Eaton Flex Shaft Manual

Contents
Description Page
1. General Information.....................2
2. Installation ............................3
3. Alternate Installation ....................4
Effective November 2014
Instruction Leaflet IL012052EN
Instructions for Drilling and Assembling High Performance Flex
Shaft™ and Dual Flex Shaft™ Handle Mechanism for F-Frame,
Series C Circuit Breakers, Molded Case Switches, and HMCPs

2
Instruction Leaflet IL012052EN
Effective November 2014
Instructions for Drilling and Assembling High Performance Flex
Shaft™ and Dual Flex Shaft™ Handle Mechanism for F-Frame,
Series C Circuit Breakers, Molded Case Switches, and HMCPs
EATON www.eaton.com
mWARNING
DO NOT ATTEMPT TO INSTALL OR PERFORM MAINTENANCE ON
EQUIPMENT WHILE IT IS ENERGIZED. DEATH, SEVERE PERSONAL INJURY,
OR SUBSTANTIAL PROPERTY DAMAGE CAN RESULT FROM CONTACT WITH
ENERGIZED EQUIPMENT. ALWAYS VERIFY THAT NO VOLTAGE IS PRESENT
BEFORE PROCEEDING WITH THE TASK AND ALWAYS FOLLOW GENERALLY
ACCEPTED SAFETY PROCEDURES. EATON IS NOT LIABLE FOR THE
MISAPPLICATION OR MISINSTALLATION OF ITS PRODUCTS.
The User is cautioned to observe all recommendations,warnings, and
cautions relating to the safety of personnel and equipment as well as
all general and local health and safety laws, codes, and procedures.
The recommendations and information contained herein are based on
Eaton experience and judgment, but should not be considered to be
all-inclusive or covering every application or circumstance which may
arise. If any questions arise, contact Eaton for further information or
instructions.
1. General Information
The High Performance Flex Shaft handle mechanism provides a
means of externally operating the circuit breaker and can be applied
to enclosures of varying heights and depths. The handle can be used
with NEMA 1, 3R, 12, and 4/4X enclosure applications, depending on
the accessory components selected. An operating handle, flexible
shaft, and mechanism are required for standard application. Eight
lengths of shafts are available for use with the wide range of depths
of various enclosures (3 through 10 ft [0.91 through 3.05 m]). When
selecting the length of the Flexible Shaft, ensure minimum bending
radius of 4 in. (101.60 mm) is maintained to operate properly. The
standard method of shipment includes the mechanism preset at
the factory. If minor field adjustments are required, see Figure 3
or Figure 8. For this publication, the term circuit breaker shall also
include the molded case switch and Series C motor circuit protector
(HMCP).
mWARNING
WHEN INSTALLING A NEW HANDLE MECHANISM, OR A NEW CIRCUIT
BREAKER AND HANDLE MECHANISM IN AN EXISTING ELECTRICAL
SYSTEM, MAKE SURE THERE IS NO VOLTAGE PRESENT WHERE WORK IS
TO BE PERFORMED. SPECIAL ATTENTION SHOULD BE PAID TO REVERSE
FEED APPLICATIONS TO ENSURE NO VOLTAGE IS PRESENT. THE VOLTAGE
IN ENERGIZED, EQUIPMENT CAN CAUSE DEATH OR SEVERE PERSONAL
INJURY.
Figure 1. Securing the Actuator Mechanism to the Breaker and Toggle Mechanism and the Handle to the Flange.
F-DUAL FRAME
ASSEMBLY
STAND-OFF
(4 PLACES)
ACTUATOR
MECHANISM
#8-32 SCREW
.500 (4 PLACES)
#8-32 SCREW
.500 (4 PLACES)
#8-32 LOCK WASHER
(8 PLACES)
BELL CRANK
TOGGLE MECHANISM
ASSEMBLY
THESE ITEMS ARE TO BE
ASSEMBLED AFTER HANDLE
IS MOUNTED TO ENCLOSURE.
OUTER HANDLE MECH
MOUTNING SCREWS,
1/4-20 x .875 HEX
(2 PLACES)
1/4 LOCK WASHERS
(2 PLACES)
ENCLOSURE
OUTER
HANDLE
MECHANISM
F-FRAME
ASSEMBLY
STAND-OFF
(4 PLACES)
ACTUATOR
MECHANISM
#8-32 LOCK WASHER
(8 PLACES)
#8-32 LOCK WASHER
(8 PLACES)
#8-32 SCREW
.500 (4 PLACES)

3
Instruction Leaflet IL012052EN
Effective November 2014
Instructions for Drilling and Assembling High Performance Flex
Shaft™ and Dual Flex Shaft™ Handle Mechanism for F-Frame,
Series C Circuit Breakers, Molded Case Switches, and HMCPs
EATON www.eaton.com
2. Installation
For assembly steps, refer to Figure 1, unless otherwise noted.
1. For a single breaker, mount the breaker with four stand-offs and
lock washers. For dual breakers, mount each breaker with two
standoffs and lock washers (inner mounting holes of the breaker)
and two mounting screws and lock washers (outer mounting
holes of the breaker). Tighten 28 in.-lb (3.16 N●m).
Figure 2. Outer Handle Mechanism Assembly.
Figure 3. F-Frame Dual Mechanism.
2. Install the handle to the enclosure by removing the two screws
and lock washers from the outer handle mechanism. Place the
outer handle mechanism with attached gasket over the enclosure
cut-out (for cut- out dimensions, refer to Figure 7). Insert the top
¼-20 outer handle mechanism mounting screw and lock washer
through the enclosure and thread into the outer handle mecha-
nism for a few turns, but not all the way.
3. Slide the toggle mechanism assembly over the top of the handle
mounting screw. Insert the bottom outer handle mechanism
mounting screw and lock washer through the toggle mechanism
bracket, through the enclosure, then into the handle. Tighten
both mounting screws 23 - 37 in.-lb (2.60 -4.18 N●m) maximum.
4. Rotate the bell crank towards the handle and rotate the outer
handle to the “ON” position. Align the actuator link (hole that is
marked “1”) and attach it to the bell crank.. Secure it using an
E-Ring (see Figure 5).
5. Connect the long end of the spring through hole in handle actua-
tor link. Hook the shorter end of the spring into the tab on the
lower portion of the toggle mechanism (see Figure 6).
Figure 4. F-Frame Dual Actuator Mechanism.
Figure 5. Assembly of Adaptor Link to Bell Crank.
6. Put outer handle mechanism in the “TRIP” position for ease of
mounting the actuator mechanism.
7. Mount the actuator mechanism to the breaker. Insert the four
#8-32 x .50 screws and lock washers through the mechanism
and into the standoffs. Tighten 28 in.-lb (3.16 N●m).
8. Mount the door interlock pin and lock washer to handle. Tighten
23 - 37 in.-lb (2.60 - 4.18 N●m).
9. Operate the handle mechanism to ensure functionality. To oper-
ate, either close the door or defeat the door interlock lever.
10. If minor adjustments are necessary, refer to the “Adjustment
Checklist” in Section 3.
11. Install the appropriate door hardware (supplied) (see Figure 7).
HANDLE MECHANISM
DOOR INTERLOCK PIN.
MODIFIED DEPENDING ON
SPRING
LOCK WASHER
WASHER/LOCKER WASHER/NUT
LIFTING WASHER/NUT
SLEEVE
FORMED CUTOUT
BULKHEAD CONNECTOR
WASHER/LOCKER WASHER/NUT
LIFTING WASHER/NUT
SLEEVE
SLIDER PLATE
BULKHEAD CONNECTOR

4
Instruction Leaflet IL012052EN
Effective November 2014
Instructions for Drilling and Assembling High Performance Flex
Shaft™ and Dual Flex Shaft™ Handle Mechanism for F-Frame,
Series C Circuit Breakers, Molded Case Switches, and HMCPs
EATON www.eaton.com
Figure 6. Assembly of Spring to Toggle Mechanism.
3. Alternate Installation
mWARNING
BEFORE ANY INSTALLATION OR MAINTENANCE IS PERFORMED, MAKE
SURE THAT THE BREAKER IS NOT ENERGIZED.
In the event a customer must disassemble the pre-assembled Flex
Shaft handle mechanism, the procedure listed below must be fol-
lowed before continuing with the "Installation" instructions (see
Figure 4).
1. Remove the flat washer, lock washer, and nut assembly.
2. Loosen the bulkhead connectors and remove Flex Shaft from the
actuator mechanism. The shaft may not be routed as required.
3. Place circuit breaker in the "ON" position.
4. Place the operating handle in the full "ON" position.
5. Replace the Flex Shaft through the actuator mechanism. Center
the bulkhead connectors on the threaded portion and tighten to
approximately 70 in.-lb (7.91 N●m).
6. Place the formed cutout in the slider plate over the breaker
handle while still in the "ON" position. Turn the lifting washer/nut
until it is flush against the slider plate.
7. Replace the flat washer, lock washer, and nut assembly for the
Flexible Shaft assembly. Tighten both nuts to approximately
45 in.-lb (5.08 N●m).
8. Check the operation of mechanism for "ON", "OFF", and "RESET".
Check the reset position of the actuator mechanism, that the
lifting nut and sleeve of shaft do not come in contact with each
other (see Figure 4). If they do, move the bulkhead connectors
accordingly. If the mechanism functions incorrectly, repeat the
procedure or go to Adjustment Checklist.
Adjustment Checklist
Situation:
Breaker turns "ON" and "OFF", but will not Reset when tripped.
Adjustment:
Loosen the lifting washer/nut while tightening the washer/lock
washer/nut. Two or three turns should be sufficient (see Figures 3
and 4).
ote:N Check the reset position of the actuator mechanism, so that the lifting
nut and sleeve of the shaft do not come into contact with each other (see
Figures 3 and 4). If they do, move the bulkhead connectors accordingly.
Situation:
The breaker resets after tripping, but does not turn "ON".
Adjustment:
For a K-Flexible Shaft Assembly, loosen the washer/lock washer/nut
on the end of the shaft while tightening the lifting washer/nut until
the breaker turns "ON" with positive action. Tighten both nuts and
recheck for "ON", "OFF",and "Reset" positions (see Figures 3 and 4).
ote:N After adjustment, be certain to have a minimum of one thread past the
washer/lock washer/nut assembly (see Figures 3 and 4).
If any other adjustment problems should arise, contact your local
Eaton representative.

5
Instruction Leaflet IL012052EN
Effective November 2014
Instructions for Drilling and Assembling High Performance Flex
Shaft™ and Dual Flex Shaft™ Handle Mechanism for F-Frame,
Series C Circuit Breakers, Molded Case Switches, and HMCPs
EATON www.eaton.com
Installation Instructions for Door Interlock
Figure 7. Flange Drilling Plan for Handle and Interlock Blade Mounting Dimensions.
1.88 (47.75)
MIN.
0.88
(22.35)
5.75 (146.05) MIN.
0.88 (22.35)
1.06
(26.92)
0.59
(14.99)
MOUNTING BRACKET WELD OR
RIVET TO COVER AS SHOWN
UPPER HOLE
LOCKWASHER
LOCKING LEVER
EXTENSION
INTERLOCK BLADE
0.59
(14.99)
2.83 (71.88)
2.00 - 1.50
(50.80 - 38.10)
0.25
(6.35)
0.03 (0.76)
DEFEATER SCREW
INTERLOCK BLADE
CHECK POSITION WITH
HANDLE IN EXTREME OFF
(OPEN COVER) POSITION
R 5.51 (139.95)
2.281 (57.94)
2.75 (69.82) MIN.
INSIDE 0.56 (14.22)
3.44 (87.38)
0.50 (12.7)
4.69 (119.13)
2 CLEARANCE HOLES
IN FLANGE FOR
1/4-20 SCREWS
R 0.250 (6.35)
0.31 (7.87)
0.63 (16.00)
2.00
(50.80)
2.59
(65.89)
2X n 0.20 (5.08) HOLES IN ENCLOSURE
DOOR FOR RIVETS
ON
OFF

6
Instruction Leaflet IL012052EN
Effective November 2014
Instructions for Drilling and Assembling High Performance Flex
Shaft™ and Dual Flex Shaft™ Handle Mechanism for F-Frame,
Series C Circuit Breakers, Molded Case Switches, and HMCPs
EATON www.eaton.com
Figure 8. Dual Flex Shaft Breaker Drilling Plan.
0.750 (19.05)
2.875
(73.03)
4.500
(114.30)
.164-32 TAP HOLES 0.688
(17.48)
0.688
(17.48)
2.750
(69.85)
1.375
(34.93) LINE END
LOAD END

7
Instruction Leaflet IL012052EN
Effective November 2014
Instructions for Drilling and Assembling High Performance Flex
Shaft™ and Dual Flex Shaft™ Handle Mechanism for F-Frame,
Series C Circuit Breakers, Molded Case Switches, and HMCPs
EATON www.eaton.com
Notes:

Eaton
Electrical Sector
1000 Eaton Boulevard
Cleveland, OH 44122
United States
877-ETN-CARE (877-386-2273)
Eaton.com
© 2014 Eaton
All Rights Reserved
Printed in USA
Publication No. IL012052EN / TBG001187
Part No. IL012052ENH01
November 2014
Eaton is a registered trademark.
All other trademarks are property of their
respective owners.
Instruction Leaflet IL012052EN
Effective November 2014
Instructions for Drilling and Assembling High Performance Flex
Shaft™ and Dual Flex Shaft™ Handle Mechanism for F-Frame,
Series C Circuit Breakers, Molded Case Switches, and HMCPs
The instructions for installation, testing, maintenance, or repair
herein are provided for the use of the product in general commercial
applications and may not be appropriate for use in nuclear applica-
tions. Additional instructions may be available upon specific request
to replace, amend, or supplement these instructions to qualify them
for use with the product in safety-related applications in a nuclear
facility.
This Instruction Booklet is published solely for information purposes
and should not be considered all-inclusive. If further information is
required, you should consult an authorized Eaton sales representa-
tive.
The sale of the product shown in this literature is subject to the
terms and conditions outlined in appropriate Eaton selling policies
or other contractual agreement between the parties. This literature
is not intended to and does not enlarge or add to any such contract.
The sole source governing the rights and remedies of any purchaser
of this equipment is the contract between the purchaser and Eaton.
NO WARRANTIES, EXPRESSED OR IMPLIED, INCLUDING
WARRANTIES OF FITNESS FOR A PARTICULAR PURPOSE OR
MERCHANTABILITY, OR WARRANTIES ARISING FROM COURSE
OF DEALING OR USAGE OF TRADE, ARE MADE REGARDING
THE INFORMATION, RECOMMENDATIONS, AND DESCRIPTIONS
CONTAINED HEREIN.
In no event will Eaton be responsible to the purchaser or user in
contract, in tort (including negligence), strict liability or otherwise
for any special, indirect, incidental or consequential damage or loss
whatsoever, including but not limited to damage or loss of use of
equipment, plant or power system, cost of capital, loss of power,
additional expenses in the use of existing power facilities, or claims
against the purchaser or user by its customers resulting from the
use of the information, recommendations and description contained
herein.
This manual suits for next models
1
Other Eaton Circuit Breaker manuals
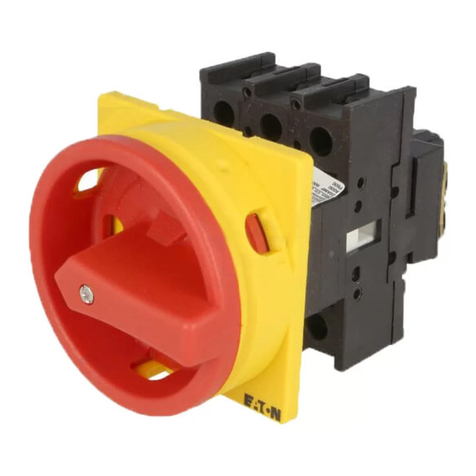
Eaton
Eaton P3 E(+SVB) Series Manual
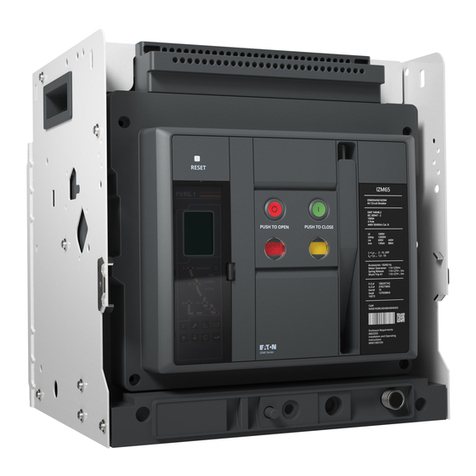
Eaton
Eaton IZM6 Series User manual
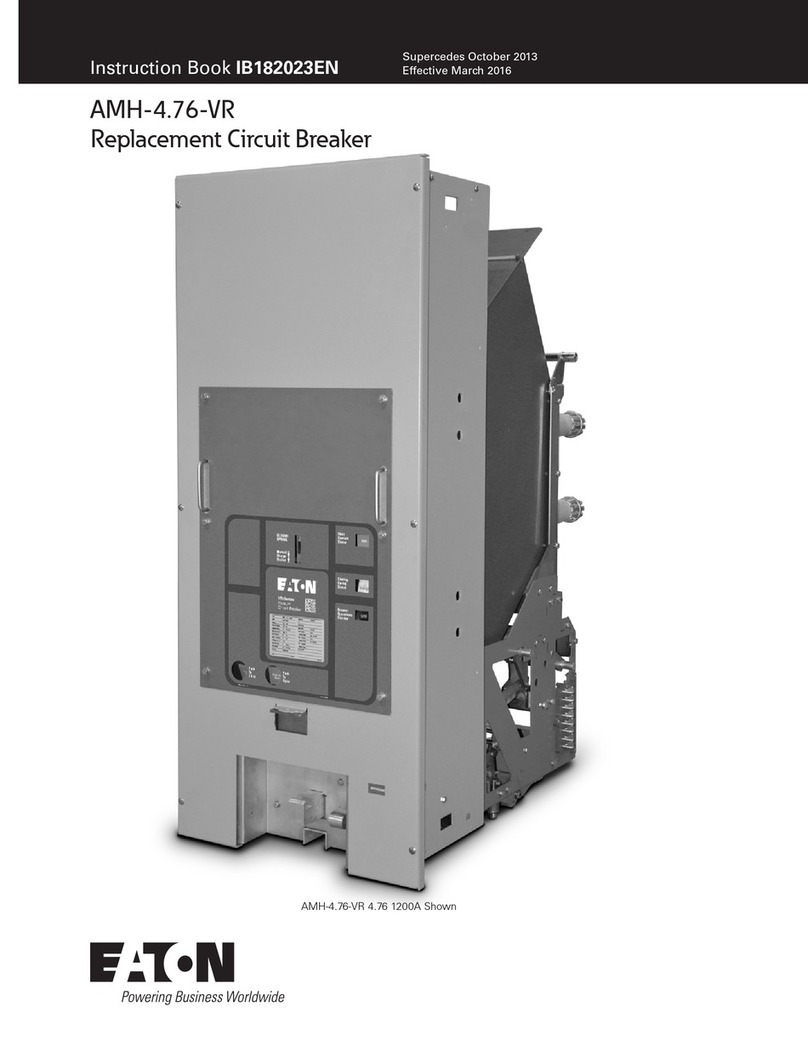
Eaton
Eaton AMH-4.76-VR User manual

Eaton
Eaton EX RT 11 Instruction Manual
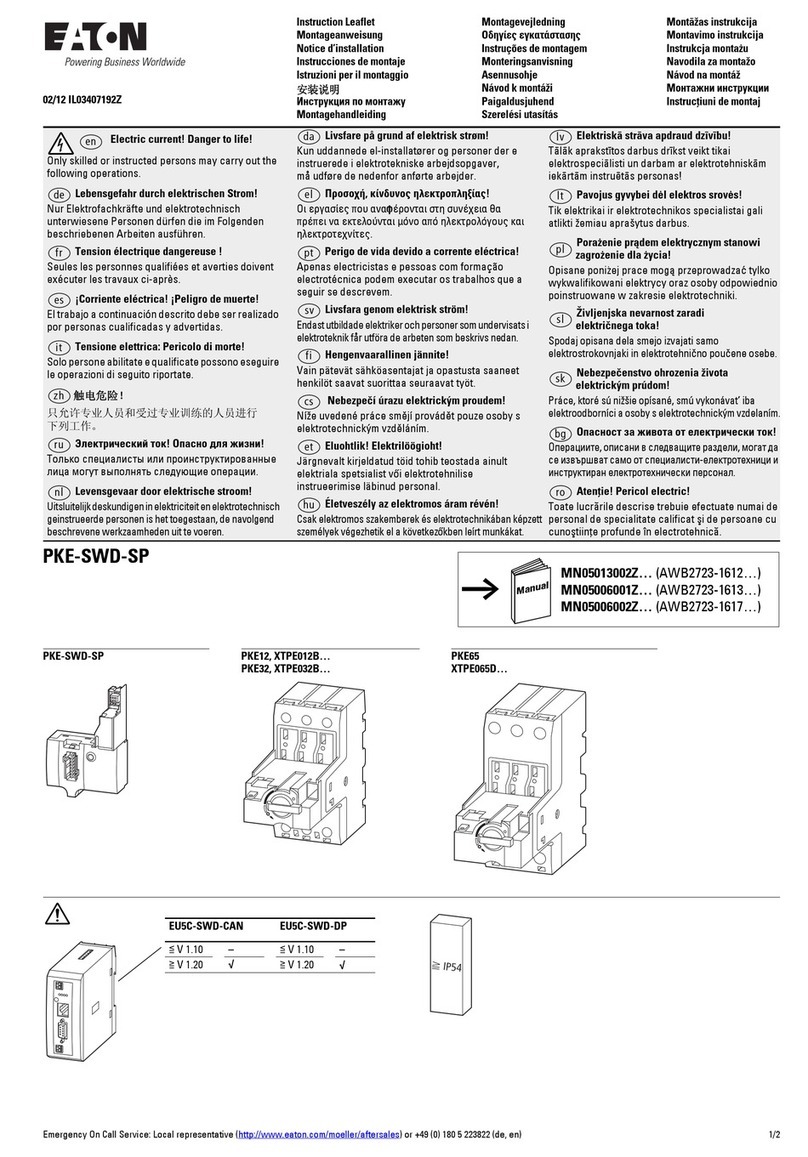
Eaton
Eaton PKE-SWD-SP Manual
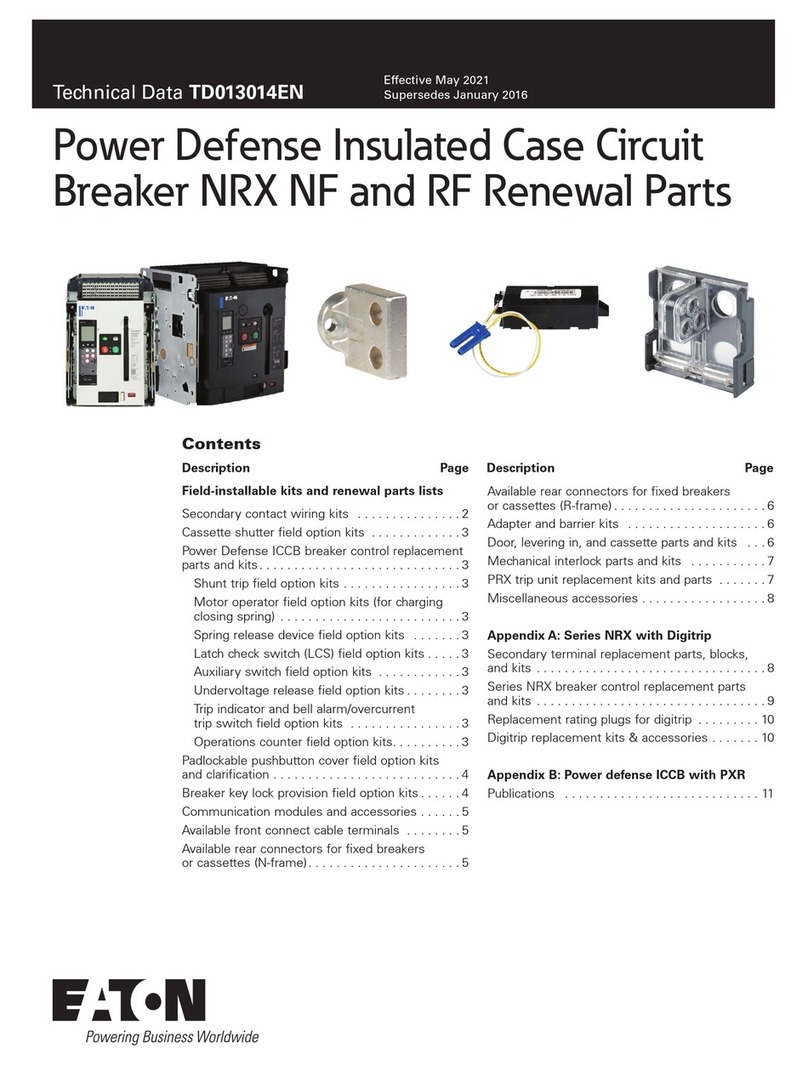
Eaton
Eaton NRX NF Instruction manual
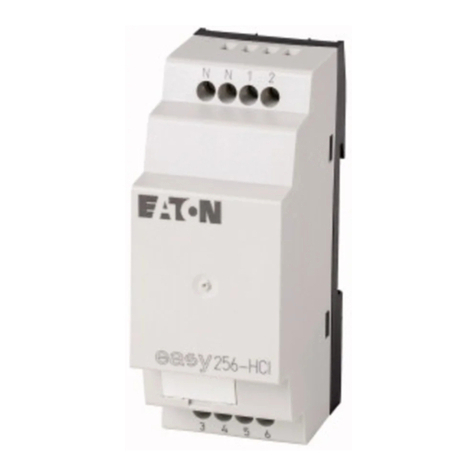
Eaton
Eaton EASY256-HCI Manual
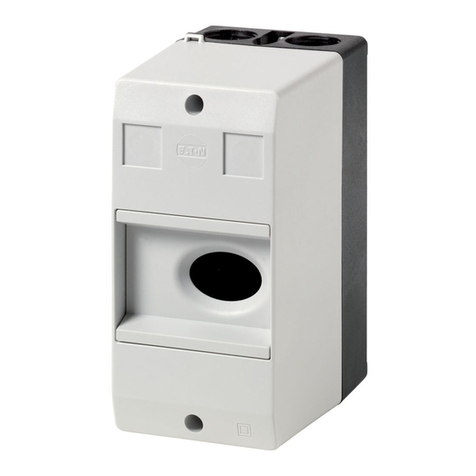
Eaton
Eaton CI-PKZ01 Series Manual
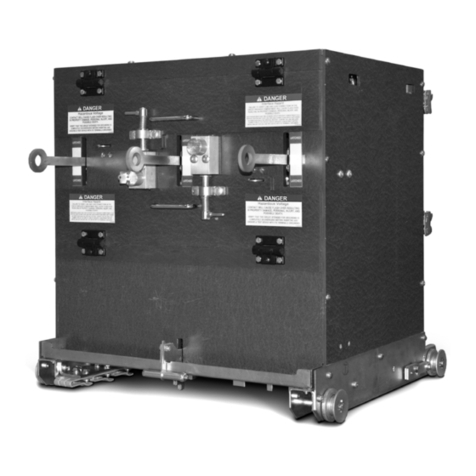
Eaton
Eaton 150VCP-W Series User manual

Eaton
Eaton 50 DHP User manual

Eaton
Eaton PXS24 Series User manual
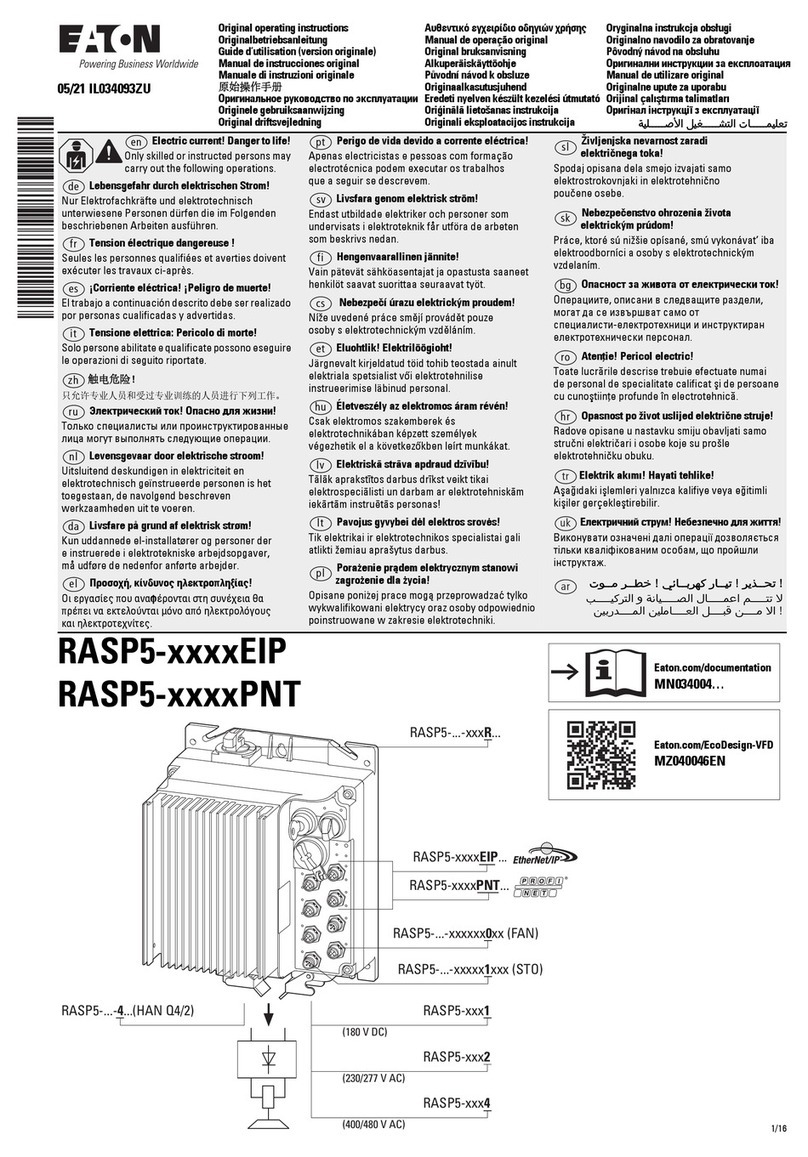
Eaton
Eaton RASP5 EIP Series User manual
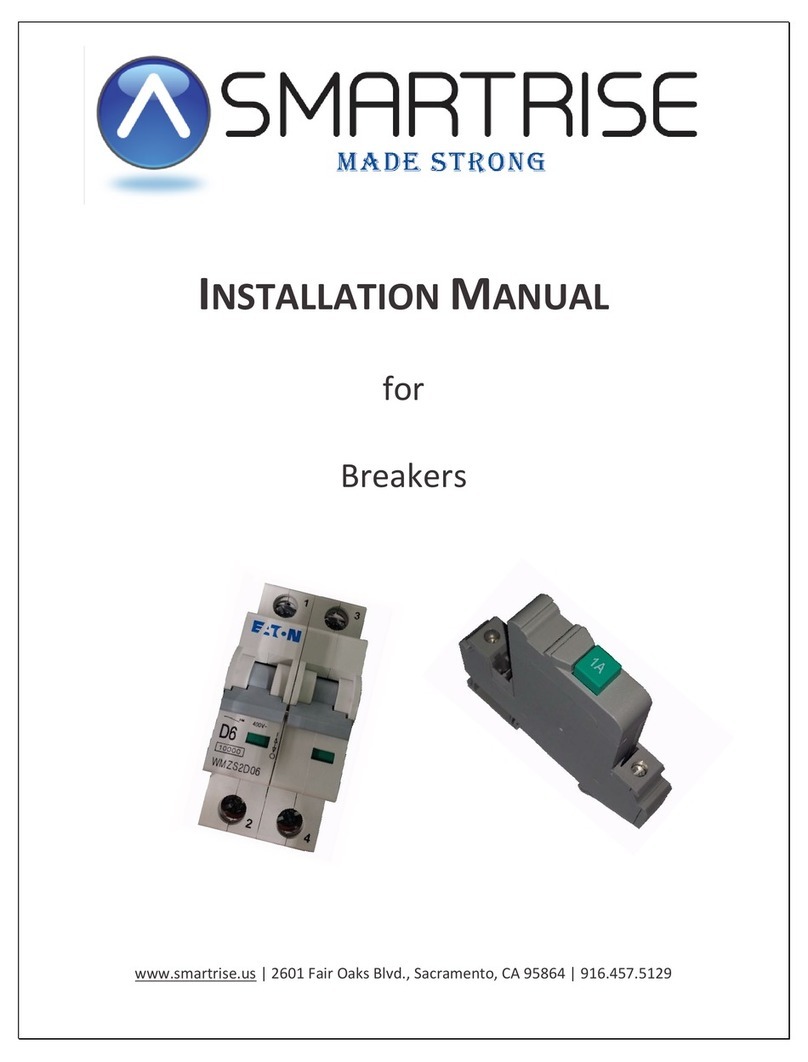
Eaton
Eaton D6 WMZS2D06 User manual
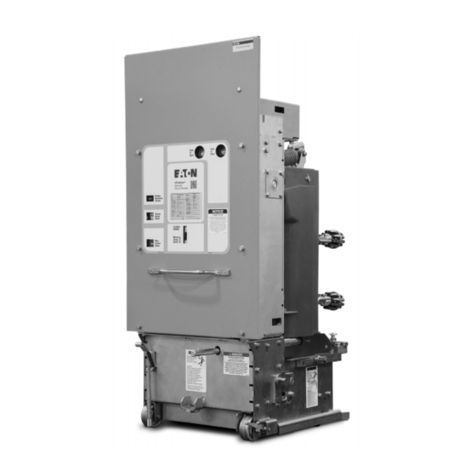
Eaton
Eaton Cutler-Hammer DHP-VR Series Programming manual
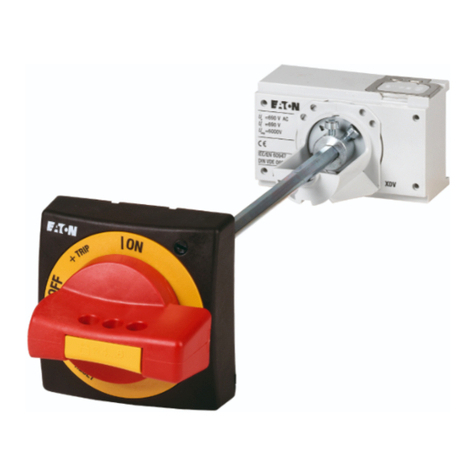
Eaton
Eaton NZM2 Manual
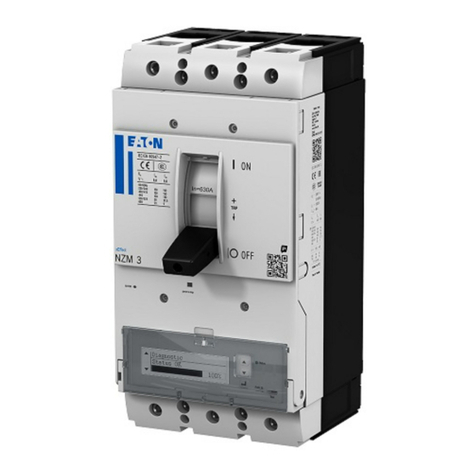
Eaton
Eaton NZM3-XAV Manual
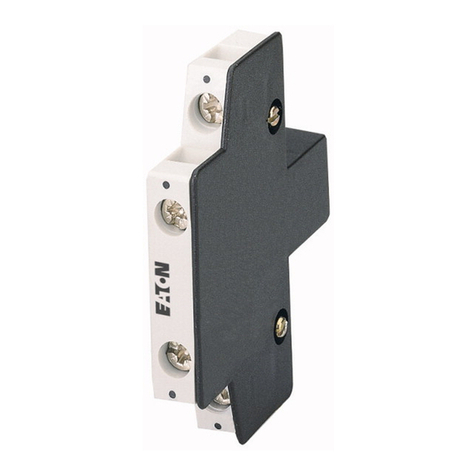
Eaton
Eaton DILM820-XHI11 Series Manual
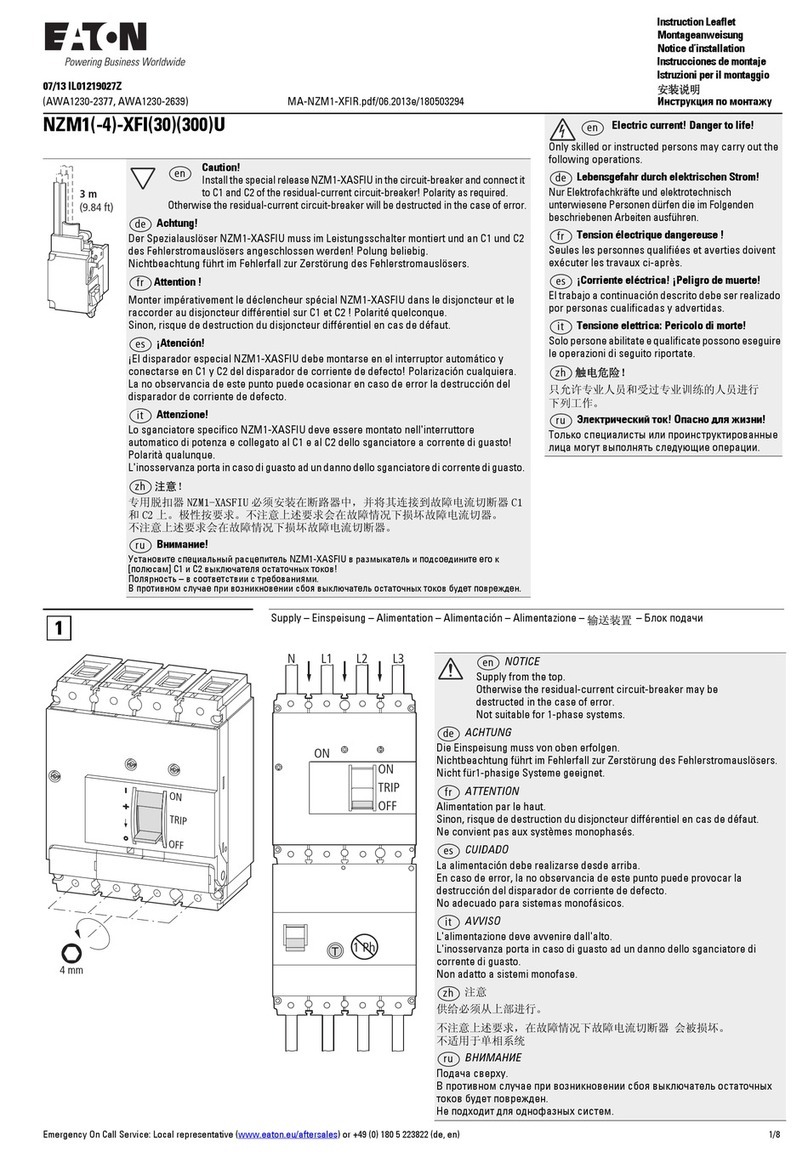
Eaton
Eaton NZM1 XFI U Series Manual
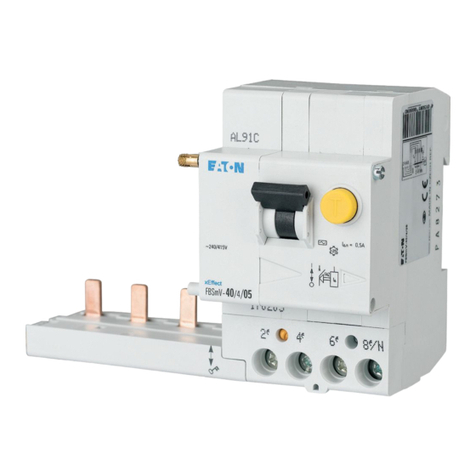
Eaton
Eaton FBSmV Manual
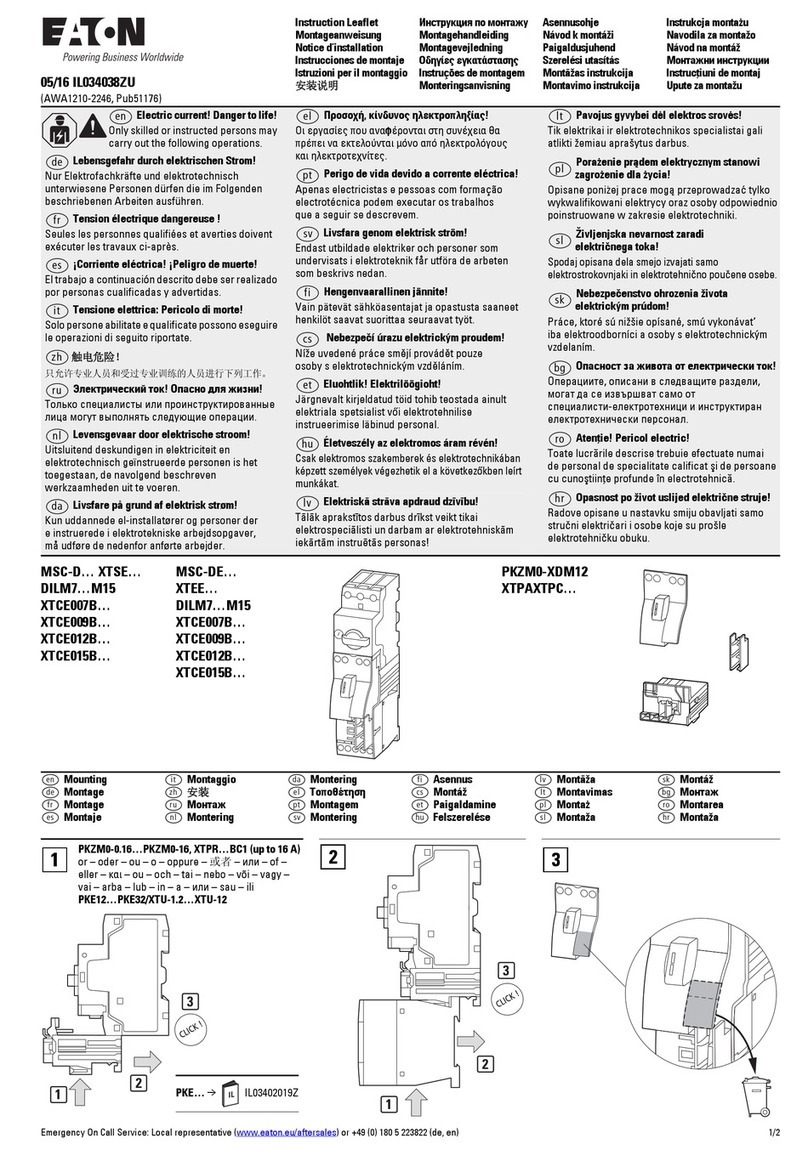
Eaton
Eaton MSC-D XTSE Series Manual