Omron A22TK User manual

1
Safety Key Selector Switch
A22TK
Key-type Selector Switch with Direct
Opening Mechanism
• Selector Switch for secure equipment activation during
maintenance
• 30 types of exclusive keys make it more difficult to disable.
• The trapped key of the D4JL Guard Lock Safety-door Switch
hasthesameshape asthe lockoutkeyof theD4GL-SK10-LK@,
D4SL-NSK10-LK@ Slide Key Unit. Units can be combined to
improve safety.
(Specify the same key type.)
• Common to the switch part of Emergency Stop Switch A22E.
(Non-lighted model only)
Features
BecausetheA22TKSafety KeySelector Switchusesthesame keyastheGuard LockSafety-door Switch,the operatoris preventedfromforgetting
to remove the key. The result is a safer working environment when performing maintenance.
For safety precautions for all pushbutton switches, refer to the website
at: www.ia.omron.com, and “Safety Precautions” on page 12 in this
catalog.
For the most recent information on models that have been certified for
safety standards, refer to your OMRON website.
Broad range of applications include use with door locks, mode switching, and emergency stops when teaching
Common Key for Door Switch and Selector Switch
With the Selector Switch, it is possible to
switch between normal operation mode
(use of Door Switch is available) and
maintenance mode (use of Enabling
Grip Switch is available).
A22TK
Safety Key
Selector Switch Safety Key
Selector Switch
Guard Lock
Safety-door Switch Guard Lock
Safety-door Switch
G9SX-GS
Safety Controllers
such as Safety Guard
Switching Unit
A4EGD4GL-SK10-LK@
D4SL-NSK10-LK@
A22TK
Enabling
Grip Switch
D4JL
D4JL
D4GL-SK10-LK@
D4SL-NSK10-LK@
Common Key
*To unify keys, specify the same key type.

A22TK
2
Key: Cannot be removed
I take the key with me when
I enter, so there is no worry
of becoming trapped inside!
Guard Lock
Safety-door Switch
Safety can be ensured, but there is a risk of human error
occurring during operation.
By using a common key, the risk of human error is reduced in operations
from when the door is open/shut until the equipment is started.
From
When only the Door Switch is used, the operator is at risk of being
shut inside the barrier if, for example, he/she forgets to remove the
trapped key and a third party locks the door.
The equipment may also be started up while the operator is inside.
The two locks on the door and equipment use the same key, reducing the likelihood that the user will forget to remove it.
In addition, the key cannot be removed when maintenance is being performed.This prevents the key from being lost and greatly
reduces the risk of an operator becoming trapped inside.
+
Forgetting to
remove the key
Assumed risks
Being
trapped inside Forgetting to
remove the key Being
trapped inside
Assumed risks
Starting equipment
To
Guard Lock Safety-door Switch only
The safety level is enhanced by switching to maintenance mode.
However, because two different types of keys are required,
the operator is still at risk of being shut inside if he/she forgets to
remove the trapped key.
Guard Lock Safety-door Switch Key Selector Switch (A22K)
+
Guard Lock Safety-door Switch Safety Key Selector Switch (A22TK)
I should close it.I should close it.
I'm trapped
inside!
The equipment
started up!
Operation starts
Common key
Furthermore
Different keys
Lock the door
4
End maintenance
3
Start maintenance
Operation stopped
RUN
MAINTENANCE
Key: Can be removed
LOCKUNLOCK
RUN
MAINTENANCE
Key: Can be removed
Unlock the door
Operation stopped
Operation double-stopped
Key: Cannot be removed
LOCKUNLOCK
1
1
2
3
4
2
Same Key
Same Key
A22TK
A22TKD4JL
D4JL
D4JL
Safety Key
Selector Switch
A22TK
Enabling Grip Switch Safety Laser Scanner
during maintenance and by using aBy using the to detect
the presence of operators, equipment malfunctions can be prevented when operators are inside, enabling a higher safety level.
or Safety Mat

A22TK
3
Model Number Structure
Model Number Legend (Ordering as a set)
The Operation Unit and Switch are delivered as a set. For information on combinations, refer to Ordering Information
on page 5.
The models numbers of only Operation Units are they same as the set model numbers without (2) Contact
Configuration.
Example: The model number of the Operation Unit from the A22TK-2LL-12-K01 Set is A22TK-2LL-K01.
Ask your OMRON representative about parts without model numbers when ordering.
(1) (2) (3) (4)
A22TK- 2LL -12-K01
(1) Operation Unit
Symbol No. of
notches Key release position
Key position of NC contact closing
2LL
2
2RL
2LR
2RR
(3) Key Availability
Symbol Type
None No key
KWith key
(4) Key Type
01 to 30: 30 types *
(2) Contact Configuration
Symbol Type
01 SPST-NC
11 SPST-NO/SPST-NC
02 DPST-NC
12 DPST-NC + SPST-NO
21 DPST-NO + SPST-NC
03 TPST-NC
* Key can be created up to 30 types. Specify keys in
order starting from 01.
Key drop preventive type
A22TK-@-@-@01-SJ
―
――
(1) (2) (3)
(1) Operation Unit
Symbol No. of
notches Key release position
Key position of NC
contact closing
2LL
2
2RL
2LR
2RR
(3) Key Availability
Symbol Type
None No key
KWith key
(2) Contact Configuration
Symbol Type
01 SPST-NC
11 SPST-NO/SPST-NC
02 DPST-NC
12 DPST-NC+SPST-NO
21 DPST-NO+SPST-NC
03 TPST-NC

A22TK
4
Key drop preventive (on the A22TK-2RL-@)
Contact Configuration
A22TK-2@L
A22TK-2@R
Operation Angle
*1. If the key is stopped at a position between FP and TTP, the contacts will not be in the states indicated above.
Always be careful to turn the key completely to the FP (HP) or TTP position to ensure that the contacts are properly switched and the direct
open circuit operation characteristics are obtained.
*2. Key drop preventive type (A22TK-@-SJ or A22TK-@-SJ only)
Key position SPST-NC SPST-NO/SPST-NC DPST-NC DPST-NC + SPST-NO DPST-NO + SPST-NO TPST-NC
Key position SPST-NC SPST-NO/SPST-NC DPST-NC DPST-NC + SPST-NO DPST-NO + SPST-NO TPST-NC
Operating rangeOperating range
NC contact: ON
Key: Hold NC contact: OFF
Key: Removed NC contact: ON
Key: Hold NC contact: OFF
Key: Removed
NC contact: OFF
Key: Hold
Key drop preventive typeStandard type
TTP 90° FP
90°
15° 15°
FP
HP
HP
*1 *1
*2*2
FP : Free position
TTP
: Total travel position
HP : Key hold position (drop prevention) *2
A22TK-2L@
A22TK-2L@-SJ A22TK-2R@
A22TK-2R@-SJ

A22TK
5
Ordering Information
Switch
List of Models (Completely Assembled)...Shipped as a set which includes the Operation Unit and Switch.
The models numbers of only Operation Units are they same as the set model numbers without (2) Contact Configuration.
Example: The model number of the Operation Unit from the A22TK-2LL-12-K01 Set is A22TK-2LL-K01.
Ask your OMRON representative about parts without model numbers when ordering.
Appearance Key release
position Key position of NC
contact closing Contact Configuration Key
availability Model
SPST-NC
Yes
A22TK-2LL-01-K01
SPST-NO/SPST-NC A22TK-2LL-11-K01
DPST-NC A22TK-2LL-02-K01
DPST-NC + SPST-NO A22TK-2LL-12-K01
DPST-NO + SPST-NC A22TK-2LL-21-K01
TPST-NC A22TK-2LL-03-K01
SPST-NC A22TK-2RL-01-K01
SPST-NO/SPST-NC A22TK-2RL-11-K01
DPST-NC A22TK-2RL-02-K01
DPST-NC + SPST-NO A22TK-2RL-12-K01
DPST-NO + SPST-NC A22TK-2RL-21-K01
TPST-NC A22TK-2RL-03-K01
SPST-NC A22TK-2LR-01-K01
SPST-NO/SPST-NC A22TK-2LR-11-K01
DPST-NC A22TK-2LR-02-K01
DPST-NC + SPST-NO A22TK-2LR-12-K01
DPST-NO + SPST-NC A22TK-2LR-21-K01
TPST-NC A22TK-2LR-03-K01
SPST-NC A22TK-2RR-01-K01
SPST-NO/SPST-NC A22TK-2RR-11-K01
DPST-NC A22TK-2RR-02-K01
DPST-NC + SPST-NO A22TK-2RR-12-K01
DPST-NO + SPST-NC A22TK-2RR-21-K01
TPST-NC A22TK-2RR-03-K01
SPST-NC
No
A22TK-2LL-01-01
SPST-NO/SPST-NC A22TK-2LL-11-01
DPST-NC A22TK-2LL-02-01
DPST-NC + SPST-NO A22TK-2LL-12-01
DPST-NO + SPST-NC A22TK-2LL-21-01
TPST-NC A22TK-2LL-03-01
SPST-NC A22TK-2RL-01-01
SPST-NO/SPST-NC A22TK-2RL-11-01
DPST-NC A22TK-2RL-02-01
DPST-NC + SPST-NO A22TK-2RL-12-01
DPST-NO + SPST-NC A22TK-2RL-21-01
TPST-NC A22TK-2RL-03-01
SPST-NC A22TK-2LR-01-01
SPST-NO/SPST-NC A22TK-2LR-11-01
DPST-NC A22TK-2LR-02-01
DPST-NC + SPST-NO A22TK-2LR-12-01
DPST-NO + SPST-NC A22TK-2LR-21-01
TPST-NC A22TK-2LR-03-01
SPST-NC A22TK-2RR-01-01
SPST-NO/SPST-NC A22TK-2RR-11-01
DPST-NC A22TK-2RR-02-01
DPST-NC + SPST-NO A22TK-2RR-12-01
DPST-NO + SPST-NC A22TK-2RR-21-01
TPST-NC A22TK-2RR-03-01

A22TK
6
Accessories
Note: For information on two-hole and three-hole control boxes, contact your OMRON representative.
The Switch Block, Mounting Latch, Connector, and Lock Plate of A22E can be used.
Appearance Key release
position Key position of NC
contact closing Contact Configuration Key
availability Model
SPST-NC
Yes
A22TK-2LL-01-K01-SJ
SPST-NO/SPST-NC A22TK-2LL-11-K01-SJ
DPST-NC A22TK-2LL-02-K01-SJ
DPST-NC + SPST-NO A22TK-2LL-12-K01-SJ
DPST-NO + SPST-NC A22TK-2LL-21-K01-SJ
TPST-NC A22TK-2LL-03-K01-SJ
SPST-NC A22TK-2RL-01-K01-SJ
SPST-NO/SPST-NC A22TK-2RL-11-K01-SJ
DPST-NC A22TK-2RL-02-K01-SJ
DPST-NC + SPST-NO A22TK-2RL-12-K01-SJ
DPST-NO + SPST-NC A22TK-2RL-21-K01-SJ
TPST-NC A22TK-2RL-03-K01-SJ
SPST-NC A22TK-2LR-01-K01-SJ
SPST-NO/SPST-NC A22TK-2LR-11-K01-SJ
DPST-NC A22TK-2LR-02-K01-SJ
DPST-NC + SPST-NO A22TK-2LR-12-K01-SJ
DPST-NO + SPST-NC A22TK-2LR-21-K01-SJ
TPST-NC A22TK-2LR-03-K01-SJ
SPST-NC A22TK-2RR-01-K01-SJ
SPST-NO/SPST-NC A22TK-2RR-11-K01-SJ
DPST-NC A22TK-2RR-02-K01-SJ
DPST-NC + SPST-NO A22TK-2RR-12-K01-SJ
DPST-NO + SPST-NC A22TK-2RR-21-K01-SJ
TPST-NC A22TK-2RR-03-K01-SJ
SPST-NC
No
A22TK-2LL-01-01-SJ
SPST-NO/SPST-NC A22TK-2LL-11-01-SJ
DPST-NC A22TK-2LL-02-01-SJ
DPST-NC + SPST-NO A22TK-2LL-12-01-SJ
DPST-NO + SPST-NC A22TK-2LL-21-01-SJ
TPST-NC A22TK-2LL-03-01-SJ
SPST-NC A22TK-2RL-01-01-SJ
SPST-NO/SPST-NC A22TK-2RL-11-01-SJ
DPST-NC A22TK-2RL-02-01-SJ
DPST-NC + SPST-NO A22TK-2RL-12-01-SJ
DPST-NO + SPST-NC A22TK-2RL-21-01-SJ
TPST-NC A22TK-2RL-03-01-SJ
SPST-NC A22TK-2LR-01-01-SJ
SPST-NO/SPST-NC A22TK-2LR-11-01-SJ
DPST-NC A22TK-2LR-02-01-SJ
DPST-NC + SPST-NO A22TK-2LR-12-01-SJ
DPST-NO + SPST-NC A22TK-2LR-21-01-SJ
TPST-NC A22TK-2LR-03-01-SJ
SPST-NC A22TK-2RR-01-01-SJ
SPST-NO/SPST-NC A22TK-2RR-11-01-SJ
DPST-NC A22TK-2RR-02-01-SJ
DPST-NC + SPST-NO A22TK-2RR-12-01-SJ
DPST-NO + SPST-NC A22TK-2RR-21-01-SJ
TPST-NC A22TK-2RR-03-01-SJ
Name Appearance Classification Model Remarks
Control Box One hole, yellow box
(for emergency stop) A22Z-B101Y Material: Polycarbonate resin

A22TK
7
Specifications
Approved Standard Ratings
• UL, cUL (File No. E41515): 6 A at 220 VAC, 10 A at 110 VAC
• TÜV (EN60947-5-1) (Low Voltage Directive): 3 A at 220 VAC
• CCC (GB14048.5): 3 A at 240 VAC, 1.5 A at 24 VDC
Certified Standards
Note: Only models with NC contacts have a direct opening mechanism.
*1. UL-certification for CSA C22.2 No. 14 has been obtained. (Certification has been obtained for the Switch Unit only)
Ratings
Contacts (Standard load)
Note: 1. Rated current values are determined according to the testing conditions. The above ratings were obtained by conducting tests under the
following conditions.
(1) Ambient temperature: 20±2C°
(2) Ambient humidity: 65±5% RH
(3)Operating frequency: 20 operations/minute
2. Minimum applicable load: 10 mA at 5 VDC
Characteristics
*1. Malfunction within 1 ms.
*2. With no icing or condensation.
*3. The degree of protection from the front of the panel.
Note: 1. Do not allow the load current to exceed the rated value.
2. The contact ON/OFF timing is not synchronized. Confirm performance before application.
3. Once the contacts have been used to switch a load, however, they cannot be used to switch smaller loads. The contact surfaces will
become rough once they have been used and contact reliability for smaller loads may be reduced.
Certification body Standards File No.
UL *1 UL508, C22.2 No.14 E41515
TÜV SÜD EN60947-5-1
(certified direct opening mechanism) Consult your OMRON
representative for details.
CQC(CCC) GB14048.5 2003010303070635
KOSHA EN60947-5-1 2009-156
Rated carry current
(A)
Rated voltage
(V)
Rated current (A)
AC15
(inductive load) AC12
(resistive load) DC13
(inductive load) DC12
(resistive load)
10
24 VAC 10 10
--
110 5 10
220 3 6
380 2 3
440 1 2
24 VDC
--
1.5 10
110 0.5
2
220 0.2
0.6
380 0.1
0.2
Item Model A22TK
Allowable operating
frequency Mechanical 30 operations/minute max.
Electrical 30 operations/minute max.
Insulation resistance 100 MΩmin. (at 500 VDC)
Dielectric strength
Between terminals
of same polarity 2,500 VAC, 50/60 Hz for 1 min.
Between each
terminal and ground 2,500 VAC, 50/60 Hz for 1 min.
Vibration resistance *1 10 to 55 Hz, 1.5-mm double amplitude (within 1 ms)
Shock resistance Destruction 1000 m/s2
Malfunction *1 250 m/s2max.
Durability Mechanical 100,000 operations min.
Electrical 100,000 operations min.
Ambient operating temperature *2 -20 to +70°C
Ambient operating humidity 35% to 85%RH
Ambient storage temperature -40 to +70°C
Degree of protection IP65 *3
Electric shock protection class Class II
PTI (tracking characteristic) 175
Degree of contamination 3 (EN60947-5-1)

A22TK
8
Structure and Nomenclature
Dimensions (Unit: mm)
Terminal Arrangement (Bottom View)
Terminal Connection
2 Contacts 3 Contacts
Type Terminal connection (Bottom View)
SPST-NO/SPST-NC DPST-NC DPST-NC + SPST-NO DPST-NO + SPST-NC TPST-NC
Non-lighted
Key * Two keys are provided.
Contact Ratings
10 A at 110 VAC (resistive load)
10 A at 24 VDC (resistive load)
Contact Configuration
SPST-NC, SPST-NO/SPST-NC, DPST-NC, DPST-NC + SPST-NO, DPST-NO + SPST-NC, and TPST-NC
Switch
Lock Plate (attached with the Switch)
(Refer to "Mounting the Lock Plate" on page 13 for use.)
(The above figures are examples of the model with key.)
Operation Unit
Key
5.9
Lock Plate (included)
(A22Z-3380)
1
10.9
0.5
34
54.7
16.5
32.6
32.2
30 dia.
29.5 dia.
27 dia.
Key
5.9
Lock Plate (included)
(A22Z-3380)
1
10.9
0.5
30 dia.
29.5 dia.
27 dia.
34
54.7
16.5
32.6
32.2
A22TK-2LL A22TK-2RL
OPEN
LOC
20.7
16.7
Switch blocks
M3.5 screws
OPEN
LOC
10
16.7
Switch blocks
3
4
1
2
1
2
1
2
3
4
1
2
1
2
3
4
3
4
1
2
1
2
1
2
1
2

A22TK
9
Application Examples
●Application Overview
•Switching between normal operation mode and maintenance mode is performed manually.
•In normal operation mode, the power supply to the motor M2 is turned OFF when the guard is opened.
•In maintenance mode, the power supply to the motor M2 is turned OFF when the enabling switch is released or strongly gripped.
•
In normal operation mode and maintenance mode, the power supply to the motor M1 and M2 is turned OFF when the emergency stop switch is pressed.
●Evaluation example
Note: The above PL is only the evaluation result of the example concerning solely the mode selection. The PL must be evaluated in an actual
application by the customer after confirming the usage conditions.
●Circuit Diagram
PL/safety category Model Stop category Reset
PLe/4 equivalent
Safety Key Selector Switch A22TK-2@@-11 (SPST-NO/SPST-NC type)
Guard lock Safety-door Switch
D4NL-@A@A-@, -@A@B-@, -@A@C-@ (Mechanical Lock Type)
Enabling Grip Switch A4EG
Safety Guard Switching Unit G9SX-GS226-T15
Flexible Safety Unit G9SX-BC202 (24 VDC)
−−
KM4
KM3
+24V
M2
KM4
KM3
KM4KM3
PLC etc.
Open Open
OpenOpen
Feedback loop
S14
A2
S24 S44 S54
L1
X3X2X1 X4
T11
A1
T12 T21
Y1 Y3
T22 T61 T62
M1 M2
T71
Y2 Y4
T72 T31 T32 T33 T41 T42
OFF
AND
Auto
Manual
G9SX-GS226-T15 (Unit 2)
Control circuit
(2)
(1)
(4)
(3)
S3
S7
+24V
GND
S14
A2
S24
L1 L2
X1 X2
T11
A1
T12 T21 T22 T31 T32 T33
Y1
KM2
KM1
S2
12
11 21
22
+24V
KM1 KM2
M1
KM2
KM1
PLC etc.
S1
+24V
Open
Feedback loop
Emergency Stop
Switch
Guard lock
Safety-door Switch
G9SX-BC202 (Unit 1)
Control circuit
GND
Indicator
(Diagnostic check enabled) Indicator
(Diagnostic check enabled)
Enabling
Switch
S4
OPEN
S5
KM3
KM4
41
42
11
12
Stop signal
Guard
Lock release signal
S6
UA UB
+24V
Selector Switch
A22TK
S8
<
G9SX-BC202(Unit 1)
>
Reset switch S2
KM1, KM2
NC contact
KM1, KM2
NO contact
KM3, KM4
NC contact
KM3, KM4
NO contact
Unit 1
Logical AND output L1
Unit 2
Logical AND input T41
Lock release
switch
Emergency
Stop Switch S1
Guard lock
safety-door switch
S4
Mode selection
input M2
Mode selection
input M1
Reset switch S7
Enabling Switch S3
S5
Unit 1 S14, S24
(10)
(8)(3)
(6)(4)
(1)
Unit 2 S14, S24
(2)
(7)(5) (9)
<
G9SX-GS226-T15(Unit 2)
>
Timing Chart
S1: Emergency Stop Switch
S2, S7: Reset switches
S3: Enabling Switch
S4: Guard lock Safety-door Switch
S5: Lock release switch
S6: Safety limit switch
S8: A22TK Safety Key Selector
Switch
KM1 to KM4: Contactors
M1 to M2: 3-phase motor
(1) The G9SX-GS starts in operation mode.
(2) The mode switches to maintenance
mode.
(3) The operator opens the guard and
performs maintenance work.
(4) The Enabling Switch is gripped to the
middle position.
(5) The G9SX-GS starts in maintenance
mode.
(6) The G9SX-GS will stop when the
Enabling Switch is released or gripped.
(7) The G9SX-GS will start again after the
guard is closed and the mode is
switched to operation mode.
(8) The G9SX-GS will stop and the guard
can be opened when the stop signal is
input while in operation mode.
(9) The guard is closed and the G9SX-GS
starts again.
(10)All the units will stop if the emergency
stop is pressed.

A22TK
10
●Application Overview
(1)In normal operation mode, the power supply to the motor M is turned ON when the reset switch S7 is pressed while the rotator is stopped and
the guard is locked after closed.
(2)The PLC sends high speed rotation command to the motor controller.
(3)The stop signal is applied with the S8.
(4)The PLC sends deceleration command to the motor controller.
(5)The guard can be unlocked when the rotator slows down to the safe speed.
(6)The power supply to the motor M is turned OFF when the guard is unlocked with the S5.
(7)The mode switches to maintenance mode with the mode selection switch.
(8)The PLC sends low speed rotation command to the motor controller.
(9)The power supply to the motor M is automatically turned ON again by gripping the enabling switch to the middle position.
(10)The operator opens the guard and performs maintenance work.
●Evaluation example
Note: The above PL is only the evaluation result of the example concerning solely the mode selection. The PL must be evaluated in an actual
application by the customer after confirming the usage conditions.
●Circuit Diagram
PL/safety category Model Stop category Reset
PLd/3 equivalent
Safety Key Selector Switch A22TK-2@@-11 (SPST-NO/SPST-NC type)
Guard lock Safety-door Switch
D4NL-@A@A-@, -@A@B-@, -@A@C-@ (Mechanical Lock Type)
Enabling Grip Switch A4EG
Low-speed Monitoring Unit G9SX-LM224-F10-R@
Flexible Safety Unit G9SX-BC202 (24 VDC)
−−
S1
Emergency Stop
Switch
Feedback loop
KM1
KM2
T42T41T33T32T31
Y2
T71 T72T62T61
M2M1
Y1
T22T21T12T11
A1
D22D21D12D11
X4X3X2X1L1
ES2ES1S24S14
A2
M
KM2
KM1
Motor controller
Lock release
switch
S5 E2E1
41
42
12
11
11
12 S3
open
Guard
S8
Stop signal
+24V
S6
OpenOpen
+24V
S7
Enabling
Switch
AND
OFF
Rotator (interlocked with M)
KM2KM1
Indicator
+24V
GND
G9SX-LM224-F10
Blue
BlackBrownBlackBrown
Control circuit
S4
Guard lock
Safety-door Switch
21
22
11
12
Open
Y1
T33
T32
T31T22T21T12T11
A1
+24V
G9SX-BC202
Control circuit
PLC etc.
X2X1
L2L1
S24S14
A2
S2
Selector Switch
A22TK
High speed rotation
Guard can be opened.
Guard closed --> opened
Emergency Stop Switch S1
Reset switch S2
Logical AND output L1
Safety limit switch S3
Guard lock
Safety-door Switch S4
KM1, KM2 NC contact
KM1, KM2 NO contact
(Operation instruction to the motor)
Motor rotation
Lock release signal
(Safe speed detection output) ES1
Lock release switch S5
Mode selection input M1
Mode selection input M2
Enabling Switch S7
Low speed rotation
Timing Chart
S1: Emergency Stop Switch
S2: Reset switch
S3: Safety limit switch
S4: Guard lock Safety-door Switch
S5: Lock release switch
S6: A22TK Safety Key Selector Switch
S7: Enabling switch
S8: Stop signal
KM1, KM2: Contactor
M: 3-phase motor

A22TK
11
Installation
Mounting to the Panel
Installing/Removing the Switch Blocks
(1) Preparing the Panel (3) Mounting the Switch on the Operation Unit
(2) Mounting the Operation Unit on the Panel (4) Removing the Switch
• The panel dimensions are shown below.
• Recommended panel thickness: 1 to 5 mm.
• A Lock Ring is provided as a standard feature.
•When painting or coating the panel, make sure that the specified panel
dimensions apply to the panel after painting or coating.
22.3 dia.
3.2 2-R0.8MAX.
+0.4
0
+0.2
0
+0.4
0
24.1
• Insert the Operation Unit into the Switch Unit, aligning the arrow mark
inscribed on the Case with the lever on the Switch Blocks, then move the
lever in the direction indicated by the arrow in the following figure.
Switch Unit
Lever
Arrow mark
Operation Unit
• Insert the Operation Unit from the front surface of the panel, insert the Lock
Ring and the mounting ring from the terminal side, then tighten the ring.
Before tightening, check that the rubber washer is present between the
Operation Unit and the panel.
• Tighten the mounting ring at a torque of 0.98 to 1.96 N·m.
•When using a Lock Ring, insert the projecting part into the lock slot, and
then tighten the mounting ring.
22 dia.
22 dia.
+0.4
0
24.1+0.4
0
Key Operation Unit Arrow mark Projecting part Mounting ring
Rubber washer Panel Lock Ring
• Move the lever in the direction indicated by the arrow in the following figure,
then pull the Operation Unit or the Switch Blocks. Since the lever has a hole
with an inside diameter of 6.5 mm, the lever can be moved in the specified
direction by inserting a screwdriver into the hole and then moving the screw-
driver.
OPEN
LOCK
Screwdriver
(1) Installing the Switch Blocks (2) Removing the Switch Blocks Wiring
• Hook the small protrusion on the Mounting Latch
into the groove on the other side of the lever,
then push up the Switch Block in the direction
indicated by the arrow in the figure below.
Switch block
Mounting Latch
Lever
Protrusion
• Insert a screwdriver between the Mounting Latch
and the Switch Block, then push down the
screwdriver in the direction indicated by the
arrow in the following figure.
Use either of the following screwdrivers.
Flat-head screwdriver 3 to 6 mm
3 to 6 mm dia.
Phillips screwdriver
Screwdriver
• Loosen the terminal screw from the Switch
Unit until it completely comes off the groove,
insert a screwdriver as shown in the follow-
ing figure, then push up the washer in the
direction indicated by the arrow to tempo-
rarily secure it. Now, a round crimp terminal
can be connected. After inserting the termi-
nal, tighten the screws to complete wiring.
Screwdriver
Washer
Screw

A22TK
12
Safety Precautions
Be sure to read the precautions for All Pushbutton Switches in the website at:http://www.ia.omron.com/.
Indication and Meaning for Safe Use
Installation Environment
• Do not use the switch in locations where explosive or flammable
gasses may be present.
• Do not use the switch submerged in oil or water or in locations
continuously subject to splashes of oil or water. Doing so may
result in oil or water entering the switch.
Wiring
• Connect a fuse in series with the A22TK to protect it from
shortcircuit damage. The value of the breaking current of the fuse
must be calculated by multiplying the rated current by 150% to
200%.
When using the A22TK for an EN rating, use a 10-A fuse of type gI
or gG that complies with IEC 60269.
• Always make sure that the power is turned OFF before wiring the
Switch.
Also, do not touch the terminals or other current-carrying ports
while power is being supplied.
• Check the contact specifications before mounting the Switch
Block. Use an NC contact for a safety circuit. It may not operate
properly. Check the Switch Block for safe operation before use.
• Check the operating specification before mounting the Operation
Unit.Itmaynot operateproperly.Check theOperation Unitfor safe
operation before use.
Installation
• Do not drop the Switch. Doing so may prevent the Switch from
functioning to its full capability.
• Make sure the Switch is mounted securely to prevent it from falling
off. Otherwise injury may result.
• Mount the Operation Key so that it will not come into contact with
persons in the area when the door is opened and closed. Injury
may result.
• Do not use a Switch as a stopper. Otherwise, the switch may be
damaged and may not operate properly.
• Be sure to use the supplied Lock Ring. Otherwise, the switch may
rotate and may not operate properly.
Others
• Do not attempt to disassemble or modify the Switch. Doing so may
cause the Switch to malfunction.
• The durability of the Switch is greatly influenced by the switching
conditions. Always test the switch under actual working conditions
before application and use it in a switching circuit for which there
are no problems with performance.
• The user must not maintain or repair equipment incorporating the
Switch. Contact the manufacturer of the equipment for any
maintenance or repairs required.
Indicates an imminently hazardous
situation which, if not avoided, is likely to
result in serious injury or may result in
death. Additionally there may be severe
property damage.
Indicatesapotentially hazardoussituation
which, if not avoided, may result in minor
or moderate injury or in property damage.
Precautions
for Safe Use Supplementary comments on what to do
or avoid doing, to use the product safely.
Precautions
for Correct
Use
Supplementary comments on what to do
or avoid doing, to prevent failure to
operate, or undesirable effect on product
performance.
DANGER
Always confirm that safety functions are operational
before stating operation. Wiring mistakes, setting
mistakes, switch failure or other factors may prevent
safety functions from operating. This may result in the
machine continuing to operate, possibly resulting in
human accidents.
CAUTION
If the Operation Unit is separated from the Socket Unit,
the equipment will not stop, creating a hazardous
condition.
Secure the lever on the Socket Unit by using the A22Z-
3380 Lock Plate so that the Operation Unit cannot be
easily separated from the Socket Unit.
(Refer to “Mounting the Lock Plate” at the right.)
[Used in combination with a Slide Key]
The machine may operate, possibly causing injury.
Do not disable safety function by using a spare door
switch operation key or spare key with the door
open.
[Used outside/inside hazardous area]
The machine may operate, possibly causing injury.
Do not disable safety function by using a spare key
outside or inside the hazardous area.
DANGER
CAUTION
Precautions for Safe Use

A22TK
13
Operating Environment
• This Switch is designed for use indoors.
Using the Switch outdoors may damage it.
• Donot usetheSwitchwhere corrosivegases(e.g., H2S,SO2, NH3,
HNO3, or CI2) are present or in locations subject to high
temperature and humidity. Doing so may result in damage to the
Switch as a result of contact failure or corrosion.
• Do not use the Switch in any of the following locations.
• Locations subject to extreme temperature changes
• Locations subject to high humidity or condensation
• Locations subject to excessive vibration
• Locations where metal dust, processing waste, oil, or chemicals
may enter through the protective door
• Locations subject to detergents, thinners, or other solvents
Storage
• Do not store the Switch where corrosive gases (e.g., H2S, SO2,
NH3,HNO3,or Cl2)or dustis present,orin locationssubject tohigh
temperature or high humidity.
Mounting
• Do not tighten the mounting ring more than necessary using tools
such as pointed-nose pliers. Doing so will damage the mounting
ring. The tightening torque is 0.98 to 1.96 N·m.
• Recommended panel thickness: 1 to 5 mm.
Mounting the Lock Plate
1. Confirm that the lever on the Mounting Latch is on the side where
the Operation Unit is secured and then insert the protrusion on the
Lock Plate into the hole in the lever on the Mounting Latch.
2. Press the hole on the Lock Plate onto the protrusion on the Mount-
ing Latch until it clicks into place.
After mounting the Lock Plate, check that the lever does not move.
Operating the Key
•When rotating the key to the total travel position or free position,
the operating force must be 1.47 N·m max.
Wiring
• Terminal screws must be Phillips or slotted M3.5 screws with a
square washer.
• The tightening torque is 1.08 to 1.27 N·m.
• Single wires, stranded wires, and crimp terminals can be
connected to the Switch
• Applicable Wiring Materials:
Twisted strands: 2 mm2max.
Solid wire: 1.6 mm dia. max.
• After wiring the Switch, maintain an appropriate clearance and
creepage distance.
• Do not pull the lead wires with excessive force. Doing so may
disconnect them.
• The cable cannot be bended repeatedly.
•When bending the cable, provide a bending radius of 45 mm min.
so as not to damage the cable insulation or sheath. Excessive
bending may cause fire or leakage current.
Operating Environment
• The IP65 model is designed with a protective structure so that it
willnotsustain damageifitissubjected towater fromany direction
to the front of the panel.
• The Switch is intended for indoor use only. Using the Switch
outdoor may cause it to fail.
Using the Microload
Contact failure may occur if a Switch designed for a standard load is
used to switch a microload. Use Switches within the application
ranges shown in the following graph. Even within the application
range, insert a contact protection circuit, if necessary, to prevent the
reduction of life expectancy due to extreme wear on the contacts
caused by loads where inrush current occurs when the contact is
opened and closed.
The minimum applicable load is the N-level reference value. This
value indicates the malfunction reference level for the reliability level
of 60% (λ60) (conforming to JIS C5003).
The equation, λ60 = 0.5 x 10-6/time indicates that the estimated
malfunction rate is less than 1/2,000,000 with a reliability level of
60%.
Precautions for Correct Use
LOCK
OPEN
Lever Lock Plate
Mounting Latch
2.
1.
Operation Unit
8 mm max.
16.0 mm max. 20.2 mm max.
8 mm dia. max. 8 mm max.
16.0 mm max. 20.2 mm max.
8 mm dia. max.
Naked Crimp Terminals Crimp Terminals with
Insulating Sheaths
Microload area Area of use
Standard
load area
Invalid area
0.1 1 10 100 1,000
10mA
1mA
5
12
24
30 0.16mA
Voltage (V)
1.6mA 100mA
Current (mA)
0

A22TK
14
Others
• If the panel is to be coated, make sure that the panel meets the
specified dimensions after coating.
• Due to the structure of the Switch, severe shock or vibration may
cause malfunctions or damage to the Switch.
Also, most Switches are made from resin and will be damaged if
they come into contact with sharp objects. Particularly scratches
on the Operation Unit may create visual and operational
obtrusions.
Handle the Switches with care, and do not throw or drop them.
• Perform maintenance inspections periodically.
• Do not use the key switch to stop/start the machine.
• Mode switching by key must be performed by the operator
specified in the operating manual.
• Apply load current not to exceed the rated value.
• The contact ON/OFF timing is not synchronized. Confirm
performance before application.
Do not place or drop
heavy objects
on the Switch.
Do not operate the Switch
with hard or sharp objects.
Screwdriver
Hammer
Do not allow the Switch
to drop and hit the floor.

READ AND UNDERSTAND THIS CATALOG
Please read and understand this catalog before purchasing the products. Please consult your OMRON representative if you have any questions
or comments.
Warranty and Limitations of Liability
WARRANTY
OMRON’s exclusive warranty is that the products are free from defects in materials and workmanship for a period of one year (or other period if
specified) from date of sale by OMRON.
OMRON MAKES NO WARRANTY OR REPRESENTATION, EXPRESS OR IMPLIED, REGARDING NON-INFRINGEMENT,
MERCHANTABILITY, OR FITNESS FOR PARTICULAR PURPOSE OF THE PRODUCTS. ANY BUYER OR USER ACKNOWLEDGES THAT
THE BUYER OR USER ALONE HAS DETERMINED THAT THE PRODUCTS WILL SUITABLY MEET THE REQUIREMENTS OF THEIR
INTENDED USE. OMRON DISCLAIMS ALL OTHER WARRANTIES, EXPRESS OR IMPLIED.
LIMITATIONS OF LIABILITY
OMRON SHALL NOT BE RESPONSIBLE FOR SPECIAL, INDIRECT, OR CONSEQUENTIAL DAMAGES, LOSS OF PROFITS OR
COMMERCIAL LOSS IN ANY WAY CONNECTED WITH THE PRODUCTS, WHETHER SUCH CLAIM IS BASED ON CONTRACT, WARRANTY,
NEGLIGENCE, OR STRICT LIABILITY.
In no event shall responsibility of OMRON for any act exceed the individual price of the product on which liability is asserted.
IN NO EVENT SHALL OMRON BE RESPONSIBLE FOR WARRANTY, REPAIR, OR OTHER CLAIMS REGARDING THE PRODUCTS UNLESS
OMRON’S ANALYSIS CONFIRMS THAT THE PRODUCTS WERE PROPERLY HANDLED, STORED, INSTALLED, AND MAINTAINED AND
NOT SUBJECT TO CONTAMINATION, ABUSE, MISUSE, OR INAPPROPRIATE MODIFICATION OR REPAIR.
Application Considerations
SUITABILITY FOR USE
OMRON shall not be responsible for conformity with any standards, codes, or regulations that apply to the combination of products in the
customer’s application or use of the product.
At the customer’s request, OMRON will provide applicable third party certification documents identifying ratings and limitations of use that apply
to the products. This information by itself is not sufficient for a complete determination of the suitability of the products in combination with the end
product, machine, system, or other application or use.
The following are some examples of applications for which particular attention must be given. This is not intended to be an exhaustive list of all
possible uses of the products, nor is it intended to imply that the uses listed may be suitable for the products:
• Outdoor use, uses involving potential chemical contamination or electrical interference, or conditions or uses not described in this document.
• Nuclear energy control systems, combustion systems, railroad systems, aviation systems, medical equipment, amusement machines, vehicles,
safety equipment, and installations subject to separate industry or government regulations.
• Systems, machines, and equipment that could present a risk to life or property.
Please know and observe all prohibitions of use applicable to the products.
NEVER USE THE PRODUCTS FOR AN APPLICATION INVOLVING SERIOUS RISK TO LIFE OR PROPERTY WITHOUT ENSURING THAT
THE SYSTEM AS A WHOLE HAS BEEN DESIGNED TO ADDRESS THE RISKS, AND THAT THE OMRON PRODUCT IS PROPERLY RATED
AND INSTALLED FOR THE INTENDED USE WITHIN THE OVERALL EQUIPMENT OR SYSTEM.
Disclaimers
CHANGE IN SPECIFICATIONS
Product specifications and accessories may be changed at any time based on improvements and other reasons.
It is our practice to change model numbers when published ratings or features are changed, or when significant construction changes are made.
However, some specifications of the product may be changed without any notice. When in doubt, special model numbers may be assigned to fix
or establish key specifications for your application on your request. Please consult with your OMRON representative at any time to confirm actual
specifications of purchased products.
DIMENSIONS AND WEIGHTS
Dimensions and weights are nominal and are not to be used for manufacturing purposes, even when tolerances are shown.
ERRORS AND OMISSIONS
The information in this document has been carefully checked and is believed to be accurate; however, no responsibility is assumed for clerical,
typographical, or proofreading errors, or omissions.
PERFORMANCE DATA
Performance data given in this catalog is provided as a guide for the user in determining suitability and does not constitute a warranty. It may
represent the result of OMRON’s test conditions, and the users must correlate it to actual application requirements. Actual performance is subject
to the OMRON Warranty and Limitations of Liability.
PROGRAMMABLE PRODUCTS
OMRON shall not be responsible for the user’s programming of a programmable product, or any consequence thereof.
Copyright and Copy Permission
COPYRIGHT AND COPY PERMISSION
This document shall not be copied for sales or promotions without permission.
This document is protected by copyright and is intended solely for use in conjunction with the product. Please notify us before copying or
reproducing this document in any manner, for any other purpose. If copying or transmitting this document to another, please copy or transmit it in
its entirety.

Authorized Distributor:
In the interest of product improvement,
specifications are subject to change without notice.
Cat. No. A189-E1-01 Printed in Japan
0409
© OMRONCorporation 2009 All Rights Reserved.
OMRON Corporation Industrial Automation Company
Regional Headquarters
OMRON EUROPE B.V.
Wegalaan 67-69-2132 JD Hoofddorp
The Netherlands
Tel: (31)2356-81-300/Fax: (31)2356-81-388
Contact: www.ia.omron.com
Tokyo, JAPAN
OMRON ASIA PACIFIC PTE. LTD.
No. 438A Alexandra Road # 05-05/08(Lobby 2),
Alexandra Technopark,
Singapore 119967
Tel: (65) 6835-3011/Fax: (65) 6835-2711
OMRON (CHINA) CO., LTD.
Room 2211, Bank of China Tower,
200Yin Cheng Zhong Road,
PuDong NewArea, Shanghai, 200120, China
Tel: (86) 21-5037-2222/Fax: (86) 21-5037-2200
OMRON SCIENTIFICTECHNOLOGIES INC.
6550 Dumbarton Circle, Fremont
CA 94555-3605 U.S.A.
Tel: (1) 510-608-3400/Fax: (1) 510-744-1442
CSM_7_1_0515
Table of contents
Other Omron Switch manuals
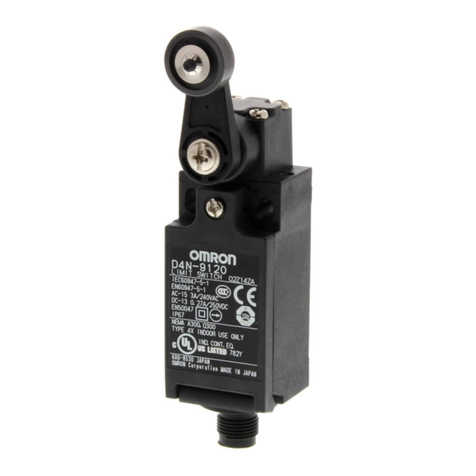
Omron
Omron D4N Series User manual
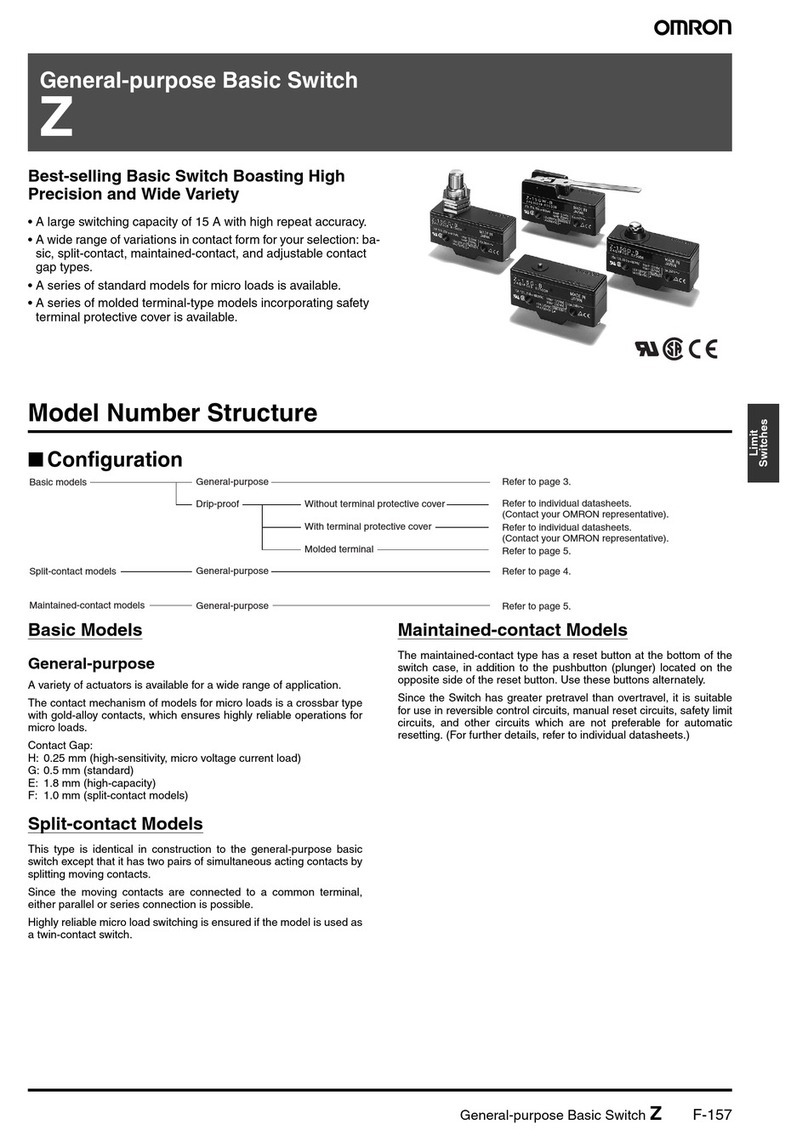
Omron
Omron Z User manual
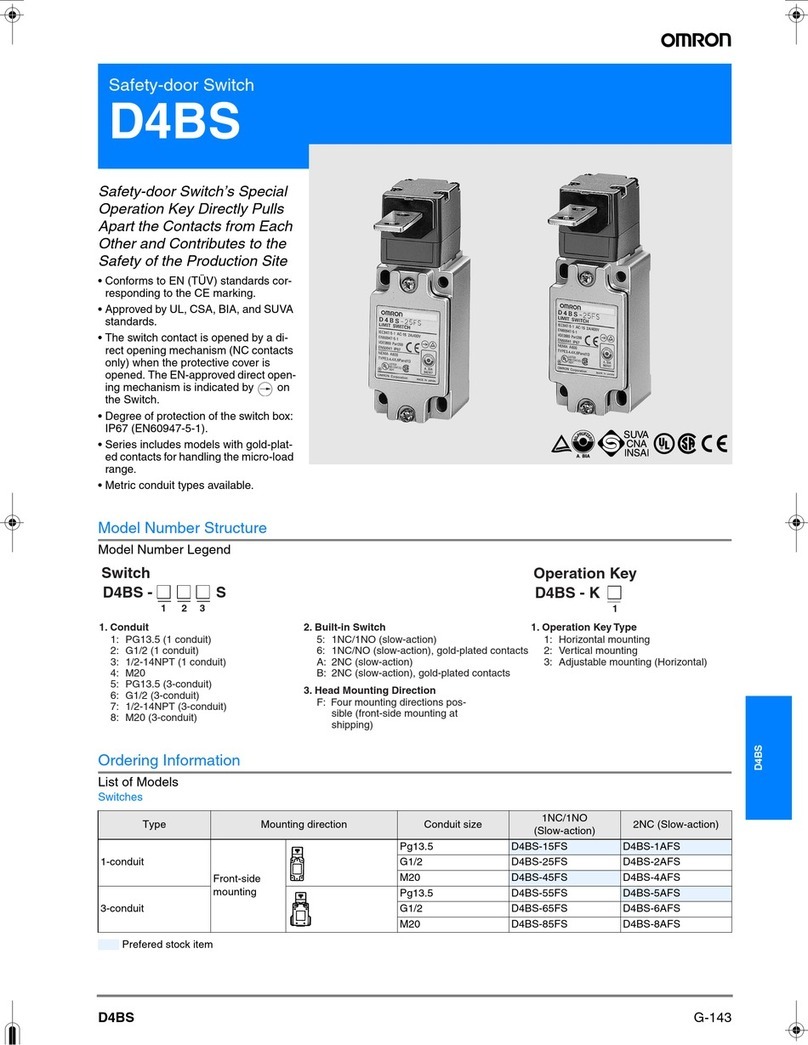
Omron
Omron D4BS - User manual
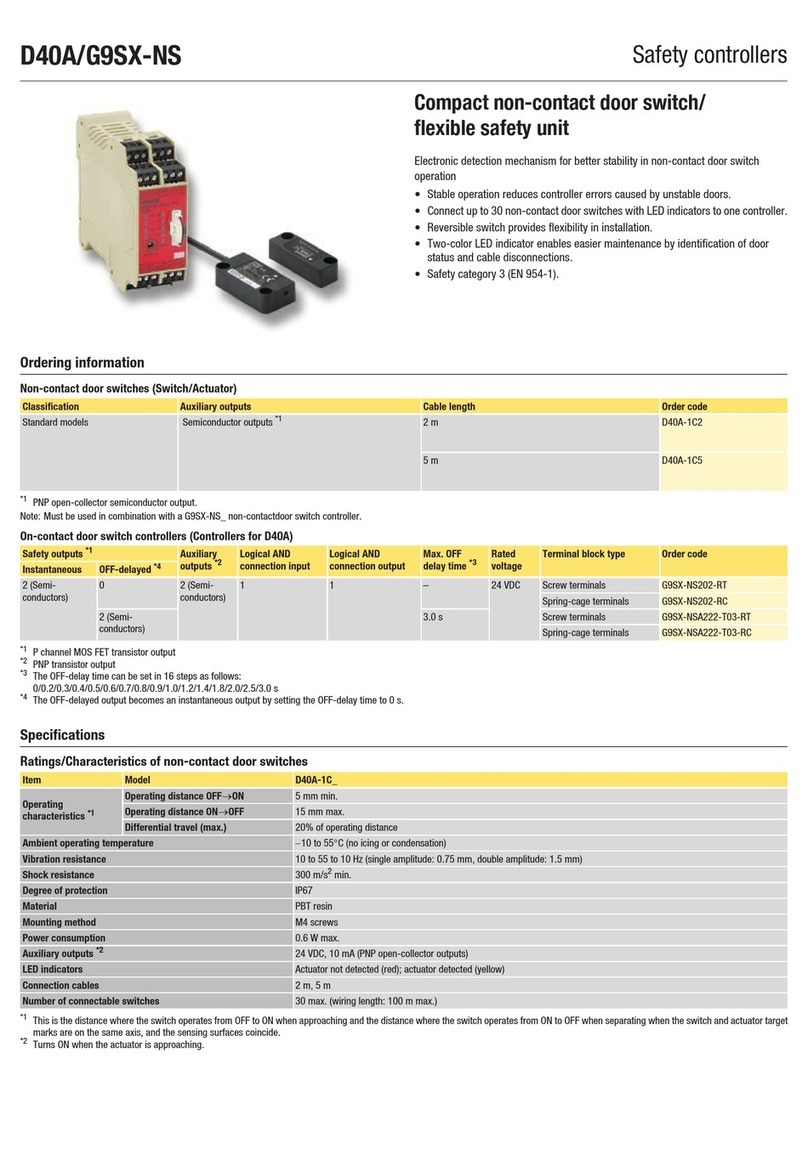
Omron
Omron D40A-G9SX-NS - User manual
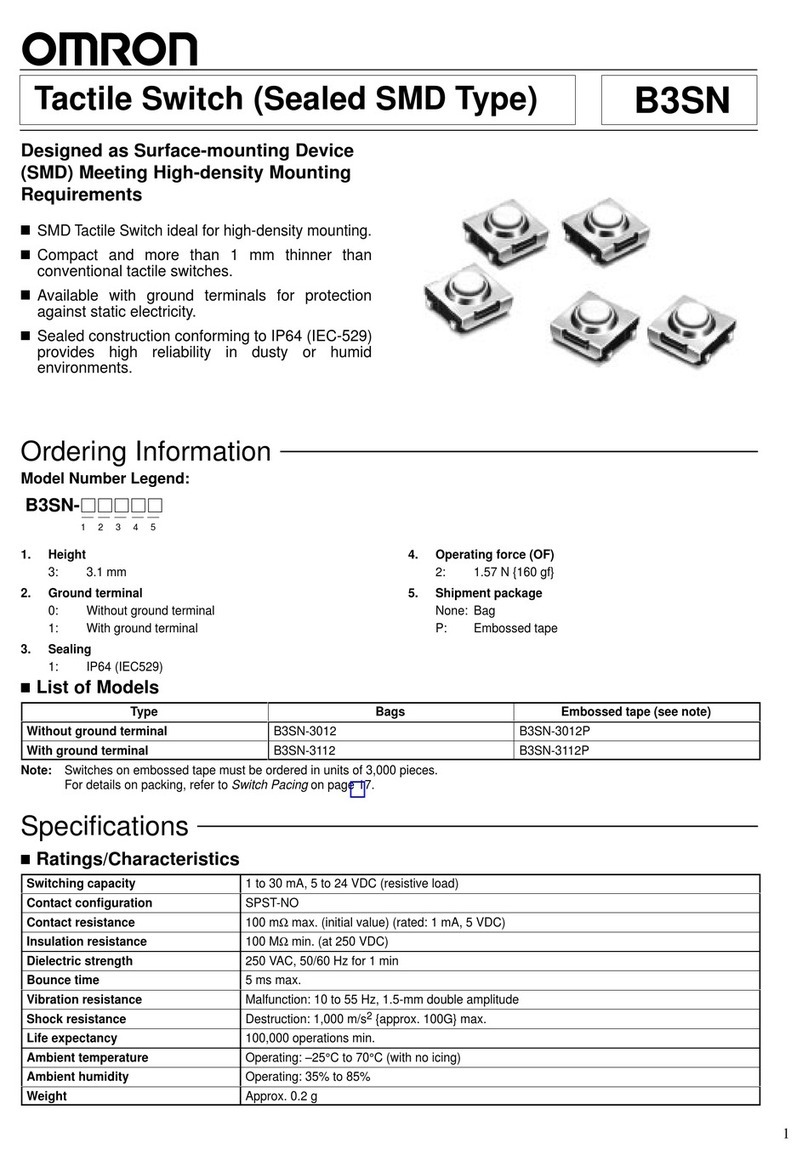
Omron
Omron B3SN-3012 User manual

Omron
Omron D4CC-1001 User manual
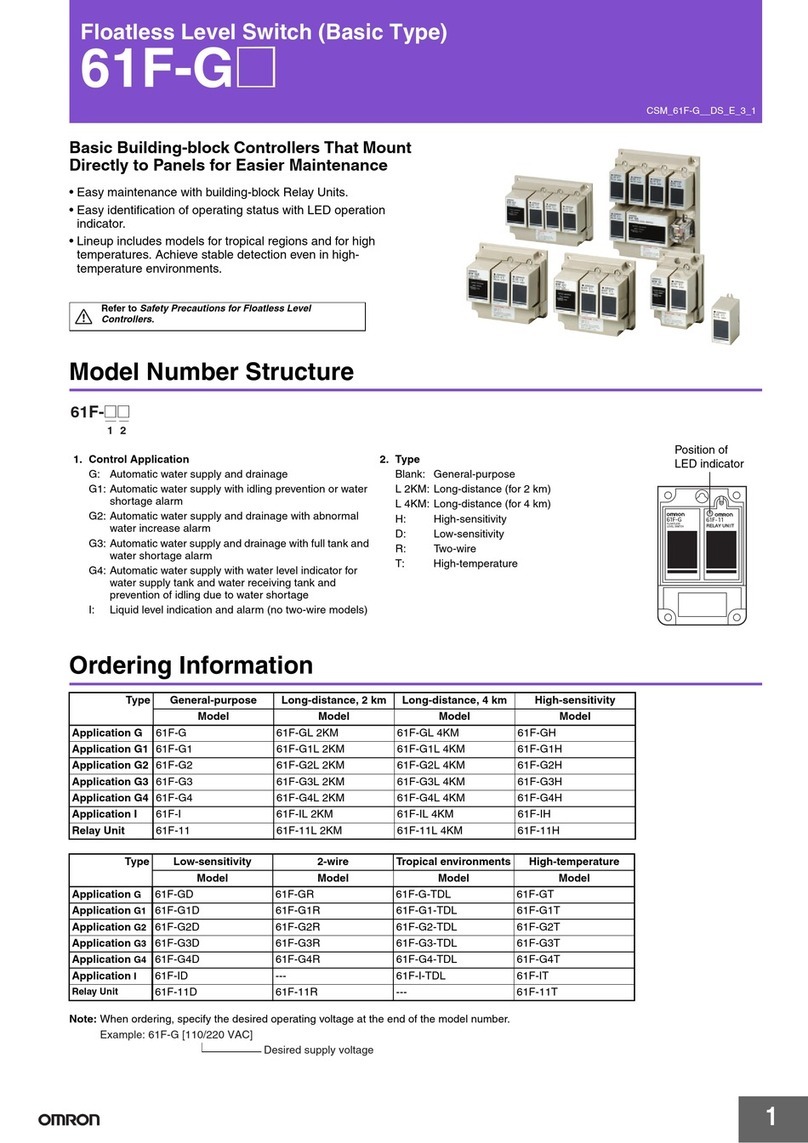
Omron
Omron 61F-GL2KM User manual
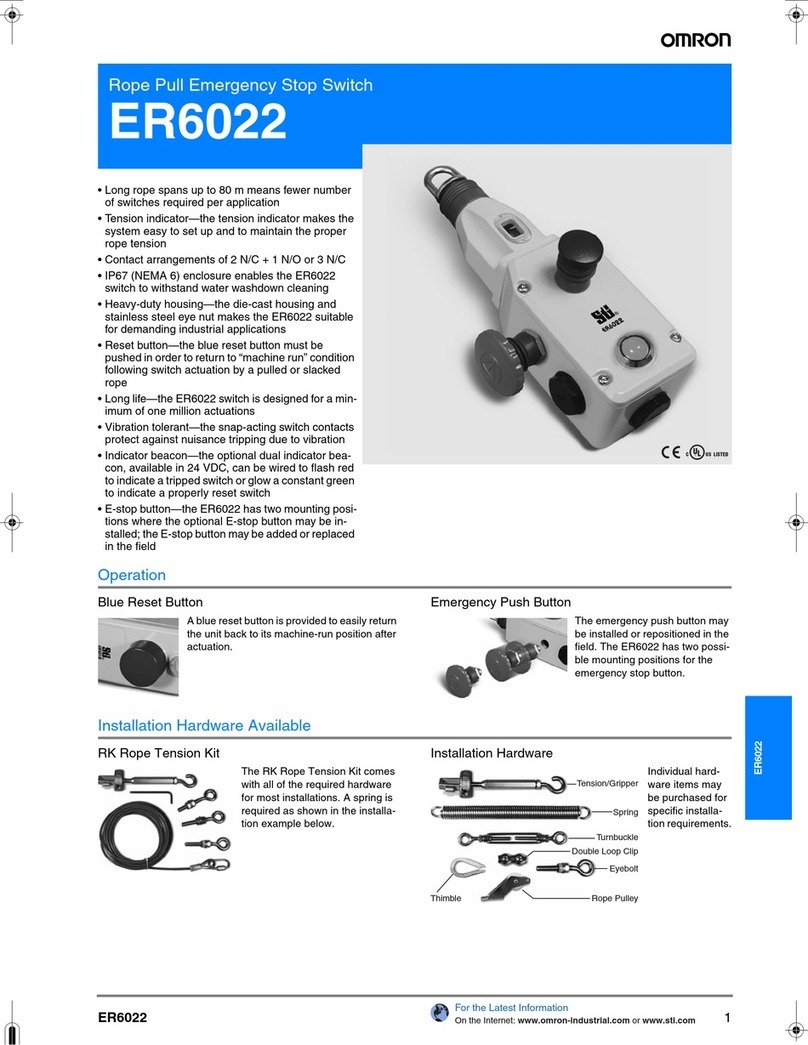
Omron
Omron ER6022 User manual
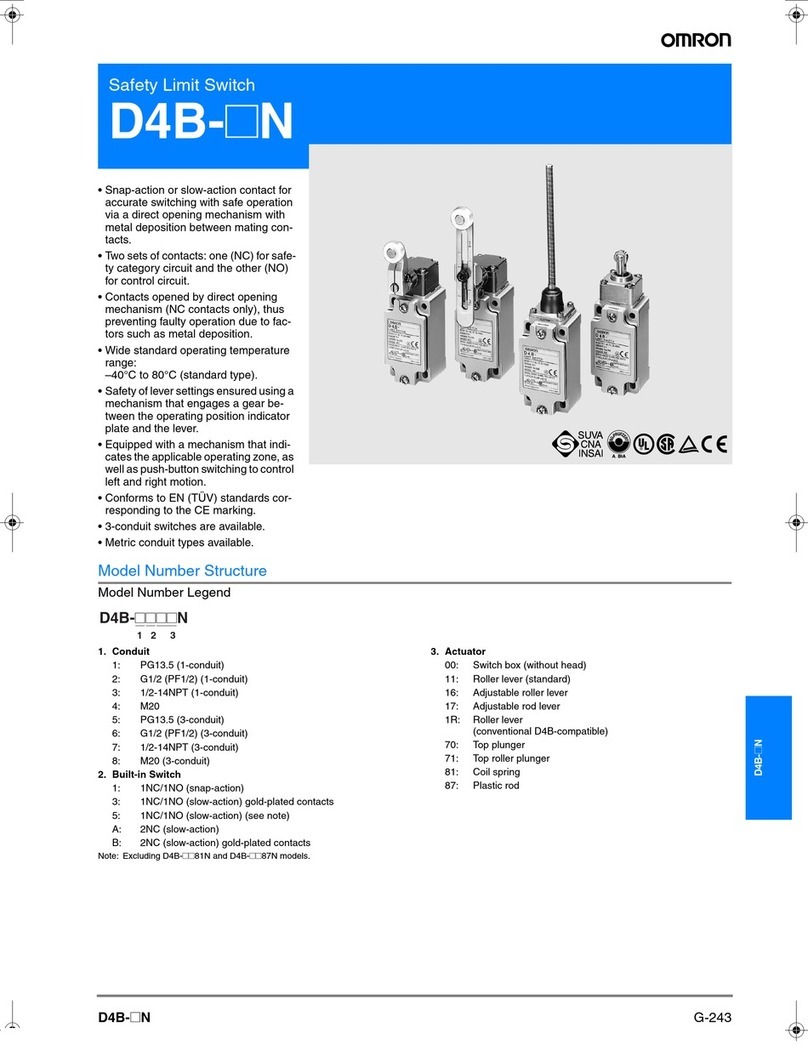
Omron
Omron D4B-N - User manual
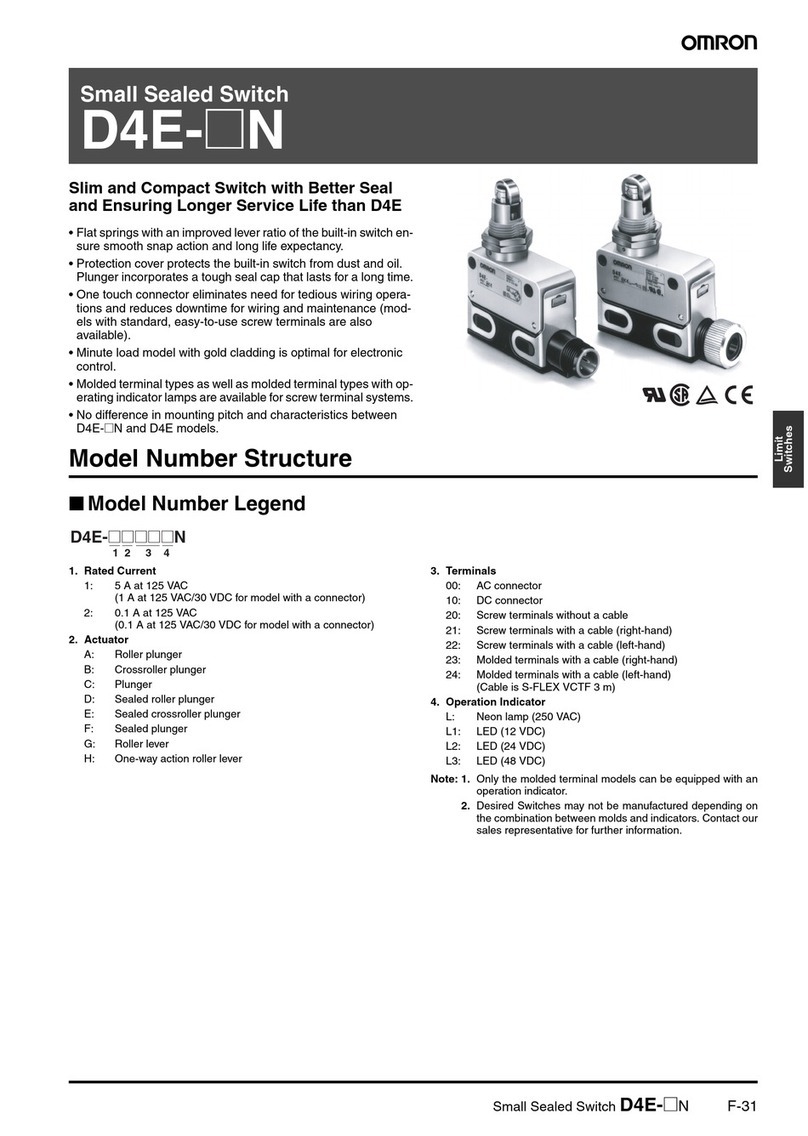
Omron
Omron D4E-N - User manual
Popular Switch manuals by other brands
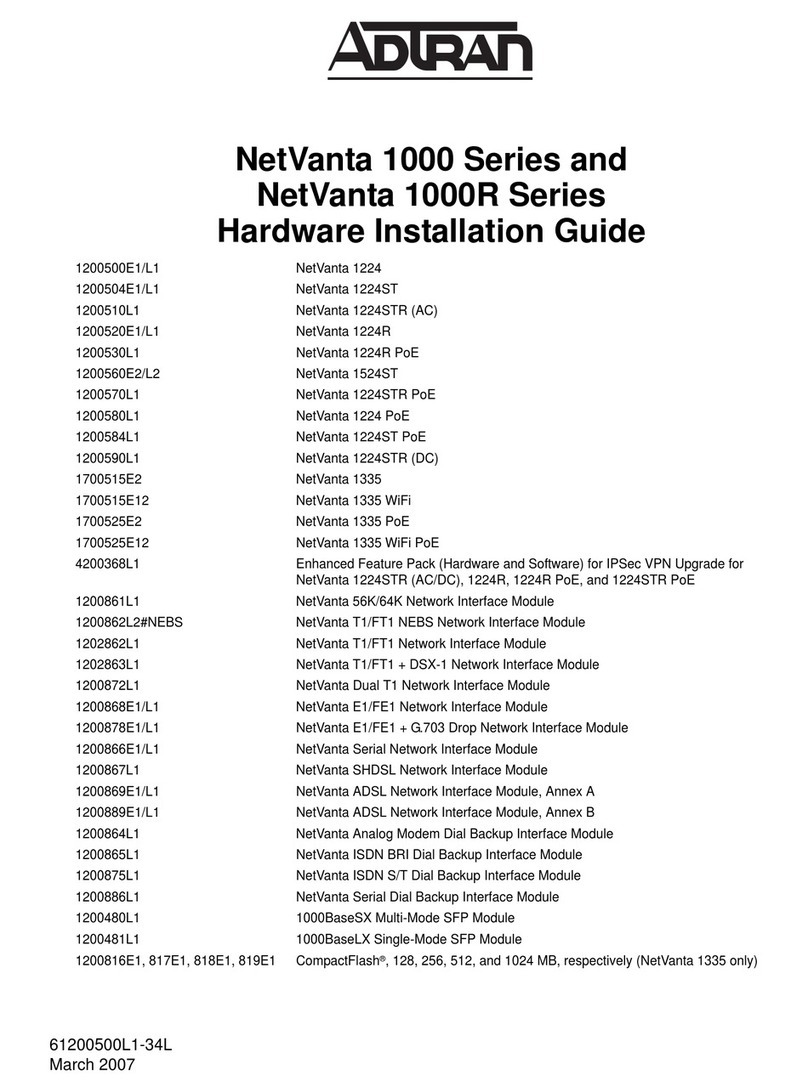
ADTRAN
ADTRAN NetVanta 1224ST Hardware installation guide
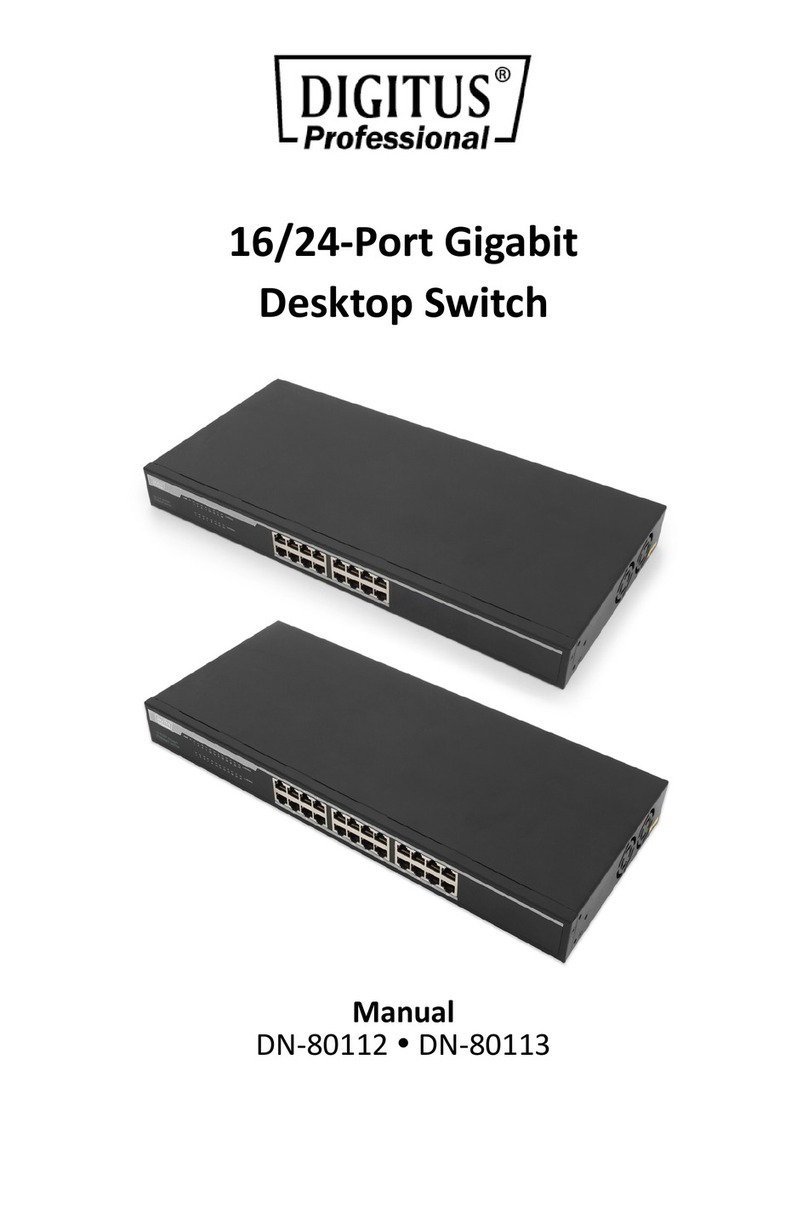
Digitus
Digitus DN-80113 user manual
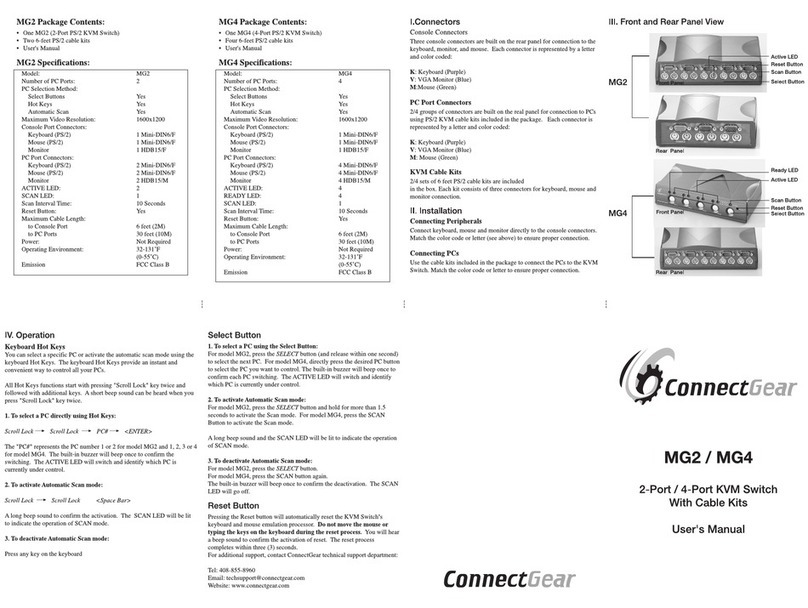
ConnectGear
ConnectGear MG2 user manual
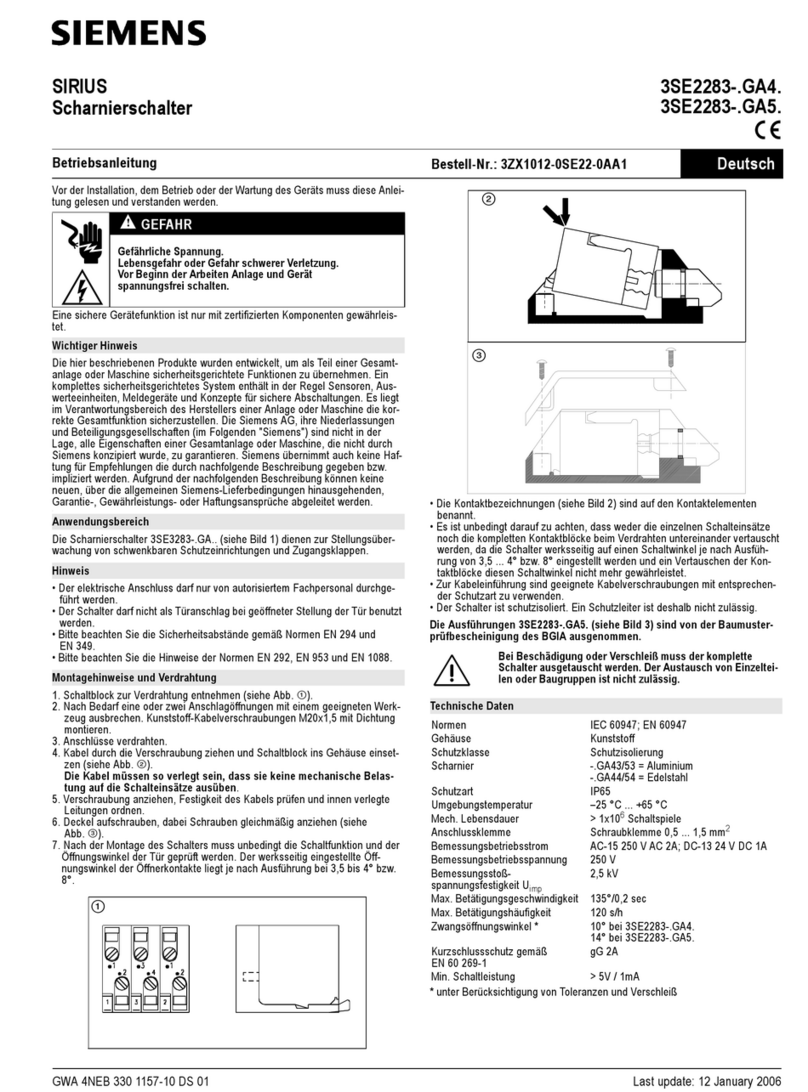
Siemens
Siemens SIRIUS 3SE2283 GA4 Series operating instructions

Intellinet
Intellinet 524117 user manual

Cooper Crouse-Hinds
Cooper Crouse-Hinds CEAG GHG 273 operating instructions