Pilz PNOZ X3 User manual

PNOZ X3
Operating Manual-20547-EN-10
}Safety relays

Preface
This document is the original document.
All rights to this documentation are reserved by Pilz GmbH & Co. KG. Copies may be made
for the user's internal purposes. Suggestions and comments for improving this documenta-
tion will be gratefully received.
Source code from third-party manufacturers or open source software has been used for
some components. The relevant licence information is available on the Internet on the Pilz
homepage.
Pilz®, PIT®, PMI®, PNOZ®, Primo®, PSEN®, PSS®, PVIS®, SafetyBUS p®,
SafetyEYE®, SafetyNET p®, the spirit of safety® are registered and protected trademarks
of Pilz GmbH & Co. KG in some countries.
SD means Secure Digital

Contents
Operating Manual PNOZ X3
20547-EN-10 3
Introduction 4
Validity of documentation 4
Using the documentation 4
Definition of symbols 4
Safety 5
Intended use 5
Safety regulations 6
Safety assessment 6
Use of qualified personnel 6
Warranty and liability 6
Disposal 6
For your safety 7
Unit features 8
Safety features 8
Block diagram/terminal configuration 8
Function Description 9
Operating modes 9
Timing diagram 10
Installation 10
Wiring 11
Preparing for operation 12
Operation 14
Status indicators 14
Faults – Interference 15
Dimensions in mm 15
Technical details 16
Safety characteristic data 31
Supplementary data 32
Service life graph 32
Order reference 33
EC declaration of conformity 33

PNOZ X3
Operating Manual PNOZ X3
20547-EN-10 4
Introduction
Validity of documentation
This documentation is valid for the product PNOZ X3. It is valid until new documentation is
published.
This operating manual explains the function and operation, describes the installation and
provides guidelines on how to connect the product.
Using the documentation
This document is intended for instruction. Only install and commission the product if you
have read and understood this document. The document should be retained for future ref-
erence.
Definition of symbols
Information that is particularly important is identified as follows:
DANGER!
This warning must be heeded! It warns of a hazardous situation that poses
an immediate threat of serious injury and death and indicates preventive
measures that can be taken.
WARNING!
This warning must be heeded! It warns of a hazardous situation that could
lead to serious injury and death and indicates preventive measures that can
be taken.
CAUTION!
This refers to a hazard that can lead to a less serious or minor injury plus
material damage, and also provides information on preventive measures
that can be taken.
NOTICE
This describes a situation in which the product or devices could be dam-
aged and also provides information on preventive measures that can be
taken. It also highlights areas within the text that are of particular import-
ance.

PNOZ X3
Operating Manual PNOZ X3
20547-EN-10 5
INFORMATION
This gives advice on applications and provides information on special fea-
tures.
Safety
Intended use
The safety relay PNOZ X3 provides a safety-related interruption of a safety circuit.
The safety relay meets the requirements of EN 60947-5-1, EN 60204-1 and VDE 0113-1
and may be used in applications with
}E-STOP pushbuttons
}Safety gates
The safety relay can be used as a safety component for lifts:
}On existing plants in accordance with Annex IV of the directive 95/16/EC and EN81-1
and
}On new plants in accordance with Annex III of the directive 2014/33/EU, EN 81-20 and
EN81-50.
These devices can also be used as a safety component:
}For lifts with an inclined travel path in accordance with EN 81-22 and
}For escalators and moving walks in accordance with EN 115-1.
The following is deemed improper use in particular
}Any component, technical or electrical modification to the product,
}Use of the product outside the areas described in this manual,
}Use of the product outside the technical details (see Technical details [ 16]).
NOTICE
EMC-compliant electrical installation
The product is designed for use in an industrial environment. The product
may cause interference if installed in other environments. If installed in other
environments, measures should be taken to comply with the applicable
standards and directives for the respective installation site with regard to in-
terference.

PNOZ X3
Operating Manual PNOZ X3
20547-EN-10 6
Safety regulations
Safety assessment
Before using a device it is necessary to perform a safety assessment in accordance with
the Machinery Directive.
Functional safety is guaranteed for the product as a single component. However, this does
not guarantee the functional safety of the overall plant/machine. In order to achieve the re-
quired safety level for the overall plant/machine, define the safety requirements for the
plant/machine and then define how these must be implemented from a technical and organ-
isational standpoint.
Use of qualified personnel
The products may only be assembled, installed, programmed, commissioned, operated,
maintained and decommissioned by competent persons.
A competent person is a qualified and knowledgeable person who, because of their train-
ing, experience and current professional activity, has the specialist knowledge required. To
be able to inspect, assess and operate devices, systems and machines, the person has to
be informed of the state of the art and the applicable national, European and international
laws, directives and standards.
It is the company’s responsibility only to employ personnel who
}Are familiar with the basic regulations concerning health and safety / accident preven-
tion,
}Have read and understood the information provided in the section entitled Safety
}Have a good knowledge of the generic and specialist standards applicable to the spe-
cific application.
Warranty and liability
All claims to warranty and liability will be rendered invalid if
}The product was used contrary to the purpose for which it is intended,
}Damage can be attributed to not having followed the guidelines in the manual,
}Operating personnel are not suitably qualified,
}Any type of modification has been made (e.g. exchanging components on the PCB
boards, soldering work etc.).
Disposal
}In safety-related applications, please comply with the mission time TM in the safety-re-
lated characteristic data.
}When decommissioning, please comply with local regulations regarding the disposal of
electronic devices (e.g. Electrical and Electronic Equipment Act).

PNOZ X3
Operating Manual PNOZ X3
20547-EN-10 7
For your safety
The unit meets all the necessary conditions for safe operation. However, please note the
following:
}Note for overvoltage category III: If voltages higher than low voltage (>50 VAC or >120
VDC) are present on the unit, connected control elements and sensors must have a
rated insulation voltage of at least 250 V.

PNOZ X3
Operating Manual PNOZ X3
20547-EN-10 8
Unit features
}Positive-guided relay outputs:
– 3 safety contacts (N/O), instantaneous
– 1 auxiliary contact (N/C), instantaneous
}1 semiconductor output
}Connection options for:
– E-STOP pushbutton
– Safety gate limit switch
– Start button
}LED display for:
– Supply voltage
– Switch status of the safety contacts
}Semiconductor output signals:
– Switch state of the safety contacts
}See order reference for unit types
Safety features
The safety relay meets the following safety requirements:
}The circuit is redundant with built-in self-monitoring.
}The safety function remains effective in the case of a component failure.
}The correct opening and closing of the safety function relays is tested automatically in
each on-off cycle.
Block diagram/terminal configuration
* *
*Insulation between the non-marked area and the relay contacts: Basic insulation (over-
voltage category III), Protective separation (overvoltage category II)

PNOZ X3
Operating Manual PNOZ X3
20547-EN-10 9
Function Description
The safety relay PNOZ X3 provides a safety-oriented interruption of a safety circuit. When
supply voltage is supplied the "POWER" LED is lit. The unit is ready for operation when the
start circuit S13-S14 is closed.
}Input circuit is closed (e.g. E-STOP pushbutton not operated):
– Safety contacts 13-14, 23-24 and 33-34 are closed, auxiliary contact 41-42 is open.
The unit is active.
– The LEDs "CH.1" and "CH.2" are lit.
– A high signal is present at the semiconductor output switch state Y32.
}Input circuit is opened (e.g. E-STOP pushbutton operated):
– Safety contacts 13-14, 23-24 and 33-34 are opened redundantly, auxiliary contact
41-42 is closed.
– The LEDs "CH.1" and "CH.2" go out.
– A low signal is present at the semiconductor output switch state Y32.
Operating modes
}Single-channel operation: No redundancy in the input circuit, earth faults in the start
and input circuit are detected.
}Dual-channel operation with detection of shorts across contacts: Redundant input cir-
cuit, PNOZ X3 detects
– earth faults in the start and input circuit,
– short circuits in the input circuit,
– shorts across contacts in the input circuit.
}Automatic start: Unit is active once the input circuit has been closed.
}Monitored start: Unit is active once the input circuit is closed and once the start circuit is
closed after the waiting period has elapsed (see Technical details [ 16]).
}Increase in the number of available contacts by connecting contact expander modules
or external contactors/relays.

PNOZ X3
Operating Manual PNOZ X3
20547-EN-10 10
Timing diagram
[1] [2]
POWER
Start
Input
Output safe
Output aux.
Out semi OUT
Legend
}Power: Supply voltage
}Start: Start circuit
}Input: Input circuit
}Output safe: Safety contacts
}Output aux: Auxiliary contact
}Out semi OUT: Semiconductor output switch state
}[1]: Automatic start
}[2]: Monitored start
}t1: Switch-on delay
}t2: Delay-on de-energisation
}t3: Recovery time
}t4: Waiting period with a monitored start
Installation
}The unit should be installed in a control cabinet with a protection type of at least IP54.
}Use the notch on the rear of the unit to attach it to a DIN rail (35 mm).
}When installed vertically: Secure the unit by using a fixing element (e.g. retaining
bracket or end angle).
}With AC supply voltage: When installing more than 2 units next to each other in the
control cabinet, a distance of at least 6mm must be maintained between the units.

PNOZ X3
Operating Manual PNOZ X3
20547-EN-10 11
Wiring
Please note:
}Information given in the "Technical details [ 16]" must be followed.
}Outputs 13-14, 23-24, 33-34 are safety contacts; output 41-42 is an auxiliary contact
(e.g. for display).
}Auxiliary contact 41-42 shouldnot be used for safety circuits!
}Delivery condition: Link between S11-S12 (dual-channel input circuit)
}To prevent contact welding, a fuse should be connected before the output contacts (see
Technical details [ 16]).
}Calculation of the max. cable length lmax in the input circuit:
Rlmax
Rl / km
Imax =
Rlmax = max. overall cable resistance (see Technical details [ 16])
Rl/km = cable resistance/km
}Use copper wire that can withstand 60/75°C.
}Do not switch low currents using contacts that have been used previously with high cur-
rents.
}Sufficient fuse protection must be provided on all output contacts with capacitive and in-
ductive loads.
}When connecting magnetically operated, reed proximity switches, ensure that the max.
peak inrush current (on the input circuit) does not overload the proximity switch.
}With a 24 VDC supply voltage via terminals B1, B2, the power supply must comply with
the regulations for extra low voltages with safe electrical separation (SELV, PELV) in
accordance with VDE 0100, Part 410.
}When operated with AC voltage: Connect terminal B2 to the functional earth.
}Ensure the wiring and EMC requirements of EN 60204-1 are met.
Important for detection of shorts across contacts:
As this function for detecting shorts across contacts is not failsafe, it is tested by Pilz during
the final control check. If there is a danger of exceeding the cable length, we recommend
the following test once the unit is installed:
1. Unit ready for operation (output contacts closed)
2. Short circuit the test terminals S22, S32 for detecting shorts across the inputs.
3. The unit‘s fuse must be triggered and the output contacts must open. Cable lengths in
the scale of the maximum length can delay the fuse triggering for up to 2 minutes.
4. Reset the fuse: Remove the short circuit and switch off the supply voltage for approx. 1
minute.

PNOZ X3
Operating Manual PNOZ X3
20547-EN-10 12
Preparing for operation
Supply voltage AC DC
FE
B1
B2
L+
L-
Input circuit Single-channel Dual-channel
E-STOP
without detection of shorts
across contacts
S1
S22
S21
S12
S32
S11
S31
E-STOP
with detection of shorts across
contacts
S1
S22
S31
S32
S21
S12
S11
Safety gate
without detection of shorts
across contacts
S1
S22
S21
S12
S32
S11
S31
Safety gate
with detection of shorts across
contacts
NOTICE
With single-channel wiring the safety level of your machine/plant may be
lower than the safety level of the unit (see Safety characteristic
data [ 31]).

PNOZ X3
Operating Manual PNOZ X3
20547-EN-10 13
Start circuit
E-STOP wiring
Safety gate without start-up
test Safety gate with start-up test
Automatic start
S33
S34
S13
S14
S33
S13
S34
S14
Monitored start
S33
S34
S3
S14
S13
NOTICE
In the event of an automatic start:
The unit starts up automatically when the safeguard is reset, e.g. when the
E-STOP pushbutton is released. Use external circuit measures to prevent
an unexpected restart.
Feedback loop Automatic start Monitored start
Contacts from external contactors
K5 K6
K5
L1
N
K6
S13
13 (23, 33)
S14
14 (24, 34)
Semiconductor output
Legend
}S1/S2: E-STOP/safety gate switch
}S3: Reset button
}: Switch operated
}: Gate open
}: Gate closed

PNOZ X3
Operating Manual PNOZ X3
20547-EN-10 14
INFORMATION
With automatic start, S33 and S34 must not be linked; with monitored start,
S13 and S14 must not be linked.
Operation
NOTICE
The safety function should be checked after initial commissioning and each
time the plant/machine is changed. The safety functions may only be
checked by qualified personnel.
When the relay outputs are switched on, the mechanical contact on the relay cannot be
tested automatically. Depending on the operational environment, measures to detect the
non-opening of switching elements may be required under some circumstances.
When the product is used in accordance with the European Machinery Directive, a check
must be carried out to ensure that the safety contacts on the relay outputs open correctly.
Open the safety contacts (switch off output) and start the device again, so that the internal
diagnostics can check that the safety contacts open correctly
}for SIL CL 3/PL e at least 1x per month
}for SIL CL 2/PL d at least 1x per year
Status indicators
LEDs indicate the status and errors during operation:
LED on
POWER
Supply voltage is present.
CH.1
Safety contacts of channel 1 are closed.
CH.2
Safety contacts of channel 2 are closed.

PNOZ X3
Operating Manual PNOZ X3
20547-EN-10 15
Faults – Interference
}Earth fault: The supply voltage fails and the safety contacts open. Once the cause of
the respective fault has been rectified and the supply voltage is switched off for approx.
1minute, the unit is ready for operation again.
}Contact malfunctions: If the contacts have welded, reactivation will not be possible after
the input circuit has opened.
}LED "POWER" does not light: Short circuit or no supply voltage.
Dimensions in mm
121 (4.76")
75 (2.95")
87 (3.42")
45
(1.77")

PNOZ X3
Operating Manual PNOZ X3
20547-EN-10 16
Technical details
Order no. 774310 – 774312
See below for more order numbers
General 774310 774311 774312
Approvals
CCC, CE, EAC (Euras-
ian), KOSHA, TÜV, cU-
Lus Listed
CCC, CE, EAC (Euras-
ian), KOSHA, TÜV, cU-
Lus Listed
CCC, CE, EAC (Euras-
ian), KOSHA, TÜV, cU-
Lus Listed
Electrical data 774310 774311 774312
Supply voltage
Voltage 24 V 42 V 48 V
Kind AC AC AC
Voltage tolerance -15 %/+10 % -15 %/+10 % -15 %/+10 %
Output of external
power supply (AC) 5 VA 5 VA 5 VA
Frequency range AC 50 - 60 Hz 50 - 60 Hz 50 - 60 Hz
Supply voltage
Voltage 24 V 24 V 24 V
Kind DC DC DC
Voltage tolerance -15 %/+10 % -15 %/+10 % -15 %/+10 %
Output of external
power supply (DC) 2,5 W 2,5 W 2,5 W
Residual ripple DC 160 % 160 % 160 %
Duty cycle 100 % 100 % 100 %
Inputs 774310 774311 774312
Number 2 2 2
Voltage at
Input circuit DC 24 V 24 V 24 V
Start circuit DC 24 V 24 V 24 V
Feedback loop DC 24 V 24 V 24 V
Current at
Input circuit DC 50 mA 50 mA 50 mA
Start circuit DC 35 mA 35 mA 35 mA
Feedback loop DC 20 mA 20 mA 20 mA
Min. input resistance at
power-on 130 Ohm 130 Ohm 130 Ohm
Max. overall cable resist-
ance Rlmax
Single-channel at UB
DC 150 Ohm 150 Ohm 150 Ohm
Single-channel at UB
AC 180 Ohm 180 Ohm 180 Ohm
Dual-channel with de-
tection of shorts across
contacts at UB DC 15 Ohm 15 Ohm 15 Ohm
Dual-channel with de-
tection of shorts across
contacts at UB AC 30 Ohm 30 Ohm 30 Ohm

PNOZ X3
Operating Manual PNOZ X3
20547-EN-10 17
Semiconductor outputs 774310 774311 774312
Number 1 1 1
Voltage 24 V 24 V 24 V
Current 20 mA 20 mA 20 mA
External supply voltage 24 V 24 V 24 V
Voltage tolerance -20 %/+20 % -20 %/+20 % -20 %/+20 %
Relay outputs 774310 774311 774312
Number of output con-
tacts
Safety contacts (N/O),
instantaneous 3 3 3
Auxiliary contacts (N/C) 1 1 1
Max. short circuit current
IK 1 kA 1 kA 1 kA
Utilisation category
In accordance with the
standard EN 60947-4-1 EN 60947-4-1 EN 60947-4-1
Utilisation category of
safety contacts
AC1 at 240 V 240 V 240 V
Min. current 0,01 A 0,01 A 0,01 A
Max. current 8 A 8 A 8 A
Max. power 2000 VA 2000 VA 2000 VA
DC1 at 24 V 24 V 24 V
Min. current 0,01 A 0,01 A 0,01 A
Max. current 8 A 8 A 8 A
Max. power 200 W 200 W 200 W
Utilisation category of
auxiliary contacts
AC1 at 240 V 240 V 240 V
Min. current 0,01 A 0,01 A 0,01 A
Max. current 8 A 8 A 8 A
Max. power 2000 VA 2000 VA 2000 VA
DC1 at 24 V 24 V 24 V
Min. current 0,01 A 0,01 A 0,01 A
Max. current 8 A 8 A 8 A
Max. power 200 W 200 W 200 W
Utilisation category
In accordance with the
standard EN 60947-5-1 EN 60947-5-1 EN 60947-5-1
Utilisation category of
safety contacts
AC15 at 230 V 230 V 230 V
Max. current 5 A 5 A 5 A
DC13 (6 cycles/min) at 24 V 24 V 24 V
Max. current 6 A 6 A 6 A

PNOZ X3
Operating Manual PNOZ X3
20547-EN-10 18
Relay outputs 774310 774311 774312
Utilisation category of
auxiliary contacts
AC15 at 230 V 230 V 230 V
Max. current 5 A 5 A 5 A
DC13 (6 cycles/min) at 24 V 24 V 24 V
Max. current 6 A 6 A 6 A
Utilisation category in ac-
cordance with UL
Voltage 240 V AC G. P. 240 V AC G. P. 240 V AC G. P.
With current 8 A 8 A 8 A
Voltage 24 V DC Resistive 24 V DC Resistive 24 V DC Resistive
With current 5 A 5 A 5 A
Pilot Duty B300, R300 B300, R300 B300, R300
External contact fuse pro-
tection, safety contacts
In accordance with the
standard EN 60947-5-1 EN 60947-5-1 EN 60947-5-1
Max. melting integral 240 A²s 240 A²s 240 A²s
Blow-out fuse, quick 10 A 10 A 10 A
Blow-out fuse, slow 6 A 6 A 6 A
Blow-out fuse, gG 10 A 10 A 10 A
Circuit breaker 24V
AC/DC, characteristic
B/C 6 A 6 A 6 A
External contact fuse pro-
tection, auxiliary contacts
Max. melting integral 240 A²s 240 A²s 240 A²s
Blow-out fuse, quick 10 A 10 A 10 A
Blow-out fuse, slow 6 A 6 A 6 A
Blow-out fuse, gG 10 A 10 A 10 A
Circuit breaker 24 V
AC/DC, characteristic
B/C 6 A 6 A 6 A
Contact material AgSnO2 + 0,2 µm Au AgSnO2 + 0,2 µm Au AgSnO2 + 0,2 µm Au
Conventional thermal
current while loading
several contacts
774310 774311 774312
Ith per contact at UB AC;
AC1:240V,DC1:24V
Conv. therm. current
with 1 contact 8 A 8 A 8 A
Conv. therm. current
with 2 contacts 7,5 A 7,5 A 7,5 A
Conv. therm. current
with 3 contacts 6,5 A 6,5 A 6,5 A

PNOZ X3
Operating Manual PNOZ X3
20547-EN-10 19
Conventional thermal
current while loading
several contacts
774310 774311 774312
Ith per contact at UB DC;
AC1:240V,DC1:24V
Conv. therm. current
with 1 contact 8 A 8 A 8 A
Conv. therm. current
with 2 contacts 8 A 8 A 8 A
Conv. therm. current
with 3 contacts 7 A 7 A 7 A
Times 774310 774311 774312
Switch-on delay
With automatic start
typ. 250 ms 250 ms 250 ms
With automatic start
max. 500 ms 500 ms 500 ms
With automatic start
after power on typ. 280 ms 280 ms 280 ms
With automatic start
after power on max. 550 ms 550 ms 550 ms
With monitored start
typ. 35 ms 35 ms 35 ms
With monitored start
max. 50 ms 50 ms 50 ms
Delay-on de-energisation
With E-STOP typ. 15 ms 15 ms 15 ms
With E-STOP max. 30 ms 30 ms 30 ms
With power failure typ. 50 ms 50 ms 50 ms
With power failure max. 70 ms 70 ms 70 ms
Recovery time at max.
switching frequency 1/s
After E-STOP 50 ms 50 ms 50 ms
After power failure 100 ms 100 ms 100 ms
Waiting period with a
monitored start 300 ms 300 ms 300 ms
Min. start pulse duration
with a monitored start 30 ms 30 ms 30 ms
Supply interruption before
de-energisation 20 ms 20 ms 20 ms
Simultaneity, channel 1
and 2 max. ∞ ∞ ∞
Environmental data 774310 774311 774312
Climatic suitability EN 60068-2-78 EN 60068-2-78 EN 60068-2-78
Ambient temperature
Temperature range -20 - 55 °C -20 - 55 °C -20 - 55 °C
Storage temperature
Temperature range -40 - 85 °C -40 - 85 °C -40 - 85 °C

PNOZ X3
Operating Manual PNOZ X3
20547-EN-10 20
Environmental data 774310 774311 774312
Climatic suitability
Humidity 93 % r. h. at 40 °C 93 % r. h. at 40 °C 93 % r. h. at 40 °C
Condensation during op-
eration Not permitted Not permitted Not permitted
EMC EN 12015, EN 12016, EN
60947-5-1, EN 61000-6-2,
EN 61326-3-1
EN 12015, EN 12016, EN
60947-5-1, EN 61000-6-2,
EN 61326-3-1
EN 12015, EN 12016, EN
60947-5-1, EN 61000-6-2,
EN 61326-3-1
Vibration
In accordance with the
standard EN 60068-2-6 EN 60068-2-6 EN 60068-2-6
Frequency 10 - 55 Hz 10 - 55 Hz 10 - 55 Hz
Amplitude 0,35 mm 0,35 mm 0,35 mm
Airgap creepage
In accordance with the
standard EN 60947-1 EN 60947-1 EN 60947-1
Overvoltage category III / II III / II III / II
Pollution degree 3 3 3
Rated insulation voltage 250 V 250 V 250 V
Rated impulse withstand
voltage 4 kV 4 kV 4 kV
Protection type
Housing IP40 IP40 IP40
Terminals IP20 IP20 IP20
Mounting area (e.g.
control cabinet) IP54 IP54 IP54
Mechanical data 774310 774311 774312
Mounting position Any Any Any
Mechanical life 10,000,000 cycles 10,000,000 cycles 10,000,000 cycles
Material
Bottom PPO UL 94 V0 PPO UL 94 V0 PPO UL 94 V0
Front ABS UL 94 V0 ABS UL 94 V0 ABS UL 94 V0
Top PPO UL 94 V0 PPO UL 94 V0 PPO UL 94 V0
Connection type Screw terminal Screw terminal Screw terminal
Mounting type Fixed Fixed Fixed
Conductor cross section
with screw terminals
1 core flexible 0,2 - 4 mm², 24 - 10 AWG 0,2 - 4 mm², 24 - 10 AWG 0,2 - 4 mm², 24 - 10 AWG
2 core with the same
cross section, flexible
with crimp connectors,
no plastic sleeve
0,2 - 2,5 mm², 24 - 14
AWG
0,2 - 2,5 mm², 24 - 14
AWG
0,2 - 2,5 mm², 24 - 14
AWG
2 core with the same
cross section, flexible
without crimp connect-
ors or with TWIN crimp
connectors
0,2 - 2,5 mm², 24 - 14
AWG
0,2 - 2,5 mm², 24 - 14
AWG
0,2 - 2,5 mm², 24 - 14
AWG
Torque setting with screw
terminals 0,6 Nm 0,6 Nm 0,6 Nm
Other manuals for PNOZ X3
4
Table of contents
Other Pilz Relay manuals
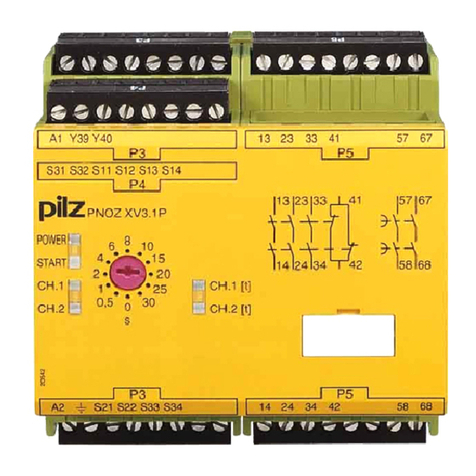
Pilz
Pilz PNOZ XV3.1P User manual

Pilz
Pilz PNOZ 15 User manual
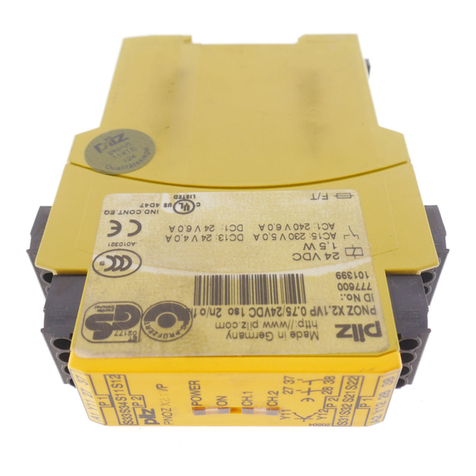
Pilz
Pilz PNOZ X2.1VP User manual
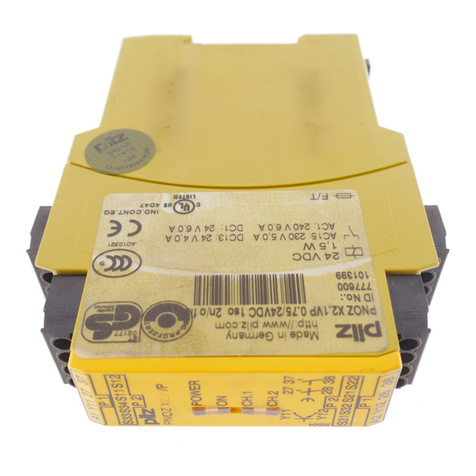
Pilz
Pilz PNOZ X2.1VP User manual
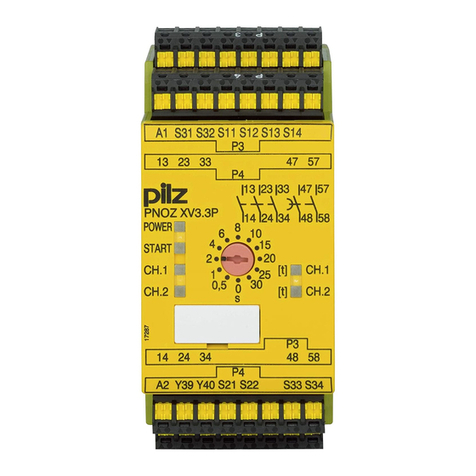
Pilz
Pilz PNOZ XV3.3P User manual
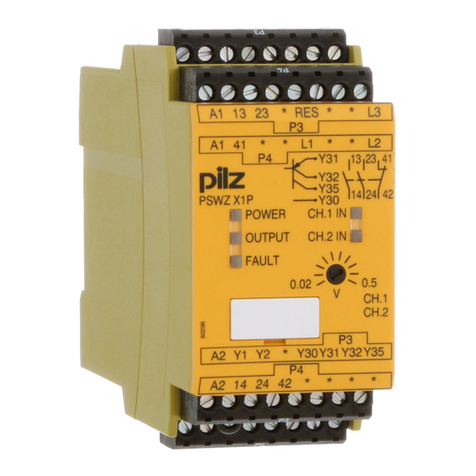
Pilz
Pilz PSWZ X1P User manual
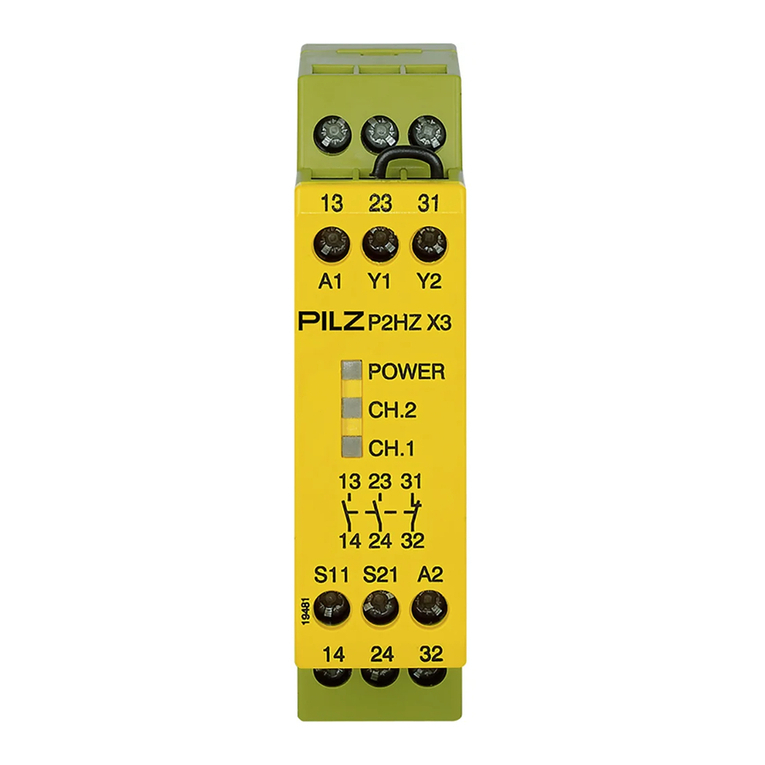
Pilz
Pilz P2HZ X3 User manual
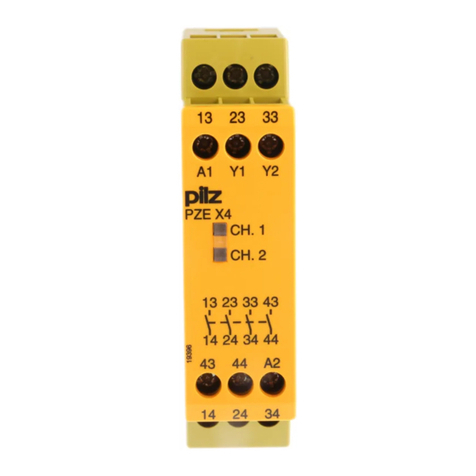
Pilz
Pilz PNOZ X Series User manual
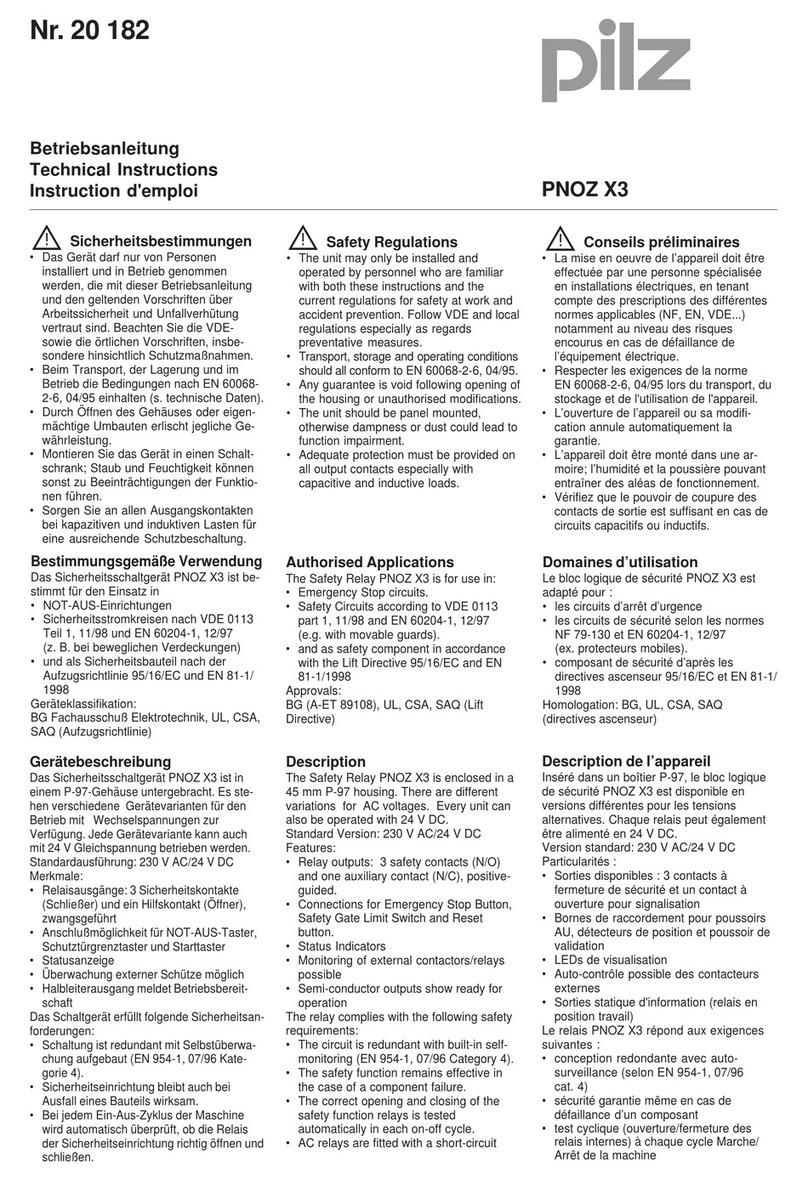
Pilz
Pilz PNOZ X3 Owner's manual
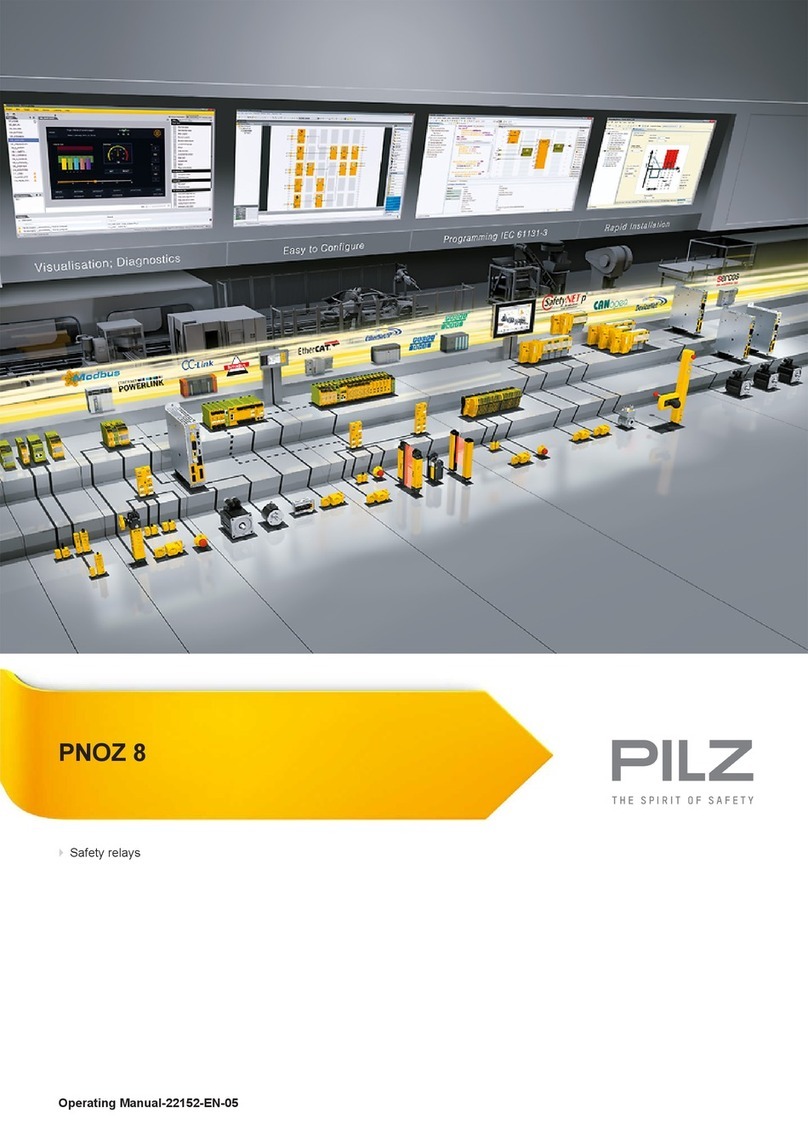
Pilz
Pilz PNOZ 8 User manual
Popular Relay manuals by other brands
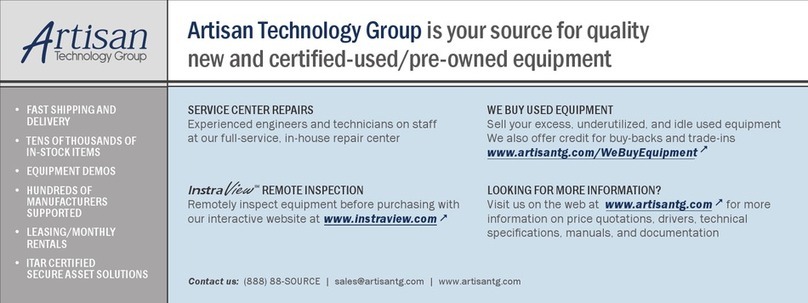
Measurement Computing
Measurement Computing PCI-PDISO8 user guide

PANL
PANL PC0144 quick start guide
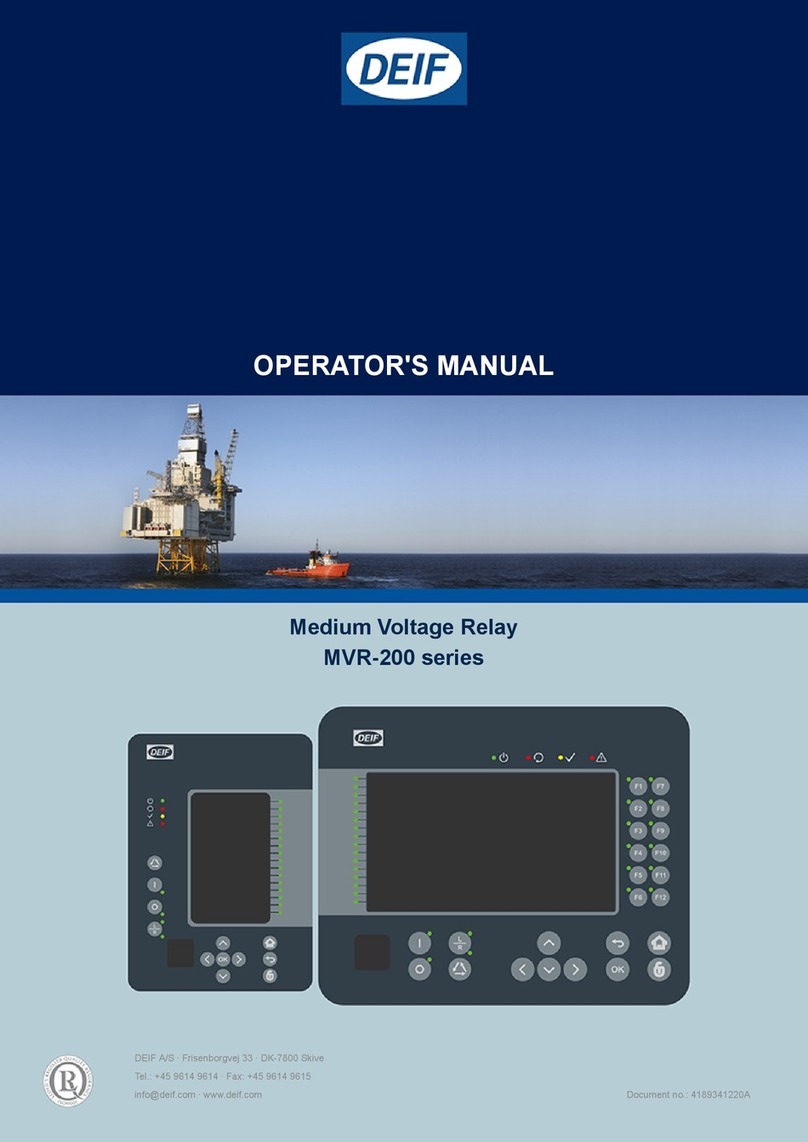
Deif
Deif MVR-200 Series Operator's manual
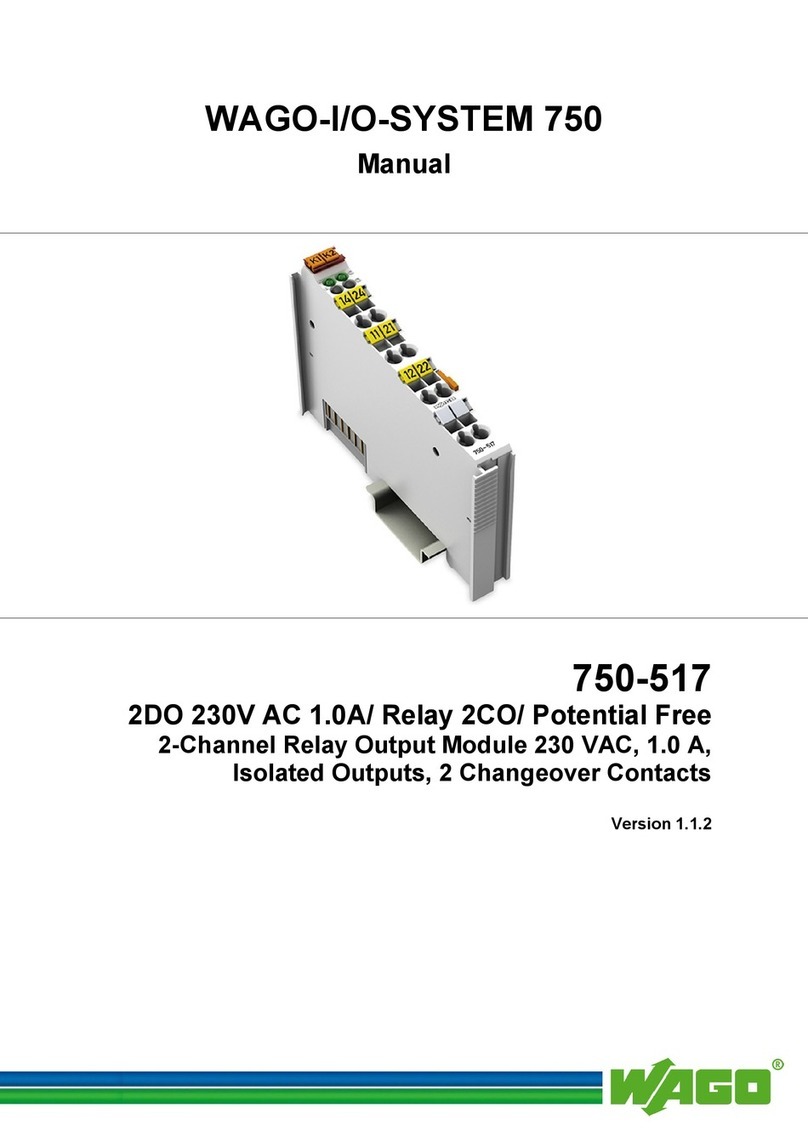
WAGO
WAGO I/O-SYSTEM 750-517 manual
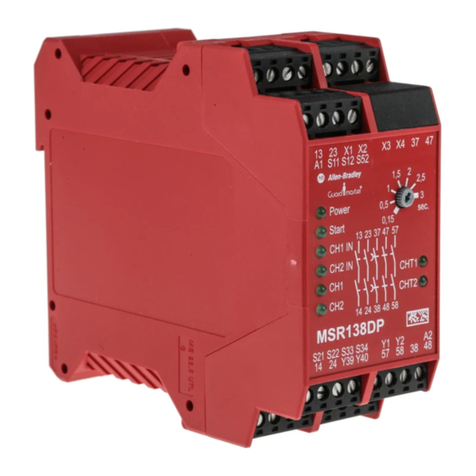
Rockwell Automation
Rockwell Automation Allen-Bradley Minotaur MSR138DP installation instructions

Arcteq
Arcteq AQ-F201 instruction manual