Zapi ZAPIMOS HP 350A User manual

ZAPIMOSZAPIMOS
ZAPIMOSZAPIMOS
ZAPIMOS HPHP
HPHP
HP 350A350A
350A350A
350A
PUMP MOPUMP MO
PUMP MOPUMP MO
PUMP MOTT
TT
TOR CONTROR CONTR
OR CONTROR CONTR
OR CONTROLLEROLLER
OLLEROLLER
OLLER
COSTRUZIONE APPARECCHIATURE ELETTRONICHE - OLEODINAMICHE - INDUSTRIALICOSTRUZIONE APPARECCHIATURE ELETTRONICHE - OLEODINAMICHE - INDUSTRIALI
COSTRUZIONE APPARECCHIATURE ELETTRONICHE - OLEODINAMICHE - INDUSTRIALICOSTRUZIONE APPARECCHIATURE ELETTRONICHE - OLEODINAMICHE - INDUSTRIALI
COSTRUZIONE APPARECCHIATURE ELETTRONICHE - OLEODINAMICHE - INDUSTRIALI
42028 - POVIGLIO - (R.E.) - Via della Costituzione,32 - ITALIA
Tel. (0522) 960050 (r.a.) - Tlx. 530021 AINDRE I - Fax (0522) 960259
MENU

Pagina 2
INDEX
Legenda
1 General characteristics
1.1 Specifications
1.2 Adjustmenttools
1.2a Microswitches
1.2b Potentiometer
1.3 Features
1.4 Compensationprinciple
1.5 Protectionfeatures
1.6 Thermicconsiderations
1.7 General notes and precautions
2 InstallingtheH2P
Standard pump diagram with 2 speeds on the lifting lever
Standard pump diagram with 2 speeds on the lifting lever + field weakening
Standard pump diagram with pedal driven hydroguide and traction contactor
Standard pump diagram with lifting potentiometer
Standard pump diagram with lifting potentiometer + general contactor
Liftingpumpdiagram+hydroguide pump
Recommended spare parts
Mainteinance
MENU

Pagina 3
LegendLegend
LegendLegend
Legend
AV = Forward
IN = Backward
IND = Weakening
VMN = Negative motor voltage
MA = Forward speed microswitch
MI = Backward microswitch
MD = Descent microswitch
MS = Rise microswitch
NT = Contactor negative
MCL = Horn microswitch
MEF = Electric brake switch
CH = Key
MT = Handle microswitch
MUM = Dead man microswitch
DF = Brake diode
DV = Flywheel diode
RV = Speed reduction
1^V = 1st lift speed request
Pubblication n.: 550174
Edition: June 1993
MENU

Pagina 4
Voltages range A: 24V
range B: 36/40/48V
range C: 60/72/80V
range D: 96V
MaxCurrent 350 Amps
OperatingFrequency 18KHz
Externaltemperature range -30 ÷ 40°C
Minimum temperature reached by the chopper 85°C
Motors series and compound
Drop voltage at 150 Amps: Supply Voltage [V] Drop Voltage [mV]
24 300
36/40/48 590
60/72/80/96 910
Microprocessor logic unit:
Via consolle it is possible to set 2 different cofigurations:
1. 5 speed pump control chopper
2. 4 speed pump control chopper + driver of hydroguide contactor
1.2 Adjustment tools
1.2a Microswitches
The microswitches send a voltage signal when the desired speed request is made.
1.2b Potentiometer
In the 3-wire configuration, the CPOT (C1) useful input signal goes from 0V to 10V.
The resistive value of the potentiometer must be between 500 ohm and 10 kohm, as lower
values overload the power supply.
2-wire potentiometer (please request while ordering):
It is possible to use the potentiometer in the 2-wire configuration but you should state its
ohmic value since a resistor on the logic boars must be installed accordingly.
Correspondence between the voltage signal to pin C1 and motor voltage.
1. GENERAL CHARACTERISTICS
1.1 Specifications
MENU

Pagina 5
The procedure for automatic potentiometer signal acquisition is carried out from the console.
This makes it possible to adjust the minimum and maximum useful signal in the respective
directions.
The sequence of procedures is described in the programming console manual.
fig. 8a fig. 8b
The first graph (Fig. 8a) shows the correspondence of the motor voltage without having made
the acquisition, while the second graph (Fig. 8b) shows the same correspondence after signal
acquisition by the potentiometer.
The acquisition procedure is invalidated by the machine if the difference between the
maximum value and the minimum value is less than 2V.
This acquisition procedure makes it possible:
- to use “reversed” potentiometric signals, i.e. those which are carried from a high initial value
to a low final value.
- to use a normal potentiometer instead of one with central zero.
For the correct functioning of signal acquisition, it is absolutely necessary that the running
microswitches be activated by the same shaft that moves the potentiometer.
- 2-wire potentiometer (request while ordering)
It is possible to use a potentiometer with 2-wire configuration, in which case the resistive value
of the potentiometer desired must be indicated, as a resistance with the correct corresponding
value must be fitted in the logic unit.
MENU

Pagina 6
1.3 PERFORMANCEFEATURES1.3 PERFORMANCEFEATURES
1.3 PERFORMANCEFEATURES1.3 PERFORMANCEFEATURES
1.3 PERFORMANCEFEATURES
- Optimum sensitivity to low speeds.
- Self-diagnosis with indication of the type of anomaly by an optional LED.
- Configurable from the console (traction or lifting).
- Modification of parameters from the console.
- Internal hour-meter with values that can be displayed on the console.
- Memorisation of the last 5 alarms tripped, with relative hour-meter value and temperature
that can be displayed on the console.
- Console tester for real time checking of the main parameters such as inputs, motor voltage,
battery, etc.
- Absence of arc on the contactors
- Internal arc suppressor of the contactors coils.
- High motor and battery efficiency thanks to high frequency commutation.
- Priority is given to the highest speed.
1.4 COMPENSATION CONCEPT
By introducing the compensation the voltage power supply of the pump is linked to the load. This
is because the pump voltage is the sum of a fix part (socket - threshold) and a part that varies with
load (current). By acting on the compensation parameter it is possible to adjust the current weight,
so that we set a rule on how to vary the motor voltage as a function of the load. In this way the
whole amount of oil that circulates can produce work. Also the hydrolic circuit is indipendent
from the requested performance, therefore it can be cheaper (reduced jack and pipe cross-section,
no back pressure valve and no neck downs).
1.5 PROTECTIONFEATURES1.5 PROTECTIONFEATURES
1.5 PROTECTIONFEATURES1.5 PROTECTIONFEATURES
1.5 PROTECTIONFEATURES
--
--
-Battery inversions:Battery inversions:
Battery inversions:Battery inversions:
Battery inversions:
It is necessary to respect the connections indicated in the diagrams in order to avoid damage to
the power unit. In the lifting versions, a general contactor may be connected which is handled
by the logic against any polarity inversions.
The logic is intrinsically protected against polarity inversions.
--
--
-Connection errors:Connection errors:
Connection errors:Connection errors:
Connection errors:
All the inputs are protected against connection errors.
The contactors do not accept loads greater than 3 amp, and are in any case protected against
overloads and short circuits.
--
--
-Thermal protection:Thermal protection:
Thermal protection:Thermal protection:
Thermal protection:
If the temperature exceeds 80°C, the maximum current is reduced in proportion to the thermal
increase. The temperature may never exceed 85°C.
--
--
-Low battery charge:Low battery charge:
Low battery charge:Low battery charge:
Low battery charge:
When the battery charge is low, the maximum current is reduced by 50%, and in the lifting
version all functions except hydrodrive (and descent) are blocked. This feature may be
excluded via the console.
--
--
-External agents:External agents:
External agents:External agents:
External agents:
The chopper body completely sealed, and thus is protected against splashes of liquid (IP54).
MENU

Pagina 7
--
--
-Protection against accidental startup:Protection against accidental startup:
Protection against accidental startup:Protection against accidental startup:
Protection against accidental startup:
A precise sequence of operations is necessary for starting the machine.
If these operations are not carried out correctly, the machine will not start.
The request for running must be activated after the key and handle microswitch (or seat micro-
switch).
--
--
-Protection against uncontrolled movements:Protection against uncontrolled movements:
Protection against uncontrolled movements:Protection against uncontrolled movements:
Protection against uncontrolled movements:
The contactors do not close if:
- the power unit is not functioning
- the accelerator does not go below the minimum value stored increased by 2 V
- the logic is not perfectly functional
- one running microswitch is stuck.
1.6 THERMAL CONSIDERATIONS1.6 THERMAL CONSIDERATIONS
1.6 THERMAL CONSIDERATIONS1.6 THERMAL CONSIDERATIONS
1.6 THERMAL CONSIDERATIONS
- The heat generated by the control unit must be dissipated. For this to be possible, the
compartment must be ventilated and the cooling surfaces ample.
- The cooling system is dimensioned on the basis of the performance required of the machine.
For situations in which ventilation is poor and heat exchange difficult because of the
materials used, it is advisable to use forced air ventilation.
- The power dissipated by the module varies depending on the current and the work cycle.
1.7 GENERAL NOTES ON USE OF H2P1.7 GENERAL NOTES ON USE OF H2P
1.7 GENERAL NOTES ON USE OF H2P1.7 GENERAL NOTES ON USE OF H2P
1.7 GENERAL NOTES ON USE OF H2P
- Never combine SCR low frequency choppers with H2 modules, as the filtre condensers
containedinthe H2module alterSCRchopper functioning,subjecting ittoexcessive workloads.
Thus, if you wish to use two or more control units (e.g. lift + traction), they must all be of
the high frequency ZAPIMOS family.
- Do not connect the chopper to a battery with a different nominal voltage than that indicated
on the chopper identification plate. A higher battery voltage can cause MOS failure. A lower
battery voltage prevents the module from functioning.
- During battery recharge, the H2 module must be completely disconnected from the battery,
as in addition to altering the charge read by the battery charger, the module can be damaged
by the overload voltages generated by the charger.
- The H2 module must only be supplied using a traction use battery; do not use outputs of
straighteners or power suppliers. For special applications, consult the nearest ZAPI service
centre.
MENU

Pagina 8
3 INSTALLATION3 INSTALLATION
3 INSTALLATION3 INSTALLATION
3 INSTALLATION
Install the chopper with the base-plate on a flat metallic surface that is clean and unpainted.
Apply a light layer of thermo-conductive grease between the two surfaces to permit better heat
dissipation.
Despite the protection provided against external agents, the continuous attack of corrosive
substances may cause the connector contacts to oxidise, thus jeopardising good functioning.
Keep this in mind when choosing the installation position on the vehicle.
Use the special holes on the base-plate for fastening the chopper.
Make sure that the wiring of the cable terminals and connectors is carried out correctly.
Fit anti-jamming filtres on the horn, solenoid valves, and contactors not connected to the
chopper such as those for activating the pump motor or hydrodrive motor, if the latter is not
handled by the chopper itself.
3.1 CONNECTIONCABLES3.1 CONNECTIONCABLES
3.1 CONNECTIONCABLES3.1 CONNECTIONCABLES
3.1 CONNECTIONCABLES
For the auxiliary circuits, use cables of 0.5mm² section.
For power connections to the motor and to the battery, use cables having sections of 35 - 5mm².
For the best chopper performance, the cables to the battery should be run side by side and be as
short as possible.
3.2 CONTACTORS3.2 CONTACTORS
3.2 CONTACTORS3.2 CONTACTORS
3.2 CONTACTORS
Choose the type of contactors on the basis of the maximum operating current of the motor and
the specific chopper configuration.
- The current absorbed by the coil must not be greater than 3 amp.
- The coil suppressors are inside the chopper; do not use contactors with arc suppressors.
- For contactors with magnetic suppressors, make sure you respect the polarity indicated on the
cap.
3.3 FUSES3.3 FUSES
3.3 FUSES3.3 FUSES
3.3 FUSES
- Use a 10 amp fuse for auxiliary circuit protection.
- For protecting the power unit, see the diagrams.
The value shown is the maximum allowable. For special applications or requirements this
value can be reduced.
For safety reasons, we recommend that you use protected fuses in order to prevent the spread
of fused particles in the event of blowout.
MENU

Pagina 9
pinpin
pinpin
pin functionfunction
functionfunction
function descriptiondescription
descriptiondescription
description
A1 -LED Alarm LED negative: to be connected to the cathode
A2 +LED Alarm LED positive: to be connected to the anode
Output current 12mA, for standard type LED
B1 PCLRXD Serial reception positive
B2 NCLRXD Serial reception negative
B3 PCLTXD Serial transmission positive
B4 NCLTXD Serial transmission negative
B5 GND Console supply negative
B6 +12 Console supply positive
B7 FUNCTIONSELECT Channel for mini-console (speed signal)
B8 UP/DOWN Channel for mini-console (speed ref.)
C1 CPOT Potentiometer central unit: connected to the potentiometer
cursor. For speed regulation, the useful signal ranges
from 0 Volt (minimum speed) to 10 V (maximum speed).
C2 NPOT Potentiometer negative: a battery negative.
C3 PPOT Potentiometer positive: a 12 V output.
Do not short circuit this terminal toward the battery negative
or apply a resistive load of less than 500 ohm.
D1 +CH IN To be connected to the key.
D2 +CHOUT The positive to be sent to the function request microswitches
is taken from this pin. This positive is taken after the
internal diode.
3.4 LOGIC BOARD CONNECTORS3.4 LOGIC BOARD CONNECTORS
3.4 LOGIC BOARD CONNECTORS3.4 LOGIC BOARD CONNECTORS
3.4 LOGIC BOARD CONNECTORS
MENU

Pagina 10
pin function description
E1 4th speed Input 4th speed request. Enabled if E1 is connected to +Batt
E2 3th speed Input 3th speed request. Enabled if E2 is connected to +Batt
E3 2nd speed Input 2th speed request. Enabled if E3 is connected to +Batt
E4 Hyd speed (Active High) Input hydroguide request. Enabled if E4 is connected
to +Batt. In the pump standard version E4 is hyd speed, in the
PUMP+HYDRO version E4 is the hydroguide contactor. In both
versions the programmable timing hydro time is active.
E5 1st speed Input 1st speed request. Enabled if E5 is connected to +Batt.
E6 Stop up Input stop lifting. When active function on pin E7 is stopped.
E7 Up (Active High) Input speed request associated to a potentiometer.
E8 Hyd speed Same function as E4 but Active Low.
E9 Hyd speed Same function as E8 but electrically disconnected from it.
3.5 POWER CONNECTORS3.5 POWER CONNECTORS
3.5 POWER CONNECTORS3.5 POWER CONNECTORS
3.5 POWER CONNECTORS
+M+M
+M+M
+M Output current sense
+B+B
+B+B
+B Battery positive
-M-M
-M-M
-M Connected to the power mosfet drain,
it supplies a negative to the motor
with variable duty cycle
-B-B
-B-B
-B Battery negative
MENU

Pagina 11
3.6 CONTACTORS CONNECTOR DESCRIPTION
In order to command the general, hydroguide and bypass contactors a 6 pin mate-N-lock connector
is available. From this connector it is possible to get contactors coils commands.
Connector G
(logic board) Wire color Connector Function
1 - - Not used
2 white-grey 3 Negative bypass or field weakening
contactor.
3 jellow-black 5 Negative hydroguide or general contactor
4 red-black 1 Contactors positive, same key voltage.
Note: If the H2P is configured as PUMP+HYDRO it is not possible to drive the general contactor
because the comand for the coil is now used for the hydroguide contactor only.
MENU

Pagina 12
3.7 MECHANICAL DRAWING
MENU

Pagina 13
4. PARAMETER MODIFICATIONS4. PARAMETER MODIFICATIONS
4. PARAMETER MODIFICATIONS4. PARAMETER MODIFICATIONS
4. PARAMETER MODIFICATIONS
Modification of the parameters, in addition to the configuration of the inputs, is made directly
by ZAPI on customer specifications, or the customer may make adjustments himself using the
programming console or the mini-console, with which only certain parameters to be modified.
The console can remain connected to the chopper when running and the parameters can also be
varied in real time during operation.
To confirm data, press ENTER when requested by the message on the console.
The parameters thus modified and optimised on one unit can be stored from the console
(SAVE) and then reloaded (RESTORED) on another chopper, thus allowing fast and
standardised calibration (see console manual for details).
Pay special attention to the polarity of the console connector when it is hooked up to the chop-
per.
HOOKING UP MUST ONLY BE DONE WITH THE MACHINE OFF.
4.2 PROGRAMMINGCONSOLE
4.3 MINI-CONSOLE
MENU

Pagina 14
4.1 MODIFYING PARAMETERS USING THE MINI-CONSOLE4.1 MODIFYING PARAMETERS USING THE MINI-CONSOLE
4.1 MODIFYING PARAMETERS USING THE MINI-CONSOLE4.1 MODIFYING PARAMETERS USING THE MINI-CONSOLE
4.1 MODIFYING PARAMETERS USING THE MINI-CONSOLE
The parameters that can be modified are:
LiftingLifting
LiftingLifting
Lifting
11
11
11STSPEED
22
22
22NDSPEED
33
33
33RDSPEED
44
44
4HYDROSPEED
55
55
5HYDROCOMP.
00
00
0NOTCONNECTED
The adjustments are possible within 10 intermediate levels.
- Connect the mini-console to connector (B) on the chopper.
(the hookup MUST BE MADE WITH THE KEY OFF).
- Supply the machine by activating the key.
- Position the dial selector on the function to be modified.
The SET-UP button increases the value of the parameter, while SET-DOWN decreases it.
Note: the variations are made through a count of the number of impulses sent from the
buttons; thus for increasing or decreasing more than one point, you need to release and then
re-press the button.
Keeping the button pressed continuously does not provide continuous variation of the
parameters.
- The parameters are modified in real time, making it possible to check the values set
immediately.
The modified parameters are automatically stored by the control logic without the need for
confirmation before switching off or disconnecting the console.
Important note: The console does not function if connected when the motor is running.
Switch the machine off and on again for activating the console functions.
MENU

Pagina 15
4.2 PROGRAMMABLE CONSOLLE FUNCTION DESCRIPTION
The digital consolle display the model type and its built in hourmeter.
Model selection PUMPStandard
PUMP+ HYDRO
Option selection PIN G3 bypass/fieldweakening
Battery free/check
HOURS running/keyon
PIN G5 status/maincontactor
Battery selection 24/36/40/48V, 60/72/80/96V + fine adjustment
Programmableparameters Acceleration
Deceleration
Maxcurrent
Creep speed
Weakdropout
Hydroguidedelay
Hydroguide speed
Hydroguidecompensation
Non-fine speed regulation 1/2/3/4
Fine speed regulation 1/2/3/4
Tester VMN 1/3 BATT
Input E1 - E7
Potentiometerinput
Motorcurrent
Choppertemperature
Batteryvoltage
Motor voltage
Savefunction Parametermemory
Restorefunction Loading parameter on the chopper
Alarm Display of in-memory alarm
ProgramVacc Potentiometer stroke parameter
MENU

Pagina 16
4.3 OPTION AND CHOPPER CONFIGURATION
Configurationofthe model MENU SEL MODEL enables to have the chopper to work in
one of the following set:
1 Standardpump
2 Pump + Hydro = pump + hydroguide contactor
Optionconfiguration MENUSELOPTIONS
fucntion/pinfucntion/pin
fucntion/pinfucntion/pin
fucntion/pin optionoption
optionoption
option descriptiondescription
descriptiondescription
description
1)1)
1)1)
1) PIN G3PIN G3
PIN G3PIN G3
PIN G3 bypassbypass
bypassbypass
bypass The contactor connected to connector G3 is handled as a
bypass, with activation current = 80%Imax., output current
= 90%Imax., activation delay=800 msec.
weakweak
weakweak
weak The contactor connected to connector G3 is handled as
weakening, with activation current = 50% of the programmable
output current (WEAK DROP OUT) from 10% to 100% Imax.
Activation delay=800 msec.
3)3)
3)3)
3) BATTERYBATTERY
BATTERYBATTERY
BATTERYfreefree
freefree
free No low charge alarm.
checkcheck
checkcheck
check Activates the check that reads the battery voltage in standby.
When the residual charge is less than 10%, the maximum
current is halved and the LED blinks continuously.
6)6)
6)6)
6) HOURSHOURS
HOURSHOURS
HOURS runningrunning
runningrunning
running Hour-metre only active when running.
key onkey on
key onkey on
key on Hour-metre active with the key on.
4) PIN G54) PIN G5
4) PIN G54) PIN G5
4) PIN G5 statusstatus
statusstatus
status PIN G5 output is active when the chopper is executing any
function but STOP UP.
main c.main c.
main c.main c.
main c. PIN G5 output drives a general contactor
Selection of battery voltage MENUSELBATTERY
It enables to set the nominal battery voltage to drive the charge status of the battery and the tester
functions.
Voltages to be selected: 24/36/40/48V, 60/72/80/96V
With ROLL UP and ROLL DOWN buttons it is possible to select the nominal battery voltage and
SET UP and SET DOWN buttons allow fine battery voltage adjustments.
MENU

Pagina 17
4.44.4
4.44.4
4.4 PARAMETERMODIFICATIONSPARAMETERMODIFICATIONS
PARAMETERMODIFICATIONSPARAMETERMODIFICATIONS
PARAMETERMODIFICATIONS
The parameters can be modified with the chopper in standby or running. In the latter case, you
must return to standby before switching off the chopper so that the modifications are stored in
the chopper’s non-volatile memory.
1)1)
1)1)
1) ACCELER.DELAY = Pump motor acceleration time
2)2)
2)2)
2) EV.ACCELERDELAY*=Accelerationtimerelativetodescent(proportionalsolenoidvalve).
3)3)
3)3)
3) DECELER DELAY = Deceleration time, i.e. to annul the voltage on the motor upon relea-
se.
4)4)
4)4)
4) EV.DECELER DELAY* = Deceleration time relative to descent.
5)5)
5)5)
5) IMAX. Defines the maximum chopper current. All current adjustments are expressed as a
percentage of this value.
The adjustment range is from 50% (level 0) to 100% (level 9).
6)6)
6)6)
6) HYD SPEED COARSE = Coarse hydrodrive speed (from 0 to 100% Vbatt on the motor).
7)7)
7)7)
7) HYD SPEED FINE = Fine hydrodrive speed (a value from 0 to 10% Vbatt is added to the
coarse speed value). The speed is given by:
motor voltage = [(coarse speed) x 10 + (fine speed)] x Vbatt /100
The interval of values ranges from 0 to total conduction.
8)8)
8)8)
8) HYDRO COMPENS = Compensation in current for hydrodrive request.
9)9)
9)9)
9) CREEP SPEED = Defines the minimum value of voltage applied to the motor with running
request active. Allows a more immediate response.
10)10)
10)10)
10) WEAK DROPOUT = Threshold of current for opening the weakening contactor (if
programmed as such and not as bypass, in which case the output threshold is fixed and not
programmable).
11)11)
11)11)
11) HYDRO TIME = Hydrodrive delay time. If set at 0, there is no delay; thus the hydrodrive
input can be handled as a 5th speed.
12)12)
12)12)
12) 1ST SPEED COARSE = Speed no. 1, coarse adjustment.
13)13)
13)13)
13) 1ST SPEED FINE = Speed no. 1, fine adjustment.
14)14)
14)14)
14) 1ST SPEED COMP. = Compensation speed no.1.
15)15)
15)15)
15) 2ND SPEED COARSE = Speed no. 2, coarse adjustment.
16)16)
16)16)
16) 2ND SPEED FINE = Speed no. 2, fine adjustment.
17)17)
17)17)
17) 2ND SPEED COMP. = Compensation speed no.2.
18)18)
18)18)
18) 3RD SPEED COARSE = Speed no. 3, coarse adjustment.
19)19)
19)19)
19) 3RD SPEED FINE = Speed no. 3, fine adjustment.
20)20)
20)20)
20) 3RD SPEED COMP. = Compensation speed no.3.
21)21)
21)21)
21) 4TH SPEED COARSE = Speed no. 4, coarse adjustment.
22)22)
22)22)
22) 4TH SPEED FINE = Speed no. 4, fine adjustment.
23)23)
23)23)
23) 4TH SPEED COMP. = Compensation speed no.4.
24)24)
24)24)
24) MIN. VALVE VOLT.* = Minimum voltage applied on the proportional solenoid valve.
25)25)
25)25)
25) MAX. VALVE VOLT.* = Maximum voltage applied on the proportional solenoid valve.
**
**
*Special function not available on standard version
MENU

Pagina 18
4.54.5
4.54.5
4.5 SEQUENCE OF SETTINGS FOR LIFTINGSEQUENCE OF SETTINGS FOR LIFTING
SEQUENCE OF SETTINGS FOR LIFTINGSEQUENCE OF SETTINGS FOR LIFTING
SEQUENCE OF SETTINGS FOR LIFTING
- With the machine switched off, connect the programming console and then switch on. If
no wiring errors or component defects are found, the display shows the manufacturer’s
name, programme release, configuration, and hour-metre value.
If the module has already been configured, the procedure passes directly to step four.
Otherwise, proceed in order as follows.
Consult the console manual for further procedure details.
1)1)
1)1)
1) Configure the chopper model.
2)2)
2)2)
2) Select the desired options.
3)3)
3)3)
3) Select and set battery voltage.
4)4)
4)4)
4) Check the functioning of all the wired inputs, including the potentiometer, by means of the
tester functions on the console.
5)5)
5)5)
5) Carry out accelerator signal acquisition on the “PROGRAM VACC” menu.
6)6)
6)6)
6) Set the maximum current by selecting the level corresponding to the desired value.
7)7)
7)7)
7) Set the speed of the respective functions with the machine in standby, and the level of
compensation set at “0”. Then apply a load and set the compensation until it reaches the
desired speed. As the adjustments of speed and compensation are interdependent, further
adjustments must be made before reaching the optimum condition.
8)8)
8)8)
8) Set the hydrodrive speed in the same way as the others, with the only difference being that
the speed is set with the steering in standby, while the compensation is set with the
steering under load.
9)9)
9)9)
9) Set acceleration, deceleration, and creep as necessary.
TABLE OF MODIFICATIONS
MENU

Pagina 19
55
55
5DIAGNOSISDIAGNOSIS
DIAGNOSISDIAGNOSIS
DIAGNOSIS
Description of the alarms signalled by the diagnostic LED.
The alarm code is shown in parentheses. A detailed description is given in the section
“DECODINGTHEALARMSDISPLAYEDONCONSOLE”.
1 BLINK1 BLINK
1 BLINK1 BLINK
1 BLINK = Logic anomaly (EEPROM DATA KO, EEPROM PAR. KO, EEPROM CONF.
KO,EEPROM OFF-LINE, CHOPPERNO CONF, WATCH-DOG).
2 BLINKS2 BLINKS
2 BLINKS2 BLINKS
2 BLINKS = Running request on startup or error in handle/speeds sequence (INCORRECT \
START).
3 BLINKS3 BLINKS
3 BLINKS3 BLINKS
3 BLINKS = Error on VMN test (NO FUL CONDUCTION).
4 BLINKS4 BLINKS
4 BLINKS4 BLINKS
4 BLINKS = Accelerator high in standby - this error inhibits machine operation (VACC > 1 V).
5 BLINKS5 BLINKS
5 BLINKS5 BLINKS
5 BLINKS = Error in reading current - this error inhibits machine operation (1 HIGH AT
STAND, I=0 EVER).
6 BLINKS6 BLINKS
6 BLINKS6 BLINKS
6 BLINKS = Malfunctioning of the contactor driver circuit (DRIVER SHORTED, COIL
SHORTED).
7 BLINKS7 BLINKS
7 BLINKS7 BLINKS
7 BLINKS = Excessive temperature, greater than 80_ (TH. PROTECTION).
CONTINUOUS BLINKING (32 BLINKS)CONTINUOUS BLINKING (32 BLINKS)
CONTINUOUS BLINKING (32 BLINKS)CONTINUOUS BLINKING (32 BLINKS)
CONTINUOUS BLINKING (32 BLINKS) =Low battery charge, battery with < 10% of
residual charge (BATTERY).
5.15.1
5.15.1
5.1 DECODINGTHE ALARMS DISPLAYEDON CONSOLEDECODINGTHE ALARMS DISPLAYEDON CONSOLE
DECODINGTHE ALARMS DISPLAYEDON CONSOLEDECODINGTHE ALARMS DISPLAYEDON CONSOLE
DECODINGTHE ALARMS DISPLAYEDON CONSOLE
1)1)
1)1)
1) STAND BY VMN LOWSTAND BY VMN LOW
STAND BY VMN LOWSTAND BY VMN LOW
STAND BY VMN LOW
The test is carried out in standby. If the VMN voltage is lower than 1/3 of the battery
voltage, an alarm is signalled. Possible causes:
a) Check the motor wiring to make sure it is correct.
b) Chopper broken, replace.
2)2)
2)2)
2) NO FULL COND.NO FULL COND.
NO FULL COND.NO FULL COND.
NO FULL COND.
The test is carried out in full conduction.
If, in this condition, the VMN is found to be greater than 1/3 VBATT, the diagnostic
circuit is faulty, causing a safety risk, and thus machine operation is inhibited. If the defect
persists, replace the logic.
3)3)
3)3)
3) TH.PROTECTIONTH.PROTECTION
TH.PROTECTIONTH.PROTECTION
TH.PROTECTION
An indication that the chopper temperature has exceeded 80°C.
The maximum current is gradually reduced, reaching 0 at a temperature of 85°C. If the
alarm occurs while cold:
a) Check the thermal sensor connection.
b) Thermal sensor failure.
c) Connection on the power interrupted (check the connector that connects the logic to
the power unit).
d) Logic failure.
4)4)
4)4)
4) BATTERYBATTERY
BATTERYBATTERY
BATTERY
The battery charge is low.
The alarm is signalled only if the BATTERY CHECK option has been selected. All
functions except hydrdrive are inhibited.
MENU

Pagina 20
5 )5 )
5 )5 )
5 ) INCORRECTSTARTINCORRECTSTART
INCORRECTSTARTINCORRECTSTART
INCORRECTSTART
A running request is present on key startup.
Possible causes:
a) Operator error.
b) Request microswitch stuck.
6)6)
6)6)
6) I HIGH AT STANDI HIGH AT STAND
I HIGH AT STANDI HIGH AT STAND
I HIGH AT STAND
Test carried out in standby, checks that the current is nil.
Ifthisisnotverified,analarmissignalled.Thisalarmshutsdownthemachine.Possiblecauses:
a) Current sensor broken and logic failure.
First replace the logic, and if the defect persists, replace the power unit.
7)7)
7)7)
7) I=0EVERI=0EVER
I=0EVERI=0EVER
I=0EVER
Test carried out in running.
Checks that the current during running is greater than a minimum value. If not, an alarm is
signalled and the machine is shut down. Possible causes:
a) The current sensor is faulty. Replace the power unit.
8)8)
8)8)
8) EEPROM PAR.KOEEPROM PAR.KO
EEPROM PAR.KOEEPROM PAR.KO
EEPROM PAR.KO
Fault in the area of memory in which the adjustment parameters are stored. This alarm
inhibits machine operation.
If the defect persists when the key is switched off and on again, replace the logic.
If the alarm disappears, remember that the parameters stored previously have been
cancelled, and replaced by the default values.
9)9)
9)9)
9) EEPROM CONF.KOEEPROM CONF.KO
EEPROM CONF.KOEEPROM CONF.KO
EEPROM CONF.KO
Fault in the area of memory in which the special chopper configuration data is stored. If
the defect persists when the key is switched off and on again, replace the logic. Otherwise,
keep in mind that the chopper configuration has been reset to the default values
(regeneration voltage, etc.); thus it must be re-programmed. Consult the console manual.
10)10)
10)10)
10) EEPROM DATA KOEEPROM DATA KO
EEPROM DATA KOEEPROM DATA KO
EEPROM DATA KO
The data in the area of memory that handles the hour-metre is incorrect. This alarm does
not shut down the machine. If the alarm disappears when the machine is switched off and
on again, keep in mind that the hour-metre data has been reset to zero.
11)11)
11)11)
11) EEPROM OFF LINEEEPROM OFF LINE
EEPROM OFF LINEEEPROM OFF LINE
EEPROM OFF LINE
Fault in the non-volatile memory that contains data relative to the area for the hour-metre,
the alarms stored and the programming parameters.
If the alarm persists when the key is switched off and on again, replace the logic.
12)12)
12)12)
12) CHOP. NO CONF.CHOP. NO CONF.
CHOP. NO CONF.CHOP. NO CONF.
CHOP. NO CONF.
An alarm similar to no.9, except that here, even though the data is correct, it does not
correspond to a hardware configuration recognised by the H2. The considerations are the
same as for alarm 9 “EEPROM CONF.KO”.
13)13)
13)13)
13) WATCH-DOGWATCH-DOG
WATCH-DOGWATCH-DOG
WATCH-DOG
The test is made in both running and standby.
It is a self-diagnosis test within the logic.
If an alarm should occur, replace the logic.
MENU
Table of contents
Other Zapi Controllers manuals
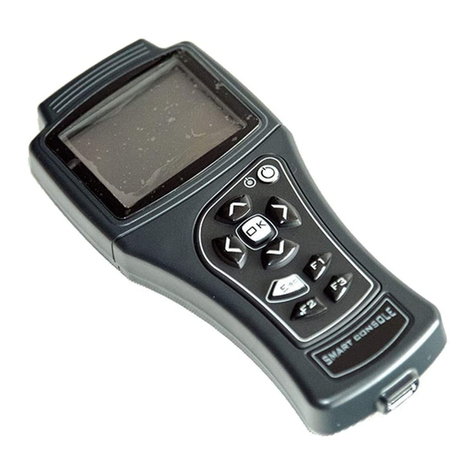
Zapi
Zapi SMART CONSOLE User manual
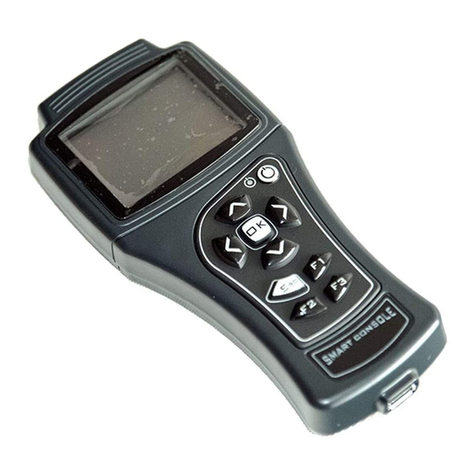
Zapi
Zapi SMART CONSOLE User manual
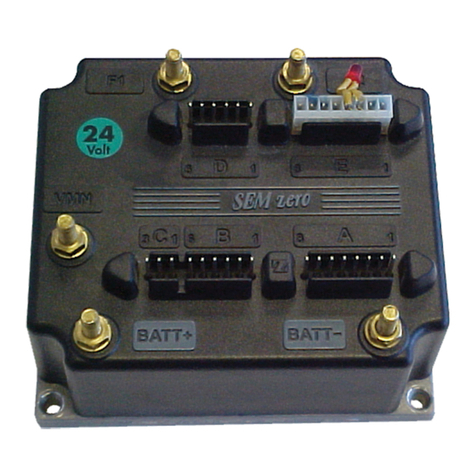
Zapi
Zapi SEM-Zero User manual
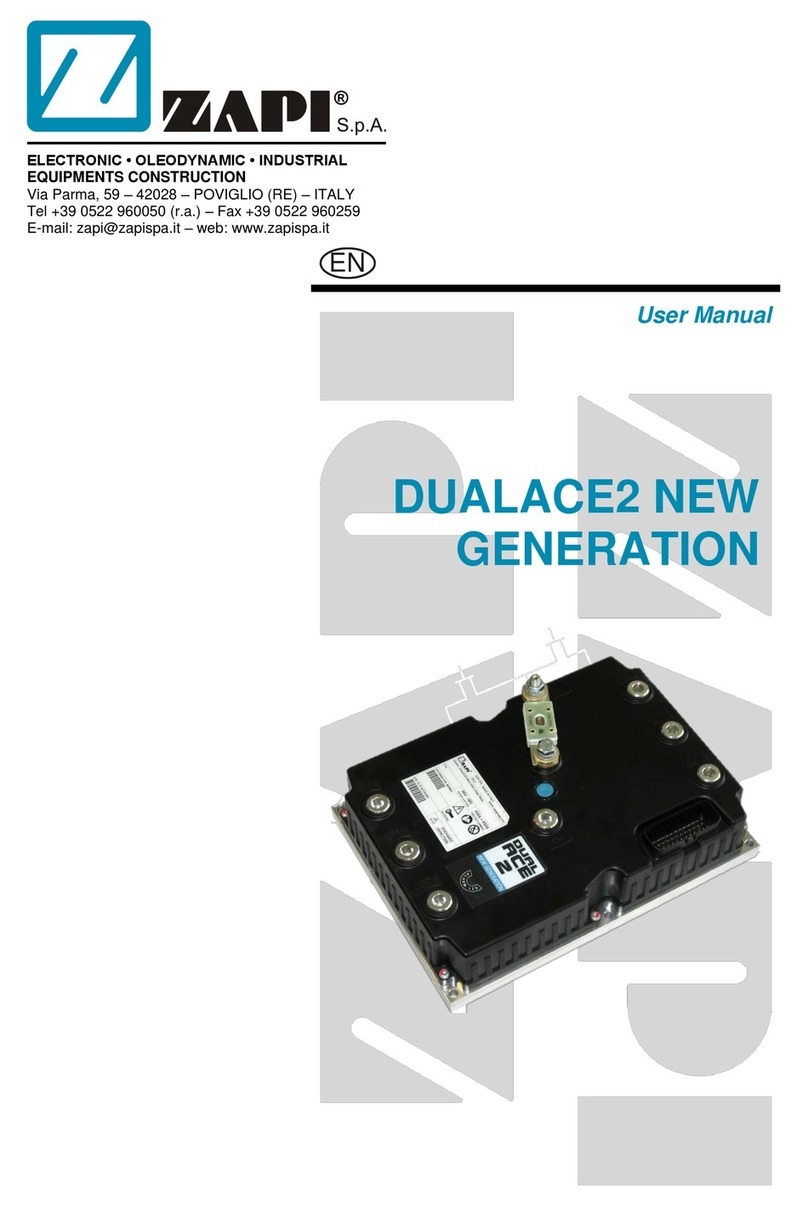
Zapi
Zapi DUALACE2 NEW GENERATION User manual
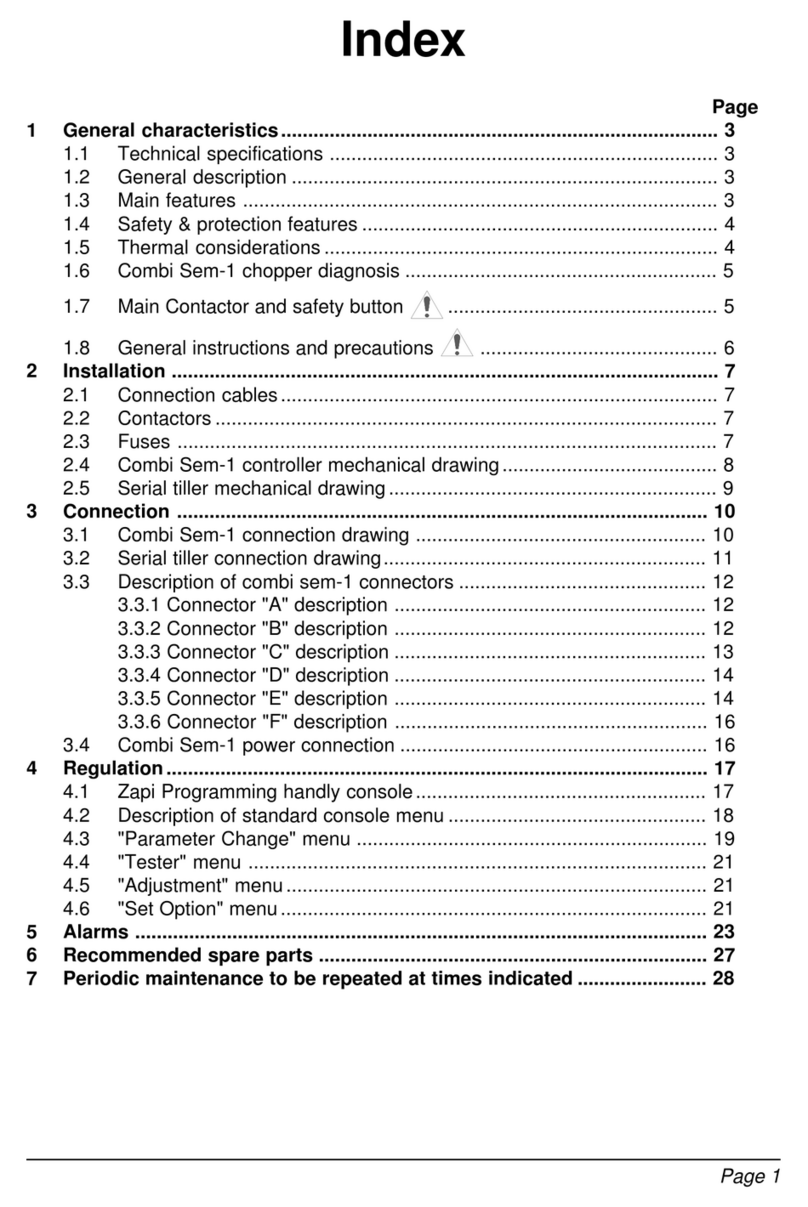
Zapi
Zapi COMBI SEM-1 User manual
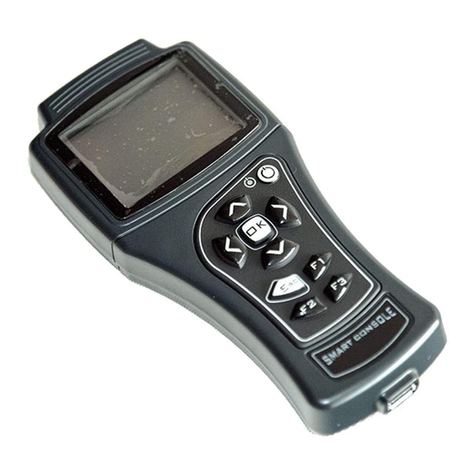
Zapi
Zapi SMART CONSOLE User manual
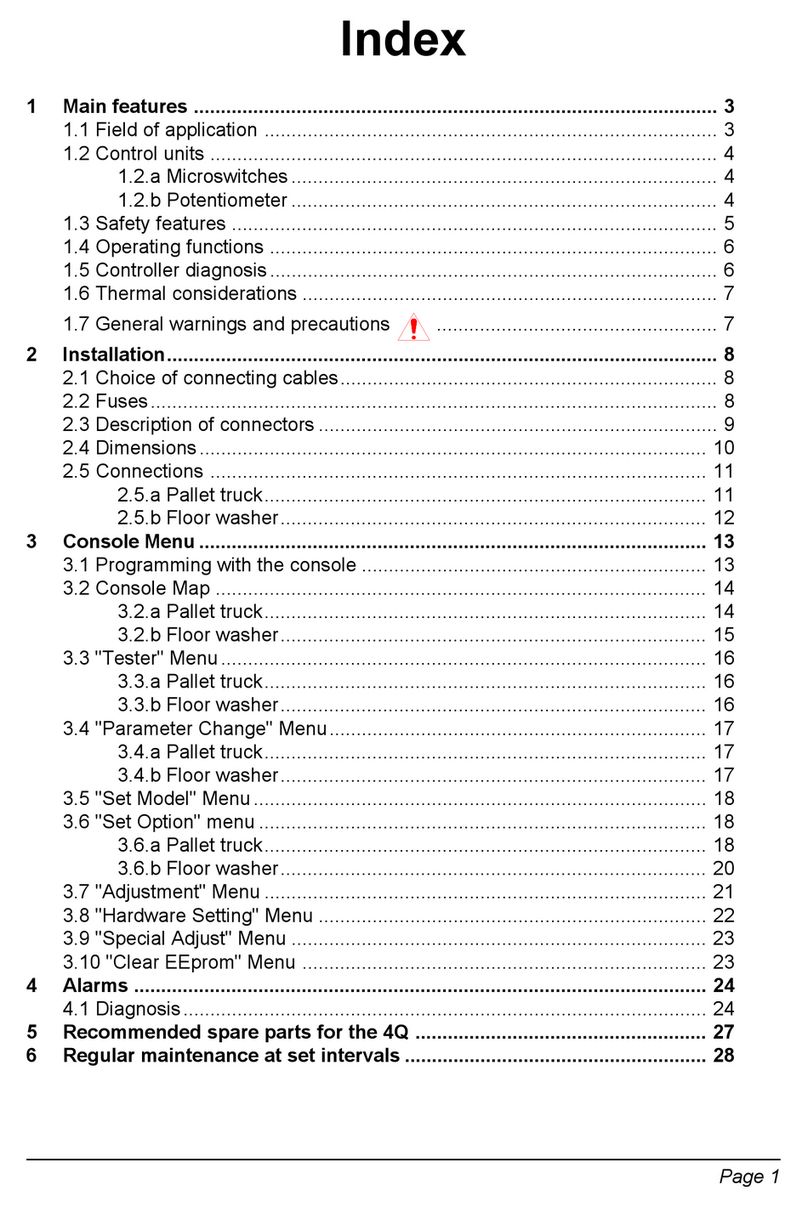
Zapi
Zapi 4Q User manual
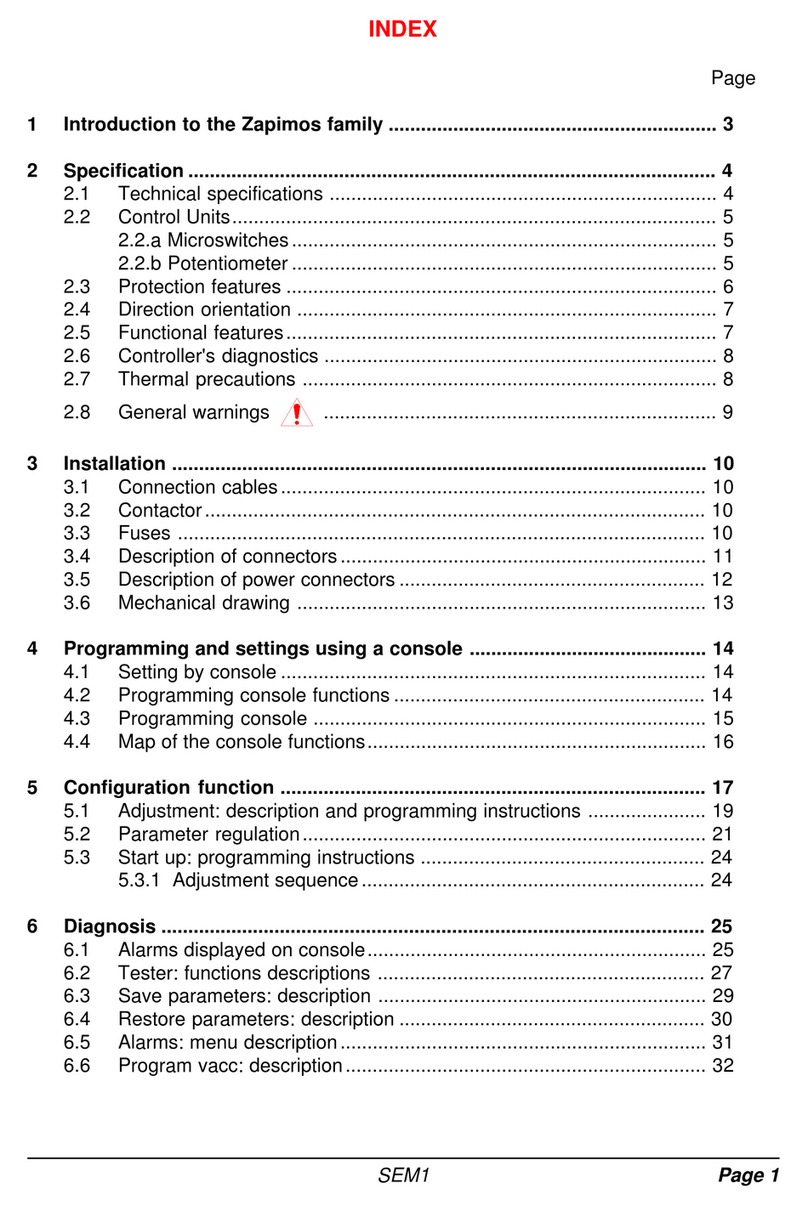
Zapi
Zapi COMBI SEM-1 User manual
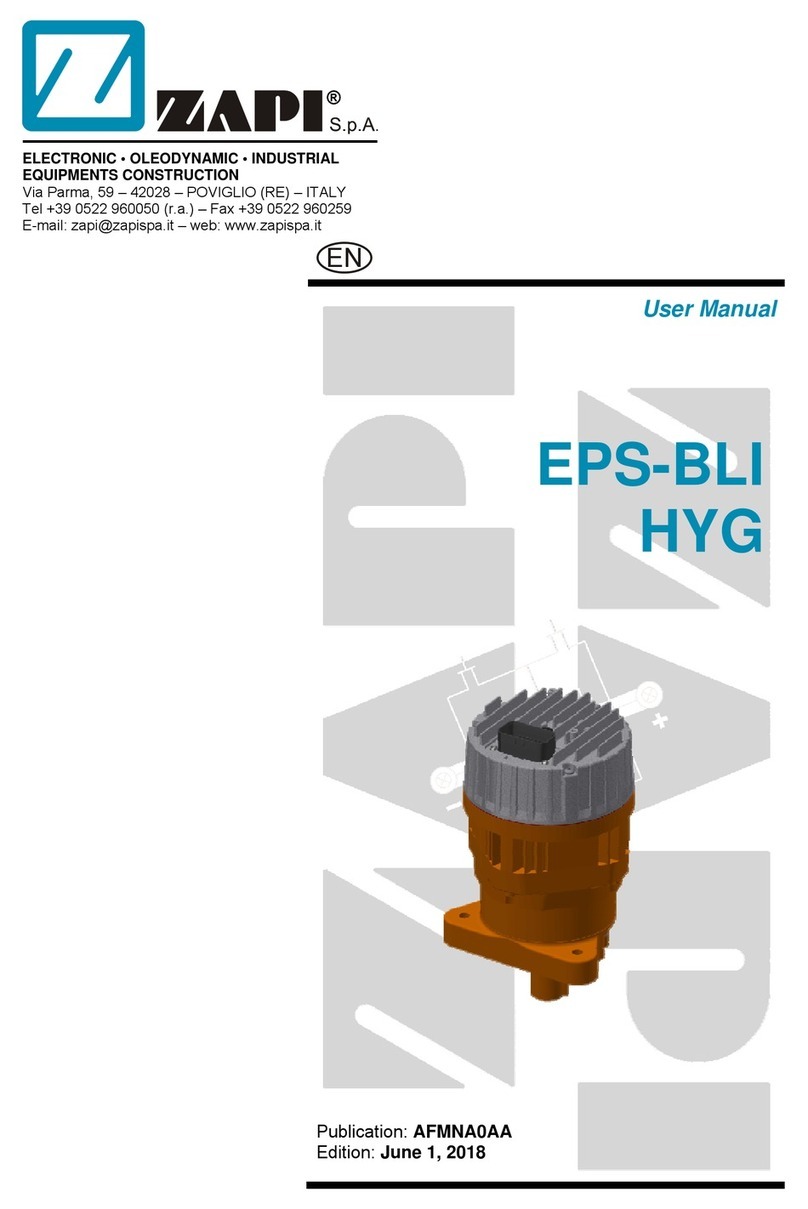
Zapi
Zapi EPS-BLI HYG User manual
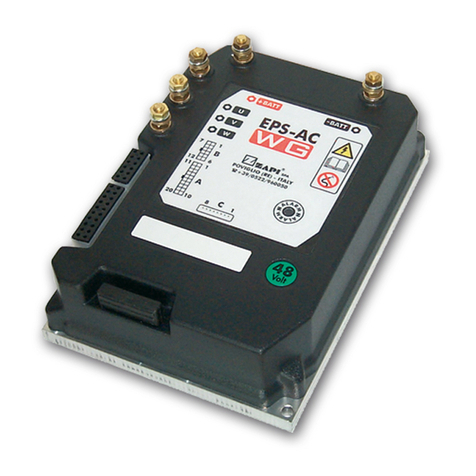
Zapi
Zapi EPS-AC User manual