Tyco DV-3 User manual

Page 1 of 10 TFP1462
JANUARY, 2005
Preaction System with Model DV-3 Deluge Valve
Double Interlock, Electric/Pneumatic Release
2-1/2 Inch (DN65)
FIGURE 1
2-1/2 INCH (DN65) ELECTRIC/PNEUMATIC DOUBLE INTERLOCK PREACTION SYSTEM
— SCHEMATIC OF TYPICAL ARRANGEMENT —
Technical Services: Tel: (800) 381-9312 / Fax: (800) 791-5500
OBSOLETE

General
Description
The 2-1/2 inch (DN65) Model DV-3
Electric/Pneumatic Double Interlock
Preaction System (Ref. Figure 1) is
designed for use in applications, such
as refrigerated areas, requiring the
maximum degree of protection against
inadvertent flooding of the sprinkler
system piping.
The DV-3 Electric/Pneumatic Double
Interlock Preaction System utilizes a
Model DV-3 Automatic Resetting Del-
uge Valve and a Model CV-2 Swing
Check Valve, with releasing trim con-
sisting of both a Solenoid Valve and a
Dry Pilot Actuator in a series configu-
ration. The Swing Check Valve isolates
the Deluge Valve from the system air
pressure that holds the Dry Pilot Ac-
tuator closed. The Solenoid Valve re-
mains closed until it is electrically en-
ergized by a deluge valve releasing
panel (automatic control unit) that is
operated by either a fire detection de-
vice or manual pull station.
In order for the Double Interlock Pre-
action System to automatically actu-
ate, two independent events must oc-
cur. The deluge valve releasing panel
must operate and open the Solenoid
Valve upon automatic operation of the
electric fire detection initiating circuit
or manual operation of the electric-
manual pull initiating circuit, and the
sprinkler system piping most lose air
pressure due to operation of one or
more sprinklers.
The Double Interlock Preaction Sys-
tem will automatically actuate only
when both the Dry Pilot Actuator and
the Solenoid Valve are open at the
same time. Accidental opening of just
the Dry Pilot Actuator (for example: a
lift truck accidentally dislodges a sprin-
kler), or just energizing the Solenoid
Valve (for example: an accidental op-
eration of an electric pull station), will
only cause an alarm, and will not actu-
ate the system or flood the sprinkler
system piping.
WARNING
The Model DV-3 Electric/Pneumatic
Double Interlock Preaction System de-
scribed herein must be installed and
maintained in compliance with this
document, as well as with the applica-
ble standards of the National Fire Pro-
tection Association, in addition to the
standards of any other authorities hav-
ing jurisdiction. Failure to do so may
impair the performance of the re-
lated devices.
The owner is responsible for maintain-
ing their fire protection system and de-
vices in proper operating condition.
The installing contractor or manufac-
turer should be contacted with any
questions.
Page2of10 TFP1462
FIGURE 2
INSTALLATION CONFIGURATION AND CLEARANCE
OBSOLETE

Technical
Data
Approvals
UL and C-UL Listed as Double Inter-
lock Type Water Control Valves. FM
Approved as Refrigerated Area Sys-
tems for use in refrigerated rooms or
buildings.
Deluge Valve
Model DV-3.
Riser Check Valve
Model CV-2.
Working Pressure Range
20 to 175 psi (1,4 to 12,1 bar).
System Design Considerations
The automatic sprinklers, as well as
the deluge valve releasing panel (auto-
matic control unit), fire detection de-
vices, manual pull stations, and signal-
ing devices, which are utilized with the
Electric/Pneumatic Double Interlock
Preaction System must be UL Listed,
ULC Listed, C-UL Listed, or FM Ap-
proved, as applicable.
Because a double interlock preaction
system requires time for a drop in sys-
tem air pressure to occur (concurrently
with the response time for the separate
fire detection system), before it will
allow water to enter the system piping,
this system has characteristics similar
to a dry pipe sprinkler system. There-
fore, the system design considerations
for a dry pipe system are normally
applied to a double interlock preaction
system — including a 30% increase in
design area and prohibition of gridded
system piping.
The deluge valve, swing check valve,
and all interconnecting piping must be
located in a readily visible and acces-
sible location and in an area which can
be maintained at a minimum tempera-
ture of 40F/4C.
NOTE
Heat tracing is not permitted for the
deluge valve, swing check valve, or
any of the interconnecting piping. Heat
tracing can promote the formation of
hardened mineral deposits which can
prevent system operation. Heat trac-
ing can also result in damage to the
DV-3 Deluge Valve Diaphragm As-
sembly.
In planning the installation, considera-
tion must also be given to the disposal
of the large quantities of water which
may be associated with draining the
system or performing a flow test.
Installation configuration and clear-
ance dimensions are given in Figure 2.
The grooved connections of the DV-3,
as well as the CV-2 Swing Check Valve
are cut in accordance with standard
groove specifications for steel pipe,
and they are suitable for use with
grooved end pipe couplings that are
listed or approved for fire protection
service.
Page 3 of 10
TFP1462
GRAPHS A-1 and A-2
NOMINAL PRESSURE LOSS VERSUS FLOW
FOR THE MODEL DV-3 DOUBLE INTERLOCK PREACTION SYSTEM
(DELUGE VALVE, ELBOW, AND CHECK VALVE COMBINATION)
GRAPH B
DOUBLE INTERLOCK PREACTION SYSTEM
AIR PRESSURE REQUIREMENTS
WATER
SU
PPLY PRE
SSU
RE IN P
S
I
AIR PRESSURE IN PSI
20 17540 60 80 100 120 140 160
30
20
10
0
40
MINIMUM SYSTEM AIR PRESSURE
RANGE OF ACTUATOR OPENING PRESSURE
OBSOLETE

Page4of10 TFP1462
FIGURE3—PART1of2
2-1/2 Inch (DN65) DOUBLE INTERLOCK PREACTION TRIM (See Page 5 for Bill of Materials)
OBSOLETE

In order to readily perform the System
Inspection Procedure described in the
Care and Maintenance section, it is
recommended that a System Shut-Off
Valve be installed above the Model
CV-2 Swing Check Valve, as shown in
Figure 1. The System Shut-Off Valve
should be a listed or approved (as ap-
propriate) indicating valve with a su-
pervisory switch to monitor the nor-
mally open position.
System Air Pressure Requirements
Graph B shows the minimum Elec-
tric/Pneumatic Double Interlock Pre-
action System air pressure require-
ments as a function of the water supply
pressure. Use of an automatic air or
nitrogen device is recommended and
may be required by the Authority Hav-
ing Jurisdiction.
NOTE
The dew point of the air or nitrogen
must be maintained below the lowest
ambient temperature to which the
Double Interlock Preaction System
piping will be exposed, or as required
by the Authority Having Jurisdiction.
Introduction of moisture into the sys-
tem piping that is exposed to freezing
temperatures can create ice build up
which could prevent proper operation
of the system.
Friction Loss
The nominal pressure losses versus
flow rate for the 2-1/2 inch (DN65)
combination of the Model DV-3 Deluge
Valve, Grooved End Elbow, and Model
CV-2 Swing Check Valve are shown in
Graphs A-1 and A-2.
The approximate friction losses, based
on the Hazen and Williams formula
and expressed in equivalent length of
Schedule 40 pipe, with C = 100 is 13.7
feet and with C = 120 is 19.2 feet. The
equivalent length of pipe has been cal-
culated on the basis of the flow rates
typically used with a 2-1/2 inch (DN65)
system.
Electric/Pneumatic Double Inter-
lock Preaction Trim
The DV-3 Electric/Pneumatic Double
Interlock Trim is illustrated in Figure 3.
The nipples utilized in the trim arrange-
ment are Schedule 40 steel per ASTM
A53 or A135 and they are threaded per
ANSI Standard B1.20.1. Fittings are
either malleable iron per ANSI B16.3
or cast iron per ANSI B16.4.
NOTE
Do not increase the length of the nipple
between the Solenoid Valve and the
Dry Pilot Actuator or the nipple above
the Dry Pilot Actuator. Increasing
either of these two nipple lengths may
impair operation of the system.
Operation
As indicated in the General Descrip-
tion section, two independent events
resulting in opening of both the Dry
Pilot Actuator and the Solenoid Valve
must occur to actuate the Model DV-3
Electric/Pneumatic Double Interlock
Preaction System.
When the Double Interlock Preaction
System is set for service, the dia-
phragm chamber of the Model DV-3
Deluge Valve is pressurized through
the diaphragm chamber supply con-
nection. The Model DV-3 Deluge Valve
is a differential type valve which de-
pends upon the water pressure in the
diaphragm chamber to hold the center
valve assembly closed against the
water supply pressure. The Model
DV-3 Deluge Valve has a nominal trip
ratio of 2.5 to 1, i.e., the valve operates
when pressure in the diaphragm
chamber is reduced to approximately
two-fifths of the water supply pressure.
The Model DV-3 Automatic Resetting
Deluge Valve is described in TFP1350.
Opening of both the Dry Pilot Actuator
and the Solenoid Valve (16 & 17 - Fig.
3), or operating the Manual Control
Station (4 - Fig. 3) will release water
from the DV-3 diaphragm chamber
faster than it can be replenished
through the 1/8 inch (3,2 mm) diameter
orifice of the Priming Supply Restric-
tion (9 - Fig. 3). A rapid pressure drop
then results in the diaphragm chamber
and the differential between the dia-
phragm chamber and the force differ-
ential holding the center valve assem-
bly down is eliminated. The water
supply pressure then forces the center
valve assembly open, permitting a flow
of water to the Double Interlock Preac-
tion System piping. Water flowing into
the system also flows to the Waterflow
Pressure Alarm Switch (Fig. 3), which
actuates the system alarm signal.
Also, water flowing into the system is
directed to the Model C-1 Pressure
Relief Valve (20 - Fig. C) which, upon
operation, constantly vents the DV-3
diaphragm chamber so as to maintain
the DV-3 Valve in the open (operated)
position.
The Double Interlock Preaction Sys-
tem will automatically operate only
when both the Solenoid Valve and the
Dry Pilot Actuator are open at the
same time. Opening of just the Dry
Pilot Actuator (e.g., a lift truck acciden-
tally dislodges a sprinkler) or just en-
ergizing the Solenoid Valve (e.g., an
accidental operation of an electric pull
station) will only cause an alarm, via
the low air pressure alarm switch or the
deluge valve releasing panel, as appli-
cable, to indicate that the system re-
Page 5 of 10
TFP1462
FIGURE 3 — PART 2 of 2
2-1/2 Inch (DN65)
DOUBLE INTERLOCK
PREACTION TRIM
(See Page 4 for Illustration)
1/4" Tubing Connector CH1..
1/2" Plug 2............. CH
46-005-1-0023 1/4" Gauge Test Valve 2..
4 Model MC-1 Manual
Control Station 52-289-2-0011.........
10 Model AD-1 Automatic
Drain Valve 52-793-2-0041...........
29
1/2" Tubing Connector CH3..
13
92-211-1-003
92-343-1-007
22
Drip Funnel Bracket
Drip Funnel
1
1...........
....
26
92-032-1-0023/32"VentFitting .......1
28
8 52-353-1-0051.........1/2" Y-Strainer
7
92-322-1-002
1/2" Spring Loaded
1CheckValve ..........
46-050-1-0041/2" Ball Valve 2.........15
11
3/4" Plug 1............. CH
1/4" Plug 2............. CH
1/2" x 30" Tubing CH3.......
NO.
1
QTY.DESCRIPTION P/N
92-343-1-005
300 psi/ 2000 kPa
2Water Pressure Gauge . .
18
32
92-211-1-005
Drip Funnel Connector 1
..
12
20
92-020-1-009
9 Priming Supply
1Restriction ............
30
31
2
92-343-1-012
250 psi/ 1750 kPa
1Air Pressure Gauge . . . . .
19
16 Model DP-1 Dry Pilot
Actuator 52-280-1-0011..............
21 1/4" Pressure Relief
Valve 92-343-1-0201................
6 1/2" Swing Check Valve 46-049-1-0042.
46-047-1-00414 1/2" Globe Valve 1.......
52-287-1-02424 VDC Solenoid Valve 1..17
Waterflow Pressure
Alarm Switch (PS10-2A) 25711.
Low Air Pressure
Alarm Switch (PS40-1A) 25721.
92-343-1-023
Pressure Operated Relief
1Valve,PORV ..........
1-1/4" Angle Valve
2-1/2" Grooved End 90°
Elbow, Figure 510
2-1/2" Rigid Grooved End
Coupling, Figure 772
1/2" x 1/4" x 1/2" Tee
System Label
..............
39
25
24
23
5
38 1/2" Tee
3.... CH
N/A1..........
51025S
77225ASC
46-048-1-007
CH
1
2
......
....
2......
10
1/4" x 30" Tubing CH2.......27
1/2" x Close Nipple
1/4" x 3" Nipple
1/2" 90° Elbow
............
..............
1/2" x 1/4" Reducing
43
42
35
34
33
1/2" Union
Bushing
2
2
11
7
1
........
.....
.........
CH
CH
CH
CH
CH
36 1/2" 45° Elbow 1......... CH
................
1/2" x 1/4" Reducing37
Elbow CH1
1/2" x 1/2" x 3/4" Tee40 1.... CH
1-1/4" x 1/2" x 1-1/4" Tee41 1.CH
1/2" x 1-1/2" Nipple44 30..... CH
45 1/2" x 2" Nipple 1 CH........
46 1/2" x 2" Nipple 3 CH........
47 1/2" x 3-1/2" Nipple 1 CH.....
48 1/2" x 3-1/2" Nipple 1 CH.....
49 1/2" x 4-1/2" Nipple 3 CH.....
50 1/2" x 7-1/2" Nipple 1 CH.....
51 1/2" x 8-1/2" Nipple 1 CH.....
52 1/2" x 10-1/2" Nipple 1 CH....
53 1/2" x 11-1/2" Nipple 1 CH....
54 1-1/4" x Close Nipple 2 CH....
55 1-1/4" x 3" Nipple 1 CH.......
All Fittings and Nipples are galvanized
(Standard Order).
NOTE:
OBSOLETE

quires attention. The system will not
actuate or flood the sprinkler system
piping.
Installation
The deluge valve, swing check valve,
and all interconnecting piping must be
installed in a readily visible and acces-
sible location and in an area which can
be maintained at a minimum tempera-
ture of 40F/4C.
NOTE
Heat tracing is not permitted for the
deluge valve, swing check valve, or
any of the interconnecting piping. Heat
tracing will promote the formation of
hardened mineral deposits which can
prevent valve operation. Heat tracing
can also result in damage to the DV-3
Deluge Valve Diaphragm Assembly.
The 2-1/2 inch (DN65) Electric/Pneu-
matic Double Interlock Preaction Sys-
tems must be installed in accordance
with the following instructions. Proper
operation of the Double Interlock Pre-
action System depends upon it being
installed in accordance with the in-
structions given below. Failure to follow
these instructions may prevent the de-
vices from functioning properly as well
as void listings, approvals, and the
manufacturer’s warranties.
Step 1. All pipe thread connections
must be free of scale and burrs before
installation. Use pipe thread sealant
sparingly on male pipe threads only.
Step 2. The DV-3 Deluge Valve must
be installed vertically as shown in Fig-
ures 2 and 3.
Step 3. The Double Interlock Preaction
Trim must be installed in accordance
with Figure 3.
The grooved end elbow fitting and cou-
plings are to be installed in accordance
with standard installation practices.
Care must be taken to make sure that
check valves, globe valves, etc. are
installed with the flow arrows in the
proper direction.
Drain tubing to the Drip Funnel must
be installed with smooth bends that will
not restrict flow.
Step 4. Attach the Model DV-3 Double
Interlock Label (25 - Fig. 3) to the 2
inch high x 4 inch (50 x 200 mm) wide
nameplate mounting pad on the Hand-
hole Cover of the CV-2 Swing Check
Valve. Place the Label over the manu-
facturer’s logo nameplate, if one is lo-
catedonthepad.
Step 5. The Diaphragm Chamber Sup-
ply Connection (Fig. 3)must be con-
nected to the water supply side of the
System Main Control Valve to facilitate
setting of the DV-3 Deluge Valve.
Step 6. Connect the Air Supply Con-
nection to an air or nitrogen supply.
Use of an automatic air or nitrogen
maintenance device is recommended
and may be required by the Authority
Having Jurisdiction. Refer to Graph B
for Double Interlock Preaction System
air pressure requirements.
An air dryer, when specified, is to be
installed as required by the Authority
Having Jurisdiction.
Step 7. The Low Air Pressure Alarm
Switch (Fig. 3) is to be adjusted to
operate on falling pressure at approxi-
mately 6 psi (0,4 bar) below the mini-
mum Double Interlock Dry System air
pressure requirement shown on Graph
B.
Step 8. The Pressure Relief Valve (21
- Fig. 3) is factory set to relieve at a
pressure of approximately 45 psi (3,1
bar), which can typically be used for a
maximum system pressure of 40 psi
(2,8 bar). The Pressure Relief Valve
may be reset; however, it must be be
reset to relieve at a pressure which is
in accordance with the requirements of
the Authority Having Jurisdiction.
To reset the Pressure Relief Valve, first
loosen the jam nut and then adjust the
cap accordingly — clockwise for a
higher pressure setting or counter-
clockwise for a lower pressure setting.
Page6of10 TFP1462
FIGURE 4
PRESSURE OPERATED RELIEF VALVE
PORV Operation
Area “A” of the PORV is connected
directly to the top of the DV-3 Dia-
phragm Chamber. In the set position,
water pressure is supplied through
the Screen (16) and the orifice in the
Diaphragm (14) to both sides of the
Diaphragm, Areas “A” and “B”.
Therefore, because of the are differ-
ential and the force exerted by the
Spring (9), the Clapper (17) is held
closed.
When the DV-3 is tripped, water
pressure from the system side of the
DV-3 is directed towards the PORV
to Area “D”. This pressure depresses
Diaphragm (3) which in turn de-
presses the Valve (6, 7). Opening of
the Valve releases pressure from
Area “B” into Area “C” where it is then
released to atmosphere.
With Area “B” reduced in pressure to
below that in Area “A”, the Clapper
(17) lifts off the Seat (20) and allows
a constant vent of the DV-3 Dia-
phragm Chamber into Area “E”
where it is then released to atmos-
phere.
OBSOLETE

After verifying the desired pressure
setting, tighten the jam nut.
Step 9. Suitable provision must be
made for disposal of drain water.
Drainage water must be directed such
that it will not cause damage or result
in dangerous conditions.
Step 10. All conduit and electrical con-
nections are to be made in accordance
with the requirements of the Authority
Having Jurisdiction and/or the National
Electrical Code.
In Case Of
Alarm
If a fire condition exist: Notify the
local fire service and follow the plan
prescribed by the Authority Having Ju-
risdiction.
If a fire condition does not exist:
Step 1. Close the Diaphragm Cham-
ber Supply Control Valve (Fig. 3) lo-
cated in the Diaphragm Chamber Sup-
ply Connections.
Step 2. Close the system’s Main Con-
trol Valve (Fig. 1).
Step 3. OpentheDV-3MainDrain
Valve (Fig. 3).
Step 4. If the system has been
flooded, open the CV-2 System Main
Drain Valve (Fig. 3), Inspector’s Test
Connection, and all auxiliary drains in
the system piping. Check to see that
the drainage water will not cause dam-
age or result in dangerous conditions.
Step 5. Notify the alarm monitoring
stations (if applicable) as well as the
Authority Having Jurisdiction that there
is an impairment to the fire protection
system.
Step 6. Determine if the false alarm
was caused by the electric fire detec-
tion system or a low air pressure con-
dition and then promptly correct the
impairment and return the fire protec-
tion system to service, as soon as pos-
sible.
System
Setting
Procedure
The Double Interlock Preaction Sys-
tem must be manually reset, and it
should be restored to service as soon
as possible; however, as the system is
being reset, the DV-3 Deluge Valve
and pressure Operated Relief Valve
will automatically reset.
NOTES
It is recommended that the individual
responsible for placing the Double In-
terlock Preaction System in service
develop a working understanding of
the system in general, prior to placing
it in operation. These instructions, as
well as individual instructions for the
deluge valve, swing check valve, dry
pilot actuator, solenoid valve, manual
control station, switches, and pressure
maintenance device should be re-
viewed.
After placing a fire protection system
in service, notify the proper authorities
and advise those responsible for moni-
toring proprietary and/or central sta-
tion alarms.
The procedure is as follows:
Step 1. Close the Diaphragm Cham-
ber Supply Control Valve (Fig. 3).
Step 2. Close the Double Interlock
System Main Control Valve (Fig.1) and
the Air Supply Control Valve (Fig. 3).
Step 3. Open the System Main Drain
Valve at the side of the CV-2 Check
Valve (Fig. 3), Main Drain Valve adja-
cent to the DV-3 Deluge Valve (Fig. 3),
Inspector’s Test Connection, and all
auxiliary drains in the system piping.
Check to see that the drainage water
will not cause damage or result in dan-
gerous conditions.
NOTE
Do not open the Inspector’s Test Con-
nection and auxiliary drains if resetting
after a system test; otherwise, system
air pressure will be relieved unneces-
sarily.
Step 4. Operate (open) the Manual
Control Station (Fig. 3) to assure that
the DV-3 Valve Diaphragm Chamber is
vented.
Step 5. Inspect for and clear all ice
plugs, where system piping has been
exposed to freezing conditions and
when there has been a flow of water
into the system.
Step 6. Close the System Main Drain
Valve at the side of the CV-2 Check
Valve, Inspector’s Test Connection,
and all auxiliary drains in the system
piping. Leave the Main Drain Valve ad-
jacent to the DV-3 Deluge Valve open.
Step 7. Depress the plunger of the
Automatic Drain Valve (Fig. 3), to verify
that it is open and that the DV-3 Valve
has been completely drained.
Step 8. Clean out the Strainer (Fig. 3)
in the connection to the DV-3 Valve
Diaphragm Chamber.
Step 9. Close the Manual Control Sta-
tion (Fig. 3) by pushing the operating
lever up. Do not close the hinged cover
at this time.
Step 10. Replace all damaged or op-
erated sprinklers. Replacement sprin-
klers must be of the same type and
temperature rating as those which op-
erated.
NOTE
In order to prevent the possibility of a
subsequent operation of an over-
heated solder type sprinkler, any sol-
der type sprinklers which were possi-
bly exposed to a temperature greater
than their maximum rated ambient
must also be replaced.
Step 11. Service the air dryer, if appli-
cable, in accordance with the manu-
facturer’s instructions.
Step 12. Open (energize) the Solenoid
Valve by manually operating the del-
uge valve releasing panel.
Step 13. Open the Diaphragm Cham-
ber Supply Control Valve (Fig. 3) and
allow water to discharge from the Dry
Pilot Actuator. Close the Diaphragm
Chamber Supply Control Valve when
air is no longer present in the dis-
charge from the Dry Pilot Actuator.
Step 14. If resetting after a test, fully
open the System Shut-Off Valve (Fig.
1), if applicable.
Step 15. Open the Air Supply Control
Valve (Fig. 3) and pressurize the sprin-
kler system in accordance with Graph
B.
Step 16. Return the Solenoid Valve to
its normally closed position by reset-
ting the deluge valve releasing panel.
Step 17. Fully open the Diaphragm
Chamber Supply Valve (Fig. 3) and
allow time for full pressure to build up
in the Diaphragm Chamber of the DV-3
Valve
Step 18. Operate (open) the Manual
Control Station (Fig. 3). SLOWLY close
the operating lever, by pushing it up,
after air is no longer present in the
discharge from the drain tubing. Close
the hinged cover and insert a new
break rod (PSN 92-289-1-008) in the
Page 7 of 10
TFP1462
OBSOLETE

small hole through the top of the en-
closing box
Step 19. Inspect the drain connections
from the Dry Pilot Actuator, Manual
Control Station, and Pressure Oper-
ated Relief Valve for leaks. Leaks, if
any, must be corrected before the sys-
tem is restored to service.
Step 20. Slowly open the Main Control
Valve (Fig. 1). Close the Main Drain
Valve adjacent to the DV-3 Deluge
Valve as soon as water discharges
from the drain connection. Observe the
Automatic Drain Valve for leaks. If
there are leaks, either the Center Valve
is not properly seated and the Double
Interlock Preaction System must be
reset, or there is internal leakage past
the Center Valve Facing or Diaphragm.
Determine/correct the cause of the
leakage problem. If there are no leaks,
fully open the Main Control Valve (Fig.
1).
Step 21. Verify that the deluge valve
releasing panel is returned to a normal
standby condition.
Step 22. It is recommended that the
Main Control Valve and the System
Shut-Off Valve (if applicable) be locked
in the full open position if they are not
monitored by supervisory switches.
NOTE
After placing a fire protection system
in service, notify the proper authorities
and advise those responsible .for
monitoring proprietary and/or central
station alarms.
The Double Interlock Preaction Sys-
tem is now set for service.
Care and
Maintenance
The following inspection must be per-
formed as indicated, in addition to any
specific requirements of the NFPA,
and any impairment must be immedi-
ately corrected. It is recommended
that the System Inspection Procedure
be performed at least semi-annually.
The owner is responsible for the in-
spection, testing, and maintenance of
their fire protection system and de-
vices in compliance with this docu-
ment, as well as with the applicable
standards of the National Fire Protec-
tion Association (e.g., NFPA 25), in
addition to the standards of any
authority having jurisdiction. The in-
stalling contractor or product manufac-
turer should be contacted relative to
any questions.
It is recommended that automatic
sprinkler systems be inspected,
tested, and maintained by a qualified
Inspection Service in accordance with
local requirements and/or national
codes.
NOTES
It is recommended that the individuals
responsible for the care and mainte-
nance of the Double Interlock Preac-
tion System develop a working under-
standing of the system, in general,
prior to performing inspection and/or
maintenance procedures. These in-
structions, as well as individual in-
structions for the deluge valve, swing
check valve, dry pilot actuator , sole-
noid valve, manual control station,
switches, and pressure maintenance
device should be reviewed.
The following procedures pertain to
the automatic control valve portion of
the Double Interlock Preaction Sys-
tem. Refer to the manufacturer’s in-
structions and NFPA 25 for care and
maintenance procedures for all other
devices (e.g., electric detection, main
control and system shut-off valves, su-
pervisory devices, sprinklers, etc.).
Before performing the System Inspec-
tion Procedure, which will result in op-
eration of alarms, notify the proper
authorities and all personnel who may
be affected.
Before closing a fire protection system
main control valve for maintenance
work on the fire protection system
which it controls, permission to shut
down the affected fire protection sys-
tem must be obtained from the proper
authorities and all personnel who may
be affected by this action must be no-
tified.
System Inspection Procedure
Step 1. Close the Main Control Valve
(Fig. 1) and then open the Main Drain
Valve adjacent to the DV-3 Deluge
valve (Fig. 3).
Step 2. Open (energize) the Solenoid
Valve by manually operating the auto-
matic control unit. Verify that there is
no leakage out the Dry Pilot Actuator
drain. Also, verify full operation of the
deluge valve releasing panel and its
associated alarms.
NOTES
During this procedure, the Solenoid
Valve is opened; however, the Dry Pi-
lot Actuator should remain closed and
the DV-3 Deluge Valve Diaphragm
Chamber should remain pressurized.
This procedure is used to verify that
the DV-3 Deluge Valve will remain set
if the electric detection system oper-
ates but the sprinkler system remains
in its normally pressurized condition.
Step 3. Open the Inspector’s Test Con-
nection but be prepared to close it im-
mediately after verifying that the Low
Pressure Alarm Switch (Fig. 3) and its
associated alarms operate properly.
The Low Pressure Alarm Switch
should operate at the previously estab-
lished pressure (refer to Installation
section, Step 7).
Close the Inspector’s Test Connection.
Step 4. Close the Diaphragm Cham-
ber Supply Control Valve (Fig. 3).
Step 5. Close the System Shut-off
Valve (Fig. 1) after the system air pres-
sure has been restored to normal.
Step 6. Manually restore the electric
fire detection system to a normal con-
dition in accordance with the manufac-
turer’s instructions.The Solenoid Valve
will then be de-energized and returned
to its normally closed position.
Step 7. Open the Diaphragm Chamber
Supply Control Valve.
Step 8. Open the Main Control Valve
(Fig. 1) one turn beyond the position at
which water just begins to flow from
the Main Drain Valve adjacent to the
DV-3 Deluge Valve.
Step 9. Close the Main Drain Valve
adjacent to the DV-3 Deluge valve (Fig.
3).
Step 10. Close the Air Supply Control
Valve (Fig. 3).
Step 11. Open the Dry Pilot Actuator
by partially opening the System Main
Drain Valve (Fig. 3) to relieve air pres-
sure at the inlet to the Actuator. Verify
that there is no leakage out the Dry
Pilot Actuator.
Page8of10 TFP1462
OBSOLETE

NOTES
During this procedure, the Dry Pilot
Actuator is opened; however, the So-
lenoid Valve should remain closed and
the DV-3 Deluge Valve Diaphragm
Chamber should remain pressurized.
This procedure is used to verify that
the DV-3 Deluge Valve will remain set
if the Dry Pilot Actuator operates due
to loss of system air pressure and the
electric detection system remains in a
normal condition.
Step 12. Open (energize) the Solenoid
Valve by operating the deluge valve
releasing panel, and verify the follow-
ing:
•Verify that the DV-3 Deluge Valve
operates, as is indicated by a dis-
charge of water from the System
Main Drain Valve and the Automatic
Drain Valve. The Automatic Drain
Valve may or may not close depend-
ing on the amount of flow past the
partially open Main Control Valve.
•Verify that the Pressure Operated
Relief Valve has operated as is indi-
cated by water discharging into the
Drip Funnel from both the 1/4 and
1/2 drain tubes connected to the
Pressure Operated Relief Valve.
•Verify that the Waterflow Pressure
Alarm Switch (Fig. 3) and its associ-
ated alarms properly operate.
•Verify that the Water Motor Alarm, if
applicable, properly operates.
NOTE
This procedure simulates opening of
both the Dry Pilot Actuator (loss of
system air pressure) and Solenoid
Valve (operation of the automatic con-
trol unit) to verify automatic system
operation.
Step 13. Reset the Double Interlock
Dry System in accordance with the
Resetting Procedure section.
Pressure Operated Relief Valve
If water does not discharge from both
the 1/4 and 1/2 inch tubes connected
to the Pressure Operated Relief Valve
(PORV) during Step 12 of the System
Inspection Procedure, the PORV is to
be disassembled, cleaned, and in-
spected as follows:
Step 1. Take the sprinkler system out
of service by using Steps 1 through 4
of the Resetting Procedure.
Step 2. Remove the PORV from the
Double Interlock Preaction Trim.
Step 3. Refer to Figure D, and then
completely disassemble the PORV,
with the exception of the Valve Core
and Body (6, 7). A special tool is re-
quired to separate the Valve Core from
the Valve Body; therefore, do not at-
tempttoseparatethesetwoparts.
Step 4. Clean all parts, and replace
worn or damaged parts as necessary.
Step 5. Reassemble the PORV in ac-
cordance with Figure 4 and then rein-
stall the PORV into the Double Inter-
lock Preaction Trim.
Step 6. Place the system into service
in accordance with the Resetting Pro-
cedure section and then perform the
System Inspection Procedure to verify
proper operation of the system, as well
as the Pressure Operated Relief Valve.
Limited
Warranty
Products manufactured by Tyco Fire
Products are warranted solely to the
original Buyer for ten (10) years
against defects in material and work-
manship when paid for and properly
installed and maintained under normal
use and service. This warranty will ex-
pire ten (10) years from date of ship-
ment by Tyco Fire Products. No war-
ranty is given for products or
components manufactured by compa-
nies not affiliated by ownership with
Tyco Fire Products or for products and
components which have been subject
to misuse, improper installation, corro-
sion, or which have not been installed,
maintained, modified or repaired in ac-
cordance with applicable Standards of
the National Fire Protection Associa-
tion, and/or the standards of any other
Authorities Having Jurisdiction. Mate-
rials found by Tyco Fire Products to be
defective shall be either repaired or
replaced, at Tyco Fire Products’ sole
option. Tyco Fire Products neither as-
sumes, nor authorizes any person to
assume for it, any other obligation in
connection with the sale of products or
parts of products. Tyco Fire Products
shall not be responsible for sprinkler
system design errors or inaccurate or
incomplete information supplied by
Buyer or Buyer’s representatives.
IN NO EVENT SHALL TYCO FIRE
PRODUCTS BE LIABLE, IN CON-
TRACT, TORT, STRICT LIABILITY OR
UNDER ANY OTHER LEGAL THE-
ORY, FOR INCIDENTAL, INDIRECT,
SPECIAL OR CONSEQUENTIAL
DAMAGES, INCLUDING BUT NOT
LIMITED TO LABOR CHARGES, RE-
GARDLESS OF WHETHER TYCO
FIRE PRODUCTS WAS INFORMED
ABOUT THE POSSIBILITY OF SUCH
DAMAGES,ANDINNOEVENT
SHALL TYCO FIRE PRODUCTS’ LI-
ABILITY EXCEED AN AMOUNT
EQUAL TO THE SALES PRICE.
THE FOREGOING WARRANTY IS
MADE IN LIEU OF ANY AND ALL
OTHER WARRANTIES EXPRESS OR
IMPLIED, INCLUDING WARRANTIES
OF MERCHANTABILITY AND FIT-
NESS FOR A PARTICULAR PUR-
POSE.
Page 9 of 10
TFP1462
OBSOLETE

Ordering
Procedure
With reference to Table A, the following
items must be ordered separately:
•Deluge Valve
•Check Valve
•Preaction Trim
•Automatic Pressure Maintenance
Device
Replacement Trim Parts:
Specify: (description) for use with
Model DV-3 Deluge Valve, P/N (see
Figure 3).
Page 10 of 10 TFP1462
TYCO FIRE PRODUCTS, 451 North Cannon Avenue, Lansdale, Pennsylvania 19446
DELUGE VALVE
P/N’s are for American Standard Groove x Groove Connections, and Threaded Ports, For
other configurations refer to Technical Data Sheet TFP1350. Specify: 2-1/2 inch, Model
DV-3 groove x groove Deluge Valve, P/N (specify).
2-1/2 Inch . . . . . . . . . . . . . . . . . . . . . . . . . . . . . . . . . . . . . . . . . . . . . . . . . . . . . . . . . . . P/N 52-445-1-002
CHECK VALVE
P/N’s are for American Standard Grooved Connections. For other configurations refer to
Technical Data Sheet TFP1560 for the Model CV-2 Check Valve.Specify: 2-1/2 inch, Model
CV-2 groove x groove Check Valve, P/N (specify).
2-1/2 Inch . . . . . . . . . . . . . . . . . . . . . . . . . . . . . . . . . . . . . . . . . . . . . . . . . . . . . . . . . . . P/N 52-520-1-110
ELECTRIC/PNEUMATIC DOUBLE INTERLOCK PREACTION TRIM
Specify: (specify finish — galvanized is standard) Preaction Trim for Model DV-3 Deluge
Valves, P/N (specify).
Galvanized . . . . . . . . . . . . . . . . . . . . . . . . . . . . . . . . . . . . . . . . . . . . . . . . . . . . . . . . . . P/N 52-445-2-100
Black. . . . . . . . . . . . . . . . . . . . . . . . . . . . . . . . . . . . . . . . . . . . . . . . . . . . . . . . . . . . . . . P/N 52-445-1-100
AUTOMATIC PRESSURE MAINTENANCE DEVICE
A device capable of maintaining a nominal system air or nitrogen pressure in accordance
with Graph B must be separately ordered. Specify: (Specify model and description), P/N
(specify).
Model AMD-1 Air Maintenance Device — Pressure Reducing Type (TFP1221) . . P/N 52-324-2-002
Model AMD-2 Air Maintenance Device — Compressor Control Type (TFP1231) . . P/N 52-326-2-001
Model AMD-3 Nitrogen Maintenance Device (TFP1241) . . . . . . . . . . . . . . . . . . . . . P/N 52-328-2-001
TABLE A — ORDERING LIST
OBSOLETE
Other manuals for DV-3
1
Table of contents
Other Tyco Control Unit manuals
Popular Control Unit manuals by other brands
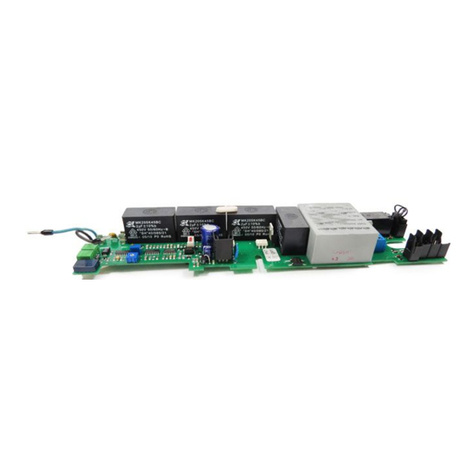
GEZE
GEZE Slimdrive SD Auxiliary installation instructions
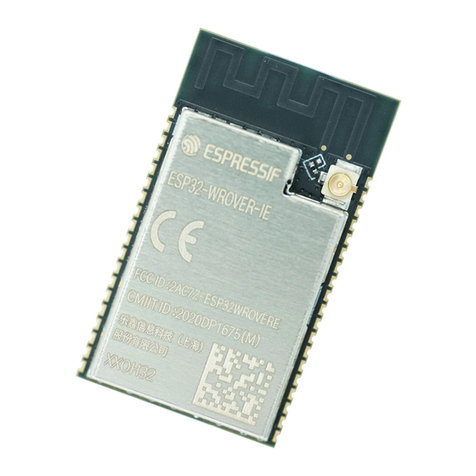
Espressif
Espressif PAN100 manual
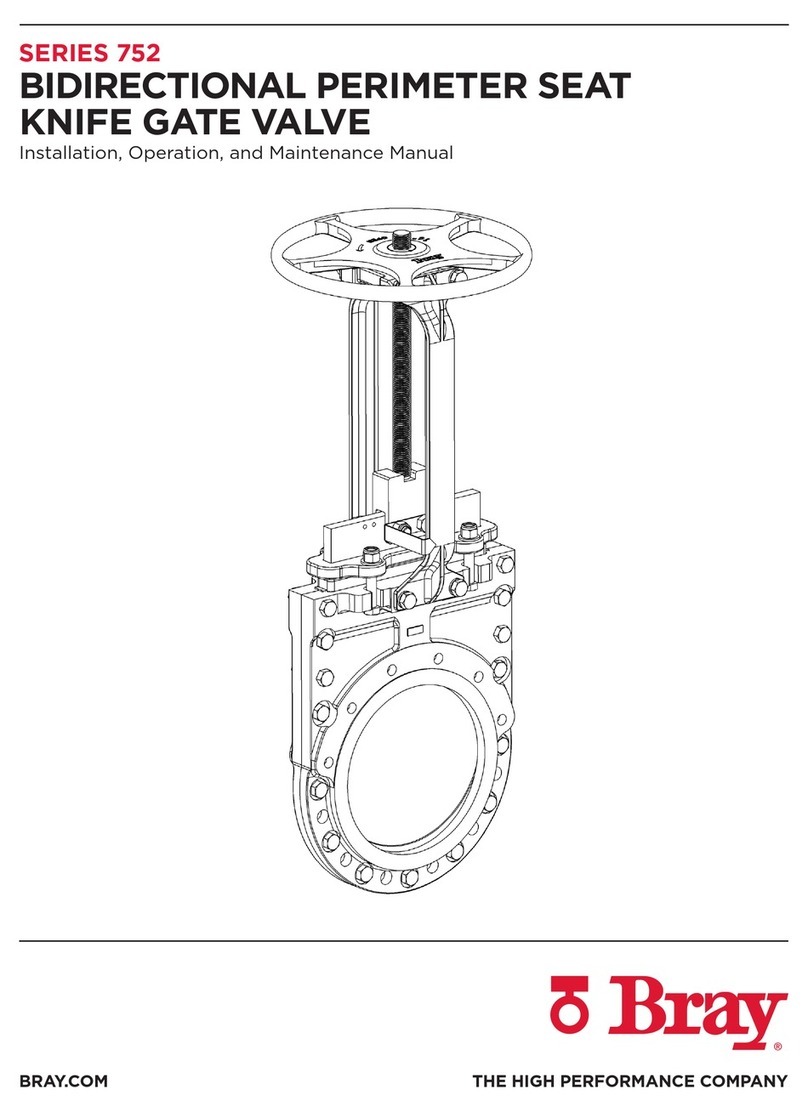
Bray
Bray 752 Series Installation, operation and maintenance manual
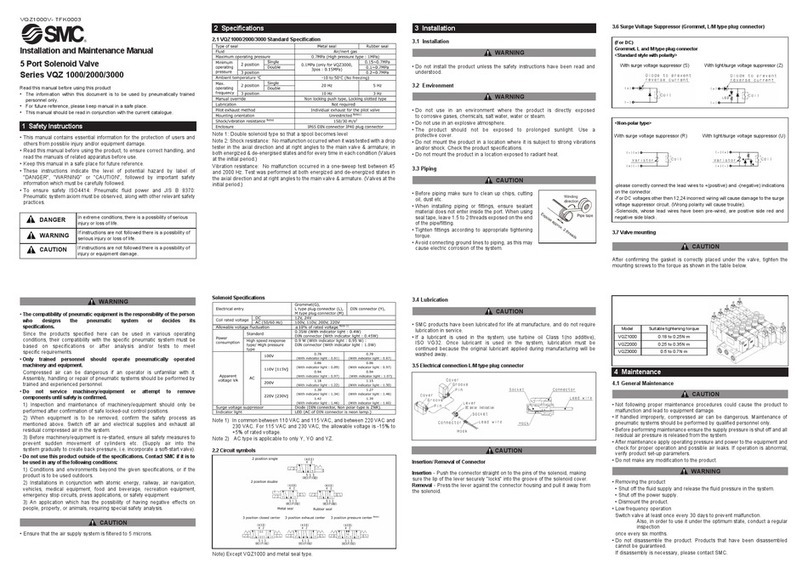
SMC Networks
SMC Networks VQZ 1000 Installation and maintenance manual

Eaton
Eaton Crouse-hinds series instruction sheet
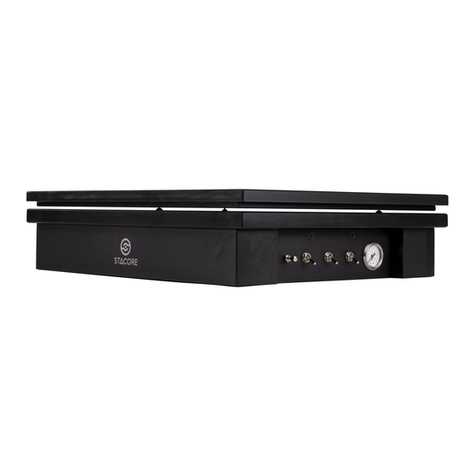
Stacore
Stacore ADVANCED user manual