Beta 1899A User manual

1899A
INSTRUCTIONS FOR USEEN

8
ISTRUZIONI PER L’USO I
INSTRUCTIONS FOR USE EN
OPERATION MANUAL AND INSTRUCTIONS FOR DIESEL PARTICULATE FILTER CLEANING
MACHINE MANUFACTURED BY:
BETA UTENSILI S.P.A.
Via A. Volta 18,
20845, Sovico (MB)
ITALY
Original documentation drawn up in ITALIAN.
IMPORTANT! READ THIS MANUAL THOROUGHLY BEFORE USING
THE DIESEL PARTICULATE FILTER CLEANING MACHINE. FAILURE
TO COMPLY WITH THE SAFETY STANDARDS AND OPERATING
INSTRUCTIONS MAY RESULT IN SERIOUS INJURY.
CAUTION
Store the safety instructions with care and hand them over to the users.
PURPOSE OF USE
- The DIESEL PARTICULATE FILTER CLEANING MACHINE can be used for the following purposes:
• Cleaning diesel particulate lters in diesel engines blocked by soot, ash and other types of contaminants
• Cleaning is suitable for cars, lorries, bus engines and stationary engines.
- Not be used for the following operations:
• Any other job on any systems other than as mentioned above.
DO NOT USE on engines with low-pressure EGR systems, as detergent substances at the outlet of the DPF/
FAP® would be sucked back into the engine feeding system, which may damage it.
WORK AREA SAFETY
Clean the DPF/FAP® lter outdoors or in places with sufcient air recirculation.
Do not use exhaust suction pipes, because foam may come out of the exhaust pipe of the vehicle following cleaning;
provide a suitable foam collecting vessel.
For safety of use to be ensured, the CLEANING MACHINE must be operated by one person.
Caution! Some detergent liquids may be ammable.
Read the safety data sheets of the detergent additives used for cleaning with care and handle them with caution.
Check both the machine and the vehicle during operation. Do not leave the machine unattended while in operation
and during cleaning jobs.
Do not smoke near the engine or the device, to prevent res.
Make sure that re protection devices are available near the machine, in accordance with current provisions concerning
hygiene and safety in the workplace.
Keep children and bystanders away from your workplace while operating the CLEANING MACHINE. Distractions from
other people can cause you to lose control over the machine during use.
PERSONNEL SAFETY
- Avoid contact of additives with the skin; wear suitable goggles and gloves, if possible (see section “PERSONAL PROTECTIVE
EQUIPMENT TO WEAR WHILE OPERATING CLEANING MACHINE”).
- Keep re extinguishers suitable for the fuel nearby.
- Use only in well-ventilated areas.
- Check that there are no leaks before treatment. The vehicle feeding system must be leak-proof.
- Use the device only with a sufciently charged 12V vehicle battery.
- Protect the heated surfaces from leaks and splashes of detergent additives and fuel during operation.

9
INSTRUCTIONS FOR USE EN
DPF/FAP® CLEANING MACHINE SAFETY
- In case of contact of additives with painted surfaces, ush with water immediately.
- The machine must always stand on a at surface, both while in operation and when not in use, to prevent any aggressive liquids
from spilling; a trolley should be used as a support.
Additional personal protective equipment to wear according to the values found in the environmental
hygiene/risk analysis survey if the values exceed the limits under current regulations.
PERSONAL PROTECTIVE EQUIPMENT TO WEAR WHILE OPERATING CLEANING MACHINE
Failure to observe the following warnings may result in physical injury and/or disease.
ALWAYS WEAR PROTECTIVE GLOVES AGAINST CHEMICAL AGENTS.
ALWAYS WEAR EYE PROTECTION WHILE OPERATING THE MACHINE.
TECHNICAL DATA
1) Display
2) Start button (START)
3) Increase (↑) / Decrease (↓) buttons for cycle duration
4) Stop button (STOP)
5) Tank cap
6) 12 Volt power supply terminals
7) Quick coupler for DPF/FAP® pipe
Tank cap
12 Volt power supply terminals
Quick coupler for DPF/FAP® pipe
Tank cap
12 Volt power supply terminals
375 mm
230 mm
152 mm
1 L
12V battery

10
ISTRUZIONI PER L’USO I
INSTRUCTIONS FOR USE EN
SYSTEM CLEANING
For Euro 6 diesel engines with low-pressure EGR valves (installed below the DPF/FAP® system), disconnect
either the valve or the power supply from the valve, in order to prevent opening during treatment. If this step
should not be taken, the engine might be severely damaged by the foam formed while cleaning the DPF/FAP®
system.
Connection to DPF/FAP® system
- Place the machine near the vehicle, on a trolley (if possible), in order to avoid vibration during operation.
Do not place the machine on the vehicle, to prevent liquid from accidentally spilling
- The adapters supplied with the machine can be used to connect the DPF/FAP® pipe to the DPF/FAP® system of the vehicle.
This operation can be performed in three different ways:
• From the DPF/FAP® pressure sensor pipe, recommended. Locate and disconnect the pressure pipe from the sensor;
t the knurled tting supplied with the machine into the disconnected pipe; then connect the DPF/FAP® pipe to the
tting.
• From the DPF/FAP® temperature probe. Remove the temperature probe from the lter; then t the spray nozzle into
the hole of the temperature probe, being careful to rotate the liquid outlet holes in the direction of the exhaust gas ow,
to make sure that the internal DPF/FAP® lter is directly wetted.
• From the lambda probe
NB: Not all the DPF/FAP® systems make this type of cleaning possible.
Check that the hole of the lambda probe is turned to the DPF/FAP® lter, without making the liquid ow through other
parts of the system; then use adapter (A).
If the liquid needs to be injected over some other parts, use adapter (B) with pipe, screwing the proper tap (supplied in
sizes M14-M16-M18). Let the pipe go through the grommet, as far as the DPF/FAP® lte.
DPF/FAP® system cleaning - Preparation
Carry out the treatment with a cold engine..
Fill the DPF/FAP® tank with cleaning liquid; 1 litre of liquid is enough for one cleaning cycle of the DPF/FAP® system.
With vehicles with large-capacity lters or in case of excessively dirty DPF/FAP®s, treatment may need to be repeated several
times, in order to achieve the required result. After treatment has been completed, regeneration may be required, through
diagnostic equipment.
CAUTION: The machine cannot operate if the tank does not contain a sufcient amount of liquid.
Use only suitable products, since the Manufacturer will not be liable for damage to the vehicles and machine caused by the use
of products with any characteristics other than those recommended.
The machine has been mainly tested to operate with liquids containing the following compounds in the following percentages:

11
INSTRUCTIONS FOR USE EN
- Connect the terminals of the electric cable of the machine to the vehicle’s battery: hook up the black terminal to the negative
pole (-) and the red terminal to the positive pole (+).
- When the machine is turned on, the screen where the waiting time recommended by the liquid manufacturer following injection
of the cleaning liquid (Cleaner) can be set will be shown.
- Select Clno if no waiting time is required, or enter the required amount of time in minutes;
then press START.
- Set the waiting time recommended by the liquid manufacturer following injection of the ushing liquid (Flush).
- Select FLno if no waiting time is required, or enter the required amount of time in minutes;
then press START.
- Set the acceleration time recommended by the liquid manufacturer following liquid injection; select ACno if no acceleration time
is required, or enter the required amount of time in minutes;
• ammonia ≤ 25%
• ethoxylated alcohol ≤ 4
• propanol ≤ 25%
• butoxyethanol ≤ 15
• sodium hydroxide ≤ 0,3%
All the stages of cleaning are shown on the displays on the front panel.
For a wide range of liquids of several brands to be used, the software provides initial settings to congure treatment according
to the operating specications requested by the liquid manufacturer. Simple initial settings allow the various stages of cleaning,
ushing and acceleration to be congured; in addition, the cycles that are not requested by liquid manufacturers can be bypassed.
Cycle indication Cycle description Time setting
CLno Bypassing of cleaning function (CLEANING) /
CL15 Waiting time adjustment following cleaning liquid
injection If, for example, value 15 is set, the waiting time
will be 15 minutes.
CLEA Displaying, alternating with minutes, throughout
cleaning liquid waiting time /
FLno Bypassing of ushing function (FLUSH) /
FL10 Waiting time adjustment following ushing liquid
injection (FLUSH) If, for example, value 10 is set, the waiting time
will be 10 minutes.
FLUS Displaying, alternating with minutes, throughout
ushing liquid waiting time /
ACno Bypassing of acceleration function /
AC05 Acceleration time adjustment at 2500 rpm If, for example, value 05 is set, the vehicle will
be kept accelerated for 5 minutes.
ACCE Displaying, alternating with minutes, throughout
acceleration time /
PURG PURGE function, for tank emptying /
---- -- Moving segments indicate that liquid is missing
in tank /

12
ISTRUZIONI PER L’USO I
INSTRUCTIONS FOR USE EN
MAINTENANCE
Routine maintenance of pump
Cleaning products for diesel or petrol injection systems, cleaners for suction pipes and cleaners for diesel particulate lters are
often extremely aggressive; in case of prolonged contact, they may eat into the electrical and mechanical parts of the pump.
In case of prolonged contact with air, the products oxidize and may form a viscous lm which settles in the gears of the pump (as
well as in the tanks and pipes).
This lm may affect pump operation. Therefore, both the pump and the tanks should be emptied after each treatment through
the PURGE function.
Maintenance of quick couplers
The quick couplers contain some moving parts. Both metal and the gaskets may get worn out as the result of the movement of
these parts.
Therefore, the quick couplers must be replaced after some time.
then press START.
- alla ne di questo ciclo se non e presente il liquido nel serbatoio apparirà il messaggio
- Fill the tank, start the vehicle and press START, the cleaning liquid will be injected into the lter through 3 alternating sprays; a
2-minute waiting time will then follow; when the 2-minute waiting time has elapsed, the pump will inject some more liquid through
alternating sprays, until the tank is completely emptied. If the waiting time has been set, it will start running, to allow the cleaning
liquid to act on the system; alternatively, the display will show the remaining waiting time.
- If the acceleration time has been set, press START and accelerate the vehicle to 2500 rpm.
Alternatively, the display will show the remaining waiting time.
- When this cycle is completed and if no liquid is available in the tank, the following message will be shown
- Fill the tank and press START; the ushing liquid will be injected into the lter, until the tank is completely emptied. Alternatively,
the display will show the remaining waiting time.
- If the acceleration time has been set, press START and accelerate the vehicle to 2500 rpm.
Alternatively, the display will show the remaining waiting time
- After the set acceleration time has elapsed, the STOP screen will be displayed, to mark the end of the cleaning cycle.
- remove the equipment and restore the vehicle’s system to its original connections.
- If some liquid is left in the tank, it can be removed by pressing the START and STOP buttons simultaneously; activate the pump
for 1 minute, inhibiting level sensor control; this will allow the liquid to be poured into an external vessel.

13
INSTRUCTIONS FOR USE EN
The life of quick couplers is affected by the following factors:
- the number of times the couplers are connected and disconnected;
- the cleaning product that remains in prolonged contact with the O-rings of the couplers. This liquid oxidizes and forms
a viscous lm or eat into the rubber of the O-rings;
- weathering: water, salt and acids eat into metals;
- dust and dirt may cause abrasion to the moving parts..
Take the following steps, to extend the life of these parts as much as possible:
- always use the PURGE function to empty both the liquids out of the pipes and ttings;
- do not expose the machine to any external agents, including rain and salt;
- lubricate the quick couplers when not in use for prolonged periods of time, before tting them in;
- if some hardening should be shown anyway, the couplers will be treated with a layer of silicone, which can be restored by
spraying LUBRICATING SILICONE.
Extraordinary maintenance
Any extraordinary maintenance and repair jobs other than those described above must be carried out by authorised personnel
only; please contact Beta Utensili S.p.A.’s repair centre.
DISPOSAL
The CLEANING MACHINE must be disposed of in accordance with the law provisions in force in the country of use.
Liquid disposal
Liquid residues must be disposed of in accordance with current law provisions and the information contained in the Safety Data
Sheet (SDS).
WARRANTY
This equipment is manufactured and tested in accordance with current EU regulations, and is covered by a 12-month warranty for
professional use and a 24-month warranty for non professional use respectively.
We will repair any breakdowns caused by material or manufacturing defects by xing or replacing the defective pieces or replacing
them at our discretion. Should assistance be required once or several times during the warranty period, the expiry date of this
warranty will remain unchanged. This warranty will not cover defects due to wear, misuse or breakdowns caused by blows and/or
falls. In addition, this warranty will no longer be valid if any changes are made, or if the cleaning machine is forced or sent to the
customer service in pieces. This warranty explicitly excludes any damage to people and/or things, whether direct or consequential.
DECLARATION OF CONFORMITY
We hereby declare, assuming full responsibility, that the described product complies with all the relevant provisions of the
following Directives:
• Machine Directive 2006/42/EC
• LVD Directive 2014/35/EU
• EMC Directive 2014/30/EU
• RoHS Directive 2011/65/EU.
The Technical Brochure is available at:
BETA UTENSILI S.P.A.
Via A. Volta 18,
20845 Sovico (MB)
ITALY
Product approved and tested also by

56
BETA UTENSILI S.p.A.
Via Alessandro Volta, 18 - 20845 Sovico (MB) ITALY
Tel. +39 039.2077.1 - Fax +39 039.2010742
www.beta-tools.com
Other manuals for 1899A
2
Table of contents
Other Beta Measuring Instrument manuals
Popular Measuring Instrument manuals by other brands
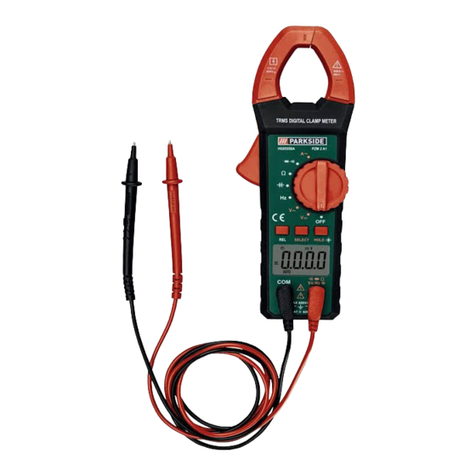
Parkside
Parkside PZM 2 A1 Operation and safety notes
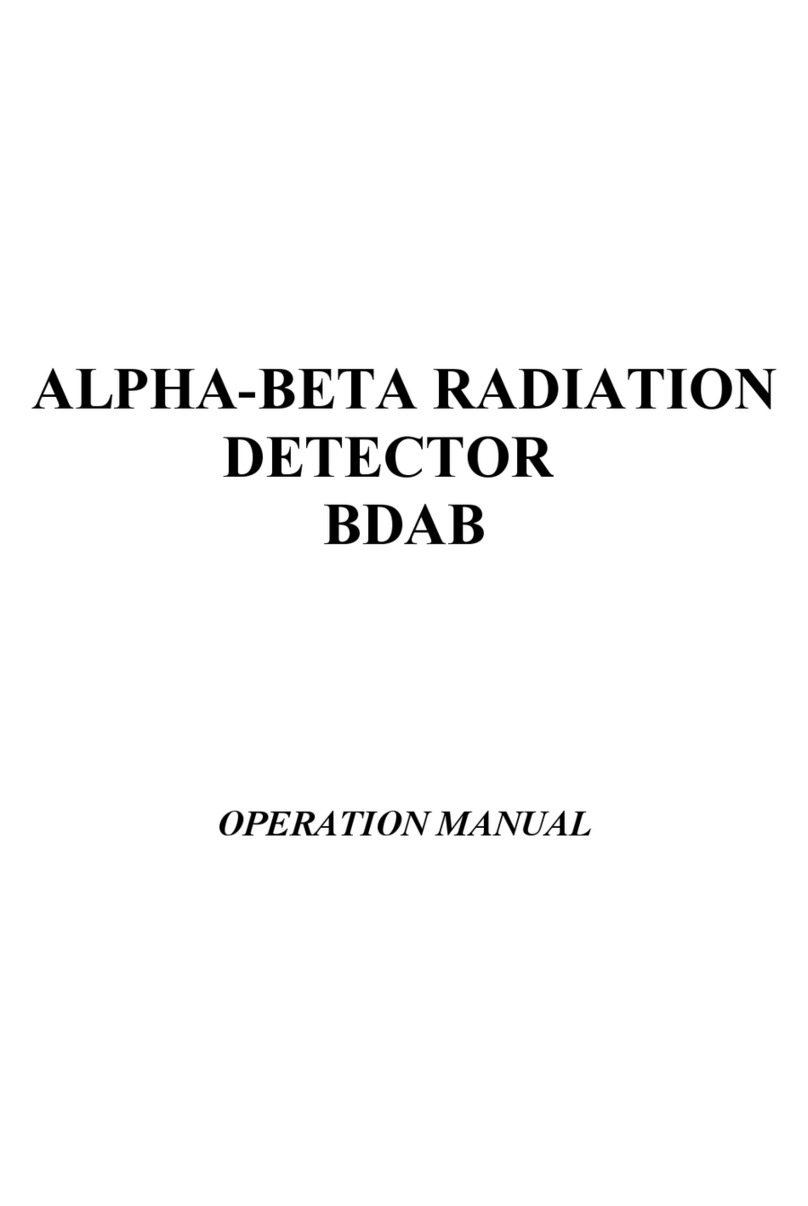
Polimaster
Polimaster PM1403 Operation manual

Sunforest
Sunforest H-100 series user manual
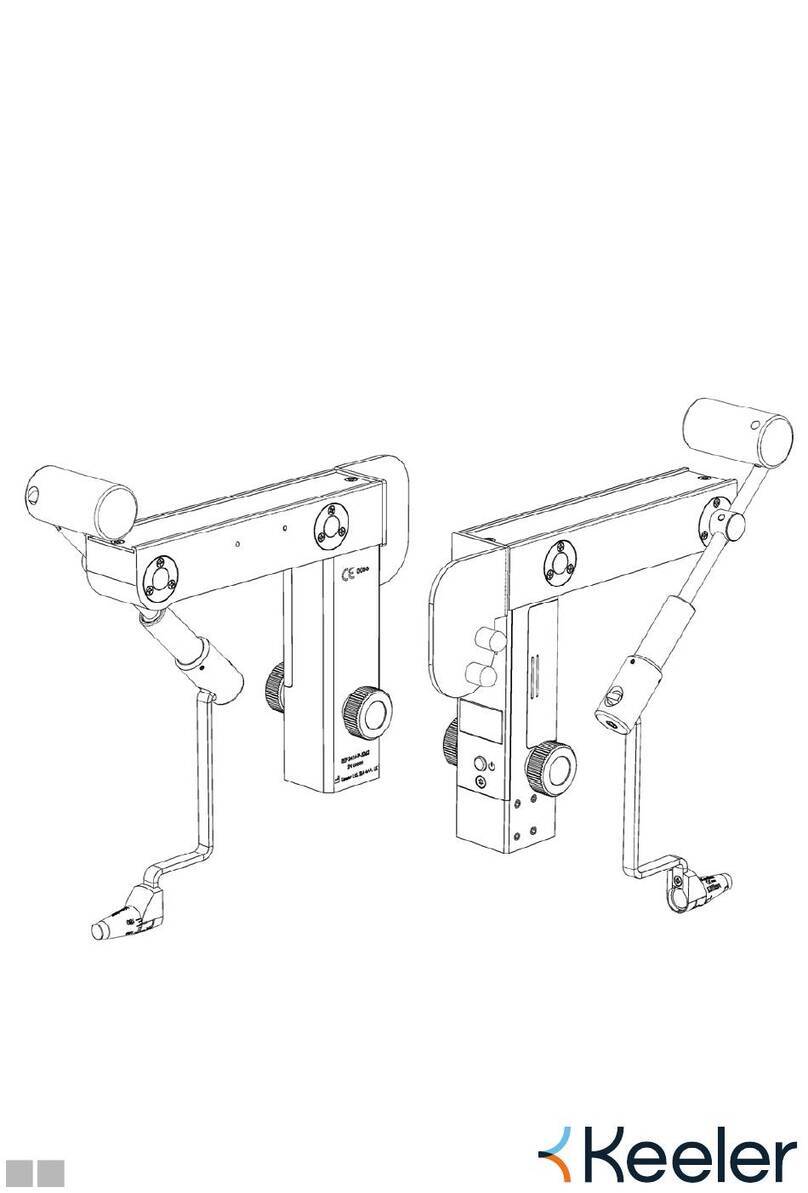
Keeler
Keeler D-KAT Z Instructions for use
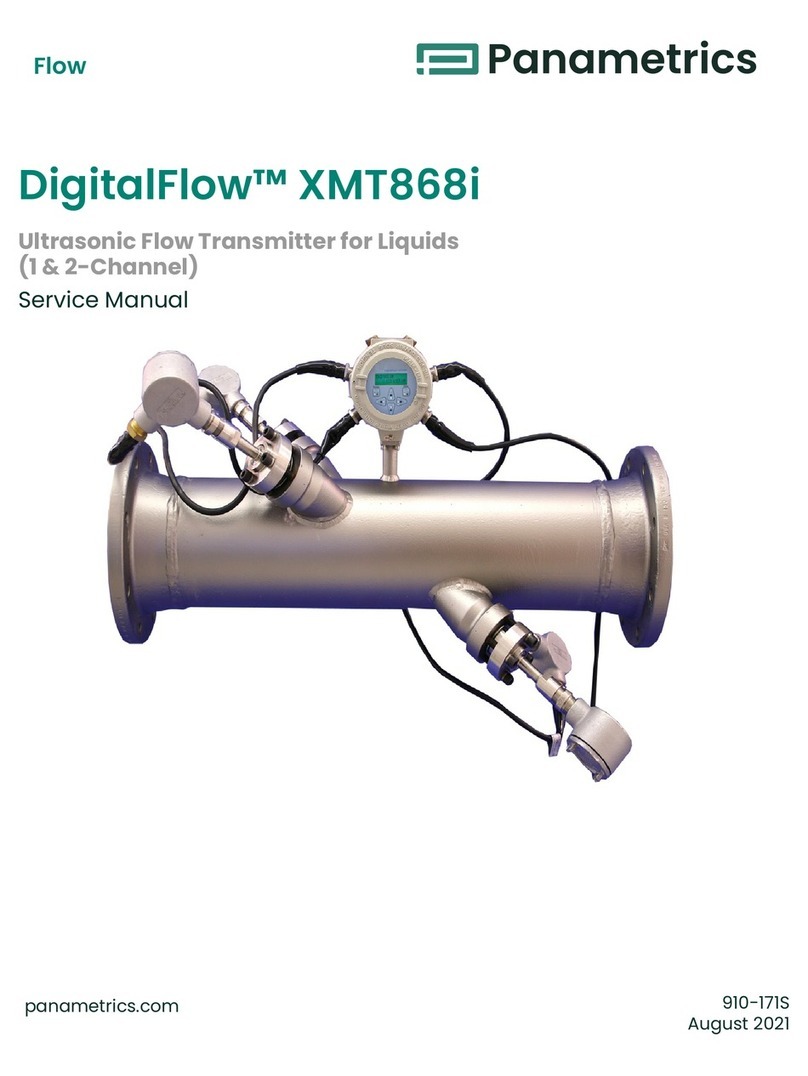
Panametrics
Panametrics DigitalFlow XMT868i Service manual

MADDALENA
MADDALENA ElecTo SJ Instructions for installation, use and maintenance