Nic Mercury/PE-1000 User manual

PE-1000 Service Manual
Document Number
NIC-704-2016-01 Date of Issue
November
20, 2017
Control Department
Technical Service Gr Page 0 / 52
PE-1000 Type-B
(S/N: 14870001-16870025)
Service Manual
Nippon Instruments Corporation
Technical Service Gr
Date Prepared Checked Approved
First Edition
November
20, 2017 Mamezaki
Kinoshita Yamada Kato

1
Revision History
Revision
No. Revision Date
Reason for Changes Prepared Approved
01 November 20,
2017 First Edition issued Mamezaki
Kinoshita
Kato
PE-1000 (Type-B)
Service Manual
Document Number
NIC-704-2016-01 Date of Issue
November
20, 2017
Control Department
Technical Service Gr Page 1 / 52

2
Mercury Analyzer
Mercury/PE-1000 (Type-B) Service Manual
Contents
1. Introduction.....................................................................................................................4
2. Troubleshooting..............................................................................................................5
2.1. Alarm/error messages .............................................................................................................................. 5
2.1.1. PE-1................................................................................................................5
2.1.2. HT-300A..........................................................................................................7
2.2. Other problems ............................................................................................................................................ 8
3. Maintenance (how to replace and adjust the parts and components)........................9
3.1. Cautions on maintenance. ..................................................................................................................... 9
3.2. PE-1 ................................................................................................................................................................... 9
3.2.1. Mercury collector tube.....................................................................................9
3.2.2. Sample heating tube .....................................................................................12
3.2.3. Disassembling the sample injection section and replacing the septum.........15
3.2.4. Replacing the tube of the automatic discharge pump....................................16
3.2.5. Replacing the automatic discharge pump .....................................................16
3.2.6. Replacing and cleaning the solenoid valves (V1-V5) ....................................17
3.2.7. Solenoid valves (V6-V7)................................................................................18
3.2.8. Mass flow controllers (HIGH and LOW) ........................................................20
3.2.9. Adjusting the mercury lamp and reference voltage .......................................21
3.2.10. Heaters (H-1 to 3)..........................................................................................22
3.2.11. Heater (H-5) ..................................................................................................23
3.2.12. H5 thermocouple...........................................................................................24
3.2.13. Main board ....................................................................................................25
3.2.14. Activated charcoal on the outlet side.............................................................26
3.2.15. Activated charcoal on the inlet side...............................................................27
3.2.16. Cell................................................................................................................27
3.2.17. SSRs.............................................................................................................29
3.2.18. Switching power supplies..............................................................................30
3.2.19. Calibrating the flow sensor............................................................................32
3.2.20. Adjusting the sensitivity of the optical unit.....................................................33
3.3. HT-300A ........................................................................................................................................................ 34

3
NIC-.704-2016-01
3.3.1. Demount HT-300A.........................................................................................34
3.3.2. Exchange Syringe and setting (Touch & Plunger Zero). ..............................34
3.3.3. Injection Set Up.............................................................................................37
3.3.4. Borders mark -out..........................................................................................38
3.3.5. Potentiometer for Needle ..............................................................................40
3.3.6. Potentiometer for Tray...................................................................................42
3.3.7. Potentiometer for Turret ................................................................................44
3.3.8. Potentiometer for Plunger and Needle connection cable. .............................47
4. Cleaning parts and maintenance.................................................................................51
4.1. How to clean parts .................................................................................................................................... 51
4.2. Mercury Collector maintenance ........................................................................................................ 51
4.3. Combustion tube maintenance .......................................................................................................... 51
4.4. Flow diagram of PE-1000 ..................................................................................................................... 52

1. Introduction
4
NIC-.704-2016-01
1. Introduction
This document describes procedures and methods for replacing and adjusting the
components and parts of the PE-1000 Type-B (S/N: 14870001 to 16870025). The work
requires disassembly, reassembly, and reinspection of the analyzer. For basic operations,
refer to the Instruction Manual.

2. Troubleshooting
5
NIC-704-2016-01
2. Troubleshooting
2.1. Alarm/error messages
2.1.1. PE-1
Message Description and CorrectiveAction
STAND-BY xx:xx
Appears for 20 minutes after the power is turned on.
Because the heater and the optical system are still unstable
during the countdown period, any measured data in the
period is unreliable.
LAMP LIFE EXCEEDED Appears when the time for which the lamp has been
powered on exceeds 5,000 hours.
CARBON FILTER FULL!! Appears when 1.5 g or more of mercury has been absorbed
in the activated carbon on the outlet side of measured gas.
SEPTUM COUNTS EXCEEDED!! Appears when the measurements are made more than 500
times. Replace the septum.
SYRINGE LIFE EXCEEDED!! Appears when the syringe has been driven more than
10,000 times. Replace the syringe.
H1 INTERLOCK
Possible cable break at the thermocouple of the H1 heater
or possible short-circuit with the heater line.
Check that the tip of the thermocouple is not in contact with
the heater line.
H2 INTERLOCK
Possible cable break at the thermocouple of the H2 heater
or possible short-circuit with the heater line.
Check that the tip of the thermocouple is not in contact with
the heater line.
H3 INTERLOCK
Possible cable break at the thermocouple of the H3 heater
or possible short-circuit with the heater line.
Check that the tip of the thermocouple is not in contact with
the heater line.
H4 INTERLOCK
Possible cable break at the thermocouple of the H4 heater
or possible disconnection of the H4 heater.
If the connector has come off, turn off the power and plug in
the connector.
H5 INTERLOCK Possible cable break at the thermocouple of the H5 heater.
Replace it.
RH INTERLOCK
Possible cable break at the thermocouple of the RH heater
or possible disconnection of the RH interlocking cable.
If the cable has come off, turn off the power and connect the
cable.
H2 is still warming up. The heater has not reached the setup temperature.
H3 is still warming up. The heater has not reached the setup temperature.
H4 is still warming up. The heater has not reached the setup temperature.
CELL is dirty. Appears when the SIG voltage is high during standby.
Wipe the optical cell with alcohol or the like.

2. Troubleshooting
6
NIC-704-2016-01
Message Description and CorrectiveAction
A/D FULL
Appears when the detected voltage of the optical unit rises
above the specified value (the Sig or Ref voltage is equal to
or higher than 5V). Wipe the optical cell with alcohol or the
like.
HT INJECTION ERROR
Appears when the syringe washing bottle of the sample
changer is not set in place. Set the bottle and restart the
process.
LAMP BROKEN
Appears when the light quantity of the lamp (REF voltage)
drops below the specified value (0.5V).
FLOW ERROR
Appears when the flow rate of the carrier gas drops below
the specified value (equal to or lower than half the setup
value).
HEATER BROKEN (H1)
Appears when the temperature does not rise at the H1
heater.
Possible cable break or possible failure of the control
system.
HEATER BROKEN (H5)
Appears when the temperature does not rise at the H5
heater.
Possible cable break or possible failure of the control
system.
HEATER BROKEN (RH)
Appears when the temperature does not rise at the RH
heater.
Check that the RH-PE is powered on.
COOLING ERROR (H1)
Appears when the H1 heater cools down too slowly.
FAN-1 may not be running.
COOLING ERROR (H5)
Appears when the H5 heater cools down too slowly.
FAN-2 may not be running.
COOLING ERROR (RH)
Appears when the RH heater cools down too slowly.
FAN-RH may not be running.
HEATER TEMP ERROR (H1)
The H1 heater is overheated. Possible problem with the
heater control.
HEATER TEMP ERROR (H2)
The H2 heater is overheated. Possible problem with the
heater control.
HEATER TEMP ERROR (H3)
The H3 heater is overheated. Possible problem with the
heater control.
HEATER TEMP ERROR (H4)
The H4 heater is overheated. Possible problem with the
heater control.
CASING FAN BROKEN
The rotation of the casing fan is not detected.
It is necessary to replace the casing fan.

2. Troubleshooting
7
NIC-704-2016-01
2.1.2. HT-300A
Error message Failed Condition Action
Check “touch sensor”
Touch sensor failure
Syringe is improperly installed. Check Needle guide.
TRAY ① remove
waiting Tray Tray is removed. Put back tray
TRAY ① not Identified
Waiting Tray
Failed in identifying tray. Retry to put tray.
Obstacle found,
press“EXIT”then remove
Mixed obstacle mixed.
Position error. Remove obstacle.
Boarders Mark-out
Waste absence. Put in,
then press “START” Failed in identifying Waste bottle. Boarders Mark-out
Vial absence. Put in,
then press “START” Failed in identifying vial. Boarders Mark-out

2. Troubleshooting
8
NIC-704-2016-01
2.2. Other problems
Problem Cause Action Refer to
High blank value Contamination inside the
line Continuously carry out measurement
with distilled water.
Replace the syringe and septum.
Replace the sample heating tube,
collector tube, and joints.
Replace the valve.
3.2.1–3
Low sensitivity Contamination inside the
line Continuously carry out measurement
with distilled water.
Replace the syringe and septum.
Replace the sample heating tube,
collector tube, and joints.
Replace the valve.
3.2.1–3
Poor calibration of the
standard sample
Presence of leak
Recalibrate the standard sample.
Conduct leak check and identify the
leak spot.
Bad peak shape Improper method and
sample volume Review the analysis method.
Defective mercury
collector tube or defective
sample heating tube
Replace the mercury collector tube.
Replace the sample heating tube. 3.2.1
3.2.2
Presence of leak Disconnected or loose
line
Poor calibration of the
flow sensor
Failure of the flow sensor
Retighten the joint or replace the line.
Recalibrate the flow sensor.
Replace the flow sensor.
Misalignment of
injector position Poor adjustment of the
injector position Realign the injector position
Vial detection
failure Poor adjustment in the
detection of vertical
positions (The horizontal
positions are detected
properly)
Poor adjustment in the
detection of horizontal
positions
Execute the Touch and Plunger Zero.
Execute the Borders Mark-Out
(BMO).
Malfunction and
abnormal noise of
needle
Failure of the touch
sensor
Failure of the needle
motor assembly
Clean the metal blocks and touch
sensor.
Replace the turret head and flex
cable.
Malfunction and
abnormal noise of
plunger
Failure of the plunger
motor assembly Replace the plunger motor assembly
and flex cable.
Malfunction and
abnormal noise of
turret
Breakage of antifriction
tape
Failure of the motor
assembly and encoder
Replace the antifriction tape.
Replace the turret motor assembly,
encoder, and flex cable.

3.
Maintenance
9
NIC-700-2009-02
3. Maintenance (how to replace and adjust the parts and
components)
This chapter describes methods and procedures for replacing and adjusting the parts and
components.
3.1. Cautions on maintenance.
Warning
• Shut off the power supply before starting the maintenance work. Otherwise, you may
suffer an electric shock.
Caution
• Before you conduct the maintenance of the heater section, be sure to turn off the power
switch and allow the heater to cool down to roughly room temperature. Otherwise, you
may burn yourself.
• Be careful when you touch any glass parts. Otherwise, you may damage them.
3.2. PE-1
3.2.1. Mercury collector tube
(1) Turn off the power, and allow it to cool down for at least 30 minutes.
* It is very dangerous to conduct this work while the machine is activated. Be sure to
cool down the machine before work.
(2) Open the front cover of the measuring section.
(3) Remove the jacket heater.

3.
Maintenance
10
NIC-700-2009-02
(4) Loosen the screw of the retaining plate of the sample heating tube, and slide the plate to the
left.
(5) Loosen the joint connected to the sample injection section as well as the joint connected to
the gas-liquid separating bottle.
(6) Loosen the five screws fixing the heaters H1, 2, and 3.
(7) Loosen the nut of the reducing T-joint.

3.
Maintenance
11
NIC-700-2009-02
(8) Slide the heaters H1, 2, and 3 to the left, and remove the reducing T-joint.
(9) Loosen the nut of the T-joint on the right side of the collector tube, and pull out the collector
tube to the left. If it is difficult to pull out the collector tube, remove the cover of the heater H5
and pull it out.
(10) Remove the T-joint.
* When attaching the collector tube, ensure that the three lugs of the dents are located on the
right side from the collector agent (cell side).
* To attach the tube, reverse the removal procedure.
* After tightening the Teflon joint by hand, further tighten it 1/8 turn. Too much tightening damages
the screw thread.

3.
Maintenance
12
NIC-700-2009-02
3.2.2. Sample heating tube
(1) Turn off the power, and allow it to cool down for at least 30 minutes.
* It is very dangerous to conduct this work while the machine is activated. Be sure to
cool down the machine before work.
(2) Open the front cover of the measuring section.
(3) Remove the jacket heater.
(4) Loosen the screw of the retaining plate of the sample heating tube, and slide the plate to the
left.
(5) Loosen the joint connected to the sample injection section as well as the joint connected to the
gas-liquid separating bottle, and remove them.
(6) Loosen the lower screw of the sample injection section, and remove the sample injection
section.

3.
Maintenance
13
NIC-700-2009-02
(7) Loosen the metal nuts on the upper and right side of the reducing T-joint.
(8) Loosen the upper, lower, left, and right screws (five screws) fixing the heater unit, and slide the
unit to the left.
(9) Remove the two hand screws on top and bottom of the heater cover, remove the cover, and
remove the heat insulation of H2 and H3.

3.
Maintenance
14
NIC-700-2009-02
(10) Loosen the screws fixing the thermocouples for H1, H2, and H3, and pull out the
thermocouples from the heater wire.
(11) Pull out the sample heating tube upward, and replace it.
(12) Assemble the parts by reversing the above procedure.
* To set each thermocouple again, push it in from the left side so that its exposed tip
touches the dent of the sample heating tube but does not touch the heater wire.
* If any of the tips touch the heater wire, the thermocouple malfunctions and the heater
cannot increase its temperature normally.
(13) After assembly, conduct the leak check.
(14) Readjust the sample injector position of the sample changer.
Tip of
thermocouple

3.
Maintenance
15
NIC-700-2009-02
3.2.3. Disassembling the sample injection section and replacing the septum
(1) Check that the power is turned off.
* After turning off the power, cool down the machine for at least 30 minutes and then carry out
the following work.
(2) Open the front cover of the measuring section.
(3) Hold the branch line at the sample injection section, rotate the dish plate counterclockwise,
and then remove it.
(4) Take out the septum with tweezers or other tools, and replace it.
(5) Attach the sample injection section by reversing the removal procedure.
(6) Conduct the leak check.
(7) Readjust the sample injector position of the sample changer.

3.
Maintenance
16
NIC-700-2009-02
3.2.4. Replacing the tube of the automatic discharge pump
As a guide, replace the pump tube after one year or 400 hours of operation. Note that a
deterioration of the tube may cause a failure of the pump.
(1) Turn off the power of the analyzer, and pull the tube out of the pump.
(2) Remove the bluish plastic cover from the pump by pulling the left side toward you.
(3) Put the pump and the tube back in place.
3.2.5. Replacing the automatic discharge pump
(1) Open the side plate in accordance with Section 3.2.7
(2) Remove the connector.
(3) Hold the pump body (gray part), lightly push the hook located on the upper side, and pull out
the pump.
(4) Replace it with a new pump, and put it back in place.
Replace the tube.
If the rotor does not run, apply
silicone grease.

3.
Maintenance
17
NIC-700-2009-02
3.2.6. Replacing and cleaning the solenoid valves (V1-V5)
(1) Open the front door, and remove the two screws. When they are removed, you can open the
front panel.
(2) The valves are installed on the back of the front panel. The following photo shows the
installation positions of the valves. (The valves V1-V5 are the same models.)
V1 V2 V3 V4
V5

3.
Maintenance
18
NIC-700-2009-02
(3) Detach each valve from the analyzer by removing the two screws from the bottom of the valve
and disconnecting connectors and tubes.
(4) Replace the valve with a new one.
(5) You can also remove the two screws from the bottom of each valve, disassemble each
solenoid valve, immerse its plastic parts into nitric acid (1+10), and wash them with an
ultrasonic cleaner.
* A large amount of oil adheres to the valves V1 and V4 because they are installed on the line
through which volatile components pass.
3.2.7. Solenoid valves (V6-V7)
(1) Open the front panel in accordance with Section 3.2.6, and remove the one screw and the two
tubes from the analyzer side.

3.
Maintenance
19
NIC-700-2009-02
(2) Open the side plate by pushing it to the left. The valves V6 and V7 are installed in the upper
part of the analyzer.
(3) Detach each valve from the analyzer by removing the two fixing screws from the bottom of the
valve and disconnecting three tubes and an electric connector.
(4) Remove two screws each from the upper and lower parts of the valve body.
V6
V7
Table of contents
Other Nic Measuring Instrument manuals
Popular Measuring Instrument manuals by other brands
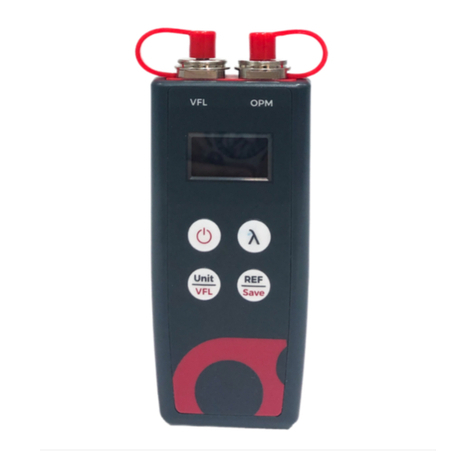
Ascentac
Ascentac OPM110 user guide
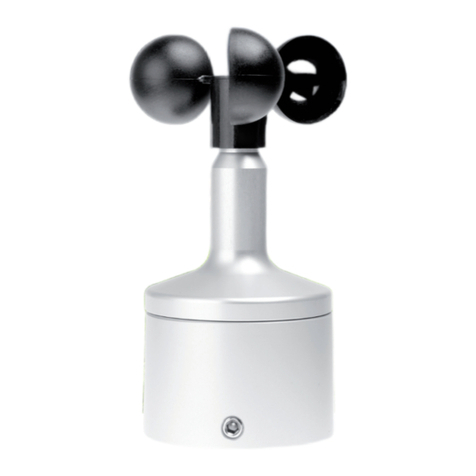
Lambrecht
Lambrecht AEM ECONOMY user manual
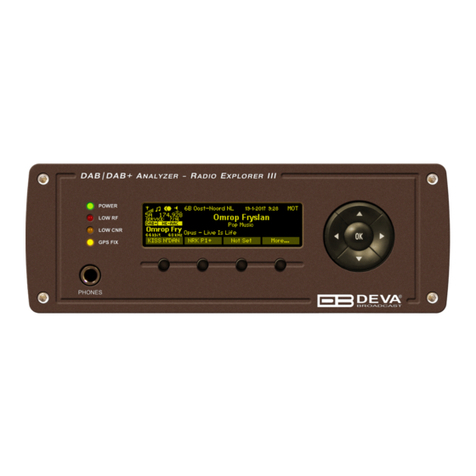
DEVA Broadcast
DEVA Broadcast Radio Explorer III DAB Maintenance and operation instruction manual

RigExpert
RigExpert AA-200 user manual

Pasco Scientific
Pasco Scientific SF-9214 Instruction manual and experiment guide
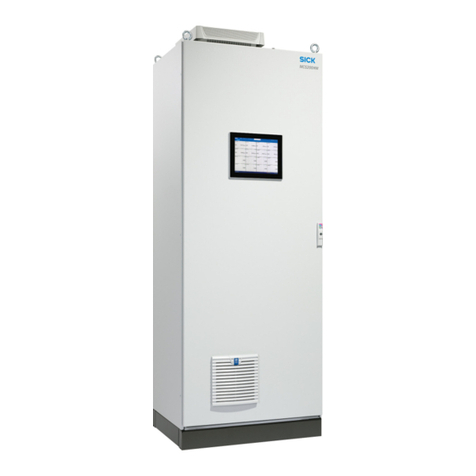
SICK
SICK MCS200HW Service manual