LORCH X Series User manual

Lorch Schweißtechnik GmbH
Im Anwänder 24 - 26
71549 Auenwald-Germany
Telefon: +49 7191 503-0
Telefax: +49 7191 503-199
Internet: www.lorch.eu
E-Mail: [email protected]
909.1550.1-08
Operation Manual
X Series
EN

- 2 -
11.18
Publisher Lorch Schweißtechnik GmbH
Im Anwänder 24 - 26
71549 Auenwald, Germany
Telephone: +49 (0) 7191 / 503-0
Fax: +49 (0) 7191 / 503-199
Website: www.lorch.biz
Email: [email protected]
Document number 909.1550.1-08
Issue date 30.11.2018
Copyright © 2012, Lorch Schweißtechnik GmbH
This documentation including all its parts is protected by copyright. Any use or
modication outside the strict limits of the copyright law without the permission of
Lorch Schweißtechnik GmbH is prohibited and liable to prosecution.
This particularly applies to reproductions, translations, microlming and storage and
processing in electronic systems.
Technicalmodications Our machines are in a constant state of further development, and the right is
reserved to make technical changes without notice.
909.1550.1-08

- 3 -
11.18 909.1550.1-08
Table of contents
1 Machine elements ..............4
2 Explanation of symbols .........4
2.1 Meaning of the symbols in the operation
manual ................................4
2.2 Meaning of the symbols on the machine ......4
3 Safety precautions .............5
4 Ambient conditions.............5
5 General regulation of use........6
6 UVV inspection ................6
7 Unit protection.................6
8 Noise emission ................6
9 Electromagnetic compatibility
(EMC) ........................6
10 Transport .....................6
11 Before start-up. . . . . . . . . . . . . . . . . 7
11.1 Fasten transportation belt..................7
11.2 Fastening accessories belt .................7
11.3 Electrode welding process .................8
11.4 TIG welding process......................8
11.5 MIG welding process .....................9
11.6 Connecting the ground cable ...............9
11.7 Connecting the power supply ...............9
12 Start-up......................10
12.1 Electrode welding process ................12
12.2 TIG welding process.....................13
12.3 MIG welding process (MIG/MAG)...........13
12.4 Call up the secondary parameters ..........14
12.5 Special functions .......................15
12.6 Remote control (optional) .................16
13 Graphs ......................18
13.1 Electrode .............................18
13.2 TIG ..................................18
13.3 Up ...................................18
14 Messages ....................19
14.1 Status messages .......................19
14.2 Error messages ........................19
15 Welding basics ...............20
15.1 Stick electrode welding...................20
15.2 TIG welding ...........................20
16 Fundamentals of the MIG/MAG
welding process ..............22
16.1 Principle of the MIG/MAG welding process ...22
16.2 Arc types..............................22
17 Technical data ................24
18 Maintenance and repair ........25
19 Disposal .....................25
20 Service ......................25
21 Declaration of conformity.......25
22 Ersatzteilliste / spare parts list /
Списокдеталей ..............26
22.1 Zeichnung / graph / Рисунок X 350 Control
Pro ..................................26
22.2 X 350 Control Pro .......................27
22.3 X 350 Control Pro PST ...................29
22.4 Zeichnung / graph / Рисунок X 350 Basic Plus 31
22.5 X 350 Basic Plus .......................32
23 Stromlaufplan / schematic /
Схематический ..............34
23.1 X 350 Control Pro .......................34
23.2 X 350 Control Pro PST ...................36
23.3 X 350 Basic Plus .......................38

Explanation of symbols
- 4 - 11.18909.1550.1-08
1Mains cable holder
2Transportation belt
3Handle (hoisting point)
4Control panel
5Accessories belt
6Main switch
7Remote control socket
8Connection socket torch/electrode holder/compo-
nent guide
9Mains cable
The carrying strap is exclusively for the
transport by a person.
Some depicted or described accessories
are not included in the scope of delivery.
Subject to change.
i
1 Machine elements
4
5
6
7
8
8
9
2 31
Abb. 1: Machine elements
2 Explanation of symbols
2.1 Meaning of the symbols in the opera-
tion manual
Danger of physical injury or death!
If the danger warnings are disregarded,
this can cause slight or severe injuries or
even death.
Danger of property damage!
Disregarding danger warnings can cause
damage to workpieces, tools, and equip-
ment.
General note.
Designates useful information about the
product and equipment.
2.2 Meaning of the symbols on the
machine
Danger!
Read the user information in the operation
manual.
Disconnect the mains plug!
Pull out the mains plug before opening the
housing.
i

Ambient conditions
- 5 -
11.18 909.1550.1-08
3 Safety precautions
Hazard-free working with the machine is
only possible if you read the operating and
safety instructions completely and strictly
observe them.
Please obtain practical training before us-
ing the machine for the rst time. Heed the
safety regulation (UVV).*
Before starting any welding work, clear
away any solvents, degreasing agents,
and other ammable materials from the
working area. Non-movable ammable
materials must be covered. Only weld if the
ambient air contains no high concentra-
tions of dust, acid vapours, gases or am-
mable substances. Special care must be
taken during repair work on pipe systems
and tanks which contain or have contained
ammable liquids or gases.
Never touch live parts inside or outside of
the housing. Never touch welding elec-
trodes or live welding current parts in a
machine that is on.
Do not expose the machine to rain; do not
clean with sprays or steam jets.
Always use a welding shield. Warn anyone
in the work area about the dangers of arc
rays.
Please use a suitable extraction system for
gases and cutting fumes.
Always wear breathing apparatus when-
ever there is a risk of inhaling welding or
cutting fumes.
If the power cable is damaged or severed
while working, do not touch the cable, but
immediately pull out the mains plug. Never
use a machine if the mains cable is dam-
aged.
Keep a re extinguisher near the welding
area.
Check the welding area for re after weld-
ing (see UVV*).
Never try to disassemble the pressure
reducer. Replace the pressure reducer if
faulty.
The machine must be transported or set up
only on rm, level surfaces.
The maximum admissible angle of inclina-
tion for setting up or transporting is 10°.
Service and repair work may only be carried out by a
trained electrician.
Ensure that there is good direct contact for the ground
cable immediately beside the weld point. Do not pass
the welding current through chains, ball bearings,
steel cables, grounding conductors, etc., as it could
cause these to fuse.
Secure yourself and the welding machine when work-
ing in elevated or inclined areas.
The machine should be connected only to a properly
grounded mains supply. (Three-phase four-wire sys-
tem with grounded neutral conductor or single phase-
three-wire system with grounded neutral conductor)
socket and extension cable must have a functional
protective conductor.
Wear protective clothing, leather gloves and leather
apron.
Protect the welding area with curtains or mobile
screens.
Do not use welding equipment to thaw out frozen wa-
ter pipes or ducts.
In closed containers, under cramped conditions, and
in high electrical risk areas, only use machines with
the S sign.
When taking a break, switch off the machine and
close the valve on the gas cylinder.
Secure the gas cylinder with a chain to prevent it fall-
ing over.
Disconnect the mains plug from the mains before
changing the place of installation or making repairs
to the machine.
*) Only applicable for Germany. Can be ordered from Carl
Heymanns-Verlag, Luxemburger Str. 449, 50939 Köln.
Please heed the safety regulations which apply to your
country. Subject to change.
4 Ambient conditions
Temperature range of ambient air:
in operation: -20 °C ...+40 °C (-4 °F to +104 °F)
Transport
and storage -25 °C to +55 °C (-13 °F to +131 °F)
Relative humidity:
up to 50 % at 40 °C (104 °F)
up to 90 % at 20 °C (68 °F)
Operation, storage and transport may only
be carries out within the ranges indicated!
Use outside of this range is considered not
used with its intended purpose. The manu-
facturer is not liable for damages cause by
misuse.
Ambient air must be free of dust, acids, corrosive gases
or other damaging substances!

Transport
- 6 - 11.18909.1550.1-08
5 General regulation of use
This machine is intended for use in the commercial and
industrial sector. It is portable and is suitable for opera-
tion on the mains supply or also on a power generator.
The machine is intended for DC electrode welding of
– unalloyed steels, low and high-alloy steels
– nickel and its alloys
Together with a TIG welding torch, the machine is
suitable for TIG welding with direct current of
– unalloyed steels, low and high-alloy steels
– copper and its alloys
– nickel and its alloys
– special metals like titanium, zirconium and tanta-
lum.
Together with a wire feed case, the machine is suit-
able for MIG welding with
– solid wire (MIG/MAG),
– ux-cored wire.
6 UVV inspection
Operators of commercially-operated welding systems
are obliged to have regular safety inspections of the
equipment carried out in accordance with EN 60974-4.
Lorch recommends inspections at 12 month intervals.
A safety inspection must also be carried out if modica-
tions or repairs have been made to the system.
Improper UVV inspections can destroy the
system. For more information about UVV
inspections of welding systems, please
contact your authorised Lorch service cen-
tre.
7 Unit protection
This machine is protected electronically against overload-
ing. Do not use fuses of higher amperage than printed on
the identication plate.
8 Noise emission
The noise level of the unit is less than 70 dB(A), meas-
ured under standard load in accordance with EN 60974-1
in the maximum working point.
9 Electromagnetic compatibility
(EMC)
This product is manufactured in conformance with the
current EMC standard. Please note the following:
Due to their high power consumption, welding ma-
chines can cause problems in the public power grid.
The mains connection is therefore subject to require-
ments with regard to the maximum permissible sys-
tem impedance. The maximum permissible system
impedance (Zmax) of the interface to the power grid
(mains connection) is indicated in the technical data.
If in doubt, please contact your power grid operator.
The machine is intended for welding in both commer-
cial and industrial applications (CISPR 11 class A).
Use in other surroundings (for example in residential
areas) may disturb other electronic devices.
Electromagnetic problems during start-up can arise
in:
– mains cables, control cables, signal and telecom-
munication lines near the welding or cutting area
– TV/radio transmitters/receivers
– Computers and other control devices
– Protection equipment such as alarm systems
– Pacemakers and hearing aids
– Measurement and calibration devices
– Equipment with too little protection against distur-
bances
If other equipment is disturbed, it may be necessary to
provide additional shielding.
The affected area may go beyond the boundaries of
the property concerned. This depends on the layout
of the building, and the other activities that may be
going on there.
Please use the machine in compliance with the manu-
facturer's instructions. The operator of the equipment is
responsible for the installation and use of the machine.
Furthermore, the owner is responsible for eliminating the
disturbances caused by electromagnetic elds.
10 Transport
For transport using mechanical lifting
gear (e.g. cranes etc.) only the handle
may be used as the hoisting point. Use
suitable load-bearing equipment. Do
not use a fork-lift truck or similar device
to lift the machine by its housing. The
carrying strap is exclusively for trans-
port by a person.

Before start-up
- 7 -
11.18 909.1550.1-08
11 Before start-up
11.1 Fasten transportation belt
2 12 13
Abb. 2: Transportation belt
2Transportation belt
12 Plastic slides
13 Velcro fastener
ÂThread the transportation belt into the welding ma-
chine and plastic slides. See sequence of the num-
bering in the picture.
11.2 Fastening accessories belt
5 1412
Abb. 3: Accessories belt
5Accessories belt with fastener
12 Plastic slides
14 Closure
ÂThread the accessories belt into the handle and plas-
tic slides. See sequence of the numbering in the pic-
ture.
ÂPlug the belt fasteners together.

Before start-up
- 8 - 11.18909.1550.1-08
Connecting the inert gas cylinder
26 23
25
28
27
24
22
Abb. 4: Gas connection
ÂPlace the inert gas cylinder 28 in a suitable location
and secure to prevent it from falling over.
The cylinder can be secured using a wall bracket or
cylinder trolley.
ÂBriey open the gas cylinder valve 27 several times in
order to blow out any dirt particles that are present.
ÂConnect the pressure reducer 22 to the inert gas cyl-
inder 28.
ÂScrew the inert gas hose 24 to pressure reducer 22
and open the gas cylinder valve 27.
Setting the inert gas quantity
ÂOpen the valve 19 on the TIG welding torch.
9Inert gas ows out.
9The ow meter 23 indicates the gas quantity, and
the content pressure gauge 26 indicates the cylinder
content.
ÂClose the valve 19 on the TIG welding torch when the
torch is not being used in order to prevent unneces-
sary use of gas.
11.3 Electrode welding process
Connecting the electrode welding cable
ÂConnect the electrode welding cable to the minus
or plus socket 8 and secure the cable by rotating it
clockwise.
The polarity of the electrode depends on
the type of electrode and the welding proc-
ess. Please follow the manufacturer's in-
structions on the electrode packaging for
this purpose.
11.4 TIG welding process
For TIG welding you require a TIG valve
torch (Type LTV2600) for this device
Installing electrodes
18 16
2021
17
19
ÂUnscrew the clamping cap 17.
ÂRemove the electrode 16 from the collet 18.
ÂGrind the end of the electrode 16.
ÂSlide the electrode 16 into the collet 18.
ÂInsert the electrode 16 into the torch and rmly tight-
en the clamping cap 17.
Do not dismantle the collet body 20 and the
gas nozzle 21.
When converting the torch to a different
electrode diameter, please pay attention to
the following.
The collet 18, collet body 20 and electrode 16 must
have the same diameter.
The gas nozzle 21 must be matched to the electrode
diameter.
Connecting the TIG torch
ÂConnect the TIG torch to the minus 8 connection
socket and secure it by turning it clockwise.
i
i
i

Before start-up
- 9 -
11.18 909.1550.1-08
11.6 Connecting the ground cable
ÂConnect the ground cable to the free minus or plus 8
socket and secure the cable by rotating it clockwise.
Fastening the ground clamp
Abb. 5: Attaching the ground clamp - Correct!
ÂFasten the grounding clamp in the immediate vicinity
of the welding area, so that the welding current can-
not seek its own return path across machine parts,
ball bearings or electric circuitry.
ÂConnect the ground clamp rmly to the welding bench
or the workpiece.
Abb. 6: Attaching the ground clamp - Wrong!
Do not place the ground clamp on the welding ma-
chine or the gas cylinder; otherwise the welding cur-
rent will be carried via the protective conductors and
it will destroy these.
11.7 Connecting the power supply
The machine is suitable for operation on the mains sup-
ply or on a current generator.
ÂPlug the mains plug into the appropriate socket.
The mains voltage and tolerance as well
as the fuse protection must correspond to
the technical specications (see Technical
Specications).
11.5 MIG welding process
A wire feed case (optional) is required for
MIG welding.
The operations required may differ depend-
ing on the version and the conguration of
the wire feed case!
Please observe the wire feed case operat-
ing manual!
ÂConnect the welding cable of the wire feed case to
the connection socket minus or plus 8 of the power
source (X 350).
ÂConnect the control cable of the wire feed case (with
adapter if necessary) to the remote control connec-
tion socket (7) of the power source (X 350). (if tted)
ÂEquipping the wire feed case. (See wire feed case
operating instructions)
i
73
7270 74
76
77
75
71
Abb. 7: MIG welding connection diagram
70 Control cable adapter (optional) 73 Welding cable 76 Component guide
71 Power source (X 350) 74 Component guide 77 MIG/MAG torch
72 Control cable 75 Wire feed case

Start-up
- 10 - 11.18909.1550.1-08
12 Start-up
44 45 46 47 48 4934 35 39 42
41 43
40
383632 33
555657 54 53 52
31
30
50
51
37
Abb. 8: Control panel X 350 Control Pro
44 45 47 48 4934 35 39 42
41 43
40
56
57 52
55 58
53
Abb. 9: Control panel X 350 Basic Plus
30 Selection button Up / Arc Force / Pulsesis used to
select uphand seam welding, arc dynamics and /
or pulsing.
31 Selection button Hotstart / Regular is used to se-
lect Hotstart (increased `start current) or regular
start current.
32 The Regular LED lights up with regular start cur-
rent. (without Hotstart)
33 The Hotstart LED lights up when Hotstart is se-
lected.
34 The Fault LED lights up continuously, and the
fault code is displayed in the 7 segment display
41.

Start-up
- 11 -
11.18 909.1550.1-08
35 The Remote control LED lights up when a remote
control is connected.
Control knob 56 species the maximum value for
the control range of the remote control. If 100A
has been set, for example, 10A - 100A can be
called up using the remote control.
36 The Pulse LED lights up when the pulse function
has been selected. (the pulse is carried out be-
tween welding current I1 and I2)
37 The Up (uphand seam welding) LED lights up
when the vertical up-welding function has been
selected.
38 The Up Force (arc dynamics) LED lights up when
the arc dynamics function has been selected.
(short time current increase with short arc)
39 The % LED lights up when a value is displayed in
the 7 segment display 41 in percent.
40 The Seconds LED lights up when a value is dis-
played in the 7 segment display 41 in sec.
41 The 7 segment display, shows the selected cur-
rent intensity.
When the secondary parameters are active, the
code and the setting value of the secondary pa-
rameter are displayed alternately.
42 The Welding voltage LED lights up when the
welding voltage is displayed in the 7 segment
display 41 in volts.
43 The Welding current LED lights up when the
welding current is displayed in the 7 segment
display 41 in amps.
44 The TIG LED lights up if TIG operating mode is
selected.
45 The CV LED lights up if the MIG welding operat-
ing mode is selected with a continuous voltage
characteristic curve.
46 THE CC LED lights up if MIG welding operating
mode is selected with a continuous current char-
acteristic curve.
47 The Electrode basic LED lights up if you select
electrode mode. (Electrodes with alkaline coating)
48 The Electrode rutile LED lights up if you select
rutile electrode operating mode. (Electrodes with
rutile acid coating)
49 THE Electrode CEL LED lights up if you select
CEL electrode operating mode. (Electrodes with
coating containing cellulose, suitable for down-
wards welding)
The Electrode CEL LED starts ashing when
gouging operating mode is selected.
50 The Electrode basic / rutile / CEL, gouging selec-
tion button
is used to select the electrode operating modes
basic / rutile / CEL. If the button is pushed for
longer than 2 seconds the gouging operating
mode is activated (Electrode CEL LED ashes).
51 The WIG / MIG selection button
is used to select the operating mode WIG /
MIG welding with continuous voltage character-
istic curve / MIG welding with continuous current
characteristic curve
52 Polarity display LEDs
LED "-" lights up (machine without polarity re-
verser)
LED "-" or "+" lights up (machine with polarity
reverser)
53 The VRD LED
lights up continuously when the VRD function is
active (no-load voltage reduction)
54 The polarity reverser LED
lights up continuously with machines that have a
polarity reverser (equipment for polarity reversal)
ashes, if the output voltage exceeds the maxi-
mum allowable value according to the standard
(example: during welding or if MIG welding oper-
ating mode LED 45, 46 is selected)
55 The Menu button
is used to call up the secondary parameters.
It is used for switching the polarity (press the but-
ton for 2 secs.), but only with machines that have
the polarity reverser.
56 The menu / welding current control knob is used
for:
●setting the welding current (rotate).
●selecting the secondary parameters (rotate).
●selecting the secondary parameters (press).
●setting the secondary parameters (rotate).
57 The polarity display LEDs
LED "+" lights up (machine without polarity re-
verser)
LED "+" or "-" lights up (machine with polarity
reverser).
58 Select button MMA/TIG/MSG is used to switch
between modes TIG, MSG-welding with constant
voltage characteristic, MMA basic/rutile/CEL.
If the button is pushed for longer than 2 seconds
the gouging operating mode is activated (Elec-
trode CEL LED ashes).

Start-up
- 12 - 11.18909.1550.1-08
ÂRepeat the operations for setting the Hotstart time
"tSt" secondary parameter.
ÂExit the secondary parameters by pressing the Menu
button 55.
Alternatively, the Hotstart secondary parameter can
be called up by keeping the selection button 31
pressed for 2 secs. with Hotstart (LED 33 lights up)
selected. (Control Pro)
Arc dynamics (Arc Force)
The electrode is prevented from burning in in the
weld pool by means of a brief current increase with
a short arc.
ÂPress button 30 until the ARC symbol (LED 38) lights
up. (Control Pro)
ÂPress button 55 to call up the secondary parameters.
ÂSelect the Arc dynamics secondary parameter (Code
"dAF") by turning the control knob 56.
ÂConrm the secondary parameter by pressing the
control knob 56.
ÂSet the desired value by rotating the control knob 56.
ÂConrm the setting by pressing the control knob 56.
ÂExit the secondary parameters by pressing the Menu
button 55.
Alternatively, the arc dynamics secondary parameter
can be called up by keeping the selection button 30
pressed for 2 secs. with Arc dynamics (LED 38 lights
up) selected. (Control Pro)
12.1 Electrode welding process
Switch on the system
ÂSwitch on the system at the main switch 6.
ÂPress button 50 (Control Pro) or 58 (BasicPlus) re-
peatedly until the desired electrode operating function
is selected.
9The electrode basic, rutile or CEL symbol (LED 47, 48
or 49) lights up.
ÂPress button 31 in order to switch on the Hotstart or
regular function. (Control Pro)
ÂPress button 30 in order to switch the Up, Arc Force
and
Pulse function on or off. (Control Pro)
ÂUse control knob 56 to set the desired welding current.
Electrode Ø[mm] Recommended current in-
tensity [A]
1,5 20...40
2,0 35...60
2,5 45...100
3,2 75...140
4,0 130...190
5,0 180...280
6,0 230...370
8,0 290...420
Tab. 1: Electrode diameter - Electrode
Please follow the electrode manufacturer's
instructions
Electrode welding cur-
rent Range Factory
setting
Welding current l1 10 to 350 A 100
Tab. 2: Electrode welding current
Arc ignition
ÂBriey touch the workpiece at the point to be welded
using the electrode and lift the electrode a little.
9The arc burns between the workpiece and the elec-
trode.
Hotstart
Ignition performance is improved by increasing the
welding current (Hotstart).
ÂPress button 31 until the Hotstart (LED 33) symbol
lights up. (Control Pro)
ÂPress button 55 to call up the secondary parameters.
ÂSelect the secondary parameter Hotstart (Code "ISt")
by rotating the control knob 56.
ÂConrm the secondary parameter by pressing the
control knob 56.
ÂSet the desired value by rotating the control knob 56.
ÂConrm the setting by pressing the control knob 56.
i

Start-up
- 13 -
11.18 909.1550.1-08
12.2 TIG welding process
Switch on the system
ÂSwitch on the system at the main switch 6.
ÂPress button 50 (Control Pro) or 58 (BasicPlus) re-
peatedly until the desired TIG operating mode is se-
lected.
9The TIG symbol (LED 44) lights up.
ÂPress button 30 to turn the Pulse function on or off.
(Control Pro)
ÂUse control knob 56 to set the desired welding cur-
rent.
TIG welding current Range Factory
setting
Welding current I1 10 to 350 A 100
Tab. 3: TIG welding current
Arc ignition
ÂOpen the valve 19 on the TIG welding torch.
ÂBriey touch the workpiece with the tip of the elec-
trode at the point to be welded.
ÂLift the electrode a little.
9The arc burns between the workpiece and the elec-
trode.
Upslope
A short-circuit current of 60 A is used for igniting during
the TIG welding process. The upslope takes place with
115 A/s until the set welding current is reached.
Guideline values for the current intensity and
the gas quantity.
Tungsten electrode
diameter [mm]
Current in-
tensity [A]
Gas quantity
[l/min]
1,0 3...40 4
1,6 15...130 5...6
2,0 45...180 5...8
2,4 70...240 6...10
3,2 140...320 6...12
4,0 220...450 6...14
12.3 MIG welding process (MIG/MAG)
Switch on the system
ÂSwitch on the system at the main switch 6.
ÂPress button 51 (Control Pro) or 58 (BasicPlus) re-
peatedly until the desired CV or CC (Control Pro) op-
erating mode has been selected.
9The CV or CC symbol (LED 45 or 46) lights up.
ÂUse control knob 56 to set the desired welding cur-
rent (CC) (Control Pro) or welding voltage (CV).

Start-up
- 14 - 11.18909.1550.1-08
12.4 Call up the secondary parameters
ÂPress button 55 to call up the secondary parameters.
ÂSet the desired secondary parameter by rotating the
control knob 56.
9The parameter code and the corresponding setting are
displayed alternately in the 7-Segment display 41.
ÂConrm the secondary parameter by pressing the
control knob 56.
ÂThe setting can be adjusted by rotating the control
knob 56.
ÂConrm the setting by pressing the control knob 56.
ÂThe previous or next secondary parameter is dis-
played by rotating the control knob 56.
Different secondary parameters are available de-
pending on the selected operating mode and func-
tion.
Parameter
Code
Default
value
Setting
range
Mode
Basic Plus
Control Pro
Electrode
TIG
MIG
Start current 50 % 5...200 % X X X
Start current time 0.1 s 0.0 to
20 s X X X
Hotstart 125
%5...200 % X X X
Hotstart time 1.0 s 0.0 to
20 s X X X
Arc dynamics 100
%0...200 % X X X
The welding current increases automatically as the weld-
ing voltage is reduced. The arc dynamic indicates the ratio
between the welding current and the automatic increase.
Up / Pulses On On...OFF X X X
The Up and Pulses function can be deactivated or activat-
ed. When switched to "OFF", the Up and Pulses functions
can no longer be selected using button 30.
Up frequency
(correction value)
100
%0...200 % X X
Up welding cur-
rent
(correction
value)
100
%0...200 % X X
Up second cur-
rent (correction
value)
100
%0...200 % X X
Up duty cycle
(correction value)
100
%0...200 % X X
Second current I2
(% of welding
current I1)
50 % 1...200 % X X X
Parameter
Code
Default
value
Setting
range
Mode
Basic Plus
Control Pro
Electrode
TIG
MIG
Pulse frequency 3.0
Hz
0.2 to
2000 Hz
(Repre-
sentation
0.2 to
2.0t)
X X X
Pulse duty cycle
(% of welding
current I1)
50 % 1...99 % X X X
Indicates the chronological ratio between welding current
I1 and second current I2 in percent. If the value set is 30,
the ratio is 30% l1 to 70% l2.
Weld end detec-
tion
(correction value)
100
%0...200 % XXXXX
Your welding machine switches the welding current off at
a certain arc length. (Weld end detection.) The maximum
length of the arc can be adapted using the "SEE“ parameter.
Inductor effect
(correction value)
100
%0...200 % XXX
Hold OFF OFF, 5,
10, On XXXXX
After the welding, with Hold = 5, 10 or On, the average values
of the last welding task are visible in the display for 5 sec., 10
sec. or permanently, the LED for V (voltage) or A (amperage)
is ashing. At Hold = OFF the set-value of the welding current
or the actual welding voltage is shown in the display.
Function lock OFF
On...OFF
(active...
inactive)
XXXXX
Remote control ON OFF...On XXXXX
MMA only OFF OFF...On X X X X
Software version
Control panel - - X X X X
Software version
Master - - X X X X
Software version
Process - - X X X X
Tab. 4: Secondary parameters
The factory setting are optimised thanks to auto-
matic parameters.
You can use these factory settings unchanged for
the majority of welding jobs.

Start-up
- 15 -
11.18 909.1550.1-08
12.5 Special functions
Gouging
Gouging is used for working out the roots or faulty
points and serves for preparing the weld seam.
A special torch is required for gouging that has car-
bon electrodes and compressed air connection.
ÂPress and hold the electrode button 50 (Control Pro)
or 58 (Basic Plus) for at least 2 seconds.
9The Electrode CEL LED 49 ashes.
ÂSet the desired current by rotating the control knob
56.
Up / Pulses (Control Pro)
The Up and Pulses function can be activated or de-
activated. The Up (LED 37) and Pulses (LED 36)
functions are only available in an active state.
If Up / Pulses is deactivated, the Arc Force can be
selected or deselected directly (without pressing but-
ton 30 several times).
Activate / deactivate Up / Pulses (Control Pro)
ÂPress button 55 to call up the secondary parameters.
ÂSelect the Up / Pulses secondary parameter (Code
"PLS") by rotating the control knob 56.
ÂConrm the secondary parameter by pressing the
control knob 56.
ÂSet the desired value by rotating the control knob 56.
– "On " = Activated
– "OFF" = Deactivated
ÂConrm the setting by pressing the control knob 56.
ÂExit the secondary parameters by pressing the Menu
button 55.
Switching Up on / off (Control Pro)
ÂPress button 30 until the Up symbol (LED 37) lights
up.
ÂPress button 55 to call up the secondary param-
eters.
ÂSelect the Up frequency secondary parameter (Code
"uPF") by rotating the control knob 56.
ÂConrm the secondary parameter by pressing the
control knob 56.
ÂSet the desired value by rotating the control knob
56.
ÂConrm the setting by pressing the control knob 56.
ÂRepeat the operations for setting the Up second cur-
rent "uPI" and Up duty cycle "uPU" secondary pa-
rameters.
ÂExit the secondary parameters by pressing the Menu
button 55.
The average welding current is displayed
and set in the 7 segment display. Welding
currents I1 and I2 deviate from the set val-
ue depending on the secondary parameter
settings "uPF", "uP1", "uP2" and "uPU".
The setting range of the average welding
current is 30 to 200 A
Switching Pulses on / off (Control Pro)
ÂPress button 30 until the Pulses symbol (LED 36)
lights up.
ÂPress button 55 to call up the secondary param-
eters.
ÂSelect the Second current I2secondary parameter
(Code "I 2") by rotating the control knob 56.
ÂConrm the secondary parameter by pressing the
control knob 56.
ÂSet the desired value by rotating the control knob
56.
ÂConrm the setting by pressing the control knob 56.
ÂRepeat the operations to set the Pulse frequency
"FPU" and Pulse duty cycle "bPU" secondary param-
eters.
ÂExit the secondary parameters by pressing the Menu
button 55.
Hold functionality
After the welding, with Hold = 5, 10 or On, the aver-
age values of the last welding task are visible in the
display for 5 sec., 10 sec. or permanently, the LED
for V (voltage) or A (amperage) is ashing. At Hold =
OFF the set-value of the welding current or the actual
welding voltage is shown in the display.
ÂPress button 55 to call up the secondary parameters.
ÂSelect the Hold secondary parameter (Code “HOL”)
by rotating the control knob 56.
ÂConrm the secondary parameter by pressing the
control knob 56.
ÂSet the desired value by rotating the control knob 56.
– “OFF” = Deactivated
– „5 “ = for 5 seconds the average values of the last
welding task are displayed
– „10 “ = for 10 seconds the average values of the
last welding task are displayed
– „On “ = Activated (permanently the average val-
ues of the last welding task are displayed)
Pressing button 56 switches between actual value of
the welding voltage and welding current.
i

Start-up
- 16 - 11.18909.1550.1-08
Function lock
The Function lock can be activated or deactivated.
The function lock can only be switched on in an active
state. When the function lock is switched on, all but-
tons on the control knob are blocked.
Function lock activation / deactivation
ÂPress button 55 to call up the secondary parameters.
ÂSelect the Function lock secondary parameter (Code
"LOC") by rotating the control knob 56.
ÂConrm the secondary parameter by pressing the
control knob 56.
ÂSet the desired value by rotating the control knob 56.
– "On " = Activated
– "OFF" = Deactivated
ÂConrm the setting by pressing the control knob 56.
Switching the Function lock on / off
ÂPress the control knob 56 for at least 3 seconds.
9"---" is briey displayed in the 7 segment display 41
as conrmation.
9All buttons on the control knob are blocked. If it is
operated, "---" is displayed.
The control knob 56 must be pressed again for at
least 3 seconds in order to disable the function lock.
The function lock setting is saved! If the
machine is switched off with the function
lock activated, the control panel is still
blocked when the machine is switched
back on.
MMA only (BasicPlus)
With this parameter the welding mode can be limited
to MMA only.
ÂPress button 55 to call up the secondary parameters.
ÂSelect the secondary parameter “MMA only” (Code
“Elo”) using the knob 56.
ÂConrm the secondary parameter by pressing the
control knob 56.
ÂSet the desired value by rotating the control knob 56.
– “on” = Only the MMA modes basic/rutile/CEL can
be selected.
– “OFF” = All modes can be selected.
ÂConrm the setting by pressing the control knob 56.
Standby mode (idle state)
ÂPress the control knob 56 and the button 55 simulta-
neously for at least 3 seconds.
9The connecting sockets are de-energized. All LEDs
are turned off. "OFF" is displayed in the 7 segment
display 41.
ÂPress the control knob 56 and the button 55 simulta-
neously for at least 3 seconds to exit standby mode.
(See also chapter Remote control)
Software version (Control Pro)
ÂPress buttons 30 and 51 simultaneously for at least
3 seconds.
9The software version will be displayed. (See second-
ary parameters)
Master reset
Warning! All personal settings will be
lost.
All welding and secondary parameters are
reset to their factory settings (master reset
function).
ÂPress buttons 31 and 50 simultaneously for at least 3
seconds. (Control Pro)
ÂPress buttons 31 and 50 simultaneously for at least 3
seconds. (Basic Plus)
9The 7 segment display and the control panel indica-
tors light up briey as conrmation.
12.6 Remote control (optional)
Manual remote control HR 33 PST
A manual remote control with polarity and standby switch
is available for the X series.
ÂPlug the remote control into the remote control con-
necting socket 7.
ÂPress button 55 to call up the secondary parameters.
ÂSelect the Remote control secondary parameter
(Code "FrA") by rotating the control knob 56.
ÂConrm the secondary parameter by pressing the
control knob 56.
ÂSet the value "On" by rotating the control knob 56.
ÂConrm the setting by pressing the control knob 56.
ÂExit the secondary parameters by pressing the Menu
button 55.
I %
1000
60
61
62
Abb. 10: Manual remote control HR 33 PST
60 The welding current rotary switch
is used to set the welding current.
The rotary knob covers the setting range from
minimum (minimum welding current of the
i
i

Start-up
- 17 -
11.18 909.1550.1-08
machine) to maximum (set welding current on the
machine).
If the setting is 100A, for example, the remote
control can call up 10A - 100A.
61 The polarity switch
is used to change the polarity (only machines with
polarity reverser)
The machine is protected against multiple chang-
es at short intervals by a 2-second delay.
62 The standby switch
is used to activate / deactivate standby mode
(idle state)
The switching position of the remote con-
trol has priority over the settings on the
welding machine.
Remote control without polarity and standby
switch
When using the Lorch remote control without polarity
and standby switch, the Remote control secondary
parameter must be set to OFF (Code "FrA" = OFF).
ÂPlug the remote control into the remote control con-
necting socket 7.
ÂPress button 55 to call up the secondary parameters.
ÂSelect the Remote control secondary parameter
(Code "FrA") by rotating the control knob 56.
ÂConrm the secondary parameter by pressing the
control knob 56.
ÂSet the value "OFF" by rotating the control knob 56.
ÂConrm the setting by pressing the control knob 56.
ÂExit the secondary parameters by pressing the Menu
button 55.
If the Remote control secondary parameter
is set to On (Code "FrA" = On), the welding
machine behaves as follows:
●Standby mode is activated when the welding cur-
rent rotary knob of the remote control is set to
minimum.
●The polarity cannot be changed on the control
panel.
Contact remote control KR 10
The contact remote controller KR 10 is not
used with the devices X 350 VRD.
A contact remote control for setting the welding current
is available for the X series (only suitable for electrode
welding).
ÂClamp the contact remote control in the electrode
holder.
ÂPosition the contact remote control with the free end
on the workpiece or the welding bench (potential of
the ground clamp).
ÂSet the desired welding current with buttons 65 and
66.
ÂTransfer the set welding current to the machine using
button 67.
65
66
67
Abb. 11: Contact remote control KR 10
i
i
i

Graphs
- 18 - 11.18909.1550.1-08
13 Graphs
13.1 Electrode
bPU Pulse duty cycle
FPU Pulse frequency
IPower
I1 Welding current
I2 Second current
ISt Hotstart
tTime
tSt Hotstart time
Abb. 12: Electrode current routing diagram
bPU Pulse duty cycle
FPU Pulse frequency
IPower
I1 Welding current
I2 Second current
ISt Start current
Iz Ignition current
tTime
tIu Upslope
tSt Start current time
Abb. 13: TIG current routing diagram
13.2 TIG
IPower
I1 Welding current
I2 Second current
tTime
uP1 Up welding current
uP2 Up second current
uPF Up frequency
uPU Up duty cycle
Abb. 14: Up current routing diagram
13.3 Up

Messages
- 19 -
11.18 909.1550.1-08
14 Messages
14.1 Status messages
An error code is displayed in the 7 segment display
41 in event of an error.
After the message has been output, the
machine will only function to a limited ex-
tent; the error must be corrected as quickly
as possible.
The status message can be deleted by
pressing the control knob 56.
i
14.2 Error messages
An error code is displayed in the 7 segment display
41 in event of an error. Press any button to display
the sub-error (Sub-Code).
As long as there is an error code on display
welding is not possible.
i
Code Note Cause Possible remedy
H08 Short-circuit Short-circuit in the output circuit Eliminate the short-circuit (pick up
electrode holder, ...)
H30 Conguration Component group recognition faulty Inform Service
H34 Fans Fan current faulty Inform Service
Tab. 5: Status messages
Code Error Cause Possible remedy
E01 Excessive temperature Duty cycle exceeded Allow switched-on machine to cool
down for a few minutes.
Dust lter contaminated Replace dust lter
E02 Overvoltage Mains voltage too high Check mains voltage
E04-1 Protective earth conductor
monitoring
Fault current to protective earth con-
ductor
Connect the welding earth lead
E06 Overvoltage secondary Initial voltage too high Inform Service
E07 EEPROM Communication with EEPROM defec-
tive
Switch machine off and on again, ex-
ecute master reset
E09 Voltage detection Voltage measuring system faulty Inform Service
E12 Power section Power section start-up faulty Inform Service
E13 Temperature sensor Temperature sensor not ready for
operation
Inform Service
E14 Supply voltage internal supply voltage too low Check mains voltages
E15 Current detection Error during current measurement Inform Service
E18 Overload protection Safety switch device to protect elec-
trical components
Inform Service
E22 Mains undervoltage Mains voltage on power unit is too
low
Check mains voltages
E25 Idle generator Idle generator faulty Inform Service
E30 Error conguration Faulty or wrong pc-board, wrong
software system installed
Inform Service
E31 Communications fault CAN bus communication faulty Switch the equipment off and on again
E32 FPGA FPGA faulty Inform Service
E33 Power section Power module not symmetrical Inform Service
E34 Fans Fan current faulty Inform Service
E40 Polarity reverser Polarity reverser faulty Inform Service
E41 Phase monitor Recognised missing mains phase Check mains fuse and mains supply
Tab. 6: Error messages

Welding basics
- 20 - 11.18909.1550.1-08
15 Welding basics
15.1 Stick electrode welding
Coated stick electrodes are used for the widely-used
manual metal arc welding process (stick electrode weld-
ing). The coating of the electrode melts off during the
welding process together with the core wire. The coating
generates the shielding gas. Additionally the burning-
off coating compensates alloy elements, which are de-
stroyed in the molten pool. A slag layer forms on top of
the welding seam, which covers and protects the cooling
welding seam against the air.
The coatings of the electrodes differ according to thick-
ness and type, i.e. chemical composition. This results in
different welding properties and consequently different
applications for the electrodes. Types and nomenclature
are dened in DIN EN 499 (formerly 1913).
Stick electrode
Arc
Coating
Core rod
Gas/slag
Molten zone
Base metal
15.2 TIG welding
The TIG welding process is a universally-applicable
process which creates high quality joints.
The electrode of the TIG process consists of non-melting
tungsten, the shielding gas is an inert gas. In English us-
age we speak of TIG welding ("Tungsten“ = Wolfram).
Inert gas is chemically neutral and does not react with
the weld metal. Inert gases are, e.g. argon, helium and
their mixtures. Usually pure argon (99.9%) is used. The
welding gas must be dry. DIN 32 526 denes the differ-
ent types of shielding gas.
TIG welding process basics
A non-melting tungsten electrode is clamped with a col-
let into a gas or water-cooled torch. The arc burns be-
tween the tungsten electrode and the workpiece in an
inert shielding gas atmosphere. Thus the tungsten elec-
trode acts as an arc carrier. The arc melts the workpiece
point by point and forms the weld pool. The shielding gas
escapes through the gas nozzle. This gas protects the
tungsten electrode, the arc and the molten pool against
the surrounding air. This prevents undesired oxidation.
Consequently, poor welding results may occur due to
trouble with the shielding gas supply.
In case additional ller material is required, ller wire
is supplied either manually, as in gas ame welding, or
automatically by means of a cold wire feeder. The ller
wire must be equally or more highly alloyed than the
base material. Flange and corner welds can be created
easily without ller wire.
Shielding gas
Tungsten
electrode
Gas nozzle
Shielding gas
Welding seam
Workpiece
Power source
Arc
Filler wire
Basically, both DC and AC may be used for TIG welding.
The current mode and polarity depend on the material to
be welded.
Non or low-alloyed steel, high-alloyed steel and copper,
as well as titanium and tantalum are welded with DC.
The electrode is connected at the minus pole because of
the stronger current loading.
When welding aluminium and magnesium as well as
their alloys, AC must be used in order to tear up the high-
melting and tough oxide skin which forms on the molten
pool or which is present on the base metal. If the oxide
skin is missing, e.g. there has been welding on the same
part for a longer time, the arc can be unstable or break
up from time to time.
Shape of the electrode tip
Tungsten electrodes always have to be ground length-
wise because crosswise grinding marks cause an un-
steady arc.
This manual suits for next models
2
Table of contents
Other LORCH Welding System manuals
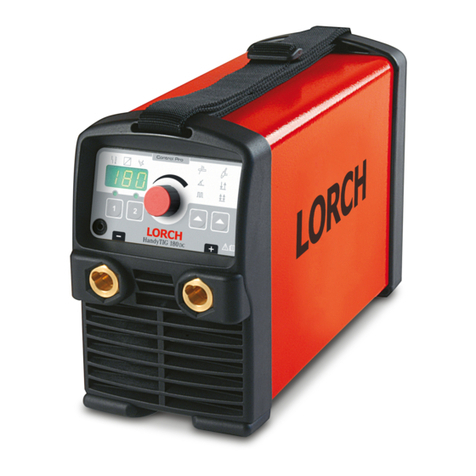
LORCH
LORCH HandyTIG 180 DC Basic Plus User manual
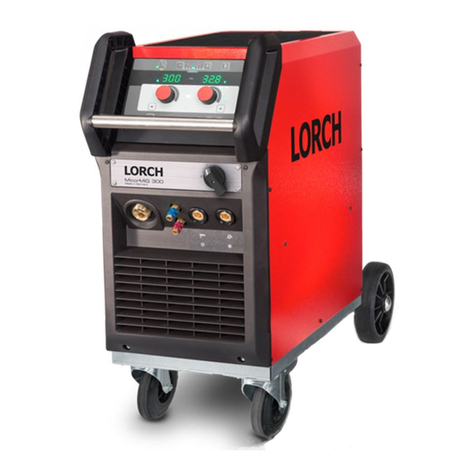
LORCH
LORCH MicorMIG Series User manual
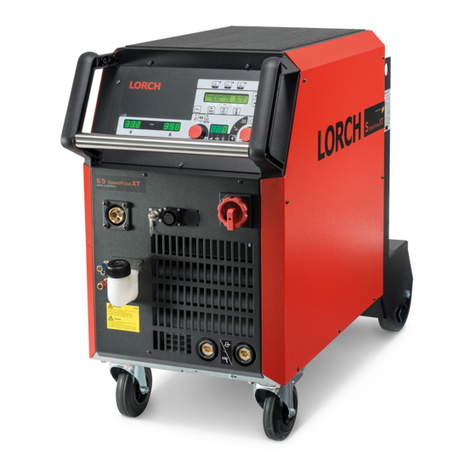
LORCH
LORCH S-Pulse User manual
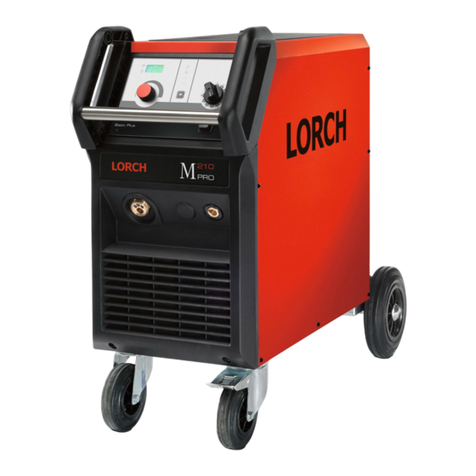
LORCH
LORCH M-Pro BasicPlus User manual
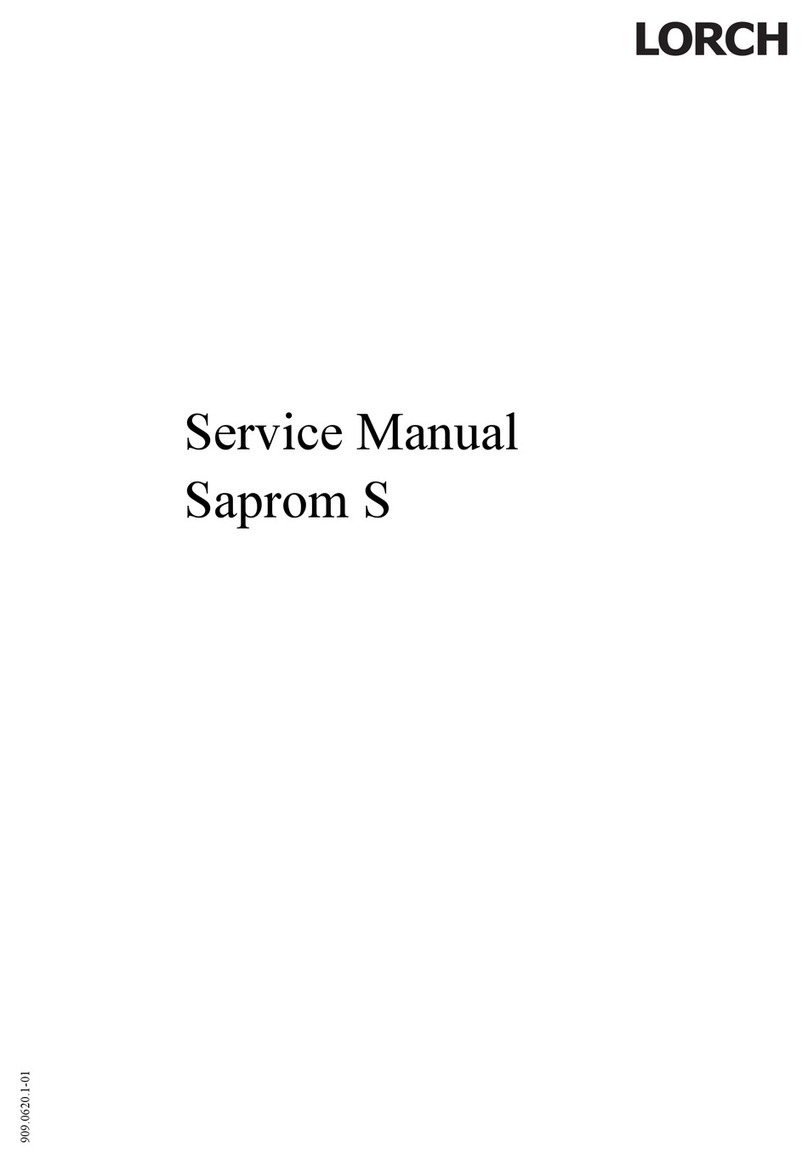
LORCH
LORCH Saprom S User manual
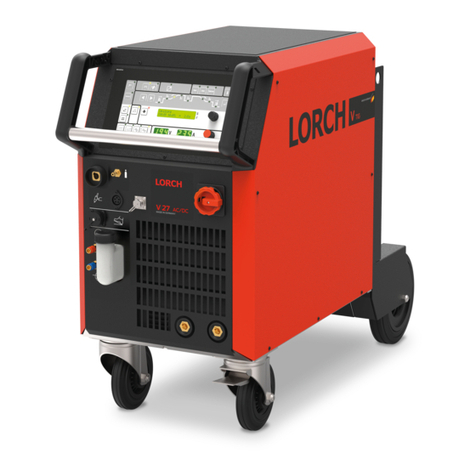
LORCH
LORCH V Series User manual

LORCH
LORCH M-Pro Performance Series User manual

LORCH
LORCH ControlPro T-Series User manual
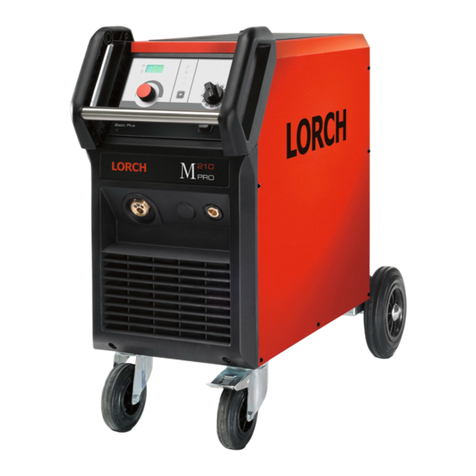
LORCH
LORCH M-Pro BasicPlus User manual
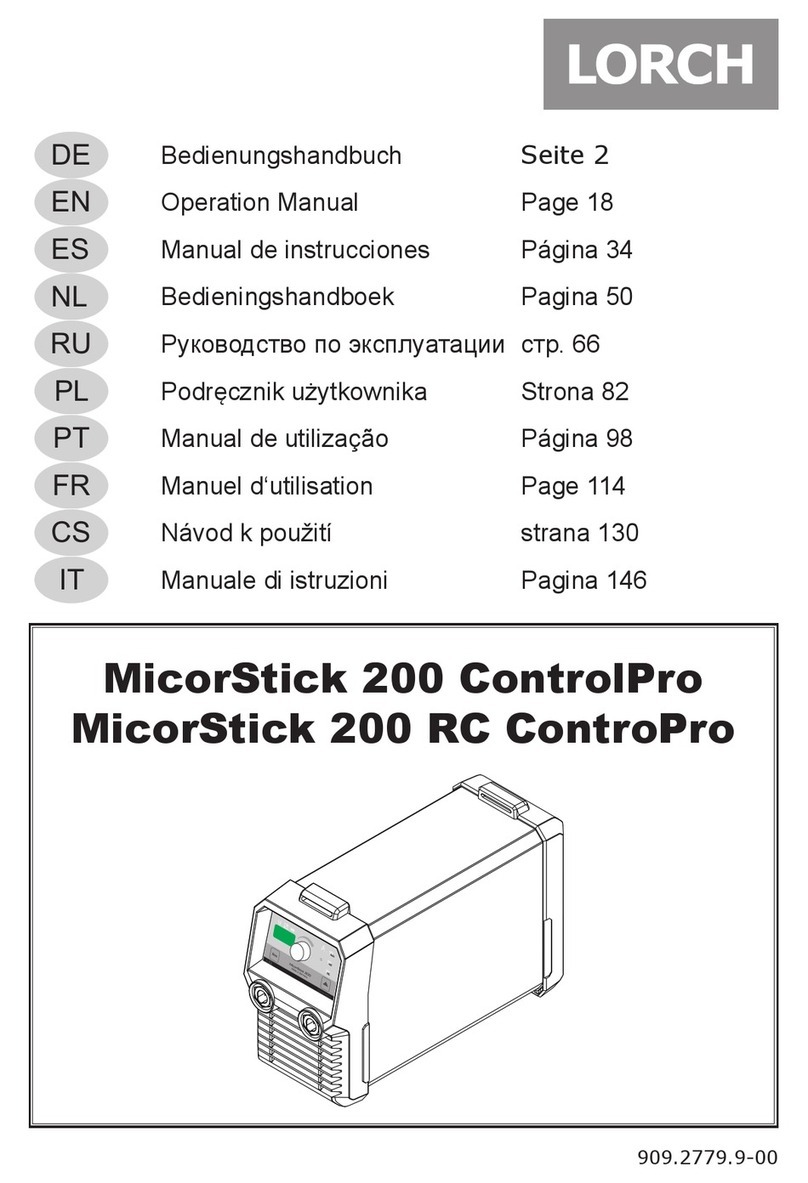
LORCH
LORCH MicorStick 200 ControlPro User manual