Festo CLR User manual




















Other Festo Controllers manuals

Festo
Festo SFC-LACI Reference guide
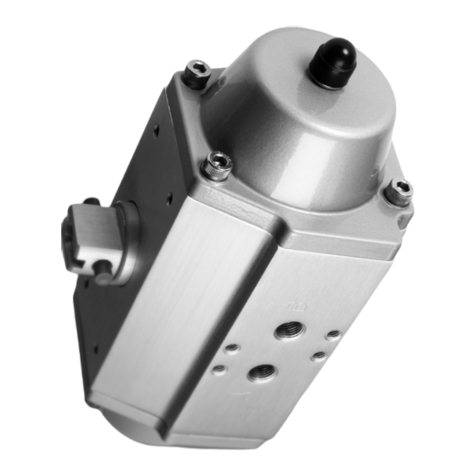
Festo
Festo DRD Series User manual
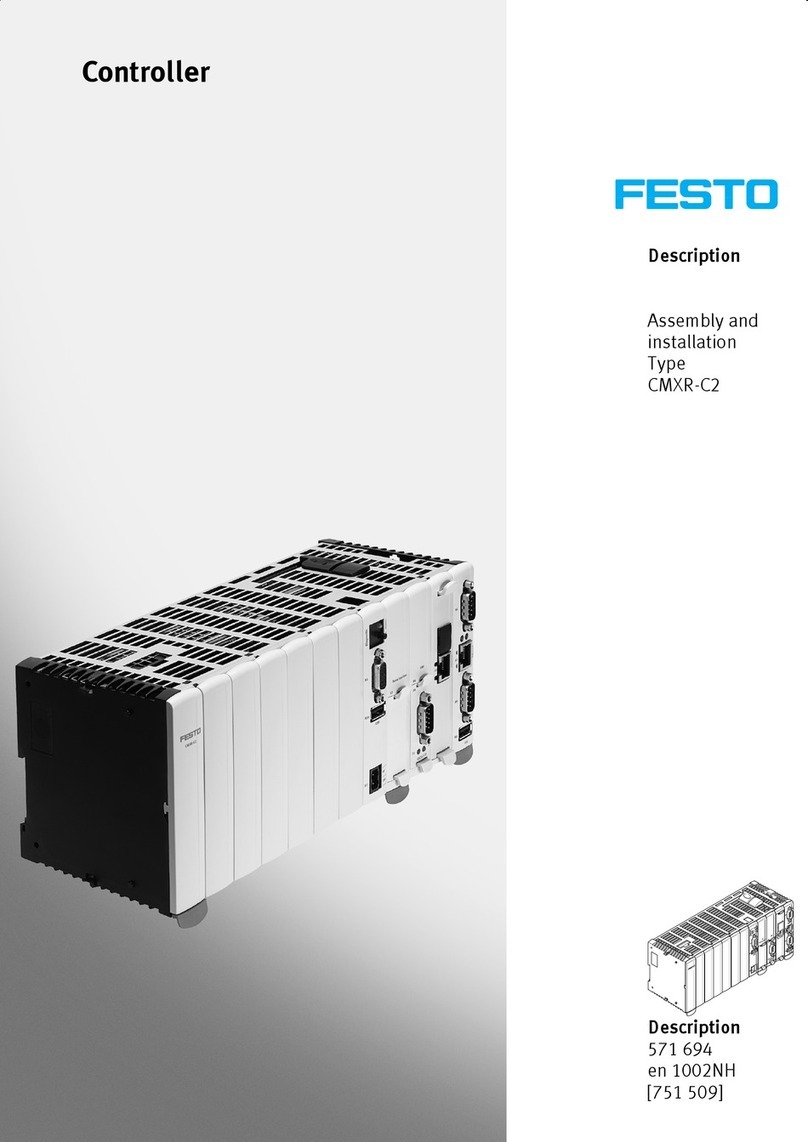
Festo
Festo CMXR-C2 Instruction Manual
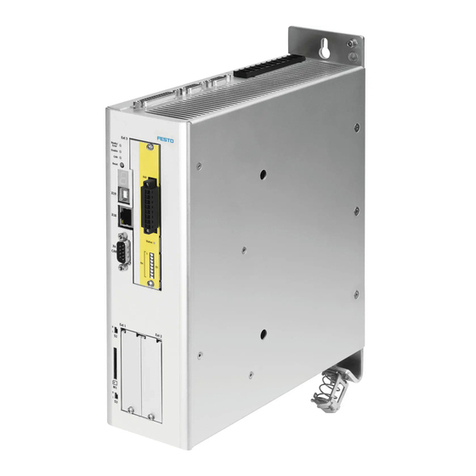
Festo
Festo CMMP-AS-***-M3 Series User manual
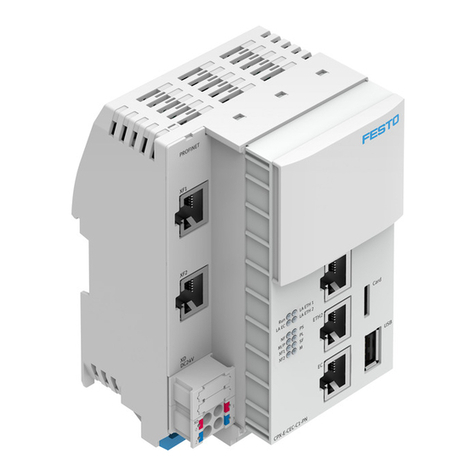
Festo
Festo CPX-E-CEC PN User manual
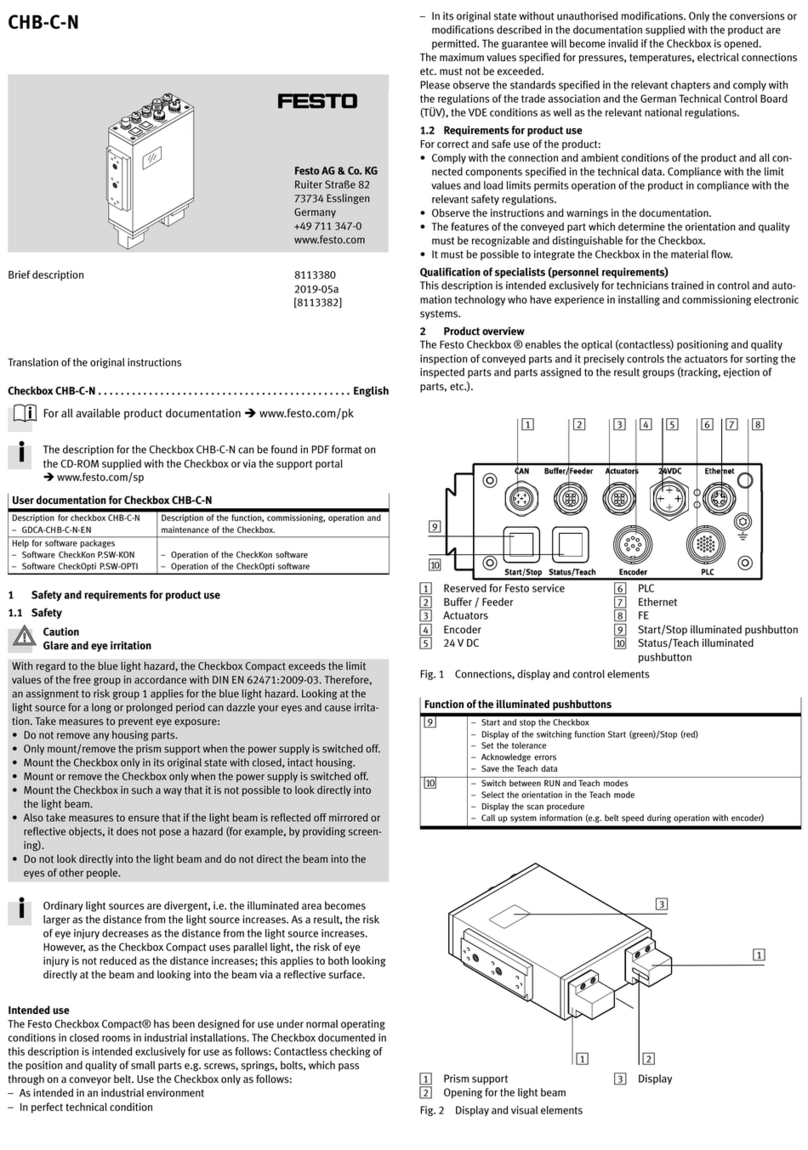
Festo
Festo CHB-C-N Parts list manual

Festo
Festo ELCC-TB User manual
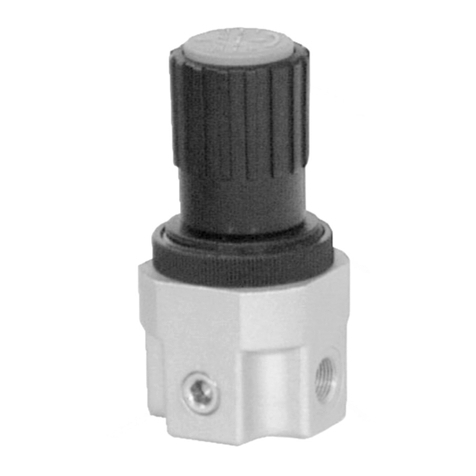
Festo
Festo LR G Series User manual
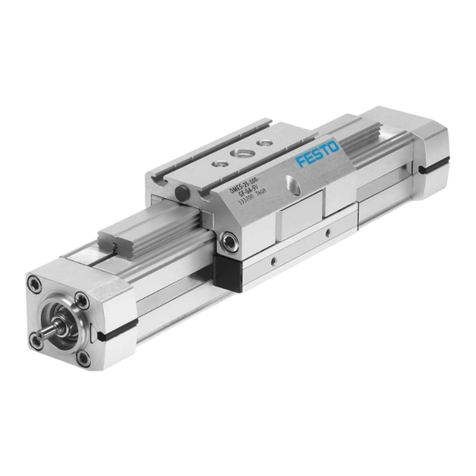
Festo
Festo DMES Series User manual
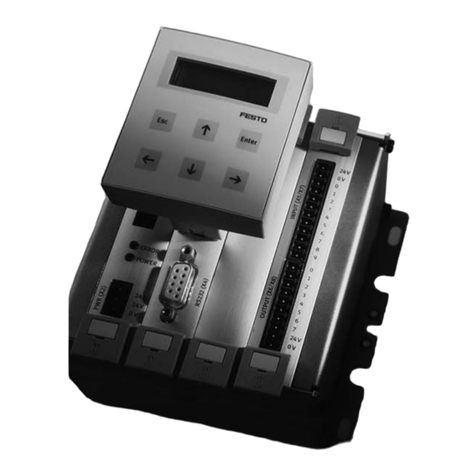
Festo
Festo SPC200 Series User manual
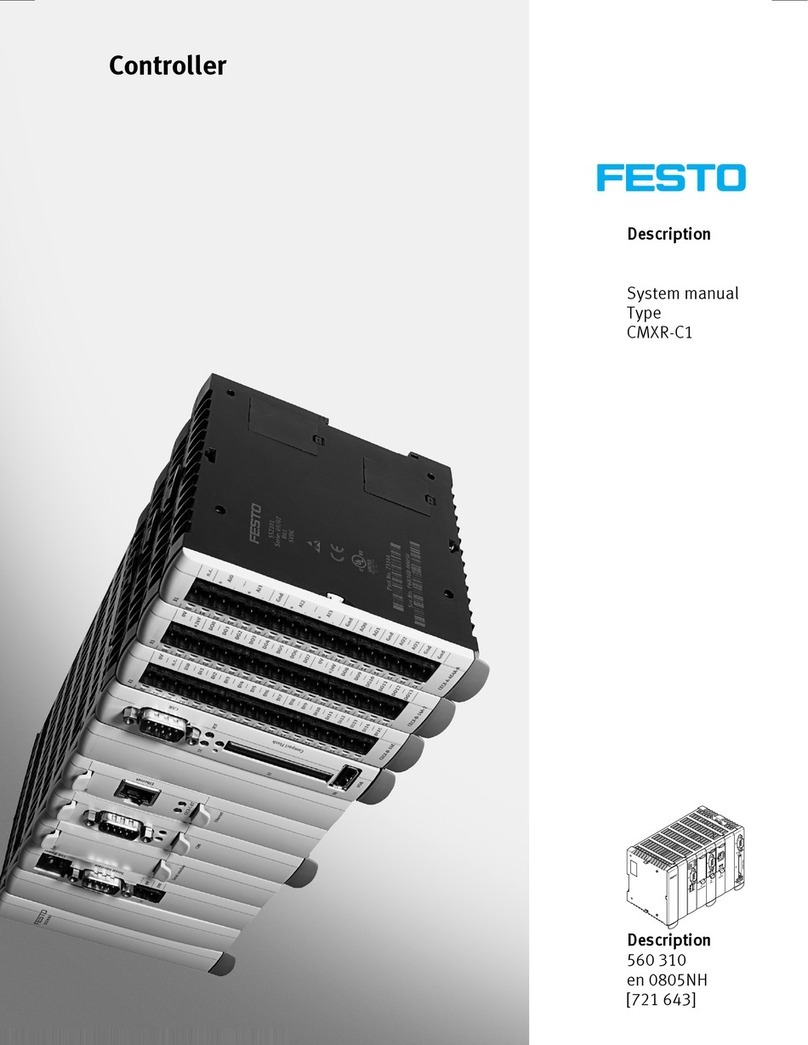
Festo
Festo CMXR-C1 User guide
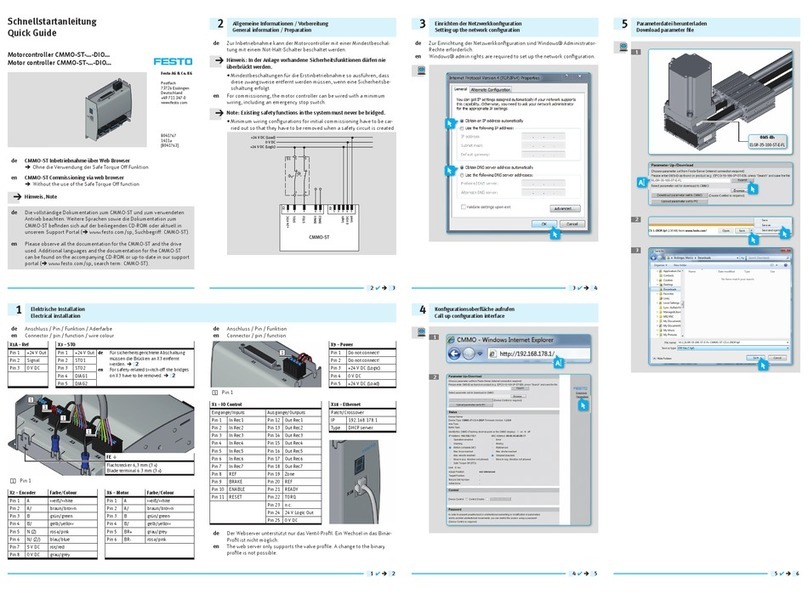
Festo
Festo CMMO-ST-...-DIO Series User manual
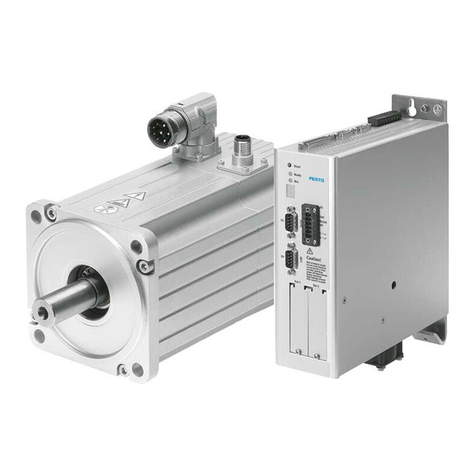
Festo
Festo CMMP-AS User manual

Festo
Festo SPC10-POT 2 Series User manual

Festo
Festo CPX-CMAX Operating and installation instructions
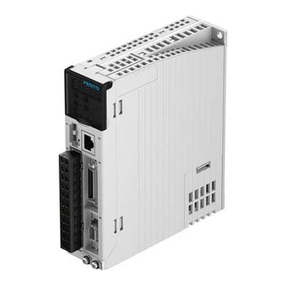
Festo
Festo CMMB-AS-0x User manual
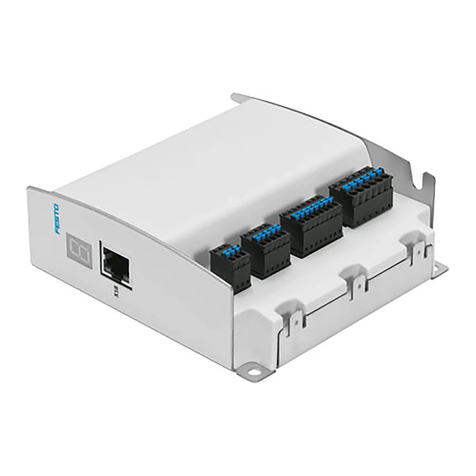
Festo
Festo CMMO-ST-C5-1-LKP User manual
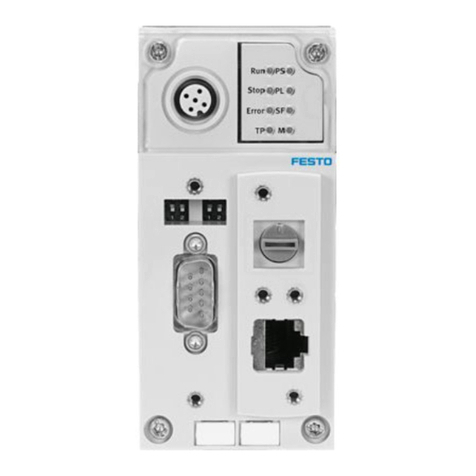
Festo
Festo CPX-CEC-C1 User manual
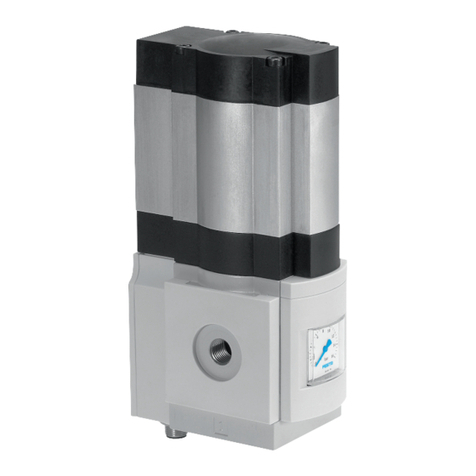
Festo
Festo MS6-LRE Parts list manual

Festo
Festo DFPD-Series User manual
Popular Controllers manuals by other brands

Kieback&Peter
Kieback&Peter DDC4200e instruction manual

STEEL-PLAY
STEEL-PLAY JVAMUL00153 user manual
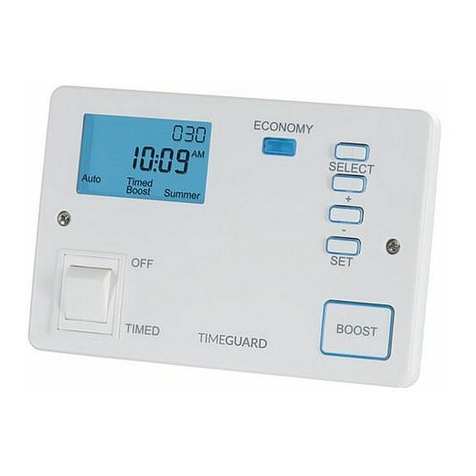
Timeguard
Timeguard TRTD7N Installation & operating instructions
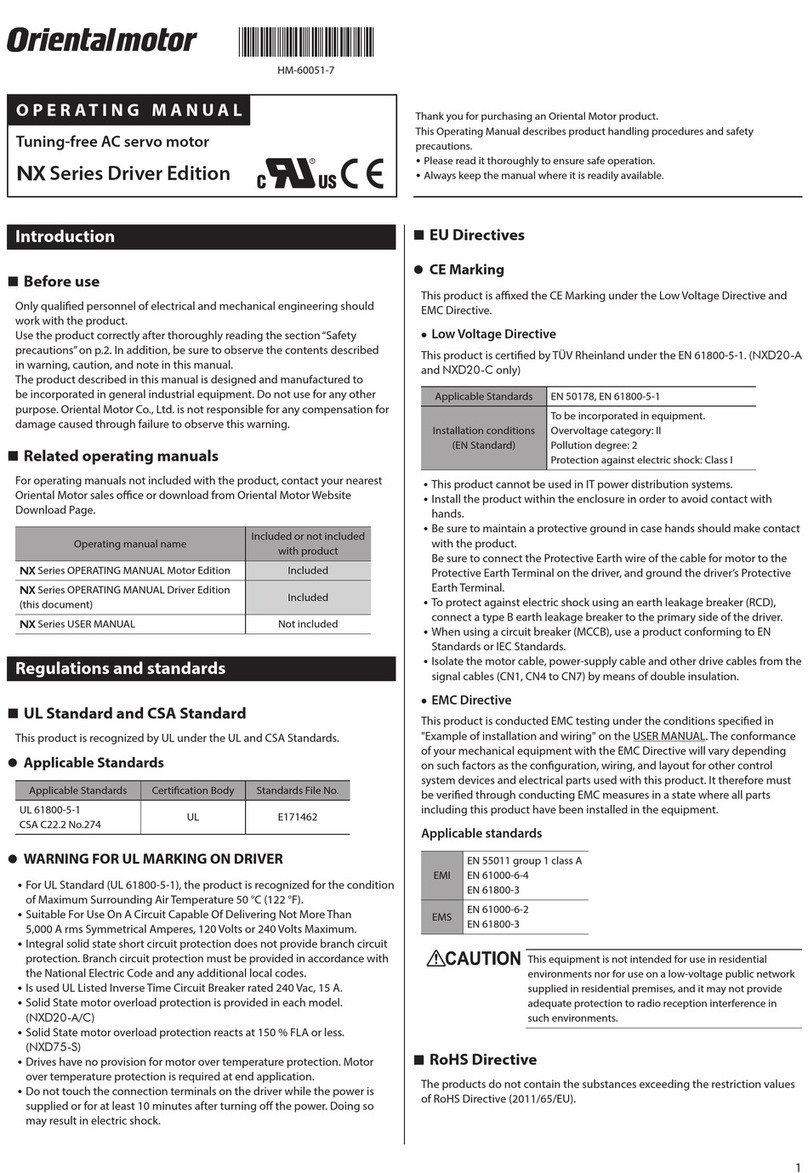
Oriental motor
Oriental motor NX Series operating manual
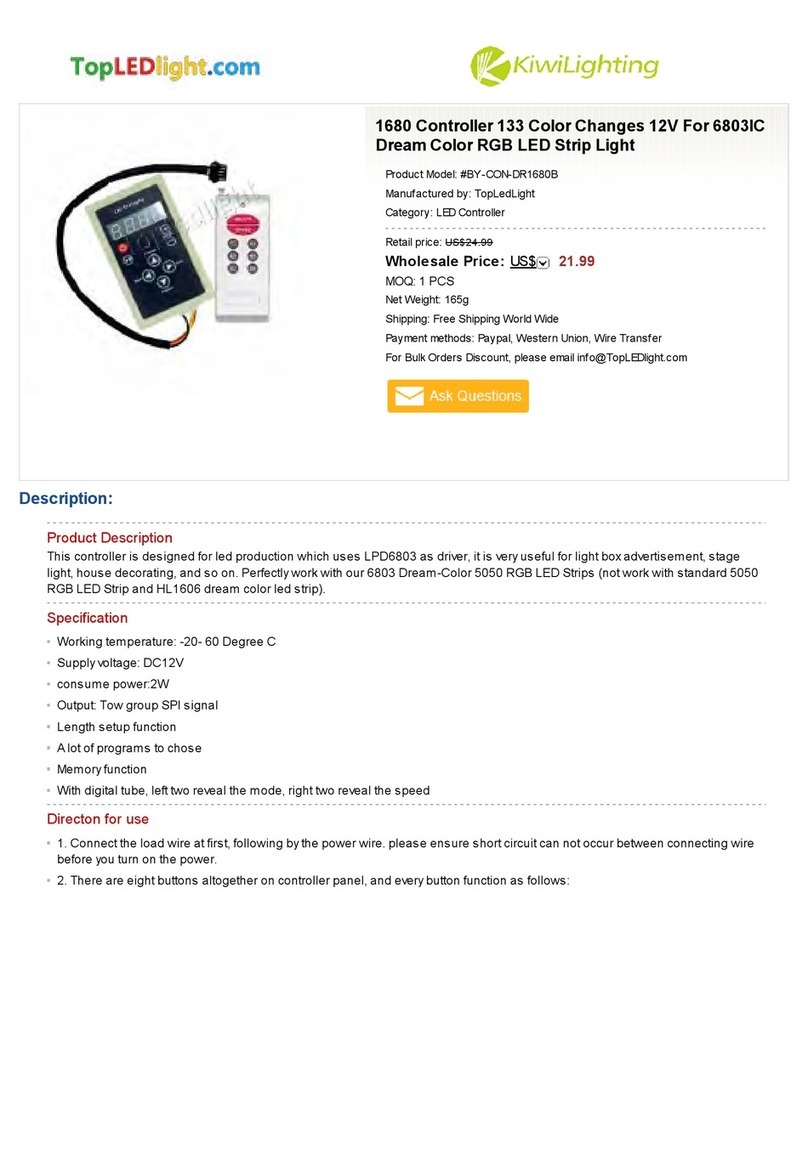
KiWi Lighting
KiWi Lighting TopLedLight BY-CON-DR1680B manual
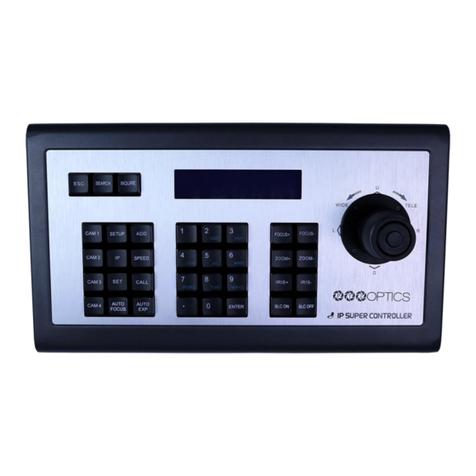
PTZOptics
PTZOptics PT-JOY-G2 Installation & operation manual