olympia electronics TC100N User manual















Other olympia electronics Security Sensor manuals
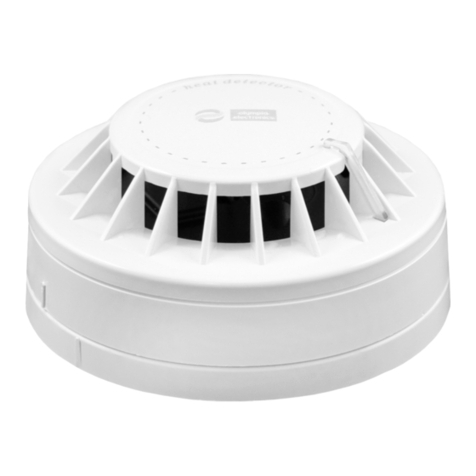
olympia electronics
olympia electronics BSR-6060/A User manual
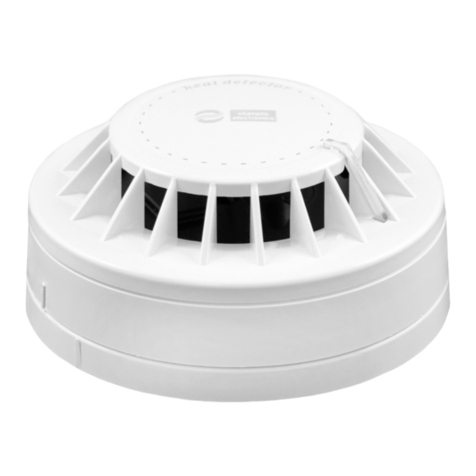
olympia electronics
olympia electronics BSR-6060/A/MAR User manual
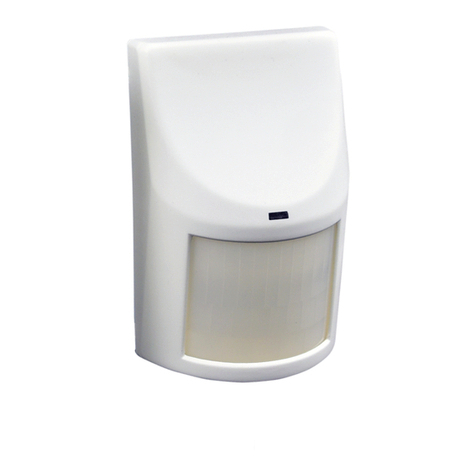
olympia electronics
olympia electronics BS-470 User manual
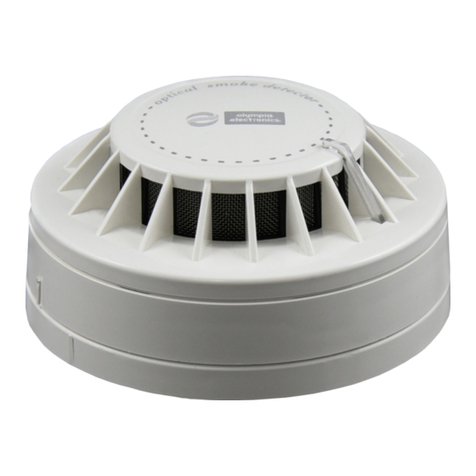
olympia electronics
olympia electronics BS- 660/A User manual
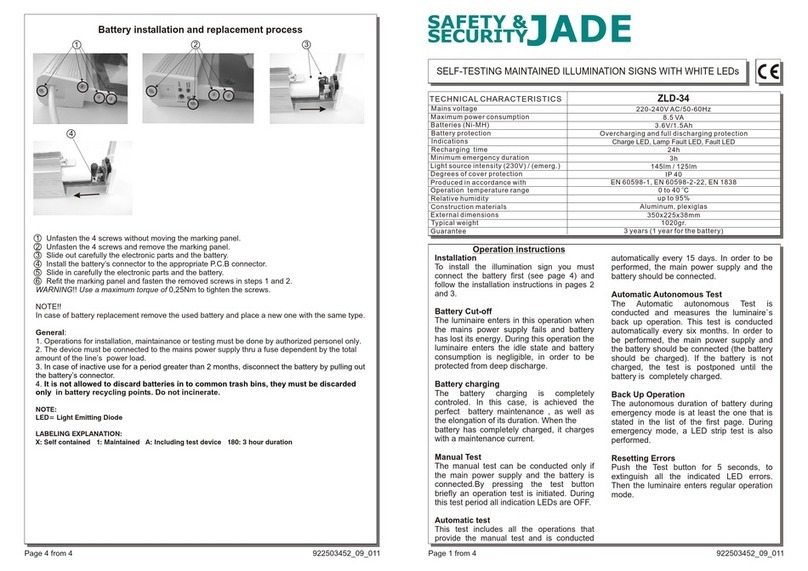
olympia electronics
olympia electronics ZLD-34 User manual
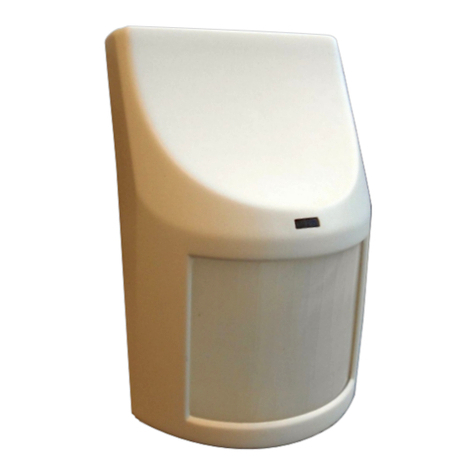
olympia electronics
olympia electronics BS-405/A User manual
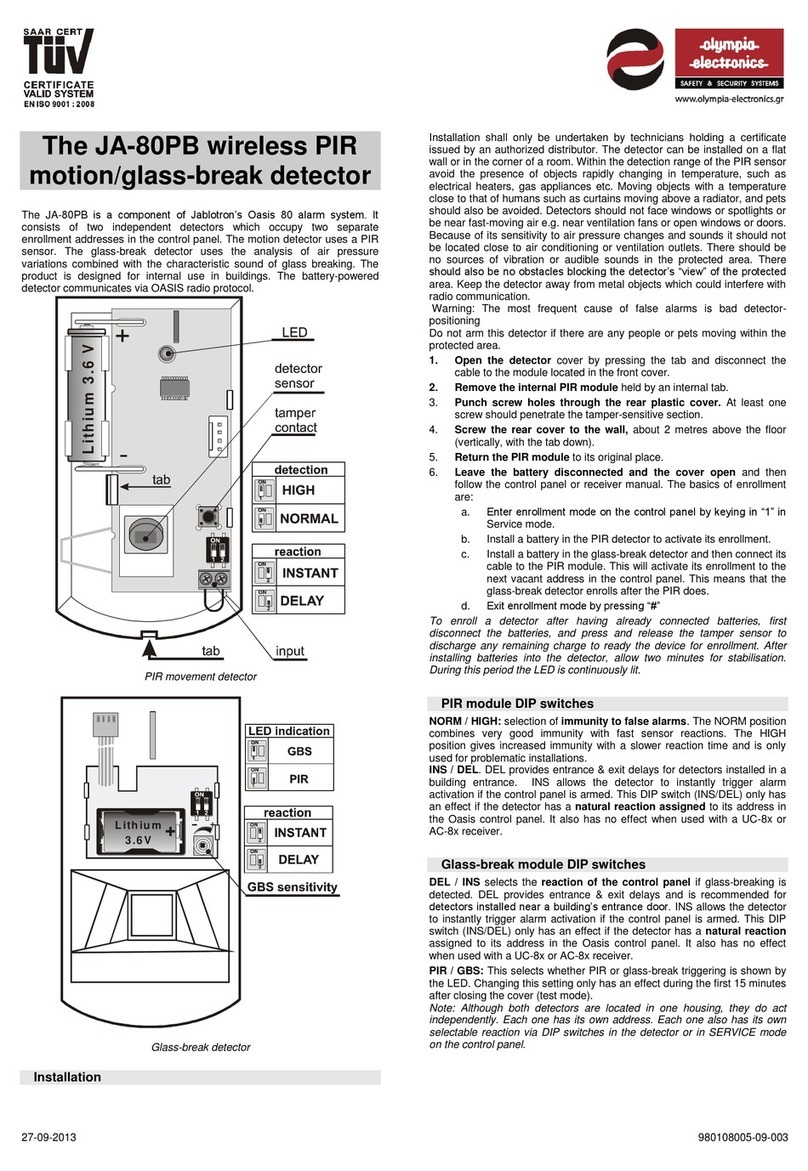
olympia electronics
olympia electronics JA-80PB User manual
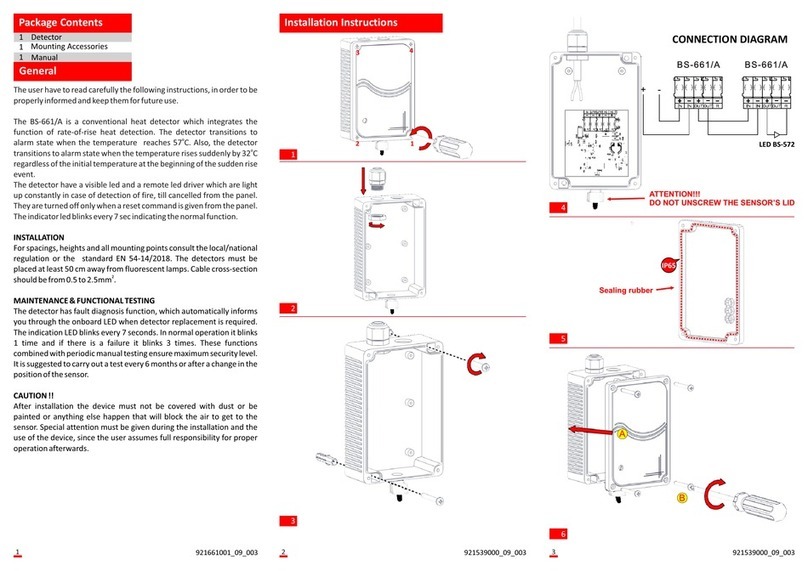
olympia electronics
olympia electronics BS-661/A User manual
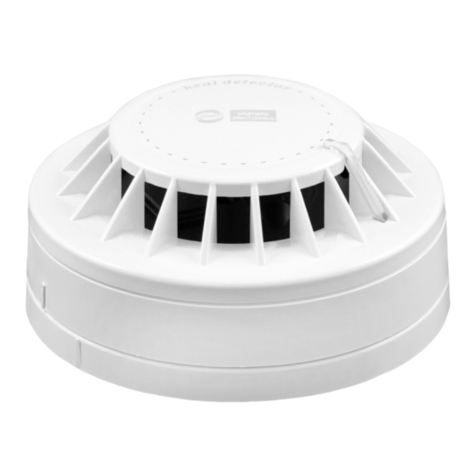
olympia electronics
olympia electronics BSR-6060/A/MAR User manual
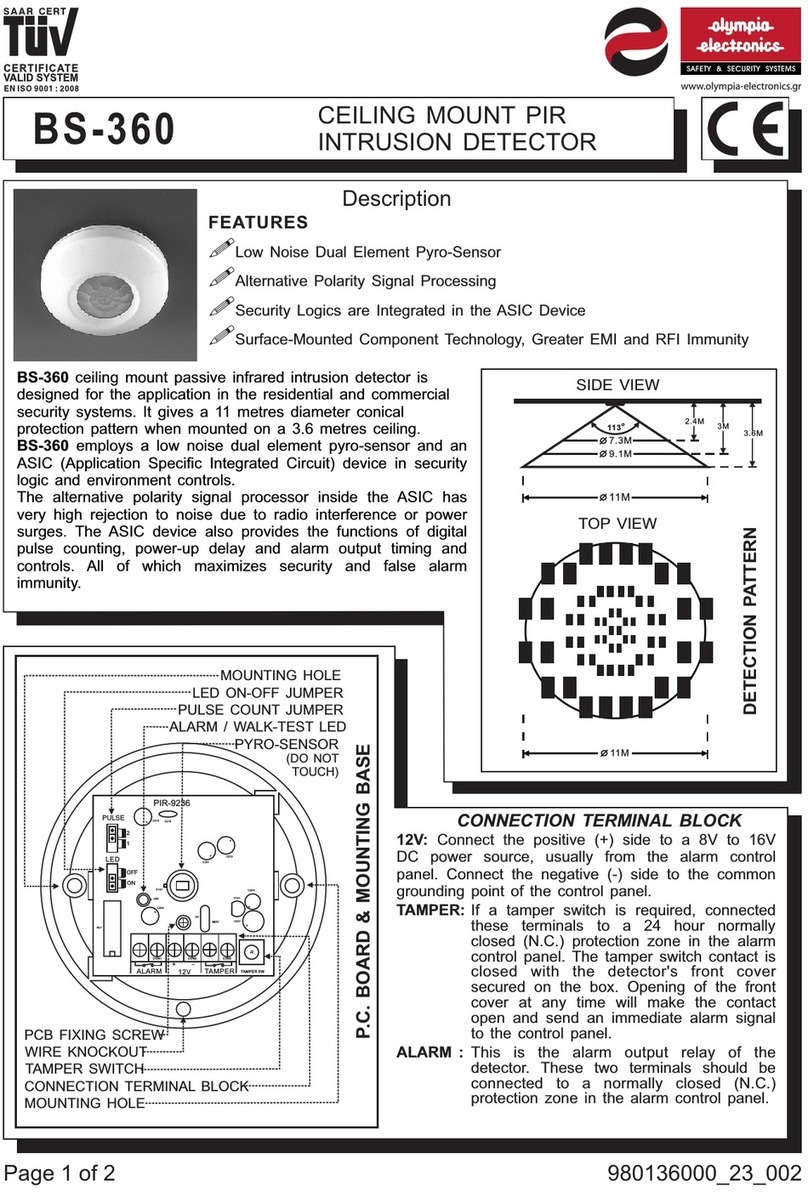
olympia electronics
olympia electronics tuv BS-360 User manual
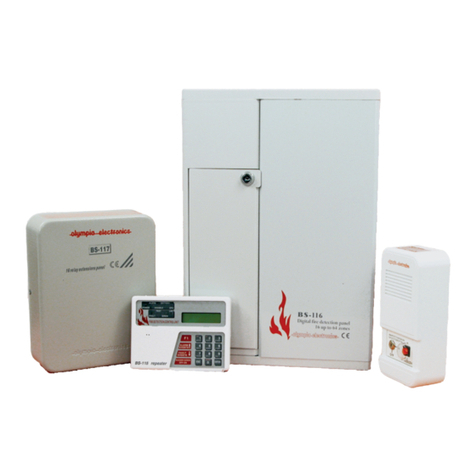
olympia electronics
olympia electronics BS-116 User manual
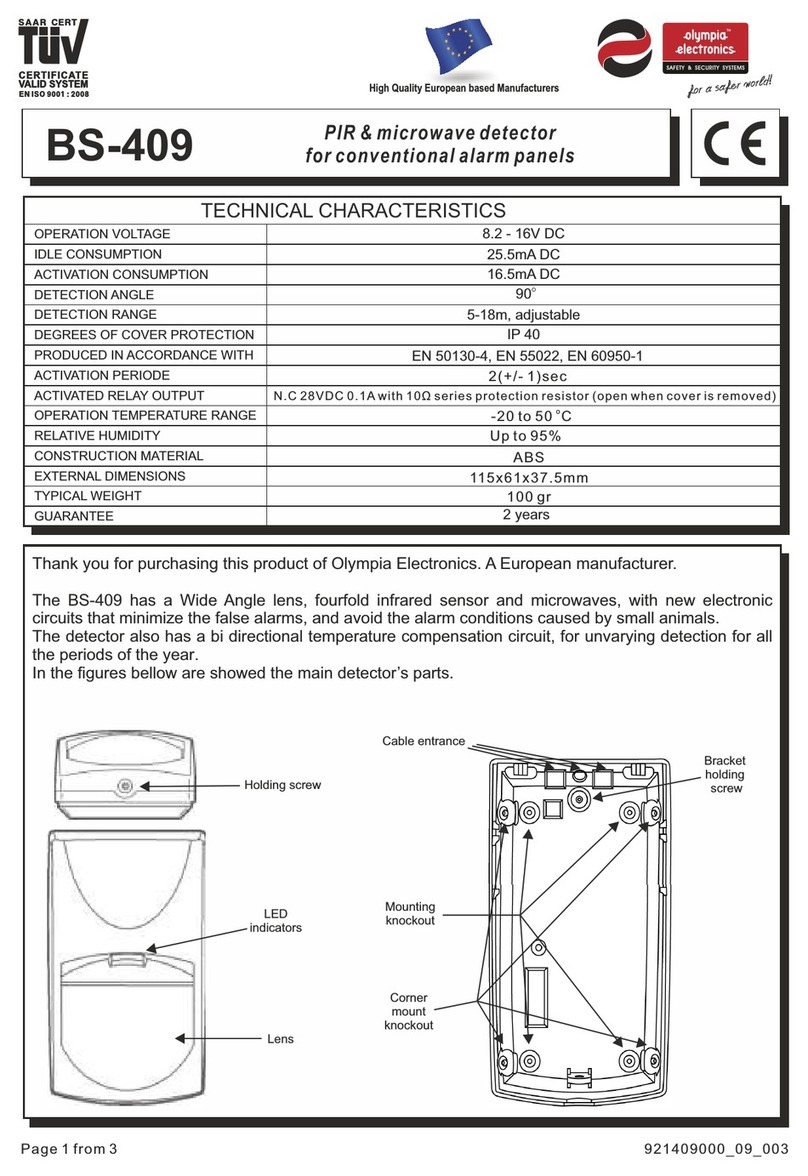
olympia electronics
olympia electronics BS-409 User manual
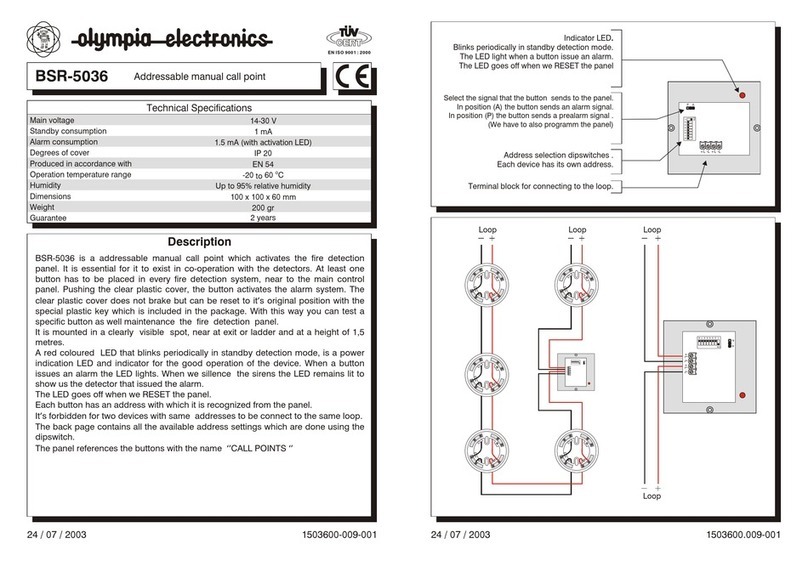
olympia electronics
olympia electronics BSR-5036 User manual

olympia electronics
olympia electronics BS-536 User manual
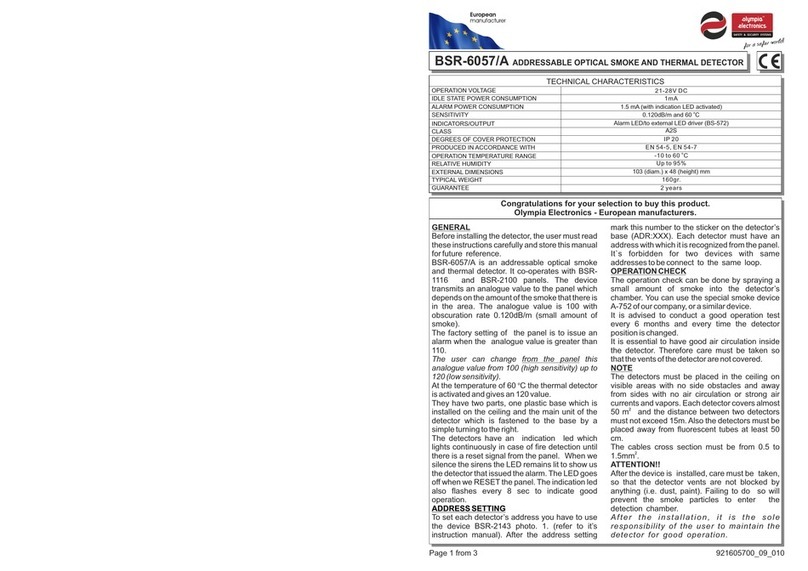
olympia electronics
olympia electronics BSR-6057/A User manual
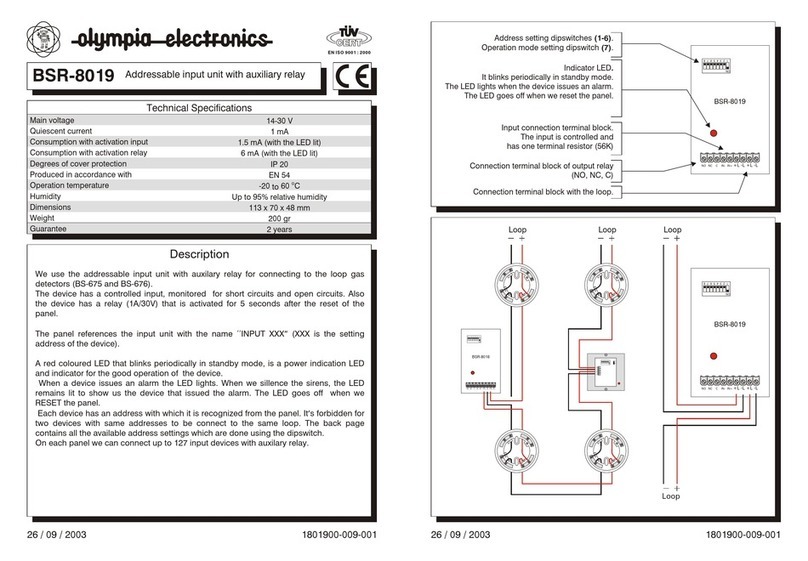
olympia electronics
olympia electronics BSR-8019 User manual
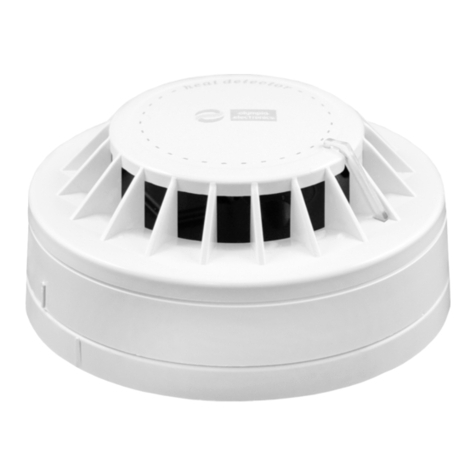
olympia electronics
olympia electronics BSR-6060/A User manual
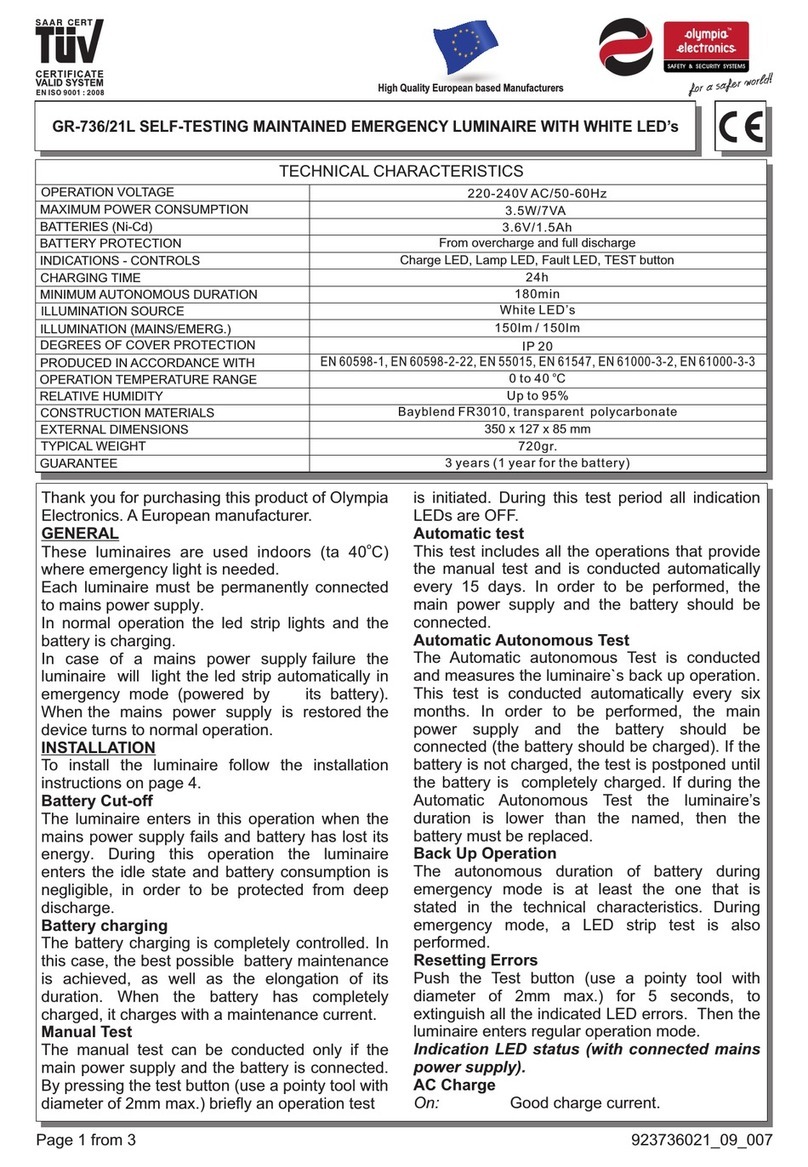
olympia electronics
olympia electronics GR-736/21L User manual
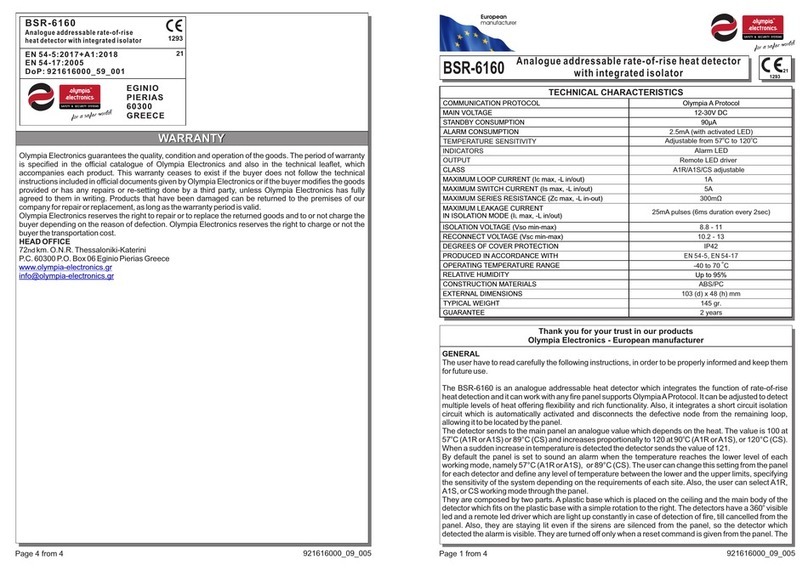
olympia electronics
olympia electronics BSR-6160 User manual
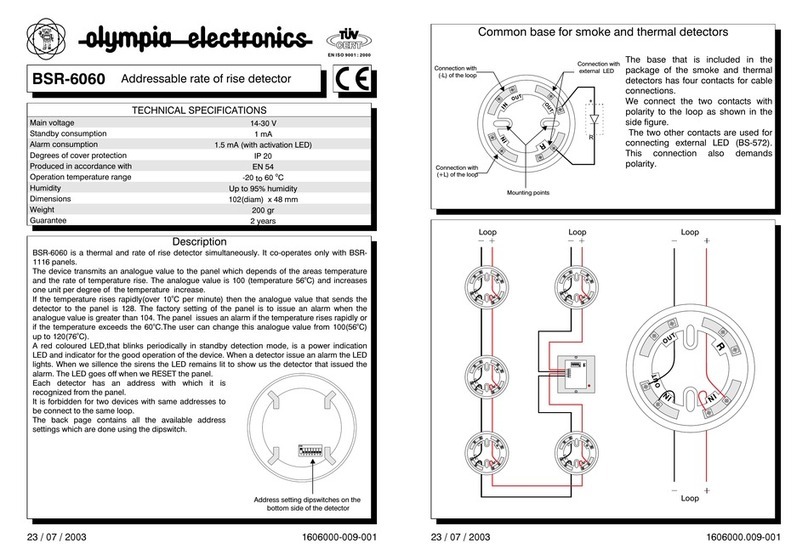
olympia electronics
olympia electronics BSR-6060 User manual
Popular Security Sensor manuals by other brands

Toors
Toors BFT ARGO T09-080-20-0057 user manual

dehn
dehn DEHNcare APHO Instructions for use
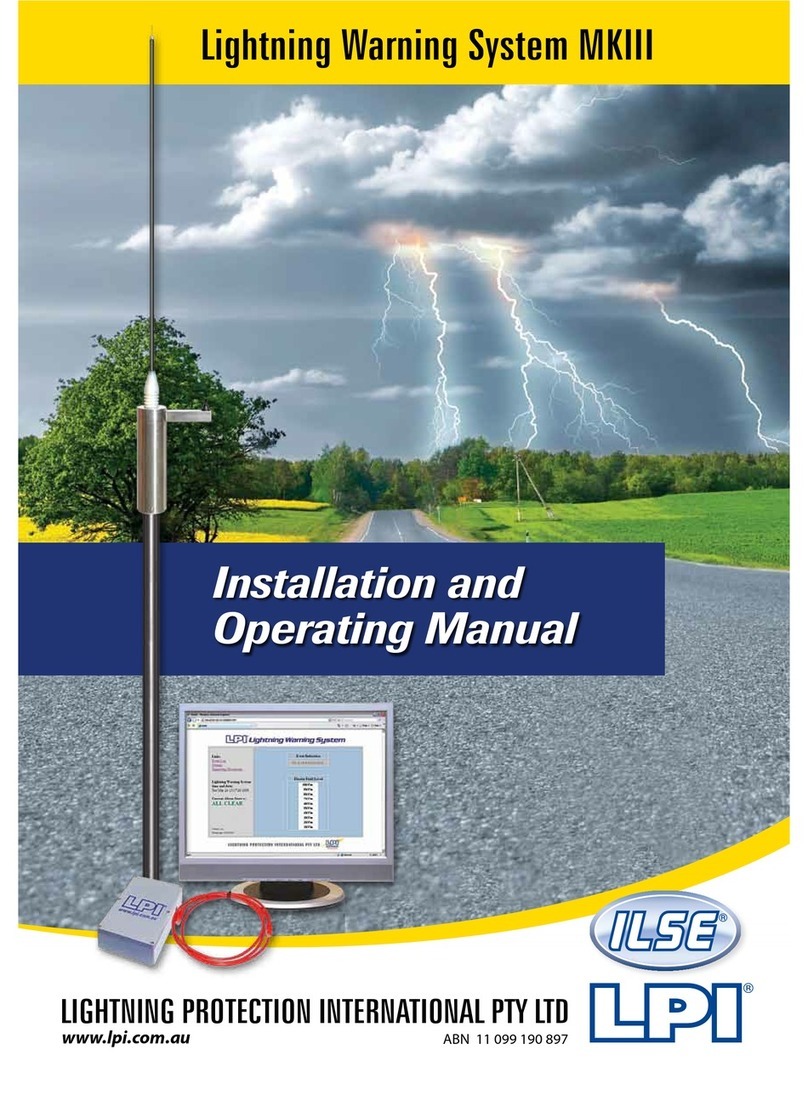
Lightning Protection International
Lightning Protection International Lightning Warning System MKIII Installation and operating manual

STEINEL PROFESSIONAL
STEINEL PROFESSIONAL HF 3360 manual
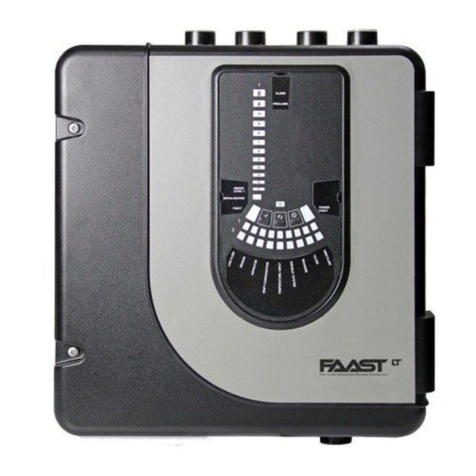
System Sensor
System Sensor FAAST LT FL01 Series Quick installation guide

Mobeye
Mobeye CMVXI-R PORTAL USER MANUAL