EFORT ER10-1600 User manual

ER10-1600 Quick Operation Manual for Industrial Robot
Ⅰ
ER10-1600 Quick Operation Manual
for Industrial Robot
EFORT Intelligent Equipment Co., Ltd.
Service Line(Tel):400-0528877

ER10-1600 Quick Operation Manual for Industrial Robot
Statement
Thank you for purchasing EFFORT ER10-1600 industrial robot. Please
read the instruction manual before starting to use the robot. The following
contents are directly related to your personal and property safety. Any
misconduct that does not strictly follow the instructions as stated in the manual
may result in physical damage or property loss. The statement and instruction
manual is the latest version for ER10-1600 series. More updates can be found at
www.efort.com.cn.
This manual only serves as the operation guide for ER10-1600 industrial
robots. EFFORT will not be responsible for any physical damage or property
loss that is not caused by the defect of the product. It is strongly recommended
that operators should have received special training before having access to
operation, teaching, repair, maintenance and inspection of the product.
Version No.:V 1.0

ER10-1600 Quick Operation Manual for Industrial Robot
III
Contents
Chapter One Safety............................................................................................................... 1
1.1 Safety Instructions.............................................................................................................1
1.2 Safety Regulations.............................................................................................................1
Chapter Two Handling and Installing the Robot.................................................................... 3
2.1 General Introduction......................................................................................................... 3
2.2 Basic Description.............................................................................................................. 3
2.2.1 Unpacking........................................................................................................... 3
2.2.2 Preparatory Work before Installation.................................................................. 4
2.2.3 Storage Environment.......................................................................................... 4
2.2.4 Operation Environment.......................................................................................4
2.2.5 Starting the Robot in a Low Temperature...........................................................4
2.2.6 Robot Performance Parameters...........................................................................5
2.2.7 Robot Motion Space........................................................................................... 7
2.2.8 Control Cabinet Position.....................................................................................8
2.3 Handling the Robot........................................................................................................... 8
2.3.1 Precautions..........................................................................................................8
2.3.2 Handling the Robot Body............................................................................... 9
2.3.3 Handling the Control Cabinet........................................................................... 11
2.4 Installing the Robot......................................................................................................... 12
2.4.1 Setting up a Safety Fence..................................................................................12

ER10-1600 Quick Operation Manual for Industrial Robot
2.4.2 Installation Procedures......................................................................................12
2.4.3 Ground Mounting..............................................................................................13
2.4.4 Supporter Installation........................................................................................14
2.4.5 Suspended Installation...................................................................................... 14
2.4.6 Installation Environment...................................................................................15
2.4.7 Integrated Connection Interface........................................................................16
Chapter Three Electrical Connection....................................................................................19
3.1 Robot Power Supply........................................................................................................19
3.2 Robot Power Cable, Signal Cable and Ground Wire...................................................... 20
3.3 Definition of Controller Local IO................................................................................... 21
3.4 IO Module Expansion..................................................................................................... 22
3.4.1 Local IO Module Expansion.............................................................................22
3.4.2 Remote IO Module Expansion..........................................................................23
3.5 IO Configuration............................................................................................................. 23
3.5.1 IO Module Update............................................................................................ 24
3.5.2 Remote IO Configuration................................................................................. 24
3.5.3 IO Function IO Configuration.......................................................................... 26
3.5.4 Analog IO Configuration.................................................................................. 32
3.6 Introduction to Emergency Stop......................................................................................34
3.6.1 External Emergency Stop..................................................................................35
3.6.2 Dry Contact of E-stop Output........................................................................... 35

ER10-1600 Quick Operation Manual for Industrial Robot
3.6.3 X12 Safety Door............................................................................................... 35
Chapter Four Teach Pendant Operations.............................................................................. 37
4.1 Teach Pendant..................................................................................................................37
4.1.1 About the Teach Pendant...................................................................................37
4.1.2 Function Keys and Interfaces............................................................................38
4.1.3 How to Hold a Teach Pendant?.........................................................................39
4.2 Power On.........................................................................................................................40
4.3 Jogging............................................................................................................................ 41
4.3.1 What is Jogging?...............................................................................................41
4.3.2 Precautions for Jogging.....................................................................................41
4.3.3 Start Jogging..................................................................................................... 41
4.3.4 Joint Coordinate System-Jogging..................................................................... 42
4.4 Power Off........................................................................................................................ 43
Chapter Five Common Faults and Recommended Solutions............................................... 44

ER10-1600 Quick Operation Manual for Industrial Robot
24
Chapter One Safety
1.1 Safety Instructions
According to the national and local laws and regulations, great importance has been attached to safety
protection in the operation of an industrial robot.
The employer of the robot operator is responsible for the physical damage or property loss in case of
an accident. Therefore it is strongly recommended that an operator should fully understand the contents
described in this manual or elsewhere and abide by the health and safety regulations.
For safety reasons, it is the fundamental requirement to abide by the instructions described in this
manual and other manuals of EFORT. The manual serves as a general introduction to safety regulations
which does not take all the aspects into consideration. Therefore, it is highly important for an operator to
take preventative measures according to the application system and the work environment when operating a
robot.
An operator must read the following information carefully and pay special attention to the safety
measures described.
An EFORT industrial robot user should promise to abide by its national or regional safety laws and
regulations and to make sure that the necessary safety protection equipment is reasonably designed and
correctly installed. An operator should get familiarized with the operation procedures described in the
following documents:
ER Series Robot Safety Manual
Electrical Operation and Maintenance Manual for Small and Medium Payload Industrial Robot
ER Series Robot Operation Manual
Mechanical Operation and Maintenance Manual for ER Series Industrial Robot
Quick Start Manual for ER Industrial Series Robot
The quick start manual includes all the safety descriptions of the robot and controller. The robot
should be well designed and manufactured to ensure that it can enter all the required areas when it is
operated, tested or maintained. The robot should be able to enter the work areas freely if there is a
safety prevention frame. An operator should not be exposed in danger of slipping, stumbling or falling.
1.2 Safety Regulations
Prohibitions
1. Do not change or dissemble the protective equipment or safety equipment arbitrarily.
2. Do not touch a robot in case of waterlogging. Cut off the power and drain off the water.
3. The operation of an industrial robot must be performed by the professionals who have
received sufficient training and guidance and have read this manual thoroughly.
4. The space around the emergency stop equipment must be emptied in case of an
emergency.
5. Improper materials must not be processed with the robot and improper adjustment or
alteration is forbidden.
6. Those who have not been authorized or who have not received any professional training

ER10-1600 Quick Operation Manual for Industrial Robot
2
regarding the operational risks are not allowed to operate the robot.
7. The robot cannot be operated under the following circumstances:
A robot element is exposed.
The safety equipment is disabled.
The fuse and (or) all or any of the mechanical equipment is disabled.
The workpiece is not qualified.
More than one person is operating the robot at the same time.
8. Any violation of the above mentioned regulations is strictly forbidden. Any attempt to
load an unoriginal accessory is forbidden in particular.
9. Do not attempt to move the safety protection equipment. Users are responsible to make
sure that the safety protection equipment is fixed properly and runs effectively as expected.
10. The safety equipment can only be moved in case of maintenance and the standard
maintenance protocols must be followed to ensure the safety of the robot.
Mandatory Measures
1. Ensure that nobody is in the dangerous areas before booting the robot.
2. Ensure that all the operators have received some professional training in operating
industrial robots.
3. A supervisor should constantly monitor the status of the running programs and to make
sure that the safety protection program is effective.
4. Maintain the robot as instructed in the manual and keep the robot clean and tidy.
5. Pack the cleaning and maintaining tools in a suitable tool box. Any worker should wear
personal safety protection equipment.
6. An operator should follow the current health and safety codes.
7. Stop the robot in case of shutdown, suspected damage, malfunction or abnormal noise.
8. Call the police for professional help in case of fire.
9. The door of the control cabinet should always be lock up and the key should be kept by
an electrician.
10. No one is allowed to enter the safety protection area if the power is on.
11. All the suspended safety functions must be restored to normal before the Auto mode is
switched on.
Warning
1. The release of the gravity braking system might lead to falling.
2. Danger might occur when a repairer performs a regular maintenance for the safety
protection equipment. Therefore, caution and preventative measures are advised.

ER10-1600 Quick Operation Manual for Industrial Robot
3
Chapter Two Handling and Installing the Robot
2.1 General Introduction
This chapter explains how to handle and install a small and medium load robot in a workplace. It is
strongly recommended that users should read the Safety Manual of EFORT Industrial Robots carefully and
refer to the first chapter of this manual for the detailed descriptions on safety issues before installation.
2.2 Basic Description
2.2.1 Unpacking
1、Please check whether the packing remains intact or not before unpacking.
2、Please check after unpacking whether all the accessories are complete and whether they match with the
model information on the order list. Contact the supplier if the accessories are not the same as ordered.
Table 2-1 Standard Accessories
Packing List
Name
Model
Qua
ntity
Unit
Remarks
Robot body
ER10-1600
1
PC
Control cabinet
EC-M6
1
PC
Teach pendant and
connection cable
11500010563
1
PC
Control cabinet-robot
power cable
10900021800
1
SET
Standard Length: 8 m
Customized Length:
12m/16m/20m
Control cabinet-robot
signal cable
10900021801
1
SET
Standard Length: 8 m
Customized Length:
12m/16m/20m
Control cabinet-robot
ground wire
10900021958
1
SET
Standard Length: 8 .5 m
Customized Length:
12.5m/16.5m/20.5m.
Control cabinet power
circular connector
10900001237
1
PC
Already installed on the
control cabinet.
10900001229
1
PC
10900001236
1
PC
Circular connector
shield
10900001113
2
PC
Already installed on the
control cabinet and the robot
boy.
10900001122
2
PC
Accessories(bracket,
pin )
\
1
SET
Already installed on the
robot body.
User Manual QR code
\
1
PC
Safety door bridgeware
10900020261
2
PC
Use the bridgeware when in
need.

ER10-1600 Quick Operation Manual for Industrial Robot
4
Note: The packing list contains only the standard articles while the customized articles are not
included.
2.2.2 Preparatory Work before Installation
This section contains the information to be used when the robot is newly installed or reinstalled.
Check the following items before installation:
Table 2-2 Checklist before Installation
1
Check whether the robot is intact.
2
Ensure that the lifting equipment is suitable to carry the robot.
3
Store the robot in a required environment if it is not installed.
4
Ensure the expected working environment meets the standard requirement.
5
Ensure the installing ground meets the standard requirement before handling the
robot.
6
Check the stability before moving the robot.
7
Handle the robot to the installation cite if the checklist is completed.
2.2.3 Storage Environment
The following table describes the permitted storage environment for the robot:
Table 2-3 Robot Storage Environment
Parameters
Value
The lowest environment temperature
-40℃
The highest environment temperature
+55℃
Maximum Humidity
93%RH,Dewing Free(40℃)
2.2.4 Operation Environment
The following table describes the permitted operation environment for the robot.
Table 2-4 Robot Operation Environment
Parameters
Value
The lowest environment temperature
0°C
The highest environment temperature
+45°C
Maximum Humidity
80%RH,Dewing Free(40℃)
2.2.5 Starting the Robot in a Low Temperature
This section explains how to start the robot in low temperature. An operator needs to adjust the heating
rate based on the environment temperature and the running programs. The following table describes the
mapping relations between the working cycles and the speed ratio.
Table 2-5 Robot Working Cycles when Started in a Low Temperature
Working Cycles
Speed Ratio
3
20
5
50
5
80
5
100

ER10-1600 Quick Operation Manual for Industrial Robot
5
2.2.6 Robot Performance Parameters
The following table describes the performance parameters for the robot.
Table 2-6 Robot Performance Parameters
Model
ER10-1600
Motion Type
Joints
Control Axes
6 Axes
Maximum
Motion Speed
Axis J1
170°/s
Axis J2
160°/s
Axis J3
180°/s
Axis J4
330°/s
Axis J5
360°/s
Axis J6
600°/s
Maximum
Motion Rage
Axis J1
±165°
Axis J2
+80°/-135°
Axis J3
+163°/-75°
Axis J4
±180°
Axis J5
±130°
Axis J6
±360°
Maximum Operation Radius
1640mm
Maximum Wrist Load
10 kg
Installation Requirement
Floor Mounted or Suspended
Prevention Rate
IP65(wrist)/ IP54(others)
Repeat Precision
±0.05mm
Robot body Weight
185kg

ER10-1600 Quick Operation Manual for Industrial Robot
6
The following table describes the performance parameters of the control cabinet.
Table 2-7 Performance Parameters of the Control Cabinet
Control Cabinet Type
EC-M6
IP Rate
IP54, Heat radiator:IP30
IO Port
16 digital input ports and 18 digital output ports
(Expansion Supported)
Communication Type
TCP/IP、Modbus-TCP、CAN、ProfibusDP、EtherCAT
Power
3×380V±10%,50/60Hz
Size
W555mm×D560mm×H1165mm
Weight
125kg
Environment
Temperature
0℃~45℃
Environment Humidity
80%RH,Dewing Free(40℃)

ER10-1600 Quick Operation Manual for Industrial Robot
7
2.2.7 Robot Motion Space
Fig. 2-1 Motion Space of ER10-1600 Robot
Note: Fig. 2-1 shows the theoretical maximum motion space of ER10-1600 robot which might be affected
by the way the robot is installed.

ER10-1600 Quick Operation Manual for Industrial Robot
8
2.2.8 Control Cabinet Position
Control Cabinet Size of Small and Medium Load Robots(unit: mm).
Fig. 2-2 Size of Robot Control Cabinet
The ventilation scoop of the control cabinet must not be covered under any circumstance and a
minimum separation space of 150 mm around the cabinet should be guaranteed in order to maximize the
heating radiator efficiency. Ensure that the robot can move freely within operation space. Limit the robot
operation space by means of adjustable stopper or software control if there is any risk of collision.
2.3 Handling the Robot
2.3.1 Precautions
Please read the following precautions carefully before handling the robot.

ER10-1600 Quick Operation Manual for Industrial Robot
9
Caution
The handling must be performed by a professional with lifting and forklifting work
qualifications. Unprofessional performance might lead to flipping or falling
accidents.
Caution
Please follow the procedures described in the manual and check whether the weight
of the robot and the control cabinet exceeds the maximum lifting load before
handling the robot. Operations that do not follow these procedures might lead to
flipping or falling accidents.
Caution
Please protect the cables when handling the robot and the control cabinet. Besides,
the cables should be covered by a shield to prevent from accidental damage.
2.3.2 Handling the Robot Body
1. Method One
Position the robot as shown in Fig. 2-3/4. Install 4 separate ring screws of M 10 type to the robot body
and lift it with four separate steel cables. The recommended length of the cables should be longer than 3
meters and rubber hoses should be placed on the cables to prevent from direct contact with the robot body.
Note: Neither the end effector nor the robot arm has any tool in Fig. 2-3 and 2-4. Caution is advised if
a tool is installed to the end effector or robot arm.
2. Method Two
Adjust the robot position with the parameters shown in table 2-8 before handling the robot with a
forklift.
Table 2-8 Joint Angles in Forklift Handling
Model
Position
J1
J2
J3
J4
J5
J6
ER10-1600
Joint Angles /°
0
+78
-72.5
﹢90
-90
0

ER10-1600 Quick Operation Manual for Industrial Robot
10
Fig. 2-3 Lifting Sketch Map
Fig. 2-4 Forklifting Sketch Map

ER10-1600 Quick Operation Manual for Industrial Robot
11
Attention
Corresponding Fixtures must be used in handling the robot.
Ensure that no pressure is put on the robot arm or electric motor if neither lifting nor
forklifting is applied.
Remove the fixtures and rubber protection after installation.
Store the fixtures in a safe place for future handling.
2.3.3 Handling the Control Cabinet
1. Method One
The 4-castered mobile control cabinet is recommended which has 2 universal casters and 2 rigid
casters. Push the control cabinet to the desired position and lock the universal casters. Ensure the control
cabinet is well balanced and not stacked upon in the process of transportation.
2. Method Two
Position the robot as shown in Fig. 2-5. Install 2 separate ring screws of M 10 type on the top and lift
the cabinet with 2 separate soft cables. The recommended length of the cables should be longer than 2
meters and rubber hoses should be placed on the cables to prevent from direct contact with the robot body.
Fig. 2-5 Lifting Sketch Map for Robot Control Cabinet
The control cabinet weighs
125kg
Lift with 2 soft cables bearing minimum
load of 100 kg. Steel cables are forbidden.

ER10-1600 Quick Operation Manual for Industrial Robot
12
2.4 Installing the Robot
Danger
1. Set up a safety fence to prevent from accidents leading to physical injury or property
damage. The robot should be placed in a position from which the end tool or the sharp end
of a workpiece can never reach the safety fence even if the robot arm is extended to its
reach limit.
2. Neither the power should be switched on nor should any operation be performed until
the robot has been properly fixed. Otherwise, accidents such as flipping, physical injury or
property damage might occur.
3. The ceiling or wall should be strong enough to bear the weight of the robot if it is
intended to be installed to a ceiling or a wall and the relevant emergency countermeasures
should be well-planned. Otherwise, accidents such as flipping, physical injury or property
damage might occur.
2.4.1 Setting up a Safety Fence
The user of the robot should set up a safety fence according to the National Standards of the People’s
Republic of China on Robots and robotic devices―Safety requirements for industrial robots
(GB11291.2-2013) . It is stated in section 5.4 that the design and integration of a robot should reduce the
possibility of an operator being exposed to danger and a user should build up a safe space around a robot
taking the position and layout of the robot and the foreseeable danger into serious consideration. Section
5.10 requires that a user should set up the protection equipment on the entrance to the dangerous area if the
risk of danger cannot be eliminated or reduced.
Therefore, please set up a safety fence with safety interlock to prevent from physical injury or property
damage.
Note: The GB11291.2-2013 standard is equivalent to the ISO 10218-2:2011 standard.
2.4.2 Installation Procedures
The fixing of the robot base and the ground should be able to bear the dynamic load in robot
acceleration and deceleration and the fixture static weight. In addition, the robot might be deformed or its
performance is affected if the ground is uneven. Ensure that the ground flatness rate is within 0.5 mm. Fig.
2-6 illustrates the size of base interface.

ER10-1600 Quick Operation Manual for Industrial Robot
13
Fig. 2-6 Size of Base Interface of ER10-1600 Robot
2.4.3 Ground Mounting
The strength rate and maximum load of the concrete ground should meet the requirements of relevant
quality regulations. The thickness of the concrete ground should be no less than the depth of the buried
chemical bolts and the concrete ground should cover the entire base area to ensure the safety and reliability
of installation. The quality of the concrete should meet the requirements of National Code for Design of
Concrete Structures (GB50010-2010 2015 edition) and the Standard for Test Method of Mechanical
Properties of on Ordinary Concrete (GB/T50081-2002) and the strength rate should be 20 MPa or 25 Mpa.
Table 2-9 Fixing Accessories for the Robot
Name
Dimension
Quantity
Floor
thickness≥30mm
1
Reference Coverage
(600mm×600mm)
Chemical Bolt
M16 or larger,strength rate≥4.8
8
Fixing Screw
M16×45,strength rate =12.9
4
Cylindrical Pin
with Internal
Thread
M12x45
2
Fix the floor on the concrete ground first with eight M16 type chemical bolts. The recommended floor
should be thicker than 30 mm. Fix the base on the floor with four M16 type socket cap screws whose length
is 1.5 times of the nominal diameter. The M12 type cylindrical pins with internal thread are installed on the
socket cap screws enhance the stability. The installing procedures for the floor and base are depicted in Fig.
2-7.
4-M10 screws for lifting

ER10-1600 Quick Operation Manual for Industrial Robot
14
Fig. 2-7 Floor and Robot Base Installation
2.4.4 Supporter Installation
The fixing procedures are the same as those described in ground mounting if the height of the
supporter is less than 600 mm. Install the supporter first and then fix the robot base to the supporter. The
connection strength and reliability between the supporter and the ground needs to be strictly verified if the
height of the supporter is more than 600 mm.
Caution
Increase the size, number and buried depth of chemical bolts for greater stability
and reliability.
Increase the concrete strength to ensure it is greater than that required by the
chemical bolts.
2.4.5 Suspended Installation
The following precautions must be taken to ensure the safety of suspended installation.
1. Install an anti-fall safety device as shown in Fig. 2-8
2. The strength rate of the connection bolts should be greater than 12.9 and the tightening torque
should match with the pre-tightening force expectations.
Caution
Accidents might occur if the fixing bolts for the robot base are either too long or too
short. The connection strength of chemical bolts is decided by the strength of the
concrete ground. There are two ways to strengthen the connection strength.
1. Increase the number of the chemical bolts.
2. Increase the buried depth of the chemical bolts.
Robot base
Chemical bolts
(M16*200 or above)
8 chemical bolts (M16 or above)
Floor depth: 30mm
Ground

ER10-1600 Quick Operation Manual for Industrial Robot
15
Fig. 2-8 Suspended Installation
2.4.6 Installation Environment
The robot should be transported, stored and operated in a suitable environment and its performance
should meet the general requirements.
Table 2-10 Robot Environment Requirement Description
Robot Environment Requirement Description
Conditions
Working
Transportation and Storage
Environment
Temperature
0-45℃
-40~55 ℃
Humidity Rate
≤80%(40℃)
≤93%(40℃)
Atmospheric
Pressure
86~106 kPa
Vibration
Less than 0.5G,4.9m/s2
Others
Without corrosive gas
Note: Please contact the service department for robot protective covers if it is installed in an
environment full of dust, cutting oil and strong vibration.
Anti-fall safety device
Anti-fall safety device
Other manuals for ER10-1600
1
Table of contents
Other EFORT Robotics manuals
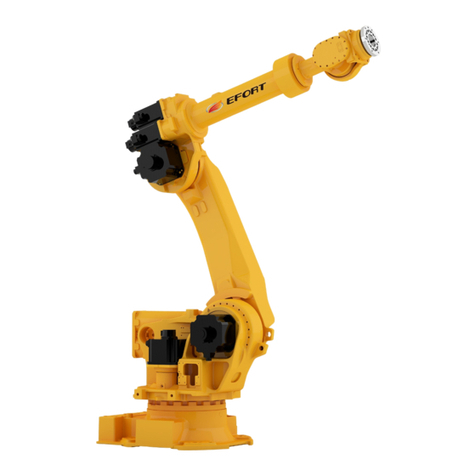
EFORT
EFORT ER210-2700 User manual
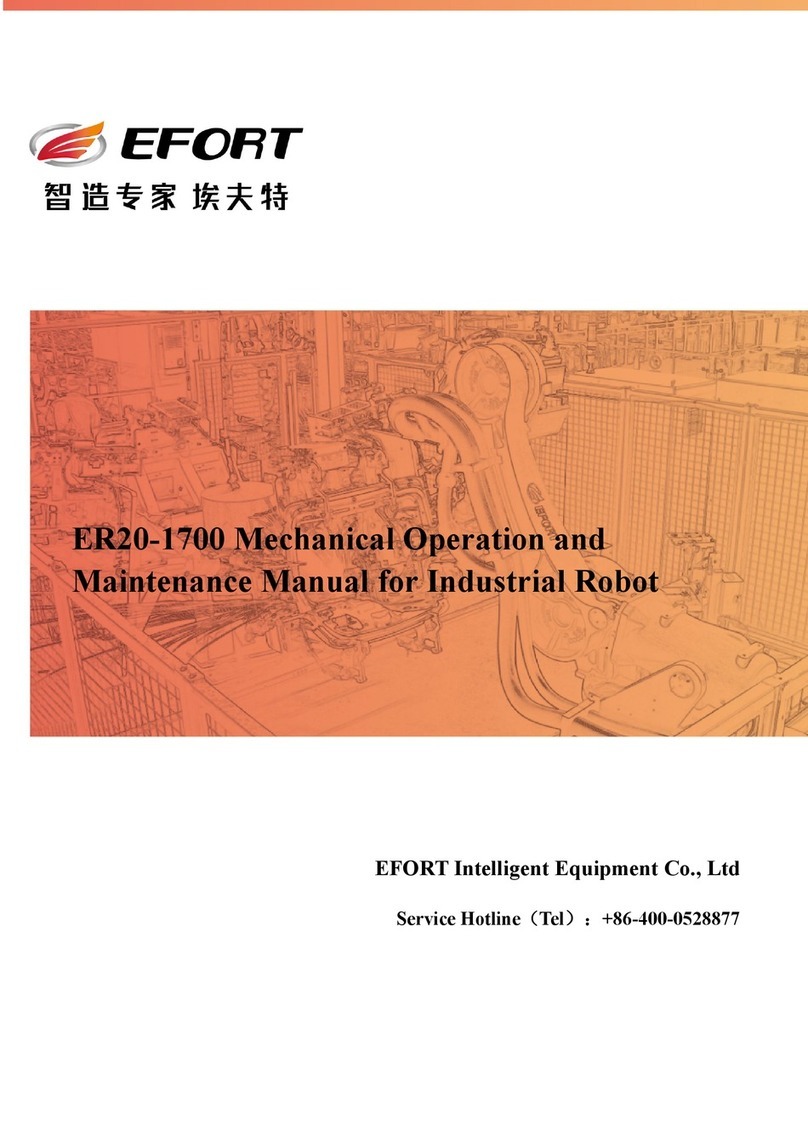
EFORT
EFORT ER20-1700 User manual

EFORT
EFORT ER15-1400 User manual
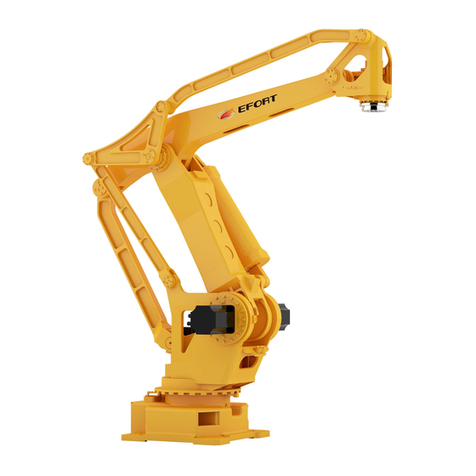
EFORT
EFORT ER180-4-3200 User manual

EFORT
EFORT ER15-1400 User manual
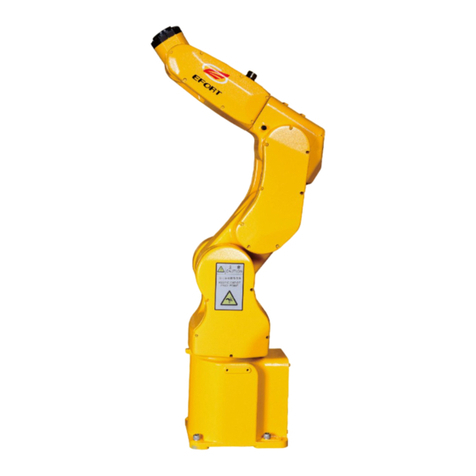
EFORT
EFORT ER3-600 User manual
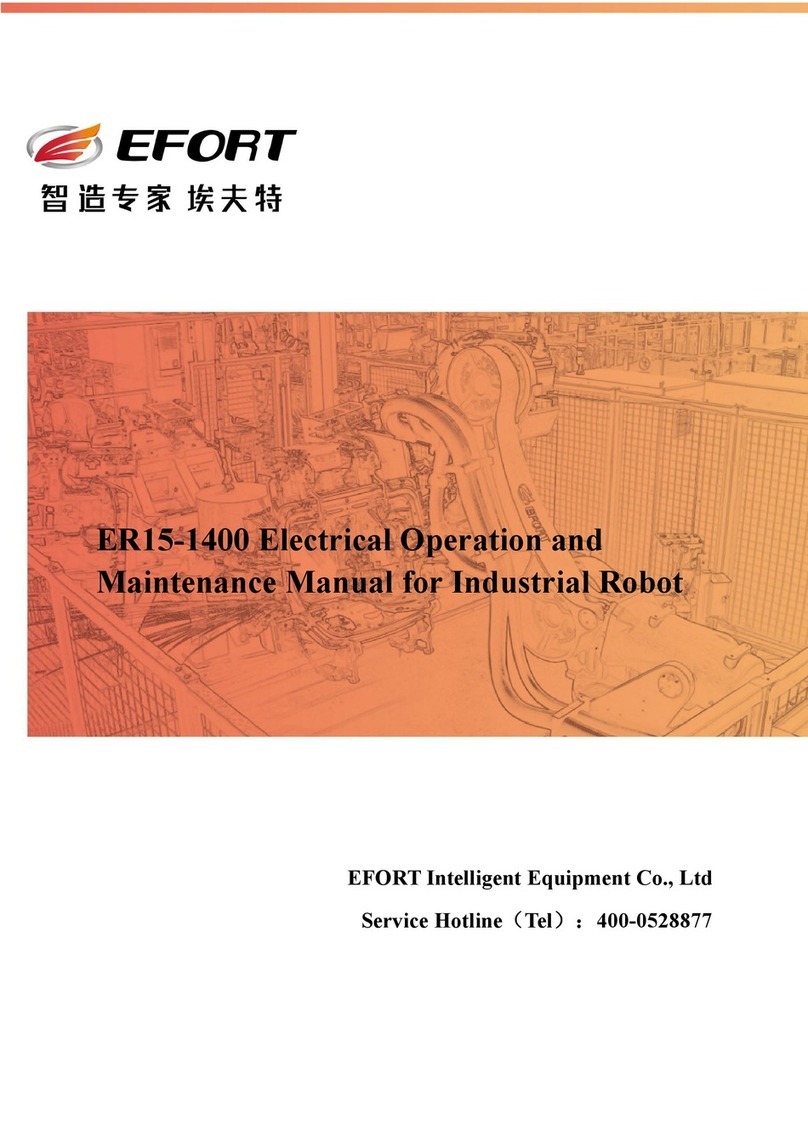
EFORT
EFORT ER15-1400 User manual

EFORT
EFORT ER15-4-1600 User manual
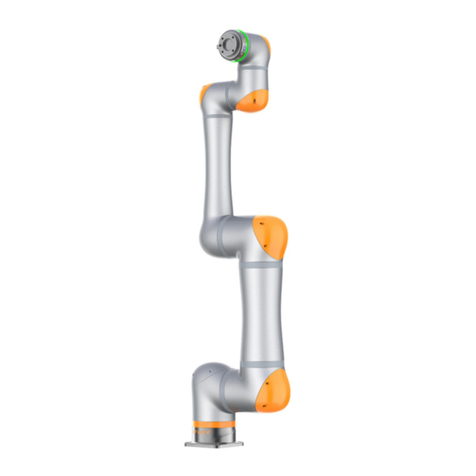
EFORT
EFORT ECR5 User manual
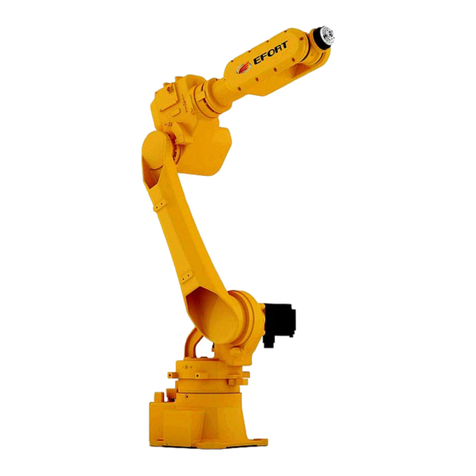
EFORT
EFORT ER20-1700 User manual
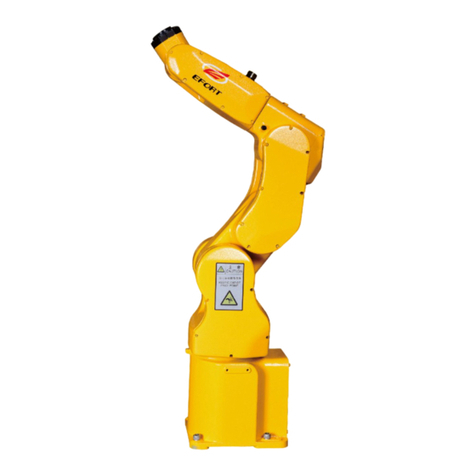
EFORT
EFORT ER3-600 User manual
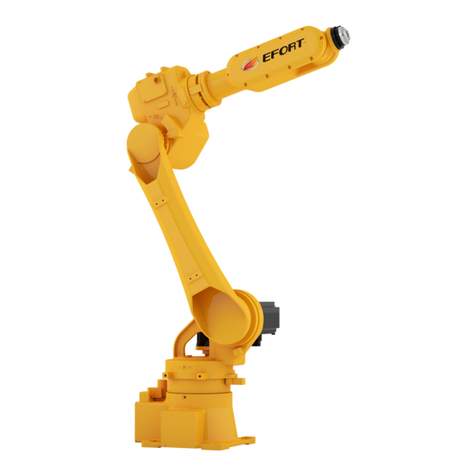
EFORT
EFORT ER20-1100 User manual
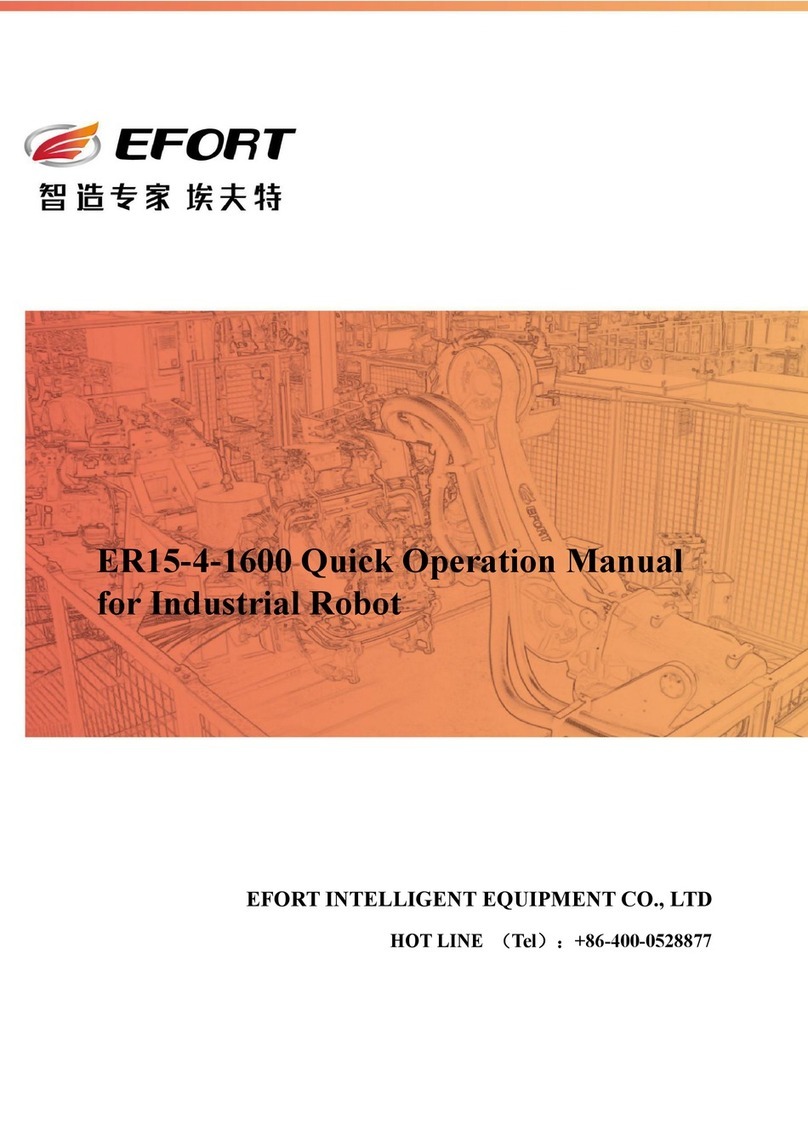
EFORT
EFORT ER15-4-1600 User manual
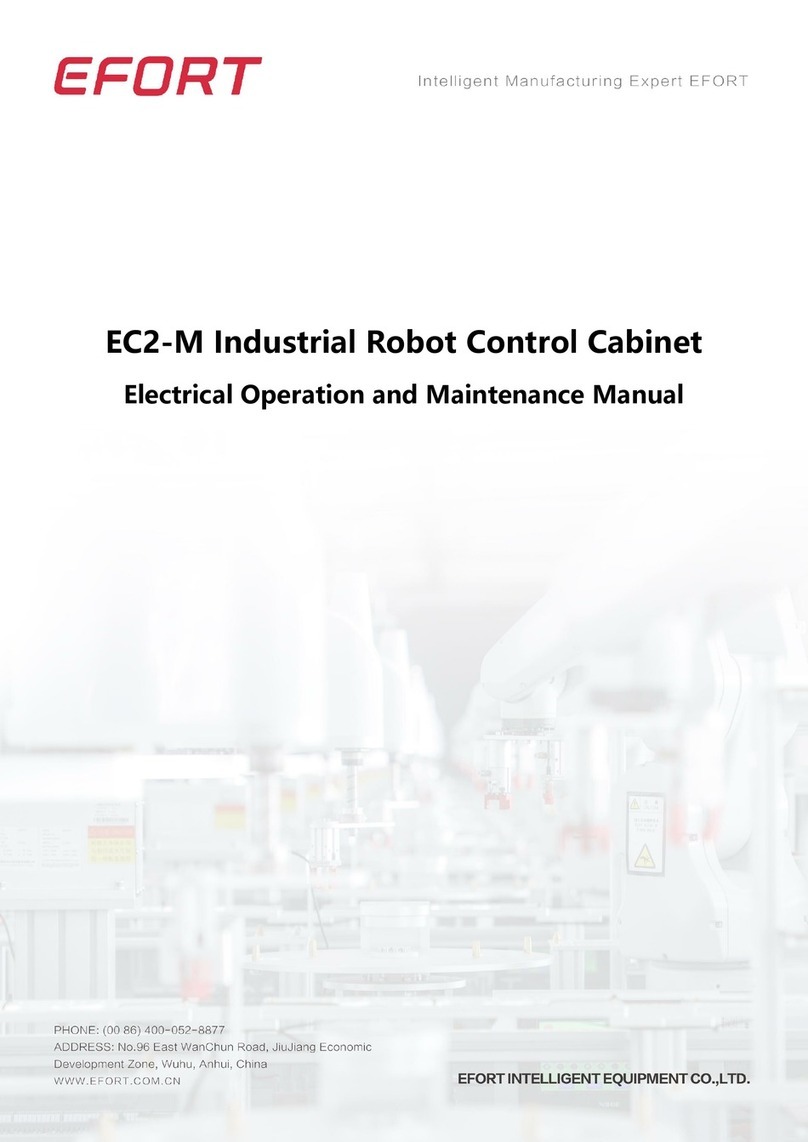
EFORT
EFORT EC2-M User manual
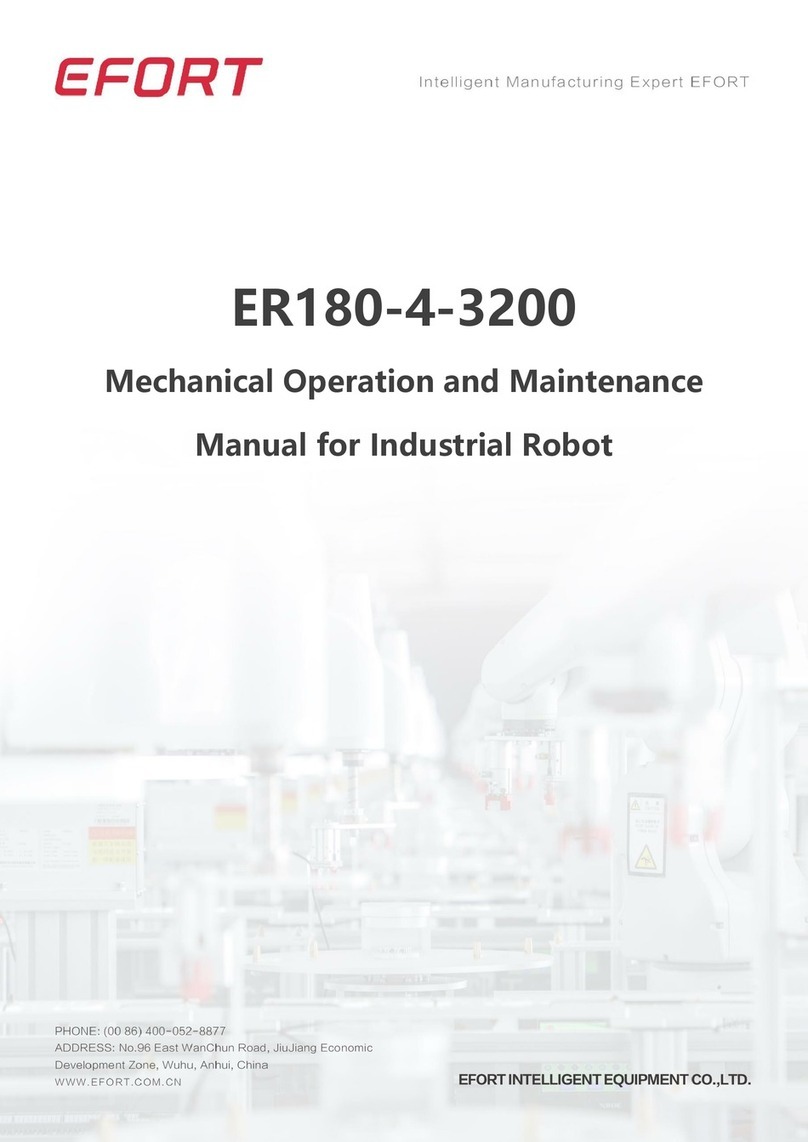
EFORT
EFORT ER130-4-2800 User manual
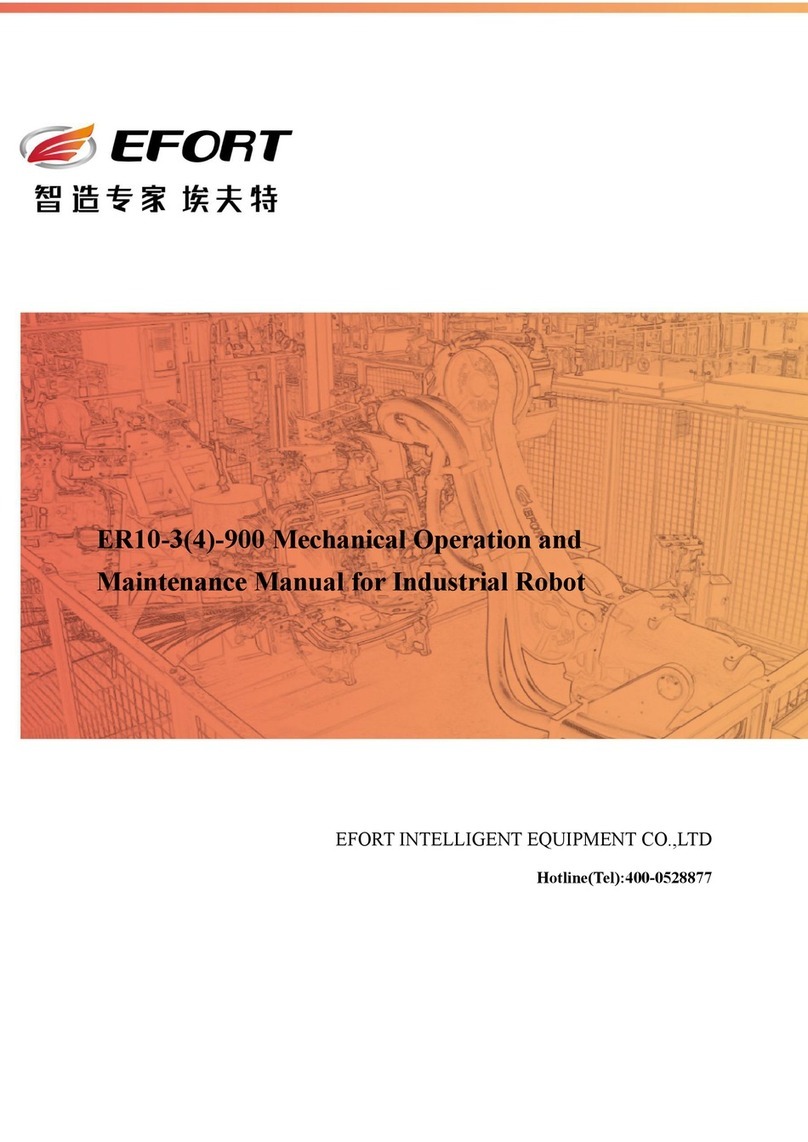
EFORT
EFORT ER10-3-900 User manual
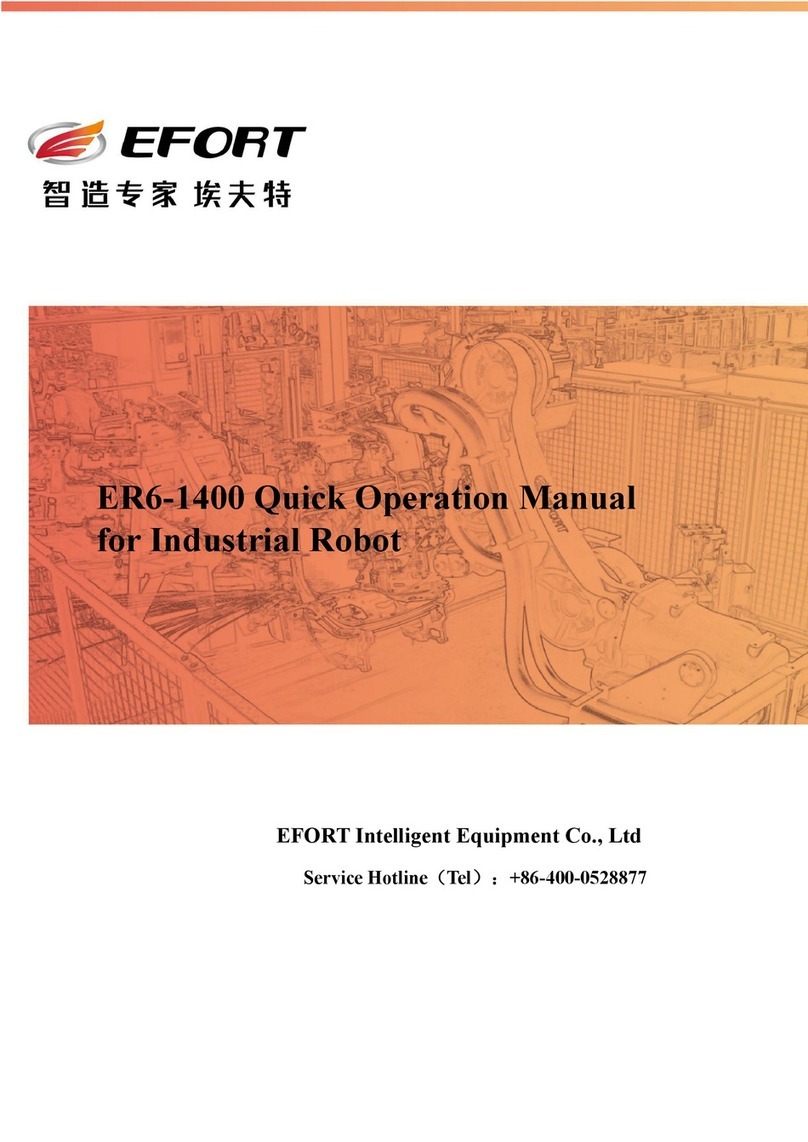
EFORT
EFORT ER6-1400 User manual

EFORT
EFORT ER6-2000 User manual

EFORT
EFORT ER180-4-3200 User manual
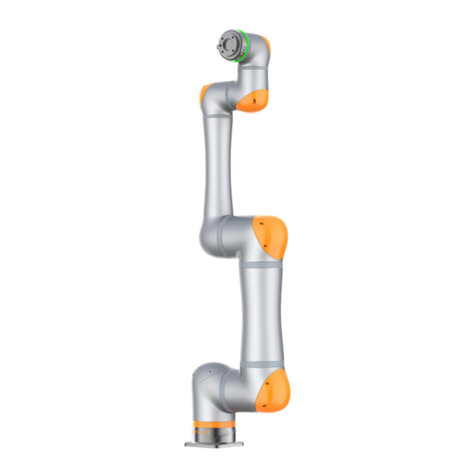
EFORT
EFORT ECR5 Instruction manual