GE CEY51A User manual

GEK
-
31144
Insert
Booklet
-
GEK
-
1275
INSTRUCTIONS
Mho
Distance
Relay
Type
CEY
Model
12
CEY
51
B
(
-
)
D
INTRODUCTION
This
insert
booklet
and
the
12
CEY
51
A
(
-
)
D
instruction
book
(
GEK
-
1275
)
form
the
instructions
for
the
12
CEY
51
B
(
-
)
D
re
1
ay
.
DESCRIPTION
The
12
CEY
5
IB
(
-
)
D
relay
is
similar
to
the
12
CEY
51
A
(
-
)
D
relay
except
that
the
contact
circuits
were
arranged
per
the
12
CEY
15
A
(
-
)
A
relay
contact
circuits
.
Check
figure
1
of
this
insert
booklet
for
the
contact
circuit
arrangement
.
These
instructions
do
not
purport
to
cover
all
details
or
variations
in
equipment
nor
to
provide
for
every
possible
contingency
to
be
siet
in
connection
with
installation
,
operation
or
Maintenance
.
Should
further
inforsiation
be
desired
or
should
particular
problems
arise
which
are
not
covered
sufficiently
for
the
purchaser
1
*
purposes
,
the
matter
should
be
referred
to
the
6
eneral
Electric
Company
.
POWER
SYSTEMS
MANAGEMENT
DEPARTMENT
m
ELECTRIC
GENERAL
PHILADELPHIA
,
PA
Courtesy of NationalSwitchgear.com

GEK
-
31144
19
17
15
11
13
O
o
o
o
o
20
18
14
16
12
AA
A
A
A
A
A
A
Ax
Ax
A
2
NT
-
1
NT
-
1
I
>
2
3
NT
-
3
-
i
NT
-
3
J
4
NT
-
2
I
;
A
>
3
02
-
3
01
-
27
%
35
^
X
11
A
POL
.
POL
.
/
CI
2
SI
CM
03
-
1
%
X
2
A
X
13
POL
.
R
23
0
135
15
95
95
15
53
10
ryrp
Lfj
~
m
r
rrpj
ryrp
NO
.
I
1
RII
01
-
2
AOPER
T
&
SI
0
i
-
R
,
-
f
URI
3
LnnnJ
TR
01
-
2
R
2
I
03
-
1
AOPER
.
C
2
I
TR
02
-
3
Rjuun
02
Z
3
/
VOPER
.
023
JRI
2
R
22
C
22
TR
01
-
2
TR
03
-
1
TR
02
-
3
TR
01
-
2
TR
03
-
1
TR
02
-
3
°
3
<
/
r
Ax
Ax
\
l
/
\
i
/
V
M
/
\
l
/
w
~
v
V
V
V
7
0
5
I
o
O
o
o
8
10
6
2
X
-
SHORT
FIBBER
01
-
2
=
TOP
UNIT
02
-
3
-
-
MIDDLE
UNIT
08
-
I
=
BOTTOM
UN
IT
FIG
.
I
(
0227
A
7013
-
0
)
Internal
Conm
-
ctions
Diagram
For
The
CEY
51
B
Relay
(
Front
View
)
BC
-
12
/
98
(
100
)
GENERAL
ELECTRIC
METER
AND
CONTROL
BUSINESS
DEPT
.
,
MALVERN
,
PA
19355
Courtesy of NationalSwitchgear.com

GEK
-
1275
CONTENTS
PAGE
INTRODUCTION
3
APPLICATION
3
CALCULATION
OF
SETTINGS
4
RATINGS
6
Contacts
Target
&
Seal
-
in
Unit
7
7
8
OPERATING
PRINCIPLES
8
CHARACTERISTICS
Mho
Unit
Tapped
Autotrarsformer
Current
Circuits
Potential
Circuits
.
.
.
8
11
11
12
13
CONSTRUCTION
14
RECEIVING
,
HANDLING
,
STORAGE
14
ACCEPTANCE
TESTS
Visual
Inspection
Mechanical
Inspection
Electrical
Checks
,
Mho
Unit
Electrical
Tests
-
Target
Seal
-
in
14
14
15
18
18
INSTALLATION
PROCEDURE
Location
Mounting
Connections
Visual
Inspection
Mechanical
Inspection
Portable
Test
Equipment
Electrical
Tests
on
the
Mho
Units
18
18
18
19
19
19
19
22
INSPECTION
Target
&
Seal
-
in
Unit
Mho
Units
22
22
23
PERIODIC
CHECKS
AND
ROUTINE
MAINTENANCE
Contact
Cleaning
23
23
SERVICING
23
Control
-
Spring
Adjustments
Ohmic
-
Reach
Adjustment
.
.
.
Angle
of
Maximum
Torque
.
.
Directional
Check
24
24
27
27
RENEWAL
PARTS
28
LIST
OF
FIGURES
Cover
(
8036548
)
2
Courtesy of NationalSwitchgear.com

GEK
-
1275
MHO
DISTANCE
RELAY
TYPE
CEY
51
A
INTRODUCTION
The
CEY
51
A
relay
is
an
extended
-
range
,
three
-
phase
,
high
-
speed
,
single
-
zone
,
mho
directional
distance
relay
.
It
is
constructed
of
three
single
-
phase
units
in
one
L
2
-
D
case
with
provisions
for
single
-
phase
testing
.
One
target
and
seal
-
in
unit
provides
indication
of
operation
for
all
three
units
.
The
transient
overreach
of
this
relay
is
limited
by
design
so
that
it
is
suitable
for
use
as
a
first
-
zone
device
.
One
CEY
51
A
relay
will
provide
complete
one
-
zone
protection
for
three
-
phase
,
phase
-
to
-
phase
and
double
phase
-
to
-
ground
faults
.
APPLICATION
The
CEY
51
A
relay
,
because
of
its
low
transient
overreach
(
maximum
of
six
percent
)
and
its
memory
action
,
is
primarily
a
first
-
zone
tripping
relay
.
As
such
,
it
is
applicable
as
a
high
-
speed
tripping
unit
in
direct
and
permissive
underreaching
transferred
tripping
schemes
,
as
well
as
a
first
-
zone
tripping
relay
in
straight
distance
and
carrier
schemes
.
When
applying
this
relay
for
the
protection
of
a
given
circuit
,
it
is
advantageous
to
set
the
relay
on
the
highest
basic
-
minimum
-
reach
tap
that
will
accomodate
the
desired
reach
setting
,
operating
torque
level
.
For
first
-
zone
applications
,
the
relay
may
be
set
for
as
much
as
90
%
of
the
distance
to
the
remote
terminal
.
This
will
ensure
the
highest
possible
Since
all
forms
of
the
CEY
51
A
relay
have
adjustable
maximum
-
torque
angle
available
,
a
consideration
of
which
angle
to
use
may
arise
.
It
is
suggested
that
arc
resistance
for
faults
near
the
relay
should
be
considered
in
this
regard
.
The
smaller
the
angle
of
maximum
torque
,
the
greater
the
arc
resistance
that
the
unit
will
accommodate
.
The
basic
sensitivity
of
the
CEY
51
A
relay
will
depend
on
the
basic
minimum
tap
that
is
used
.
Figure
2
gives
the
steady
-
state
and
dynamic
sensitivity
of
the
relay
.
In
order
to
be
sure
that
the
relay
will
reach
no
less
than
90
%
of
its
setting
,
the
minimum
three
-
phase
fault
current
flowing
in
the
relay
for
a
fault
at
the
remote
end
of
the
line
should
be
at
least
those
values
given
in
table
I
.
3
Courtesy of NationalSwitchgear.com

GEK
-
1275
TABLE
I
Basic
Minimum
Tap
Setting
Restraint
Tap
Setting
Min
.
3
-
phase
Fault
Current
Required
0.2
ohms
25
%
15.0
amps
0.2
50
%
22.5
0.2
100
%
30.0
0.375
0.375
0.375
25
%
8.0
50
%
12.0
100
%
16.0
0.4
25
%
7.5
0.4
50
%
11.25
0.4
100
%
15.0
0.75
25
%
4.0
0.75
50
%
6.0
0.75
100
%
8.0
0.8
25
%
3.75
50
%
0.8
5.6
100
%
0.8
7.5
1.5
25
%
2.0
1.5
50
%
3.0
1.5
100
%
4.0
3.0
25
%
1.0
3.0
50
%
1.5
100
%
3.0
2.0
6.0
25
%
0.5
6.0
50
%
0.75
6.0
100
%
1.0
The
CEY
51
A
and
its
companion
zone
-
packaged
relays
may
be
combined
in
many
different
ways
for
use
in
different
schemes
,
including
straight
distance
protection
,
directional
-
comparison
carrier
protection
,
permissive
overreaching
,
permissive
-
and
di
rect
-
underreaching
transferred
tripping
and
many
different
back
-
up
schemes
.
Figure
3
illustrates
the
external
connections
to
the
CEY
51
A
when
used
in
conjunction
with
a
CEY
52
A
,
a
CEB
52
A
and
an
RPM
21
D
for
three
-
zone
protection
of
a
transmission
line
against
all
multi
-
phase
faults
.
The
section
under
CALCULATION
OF
SETTINGS
provides
a
worked
example
for
a
typical
application
of
the
CEY
51
A
relay
.
CALCULATION
OF
SETTINGS
Consider
a
230
kV
transmission
line
50
miles
long
having
a
phase
-
to
-
neutral
impedance
of
:
zprim
=
0.14
+
j
0.80
ohms
per
mile
4
Courtesy of NationalSwitchgear.com

GEK
-
1275
Zprim
=
50
(
0.14
+
j
0.80
)
=
7
+
j
40
ohms
total
PT
Ratio
=
230
,
000
/
115
=
2000
/
1
CT
Ratio
=
600
/
5
=
120
/
1
Assume
that
the
minimum
three
-
phase
fault
current
flowing
in
the
relay
for
a
three
-
phase
fault
at
the
remote
end
of
the
line
is
about
8
secondary
amperes
,
and
for
a
close
-
in
fault
,
it
is
11
secondary
amperes
.
CT
Ratio
Zsec
.
=
Zprim
PT
Ratio
^
sec
.
=
(
7.0
-
t
j
40.0
)
120
=
0.42
+
j
2.4
ohms
7
UUTT
=
2.43
/
80.5
o
ohms
Zsec
.
Assume
that
the
CEY
51
A
is
to
be
used
to
provide
first
-
zone
protection
and
it
is
desired
to
set
the
relay
to
protect
90
%
of
the
line
0.9
(
Zsec
)
=
0.9
(
2.43
)
For
this
application
,
the
highest
suitable
basic
minimum
tap
is
1.5
ohms
.
/
80.5
=
2.19
/
80.5
The
ohmic
-
reach
equation
given
in
the
section
under
OPERATING
CHARACTERISTICS
-
TAPPED
AUTOTRANSFORMER
is
used
to
obtain
the
required
tap
setting
.
(
100
)
(
Min
.
Ohms
)
Cos
(
0
-
9
)
Percent
Tap
Setting
=
Z
Minimum
Ohms
=
1.5
Z
=
Zsec
.
=
2.19
ohms
0
-
80.50
The
selection
of
the
maximum
-
torque
angle
for
a
first
-
zone
relay
should
depend
primarily
on
accommodation
of
arc
resistance
.
Smaller
maximum
-
torque
angles
will
accommodate
more
arc
resistance
than
larger
maximum
-
torque
angles
.
Since
arc
resistance
is
independent
of
line
length
,
the
shorter
lines
will
provide
the
greatest
problem
on
this
score
because
of
the
shorter
reach
setting
on
the
relay
.
Thus
,
on
short
lines
it
is
desirable
to
use
smaller
angles
of
maximum
torque
.
On
longer
lines
,
where
the
mho
unit
must
be
set
with
a
longer
reach
,
it
would
have
more
significant
arc
-
resistance
capability
even
with
a
larger
angle
of
maximum
torque
.
Another
factor
to
consider
is
immunity
to
system
swings
.
In
general
,
an
angle
of
maximum
torque
approaching
the
angle
of
the
line
will
provide
the
greatest
immunity
to
system
swings
.
Thus
,
for
most
lines
,
the
75
°
setting
would
provide
the
greatest
immunity
.
5
Courtesy of NationalSwitchgear.com

GEK
-
1275
Since
system
swings
are
not
usually
a
problem
on
short
lines
,
but
arc
resistance
is
,
and
since
arc
resistance
may
not
be
a
problem
on
long
lines
but
system
swings
might
be
,
it
is
a
good
general
practice
to
use
the
lower
maximum
-
torque
angle
universally
except
where
system
swings
may
be
a
problem
.
Since
this
is
a
short
line
,
the
normal
60
o
angle
of
maximum
torque
will
be
used
.
Thus
,
9
=
600
.
100
(
1.5
)
Cos
(
80.5
-
60
)
64
%
Percent
Tap
Setting
=
2.19
T
=
64
%
A
check
with
the
table
in
the
APPLICATION
section
will
indicate
that
the
minimum
fault
current
of
8
amperes
is
sufficient
to
operate
the
relay
for
the
settings
selected
.
A
plot
of
this
characteristic
on
the
R
-
X
diagram
will
show
that
the
unit
will
accommodate
approximately
1.15
secondary
ohms
of
arc
resistance
for
a
fault
at
the
ori
gi
n
.
A
rough
estimate
of
the
arc
resistance
that
a
relay
will
see
for
a
multi
-
phase
fault
is
given
by
RA
=
3
130
where
130
=
three
-
phase
fault
current
flowing
in
the
relay
.
Since
the
minimum
three
-
phase
fault
current
in
the
relay
for
a
close
-
in
fault
was
given
as
11
amperes
,
the
maximum
arc
resistance
is
0.27
secondary
ohms
RA
=
11
The
60
°
relay
setting
will
accommodate
this
very
easily
and
so
would
a
75
o
setting
.
However
,
the
6
O
0
setting
will
accommodate
more
arc
resistance
near
the
balance
point
,
and
since
the
line
is
short
,
and
if
system
swings
are
not
apt
to
be
a
problem
,
the
60
o
setting
is
desirable
.
RATINGS
The
type
-
CEY
51
A
relay
covered
by
these
instructions
is
available
for
120
volts
,
5
amperes
,
60
cycle
rating
.
The
one
-
second
rating
of
the
current
circuits
is
225
amperes
.
The
basic
minimum
reach
and
adjustment
ranges
of
the
mho
units
are
given
in
Tabl
e
II
.
6
Courtesy of NationalSwitchgear.com

GEK
-
1275
TABLE
II
MINIMUM
REACH
MHO
RANGE
ANGLE
UNIT
0.2
/
0.4
/
0.8
0.375
/
0.75
/
1.5
0.75
/
1.5
/
3.0
0.2
to
8
0.375
to
15
0.75
to
30
60
*
*
01
-
2
60
*
*
or
02
-
3
60
*
*
or
or
or
1.5
/
3.0
/
6.0
1.5
to
60
60
**
03
-
1
Adjustment
taps
are
set
for
1.5
ohms
(
or
0.4
ohms
)
*
*
The
angle
of
maximum
torque
can
be
adjusted
up
to
75
o
.
The
reach
of
the
mho
units
at
the
75
o
setting
will
increase
to
approximately
103
%
of
its
reach
at
the
60
o
setting
.
It
will
be
noted
that
three
basic
-
minimum
-
reach
settings
are
listed
for
the
mho
units
.
Selection
of
the
desired
basic
-
minimum
-
reach
setting
for
each
unit
is
made
by
means
of
two
tap
screws
on
a
two
-
section
tap
block
located
at
the
back
of
the
relay
(
see
Figure
1
)
.
The
position
of
these
screws
determines
the
tap
setting
of
the
two
primary
windings
of
the
transactors
(
TR
-
01
-
2
,
TR
-
02
-
3
,
TR
-
03
-
l
)
.
The
ohmic
reach
of
the
mho
units
can
be
adjusted
in
1
%
steps
over
a
10
/
1
range
for
any
of
the
basic
-
minimum
-
reach
settings
listed
in
Table
II
by
means
of
autotransformer
tap
leads
on
the
tap
blocks
at
the
right
side
of
the
relay
.
CONTACTS
The
contacts
of
the
CEY
51
A
relay
will
close
and
momentarily
carry
30
amperes
DC
.
However
,
the
circuit
-
breaker
trip
circuit
must
be
opened
by
an
auxiliary
switch
contact
or
other
suitable
means
,
since
the
relay
contacts
have
no
interrupting
rating
.
TARGET
SEAL
-
IN
UNIT
The
target
seal
-
in
unit
used
in
the
CEY
51
A
relay
has
ratings
as
shown
in
Table
III
.
TABLE
III
0
,
6
/
2.0
Amp
0.2
/
2.0
Amp
2.0
2.0
0.6
0.2
Carry
30
Amps
for
(
seconds
)
Carry
10
Amps
for
(
seconds
)
Carry
Continuously
(
Amp
)
Minimum
Operating
(
Amp
)
Minimum
Dropout
(
Amp
)
DC
resistance
(
Ohms
)
60
Hz
Impedance
(
Ohms
)
50
Hz
impedance
(
Ohms
)
2.2
0.5
3.5
0.05
5.0
30.0
0.45
2.0
2.6
1.2
2.3
0.37
2.0
2.0
0.6
0.2
0.5
0.15
0.5
0.24
0.78 0.18
0.65
6.2
0.65
0.54
5.1
0.54
0.05
8.3
50
42
2.5
Amp
@
125
VDC
DC
Resistive
Interrupting
Rating
(
Amps
)
7
Courtesy of NationalSwitchgear.com

GEK
-
1275
OPERATING
PRINCIPLES
The
mho
units
of
the
CEY
51
relay
are
of
the
four
-
pole
induction
-
cylinder
construction
in
which
torque
is
produced
by
the
interaction
between
a
polarizing
flux
and
fluxes
proportional
to
the
restraining
or
operating
quantities
.
The
schematic
connections
of
the
Mi
unit
are
shown
in
Figure
4
.
poles
,
energized
by
phase
-
to
-
phase
voltage
,
produce
the
polarizing
flux
,
from
the
front
and
rear
poles
,
energized
by
the
difference
between
the
secondary
voltage
of
transactor
TR
-
0
i
_
2
and
a
percentage
of
the
same
phase
-
to
-
phase
voltage
,
interacts
with
the
polarizing
flux
to
produce
torque
.
The
torque
equation
can
be
written
as
follows
:
The
two
side
The
flux
Torque
=
KE
(
IZJI
_
JE
)
3
(
1
)
cos
where
:
E
=
phase
-
to
-
phase
voltage
(
Ej
2
)
I
=
delta
current
(
II
-
12
)
ZjT
=
transfer
impedance
of
transactor
TR
-
0
I
_
2
(
design
constant
)
p
=
angle
between
E
and
(
IZJI
-
E
)
K
=
design
constant
T
=
autotransformer
tap
setting
That
this
equation
(
1
)
defines
a
mho
characteristic
can
be
shown
graphically
by
means
of
Figure
5
.
The
vector
IZJ
13
at
an
angle
0
determines
the
basic
minimum
reach
of
the
unit
for
a
particular
tap
setting
of
the
transactor
TR
-
0
I
_
2
primary
.
Assuming
finite
values
of
E
and
(
IZT
1
-
TE
)
,
the
balance
point
,
torque
=
0
,
will
occur
where
cos
=
0
,
that
is
,
where
the
angle
P
is
90
o
.
The
locus
of
the
terminus
vector
TE
(
Point
A
in
Figure
5
)
that
will
cause
the
angle
$
to
be
always
900
in
a
circle
passing
through
the
origin
and
with
the
vector
IZT
1
as
a
diameter
.
B
Considering
further
the
diagram
in
Figure
5
,
we
note
that
the
angle
is
less
than
900
for
an
internal
fault
(
point
C
)
and
net
tprque
will
be
in
the
closing
direction
(
cos
^
is
positive
)
;
and
that
the
angle
P
is
greater
than
90
°
for
an
external
fault
(
point
D
)
and
the
net
torque
will
be
in
the
opening
direction
(
cos
$
is
negative
)
.
B
See
Figure
5
,
Graphical
Representation
of
Mho
Operating
Principle
.
CHARACTERISTICS
MHO
UNIT
Impedance
Characteristic
The
impedance
characteristic
of
the
mho
unit
is
shown
in
Figure
6
for
the
0.75
-
ohm
basic
-
minimum
-
reach
setting
at
a
maximum
-
torque
angle
of
6
O
0
.
This
characteristic
is
obtained
with
the
terminal
voltage
of
the
relay
supplied
directly
to
the
restraint
circuit
of
the
mho
unit
,
that
is
,
with
the
mho
taps
on
the
auto
-
transformer
tap
block
set
at
100
%
.
This
circular
impedance
characteristic
can
8
Courtesy of NationalSwitchgear.com

GEK
-
1275
be
enlarged
,
that
is
,
the
mho
-
unit
reach
can
be
increased
by
up
to
10
/
1
by
reducing
the
percentage
of
the
terminal
voltage
supplied
to
the
restraint
circuit
by
means
of
the
taps
on
the
autotransformer
tap
blocks
,
and
the
circle
can
be
further
enlarged
,
providing
a
total
range
adjustment
of
up
to
40
/
1
,
by
means
of
the
basic
-
minimum
-
reach
tap
screws
.
diameter
along
the
60
o
impedance
line
equal
to
the
ohmic
reach
of
the
unit
as
expressed
by
the
following
equation
:
The
circle
will
always
pass
through
the
origin
and
have
a
(
100
)
Zmin
Tap
Setting
(
%
)
Ohmic
Reach
where
:
=
Basic
minimum
phase
-
to
-
neutral
ohmic
reach
of
the
unit
(
as
set
by
taps
)
.
The
angle
of
maximum
torque
of
the
mho
unit
can
be
adjusted
up
to
75
o
(
see
SERVICI
1
G
)
with
negligible
effect
on
the
reach
of
the
unit
.
^
mi
n
Directional
Action
The
mho
unit
is
carefully
adjusted
to
have
correct
directional
action
under
For
faults
in
the
non
-
steady
-
state
,
low
-
voltage
and
low
-
current
conditions
,
tripping
direction
,
the
contacts
will
remain
open
at
zero
volts
between
0
and
60
For
faults
in
the
tripping
direction
,
the
unit
will
close
its
contacts
amperes
.
between
the
current
limits
in
Table
IV
for
the
three
basic
-
minimum
-
reach
settings
(
see
Table
II
)
at
the
voltage
shown
.
TABLE
IV
Current
Range
For
Correct
Directional
Action
Vol
ts
(
See
Figure
10
)
Basi
c
-
Minimum
-
Reach
Tap
22.5
-
60
A
12.0
-
60
A
11.25
-
60
A
6.0
-
60
A
5.6
-
60
A
3.0
-
60
A
1.5
-
60
A
0.75
-
60
A
2.0
V
0.2
2.0
V
0.375
2.0
V
0.4
2.0
V
0.75
2.0
V
0.8
2.0
V
1.5
2.0
V
3.0
2.0
V
6.0
The
unit
is
set
at
the
factory
on
the
1.5
ohm
or
0.4
ohm
tap
for
correct
directional
action
over
the
indicated
current
range
.
A
variation
of
+
10
%
can
be
expected
on
the
values
listed
.
For
performance
during
transient
low
-
voltage
conditions
,
where
the
voltage
was
normal
at
120
volts
prior
to
the
fault
,
refer
to
the
paragraph
on
MEMORY
ACTION
.
9
Courtesy of NationalSwitchgear.com

GEK
-
1275
Underreach
At
reduced
voltage
the
ohmic
value
at
which
the
mho
unit
will
operate
may
be
somewhat
lower
than
the
calculated
value
.
This
"
pullback
"
or
reduction
in
reach
is
shown
in
Figure
2
.
The
unit
reach
in
percent
of
setting
is
plotted
against
the
three
-
phase
fault
current
for
three
ohmic
-
reach
tap
settings
.
Note
that
the
fault
-
current
scale
changes
with
the
basic
-
minimum
-
reach
setting
.
The
mho
unit
will
operate
for
all
points
to
the
right
of
the
curve
.
The
steady
-
state
curves
of
Figure
2
were
determined
by
tests
performed
with
no
voltage
supplied
to
the
relay
before
the
fault
was
applied
.
The
dynamic
curves
were
obtained
with
full
-
rated
voltage
of
120
volts
supplied
to
the
relay
before
the
fault
was
applied
.
See
Figure
2
,
Steady
-
State
and
Dynamic
-
Reach
Curves
for
the
MHO
Unit
of
the
CEY
51
A
Relay
.
Memory
Action
The
dynamic
curves
of
Figure
2
illustrate
the
effect
of
memory
action
in
the
mho
unit
,
which
maintains
the
polarizing
flux
for
a
few
cycles
following
the
inception
of
the
fault
.
This
memory
action
is
particularly
effective
at
low
voltage
levels
,
where
it
enables
the
mho
unit
to
operate
for
low
-
fault
currents
.
This
can
be
most
forcefully
illustrated
for
a
zero
-
voltage
fault
by
referring
to
Figure
2
.
A
zero
-
voltage
fault
is
likely
to
be
right
at
the
relay
bus
and
therefore
,
to
protect
for
this
fault
,
it
is
imperative
that
the
relay
reach
zero
percent
of
its
setting
.
Figure
2
shows
that
the
mho
unit
,
under
static
conditions
,
will
not
see
a
fault
at
0
%
(
zero
percent
)
of
the
relay
setting
,
regardless
of
the
tap
setting
.
However
,
under
dynamic
conditions
when
the
memory
action
is
effective
,
Figure
2
shows
that
an
mho
unit
with
a
3
-
ohm
basic
-
minimum
-
reach
and
100
%
tap
setting
will
operate
if
130
is
greater
than
1.5
amperes
.
Transient
Overreach
The
operation
of
the
mho
unit
under
transient
conditions
at
the
inception
of
a
fault
is
important
because
the
relay
is
normally
connected
so
that
the
mho
contacts
will
trip
a
circuit
breaker
independently
of
any
other
contacts
.
The
impedance
characteristic
of
Figure
6
and
the
steady
-
state
curves
of
Figure
2
represent
steady
-
state
conditions
.
If
the
fault
current
contains
a
DC
transient
,
the
unit
may
close
its
contacts
momentarily
even
though
the
impedance
being
measured
is
slightly
greater
than
the
calculated
steady
-
state
reach
.
This
overreaching
tendency
will
be
at
a
maximum
when
a
fault
occurs
at
the
one
instant
in
either
half
-
cycle
that
produces
the
maximum
DC
offset
of
the
current
wave
.
The
maximum
transient
overreach
of
the
mho
unit
will
not
exceed
6
%
of
the
steady
-
state
reach
for
line
angles
up
to
850
.
Operating
Time
The
operating
time
of
the
mho
unit
is
determined
by
a
number
of
factors
such
as
the
basic
-
minimum
-
reach
setting
of
the
unit
,
fault
-
current
magnitude
,
ratio
of
fault
impedance
to
relay
reach
,
and
magnitude
of
relay
voltage
prior
to
the
fault
.
The
curves
in
Figure
7
are
for
the
condition
of
rated
volts
prior
to
the
fault
.
Time
curves
are
given
for
four
ratios
of
fault
impedance
to
relay
-
reach
setting
.
In
all
cases
,
the
mho
taps
were
in
the
100
%
position
and
the
angle
of
maximum
torque
was
set
at
60
°
lag
.
See
Figure
7
,
Operating
-
time
Curves
for
the
Mho
Unit
in
the
CEY
51
A
Relay
.
10
Courtesy of NationalSwitchgear.com

GEK
-
1275
TAPPED
AUTOTRANSFORMER
The
ohmic
reach
of
the
mho
units
may
be
adjusted
by
means
of
taps
on
the
two
autotransformers
.
Each
autotransformer
has
two
windings
.
One
winding
is
tapped
in
10
%
steps
from
15
%
to
95
%
.
The
other
winding
is
tapped
at
0
%
,
1
%
,
3
%
and
5
%
.
The
desired
tap
setting
is
made
by
the
proper
location
of
the
(
two
)
leads
marked
#
1
and
the
jumper
connecting
the
two
windings
of
the
autotransformer
.
Note
that
the
0
%
-
to
-
5
%
winding
may
be
added
or
subtracted
from
the
15
%
-
95
%
winding
.
The
tap
setting
required
to
protect
a
zone
Z
-
ohms
long
,
where
Z
is
the
positive
phase
-
sequence
-
phase
-
to
-
neutral
impedance
expressed
in
secondary
terms
,
is
determined
by
the
following
equation
.
Tap
Setting
=
(
100
)
(
Min
.
Ohms
Setting
)
Cos
(
0
-
9
)
Z
where
:
Angle
of
maximum
torque
Power
factor
angle
of
fault
impedance
.
9
0
Example
1
:
TAP
SETTING
DESIRED
91
Set
one
end
of
jumper
lead
to
95
%
.
Set
the
other
end
to
5
%
.
Set
#
1
on
1
%
.
(
Note
the
4
%
setting
of
the
0
%
-
to
-
5
%
winding
subtracts
from
the
95
%
setting
.
)
Example
2
:
TAP
SETTING
DESIRED
=
89
Set
#
1
to
5
%
.
Set
the
other
end
to
1
%
.
Set
one
end
of
jumper
lead
to
85
%
.
(
Note
the
4
%
setting
of
the
0
%
-
to
-
5
%
winding
adds
to
the
85
%
setting
.
)
CURRENT
CIRCUITS
The
maximum
current
burden
imposed
on
each
current
transformer
at
5
amperes
and
60
cycles
is
listed
in
Table
V
.
TABLE
V
VA
P
.
F
.
W
AMPS
CYCLES
R
X
0.98
2.22
2.5
0.019
5
60
0.089
11
Courtesy of NationalSwitchgear.com

GEK
-
1275
The
burden
for
other
tap
This
data
is
for
the
3.0
-
ohm
basic
-
reach
tap
setting
,
settings
may
be
calculated
from
the
following
equation
:
x
B
3
ohms
(
-
W
Bnew
where
:
B
Burden
at
new
tap
setting
Basic
reach
of
new
tap
setting
b
3
ohms
=
Burden
from
Table
V
new
B
.
R
.
POTENTIAL
CIRCUITS
The
maximum
potential
burden
(
with
restraint
tap
set
for
100
%
)
imposed
on
each
potential
transformer
at
120
volts
and
60
cycles
is
listed
in
Table
VI
.
TABLE
VI
V
A
WATTS
P
.
F
.
R
X
CIRCUIT
9.8
0.89
8.7
Polarizing
1300
-
j
680
4.5
4.5
1.0
3200
JO
Restraint
The
restraint
circuit
burden
,
and
hence
the
total
relay
burden
,
will
decrease
when
the
restraint
tap
setting
is
less
than
100
%
.
The
potential
burden
at
tap
settings
less
than
100
%
can
be
calculated
from
the
following
formula
.
(
a
+
jb
)
+
(
c
+
jd
)
Tap
Setting
2
VA
100
The
terms
(
a
+
jb
)(
c
+
jd
)
,
etc
represent
the
burdens
of
the
mho
-
unit
-
potential
circuit
expressed
in
watts
and
vars
with
their
taps
on
100
%
.
of
these
terms
for
60
-
cycle
relays
are
given
in
Table
VII
.
•
1
The
values
TABLE
VII
TERM
(
Watts
+
j
Vars
)
TERM
(
Watts
+
j
Vars
)
CIRCUIT
(
4.5
+
jO
)
(
8.7
-
j
4.5
)
(
a
+
jb
)
(
c
+
jd
)
Restraint
Polarizing
12
Courtesy of NationalSwitchgear.com

GEK
-
1275
CONSTRUCTION
The
type
CEY
51
A
relays
are
assembled
in
a
deep
,
large
-
size
,
double
-
end
(
L
2
D
)
drawout
case
having
studs
at
both
ends
in
the
rear
for
external
connections
.
The
electrical
connections
between
the
relay
units
and
the
case
studs
are
made
through
stationary
molded
inner
and
outer
blocks
,
between
which
nests
a
removable
connecting
plug
that
completes
the
circuits
.
The
outer
blocks
attached
to
the
case
have
the
studs
for
the
external
connections
,
and
the
inner
blocks
have
the
terminals
for
the
internal
connections
.
Every
circuit
in
the
drawout
case
has
an
auxiliary
brush
,
as
shown
in
Figure
8
,
to
provide
adequate
overlap
when
the
connecting
plug
is
withdrawn
or
inserted
.
Some
circuits
are
equipped
with
shorting
bars
(
see
internal
connections
in
Figure
9
)
,
and
on
those
circuits
it
is
especially
important
that
the
auxiliary
brushes
make
contact
,
as
indicated
in
Figure
8
,
with
adequate
pressure
to
prevent
the
opening
of
important
interlocking
circuits
.
The
relay
mechanism
is
mounted
in
a
steel
framework
called
the
cradle
,
and
is
a
This
cradle
is
held
complete
unit
with
all
leads
terminated
at
the
inner
blocks
,
firmly
in
the
case
with
a
latch
at
both
top
and
bottom
and
by
a
guide
pin
at
the
back
of
the
case
.
The
connecting
plug
,
besides
making
the
electrical
connections
between
the
respective
blocks
of
the
cradle
and
case
,
also
locks
the
latch
in
place
.
The
cover
,
which
is
drawn
to
the
case
by
thumbscrews
,
holds
the
connecting
plugs
in
place
.
The
target
-
reset
mechanism
is
part
of
the
cover
assembly
.
The
relay
case
is
suitable
for
either
semi
-
flush
or
surface
mounting
on
all
panels
up
to
two
inches
thick
and
appropriate
hardware
is
available
.
However
,
panel
thickness
must
be
indicated
on
the
relay
requisition
in
order
to
make
sure
that
proper
hardware
will
be
included
.
A
separate
testing
plug
can
be
inserted
in
place
of
the
connecting
plug
to
test
the
relay
in
place
on
the
panel
,
either
from
its
own
source
of
current
and
voltage
,
or
from
other
sources
.
Or
the
relay
can
be
drawn
out
and
replaced
by
another
that
has
been
tested
in
the
laboratory
.
Figure
1
A
and
IB
show
the
relay
removed
from
its
drawout
case
,
with
all
major
components
identified
.
Symbols
used
to
identify
circuit
components
are
the
same
as
those
that
appear
on
the
internal
connection
diagram
in
Figure
9
.
The
relay
includes
three
similar
mho
subassembly
elements
mounted
on
the
front
of
the
cradle
and
a
plate
with
transformers
and
transactors
mounted
on
the
back
of
the
cradle
.
The
mho
subassembly
includes
the
four
-
pole
unit
and
associated
circuit
components
.
Adjustable
reactors
XI
1
,
Xl
2
,
X
13
,
used
in
setting
the
angle
of
maximum
torque
,
and
rheostats
R
11
,
R
12
,
R
13
,
used
in
setting
the
basic
minimum
reach
,
can
be
adjusted
from
the
front
of
the
relay
.
The
transactors
(
TR
-
01
-
2
,
TR
-
02
-
3
,
TR
-
03
-
1
)
with
their
tap
blocks
are
mounted
on
the
back
.
The
relay
must
be
removed
from
its
case
to
make
the
transactor
(
or
minimum
ohm
)
settings
.
See
Figure
8
,
Cross
Section
of
Case
and
Cradle
Block
Showing
Auxiliary
Brush
and
Shorting
Bar
.
13
Courtesy of NationalSwitchgear.com

GEK
-
1275
RECEIVING
,
HANDLING
AND
STORAGE
These
relays
,
when
not
included
as
part
of
a
control
panel
,
will
be
shipped
in
cartons
designed
to
protect
them
against
damage
.
Immediately
upon
receipt
of
a
relay
,
examine
it
for
any
damage
sustained
in
transit
.
If
injury
or
damage
resulting
from
rough
handling
is
evident
,
file
a
damage
claim
at
once
with
the
transportation
company
and
promptly
notify
the
nearest
General
Electric
Sales
Office
.
Reasonable
care
should
be
exercised
in
unpacking
the
relay
in
order
that
none
of
the
parts
are
injured
nor
the
adjustments
disturbed
.
If
the
relays
are
not
to
be
installed
immediately
,
they
should
be
stored
in
their
original
cartons
in
a
place
that
is
free
from
moisture
,
dust
and
metallic
chips
.
Foreign
matter
collected
on
the
outside
of
the
case
may
find
its
way
inside
when
the
cover
is
removed
,
and
cause
trouble
in
the
operation
of
the
relay
.
ACCEPTANCE
TESTS
Immediately
upon
receipt
of
the
relay
,
an
inspection
and
acceptance
test
should
be
made
to
make
sure
that
no
damage
has
been
sustained
in
shipment
and
that
the
relay
calibrations
have
not
been
disturbed
.
indicates
that
readjustment
is
necessary
,
refer
to
the
section
on
SERVICING
.
If
the
examination
or
the
test
VISUAL
INSPECTION
Check
the
nameplate
stamping
to
make
sure
that
the
model
number
and
rating
of
the
rel
ay
agree
with
the
requisition
.
Remove
the
relay
from
its
case
and
check
that
there
are
no
broken
or
cracked
molded
parts
or
other
signs
of
physical
damage
,
and
that
all
screws
are
tight
.
MECHANICAL
INSPECTION
It
is
recommended
that
the
mechanical
adjustments
in
Table
VIII
be
checked
.
There
should
be
no
noticeable
friction
in
the
rotating
structure
of
the
units
.
Make
sure
control
springs
are
not
deformed
and
spring
convolutions
do
not
touch
each
other
.
1
.
2
.
3
.
With
the
relay
well
-
leveled
in
its
upright
position
,
the
contacts
of
all
three
units
must
be
open
.
The
moving
contacts
of
the
units
should
rest
against
the
backstop
.
The
armature
and
contacts
of
the
seal
-
in
unit
should
move
freely
when
operated
by
hand
.
There
should
be
at
least
1
/
32
inch
wipe
on
the
seal
-
in
contacts
.
Check
the
location
of
the
contact
brushes
on
the
cradle
and
case
blocks
against
the
internal
connection
diagram
for
the
relay
.
4
.
5
.
6
.
14
Courtesy of NationalSwitchgear.com

GEK
-
1275
TABLE
VIII
MHO
Units
Check
Points
Rotating
Shaft
End
Play
Contact
Gap
Contact
Wipe
0.010
-
0.015
inch
0.030
-
0.035
inch
0.003
-
0.005
inch
ELECTRICAL
CHECKS
-
MHO
UNIT
Before
any
electrical
checks
are
made
on
the
mho
units
,
the
relay
should
be
connected
as
shown
in
Figure
10
and
be
allowed
to
warm
up
for
approximately
15
minutes
with
the
potential
circuit
alone
energized
at
rated
voltage
and
the
restraint
taps
set
as
shown
in
Table
IX
.
The
units
were
warmed
up
prior
to
factory
adjustment
,
and
if
rechecked
when
cold
will
tend
to
underreach
by
3
%
or
4
%
.
Accurately
-
calibrated
meters
are
of
course
essential
for
correct
test
results
.
It
is
desirable
to
check
the
factory
setting
and
calibrations
by
means
of
the
tests
described
in
the
following
sections
.
The
mho
units
were
carefully
adjusted
at
the
factory
and
it
is
not
advisable
to
disturb
these
settings
unless
the
following
checks
indicate
conclusively
that
the
settings
have
been
disturbed
,
readjustments
are
necessary
,
refer
to
the
section
on
SERVICING
for
the
recommended
procedures
.
(
a
)
Control
-
Spring
Adjustment
If
Leave
the
relay
Be
sure
that
the
relay
is
level
connected
as
shorn
in
Figure
10
and
position
the
restraint
taps
according
to
Table
XII
.
in
its
upright
position
.
Use
the
following
procedure
in
checking
each
unit
.
With
the
current
set
at
5
amperes
and
the
voltage
across
the
relay
voltage
studs
at
120
volts
,
set
the
phase
shifter
so
that
the
phase
-
angle
meter
reads
the
value
shown
in
Table
IX
for
the
unit
being
tested
;
that
is
,
so
current
lags
voltage
by
an
angle
equal
to
the
angle
of
maximum
torque
of
the
unit
.
Now
reduce
the
voltage
to
the
low
test
voltage
of
2.0
volts
,
and
reduce
the
current
to
about
2
amperes
.
Gradually
increase
the
current
until
the
contacts
of
the
unit
just
close
.
This
should
occur
between
2.7
and
3.3
amperes
for
the
1.5
ohm
setting
or
10.1
and
12.4
for
the
0.4
ohm
setting
.
(
b
)
Clutch
Adjustment
The
mho
units
include
a
high
-
set
clutch
between
the
cup
-
and
-
shaft
assembly
and
the
moving
contact
to
prevent
damage
during
heavy
fault
conditions
.
These
clutches
have
been
set
at
the
factory
to
slip
at
approximately
40
-
60
grams
applied
tangentially
at
the
moving
contact
,
field
in
terms
of
volt
-
amperes
by
the
following
method
.
Use
the
connections
of
Figure
10
and
set
the
phase
shifter
so
that
the
phase
-
angle
meter
reads
300
o
at
120
volts
and
5
amperes
,
restraint
tap
leads
from
the
tap
block
and
short
to
stud
16
,
then
set
the
This
can
best
be
checked
in
the
Disconnect
the
No
.
1
15
Courtesy of NationalSwitchgear.com

GEK
-
1275
mho
units
for
3
-
ohm
basic
minimum
reach
,
relay
studs
set
at
120
volts
,
increase
the
current
until
the
clutch
just
slips
.
This
should
occur
between
35
and
55
amperes
.
On
short
range
0.375
/
1.5
ohms
(
or
0.2
ohms
)
,
set
the
tap
in
1.5
(
or
0.8
ohms
)
;
clutch
must
not
slip
below
60
amperes
.
With
the
voltage
across
the
TABLE
IX
OHMIC
REACH
ADJUSTMENT
TABLE
Phase
Connect
Lead
to
Relay
Jumper
Angle
VA
_
B
Studs
as
Follows
Relay
Meter
Set
Pickup
Lead
A
Lead
B
Lead
C
Lead
D
Studs
Reads
At
Amps
Unit
Loca
-
Unit
Tap
traint
Ohms
Tap
Reach
Res
-
tion
6
-
8
-
10
3000
45
V
14.6
-
15.4
6
-
8
-
10
3000
45
V
14.6
-
15.4
6
-
8
-
10
3000
45
V
14.6
-
15.4
Top
01
-
2
1.5
100
%
Middle
02
-
3
1.5
100
%
Bottom
03
-
1
1.5
100
%
14
-
15
13
-
16
-
17
5
13
-
16
-
17
18
-
19
-
20
7
18
-
19
-
20
14
-
15
7
9
9
5
6
-
8
-
10
3000
45
V
27.3
-
29.0
6
-
8
-
10
3000
45
V
27.3
-
29.0
6
-
8
-
10
3000
45
V
27.3
-
29.0
Top
01
-
2
0.4
50
%
14
-
15
13
-
16
-
17
5
Middle
02
-
3
0.4
50
%
13
-
16
-
17
18
-
19
-
20
7
Bottom
03
-
1
0.4
50
%
18
-
19
-
20
14
-
15
9
7
9
5
6
-
8
-
10
3000
90
V
14.5
-
15.4
6
-
8
-
10
3000
90
V
14.5
-
15.4
6
-
8
-
10
3000
90
V
14.5
-
15.4
Top
01
-
2
3.0
100
%
14
-
15
13
-
16
-
17
5
Middle
02
-
3
3.0
100
%
13
-
16
-
17
18
-
19
-
20
7
Bottom
03
-
1
3.0
100
%
18
-
19
-
20
14
-
15
9
7
9
5
6
-
8
-
10
3000
45
V
29.1
-
30.6
6
-
8
-
10
3000
45
V
29.1
-
30.6
6
-
8
-
10
3000
45
V
29.1
-
30.6
.
75
100
%
.
75
100
%
.
75
100
%
14
-
15
13
-
16
-
17
5
13
-
16
-
17
18
-
19
-
20
7
18
-
19
-
20
14
-
15
7
Top
0
l
-
2
Middle
02
-
3
Bottom
03
-
1
9
9
5
(
c
)
Ohmic
Reach
With
the
relay
still
connected
as
shown
in
Figure
10
,
make
connections
shown
in
Table
IX
and
set
the
phase
shifter
so
that
the
phase
-
angle
meter
reads
the
angle
shown
in
Table
IX
for
the
unit
to
be
checked
.
Now
reduce
the
voltage
to
the
value
shown
in
Table
IX
and
increase
the
current
gradually
until
the
normally
-
open
contacts
of
the
unit
just
close
.
This
should
occur
within
the
pickup
limits
shown
in
Table
IX
.
Note
that
the
tap
screws
on
the
transactor
tap
blocks
are
set
to
the
position
which
gives
the
basic
minimum
reach
shown
in
the
table
.
Note
that
for
the
test
conditions
,
the
mho
units
see
a
phase
-
to
-
phase
fault
of
twice
the
basic
minimum
reach
.
The
relays
are
normally
shipped
from
the
factory
with
the
basic
minimum
reach
adjustment
taps
of
the
units
(
on
the
back
of
the
relay
)
in
the
intermediate
16
Courtesy of NationalSwitchgear.com

GEK
-
1275
setting
,
that
is
,
1.5
ohms
or
0.4
ohm
(
the
value
shown
in
Table
IX
)
.
If
the
units
are
set
on
either
of
the
remaining
basic
minimum
reach
taps
,
the
basic
reach
of
the
units
will
be
within
+
4
%
of
the
tap
plate
marking
.
(
d
)
Angle
of
Maximum
Torque
For
checking
the
angle
of
maximum
torque
the
connections
of
Figure
10
will
be
used
with
the
restraint
tap
leads
,
and
the
voltage
,
set
at
the
value
shown
in
the
upper
and
lower
portions
,
respectively
,
of
Table
X
for
the
unit
to
be
checked
.
The
minimum
reach
taps
should
be
set
to
the
1.5
ohm
or
0.4
ohm
position
.
In
checking
the
mho
units
the
following
procedure
should
be
used
.
First
set
the
phase
shifter
so
that
the
phase
-
angle
meter
reads
330
°
.
Note
that
while
the
phase
angle
is
being
set
,
the
current
should
be
5
amperes
and
the
voltage
at
120
volts
.
Now
set
the
voltage
at
the
value
shown
in
Table
X
,
and
increase
the
current
slowly
until
the
mho
unit
picks
up
.
The
pickup
current
should
be
within
the
limits
shown
in
the
table
.
Now
reset
the
phase
angle
at
270
°
and
again
check
the
current
required
to
pick
up
the
mho
unit
.
This
current
should
fall
within
the
same
limits
as
for
the
330
°
check
.
330
°
and
2700
,
are
An
examination
of
the
mho
unit
Note
that
the
two
angles
used
in
the
previous
check
,
i
.
e
300
away
from
the
angle
of
maximum
torque
,
impedance
characteristic
in
Figure
6
shows
that
the
ohmic
reach
of
the
unit
should
be
the
same
at
both
330
°
and
2700
and
should
be
0.866
times
the
reach
at
the
angle
of
maximum
torque
.
•
*
TABLE
X
ANGLE
OF
MAXIMUM
TORQUE
ADJUSTMENT
TABLE
0
-
Anqle
Meter
Reading
Connect
Leads
to
Relay
Reach
Restraint
Jumper
Pickup
Angle
of
Relay
Studs
Test
VA
-
B
Set
At
Studs
as
Follows
Tap
Tap
Unit
Angles
Lead
A
Lead
B
Lead
C
Lead
D
Amps
+
Ohms
Max
.
Torque
Unit
Location
300
°
45
V
16.8
-
17.8
330
&
270
7
6
-
8
-
10
100
%
14
-
15
13
16
17
5
Top
012
1.5
300
°
16.8
-
17.8
330
&
270
45
V
9
6
-
8
-
10
Middle
100
%
13
16
17
18
-
19
-
20
7
02
3
1.5
300
°
45
V
16.8
-
17.8
330
&
270
18
19
20
14
-
15
9
5
6
-
8
-
10
1.5
100
%
Bottom
03
1
300
°
16.8
-
17.8
330
&
270
90
V
14
15
13
16
-
17
5
7
6
-
8
10
100
%
Top
01
2
3
0
300
°
16.8
-
17.8
330
&
270
90
V
7
9
6
-
8
-
10
Middle
100
%
13
16
-
17
18
-
19
-
20
02
-
3 3
0
300
°
16.8
-
17.8
330
&
270
90
V
5
6
-
8
-
10
18
19
20
14
-
15
9
03
1
3
0
100
%
Bottom
300
°
330
&
270
45
V
31.5
-
33.5
7
6
-
8
-
10
14
-
15
13
-
16
-
17
5
01
2
0.4
50
%
Top
300
°
31.5
-
33
5
330
&
270
45
V
13
16
17
18
19
20
7
9
6
-
8
-
10
Middle
0
4
50
%
02
3
300
°
31.5
-
33.5
330
&
270
45
V
5
6
-
8
-
10
50
%
18
-
19
-
20
14
15
9
03
1
0
4
Bottom
300
°
330
&
270
45
V
16.8
-
17.8
6
-
8
-
10
14
15
13
-
16
-
17
5
7
0
75
50
%
Top
01
2
300
°
16.8
-
17.8
330
&
270
45
V
7
9
6
-
8
-
10
Middle
50
%
13
16
17
18
19
20
02
3
0
75
300
°
45
V
16
8
17.8
330
&
270
14
15
9
5
6
-
8
-
10
0
75
50
%
18
-
19
-
20
Bottom
03
1
+
Pickup
amps
should
be
as
dose
to
equal
as
possible
for
the
330
o
&
270
o
tests
17
Courtesy of NationalSwitchgear.com

GEK
-
1275
ELECTRICAL
TESTS
-
TARGET
SEAL
-
IN
The
target
seal
-
in
unit
has
an
operating
coil
tapped
at
either
0.6
and
2.0
amperes
,
0.2
and
2.0
amperes
,
or
0.2
and
0.6
amperes
.
The
relay
is
shipped
from
the
factory
with
the
tap
screw
in
the
lower
ampere
position
.
The
operating
point
of
the
seal
-
in
unit
can
be
checked
by
connecting
from
DC
source
(
+
)
to
stud
11
of
the
relay
and
from
stud
1
through
an
adjustable
resistor
and
ammeter
back
to
(
-
)
.
Connect
a
jumper
from
stud
12
to
stud
11
also
,
so
that
the
seal
-
in
contact
will
protect
the
mho
unit
contacts
.
Then
close
the
mho
unit
contact
by
hand
and
increase
the
DC
current
until
the
seal
-
in
unit
operates
.
It
should
pick
up
at
tap
value
or
slightly
lower
.
Do
not
attempt
to
interrupt
the
DC
current
by
means
of
the
mho
contacts
.
INSTALLATION
PROCEDURE
LOCATION
The
location
of
the
relay
should
be
clean
and
dry
,
free
from
dust
,
excessive
heat
and
vibration
,
and
should
be
well
lighted
to
facilitate
inspection
and
testing
.
MOUNTING
The
relay
should
be
mounted
on
a
vertical
surface
,
drilling
dimensions
are
shown
in
Figure
14
.
The
outline
and
panel
CONNECTIONS
The
internal
connections
of
the
CEY
51
A
rel
ay
are
shown
in
Figure
9
.
elementary
diagram
of
typical
external
connections
is
shown
in
Figure
3
.
An
VISUAL
INSPECTION
Remove
the
relay
from
its
case
and
check
that
there
are
no
broken
or
cracked
component
parts
and
that
all
screws
are
tight
.
MECHANICAL
INSPECTION
Recheck
the
six
adjustments
mentioned
under
MECHANICAL
INSPECTION
in
the
section
on
ACCEPTANCE
TESTS
.
PORTABLE
TEST
EQUIPMENT
To
eliminate
the
errors
that
may
result
from
instrument
inaccuracies
,
and
to
permit
testing
the
mho
units
from
a
single
-
phase
AC
test
source
,
the
test
circuit
shown
in
schematic
form
in
Figure
12
is
recommended
.
In
this
figure
Rs
+
jXs
is
the
source
impedance
,
SF
is
the
fault
switch
,
and
R
|
_
+
JXL
is
the
impedance
of
the
line
section
for
which
the
relay
is
being
tested
,
across
the
fault
switch
and
line
impedance
,
is
tapped
in
10
%
and
1
%
steps
so
that
the
line
impedance
R
|
_
+
j
XL
may
be
made
to
appear
to
the
relay
very
The
autotransformer
TA
,
which
is
18
Courtesy of NationalSwitchgear.com
This manual suits for next models
2
Table of contents
Other GE Relay manuals
Popular Relay manuals by other brands
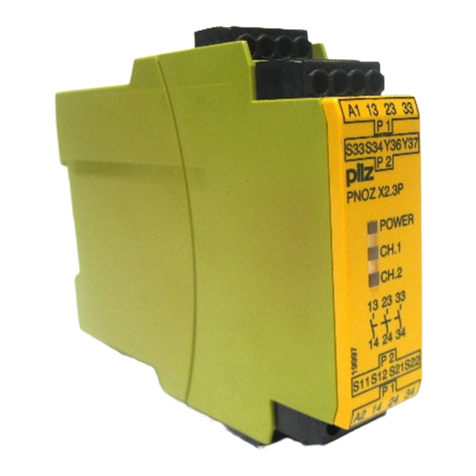
Pilz
Pilz PNOZ X2.3P operating instructions

ENGO CONTROLS
ENGO CONTROLS ERM12A quick guide
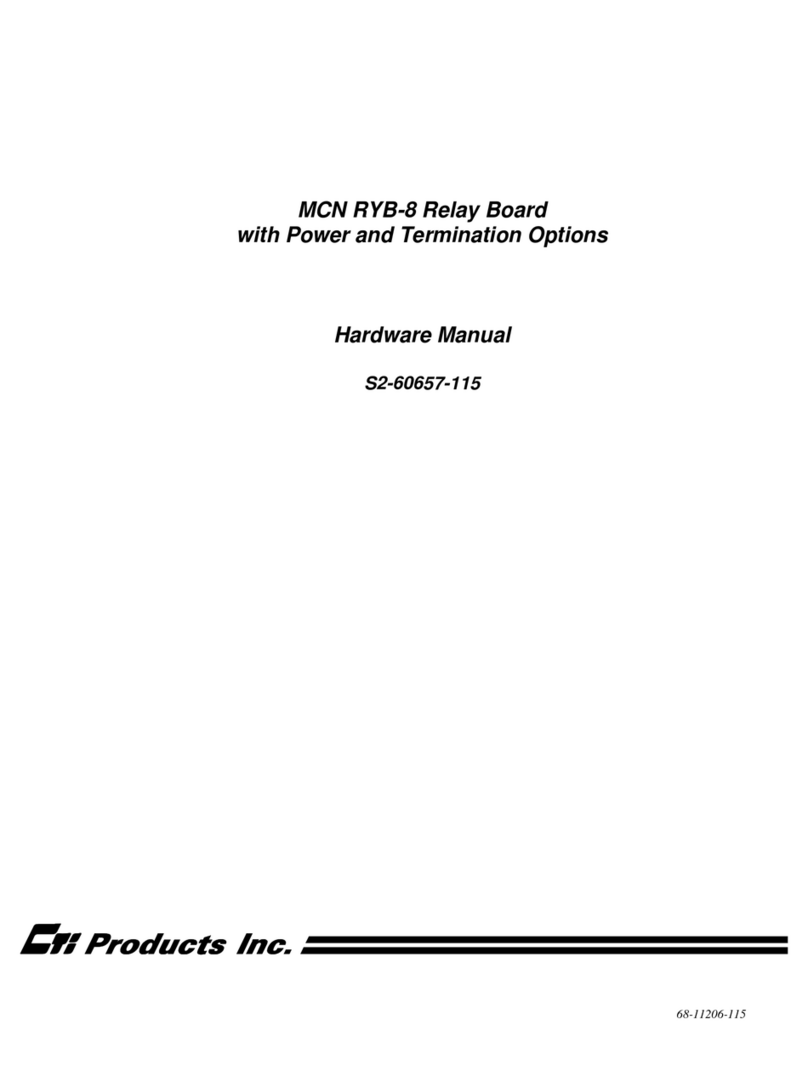
CTI Products
CTI Products MCN RYB-8 Hardware manual

Vitals
Vitals Rs 50k Manual For Technical Use
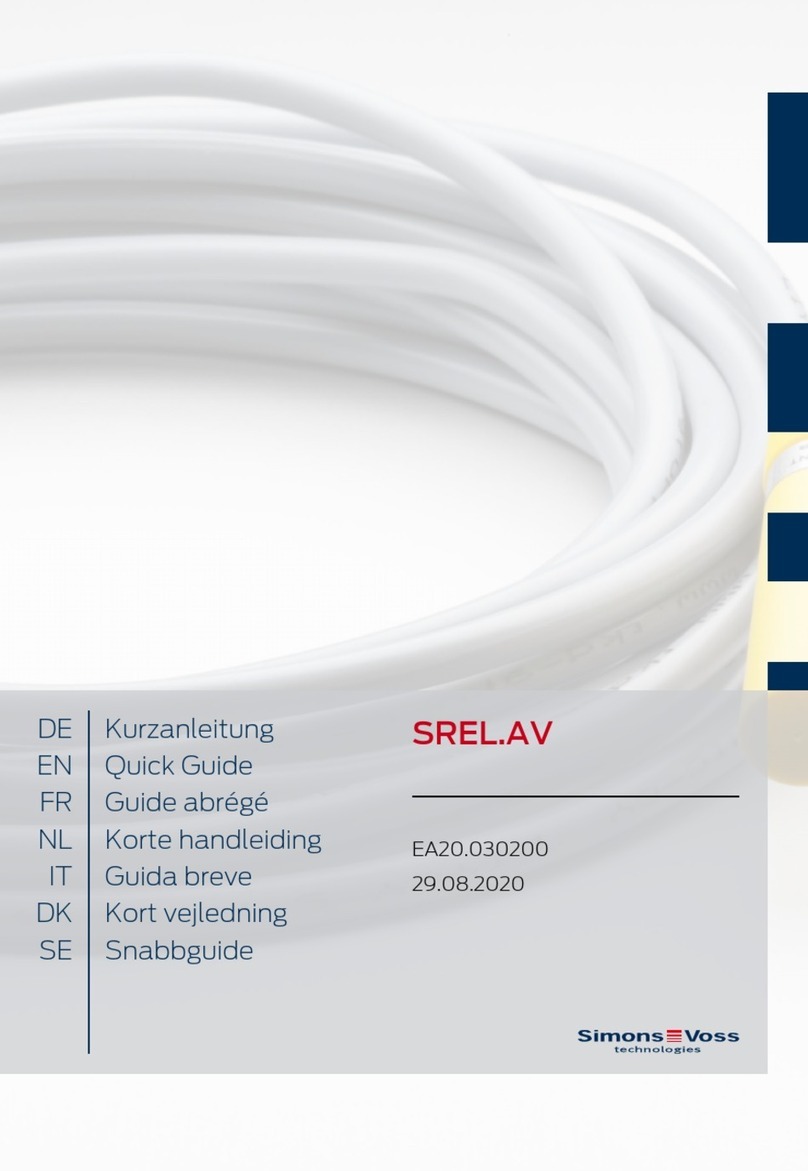
Simons Voss Technologies
Simons Voss Technologies SREL.AV quick guide
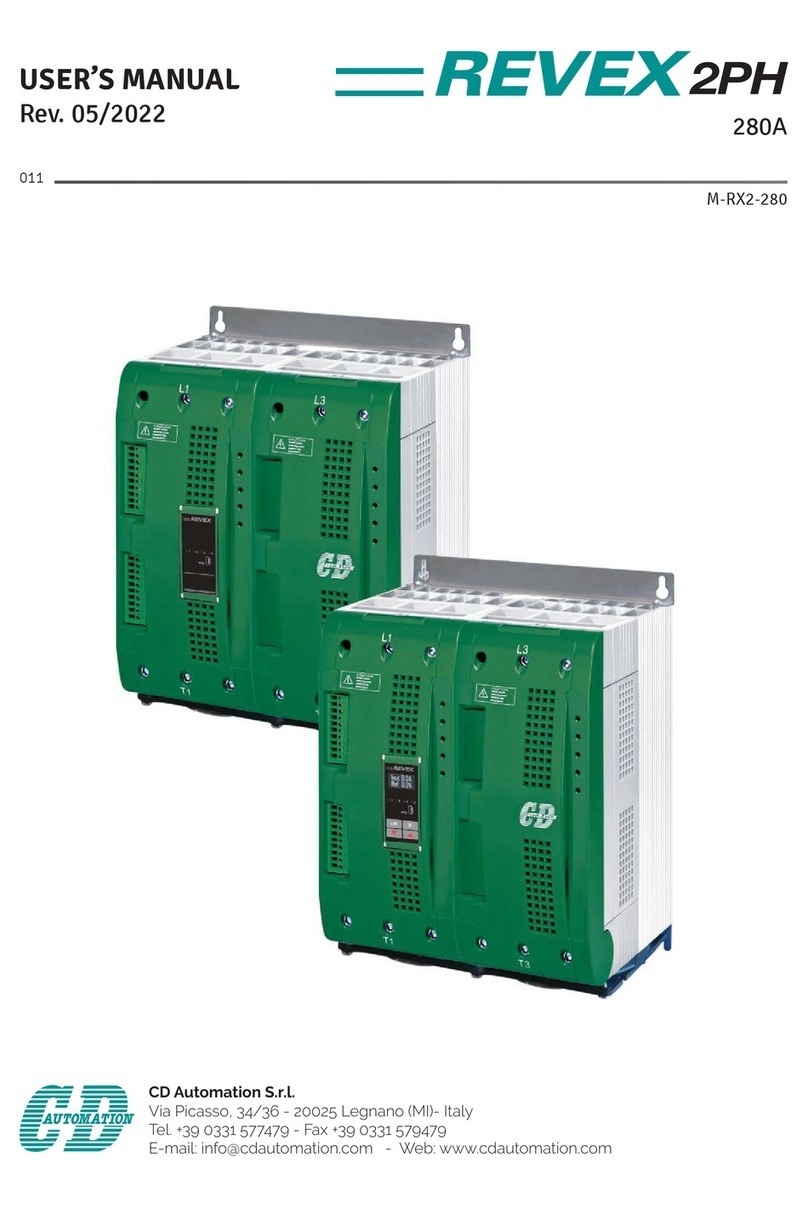
CD Automation
CD Automation REVEX 2PH RX2 280 Series user manual