GE PACE5000 User manual

GE
Sensing & Inspection Technologies
Pressure Automated Calibration Equipment
User manual K0443
PACE5000
PACE6000
g

© The General Electric Company. All rights reserved

K0443 Issue No. 3 i
Introduction
This technical manual provides operating instructions for the PACE Pneumatic Pressure
Controllers.
The features shown and described in this manual may not be available on some models.
Safety
The manufacturer has designed this equipment to be safe when operated using the
procedures detailed in this manual. Do not use this equipment for any other purpose than
that stated.
This publication contains operating and safety instructions that must be followed to ensure
safe operation and to maintain the equipment in a safe condition. The safety instructions
are either warnings or cautions issued to protect the user and the equipment from injury or
damage.
Use suitably qualified * technicians and good engineering practice for all procedures in this
publication.
Pressure
Do not apply pressures greater than the maximum working pressure to the equipment.
Toxic Materials
There are no known toxic materials used in construction of this equipment.
Maintenance
The equipment must be maintained using the procedures in this publication. Further
manufacturer’s procedures should be carried out by authorized service agents or the
manufacturer’s service departments.
Technical Advice
For technical advice contact the manufacturer.
* A qualified technician must have the necessary technical knowledge, documentation,
special test equipment and tools to carry out the required work on this equipment.

K0443 Issue No. 3 ii
Abbreviations
The following abbreviations are used in this manual; the abbreviations are the same in the
singular and plural.
abs Absolute
a.c. Alternating current
ALT Altitude
BSP British pipe thread
CAS Calculated airspeed
CSK Countersunk
d.c. Direct current
DPI Digital Pressure Instrument
e.g. For example
etc. And so on
Fig. Figure
ft Foot
g Gauge
Hg Mercury
HTS High tensile steel
Hz Hertz
IAS Indicated airspeed
i.e. That is
IEC International Electrotechnical Commission
IEEE 488 Institute of Electrical and Electronic Engineers standard 488 data
in Inch
kg Kilogram
kts/kn knot
LCD Liquid crystal display
mMetre
mA Milliampere
max Maximum
mbar Millibar
min Minute or minimum
mm Millimetre
mV Millivolts
MWP Maximum working pressure
No. Number
NPT National Pipe Thread
PACE Pressure Automated Calibration Equipment
Para. Paragraph
PDCR Pressure transducer
PED Pressure Equipment Directive
psi Pounds per square inch
PTX Pressue transmitter

K0443 Issue No. 3 iii
ROC Rate of Climb
RS232 Serial communications data standard
SCPI Standard Commands for Programmable Instruments
UUT Unit under test
VVolts
VFC Volts-free contact
+ve Positive
-ve Negative
°C Degrees Celsius
Associated publications
K0447 PACE 5000/6000 User Guide and Safety Instructions
K0450 PACE Series Calibration Manual
K0476 Pressure Control Module User Guide and Safety Instructions
K0472 Remote Communications Manual
K0469 Heritage Communications Manual - Instrument Emulation
Symbols
The equipment contains the following symbols to identify hazards.
This equipment meets the requirements of all relevant European safety directives.
The equipment carries the CE mark.
This symbol, on the instrument, indicates that the user should refer to the user
manual.
This symbol, on the instrument, indicates do not throw-away in domestic bin,
hazardous material, dispose correctly in accordance with local regulations.

K0443 Issue No. 3 iv
Pressure units and conversion factors
Unit Conversion
To convert FROM pressure VALUE 1 in pressure UNITS 1
TO pressure VALUE 2 in pressure UNITS 2, calculate as follows:
VALUE 2 = VALUE 1 x FACTOR 1
FACTOR 2
Note:
The PACE instrument contains selectable pressure units and user defined units. Use the conversion
factors to calculate a user defined unit from the table above. Refer to the data sheets SDS0001 or
SDS0008 for the list of selectable pressure units.
Pressure units Factor (hPa) Pressure units Factor (hPa)
mbar 1.0 cmH2O @ 20°C 0.978903642
bar 1000.0 mH2O @ 20°C 97.8903642
Pa (N/m2)0.01 kg/m20.0980665
hPa 1.0 kg/cm2980.665
kPa 10.0 torr 1.333223684
MPa 10000.0 atm 1013.25
mmHg @ 0°C 1.333223874 psi 68.94757293
cmHg @ 0°C 13.33223874 lb/ft20.4788025898
mHg @ 0°C 1333.223874 inH2O @ 4°C 2.4908891
inHg @ 0°C 33.86388640341 inH2O @ 20°C 2.486413
mmH2O @ 4°C 0.0980665 inH20 @ 60°F 2.487641558
cmH2O @ 4°C 0.980665 ftH2O @ 4°C 29.8906692
mH2O @ 4°C 98.0665 ftH2O @ 20°C 29.836983
mmH2O @ 20°C 0.097890364 ftH20 @ 60°F 29.8516987

K0443 Issue No. 3 v
CONTENTS
Section Title Page
1Description...................................................................................................................... 1-1
1.1 Introduction ....................................................................................................................1-1
2Installation....................................................................................................................... 2-1
2.1 Packaging........................................................................................................................ 2-1
2.2 Packaging for Storage and Transportation..................................................... 2-1
2.3 Preparation for Use..................................................................................................... 2-1
2.4 Pneumatic connections ............................................................................................ 2-2
2.5 Rack-mount option ..................................................................................................... 2-7
2.6 Electrical connections................................................................................................ 2-8
3OPERATION...................................................................................................................... 3-1
3.1 Preparation .....................................................................................................................3-1
3.2 Power-up Sequence ................................................................................................... 3-2
3.3 Measure Mode............................................................................................................... 3-3
3.4 Control Mode.................................................................................................................. 3-5
3.5 Operation and Example Procedures................................................................... 3-8
3.6 Global Set-up ................................................................................................................. 3-12
3.7 Barometric Reference Option................................................................................. 3-13
3.8 Supervisor Set-up ........................................................................................................ 3-14
3.9 Instrument Status ........................................................................................................ 3-15

K0443 Issue No. 3 vi
4MAINTENANCE............................................................................................................... 4-1
4.1 Introduction ....................................................................................................................4-1
4.2 Visual inspection .......................................................................................................... 4-1
4.3 Cleaning ........................................................................................................................... 4-1
4.4 Test ..................................................................................................................................... 4-1
4.5 Calibration....................................................................................................................... 4-1
4.6 Replacement parts...................................................................................................... 4-2
4.7 Fuse replacement........................................................................................................ 4-2
4.8 Filter replacement ....................................................................................................... 4-4
4.9 Pressure module replacement .............................................................................. 4-5
5TESTING AND FAULT FINDING................................................................................. 5-1
5.1 Introduction ....................................................................................................................5-1
5.2 Standard Serviceability Test ................................................................................... 5-1
5.3 Fault Finding...................................................................................................................5-2
5.4 Approved Service Agents ......................................................................................... 5-3
6REFERENCE AND SPECIFICATION .......................................................................... 6-1
6.1 Installation notes.......................................................................................................... 6-1
6.2 Operational Requirements ...................................................................................... 6-4
6.3 Icons.................................................................................................................................. . 6-6
6.4 Measure Set-up............................................................................................................. 6-9
6.5 Control Set-up................................................................................................................ 6-10
6.6 Global Set-up ................................................................................................................. 6-11
6.7 Supervisor Set-up ........................................................................................................ 6-12
6.8 Options.............................................................................................................................. 6-15

K0443 Issue No. 3 vii
6.8 Calibration....................................................................................................................... 6-28
6.9 Communications - Instrument Emulation....................................................... 6-29
6.10 Specification...................................................................................................................6-29
6.11 Return Goods/Material Procedure....................................................................... 6-29
6.12 Packaging Procedure................................................................................................. 6-30

K0443 Issue No. 3 viii
intentionally left blank

PACE Pressure Controller User Manual
K0443 Issue No. 3 1 - 1
1Description
1.1 Introduction
The PACE5000 single-channel and PACE6000 single/dual-channel, Pressure Automated
Calibration Equipment measures and controls pneumatic pressures and displays, on a
touch-screen, the pressure measurement and controller status. The touch-screen enables
selections and settings in both measure and control modes. The instrument can be
operated remotely through communication interfaces.
Figure 1-1 PACE5000 General view
Figure 1-2 PACE6000 General view
The rear of the instrument houses all the electrical and pneumatic output and input
connections. The electrical connections provide an a.c. power supply, serial and parallel
communication interfaces, d.c. output and logic input and output. The system pneumatic
controller module contains a positive and negative pressure supply port, an output port,
vent port and reference port.

1 Description
K0443 Issue No. 3 1 - 2
The instrument can be mounted in a standard 19 inch rack system (rack-mount option).
Figure 1-3 PACE5000 Rear view
Figure 1-4 PACE6000 Rear view
Options available for the PACE5000 and PACE6000 are detailed in datasheet SDS0001
(PACE5000) and SDS00008 (PACE6000).
Further information and notes on applications are available in section 6 of this manual and
on the GE Sensing & Inspection web site at www.gesensinginspection.com.

PACE Pressure Controller User Manual
K0443 Issue No. 3 2 - 1
2 Installation
2.1 Packaging
On receipt of the PACE5000 or PACE6000 check the contents of the packaging against the
following list:
Packaging List
i) PACE5000 or PACE6000 Pressure Controller.
ii) Cable, power supply.
iii) User guide and CD (UD-0001) containing the full documentation suite.
iv) Pneumatic Control Module blanking plate (keep this plate for future use).
CAUTIONS:
1. AFTER REMOVING ACONTROL MODULE, USE ABLANKING PLATE TO KEEP THE FLOW OF COOLING AIR.
2. AFTER UNPACKING AN INSTRUMENT THAT HAS BEEN IN COLD CONDITIONS ALLOW TIME TO STABILISE
AND ANY CONDENSATION TO EVAPORATE.
2.2 Packaging for Storage or Transportation
To store the instrument or to return the instrument* for calibration or repair carry out the following
procedures:
1. Pack the instrument as detailed in section 6.8, Reference and Specification.
2. Return the instrument for calibration or repair complete the return goods procedure
detailed in section 6.8, Reference and Specification.
* This procedure also applies to the pressure control module as a separate item.
2.3 Preparation for Use
The instrument can be used as a:
• Free-standing instrument positioned on a horizontal surface.
• Rack-mounted in a standard 19 inch rack using the rack-mount accessory option kit (refer to
section 2.5).
For free-standing instruments, use the two front feet on the base to elevate the instrument to
provide a better viewing angle.
Note: The cooling air outlet on the underside of the instrument must not be obstructed. Allow a free flow
of air around the instrument, especially at high ambient temperatures.

2 Installation
K0443 Issue No. 3 2 - 2
2.4 Pneumatic connections
WARNINGS:
TURN OFF THE SOURCE PRESSURE AND CAREFULLY VENT THE PRESSURE LINES BEFORE
DISCONNECTING OR CONNECTING THE PRESSURE LINES. PROCEED WITH CARE.
ONLY USE EQUIPMENT WITH THE CORRECT PRESSURE RATING.
BEFORE APPLYING PRESSURE, EXAMINE ALL FITTINGS AND EQUIPMENT FOR DAMAGE.
REPLACE ALL DAMAGED FITTINGS AND EQUIPMENT. DO NOT USE ANY DAMAGED
FITTINGS AND EQUIPMENT.
Connection adaptor
Input supply + G 1/8
supply - G 1/8
Output G 1/8
Vent G 1/8
Reference G 1/8
Refer to the data sheets SDS0001 or SDS0008 for a complete range of adaptors.
Pressure supply (Figure 2-1)
1. The pressure supply must be clean, dry gas, nitrogen or air and at the correct pressure,
refer to the specification (Section 6).
2. Ensure the user systems can be isolated and vented.
3. Connect pressure and vacuum supplies to the SUPPLY + and SUPPLY - connection
ports.
4. Connect the Unit Under Test (UUT) to the required outlet connection port.
1 BSP connector 2 Bonded seal
Note: For instruments with NPT connections, use adequate pressure sealing.
Figure 2-1, Pneumatic Connections
Example instrument

PACE Pressure Controller User Manual
K0443 Issue No. 3 2 - 3
Installation
The instrument requires a positive pressure supply, instruments operating in an absolute range or
negative pressure range require a vacuum supply. A vacuum supply should be used for a fast
response for instruments operating near atmospheric pressure. For dual channel operation two
independent pressure and vacuum supplies can be used.
Important notes
When using two pressure modules, make sure that the modules are compatible, refer to Section
4.9. All connections must comply with the Pressure Equipment Directive (PED).
When connecting the output ports of two pressure modules together make sure both are either:
• below 70 bar.
OR
• between 100 to 210 bar.
To comply with the Pressure Equipment Directive (PED) do not mix these categories.
Supply equipment
Pneumatic supplies should have isolation valves and, where necessary, conditioning equipment.
The positive pressure supply should be regulated to between 110% of the full-scale pressure range
and MWP stated on the control module.
To protect the control module, for ranges above 100 bar, from over-pressure a suitable protection
device (such as a relief valve or bursting disc) must be fitted to limit the applied supply pressure to
below the MWP.
On instruments without a negative supply, the positive pressure discharges from the system to
atmosphere through the negative supply port. Fit the diffuser to the negative port to diffuse
airflow.
During system pressure vent operations, the pressure discharges from the system to atmosphere
through the vent port. Fit a diffuser to the vent port to diffuse airflow.

2 Installation
K0443 Issue No. 3 2 - 4
Pneumatic Connection Examples (Figures 2-2 and 2-4)
These examples show a single channel connection detail using supply equipment described above.
Figure 2-2, Pneumatic Connections without vacuum supply
Key to Figure 2-2
1 Pressure source 2 Conditioner 3 Filter
4 Regulate to between 110% full-scale and MWP
5 Diffuser * 6 Unit under test 7 Optional reservoir †
8 Protection device 9 Optional differential connection aatmosphere
Notes: Refer to Section 6 Reference and Specification for details of other system components.
* High pressure gas exhaust - depending on pressure range.
† Optimum controller transient response and minimum time to set-point may be degraded if either
the pneumatic supply or vacuum system has restricted flow. Installing a reservoir volume, which
has larger capacity than the load volume, located in close proximity to the controller supply ports
can improve the controller response.
To protect the control module, for ranges above 100 bar, from over-pressure a suitable protection
device (such as a relief valve or bursting disc) must be fitted to limit the applied supply pressure to
below the MWP.
Optional differential connection kit.
SUPPLY OUTLET VENT REF
a
8
8

PACE Pressure Controller User Manual
K0443 Issue No. 3 2 - 5
Figure 2-3, Pneumatic Connections with vacuum supply
Key to Figure 2-3
1 Pressure source 2 Conditioner 3 Filter
4 Regulate to between 110% full-scale and MWP
5 Diffuser* 6 Unit under test 7 Optional reservoir †
8 Protection device 9 Optional differential connection
10 Oil mist trap 11 Vacuum source 12 Normally open electrical release valve
13 Check valve ‡ a atmosphere
Notes:Refer to Section 6 Reference and Specification for details of other system components.
* High pressure gas exhaust - depending on pressure range.
† Optimum controller transient response and minimum time to set-point may be degraded if either
the pneumatic supply or vacuum system has restricted flow. Installing a reservoir volume, which
has larger capacity than the load volume, located in close proximity to the controller supply ports
can improve the controller response.
‡ Optional vacuum system kit.
To protect the control module, for ranges above 100 bar, from over-pressure a suitable protection
device (such as a relief valve or bursting disc) must be fitted to limit the applied supply pressure to
below the MWP.
Optional differential connection kit.
SUPPLY OUTLET VENT REF
11
13
12
a
*
8
8

2 Installation
K0443 Issue No. 3 2 - 6
Figure 2-4, Pneumatic Connections with negative gauge pressure generator
Key to Figure 2-4
1 Pressure source 2 Conditioner 3 Filter
4 Regulate to between 110% full-scale and MWP
5 Diffuser * 6 Unit under test 7 Optional reservoir †
8 Protection device 9 Optional differential connection a atmosphere
10 Vacuum generator ‡11 Source pressure (regulated compressed air supply)
12 Exhaust to atmosphere 13 Check valve ‡
Notes:Refer to Section 6 Reference and Specification for details of other system components.
* High pressure gas exhaust - depending on pressure range.
† Optimum controller transient response and minimum time to set-point may be degraded if either
the pneumatic supply or vacuum system has restricted flow. Installing a reservoir volume, which
has larger capacity than the load volume, located in close proximity to the controller supply ports
can improve the controller response.
‡ Optional negative gauge generator kit.
To protect the control module, for ranges above 100 bar, from over-pressure a suitable protection
device (such as a relief valve or bursting disc) must be fitted to limit the applied supply pressure to
below the MWP.
Optional differential connection kit.
SUPPLY OUTLET VENT REF
13
11
12
a
*
8
8

PACE Pressure Controller User Manual
K0443 Issue No. 3 2 - 7
2.5 Rack-mount option (Figure 2-5)
General
There must be enough space at the rear of the instrument for all the cables and pipes. The length
of the cables and pipes must allow for the removal and fitment of the instrument. The cooling air
of the instrument must not be obstructed. Allow a free flow of air through the equipment rack and
around the instrument, especially at high ambient temperatures.
Figure 2-5 Rack-mounting
Procedure
• Locate and secure the back brackets to the rear of the equipment rack.
• Unscrew and remove the four countersunk screws from each of the instrument side panels.
• Locate the two brackets on each side of the instrument and secure with the four
countersunk screws.
• Support the instrument and connect the cables and pipes.
Example instrument

2 Installation
K0443 Issue No. 3 2 - 8
• Refer to the electrical connections below before finally fitting the instrument into the equipment
rack.
• Temporarily locate and screw in the two spigots* to each side of the equipment rack.
• Locate and slide the instrument into the rack, locating the instrument on the spigots*.
• Secure the instrument in the equipment rack with two of the screws and washers (supplied).
• Remove the two spigots* and replace with the remaining two screws and washers (supplied).
2.6 Electrical connections
WARNINGS
1. THE GROUND LEAD OF THE INSTRUMENT MUST BE CONNECTED TO THE AC SUPPLY
PROTECTIVE SAFETY GROUND.
2. ISOLATE THE POWER SUPPLY BEFORE MAKING ANY ELECTRICAL CONNECTIONS TO THE
REAR PANEL.
General
The instrument must be connected to the correct electrical power supply as stated on a label next
to the power connector. Also see section 6 Reference and Specification.
Make sure that the power supply is off before connecting the power cable.
Requirements for rack-mounted instruments
• Install an isolator in the power supply circuit. The power supply connector and switch on the
rear panel of the instrument will not be accessible.
• Set the power supply isolator to OFF. Connect the power supply and set the power supply
switch to ON before sliding the instrument into the rack.
• Set the power supply isolator to ON .
Check that the front panel display shows the power-up sequence.
Connecting (Figure 2-6)
To connect the power supply to the instrument proceed as follows:
• Insert the IEC power connector (1) into the power supply connector at the rear of the
instrument.
• Set the ON/OFF switch to ON.
• Check that the front panel display shows the power-up sequence.
Other manuals for PACE5000
2
This manual suits for next models
1
Table of contents
Other GE Test Equipment manuals
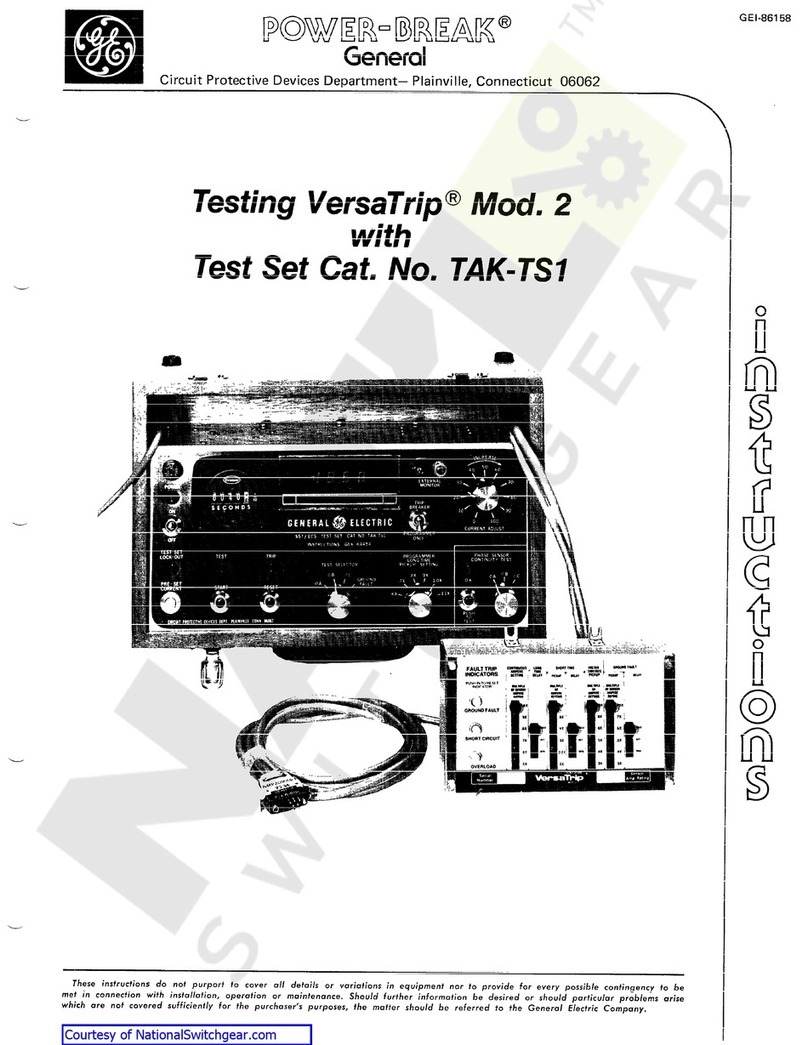
GE
GE POWER-BREAK TAK-TS1 User manual
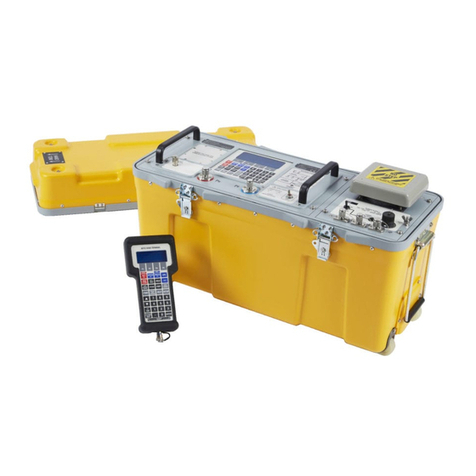
GE
GE Druck ADTS 405 User manual
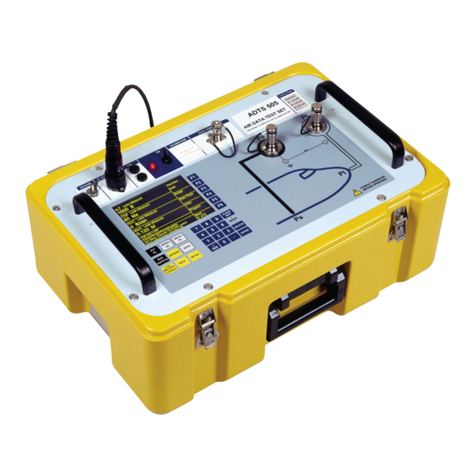
GE
GE Druck ADTS 505 User manual
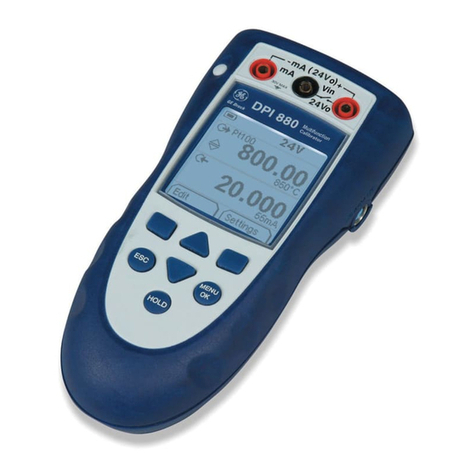
GE
GE Druck DPI 880 User manual

GE
GE Druck DPI 821 User manual
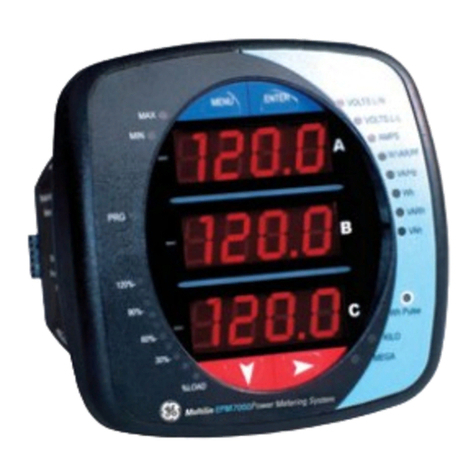
GE
GE Multilin EPM 7000 User manual

GE
GE Druck DPI 832 User manual

GE
GE Mentor EM User manual
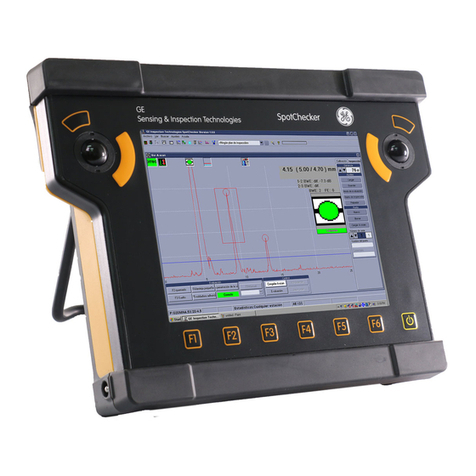
GE
GE SpotChecker User manual
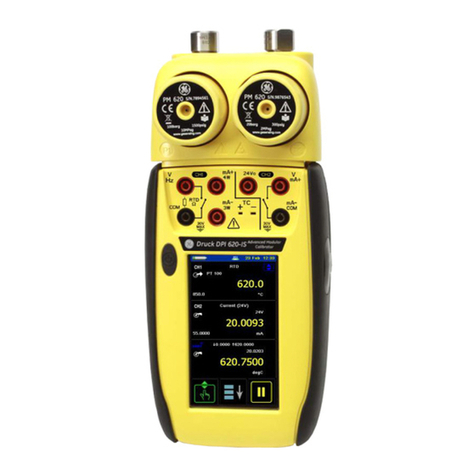
GE
GE Druck DPI 620-IS User manual