YOKOGAWA SMARTDAC+ GX10 User manual

User’s
Manual
IM 04L51B01-22EN
1st Edition
Model GX10/GX20/GP10/GP20/GM10
GX90NW
PROFINET Communication
User’s Manual

i
IM 04L51B01-22EN
Introduction
Thank you for purchasing the SMARTDAC+ GX10/GX20/GP20/GM10 (hereafter referred to
as the GX, GP, or GM) and the Network Module GX90NW-02-PN (hereafter referred to as
the PROFINET module).
This manual explains how to use the GX/GP/GM PROFINET communication function.
To use the PROFINET communication function, a GX/GP/GM main unit (version R5.02 and
later) and the PROFINET module are required (hereinafter, the GX/GP/GM main unit and
the PROFINET module are jointly referred to as the “SMARTDAC+”).
To ensure correct use, please read this manual thoroughly before beginning operation.
Please use this manual in conjunction with the GX, GP, or GM User’s Manual (GX/GP: IM
04L51B01-01EN, GM: IM 04L55B01-01EN).
The following manuals are provided for the GX/GP/GM.
• Paper manuals
Model Manual title Manual No. Description
GX/GP Model GX10/GX20/GP10/GP20
Paperless Recorder
First Step Guide
IM 04L51B01-02EN Explains the basic operations of the GX/GP.
GM Data Acquisition System GM
First Step Guide
IM 04L55B01-02EN Explains the basic operations of the GM.
GX/GP
GM
Precaution on the use of SMARTDAC+ IM 04L51B01-91EN Provides precautions common to the SMARTDAC+ series.
Regarding the Downloading and
Installing / the Usage of Open Source
Software for the Software, Manuals and
Labels
IM 04L61B01-11EN Explains where software applications and electronic manuals
common to the SMARTDAC+ series can be downloaded from
and how to install the software applications.
• Downloadable electronic manuals
You can download the latest manuals from the following website.
www.smartdacplus.com/manual/en/
Model Manual title Manual No. Description
GX/GP Model GX10/GX20/GP10/GP20
Paperless Recorder
First Step Guide
IM 04L51B01-02EN This is the electronic version of the paper manual.
Model GX10/GX20/GP10/GP20
Paperless Recorder
User’s Manual
IM 04L51B01-01EN Describes how to use the GX/GP. The communication control
commands and some of the options are excluded.
Model GX10/GX20/GP10/GP20
Advanced Security Function (/AS)
User’s Manual
IM 04L51B01-05EN Describes how to use the advanced security function (/AS
option).
GM GM Data Acquisition System
First Step Guide
IM 04L55B01-02EN This is the electronic version of the paper manual.
GM Data Acquisition System
User’s Manual
IM 04L55B01-01EN Describes how to use the GM. The communication control
commands and some of the options are excluded.
GM Data Acquisition System
Advanced Security Function (/AS)
User’s Manual
IM 04L55B01-05EN Describes how to use the advanced security function (/AS
option).
GX/GP
GM
Model GX10/GX20/GP10/GP20/GM10
Communication Commands
User’s Manual
IM 04L51B01-17EN Describes how to use command control communication
functions.
SMARTDAC+STANDARD
Universal Viewer
User’s Manual
IM 04L61B01-01EN Describes how to use Universal Viewer, which is a software that
displays GX/GP/GM measurement data files.
SMARTDAC+STANDARD
Hardware configuration
User’s Manual
IM 04L61B01-02EN Describes how to use the PC software for creating setting
parameters for various GX/GP/GM functions.
Model GX10/GX20/GP10/GP20/GM10
Multi Batch Function (/BT)
User’s Manual
IM 04L51B01-03EN Describes how to use the multi batch function (/BT option).
Model GX10/GX20/GP10/GP20/GM10
Log Scale (/LG)
User’s Manual
IM 04L51B01-06EN Describes how to use the log scale (/LG option).
Model GX10/GX20/GP10/GP20/GM10
EtherNet/IP Communication (/E1)
User’s Manual
IM 04L51B01-18EN Describes how to use the communication functions through the
EtherNet/IP (/E1 option).
Model GX10/GX20/GP10/GP20/GM10
WT Communication (/E2)
User’s Manual
IM 04L51B01-19EN Describes how to use WT communication (/E2 option).
Model GX10/GX20/GP10/GP20/GM10
OPC-UA Server (/E3)
User’s Manual
IM 04L51B01-20EN Describes how to use the OPC-UA server function (/E3 option).
Model GX10/GX20/GP10/GP20/GM10
SLMP Communication (/E4)
User’s Manual
IM 04L51B01-21EN Describes how to use the SLMP communication function (/E4
option).
Model GX10/GX20/GP10/GP20/GM10
Loop Control Function, Program Control
Function (/PG Option)
User’s Manual
IM 04L51B01-31EN Describes how to use the PID control module, loop control
function, and program control function (/PG option).
Continued on next page
1st Edition: September 2022 (YK)
All Right Reserved, Copyright © 2022, Yokogawa Electric Corporation

ii IM 04L51B01-22EN
Model Manual title Manual No. Description
GX/GP DXA170 DAQStudio
User’s Manual
IM 04L41B01-62EN Describes how to create custom displays (/CG option).
Notes
• The contents of this manual are subject to change without prior notice as a result of
continuing improvements to the instrument's performance and functions.
• Every effort has been made in the preparation of this manual to ensure the accuracy of its
contents. However, should you have any questions or find any errors, please contact your
nearest YOKOGAWA dealer.
• Copying or reproducing all or any part of the contents of this manual without the
permission of YOKOGAWA is strictly prohibited.
QR code
The product has a QR Code pasted for efficient plant maintenance work and asset
information management. It enables confirming the specifications of purchased products and
user’s manuals. For more details, please refer to the following URL.
https://www.yokogawa.com/qr-code
QR Code is a registered trademark of DENSO WAVE INCORPORATED.
Trademarks
• SMARTDAC+ is a registered trademark or trademark of Yokogawa Electric Corporation.
• Microsoft, MS, Microsoft Edge, and Windows are registered trademarks or trademarks of
Microsoft Corporation in the United States and other countries.
• Adobe and Acrobat are registered trademarks or trademarks of Adobe Incorporated.
• Google Chrome is a registered trademark of Google LLC.
• Company and product names that appear in this manual are registered trademarks or
trademarks of their respective holders.
• The company and product names used in this manual are not accompanied by the
registered trademark or trademark symbols (® and ™).
Using open source software
This product uses open source software.
For details on using open source software, see Regarding the Downloading and Installing
for the Software, Manuals and Labels (IM 04L61B01-11EN).
Revisions
September 2022 1st Edition

iii
IM 04L51B01-22EN
Conventions used in this manual
Unit
KDenotes 1024. Example: 768K (file size)
kDenotes 1000.
Note
Improper handling or use can lead to injury to the user or damage
to the SMARTDAC+. This symbol appears on the SMARTDAC+
to indicate that the user must refer to the user's manual for special
instructions. The same symbol appears in the corresponding place
in the user's manual to identify those instructions. In the manual,
the symbol is used in conjunction with the word “WARNING” or
“CAUTION.”
WARNING Calls attention to actions or conditions that could cause serious or fatal
injury to the user, and precautions that can be taken to prevent such
occurrences.
CAUTION Calls attention to actions or conditions that could cause light injury
to the user or cause damage to the instrument or user’s data, and
precautions that can be taken to prevent such occurrences.
Note Calls attention to information that is important for the proper
operation of the SMARTDAC+.
Reference item
Reference to related operation or explanation is indicated after this
mark.
Example: Section 4.1
Conventions used in the procedural explanations
Bold characters Denotes key or character strings that appear on the screen.
Example: Volt
Aa # 1
Indicates the character types that can be used.
a symbol,
uppercase alphabet,
numbers
A
1
lowercase alphabet,
#
Procedure Carry out the procedure according to the step numbers. All procedures
are written with inexperienced users in mind; depending on the
operation, not all steps need to be taken.
Explanation gives information such as limitations related the procedure.
Indicates the setup screen and explains the settings.
Explanation
Path
Description

iv IM 04L51B01-22EN
What this manual explains
This manual assumes communication between the SMARTDAC+ and the Programmable
Logic Controller (PLC). For instructions on how to use the PLC, see the user’s manual for
your PLC.
This manual is intended for persons who have previously used PROFINET.
Recorder version described in this manual
The contents of this manual correspond to the GX/GP with release number 5 (see the
STYLE S number) and style number 3 (GX10/GX20/GP10) (see the STYLE H number) and
style number 4 (GP20), and the GM10 with release number 5 (see the STYLE S number)
and style number 1 (see the STYLE H number).
Edition Product Description
1 GX/GP: Version 5.02 and later —
GM: Version 5.02 and later
GX90NW: Version 1.01.01

v
IM 04L51B01-22EN
Contents
Introduction................................................................................................................................................ i
Conventions used in this manual..............................................................................................................iii
What this manual explains....................................................................................................................... iv
Recorder version described in this manual ............................................................................................. iv
Introduction of Features....................................................................................................................... 1
PROFINET ............................................................................................................................................... 1
What the SMARTDAC+ can do ................................................................................................................ 2
PROFINET communication setup ............................................................................................................ 2
SMARTDAC+ access ............................................................................................................................... 3
Preparation of the SMARTDAC+......................................................................................................... 4
PROFINET module installation................................................................................................................. 4
Cable connection...................................................................................................................................... 5
SMARTDAC+ configuration...................................................................................................................... 5
Limitations when using the PROFINET module ....................................................................................... 6
PLC Preparation .................................................................................................................................. 8
GSDML file ............................................................................................................................................... 8
System configuration................................................................................................................................ 8
Data Access via Cyclic Communication............................................................................................... 9
Data mapping ......................................................................................................................................... 10
Data Access via Acyclic Communication ........................................................................................... 11
Data mapping ......................................................................................................................................... 12
PROFINET module specifications ..................................................................................................... 24
PROFINET specifications....................................................................................................................... 24
Hardware specifications ......................................................................................................................... 24
Names of the PROFINET modules ........................................................................................................ 25
Troubleshooting ................................................................................................................................. 26
PROFINET module operation and description ....................................................................................... 26
Error messages and corrective actions .................................................................................................. 27
Appendix............................................................................................................................................ 28
Register configuration of PID control module channels.......................................................................... 28

Blank

1
IM 04L51B01-22EN
Introduction of Features
PROFINET
PROFINET is an Ethernet-based industrial network communication protocol created by PI
(Profibus & Profinet International). By using Ethernet-based communication, you can meet
the requirements of high-speed input/output data communication and equipment parameter
monitoring and configuration.
Devices that support PROFINET are available from many vendors. Our GX, GP, and GM
support communications with PROFINET IO controllers, such as PLCs, by incorporating a
PROFINET communication function (PROFINET module).
Component devices
• IO controller
The IO controller is a controller such as a PLC with a control program. Data exchange is
performed to the specified IO device when configuring the system.
• IO device
An IO device is a device that the IO controller accesses to read and write data to.
The SMARTDAC+ is an IO device.
• Configuration tool
A tool to configure the system. The PC or software that the configuration software is
installed on.
• Switch
A network repeater.
• Cables
Use a PROFINET communication-compatible cable.
PROFINET
GX/GP
IO controller
IO device
Switch
IO device
Configuration tool
GM
Note
For details about PROFINET, please refer to the information issued by PROFIBUS and PROFINET
International.

2IM 04L51B01-22EN
Introduction of Features
What the SMARTDAC+ can do
The SMARTDAC+ provides the following functions.
• It can participate in a PROFINET network as an IO device.
• It can communicate with an IO controller (PLC, etc.).
• It supports both cyclic and acyclic communication.
• PLCs can access internal data of the SMARTDAC+.
Data Access
I/O channel measured value Read
Math channel1measured value Read
Communication channel2measured
value
Writable
AO channel, DO channel output value Write (acyclic communication)
Each channel status information Read
*1 /MT option
*2 /MC option
The following are examples of use.
• Data from devices on the network can be recorded to the SMARTDAC+ by PLCs.
• PLCs can acquire the data measured by the SMARTDAC+.
PROFINET communication setup
Equipment needed
• GX/GP/GM main unit and GX90NW-02-PN
• PLC to act as IO controller (Siemens PLC S7-1200, S7-1500, etc.)
• PC with configuration tool (such as TIA Portal) installed
• PROFINET-compatible switches (as needed)
• PROFINET-compatible communication cables
SMARTDAC+ setup
1. Reconfigure the PROFINET module
2. SMARTDAC+ configuration
PROFINET equipment configuration
Use a configuration tool (such as the TIA Portal) to configure cyclic communication between
the PLC and the SMARTDAC+.
In addition, acyclic communication is performed by creating a ladder program.
Cyclic communication
1. Creating a New Project
2. Install the GSDML file on the SMARTDAC+
3. Select a connected device (PLC, SMARTDAC+, etc.) from the catalog
4. Set the network configuration of the IO device and the IO controller (PLC, etc.),
including the SMARTDAC+
5. Set the station name and IP address of the IO device including the PLC and the
SMARTDAC+
6. Set the configuration tool and the PLC online to reflect the settings of the PLC and the
SMARTDAC+
Acyclic communication
1. Open the project
2. Creating ladder programs (defining tags, creating programs)
3. Set the configuration tool and PLC online to download the ladder program created in
the PLC

3
IM 04L51B01-22EN
Introduction of Features
List of settings
GX/GP/GM Configuration
GX/GP/GM Ethernet Communication
(Server)
DHCP ON setting
IP address
Subnet mask
Default gateway
Modbus Server Settings (On/Off, Port Number, Delayed
Response)
PROFINET Module Ethernet
Communication
(Client)
IP address
Data interval
Maximum number of update cycles without data
Configuring PROFINET with the configuration tool
The settings are downloaded to the PLC.
Configuration information
IO controller (PLC) settings Station name
DHCP ON/OFF setting (OFF fixed)
IP address
Subnet mask
Default gateway
IO device #1 setting Station name
DHCP ON/OFF setting (OFF fixed)
IP address
Subnet mask
Default gateway
: :
IO device #N settings Station name
DHCP ON/OFF setting (OFF fixed)
IP address
Subnet mask
Default gateway
Ladder program
SMARTDAC+ access
The SMARTDAC+ is passive on PROFINET. The SMARTDAC+ cannot initiate a request.
The IO controller (PLC) initiates a request to the SMARTDAC+.

4IM 04L51B01-22EN
Preparation of the SMARTDAC+
PROFINET module installation
GX10 and GP10
Install the PROFINET module into slot 2.
GX20 and GP20
Install the PROFINET module into slot 9.
GM
For the main unit, link the PROFINET module to the left end as seen from the front.
GM10 Ethernet port
PROFINET module (installed in slot 2)
PROFINET port
PROFINET Module
GX10 (GP10) rear panel
GM main unit
GX20 (GP20) rear panel
PROFINET module (linked to the left end as seen from the front of the GM main unit)
PROFINET module (installed in slot 9)
GX10 (GP10) Ethernet port
GX20 (GP20) Ethernet port
Ethernet port
Note
If the installation position of the PROFINET module is incorrect, the PROFINET module will not be
recognized when the SMARTDAC+ is reconfigured.

5
IM 04L51B01-22EN
Preparation of the SMARTDAC+
Cable connection
Connect the Ethernet port of the GX/GP/GM main unit and the Ethernet port of the
PROFINET module (either one of the two ports) with an Ethernet cable (STP cable, CAT 5 or
higher)1.
• Communication between the GX/GP/GM main unit and the PROFINET module is
performed using the Modbus protocol.
1: We recommend an Ethernet cable length of 1 m or less.
• You can connect to the Ethernet network from the other Ethernet port of the PROFINET
module.
There are limitations on the link detection operation of the GX/GP/GM main unit.See
“Restriction on link detection operation of the GX/GP/GM main unit when connecting to
an Ethernet network” on page 7.
Connect the PROFINET communication cable to the PROFINET port of the PROFINET
module to connect to the PROFINET network.
Do not use an Ethernet cable whose plug does not comply with FCC specifications.
Doing so can cause a malfunction.
SMARTDAC+ configuration
Reconfiguring the PROFINET module
Reconfiguration is performed to recognize the PROFINET module installed in the main unit.
For details on the reconfiguration, see below.
GX/GP: Section 1.29.4, “Reconfiguring the GX/GP” in the User's Manual (IM
04L51B01-01EN)
GM: Section 2.29.4, “Reconfiguring the GM” in the User's Manual (IM 04L55B01-
01EN)
Ethernet communication function settings
Set the DHCP On/Off, IP address, subnet mask, and default gateway.
Modbus server setting
Set the Modbus to On, and set the port number and the Modbus delay response.
For details on the Ethernet communication function settings and the Modbus server settings,
see below.
GX/GP: Section 1.21, “Configuring the Ethernet Communication Function” in the
User’s Manual (IM 04L51B01-01EN)
GM: Section 2.22, “Configuring the Ethernet Communication Function” in the User’s
Manual (IM 04L55B01-01EN)

6IM 04L51B01-22EN
Preparation of the SMARTDAC+
PROFINET module settings
Path
GX/GP: MENU key > Browse tab > Setting > Setting menu Network module settings
Web browser: Setting tab > Network module settings
Hardware configurator: Network module settings
Description
Network module settings
Settings Selectable range or options Initial value
IP address 0.0.0.0 to 255.255.255.255 0.0.0.0
Data interval 100ms/200ms/500ms/1s/2s/5s/10s 1s
Maximum number of update cycles
without data
Off/1/2/5/10/20/50/100 10
IP address
The IP address of the PROFINET module’s Ethernet port (for Modbus clients).
• When the GX/GP/GM main unit setting is set to DHCP On, DHCP is also enabled for the
module, and the setting is disabled.
• Make sure that the IP address of the GX/GP/GM main unit does not overlap with the
default gateway and that it is the same subnet mask as the IP address of the GX/GP/GM
main unit.
Data interval
The interval at which the data is updated.
Maximum number of update cycles without data
Depending on the load of the GX/GP/GM main unit and the network status of the Ethernet,
data may not be updated. If data is not updated continuously for a set number of times,
the diagnostic information is sent to the IO controller. When the data is updated, the
transmission to the IO controller is stopped.
• While the diagnostic information is being transmitted, the module status LED blinks
green.
See “Troubleshooting” on page 26.
Obtain/release the IP address of the PROFINET module when using DHCP
GX/GP
Display the network information screen and perform the following operation.
MENU key > Context tab > Obtain IP address or Release IP address
GM
Using the IP address setting software, select Obtain IP address automatically or the
Release button.
Limitations when using the PROFINET module
Module limitations
• The PROFINET module can only be used with one module of the GX/GP/GM main unit.
• The PROFINET module and the expansion module (GX90EX) cannot be used
simultaneously.
• The extended unit (GX60) and GM sub units cannot be used.
In addition, the following limitations apply to each model of the SMARTDAC+.
GX10 and GP10
• A single module can be installed with either GX90UT or GX90YA.
• GX10 and GP10 cannot be installed to the GP10 of the power supply voltage
specification code “2” (12 V DC).
GX20 and GP20
• When GX90UT is included, up to 7 modules can be installed, including GX90NW.
• When GX90XA-10-T1 is included, up to 8 modules can be installed, including GX90NW.
GM main unit
• When GX90XA or GX90YA is included, up to 6 modules can be connected, including
GX90NW.

7
IM 04L51B01-22EN
Preparation of the SMARTDAC+
Modbus server function limitations
• Number of Modbus server connections: Max 2
Limitations when using communication channels
In PROFINET cyclic communication, the following communication channels are always
written from the PLC.
Model Communication channel
GX10/GP10 From C001 to C020
GX20/GP20/GM10 From C001 to C050
If you want to use the communication channel with other functions, check whether the above
channels are used. If the writing conflicts, change the setting to avoid conflicts.
• When using the wireless input unit GX70SM (for GX20/GP20/GM10)
Conflicting channels C001 to C050 correspond to wireless input unit numbers 1 to 10.
When using wireless input unit numbers 1 to 10, the unit number must be changed
(wireless input unit reconfiguration). For details on wireless input unit reconfiguration, see
below.
GX70SM Wireless Input Unit User’s Manual (IM 04L57B01-01EN)
Restriction on link detection operation of the GX/GP/GM main unit when
connecting to an Ethernet network
• The status of the link between the PROFINET module and the Ethernet network cannot
be checked on the general log screen of the GX/GP/GM main unit.
• The following messages are not displayed even if the Ethernet network link status
changes.
“821 Ethernet cable connected.”
“822 Ethernet cable disconnected.”
• When using DHCP, the IP address acquisition/release operation is not performed when
connecting to/disconnecting from the Ethernet network after powering on.
• When the IP address is not obtained, the GX/GP/GM main unit and the PROFINET
module do not obtain the IP address even when connected to an Ethernet network.
• When obtaining the IP address, the GX/GP/GM main unit and the PROFINET module
do not release the IP address even when disconnected from the Ethernet network.
If you need to obtain/release the IP address,See “Obtain/release the IP address of the
PROFINET module when using DHCP” on page 6.
• When using an email/FTP client, if the cable of the Ethernet network is disconnected, the
following error message is displayed.
“658 Could not connect to SMTP server.”
“692 FTP control connection error.”

8IM 04L51B01-22EN
PLC Preparation
GSDML file
Installation
To join the SMARTDAC+ to the network, you must first install the SMARTDAC+ device
profile (GSDML file, General Station Description Markup Language) in the configuration tool.
The PLC communicates with the SMARTDAC+ based on the information in the GSDML file.
For instructions on how to use the configuration tool, see the Configuration Tools User’s
Manual.
PROFINET
GX/GP
IO controller
IO device
Configuration tool
Switch
GM
GSDML file
GSDML file
How to obtain the GSDML file
Please obtain it from our website.
URL: www.smartdacplus.com/software/en/
GSDML file format
File name Description
GSDML-V2.42-Yokogawa-SMARTDACplus-YYYYMMDD.xml
(YYYYMMDD: The file release date (e.g., 20220401))
Device profile of the SMARTDAC+
GSDML-0037-0400-SMARTDACplus.bmp Icon image file referenced from the
GSDML file
System configuration
Sets the communication contents in the configuration tool.
For details on how to use the configuration tool and PLC, see the relevant User’s Manual.

9
IM 04L51B01-22EN
Data Access via Cyclic Communication
After PROFINET configuration, the PLC can exchange data according to the information in
the GSDML file of the SMARTDAC+.
Action
After Modbus communication between the GX/GP/GM main unit and the PROFINET module
is started, PROFINET communication with the PLC starts automatically.
Accessible channels
Channel type Model Accessible channels
I/O
GX10/GP10 0001 to 0010, 0101 to 0110
GX20/GP20/GM10 0001 to 0010, 0101 to 0110, 0201 to 0210,
0301 to 0310, 0401 to 0410
Math1GX10/GP10
GX20/GP20/GM10 From A001 to A050
Communication2GX10/GP10 From C001 to C020
GX20/GP20/GM10 From C001 to C050
*1 On models with computation (/MT option)
*2 On models with communication channel function (/MC option)
Readable data: I/O channel, math channel measured value and status information
Communication channel status information
Writable Data: Communication channel measured value
Status information
5 bits
Status information Alarm list
0
Reserved area
Error code
RJC error
A/D calibration value error
Level 1
Level 2
Level 3
Level 4
2 bytes
Higher Lower
4 bits0 0 0 0
Error code Function
0 No error
1 Skip
2 +Over
3 –Over
4 +Burnout
5 –Burnout
6 A/D error
7 Invalid data
16 Math error
17 Communication error
When the I/O channel is a PID control module, see “Appendix” on page 28.

10 IM 04L51B01-22EN
Data Access via Cyclic Communication
Data mapping
The following data can be accessed.
Device Access Point (DAP) Name: GX90NW
Module name Direction Data type Quantity Description
IO_CH_Value Read INT32 50 Reads the measured value of an accessible
I/O channel.
MATH_CH_Value Read INT32 50 Reads the measured value of an accessible
math channel.
IO_CH_Status Read INT16 50 Reads the status of an accessible I/O channel.
MATH_CH_Status Read INT16 50 Reads the status of an accessible math
channel.
COM_CH_Status Read INT16 50 Reads the status of an accessible
communication channel.
Update_Counter Read UINT32 1 The data update counter.
Increments each time you refresh.
COM_CH_Value Write INT32 50 Writes the measured value of the accessible
communication channel.
Watchdog timer of a communication channel
When writing a communication channel, we recommend that you use the communication
channel's watchdog timer.
• When the data of the communication channel is not updated due to a network
communication failure, etc., the data can be detected as not updated and replaced with
preset values or final values based on the watchdog timer settings.

11
IM 04L51B01-22EN
Data Access via Acyclic Communication
By creating a ladder program on the PLC, data exchange and control operations are
possible.
Action
The PLC reads and writes each data by specifying the corresponding number (INDEX).
If a command error or Modbus timeout (communication error) occurs, notify the PLC by
returning an error response.
Accessible channels
All I/O channels, all math channels (/MT) and all communication channels (/MC) can be
accessed, except for the ext. channel.
Readable data: Measured values and status information for all types of channels *
Writable data: Communication channel measured values and AO channel, DO channel
output values
* For details on status information, see “Data access via cyclic communication.”
Write to the I/O channel in units of 1CH (INDEX10001 to 10950).
Control operation
The following controls are possible.
• Start/stop recording
• Math computations
• Writing Messages
• Write batch information
• Read and write alarm settings
• Alarm ACK
Note
The following operations are not possible: Read control alarm status, read/write control alarm
settings, control alarm ACK.
Ladder program example
Read Write

12 IM 04L51B01-22EN
Data Access via Acyclic Communication
Data mapping
The following data can be accessed.
INDEX Data Direction Size
(byte)
Data
type Array Supplementary information
101
Alarm setting (channel type)
Read/Write 12 INT16
0
1: I/O channel
2: Math channel
3: Communication channel
(Write) Write alarm
settings
(Read) Read next
INDEX channel, alarm
level setpoint
Alarm setting
(channel number) 1
I/O channel: 1 to 6932
Math channel: 1 to 200
Communication channel: 1 to
500
Alarm setting (alarm level) 2 1 to 4: Alarm level
Alarm type 3
0: OFF
1: High limit alarm
2: Low limit alarm
3: High limit on rate-of-change
alarm
4: Low limit on rate-of-change
alarm
5: Delay high limit alarm
6: Delay low limit alarm
7: Difference high limit alarm
8: Difference low limit alarm
10: Profile upper limit alarm
11: Profile lower limit alarm
Alarm setpoint
4 Lower word of alarm value
5 Upper word of alarm value
102
Alarm setting (channel type)
Read/Write 6 INT16
0
1: I/O channel
2: Math channel
3: Communication channel
Specify the channel
and level from which to
read alarm settings
Alarm setting
(channel number) 1
I/O channel: 1 to 6932
Math channel: 1 to 200
Communication channel: 1 to
500
Alarm setting (alarm level) 2 1 to 4: Alarm level
103
Alarm delay setting
(channel type)
Read/Write 8 INT16
0
1: I/O channel
2: Math channel
3: Communication channel
(Write) Write alarm
delay setting
(Read) Read next
INDEX channel
setpoint
Alarm delay setting (channel
number) 1
I/O channel: 1 to 6932
Math channel: 1 to 200
Communication channel: 1 to
500
Alarm delay
2Alarm delay seconds lower
word
3Alarm delay seconds upper
word
104
Alarm delay setting
(channel type)
Read/Write 4 INT16
0
1: I/O channel
2: Math channel
3: Communication channel Specify the channel
from which to read
alarm delay setting
Alarm delay setting
(channel number) 1
I/O channel: 1 to 6932
Math channel: 1 to 200
Communication channel: 1 to
500
Continued on next page

13
IM 04L51B01-22EN
Data Access via Acyclic Communication
INDEX Data Direction Size
(byte)
Data
type Array Supplementary information
113 Batch, lot number
(multi batch support) Read/Write 58 INT16
0
1 to 12: Batch group number
When reading, the batch group
number that performed writing
previously
Default value: 0
(Write) Write batch, lot
number setting
(Read) Setpoint
reading of the next
INDEX batch group
number
If there is no multi
batch, the batch group
number is “1”
1
Lower bytes of the lot number
When reading, the lot number
corresponding to the above
batch group number
0 if there is no corresponding
batch group number
2
Higher bytes of the lot number
When reading, the lot number
corresponding to the above
batch group number
0 if there is no corresponding
batch group number
3
Batch number
UTF-8 characters (2
characters)
Up to 32 characters [attach the
terminator '\0' at the end]
When reading, the batch
number corresponding to the
above batch group number
NULL character if there is no
corresponding batch group
number
: :
28
Batch number
UTF-8 characters (2
characters)
Up to 32 characters [attach the
terminator '\0' at the end]
When reading, the batch
number corresponding to the
above batch group number
NULL character if there is no
corresponding batch group
number
114 Batch, lot number
(multi batch support) Read/Write 2 INT16 0
1 to 12: Batch group number
When reading, the batch group
number that performed writing
previously
Default value: 0
Specify batch group
number to read batch,
lot number
Continued on next page
Other manuals for SMARTDAC+ GX10
7
This manual suits for next models
4
Table of contents
Other YOKOGAWA Analytical Instrument manuals
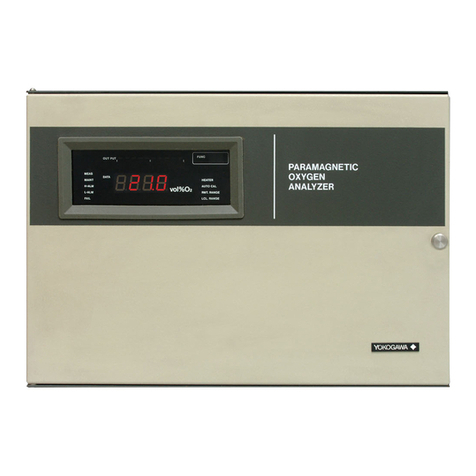
YOKOGAWA
YOKOGAWA MG8G User manual
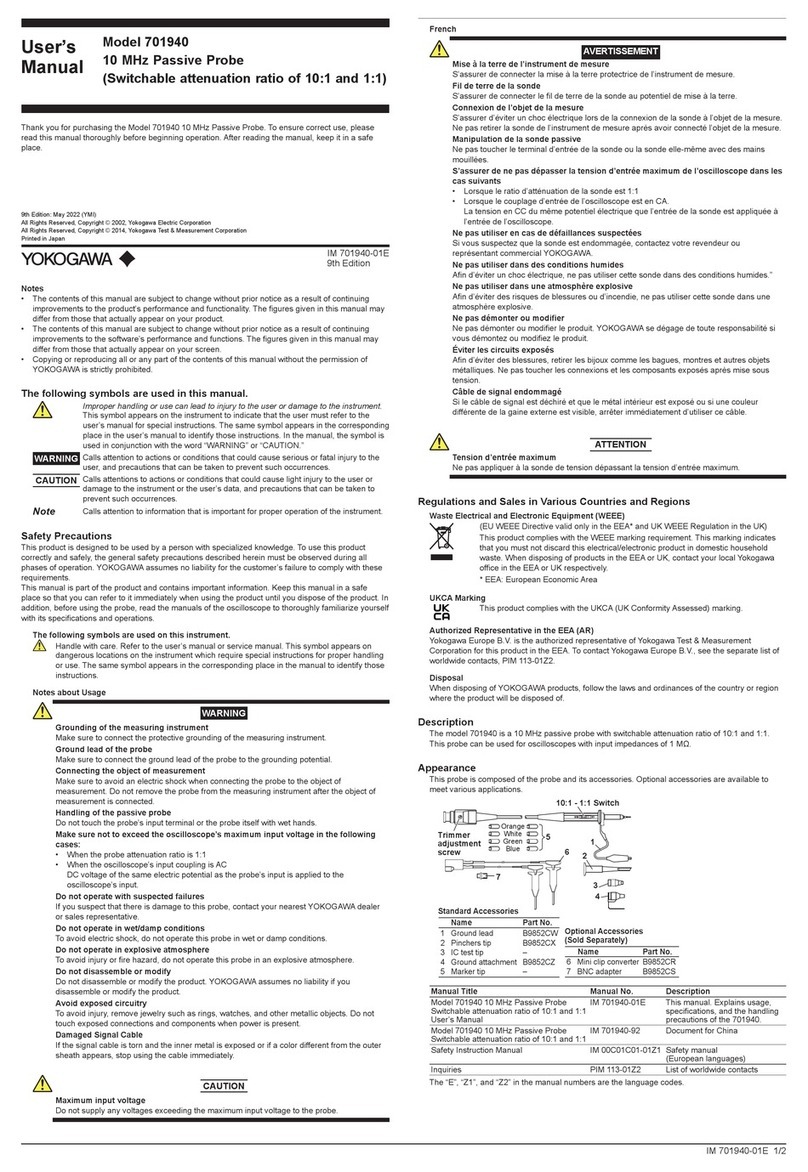
YOKOGAWA
YOKOGAWA 701940 User manual
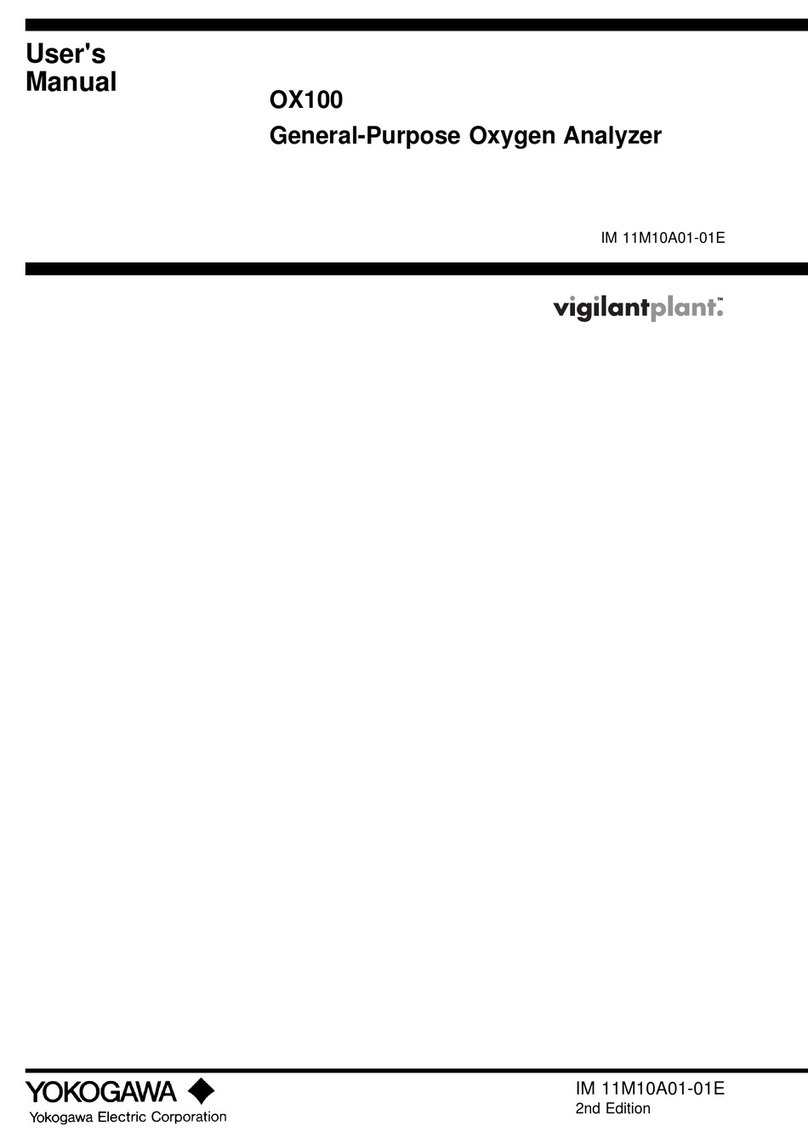
YOKOGAWA
YOKOGAWA OX100 User manual
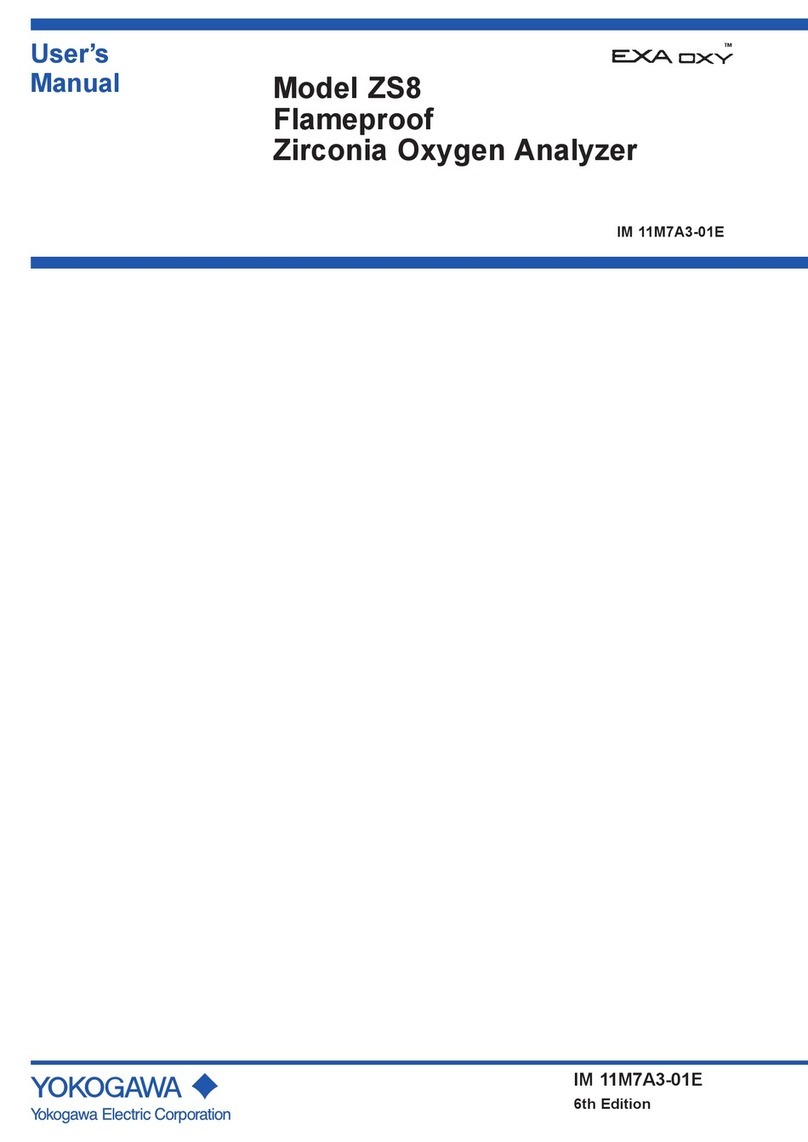
YOKOGAWA
YOKOGAWA ZS8 User manual
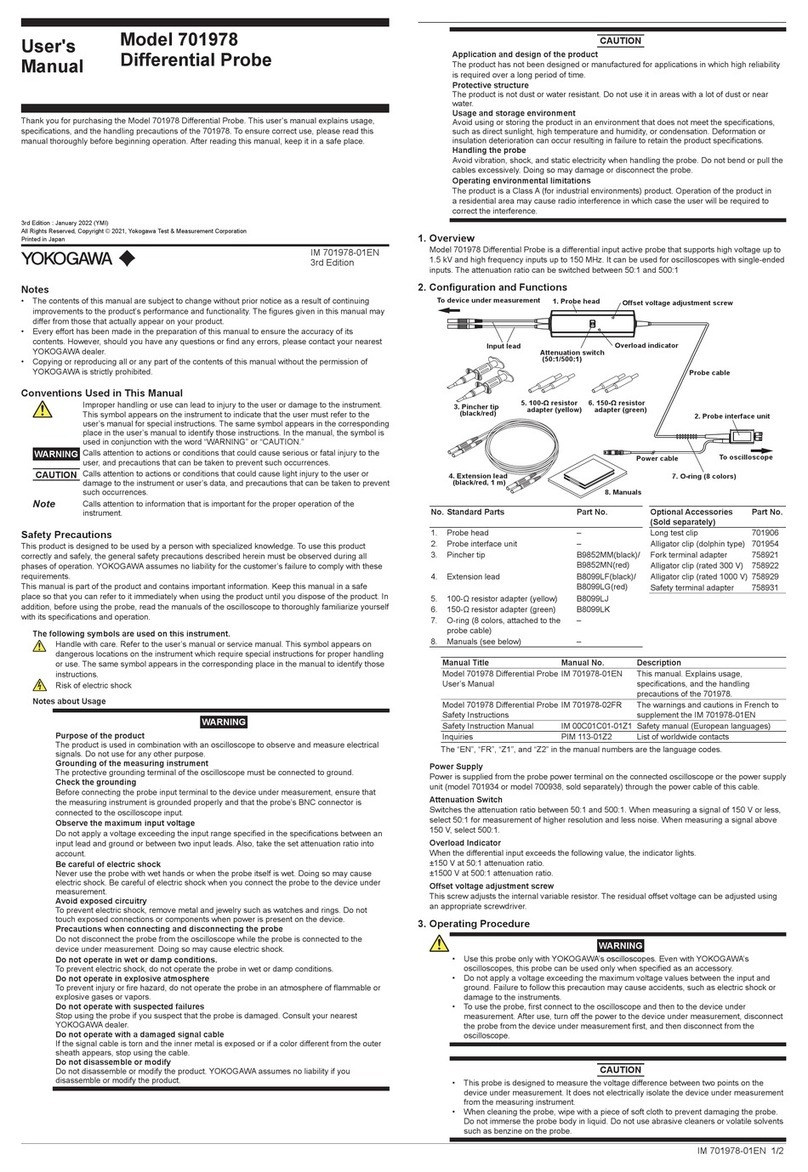
YOKOGAWA
YOKOGAWA 701978 User manual
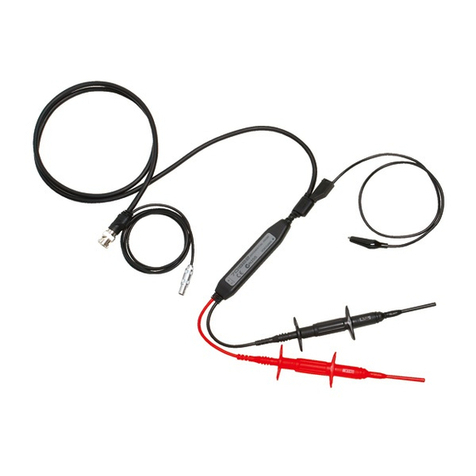
YOKOGAWA
YOKOGAWA 701922 User manual

YOKOGAWA
YOKOGAWA Vigilantplant NFBU200-S Series User manual
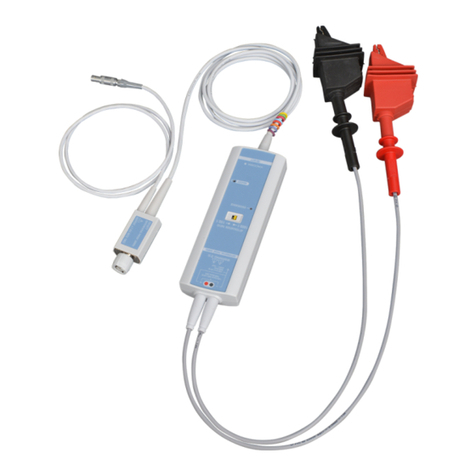
YOKOGAWA
YOKOGAWA 701977 User manual
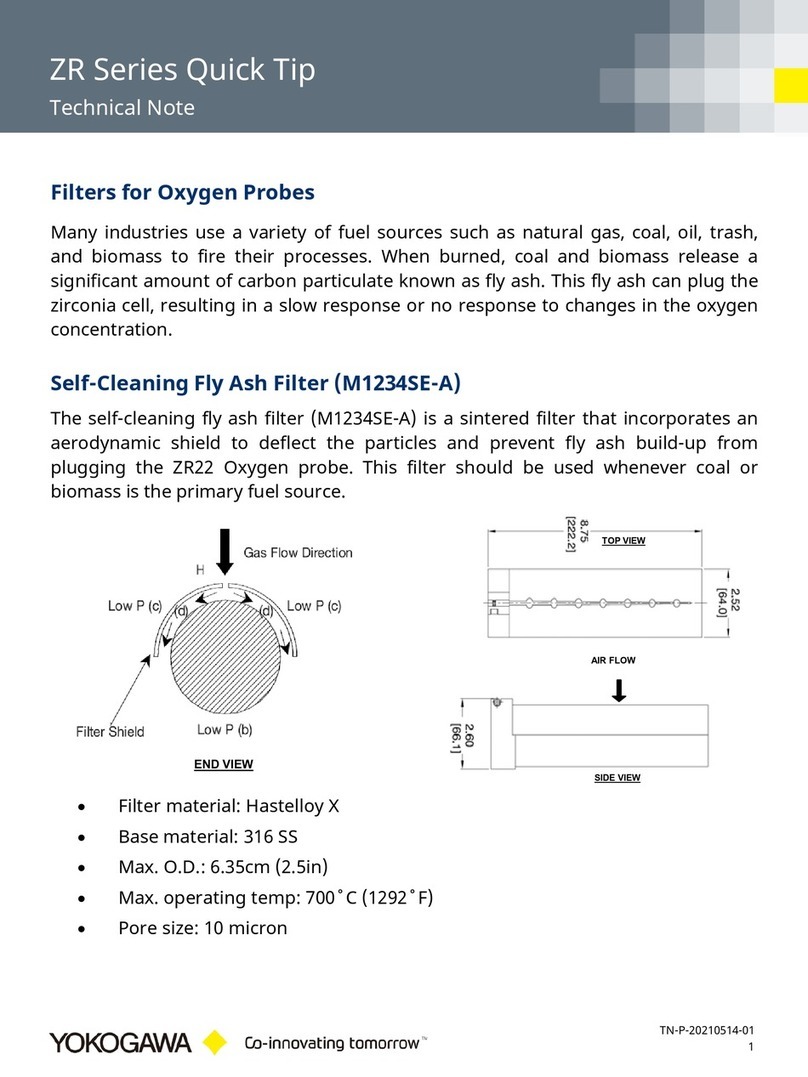
YOKOGAWA
YOKOGAWA ZR Series Specification sheet
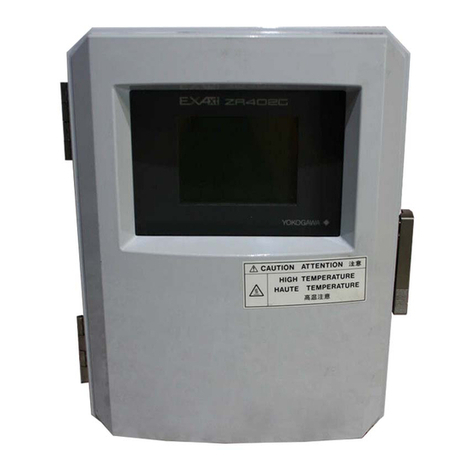
YOKOGAWA
YOKOGAWA EXAxtZR User manual