GE MULTILIN 269 MOTOR MANAGEMENT RELAY Series User manual

Instruction Manual
CANADA
215 Anderson Avenue, Markham, Ont., L6E 1B3
Tel: (905) 294-6222 Fax: (905) 201-2098
Internet: http://www.ge.com/edc/pm
269
MOTOR MANAGEMENT RELAY®
Firmware Rev.: 269P.D6.0.4
Manual P/N: 1601-0013-D3
Copyright 1999 GE Multilin

TABLE OF CONTENTS
i
1 INTRODUCTION
1.1 Motor Protection Requirements................1-1
1.2 269 Relay Features..................................1-1
1.3 Typical Applications.................................1-1
1.4 Order Code/Information..........................1-3
1.5 Technical Specifications...........................1-4
2 INSTALLATION
2.1 Physical Dimensions...............................2-1
2.2 Mounting.................................................2-6
2.3 External Connections...............................2-6
2.4 Control Power........................................2-12
2.5 Phase CT Inputs....................................2-12
2.6 Ground CT Input....................................2-15
2.7 Trip Relay Contacts...............................2-15
2.8 Alarm Relay Contacts............................2-16
2.9 Auxiliary Relay #1 Contacts...................2-16
2.10 Auxiliary Relay #2 Contacts.................2-16
2.11 RTD Sensor Connections.....................2-17
2.12 Emergency Restart Terminals..............2-18
2.13 External Reset Terminals.....................2-18
2.14 Analog Output Terminals
(Non-Isolated)......................................2-18
2.15 Programming Access Terminals...........2-18
2.16 Display Adjustment..............................2-19
2.17 Front Panel Faceplate..........................2-19
2.18 269 Drawout Relay..............................2-19
2.19 Meter Option Installation......................2-23
3 SETUP AND USE
3.1 Controls and Indicators............................3-2
3.2 269 Relay Display Modes........................3-6
3.3 ACTUAL VALUES Mode..........................3-6
3.3a Starts/Hour Timer...............................3-16
3.3b Time Between Starts Timer..................3-16
3.3c Cause of Last Trip................................3-16
3.3d Cause of Last Event.............................3-16
3.4 SETPOINTS Mode.................................3-16
3.5 HELP Mode..........................................3-41
3.6 TRIP/ALARM Mode...............................3-41
3.7 Phase CT and Motor Full Load Current
Setpoints..............................................3-44
3.8 Acceleration Time Setpoint....................3-44
3.9 Inhibits..................................................3-44
3.10 Unbalance Setpoints............................3-45
3.11 Ground Fault (Earth Leakage)
Setpoints............................................ 3-46
3.12 Undercurrent Setpoints........................3-49
3.13 Rapid Trip / Mechanical Jam Setpoints3-49
3.14 Short Circuit Setpoints.........................3-50
3.15 Immediate Overload Alarm Level
Setpoint...............................................3-50
3.16 Stator RTD Setpoints...........................3-50
3.17 Other RTD Setpoints............................3-51
3.18 Overload Curve Setpoints....................3-51
3.19 Thermal Capacity Alarm......................3-55
3.20 Thermal Memory.................................3-55
3.21 Emergency Restart..............................3-56
3.22 Resetting The 269 Relay......................3-57
3.23 269 Relay Self-Test..............................3-57
3.24 Statistical Data Features.....................3-58
3.25 Factory Setpoints................................3-58
3.26 Meter Option.......................................3-58
4 TESTING
4.1 Primary Injection Testing.........................4-1
4.2 Secondary Injection Testing.....................4-1
4.3 Phase Current Input Functions................4-1
4.4 Ground Fault Current Functions..............4-4
4.5 RTD Measurement Tests.........................4-4
4.6 Power Failure Testing..............................4-5
4.7 Analog Current Output............................4-5
4.8 Routine Maintenance Verification.............4-5
4.9 Dielectric Strength (Hi-Pot) Test...............4-5
5 THEORY OF OPERATION
5.1 Hardware................................................5-1
5.2 Firmware.................................................5-1
6 APPLICATION EXAMPLES
6.1 269 Relay Powered from One of Motor
Phase Inputs..........................................6-1
6.2 Loss of Control Power Due to Short Circuit
or Ground Fault......................................6-1
6.3 Example Using FLC Thermal Capacity
Reduction Setpoint.................................6-1
APPENDIX A
269 UNBALANCE EXAMPLE........................A-1
APPENDIX B
269 Thermal Model.......................................B-1
269 RTD Bias Feature...................................B-2
APPENDIX C
269 RTD Circuitry.........................................C-1
APPENDIX D
2φCT Configuration......................................D-1
APPENDIX E
Asymmetrical Starting Current......................E-1
APPENDIX F
269 Do's and Don'ts Checklist.......................F-1
APPENDIX G
Ground Fault and Short Circuit Instantaneous
Elements...............................................G-1
APPENDIX H
I. 269 CT Withstand......................................H-1
II. CT Size and Saturation.............................H-1
APPENDIX I
269 Commissioning Summary.......................I-1

TABLE OF CONTENTS
ii
GLOSSARY

1 INTRODUCTION
1-1
1.1 Motor Protection Requirements
Three phase AC motors have become standard in
modern industry. These motors are generally rugged
and very reliable when used within their rated limits.
Newer motors, however, tend to be designed to run
much closer to these operational limits and thus, there
is less margin available for any type of abnormal sup-
ply, load, or operating conditions.
In order to fully protect these motors, a modern protec-
tive device is required. Accurate stator and rotor ther-
mal modeling is necessary to allow the motor to
operate within its thermal limits and still give the maxi-
mum desired output. As well, other features can be
incorporated into a modern relay to fully protect the
motor, the associated mechanical system, and the
motor operator from all types of faults or overloads.
Motor thermal limits can be exceeded due to increased
current from mechanical overloads or supply unbal-
ance. Unbalance can greatly increase heating in the
rotor because of the large negative sequence current
components present during even small voltage unbal-
ances. A locked or stalled rotor can cause severe
heating because of the associated large currents drawn
from the supply. Many motor starts over a short period
of time can cause overheating as well. Phase-to-phase
and phase-to-ground faults can also cause damage to
motors and hazards to personnel. Bearing overheating
and loss of load can cause damage to the mechanical
load being driven by the motor.
The ideal motor protection relay should monitor the
rotor and stator winding temperatures exactly and shut
off the motor when thermal limits are reached. This
relay should have an exact knowledge of the tempera-
ture and proper operating characteristics of the motor
and should shut down the motor on the occurrence of
any potentially damaging or hazardous condition.
The GE Multilin Model 269 Motor Management Relay®
uses motor phase current readings combined with sta-
tor RTD temperature readings to thermally model the
motor being protected. The relay also monitors the
motor and mechanical load for faults and problems.
With the addition of a GE Multilin meter (MPM), the
269 may also monitor voltages and power and perform
several protection functions based on these values.
1.2 269 Relay Features
The GE Multilin Model 269 Motor Management Relay®
is a modern microcomputer-based product designed to
provide complete, accurate protection for industrial
motors and their associated mechanical systems. The
269 offers a wide range of protection, monitoring, and
diagnostic features in a single, integrated package. All
of the relay setpoints may be programmed in the field
using a simple 12-position keypad and 48 character
alphanumeric display. A built-in "HELP" function can
instruct the user on the proper function of each of the
programming keys and on the meaning of each dis-
played message.
One 269 relay is required per motor. Phase and
ground fault currents are monitored through current
transformers so that motors of any line voltage can be
protected. The relay is used as a pilot device to cause
a contactor or breaker to open under fault conditions;
that is, it does not carry the primary motor current.
All setpoints are stored in the 269 non-volatile memory
within the relay. Thus, even when control power is re-
moved from the 269, all relay setpoints and pre-trip
values will remain intact.
The 269 can provide one of various output signals for
remote metering or programmable controller attach-
ment. Analog signals of motor current as a percentage
of full load, hottest stator RTD temperature, percentage
of phase CT secondary current, motor thermal capac-
ity, or bearing temperature are available by simple field
programming. A total of four output relays are provided
on the 269, including a latched trip relay, an alarm re-
lay, and two auxiliary relays. All output relays may be
programmed via the keypad to trip on specific types of
faults or alarms.
When an output relay becomes active, the 269 will dis-
play the cause of the trip, and if applicable, the lock-out
time remaining. Pre-trip values of average and individ-
ual line motor current, unbalance, ground fault current,
and maximum stator RTD temperature are stored by
the 269 and may be recalled using the keypad.
The correct operation of the GE Multilin 269 relay is
continually checked by a built-in firmware self-test rou-
tine. If any part of the relay malfunctions under this
self-test, an alarm indication will tell the operator that
service is required.
1.3 Typical Applications
The many features of the 269 make it an ideal choice
for a wide range of motor protection applications. Ver-
satile features and controls allow the relay to protect
associated mechanical equipment as well as the motor.
The 269 should be considered for the following and
other typical uses:
1. Protection of motors and equipment from operator
abuse.
2. Protection of personnel from shock hazards due to
winding shorts or earth leakage current from
moisture.
3. Protection of gears, pumps, fans, saw mills, cut-
ters, and compressors from mechanical jam.

1 INTRODUCTION
1-2
Table 1-1Model 269 Relay Features
Protection Features
-Overloads
-Stator Winding Overtemperature (Alarm, High Alarm and Trip)
-Multiple Starts
-Short Circuit
-Locked Rotor
-Rapid Trip/Mechanical Jam
-Unbalance/Single Phasing
-Ground Fault (Alarm and Trip)
-Bearing Overtemperature (Alarm and Trip)
-Undercurrent (Alarm and Trip)
-Variable Lock-Out Time
- Phase Reversal (Meter Option)
Operational Features
-Microcomputer controlled
-Keypad programmable
-48 character alphanumeric display
-Built-in "HELP" function
-Eight selectable standard overload curves
-Continual relay circuitry self-check
Monitoring and Display Features
-Negative sequence phase current unbalance measurement
-Ground fault (earth leakage) current measurement
-Up to six stator RTD inputs
-Two additional RTD inputs
-Monitoring of motor ambient air temperature
-Display of all SETPOINTS or ACTUAL VALUES upon request
-Display of relay TRIP/ALARM and HELP messages
Communications and Control Features
-One latched, main trip relay
-One alarm relay
-Two auxiliary relays
-Emergency restart capability
-Pre-trip alarm warnings
-4-20mA output of motor current as a percentage of full load, motor thermal capacity, hottest stator RTD tem-
perature, percentage of phase CT secondary current, or bearing RTD
Statistical and Memory Features
-Recall of all pre-trip motor values
-Tamperproof setpoints stored in non-volatile memory
-Microcomputer "learns" motor inrush current
-Accumulation of motor running hours
Voltage and Power Metering (available with MPM)
-Display of 3 phase or line voltages, kWatts, kVars, Power Factor, and frequency.
-Protection features based on Voltage, Power Factor, kVars, and voltage sensed phase reversals.
-Pre-trip values of average voltage, kWatts, kVars, Power Factor, and frequency.
-Accumulated MegaWattHours.
4. Protection for loss of suction for pumps or loss of
air flow for fans using the undercurrent feature.
5. Protection of motor and load bearings from exces-
sive heat buildup due to mechanical wear.
6. Protection of motors operated in environments with
varying ambient temperatures.
7. Complete protection, allowing maximum motor
utilization with minimum downtime, for all AC mo-
tors.

1 INTRODUCTION
1-3
The model 269 relay is almost entirely field program-
mable. The information shown above must be speci-
fied when the relay is ordered, as these options are not
selectable in the field. Additional features can be made
available on special order by contacting the GE Multilin
factory.
** See Glossary for definitions
*CT information, failsafe code, and contact ar-
rangement must be specified for drawout relays
only; on standard 269's these features are field
selectable.
1.4 Order Code/Information

1 INTRODUCTION
1-4
1.5 Technical Specifications
Phase Current Inputs
conversion: calibrated RMS, sample time 2ms
range: 0.05 to 12 × phase CT primary amps set-
point
full scale: 12 × phase CT primary amps setpoint
accuracy: ± 0.5% of full scale
(0.05 to 2 × phase CT primary amps set-
point)
± 1.0% of full scale
(over 2 × phase CT primary amps set-
point)
Frequency: 20–400 Hz
Ground Fault Current Input
conversion: calibrated RMS, sample time 2ms
range: 0.1 to 1.0 × G/F CT primary amps set-
point (5 Amp secondary CT)
1.0 to 10.0 amps 50:0.025A (2000:1 ratio)
full scale: 1 × G/F CT primary amps setpoint
(5 Amp secondary CT)
10 amps (2000:1 CT)
accuracy: ± 4% of G/F CT primary amps setpoint
(5 Amp secondary CT)
± 0.3 amps primary (2000:1 CT)
Frequency: 20–400 Hz
Overload Curves
curves: 8 curves fixed shape
trip time accuracy: ± 1 sec. up to 13 sec.
± 8% of trip time over 13 sec.
detection level: ± 1% of primary CT amps
Unbalance
display accuracy:± 2 percentage points of true negative
sequence unbalance (In/Ip)
Running Hours Counter
accuracy: ± 1%
Relay Lock-out Time
accuracy: ± 1 minute with control power applied
± 20% of total lock-out time with no con-
trol power applied
Trip/Alarm Delay Times
accuracy: ± 0.5 sec. or 2% of total time, whichever
is greater with the exception of:
1. "INST."setpoints: 20–45ms
2. Ground Fault 0.5 Second delay: +/-
150 msec.
3. Ground Fault 250 msec delay: +75
msec, -150 msec.
4. Metering setpoints (Page 7): +/- 1.5sec
or 2% of total time
Differential Relay Input
relay response time: 100 msec. maximum (contact
closure to output relay activation)
RTD Inputs
sensor types: 10 OHM copper
100 OHM nickel
120 OHM nickel
100 OHM platinum
(specified with order)
display accuracy: ± 2 C
trip/alarm setpoint range: 0-200 °C
dead band: 3 C
maximum lead resistance:25% of RTD 0 °C resistance
Analog Current Output (4-20 mA standard)
PROGRAMMABLE
OUTPUT 0-1 mA 0-20 mA 4-20 mA
MAX LOAD 2000 Ω300 Ω300 Ω
MAX OUTPUT 1.01 mA 20.2 mA 20.2 mA
accuracy: ± 1% of full scale reading
polarity: terminal 58 ("-") must be at
ground potential (i.e. output is
not isolated)
Isolation: non-isolated, active source
Update Time: 250 ms max.
Communications
Type: RS485 2-wire, half duplex, isolated
Baud Rate: 300, 1200, 2400
Protocol: Subset of Modbus® RTU
Functions: Read/write setpoints (03/16),
Read actual values (03/04)
Relay Contacts
VOLTAGE MAKE/CARRY
CONTINUOUS MAKE/CARRY
0.2 sec BREAK
30 VDC 10 30 10
RESISTIVE 125 VDC 10 30 0.5
250 VDC 10 30 0.3
30 VDC 10 30 5
INDUCTIVE 125 VDC 10 30 0.25
(L/R=7ms) 250 VDC 10 30 0.15
RESISTIVE 120 VAC 10 30 10
250 VAC 10 30 10
INDUCTIVE 120 VAC 10 30 4
PF=0.4 250 VAC 10 30 3
CONFIGURATION FORM C NO/NC
CONTACT MATERIAL SILVER ALLOY
MINIMUM PERMISSIBLE LOAD 5 VDC, 100 mA
12 VAC, 100 mA
Switch Inputs
Type: dry contacts

1 INTRODUCTION
1-5
CT Burden Due to Connection of 269 Relay
CT INPUT BURDEN
(AMPS) (VA) (mΩ)
10.04 43
PHASE CT 40.5 31
(1A) 13 4.8 28
50.06 2.4
PHASE CT 20 12.5
(5A) 65 8.5 2.01
G/F CT 50.08 3
(5A) 10 0.3 3
G/F CT 0.025 0.435 696 Ω
(50:0.025) 0.1 3.29 329 Ω
0.5 50 200 Ω
CT Thermal Withstand
Phase CT & G/F 5 amp tap:3 × - continuous
6 × - 40 sec
12 × - 3 sec
G/F 50:0.025 mA 6 × - continuous
Control Power (Includes Tolerances)
frequency:50/60 Hz
24 VDC, range: 20-30 VDC
48 VDC, range: 30-55 VDC
120 VAC/125 VDC, range: 80-150 VAC/VDC
240 VAC/250 VDC, range: 160-300 VAC/VDC
max. power consumption: 20 VA
Voltage low ride-through time:
100ms (@ 120VAC/125VDC)
NOTE:Relay can be powered from either AC or DC
source. If Control Power input exceeds 250 V,
an external 3A fuse must be used rated to the
required voltage.
Fuse Specifications
T3.15A H 250V
Timelag high breaking capacity
Dielectric Strength
2200 VAC, 50/60 Hz for 1 sec.
GROUND (Terminal 42) to
Output Contacts (Terminals 29 through 40)
Control Power (Terminals 41 & 43)
Current Transformer Inputs (Terminals 72
through 83)
NOTE: If Hi-Pot tests are performed, jumper J201
beside terminal 43 should be placed in the "HI-
POT" position. Upon completion of Hi-Pot tests, the
jumper should be placed in the "GND" position.
See Fig. 4.3.
Type Tests
Dielectric Strength: 2.0 kV for 1 minute to relays,
CTs, power supply
Insulation Resistance:IEC255-5,500Vdc
Transients: ANSI C37.90.1 Oscillatory 2.5kV/1MHz
ANSI C37.90.1 Fast Rise 5kV/10ns
Ontario Hydro A-28M-82
IEC255-4 Impulse/High
Frequency Disturbance
Class III Level
Impulse Test: IEC 255-5 0.5 Joule 5kV
RFI: 50 MHz/15W Transmitter
EMI: C37.90.2 Electromagnetic Interference
@ 150 MHz and 450 MHz, 10V/m
Static: IEC 801-2 Static Discharge
Humidity: 95% non- condensing
Temperature: -25°C to +60°C ambient
Environment: IEC 68-2-38 Temperature/Humidity
Cycle
Dust/Moisture: NEMA 12/IP53
Ambient Temperature and Storage Temperature
-25°C to +60°C
Packaging
Shipping box: 11.40" x 7.50" x 16.00" (WxHxD)
290mm x 190mm x 410mm (WxHxD)
Ship weight: 3.5 kg
7.75 lb.
269 Plus drawout:
Shipping box: 13.25" x 12.50" x 20.50" (LxHxD)
340mm x 320mm x 520mm
Ship weight: 12 kg
26.4 lb.
Certifications
ISO: Manufactured to an ISO9001 certified program
UL: UL recognized under E83849
CSA: Approved under LR41286
CE: Conforms to IEC 947-1, IEC 1010-1
Overvoltage Category: II
Pollution Degree: 2
IP Code: 40X
Note: 269 Drawout does not meet CE compliance.
WARNING:HAZARD may result if the product is
not used for intended purposes.
This equipment can only be serviced
by trained personnel.

1 INTRODUCTION
1-6
MPM OPTION SPECIFICATIONS
PHASE CURRENT INPUTS
Conversion: true rms, 64 samples/cycle
CT input: 1A & 5A secondary
Burden: 0.2 VA
Overload: 20xCT for 1s, 100xCT for 0.2s
Range: 1-150% of CT pri
Frequency: up to 32nd harmonic
Accuracy: ± 1% of display
VOLTAGE INPUTS
Conversion: true rms, 64 samples/cycle
VT pri/Sec: direct or 120-72000:69-240
Input range: 20-600 VAC
Full scale: 150/600 VAC autoscaled
Frequency: up to 32nd harmonic
Accuracy: ± 1% of display
ANALOG OUTPUTS OUTPUT
0-1 mA (T1 Option) 4-20 mA (T20 Option)
MAX LOAD 2400 Ω600 Ω
MAX OUTPUT 1.1 mA 21 mA
Accuracy: ±2% of full scale reading
Isolation: 50V isolated, active source
MEASURED VALUES
PARAMETER ACCURACY (%
OF FULL SCALE) RANGE
VOLTAGE ±0.2% 20% TO 100% OF VT
kW ±0.4% 0-999,999.99 kW
kVar ±0.4% 0-999,999.99 kVar
kVA ±0.4% 0-999,999.99 kVA
kWh ±0.4% 0-999,999,999 kWh
PF ±1.0% ±0.00-1.00
FREQUENCY ±0.02Hz 20.00-70.00 Hz
CONTROL POWER
Input: 90 – 300 VDC or
70 – 265 VAC, 50/60 Hz
Power: nominal 10VA
maximum 20VA
Holdup: 100 ms typical (@ 120 VAC/125
VDC)
TYPE TESTS
Dielectric strength: 2.0 kV for 1 minute to relays,
CTs, VTs, power supply
Insulation resistance: IEC255-5,500Vdc
Transients: ANSI C37.90.1 Oscillatory
2.5kV/1MHz
ANSI C37.90.1 Fast Rise
5kV/10ns
Ontario Hydro A-28M-82
IEC255-4 Impulse/High
Frequency Disturbance
Class III Level
Impulse test: IEC 255-5 0.5 Joule 5kV
RFI: 50 MHz/15W Transmitter
EMI: C37.90.2 Electromagnetic Inter-
ference @ 150 MHz and 450
MHz, 10V/m
Static: IEC 801-2 Static Discharge
Humidity: 95% non-condensing
Temperature: -10°C to +60°C ambient
Environment: IEC 68-2-38 Tempera-
ture/Humidity Cycle
Dust/moisture: NEMA 12/IP53
PACKAGING
Shipping box: 8½" × 6" × 6" (L×H×D) 215cm ×
152cm × 152 cm (L×H×D)
Ship weight: 5 lbs/2.3 kg
CERTIFICATION
ISO: Manufactured to an ISO9001 certified
program
UL: Recognized under E83849
CSA: Recognized under LR41286
Note: It is recommended that all relays be powered
up at least once per year to avoid deterioration of
electrolytic capacitors in the power supply.
Due to updating technology, specifications may be improved with-
out notice.

2 INSTALLATION
2-1
2.1 Physical Dimensions
The 269 relay is contained in a compact plastic and
metal housing with the keypad, display, and all
indicators located on the front panel. The physical
dimensions of the 269 unit are given in Figure 2.1.
GE Multilin also provides phase and ground fault CTs
if required. Dimensions for these are shown in Figure
2.2a, Figure 2.2b, Figure 2.2c, and Figure 2.2d.
Note
:
Dimensions of a are for 100:5 to 1000:5 phase CT's;
for the dimensions of 50:5 and 75:5 CT's, consult
factory.
Figure 2.1 Physical Dimensions

2 INSTALLATION
2-2
Figure 2.2a Phase CT Dimensions

2 INSTALLATION
2-3
Figure 2.2b Ground CT (50:0.025) 3” and 5” window

2 INSTALLATION
2-4
Figure 2.2c Ground CT (50:0.025) 8” window

2 INSTALLATION
2-5
Figure 2.2d Ground CT (x:5) Dimensions

2 INSTALLATION
2-6
2.2 Mounting
The 269 should be positioned so that the display is
visible and the front panel keypad is accessible. A
cut-out is made in the mounting panel and the unit is
mounted as shown in Figure 2.3. Four washers and
10-32 × 3/8" mounting screws are provided.
Although the 269 circuitry is internally shielded, to
minimize noise pickup and interference the relay
should be placed away from high current conductors
or sources of strong magnetic fields. Connections to
the relay are made through terminal blocks and CTs
located on the rear of the unit.
2.3 External Connections
The connections made to the 269 relay will vary
depending on the programming of the unit. It is not
necessary to use all of the connections provided; a
minimal configuration would include supply power,
three phase current CT inputs and the Trip relay
contacts wired in series with the contactor control
relay or circuit breaker shunt trip coil. Connections to
these and the other terminals outlined below will be
explained in the following sections.
Figure 2.3 Relay Mounting

2 INSTALLATION
2-7
Figure 2.4, Figure 2.6, and Figure 2.7 show typical
connections to the 269 relay.
NOTE: The rear of the 269 relay shows output relay
contacts in their power down state. Figure 2.4, Figure
2.6, and Figure 2.7 show output relay contacts with
power applied, no trips or alarms, Factory
Configurations, i.e. TRIP - fail-safe, ALARM - non-fail-
safe, AUX.1 - non-fail-safe, AUX.2 - fail-safe). See
Figure 2.5 for a complete list of all possible output
relay contact states. See SETPOINTS page 5 for a
description of the RELAY FAILSAFE CODE.
Table 2-1 269 External Connections
Inputs
-Supply Power L(+), G, N(–) - universal AC/DC
supply
-Phase CTs
-Ground Fault CTs (core balance CT)
-6 Stator RTDs
-2 additional RTDs
-Emergency Restart keyswitch
-External Reset pushbutton
-Programming Access jumper or keyswitch
-Meter Communication Port
Outputs
-4 Sets of Relay Contacts (NO/NC)
-Programmable Analog Current Output Terminals
WARNING: HAZARD may result if the product is
not used for intended purposes. This
equipment can only be serviced by
trained personnel.

2 INSTALLATION
2-8
Figure 2.4 Relay Wiring Diagram (AC Control Power)

2 INSTALLATION
2-9
Figure 2.5 Output Relay Contact States
WARNING: In locations where system voltage
disturbances cause voltage levels to dip below the
range specified in the Specifications (1.5), any relay
contact programmed failsafe may change state.
Therefore, in any application where the "process" is
more critical than the motor, it is recommended that
the trip relay contacts be programmed non-failsafe. In
this case, it is also recommended that the AUX2
contacts be monitored for relay failure. If, however,
the motor is more critical than the "process," then the
trip contacts should be programmed failsafe.

2 INSTALLATION
2-10
Figure 2.6 Relay Wiring Diagram (Two Phase CTs)

2 INSTALLATION
2-11
Figure 2.7 Relay Wiring Diagram (DC Control Power)
Table of contents
Other GE Relay manuals
Popular Relay manuals by other brands
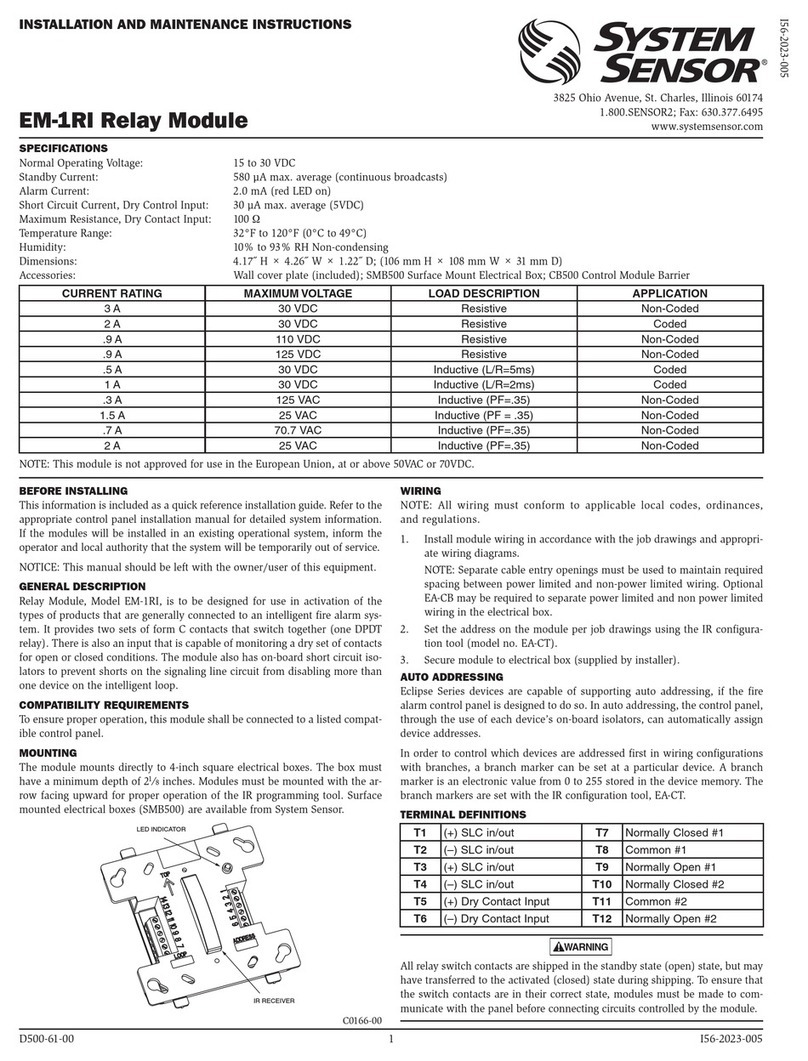
System Sensor
System Sensor EM-1RI Installation and maintenance instructions
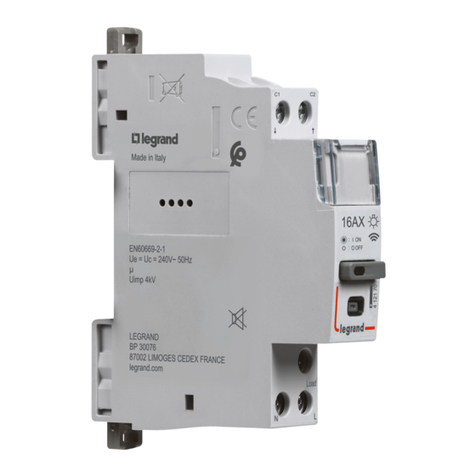
LEGRAND
LEGRAND 4 121 70 quick start guide
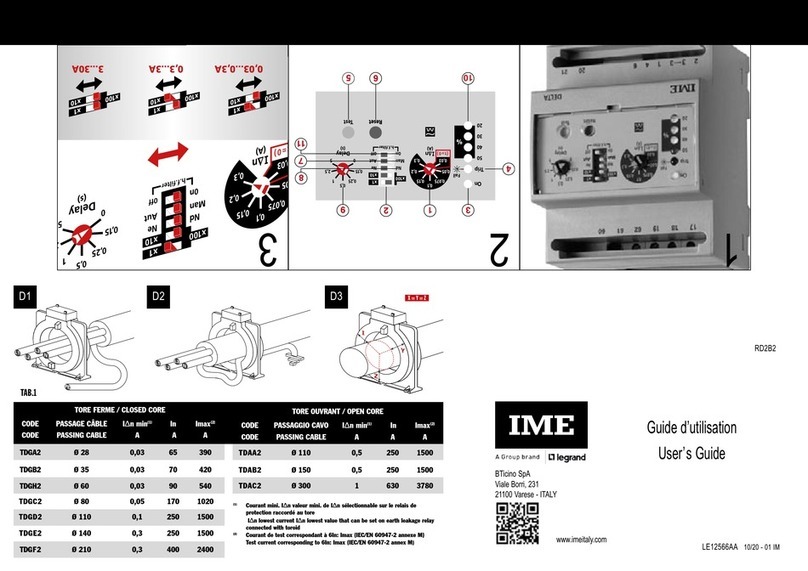
LEGRAND
LEGRAND IME DELTA TDGA2 user guide
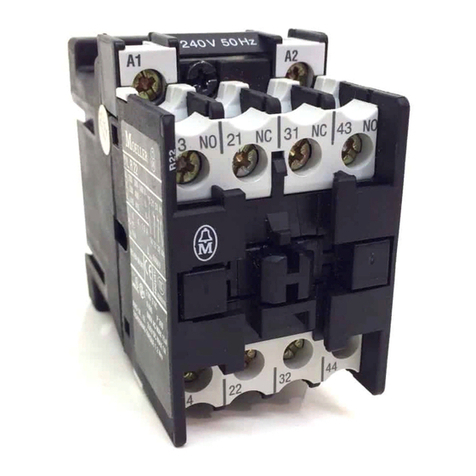
Moeller
Moeller DILR Series installation instructions
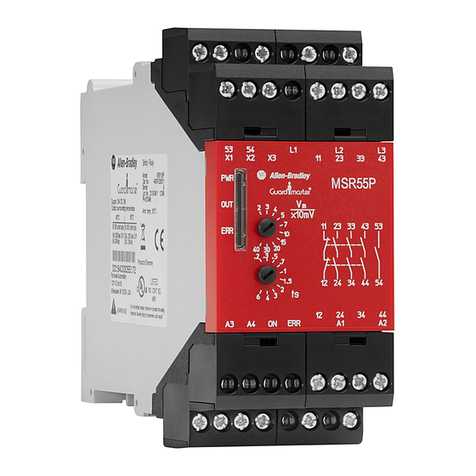
Rockwell Automation
Rockwell Automation Allen-Bradley GuardMaster MSR55P Back EMF... user manual

FANOX
FANOX D30 quick start guide
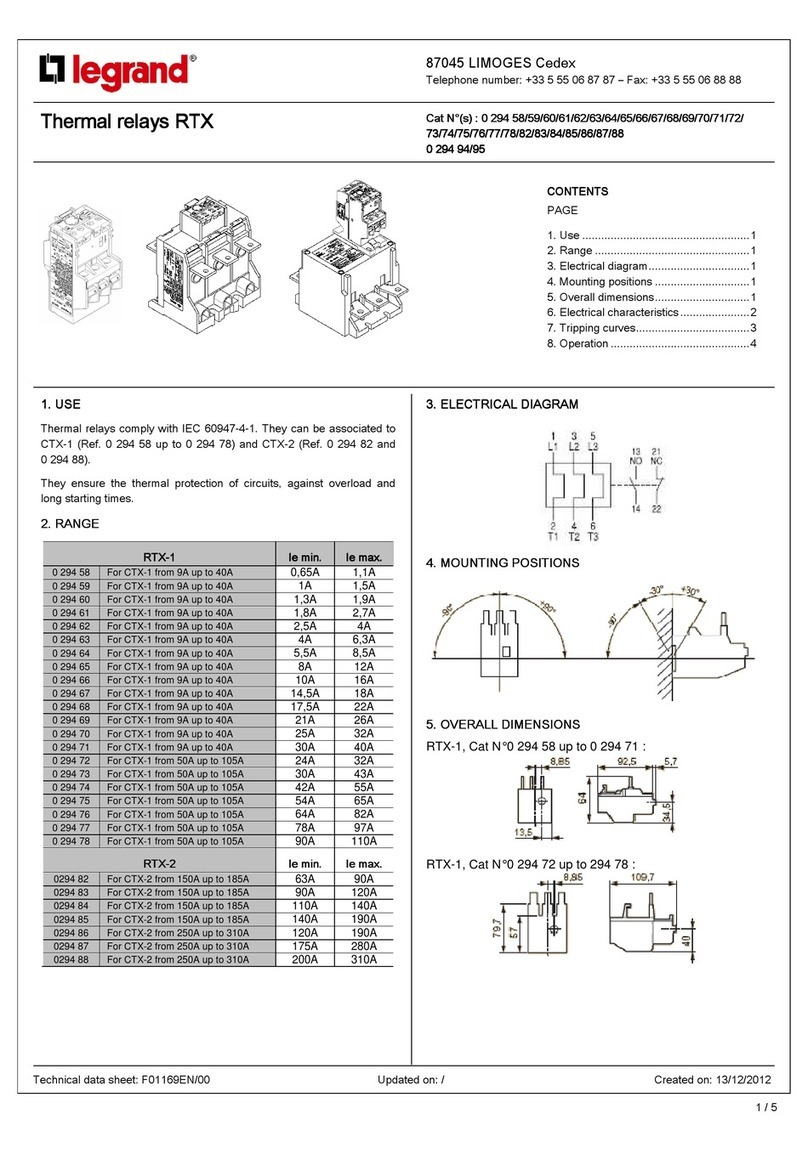
LEGRAND
LEGRAND RTX Series Technical data sheet

Perenio
Perenio PEHWE20 quick start guide

Hella marine
Hella marine 5XA 998 572-001 Installation & operating instructions
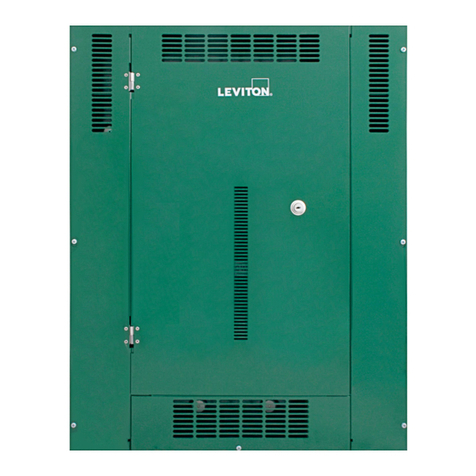
Leviton
Leviton GreenMAX R16TC-100 manual

Sensitron
Sensitron STS3REL instruction manual
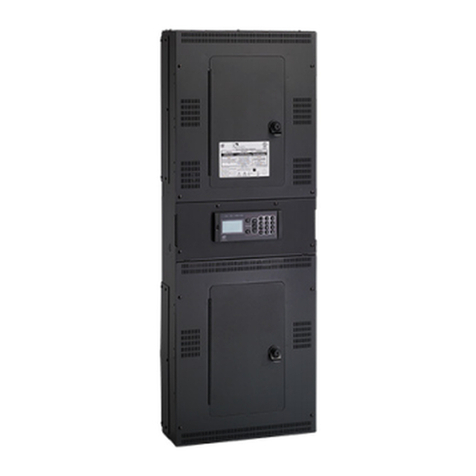
ETC
ETC Unison Echo ERP-FT Series installation manual