Eraser MMC100 User manual

The Eraser Company, Inc.
POBox4961/OlivaDrive
Syracuse,NY13221,USA
Phone:(315)454-3237/Fax:(315)454-3090
Website:www.eraser.com
E-mail:info@eraser.com
Eraser International Ltd.
UnitM,HuntingGate
AndoverSP103SJ,England
Phone:(01264) 351347/Fax:(01264)355030
Website:www.eraser-international.com
Email:[email protected]
Service and All Spare Parts Available
Operating Manual
Please Read Before Operating Unit
Always Moving Forward
Model MMC100 Multi-Material Cutter

Eraser Company Inc. • Syracuse, NY USA • Ph: 315-454-3237 • info@eraser.com • www.eraser.com • Fax 315-454-3090
Eraser International Ltd. • England • Ph:(01264)351347 • [email protected] • www.eraser-international.com • Fax (01264)355030
MODEL MMC100
MULTI-MATERIAL CUTTER
SPECIFICATIONS
Maximum Cut Length...........9,999,999.00in./mm
Minimum Cut Length..................0.100”(2.54mm)
Maximum Material Size
Tubing........0.625”(5/8”)OD(15.875mmø)
Flat Material........3.94”(100.076mm) wide
Wire..........8AWG(3.25mmø)solidcopper
Tolerances........................................1% or better
dependent on material and feed
Feed Rates..................Threeselectablefeedrates
Feed Rate 1........9.5”/sec.(241.3mm/sec.)
Feed Rate 2......16.5”/sec.(419.1mm/sec.)
Feed Rate 3........31”/sec. (787.4mm/sec.)
Production Rates
Batching.............Upto10programmablebatches.
Blades...........................Hardenedandgroundtool
steel guillotine and anvil blades.
DecibelRating..........................................65dB(A)
ORDERING INFORMATION
AR0371(MMC100)...Multi-materialcutter115V60Hz
AR0372 (MMC100).................Multi-materialcutter
European plug 220/240V 50Hz
AR0373 (MMC100).................Multi-materialcutter
UK plug 220/240V 50Hz
AR3801(DE400)................Optionalverticaldereeler
AR0170(DE700)....Optionalcompensationdereeler
IR1205......................Replacementguillotine blade
IR1203.............................Replacementanvilblade
Representative rates
Size 123
4" 4,045 5,900 7,200
10" 2,365 4,290 5,215
20" 1,395 3,000 3,530
Feed Rate
Production Rates (PCs/hr.)

SET-UP
The MMC100 is supplied with one fixed station-
ary blade and one moveable blade. Also included
are three Allen wrenches; 1/8”, 3/16” & 9/64”.
Caution: The MMC100 comes with the blades
completely installed. These blades are intended
for use on wire and tubing and are extremely
sharp. Caution must be used when removing or
installing either of these blades.
Placethe unit ona sturdy workbenchwith the right
side exit chute even with the right side of the
bench. Short and long cut lengths will drop out
the right side of the exit chute. Material collection
bins can be placed to collect the cut material as it
exits. If using the DE700 (or any other tensioning
de-reeler) place the de-reeler to the left of the unit
at least 24” from the entrance. Refer to the de-
reeler’s operating instructions for further set up
details.
Insert the power cord into the IEC connector. Plug
the unit into the appropriate power supply using
thecorrectplugfor the unit purchased.Useaprop-
erly grounded mains supply. The American plug
is for use on 110/120V 60Hz mains supply. The
European and United Kingdom plugs are for 220/
240V50Hzmainssupply.Connectclean,dry, com-
pressed air at 90 P.S.I..
Caution: Environmental conditions for proper op-
eration should be 50° F-104° F (10° C-40° C) and
30-75% relative humidity. The MMC100 should be
operatedinawell-ventilated open workspace.This
machine may be effected by outside environmen-
tal disturbances. The unit is rated for continuous
use and is protected by one fuse located in the
IEC connector.
Caution: Safetyglasses or othersuitableeye pro-
tection should be worn when operating this unit.
OPERATION
Place the material to be cut on the de-reeler. Turn
the MMC100 on using the I/O switch on the side
of the unit. Do not turn the unit on and off repeat-
edly without waiting 5 seconds for the controller to
removeinformation correctly. Removing theguard
during a run is not recommended. It will stop the
stepper motor and the piece being processed will
not be of the correct length. If cutting long pieces
of material and the guard is opened and closed
before the end of the cycle the stepper motor will
resume feeding material. This piece will not be the
correct length and should be discarded.
Open the belt feed by turning the switch counter-
clockwise to disengage the belt feed. Rotate the
knobs on the front of the unit to open the guides
wide enough to accommodate the material being
cut. Feed the material through the guides until it
protrudes past the blades on the right side of the
unit. Make certain the material is between the two
sets of guides located on the left and right side of
the belt feed.
Turn the switch clockwise to close the belt feed
and engage the upper belt. Make certain the unit
is at the beginning of the batch. Press the cut
button twice to zero the machine. NOTE: The guil-
lotine blade will cut the material off at the blade.
When using the JOG or CUT keys this will place
the operator in the manual mode. In the manual
mode “MANUALC” will be displayed in the STA-
TUS area. This is a continuous jog function and
the length displayed is the actual length of mate-
rial moved. Pressing the CUT key will cut off the
lengthof material justtransported. Press theESC/
PAUSE key to return to the batch screen. If the
material does not feed it can be inserted manually
with the belt feed open.
The MMC100 is equipped with an out of material
sensor. From the factory this option is disabled. To
enable this option, use the following procedure.
From the “SELECT BATCH” screen, hit the edit
key twice. The display will read “WIRE SENSOR
1=Y0=N”.Select 1 if youwouldlike to use thesen-
sor and 0 if you would like to disable the sensor.
Afterselecting your option,press the <ENTER>or
<ESCAPE> key to return you to the “SELECT
BATCH”screen.Theunitisnowreadyforprogram-
ming.
Model MMC MULTI-MATERIAL CUTTER
OPERATINGINSTRUCTIONS

PROGRAMMING
When the unit is turned on the controller will report
that it is initializing and display The Eraser Co.
MMC100. The controller will request that you se-
lect a batch. Select a batch from 1-10. Numbers
other than 1-10 will not be accepted. Inputs that
are not recognized will emit a beep. Press ENTER
or RUN to continue. The functions in figure 1 will
be displayed on the keypad display.
BATCH Units LENGTH
IN/MM
• • • • ••••••••••
•••••• • •••••••
STATUS FEED RATE QUANTITY
To begin the run cycle press RUN again only if all
the information has been previously inputted for
the batch. If a variable is entered with a value of 0
an error will cause the controller to beep. Press
ENTER after each inputted value. This will high-
light the next variable to be inputted. After press-
ing ENTER IN/MM will be blinking on the display.
Pressing the + or – keys will change the display
from IN to MM or MM to IN. Press ENTER and
input the length needed. This has a total of 10
characters, one of which is reserved for a deci-
malandtwo for zeroes(9999999.00”).Afterpress-
ing ENTER select a feed rate of 1-3. One is the
slowest at 9.5”/sec and 3 is the fastest at 31”/sec.
Itisadvisedtostartwiththelowest feed rate, check
the results and then adjust as necessary. The next
variable to be entered is QUANTITY. The maxi-
mum allowed is 9999999 pieces. Enter the quan-
tity and press ENTER or RUN. Pressing ENTER
will display “READY” in the status and pressing
run will start the run cycle immediately. Pressing
ENTER will cycle the operator through the vari-
ables. During the run cycle the quantity will count
down until 0 is reached. After reaching 0 “END”
will be displayed. If it is necessary to pause the
unit during a run press ESC/PAUSE. After press-
ingthePAUSEkey“PAUSE”will be displayed.The
amountof material transportedbefore pausing will
bedisplayedunder LENGTH. PressingESCagain
will abort the program. Pressing RUN will display
“READY”andpressingRUNagainwillcontinuethe
run. At the end of the run “END” will be displayed.
Pressing RUN will put the operator back at the
BATCH screen and pressing RUN will start the
same batch again or the operator may change the
batch at this time.
POWER FAILURE
In case of power failure the MMC100 will be
reinitialized and should not start unexpectedly. All
parameters stored in a batch program will remain
inmemory.Afuseanda line filter locatedintheIEC
connector protect the controller.
BLADE REPLACEMENT
Caution: Always remove compressed air sup-
ply and unplug electrical supply when replac-
ing blades or servicing the unit.
Note:Wheneverabladeorbothbladesarereplaced
follow the adjustment procedure.
1. Remove guard and chute assembly by remov-
ing the four thumbscrews.
2. Manually raise the moveable blade to its upper
most position, if it is not currently there, by forcing
the upper blade holders up.
3. Using the 9/64”Allen wrench provided, remove
the fixed lower blade by removing the three cap
screws securing it to the lower blade holder.
4. Remove the cap screw securing the upper
moveable blade to the right upper blade holder us-
ing the 3/16” Allen wrench provided. Rotate the
upperbladeholderblock out to revealthethreaded
holein the blade (ifthe blade holderblockdoes not
rotate easily, try sliding it up and down while rotat-
ing). Insert the screw that was just removed into
thethreaded hole about3full turns. Usethis screw
tosupporttheblade while removing thescrewfrom
theleftupperblade holder (see SpecificationPhoto
1).Rotatethe left upperbladeholder out and insert
the removed screw back into the threaded hole.
Caution: the blade is now free and may fall if
not supported. Use the screws in the blade as
handlesto safely removetheblade (see Specifica-
tion Photo 2). Move the blade back until it disen-
gages from the knuckle key. Then move the blade
down and out of the machine.
Figure 1

5. Replace the lower blade by securing it with the
three fasteners using the 9/64” Allen wrench pro-
vided.
6. Replace the upper blade by inserting the cap
screws into the threaded holes and using them as
handles to raise the blade up into the machine so
that it engages the knuckle key. Remove the left
screw and swing the blade holder over the blade
andinsertthe screw into theholder. Snug thescrew
with the 3/16” Allen wrench. DO NOT TIGHTEN.
Remove the screw from the right side of the blade
and swing the right blade holder over the blade.
Insert the screw into the hole and tighten with the
3/16” Allen wrench provided. Tighten the left side
blade holder. Make sure upper blade is centered
with the lower blade.
7. Whenever a blade or both blades are replaced
follow the adjustment procedure.
BLADE ADJUSTMENT
1. Tip the machine onto its backside and loosen
the two large screws on the bottom of the ma-
chine with the 3/16” Allen wrench (see Specifica-
tion Photo 4).
2. Tip the machine back onto its feet and loosen
the two tension screws in the bottom of the lower
blade holder with the 3/16”Allen wrench. Push the
lower blade holder towards the center of the ma-
chine.
3. Lower the upper blade so that only the leading
edge of the upper blade covers the lower blade.
Caution: ensure the upper blade does not hit
the top of the lower blade as this will damage
the upper blade.
4. Tighten the tension screw in the lower blade
holder so the lower blade comes in contact with
the upper blade. Raise the upper blade and slowly
loweritdownagaintoensure the upper blade does
not come down on top of the lower blade.
5. Lower the upper blade all the way down and
tighten the left tension screw on the lower blade
holder until the lower blade is snug against the up-
perblade.
6. Raise the upper blade and slowly lower it back
down. There should be a smooth shearing action
like a pair of scissors. If not, repeat steps 3 thru 5
again until you achieve a smooth shearing action.
7. Tip the machine onto its backside and tighten
the two screws securing the lower blade holder
with the 3/16”Allen wrench.
8. Return the machine to an upright position and
recheck the shearing action of the blades.
9. Return the machine to service by installing the
safety guard, air supply and power.
GROUND LOCATION
This protective Earth ground la-
bel is located inside the hous-
ingbeside the ground wire. This
wire is connected to the Power
Supply Cable and is wired back
through the Mains supply to
ground.
CAUTION LABEL
Refer to the operating instruc-
tionsbefore using thisunit. High
voltage is inside this unit and
power must be disconnected
before servicing.
ON/OFF LABEL
This is the ON/OFF switch.
Press I for on and press O for
off. This switch is also the anti-
start switch. In case of power
outage,thisswitchmustbereset
for the unit to operate.
CE MARKING
Indicatescompliancewithall ap-
plicable EU directives.

WARNING
DO NOT OPERATE TOOL UNTIL YOU HAVE READ
THOROUGHLY,AND UNDERSTAND COMPLETELY,
ALL INSTRUCTIONS, RULES, ETC. ON THIS PAGE,
AND IN THE OPERATING MANUAL. WHEN USING
ELECTRIC TOOLS, BASIC SAFETY PRECAUTIONS
SHOULDALWAYSBE FOLLOWED TOREDUCE RISK
OF FIRE, ELECTRIC SHOCK, AND PERSONAL IN-
JURY, INCLUDING THE FOLLOWING:
GROUNDINGINSTRUCTIONS
In the event of a malfunction or breakdown, grounding
providesa path of least resistancefor electriccurrent to
reduce the risk of electric shock. This tool is equipped
withanelectriccordhavinganequipment-groundingcon-
ductorand agrounding plug. Theplug mustbe plugged
into a matching outlet that is properly installed and
grounded in accordance with all local codes and ordi-
nances.
Do not modify the plug provided – if it will not fit the out-
let,have theproper outletinstalled bya qualifiedelectri-
cian.
Improperconnectionoftheequipment-groundingconduc-
tor can result in a risk of electric shock. The green con-
ductor with or without yellow stripes is the equipment-
groundingconductor.If repairor replacementoftheelec-
tric cord or plug is necessary, do not connect the equip-
ment-groundingconductor toa live terminal.
Checkwith aqualified electricianor service personnelif
thegroundinginstructionsarenotcompletelyunderstood,
orif in doubtas towhether thetoolis properlygrounded.
Useonly3-wireextensioncordsthathave3-prongground-
ing plugs and 3-pole receptacles that accept the tool’s
plug. Repair or replace damaged or worn cord immedi-
ately.
GENERALINSTRUCTIONS
REMOVEADJUSTINGKEYS AND WRENCHES. Form
habitofcheckingtoseethatkeysand adjusting wrenches
areremovedfrom toolbeforeturning on.
KEEP WORK AREA CLEAN. Cluttered areas and
benchesinvite accidents.
DON’TUSE IN DANGEROUS ENVIRONMENTS.Don’t
use power tools in damp or wet locations, or expose
them to rain. Keep work area well lighted.
ALWAYS USE SAFETY GLASSES. Everyday eye-
glassesonlyhave impactresistantlenses; they areNOT
safety glasses. Also use face or dust mask if cutting
operation is dusty.
WEAR PROPER APPAREL. Do not wear loose cloth-
ing, gloves, neckties, rings, bracelets, or other jewelry
thatmight getcaught inmoving parts. Nonslipfootwear
isrecommended. Wear protectivehair coveringto con-
tainlonghair.
DON’TOVERREACH.Keepproperfooting and balance
at all times.
MAINTAIN TOOLS WITH CARE. Keeptools sharpand
clean for best performance and to reduce the risk of in-
jury. Follow instructions for lubricating and changing
accessories.
DISCONNECT TOOL beforeservicing; whenchanging
accessories, such as blades, wheels, cutters, and like.
USERECOMMENDED ACCESSORIES.Consulttheop-
eratingmanual forrecommended accessories.The use
ofimproper accessories maycause riskof injury toper-
sons.
CHECK DAMAGED PARTS. Before further use of the
tool, a guard or other part that is damaged should be
carefully checked to determine that it will operate prop-
erly and perform its intended function. Check for align-
mentofmoving parts,bindingof moving parts,breakage
of parts, mounting, and any other conditions that may
affectitsoperation.Aguardor otherpartthatisdamaged
shouldbe properly repairedor replaced.
DONOT EXCEED THEMAXIMUM MATERIALSPECI-
FICATIONS.
DO NOT OPERATED UNIT WITHOUT GUARDS IN
PLACEOR GUARDS NOTIN WORKING ORDER.
DO NOT PERFORM MAINTENANCE OR ADJUST-
MENTS WITH POWER ON.
DO NOT PLACE FINGERS OR APPENDAGES IN OR
NEAROPENINGS IN GUARDS.
DO NOT RUN UNIT WITH INCORRECT LINE VOLT-
AGE.REFERTO LABEL PLACED OVER I/O SWITCH.
DONOTALLOWUNTRAINEDORUNQUALIFIEDPER-
SONNELTO OPERATE UNIT.
DO NOT DEFEAT ANYOF THE SAFETY FEATURES
DESIGNEDINTOTHE UNIT.
IMPORTANT SAFETY INSTRUCTIONS
READ ALL INSTRUCTIONS
IMPORTANT: No liability will be incurred by The
Eraser Co. for injury, death, or property damage
caused by a product which has been set up, oper-
ated, and/or installed contrary to Eraser's written
instruction manual, or which as been subjected to
misuse,negligence, or accident,or which has been
repaired or altered by anyone other than Eraser, or
which has been used in a manner or for a purpose
for which the product was not designed.

Right Blade
Holder
Knuckle with Key
Left Tension
Screw
Right Tension
Screw
Lower Blade
Holder
Upper
Blade
Replace screw to use as a
handle (repeat for left side)
Left Blade
Holder
SPECIFICATIONS
Specification Photo 1
Specification Photo 2 Specification Photo 3
Knuckle with Key
Firmly grasp both cap screws and push blade
off of the knuckle key, lower blade and
remove from machine.

Lower Blade
Holder Screws
Specification Photo 4
Eraser International Ltd.
UnitM, Hunting Gate
Andover SP10 3SJ, England
Phone: (01264) 351347 / Fax: (01264) 355030
Website: www.eraser-international.com
Email: [email protected]
The Eraser Company, Inc.
PO Box 4961/ Oliva Drive
Syracuse, NY 13221, USA
Phone: (315) 454-3237 / Fax: (315) 454-3090
Website: www.eraser.com
E-mail: info@eraser.com
IR1266
REV9/03
Table of contents
Other Eraser Cutter manuals
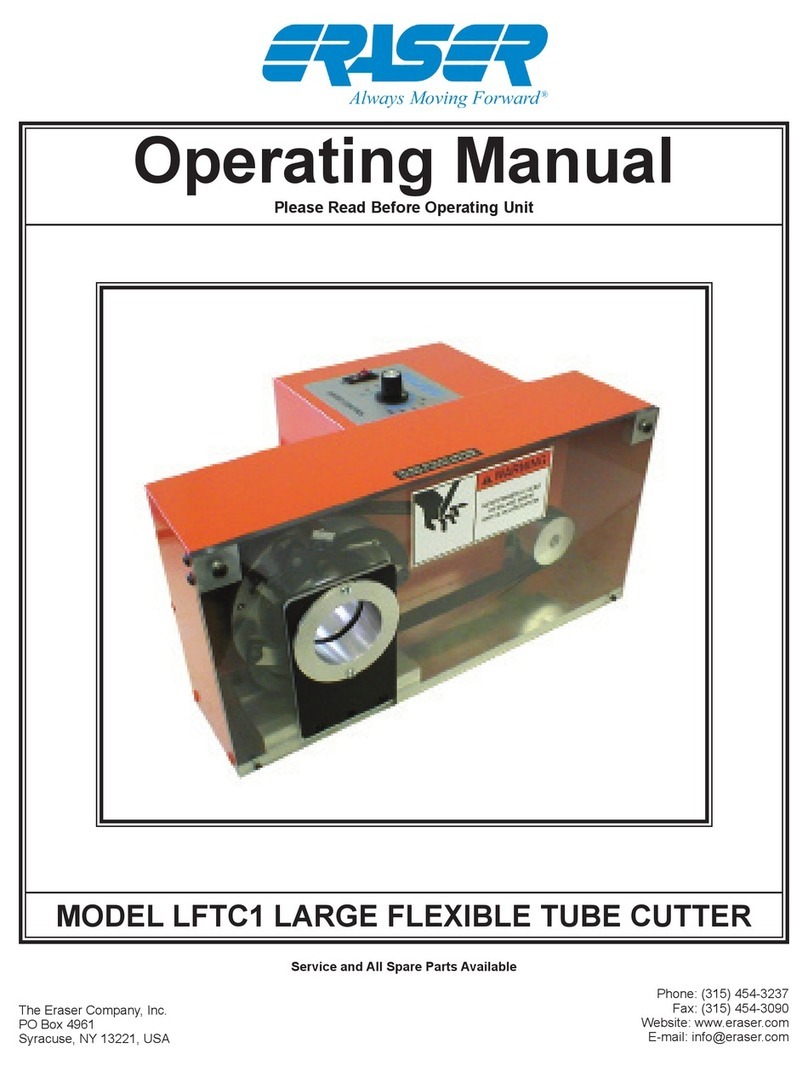
Eraser
Eraser LFTC1 User manual

Eraser
Eraser CCB100 User manual
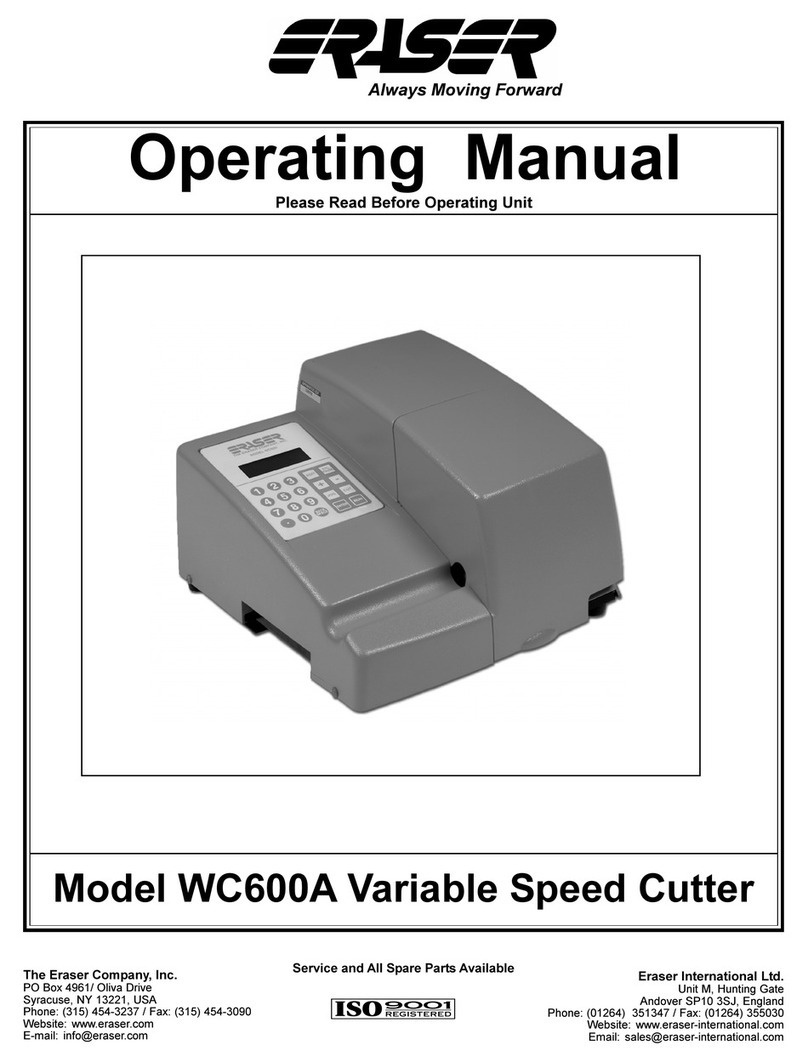
Eraser
Eraser WC600A User manual
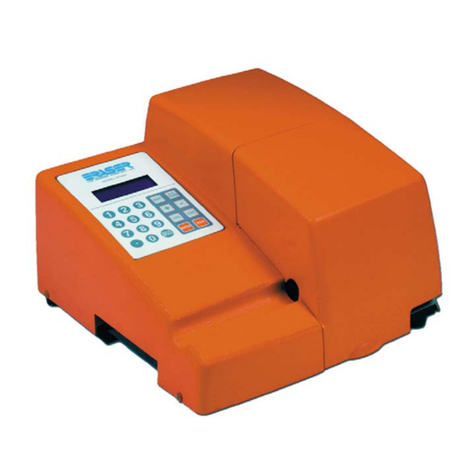
Eraser
Eraser WC601B User manual
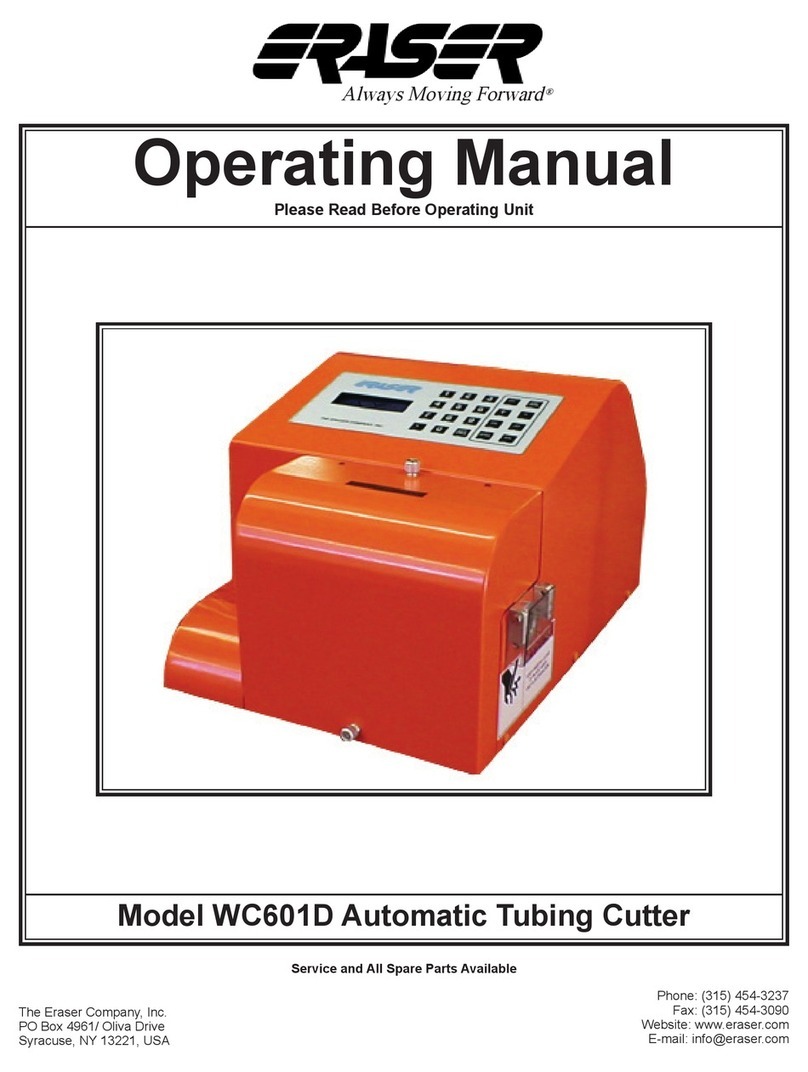
Eraser
Eraser WC601D User manual
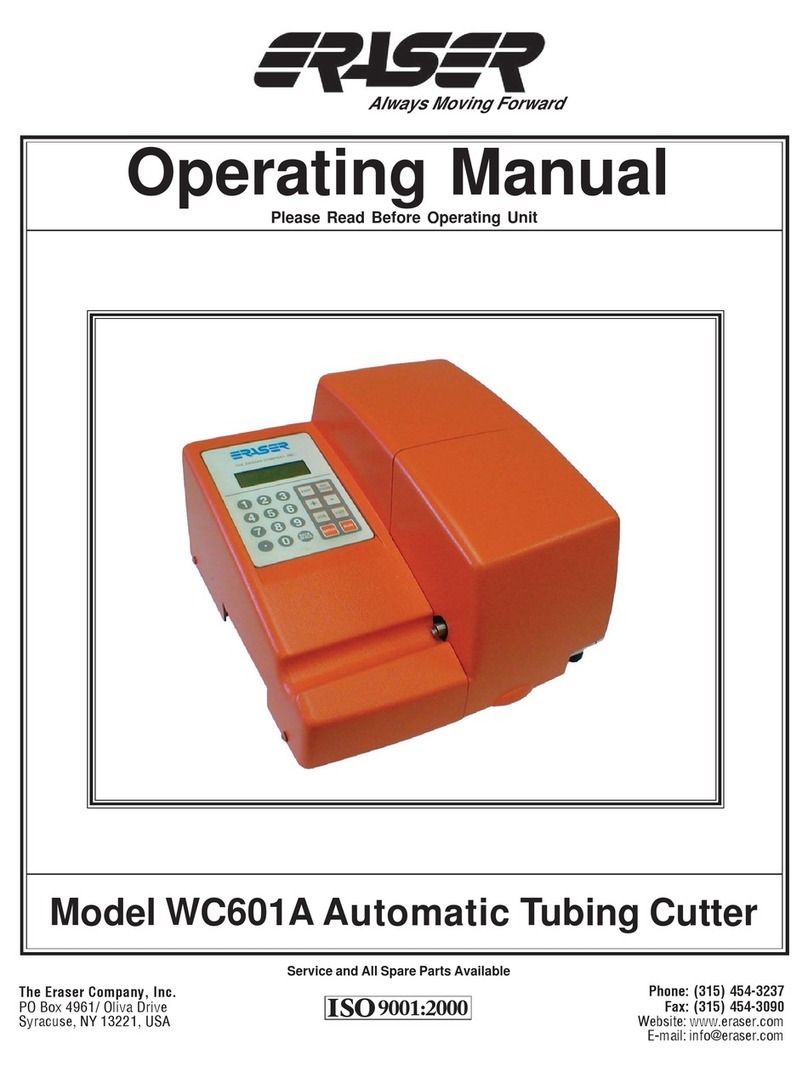
Eraser
Eraser WC601A User manual
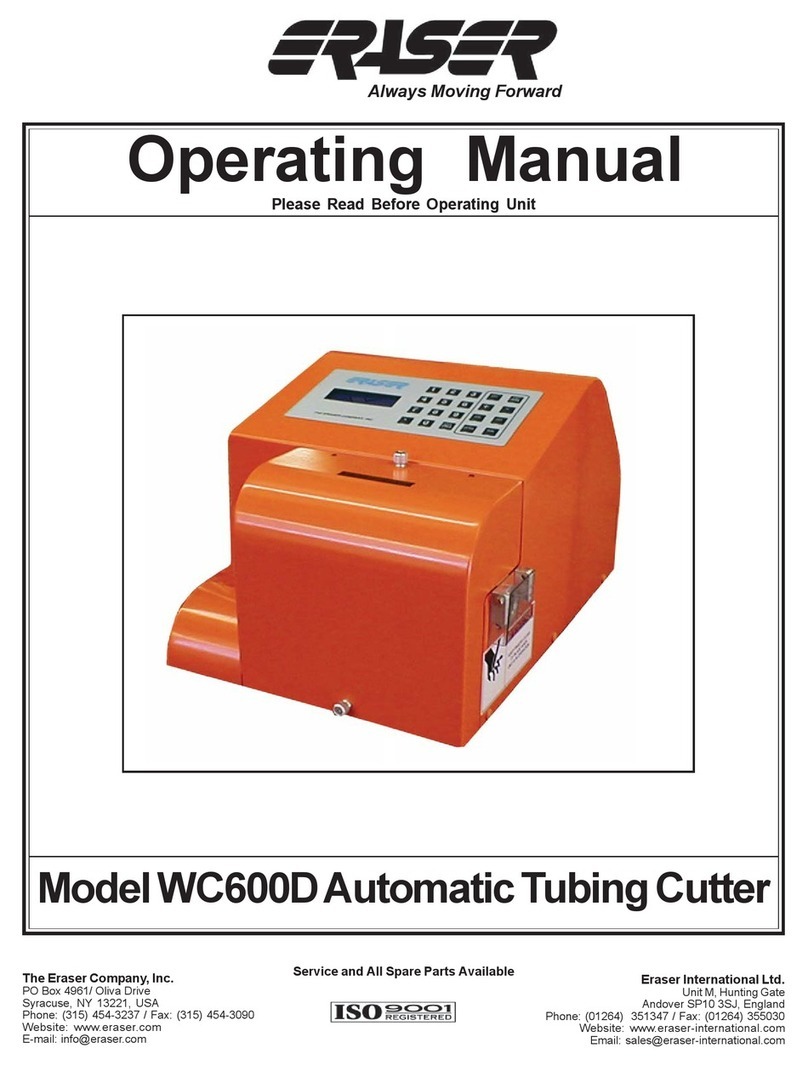
Eraser
Eraser WC600D User manual
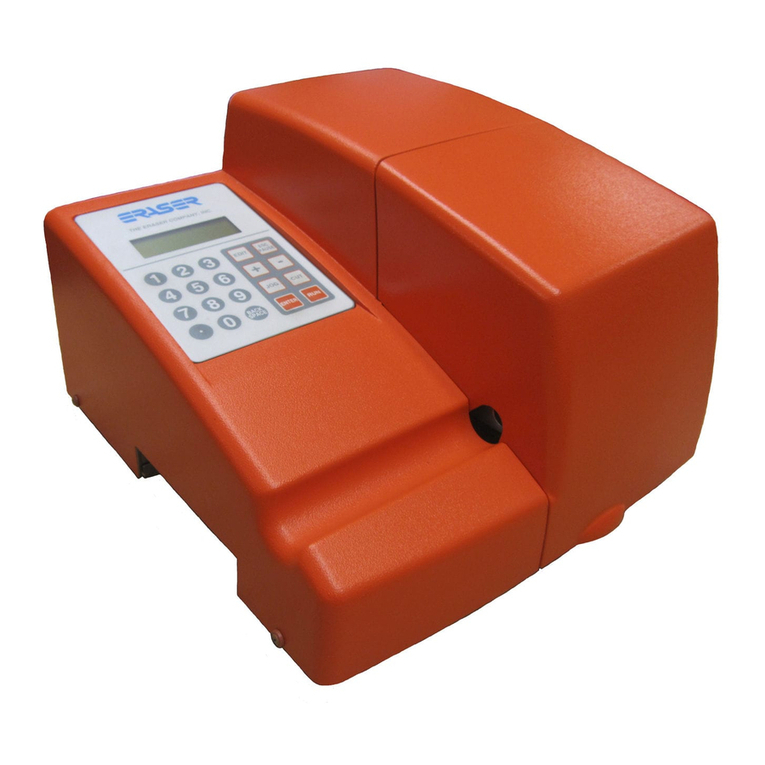
Eraser
Eraser WC601A User manual
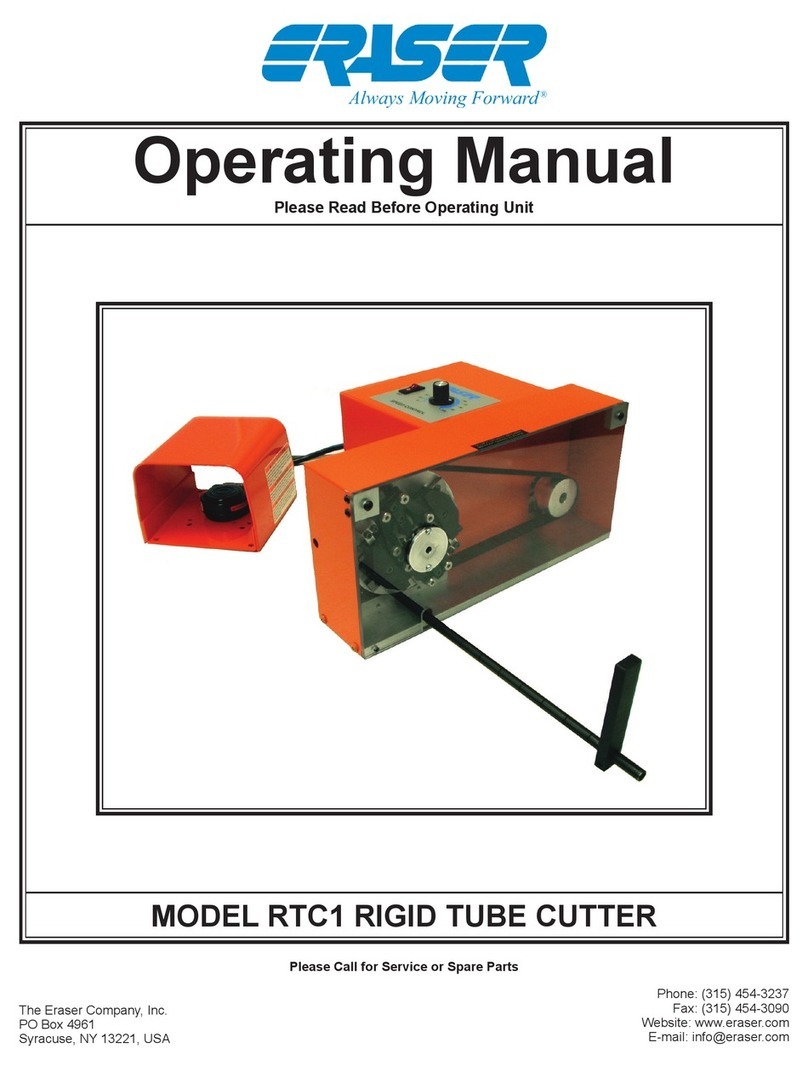
Eraser
Eraser RTC1 User manual
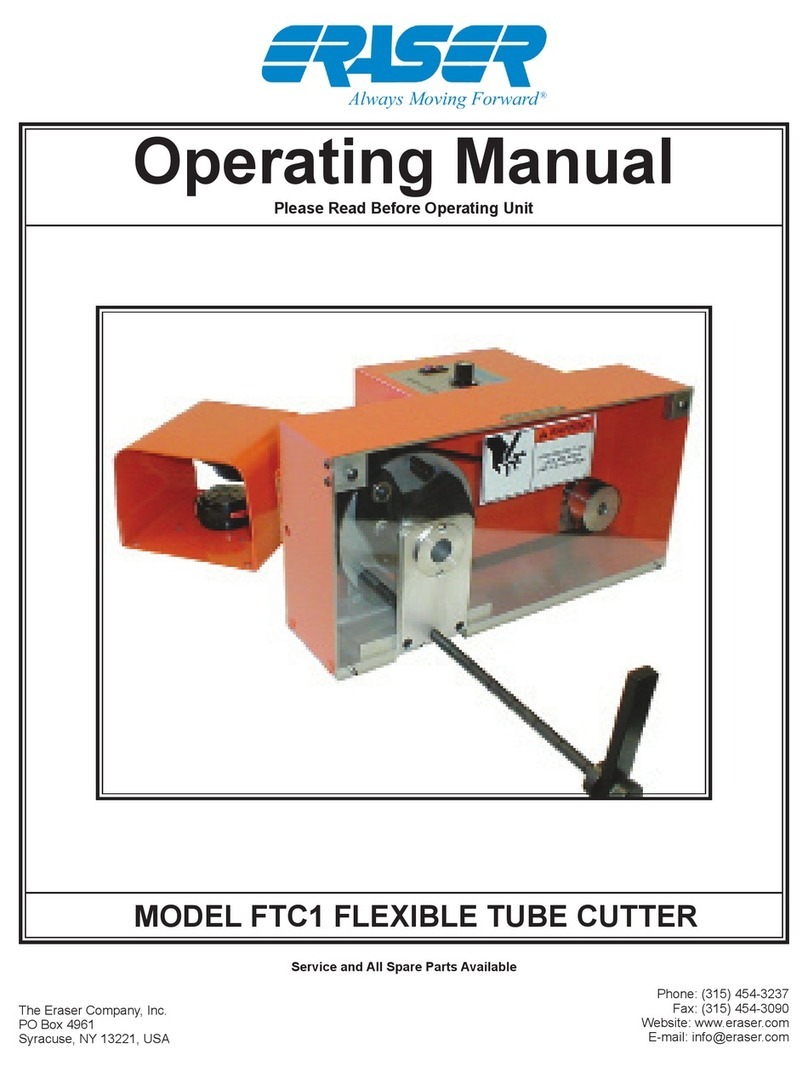
Eraser
Eraser FTC1 User manual
Popular Cutter manuals by other brands
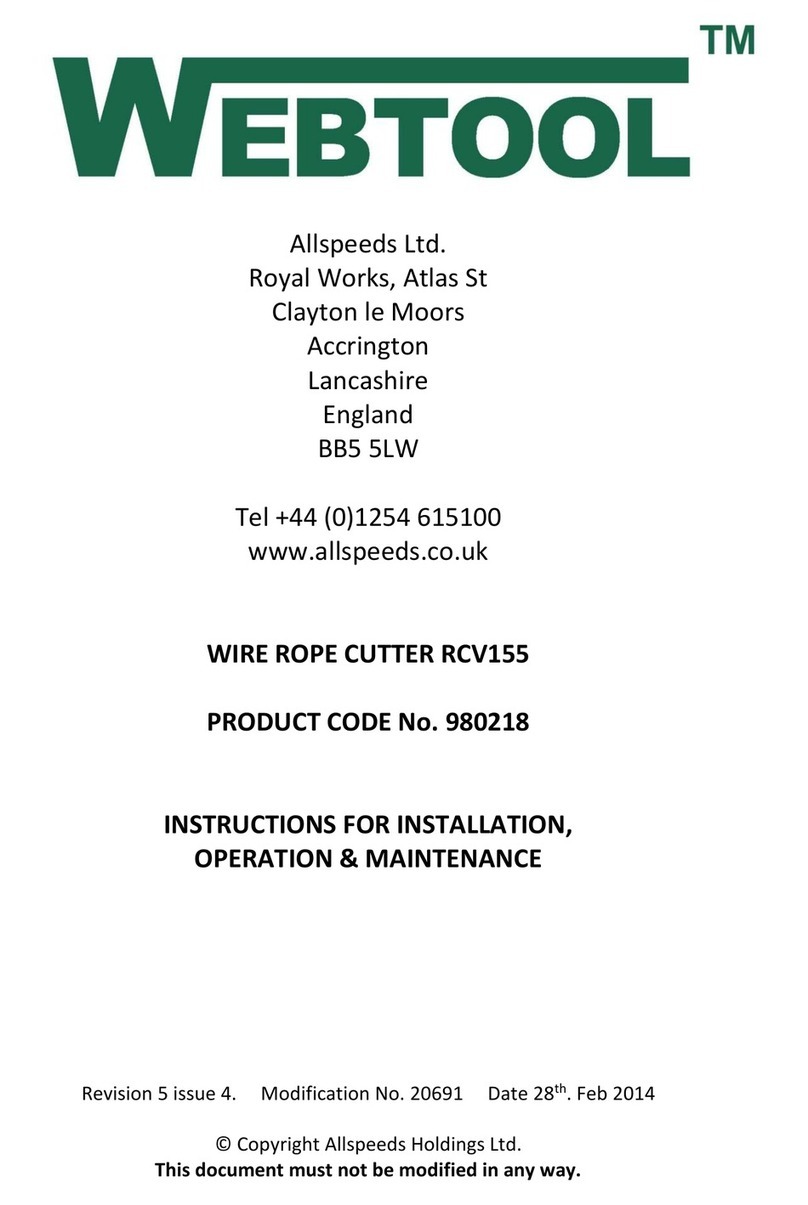
Webtool
Webtool RCV155 Instructions for installation, operation care and maintenance

Leister
Leister COUPON CUTTER 500 operating instructions
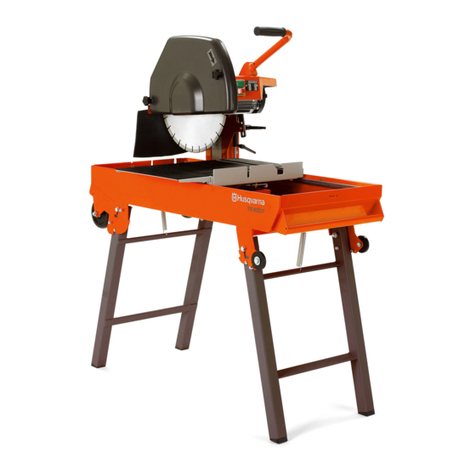
Husqvarna
Husqvarna TS 400 F Operator's manual
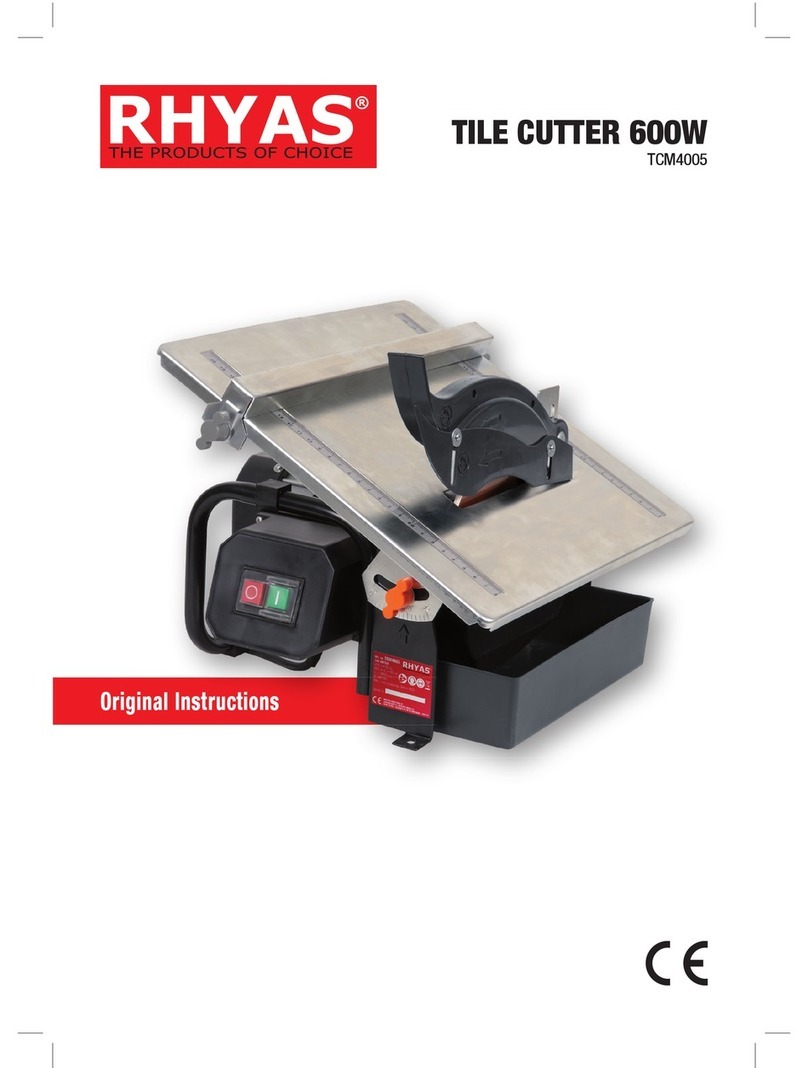
Rhyas
Rhyas TCM4005 Original instructions
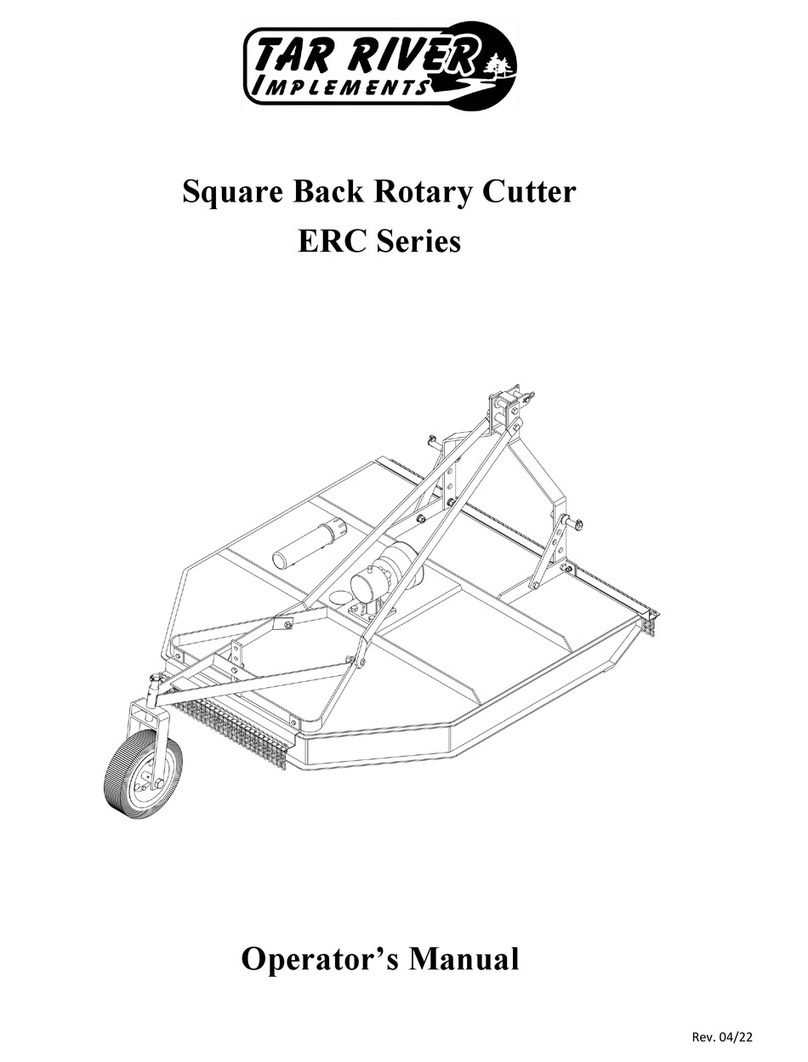
Tar River
Tar River ERC Series Operator's manual

EASTMAN
EASTMAN Raptor Service manual