Ross HBH Series User manual

HBH Series
Redundant Valve Systems
Hydraulic Block & Stop
Safety Valves
Operating Instructions
RC-HBH-OI EN
Cat. 3
PL d SIL 2
Functional Safety
Pending
Pending
www.rosscontrols.com

HBH Series Operating Instructions
2www.rosscontrols.com
PRODUCT LABEL IDENTIFICATION
SCHEMATIC
X
B
Y
A
C
Z1 Z2 X
B
Y
A
CZ1
Z2
2
1
2
1
PABT
PA B T
G G
2A
P1 P2
2B
MP1 MP2
5A 5B
3B
Y
3A
M-M
XX
Y
WIRING DIAGRAM
Inductive Position Switch Connector
1 = Supply +24 volts DC
2 = Output Signal NC
3 = Ground
4 = Output Signal NO
NO NC
1
4
3
2
Valve Type
Double
Revision
Level
Voltage
24 volts DC
Series
Communication
None
Material Type
Ductile Iron
Seal Type
Buna-N
Monitoring
External
HBH D D XX 682F B A E X A
Pressure Relief
No Pressure Relief Valve
Body Size Flow Rate Port Size Port Type
25 0 to 90 gpm
1-1/2 Code 62 Flange 682F
2Code 62 Flange 692F
32 0 to 145 gpm
2Code 62 Flange 792F
PRODUCT KEY IDENTIFICATION

HBH Series Operating Instructions
www.rosscontrols.com 3
Body Size 25
Port Size 1-1/2
Ports List
ID Name
P1 1.500 MT 62
P2 1.500 MT 62
X SAE # 6
Y SAE # 6
MP1 SAE # 6
M-M SAE # 6
MP2 SAE # 6
Body Size 32
Ports List
ID Name
P1 2.000 MT 62
P2 2.000 MT 62
X SAE # 6
Y SAE # 6
MP1 SAE # 6
M-M SAE # 6
MP2 SAE # 6
MOUNTING INFORMATION AND OVERALL DIMENSIONS (inches/mm)
Inductive Position
Switch Connector
Solenoid
Connector
C
E
14.2 [360]~
(4X)
M12 X 1.75
M10 X 1.5 LIFTING BOLT HOLE
(4X)
M12 X 1.75
(4X)
M16 X 2.0
9.2 [234]~
10.00 [254.0]
1.75 [44.5]
4.13 [104.8]
6.00 [152.4]
0.69 [17.5]
3.00 [76.2]
5.25 [133.4]
6.00 [152.4]
2.25 [57.2]
7.75 [196.9]
10.00 [254.0]
0.50 [12.7]
5.50[139.7]
6.00 [152.4]
0.50 [12.7]
5.50 [139.7]
6.00 [152.4]
0.50[12.7]
9.50 [241.3]
10.00 [254.0]
3.13 [79.4]
BOTH ENDS
1.44 [36.5]
BOTH ENDS
D
(4X)
M16 X 2.0
Inductive Position
Switch Connector
Solenoid
Connector
4.09 [104.0]
6.00 [152.4]
3.00 [76.2]
6.00 [152.4]
13.8 [ 349.4]
~
9.2 [233.7]~
10.00 [254.0] 1.00 [25.4]
5.00 [127.0] 0.50 [12.7]
(4X)
M12 X 1.75
12.00 [304.8]
(4X)
M20 X 2.50
(4X)
M20 X 2.50
(4X)
M12 X 1.75
2.25 [57.2] 7.50 [190.5]
0.50 [12.7] 5.00 [127.0]
7. 8 [19 7.0 ]~
1.2 [31.4]~
1.75 [44.5]
BOTH ENDS
3.81 [96.8]
BOTH ENDS
Inductive Position
Switch Connector
Solenoid
Connector
C
D E
14.2 [360]
~
(4X)
M12 X 1.75
M10 X 1.5 LIFTING BOLT HOLE
(4X)
M12 X 1.75
(4X) M20 X 2.5
(4X)
M20 X 2.5
9.2 [234]~
10.00 [254.0]
1.75 [44.5]
4.13 [104.8]
6.00 [152.4]
0.69 [17.5]
3.00 [76.2]
5.25 [133.4]
6.00 [152.4]
2.25 [57.2]
7.75 [196.9]
10.00 [254.0]
0.50 [12.7]
5.50 [139.7]
6.00 [152.4]
0.50 [12.7]
5.50 [139.7]
6.00 [152.4]
0.50 [12.7]
9.50 [241.3]
10.00 [254.0]
1.75 [44.5]
BOTH ENDS
3.81 [96.8]
BOTH ENDS
Ports List
ID Name
P1 2.000 MT 62
P2 2.000 MT 62
X SAE # 6
Y SAE # 6
MP1 SAE # 6
M-M SAE # 6
MP2 SAE # 6
Body Size 25
Port Size 2

HBH Series Operating Instructions
4www.rosscontrols.com
1. About this Documentation
These instructions contain important information for the safe and appropriate assembly
and commissioning of the product.
fRead these instructions all the way through, particularly section 6 “Notes on
Safety,” before working with the product.
For more information see last page for contact information, or visit www.rosscontrols.com.
fIn addition, observe all applicable local and national regulations on accident
prevention and on environmental protection.
1.1. Warning Notices in these Operating Instructions
In these operating instructions, warning notices precede sections with handling
requirements which incur risks of personal injury or material damage.
Warnings are structured as follows:
SIGNAL WORD
Type or source of hazard!
Consequences
fMeasures to avert danger
• Warning triangle: Indicates a risk of fatal or severe injuries.
• Signal word: Indicates the severity of the danger.
• Type or source of hazard: States the type of danger or the source of the hazard.
• Consequences: Describes possible consequences of ignoring the warning.
• Measures to avert danger:Indicates how to avoid the danger. It is essential that
the measures to avert danger are complied with.
DANGER
Indicates an imminent and serious danger that will result in severe
or even fatal injury if you fail to avoid it.
WARNING
Indicates a possible danger that could result in severe or even fatal
injury if you fail to avoid it.
CAUTION
Indicates a danger that may result in minor to moderate injuries if
you fail to avoid it.
ATTENTION
Indicates potential property damage that may be incurred by the
product or its surroundings if you fail to avoid it.
2. Product Identication
The valve assembly is marked with Model Number, Revision level, and a serial number
which can be used to identify date of manufacture and location. Please contact ROSS
Controls for further information.
Product label identification & product key identification example, see page 2.
3. Prerequisites for Use of the Product
fMake these operating instructions available to the engineer and assembly
technician of the machine/system in which the product will be used.
fKeep these operating instructions for the entire product life cycle.
3.1. Qualied Personnel
Assembly, installation, commissioning, maintenance, and decommissioning should
only be carried out by qualied personnel that have the required knowledge of and
experience in dealing with electrical and hydraulic control technology.
All work may be performed only by properly trained and qualied individuals who have
been specically instructed for the tasks assigned to them. The levels of responsibility
of personnel are to be clearly delineated by the owner/operator. Protective clothing
and gear is to be worn when performing all work. The relevant safety and accident
prevention regulations are to be adhered to. Any special safety requirements specied
in the documentation for the unit/system are to be complied with.
4. Package Contents
Items included:
• Block & Stop control valve system
• Operating instructions
5. Service, Repair, and Maintenance
fIn case of technical problems or a required repair, please contact your local
ROSS®representative.
fChecks should be conducted once a month to ensure valves are in functioning order.
5.1. Maintenance
WARNING
- All activities of maintenance must be conducted by competent and qualied staff
- Always depressurize the relevant part of the system before any maintenance
operation on the hydraulic system.
When/if a valve is replaced; a basic functional test should be performed (see 8.1 Test
Procedure).
It is important that all the check-up operations, even if simple, are programmed and
reported on specic maintenance program schedules.
Before the inspection, cleaning should be undertaken if necessary.
WARNING
- Always ensure cleanliness when working on the HBH Valve.
- Do not perform maintenance with the equipment functioning!
- Penetrating dirt and liquids will cause faults!
- Safe function of the HBH valve is not ensured when operated with contaminated uid.
- Certain solvents and aggressive cleaning agents or detergents may damage the
seals on the HBH valve and make them age faster.
- Never use solvents or aggressive detergents as these can cause damage to the
hydraulic system and seals!
- The water pressure of a high-pressure cleaner can damage the seals of the HBH valve.
- Do not use a high-pressure cleaner.
- Pay attention to prevent detergent penetration into the HBH valve.
- Check that all seals and electrical plug connections are rmly tted to prevent the
penetration of detergents.
6. Notes on Safety
The product has been manufactured according to the accepted rules of current
technology. There is risk of injury or damage if the following safety instructions and
warnings given in this instruction manual are not observed.
6.1. Intended Use
The HBH Series Block & Stop Control systems are safety components designed and
manufactured in accordance with Machinery Directive 2006/42/EC.
The HBH system is comprised of two single valves which make it a redundant design
for meeting the needs and requirements of safe hydraulic Block & Stop applications.
Typically, these systems are designed to meet Category 3, PL d, SIL 2 applications if
properly implemented into the safety control & monitoring system.
The HBH Series Block & Stop system is designed to allow the ow of hydraulic uid
into or out of a cylinder or to block the ow in order to stop cylinder motion (Block &
Stop) when needed.
During normal operation, the HBH system is held actuated, allowing the ow of
hydraulic uid through the HBH unit from inlet to outlet. In a situation when immediate
pressure and ow shut-off is needed, the HBH Series Block & Stop system can be
turned off to provide an immediate ow and pressure blocking action.
The HBH Series Block & Stop systems are designed to be externally monitored by a
safety control & monitoring system for safe, redundant operation of the valves. Each
single valve is equipped with a PNP inductive position switch. Monitoring both of these
switches on each actuation and de-actuation of the HBH Block & Stop system provides
a diagnostic coverage of up to 90%. Monitoring of these switches must be done by an
external monitoring system.
The unit cannot be used by itself. It is designed for installation in a machine. ROSS
and its suppliers will assume no liability in the event that the system or parts thereof
are not used in accordance with their designated use or if modications are made in
a non-authorized manner.
Any drawings, hydraulic or electric circuit diagrams, parts lists and acceptance
certicates (inspection reports) supplied do not form a part of these operating
instructions. They are supplied for the purpose of illustrating the unit or procuring parts.
6.1.1. Safety Function According to ISO 13849 and EN 692
The Machinery Directive has a dual objective: to permit the free movement of
machinery within the internal market while ensuring a high level of protection of health
and safety. A hydraulic valve system designed and specied as being capable of
performing a safety function as well as normal production use is a “safety component”
where other parts of the denition are met. However, a similar valve where the
manufacturer markets it only for normal production use would not be considered a
safety component.
HBH Block & Stop systems are designed in accordance with the requirements listed
in ISO 13849-1 and -2. Their “fail-to-safe” safety function is ensured even in case of
a fault within the valve (e.g., caused by power loss, wear, contamination, or similar
situations).
The safety function of the HBH Series Block & Stop system is to only supply ow
into a cylinder or designated portion of the hydraulic machine/system when the two
valve elements are actuated simultaneously, but to block the ow in both directions
when both valves are shut-off or if only one of the two valves is de-actuated. A fault
in the system where only one valve actuates when switching on or only one de-
actuates when switching off prevents ow of hydraulic uid from moving downstream
or upstream. Monitoring of the two inductive position switches by the user’s external
safety control & monitoring system makes it possible to detect these fault situations
and to shut off and prevent further electrical energization of the solenoids.

HBH Series Operating Instructions
www.rosscontrols.com 5
Port identication on the manifold according to ISO 16874
The HBH Series Block & Stop system is designed and manufactured in accordance
with the identication requirements laid out in the ISO 16874:2004 standard.
6.1.2. Common Cause Failure – CCF
The product has been engineered and manufactured according to the fundamental and
proven safety principles of ISO 13849-1:2015 and -2:2012.
Common Cause Failures (CCF) are failures of different components, resulting from
a single event. CCF are not to be confused with cascading faults or common mode
faults. Common cause failures can cause loss of the safety function, especially in dual
channel circuits where both channels could fail simultaneously due to a single event.
6.1.3. Critical failure modes and causes:
• Failure of the safety function - caused by simultaneous incomplete return of both
solenoid pilot valves (3A and 3B) or main cartridge valves (2A and 2B).
• Maintain hydraulic uid quality, i.e., proper ltration.
• Operate within prescribed temperature limits.
• Install the valve such that the normal stroke travel of the valve elements is
perpendicular to the main direction of machine vibration and/or mechanical shock.
• Avoid external magnetic elds.
6.1.4. Diagnostic Coverage
A diagnostic coverage of 90% is achievable through appropriate integration of the
HBH Series Block & Stop system into the safety control system. The monitoring
system must check for the proper change of state of each valve’s inductive position
switch (Switch 2A & Switch 2B) with each change of state of the safety control system
outputs to the valve solenoids (Sol 3A & Sol 3B). Detection of a fault by the safety
control & monitoring system must trigger a shut-off of the safety controller’s outputs to
the valve solenoids (Sol 3A & Sol 3B).
6.1.5. Fault Modes
Note that normal operation requires that Sol 3A & Sol 3B be energized simultaneously
for switching the HBH Series Block & Stop system on, and de-energizing both Sol
3A and Sol 3B simultaneously for switching the HBH Series Block & Stop system off.
NOTE: The switches are supplied with both NC and NO contacts. The statements
below only refer to whether or not the switches are actuated.
Faults that could occur during normal operation are:
Sol 3A & Sol 3B energized simultaneously
Switch 2A ON, Switch 3A OFF
Switch 2A OFF, Switch 3A ON
Switch 2A OFF, Switch 3A OFF
Sol 3A & Sol 3B de-energized simultaneously
Switch 2A ON, Switch 3A OFF
Switch 2A OFF, Switch 3A ON
Switch 2A ON, Switch 3A ON
6.1.6. Foreseeable Misuse
WARNING
Risk of Injury!
Misuse may result in injury or damage.
fThe product must be used exclusively as intended.
Foreseeable misuse includes:
• Bypassing the safety function or diagnostics.
• Replacing the safety valves with unauthorized valves.
• Tampering with the position switches.
• Failing to utilize the position switches to verify valve operation on every cycle -
when energizing and de-energizing.
• Allowing continued operation of the valve when one or both valve shifted signals
(from position switches) are not conrmed.
• Operating at pressures above maximum operating pressure.
6.2. Responsibilities of the System Owner
Observation of general requirements pertaining to hazards:
• Unusual noises, vibration, defects or damage is to be remedied immediately as it
may point to potential hazards.
• Generally speaking, no maintenance work may be done on the hydraulic system
and power units as long as they are under hydraulic pressure or the power supply
has not been switched off.
• Prior to performing any maintenance work, pressure accumulators are to be
depressurized.
• The hydraulic system has to be depressurized at any time work is done on the gas
side of an accumulator.
• Note the load pressures present. Also note any loads applied. If necessary, make
sure that the loads are secured or properly supported.
• Hydraulic systems may only be operated by properly trained and instructed
personnel.
• All safety devices and equipment are to be checked to see that they function
properly.
• The setting of pressure relief valves featuring a tamper-resistant seal may not be
changed.
• Safety devices and equipment may not be removed, deactivated or circumvented
owing to the accident hazard posed by this action.
• General safety and accident prevention regulations pertaining to operating the
unit/system are to be adhered to.
• Comply with the further requirements of ISO 13849 (e. g., MTTFD, CCF, DC, PLr,)
if you intend to use the product in higher categories (2 or 3).
• Check the valve at least once a month to ensure its proper operation.
• Make sure that the fundamental and proven safety principles in accordance with
ISO 13849 for implementation and operation of the component are complied with.
• Selection and installation of replacement valves must take place in accordance
with the manufacturer’s specications.
6.3. Safety Instructions
The HBH Block & Stop System features a state-of-the-art design. Reliable and safe
operation cannot be ensured unless all the instructions, settings and output limits
applicable to the unit supplied are adhered to.
The systems involved are pressure-generating systems whose components feature
pressurized liquid; consequently, the systems may pose a hazard if not dealt with properly.
6.3.1. Additional Safety Considerations
• When implementing surge suppression measures, be sure to check whether or
not this extends the valve system shut off response time which could extend the
machine stopping time.
• In case of high levels of machine vibration, use appropriate vibration-reducing
elements when installing the valve system.
• Supply the proper voltage as overvoltage situations can result in solenoid burnout.
7. Assembly and Installation
CAUTIONS
Risk of injury due to installation while pressurized or with live parts!
Installation while pressurized or with electrical power switched on can result in injuries due to
sudden pressure build-up or electric shock.
fInstallation while pressurized or with electrical power switched on can result in injuries
due to sudden pressure build-up or electric shock.
fDe-energize and de-pressurize the relevant system parts before installing the valves.
fSecure the system to prevent it from being switched back on again.
ATTENTION
Destruction of components!
Chemical substances can damage the surface, the markings and the seals of the device.
fInstall the valve such that it is protected against the effects of chemicals.
Damage to the device through storage at incorrect temperatures!
The storage temperature represents the permissible ambient temperature and depends on the
type of valve in question.
fObserve the temperature information in chapter 10 “Technical Data.”
7.1. Installation Instructions
Secure the system using the through holes in the manifold. Refer to pattern for the
required dimensions, - see dimensional drawings on page 3.
7.1.1. Component Inspection: Prior to use, a careful examination of the
HBH valve system must be performed. The HBH valve system must be checked for
correct style, size, catalog number and external condition, and must be examined
for cleanliness, absence of external defects or gouges or otherwise deformed
parts or other imperfections. DO NOT use any item that displays any signs of
nonconformance. Any accessory including, but not limited to, ttings, bolt kits,
hoses, sub-bases, manifolds and electrical connectors must be subjected to the
same examination.
7.1.2. Filtration: Fluid cleanliness is a necessity in any hydraulic system. Fluid
lters need to be installed and maintained in the system to provide the required level
of cleanliness. Filters can be placed in the inlets.
7.1.3. Accessory Ratings: All accessories used in combination with the
selected or intended HBH valve system must be used in accordance with the HBH
specications.

HBH Series Operating Instructions
6www.rosscontrols.com
7.2. Electrical Connections
Install the electrical connectors (EN 175301-803 Form A type, pre-wired or non-
prewired) for both the valve solenoids.
Install the inductive position switch connectors (M12, 5-pin, A-coded) on each valve
and follow the electrical wiring schematic of the switch on page 2.
8. Commissioning and Operation
CAUTIONS
Damage to health due to loud noise!
Levels above 70 dB(A) may lead to damage to health!
fAlways wear ear protectors when working on the product.
Before commissioning, the installation must be carefully inspected by a qualied,
trained professional.
Make sure that the technical specications match the operating criteria of the machine
and/or the hydraulic system.
8.1. HBH Test Procedure for Valve Operation
NOTE 1: This valve test procedure only checks for proper function of the
HBH valve system. Please refer to the HBH Integration Guide for the External
Monitoring Validation Procedure.
NOTE 2: The valve test procedure requires fault simulation. It will be necessary
to induce faults electrically by disabling a different solenoid or switch at different
times. This will be most easily done by disconnecting solenoid or switch cables
at the valve.
NOTE 3: The PNP position switches are supplied with both NC and NO contacts.
NOTE 4: “-” indicates no change from the previous step.
Step Action Sol 3A Sol 3B
Flow
P1 to P2
Switch Conditions Pass/Fail
Switch 2A Switch 2B
YES/NO? (NC) (NO) (NC) (NO) (P/F)
1Energize
solenoid 3A ON OFF NO OPEN CLOSED CLOSED OPEN
2
De-energize
both
solenoids
OFF OFF NO CLOSED OPEN - -
3Energize
solenoid 3B OFF ON NO - - OPEN CLOSED
4
De-energize
both
solenoids
OFF OFF NO - - CLOSED OPEN
5
Energize
both
solenoids
3A & 3B
ON ON YES OPEN CLOSED OPEN CLOSED
6
De-energize
both
solenoids
OFF OFF NO CLOSED OPEN CLOSED OPEN
8.1. Limitations Due to System Leakage
Even though the HBH is designed to redundantly block ow, it is important to
periodically test for leakage within the HBH and the system it controls, as any leak
within the HBH itself, interconnecting hoses, connectors, cylinders or other actuators,
or even other valves in the circuit may cause unexpected movement. In order to
test for leakage within the HBH itself, it is necessary to check for actuator (cylinder)
movement when the HBH is in each of the following conditions:
WARNING
Performing this test could cause injury or damage to equipment due to unexpected or
uncontrolled movement. Take all necessary precautions to ensure worker safety prior to
initiating this test.
A) fully de-energized (both solenoids 3A & 3B de-energized)
B) solenoid 3A energized with solenoid 3B de-energized
C) solenoid 3A de-energized with solenoid 3B energized.
Depending on the application, it may be necessary to preposition actuators and/or
other valves such that energizing the HBH would allow motion to occur. This sets up
the circuit so that the HBH valve is the sole motion-controlling device during testing.
For example, if a cylinder is fully retracted, a leak that normally allows retract motion to
occur could be masked because the cylinder is already fully retracted.
This test helps to troubleshoot leaks within the HBH system. Other leaks within the
associated system can affect the outcome of this test.
WARNING
If any leakage is discovered within the system, measures should be taken to eliminate the
leak(s) as failing to do so could limit the ability of the safety system to safely stop motion
when required.
WARNING
Continued operation of the system without periodic leakage inspections can lead to unexpected
movement.
WARNING
Unexpected movement could occur if one of the check valves in the pilot system, including
any check valve installed in the external pilot supply line, were to fail open. A failure of one
of these check valves could allow as much as 10 gpm ow from P1 to P2, P2 to P1 or P2 to
X (external pilot port). The amount of ow could be higher from P2 to X when using external
pilot supply depending on the ow capability of the check valve that the user installs in that
line or, especially, if no check is installed in the external pilot line.
9. Disconnecting and Removal
CAUTIONS
Risk of injury due to installation while pressurized or with live parts!
fDisconnecting a hydraulic component while the system is pressurized or while electrical power
is supplied can result in injury or death due to sudden pressure release, unexpected movement,
or electric shock.
fIsolate and lock out the electrical and hydraulic systems before disconnecting the unit.
10. Technical Specications
Construction Design Poppet type with spool type pilot valves
Actuation
One solenoid per valve element
Solenoids must be operated synchronously
Solenoid Pilot Operated, spring return
Mounting Type: In-line
Orientation: Any, preferably horizontal
Solenoids
Version as per VDE 0580. Rated for continuous duty.
Electrical connection according to EN 175301-803 Form A.
Enclosure rating according to DIN 400 50 IP 65.
Standard Voltages 24 volts DC
Power Consumption (each solenoid) 30 watts
Inductive Position Switch (2 per system) PNP (M12, 5-pin, A-coded)
Maximum Current (each switch) 400mA maximum
Temperature Range (recommended) Ambient: -4° to 160°F (-20° to 71°C)
Media: -4° to 140°F (-20° to 60°C)
Flow Media
Hydraulic Fluids:
Mineral Oil HLP, HL-DIN 51524
Vegetable Oil HETG - VDMA 24568
Inlet Pressure
5000 psi (344 bar)
Construction Material
Valve Body & Manifold: Ductile Iron
Spool: Steel
Seals: Buna-N
Technical Characteristics Of PNP Inductive Position Switch
Type Of Switch Contactless inductive position switch with integrated amplifier
Supply Voltage [V] 20-32 V DC
Ripple Max [%] ≤ 10
Max Current [mA] 400

HBH Series Operating Instructions
www.rosscontrols.com 7
Reaction Time [ms] 15
Max Peak Pressure [bar] 400
Mechanical Life Virtually Infinite
Switch Logic PNP
1supply + 24 V DC
4NO output signal
2NC output signal
3GND
OUTPUT SIGNAL STATUS FOR EACH VALVE IN THE HBH SYSTEM
Hydraulic configuration
ON
OFF
ON
OFF
Spool position
Pin 2
Pin 4
S
Note: PNP Position Switch can be electrically wired by the consumer as NO or NC and then the status
of the output signal will be in accordance to the selected configuration.
= Intermediate spool position corresponding to the hydraulic configuration change.
STATUS OF OUTPUT SIGNAL
A: overlapping stroke
B: damping stroke
According to the criteria of safety specications, the
poppet position signal must change state during the
overlapping stroke (before the effective valve opening.)
WARNING
Risk of Injury!
Misuse may result in injury or damage.
fThe product must be used exclusively as intended.
1. Failure to observe the prescribed procedures and cautions may represent a risk for personal
injury.
2. Safety valves must only be installed by qualied personnel.
3. Safety valves must not be disassembled.
4. The inductive position switches can only be adjusted by the valve manufacturer.
5. Valve components cannot be interchanged.
6. The valves must operate without switching shocks or spool vibration.
7. There is a small portion of the main cartridge overlap stroke that may be undetectable and
may allow ow if the other main cartridge is in the open position. This could be as much as
15 gpm on size DIN 25 and 18 gpm on size DIN 32.
8. Check valves are used in the pilot supply system to ensure that the highest available pres-
sure within the HBH system is supplied to the pilot valves. A failure of one of these check
valves to close could allow as much as 10 gpm ow from P1 to P2, P2 to P1, or P2 to X
(external pilot port).
9. It is recommended that a check valve be installed in the X (external pilot supply port) to help
prevent ow from P2 to X when pressure in P2 is higher than the pressure in X.
11. Disposal
Dispose of the valve in accordance with the applicable statutory regulations in your
country.

AmericAs
U.S.A.
ROSS CONTROLS
+1-248-764-1800
sales@rosscontrols.com
www.rosscontrols.com
Customer Service
1-800-GET-ROSS (438-1800)
Technical Service
1-888-TEK-ROSS (835-7677)
Canada
ROSS CANADA
+1-416-251-7677
sales@rosscanada.com
www.rosscanada.com
6077170 CANADA INC.
AnIndependent RepResentatIve
Brazil
ROSS BRASIL
+55-11-4335-2200
vendas@rosscontrols.com
www.rosscontrols.com.br
europe
Germany
ROSS EUROPA GmbH
+49-6103-7597-100
sales@rosseuropa.com
www.rosseuropa.com
United Kingdom
ROSS UK Ltd.
+44 (0)1254 872277
sales.uk@rosscontrols.com
www.rossuk.co.uk
France
ROSS FRANCE SAS
+33-1-49-45-65-65
sales@rossfrance.com
www.rossfrance.com
AsiA & pAcific
Japan
ROSS ASIA K.K.
+81-42-778-7251
custsvc.ra@rosscontrols.com
www.rossasia.co.jp
India
ROSS CONTROLS INDIA Pvt. Ltd.
+91-44-2624-9040
sales.ri@rosscontrols.com
www.rosscontrols.com
China
ROSS CONTROLS (CHINA) Ltd.
+86-21-6915-7942
sales.cn@rosscontrols.com
www.rosscontrolschina.com
United Kingdom
PNEUMATROL
+44 (0)1254 872277
sales@pneumatrol.com
www.pneumatrol.com
U.S.A.
AUTOMATIC VALVE
+1-248-474-6700
avc@automaticvalve.com
www.automaticvalve.com
U.S.A.
ROSS DECCO
+1-248-764-1800
decco.sales@rosscontrols.com
www.rossdecco.com
Germany
manufactIS
+49 (0)201 316843-0
info@manufactis.net
www.manufactis.net
Printed in the U.S.A. – Rev. 11/10/20, © 2020 ROSS CONTROLS®. All Rights Reserved. Content subject to change. Form RC-HBH-OI
ROSS CONTROLS compAnies
Table of contents
Other Ross Control Unit manuals
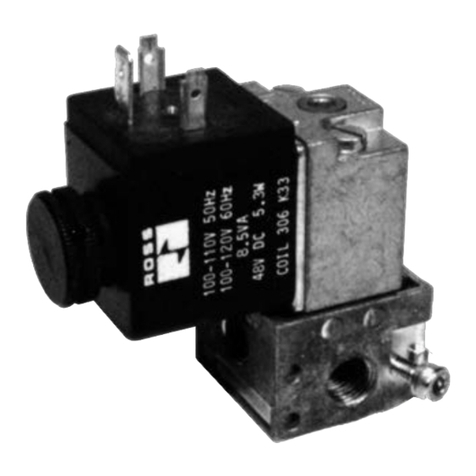
Ross
Ross W14 Series User manual
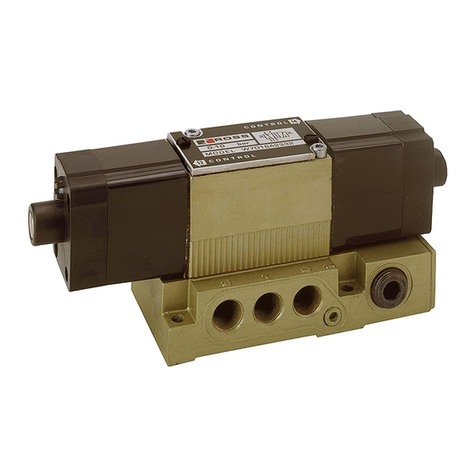
Ross
Ross W70 Series User manual

Ross
Ross CrossMirror CM26 Series User manual

Ross
Ross CrossMirror 77 Series User manual

Ross
Ross HDBH Series User manual

Ross
Ross SideBox Manual
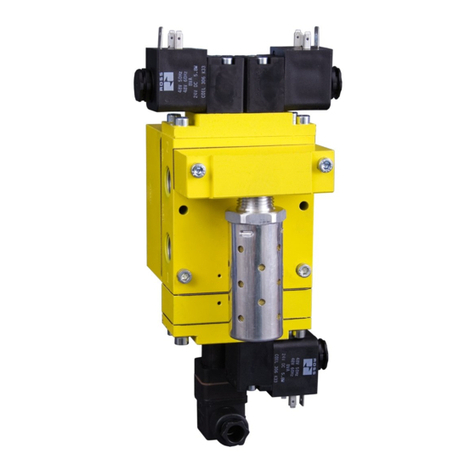
Ross
Ross DM2E User manual
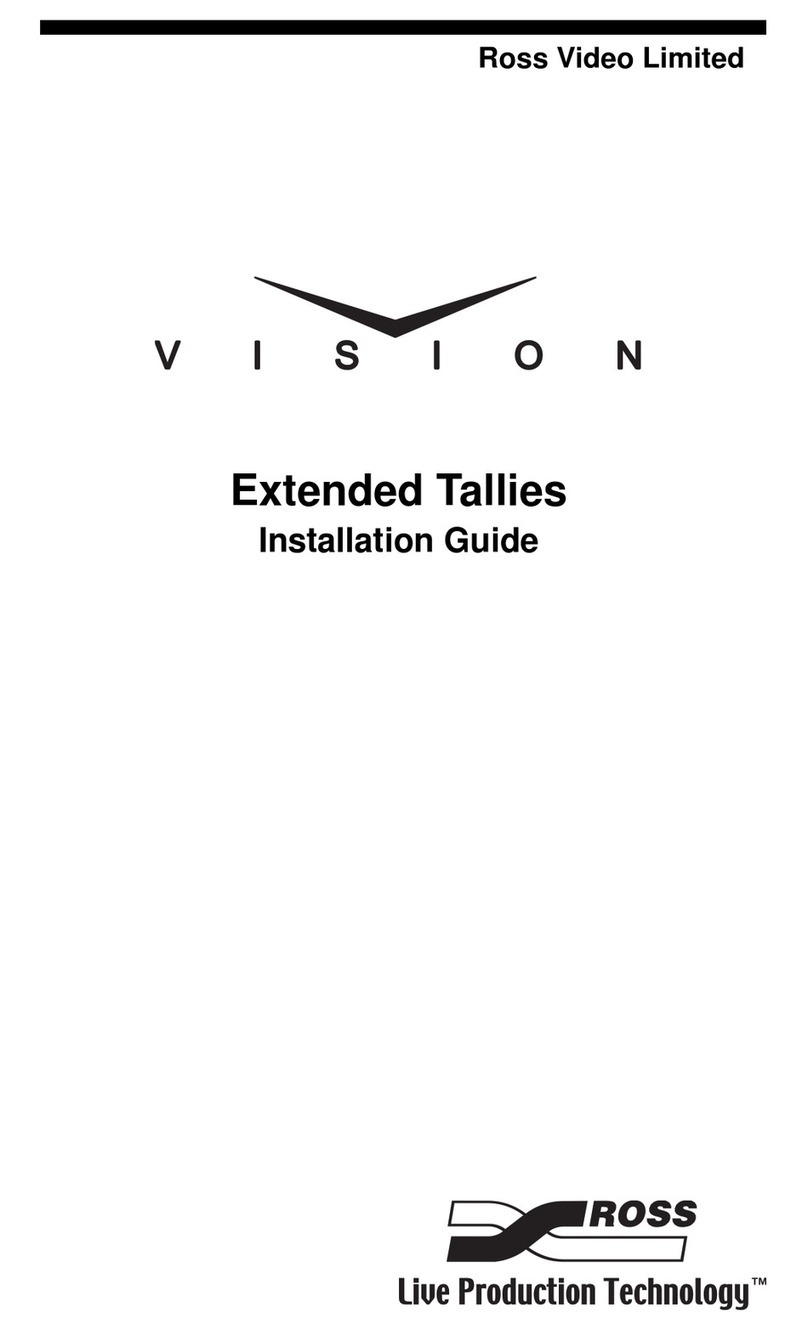
Ross
Ross Vision 4800DR-332-02 User manual
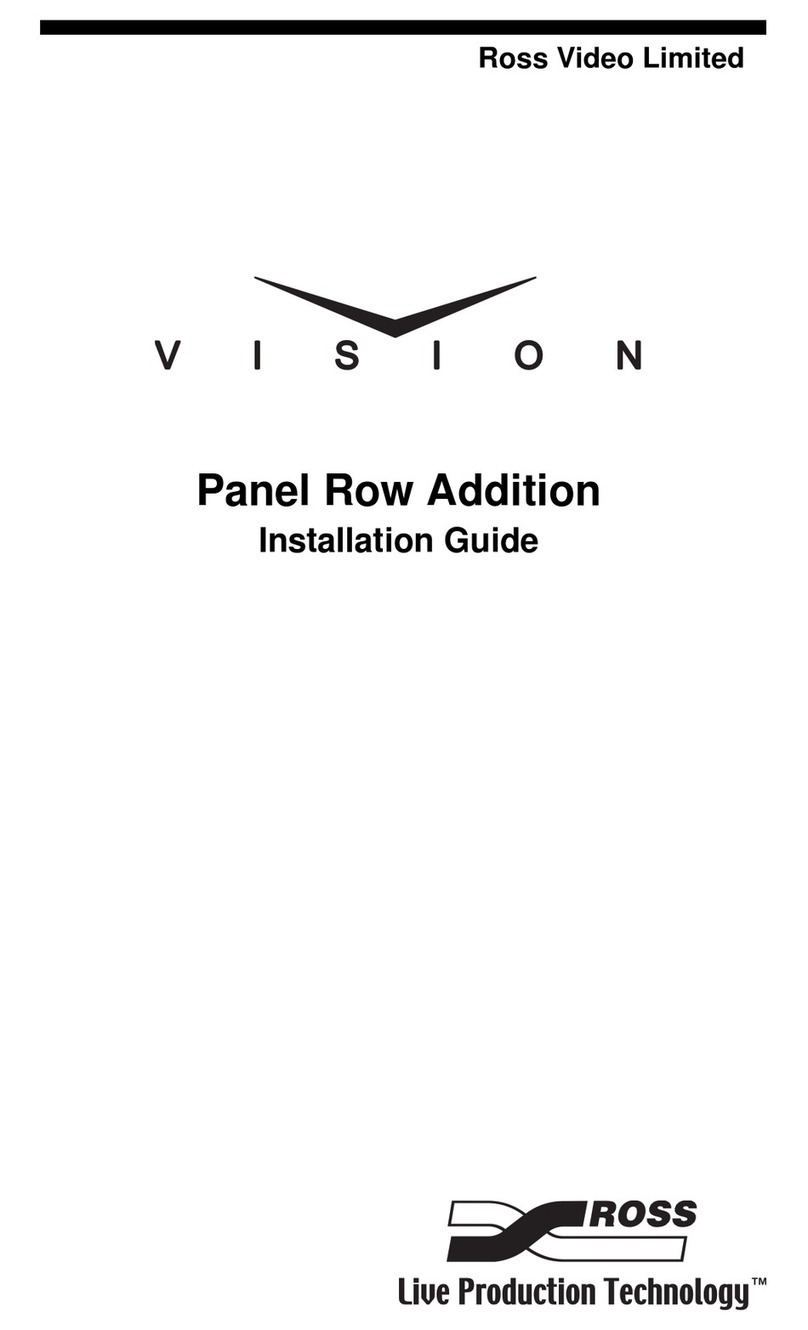
Ross
Ross Vision 4800DR-325-02 User manual

Ross
Ross 27 Series User manual
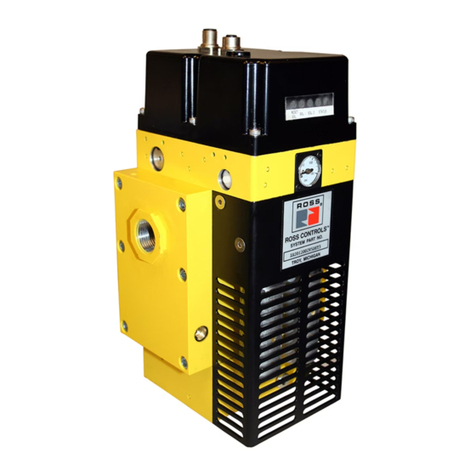
Ross
Ross M DM2 C Series User manual
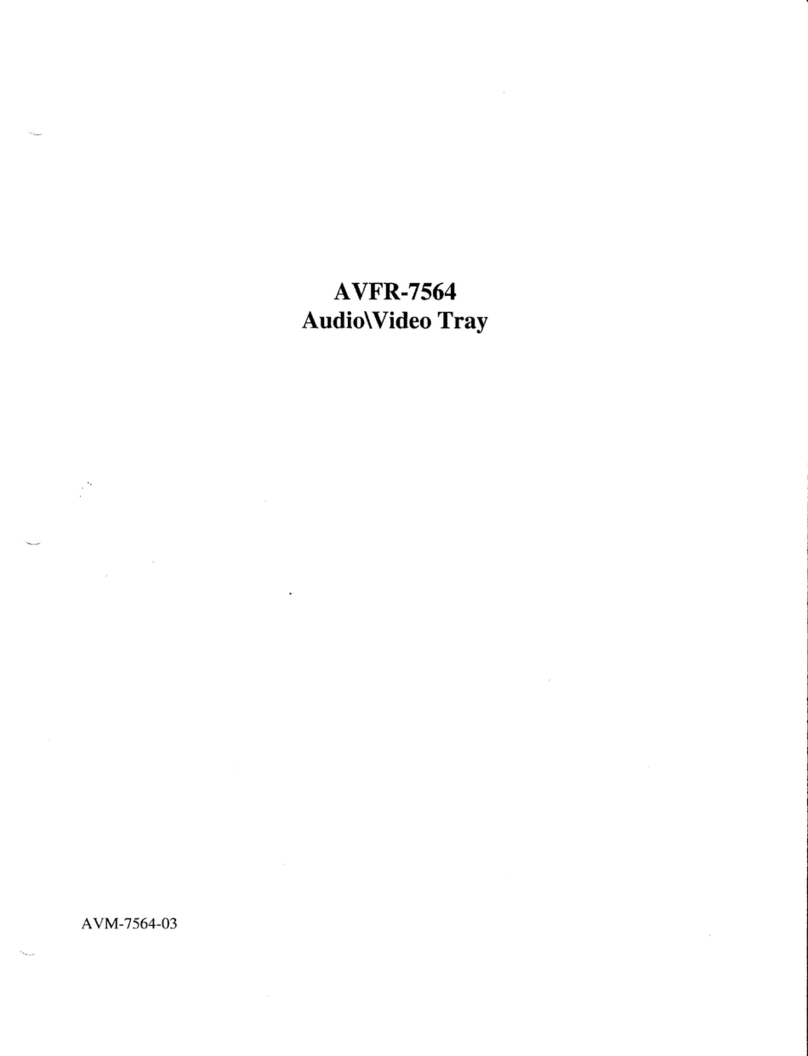
Ross
Ross AVFR-7564 User manual
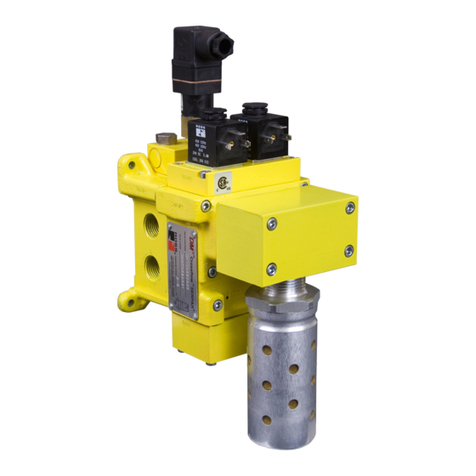
Ross
Ross DM1 C User manual

Ross
Ross Serpar 35 Series User manual

Ross
Ross Vision Crosspoint Module User manual

Ross
Ross M35 Series Quick setup guide
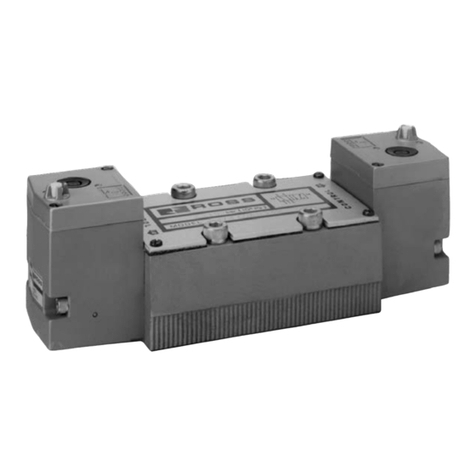
Ross
Ross W70 Series User manual
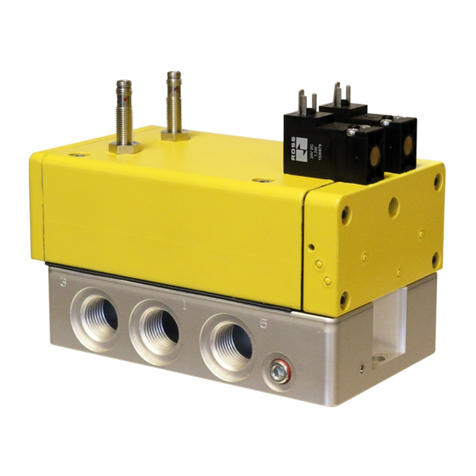
Ross
Ross RSe Series User manual
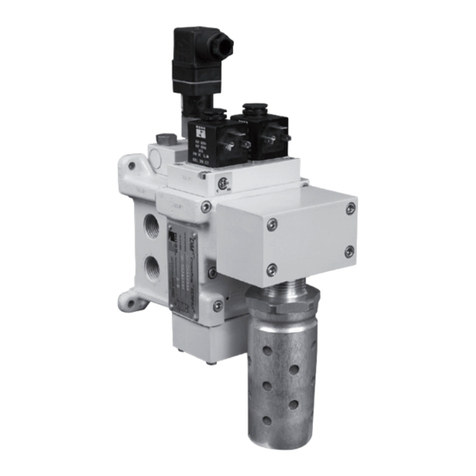
Ross
Ross DM1 C User manual

Ross
Ross Serpar 35 Series User manual