2 Storage 132
7.2.1 Regenerating the Electrolytic Capacitors after Storage 132
Moog Casella DS2020 Installation and Startup Guide Table Of Contents
PN: L-MAS2-E-221, Rev. April 2022
Page 6 of 171

8 Maintenance 133
8.1 Periodic Maintenance 133
8.2 What to Do If Repairs Are Required? 134
9 Troubleshooting 135
9.1 Power Section Anomalies 135
9.2 Drive Alarms (Faults) 135
9.2.1 Alarms on the Power Section 136
9.2.2 Alarm for VBUS Voltage Out of Tolerance 137
9.2.3 Drive or Motor Overtemperature 137
9.2.4 Removal of STO Signal 138
9.2.5 Errors on Memory Devices 138
9.2.6 Data Corrupted Fault 138
9.2.7 Brake Feedback Fault 139
9.2.8 Errors on Feedback Devices 139
9.2.9 Synchronization , Interrupt Time and Task Time Error 141
9.2.10 EtherCAT Fault 141
9.2.11 Alarms Related to the Control Loops 141
9.2.12 CAN Bus Alarms 141
9.3 Alarm Display in Analog Operating Mode 142
9.4 Faults During the GUI – Drive Connection 146
10 Safe Torque Off Safety Function 148
10.1 Application 149
10.2 Installation Risk Assessment 149
10.3 Safe Torque Off Function 149
10.3.1 Characteristic Values According to UNI EN ISO 13849-1 150
10.3.2 Characteristic Values According to CEI EN 62061 151
10.4 Safety Requirements 151
10.4.1 Full Stop 151
10.5 Safe Torque Off Circuit 153
10.6 Safe Torque Off Connections 154
10.6.1 Connector X6 – JRC1 154
10.6.2 Electrical Input/Output Specifications 155
10.7 Example Application 156
10.7.1 Description 156
10.7.2 Example Requirements 157
10.8 Safe Torque Off Installation and Maintenance Procedure 158
Moog Casella DS2020 Installation and Startup Guide Table Of Contents
PN: L-MAS2-E-221, Rev. April 2022
Page 7 of 171

10.9 Assembly and Serial Tests 159
10.10 Identification of the STO Function on the Drive Plate 159
11 System Disposition 160
11.1 What to Do If Repairs Are Required? 160
12 Ordering Code 161
12.1 DS2020 Ordering Code 161
12.2 Moog Motor Ordering Code 161
13 Appendix 162
13.1 Example I/OConnections on X5 163
13.2 Example RS-485 Driver on X4 164
13.1 Glossary 165
13.2 Metric/AWG Conversion Table 169
Moog Casella DS2020 Installation and Startup Guide Table Of Contents
PN: L-MAS2-E-221, Rev. April 2022
Page 8 of 171

List of Figures
Figure 1: DS2020 Front View.................................................................................................................................................28
Figure 2: DS2020 System Theory of Operation Flow Chart.......................................................................................29
Figure 3: Example Drive Plate................................................................................................................................................31
Figure 4: Drive Model Codes..................................................................................................................................................32
Figure 5: Drive Chassis Dimensions (L50 and L75).......................................................................................................32
Figure 6: Drive Chassis Dimensions (L85 and L125)....................................................................................................36
Figure 7: Drive Chassis Dimensions (L165 and L355).................................................................................................37
Figure 8: Drive Front Panel and Bottom Connectors...................................................................................................39
Figure 9: Top and Bottom Connectors L355...................................................................................................................40
Figure 10: CE Declaration of Conformity.........................................................................................................................40
Figure 11: CE "Safe Torque Off" Certificate of Conformity......................................................................................59
Figure 12: EC-Type Examination Certificate..................................................................................................................62
Figure 13: External Braking Resistor (with brackets).................................................................................................70
Figure 14: Structure of the Electrical Panel with the Components of a Servo System..................................72
Figure 15: Connection Cables EMC Bracket on size 50 mm......................................................................................74
Figure 16: Location of the Ground Stud (M5).................................................................................................................79
Figure 17: Location of the Ground Connector size L355...........................................................................................80
Figure 18: Connector X11 – [W1-V1-U1] sizes L50 and L75.....................................................................................81
Figure 19: Connector – [W1-V1-U1] sizes L355............................................................................................................82
Figure 20: Connector X11 – [RRe – RRi - RR] size L50 and L75...............................................................................83
Figure 21: Connector X11 – [RRe-RRi-RR] sizes L85 L125 L165...........................................................................83
Figure 22: Connector [DC- RR DC+] sizes L355.............................................................................................................83
Figure 23: Connector X11 – [W2-V2-U2- ] Sizes L50 and L75................................................................................84
Figure 24: Connector X12– [W2-V2-U2- ] Sizes L85 and L125..............................................................................84
Figure 25: Connector [W2-V2-U2- ] Sizes L355...........................................................................................................84
Figure 26: Brake Activation Timing Diagram.................................................................................................................86
Figure 27: Detail of the Feedback Contact Circuit......................................................................................................88
Figure 28 : DS2020 Drive State Machine.....................................................................................................................120
Figure 29: Movable Connector Pinout: 6 Contacts, Model B2 3.50 / 06/180 SN BK BX Weidmuller....154
Figure 30: Example of Safe Torque Off After a Controlled Stop........................................................................156
Figure 31: STO Mandatory Sequence Circuit Test...................................................................................................159
Figure 32: Example I/O
Connections on the X5 Connector...................................................................................163
Figure 33: Example RS-485 Driver Using the SN75176 IC........................................................................................164
Moog Casella DS2020 Installation and Startup Guide List of Figures
PN: L-MAS2-E-221, Rev. April 2022
Page 9 of 171

Foreword
The DS2020 drives meet the Low Voltage Directive (2014/35/EU) and EMC Directive (2014/30/EU).
The safety function "Safe Torque Off" (STO) integrated in the drive complies with the Machinery
Directive (2006/42 / EC).
To comply with the European Directives, the drive meets the requirements of the relevant harmonized
installation standards EN 50178 (LVD), EN61800-3 (EMC) and EN 61800-5-2 (Safety of machinery).
The DS2020 drives are CE certified; certain models are also ULcertified. Contact Moog for details.
The manual was written and checked by technical experts at Moog.
About Moog
The Moog Industrial Group designs and manufactures high performance motion control solutions
combining electric, hydraulic, and hybrid technologies with expert consultative support in a range of
applications including test, simulation, plastics, metal forming, and power generation.
Customers of Moog include leading automotive manufacturers, aerospace manufacturers, testing labs
and global automotive racing teams.
We help performance-driven companies design and develop their next-generation machines.
The Moog Industrial Group is part of Moog Inc.
Info Description
Moog Company Moog Italiana Srl
Address Via Avosso, 94, Casella (GE) 16015
Phone Tel: +39 010 96711
Fax Fax: +39 010 9671280
E-Mail info.casella@moog.com
Web Site www.moog.it
Document Version
The following table shows the version of this document and all other possible versions:
ES DA DE EL EN FR IT NL PT FL SV CS ET LV HU MT PL SK SL BG RO GA
X
The language of documents and drawings are subject to contractual negotiations with the Customer.
In case of "Translation of the Original Instructions", the manufacturer of the machinery must also
supply the "Original Instructions".
Revision Record
The following table shows the revision record:
Moog Casella DS2020 Installation and Startup Guide Foreword
PN: L-MAS2-E-221, Rev. April 2022
Page 10 of 171

Revision Description Date
A First release January 2020
Reader Instructions
The following table shows the symbols adopted in Moog documents:
DANGER
DANGER indicates a hazardous situation which, if not avoided, will result in death or serious
injury.
WARNING
WARNING indicates a hazardous situation which, if not avoided, could result in death or serious
injury.
CAUTION
CAUTION indicates a hazardous situation which, if not avoided, could result in minor or moderate
injury.
The following table shows the structure of a warning:
SIGNAL WORD
Type and source of hazard
Possible consequences of not avoiding the potential hazard
ØHow to avoid the hazardous situation
The following table shows other typographic elements:
Symbol Explanation
Electrical hazard alert symbol.
Moog Casella DS2020 Installation and Startup Guide Reader Instructions
NOTICE
NOTE indicates possible property damage.
Aa2 Second release February 2022
PN: L-MAS2-E-221, Rev. April 2022
Page 11 of 171

Symbol Explanation
Thermal hazard alert symbol.
Mechanical hazard alert symbol.
General hazard alert symbol.
Notes about important operations and other useful information.
ØThis is an action to be carried out.
●/ - This is a bullet list.
1., 2., ... These are steps in a procedure that must be performed in consecutive order.
Moog Casella DS2020 Installation and Startup Guide Reader Instructions
PN: L-MAS2-E-221, Rev. April 2022
Page 12 of 171

1 Introduction
This chapter provides introductory information about this guide and the DS2020 system.
1.1 Contents 14
1.2 Related Documents 14
1.3 Package Contents 14
1.4 Required Qualifications of Personnel 15
1.5 Applicable Laws 15
1.6 Getting Started 16
Moog Casella DS2020 Installation and Startup Guide 1 Introduction
PN: L-MAS2-E-221, Rev. April 2022
Page 13 of 171

1.1 Contents
The
DS2020 Installation and Startup Guide
, the document you are currently reading, provides
information to ensure proper installation and startup of the DS2020 series digital servo drive system.
See the Table Of Contents on page 3 for a list of all the topics covered in this guide.
All information contained herein, including methods, techniques and concepts are the exclusive
property of Moog and may be neither copied nor used without specific authorization. Moog reserves
the right to modify products, and related documentation, at any time, without notice.
1.2 Related Documents
The following related documents are also available:
lDS2020
Safety
Guide
(shipped in the box with the DS2020 and also available on the Moog
website)
lMoog motor installation guides (available on the Moog website)
lMoog motor installation drawing - provides information on motor mounting and wiring
schematics for electrical installation (shipped in the box with the motor)
lDx2020 GUI online help (available within the Dx2020 software)
1.3 Package Contents
The complete DS2020 system includes:
lOne DS2020 drive
lAnchoring support for the shields
lInterconnect cables
An optional connector kit must be ordered individually and is supplied separately.
Moog Casella DS2020 Installation and Startup Guide 1.1 Contents
PN: L-MAS2-E-221, Rev. April 2022
Page 14 of 171

1.4 Required Qualifications of Personnel
WARNING
WARNING:Personal injury and property damage risk.
Failure to follow all safety precautions when the drive is installed, operated or
maintained may pose a risk of death or serious injury to personnel, or serious
damage to property.
ØThe system builder and end-use company are required to ensure that the
safety instructions detailed in this manual and in the DS2020
Safety Guide
are
available to, read, understood and observed by all personnel responsible for
the installation, operation and maintenance of the DS2020 system.
In addition to the following information, also follow the instructions in Safety and Usage Guidelines on
page 18.
This manual and the equipment described in it are intended only for qualified personnel who have
proper training and expertise in the following:
lTransport: All personnel must have knowledge and experience handling components that are
sensitive to mechanical shock and electrostatic discharge (ESD).
lUnpacking: All personnel must have knowledge and experience handling components that are
sensitive to mechanical shock and electrostatic discharge (ESD).
lInstallation and Maintenance: All personnel must have extensive technical knowledge and
experience with the installation and maintenance of AC- and DC-poweredelectrical and electro-
mechanical equipment.
lStartup: All personnel must have extensive technical knowledge and experience with electrical
drives, motors and their technology.
The qualified personnel must know and observe the following standards: IEC 60364, IEC 60664, and
all relevant national accident prevention regulations.
1.5 Applicable Laws
The DS2020 drives meet the Low Voltage Directive (2014/35/EU) and EMC Directive (2014/30/EU).
The safety function "Safe Torque Off" (STO) integrated in the drive complies with the Machinery
Directive (2006/42 / EC).
To comply with the European Directives, the drive meets the requirements of the relevant harmonized
installation standards EN 50178 (LVD), EN61800-3 (EMC) and EN 61800-5-2 (Safety of machinery).
The DS2020 drives are CE certified; certain models are also ULcertified. Contact Moog for details.
Moog Casella DS2020 Installation and Startup Guide 1.4 Required Qualifications of Personnel
PN: L-MAS2-E-221, Rev. April 2022
Page 15 of 171

1.6 Getting Started
The process for getting the DS2020 system installed, configured and operational looks like this:
1. Read this guide.
2. Read the related documents that are supplied with the DS2020 system, see Related Documents
on page 14.
3. Install the DS2020 drive, see Mechanical Installation on page 69.
4. Install the supplied Moog motor, see the motor installation guide for your motor.
5. Install the cables and connect power, see Electrical Installation and Thermal Rating on page 71.
6. Provide a PC in the work area for the Dx2020 software.
7. Commission the system with the Dx2020 software, see Commissioning with Dx2020 Software
on page 91.
Moog Casella DS2020 Installation and Startup Guide 1.6 Getting Started
PN: L-MAS2-E-221, Rev. April 2022
Page 16 of 171

2 Safety Information
This chapter provides safety information for the DS2020 system.
2.1 Safety and Usage Guidelines 18
2.2 Qualified Personnel 18
2.3 Electrical Hazards 19
2.3.1 Voltage Arcs and High Voltage 19
2.3.2 General Hazards and Safeguards 20
2.4 Thermal Hazards 20
2.5 Mechanical Hazards 20
2.6 STO Safety Feature 21
2.6.1 Description 21
2.6.2 Directives on Safety 21
2.7 Safe Use of the DS2020 System 22
2.7.1 Risk Assessment 22
2.7.2 Electrical Connections 22
2.7.3 Motor Selection 22
2.7.4 Power Supply 22
2.7.5 Prohibited Use 23
2.8 Risk Assessment 24
2.8.1 Installation Risk Assessment 24
2.8.2 General Machine/System Safeguards Information 25
2.8.3 Safeguards Related to SCRF 25
Moog Casella DS2020 Installation and Startup Guide 2 Safety Information
PN: L-MAS2-E-221, Rev. April 2022
Page 17 of 171

2.1 Safety and Usage Guidelines
Do not attempt to install, operate, maintain or inspect the DS2020 system until you have carefully
read this guide and the other supplied documents, and you are properly trained in the correct use of
the equipment. The DS2020 system may only be set up and operated in conjunction with this manual
and the supplied documentation.
SAFETY
FIRST
Human safety and equipment safety must be the first considerations when per-
forming the installation, operation or maintenance procedures for the drive system.
When it comes to electronics in your factory or workplace, you want to make sure
both your facility and its employees are safe. The following gives safety instructions
that must be followed when you are working on the DS2020 system.
WARNING
WARNING:Risk of death or serious injury to personnel or damage to equipment.
Failure to follow the safety and usage guidelines in this chapter can result in
death or serious injury to personnel, or damage to equipment.
ØIn addition to the
DS2020 Installation and Startup Guide
(the guide you are cur-
rently reading), you must read the guides listed in Related Documents on page
14.
ØObserve and adhere to the technical data and, in particular, the information given on the
system component nameplates.
ØThe installation must comply with the local regulations and use of equipment and
installation practices that promote electromagnetic compatibility and safety.
ØSafety equipment - To protect yourself against personal injury, always wear suitable safety
equipment, such as safety glasses, work shoes, and other safety equipment required by the
operation.
2.2 Qualified Personnel
WARNING
WARNING:Risk of death or serious injury to personnel or damage to equipment.
Only qualified, properly trained and certified personnel are permitted to operate
and interact with the system.
This manual and the equipment described in it are intended only for qualified personnel who have
proper training and expertise.
Qualified personnel are those who are specialized with required knowledge and experience, who have
been trained to perform such work and are authorized to commission, systems and circuits in
accordance with established safety practices and standards. The qualified personnel must know and
observe the following standards and regulations:
Moog Casella DS2020 Installation and Startup Guide 2.1 Safety and Usage Guidelines
PN: L-MAS2-E-221, Rev. April 2022
Page 18 of 171

lIEC 60364
lIEC 60664
lAccident prevention national, regional and local regulations for the site where the system or
machine will be operated
2.3 Electrical Hazards
WARNING
WARNING:Electrical hazard.
High voltage may be present, which can result in death or serious injury to
personnel, or damage to equipment.
ØFollow these safety instructions.
Certain electrical systems have to be maintained and cleaned by staff. Before they can be accessed,
the systems have to be disconnected from the mains supply to eliminate electrical hazards to
operating staff. According to the state of technology, this is accomplished with the five safety rules of
DIN VDE 0105-100.
1. Disconnect the mains.
2. Secure against reconnection.
3. Verify that the system is dead.
4. Carry out earthing and short circuiting.
5. Provide protection from adjacent live parts.
2.3.1 Voltage Arcs and High Voltage
Voltage arcs may occur and/or high voltage may be present that can fatally or seriously harm
personnel or damage equipment. Additionally, the drive's capacitors can have dangerous voltages
present up to eight minutes after the removal of the mains voltage.
lNever attempt to remove safety covers, or loosen or disconnect the electrical connections when
the DS2020 system is powered up,
lNever attempt to perform any cleaning or maintenance operations when the DS2020 system is
powered up.
lAlways ensure that the mains power supply is disconnected and locked out before attempting
any work on the system.
lAlways wait at least eight minutes after disconnecting and locking out the AC mains power
before attempting to work on the DS2020 system equipment. The DS2020 capacitors can still
have dangerous voltages present up to eight minutes after power is switched off.
lAlways measure the voltage of the direct current circuit (BUS) and wait until the voltage drops
below 40V.
lAlways measure the voltage of any other contact point(s) to ensure the power is off and there is
no voltage present.
Moog Casella DS2020 Installation and Startup Guide 2.3 Electrical Hazards
PN: L-MAS2-E-221, Rev. April 2022
Page 19 of 171

lNever attempt to remove safety covers, or loosen or disconnect the electrical connections when
the DS2020 system is powered up,
lNever attempt to perform any cleaning or maintenance operations when the DS2020 system is
powered up.
2.3.2 General Hazards and Safeguards
The power from the drive to the motor can be removed in "a safe manner". In this way, when the safe
power stage is disabled, the motor is not able to produce torque.
During normal operation, the equipment should not be accessible (i.e., protected as described in the
Risk Assessment by covers, guards, barriers, and safety interlocked gates/doors, etc.), all
covers/guards must be installed, and cabinet doors must be kept closed/locked.
During the operation of the drives, there may be uncovered live parts in the control cabinet
installation, depending on the degree of mechanical protection required by regulations governing the
site where the equipment is operated.
At the drive and/or motor, the power and control connections may be live, even when the motor is
stopped.
2.4 Thermal Hazards
CAUTION
CAUTION:Burn hazard.
The surface temperature of the drive may reach a temperature of 80 °C, and the
motor may reach up to 100 °C (212 °F), and may become very hot in operation,
according to their protection category.
ØDo not touch hot surfaces, measure the temperature, and wait until the drive
and motor has cooled down below 40 °C (104 °F) before touching it.
ØIt is recommended to always wear gloves when attempting to handle DS2020
system components that have been recently operating.
2.5 Mechanical Hazards
WARNING
WARNING:Mechanical hazard.
Large motors can generate very high torque and impact or trapping hazards, which
can result in death or serious injury to personnel, or damage to equipment.
ØFollow these safety instructions.
The motor must be properly mounted and anchored as specified in the Moog motor installation guide
supplied with the DS2020 system motor. For details, consult the Moog motor installation guide.
Moog Casella DS2020 Installation and Startup Guide 2.3.2 General Hazards and Safeguards
PN: L-MAS2-E-221, Rev. April 2022
Page 20 of 171
Other manuals for DS2020
1
Table of contents
Other Moog Servo Drive manuals
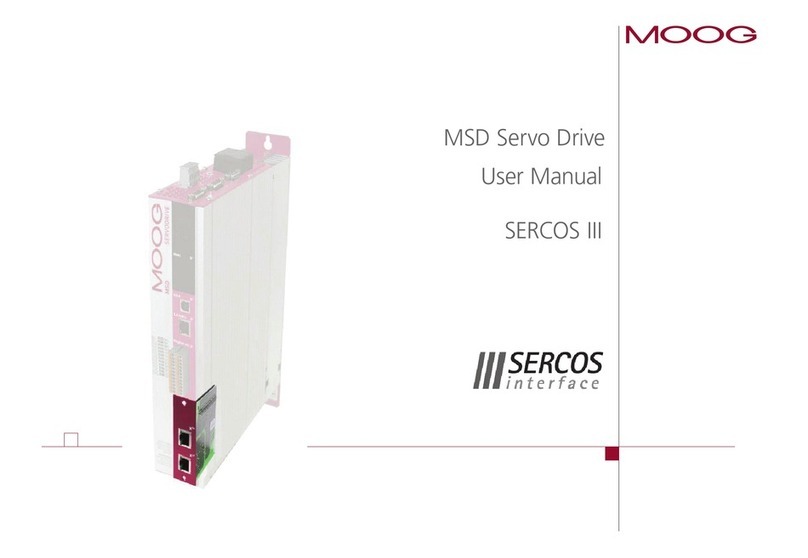
Moog
Moog MSD User manual
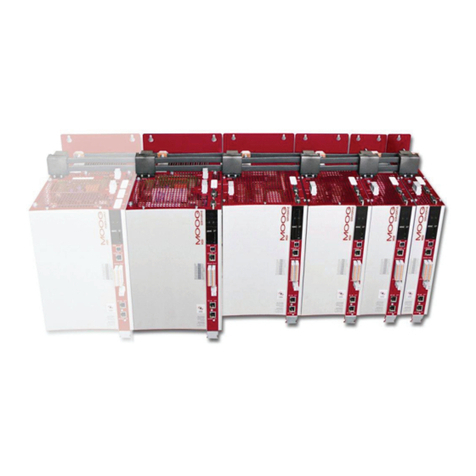
Moog
Moog MSD G393-004 User manual
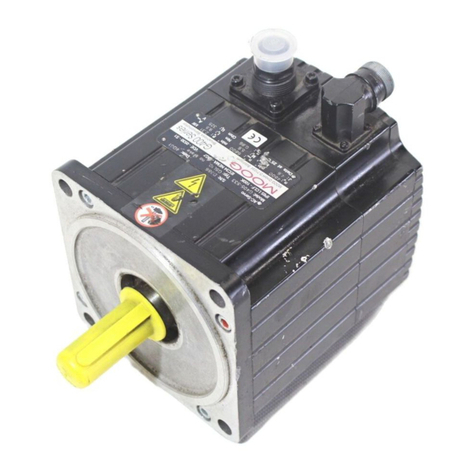
Moog
Moog G400 Series User manual
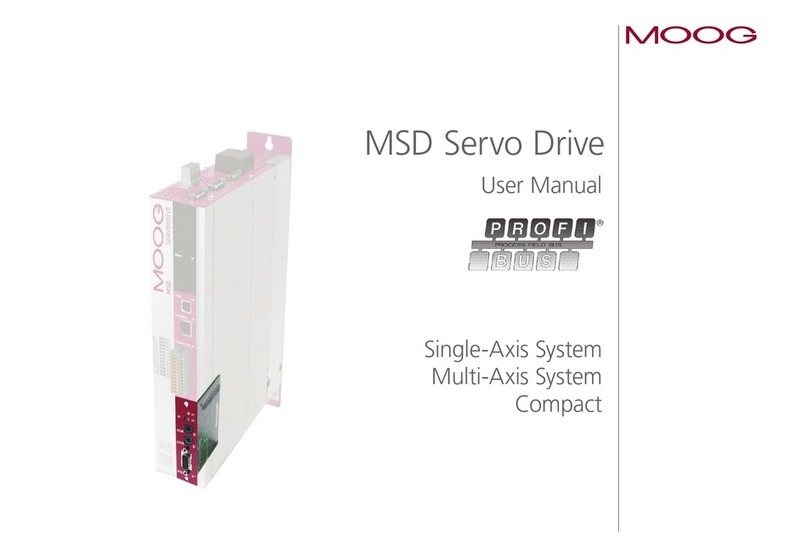
Moog
Moog MSD User manual
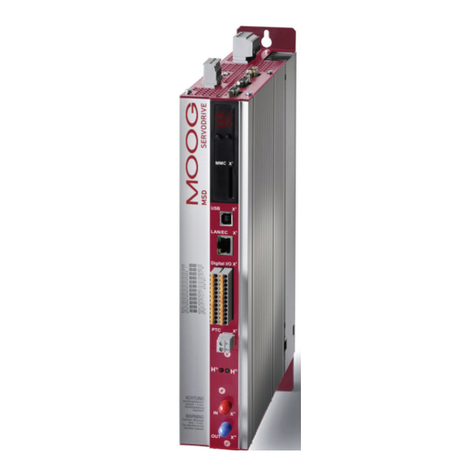
Moog
Moog G392-004 User manual
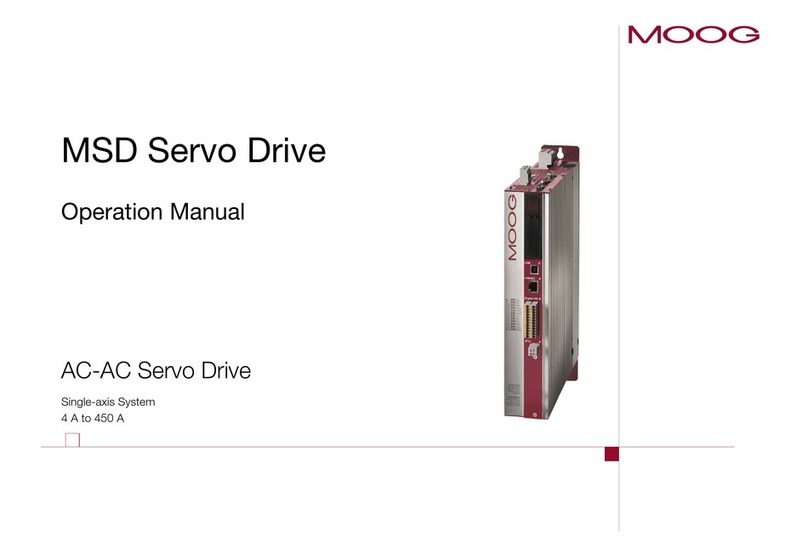
Moog
Moog MSD User manual
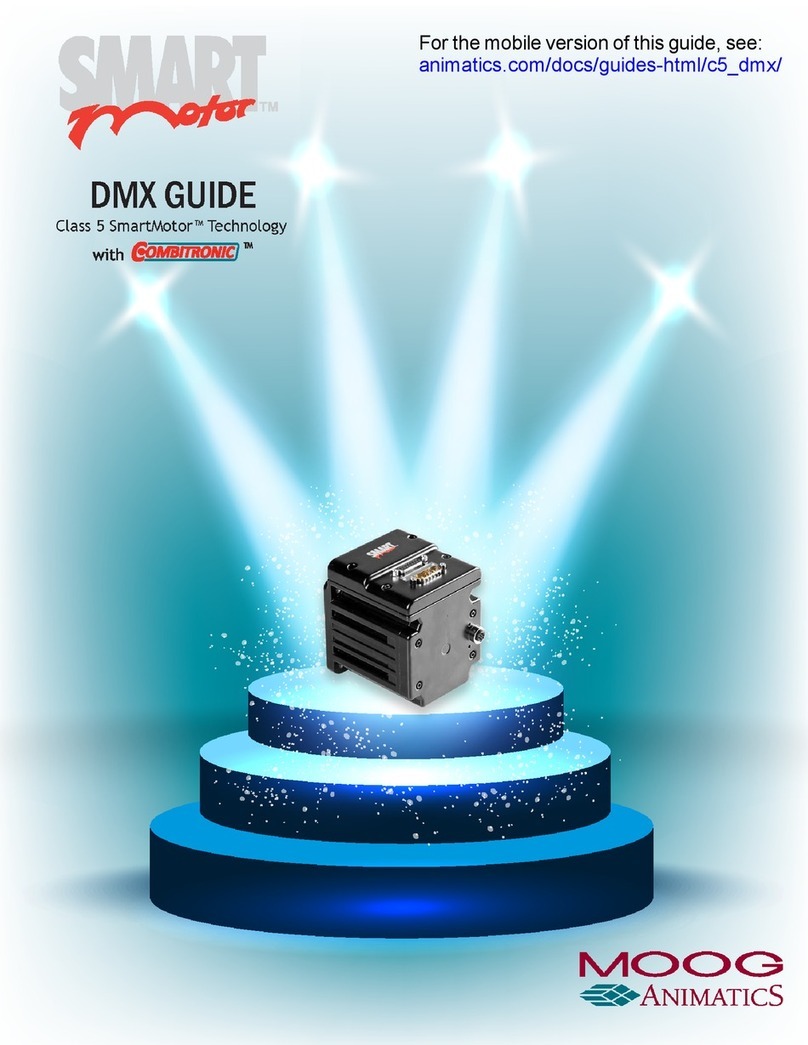
Moog
Moog Class 5 SmartMotor User manual
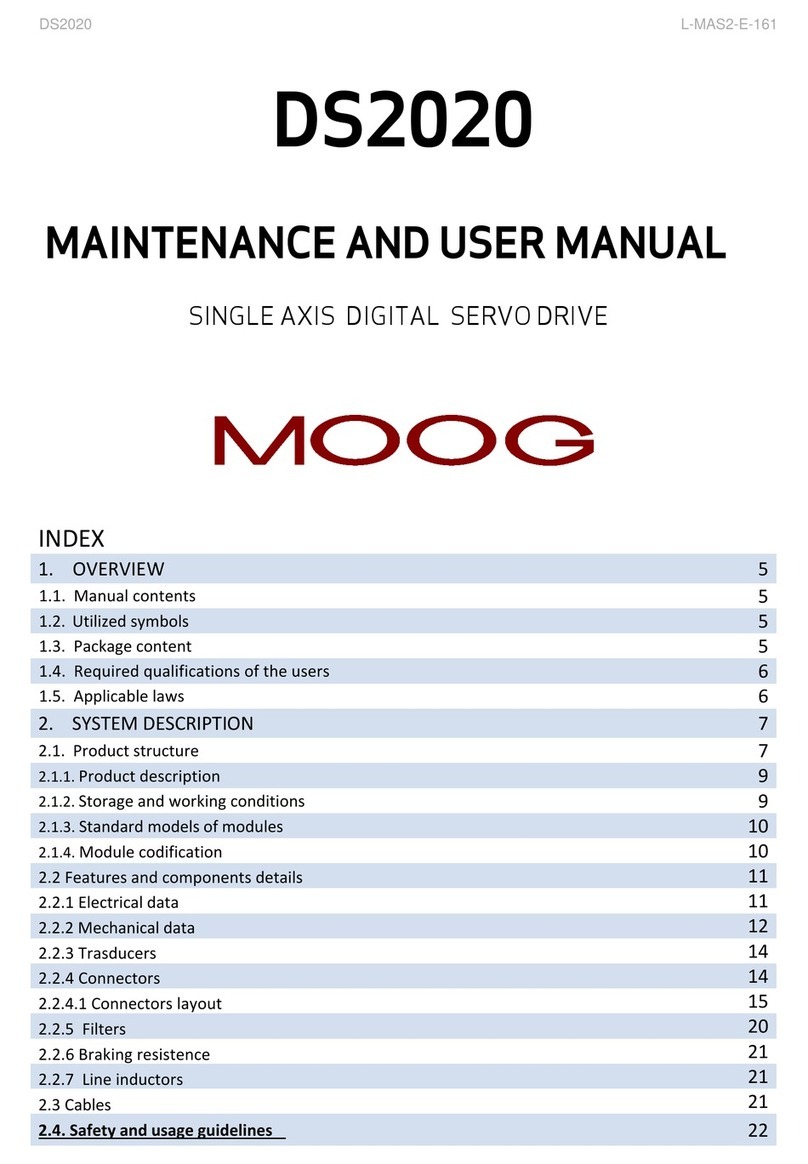
Moog
Moog DS2020 Mounting instructions

Moog
Moog SmartMotor Instruction Manual
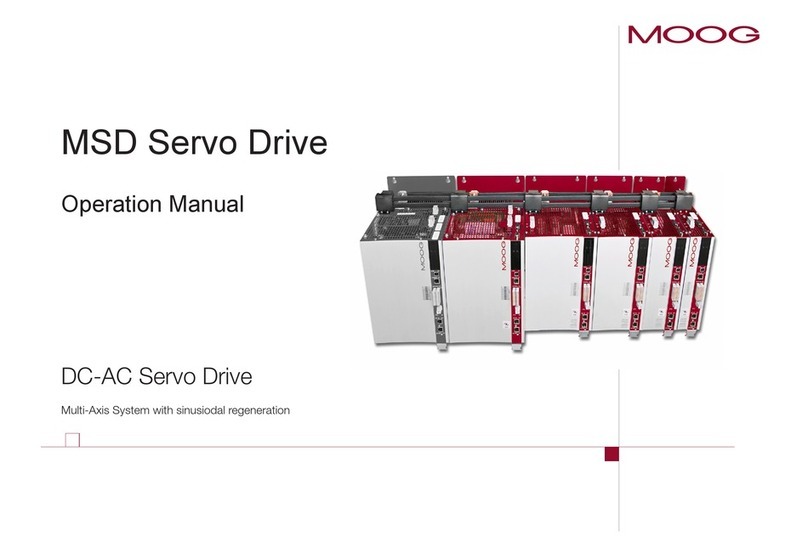
Moog
Moog G393-004 User manual