Vision PHOENIX TABLE User manual

Page1
Table of
Contents
Table Of Contents
Liability Statement................................................................2
Safety ...........................................................................3
Chapter 1. Unpacking and Taking Inventory.................. 5
Chapter 2: Table Description........................................ 7-9
Chapter 3: Setting Up The Table ....................................11
Chapter 4: Table Adjustments..................................13-16
Chapter 5: Table Maintenance .................................17-21
Chapter 6: Optional Accessories and Uses ...........23-31
Chapter 7: Troubleshooting ......................................33-36
Thismanualisdesignedtoprovideyouwithinformation aboutyourVision
Computerized Engraving and Routing Systems table, beginning with
unpackingthe tableandcontinuing throughinstallationand lifetimetable
maintenance.Thismanualdoesnotattempttoteachyouhowtoengrave,
how to use a computer, or how to use your engraving software. Some
previous knowledge of engraving terms and the engraving process is
assumed. For information on your individual computer system, see your
computer’s user manual or contact your computer distributor. For
information on the engraving software you use to drive your engraving
system, see the manual for the individual software package supplied by
thesoftwaredeveloper.
PHOENIX
ENGRAVING
TABLE
OPERATINGMANUAL

Page2
Copyright 1999 Vision Computerized Engraving & Routing SystemsCopyright 1999 Vision Computerized Engraving & Routing Systems
Copyright 1999 Vision Computerized Engraving & Routing SystemsCopyright 1999 Vision Computerized Engraving & Routing Systems
Copyright 1999 Vision Computerized Engraving & Routing Systems
(A Division of W(A Division of W
(A Division of W(A Division of W
(A Division of Western Engravers Supplyestern Engravers Supply
estern Engravers Supplyestern Engravers Supply
estern Engravers Supply, Inc.), Inc.)
, Inc.), Inc.)
, Inc.)
All Rights ReserAll Rights Reser
All Rights ReserAll Rights Reser
All Rights Reservedved
vedved
ved
This publication is protected by copyright, and all rights are reserved. No part of this manual may be reproduced or
transmitted by any means or in any form, without prior written consent from Vision.
Limits of Liability / Disclaimer of WLimits of Liability / Disclaimer of W
Limits of Liability / Disclaimer of WLimits of Liability / Disclaimer of W
Limits of Liability / Disclaimer of Warar
arar
arranty for this Tranty for this T
ranty for this Tranty for this T
ranty for this Table Manual:able Manual:
able Manual:able Manual:
able Manual:
The information contained within this manual has been carefully checked and is believed to be accurate, however,
Vision makes no representations or warranties for this manual, and assumes no responsibility for inaccuracies, errors,
or omissions that may be contained within this manual. In no event shall Vision be liable for any loss of profit including
(but not limited to) direct, indirect, special, incidental, consequential, or other damages resulting from any defect or
omission in this manual, even if previously advised of the possibility of such damages.
In the interest of continued product development, Vision reserves the right to make improvements to this manual and
the products it describes at any time, without notice or obligation.
Vision Computerized Engraving and Routing Systems WVision Computerized Engraving and Routing Systems W
Vision Computerized Engraving and Routing Systems WVision Computerized Engraving and Routing Systems W
Vision Computerized Engraving and Routing Systems Warar
arar
arranty Franty F
ranty Franty F
ranty For The Vision Tor The Vision T
or The Vision Tor The Vision T
or The Vision Table:able:
able:able:
able:
Vision Computerized Engraving and Routing Systems warrants that for a period of one (1) year from the date of
delivery to the user of the Vision table, that the table will be free from defects in material and workmanship under
normal use and service. It is specifically understood that this warranty covers normal use only and shall be null and void
in the event that the Vision table is altered or modified by the user without authorization, or is subject to abuse,
neglect, or other misuse by the user. The spindle is covered by a ninety-day (90) warranty. Other equipment may be
purchased which is not included in this warranty, and may have a separate manufacturer’s warranty, which applies.
Other items considered “consumable”, are not covered and are excluded from any and all warranties. Specifically these
items include spindle motor brushes, spindle belts, lubricant, and cutters furnished with the table.
In the event a defect is discovered during the warranty period, the user shall contact Vision Computerized Engraving
and Routing Systems for instructions regarding resolution of the problem. Vision Computerized Engraving and Routing
Systems shall at its option, replace the Vision table or correct the defect or problem by repair at Vision’s manufacturing
facility or at one of its authorized field service offices. In the event of either replacement or repair, Vision Computerized
Engraving and Routing Systems shall be liable only for the cost of repairs, including parts and labor. Any incidental costs,
including the cost of shipment from the user’s location to the point of repair, and subsequent return, shall be at the
expense of the user. Vision Computerized Engraving and Routing Systems shall have no further liability hereunder.
Vision Computerized Engraving and Routing Systems shall have no obligation or liability to repair or replace, during the
warranty period, those items that form a part of the Vision table and are considered expendable by design, including
but not limited to, cutters, spindle motor brushes, and spindle belts.
The above and foregoing is the only warranty of any kind, either express or implied, including but not limited to any
warranties of merchantability and fitness for a particular purpose, made by Vision Computerized Engraving and Routing
Systems on the Vision table. Any warranties expressed by law are hereby expressly disclaimed. No oral or written
information, advice, or other communications given by Vision Computerized Engraving and Routing Systems, its
dealers, distributors, agents, or employees shall create a warranty or in any way increase the scope of this warranty.
Neither Vision Computerized Engraving and Routing Systems nor anyone who has ever been involved in the creation,
production, or delivery of the Vision table shall be liable for any direct, indirect, consequential, or incidental damages
(including but not limited to damages for loss of business profits, business interruption, loss of business information, and
the like) arising out of the use or inability to use this product.
Any software supplied by Vision Computerized Engraving and Routing Systems in conjunction with the purchase of the
Vision Engraving table, for use therewith, shall be governed by its own separate software license and warranty agree-
ment.

Page3
Safety
Safety PrecautionsSafety Precautions
Safety PrecautionsSafety Precautions
Safety Precautions
for The Phoenix Engraverfor The Phoenix Engraver
for The Phoenix Engraverfor The Phoenix Engraver
for The Phoenix Engraver
!Keep hands clear of the spindle belt during operation.
!Keep hands clear of the bottom of the spindle during operation.
!Always stop the machine before making any adjustments.
!Disconnect the table cable before servicing.
!Do not operate the system with covers removed.
!Wear safety glasses when cutting any materials that emit chips. Use of the optional vacuum
system will remove most chips
!Use extreme caution when inserting or removing cutters.

Page4

Page5
The engraving system has been shipped in more than one carton. Examine the condition of all
containers for external damage. In the event of apparent external damage, notify your carrier upon
receipt, and call your sales representative or Vision immediately.
Note: The shipping containers are considered reusable and should be stored for use in the event
of service need or upgrade.
Step 1.
Open the foam packed shipping cartons. The following items should be included:
a. The table
b. Control unit
c. Control unit accessory kit (with power strip)
d. Optional accessories you may have purchased
Check all the items in the cartons to assure they are of the correct type. Should any of the
contents be missing, damaged, or of the incorrect type, please call your sales representative
immediately.
Step 2.
Prepare a clean, level surface to put the engraving table and controller on. Carefully lift the table
and controller out of the cartons and place each on the table.
Step 3.
After unpacking the table and control unit, SAVE THE CARTONS AND FOAM PACK and
ANY OTHER BOXES. They can be reused in the event the system must be transported
to another location or returned for service. Improper packaging for shipment can
damage the table or controller and may void the warranty.
Chapter 1
Chapter 1:Chapter 1:
Chapter 1:Chapter 1:
Chapter 1:
UU
UU
Unn
nn
npacking and Tpacking and T
packing and Tpacking and T
packing and Taking Inaking In
aking Inaking In
aking Invv
vv
ventent
entent
entoror
oror
oryy
yy
y

Page6

Page7
Chapter 2:Chapter 2:
Chapter 2:Chapter 2:
Chapter 2:
TT
TT
Table Descriptionable Description
able Descriptionable Description
able Description
This chapter briefly describes the major components of the Phoenix table. Figure 2.1 shows a
labeled drawing of the Phoenix Engraver. This chapter will help you identify the parts of your table
discussed elsewhere in the manual.
*Optional equipment such as accessory vises, clamps, fixtures or vacuum systems may*Optional equipment such as accessory vises, clamps, fixtures or vacuum systems may
*Optional equipment such as accessory vises, clamps, fixtures or vacuum systems may*Optional equipment such as accessory vises, clamps, fixtures or vacuum systems may
*Optional equipment such as accessory vises, clamps, fixtures or vacuum systems may
haha
haha
havv
vv
ve been included with ye been included with y
e been included with ye been included with y
e been included with your sysour sys
our sysour sys
our systt
tt
tem. Fem. F
em. Fem. F
em. For infor inf
or infor inf
or information regarormation regar
ormation regarormation regar
ormation regarding this eqding this eq
ding this eqding this eq
ding this equipment, see theuipment, see the
uipment, see theuipment, see the
uipment, see the
individual insindividual ins
individual insindividual ins
individual instructions ftructions f
tructions ftructions f
tructions for these opor these op
or these opor these op
or these options. Ftions. F
tions. Ftions. F
tions. For descripor descrip
or descripor descrip
or descriptions of contrtions of contr
tions of contrtions of contr
tions of controlleroller
olleroller
ollers, coms, com
s, coms, com
s, computput
putput
puterer
erer
ers, ands, and
s, ands, and
s, and
software used in your system, see the manuals from the manufacturers of these units.software used in your system, see the manuals from the manufacturers of these units.
software used in your system, see the manuals from the manufacturers of these units.software used in your system, see the manuals from the manufacturers of these units.
software used in your system, see the manuals from the manufacturers of these units.
TABLE SPECIFICATIONS:
Z-Axis ClearanceZ-Axis Clearance
Z-Axis ClearanceZ-Axis Clearance
Z-Axis Clearance
(definition: the distance between the bottom of the spindle and the work surface)
Phoenix Table: 3-Inches (76 mm) Clearance
Z-Z-
Z-Z-
Z-Axis StrAxis Str
Axis StrAxis Str
Axis Strokok
okok
okee
ee
e
(definition: the travel distance of the Z-axis mechanism or spindle)
Phoenix Table: 1 Inch (25.4 mm)
TT
TT
Table Rable R
able Rable R
able Resolutionesolution
esolutionesolution
esolution
(definition: the smallest controlled motion the table is capable of)
.0005 inch on all tables (when connected by a Vision Controller)
Engraving Overall Table Shipping
Area Dimensions Type Weight
PHOENIX 12”x12” 21”x22”x11” T-Slot 75lbs.
(non-moving)
DEFINITION OF TERMS (as labeled in Fig.2.1)
1. Table Base Plate. This is the large flat plate upon which everything else is mounted. All
mechanical alignments are referenced to this plate, so the space upon which you place the
engraving table must be a reasonably level surface.
2. X-Axis Linear Rails. The steel V-rails, which allow the motion of the carriage in the X-
axis direction.
3. X-Axis Stepper Motor. Drives the carriage in the X-Axis.
4. T-Slot Table. Also referred to as the work surface, this aluminum bed supported by the
linear rails allows placement of the engraving material or special clamps and fixtures. The
slots in this table are shaped with an upside-down T, with the bottom of the T being a single-
line slot across the top of the table. The slots are used to hold various accessory holders,
clamps, and jigs. (A selection of various T-slot accessories appears in chapter 7.).
5. Gantry Assembly. The gantry or “bridge” is a large, rectangular bar suspended across
the width of the table in the X-axis. Supports the carriage assembly and travels along. the Y-
axis.
Chapter 2

Page8
(Figure 2.1) The Phoenix 1212 (non-moving T-slot table)
10. Quick Lock Vise
1. Table Base Plate
4. T-Slot Table
11. Stantions
(risers)
8. Y-Axis Stepper Motor (Dual)
7. Breakout Connector
8. Y-Axis Stepper
Motor (Dual)
3. X-Axis Stepper Motor
2. X-Axis Linear Rails
9. Engraving Motor
5. Gantry Assembly
6. Carriage Assembly
6. Carriage Assembly. The carriage assembly houses the engraving spindle, Z-Axis
mechanism and engraving motor. The carriage moves along the gantry assembly on a V-Rail.
The carriage assembly holds the engraving spindle; it raises and lowers the spindle during the
engraving process using a lead screw and stepper motor.
7. Breakout Connector. This electrical access is used to connect the table to the system
controller. The breakout connector is located on the left side of the table near the back.
8. Y-Axis Stepper Motors (2). Drives the carriage in the Y-Axis. Incorporates a dual drive
mechanism.
9. X-Axis Stepper Motor. Drives the carriage in the X-Axis. Located under the protective
sheet metal cover.
10. Engraving Motor. Drives the spindle for rotary engraving.
11. Quick-Lock Vise. A “cam” type locking device that allows quick change of parts for
engraving..
12. Stantions (Risers). Larger ones are pictured in Fig.2.1.and come standard with the
Phoenix Engraver. For added clearance, shorter ones may replace these to get more
distance between the T-Slot table and the spindle.
Chapter 2
13. Spindle
Up/Down
Knob

Page9
Chapter 2
(Figure 2.2) Current Phoenix Carriage Front view with metal covers removed
Proximity Switch
Z-Axis Stepper Motor
Down Pressure Spring Adjust
Spindle Block
13. Spindle Up/Down Knob. Raises and lowers head when power is off the the stepper
motor
SpindleUp/DownKnob

Page10

Page11
Connection of Power, Cables, and Controllers
Additional boxes may have been shipped along with your table, depending on the system ordered.
These will typically include a control unit and associated cables. The proper connection of these
cables is essential. Check the appropriate user’s manuals for your controller before attempting to
connect them it to the table. After connection of the cables as directed by your controller manual,
power can be connected to the system. It is suggested that a surge protector be used. (Surge
protectors--often called “power strips” can be purchased inexpensively at your local hardware
store.) This will allow powering all of the elements of the system at once.
NOTE: Most of the newer Vision Serial Controllers include a surge protector.
Chapter 3:Chapter 3:
Chapter 3:Chapter 3:
Chapter 3:
SeSe
SeSe
Setting Utting U
tting Utting U
tting Up The Tp The T
p The Tp The T
p The Tableable
ableable
able
(Figure 3.1) 25-pin Breakout Connector to the Vision Serial Controller
Chapter 3
Left side view of the Phoenix Engraver
Back view of the Vision Serial Controller

Page12

Page13
(Figure 4.2) Top-and-Bottom
Loading Collet Spindle
(Figure 4.1) Top-Loading Spindle
7. Cutter
8. Solid Collet
9. Split Collet
10. Pointer
11. Cutter Knob
12. Cutter Knob Setscrew
2.
4.
1.
7.
11.
5.
All Phoenix Table models include one of the following spindles:
3.
10.
1. Pulley
2. Spindle Housing
3. Micrometer
4. Retainer Ring
5. Nose cone
6. Draw Bar
12.
9.
8.
6.
Chapter 4
Chapter 4:Chapter 4:
Chapter 4:Chapter 4:
Chapter 4:
TT
TT
Table Aable A
able Aable A
able Adjustmentsdjustments
djustmentsdjustments
djustments

Page14
Zeroing Cutters for Top-Loaded Spindles (see figure 4.1)
1. Turn the micrometer to zero. This provides a starting point and reference for setting the
depth accurately. It’s important to note that the micrometer should be threaded onto the
spindle housing sufficiently to prevent excessive play in the micrometer and nosecone. If
there are too few threads holding the micrometer in place it will move during the engraving
process. The best starting position is 3 or 4 complete revolutions from the top.
CAUTION: When you loosen the setscrew in this step, the cutter may
easily fall out of the spindle and can cause cutter tip damage. Use
one hand to hold the cutter before loosening.
2. With the appropriate cutter installed in the spindle, loosen the setscrew in the brass
cutter knob with a spline wrench (commonly referred to as the cutter wrench).
3. Gently place a piece of metal (brass preferred) against the nosecone so as to push the
cutter even with the bottom of the nosecone. Now the cutter should be flush with the
nosecone. Retighten the cutter knob setscrew. Your cutter is now zeroed. Rotating the
micrometer clockwise will adjust the depth of the cut. Each click of the micrometer = .001”.
A full revolution is .025”.
Zeroing Cutters for Top-and-Bottom-Loaded Collet Spindles (see
figure 4.2)
The collet spindle can be used for either top loaded or bottom loaded cutters. To install a top
loaded cutter in the collet spindle, first set the micrometer to zero. Loosen the knurled draw bar
on the very top of the spindle slightly. Remove the cutter knob from
the cutter, and slide the cutter into the spindle. Place a piece of flat
material against the bottom of the nosecone and lower the cutter until
it rests against the material. Tighten the draw bar around the cutter,
make sure it is tight. Then reattach the cutter knob to the top of the
cutter and screw it in counterclockwise until secure. Be careful
screwing the cutter knob in, as counterclockwise is the direction to
unscrew the draw bar (see fig 4.3). Never use pliers! The cutter
depth can be adjusted by turning the micrometer counter clockwise.
Note: If using 2" short cutters, install them from the bottom. Use the
draw bar on the very top of the spindle to tightly secure the cutter.
A solid collet, if purchased, can be installed in place of the split collet
for burnishing. Install the collet in the bottom of the spindle and
tighten the draw bar firmly. The spindle now acts as a normal top
loaded spindle for ease of operation. The split collet can be reinstalled
when required.
(Figure 4.3) Tightening the
cutter knob in the draw bar.
Chapter 4

Page15
(Figure 4.4) Diamond Drag Adapter
Pulley
Spindle
Housing
Micrometer
Diamond Drag
Adapter
Diamond Engraving
To install a diamond drag adapter, remove the retainer ring and nose cone from the bottom of the
spindle and replace with the diamond drag adapter. (See fig.4.4) For diamond drag cutting, the
engraving motor is turned off and the cutter “drags” across the material. This is accomplished
with the motor on/off switch in the “off” position. Down pressure against the material can be
reduced or increased as necessary by adjusting the spindle pressure knob as described in the
next section.
Chapter 4
Leveling the Phoenix Table (see fig.4.5)
All current Phoenix tables will have table level adjustments. The table may be leveled by first
loosening the 4 hex head screws that secure the t-slot table to the risers (see figure 4.5), and
then tightening or loosening the small set screws located next to the hex head screws. Once
level, the hex head screws can be re-tightened. This is a tricky process without a dial indicator to
measure accurately the run out from corner to corner. Table level adjustment can be made
without the indicator but the accuracy and time may be prohibitive.

Page16
Chapter 4
(Figure 4.5) Front Angled View of Phoenix Table
Showing the location of hex head shoulder bolts
hex head shoulder bolts (4)
Replacing The Stantions For Additional Clearance (see fig.4.5 and 4.6)
This procedure will allow the user to lower the t-slot table for fixturing of taller objects. It’s
important to understand that the total Z-axis stroke does not increase, however some additional
reach can be achieved by lowering the spindle in its block.
To change from the standard 2 3/8” stantions (risers) to the shorter 1 5/8” stantions, remove the
4 shoulder bolts from the top of the t-slot table. Use a 1/8” hex key. Be careful not to strip the
bolt head when removing or replacing. After the bolts are removed, the t-slot table may be set
aside. Mark the 4 stantions as shown in fig.4.6. Keep the orientation the same when you
replace the stantions. This will ensure that the table will be level when the taller stantions are put
back in place. A flat groove has been
machined into the sides (near the top) of
the stantions (see fig.4.5a). Use a 7/8”
open end or crescent wrench to remove the
stantions by turning counterclockwise. You
can add the shorter stantions to the table
base by following the above procedure in
reverse order. Tighten the stantion in place
and replace the t-slot table. If the table is
equipped with leveling screws, you may
further level the table using the procedure
mentioned in the previous section.
stantions (4)
(Figure 4.6) Top View of
Current Phoenix Model
12
3
4
(Figure 4.5a) Close Up
side view of a stantion

Page17
Chapter 5:Chapter 5:
Chapter 5:Chapter 5:
Chapter 5:
TT
TT
Table Maintable Maint
able Maintable Maint
able Maintenanceenance
enanceenance
enance
Chapter 5
Vision strives for the highest quality in their manufacturing process to
provide you with the most cost effective, reliable engraving machine
in use today. Please remember that proper maintenance and care is
necessary to achieve maximum product life expectancy.
The engraving environment generates small plastic and metal chips as well as other particles
during operation. As with any machinery, your engraving system should be kept as clean as
possible to minimize wear and tear, and to improve final quality of the engraved product.
REMOVING CHIPS
Plastic and metal chips, generated during the engraving process, should be removed from the
engraving surface periodically. A portable vacuum is suggested for chip removal, but applying
direct suction to the spindle area is not recommended.
Note that this cleaning can be minimized and greatly simplified through the use of the optional
vacuum chip removal system. The vacuum chip removal system removes chips and dust created
by engraving. This system can also extend the life of other components in the system, as prompt
removal of chips reduces contamination and overheating in the spindle area. The vacuum chip
removal system also keeps the nose cone from skipping over letters due to chips on the
engraving surface.
Cleaning The Nose Cone
The nose cone around the cutter may accumulate dust and chips that cannot be removed by
sucking them off or blowing on them with low pressure air. (CAUTION! High pressure air can
damage the spindle.) Two types of nose cones are available; one nose cone is designed to be
used with the vacuum system, the other is not. Cleaning methods depend on the type of nose
cone in use.
With a vacuum chip removal system (see fig 5.1), most of the chips will be removed during the
engraving process. If the suction nozzle becomes clogged, remove the hose connection to the
nose cone. Remove the cutter, then unscrew the vacuum nose cone. Using a vacuum or an air
hose, clean out the nose and the vacuum tube leading to the nose cone. Reinstall the nose cone
and the vacuum hose.
(Figure 5.1) Vacuum nose with hose

Page18
Without a vacuum chip removal system you should remove the cutter before attempting to clean
the nose cone. The nose cone retainer ring, the nose cone, and the micrometer collar should all
be removed and cleaned using a vacuum or blowing air. The three nose cone components should
be removed and cleaned at least every day, and as frequently as necessary. Failure to clean the
nose cone regularly will result in premature spindle failure.
Cleaning the Vacuum Filter (only with the vacuum chip removal option)
On systems with a vacuum chip removal system, frequent cleaning of the vacuum filter is
necessary for proper performance. When engraving with the vacuum filter system, the filter
should be checked and cleaned several times a day, depending on the amount of engraving
done. If the vacuum does not appear to be functioning efficiently, clean the filter more frequently
as needed.
To clean the vacuum filter system, disconnect the vacuum hose from the canister. On the lid of
the canister, note the three wing nuts. Loosen these nuts enough to allow the attached bolts to
swing away from the lid, allowing removal of the lid. Do not loosen the nuts enough to remove
them completely. Remove the canister lid and inside you will find two filters. Carefully remove the
inner, paper filter. (The paper and cloth filters tend to stick together.) Empty the paper filter, and
shake it out completely, being careful not to damage it as the filters are reusable. After shaking
out the paper filter remove and empty the cloth filter in the same manner as the paper filter. Do
not wash either filter. Place the paper filter back inside the cloth filter, and place the cloth filter
back inside the vacuum canister.
LUBRICATION FOR PHOENIX MODELS
Lubricating the Z-Axis Assembly
A light amount of oil (3-in-1 preferred) should be used to coat the V-rails. Do not allow any
excess oil to accumulate on the rails since it will attract dust and engraving chips. After applying
lubricant, run the mechanism up and down the rail to evenly distribute the oil.
Lubricating the X-Axis Bridge Assembly
Same as above.
Lubricating the Y-Axis Linear Rails
Apply 2-3 drops of light oil on the rail and rub in with your fingers. XY jog the bridge back and
forth to evenly distribute the oil.
Lubricating the X-Y-Z-Axis lead screws
A light lubrication of the X and Y lead screws should be performed after every week of
usage. Use silicone lubricant only. To reach the Z-Axis lead screw, turn the spindle up/
down knob to the furthest down position, which exposes the portion of the Z lead screw
that requires lubrication. Spray a light coating along the lead screw.
HINT: To avoid having to remove the metal covers, use a nozzle
extension for your can of spray lubricant. DO NOT use any lubricant
other than silicone, as it may become sticky and cause a
buildup that can cause mechanical failure.
Chapter 5

Page19
What not to lubricate
Many of the bearings and assemblies in your engraving machine are sealed and/or coated using
special low-friction methods and should not be lubricated.
DO NOT attempt to lubricate the spindle or the spindle bearings. If you suspect
lubrication problems, call your dealer/representative for instructions, as further
lubrication may harm the machine.
DO NOT oil the X or Y stepper motors. The only motor that requires lubrication is the
Z-motor and lead screw combination. (See lubricating the Z-axis assembly above.)
Oiling the stepper motors can permanently damage the motors.
REPAIRS, REPLACEMENTS, AND ADJUSTMENTS
How to replace a belt
A belt is used to drive the spindle engraving system. It runs between a drive pulley and the
spindle pulley. If it needs replacement, remove the old belt by rolling it to the top of the spindle
pulley, and give it a slight stretching motion to snap it off the end. Once loose, it can easily be
removed from the machine. Now position the new belt around the drive pulley, then stretch it to
snap over the top of the pulley.
Motor Brushes
Carbon Motor Brush
Chapter 5
(Figure 5.2) The Phoenix
engraving motor and brushes
Shown from front and side view
Current Phoenix 24V Motor
Threaded Brush Cap

Page20
Chapter 5
The motor brushes on the engraving motor should be inspected regularly, and replaced when
worn. Two brush assemblies are included with the accessories package. (One for each side of
the motor.)
Inspect the brushes for possible replacement annually using the following procedure
(see figure 5.3).
The engraving motor is located under the sheet metal top cover. Remove the cover to gain acces
to the engraving motor.
CAUTION: Disconnect the gray table cable from the Phoenix table.
This will ensure that no power is applied to the table.
Locate and remove the 4 button head screws that mount the engraving motor to the carriage.
This will allow the engraving motor to be rotated to gain access to the motor brush caps. You do
not need to remove the motor from the carriage to get to the brush caps. Simply rotate the
motor left or right 1/4 turn to fully see the brush cap. Using a flat tip screwdriver, carefully
remove the motor brush caps and inspect the carbon brush for wear. DO NOT ATTEMPT TO
SEPARATE THE MOTOR BRUSH FROM THE SPRING. Replace brushes as necessary.
To complete the job, reverse the order of the above listed steps and ensure that the motor mount
is secure to the carriage before replacing the carriage top cover.
If either brush needs to be replaced, replace both brushes as a set.
(Figure 5.3) The Phoenix Carriage
Shown from rear view with top cover removed
SpindleUp/DownKnob
(for pressure spring adjustment)
Z-Axis Limit
Motor Mount
X-Axis Leadscrew
Brush Cap (x2)
Button Head
Screws (x4)
EngravingMotor
This manual suits for next models
2
Table of contents
Other Vision Engraver manuals

Vision
Vision Phoenix 1212 User manual
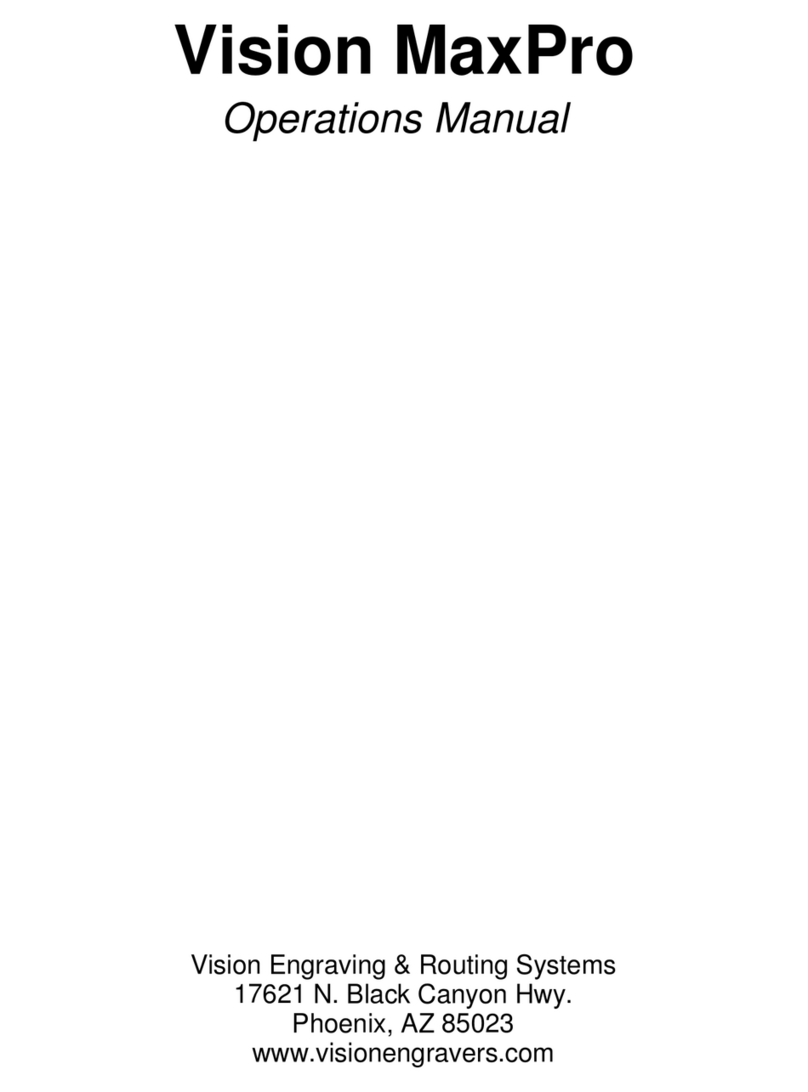
Vision
Vision MaxPro User manual
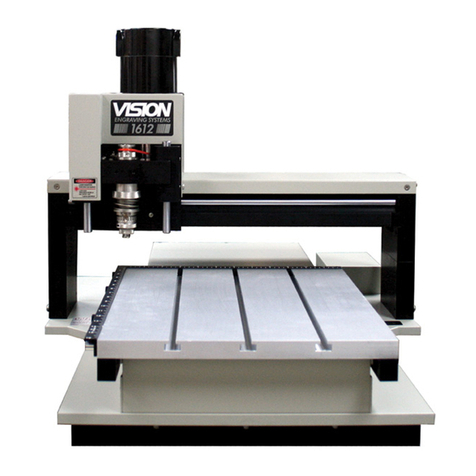
Vision
Vision 5 Series User manual
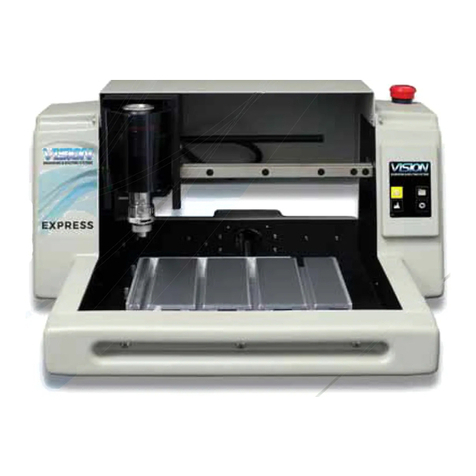
Vision
Vision Express S5 User manual

Vision
Vision Cylindrical User manual
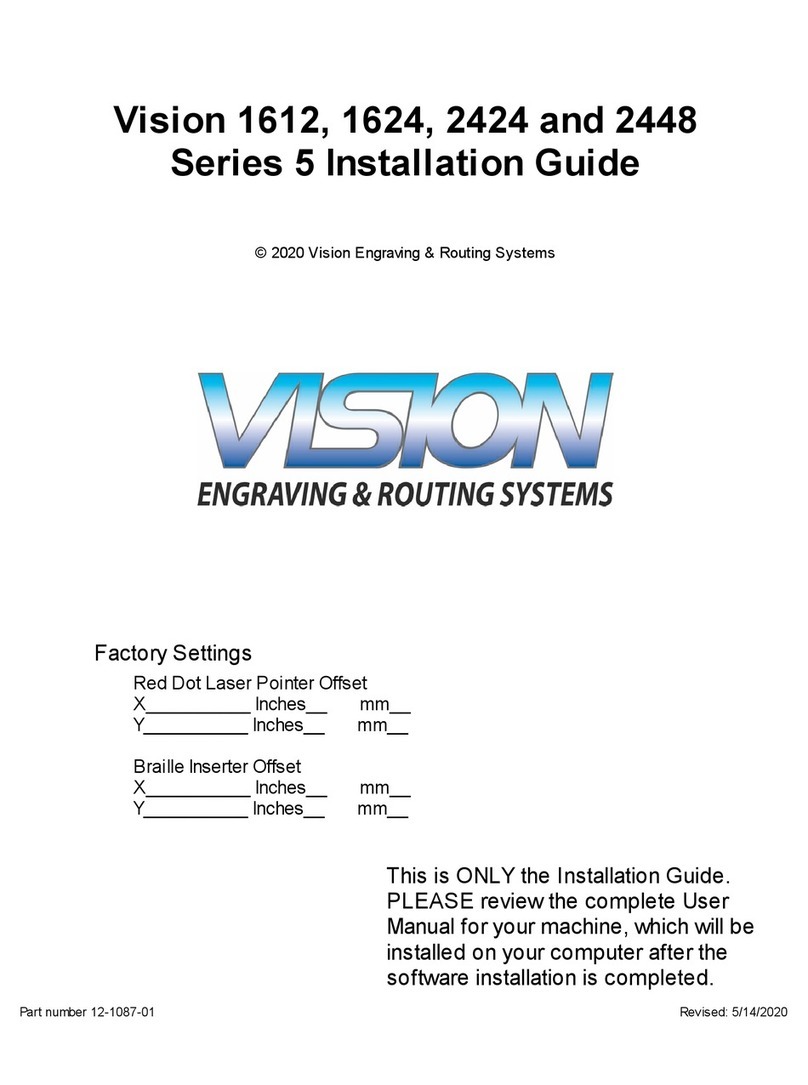
Vision
Vision 5 Series User manual
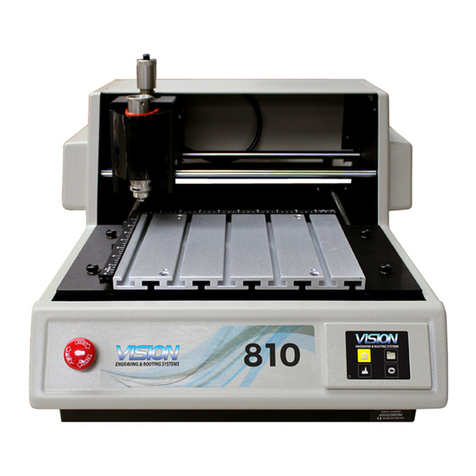
Vision
Vision VE-810 User manual
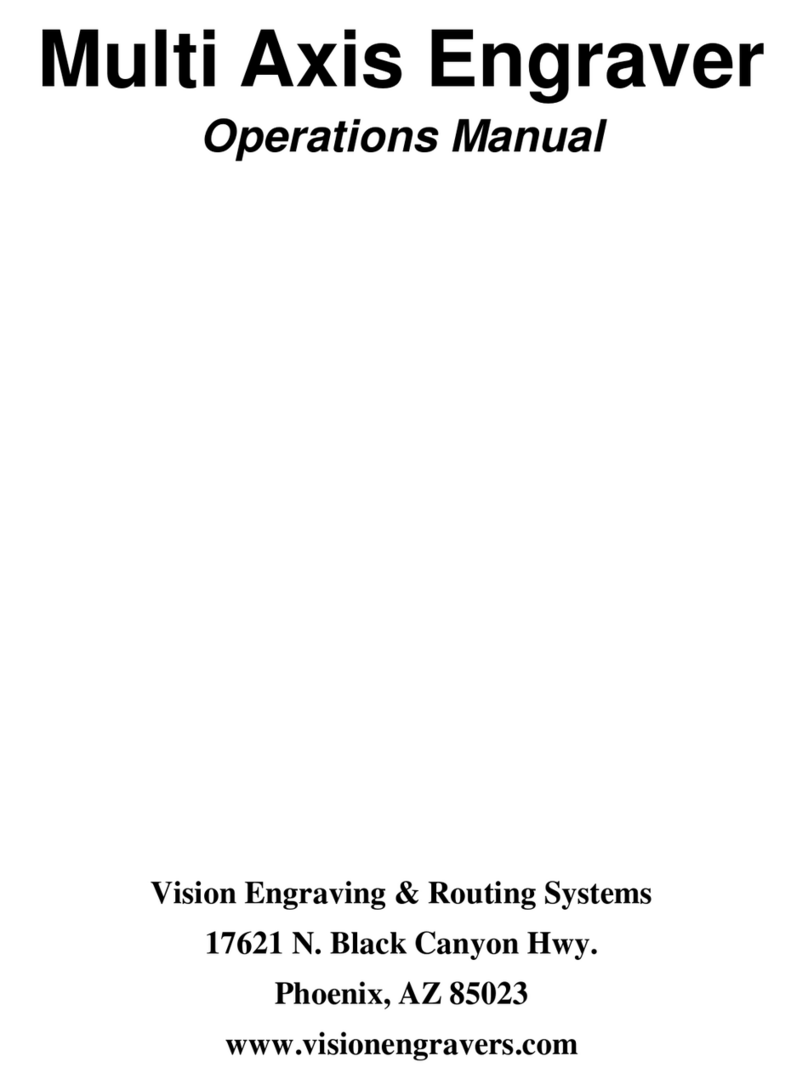
Vision
Vision Multi Axis User manual

Vision
Vision MAX Pro User manual

Vision
Vision 1624R User manual