GF 369 User manual

700278067 / GFDO 6025 / 05 (12.2021)
© Georg Fischer Piping System Ltd.
CH-8201 Schahausen/Schweiz
Printed in Switzerland
Phone +41 52 631 11 11/ info.ps@georgfischer.com
www.gfps.com
4 Safety Instructions
4.1 Explanations of Warning Symbols
Hazard notices are used in this instruction manual to warn you of
possible injuries or damages to property. Please read and abide by these
warnings at all times!
DANGER!
Imminent acute danger! Failure to comply could result in death or
extremely serious injury.
WARNING!
Possible acute danger! Failure to comply could result in serious injury.
CAUTION!
Dangerous situation! Failure to comply could lead to injury or damage to
property.
4.2 Requirements Placed on the User and Operator’s Due Care
It is the responsibility of the piping systems engineer / installer and of
the operator of such systems into which the wafer check valve is built to
warrant that:
►the wafer check valve is only used according to the specifications for
which it has been intended (see next paragraph),
►the piping system is installed by professionals and its functionality
checked regularly,
►only technical correct and functional wafer check valves must be
installed and the security advice is attended,
►only qualified and authorized personnel installs, operates, services
and repairs the wafer check valve,
►instruction of the employees is being held on a regular basis in all the
aspects of work safety and environmental protection – in particular
those to pressure-bearing piping,
►the employees are familiar with the instruction manual and adhere to
the information contained therein.
4.3 Intended Use
These GF wafer check valves type 369 are intended exclusively for
prevention the reflow of media in the allowable pressure and
temperature or for controlling flow in piping systems into which they
have been installed.
The wafer check valves are available with or without reset springs made
of stainless steel V4A or Hastelloy C. The valves are suitable for a
horizontal or vertical installation.
2 List of abbreviation
1 EC Manufacturer’s Declaration
The manufacturer GF Piping Systems, 8201 Schahausen (Switzerland)
declares that the industrial valves listed below do not fall within the
scope of the Pressure Equipment Directive 2014/68/EU (Art.4, Par.3) due
to the exclusion of their use with hazardous, flammable or gaseous
media and because of their nominal size and pressure rating, and
therefore may not bear the CE marking.
The commissioning of these industrial valves is prohibited until the entire
plant in which the industrial valves are installed has been declared to be
in conformity with the mentioned EC directive.
Product group Type designation Harmonized design
standards
Thermoplastic backflow
preventers
Wafer check valve
type 369
EN ISO 16137
Schahausen, 22.12.2021
Bastian Lübke
Head of Global R&D
Abbreviation Explanation
WCV Wafer check valve
Type 369 Wafer check valve type 369
DN Nominal diameter
PN Pressure rate
d Diameter
3 Congratulations on the purchase and delivery contents
The delivery contents include:
• Wafer Check Valve Type 369
• Instruction manual
• Supporting eyelet
• Reset spring, depending on the version
CAUTION!
►Wafer check valves are not recommended for media containing solids.
In control operations cavitations have to be avoided.
WARNING!
►The allowable pressure range for all allowable temperatures for every
housing material is illustrated in diagrams in the «Georg Fischer
Planning Fundamentals»(Chapter wafer check valves). This
documentation also contains the «Chemical Resistance List» for the
dierent type of valve materials.
4.4 Special Hazards
DANGER!
►Pressure strokes have to be avoided, because they can cause
damages on the valve.
The following hazardous situations may occur during dismounting of the
check valve:
DANGER!
►the medium may exit uncontrollably from the pipe or the valve,
whether under pressure or not,
►the medium may flow out of the open pipe,
►the valve may contain residues or remnants of aggressive, hazardous,
flammable or explosive media.
Therefore prior opening the pipe and dismounting the valve, it is
necessary to:
►remove all pressure from the piping system,
►empty the piping system completely,
►rinse the piping system, if aggressive, hazardous, flammable or
explosive media are inside the system,
►to drain the wafer check valve completely when it has been
dismounted. For that, put the valve in vertical position and drain it
completely until it is empty.
4.5 Transport and Storage
The wafer check valve must be handled, transported and stored with
care:
►Transport and store the wafer check valves in its original packaging.
►If the wafer check valve needs to be stored before installation, it must
be protected from harmful influences such as dirt, dust, humidity,
especially heat and UV radiation.
►The connecting ends of the wafer check valve in particular may not be
damaged mechanically or in any other way.
5 Installation in the Piping System
5.1 Note for the Installation
As connecting part we recommend socket flange adaptor or butt fusion
flange adaptor in connection with flanges of PVC-U, PP-V or PP/steel.
WARNING!
►The wafer check valve is approved for PN6.
►No direct installation on pump flange or bend allowed.
CAUTION!
►Torques for fastening has to be taken out of paragraph 5.5.
►The selection of the connection elements must be taken out of the
technical documentation.
►Make sure that only wafer check valves will be installed which
correspond to the pressure class, type of connection, dimension and
materials of the particular application.
►A stabilization zone of at least 5 times nominal diameter (DN) should
be provided before and after the wafer check.
►Carry out a functional test: close the wafer check valve and open it
again.
►Don’t install a wafer check valve which has a functional failure.
5.2 Important Notes on connecting elements
Components and tightening torques can be determined via the online tool
„Perfect flange connection“ at the following link:
https://www.gfps.com/perfectflangeconnection
CAUTION!
• PVC-U
The using of PVC-U pipe PN16 is only possible up to d63. Pay attention on
installation between ISO/ANSI/BS flange adaptors. The WCV DN32 does
not fit together with ANSI/BS flange adaptors. For wafer check valve in
the dimensions DN40 to DN80 and DN200 the next larger size of ANSI/BS
flange adapter has to be used (example: a DN40 valve has to be mounted
between DN50 and DN150 ISO/ANSI/BS flange adaptors).
For dimensions DN100 and DN150, PP-GF flanges must be used.
• PP and PE
To ensure the proper function of the valve in PP and PE piping systems, a
suitable outlet adaptor is required on the outlet side. The outlet adaptor
can be used in the same way as the respective check valve dimension.
Please contact your local GF sales representative for further information.
• PVDF
GF recommends for PVDF piping systems the use of a fusion neck one
size larger than the pipeline or the use of a wafer check valve one size
smaller than the pipe (example: two d110 fusion necks should be used
for the wafer check valve d90).
1
2
3
4
5
43
26
1 = screw and washer
2 = flange
3 = socket flange adaptor / butt fusion flange adaptor
4 = special flange gasket
5 = wafer check valve type 369
6 = nut and washer
5.3 Description of Installation
Before installing
• Keep enough space between both flanges.
• Function and tightness testing (reset spring and seals).
• Fixing of supporting eylet in the provided thread .
While installing
• Put the wafer check valve in closed position.
• Attention on the wanted flow direction.
• Move the wafer check valve with the seals between both flange ends.
• Realign the pipeline. Make sure that the disc can be fully opened
and that the disk attach on the inner pipe wall.
• Fasten the wafer check valve with flange screws (see chapter 5.5).
After installing
• Do another functional test.
• Carry out an leakage test.
5.4 Possible Faults and Problems During Installation
5.6 Centering and Opening Angle of The Valve
CAUTION!
Make sure that the disk attach on the inner pipe wall. It is not allowed
that the disk attach on the limit stop of the valve.
The geometry of the wafer check valve ensures an optimal positioning
and mounting between ISO/DIN and also of ANSI/BS flange adapters.
The supporting eylets will help during centering the valve.
Faults/Problems Reason Eect Solution
WCV does not fit between
the flanges
• Wrong dimensioning
• Flange ends are too close
to each other
Installation not possible • Selection of the correct dimension on base of
the technical documentation
• Press apart flanges with spreader
Disc does not open • Disc larger as the opening
of the chosen adaptor
• Incorrect centring
No flow possible after
installation
• Selection of the correct dimension on base of
the technical documentation
• Demounting and chamfer of the pipe
• Correct centring
Disc does not attach on the
inside of the pipe
• Incorrect centring
• Wrong dimensioning
Disc could break • Correct centring
• Selection of the correct dimension on base of
the technical documentation
Other problems during
installation
• Wrong dimensioning of the
components
Installation not possible • Selection of the correct dimension on base of
the technical documentation
5.5 Standard Values for the Screw Fixing
ISO/DIN flange adaptors
WCV dimension
[DN] flange dimension
[DN] flange dimension
[d] quantity of screws screw dimension
[ISO] torque
[Nm] torque
[lbf in]
DN32 DN32 40 4 M16 x 85 mm 15 133
DN40 DN40 50 4 M16 x 85 mm 15 133
DN50 DN50 63 4 M16 x 95 mm 20 177
DN65 DN65 75 4 M16 x 100 mm 25 221
DN80 DN80 90 8 M16 x 110 mm 25 221
DN100 DN100 110 8 M16 x 130 mm 30 266
DN125 DN125 140 8 M16 x 130 mm 35 310
DN150 DN150 160 8 M20 x 180 mm 40 354
DN200 DN200 225 8 M20 x 180 mm 50 442
DN250 DN250 280 12 M20 x 180 mm 55 487
DN300 DN300 315 12 M20 x 180 mm 60 531
ANSI/BS flange adaptors , PVC-U wafer check valves only
WCV dimension
[DN] flange dimension [Inch] flange dimension
[d] quantity of screws screw dimension
[ANSI/BS] torque
[Nm] torque
[lbf in]
DN40 2“ 50 4 UNC5/8“ x 3 1/2“ 20 177
DN50 2 1/2“ 63 4 UNC5/8“ x 4“ 25 221
DN65 3“ 75 4 UNC5/8“ x 4“ 25 221
DN80 4“ 90 8 UNC5/8“ x 4 1/2“ 30 266
DN100 4“ 110 8 UNC5/8“ x 4 1/2“ 30 266
DN150 6“ 160 8 UNC3/4“ x 5 40 354
DN200 8“ 225 8 UNC3/4“ x 6“ 50 442
DN250 10“ 280 12 UNC7/8“ x 6 1/2“ 55 487
DN300 12“ 315 12 UNC7/8“ x 7“ 60 531
Wafer check valve PVC-U
• Centring on ISO/DIN adaptors over the cut-out
• Centring on ANSI/BS over the external diameter of the valve
Wafer check valves PP and PVDF
• Centring over the external diameter of the valve
Cut-out
ANSI/BS flange adaptors External diameter ISO/DIN flange adaptors
6 Normal Operation and Maintenance
Normally the wafer check valves don’t need maintenance. It is enough to
control periodically, if there is a leakage. If you have a leakage in
the flange connections, refasten these acc. to the table in chapter 5.5 or if
it is necessary replace the flange gaskets.
7 Pressure Test and Commissioning
CAUTION!
►For pressure testing of the wafer check valve use the same
instructions as for the piping system.
WARNING!
►Check all valves if they are in the required open or closed position.
►Fill the piping system and bleed it completely.
►Pressure may not exceed the value of 1.5 x PN.
►During the pressure test the valves and connections should be
checked for leackages.
CAUTION!
Maximum permissible test pressure!
For the pressure test of valves in open position, the same instructions
apply as for the piping system (max. 1.5 x PN, and max. PN + 5 bar), but
the test pressure in closed valve position must not exceed max. 1.1 x PN.
►For detailed information, see the Georg Fischer Planning Fundamen-
tals.
►After successful pressure test: Remove test medium.
►Record the results.
8 Help in Case of Failures
In case of failures please consider paragraph 4.1 to 4.5. If there is a
leakage in the pipe or to the outside, dismount the wafer check valves
and replace defect gaskets. Orders for spare parts for the waver check
valve should include a detailed specification, i.e. details given on the type
plate. Only the prescribed original spare parts from GF may be used.
Kind of failure Measures
Leakage on the outside of the
flange adaptor Connection retightening
Leakage in the pass Demounting of the valve and replace the
disc and sealing. Order spare parts with the
description from the type label
Other function failures Displace the sealings
Order spare parts with the description from
the type label
Handling of sealings
CAUTION!
►All sealings (material e.g. EPDM, FKM) are of organic materials and
react to environment influences. They must be stored in their original
packing if possible in a cool,
dry and dark place. The sealings have to be assayed on possible
ageing damages as fissures and hardenings before installing.
►Damaged sealings and spare parts must not come into operation.
Choice of the lubricant
CAUTION!
►The use of inadequate lubricants can aect the material of the wafer
check valve or of the sealings. Lubricants on the base of mineral oil or
of Vaseline (petrolatum) must not
be used at all. For clean silicone-free wafer check valves we refer to
the special manufacturer’s information.
►All sealings need to be lubricated with lubricants on the base of
silicone or polycole. Other lubricants are not allowed!
Piping strengths, especially these caused by thermal expANSI/BSon,
could be the reason for the malfunction. The support of the piping should
be improved.
If there is a indication after dismounting, that the materials of the body,
the disc or the sealings are not resistant enough, choose a better suited
material from the chemical resistance list, which you will find in our
planning fundamentals.
9 Additional Information
The above mentioned Planning Fundamentals may be obtained from the
GF sales company responsible for your country or from the internet at:
www.gfps.com
The technical data are not binding.
They are not expressly warranted characteristics of the goods and are
subject to change.
Please consult our General Conditions of Supply.
Many thanks that you have decided for the purchase of a Wafer Check
Valve Type 369 from GF Piping Systems.
Please take some time to read carefully this Instruction Manual. It
contains important information and useful tips.
Wafer Check Valve
Type 369
Operating Instructions

1
2
3
4
5
43
26
4 Sicherheitshinweise
4.1 Erläuterung der Symbole
In dieser Anleitung werden Warnhinweise verwendet, um Sie vor
Verletzungen oder vor Sachschäden zu warnen. Lesen und beachten Sie
diese Warnhinweise immer!
GEFAHR!
Unmittelbar drohende Gefahr! Bei Nichtbeachtung drohen Tod oder
schwerste Verletzungen.
WARNUNG!
Möglicherweise drohende Gefahr! Bei Nichtbeachtung drohen schwere
Verletzungen
VORSICHT!
Bei Nichtbeachtung drohen leichte Verletzungen oder Sachschäden
4.2 Anforderungen an den Anwender und Sorgfaltspflicht des
Betreibers
Es unterliegt der Verantwortung des Planers / Installateurs von
Rohrleitungssystemen und des Betreibers solcher Anlagen, in welche die
Rückschlagklappe eingebaut ist, sicherzustellen, dass:
►die Rückschlagklappe nur bestimmungsgemäss verwendet wird [siehe
nächsten Abschnitt],
►das Rohrleitungssystem fachgerecht verlegt ist und regelmässig auf
seine Funktionstüchtigkeit überprüft wird,
►die Rückschlagklappe nur in technisch einwandfreiem, funktionstüch-
tigem Zustand eingebaut wird und diese Sicherheitshinweise beachtet
werden.
►Einbau, Bedienung, Wartung und Reparatur nur durch autorisiertes
Fachpersonal durchgeführt wird,
►eine regelmässige Personalunterweisung in Arbeitssicherheit und
Umweltschutz – insbesondere für druckführende Rohrleitungen –
stattfindet,
►das Personal die Betriebsanleitung kennt und die darin enthaltenen
Hinweise beachtet.
4.3 Bestimmungsgemässe Verwendung
Die GF Rückschlagklappen Typ 369 sind ausschliesslich dazu bestimmt,
nach Einbau in ein Rohrleitungssystem, das Zurückfliessen von Medien
innerhalb der zugelassenen Druck- und Temperatur-Grenzen zu
verhindern.
Die Rückschlagklappen sind ohne oder mit Rückstellfeder aus V4A oder
Hastelloy erhältlich. Sie eignen sich für einen horizontalen oder
vertikalen Einbau.
2 Abkürzungsverzeichnis
1 EG-Herstellererklärung
Der Hersteller GF Rohrleitungssysteme AG, 8201 Schahausen (Schweiz)
erklärt, dass die nachfolgend genannten Industriearmaturen durch den
Ausschluss, diese bei gefährlichen, brennbaren oder gasförmigen
Medien einzusetzen, aufgrund von Nennweite und Druckstufe nicht in den
Geltungsbereich der Druckgeräterichtlinie 2014/68/EU fallen (Art.4,
Abs.3) und somit die CE-Kennzeichnung nicht tragen dürfen.
Die Inbetriebnahme dieser Industriearmaturen ist so lange untersagt, bis
die Konformität der Gesamtanlage, in die die Industriearmaturen
eingebaut sind, mit der genannten EG-Richtlinie erklärt ist.
Produktgruppe Typenbezeichnung Harmonisierte
Bauart-Normen
Rückflussverhinderer
aus Thermoplasten
Rückschlagklappe
Typ 369
EN ISO 16137
Schahausen, 22.12.2021
Bastian Lübke
Head of Global R&D
Abkürzung Bedeutung
RSK Rückschlagklappe
Typ 369 Rückschlagklappe Typ 369
DN Nenndurchmesser
PN Nenndruck
d Durchmesser
3 Gratulation zum Kauf und Lieferumfang
Vielen Dank, dass Sie sich für den Kauf einer Rückschlagklappe Typ 369
von GF Piping Systems entschieden haben.
Bitte nehmen Sie sich etwas Zeit, um diese Bedienungsanleitung
aufmerksam durchzulesen. Sie enthält wichtige Hinweise und nützliche
Tipps.
Im Lieferumfang sind enthalten:
• Rückschlagklappe Typ 369
• Bedienungsanleitung
• Halteöse
• Je nach Ausführung evtl. Rückstellfeder
VORSICHT!
►Rückschlagklappen werden für Medien mit Feststoen nicht
empfohlen. Im Regelbetrieb ist Kavitation zu vermeiden.
WARNUNG!
►In den «Georg Fischer Planungsgrundlagen» [Kapitel Rückschlagklap-
pen] ist für jeden Gehäusewerksto der zugelassene Druckbereich für
alle zugelassenen Temperaturen beschrieben.
►In diesen Unterlagen ist auch die «Chemische Widerstandsfähigkeits-
liste» für die unterschiedlichen Armaturenwerkstoe enthalten.
4.4 Besondere Arten von Gefahren
GEFAHR!
►Druckschläge vermeiden, da diese zur Beschädigung des Gerätes
führen können.
Beim Ausbau der Rückschlagklappe können folgende Gefahren auftreten:
GEFAHR!
►unkontrolliertes Austreten des Mediums aus der Leitung oder der
Rückschlagklappe, unter Druck oder drucklos,
►nachfliessen des Mediums aus der oenen Leitung,
►Rückstände oder Reste eines aggressiven, gesundheitsschädlichen,
brennbaren oder explosiven Mediums in der Armatur.
Daher muss vor dem Önen der Leitung und dem Ausbau der
Rückschlagklappe:
►der Druck in der Rohrleitung vollständig abgebaut sein,
►die Rohrleitung vollständig entleert sein,
►bei aggressiven, gesundheitsschädlichen, brennbaren oder explosiven
Medien die Leitung gespült sein,
►nach dem Ausbau muss die Rückschlagklappe vollständig entleert
werden. Dazu die Rückschlagklappe in senkrechter Lage vollständig
leer laufen lassen.
4.5 Transport und Lagerung
Die Rückschlagklappe muss sorgfältig behandelt, transportiert und
gelagert werden. Hierzu sind folgende Punkte zu beachten:
►Die Rückschlagklappe ist in ihrer Originalverpackung zu transportie-
ren und zu lagern.
►Wenn die Rückschlagklappe vor dem Einbau gelagert werden muss,
ist sie vor schädlichen Einflüssen wie Staub, Schmutz, Feuchtigkeit
und insbesondere vor Wärme- und UV-Strahlung zu schützen.
►Unmittelbar vor der Montage ist die Rückschlagklappe auf
Transportschäden hin zu untersuchen.
5 Einbau in die Rohrleitung
5.1 Hinweise für den Einbau
Als Anschlusselemente empfehlen wir Bundbuchsen oder Vorschweiss-
bunde in Verbindung mit Flanschen aus PVC-U, PP-V oder PP-Stahl.
WARNUNG!
►Die Rückschlagklappe ist nur für PN6 zugelassen
►Keine direkte Montage auf Pumpenflansch oder nachfolgenden Bogen
VORSICHT!
►Anzugsmomente für den Einbau sind der Tabelle in Kapitel 5.5 zu
entnehmen.
►Die Auswahl der Anschlusselemente muss nach Anweisung der
technischen Dokumentation erfolgen.
►Stellen Sie sicher, dass nur Rückschlagklappen eingebaut werden,
deren Druckklasse, Anschlussart, Anschluss-abmessungen und
Werkstoe den Einsatzbedingungen entsprechen.
►Vor und nach der Rückschlagklappe ist eine Beruhigungszone von
mindesten 5x dem Nenndurchmesser (DN) einzuplanen.
►Führen Sie vor dem Einbau eine Funktionsprobe durch, indem Sie die
Rückschlagklappe schliessen und wieder önen.
►Bauen Sie keine Rückschlagklappe mit Funktionsstörung ein.
5.2 Wichtige Hinweise zu Anschlusselementen
Komponenten und Anzugsmomente können über das Online Tool
„Perfekte Flanschverbindung“ unter folgendem Link ermittelt werden:
httpd://gfps.com/perfectflangeconnection.
VORSICHT!
• PVC-U
Die Verwendung mit PVC-U-Rohren PN16 ist nur bis d63 möglich. Bei der
Montage zwischen ISO/ANSI/BS Bundbuchsen ist zu beachten, dass
Rückschlagklappen der Dimension DN32 nicht geeignet sind und dass für
die Rückschlagklappendimensionen DN40 bis DN80 und DN200 die
nächst grössere ANSI/BS Bundbuchsendimension verwendet werden
muss (Beispiel: Montage einer DN40 Rückschlagklappe zwischen DN50
ISO/ANSI/BS Bundbuchsen).
Für die Dimensionen DN100 und DN150 müssen PP-GF Flansche
verwendet werden.
• PP und PE
Um eine einwandfreie Funktion der Armatur zu gewährleisten, muss bei
Rohrleitungssystemen aus PP und PE abgangsseitig eine geeignete
Austrittshilfe verwendet werden. Die Austrittshilfen können gleich wie
die jeweilige Rückschlagklappendimension verwendet werden.
Bitte kontaktieren Sie Ihren lokalen GF Verkaufsberater für weitere
Informationen.
• PVDF
GF empfiehlt PVDF-Vorschweissbunde der jeweils nächst grösseren
Dimensionierung oder eine Rückschlagklappe in der nächst kleineren
Durchmesserstufe. (Bsp.: Rückschlagklappe d90 mit zwei
Vorschweissbunden d110).
1 = Schraube und Unterlegscheibe
2 = Flansch
3 = Bundbuchse/Vorschweissbund
4 = Flanschdichtung
5 = Rückschlagklappe TYP 369
6 = Muttern und Unterlegscheiben
5.3 Einbaubeschreibung
Vor dem Einbau
• Genügend Abstand zwischen den Flanschenden vorsehen.
• Funktion und Dichtheit der RSK (Rückstellfeder und Dichtungen)
überprüfen.
• Halteöse in der vorgesehen Bohrung befestigen.
Beim Einbau
• Rückschlagklappe im geschlossenen Zustand halten.
• Gewünschte Durchflussrichtung beachten.
• Rückschlagklappe mit den Dichtungen zwischen die Rohrenden
schieben.
• Rohrleitungen ausrichten und sicherstellen, dass die Klappe sich
nach dem Einbau optimal önen lässt und an der Rohrinnenwand
anschlägt.
• Rückschlagklappen mittels Flanschschrauben festschrauben.
Nach dem Einbau
• Erneute Funktionsüberprüfung durchführen.
• Leckageüberprüfung durchführen.
5.4 Mögliche Fehler und Probleme beim Einbau
5.6 Zentrierung und Önungswinkel des Tellers
VORSICHT!
Der Teller der eingebauten Rückschlagklappe darf nicht am oberen
Anschlag des Gehäuses der RSK anstehen. Er muss gegen die
Anschlussrohrinnenseite an der Austrittseite anschlagen.
Durch die Geometrie der Rückschlagklappe ist eine optimale
Positionierung und Einbau zwischen ISO/DIN als auch für ANSI/BS
Anschlusselementen gewährleistet. Die Halteöse dient als Hilfsmittel zur
Zentrierung.
Fehler/Problem Fehlerursache Folge Lösung
RK passt nicht zwischen die
Flansche
• Falsche Dimensionierung
• Flansche stehen zu eng
zusammen
Montage nicht möglich • Auswahl der richtigen Dimension anhand der
technischen Dokumentation.
• Flansche mit Spreizgerät auseinanderdrücken
Teller önet nicht
> kein Durchfluss
• Teller grösser als Önung
des gewählten Anschlusses
• Zentrierung fehlerhaft
Nach Montage kein Durchfluss
möglich
• Auswahl der richtigen Dimensionierung anhand
der technischen Dokumentation
• Demontage und Anfasung des Rohres
• Richtig zentrieren
Teller schlägt nicht an
Rohrinnenseite an
• Zentrierung fehlerhaft
• Falsche Dimensionierung
Teller kann nach einiger
Betriebszeit abbrechen
• Richtig zentrieren
• Auswahl der richtigen Dimension anhand der
technischen Dokumentation
Sonstige Probleme beim
Aufbau
• Falsche Dimension der
Bauteile
Montage nicht möglich • Auswahl der richtigen Dimensionierung anhand
der technischen Dokumentation
5.5 Richtwerte für die Schraubbefestigung
ISO/DIN Anschlusselemente
RSK Dimension
[DN] Flansch Dimension
[DN] Flansch Dimension
[d] Gesamtanzahl
der Schrauben Schraubendimension
[ISO] Drehmoment
[Nm] Drehmoment
[Ibf in]
DN32 DN32 40 4 M16 x 85 mm 15 133
DN40 DN40 50 4 M16 x 85 mm 15 133
DN50 DN50 63 4 M16 x 95 mm 20 177
DN65 DN65 75 4 M16 x 100 mm 25 221
DN80 DN80 90 8 M16 x 110 mm 25 221
DN100 DN100 110 8 M16 x 130 mm 30 266
DN125 DN125 140 8 M16 x 130 mm 35 310
DN150 DN150 160 8 M20 x 180 mm 40 354
DN200 DN200 225 8 M20 x 180 mm 50 442
DN250 DN250 280 12 M20 x 180 mm 55 487
DN300 DN300 315 12 M20 x 180 mm 60 531
ANSI/BS Anschlusselemente, nur für PVC-U Rückschlagklappen
RSK Dimension
[DN] Flansch Dimension
[Zoll] Flansch Dimension [d] Gesamtanzahl
der Schrauben Schraubendimension
[ANSI/BS] Drehmoment
[Nm] Drehmoment
[Ibf in]
DN40 2“ 50 4 UNC5/8“ x 3 1/2“ 20 177
DN50 2 1/2“ 63 4 UNC5/8“ x 4“ 25 221
DN65 3“ 75 4 UNC5/8“ x 4“ 25 221
DN80 4“ 90 8 UNC5/8“ x 4 1/2“ 30 266
DN100 4“ 110 8 UNC5/8“ x 4 1/2“ 30 266
DN150 6“ 160 8 UNC3/4“ x 5 40 354
DN200 8“ 225 8 UNC3/4“ x 6“ 50 442
DN250 10“ 280 12 UNC7/8“ x 6 1/2“ 55 487
DN300 12“ 315 12 UNC7/8“ x 7“ 60 531
RSK aus PVC-U
• Zentrierung bei ISO/DIN Anschlusselemente über die
Aussparungen.
• Zentrierung bei ANSI/BS über den Aussendurchmesser.
RSK aus PP und PVDF
• Zentrierung bei ISO/DIN Anschlusselemente über den
Aussendurchmesser.
Aussparung
ANSI/BS- Anschlusselemente Aussendurchmesser ISO-DIN Anschlusselemente
6 Normalbetrieb und Wartung
Rückschlagklappen benötigen im normalen Betrieb keine Wartung.
Es reicht aus, periodisch zu überprüfen, ob nach aussen kein Medium
austritt. Tritt Medium an den Flanschverbindungen aus, diese gemäss
Tabellen in Kapitel 5.5 nachzuziehen bzw. ggf. die Flanschdichtungen
zu ersetzen.
7 Druckprobe und Inbetriebnahme
VORSICHT!
►Für die Druckprobe der Rückschlagklappe gelten die gleichen
Anweisungen wie für die Rohrleitungen.
WARNUNG!
►Kontrolle, ob alle Armaturen in der erforderlichen Oen- oder
Geschlossenstellung sind.
►Leitungssystem füllen und vollständig entlüften.
►Maximal zulässigen Prüfdruck nicht überschreiten.
►Während der Druckprobe sind Armaturen und Anschlüsse auf
Dichtheit zu prüfen.
VORSICHT!
Maximal zulässiger Prüfdruck!
Für die Druckprobe von Ventilen in Oenstellung gelten dieselben
Anweisungen wie für die Rohrleitungen (max. 1.5 x PN, bzw. max. PN + 5
bar), jedoch darf der Prüfdruck in Geschlossenstellung max. 1.1 x PN
nicht überschreiten.
►Detaillierte Informationen, siehe Georg Fischer Planungsgrundlagen
Industrie.
►Nach erfolgreicher Dichtheitsprüfung: Prüfmedium entfernen.
►Ergebnisse protokollieren.
8 Hilfe bei Störungen
Bei Störung unbedingt die Kapitel 4.1 bis 4.5 beachten. Bei Undichtheit im
Durchgang oder nach aussen, können Rückschlagklappen ausgebaut und
beschädigte Dichtungen ausgetauscht werden. Ersatzteile für
Rückschlagklappen sind mit vollständiger Spezifikation, z. B. allen
Angaben des Typenschildes zu bestellen. Es dürfen ausschliesslich
Originalteile von GF eingebaut werden.
Art der Störung Massnahmen
Leckage nach aussen an
Flanschverbindung Verbindung nachziehen
Leckage im Durchgang Armatur ausbauen, Teller und Dichtung
ersetzten.
Ersatzteile mit Angaben im Typenschild
bestellen
Sonstige Funktionsstörrungen Dichtungen und gegebenenfalls
Funktionsteile ersetzen. Ersatzteile mit
Angaben im Typenschild bestellen
Handhabung der Dichtungen
VORSICHT!
►Alle Dichtungen (Material z. B. EPDM, FKM) sind organische Werkstoe
und reagieren auf Umwelteinflüsse. Sie müssen daher in ihrer
Originalverpackung möglichst kühl, trocken und dunkel gelagert
werden. Die Dichtungen sind vor dem Einbau auf mögliche
Alterungsschäden wie Anrisse und Verhärtungen zu prüfen.
►Schadhafte Dichtungen und Ersatzteile dürfen nicht zum Einsatz
gelangen.
Schmiermittelauswahl
VORSICHT!
►Der Einsatz ungeeigneter Schmiermittel kann den Werksto der
Rückschlag oder der Dichtungen angreifen. Es dürfen keinesfalls
Schmiermittel auf Mineralölbasis oder Vaseline (Petrolatum)
verwendet werden.
►Alle Dichtungen sind mit Fett auf Silikon- oder Polykolbasis zu
schmieren. Andere Schmierstoe sind nicht zulässig!
Rohrleitungskräfte, besonders solche aus behinderter Wärmedehnung,
können die Störungsursache sein. Die Abstützung der Rohrleitung sollte
verbessert werden.
Wird nach dem Ausbau festgestellt, dass die Werkstoe des Gehäuses,
des Tellers oder der Dichtung nicht genügend beständig sind, geeignete
Werkstoe aus der Liste «Chemische Widerstandsfähigkeit» auswählen.
9 Weitere Informationen
Die im Text erwähnten Planungsgrundlagen und Ersatzteile erhalten Sie
bei Ihrer zuständigen GF Verkaufsgesellschaft in ihrem Land oder im
Internet unter www.gfps.com
Die technischen Daten sind unverbindlich.
Sie gelten nicht als zugesicherte Eigenschaften oder als Beschaenheits-
oder Haltbarkeitsgarantien. Änderungen vorbehalten.
Es gelten unsere allgemeinen Verkaufsbedingungen.
700278067 / GFDO 6025 / 05 (12.2021)
© Georg Fischer Piping System Ltd.
CH-8201 Schahausen/Schweiz
Printed in Switzerland
Phone +41 52 631 11 11/ info.ps@georgfischer.com
www.gfps.com
Rückschlagklappe
Typ 369
Betriebsanleitung
Table of contents
Languages:
Other GF Control Unit manuals
Popular Control Unit manuals by other brands
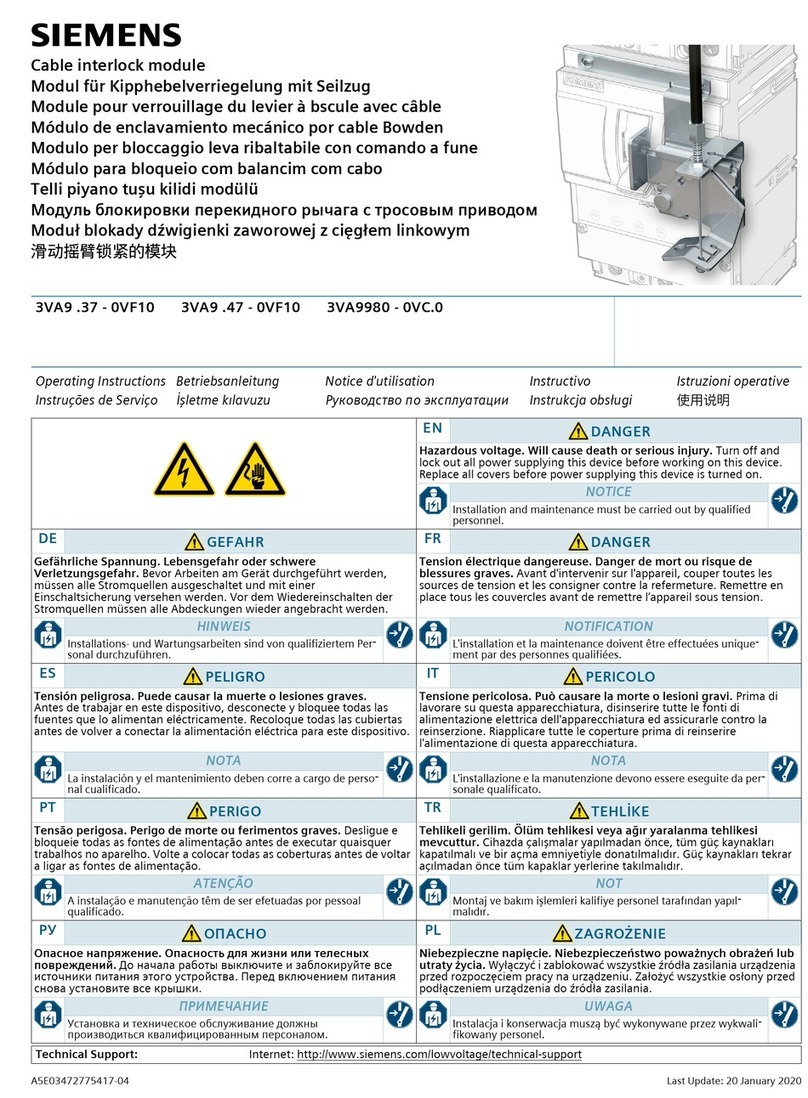
Siemens
Siemens 3VA9.37-0VF10 quick start guide
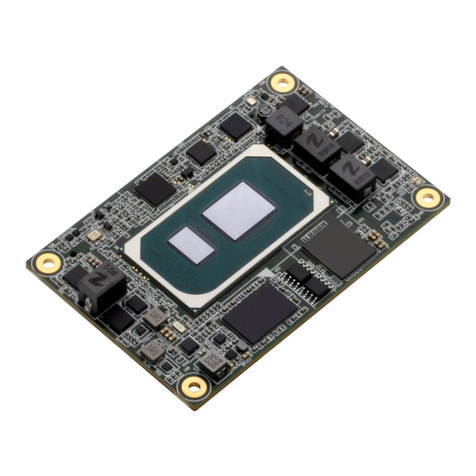
Asus
Asus Aaeon NanoCOM-TGU user manual
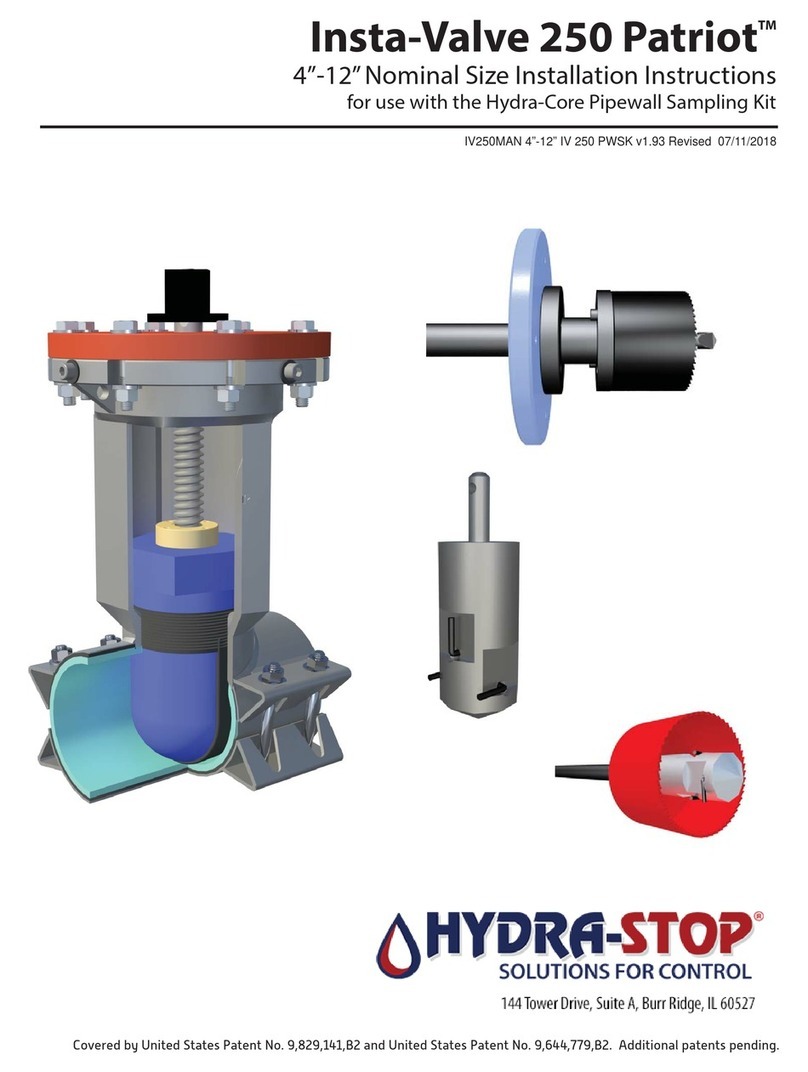
Hydra-Stop
Hydra-Stop Insta-Valve 250 Patriot installation instructions
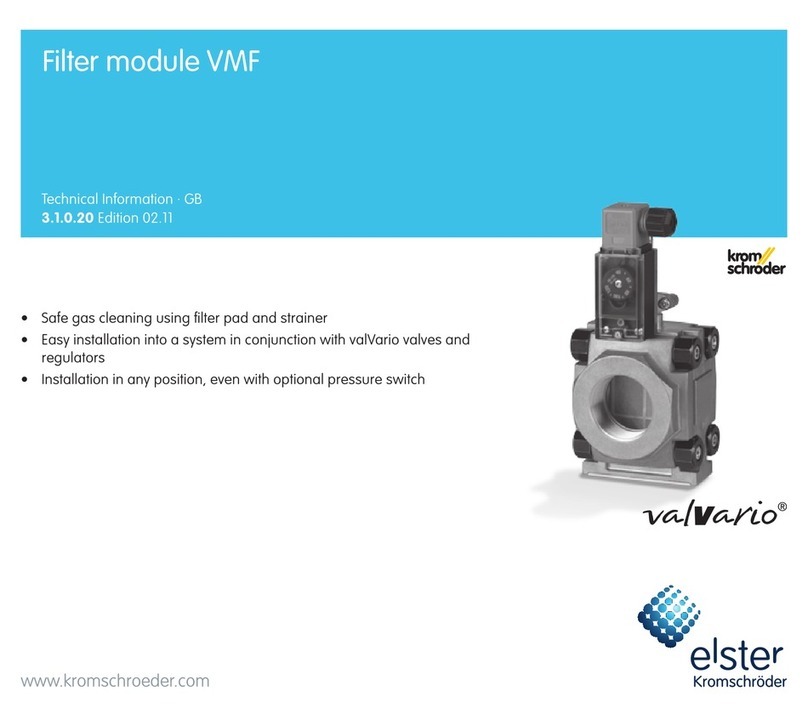
Elster
Elster Kromschroder VMF Series technical information

Grundfos
Grundfos CIM 260 Functional profile and user manual

Newland
Newland NLS-EM3096 Integration guide