SKF Lubrigun 85100 Series Instruction Manual

User and maintenance instructions
Models 917, 989, 86267 with air operated grease pumps 82050, 82716, 85100*, 802330* and 83513
Lubrigun® lubrication unit
Date of issue July 2017
Form number 403404
Version 2
* Indicates change.

Contents
EC Declaration of Conformity
in accordance with Machinery
Directive 2006/42/EC, Annex II
Part 1 A . . . . . . . . . . . . . . . . . . . . . . . . . . 2
Description. . . . . . . . . . . . . . . . . . . . . . . 3
Safety information . . . . . . . . . . . . . . . . 3
Installation. . . . . . . . . . . . . . . . . . . . . . . 3
Accessories . . . . . . . . . . . . . . . . . . . . . . 3
Typical system hookup . . . . . . . . . . . . . 4
Assembly instructions . . . . . . . . . . . . . 4
Pressure relief procedure . . . . . . . . . . 5
Operation . . . . . . . . . . . . . . . . . . . . . . . . 5
Lubrication. . . . . . . . . . . . . . . . . . . . . . . 6
Material restriction prevention. . . . . . 6
Corrosion prevention . . . . . . . . . . . . . . 6
Exploded views . . . . . . . . . . . . . . . . . . . 7
Parts list. . . . . . . . . . . . . . . . . . . . . . . . . 11
EC Declaration of
Conformity in
accordance with
Machinery Directive
2006/42/EC, Annex II
Part 1 A
The manufacturer Lincoln Industrial,
5148 North Hanley Road, St. Louis, MO
63134 USA hereby declares that machine
Designation: High-pressure air operated
chassis pump
Type: Lubrigun
Model number: 82050, 82716, 85100,
802330 and 83513
Year of construction: (see type identification
plate)
complies with all basic requirements of the
following directives at the time when first
being launched in the market.
Machinery Directive 2006/42/EC, EMC
2009/19/EC and 2004/108/EC
RoHS II 2011/65/EC
Applied standards DIN EN ISO 12100:2011-
3, DIN EN 61000-2:2003-5, DIN
40050-9:1993-5
DIN EN 809-1:2011, DIN EN 60204-
1:2011-1, DIN EN 55011:2011-4
In the case of modifications or alterations of
the above mentioned machine not authori-
zed by the manufacturer, validity of this EC
declaration of conformity will cease. The
person empowered to assemble the techni-
cal documentation on behalf of the manu-
facturer is the head of standardization; see
EC-representative‘s address.
EC-Representative
SKF Lubrication Systems Germany GmbH
Heinrich-Hertz-Str. 2-8
DE - 69190 Walldorf
Robert Hoefler,
Director Product Development/
Product Engineering
July 10 2017
2

Description
Models 82050, 82716, 83513, 85100 and
802330 are air operated grease pumps
designed to pump low and medium viscosity
materials (grease) from drums and pails.
Safety information
Read and understand all warnings, cautions
and instructions before operating
equipment.
Specifications
Air motor effective diameter 2.5 in. (63,5 mm)
Air inlet 1/4in. NPTF
Outlet adapter 1/4in. NPTF
Ratio 50:1
Delivery output 80 in.3/min. (1 310 cm3/min.)
Delivery cycle 0.35 in.3/cycle (5,7 cm3/cycle)
Minimum air pressure 30 psi (2 bar)
Maximum air pressure 150 psi (10 bar)
Maximum output pressure 7 500 psi (517 bar)
Noise level @ 120 psig <85 dBA
Installation
Typical drum and pail hookups are described
only as guide in selecting and installing
system.
Accessories
• Filter/regulator/lubricator and gauge
• Eyebolt kit
• Follower plate – 120 lb. (54 kg),
400 lb. (181 kg)
• Drum cover – 120 lb. (54 kg), 400 lb.
(181 kg)
• Drum cover with tie rods
• 1709 hoist
WARNING
Do not exceed maximum working pressure of
lowest rated component in system.
Pump can develop 7 500 psi (517 bar)
working pressure at 150 psi (10 bar)
maximum incoming air pressure. All system
equipment and accessories must be rated to
withstand maximum working pressure of
pump.
Failure to comply may result in serious
injury or damage to equipment.
3

Assembly
instructions
Assemble unit as shown in diagrams.
Read and understand all warnings and
directions in component manuals.
1
Remove cover nut from top of pump. Lift air
motor cover from pump.
2
Remove four screws holding cover-bottom
to pump outlet body.
3
Hold pump with pump outlet body resting
securely on inner surface of cover-
bottom. Insert end of pump tube
through hole in drum cover. Line up
holes in drum cover, cover-bottom and
pump outlet body.
4
Replace four screws and tighten securely.
5
Push insert through follower with small cone
of wiper body facing up. Place insert
retainer over insert and align holes on
insert and insert retainer. Secure
assembly with four self-tapping screws.
6
Remove drum top and insert follower into
drum against surface of lubricant.
7
Guide end of pump tube into follower insert.
8
Lower pump tube into lubricant drum until
drum cover rests on top bead drum.
9 Assemble lubricant hose to pump outlet
body. Connections must be leak proof.
10
Place cover over air motor and position over
cover-bottom.
11
Replace cover nut on pump stud to hold air
motor cover securely in place.
12
Assemble nipple and adapter through hole in
side of air motor cover and into air
motor. Connection must be leak proof.
13 Connect air coupler to an air hose of
sufficient length so lubrigun can be used
to cover entire lubrication area.
Typical system
hookup
1 Determine drum or pail system for
requirement.
2
Obtain air line filter/regulator/lubricator to
use with inlet air supply.
3 Clean supply lines, hoses, reducers,
connectors and accessories of matter
that could damage pump or system
components. Clean/flush pump with
mineral spirits or solvents if necessary.
4 Assemble cleaned pump and supply line
together with any required accessory.
5 Mount assembled pump to drum or pail.
6
Connect material output line/hose to pump.
Connect air regulator to pump.
7 Make sure all connections are securely
tightened.
NOTE
Pump was tested in lightweight oil and was
left in to prevent corrosion.
Flush pump before connecting to system
to prevent possible contamination of grease
being pumped.
WARNING
Do not exceed 90 psi (6 bar) air pressure to
pump when using whip hoses.
Accessory item whip hoses for dispensing
valve are rated at 4 500 psi (310 bar).
Failure to comply may result in serious
injury or damage to equipment.
4

Pressure relief
procedure
Always perform this procedure before
servicing:
1 Disconnect air supply to pump.
2 Point dispensing valve away from yourself
and others.
3 Open dispensing valve into container until
pressure is relieved.
If above procedure does not relieve pressure,
dispensing valve or hose may be restricted.
To relieve pressure, very slowly loosen hose
end coupling. Then, loosen completely and
clear dispensing valve and/or hose.
Operation
Inspect before use
Any pump that appears to be damaged in
any way, shall be removed from use until
repairs are made. Contact factory authorized
service center for repairs.
Pump use
To start pump, turn on main air supply.
Slowly open air regulator. Regulate air
pressure from 20–40 psi (1,3–2,7 bar) and
throttle to prime pump. Open dispensing
valve to allow air to be purged from system.
Allow pump to cycle until grease, without air
pockets, flows from dispensing valve, and
then close dispensing valve.
After pump is primed, adjust air pressure
to achieve smooth flow of grease from
dispensing valve. Do not allow pump to
operate when out of material. Pump will
accelerate quickly and run too fast, resulting
in costly damage to pump.
If pump accelerates quickly or is running
too fast, stop it immediately. Check grease
supply and refill it if necessary.
In circulating system, pump runs
continuously and slows down or speeds up
as supply demands, until the air supply is
shut off.
In direct supply system, with adequate air
pressure supplied to motor, pump starts
when gun or dispensing valve is opened and
stalls against pressure when it is closed.
Use air regulator to control pump speed
and grease pressure. Always use lowest
pressure required to achieve desired results.
WARNING
Do not operate pump or system with
pressure applied. Perform pressure relief
procedure prior to starting pump.
Failure to comply may result in serious
injury or damage to equipment.
WARNING
Failure to heed the following warnings
including misuse, over pressurizing, modify-
ing parts, using incompatible chemicals and
fluids, or using worn or damaged parts, may
result in serious personal injury and/or
equipment damage, fire, explosion, or prop-
erty damage.
• Do not exceed the stated maximum work-
ing pressure of the pump, or of the lowest
rated component in your system.
• Do not alter or modify any part of this
equipment.
• Do not operate this equipment with com-
bustible gas.
• Do not attempt to repair or disassemble
the equipment while the system is
pressurized.
• Make sure all grease connections are
securely tightened before using this
equipment.
• Always read and follow the grease manu-
facturers recommendations regarding
grease compatibility, and the use of pro-
tective clothing and equipment.
• Check all equipment regularly and repair
or replace worn or damaged parts
immediately.
• Never point the dispensing valve at any
part of the body or at another person.
• Never try to stop or deflect material from
dispensing valve, leading connection or
component with your hand or body.
• Always check equipment for proper opera-
tion before each use, making sure safety
devices are in place and operating
properly.
• Always follow the pressure relief procedure
after shutting off the pump, when checking
or servicing any part of the system, and
when installing, cleaning or changing any
part of the system.
5

Lubrication
Air line filter/regulator/lubricator is recom-
mended for use with Lincoln pump to
remove harmful dirt and moisture from
compressor air supply, and to provide auto-
matic air motor lubrication.
If air lubricator is not used, the following
procedure should be performed daily:
1 Disconnect air coupler from air fitting.
2
Fill air coupler with NO. 10 SAE motor oil and
reconnect to air fitting.
Material restriction
prevention
Flush system as required with compatible
solvent to prevent material buildup when
pumping material that dries or hardens.
Corrosion prevention
To prevent water or air corrosion, never
leave the pump filled with water or air.
6

1
2
3
4
5
6
7
8
9
5
7
11
12
13
14
15
13
16
17
18
14
19
1)
24
23
22
21
20
1) Screw included with 46007.
Fig. IPB1
Model 917, 120 lbs. (54 kg) container, 50:1 ratio
7

Model 989, 35 lb. (15,8 kg) container, 50:1 ratio
2
1
7
6
25
3
4
5
26
7
27
11
28
29
30
31
32
33
21
34
5
Fig. IPB2
8

Model 86267, 802330, 35 lb. (15,8 kg) container, 50:1 ratio
7
6
3
4
5
26
7
27
11
28
29
30
31
32
33
5
25
Fig. IPB3
9

Model 85100, 60 lb. (27 kg) container, 50:1 ratio
25
7
6
7
30
5
Fig. IPB4
10

Refer to separate
instructions:
740 Control valve: 403742
815 Air coupler: 405457
81387 Swivel: 404221
82716 Basic pump: 404216
Parts list
Used on model
Item no. Description Part number 917 989 86267 85100* 802330* Quantity
1Small swivel, universal D 81387 X X 1
2Coupler and extension 740 X X 1
3Coupler, air 1/4FPT 815 X X X X 1
4Coupler, air-nipple 11659 X X X X 1
5Outlet adapter 11348 X X X X X 21)
6Cover nut 11478 X X X X X 1
7Pump cover assembly 84935 X X X X X 1
8Chassis high pressure pump 82050 X 1
9Small swivel, straight 82399 X 1
10 Screw HHCS 1/4-20 x 9/1 50060 X X X X 4
11 Follower assembly 84780 X 1
12 Plate, truck assembly 45880 X 1
13 Caster 66060 X 4
14 Clamp 360266 X 4
15 Washer, flat 5/16 w 48238 X 4
16 Screws 50016 X 4
17 Set screw 11123 X 4
18 Truck assembly 80895 X 1
19 Screw HHCS 1/4-20 x 3/850113 X 2
20 Hose assembly 1/4x 84 75084 X X 1
21 Hanger, control valve 45761 X 1
22 Nut, hex 1/4-20 SEM 50754 X 2
23 Drum cover 46007 X 1
24 Pump 50:1 82716 X X X 1
83513 X
25 Handle 63088 X X 1
26 Screw, thumb 66130 X X X 3
27 Button, snap 11/32 66057 X X X 1
28 Drum cover 91499 X X 1
Drum cover (802330) 081523-E025 X 1
29 Follower assembly 84775 X X X 1
Follower assembly (802330) 083366-E025 X 1
30 Stove bolt nut 51300 X X X 4
31 Washer, package 13/64 b 48218 X X X 4
32 Screw RHMS #10-24 x 1/250301-1 X X X 4
33 Hose connector 10198 X 1
34 Set screw 950000-E2) X 3
35 Clamp 012643-E0592) X 1
1) 86267 - Requires (1) 11348
2) Not shown
*Indicates change.
11

skf.com | lincolnindustrial.com
® SKF, Lincoln and Lubrigun are registered trademarks of the SKF Group.
© SKF Group 2017
The contents of this publication are the copyright of the publisher and may not be reproduced (even
extracts) unless prior written permission is granted. Every care has been taken to ensure the accuracy
of the information contained in this publication but no liability can be accepted for any loss or damage
whether direct, indirect or consequential arising out of the use of the information contained herein.
July 2017 · Form 403404 Version 2
Warranty
The instructions do not contain any informa-
tion on the warranty. This can be found in
the General Conditions of Sales, available at:
www.lincolnindustrial.com/technicalservice
or www.skf.com/lubrication.
This manual suits for next models
7
Table of contents
Other SKF Lubrication System manuals

SKF
SKF OLA 1 Series User manual
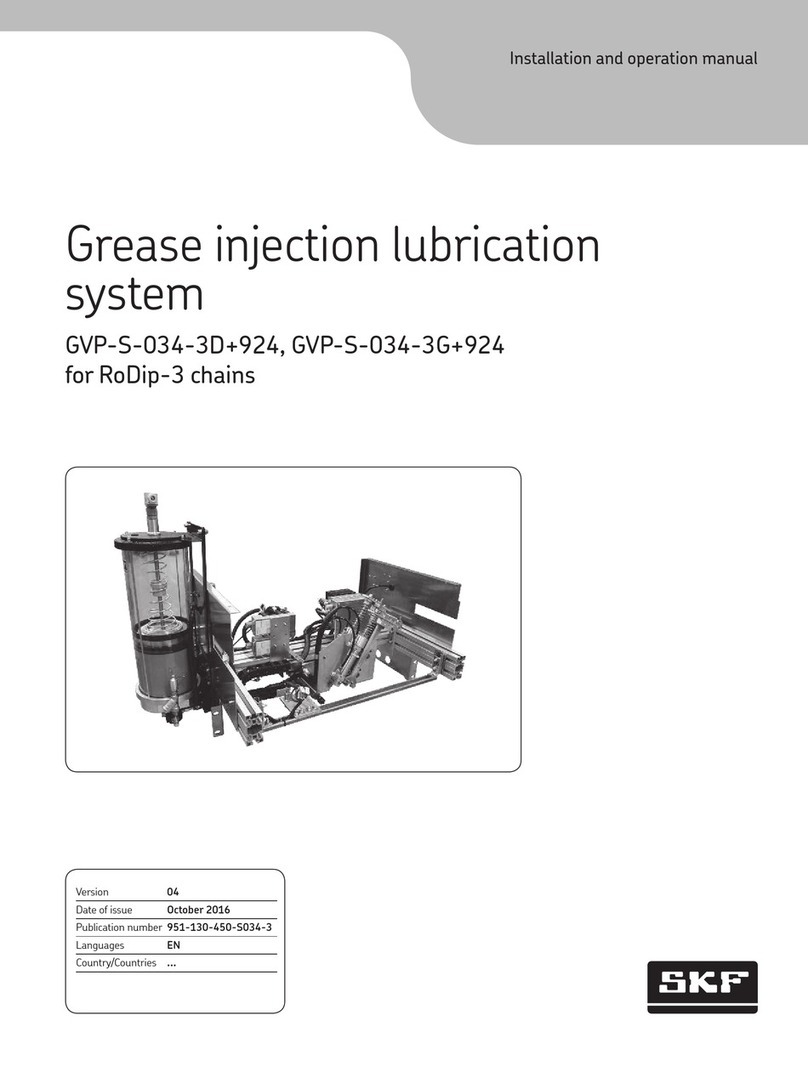
SKF
SKF GVP-S-034-3D+924 User manual
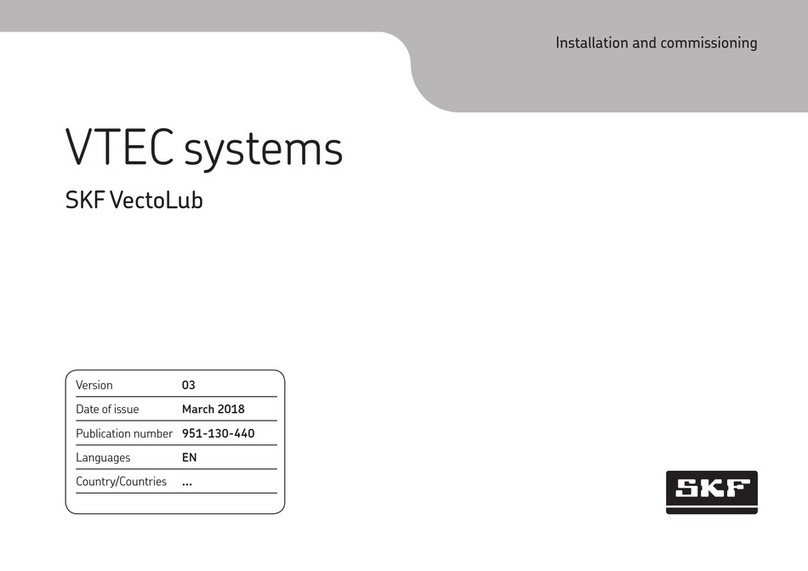
SKF
SKF Vectolub VTEC Guide
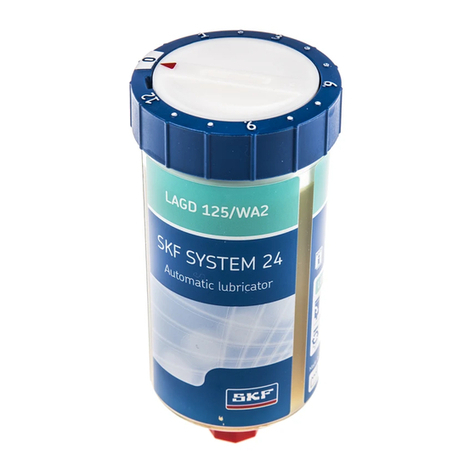
SKF
SKF LAGD 125 User manual
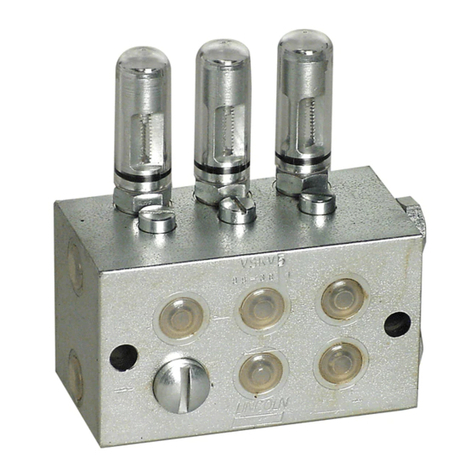
SKF
SKF VSG Series User manual
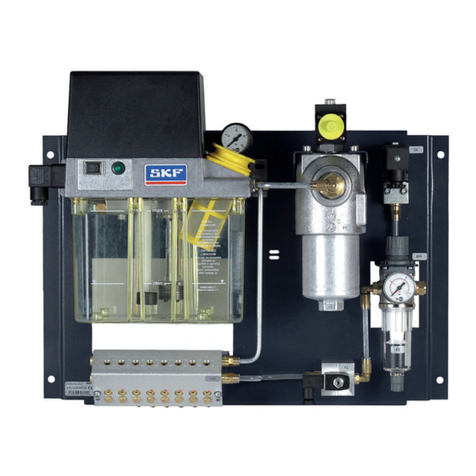
SKF
SKF OLA Series User manual
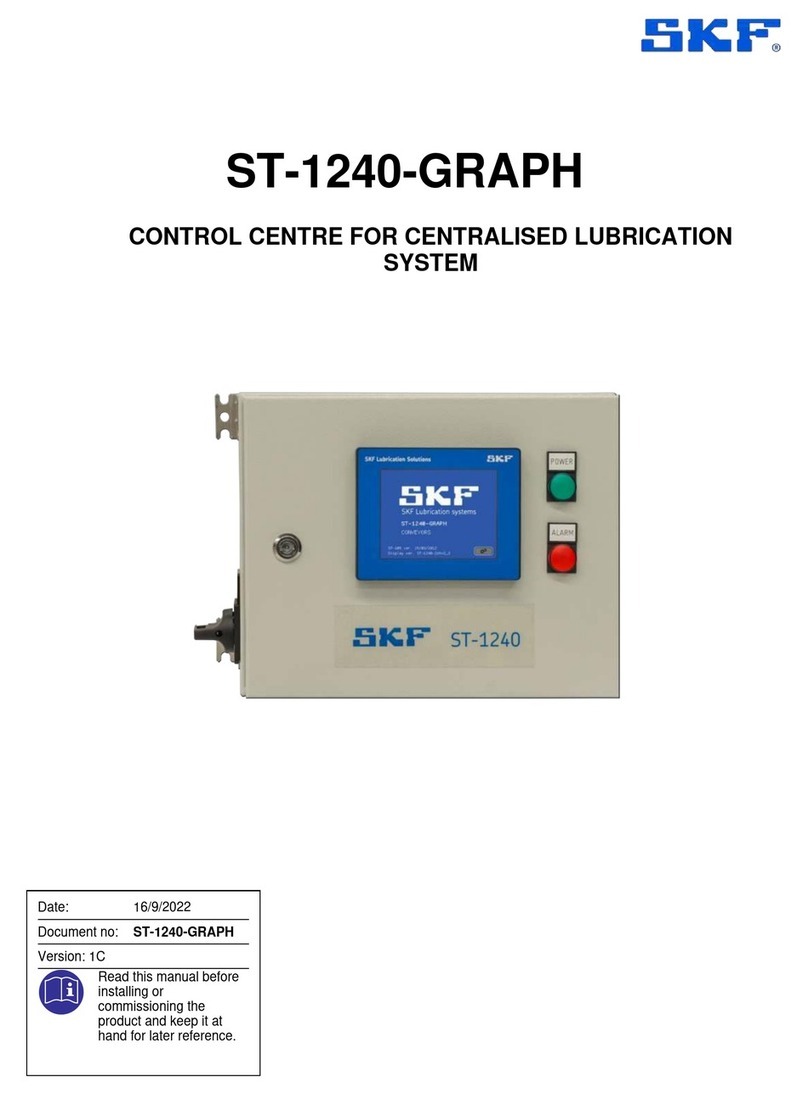
SKF
SKF ST-1240-GRAPH User manual
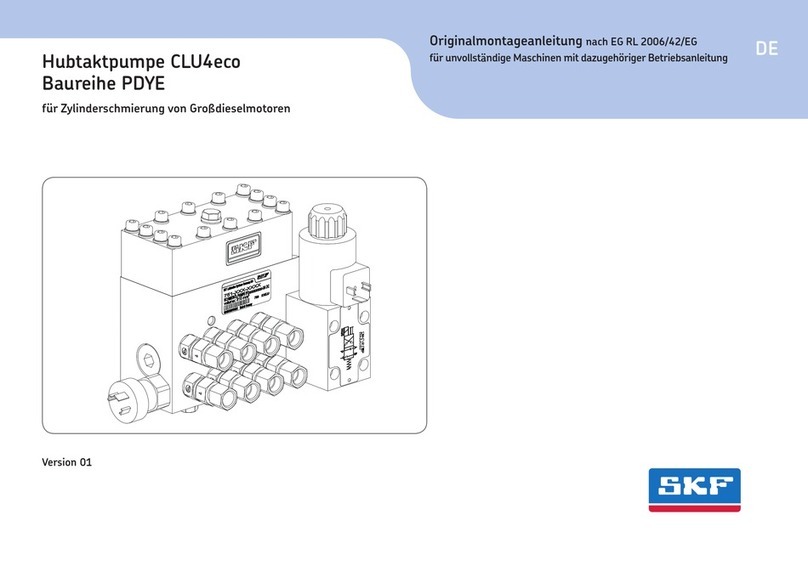
SKF
SKF CLU4eco PDYE Series Quick start guide
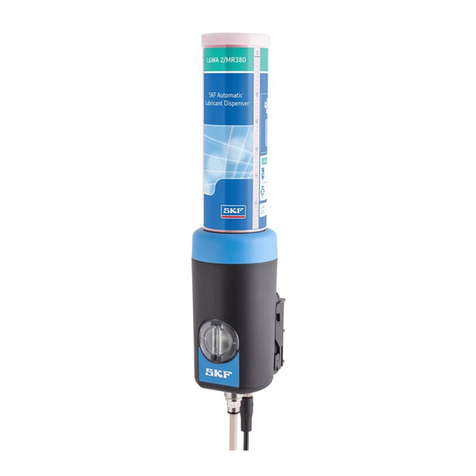
SKF
SKF TLMR User manual
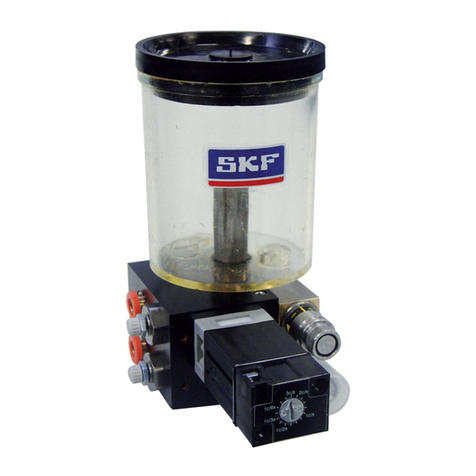
SKF
SKF VectoLub VE1B Guide