Promac JDT-5030 User manual

JDT-5030
Drill Press
Bohrmaschinen
Perceuses
05-2019
Schweiz / Suisse
JPW (TOOL) AG
Ackerstrasse 45, CH-8610 Uster,
Switzerland
www.promac.ch
France
TOOL FRANCE SARL
9 Rue des Pyrénées, 91090 LISSES, France
www.promac.fr

2
CE-Conformity Declara on
CE-Konformitätserklärung
Déclara on de Conformité CE
Product / Produkt / Produit:
JDT-5030
Drill Press / Säulenbohrmaschinen / Perceuses à colonne
Brand / Marke / Marque:
PROMAC
Manufacturer / Hersteller / Fabricant:
We hereby declare that this product complies with the regula ns
Wir erklären hiermit, dass dieses Produkt der folgenden Richtlinie entspricht
Par la présente, nous déclarons que ce produit correspond aux dire ves suivantes
2006/42/EC
Machinery Direc ve
Maschinenrichtlinie
Direc ve Machines
2014/30/EU
electromagne compa bility
elektromagne sche Verträglichkeit
compa bilité électromagné que
designed in considera on of the standards
und entsprechend folgender zusätzlicher Normen entwickelt wurde
et été développé dans le respect des normes complémentaires suivantes
EN ISO 12100:2010
EN 13128:2001+A1:2006EN+ A2:2009
EN 12717:2001 + A1:2009 + AC:2010
EN 60204-1:2006/AC2010
EN 61000-6-2:2005
EN 61000-6-
4:2007/A1:2011
Responsible for the Documen / Doku -Verantwortung / Responsabilité de Document
Head of Product-Mgmt. / Leiter Produkt-Mgmt. / Resp. Ges n des Produits
2019-05-05 Christophe SAINT SULPICE, General Manager
TOOL FRANCE SARL
9 Rue des Pyrénées, 91090 LISSES, France
TOOL FRANCE SARL
TOOL FRANCE SARL
9 Rue des Pyrénées, 91090 LISSES, France

Operation Manual Total 1
page 1
Contents
1. Main use and features of the machine
2. Main technical data
3. Brief description
of the driving system and its structure
4. Electrical system
5. Lubrication and coolant system
6. Hoisting and installation
7. Use and operation of the machine
8. Machine adjustment
9. Machine use and maintenance
10. Machine accessories

Operation Manual Total 26
page 1
Dear end-user,
Thank you very much for choosing our products. Please let us have the model of your machine,
series number, as well as the name, address and correspondence method of your company in
order to facilitate us to let you have a good service.
Important notice:
1. Please immediately contact your dealer in case the machine, accessories or documents are
not in conformity with those indicated in the packing list after the machine package is
opened.
2. Please carefully read this Operation Manual particularly the electric part of this documents
before installation, testing and running the machine.
3. Removing grease on the machine (particularly on the column) and checking lubrication oil
in each place is well filled . Running the machine without lubrication
oil is strictly
forbidden. Lubrication of the machine as per the stipulation of this documents is required.
4. Ground wire of the machine shall be well connected. When test running, push jog button in
slow spindle speed to check if direction of spindle revolution is correct.
5. Machine must be stopped if spindle speed or feed rate change is necessary.
6. Please check if cutting tool or work piece is well clamped before machining
7.
The red mushroom push button located in front of the spindle box is an emergence push
button for emergency purpose only. Familiar with its position and its use are necessary.
8. Professional electric service engineer is required for electric maintenance.
9. The machine must be stopped when you need removing away the cutting material around the
drill. Moving the cutting material by hand or by hook is definitely forbidden.
10. Correct use and daily maintenance of the machine are required in order to keep machine
accuracy and its lifetime in long time.
11. We will much appreciate if you could solve some problems of the machine.
In order to facilitate us for the service, please let us know the details regarding the places and
phenomenon of the troubles if you could not solve problems.

Operation Manual Total 26
page 2
1.Main use and features of the machine:
JDT series vertical drilling machines are our new products designed and developed by our-
self based on our accumulated experience in so many years in this field. It is
really a multi-function universal machine which could be widely used for small and
middle sizes of work pieces for drilling, spot facing, reaming, tapping etc. Besides,
some machine tool accessories could also be used on this machine. The machines are
suitable for the machining workshop, maintenance workshop and production line etc.
Features:
1.1 Good in appearance, easy in operation, convenience in maintenance and well
consideration in safety protection
1.2 Double speed motor is to be used for the main drive system with sufficient driving
power but saving energy. Wide spindle speed range is adopted driven by gears.
1.3 Oil lubrication both for the main driving system and for the feed driving system could
be supplied automatically by a new type of trochoid pump when it is working in forward
and reverse revolution.
1.4 The spindle features good rigidity and good wear resisting and equipped with
tool
disassembly and balancing device.
1.5 The worktable could be turned round the column center line or worktable center line itself
or horizontal shaft centerline by manual and could be moving up a
nd down by manual or
automatically.
1.6
Main operation levers and push buttons could be reached easily that makes you
comfortable when you operate the machine.
1.7 Spindle feed both in mechanical and in electrical with micro feed structure is available
in this series machines.
1.8 Superior quality material with special treatment for the wear-resisting purpose has been
used for transmission parts such as gears, worm and worm shaft, rack, lead screw etc as
well as for some key parts like spindle and spindle quill.
1.9 An adjustable safety protection clutch in the spindle feed device is available in order to
prevent the machine and tools from damage when overloaded.

Operation Manual Total 26
page 3
1.10 A safety protection guard under the spindle
box is available as it is not only prevent
coolant splash while cutting but also could observe the machining status.
The guard is interlocked with the spindle, so when the guard is opened, the spindle
could not be running until the protection guard keeps his position.
2. Main technical data:
2.1 Main technical data
No. Name of the items Unit Data
1 Max. drilling diameter (steel) mm 50
2 Max. tapping diameter (steel) mm M30
3 Distance between spindle center line to the center line of column mm 370
4 Max. distance between spindle end to the surface of the worktable
(automatic) mm 585(410)
5 Max. distance between spindle end to the worktable surface of the base mm 1170
6 Max. stroke of the spindle mm 240
7 Spindle taper Morse MT4
8 Number of speed steps of the spindle Step 12
9 Spindle speed range r/min 40-2100
10 Feed steps of the spindle Step 4
11 Feed range of the spindle mm/r 0.1-0.4
12 Max. stroke of worktable and its bracket mm 530(410)
13 Rotation degree of worktable and its bracket in cross direction degree ±45°
14 Working area of the worktable (Lx W) mm 600×500
15 Working area of the worktable of the base (L x W) mm 445×435
16
Numbers and width of the T slots both for worktable and
worktable of base mm 2-T14, 2-T14
17 Diameter of column mm φ200
18 Power and speed of the main motor kW, rpm 2.2/2.8; 960/1440
19 Power and speed of the worktable up and down motor. kW, rpm 0.25/1440
20 Power and flow rate of the coolant pump motor kW, L/min 0.18/6
21 Machine dimension (L x W x H) mm 1020×700×2350
22 Weight of the machine (Net weight/Gross weight) kg 660/720

Operation Manual Total 26
page 4
2.2 For the machine appearance and its main technical data, see diagram 1.
3. Brief description of the driving system and its structure:
The machine consists of spindle box, column, machine base, worktable and its bracket,
electric cabinet, coolant device and machine accessories, total seven component parts.
Spindle revolution is main motion of the machine. During drilling and milling processing,
spindle movement along with its axis is a feed motion. Worktable up and down movement
and worktable turn round itself is an auxiliary motion. To those big or higher work piece that
could be clamped on the worktable of the base. The worktable and its bracket should turn
round the column to a proper area far away from the machining area.
Double-speed vertical motors realize machine transmission. A special pump supplies coolant
water.
Operating lever in the front of spindle box could make changes for the spindle speed in 12
steps.Run the lever position could drive a triple gear and a quadruple gear moving along
with axis direction results the speed change. The lever has an idle position that is for the
spindle rotation by manual for loading and unloadin
g of tool cutters as well as for the
adjustment of work piece only. Adjustment of the feed rate could be realized by shifting a
set of gears controlled by changing a lever position in the right corner of spindle box. It also
has an idle position for disengaging power feed transmission of the spindle for the micro
adjustment of the spindle by manual.
Up and down movement of the worktable and its bracket is completed by a vertical speed
reduction motor. Of cause, little adjustment for the height of the worktable could also be
made by manual.
Two kinds of lubrication, auto or manual, of the machine are available. Auto lubrication
system consists of a filter ( located inside of a tank under spindle box), a lubrication oil
pump (located on the middle of spindle box), a visual window and an oil nozzle etc.
Please refer to the diagram 2 for the transmission system of the machine.
For the gear, worm and worm shaft, rack and pinion etc, please see table 1.
For the details of roller bears to be used on the machine, please refer to the diagram 3 and for
a list of roller bears, please refer to the table 2.

20°40°50° 30° 0°10° 40°20°10° 30° 50°
mm/r
OFF
0
0"
70
60
30
40
50
10
20
120
100
110
90
80
130
200
150
160
140
190
170
180
240
220
230
210
2"
1"
5"
4"
3"
8"
7"
6"
9"
0.4
0
165
120
0
80
340
250
510
2100
r/min
60
40
1000
1400
675
0.1
0.2
0
0.3
5
1
3
2
4
6
7
8
10
9
11
12
13
19
21
20
18
17
16
14
15
22
Operation Manual Total 26
drawing(1)picture of appearance of machine
Page 5
column
base
bracket seat
worktable
spindle box
electric box
speed-change box
mm/in
OFF
ON/O

7
8
13
12
11
9
10
14
15
16
17
18
19
20
22 23 2421 25 26 27 28
29
30
31
32
33
34
35
3
2
1
4
5
6
Operation Manual Total 26
drawing 2 picture of transmission
page 6

Operation Manual Total 26
page 7
4.1 list of gear, worm wheel,worm and rack table
(
1
)
Number on
the drawing 1 2 3 4 5 6 7 8 9 10
Part
drawing
NO.
11016/
ZY5050
12013/
ZY5050
12011/Z
Y5050
12012/
ZY5050
32001/Z
Y5050A
31001/Z
Y5050A
32036/Z
Y5050
32064/
ZY5050
32041/
ZY5050
32042/Z
Y5050
N
umber of
teeth and
starts
40 26 30 30 15 70 37 1 36 26
Module 2 1.5 1.5 2 2.5 2 2.5 2 1.75 1.75
D
irection of
helical
angle
Left Left
Class of
Accuracy 9 9 9 9 8-7-7 8 8 9 8-7-7 8-7-7
Material 45 45 45 45 QT400 40Cr 45 45 45
Heat
treatment
and
hardness
T235 T235 T235 T235 HV500 G48 G48
Number on
the drawing 11 12 13 14 15 16 17 18 19 20
Part
drawing
NO.
32043/Z
Y5050
32059/Z
Y5050
32058/Z
Y5050
32057/Z
Y5050
32056/Z
Y5050
32044/Z
Y5050
32045/Z
Y5050
32013/Z
Y5050
32052/Z
Y5050
32048/Z
Y5050
Number of
teeth and starts
17 22 32 41 26 32 43 15 60 25
Module 1.75 1.75 1.75 1.75 1.75 1.75 1.75 1.75 1.75 1.75
D
irection of
helical
angle
Class of
Accuracy 8-7-7 8-7-7 8-7-7 8-7-7 8-7-7 8-7-7 8-7-7 8-7-7 8-7-7 8-7-7
Material 45 45 45 45 45 45 45 45 45 45
Heat
treatment
and
hardness
G48 G48 G48 G48 G48 G48 G48 G48 G52 G52

Operation Manual Total 26
page 8
4.1 list of gear, worm wheel,worm and rack
table(1)
Number on
the drawing 21 22 23 24 25 26 27 28 29 30
Part
drawing
NO.
32012/Z
Y5050
32012/Z
50
32010/Z
50
32011/Z
50
30007/Z
50
32006/Z
50
32008/Z
50
32002/Z
50
32003/Z
50
32001/Z
50
N
umber of
teeth and
starts
51 40 18 40 28 50 17 59 17 22
Module 2.5 1.5 2.5 1.5 2.5 2.5 2.5 2 2.5 2
D
irection of
helical angle
Class of
Accuracy 7-6-6 9 7-6-6 9 7-6-6 7-6-6 7-6-6 7-6-6 7-6-6 7-6-6
Material 40Cr 40Cr 40Cr 40Cr 40Cr 40Cr 40Cr 40Cr 40Cr 40Cr
Heat
treatment
and
hardness
G42 G42 G42 G52 G52 G52 G52 G52 G52 G52
Number on
the drawing 31 32 33 34 35
Part
drawing
NO.
32004/Z
50
32005/Z
50
32009/Z
Y5050
12004/Z
Y5050
12015/Z
Y5050
Number of
teeth and starts
39 27 40 77 14
Module 2.5 2.5 2.5 2.5 2.5
D
irection of
helical angle
Class of
Accuracy 7-6-6 7-6-6 7-6-6 9 9
Material 40Cr 40Cr 40Cr 45Cr 45Cr
Heat
treatment
and
hardness
G52 G52 G52 T235 T235

12
20
11
5
14
18
1
17
15
14
8
3
9
10
7
19
2
13
13
16 6 4
Operation Manual Total 26
drawing 3 picture of rolling bearing
page 9

Operation Manual Total 26
page 10
Roller bearing table
Table (2)
No. Model Name Specification Q’ty
Accuracy
1 GB276,102 Deep racing ball bearing 15×32×9 1
2 GB276,104 Deep racing ball bearing 20×42×12 1
3 GB276,106 Deep racing ball bearing 30×55×13 1
4 GB276,108 Deep racing ball bearing 40×68×15 1
5 GB276,303 Deep racing ball bearing 17×47×14 1
6 GB276,304 Deep racing ball bearing 20×52×15 2
7 GB276,7000102 Deep racing ball bearing 15×32×8 1
8 GB276,7000103 Deep racing ball bearing 17×35×8 2
9 GB276;7000106 Deep racing ball bearing 30×55×9 2
10 GB276;7000111 Deep racing ball bearing 50×90×11 1
11 GB276,D1000909 Deep racing ball bearing 45×68×12 1 D
12 GB276;D7000110 Deep racing ball bearing 50×80×10 2 D
13 GB276;1180909K Deep racing ball bearing 45×68×12 2
14 GB277;50302 Deep racing ball bearing 15×42×12 2
15 GB277;50303 Deep racing ball bearing 17×47×14 1
16 GB277;50205 Deep racing ball bearing 25×52×15 3
17 GB297;2007107E Roller bearing 35×62×18 1
18 GB301,8102 Thrust bearing 15×28×9 2
19 GB301,8104 Thrust bearing 20×35×10 1
20 GB301,8110 Thrust bearing 50×70×14 1

Operation Manual Total 26
page 11
4. Electrical system
4.1 Brief description
The machine with foreign advanced single chip and superior quality electric element is controlled by
electric system, the software syst
em not only realize all kinds movement control ,but also has many
protective function with catenation, the capability of this system is very good ,and the movement of this
system is jarless and reliable. the move and stop of the main motor function are used by electric circuitry,
and it improved the accuracy of machine’s drilling.
4.2 Explanation of the circuit
When using the machine, breaker QF1,QF2,QF3 which positioned electric box B1( drawing 4) must be
closed, it can be opened when examined and repaired. The three breakers separately protect short circuit、
over loading and short phase of spindle motor, pump motor and lifting motor. when close the chief switch
QS1, the system is entering working state and the single lamp HL1 light up ,when break the chief electric
source, the lamp crush out and working stopped.
4.3 Tapping operation:
Electric Element for the tapping control mainly contactors KM1 and KM2, selection switch SX1 and limit
switches SQ2 and SQ3 for tapping depth control. Put the selection switch SX1 into the “1”(“0”is for hole
drilling only),arrange the spindle revolution in clockwise direction KM1 engaged), put the spindle manual
operation lever in down position until touches work piece, tapping job noe is starting. When required depth
is
reached , the limit switch SQ3 works, the spindle immediately runs in counter clockwise direction (KM2
engaged), the tap returns out of the work piece, when spindle returns to the up highest position ,the limit
switch SQ2 works, spindle runs in clockwise direction, now one tapping job is finished. If tapping stop is
required, push the button (SB4) on the lever end , the spindle motor will immediately run in count
clockwise direction, that’s all.
If the selection switch SX1 is in the “0”position, normal drilling work starts.
Attention: As the spindle motor works frequently during tapping, the motor will be hot quickly ,so the
tapping job could not be down for a long time, eight times of tapping per minutes maximum
is recommended as the motor needs cool when it is hot otherwise it will be burned.
4.4Auto feed operation:
When auto feed , moving spindle down 5-6mm, press a push button at the end of either one of the three
levers, now feed clutch is engaged and indicator HL2 on the panel is lighted auto feed job is started.
When required drilling depth is reached ,the limited switch will be pressed, then spindle returns
automatically. Press the push button of the lever once again, auto feed will be stopped and the spindle will
return back to the original place.

SB6
SB6
SB5
SB2
SB1
SX3
20°40°50° 30° 0°10° 40°20°10° 30° 50°
mm/r
OFF
High-speed spindle motor SQ8
signal switch
Operation Manual Total 26
drawing(4) picture of electrical element of machine
Page 12
button of hand lever SB4
button of hand lever SB4
lamp EL1
limit switch SQ3
limit switch SQ1
limit switch SQ2
digital lable
operation panel
operation panel
pump motor M3
limit switch SQ4
limit switch SQ6
wiring box B2
pump motor M2
limit switch SQ5
electric box B1
button of hand lever SB4
motor of spindle M1
instruction switch(QS1)
switch of coolant pump SX2
SX1

Operation Manual Total 26
page 13
4.5 Emergency stop operation:
If emergency stop is necessary during operation, press emergency push button SB1,so the
machine is completely stopped .After eliminating the breakdown ,release the lock of the push
button then restart the machine.
4.6 Coolant pump
Revolving the switch of coolant pump right, then the coolant pump is moving and working
with the spindle. When the spindle stopped, the coolant pump stopped too.
4.7 Lifting motor
The clamping handle 22 must be opened when the worktable lifting, turn the push button SX3
at required position.
4.8 Installation of the main motor:
Insert the key of the main motor into the solt position of the spline shaft then fixed by 4-M10
×35 hex screw bolts. Connect three phases and one ground wires to the power supply as per
the electrical Diagram(5) of the machine.(please note the direction of main revolving).
4.9 Sheet metal guard:
The sheet metal guard of this machine has a safety protection function, when it is opened
The spindle can’
t working, until it is closed when the spindle is working now, it immediately
stopped if The sheet metal guard is opened .
4.10 Maintenance of the electric equipment:
Turn off the electric power before maintenance of the electric equipment starts. The electric
equipment must keep on clean condition. Therefore, regularly cleaning is necessary.
However .liquid such as kerosene, gasoline and detergent etc. is not be allowed for the
cleaning. Wave of power supply shall not be over ±10% required by the electric motor.
Maintenance of electric equipment is absolutely important in order to keep machine works
well.

advise 25A
blue
picture of connecting wiring of speed
8
yellow
14
yellow
brown
RVP1
S1
black
bluebrown black
3
2.2/2.8kW 0.13kW
M2
M1
0.25kW
M3 EL1
V2
V3
1V4
KM1
2V42U4 2W4 1U4
U3
KM5 KM3
PE
U2
QF1
3φ AC400V 50Hz
U1
L1
L3
L2
W1
V1
QS1
KM2
KM8
0.75mm
KM4
M
S
V6U6
1W4
2
U8W6 V8 W8
2
1.5mm
W3
KM6 KM7
9
HL1
(3A)FU3
1
(5A)FU4
2
24V
3
13 14
(1A)FU5
4
24V
5
(1A)FU6
6
24V
7
W2
V5U5
QF2
U7W5 V7 W7
QF3
T1
W20U20
(3A) (3A)
FU1 FU2
1.5mm
2
24V 45V
W12
KM10
2W41U4
KM9
2U4 1W4
KM10 KM9
U12
58
55
QL2
8
9V
(5A)FU9
53 54
57
KM10
KM9
(10A)FU10
56
W11U11
T2
FU7
FU8
(3A)
(3A)
M
S
3
M
S
3
Attention: The diameter of the line without indicating is 0.75mm .
drawing(5-1) picture of electric element
2
equipment dividing line
brake
for
high
speed
brake
for
low
speed
81 82 83
pump motor
total
switch
total power
supply splind motor
Operation Manual
lifting motor
Total 26
1.5mm
2
control
page 14
1.5mm
2
12
SB1
11
SQ1
30

drawing(5-2) picture of electric element
Operation Manual
lifting for table
Total 26
page 15
Attention: The diameter of the line without indicating is 0.75mm .
P L C contrl
4
12
SQ4
SX3-2SX3-1
KM8KM7
35 39
KM8 KM7
33 37
32 36
31
SQ6SQ5
52
4
12
FU22(3A)
COM1COM
24 72 40
QL1
Q1
AC24V
6
13
L
16
NI1
SB2
60
KM10
KM9
Q12
69
KM4
KM10
51
6
13 KM5
I7
Q6
U1(WJ1-10/12F)
Q3
KM1
KM2
FU23(3A)
HL2
YC
YC1 R1
66
V1 42
KM1
KM2
44
Q2
41 43
SX2
KM4
KM4
KM3
KM9
50
KM3
KM5
47
46
49
KM5
68
KM6
Q4
45 48
Q5
67
73
18
I3I2
10
SQ7 SX1
I4
19
SB4
SQ1
SQ4
22
SB3
17
SQ3
I5
20
SQ2
I6
21 25
SB5
Q10Q8Q7 Q9
64
65
KM3
KM9 62
KM10
COM2
59
Q11
I10
23
I8
SB1
I9
26 27
SB6 SQ8
Jog
NC NC NC
63
NC NC
15
FU21(1A)
NC V+
71
limit position (below) for feed
limit position(above) for feed black
brown
blue
black
blue
brown
reverse rotate
emergency stop
out/in for tapping
start/stop for feed
tapping
switch for spindle
rotate in clockwise
stop
coolant
pump
clutch
High-speed signal
switch for spindle
motor
High-speedLow-speed
turn right turn left
spindle
brake of
low speed
brake of
high speed
2

Operation Manual Total 26
page 16
Electric components list: Table (3)
Code of elements Name Specification Q’ty Remark
QF1 Breaker GV2-ME14 1
QF2 Breaker GV2-ME04 1
QF3 Breaker GV2-ME06 1
QS1 Instruction switch JCH13-20 1
SX1,2 Selection switch C2SS2-10B-10 2
SB1 Emergency stop button CE4T-10R-02 1
SB2,5 Push button CP1-10G-10 2
SB6 Push button CP1-10B-10 1
SB3 Push button CP1-10R-01 1
HL1,HL2 Single lamp AD17-16 AC24V 1
SB4 Push button Homedade 3
SX3 Selection push button C3SS2-10B-20 1
SQ1 Micro switch C2-A2Z 1
SQ5,SQ6 Micro switch E62-10A 2
SQ2,SQ3 Adjacent switch TL-Q5MC1 2
SQ4 Micro switch XCKN2102P20C 1
KM1-5,KM7-10 Contactor LC1E1201B5N(AC24V) 9
Secondary contact LAEN02N 5
KM6 Contactor LC1 D0901 (AC24V) 1
SQ8 Micro switch Z-15GD 1
EL1 Illuminating light AC24V;25W 1
T1 Transformer JBK5-160TH ,400/24,24,24,9 1
T2 Transformer JBK5-300TH 400V/0V,24V,45V 1
R1 Resistor RT 2W62Ω1
V1 Diode IN5404 1
U1 Control panel WJ1-10/12F 1
QL1 Bridge wiring QL5A 200V 1
QL2 Bridge wiring QL10A 200V 1
RVP1 Tachometer RSD-42 1
SQ7 Door switch JWM6-11A 1

Operation Manual Total 26
page 17
5.Lubrication and coolant system:
5.1 Lubrication system:
Parts and bearings inside of the spindle box are all automatically lubricated. Oil level shall
be a little bit higher than the centerline of the oil window when you fill lubrication oil. Too
much oil filling will cause overflowing. Oil release plug and a filter device are in the same
unit located at left side down of the spindle box. Please pay attention that when fastening
your oil release plug, don’
t forget to put the oil absorption pipe inside of the filter,
otherwise no filtered oil will be available. The filter needs to be washed once every two
weeks.
For lubrication places and its requirements by manual. Please refer to the diagram 6.
5.2 Coolant system:
A special pump will supply coolant both for tool cutter and for work piece during machining.
Coolant liquid is stored in a compartment located at the backside of the machine base. Flow
rate of the coolant could be adjusted by a ball valve. Regularly washing for the coolant
system is necessary and coolant water shall be exchanged as per actual condition.
6. Hoisting and installation:
6.1 Hoisting:
The machine is strongly fixed inside of the crate. When hoisting the machine, please pay
close attention to the sign outside of the crate (where the wire cable shall be placed and
where the gravity center is).
The crate must not be reversed or inclined and must not be strongly stroked when lift up the
machine.
Considering small size of the bottom and higher size of the height of the machine package,
therefore, moving the machine by roller is forbidden. Lifting by a crane or by forklift is
recommended.
Please refer to the diagram 7 for the machine lifting. A soft pad between machine and wire
cable is necessary in order to avoid paint damage of the machine. Lifting must be slow at
beginning to see if the gravity center is correct.
Table of contents
Other Promac Power Tools manuals
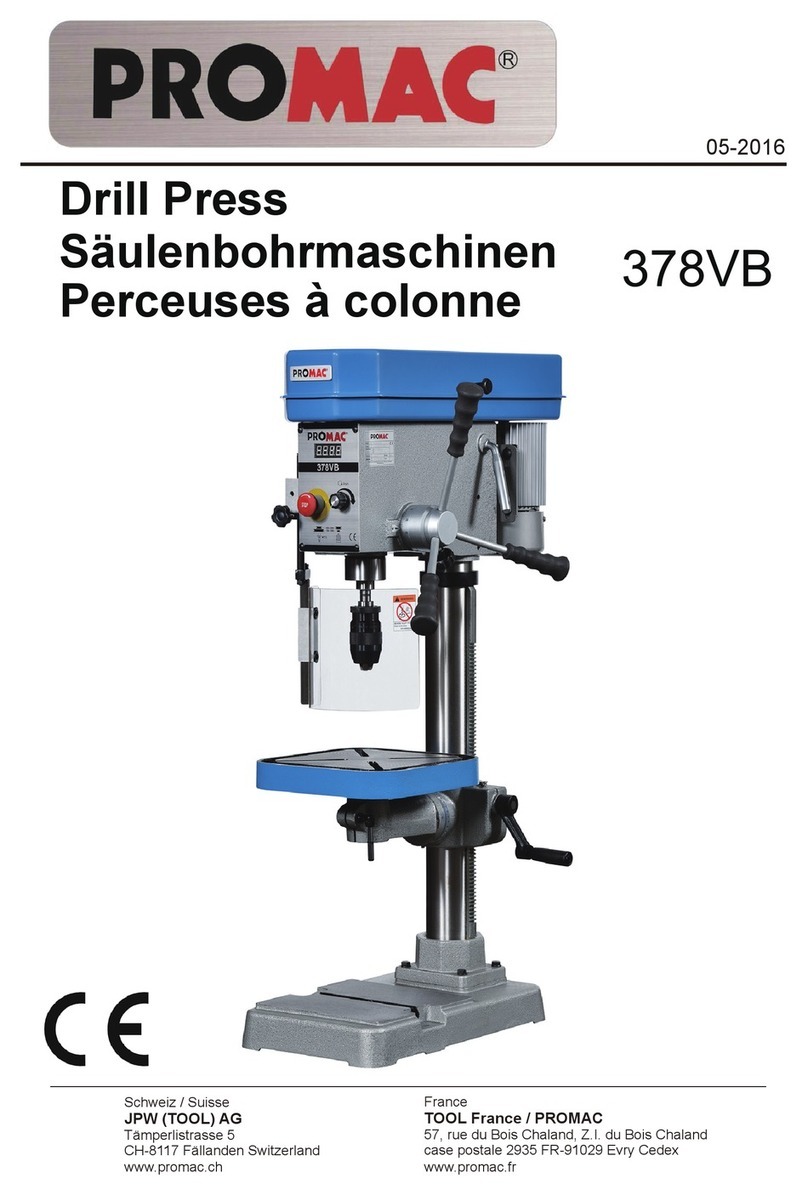
Promac
Promac 378VB User manual
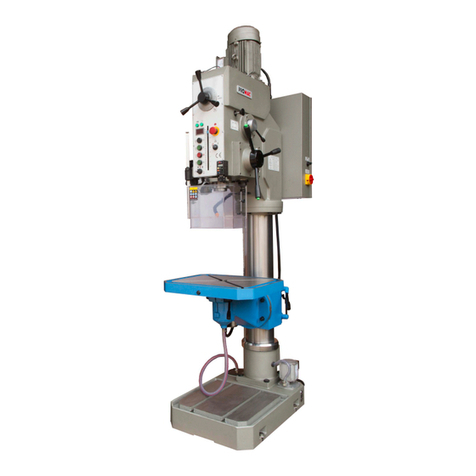
Promac
Promac JDT-4024 User manual
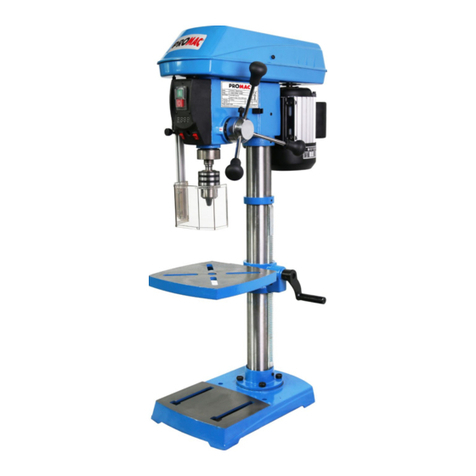
Promac
Promac 212VLL User manual
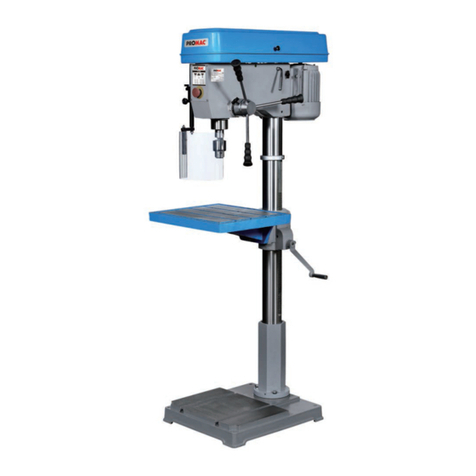
Promac
Promac 214AB-M User manual
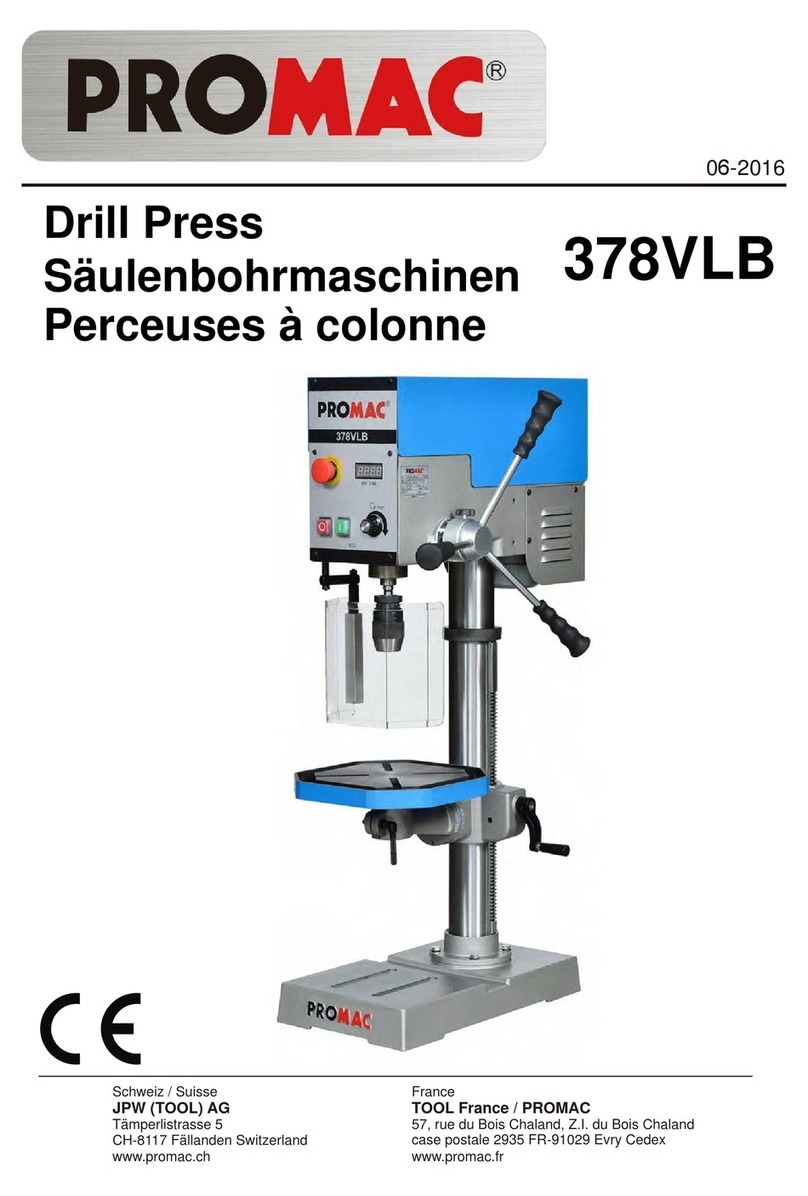
Promac
Promac 378VLB User manual
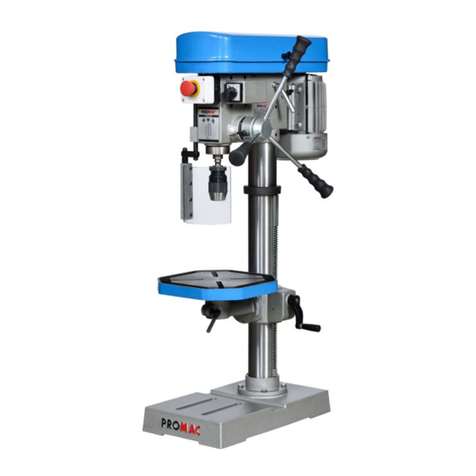
Promac
Promac 378CLB User manual
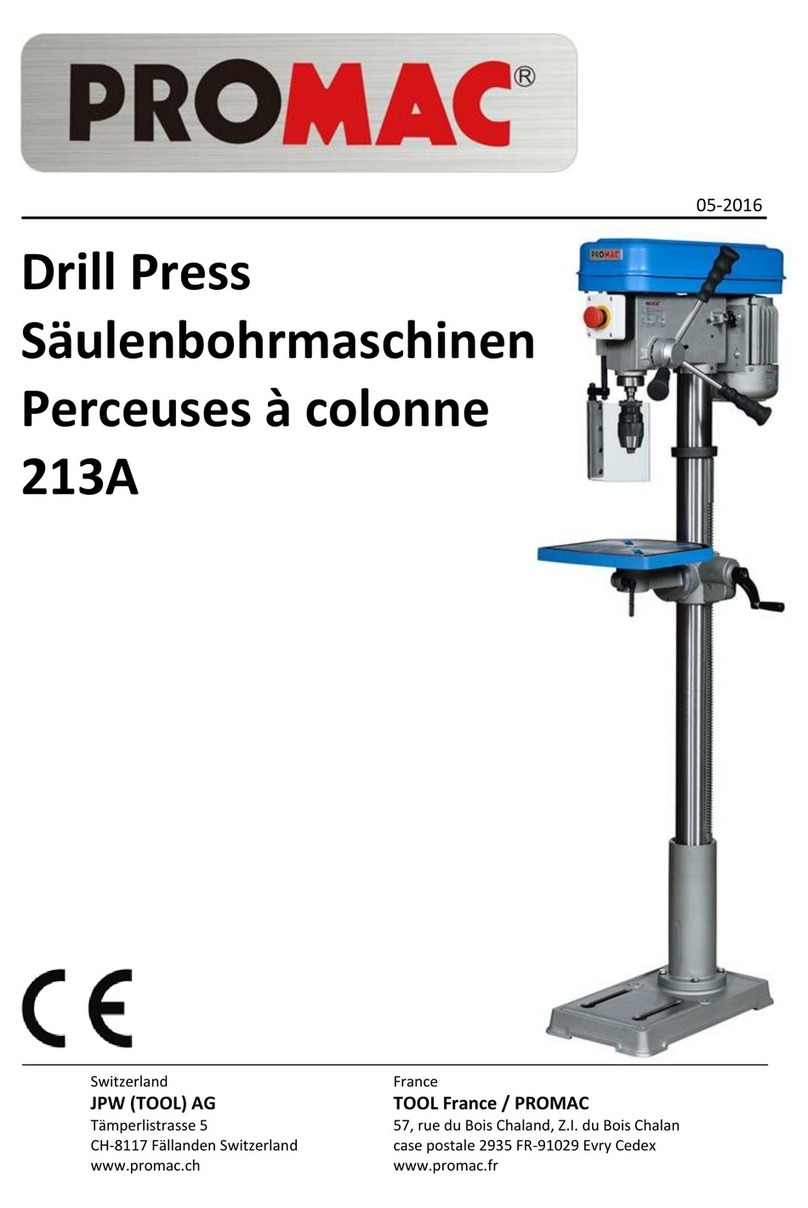
Promac
Promac 213A User manual
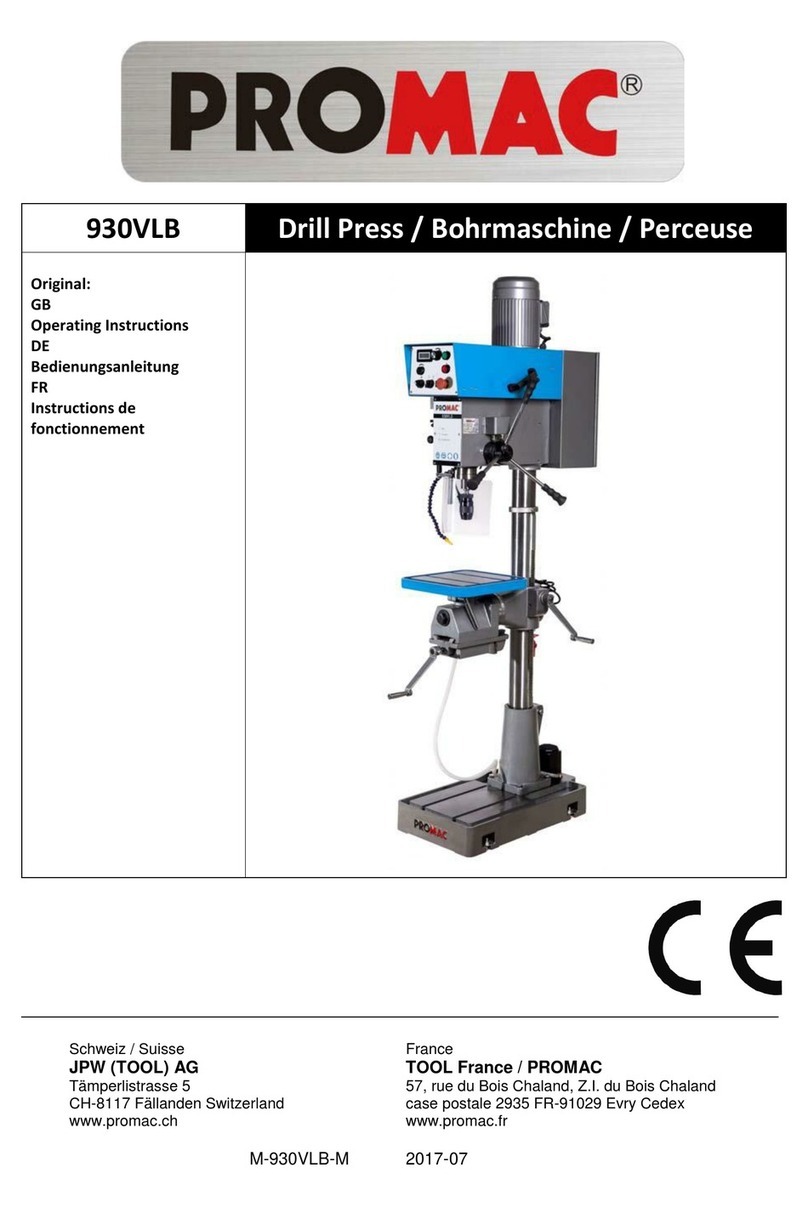
Promac
Promac 930VLB User manual

Promac
Promac 930ELB User manual
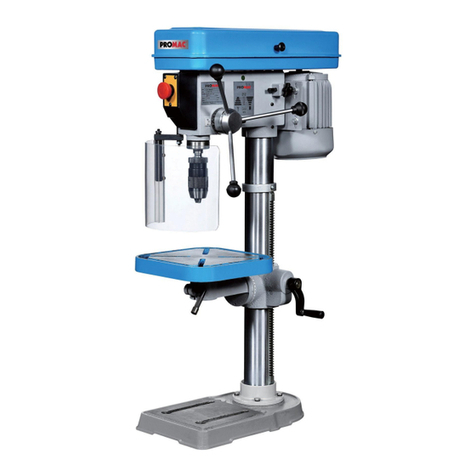
Promac
Promac 212 User manual
Popular Power Tools manuals by other brands
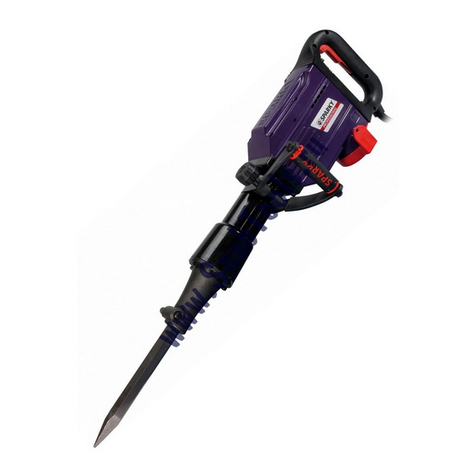
Sparky Group
Sparky Group K 2050 Original instructions
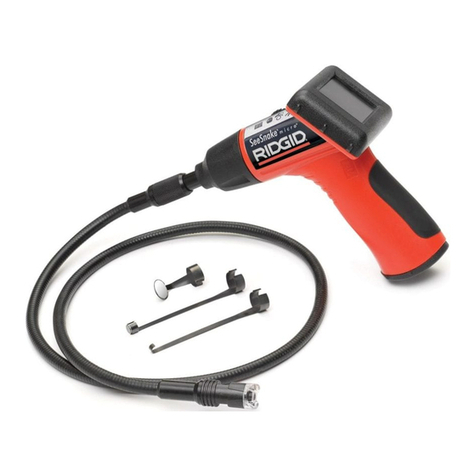
RIDGID
RIDGID SeeSnake Micro operating instructions
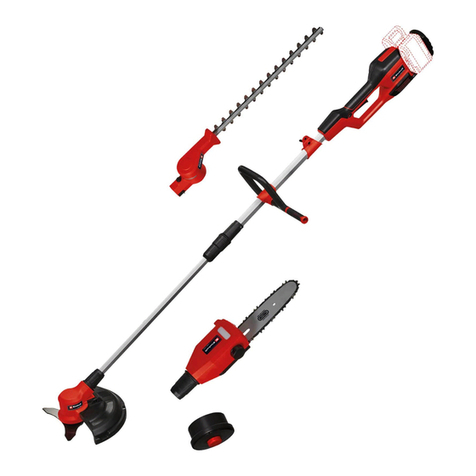
EINHELL
EINHELL GE-LM 36/4in1 Li operating instructions
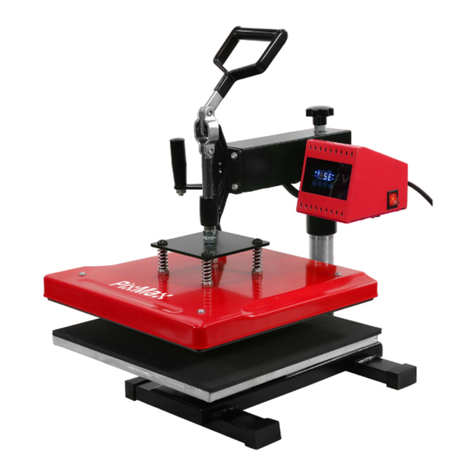
MonsterShop
MonsterShop PixMax 210509 instruction manual

ACDelco
ACDelco ARM601-4 Product information manual
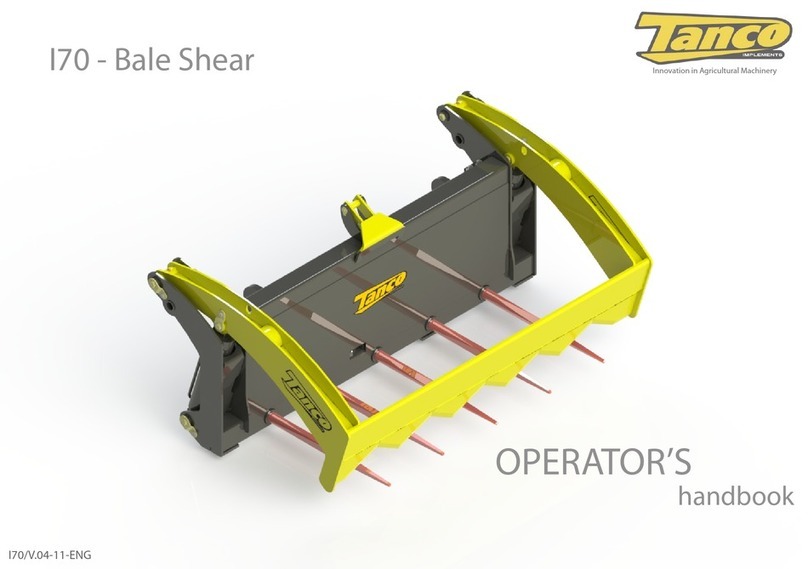
Tanco
Tanco AUTOWRAP I70 Operator's handbook