Ricoh FT5034C User manual

SERVICE MANUAL
FT5034C

CONTENTS
1. INSTALLATION.................................................... 2
2. OVERVIEW........................................................... 7
3. COPY PROCESS ................................................. 11
4. SECTION DESCRIPTIONS .................................. 13
5. SP MODE/DIP SW TABLE................................... 92
6. CALL SERVICE CONDITIONS ............................ 98
7. PREVENTIVE MAINTENANCE............................105
8. TROUBLESHOOTING..........................................114
9. ELECTRICAL DATA
- 1 -

1. INSTALLATION
1.1 INSTALLATION REQUIREMENTS....................3
1.2 INSTALLATION PROCEDURE..........................4
- 2 -

1.1 INSTALLATION REQUIREMENTS
The installation location should be carefully chosen because environmental
conditions greatly affect the performance of a copier.
1. Environments to Avoid
•Avoid any area exposed to direct sunlight or strong light (Illumination must be
less than 1500 Lux).
•Avoid any area exposed to extremes of temperature and humidity (standard
condition: 10°C ~ 30°C, 15% ~ 90%).
•Avoid any area exposed to heated air from a heater.
•Avoid any area where temperature suddenly changes from low to high or vice
versa.
•Avoid placing the copier in an area filled with dust, and subjected to frequent
strong vibration.
•Avoid narrow space (10 m3).
2. Access to Copier
Place the copier near a power source, providing clearance as shown. The copier
must be level within 5 mm both front to rear and left to right.
3. Power Connection
•Input voltage level:
220 V/50 Hz, more than 10 A
•Avoid connecting the power cord
to a socket that already has
power cords attached
•Permissible voltage fluctuation:
220 V (±10%)
•Avoid using a power cord
extension. If you must use one,
make sure that it can carry 250
V, 10 A and that it is less than 5
m long.
4. Earth Connection
•Be sure to ground the machine properly.
•Do not connect the grounding wire to a gas pipe.
more than 10 cm
more than 80 cm
more than
50 cm more than
70 cm Front
- 3 -

1.2 INSTALLATION PROCEDURE
NOTE: 1. When lifting and moving the
copier, grasp the black painted
stays on each side as shown.
2. When the optional sorter is
installed, the above mentioned
stays can not be held. Wear
gloves to protect hands from the
edges of the copier base plate.
3. When transporting the copier,
remove all the developer and
toner inside the machine. Also
make sure to lock the scanner
with the lock plate.
1. Unpacking and Clamps Removal
1. Remove the shipping tapes from the copier
as follows:
1) From platen cover to front cover
2) Manual table
3) Feed guide (cassette insert section)
4) Transport guide plate
5) T/S corona unit
6) Toner shield glass
7) Front loading cassette lever
8) Operation panel cover
9) PTL, QL filter
10) Relay lower guide plate
2. Remove the seal from the toner tank
entrance.
3. Remove the wedge (red) from between the
registration rollers.
4. Remove the scanner lock plate cover.
5. Remove the scanner lock plate (1 screw).
(Save the scanner lock plate for future use.)
6. Reinstall the scanner lock plate cover.
7. Adjust the machine level by turning the
rubber foot on the base plate.
Scanner Lock
Plate Cover
Scanner Lock
Plate
Development
Lock Lever
- 4 -

2. Developer Supply
Place a clean sheet of paper on your work
surface.
1. Raise the development lock lever and pull
out the development unit. Place the unit on
a clean sheet of paper.
2. Separate the toner tank from the
development unit (2 screws).
3. Pour one bag of developer (1 kg) into the
development unit while turning the knob
counterclockwise to distribute the developer
evenly.
4. Remount the toner tank on the development
unit.
NOTE: Make sure that there is no gap
between the toner tank and the
development unit.
3. Drum Protective Sheet Removal
1. Lower the T/S corona unit lever.
2. Remove the charge corona unit together
with the wire cleaner (1 screw).
3. Remove the drum stay (1 knob and 1
screw). The drum knob is reverse threaded.
4. Pull out the drum protective sheet.
5. Reinstall the drum stay and the charge
corona unit with the wire cleaner.
6. Raise the T/S corona unit lever.
4. Development Unit Installation
1. When installing the development unit, be
sure the development unit rail is properly
engaged with the unit guide rail on the
copier. (Make sure that the PTL and QL
filters are in their original positions.)
2. Shake the toner cartridge well and insert
the cartridge. (Refer to the toner supply
guide decal on the front right cover.)
Toner Tank
Drum Protective
Sheet
Drum Stay
T/S Corona Unit
Lever
Charge Corona Unit
Drum Knob
Toner Cartridge
- 5 -

5. Perform the Drum Conditioning
(This operation must be performed after
developer and drum installation.)
1. Open the front right cover and move the
drum conditioning switch on the reverse
side of the operation panel to the left. Close
the front right cover and switch the power
on. (The Start key changes from red to
green after 2 min.)
2. Lower the platen cover and enter "99"
using the number keys and press the Start
key. (Drum conditioning takes about 5 min.)
3. After the drum conditioning is finished,
open the front right cover, move the drum
conditioning switch to the right and close
the front right cover.
4. Place the paper size actuator and size
decal on the cassette (A4 lengthwise or B5
lengthwise) and load paper into the
cassette.
5. Check the machine operation and copy
quality.
Drum Conditioning
Switch
- 6 -

2. OVERVIEW
2.1 SPECIFICATIONS..............................................8
2.2 GUIDE TO COMPONENTS................................9
- 7 -

2.1 SPECIFICATIONS
Items Specifications Remarks
Configuration Desk top
Copy Process Dry electrostatic transfer system
Originals Sheet/book
Original Size Maximum A3
Copy Paper Size Maximum A3, Minimum A6 Lengthwise
Copy Paper Weight 52 g/m2~ 157 g/m2F/L cassette: 64 ~ 90 g/m2
1st & 2nd cassette:
52 ~ 127 g/m2
By-pass feed: 52 ~ 157 g/m2
Copy Speed
Warm-up Time Less than 2 min.
First Copy Time 4.5 seconds/A4 sideways
Copy Number Input 1 to 99, Numeric key pad
Paper Feed Three Cassettes (including the front loading
cassette) + Bypass Feed Table Cassette: 250 sheets x 3
Bypass Feed: 50 sheets
Charge System Dual wire corotron system
Exposure System Slit exposure
(exposure lamp: 180 V, 320 W)
Reproduction
Ratios
Reproduction Ratio Change:
Full size ↔Reduction or
Enlargement:
Less than 3.5 seconds
Enlargement ↔Reduction:
Less than 5.0 seconds
Photoconductor Selenium-drum (F type)
Development
System Magnetic brush system
Image Density
Control Development Bias system + Exposure Control
System
Toner
Replenishment Cartridge exchange (300 g): oilless
Cleaning Type Cleaning blade and brush with PCC
Image Fusing Heat roll type (220 V, 800 W)
Image Transfer Corotron system
Paper Separation Dual wire ac corona and pick-off pawls
Quenching System Photo-quenching
Auto Clear All input modes are reset 60 seconds after the
copier is last used.
Power Source 220 V/50 Hz, 8 A
Power
Consumption Maximum: Less than 1.5 kW
Average: Warm-up 0.8 kW
Stand by 0.18 kW
Copy cycle 1.0 kW
Weight 79 kg
Dimensions 765 (W) x 666 (D) x 426 (H) mm
Peripheral
Equipment Sorter and Auto Document Feeder
Originals A3 B4 A4 B5 A4R B5R
Speed 20 23 34 37 26 30
Full Size 1 : 1
Reduction 93%, 87%, 82%, 71%, 61%,
50%
Enlargement 115%, 122%, 141%
Zoom 50%~200% in 1% steps
- 8 -

2.2 GUIDE TO COMPONENTS
1. Operation Panel
- 9 -

2. Indicator Panel
- 10 -

3. COPY PROCESS
3.1 COPY PROCESS DIAGRAM .............................12
- 11 -

3.1 COPY PROCESS DIAGRAM
Charge Corona Unit
Erase Lamp Exposure
Carrier
Toner
Development
Roller
ID Sensor
Pre-Transfer Lamp
Paper
Separation
Corona Wire
Transfer
Corona Wire
Pre-Cleaning
Corona (PCC)
Cleaning
Brush
Cleaning Blade
Quenching
Lamp
F TYPE
Photoconductor Drum
Pick-off Pawls
1. DRUM CHARGE
In the dark the charge corona unit gives a uniform
positive charge to the selenium drum. The charge
remains on the surface of the drum because the
photoconductive selenium has high electrical resistance
in the dark.
2. ERASE
The erase lamp illuminates the areas of the charged
drum surface that will not be used for the copy image.
The resistance of the drum in the illuminated areas
drops and the charge on those areas dissipates.
3. EXPOSURE
An image of the original is reflected onto the selenium
drum surface via the optics assembly. The charge on
the drum surface is dissipated in direct proportion to the
intensity of the reflected light, thus producing an
electrical latent image on the drum surface.
4. DEVELOPMENT
Negatively charged toner is attracted to the positively
charged areas of the drum, thus developing the latent
image. (The negative triboelectric charge is caused by
rubbing action between the carrier and toner particles.)
5. ID SENSOR
The main CPU checks toner density by directly sensing
the image density at the beginning of the first copy cycle
after the main switch is turned on, and at every 10th
copy after that.
6. PRE-TRANSFER LAMP (PTL)
The PTL illuminates the drum to remove all positive
charge from the exposed areas of the drum. This
prevents the toner particles from being reattracted to
the drum surface during paper separation and makes
paper separation easier.
7. IMAGE TRANSFER
Paper is fed to the drum surface at the proper time so
as to align the copy paper and the developed image on
the drum surface. Then, a strong positive charge is
applied to the reverse side of the copy paper, providing
the electrical force to pull the toner particles from the
drum surface to the copy paper. At the same time, the
copy paper is electrically attracted to the drum surface.
8. PAPER SEPARATION
A strong ac corona discharge is applied to the reverse
side of the copy paper, gradually reducing the positive
charge on the copy paper and breaking the electrical
attraction between the paper and the drum. Then, the
stiffness of the copy paper causes it to separate from
the drum surface. The pick-off pawls help paper which
has low stiffness to separate from the drum.
9. PRE-CLEANING CORONA (PCC)
The PCC applies a positive charge to any toner
remaining on the drum after image transfer. This
causes repulsion between the toner particles and the
drum and thereby makes cleaning more effective.
10. CLEANING
The cleaning brush removes part of the toner on the
drum and loosens the remainder. The cleaning blade
then scrapes off the loosened toner.
11. QUENCHING
The light from the quenching lamp, which is a cold
cathode tube, electrically neutralizes the surface of the
selenium drum.
- 12 -

4. SECTION DESCRIPTIONS
4.1 MECHANICAL COMPONENT LAYOUT............14
4.2 DRIVE LAYOUT
(INCLUDING PERIPHERALS) ...........................15
4.3 ELECTRICAL COMPONENT LAYOUT .............16
4.4 PAPER FEED AND REGISTRATION ................18
4.5 OPTICS...............................................................28
4.6 AROUND THE DRUM ........................................44
4.7 DEVELOPMENT AND TONER SUPPLY...........50
4.8 ID SENSOR AND PTL........................................62
4.9 IMAGE TRANSFER, PAPER SEPARATION
AND PAPER TRANSPORT................................71
4.10 CLEANING .......................................................75
4.11 FUSING.............................................................83
4.12 MISFEED CHECK ............................................89
4.13 PULSE GENERATOR ......................................90
4.14 OTHERS...........................................................91
- 13 -

4.1 MECHANICAL COMPONENT LAYOUT
1. 3rd Mirror
2. 2nd Mirror
3. 1st Mirror
4. Exposure Lamp
5. Exposure Glass
6. Hot Roller Stripper
7. Hot Roller
8. Main Motor
9. Transport Belt
10. Lens
11. Cleaning Unit
12. Quenching Lamp
13. Separation Corona Wire
14. Drum
15. Charge Corona Wire
16. Transfer Corona Wire
17. Erase Lamp
18. Development Unit
19. 4th Mirror
20. Feed Roller (By-pass Feed)
21. Toner Tank
22. Pick-up Roller
23. Pressure Lever
24. Pressure Roller
25. Front Loading Ass’y
26. Registration Roller
27. Feed Roller (F/L)
28. Relay Roller
29. Feed Roller (2nd)
30. Friction Pad
31. Feed Roller (1st)
32. 2nd Cassette
33. 1st Cassette
34. By-pass Feed Table
- 14 -

4.2 DRIVE LAYOUT (INCLUDING PERIPHERALS)
1234567
8910 11 12
13
14
15
16
17
18
19
20
21
2223
34
35
26
27
28
29
30
31
32
33
2425
1. DF Feed-out Roller
2. Feed-out Roller Drive Belt
3. Pulse Generator Sprocket/Toner
Supply Drive Gear
→34. Development Drive Gear
4. Drum Drive Pulley
5. Drum Drive Belt
6. Cleaning Drive Sprocket
7. 2nd Scanner Drive Pulley
8. Main Motor Sprocket
9. DF Transport Belt
10. DF Belt Drive Motor Gear
11. DF Feed Roller
12. Bin Transfer Wheel
13. Bin Support Rack
14. Bin Support Pinion Gear
15. Bin Drive Motor Gear
16. (Sorter Adapter) Feed Motor Pulley
17. Sorter Adapter Drive Belt
18. Fusing Exit Roller Gear
19. Fusing Drive Release Gear
20. Transport/Fusing Drive Sprocket
21. Cam Wheel
22. Cam Drive Gear
23. Cam Drive Sprocket
24. Main Drive Chain
25. Registration Clutch
26. F/L Feed Clutch
27. 2nd Cassette Feed Clutch
28. Relay Clutch
29. 1st Cassette Feed Clutch
30. By-pass Feed Clutch
31. Toner Supply Clutch
→35. Toner Supply Drive Gear
32. Scanner Motor Pulley
33. Scanner Drive Wire
- 15 -

4.3 ELECTRICAL COMPONENT LAYOUT
1
23456
7
8
9
10
11
12
13
14
15
16
17
18
19
20
21
22
23
24
25
26
27
28 29 30 31 323334 3536 37 38
1. Scanner Motor
2. By-pass Feed Clutch
3. Pulse Generator Sensor
4. 1st Cassette Paper End Sensor
5. By-pass Pick-up Solenoid
6. Feed Control Board
7. Operation Panel Board
8. 1st Feed Clutch
9. Total Counter
10. 2nd Cassette Paper End Sensor
11. Door Switch
12. Door Switch
13. 2nd Feed Clutch
14. Relay Roller Clutch
15. F/L (Front Loading) Feed Clutch
16. F/L Tray Paper End Sensor
17. Cleaning Solenoid
18. Main Power Relay
19. Main Switch
20. Power Supply Board
21. Lamp Regulator Board
22. Power Transformer
23. Main Fuse
24. Fusing Control Board
25. Noise Filter
26. Power Pack - T/S/PCC
27. Scanner Home Position Sensor
28. Lens Motor
29. Main Motor Capacitor
30. Lamp Stabilizer
31. ADF Control Board
32. 2nd Scanner Home Position Sensor
33. Pick-off Solenoid
34. 2nd Scanner Motor
35. Main Board
36. Registration Clutch
37. Power Pack - C/B
38. Toner Supply Clutch
- 16 -

3939
40
41
42
43
44
59
58
57
56
55
54
53
52
51
50 49
45
46
47
48
39. Exposure Lamp
40. Thermofuse
41. Fusing Exit Sensor
42. Fusing Thermistor
43. Main Motor
44. Vacuum Fan
45. Erase Lamp
46. ID Sensor Board
47. PTL (Pre-Transfer Lamp)
48. Registration Sensor Board
49. 2nd Cassette Paper Size Sensor
50. 1st Cassette Paper Size Sensor
51. By-pass Table Sensor
52. By-pass Paper End Sensor
53. Optics Cooling Fan
54. Drum Heater
55. QL (Quenching Lamp)
56. Lens Home Position Sensor
57. ADS Sensor
58. Fusing Heater
59. Exhaust Blower
- 17 -

4.4 PAPER FEED AND REGISTRATION
4.4.1 Mechanical Parts
1. Overview
In total this machine has four feed stations. They are three cassette feed stations
and a by-pass feed station.
The 1st and 2nd feed stations each use a size adjustable cassette, but the 3rd feed
station located inside the copier uses only an A3 cassette.
The capacity of each cassette is 250 sheets. The maximum paper capacity of the
by-pass feed station is 50 sheets.
All four feed stations use the feed roller and friction pad system. Only the by-pass
feed station uses a pick-up roller.
2. Feed System
1) Feed Roller
The CPU starts paper feed by energizing
the appropriate paper feed clutch (the
paper feed clutches are all magnetic
clutches).
The CPU turns on the paper feed clutch for
the required station, at a programmed time
after the Start key is pressed.
Upon receiving the signal from the
registration sensor, the CPU turns off the
paper feed clutch.
2) Friction Pad Feed System
When a cassette is inserted into the copier, the friction pad contacts the feed
roller (in the by-pass feed station, it always contacts the feed roller). The friction
pad holder is mounted on one end of the swivel plate with a swivel screw, so it
automatically applies even pressure against the feed roller and the copy paper.
The coefficients of friction are µ1 > µ2 > µ3.
Feed Roller
1st Feed Clutch
Friction Pad
2nd Feed
Clutch
The coefficient of friction between
the friction pad and paper.
<Single sheet
feeding> <Multiple sheet
feeding>
Feed Roller
µ1
µ2
µ1µ3
µ2
- 18 -

3. Paper End Detection and Paper Size Detection
1) Paper End Detection
This machine uses a photointerrupter
sensor for paper end detection. The paper
end actuator, which is on the same shaft as
the paper end feeler, pivots into the sensor.
2) Paper Size Detection
Paper size is detected by an array of five
photointerrupters in the cassette entrance.
The paper size sensors are actuated by a
plate on the front of the cassette. Each
paper size has its own unique combination
of notches in the actuator plate.
(For the front loading feed station, if paper
is detected, the copier automatically
detects A3 size. The A3 cassette has a
paper size actuator in case it is used in the
1st or 2nd feeding station for some reason.)
Size Detection Code
A3 B4 A4 A4R B5 B5R A5 A5R B6 B6R
1●●❍●❍●❍●❍●
2❍●❍❍●●❍❍●●
3❍❍●●●●❍❍❍❍
4❍❍❍❍❍❍●●●●
5❍❍❍❍❍❍❍❍❍❍
Detected: ❍
Not detected: ●
Other sizes are indicated as ❋on the
operation panel.
Paper Size Sensor
Actuator Plate
- 19 -
Table of contents
Other Ricoh Copier manuals

Ricoh
Ricoh 8700W User manual
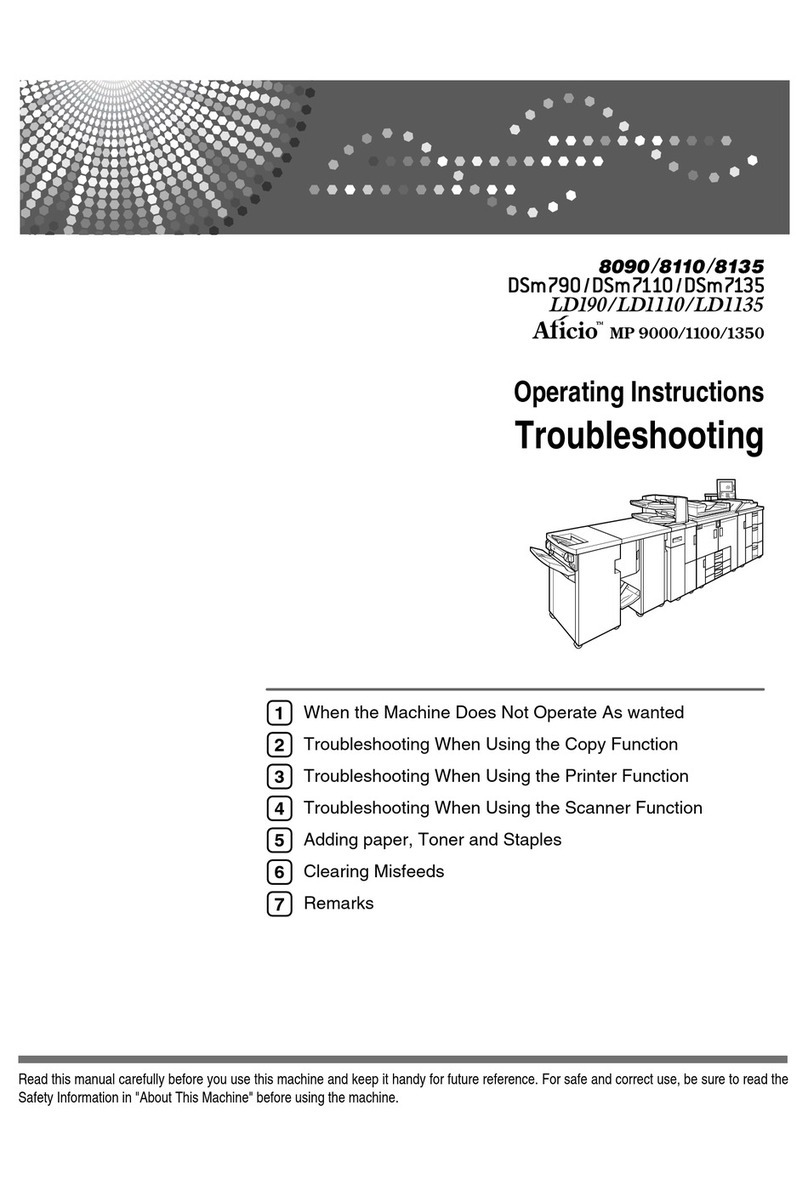
Ricoh
Ricoh feeder User manual

Ricoh
Ricoh Aficio FX10 User manual
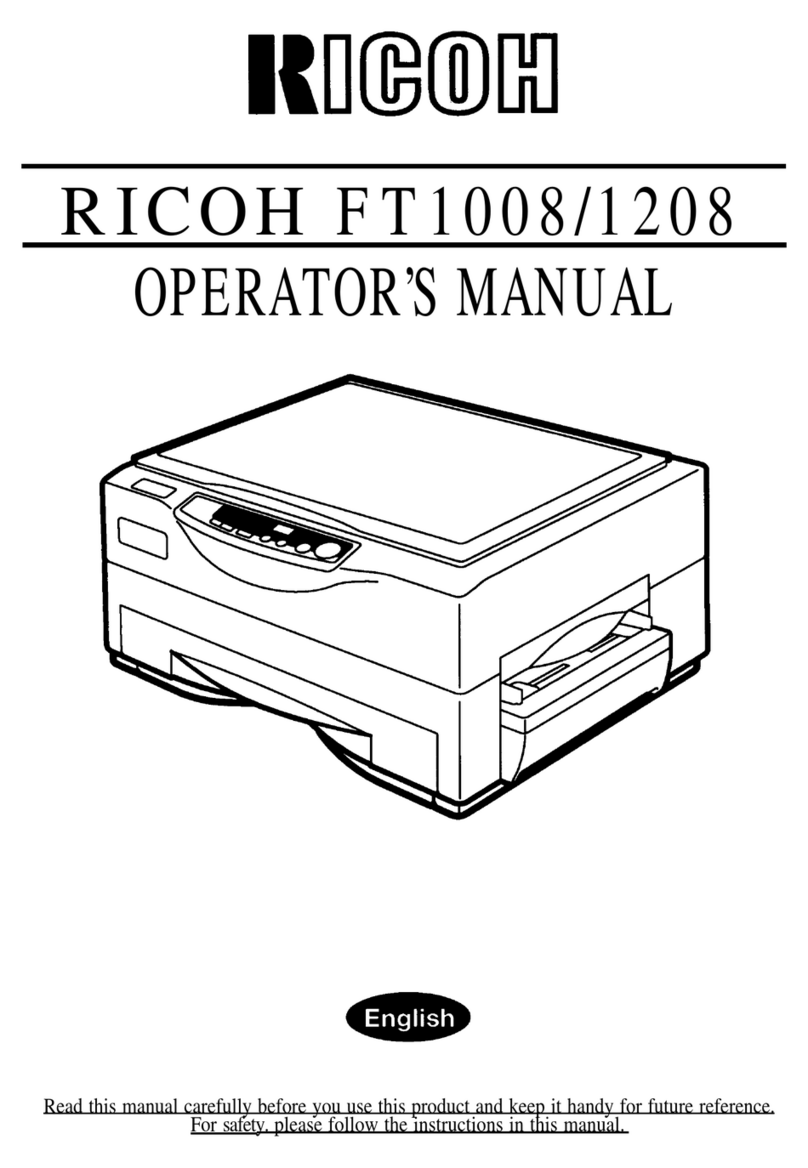
Ricoh
Ricoh FT 1008 User manual

Ricoh
Ricoh FT5580 User manual

Ricoh
Ricoh Aficio C3002 User manual

Ricoh
Ricoh 920F User manual
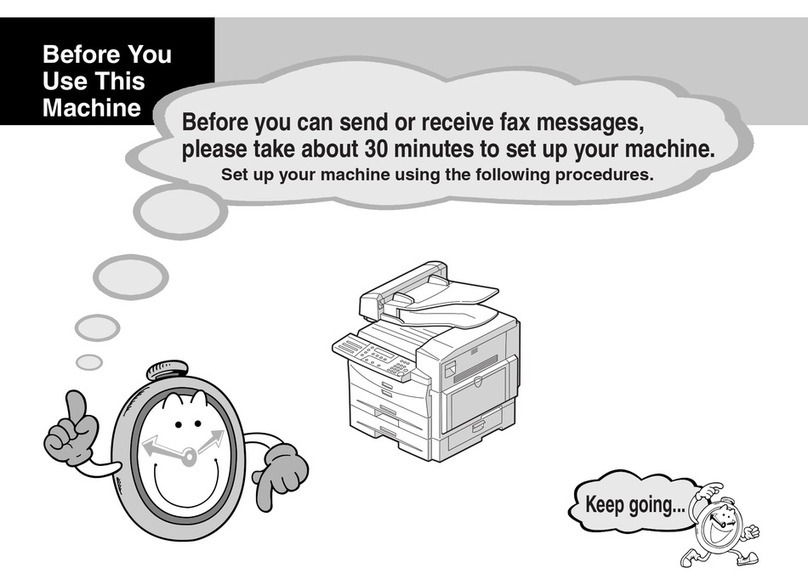
Ricoh
Ricoh aficio 1013 User manual

Ricoh
Ricoh A-C4 User manual
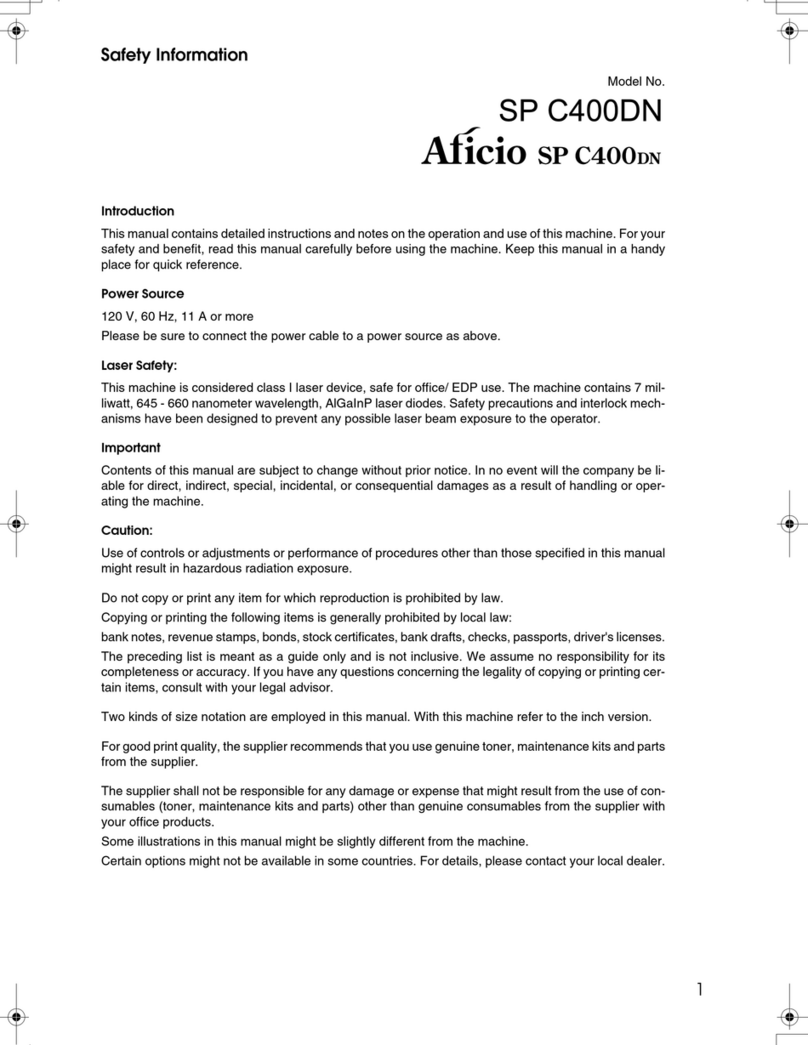
Ricoh
Ricoh Aficio SP C400DN User manual