WIKA GDM-100-T User manual

Operating instructions
Betriebsanleitung
EN
DE
Hybrid-Gasdichtewächter, Typ GDM-100-T
Hybrid gas density monitor with Modbus®- or analog 4 ... 20 mA output signal
Hybrid gas density monitor, model GDM-100-T

2
14535893.01 01/2022 EN/DE
WIKA operating instructions, model GDM-100-T
EN
DE
© 01/2022 WIKA Alexander Wiegand SE & Co. KG
All rights reserved. / Alle Rechte vorbehalten.
WIKA®is a registered trademark in various countries.
WIKA®ist eine geschützte Marke in verschiedenen Ländern.
Prior to starting any work, read the operating instructions!
Keep for later use!
Vor Beginn aller Arbeiten Betriebsanleitung lesen!
Zum späteren Gebrauch aufbewahren!
Betriebsanleitung Typ GDM-100-T Seite 41 - 77
Operating instructions model GDM-100-T Page 3 - 40

3WIKA operating instructions, model GDM-100-T
EN
14535893.01 01/2022 EN/DE
Contents
1. General information 4
2. Design and function 5
3. Safety 6
4. Transport, packaging and storage 13
5. Commissioning, operation 14
6. Faults 28
7. Maintenance, cleaning and recalibration 30
8. Dismounting, return and disposal 31
9. Specifications 32
Contents
Declarations of conformity can be found online at www.wika.com

4WIKA operating instructions, model GDM-100-T
EN
14535893.01 01/2022 EN/DE
1. General information
■The instrument described in the operating instructions has been designed and
manufactured using state-of-the-art technology. All components are subject to strin-
gent quality and environmental criteria during production. Our management systems
are certified to ISO 9001 and ISO 14001.
■These operating instructions contain important information on handling the instru-
ment. Working safely requires that all safety instructions and work instructions are
observed.
■Observe the relevant local accident prevention regulations and general safety regula-
tions for the instrument's range of use.
■The operating instructions are part of the product and must be kept in the immediate
vicinity of the instrument and readily accessible to skilled personnel at any time. Pass
the operating instructions on to the next operator or owner of the instrument.
■Skilled personnel must have carefully read and understood the operating instructions
prior to beginning any work.
■The general terms and conditions contained in the sales documentation shall apply.
■Subject to technical modifications.
■Further information:
- Internet address: www.wika.de / www.wika.com
- Relevant data sheets: SP 60.23
SP 61.16 (model GLTC-CV)
- Application consultant: Tel.: +49 9372 132-0
Fax: +49 9372 132-406
info@wika.de
1. General information

5WIKA operating instructions, model GDM-100-T
EN
14535893.01 01/2022 EN/DE
Hybrid gas density monitor with integrated
transmitter, model GDM-100-T
Electrical connection
Front cable socket: Switching outputs
Rear cable socket: Transmitter
Process connection, spanner flats
Process connection, thread
Hybrid gas density monitor with attached
transmitter, model GDM-100-T
2. Design and function
2.1 Overview
2. Design and function
2.2 Description
The switch contacts permanently installed in the gas density monitor close or open at
set limit values, depending on the switching function. Switching functions are: Normally
closed, normally open, change-over contact.
The magnetic snap-action contacts are control switches which open or close connected
electric circuits via a contact arm which is moved by the instrument pointer.
The integrated or attached transmitter transmits the measured value via an analogue or
digital output signal.
2.3 Scope of delivery
Cross-check scope of delivery with delivery note.

6WIKA operating instructions, model GDM-100-T
EN
14535893.01 01/2022 EN/DE
3. Safety
3.1 Explanation of symbols
WARNING!
... indicates a potentially dangerous situation that can result in serious
injury or death, if not avoided.
CAUTION!
... indicates a potentially dangerous situation that can result in light injuries
or damage to property or the environment, if not avoided.
Information
... points out useful tips, recommendations and information for efficient
and trouble-free operation.
3.2 Intended use
Wherever the gas density of SF6gas must be indicated locally and, at the same time,
circuits need to be switched, the model GDM-100-T hybrid gas density monitor finds its
use.
The integrated or attached digital transmitter transmits the parameters of gas density,
pressure and temperature as electrical signals via a Modbus®RTU protocol.
The integrated or attached analogue transmitter transmits the absolute pressure refer-
enced to 20 °C or the gas density in g/l for SF6gas as a 4 ... 20 mA signal.
Gas density monitors are modified contact pressure gauges, specially developed for the
use of SF6gas.Temperature influences acting on the enclosed SF6gas are compensat-
ed by a compensation system.
The gas density monitors are specially designed for the respective application in switch-
gear (pure SF₆ gas, gas mixtures, calibration pressure, switch points ...). Before use,
check whether this instrument is suitable for the intended application.
Only use the instrument in applications that lie within its technical performance limits
(e.g. max. ambient temperature, material compatibility, ...).
→ For performance limits, see chapter 9 “Specifications”.
This instrument is not permitted to be used in hazardous areas!
The instrument has been designed and built solely for the intended use described here,
and may only be used accordingly.
3. Safety

7WIKA operating instructions, model GDM-100-T
EN
14535893.01 01/2022 EN/DE
The technical specifications contained in these operating instructions must be
observed. Improper handling or operation of the instrument outside of its technical
specifications requires the instrument to be taken out of service immediately and
inspected by an authorised WIKA service engineer.
The manufacturer shall not be liable for claims of any type based on operation contrary
to the intended use.
3.3 Improper use
WARNING!
Injuries through improper use
Improper use of the instrument can lead to hazardous situations and
injuries.
▶Refrain from unauthorised modifications to the instrument.
▶Do not use the instrument within hazardous areas.
Any use beyond or different to the intended use is considered as improper use.
3.4 Responsibility of the operator
The instrument is used in the industrial sector. The operator is therefore responsible for
legal obligations regarding safety at work.
The safety instructions within these operating instructions, as well as the safety, accident
prevention and environmental protection regulations for the application area of the instru-
ment must be maintained.
The operator is obliged to maintain the product label in a legible condition.
To ensure safe working on the instrument, the operating company must ensure
■that suitable first-aid equipment is available and aid is provided whenever required.
■that the operating personnel are regularly instructed in all topics regarding work
safety, first aid and environmental protection and know the operating instructions and
in particular, the safety instructions contained therein.
■that the instrument is suitable for the particular application in accordance with its
intended use.
■that personal protective equipment is available.
3. Safety

8WIKA operating instructions, model GDM-100-T
EN
14535893.01 01/2022 EN/DE
3.5 Personnel qualification
WARNING!
Risk of injury should qualification be insufficient
Improper handling can result in considerable injury and damage to property.
▶The activities described in these operating instructions may only be
carried out by skilled personnel who have the qualifications described
below.
Skilled personnel
Skilled personnel, authorised by the operator, are understood to be personnel who,
based on their technical training, knowledge of measurement and control technology
and on their experience and knowledge of country-specific regulations, current stand-
ards and directives, are capable of carrying out the work described and independently
recognising potential hazards.
Specically when using SF₆ gas
The plant operator must ensure that the handling of SF₆ gas is only carried out by a
qualied company or by qualied persons who have been specically trained in accord-
ance with IEC 62271-4 or IEC 60480, section 10.3.1.
3.6 Personal protective equipment
The personal protective equipment is designed to protect the skilled personnel from
hazards that could impair their safety or health during work. When carrying out the
various tasks on and with the instrument, the skilled personnel must wear personal
protective equipment.
Follow the instructions displayed in the work area regarding personal protective
equipment!
The requisite personal protective equipment must be provided by the operating company.
Safety goggles in accordance with EN 166, class 2, mechanical
strength class S
The safety goggles must be worn over the entire period when working on
hoses or gas containers (e.g. gas cylinders, tanks).
The safety goggles protect the eyes from any flying particles, escaping
gas and liquid splashes.
Protective gloves against heat in accordance with EN ISO 13732-1
and against cold in accordance with EN ISO 13732-3
The protective gloves must be worn over the entire period when working
on hoses, gas containers (e.g. gas cylinders, tanks) or components which
heat up to over 60 °C.
3. Safety

9WIKA operating instructions, model GDM-100-T
EN
14535893.01 01/2022 EN/DE
3.7 Handling of insulating gases and gas mixtures
SF₆ gas is a greenhouse gas which is listed in the Kyoto Protocol. SF₆ gas must not be
released into the atmosphere, but must be collected in suitable containers.
Properties of insulating gases
■Colourless and odourless
■Chemically neutral
■Inert
■Not flammable
■Heavier than air
■No toxicity
■No damage to the ozone layer
Detailed information is given in IEC 60376 and IEC 62271-4.
Danger of suocation caused by insulating gases and gas mixtures
High concentrations of gases can lead to asphyxiation, since breathable air is displaced
from the lungs with the inhalation of gas.
Since SF₆ gas is heavier than air, it collects, especially, at ground level or lower-lying
rooms below the reference level (e.g. cellars). This is particularly dangerous since SF₆
gas is colourless and odourless and thus may be imperceptible to people.
3.8 Danger caused by decomposition products
Insulating gas in electrical systems may contain decomposition products generated by
electric arcs:
■Gaseous sulphur fluorides
■Sulphur hexafluorides
■Solid and atomized metal fluorides, metal sulphides, metal oxides
■Hydrogen fluoride
■Sulphur dioxide
Decomposition products can be harmful to health.
■They can cause poisoning by inhalation, ingestion or contact with the skin.
■They may be irritating to the eyes, the respiratory system or the skin and burn them.
■Inhalation of large quantities may damage the lungs.
Observe the following safety instructions in order to avoid danger from insulating gas:
■Wear personal protective equipment.
■Read the material safety data sheet of the gas supplier.
■With large leakage, evacuate the area quickly.
■Ensure good ventilation.
■Ensure the leak tightness of the equipment with a leak detector (e.g. model GIR-10).
3. Safety

10 WIKA operating instructions, model GDM-100-T
EN
14535893.01 01/2022 EN/DE
3. Safety
3.9 Valid standards and directives for SF₆ gas
Installation, assembly, commissioning
■BGI 753 (SF₆ plants and equipment in Germany)
■IEC 62271-4 (Handling of SF₆ gas)
■IEC 60376 (New SF₆ gas, technical grade SF₆ gas)
■IEC 60480 (Used SF₆ gas)
■CIGRE report 276, 2005 (Practical SF₆ gas handling instructions)
Leakages during operation
■IEC 60376 (New SF₆ gas, technical grade SF₆ gas)
■IEC 60480 (Used SF₆ gas)
■CIGRE 2002 (“SF₆ gas in the electrical industry”)
Repair work and maintenance
■IEC 62271-4 (Use and handling of SF₆ gas in high-voltage switchgear and controlgear)
■CIGRE 1991 (Handling of SF₆ gas)
■CIGRE report 276, 2005 (Practical SF₆ gas handling instructions)
Information
SF₆ gas is a colourless and odourless, chemically neutral, inert and non-in-
ammable gas which is approx. ve times heavier than air, not toxic and not
harmful to the ozone layer.
Detailed information is given in IEC 60376 and IEC 62271-4.

11WIKA operating instructions, model GDM-100-T
EN
14535893.01 01/2022 EN/DE
3. Safety
3.10 Labelling, safety marks
Product label, model GDM-100-T with integrated transmitter (example)
11
Model description
Switch contacts: Front cable box
Electrical characteristics of the sensor
Sensor: rear cable box
Pin assignment of the sensor
Switching thresholds of the switch contacts
Date of manufacture
P# product number
State of the switch at minimum scale value
Pin assignment and switching thresholds
Electrical characteristics of the switch contacts
11

12 WIKA operating instructions, model GDM-100-T
EN
14535893.01 01/2022 EN/DE
Product label, model GDM-100-T with attached transmitter (example)
Model description
Model designation of the switch contact
Electrical characteristics
Switching thresholds
Date of manufacture
P# product number
State of the switch at minimum scale value
Case filling
Pin assignment
Product label of the attached transmitter (example)
Model
Measuring range compensated pressure
Density equivalent of the full scale of compensated pressure
Pin assignment
Logos
Coded date of manufacture
Temperature range
Communication
Supply voltage
Gas mixture
P# article number
S# serial number
GD-20-A
DE-63911 Klingenberg
Made in Germany
11
11
3. Safety

13WIKA operating instructions, model GDM-100-T
EN
14535893.01 01/2022 EN/DE
4. Transport, packaging and storage
4.1 Transport
Check the instrument for any damage that may have been caused by transport.
Obvious damage must be reported immediately.
CAUTION!
Damage through improper transport
With improper transport, a high level of damage to property can occur.
▶When unloading packed goods upon delivery as well as during internal
transport, proceed carefully and observe the symbols on the packaging.
▶With internal transport, observe the instructions in chapter 4.2 “Packag-
ing and storage”.
4.2 Packaging and storage
Do not remove packaging until just before mounting.
Keep the packaging as it will provide optimum protection during transport (e.g. change
in installation site, sending for repair).
WARNING!
Physical injuries and damage to property and the environment
caused by hazardous decomposition products
Before storing the instrument, any residual decomposition products must
be removed.
▶For cleaning, see chapter 7.2 “Cleaning”
Permissible conditions at the place of storage:
■Storage temperature: -40 ... +60 °C
■Humidity: ≤ 90 % r. h. (non-condensing)
Avoid exposure to the following factors:
■Soot, vapour, dust and corrosive gases
■Hazardous environments, flammable atmospheres
Store the instrument in its original packaging in a location that fulfils the conditions
listed above. If the original packaging is not available, pack and store the instrument as
described below:
1. Place the instrument, along with the shock-absorbent material, in the packaging.
2. If stored for a prolonged period of time (more than 30 days), place a bag containing
a desiccant inside the packaging.
4. Transport, packaging and storage

14 WIKA operating instructions, model GDM-100-T
EN
14535893.01 01/2022 EN/DE
5. Commissioning, operation
5.1 Mechanical mounting
CAUTION!
Physical injuries and damage to property and the environment
through faulty instrument
Prior to commissioning, the instrument must be subjected to a visual
inspection. Only use the instrument if it is in perfect condition with respect
to safety.
5.1.1 Requirements for the installation point
■For outdoor applications, the selected installation location has to be suitable for the
specified ingress protection, so that the instrument is not exposed to impermissible
weather conditions.
■The sealing faces at the instrument and at the measuring location have to be undam-
aged and clean.
The measuring instruments must be mounted in the common mounting position per
EN 837-1, with a max. permissible incline of 5° on all sides.
The measuring location should preferably be positioned directly at the
gas compartment. A measurement at the end of measuring lines prevents
optimal results through unwanted temperature differences to the main
tank.
5.1.2 Installation
■With transport or storage, it can occur that gas density monitors warm up or cool
down and this results in pointer movements.These pointer movements are caused by
the compensation system. To make sure that the instruments have adapted sufficient-
ly to ambient temperature, at least 2 hours at 20 °C must be allowed for adaptation
to the temperature.Then, in the depressurised state, the pointer will sit within the
tolerance bar.
■Corresponding to the general technical rules for pressure gauges (e.g. EN 837-2
“Selection and installation recommendations for pressure gauges”) when screwing in
the instrument, the force required to do this must not be applied through the case, but
only through the spanner flats provided for this purpose and using a suitable tool.
■When screwing in, do not cross the threads.
For parallel threads, use flat gaskets, lens-type sealing rings or WIKA profile sealings
at the sealing face . With tapered threads (e.g. NPT threads), sealing is made in the
threads , using a suitable sealing material (EN 837-2).
5. Commissioning, operation

15WIKA operating instructions, model GDM-100-T
EN
14535893.01 01/2022 EN/DE
The tightening torque depends on the sealing used. In order to orientate the measuring
instrument so that it can be read as well as possible, a connection with LH-RH adjusting
nut or union nut should be used.When a blow-out device is fitted to an instrument, it must
be protected against being blocked by debris and dirt.
5.1.3 Temperature load
The installation of the instrument should be made in such a way that the permissible
operating temperature, also considering the effects of convection and thermal radiation,
neither exceeds nor falls below the permissible limits.
The influence of temperature on the indication and measurement accuracy must be
observed.
5.2 Electrical mounting of the gas density monitor
■The instrument must be grounded via the process connection.
■For cable outlets, make sure that no moisture enters at the cable end.
■Select a cable diameter that matches the cable bushing of the connector. Make sure
that the cable gland of the mounted connector has a tight fit and that the seals are
present and undamaged.Tighten the threaded connection and check that the sealing
is correctly seated, in order to ensure the ingress protection.
■Connection details and switching functions are given on the product label. Connec-
tion terminals and ground terminal are appropriately marked.
5.2.1 Limit values for the contact load with resistive load
Gas-filled instruments Liquid-filled instruments
Maximum rated operating
voltage Ueff
AC 250 V AC 250 V
Rated operating current
Switch-on current 1 A 1 A
Switch-off current 1 A 1 A
Continuous current 0.6 A 0.6 A
Maximum switching power 30 W, 50 VA 20 W, 20 VA
Sealing in the thread
Spanner ats
Sealing face
5. Commissioning, operation

16 WIKA operating instructions, model GDM-100-T
EN
14535893.01 01/2022 EN/DE
Do not exceed the limit values. In order to permanently ensure safe operation, the
following load values are recommended:
Voltage (per
IEC 38)
Gas-filled instruments Liquid-filled instruments
Resistive load Inductive load Resistive load Inductive load
DC/AC DC AC cos ϕ >0.7 DC AC cos ϕ >0.7
230 V 100 mA 120 mA 65 mA 65 mA 90 mA 40 mA
110 V 200 mA 240 mA 130 mA 130 mA 180 mA 85 mA
48 V 300 mA 450 mA 200 mA 190 mA 330 mA 130 mA
24 V 400 mA 600 mA 250 mA 250 mA 450 mA 150 mA
The switching current must not be less than 20 mA with low voltages for switching relia-
bility reasons.
For higher loads, and for instruments with liquid-lled cases, WIKA model
905.1X contact protection relays are recommended
Overcurrent protectors
The instruments do not provide for incorporated overcurrent protectors. Should protec-
tors be required, the following values in accordance with EN 60 947-5-1 are to be
recommended.
■Voltage 24 V: 2 A
■Voltage 250 V: 1 A
5.2.2 Contact protection measures
Mechanical contacts must not exceed the specified electrical values for switching
current, switching voltage and switching power independent of each other, not even for
a short time only.
For capacitive or inductive loads we recommend one of the following protective circuits:
5. Commissioning, operation

17WIKA operating instructions, model GDM-100-T
EN
14535893.01 01/2022 EN/DE
Inductive load with DC voltage
With DC voltage the contact protection can be achieved via a free-wheeling diode,
connected in parallel to the load.The polarity of the diode must be arranged so that it
closes when the operating voltage is on.
Inductive load with AC voltage
With AC voltage two protective measures are possible:
Capacitive load
With capacitive loads elevated switch-on currents arise.These can be reduced by
series-connecting resistors in the supply line.
Example: Contact
protection measure
with free-wheeling
diode
Contact
Diode Load
Example: Contact
protection measure
with voltage-dependent
resistor VDR
Example: Contact
protection measure
with RC element
Load
Load
Examples: Contact protection measure with current-limiting resistor
Load Load
U
B
R1
U
B
R1
5. Commissioning, operation

18 WIKA operating instructions, model GDM-100-T
EN
14535893.01 01/2022 EN/DE
5.2.3 Switch point setting
The switch points have a fixed setting as standard and cannot be adjusted. Thus, an
undesired adjustment of the switch points is excluded.
With customer-specific, adjustable switch points, with the accompanying adjustment
key, the desired set point can be set via the adjustment lock in the window.
5.3 Electrical installation of the gas density monitor with digital output signal
(Modbus®RTU)
WARNING!
The instrument shield does not act as a protective conductor for protection
of personnel, rather as a functional ground in order to shield the instru-
ment from electromagnetic fields.
5.3.1 Connection assembly (model GD-20-D)
■Use a cable consisting of shielded twisted pair data lines with suitable characteristics
for the particular operating conditions.
■Select a cable diameter that matches the cable bushing of the connector or the cable
socket. Make sure that the cable gland of the mounted connector or mounted cable
socket has a tight fit and that the seals are present and undamaged.Tighten the
threaded connection and check that the seal is correctly seated, in order to ensure the
ingress protection.
■Make sure that no moisture enters at the cable end.
5. Commissioning, operation

19WIKA operating instructions, model GDM-100-T
EN
14535893.01 01/2022 EN/DE
5.3.2 Pin assignment of attached, digital transmitter (model GD-20-D)
Circular connector M12 x 1 (5-pin)
1 - -
2 U+Supply voltage
3 U-Ground
4 A Signal RS-485
5 B Signal RS-485
5.3.3 Pin assignment of integrated, digital transmitter (model GD-20-D)
Modbus®-RTU via RS-485 interface in rear cable socket
Rear cable socket
1- -
2U+DC 10 ... 30 V
3U-Ground
4A RS-485 signal
5B RS-485 signal
6- -
5.3.4 Requirements for shielding and grounding
■Only use shielded cables and connect the shield on one side to the read-out unit.
■The gas density sensor is grounded via the process connection of the mechanical
base instrument.
■Ensure that no earth circuits can occur.
5.3.5 RS-485
The physical layer for the Modbus®protocol is the serial RS-485 interface per EIA/
TIA-485.The differential signal between pins 4 and 5 (A and B) is evaluated with a
2-wire system (half-duplex).
5.4 Modbus®
The Modbus®communication protocol is based on a master/slave architecture.The
protocol implemented in the model GD-20 gas density sensor is Modbus®-RTU with serial
transmission via a 2-wire RS-485 interface.
The Modbus®protocol is a single-master protocol.This master controls the entire data
transfer and monitors any possible timeouts (no reply from the addressed instrument).
The connected instruments may only send telegrams after request by means of the
master.
5. Commissioning, operation

20 WIKA operating instructions, model GDM-100-T
EN
14535893.01 01/2022 EN/DE
Modbus®RTU (RTU: Remote Terminal Unit) transmits the data in binary form, guaran-
teeing a good data throughput.
Detailed information on the protocol under www.Modbus.org
5.5 Modbus®start-up kit
The gas density sensor, with the optionally available start-up kit (order no. 14075896),
can be configured for operation at the measuring location.
A further function is an integrated data logger, showing measured data in a specific
cycle or writing it in a file.
The start-up kit consists of:
■Power supply unit
■Interface converter (RS-485 to USB)
■USB cable type A to type B
■Sensor cable with M12 x 1 connector
■Adapter cable for models GDM-100-T and GDM-RC-100-T
■Modbus®tool
5.5.1 Establish connection to the PC
5.5.2 Modbus®tool
The software is available, free-of-charge, from the WIKA website.
After wiring and installing the software of the interface converter or copying the
Modbus®tool software, the program can be started.
System requirements
At least Microsoft®Windows®7 (32-bit)
Windows is a registered trademark of Microsoft Corporation in the United States and other countries.
RS-485 USB
+
-
Interface converter
Voltage supply
5. Commissioning, operation
Table of contents
Languages:
Other WIKA Measuring Instrument manuals
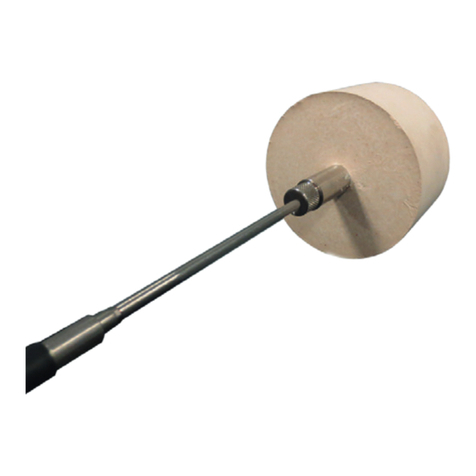
WIKA
WIKA TC52-M User manual
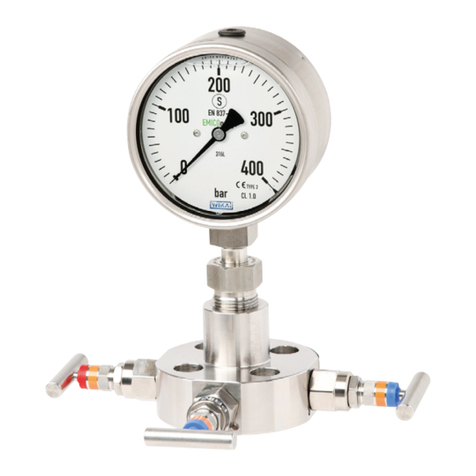
WIKA
WIKA 232.30.100 Operating instructions

WIKA
WIKA CTD9100-1100 User manual

WIKA
WIKA GDM-63 User manual
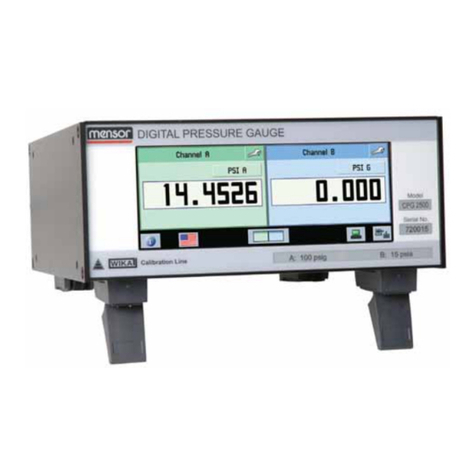
WIKA
WIKA SERIES CPG 2500 User manual
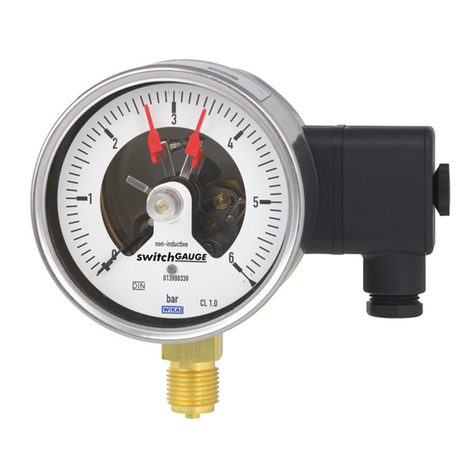
WIKA
WIKA 212.20.100 User manual
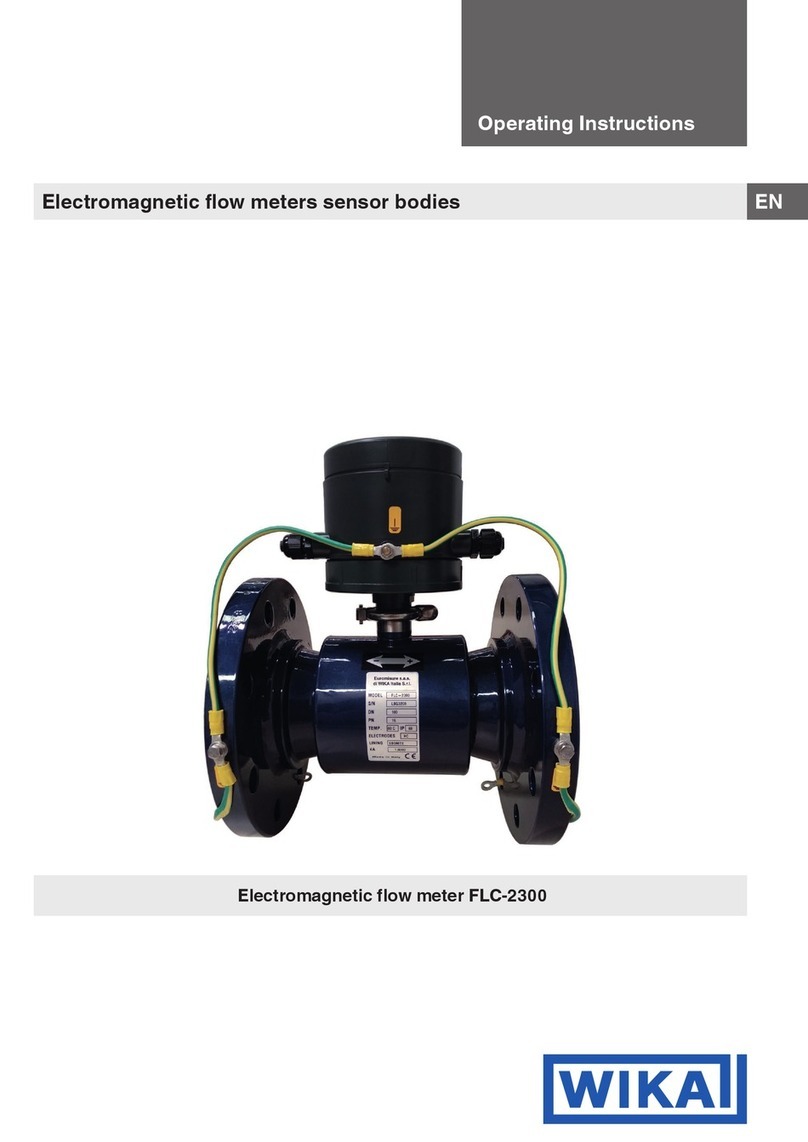
WIKA
WIKA FLC-2300 User manual
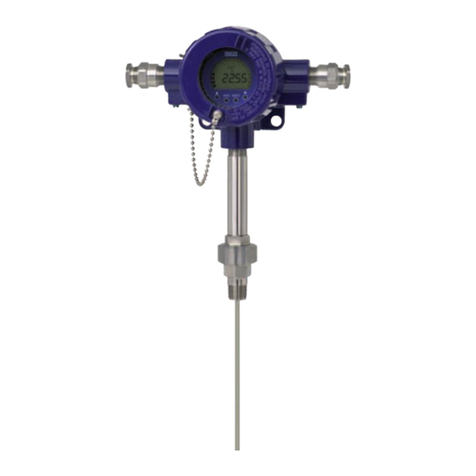
WIKA
WIKA TR12 Series Operating instructions
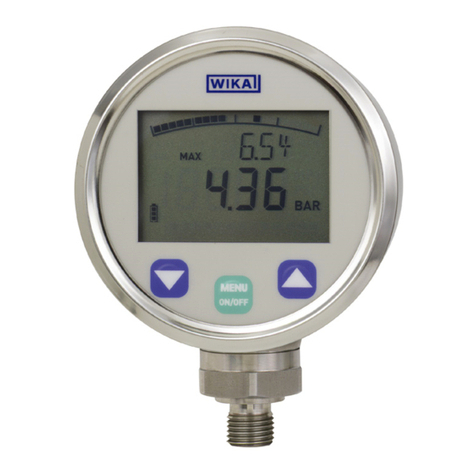
WIKA
WIKA DG-10-S User manual
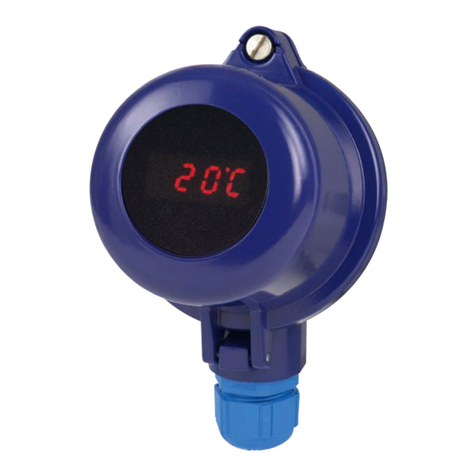
WIKA
WIKA DIH10-Ex User manual
Popular Measuring Instrument manuals by other brands
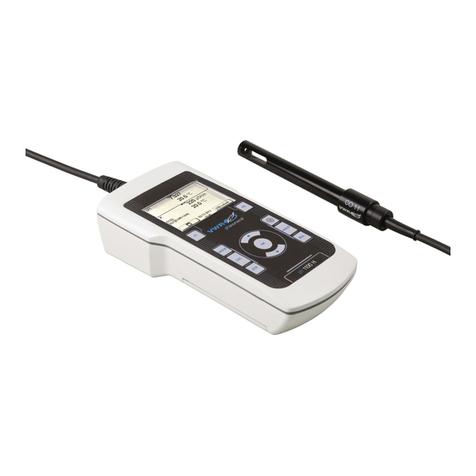
VWR
VWR OX 4100 H operating manual
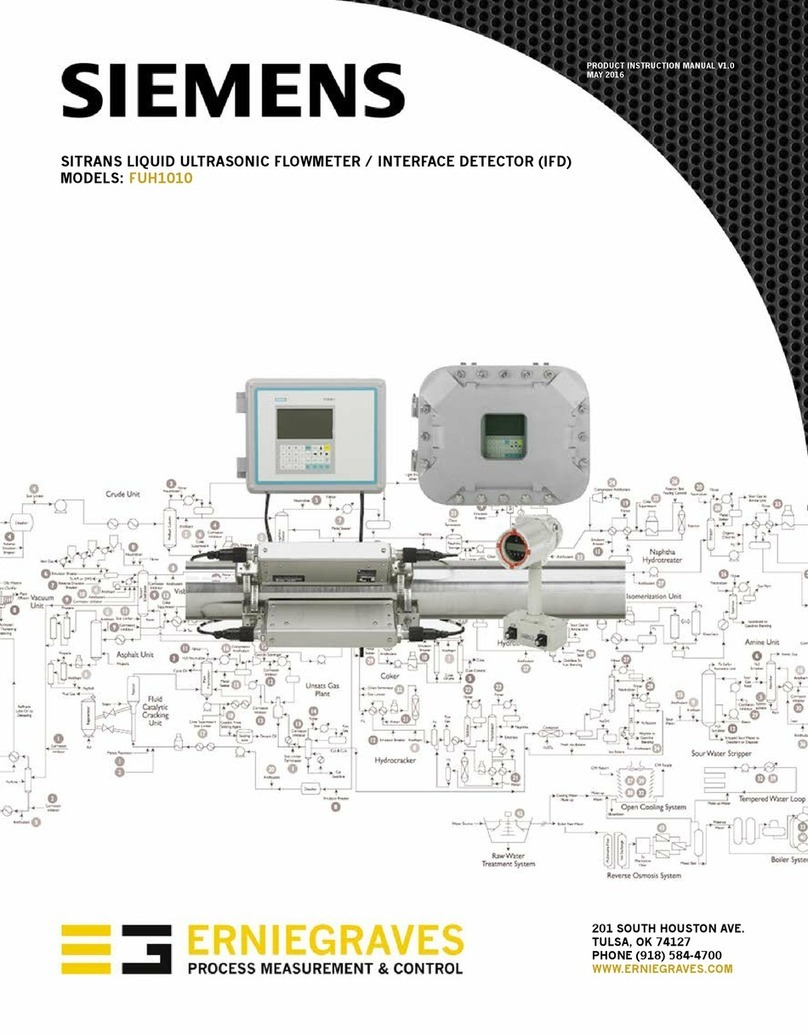
Siemens
Siemens SITRANS FUH1010 Product instruction manual
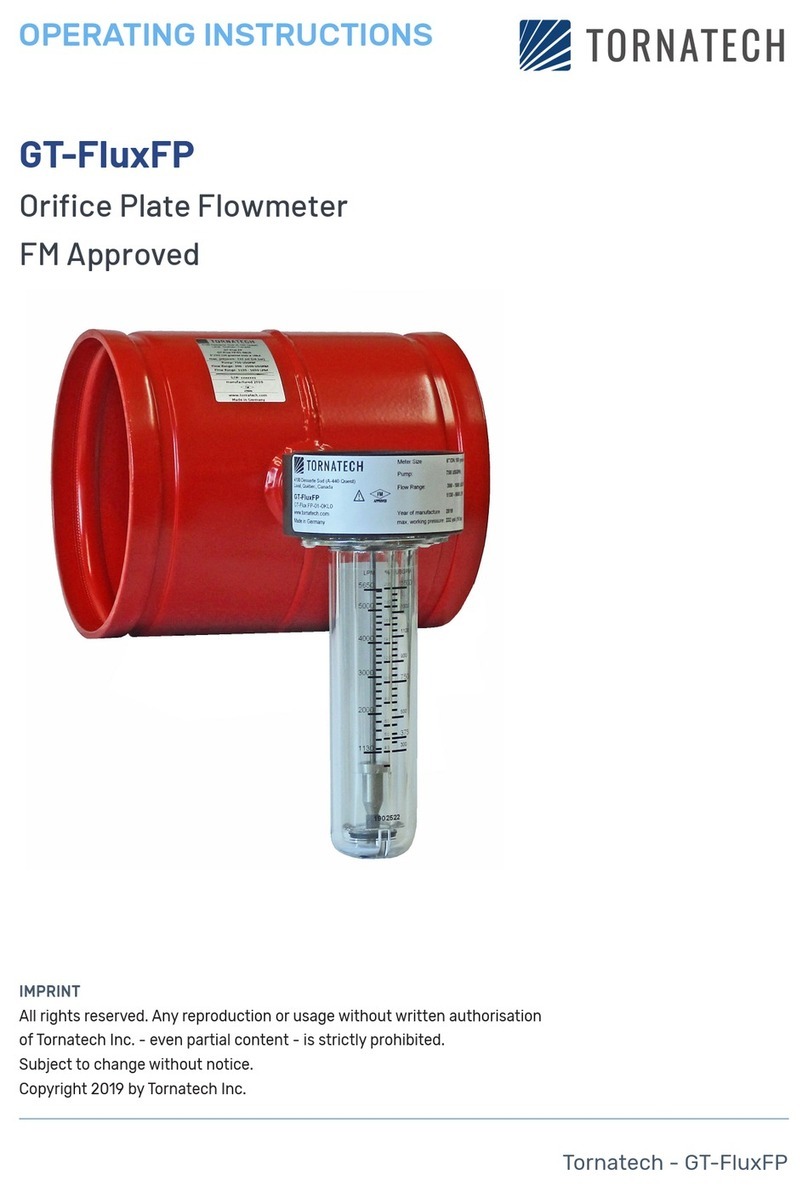
Tornatech
Tornatech GT-FluxFP operating instructions
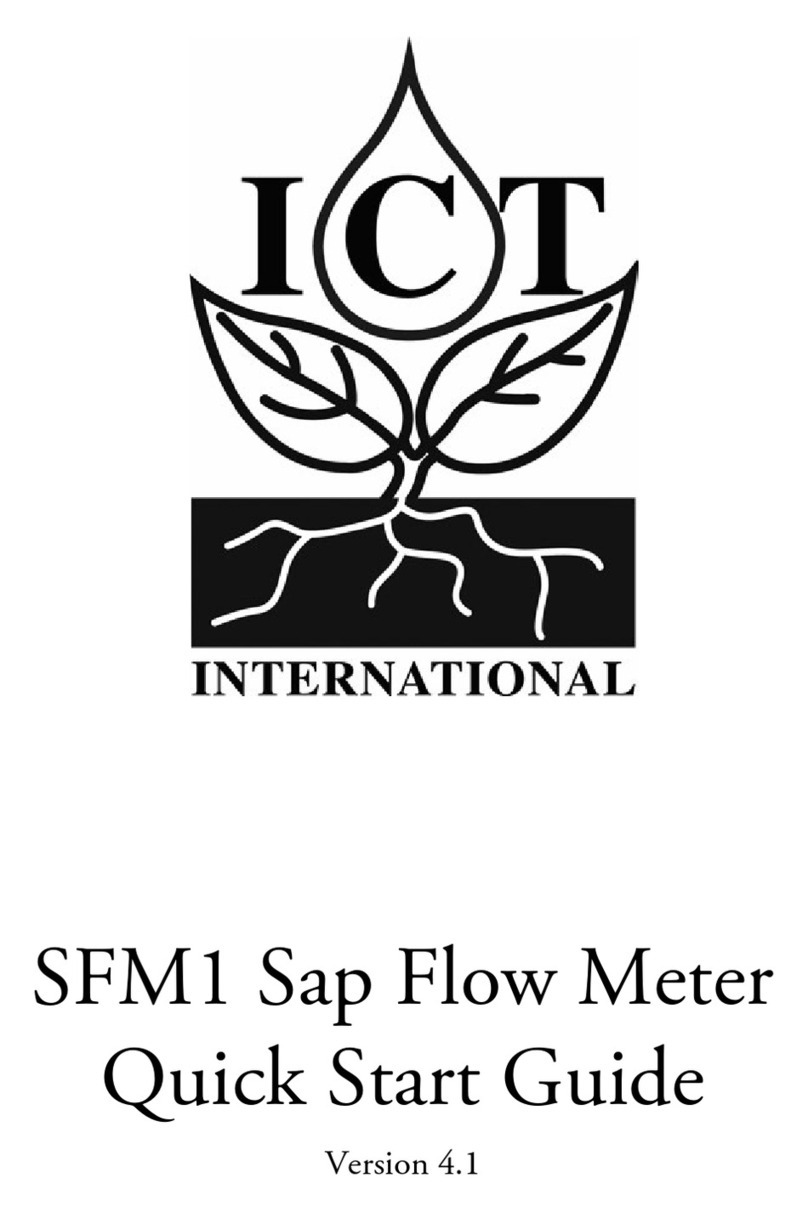
ICT
ICT SFM1 quick start guide
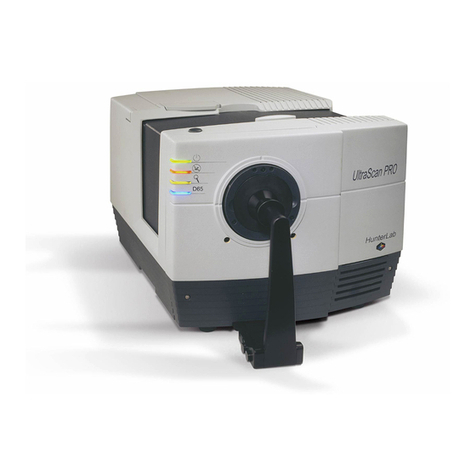
HunterLab
HunterLab UltraScan VIS Supplemental manual
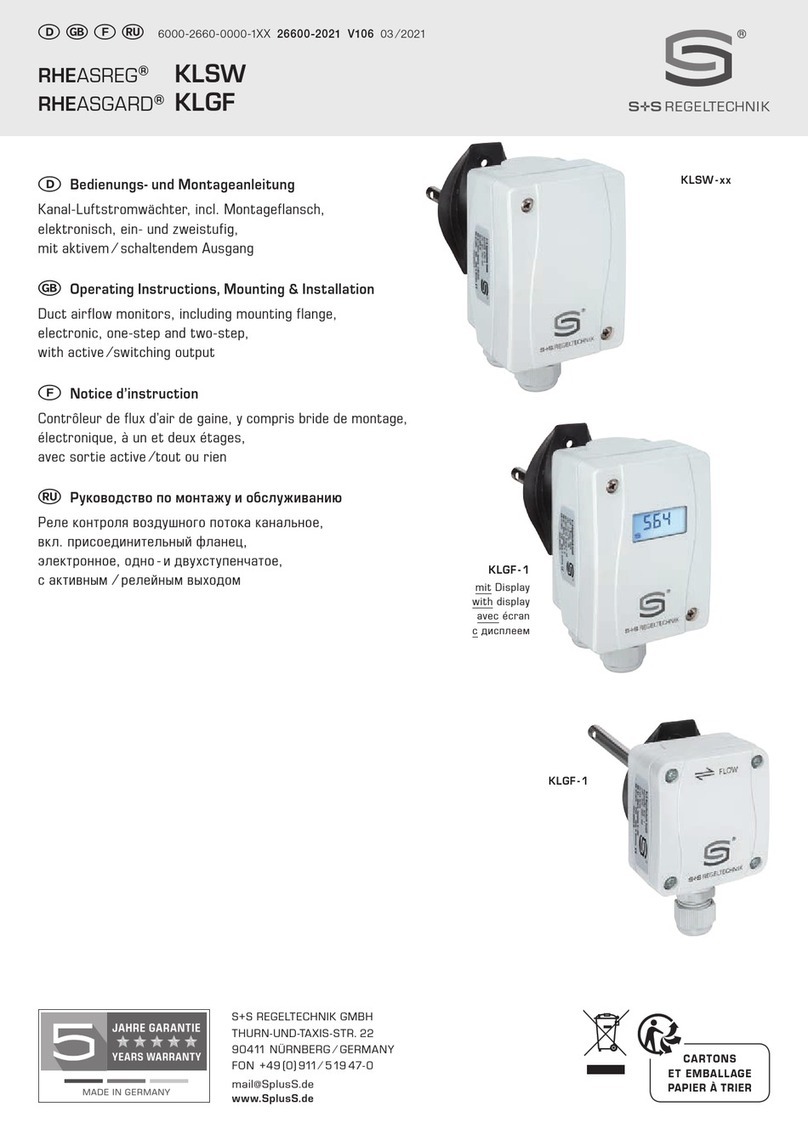
S+S Regeltechnik
S+S Regeltechnik RHEASREG KLSW Operating Instructions, Mounting & Installation