Parker A4AL-DN User manual

Refrigerating Specialties Division 1
BULLETIN DN23-10B
Type A4AL-DN
A4AL-DN
Fig 1
DIFFERENTIAL PRESSURE
RELIEF REGULATOR
TYPE A4AL-DN
Port Size 3/4"- 4" (20-100mm)
For Ammonia, R-22, R134a, R404a, R507
and other common refrigerants.
FEATURES
• Pilot operated characterized Modulating
Plug for precise control
• Suitable for all common refrigerants and oil
•406 psig (28bar) design pressure (PS)
• Flanges for threaded or welded steel pipe
and copper tube (copper not for ammonia)
• Unique Modular construction
• Interchangeable parts
• Easy to Service
• Close coupled strainers, optional
• Stainless Steel Diaphragm
• Manual Opening Stem
• Complies with Pressure Equipment Direc-
tive 97/23/EC
Description:
Thesecompact,heavyduty,pilotoperated, Differential
Pressure Regulators are suitable for Ammonia, R22,
R134a,R404a,R507andothercommonrefrigerantsand
fluids approved for use in refrigeration systems.
All A4AL Regulators are pilot operated using upstream
pressurefortheopeningforceandrequireaminimum2
psi (0.14 bar) pressure drop to fully open.
These valves are generally ordered with close coupled
upstreamstrainertoprevententranceofforeignmaterial
into the valve and the rest of the system.
Purpose:
Modulates flow of refrigerant liquid or gas to maintain a
constantset-forpressuredifferentialbetweenregulator
inletandregulatoroutlet.
Regulator applications are as follows: As a relief valve
frompumpoutlettoaccumulatorofaliquidrecirculating
pumpsystemtopreventpumpoverloadordrypumping
when evaporator liquid solenoid valves are closed.
Differential pressure will not vary despite fluctuating
accumulator pressures. As a gas or liquid pressure
regulator whenever it is desired to maintain a set-for
pressuredifferencebetweenregulatorinletandoutlet.
The fluid temperature range for the A4AL Series of
Regulatorsis-50°Fto220°F(-45°Cto105°C).
January 2007
InstallationandServiceInformation
ISO 9001 CERTIFIED
310218

Refrigerating Specialties Division 2
Principles of Operation
This is a pilot operated regulator whose main
valve is opened by a power piston in response
to the inlet fluid pressure received from below
theregulatordiaphragm. Theoutletpressureis
introducedthroughasensingtube,whichispart
oftheFlangeRing-tubeAssembly(20),fromthe
outletoftheregulatorintothebonnetandtothe
top of the diaphragm, thus allowing the regula-
tor to maintain a differential pressure between
the inlet and outlet equivalent to the spring
pressure.
Aftertheregulatorissetforthedesiredpressure
differential,thepressureattheinletoftheregu-
lator will rise and fall, pound for pound, with the
rise and fall of pressure at the regulator outlet,
alwaysmaintainingtheset-for differential pres-
sure across the regulator. If the difference be-
tween inlet pressure and outlet pressure of the
regulator is less than the set-for pressure, the
regulator will remain tightly closed.
Manual Opening Stem:
All Type A4AL Regulators are provided with a
manual opening stem. To open the regulator
manually,backthestemout(turncounterclock-
wise) until it stops. To put the regulator into
automatic operation, turn the stem in (clock-
wise) until only the flats on the stem protrude
from the packing nut.
Adjustment
For adjustment, pressure gauges should be
connected to the gauge port at the regulator
inletandalsodownstreamoftheregulator. With
the system operating, back the adjusting stem
all the way out to stop (counterclockwise) to
give minimum differential, which is about 2 psi.
Graduallyturntheadjustingstemin(clockwise)
untilthedesireddifferentialpressureisreached,
assuming the system is capable of achieving
suchadifferential. Checkthedifferentialsetting
after the system has been in operation for a
while and make any minor corrections neces-
sary.
Installation
All regulators are packed for maximum protec-
tion. Unpack carefully, check the carton to
make sure all flanges and other items are un-
packed. Save the enclosed instructions for the
installer and eventual user.
Donotremovetheprotectivecoveringsfromthe
inlet and outlet of the regulator until the regula-
torisreadyto be installed. Protecttheinsideof
the regulator from moisture, dirt and chips be-
fore and during installation. When welded or
brazed flange connections are used, all slag,
scale and loose particles should be removed
from the flange interior before the regulator is
installedbetweenthe flanges. Itisadvisableto
install a close-coupled companion strainer
(RSF)attheinletoftheregulatortohelpprotect
it from any foreign material in the system.
TheA4ALseriesofregulatorswillgiveoptimum
performance if mounted in a horizontal line in a
vertical position with the manual opening stem
on bottom. Where other positions are desired,
the factory should be consulted: please give
application and piping details. The regulator
must be installed with the arrow on the valve
bodypointinginthedirectionofthefluidflowfor
the regulator to function properly. Backward
flow through the regulator is uncontrolled and
willvarywithvalvemodelandthereversepres-
sure drop encountered. The regulator is not a
check valve.
Tighten the flange bolts and nuts evenly to
provideproperseatingoftheflangegasketand
to avoid damage to gaskets or flanges. (See
Bolt Torque Table). Avoid using the regulator
flange bolts to stretch or align pipe. Even the
heavy duty body of an A4A can be distorted,
causing the precision parts to bind.
The regulator should be installed in a location
whereitiseasilyaccessible for adjustmentand
maintenance. Thelocationshouldbesuchthat
the regulator can not be easily damaged by

Refrigerating Specialties Division 3
materialhandlingequipment. Whenitisneces-
sary to insulate the regulator (and companion
strainer), the insulation should be installed to
provideaccesstotheregulator(andcompanion
strainer) for adjustment and maintenance. Do
not insulate the solenoid coil and coil housing.
Properindicating gauges shouldbe installedto
be easily visible to the operating engineer for
system checking and adjusting purposes.
Disassembly and Assembly
Before disassembling any A4A type regulator,
read the information in this bulletin and Bulletin
RSB,SafetyProceduresforRefrigerating Spe-
cialties Division Refrigeration Control Valves.
Before a regulator is removed from the line or
disassembled in the line, make sure that all
refrigerant has been removed from the regula-
tor,includingthebonnet,whereapplicable,and
theclose-coupled strainer. The regulator must
beisolated from therest ofthe system ina safe
manner. When pumping down to remove the
refrigerant,themanualopeningstem33Amust
beturned out(counter clockwise) tomake sure
the valve is open.
All A4A Regulators
General Procedure
Theconstructionoftheregulatorandthemethod
of disassembly are relatively simple, but some
proceduresmustbe followedto avoid damage.
The following describes the procedure for the
basic A4A; special instruction for other styles
will be included in other appropriate sections.
Disassembly-TakecarewhenremovingSeal
Caps(1)and(44)incasesomerefrigerantmay
betrappedinside. Backthe AdjustingStem(6)
all the way out to remove any pressure from
Range Spring (13) otherwise damage to Dia-
phragm (17) or Pilot Seat (18) may occur. Re-
move Bonnet (8) by carefully removing Cap
Screws (11). Take care not to damage Dia-
phragmFollower(15). RemoveAdapter(28)by
removing Cap Screws (31). Turn the Manual
OpeningStem(33A)allthewayinuntiltheflats
onthestembarelyprotrudefromthestuffingbox
nut. Push Piston (30) down against the spring
force. Thepistonshouldmovefreelydownand
be returned by the spring force. If the piston is
jammed or sticky, remove Bottom Cap Assem-
bly, which includes Items (33) through (42), by
removing Cap Screws (39) or unscrewing Bot-
tom Cap, 3/4" through 1-1/4" (20mm through
32mm). Using a hard wood dowel rod inserted
through the bottom of the valve, tap the piston
upward and out. Thoroughly clean all parts. If
jamming has taken place and the piston and
bore are scored, remove all burrs by polishing
the piston, bore and modulating plug with fine
crocus cloth. Inspect the seating area of the
Modulating Plug (33) for damage or erosion. If
damaged it should be replaced. It would be
advisable to replace the entire bottom cap as-
sembly. Inspect all gaskets and “o” rings for
damage and replace where necessary.
Assembly - When reassembling the valve, all
internal parts should be clean, dry and lightly
oiledwithrefrigerantoil,except“o”rings. Apply
silicone grease to the “o” rings. Care must be
taken especially when the parts are cold since
moisture can condense on parts and cause
rapid rusting. When replacing gaskets, they
should be oiled very lightly with refrigerant oil
before assembly. Items which require several
bolts to fasten must be tightened uniformly to
provide proper alignment and seating. (See
Bolt Torque Table). Install bottom cap assem-
bly first and tighten in place. Carefully replace
thepiston;nevertrytoforceitinplace. Alignthe
Adapter Gasket (29) carefully with the proper
holes in the adapter and the valve body and
fastenadapterinplace. Beforeassemblingthe
bonnetbe surethe adjusting Stem (6) isturned
all the way out. Place Gasket (19), Diaphragm
(17)andGasket(16)inAdapter(28). Theraised
center of the diaphragm must be towards the
bonnet. StackDiaphragmFollower(15),Lower
SpringRest(14),Spring(13)andUpperSpring
Rest (12) on top of diaphragm and carefully
lower bonnet in place and tighten Screws (11)
inplace. TightenCapScrews(11)evenly. The

Refrigerating Specialties Division 4
ideal tightening torque is 11 ft. lbs. (1.5 kg-m).
Valve is now ready to be adjusted for normal
operation.
If close coupled strainer is used, it may be
cleanedbefore puttingthe valveback inopera-
tion. Theregulatormustbetestedforleakswith
refrigerant gas or other appropriate gas before
the system is put into operation.
After the General Procedure for disassembly,
inspect the Pilot Seat (18) top seating surface
for dirt, wear or damage. Remove seat from
valve body and clean, lap on a flat plate or
replaceasnecessary. Examinethediaphragm
regionwhichcontactstheseatsurface,look for
dirt, heavy scratches or corrosion. If the dia-
phragm cannot be easily wiped clean, it should
be replaced. Reassemble the regulator follow-
ing the General Procedure.
Maintenance and Service
General Procedure:
Dirtinthesystemisthegreatestsinglecauseof
regulatormalfunction. Allscreensorfiltersmust
be cleaned or replaced when they become
dirty. At start up it is especially important that
theseitemsarecleanedorchangedfrequently.
WhentheRSFclose-coupledcompanionstrain-
ers are used, maintain according to instruction
in Bulletin 00-10. Moisture in halocarbon sys-
tems in particular can cause corrosion or form
ice, causing the piston to freeze in position.
Filter-driers should be used and maintained for
halocarbon systems.
Before deciding to disassemble a regulator for
servicing, the following investigations should
be made:
Check the manual opening stem; it should be
turned in for automatic operation.
Check the regulator setting to make sure it is
properlyadjusted. Turnadjusting screwslowly
to see if regulator responds. Check regulator
pressure range; if wrong, range spring must be
replaced.
Checkothersystemcomponentsforproperop-
eration. Check hand valves in the system to
make sure they are open or closed as required
and the system is receiving liquid or gas as the
case may be.
Before disassembly of regulator, make certain
that all refrigerant has been removed (pumped
out)fromtheregulatoranditcompanionstrainer
where one is used. Read Safety Bulletin
RSBCV.
Safe Operation (See also Bulletin RSBCV)
People doing any work on a refrigeration
system must be qualified and completely
familiar with the system and the Refrigerat-
ing Specialties Division valves involved, or
all other precautions will be meaningless.
This includes reading and understanding
pertinent Refrigerating Specialties Division
productBulletinsandSafetyBulletinRSBCV
prior to installation or servicing work.
Where cold refrigerant liquid lines are used, it is
necessary that certain precautions be taken to
avoiddamagewhichcouldresultfromliquidexpan-
sion. Temperatureincreaseinapipingsectionfullof
solid liquid will cause high pressure due to the
expanding liquid which can possibly rupture a gas-
ket, pipe or valve. All hand valves isolating such
sections should be marked, warning against acci-
dentalclosing,andmustnotbecloseduntiltheliquid
is removed. Check valves must never be installed
upstream of solenoid valves, or regulators with
electricshut-off, norshouldhand valveupstreamof
solenoid valves or downstream of check valves be
close until the liquid has been removed. It is advis-
able to properly install relief devices in any section
where liquid expansion could take place.
Avoidallpipingorcontrolarrangementswhichmight
produce thermal or pressure shock. For the protec-
tion of people and products, all refrigerant must be
removed from the section to be worked on before a
valve, strainer, or other device is opened or re-
moved. Flanges with ODS connections are not
suitable for ammonia service.

Refrigerating Specialties Division 5
Item Description
1 Seal Cap
2 Gasket, Seal Cap
3 Nut, Stuffing Box
4 Packing Ring
5 Packing Washer
6 Adjusting Stem
8 Bonnet
9 Nameplate
10 Screw, Name Plate
11 Screw, Bonnet
12 Spring Rest, Upper
13 Spring, Range
14 Spring Rest, Lower
15 Diaphragm Follower
16 Gasket, Bonnet
17 Diaphragm
18 Seat, Pilot
19 Gasket, Adapter
20 Flg Ring-tube Asm
27 Gauge Port Pipe Plug
28 Adapter, Body
29 Gasket, Body
30 Piston-Stem
31 Screw, Body
32 Body
33 Throttling Plug Asm
34 Spring, Closing
35 Dirt Wiper Retainer
36 Dirt Wiper
37 Seal, Bottom Cap
38 Bottom Cap
39 Screw, Bottom Cap
40 Packing Washer
41 Packing Ring
42 Stuffing Box Nut
43 Gasket, Seal Cap
44 Seal Cap
45 Gasket, Flange

Refrigerating Specialties Division 6
PRESSURE CONTAINING COMPONENTS A4A DN LINE: 3/4" & 1"
COMPONENT DESCRIPTION MATERIAL Kv VOLUME
BODY, A4A DN ASTM A-126 CLASS B 6.2
ADAPTER, A4A DN ASTM A-126 CLASS B &
COVER BOTTOM, A4A/S4A BARSTOCK ASTM 1213 CR 8.6
BONNET A4W ASTM A-126 CLASS B
BODY,S6A (REGULAR MATL) DUCTILE IRON ASTM A536
TUBE SOLENOID, S6 SS TUBING 304
SLEEVE, SOLENOID TUBE AISI 1117 CRS BARSTOCK
BODY, A2D DN ASTM A-126 CLASS B
PRESSURE CONTAINING COMPONENTS A4A DN LINE: 1-1/4 TO 4
COMPONENT DESCRIPTION MATERIAL Kv VOLUME
BODY, A4A DN DUCTILE IRON GGG 40.3 15 0.57 L
ADAPTER, A4A DN DUCTILE IRON GGG 40.3
COVER BOTTOM, A4A/S4A BARSTOCK ASTM 1213 CRS
BONNET A4W DUCTILE IRON GGG 40.6
COMPONENT DESCRIPTION MATERIAL Kv VOLUME
BODY, 2 A4A DN DUCTILE IRON GGG 40.3 28.6 1.61 L
ADAPTER, 2 A4A DN DUCTILE IRON GGG 40.3
COVER BOTTOM, A4A/S4A 1-5/8 to 2-1/2 DUCTILE IRON GGG 40.3
BONNET A4W DUCTILE IRON GGG 40.3
COMPONENT DESCRIPTION MATERIAL Kv VOLUME
BODY, 2 A4A DN DUCTILE IRON GGG 40.3 42.4 1.61 L
ADAPTER, 2 A4A DN DUCTILE IRON GGG 40.3
COVER BOTTOM, A4A/S4A 1-5/8 to 2-1/2 DUCTILE IRON GGG 40.3
BONNET A4W DUCTILE IRON GGG 40.3
COMPONENT DESCRIPTION MATERIAL Kv VOLUME
BODY, 2-1/2 A4A DN DUCTILE IRON GGG 40.3 60 3.19 L
ADAPTER, 3 A4A DN DUCTILE IRON GGG 40.3
COVER BOTTOM, 3 A4A/S4A DUCTILE IRON GGG 40.3
BONNET A4W DUCTILE IRON GGG 40.3
COMPONENT DESCRIPTION MATERIAL Kv VOLUME
BODY, 3 A4A DN DUCTILE IRON GGG 40.3 86 3.91 L
ADAPTER, 3 A4A DN DUCTILE IRON GGG 40.3
COVER BOTTOM, 3 A4A/S4A DUCTILE IRON GGG 40.4
BONNET A4W DUCTILE IRON GGG 40.3
COMPONENT DESCRIPTION MATERIAL Kv VOLUME
BODY, 4 A4A DN DUCTILE IRON GGG 40.3 116 6.5 L
ADAPTER, 4 A4A DN DUCTILE IRON GGG 40.3
COVER BOTTOM,4 A4A/S4A DUCTILE IRON GGG 40.4
BONNET A4W DUCTILE IRON GGG 40.3
75 MM
1-1/4 IN
1-5/8 IN
2 IN
2-1/2 IN
3/4 & 1IN
20 & 25
MM
100 MM
3 IN
4 IN
32 MM
40 MM
50 MM
65 MM

Refrigerating Specialties Division 7
BO LT TO RQUE TABLE
ITEM PO RT SIZE TORQUE
7/16"Flange Bolt1/2" 28 ftlb
5/8"Flange Bolt3/4"-2" 85 ftlb
3/4"Flange Bolt2-1/2"-3" 105 ftlb
7/8"Flange Bolt 4" 150 ftlb
5/16"-18 BonnetBolt3/4"-4" 15ftlb
5/16"-18 AdapterBolt3/4"-2" 15ftlb
5/8"-11 AdapterBolt 3"-4" 75 ftlb
Bottom Cap 3/4"-1-1/4" 150 ftlb
1/2"-13 Bottom Cap Bolt1-5/8"-2-1/2" 50 ftlb
5/8"-11 Bottom Cap Bolt3"-4" 75 ftlb
A4AL
Dimensions
A
G
C
D
H
FPT
SW
J
Add for Strainer
F
E
Weld Neck
Flange
ODS
Flange
OVERALLVALVEDIMENSIONS
Port Size 20mm & 25mm 32mm 40mm& 50mm 65mm 75mm 100mm
(3/4 & 1") (1-1/4") (1-5/8 & 2") (2-1/2") (3") (4")
DIMENSION mm inches mm inches mm inches mm inches mm inches mm inches
AA4P, A4L 392 15.4 410 15.6 464 16.2 483 19.0 597 23.5 653 25.7
A43P 414 16.3 432 17.0 485 19.1 505 19.9 620 24.4 676 26.6
C164 6.2 203 8.0 251 9.9 252 9.9 311 12.2 359 14.1
GA4P, A4L 244 9.6 248 9.8 287 11.3 302 11.9 324 12.8 361 14.2
A43P 266 10.5 270 10.7 308 12.2 324 12.8 347 13.7 384 15.1
H117 4.6 117 4.6 140 5.5 159 6.2 176 7.0 222 8.8
J98 3.9 178 7.0 251 9.9 314 12.4 314 12.4 363 14.3
OVERALL LENGTH DIMENSIONS WITH FLANGES
*Add 13mm (0.5") to D,E & F Dimensions for A4LVariation
FPT & SW 3/4" 216 8.5 1-1/4" 256 10.1 1-1/2" 307 12.1
D* FORPIPE 1" 216 8.5 1-1/2" 256 10.1 2" 307 12.1 2-1/2" 331 13.0 3" 389 15.3 4" 450 17.7
SIZES 1-1/4" 216 8.5
WN FOR 3/4" 254 10.0 1-1/4" 300 11.8 1-1/2" 364 14.3
E* FORPIPE 1" 261 10.3 1-1/2" 304 12.0 2" 371 14.6 2-1/2" 401 15.8 3" 478 18.8 4" 571 22.5
SIZES 1-1/4" 261 10.3
ODS FOR 7/8" 239 9.4 1-3/8" 269 10.6 1-5/8" 358 14.1 2-5/8" 348 13.7 3-1/8" 414 16.3
F* TUBE 1-1/8" 239 9.4 1-5/8" 279 11.0 2-1/8" 338 13.3 4-1/8" 503 19.8
SIZES 1-3/8" 231 9.1 2-1/8" 305 12.0 2-5/8" 358 14.1 3-1/8" 389 15.3 3-5/8" 432 17.0
1-5/8" 239 9.4

Refrigerating Specialties Division 8
Parker Hannifin Corporation • Refrigerating Specialties Division
2445 South 25th Avenue • Broadview, IL 60155-3891
Telephone (708) 681-6300 • Fax (708) 681-6306
Warranty
AllRefrigeratingSpecialtiesproductsarewarranted
against defects in workmanship and materials for a
period of one year from date of shipment from
originating factory. This warranty is in force only
when products are properly installed, field as-
sembled, maintained, and operated in use and ser-
vice as specifically stated in Refrigerating Special-
ties Catalogs or Bulletins for normal refrigeration
applications, unless otherwise approved in writing
by Refrigerating Specialties Company. Defective
products, or parts thereof returned to the factory
withtransportationchargesprepaidandfoundtobe
defective by factory inspection will be replaced or
repaired at Refrigerating Specialties option, free of
charge F.O.B. factory. Warranty does not cover
productswhichhavebeenaltered,orrepairedinthe
field; damaged in transit, accidents, misuse, or
abuse. Products disabled by dirt or other foreign
substances will not be considered defective.
The express warranty above constitutes the only
warranty of Refrigerating Specialties products, and
isinlieuofallotherwarranties,expressedorimplied,
written or oral, including any warranty of merchant-
abilityorwarrantyoffitnessforaparticularpurpose
andinno event is Refrigerating Specialties respon-
sible for any consequential damages of any nature
whatsoever. No employee, agent, dealer or other
person is authorized to give any warranties on
behalfofRefrigeratingSpecialtiesnortoassumefor
Refrigerating Specialties any other liability in con-
nection with any of it products.
SYMPTOM PROBABLE REASON CORRECTION
Regulator does not
shut off flow Diaphragm or seat dirty, damaged or
frozen Clean or replace. Clean strainer
Diaphragm follower stuck or damaged Clean or replace. Install follower
carefully
Piston jammed with excess dirt Remove and polish piston and bore
with crocus cloth. Clean valve and
strainer
Modulating plug leaking due to excess
dirt or damaged Clean or replace. If used on liquid,
check for erosion due to excessive
flash gas by subcooling or by reducing
pressure drop across valve by providing
restriction at valve outlet.
Regulator does not
open Pressure Regulator Diaphragm
ruptured or badly deformed Replace. Make sure 2 diaphragms are
installed.
Diaphragm follower stuck, damaged or
frozen Clean or replace. Install follower
carefully
Piston worn, too much clearance Replace piston. Check for reason. If
used or liquid, check for flash gas.
Regulator Operation
erratic Diaphragm or seat dirty, damaged. Clean or replace. Clean strainer
Diaphragm follower has dirt on the
outside diameter or outside diameter is
damaged.
Clean or replace
Regulator too far oversized. Check load. Replace with smaller
regulator or investigate use of Reduced
Capacity Plug Kit.
Pressure drop across
regulator too high Inlet or outlet restricted Check for restriction. Clean strainer.
Regulator too small Replace with proper size regulator
Large amount of flash gas in liquid line Reduce flash gas by subcooling.
Reduce line restriction by increasing
line size, particularly at the regulator
outlet. Replace with larger regulator.
High pressure drop causes high rate of
expansion of gas at regulator outlet Increase pipe size at the outlet of the
regulator
Regulator does not open all the way. Check piston for wear. Replace, if
needed.
Table of contents
Other Parker Controllers manuals

Parker
Parker ACR9000 User manual
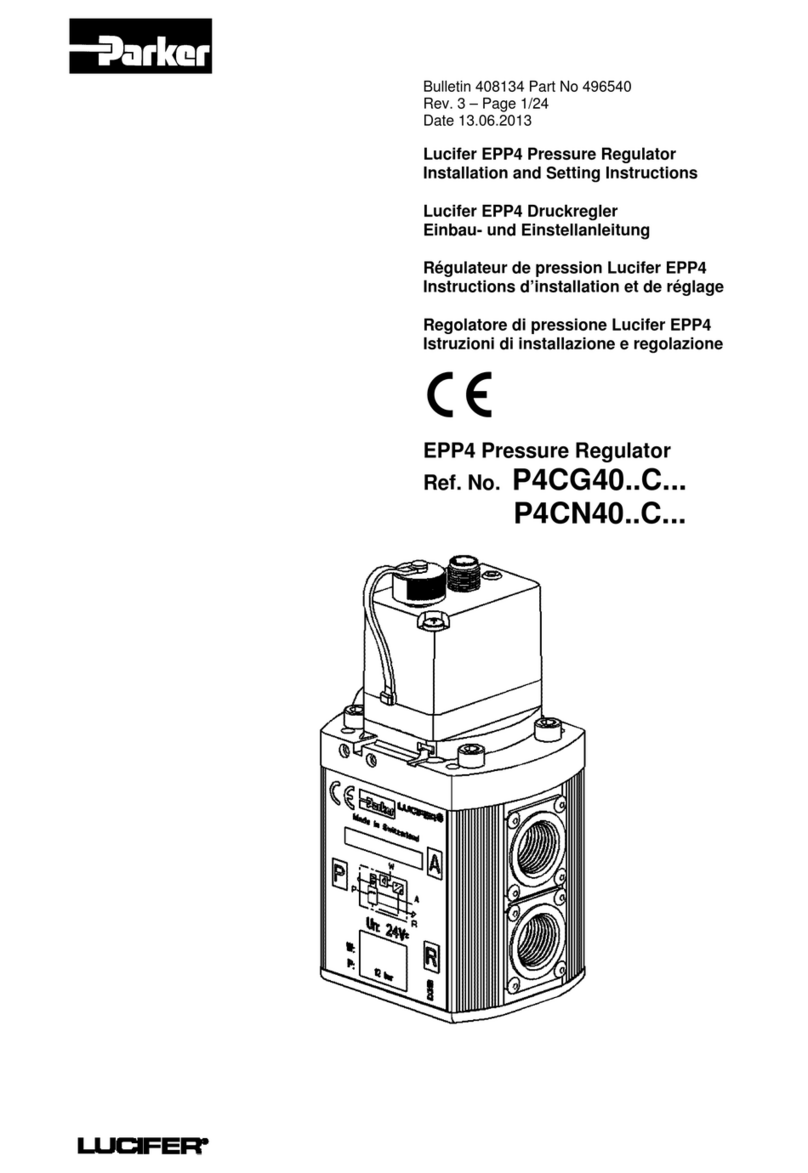
Parker
Parker Lucifer P4CN40 C Series Manual

Parker
Parker IQAN-MC31 User manual

Parker
Parker ET Series Datasheet
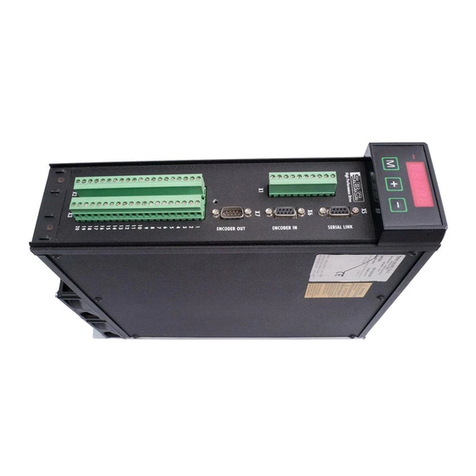
Parker
Parker HPD2N User manual
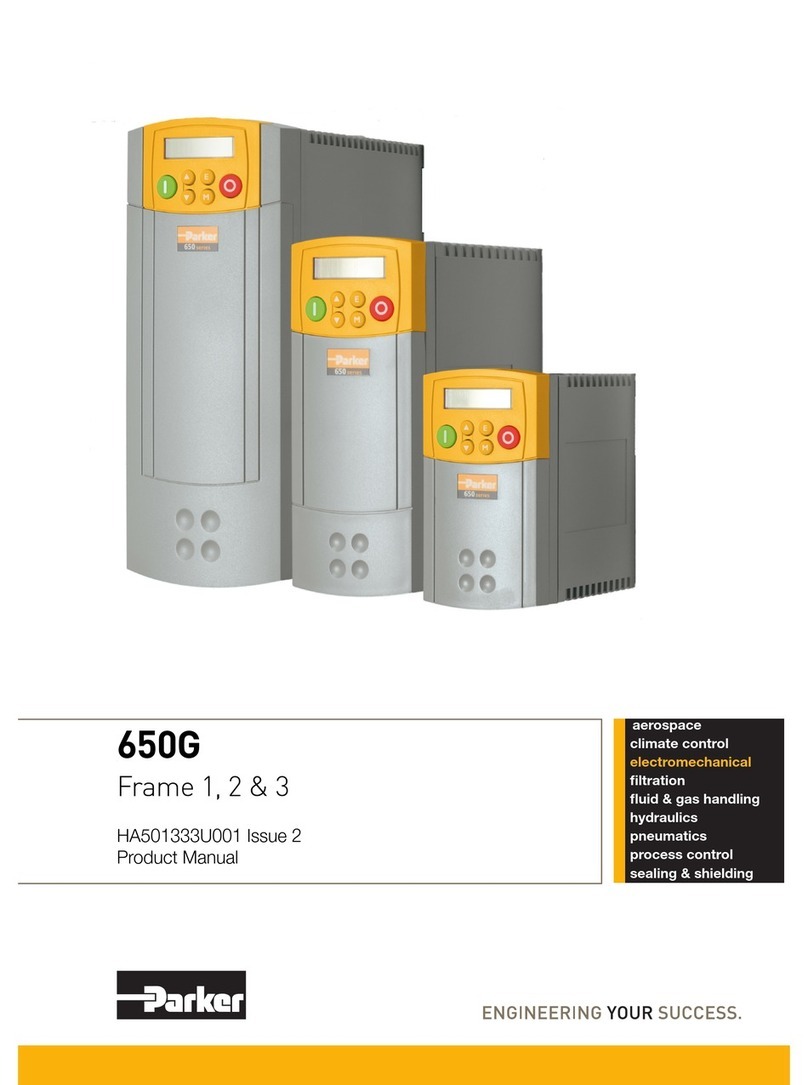
Parker
Parker 650G Frame 1 User manual
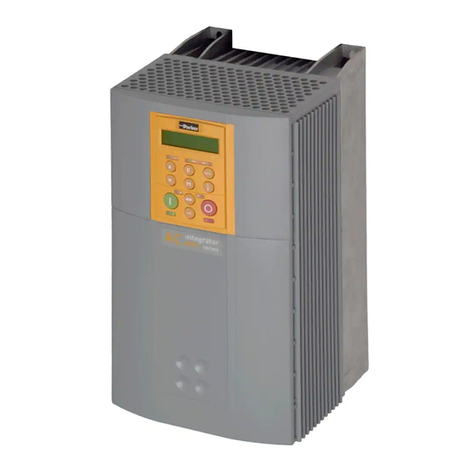
Parker
Parker 690+ series User manual
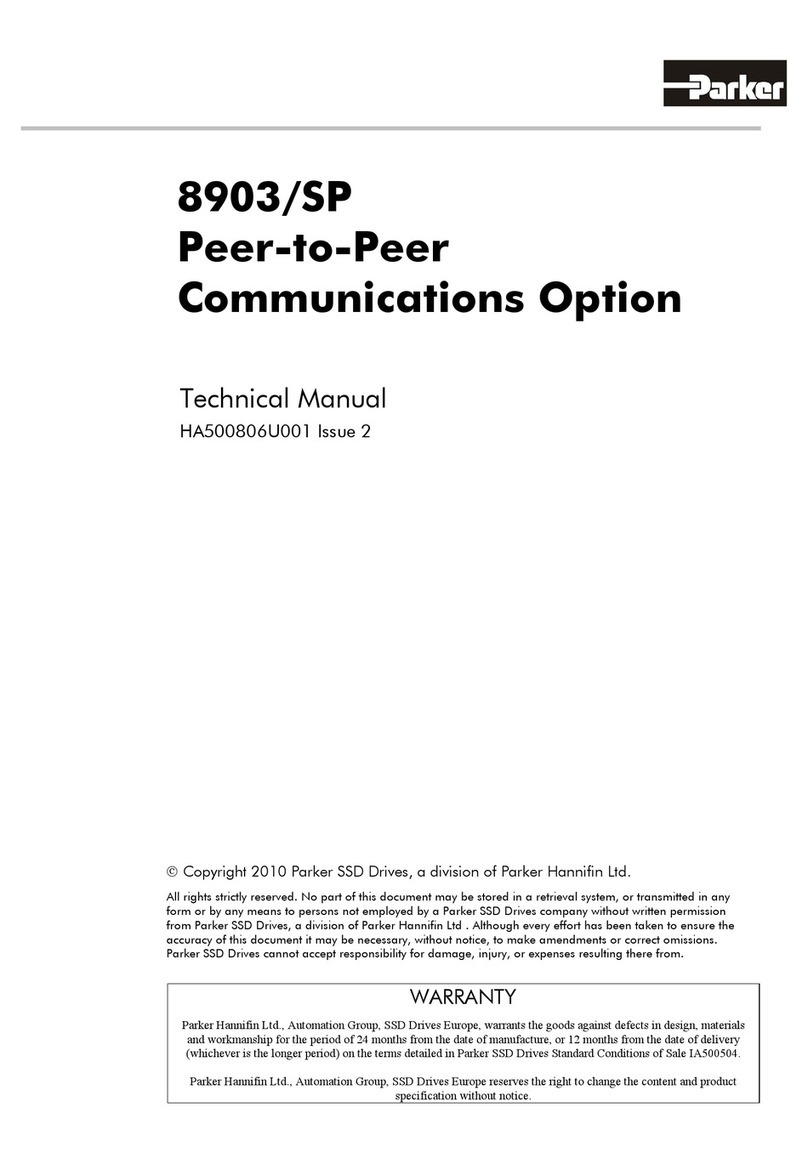
Parker
Parker 8903/SP User manual
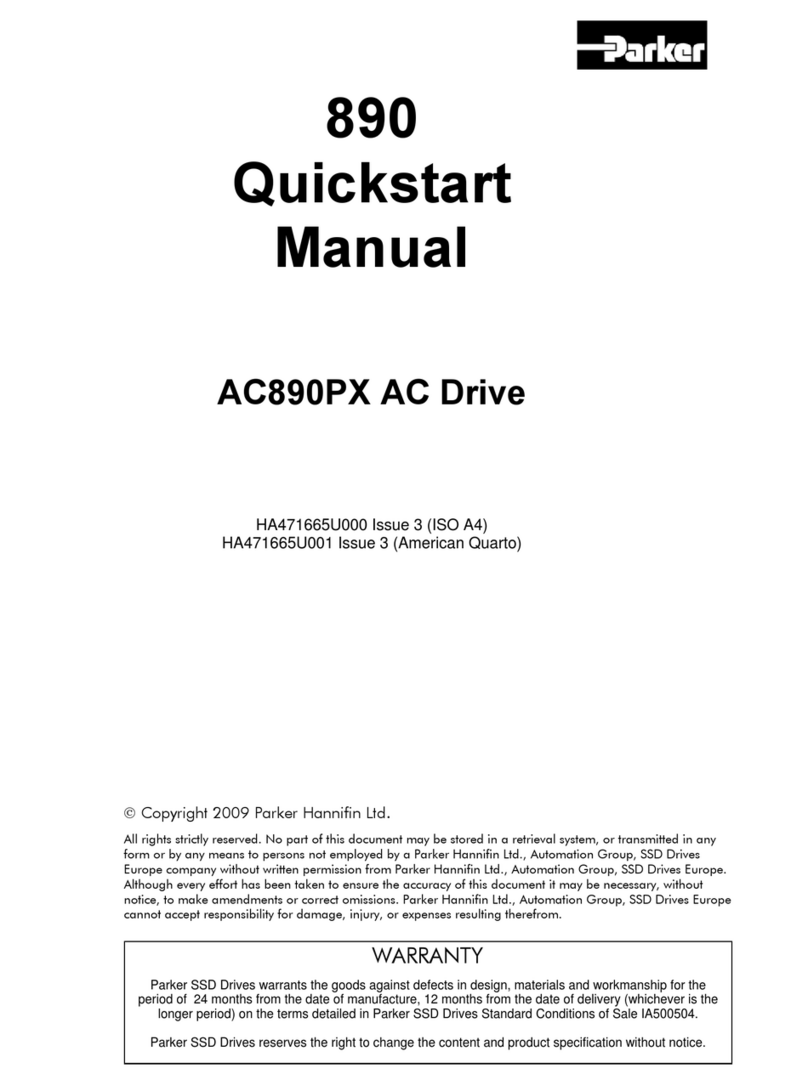
Parker
Parker AC890PX Series Instruction manual
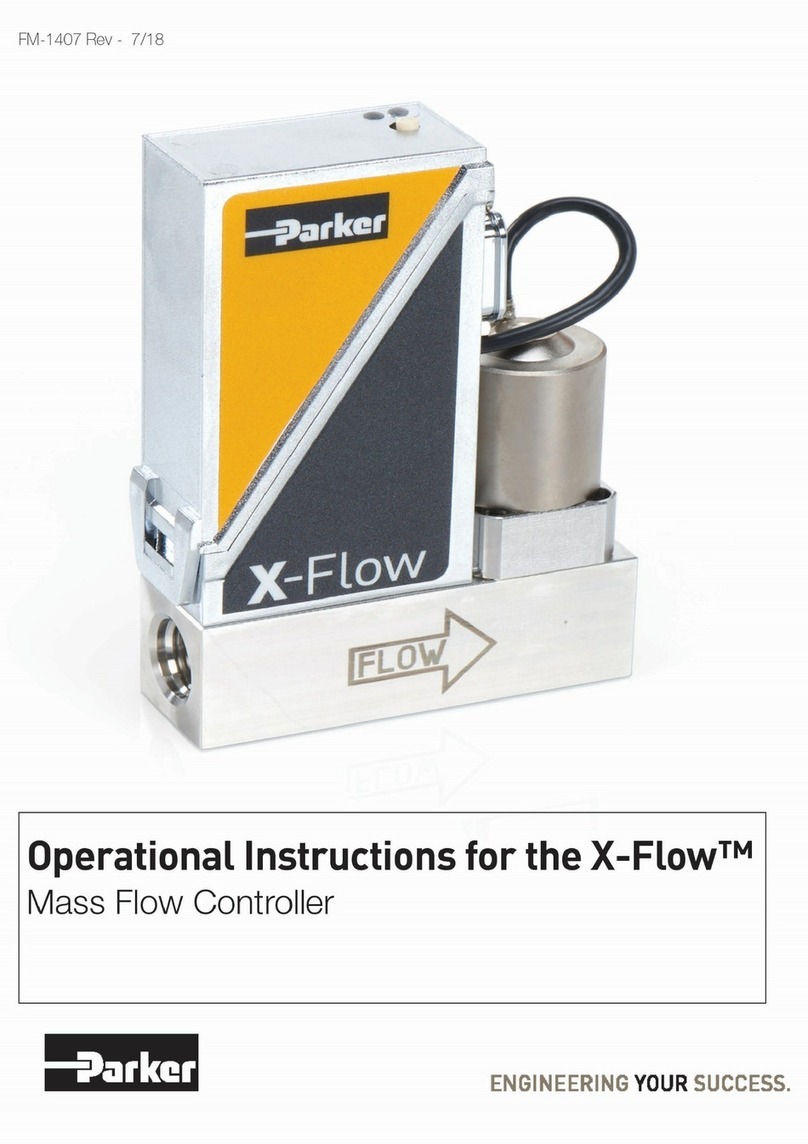
Parker
Parker X-Flow Quick start guide
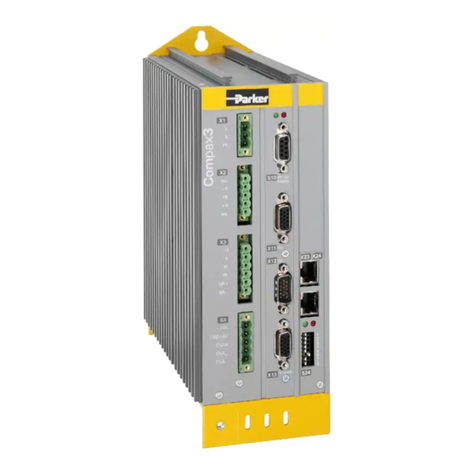
Parker
Parker Compax3 Series User manual

Parker
Parker GEM6K Series Manual
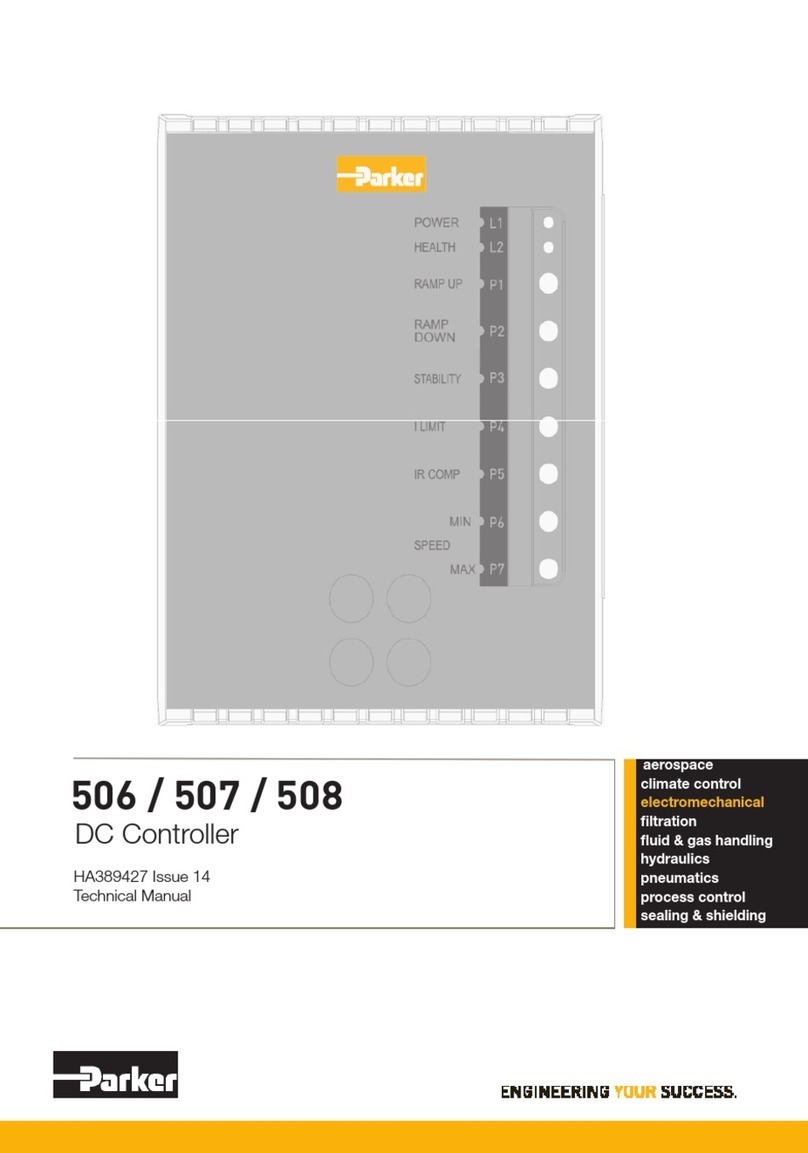
Parker
Parker 507 Series User manual
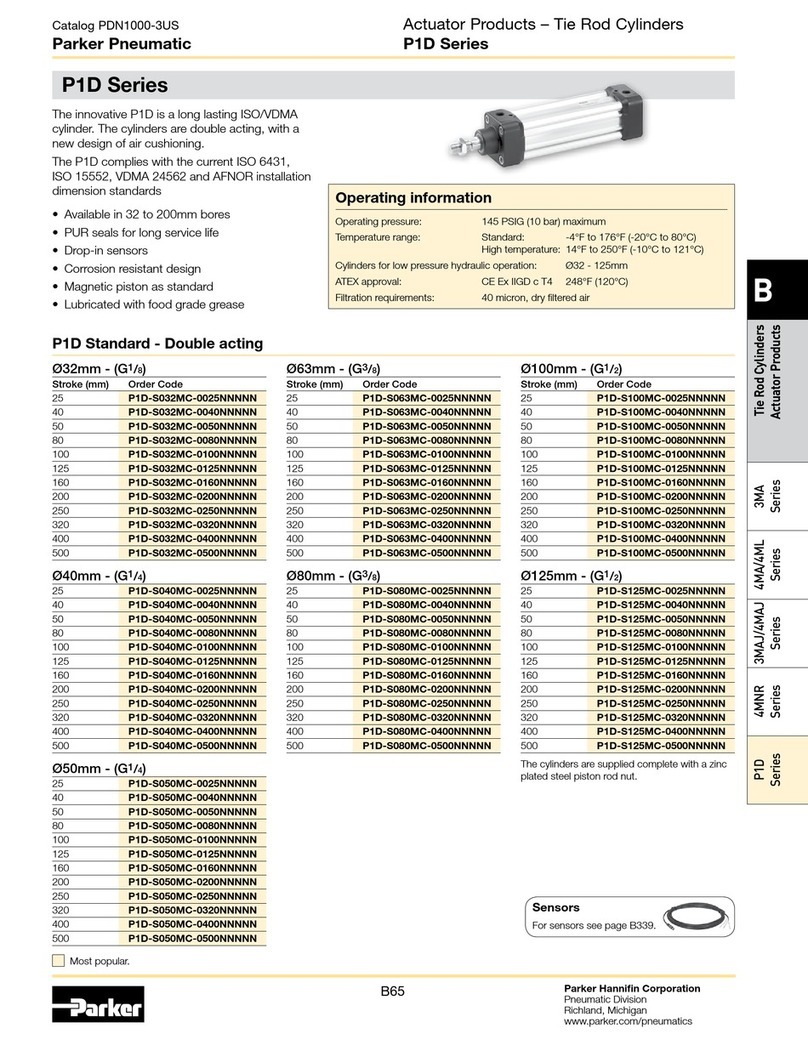
Parker
Parker P1D Series Owner's manual
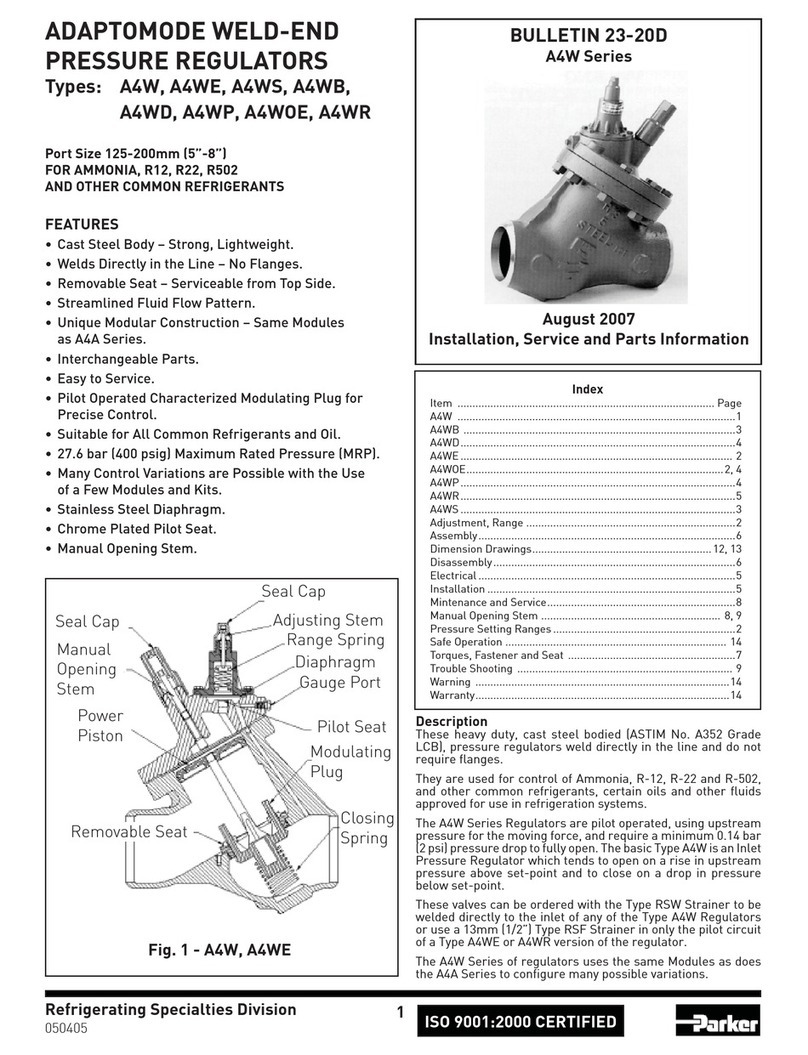
Parker
Parker A4W Series Guide
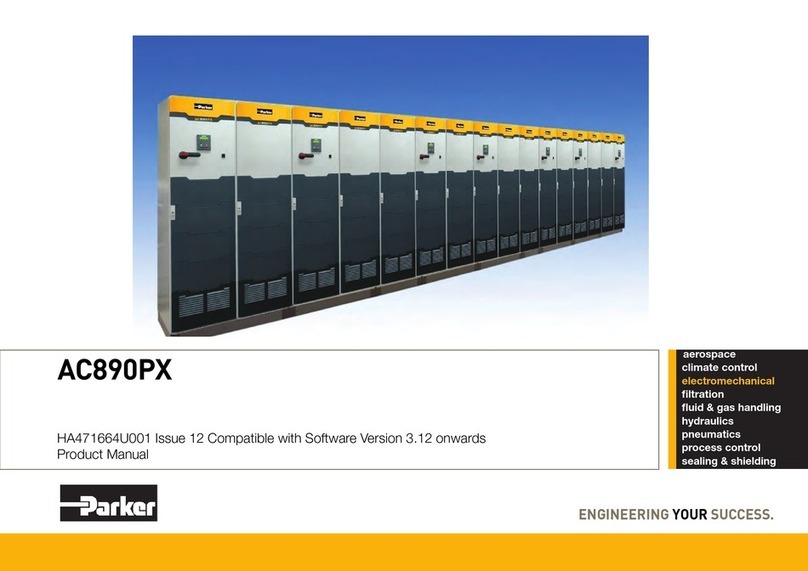
Parker
Parker AC890PX Series User manual
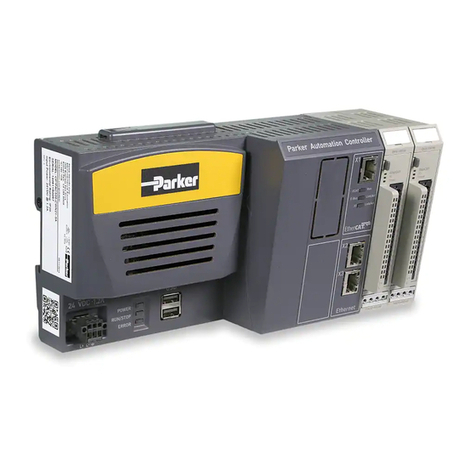
Parker
Parker PAC User manual
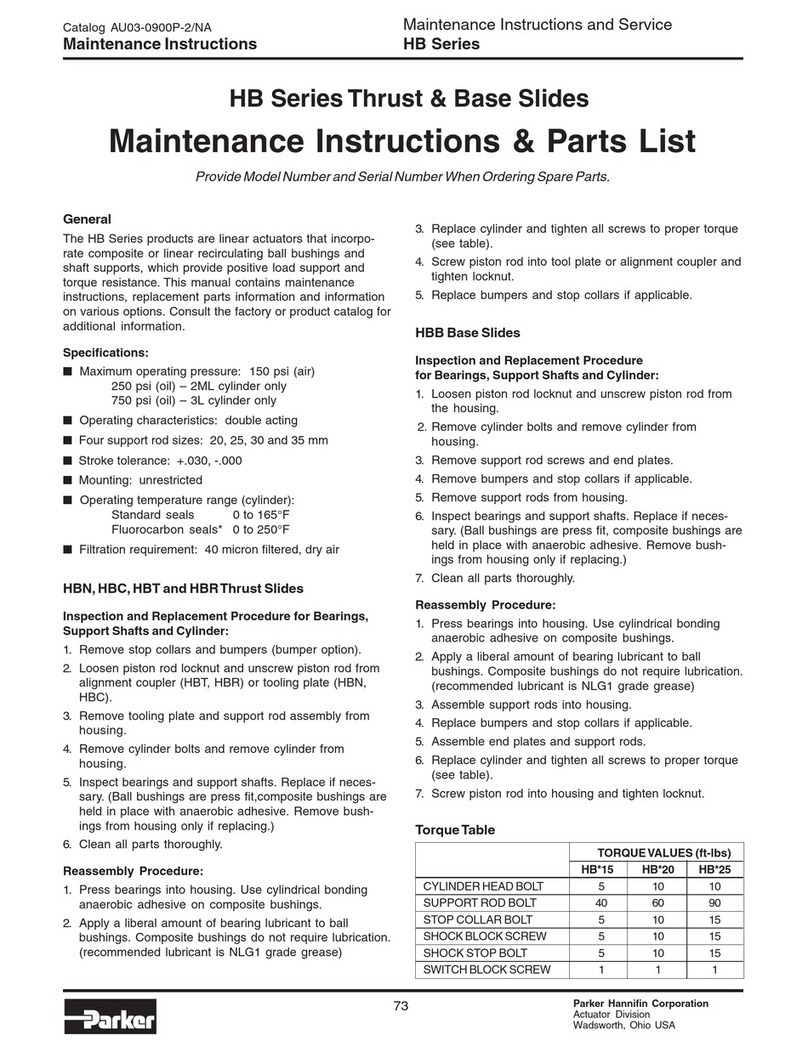
Parker
Parker HBN15 Datasheet

Parker
Parker ac890 User manual
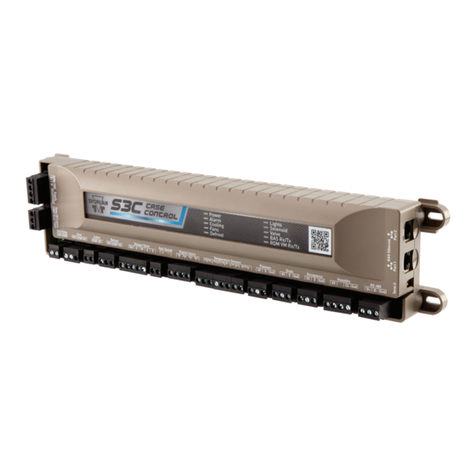
Parker
Parker Sporlan S3C User guide