SICK GM35 User manual

OPERATING INSTRUCTIONS
GM35
In-situ IR Gas Analyzer,
Probe Version

Described product
GM35
Probe version
GM35-1, GM35-2, GM35-3, GM35-4, GM35-5, GM35-6, GM35-7, GM35-10
Manufacturer
SICK AG
Erwin-Sick-Str. 1
79183 Waldkirch
Germany
Production location
SICK AG
Gisela-Sick-Str. 1 · D-79276 Reute · Germany
Legal information
This work is protected by copyright. Any rights derived from the copyright shall be
reserved for SICK AG. Reproduction of this document or parts of this document is
only permissible within the limits of the legal determination of Copyright Law. Any modi‐
fication, abridgment or translation of this document is prohibited without the express
written permission of SICK AG.
The trademarks stated in this document are the property of their respective owner.
© SICK AG. All rights reserved.
Original document
This document is an original document of SICK AG.
2O P E R A T I N G I N S T R U C T I O N S | GM35 8009389/147I/V4-0/2021-03 | SICK
Subject to change without notice

Contents
1 About this document........................................................................ 7
1.1 Function of this document....................................................................... 7
1.2 Scope of application................................................................................. 7
1.3 Target groups............................................................................................ 7
1.4 Further information................................................................................... 7
1.5 Symbols and document conventions...................................................... 7
1.5.1 Warning symbols...................................................................... 7
1.5.2 Warning levels / Signal words................................................. 8
1.5.3 Information symbols................................................................ 8
1.6 Data integrity............................................................................................. 8
2 Safety information............................................................................ 9
2.1 Main operating information..................................................................... 9
2.2 Warning information on the device.......................................................... 10
2.3 Intended use............................................................................................. 10
2.4 Responsibility of user............................................................................... 10
3 Product description........................................................................... 12
3.1 Product identification............................................................................... 12
3.2 Product characteristics............................................................................ 12
3.3 Device variants......................................................................................... 12
3.4 Layout and function.................................................................................. 13
3.5 Options...................................................................................................... 15
3.6 Check cycle............................................................................................... 15
3.7 Measuring probes .................................................................................... 15
3.7.1 Open GMP measuring probe in detail.................................... 16
3.7.2 Gas-testable GPP measuring probe in detail......................... 17
4 Transport and storage....................................................................... 18
4.1 Storage...................................................................................................... 18
5 Mounting............................................................................................. 19
5.1 Safety......................................................................................................... 19
5.2 Tools required............................................................................................ 19
5.3 Material required...................................................................................... 19
5.4 Preparing the measuring point................................................................ 19
5.5 Checking the scope of delivery................................................................ 20
5.6 Installation sequence............................................................................... 20
5.6.1 Installation steps..................................................................... 20
5.6.2 Installing the flange with tube................................................. 21
5.6.3 Installing the purge air unit..................................................... 23
5.6.4 Connecting the purge air unit electrically.............................. 23
5.6.5 Removing the transport safety devices of the measuring
probe........................................................................................ 23
CONTENTS
8009389/147I/V4-0/2021-03 | SICK O P E R A T I N G I N S T R U C T I O N S | GM35 3
Subject to change without notice

5.6.5.1 Removing the transport safety device of the
GMP measuring probe............................................ 23
5.6.5.2 Removing the transport safety device of the GPP
measuring probe..................................................... 24
5.6.6 Fitting the measuring probe on the flange with tube............ 24
5.6.7 Putting the purge air unit into operation................................ 25
5.6.8 Fitting the flange fixture on the measuring probe................. 26
5.6.9 Fitting the control unit............................................................. 27
5.6.9.1 Fitting the control unit at a greater distance
(option).................................................................... 29
6 Electrical installation........................................................................ 31
6.1 Safety......................................................................................................... 31
6.2 Tools required............................................................................................ 32
6.3 Overview of electrical connection steps.................................................. 32
6.4 Connection overview................................................................................ 33
6.4.1 Lines overview.......................................................................... 34
6.4.2 Laying lines.............................................................................. 34
6.5 Electrical connection of the control unit................................................. 34
6.5.1 Correct connection of the CAN bus line................................. 35
6.5.2 Connecting the control unit electrically.................................. 35
6.5.3 Connecting the grounding conductor on the control unit..... 37
6.6 Connecting the connection unit (option)................................................. 38
7 Commissioning.................................................................................. 40
7.1 Safety......................................................................................................... 40
7.2 Requirements............................................................................................ 40
7.3 Tools required............................................................................................ 40
7.4 Material required...................................................................................... 40
7.5 Commissioning steps overview................................................................ 40
7.6 Removing the transport safety device of the sender/receiver unit....... 41
7.7 Fitting the sender/receiver unit on the flange fixture............................ 41
7.8 Connecting the sender/receiver unit with measuring probe................. 42
7.9 Fine optical alignment.............................................................................. 43
7.10 Fitting the weather hood (option)............................................................ 45
7.11 Starting measuring operation.................................................................. 46
7.11.1 Operating states...................................................................... 46
8 Operation............................................................................................ 47
8.1 Operating and display elements.............................................................. 47
8.2 Control unit menu tree............................................................................. 48
8.2.1 Menu tree, Measuring............................................................. 48
8.2.2 Menu tree, Diagnosis.............................................................. 48
8.2.3 Menu tree, Parameters........................................................... 48
8.2.4 Menu tree, Calibration............................................................. 50
8.2.5 Menu tree, Maintenance......................................................... 50
CONTENTS
4O P E R A T I N G I N S T R U C T I O N S | GM35 8009389/147I/V4-0/2021-03 | SICK
Subject to change without notice

9 Maintenance...................................................................................... 51
9.1 Safety......................................................................................................... 51
9.2 Maintenance plan..................................................................................... 52
9.2.1 Maintenance protocol.............................................................. 52
9.2.2 Expendable, wearing and spare parts.................................... 53
9.3 Preparatory work....................................................................................... 53
9.4 Visual check.............................................................................................. 53
9.5 Removing the sender/receiver unit......................................................... 54
9.6 Cleaning optical surfaces......................................................................... 54
9.6.1 Cleaning the optical surface of the sender/receiver unit..... 55
9.6.2 Cleaning the optical surface of the GMP measuring probe.. 55
9.6.3 Cleaning the optical surface of the GPP measuring probe... 56
9.7 Cleaning the control unit.......................................................................... 58
9.8 Cleaning the purge air unit....................................................................... 58
9.9 Checking the function of the IR source................................................... 58
10 Troubleshooting................................................................................. 59
10.1 Safety......................................................................................................... 59
10.2 Monitoring and diagnostic system........................................................... 60
10.3 Device not functioning.............................................................................. 60
10.4 Clearing malfunctions on the control unit............................................... 61
10.4.1 Communication error between control unit and receiver..... 61
10.5 Malfunction messages............................................................................. 62
10.6 Warning messages................................................................................... 63
10.7 Repairing inadequate purge air supply................................................... 64
10.8 Corrosion on flange.................................................................................. 65
11 Decommissioning............................................................................. 66
11.1 Safety......................................................................................................... 66
11.2 Removing the device................................................................................ 67
11.3 Preparing the device ready for shipping.................................................. 68
11.4 Environmentally compatible disposal ..................................................... 68
12 Technical data.................................................................................... 70
12.1 GM35 system............................................................................................ 70
12.2 Sender/receiver unit................................................................................ 70
12.3 Open GMP measuring probe.................................................................... 71
12.4 Gas-testable GPP measuring probe........................................................ 71
12.5 Control unit, AWE, sheet steel enclosure................................................ 72
12.6 Control unit, AWE, cast metal enclosure................................................. 72
12.7 Connection unit......................................................................................... 73
12.8 Dimension drawing, sender/receiver unit .............................................. 74
12.9 Dimension drawing, open GMP measuring probe.................................. 75
12.10 Dimension drawing, gas-testable GPP measuring probe....................... 76
12.11 Dimension drawing, control units............................................................ 77
12.12 Dimension drawing, flange with tube, DN125........................................ 78
CONTENTS
8009389/147I/V4-0/2021-03 | SICK O P E R A T I N G I N S T R U C T I O N S | GM35 5
Subject to change without notice

12.13 Dimension drawing, connection unit....................................................... 78
12.14 Dimension drawing, purge air unit, SLV4-2............................................. 79
12.15 Dimension drawing, weather hoods........................................................ 80
CONTENTS
6O P E R A T I N G I N S T R U C T I O N S | GM35 8009389/147I/V4-0/2021-03 | SICK
Subject to change without notice

1 About this document
1.1 Function of this document
These Operating Instructions describe:
•Device components
•Installation
•Operation
•Maintenance work required for reliable operation
1.2 Scope of application
These Operating Instructions are only applicable for the measuring device described in
the product identification.
They are not applicable for other SICK measuring devices.
The standards referred to in these Operating Instructions are to be observed in the
respective valid version.
1.3 Target groups
This Manual is intended for persons installing, operating and maintaining the device.
Operation
The device may only be operated by qualified persons who, based on their device-spe‐
cific training and knowledge as well as knowledge of the relevant regulations, can
assess the tasks given and recognize the hazards involved.
Installation and maintenance
Installation and maintenance may only be carried out by trained specialists familiar
with the installation conditions.
Please observe the information at the beginning of the respective Sections.
1.4 Further information
•Purge air unit Operating Instructions
•Final inspection record
NOTE
bObserve all documents provided.
1.5 Symbols and document conventions
1.5.1 Warning symbols
Table 1: Warning symbols
Symbol Significance
Hazard (general)
Hazard by electrical voltage
ABOUT THIS DOCUMENT 1
8009389/147I/V4-0/2021-03 | SICK O P E R A T I N G I N S T R U C T I O N S | GM35 7
Subject to change without notice

Symbol Significance
Hazard by toxic substances
Hazard by unhealthy substances
Hazard through pressure/temperature
Hazard for environment and organisms
1.5.2 Warning levels / Signal words
DANGER
Risk or hazardous situation which will result in severe personal injury or death.
WARNING
Risk or hazardous situation which could result in severe personal injury or death.
CAUTION
Hazard or unsafe practice which could result in less severe or minor injuries.
Notice
Hazard which could result in property damage.
Note
Hints
1.5.3 Information symbols
Table 2: Information symbols
Symbol Significance
Important technical information for this product
Important information on electric or electronic functions
1.6 Data integrity
SICK AG uses standardized data interfaces such as, for example, standard IP technol‐
ogy, in its products. The focus here is on product availability and features.
SICK AG always assumes that the customer is responsible for the integrity and confi‐
dentiality of data and rights involved in connection with using the products.
In all cases, the customer is responsible for the implementation of safety measures
suitable for the respective situation, e.g., network separation, firewalls, virus protection
and patch management.
1 ABOUT THIS DOCUMENT
8O P E R A T I N G I N S T R U C T I O N S | GM35 8009389/147I/V4-0/2021-03 | SICK
Subject to change without notice

2 Safety information
2.1 Main operating information
NOTICE
Risk for system safety through work on the device not described in these Operating
Instructions
Work on the device not described in these Operating Instructions or associated docu‐
ments can lead to unsafe operation of the measuring system and therefore endanger
plant safety.
bOnly carry out the work described in these Operating Instructions or the corre‐
sponding documents on the device.
WARNING
Danger of ineffectiveness of the protective device
In case of nonobservance, persons or parts of the body to be protected are not
detected.
bPay special attention to all safety information in these Operating Instructions.
CAUTION
Hazard for persons and plant through unsafe operation of the measuring device
If the device is or could be in an unsafe state:
bPut the device out of operation.
bDisconnect the device from the main supply voltage and signal voltage.
bSecure the device against unallowed or unintentional start-up.
CAUTION
Risk of injury through incorrect lifting and carrying the device
Injuries can occur due to the weight and projecting enclosure parts when the equip‐
ment tips over or drops.
bConsider the device weight before lifting.
bObserve the regulations for protective clothing (e.g., safety shoes, non-slip gloves).
bGrip underneath the equipment when possible to carry it safely.
bDo not use projecting parts on the device to carry the device.
bCall in further personnel for assistance as required.
bUse a hoist or transport equipment as an option.
bPay attention to the transport safety device.
bClear obstacles that could cause falls and collisions out of the way.
SAFETY INFORMATION 2
8009389/147I/V4-0/2021-03 | SICK O P E R A T I N G I N S T R U C T I O N S | GM35 9
Subject to change without notice

2.2 Warning information on the device
Sender/receiver unit
Figure 1: Sender/receiver unit from the front and right side
1Warning sign: Disconnect the power plug before opening the device.
2Do not disconnect under voltage.
2.3 Intended use
The device serves exclusively for emission and process monitoring of gases in industrial
plants.
The device measures continuously directly in the gas duct (in-situ).
2.4 Responsibility of user
Intended users
see "Target groups", page 7.
Correct project planning
•Basis of this Manual is the delivery of the device according to the preceding
project planning (e.g., based on the SICK application questionnaire) and the rele‐
vant delivery state of the device (see delivered System Documentation).
bIf you are not sure whether the device corresponds to the state defined
during project planning or to the delivered system documentation: Please
contact SICK Customer Service.
Special local conditions
In addition to the information in these Operating Instructions, follow all local laws, tech‐
nical rules and company-internal operating directives applicable wherever the device is
installed.
Read the Operating Instructions
bRead and observe these Operating Instructions.
bObserve all safety instructions.
bIf anything is not clear: Please contact SICK Customer Service.
2 SAFETY INFORMATION
10 O P E R A T I N G I N S T R U C T I O N S | GM35 8009389/147I/V4-0/2021-03 | SICK
Subject to change without notice

Document retention
bMust be kept for reference.
bMust be passed on to new owners.
SAFETY INFORMATION 2
8009389/147I/V4-0/2021-03 | SICK O P E R A T I N G I N S T R U C T I O N S | GM35 11
Subject to change without notice

3 Product description
3.1 Product identification
Product name GM35
Device version Measuring Probe Version
Manufacturer SICK AG
Erwin-Sick-Str. 1 · D-79183 Waldkirch · Germany
Type plates •Sender/receiver unit: On right side
•On purge air attachment: On tube
•Control unit: On right side
3.2 Product characteristics
•The device serves for continuous measurement of the gas concentrations in indus‐
trial plants..
•The device is an in-situ measuring device which means measuring is done directly
in the gas carrying duct.
•Measuring components:CO2, H2O, CO, N2O
•Measuring principle:
°Gas filter correlation
°Interference filter correlation
3.3 Device variants
The following device variants are available depending on the measuring task and
application:
Variant Measured components
GM35-1 CO
GM35-2 CO, H2O
GM35-3 CO, H2O, CO2
GM35-4 CO, CO2
GM35-5 H2O, CO2
GM35-6 H2O
GM35-7 CO2
GM35-10 N2O, H2O, CO2
3 PRODUCT DESCRIPTION
12 O P E R A T I N G I N S T R U C T I O N S | GM35 8009389/147I/V4-0/2021-03 | SICK
Subject to change without notice

3.4 Layout and function
maintcalpardiag
GM
Evaluation Unit
CO
CO 2
H2O
mg/
m3
236
Ref. conditions
Hum: wet
Measuring
Operation
Service
Warnin
Malfunction
Figure 2: Measuring device components layout
Connection lines
Purge air hose (only for GMP)
1Sender/receiver unit
2Purge air attachment, integrated pressure and temperature sensor
3Probe tube
4Connection unit
5Control unit
6Purge air unit (only for GMP)
The measuring device comprises the following components:
PRODUCT DESCRIPTION 3
8009389/147I/V4-0/2021-03 | SICK O P E R A T I N G I N S T R U C T I O N S | GM35 13
Subject to change without notice

Sender/receiver unit
The sender/receiver unit contains the optical-electronic assemblies and determines the
measured values of the concentration of the measuring component(s) of the measuring
device.
Measuring probe
The measuring probe takes the sample gases at the measuring location and passes
these to the sender/receiver unit for determination of the measured values. Two meas‐
uring probe versions are available for the different application conditions:
•Open GMP measuring probe with open measuring gap as measuring distance and
purge air attachment.
•Gas-testable GPP measuring probe with ceramic filter for dry sample gases and
test gas attachment.
Purge air attachments
The purge air attachments serve to attach the sender/receiver unit and reflector unit to
the flanges with tube. They contain the purge air nozzles for connecting the purge air
hoses of the purge air units and the connections for external sensors e.g., temperature
or pressure sensors as well as the connections for purge air monitoring.
Control unit
The control unit serves as user interface, and prepares and outputs the measured
values and performs control and monitoring functions.
These functions include the following:
•Output of measured values, computed data and operating states
•Communication with peripheral equipment
•Output of error messages and other status signals
•Control of automatic test functions and access during service work (diagnosis)
Flanges with tube
The flanges with tube are attached directly to the gas duct of the measuring point and
serves to fit the purge air attachments of the sender/receiver unit and reflector unit.
ANSI or DIN flanges can be used alternatively to the flanges supplied.
Purge air unit
The purge air unit supplies filtered ambient air to the purge air attachments and
protects the optical surfaces of the sender/receiver unit and reflector unit from con‐
tamination and high gas temperatures.
NOTE
As standard, SICK recommends a separate purge air unit for the sender/receiver unit
and reflector unit when using the GMP measuring probe to ensure an optimal purge air
supply.
If the supply of purge air is insufficient, hot and corrosive gases can destroy the
measuring device within a few minutes.
Further information on the purge air unit, see Operating Instructions of the purge air
unit.
3 PRODUCT DESCRIPTION
14 O P E R A T I N G I N S T R U C T I O N S | GM35 8009389/147I/V4-0/2021-03 | SICK
Subject to change without notice

3.5 Options
Connection unit
If the distance between the sender/receiver unit and and control unit is > 4 m, the
connection can be established via the connection unit and a CAN bus line provided by
the customer.
Total length of all CAN bus lines: max. 300 m.
Weather hoods
For the components sender/receiver unit, reflector unit and purge air unit when instal‐
ling the measuring device outdoors.
Air heater for purge air supply
To avoid condensation in the purge air. An air heater is required when the difference
between gas temperature and dew point temperature is too small.
The following formula serves as a guideline:
•Gas temperature [°C] – dew point temperature [°C] < abs. humidity [Vol.-%].
•Values are compared without considering the units of measure.
3.6 Check cycle
The check cycle serves to check the zero point and a reference point without feeding
test gases. Here, a measuring sequence is run through to determine the zero and check
point (usually 70 % of the measuring range end value).
“Function check” is signaled per digital output during output of the zero and reference
point.
The output for each takes 90 s for the zero point, followed by the reference point.
•Unit and scaling for the current zero point according to the setting.
•Reference point is displayed as percentage scaled to 70 % of the measuring
range.
3.7 Measuring probes
The measuring probe versions are compatible with all sender/receiver units. The
sender/receiver unit is calibrated to the respective probe length on delivery.
Table 3: Measuring probes: Characteristics and application
Characteristic Open GMP measuring probe Gas-testable GPP measuring
probe
Version Measuring path open in flow
direction; purge air guidance
with outlet aligned 90° to gas
flow
Gas-testable measuring probe
with ceramic filter, for dry sam‐
ple gas
Maximum process tempera‐
ture
≤ +430 °C
For N2O measurement max.
180 °C
≤ +430 °C
For N2O measurement max.
180 °C
Gas test according to EPA reg‐
ulation
No Yes
Purge air supply required Yes No
Optical surface heating in
measuring probe
No Yes, with integrated control
PRODUCT DESCRIPTION 3
8009389/147I/V4-0/2021-03 | SICK O P E R A T I N G I N S T R U C T I O N S | GM35 15
Subject to change without notice

Characteristic Open GMP measuring probe Gas-testable GPP measuring
probe
Suitable for wet sample gas Yes No
Measurable components CO2, H2O, CO, N2O CO2, H2O, CO, N2O
Response time (t90) > 5 s > 120 s
Duct diameter > 500 mm > 380 mm
Dust load ≤ 3 g/m3
Relative to 1 m measuring dis‐
tance, depending on applica‐
tion
≤ 30 g/m3
Probe lengths available see "Dimension drawing,
open GMP measuring probe",
page 75
see "Dimension drawing,
gas-testable GPP measuring
probe", page 76
Available measuring distances see "Dimension drawing,
open GMP measuring probe",
page 75
see "Dimension drawing,
gas-testable GPP measuring
probe", page 76
3.7.1 Open GMP measuring probe in detail
Figure 3: Open measuring probe GMP
1Probe end with reflector assembly
2Air slots: Purge air outlet 90° to gas flow (directed purge air)
3Process flange: Attached to flange with tube (at installation location)
4Device flange: Attached to sender/receiver unit
5Locking device
6Purge air attachment with connections (purge air, electric connection cables)
7Integrated temperature sensor PT1000
8Measuring gap
3 PRODUCT DESCRIPTION
16 O P E R A T I N G I N S T R U C T I O N S | GM35 8009389/147I/V4-0/2021-03 | SICK
Subject to change without notice

9Lever for locking device
3.7.2 Gas-testable GPP measuring probe in detail
Figure 4: Gas-testable measuring probe GPP
1Probe end with reflector assembly
2Process flange: Attached to flange with tube (at installation location)
3Test gas attachment with connections
4Integrated temperature sensor PT1000
5Filter element (gas permeable)
PRODUCT DESCRIPTION 3
8009389/147I/V4-0/2021-03 | SICK O P E R A T I N G I N S T R U C T I O N S | GM35 17
Subject to change without notice

4 Transport and storage
4.1 Storage
bClean all components of the measuring device (not the optical surfaces) with
slightly moistened cleaning cloths. Use a mild cleaning agent here.
bProtect the openings of the sender/receiver-unit and measuring probe from atmos‐
pheric influences, preferably with the original transport safety devices.
bPack all components for storage or transport. Preferably use the original packing.
bStore all components of the measuring device in a dry, clean area.
4 TRANSPORT AND STORAGE
18 O P E R A T I N G I N S T R U C T I O N S | GM35 8009389/147I/V4-0/2021-03 | SICK
Subject to change without notice

5 Mounting
5.1 Safety
WARNING
Risk of injury through improper assembly work
All assembly work must be carried out only by authorized persons who, based on their
training and knowledge as well as knowledge of the relevant regulations, can assess
the tasks given and recognize the hazards involved.
CAUTION
Accident risk through inadequate fastening of the device
bConsider the device weight specifications when planning the fitting supports.
bCheck the load capacity/condition of the duct on which the device is to be instal‐
led.
NOTICE
Damage to device and plant through unsecured parts during installation
During installation, parts of the device or flange can fall into the duct and cause
damage.
bSecure all parts with wire.
NOTICE
Damage to the measuring device due to premature installation on the stack
Unsuitable ambient conditions in the measuring duct can damage the measuring
device and make commissioning impossible.
bFirst install the measuring device on the stack after commissioning.
5.2 Tools required
•Fork or ring spanner set
•Insulated screwdriver set
•Allen key set, metric
5.3 Material required
•Optics cleaning wipes without detergent
•Personal protective equipment
5.4 Preparing the measuring point
Responsibility of the operator
•Determining the measuring point (e.g. determining a representative sampling
point)
•Preparing the measuring point (e.g. load capacity of welded-on flange)
MOUNTING 5
8009389/147I/V4-0/2021-03 | SICK O P E R A T I N G I N S T R U C T I O N S | GM35 19
Subject to change without notice

NOTICE
Basis for determining the measuring point:
•Preceding project planning
•Final inspection specifications for device
•Regulations of local authorities
5.5 Checking the scope of delivery
bCheck the scope of delivery according to the order confirmation/delivery note.
bEnsure the supply voltages indicated on the type plates correspond to the system
conditions.
bCheck all components for externally perfect delivery condition.
5.6 Installation sequence
5.6.1 Installation steps
Installation comprises two main steps:
1 Installing the required device components at the measuring point before commis‐
sioning.
2 Installing the measuring device at the measuring point (carried out by SICK Serv‐
ice during commissioning).
NOTICE
GMP measuring probe device damage: To prevent contamination of the optical surfa‐
ces, the purge air must be connected immediately after installation.
Table 4: GMP measuring probe: Overview of installation steps before commissioning
Step Procedure Reference
1 Install the flange with tube. see "Installing the flange with tube",
page 21
2 Install the purge air unit. see Purge air unit Operating Instructions
3 Connect the purge air unit electrically. see Purge air unit Operating Instructions
4 Remove the transport safety devices of the
measuring probe.
see "Removing the transport safety
device of the GMP measuring probe",
page 23
5 Install the measuring probe. see "Fitting the measuring probe on the
flange with tube", page 24
6 Put the purge air unit into operation. see "Putting the purge air unit into oper‐
ation", page 25
7 Fit the flange attachment on the measuring
probe.
see "Fitting the flange fixture on the
measuring probe", page 26
8 Fit the control unit. see "Fitting the control unit", page 27
NOTICE
GPP measuring probe device damage: To prevent contamination of the optical surfaces,
the measuring probe must be heated before installation.
5 MOUNTING
20 O P E R A T I N G I N S T R U C T I O N S | GM35 8009389/147I/V4-0/2021-03 | SICK
Subject to change without notice
Other manuals for GM35
3
This manual suits for next models
8
Table of contents
Other SICK Measuring Instrument manuals

SICK
SICK GM35 User manual
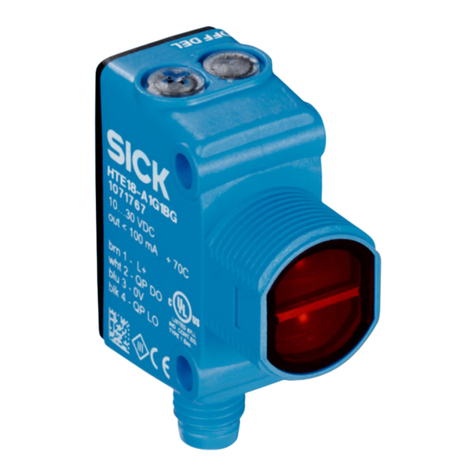
SICK
SICK HTF18 User manual
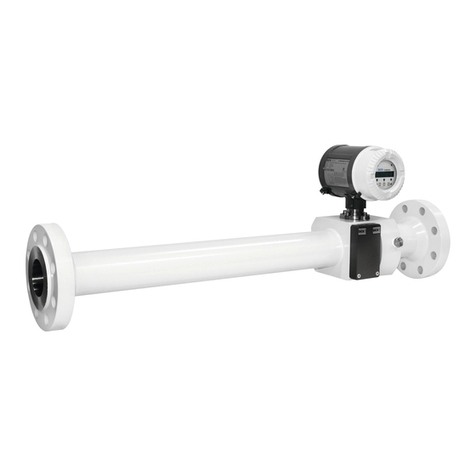
SICK
SICK FLOWSIC600 User manual
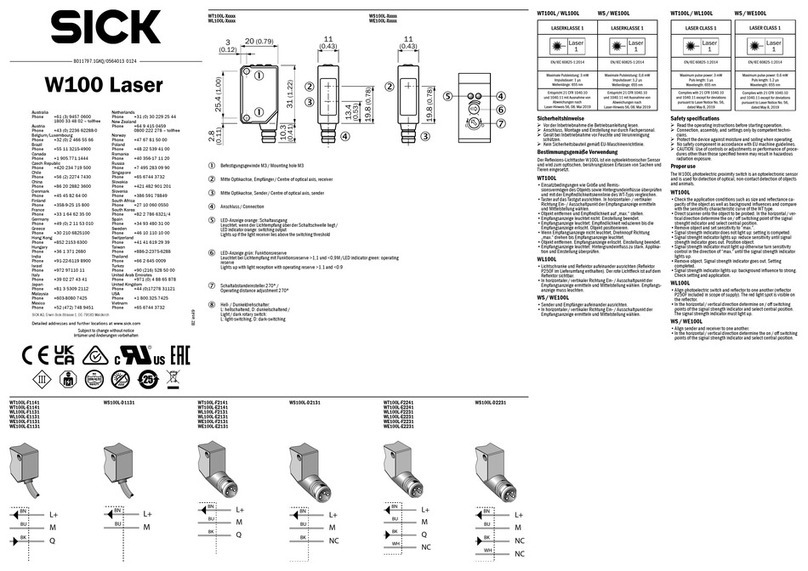
SICK
SICK W100 User manual
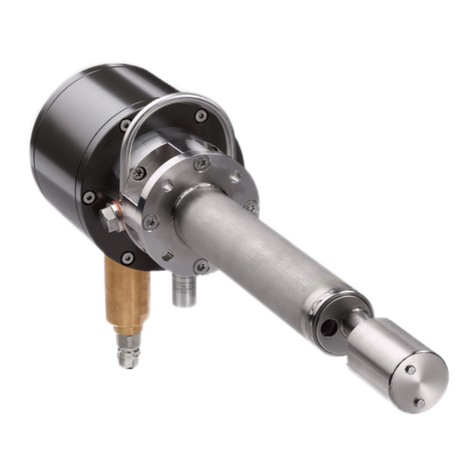
SICK
SICK DUSTHUNTER SP100 Ex-2K User manual
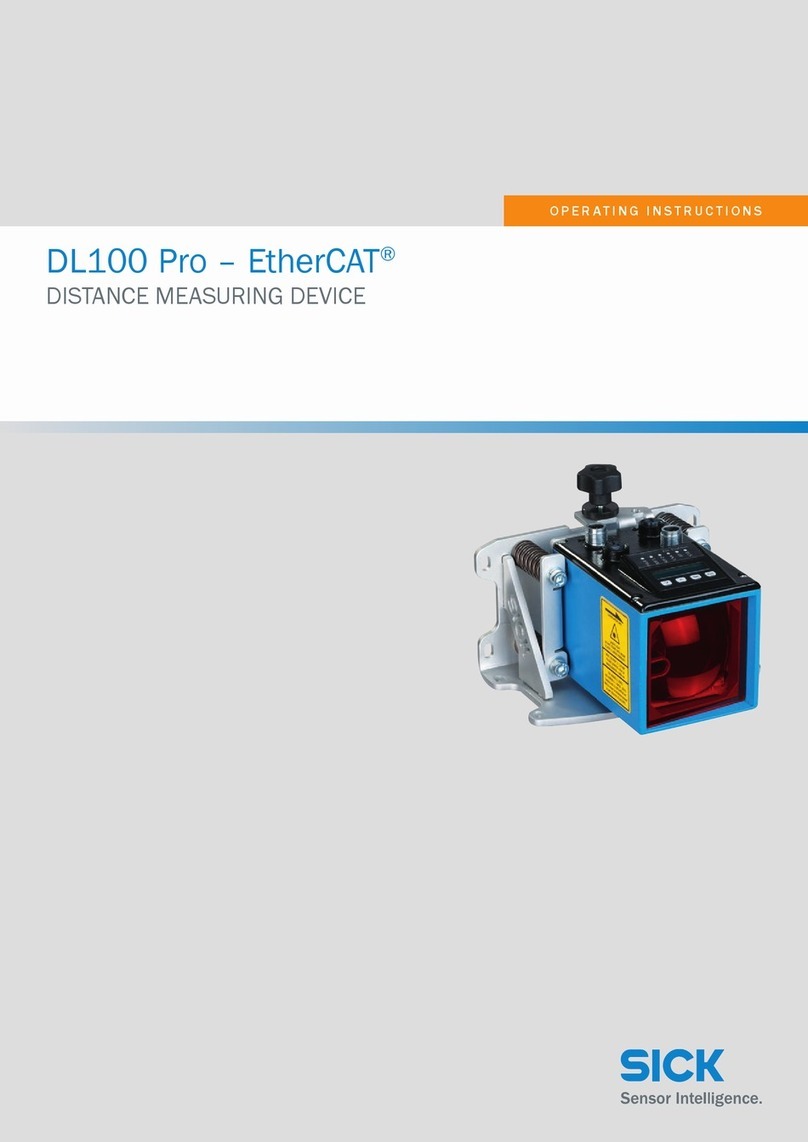
SICK
SICK DL100 Pro User manual
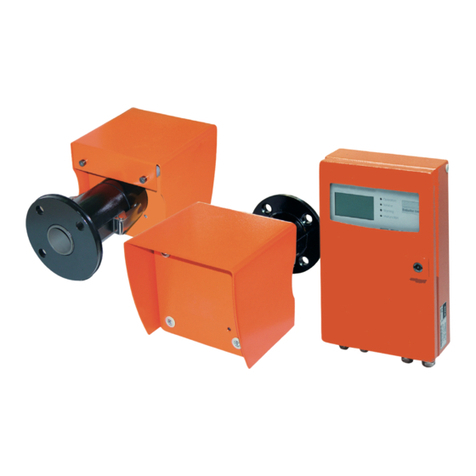
SICK
SICK GM901 User manual
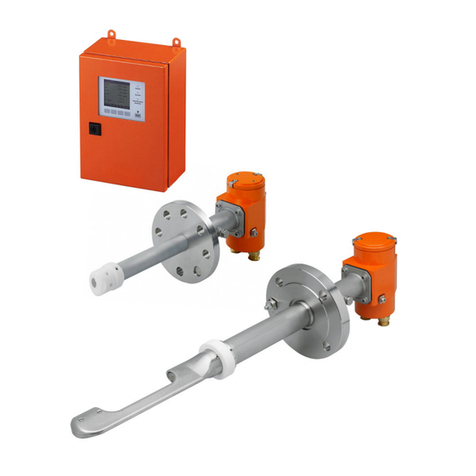
SICK
SICK FLOWSIC100 Flare User manual
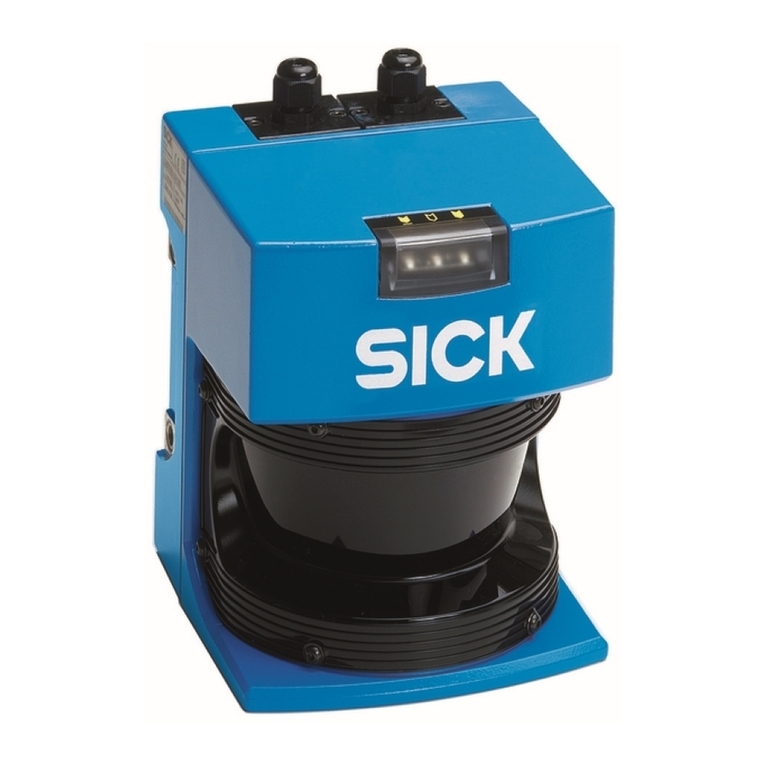
SICK
SICK LMS 200 Parts list manual
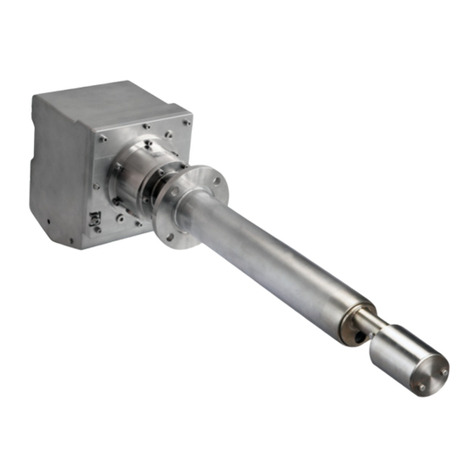
SICK
SICK DUSTHUNTER SP100 Ex-3K User manual
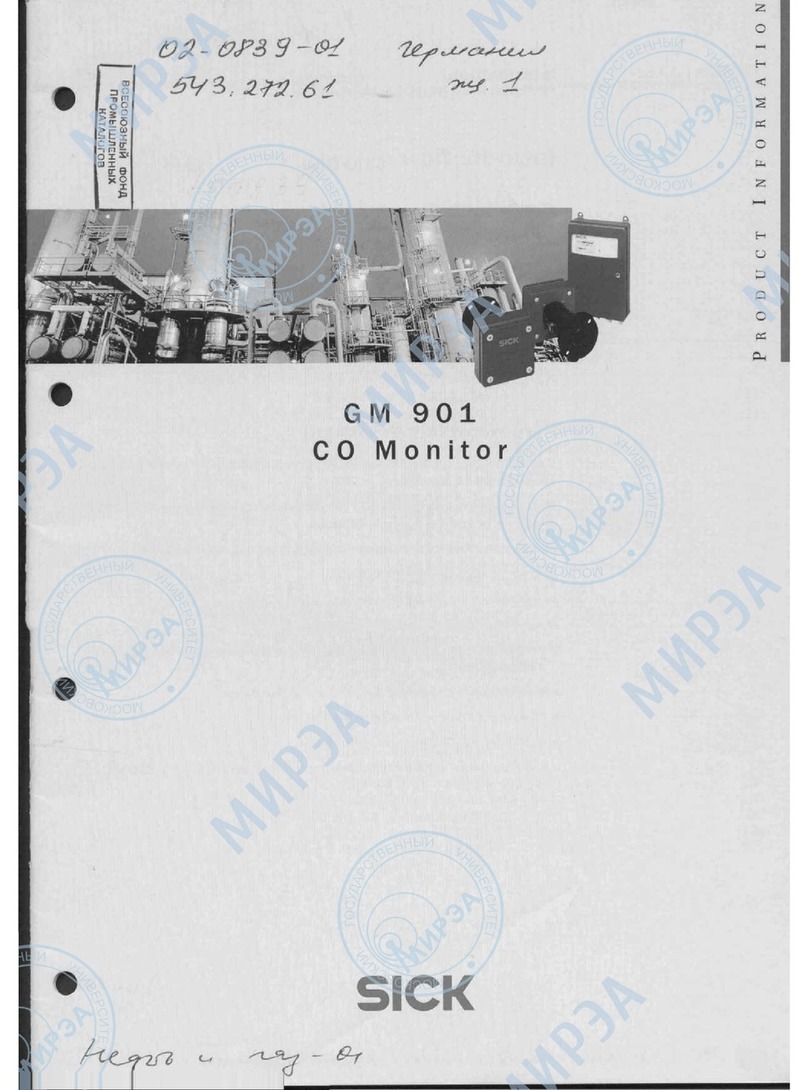
SICK
SICK GM901 User manual
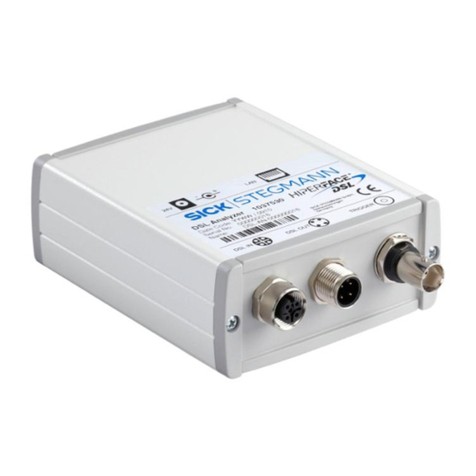
SICK
SICK PGT-09-S User manual
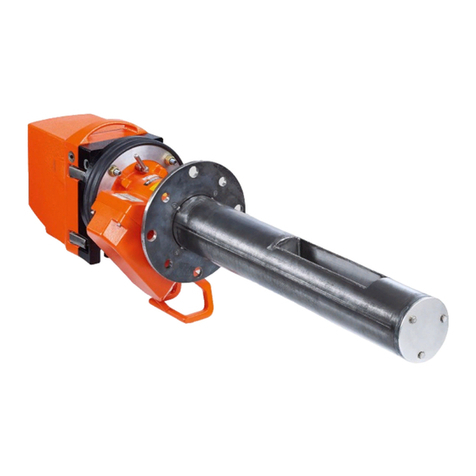
SICK
SICK GM700 User manual
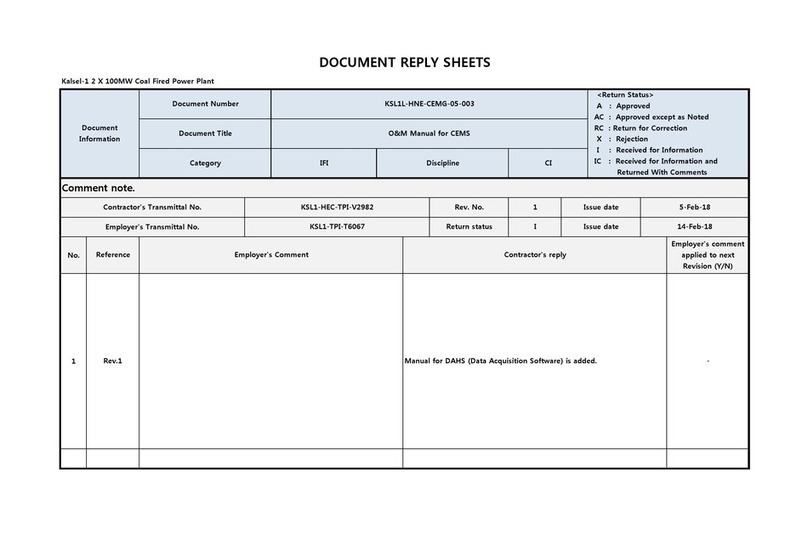
SICK
SICK DUSTHUNTER T User manual
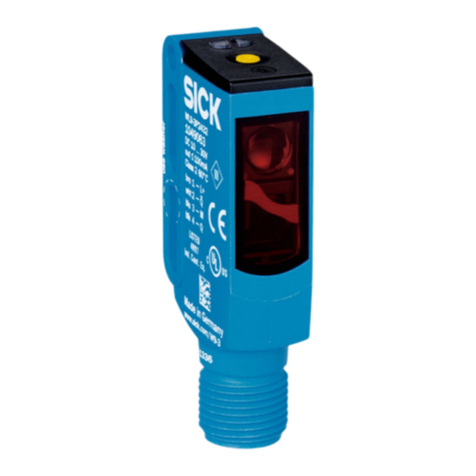
SICK
SICK WTF9-3 User manual

SICK
SICK Master Data Analyzer User manual

SICK
SICK GM901 User manual

SICK
SICK InspectorP64 Series User manual

SICK
SICK MLG-2 Prime User manual

SICK
SICK GM32 Series Manual