Advanced MxPro4 Series User manual

Installation & Commissioning
The operation and functions described in this manual are available from Software Version Mx4200V-023 and Mx4400V-
023 onwards.
www.acornfiresecurity.com
www.acornfiresecurity.com

Specifications:
Item
Specification Details
Enclosure
Steel IP30
Steel IP30
Steel IP30
Steel IP30
Dimensions H
x W x D mm
475 x 450 x 125
475 x 450 x 190 (/D)
475 x 450 x 125
475 x 450 x 190 (/D)
950 x 450 x 190
950 x 450 x 190
Weight
(excluding
batteries)
10.5Kg / 12Kg (/D)
10.5Kg/ 12Kg (/D)
20Kg
23Kg
Temperature
-5°C to 40°C
-5°C to 40°C
-5°C to 40°C
-5°C to 40°C
Humidity
95 % Max
95 % Max
95 % Max
95 % Max
Cable Entries
(20mm
knockouts)
18x top, 9x top rear and 2x
bottom
36x top, 9x top rear (/D)
18x top, 9x top rear and 2x
bottom
36x top, 9x top rear (/D)
36x top, 9x top rear and 2x
bottom
36 x top, 9 x top rear and 2 x
bottom
Mains Supply
220-240V, +10%, -15%
47 –63 Hz AC
1 A max
220-240V, +10%, -15%
47 –63 Hz AC
1 A max
220-240V, +10%, -15%
47 –63 Hz AC
1 A max
220-240V, +10%, -15%
47 –63 Hz AC
2 A max
Battery
Capacity
24V 4Ah Internal (min)
24V 17Ah Internal (max)
(Mx4200)
24V 38Ah Internal (max)
(Mx4200/D)
24V 4Ah Internal (min)
24V 17Ah Internal (max) (Mx-
4400)
24V 38Ah Internal (max) (Mx-
4400/D)
24V 4Ah Internal (min)
24V 48Ah Internal (max) (2x
24Ah in parallel)
2x 24V 4Ah Internal (min)
2x 24V 38Ah Internal (max)
Charging
Current
2.4A
Temperature Compensated
2.4A
Temperature Compensated
2.4A
Temperature Compensated
2 x 2.4A
Temperature Compensated
Max Battery
Resistance
(+/-10%)
1.5Ω
1.5Ω
1.5Ω
1.5Ω
Power Supply
Separate 24V DC, 4A
Off-Line
Switched Mode
Separate 24V DC, 5A
Off-Line
Switched Mode
Separate 24V DC, 5A
Off-Line
Switched Mode
2x Separate 24V DC, 5A
Off-Line
Switched Mode
Imax(a) =
Imax(b)
2.6A
2.6A
2.6A
2.6A
Output
Voltage1
18.5V –28.0V
18.5V –28.0V
18.5V –28.0V
18.5V –28.0V
Ripple (Vpkpk)
1.0V
1.0V
1.0V
1.0V
Number of
Fire Zones
200 max, across 2 loops
(1000 when networked)
200 max, across 4 loops
(1000 when Networked)
200 max, across 4 loops
(1000 when Networked)
400 max, across 8 loops
(1000 when Networked)
Number of
Loops
1 to 2
1 to 4
1 to 4
2 to 8
Devices per
Loop
2402
Loop Current 3
(max. / Loop)
400mA quiescent
500mA alarm
400mA quiescent
500mA alarm
400mA quiescent
500mA alarm
400mA quiescent
500mA alarm
Protocols
ADVANCED / ARGUS VEGA
Sounder 3
Outputs
2 x 1A Programmable
4 x 1A Programmable
4 x 1A Programmable
8 x 1A Programmable
Relay Outputs
2 x 1A 30V AC/DC (max)
10mA. 5V (min)
Programmable
2 x 1A 30V AC/DC (max)
10mA. 5V (min)
Programmable
2 x 1A 30V AC/DC (max)
10mA. 5V (min)
Programmable
4 x 1A 30V AC/DC (max)
10mA. 5V (min)
Programmable
Open
Collector
Outputs
2 x Programmable
10mA 30V DC (max)
2 x Programmable
10mA 30V DC (max)
2 x Programmable
10mA 30V DC (max)
4 x Programmable
10mA 30V DC (max)
Digital Outputs
6 x Programmable
6 x Programmable
6 x Programmable
12 x Programmable
Auxiliary
Supply Output
3
24V DC, 500mA
24V DC, 500mA
24V DC, 500mA
2 x 24V DC, 500mA
Event Log
1000 Event & Diagnostic + 500 Fire
As our policy is one of constant product improvement the right is therefore reserved to modify product specifications without prior notice
1
Minimum/maximum specifications for the AUX, and Sounder outputs. Detector Loop voltage is not dependant on AC or battery voltage.
2
See Section 2.6.3 for details of EN54-2 detection device limits.
3
Total output current and panel load should not to exceed Imax(a).
www.acornfiresecurity.com
www.acornfiresecurity.com

3
Table of Contents
1INTRODUCTION 6
1.1 STANDARDS 6
1.2 CAUTIONS AND WARNINGS 7
1.3 DESCRIPTION 7
1.4 EN54 FUNCTIONS 8
1.5 EN54 OPTIONAL FEATURES WITH REQUIREMENTS 9
1.6 INSTALLATION APPROVALS 10
1.6.1 Fire System Installations 10
1.6.2 Wiring Regulations 10
2INSTALLATION 11
2.1 IDENTIFICATION OF PARTS 11
2.1.1 Mx-4200V & Mx-4400V 11
2.1.2 Mx-4400V/LE 11
2.1.3 Mx-4800V 12
2.2 INSTALLING THE MX-4200V &MX-4400V ENCLOSURES 13
2.2.1 Opening the Enclosure Cover 13
2.2.2 Removing the Chassis 13
2.2.3 Mounting the Enclosure 14
2.2.4 Remounting the Chassis 14
2.2.5 Recommended Cable Routing Arrangement 14
2.3 INSTALLING THE MX-4400V/LE AND MX-4800V ENCLOSURES 15
2.3.1 Opening the Enclosure Cover 15
2.3.2 Removing the Chassis 15
2.3.3 Mounting the Enclosure 15
2.3.4 Remounting the Chassis 16
2.3.5 Recommended Cable Routing Arrangement 16
2.4 LOOP DRIVER INSTALLATION 17
2.4.1 Fitting the cards in the Mx4200V, Mx-4400V & Mx-4800V 17
2.4.2 Removing a Loop Driver Card 17
2.5 LOCAL PERIPHERAL MODULES 18
2.5.1 Peripheral Bus Interface Adaptor 18
2.5.2 Routing Interface Card 18
2.6 WIRING INSTALLATION 19
2.6.1AC Mains Wiring 19
2.6.1.1 Cable Gland 20
2.6.2 Battery Installation 20
2.6.2.1 Mx-4200V & Mx-4400V 21
2.6.2.2 Mx-4400V/LE & Mx-4800V 22
2.6.2.3 Battery Temperature Monitoring 22
2.6.3 Detector Loop Installation 23
2.6.4 Sounder Circuits 24
2.6.5 Relay Circuits 24
2.6.6 Open Collector Outputs 25
2.6.7 Auxiliary Supply Output 25
2.6.8 Switch Inputs 25
2.6.9 RS232 Interface 26
2.6.10 Isolated Bus Interface 26
2.6.11 Routing Interface 26
3PROGRAMMING 27
3.1 INTRODUCTION 27
3.1.1 Access Levels 27
3.1.2 Memory Lock 27
3.1.3 Navigating through menus 27
3.1.4 Changing Text Descriptions 28
3.1.5 Numeric data entry 28
3.2 RECOMMENDED PROGRAMMING PROCEDURE 29
3.3 LEVEL 3MENU FUNCTIONS 29
3.3.1 Loops 30
3.3.2 Loops –View/Edit 30
www.acornfiresecurity.com
www.acornfiresecurity.com

4
3.3.2.1 State 30
3.3.2.2 Type 30
3.3.2.3 Value 30
3.3.2.4 Zone 30
3.3.2.5 Device Text 31
3.3.2.6 Action 31
3.3.2.7 Sensitivity 32
3.3.2.8 O/P Group 33
3.3.2.9 Additional Info 34
3.3.2.10 Device Testing 34
3.3.3Loops –Auto Learn 34
3.3.3.1 Normal Procedure / Initial learn 34
3.3.3.2 Procedure if the Panel finds Devices Missing 35
3.3.3.3 Procedure if the Panel finds Devices Added 35
3.3.3.4 Procedure if the Panel finds Devices Changed 35
3.3.3.5 Double Address 36
3.3.4 Loop –Calibrate 36
3.3.5 Loop –Driver 36
3.3.6 Loop –SEQ Address 36
3.3.7 Loop –Line Quality 37
3.3.8 Zones 38
3.3.9 Exit 38
3.3.10 Outputs 38
3.3.10.1 Default Output Settings 39
3.3.10.2 Cause 39
3.3.10.3 Style 40
3.3.10.4 Copying Output Settings to Multiple Zones 41
3.3.11 Investigation Delays 41
3.3.11.1 Overriding Delays at Level 1 41
3.3.12 Time and Date 42
3.3.13 View Options 42
3.3.14 Passwords 42
3.3.15 Panel 43
3.3.16 PC Config 43
3.3.17 Setup 43
3.3.17.1 Network 43
3.3.17.2 Panel Zone 43
3.3.17.3 Service Number 43
3.3.17.4 Service Due Date 44
3.3.17.5 Trace Logging Mode 44
3.3.17.6 Detector Blinking 44
3.3.17.7 Earth Fault Notification 45
3.3.17.8 Routing Interface 45
3.3.17.9 Program ID 45
3.3.17.10 Config Data 45
4SERVICE AND MAINTENANCE 46
4.1MAINTENANCE SCHEDULE 46
4.1.1 Daily Actions 46
4.1.2 Monthly Actions 46
4.1.3 Quarterly Actions 46
4.1.4 Annual Actions 46
4.2 REPLACEMENT OF COMPONENTS 47
4.2.1 Batteries 47
4.2.1.1 Standby Batteries 47
4.2.1.2 Lithium Battery 48
4.2.2 Liquid Crystal Display 48
5APPENDICES 49
5.1 APPENDIX 1–FORGOTTEN LEVEL 3PASSWORD 49
5.2 APPENDIX 2–RECOMMENDED FIRE RATED CABLES 50
5.2.1 Detector Loop Lengths 51
5.2.2 Sounder Circuit Lengths 51
5.2.3 Fire / Fault Routing Circuit Lengths 52
5.2.4 Network Cables 52
5.3 APPENDIX 3–BATTERY STANDBY CALCULATION CHART 53
5.3.1 Mx-4200V / Mx-4400V / Mx-4800V 53
www.acornfiresecurity.com
www.acornfiresecurity.com

5
5.4 APPENDIX 4–CAUSE AND EFFECT PROGRAMMING EXAMPLE 54
5.4.1 Introduction 54
5.4.2 Output Groups 54
5.4.3 Styles 54
5.4.4 Output Group Programming 55
5.5 APPENDIX 5–LOOP DEVICE SPECIFIC INFORMATION 56
5.5.1 Detectors 56
5.5.1.1 V100 Smoke Detector 56
5.5.1.2 V200 Multi Sensor Detector 56
5.5.1.3 V350 Heat Detector 57
5.5.1.4 LV100 Smoke Detector 57
5.5.1.5 LV200 Multi Detector 57
5.5.1.6 LV350 Heat Detector 57
5.5.1.7 Mounting Base VB100 57
5.5.1.8 Detector Magnet Testing 57
5.5.2 VCP100 Call point 58
5.5.3 Modules 58
5.5.3.1 Standard Modules 58
5.5.3.2 Loop Wiring 59
5.5.3.3 Input Module 59
5.5.3.4 Input / Output Module 59
5.5.3.5 Supervised Output Module 59
5.5.3.6 Relay Output Module21 59
5.5.3.7 Micro Modules 59
5.5.3.8 Zone Monitor Module 60
5.5.3.9 Multiple Input / Output Modules 61
5.5.4 Sounders / Beacons 61
5.5.4.1 VLS100 Wall Mounting 95dbA Sounder 61
5.5.4.2 VLBS100 Base Sounder 62
5.5.4.3 VLS100AV Sounder Beacon 62
5.5.4.4 VLBE100 Beacon 63
5.5.5 Radio Devices 63
5.5.5.1 VW2W100 Wireless Translater Interface 63
5.5.5.2 SGWE Wireless Expander 63
5.5.5.3 SG100 Wireless Smoke Detector 63
5.5.5.4 SG200 Wireless Smoke Thermal Detector 63
5.5.5.5 SG350 Wireless Thermal Detector 63
5.5.5.6 SGCP100 Wireless Call Point 63
5.5.5.7 SGMI100 Wireless Input Module 63
5.5.5.8 SGMC100 Wireless Relay Output 63
5.5.5.9 SGRS100 Wireless Wall Sounder 63
5.6 APPENDIX 6–MX4000 SERIES LOOP OUTPUT DRIVE CAPABILITY 64
5.7 APPENDIX 7–OTHER USEFUL DOCUMENTS 65
5.8 APPENDIX 8–MX-4800V /NETWORK DESIGN PRINCIPLES 66
5.8.1 Mandatory Functions 66
5.8.2 Network Wiring 66
5.9 APPENDIX 9–MX SERIES PRODUCT CAPABILITIES /MAX LIMITS 67
www.acornfiresecurity.com
www.acornfiresecurity.com

6
1 Introduction
1.1 Standards
Advanced Electronics Ltd declare that the products identified below conform to the essential requirements
specified in the Construction Products Directive 89/106/EEC:
0086-CPD-549125
EN54-2: 1997 +A1:2006
Control and indicating equipment for fire detection and fire
alarm systems for buildings
Provided options:
- Outputs to Fire Alarm Devices
- Output to Fire Routing Equipment
- Output to Fault Routing Equipment
- Investigation Delays to Outputs
- Dependency on more than one alarm signal
- Fault Signals from Points
- Disablement of Points
- Alarm Counter
- Test Condition
- Standardised Input / Output
EN54-4: 1997 +A1:2002 +A2:2006
Power supply equipment for fire detection and fire alarm
systems for buildings
Mx-4200V, Mx-4200V/LE, Mx-4400V, Mx-4400V/LE and Mx-
4800V
In addition, the products comply with the following:
Low Voltage Directive 2006/95/EC
EN60950-1: 2006 Safety of information technology equipment
Electromagnetic Compatibility Directive 2004/108/EC
EN61000-6-3:2001 Emissions, Class B
EN50130-4: 1995 +A1:1998 +A2: 2003 Immunity, Product Family Standard
www.acornfiresecurity.com
www.acornfiresecurity.com

7
1.2 Cautions and Warnings
STOP
BEFORE INSTALLATION –Refer To the Ratings shown on the label inside
the product and to the ‘Specifications Chart’ in this document.
Please read this manual carefully. If you are unclear on any point DO NOT
proceed. Contact the manufacturer or supplier for clarification and guidance.
Only Trained service personnel should undertake the Installation,
Programming and Maintenance of this equipment.
This product has been designed to comply with the requirements of the Low
Voltage Safety and the EMC Directives. Failure to follow the installation
instructions may compromise its adherence to these standards.
ATTENTION
OBSERVE PRECAUTIONS
FOR HANDLING
ELECTROSTATIC
SENSITIVE DEVICES
This equipment is constructed with static sensitive components. Observe anti-
static precautions at all times when handling printed circuit boards. Wear an
anti-static earth strap connected to panel enclosure earth point. Before installing
or removing any printed circuit boards remove all sources of power (mains and
battery).
1.3 Description
This manual covers the installation, programming and commissioning of the Mx-4200V, Mx-4400V and Mx-
4800V Fire Alarm Control Panels. Refer to the User Manual (Document No. 680-159) for details of how to
operate the panel.
The Mx-4200V is a Multiple Loop, Analogue Addressable Fire Alarm Control Panel with provision for up to two
loops.
The Mx-4400V is a Multiple Loop, Analogue Addressable Fire Alarm Control Panel with provision for up to four
loops.
The Mx-4800V is a Multiple Loop, Analogue Addressable Fire Alarm Control Panel with provision for up to eight
loops.
All models are designed for use with the ADVANCED / ARGUS VEGA fire detection devices.
Install the panel, detection loops, sounder circuits, etc. in accordance with the instructions in Section 2
and then program the operation in accordance with the instructions detailed in Section 3.
www.acornfiresecurity.com
www.acornfiresecurity.com

8
1.4 EN54 Functions
This Fire Alarm Control Panel is compliant with the requirements of EN54 parts 2
and 4 (1997).
In addition to the basic requirements, the following optional functions are provided
and these comply with the requirements of EN54.
C.I.E Optional Functions
EN54-2 Clause
Indication
Outputs
Controls
Outputs to Fire Alarm Devices
Outputs to Fire Routing Equipment
Investigation Delays to Outputs
Co-incidence Detection
Alarm Counter
Fault Signals from Points
Output to Fault Routing Equipment
Disablement of Points
Test Condition
Standardised I/O
7.8
7.9
7.11
7.12
7.13
8.3
8.9
9.5
10
11
P.S.E Functions
EN54-4 Clause
Operation from a main power supply
Operation from a standby battery
Monitor and Charge the Standby Battery
Recognise and Notify Supply Faults
5.1
5.2
5.3
5.4
This Fire Alarm Control Panel also supports additional functions that are not covered
by EN54. These are as follows:
Additional Function
Refer to
Paragraphs
Auxiliary Power Supply Output
Auxiliary Relay Outputs
Programmable Cause / Effect on Outputs (Phased Evacuation)
Printer Option
2.6.7
2.6.5
5.4
User Manual
www.acornfiresecurity.com
www.acornfiresecurity.com

9
1.5 EN54 Optional Features with Requirements
In addition to the mandatory requirements of EN54 Part 2, the Control and Indicating Equipment (C.I.E)
supports the following optional features with requirements: -
Section 7.8
Outputs to Fire Alarm Devices.
The C.I.E has provision for connection to Fire Alarm Devices. It is possible to Silence
and Resound the alarms at Level 2. Refer to the User Manual for further information.
Refer to Sections 3.3.10 and 3.3.11 for information on output programming.
Section 7.9
Outputs to Fire Routing Equipment.
The C.I.E has provision to signal the fire condition to a remote receiving station such
as the fire brigade office. Requires installation of a routing interface card. Refer to
Sections 2.5.2, 2.6.11, 3.3.10, 3.3.11 and 3.3.17.8 for further information
Section 7.11
Delays to Outputs.
The C.I.E has provision for Output and Investigation Delays. Refer to Sections 3.3.10
& 3.3.11 for further information
Section 7.12
Coincidence Detection.
The C.I.E has provision for Coincidence Detection. Refer to Section 3.3.10 for further
information. Types B and C are supported.
Section 7.13
Alarm Counter.
The C.I.E has provision record the number of times that the fire alarm condition is
entered. Refer to the User Manual for further information.
Section 8.3
Fault Signals from Points.
The C.I.E is able to receive and process fault signals from points. These are indicated
on a per zone basis. Refer to the User Manual for further information.
Section 8.9
Outputs to Fault Routing Equipment.
The C.I.E has provision to signal the fault condition to a remote receiving station such
as the service centre office. Requires installation of a routing interface card. Refer to
Sections 2.5.2, 2.6.11, 3.3.10, 3.3.11 and 3.3.17.8 for further information
Section 9.5
Disablement of Points.
The C.I.E has provision for enabling and disabling signals from points. Refer to the
User Manual for further information.
www.acornfiresecurity.com
www.acornfiresecurity.com

10
Section 10
Test Condition.
The C.I.E has provision for testing the installation on a per zone basis. Refer to the
User Manual for further information.
Section 11
Standardised Input/Output interface.
Standardised I/O interfaces are supported over the Ad-Net Network.
1.6 Installation Approvals
1.6.1 Fire System Installations
The panel must be installed and configured for operation in accordance with these instructions and the
applicable code of practice or national standard regulations for fire systems installation (for example BS5839-1:
2002) appropriate to the country and location of the installation.
1.6.2 Wiring Regulations
The panel and system must be installed in accordance with these instructions and the applicable wiring codes
and regulations (for example BS7671) appropriate to the country and location of the installation.
www.acornfiresecurity.com
www.acornfiresecurity.com

11
2 Installation
2.1 Identification of Parts
The following diagrams show the major parts of the panels.
2.1.1 Mx-4200V & Mx-4400V
2.1.2 Mx-4400V/LE
Earth Lead to
Cover
Chassis Assembly
Loops 1 - 4
Rear Enclosure
Door
Battery Shelf
Loops 1 - 4
Bus-bars for cable earth
connections
Viewing Window
for Loops 1-4
Additional
Battery Shelf
Chassis
Assembly
Rear
Enclosure
AC Mains
Input
Battery
Leads
www.acornfiresecurity.com
www.acornfiresecurity.com

12
2.1.3 Mx-4800V
Earth Lead to
Cover
Chassis Assembly
Loops 1-4
Rear Enclosure
Door
Battery Shelf
Loops 1-4
Bus-bars for cable earth
connections
Viewing Window
for Loops 1-4
Viewing Window
for Loops 5-8
Chassis Assembly
Loops 5-8
Battery Shelf
Loops 5-8
www.acornfiresecurity.com
www.acornfiresecurity.com

13
2.2 Installing the Mx-4200V & Mx-4400V Enclosures
The panel can weigh in excess of 20kg when the batteries are installed. Use the
appropriate fixing hardware necessary to secure the panel to the wall. Observe
recommended lifting practices to guard against spinal injury.
2.2.1 Opening the Enclosure Cover
The Mx-4200V & Mx-4400V are provided with a key-lock assembly for securing the hinged door to the back box.
Insert and turn the key to open the enclosure.
2.2.2 Removing the Chassis
It is recommended that the chassis be
removed before fitting the panel to the
wall. To remove the chassis:
Refer to the diagram opposite.
Disconnect the earth cable connecting
the chassis to the spade terminal on the
rear enclosure.
Remove the bottom two screws holding
the chassis to the back box. Keep these
items in a safe place for later re-use.
Loosen the top two screws holding the
chassis to the back box via the keyhole
slots. The chassis assembly can now be
removed.
Carefully remove the chassis from the
rear enclosure and place in a safe place
to prevent accidental damage.
Earth
Connection
Fixing
Screws.
Do not lift the chassis by holding onto any of the printed circuit cards. Hold the
chassis by the metal plate only.
www.acornfiresecurity.com
www.acornfiresecurity.com

14
2.2.3 Mounting the Enclosure
Firstly, remove the required knockouts for the
installation wiring. There are sufficient
knockouts on the top of the enclosure for all
installation wiring. In addition, there are
knockouts at the top of the back wall, if
required, for rear entry cabling.
The diagram opposite shows the positions of
the four holes. Use all four positions to ensure
the panel is held securely to the wall.
Drill the required holes in the supporting wall
using a drill bit diameter 7.0 mm and plug with
a suitable 40mm long expansion plug. Affix the
panel to the wall with M5 screws (length
40mm) or No.10 screws (length 1½”).
Ensure that there is sufficient space to allow
the door to be opened when the panel is
mounted.
Finally, use a brush to remove any dust or
swarf from inside the enclosure.
450
380
35
25
475
405
Earth
Studs
x4
Cable Tie
Anchor Points x9
Enclosure Size and Fixing Point Dimensions
2.2.4 Remounting the Chassis
Carefully replace the chassis and locate onto the upper two screws. Replace the bottom two screws and tighten
all four screws to hold the chassis securely to the back box.
Reconnect the chassis earth cable to the spade terminal in the rear of the enclosure.
2.2.5 Recommended Cable Routing Arrangement
It is recommended that the routing
arrangement shown in the diagram
opposite be employed.
Segregate the low voltage wiring (Loop
Circuit, Sounder Circuits, RS485 and
AUX Supply) from the AC Mains Wiring
and any wiring connected to the relay
contacts.
Eyelets are provided in the rear of the
back box to enable the cables to be
securely fastened using tie-wraps.
Sounders and AUX wiring should be
routed behind the chassis assembly and
tie-wrapped to the back box.
Cable screens / shields should be
connected to the back box using the
threaded studs provided near the
knockout holes. Multi-way Bus bars are
available separately for mounting on the
threaded studs.
Refer to Appendix 2 –Recommended
Fire Rated Cables for further information
on cable types to be used.
Refer to specific sections on how to install AC
Mains input and loop, sounder, relay and AUX
outputs circuits.
AC Mains
Relays
Sounders + AUX
Ad-NeT /
Network
LOOPS
Sounders + AUX
Internal arrangement showing recommended
routing of cables.
www.acornfiresecurity.com
www.acornfiresecurity.com

15
2.3 Installing the Mx-4400V/LE and Mx-4800V Enclosures
The panel can weigh in excess of 80kg when the batteries are installed. Use the
appropriate fixing hardware necessary to secure the panel to the wall. Observe
recommended lifting practices to guard against spinal injury.
2.3.1 Opening the Enclosure Cover
The Mx-4400V/LE and Mx-4800V are provided with two key-lock assemblies for securing the hinged door to the
back box. Insert and turn both keys to open the enclosure.
2.3.2 Removing the Chassis
It is recommended that the chassis
assemblies be removed before fitting the
panel to the wall. To remove the chassis:
Refer to the diagram opposite.
Disconnect the earth cable connecting the
chassis to the spade terminal on the rear
enclosure.
Remove the bottom two screws holding the
chassis to the back box. Keep these items in a
safe place for later re-use.
Loosen the top two screws holding the
chassis to the back box via the keyhole slots.
The chassis assembly can now be removed.
Carefully remove the chassis from the rear
enclosure and place in a safe place to prevent
accidental damage.
Earth
Connection
Fixing
Screws.
2.3.3 Mounting the Enclosure
Firstly, remove the required knockouts for the
installation wiring. There are sufficient
knockouts on the top of the enclosure for all
installation wiring. In addition, there are
knockouts at the top of the back wall, if
required, for rear entry cabling.
The diagram opposite shows the positions of
the six holes. Use all six positions to ensure the
panel is held securely to the wall.
Drill the required holes in the supporting wall
using a drill bit diameter 10.0 mm and plug with
a suitable 50mm (minimum) long metal
expansion plug. Affix the panel to the wall with
M6 screws (length 50mm minimum).
Ensure that there is sufficient space to allow
the door to be opened when the panel is
mounted.
Finally, use a brush to remove any dust or
swarf from inside the enclosure.
450
380
35
20
515
370
950
Enclosure Size and Fixing Point Dimensions
www.acornfiresecurity.com
www.acornfiresecurity.com

16
2.3.4 Remounting the Chassis
Carefully replace the chassis and locate onto the upper two screws. Replace the bottom two screws and tighten
all four screws to hold the chassis securely to the back box.
Reconnect the chassis earth cable to the spade terminal in the rear of the enclosure.
2.3.5 Recommended Cable Routing Arrangement
It is recommended that the routing
arrangement shown in the diagram
opposite be employed.
Segregate the low voltage wiring
(Loop Circuit, Sounder Circuits,
RS485 and AUX Supply) from the
AC Mains Wiring.
Segregate any wiring connected to
the relay contacts.
Eyelets are provided in the rear of
the back box to enable the cables to
be securely fastened using tie-
wraps.
Sounders and AUX wiring should be
routed behind the chassis assembly
and tie-wrapped to the back box.
Cable screens / shields should be
connected to the back box using Bus
Bars provided near the knockout
holes.
Refer to Appendix 2 –
Recommended Fire Rated Cables
for further information on cable types
to be used.
Refer to specific sections on how to
install AC Mains input and loop,
sounder, relay and AUX outputs
circuits.
Use front
knockout rows for
upper chassis
cables
Use rear knockout
rows for lower
chassis cables
Route battery
cables through
hole in upper
battery shelf –
Ensure that the
hole is protected
by a grommet.
Field
Installation
Wiring
Battery Wiring
Internal arrangement showing recommended routing of
cables.
www.acornfiresecurity.com
www.acornfiresecurity.com

17
2.4 Loop Driver Installation
The Mx-4100V has one in-built loop driver, for connection of detectors, call points and other signalling devices.
2.4.1 Fitting the cards in the Mx4200V, Mx-4400V & Mx-4800V
To extend the number of detector loops or to
replace an existing loop driver card follow the
procedure described below.
An example of the loop driver is shown opposite.
This is provided with a plastic grip handle on the
top edge to ease removal of the card from the
Base Card.
Loop Driver –Component Side View
Isolate ALL sources of power before
installing or removing printed circuit
boards.
Observe anti-static precautions at all
times when handling printed circuit
boards.
Open the enclosure and then open the display
plate (it is hinged on the right hand side and there
is a magnetic catch strip on the left-hand side) to
gain access to the Base Card.
A section of the Base Card identifying the
locations for each loop driver is shown in the
picture opposite
To install a loop driver, remove the retaining strap,
then gently guide the loop driver printed circuit
card into the guide slots of the machined end
blocks and then push into place onto the
connector on the Base Card.
Ensure that the pins of the connectors are
correctly aligned. The loop driver should be
inserted with the component side of the board
placed on the left-hand side. Replace the retaining
strap.
The Base Card can accept up to four loop driver
cards –it does not matter which positions are
used. Ensure that the detector loop wiring is made
to the terminal block positions appropriate to the
loop driver cards actually installed.
Close the chassis display plate and then close up
the enclosure.
Component side of
Loop Driver Card
Machined End
Block
LOOPS
1
2
3
4
NB: The Mx-4200V only has positions 1 & 2
available.
2.4.2 Removing a Loop Driver Card
To remove a loop driver, remove all power and follow the procedure above but:
Take a firm hold of the lever located on top of the loop driver card. Gradually and carefully pull the loop
driver away from the base card and guide it out of the slots in the machined end blocks.
www.acornfiresecurity.com
www.acornfiresecurity.com

18
2.5 Local Peripheral Modules
The Mx-4200V, Mx-4400V and Mx-4800V panels provide provision for installation / use of local peripheral cards
to provide additional functions. The peripherals are connected via an isolated bus interface.
The panel supports the Mxp-032 General Routing Interface and up to sixteen Mxp-034 4-Way Programmable
Sounder Modules
4
.
2.5.1 Peripheral Bus Interface Adaptor
To use the local peripheral bus Interface
requires the installation of an Adaptor Card –
Mxp-031.
Refer to the diagram opposite for location.
Secure the board in place (to prevent problems
due to vibration) using the clamping plate to
hold the card securely to the lower loop driver
location block.
A tab on the adaptor card fits into a slot in the
clamp.
Peripheral Interface Adaptor
Card
Note orientation
Clamp –use to hold Loop
Driver Cards and Peripheral
Interface Adaptor in place
Mounting Position for the Interface Adaptor
2.5.2 Routing Interface Card
Outputs to Routing Equipment –Clauses 7.9 and 8.9.
The Routing Interface Card (Mxp-032) provides monitored outputs for
connection to Fire Routing Equipment (Item E) and Fault Routing Equipment
(Item J) in accordance with EN54-2.
The card is
fitted to the
chassis using
4x M3 screws.
Refer to the
diagram
opposite.
Cables are
provided for
connection of a
local 24V DC
supply and
communications
connections.
Connect the DC
Supply from the
AUX output to
the connections
on TB4
observing
polarities.
Base Card
DC SUPPLY
Routing Interface
Communications
M3 Fixing
Screws
TB3
TB4
Mounting Position for the Routing Interface Card
Connect the communications cable between TB3 on the Base Card and TB4 on the routing
interface so that 'A' is connected to 'A' and 'B' to 'B'.
For further information, refer to Document 680-081.
4
The Mxp-034 modules must be configured using the PC CONFIG TOOL.
www.acornfiresecurity.com
www.acornfiresecurity.com

19
2.6 Wiring Installation
All electrical wiring installation work should be carried out in accordance with the code of practice or applicable
national standards appropriate to the country of installation.
To maintain electrical integrity of the SELV wiring on the input, output, loop and communications lines all SELV
wiring should be segregated from the LV mains wiring and be wired using cable with insulation suitable for the
application.
To minimise the effects of EMC interference all data wiring circuits should be wired with a twisted pair of
conductors with a cross sectional area suitable for the loading conditions.
In areas where cabling may come into contact with high frequency interference, such as portable radio
transceivers etc. the data wiring cable should be of a twisted pair construction within an overall screen. Care
should be taken to correctly terminate this screen, refer to the appropriate sections of this manual for further
information for each circuit type.
NB: Minimum / Maximum cable size for all external connections is limited to 0.5mm² / 2.5mm² (22-14AWG).
2.6.1 AC Mains Wiring
Route the high voltage mains AC wiring into the
enclosure at the upper left corner only. Keep the
AC wiring away from the circuit boards and all
other wiring.
FUSE
Brown
Green
LIVE
EARTH
NEUTRAL
Panel Wiring
Blue
3.15A
AC Mains terminations
The Mx-4800V employs two terminal blocks for
the AC Mains connections (one on each chassis
assembly) as per the Mx-4400V.
Must be
earthed
The panels must be connected to
the supply earth through the power
cable.
The mains input connector is shown in the
diagram opposite. Note the positions of the earth,
neutral and live terminal connections. These are
clearly marked on the label next to the connector.
The connector block contains an integral fuse
holder.
Secure the mains input wiring by tie wrap as close
to the terminal block as possible.
The fuses are rated as follows:
T 3.15A H 250V
Replace with correct rating and specification only.
Connect the Control Panel to the mains supply via
a readily accessible disconnect-device (Isolation
Switch) and suitable earth fault protection
incorporated in the building installation wiring. The
Mains cable should be 0.75mm2cable rated at
250V and fused via a 5A anti-surge fuse.
www.acornfiresecurity.com
www.acornfiresecurity.com

20
2.6.1.1 Cable Gland
The cable gland and any cord clamp bushing s used in routing the Mains cable through the
20mm knockout must have a minimum flame-retardant rating of 94HB.
Suggested glands and bushings are: -
Type
Gland IP65 –Brass M20, EExd / Eexe
Gland IP68 –Nylon 66 M20 Black, UL94V2
Bushing –Nylon 66 M20 Black, UL94V2
Manufacturer
Lappcable
Multicomp
Multipcomp
2.6.2 Battery Installation
The panel requires two 12V
batteries for standby operation.
The battery leads are connected
onto the base card via a two-part
plug and socket, as shown in the
diagram opposite.
Refer to the Specifications for
minimum and maximum battery
sizes allowed.
Base Card Terminations
BAT +
BAT –
AUX -
AUX +
Mx-4200V, Mx4400V & Mx4800V
Place the batteries in the bottom of the enclosure
and connect the ‘Red’ lead to the positive (+)
terminal of battery #1 and the ‘Black’ lead to the
negative (-) terminal of battery #2. Connect the
negative of battery #1 to the positive of battery #2
using the supplied link cable.
Ensure that the battery terminals do not short out
against any part of the enclosure, circuit board or
chassis plate.
+
-
+
-
+
-
#1
#2
RED
BLACK
Link Cable
Do not make the final battery connections until the installation wiring is completed and the
system is to be powered up.
Always connect the AC Mains input before connecting the battery.
New batteries require ‘top-charging’ before installation. Refer to Section 4.2.1.1 for a list of
recommended batteries.
www.acornfiresecurity.com
www.acornfiresecurity.com
Other manuals for MxPro4 Series
4
This manual suits for next models
6
Table of contents
Other Advanced Control Panel manuals
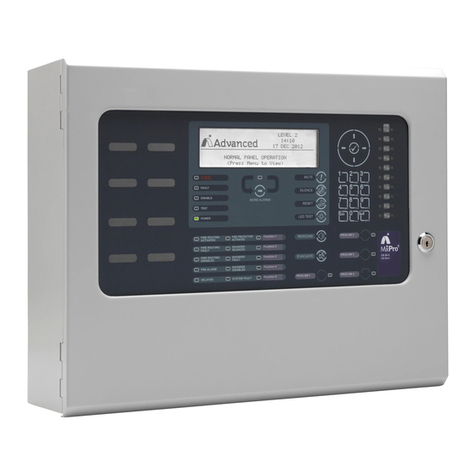
Advanced
Advanced MxPro 5 Installation and operating instructions
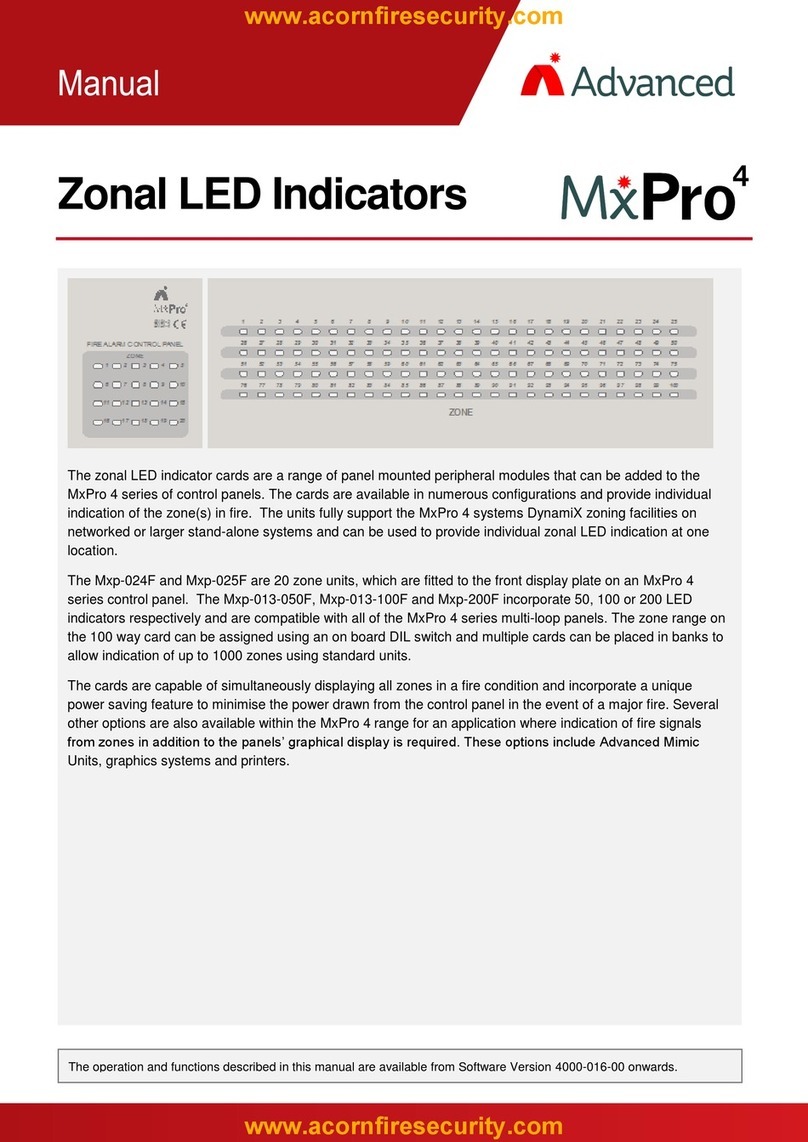
Advanced
Advanced Mx Pro 4 User manual
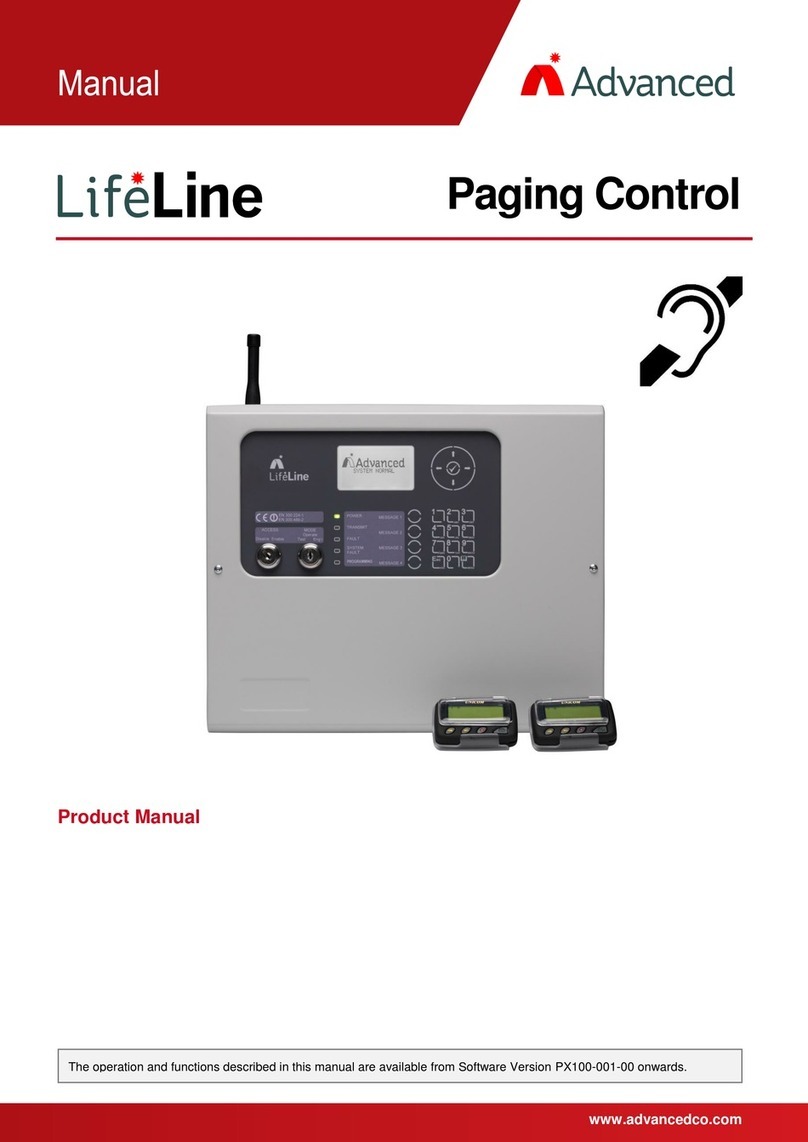
Advanced
Advanced LIFELINE Px-100 User manual
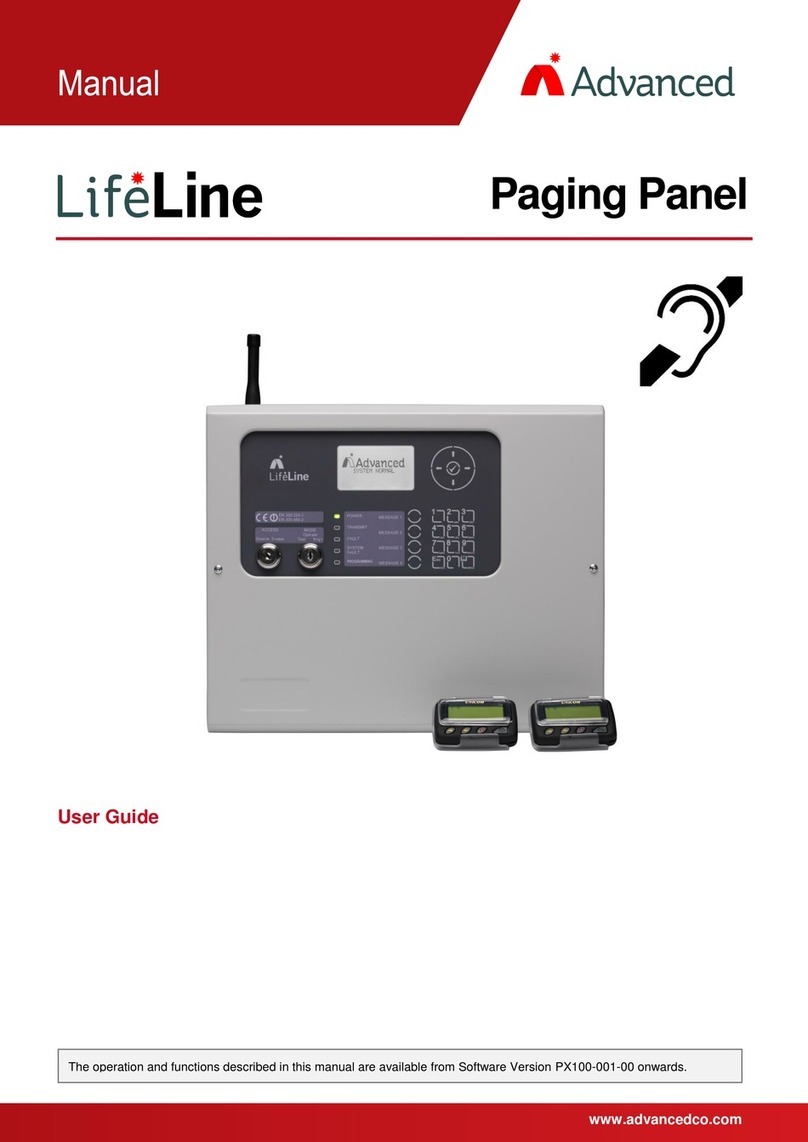
Advanced
Advanced LIFELINE Px-100 User manual
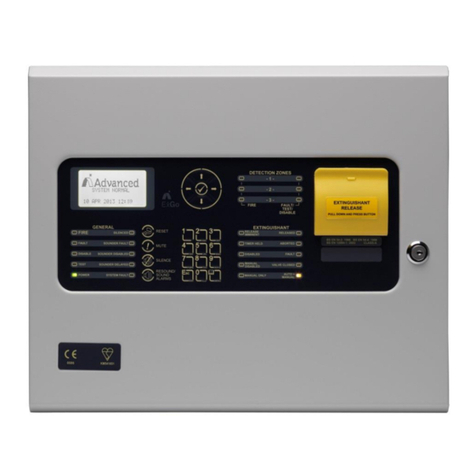
Advanced
Advanced Ex-3001 User manual
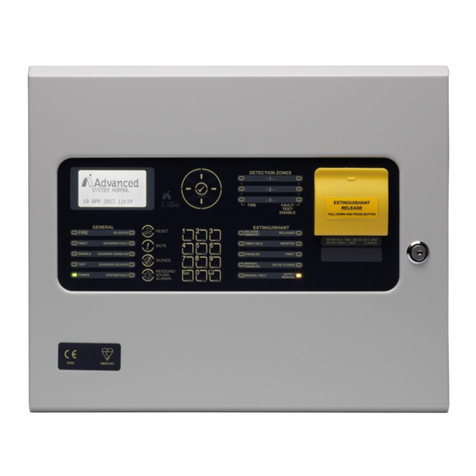
Advanced
Advanced ExGo Series User manual
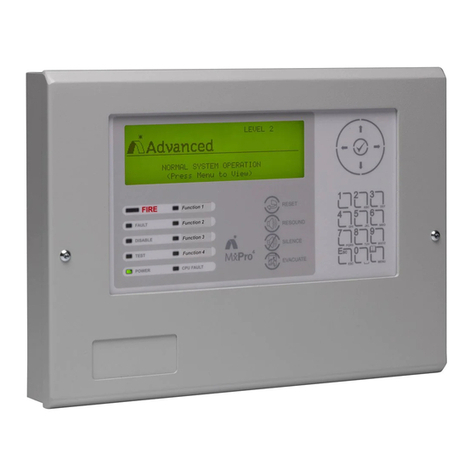
Advanced
Advanced MxPro4 Mx-4200 User manual
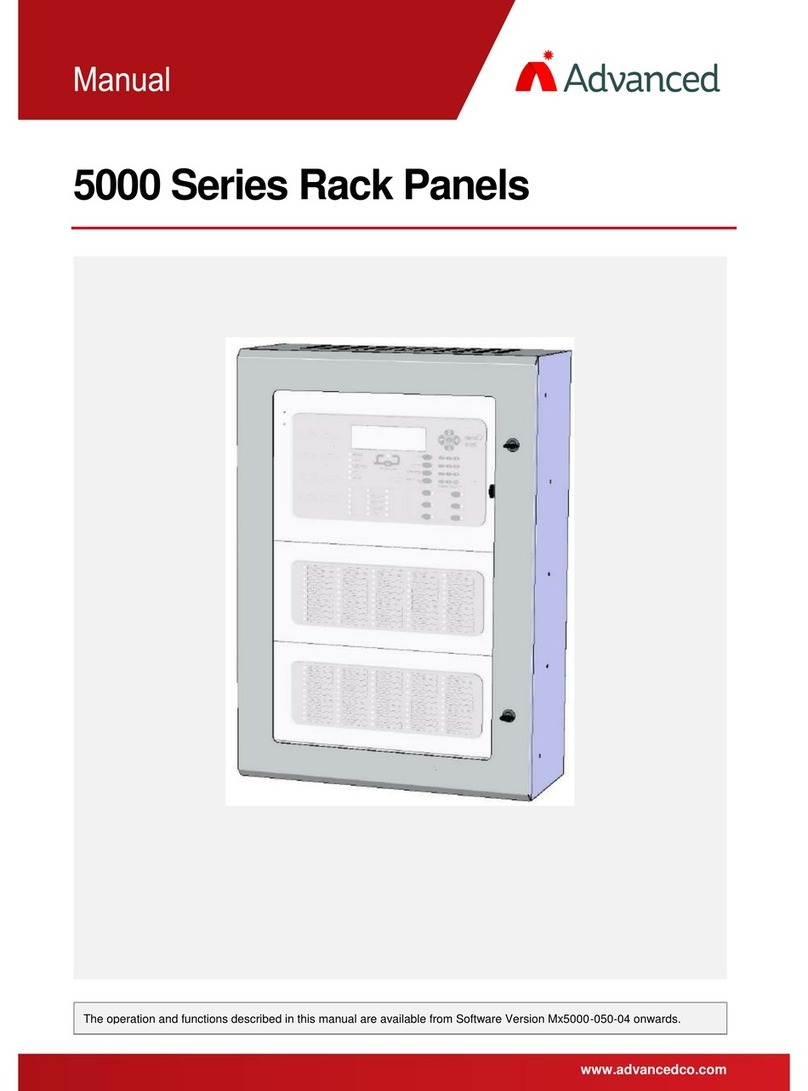
Advanced
Advanced Mx-5101xR User manual
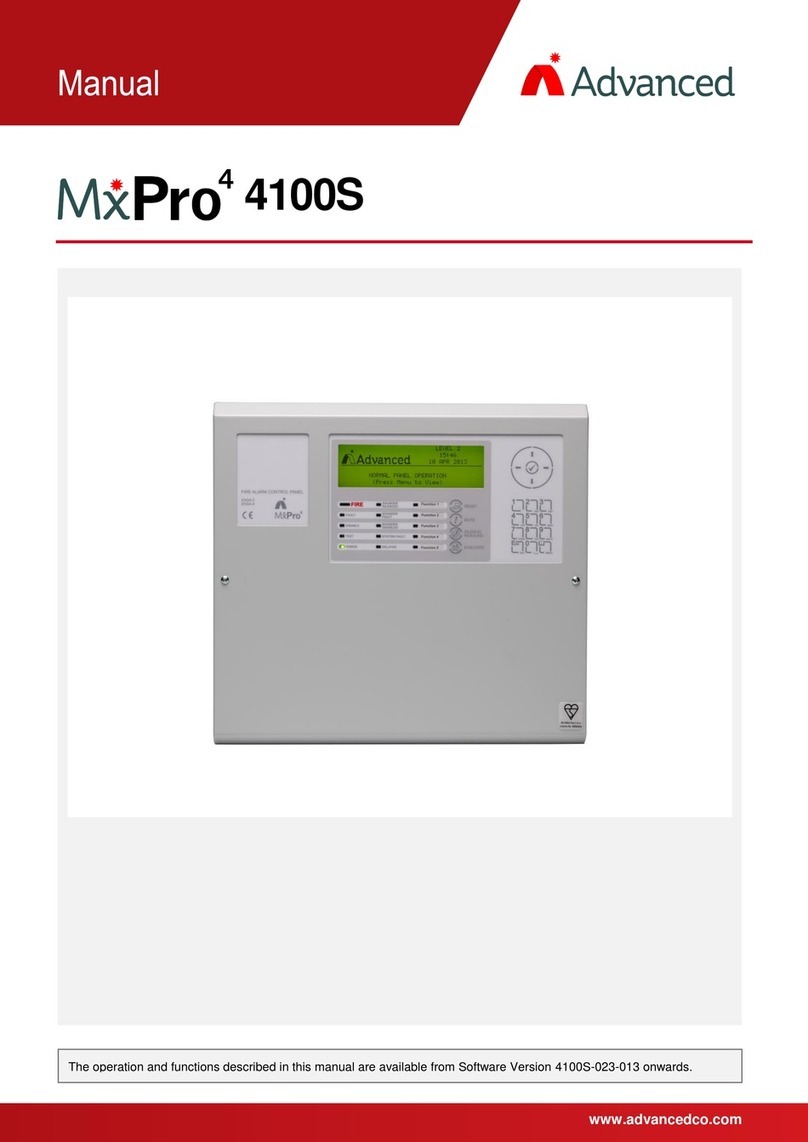
Advanced
Advanced MxPro 4 4100S User manual
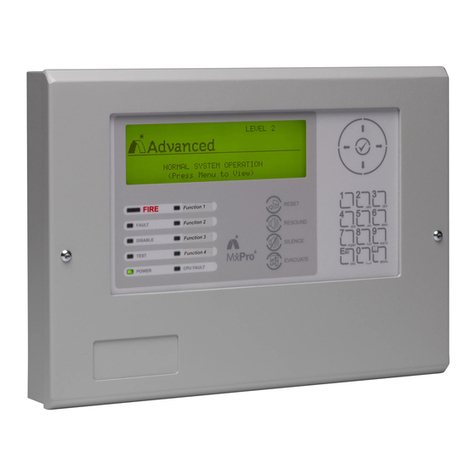
Advanced
Advanced MxPro4 Series User manual