Geokon 1100 User manual

Instruction Manual
Model 1100
Borehole Extensometer
No part of this instruction manual may be reproduced, by any means, without the written consent of GEOKON®.
The information contained herein isbelieved tobe accurate and reliable. However, GEOKON®assumes no responsibility for
errors, omissions, or misinterpretations.The information herein is subject to change without notification.
Copyright © 2022 by GEOKON®(Document Revision A.1, 05/01/2023)


Warranty Statement
GEOKON warrants its products to be free of defects in materials and workmanship, under
normal use and service for a period of 13 months from date of purchase. If the unit should
malfunction, it must be returned to the factory for evaluation, freight prepaid. Upon examination
by GEOKON, if the unit is found to be defective, it will be repaired or replaced at no charge.
However, the WARRANTY is VOID if the unit shows evidence of having been tampered with
or shows evidence of being damaged as a result of excessive corrosion or current, heat, moisture
or vibration, improper specification, misapplication, misuse or other operating conditions outside
of GEOKON's control. Components which wear or which are damaged by misuse are not
warranted. This includes fuses and batteries.
GEOKON manufactures scientific instruments whose misuse is potentially dangerous. The
instruments are intended to be installed and used only by qualified personnel. There are no
warranties except as stated herein. There are no other warranties, expressed or implied, including
but not limited to the implied warranties of merchantability and of fitness for a particular
purpose. GEOKON is not responsible for any damages or losses caused to other equipment,
whether direct, indirect, incidental, special or consequential which the purchaser may experience
as a result of the installation or use of the product. The buyer's sole remedy for any breach of this
agreement by GEOKON or any breach of any warranty by GEOKON shall not exceed the
purchase price paid by the purchaser to GEOKON for the unit or units, or equipment directly
affected by such breach. Under no circumstances will GEOKON reimburse the claimant for loss
incurred in removing and/or reinstalling equipment.
Every precaution for accuracy has been taken in the preparation of manuals and/or software,
however, GEOKON neither assumes responsibility for any omissions or errors that may appear
nor assumes liability for any damages or losses that result from the use of the products in
accordance with the information contained in the manual or software.


1THEORY OF OPERATION .................................................................................................................... 1
1.1 INTRODUCTION....................................................................................................................................................1
1.2 SYSTEM COMPONENTS..........................................................................................................................................1
1.2.1 Head Assembly.......................................................................................................................................2
1.2.2 Coupling, Standpipe, and Flange ...........................................................................................................3
1.2.3 Vibrating Wire Displacement Transducers ............................................................................................4
1.2.4 Connecting Rods ....................................................................................................................................5
1.2.5 Borehole Anchors...................................................................................................................................6
2INSTALLATION CONSIDERATIONS ....................................................................................................... 9
2.1 TOOLS................................................................................................................................................................9
2.1.1 P/N 1100-TOOLKIT (Set of installation tools).........................................................................................9
2.1.2 P/N 1100-RECESSED-TOOLS (Accessories for recessed installations)...............................................9
2.1.3 P/N 1100-GROUT-DOWN (Accessories for inclined downward installations) ....................................9
2.1.4 P/N 1100-GROUT-UP (Accessories for overhead/upward installations) .............................................9
2.2 BOREHOLE DIAMETER .........................................................................................................................................10
2.2.1 Extensometers without an Over Core ..................................................................................................10
2.2.2 Extensometers Recessed in an Over Core Borehole .............................................................................11
2.3 ANCHOR SPACING ..............................................................................................................................................13
2.4 CABLE INSTALLATION AND SPLICING .......................................................................................................................13
3ASSEMBLY AND INSTALLATION .........................................................................................................15
3.1 PREPARATION....................................................................................................................................................15
3.2 CONNECTING ROD ASSEMBLY...............................................................................................................................15
3.2.1 Stainless Steel Connecting Rods...........................................................................................................15
3.2.2 For All Anchor Types: ...........................................................................................................................19
3.2.3 Fiberglass Connecting Rods .................................................................................................................20
3.3 ATTACH EXTENSION RODS TO CONNECTING ROD COLUMN ........................................................................................20
3.4 INSTALL HYDRAULIC LINES (HYDRAULIC ACTUATED ANCHORS ONLY)............................................................................21
3.5 BUNDLE THE RODS AND ANCHORS TOGETHER..........................................................................................................21
3.6 INSTALL GROUT PIPE (GROUTED BOREHOLES/CASING ONLY) .....................................................................................21
3.7 PVC STANDPIPE AND COUPLING ASSEMBLY ............................................................................................................21
3.8 FLANGE INSTALLATION ........................................................................................................................................21
3.9 LIFTING THE EXTENSOMETER ASSEMBLY INTO THE BOREHOLE .....................................................................................22
3.10 SETTING ANCHORS.........................................................................................................................................22
3.10.1 Groutable Anchors ..........................................................................................................................22
3.10.2 Hydraulic Anchors (Bladder and Borros Style) ................................................................................23
3.11 REMOVE ANCHOR HARDWARE.........................................................................................................................23
3.12 ATTACH THE TRANSDUCER HOUSING ASSEMBLY ..................................................................................................24
3.13 INSTALLING THE VIBRATING WIRE TRANSDUCERS.................................................................................................24
3.14 INSTRUMENT HEAD PROTECTION ......................................................................................................................26
4TAKING READINGS ...........................................................................................................................26
4.1 ELECTRONIC READINGS........................................................................................................................................26
4.1.1 Readout Box.........................................................................................................................................26
5TROUBLESHOOTING.........................................................................................................................27
APPENDIX A. SPECIFICATIONS....................................................................................................................28
A.1 MODEL 1100 SPECIFICATIONS .................................................................................................................................28
A.2 ROD SPECIFICATIONS..............................................................................................................................................28
A.3 MODEL 4450 VIBRATING WIRE TRANSDUCER SPECIFICATIONS.......................................................................................28
A.4 HEAD ASSEMBLY DIMENSIONS .................................................................................................................................29
APPENDIX B. THERMISTOR TEMPERATURE DERIVATION ..............................................................................31
APPENDIX C. WIRING CHARTS FOR VIBRATING WIRE TRANSDUCERS .............................................................32

C.1 SINGLE TRANSDUCER WIRING CHART .........................................................................................................................32
C.2 TWO TRANSDUCER WIRING CHART............................................................................................................................32
C.3 THREE TRANSDUCERS WIRING CHART ........................................................................................................................32
C.4 FOUR TRANSDUCERS WIRING CHART .........................................................................................................................32
C.5 FIVE TRANSDUCERS WIRING CHART ...........................................................................................................................33
C.6 SIX TRANSDUCERS WIRING CHART.............................................................................................................................34
APPENDIX D. SWAGELOK TUBE FITTING INSTRUCTIONS............................................................................... 35
D.1 INSTALLATION .......................................................................................................................................................35
D.2 REASSEMBLY INSTRUCTIONS .....................................................................................................................................36
APPENDIX E. GUIDE TO ORDERING EXTENSOMETERS................................................................................... 36

1
1 THEORY OF OPERATION
1.1 Introduction
Borehole extensometers are used for monitoring displacements along the axis of the instrument
in various applications (tunnels, shoring sidewalls, earthen dams, landslides, etc.) A series of
borehole anchors interconnected by fiberglass, composite/graphite, or stainless steel connecting
rods are installed at predetermined depths, with the deepest anchor installed in stable ground to
serve as a nonmoving reference point. If a stable point cannot be established with the deepest
anchor, the head of the extensometer can serve as the reference point but must be tied into an
external survey system.
Each borehole anchor is typically coupled to a Vibrating Wire (VW) Displacement Transducer to
measure the movement in each zone relative to the head. Anchor movements are sensed
electronically with transducers or mechanically determined with a dial gauge where applicable,
and a measurement of the position of the top of connecting rod relative to the anchor is
determined. This not only enables the measurement of the magnitude of any movements but also
narrows down the identification of zones of movements.
To ease installation, the extensometer should be assembled on the ground next to the borehole
and then suspended and lowered into the borehole. The anchors are then set in place, either by
applying hydraulic pressure (borros and bladder type anchors) or using cement grout
(groutable anchors).
1.2 System Components
The four basic components of the extensometer are: the head assembly, Vibrating Wire
Displacement Transducers (contained within the head assembly), connecting rods and tubing,
and the borehole anchors. Each of these components are described in the sections that follow.

2
1.2.1 Head Assembly
Figure 1 - Four Main Components of the Extensometer

3
The extensometer head assembly houses and protects the VW displacement transducers.
The head assembly includes the following components:
•Protective cap
•Side-exit cable (custom top exit available)
•PVC coupling (or flange)
•PVC standpipe.
Figure 2 - Main Components of the Head Assembly
Head assembly sizes vary and are dependent upon the quantity and range of VW
displacement transducers. (See appendix A.4 Head Assembly for more information.) The
head assembly may be located above grade, recessed in a borehole, or seated in an
enlarged section of the borehole known as an overcore.
1.2.2 Coupling, Standpipe, and Flange
A standpipe is cemented into the bore hole and is connected to the head assembly either
with a PVC coupling or a set of PVC flanges. A custom bladder anchor can replace the
tube mount and standpipe. This is recommended for upward installations.
The head can be attached to the standpipe by gluing the PVC coupling on the head
assembly to a PVC standpipe inserted into the borehole. Two flanges can also be used
(glued to the head and the standpipe ahead of time) which are bolted together. The
standpipe and coupling, or flange/coupling assembly, are installed into the borehole. If

4
using a coupling, the standpipe and coupling would be cemented in place and left to set
up. With the standpipe secured in place, the MPBX string is lowered into the borehole
through the standpipe and then the tube mount is glued into the coupling or flange.
1.2.2.1 Inline Slip Couplings
The inline slip couplings are attached to individual rod columns by cementing the
coupling to the TUB-101 PVC pipe or using a barb fitting (on each end of the coupling)
to attach the coupling to the TUB-103 or TUB-109 ½-inch tubing. Both types are shown
below and come with a 10-cm or 30-cm range of motion. Multiple units in a single
column can be implemented if desired. The range of motion allows compression (or
extension) of the rod column in settlement (or heave) situations. Without the range of
motion, there might be substantial bending or breaking of the PVC tubing or coiling of
the rod column, which would introduce errors in the measured movement. They can be
set anywhere in their range and are shipped with dissolvable tape to wrap around the slip
location to temporarily hold it until the stainless steel or fiberglass rods can be locked.
They are usually installed just below the head assembly but can be placed anywhere
along the column. These couplings would be recommended where there is more than 1
inch of compressive movement. However, other considerations including grout stiffness,
hole diameter, and installation depth can influence decisions on the use of slip couplings.
Using a slip joint may also be considered where separation of the pipe or tube column
under significant extension situations would be undesirable.
Figure 3 - Slip Location for Inline Slip Couplings
1.2.3 Vibrating Wire Displacement Transducers
GEOKON Model 4450 Vibrating Wire Displacement Transducers consist of a vibrating
wire sensing element, in series with a heat treated, stress relieved spring. One end of the
spring is connected to a vibrating wire, the other end to the transducer shaft. Movement of
the anchors and attached connecting rods cause the spring inside the transducer to expand
or contract, which changes the tension in the vibrating wire. The change in tension
(strain) of the wire is directly proportional to the movement of the head relative to the
anchors or vice versa.
Slip Location

5
The standard ranges of VW displacement transducer which can be installed in the
extensometer are: 12.5 mm (0.5 inch), 25 mm (1 inch), 50 mm (2 inch), 100 mm (4 inch),
150 mm (6 inch), 200 mm (8 inch) & 300 mm (12 inch).
Figure 4 – Model 4450 Displacement Transducer
1.2.4 Connecting Rods
Connecting rods connect the borehole anchors to the displacement transducers located in
the head assembly. There are 2 standard types of connecting rods available, fiberglass and
stainless steel. Graphite rods are available as a custom option. Graphite rods are used for
applications where thermal fluctuations can potentially influence rod behavior, as these
rods have a significantly lower thermal coefficient of expansion than steel or fiberglass.
1.2.4.1 Stainless Steel Rods
The standard stainless steel connecting rods are made from 1/4-inch stainless steel rod
sections, flush coupled to form a continuous string. Standard lengths are 5 ft and 10 ft but
are available in lengths necessary for installation. They are encased in rigid PVC pipe,
which protects them from grout (where applicable) thereby ensuring their ability to move
freely as they are acted upon by forces along the axis of the instrument..
1.2.4.2 Fiberglass Rods
The standard fiberglass connecting rods are made from continuous length, 1/4-inch
fiberglass. The rods are encased in polyethylene tubing for borehole lengths less than
30 meters (100 feet), and nylon tubing for borehole depths greater than 30 meters (100
feet). Fiberglass rods are typically not recommended for installations of 30 meters (100
feet) or greater. The tubing protects them from grout (where applicable) thereby ensuring
their ability to move freely as they are acted upon by forces along the axis of the
instrument.
The flexibility of the rods and tubing allows the extensometer to be preassembled and
coiled at the factory for shipment to the jobsite where it can be uncoiled and inserted into
the borehole. This greatly speeds up the installation process.

6
Note: Fiberglass rods have a lower modulus of elasticity than stainless steel rods. This,
combined with friction effects, may lead to insufficient precision in applications where
high resolution (< 0.1 mm) is required. Fiberglass rods are more stable thermally and can
be a better choice than stainless steel rods in areas where temperatures may vary.
1.2.5 Borehole Anchors
Borehole anchors are installed at predetermined depths. The deepest anchor is normally
installed in stable ground so that it can serve as a nonmoving point of reference for the
rest of the anchors. There are three types of anchors available: groutable, hydraulic
bladder, and hydraulic borros.
1.2.5.1 Groutable Anchors
Groutable anchors are usually recommended for downward directed boreholes or holes
that must remain sealed. Each groutable anchor is made from a 229 mm (9 inch) length of
#6 steel reinforcing bar. For stainless steel and fiberglass rods, the anchors are attached to
the connecting rod with a Swagelok connector on the bottom using a through-hole in the
rebar. PVC tubes are connected to the top of the anchors using the PVC adapter shown
below, and tubing for fiberglass rods are connected to the top of the anchors using the
barb connector. See Figure 5 below.
Figure 5 - Groutable Anchors
1.2.5.2 Hydraulic Bladder Anchor
Hydraulic bladder anchors use friction to secure the anchor to the borehole wall. They are
designed to be used in all kinds of rock materials and dense soil. These anchors can be
easily installed in boreholes oriented in any direction, which make them particularly
useful in boreholes which are difficult to grout, such as fractured boreholes or ones which
are oriented upwards.
The anchor comprises a spool of high strength plastic with a sealed copper bladder
wrapped around the outside diameter. The bladder has a high-pressure nylon inflation line
and built-in check valve. A hydraulic pump is used to inflate the copper bladder, causing

7
it to expand and unwind. The soft copper material of the bladder allows it to deform and
fill the space between the plastic spool and the borehole wall, thus wedging the anchor in
place. The deformation of the copper bladder is permanent; and the anchor will stay in
place even if the check valve fails.
Hydraulic bladder anchors are designed for customer-specified borehole sizes. Like the
groutable anchor there is a through-hole in the anchor that allows the rod to attach to a
Swagelok on the bottom side.
Figure 6 - Hydraulic Bladder Anchors

8
1.2.5.3 Single or Double Hydraulic Borros Anchor
Hydraulic borros anchors are a type of end-bearing anchor recommended for soft soils.
Hydraulically actuated prongs, spaced 120º from one another, penetrate the walls of the
borehole, ensuring positive end-bearing anchorage. Single borros anchors (Figure 7) have
three prongs located on the bottom end of the anchor; double borros anchors (Figure 8)
have an additional three prongs on the top end of the anchor. On both models, the prongs
protrude approximately 150 mm from the anchor body when actuated.
Figure 7 - Single Hydraulic Borros Anchors
For SS and Rods For Fiberglass Rods
Figure 8 - Double Hydraulic Borros Anchors

9
2 INSTALLATION CONSIDERATIONS
2.1 Tools
2.1.1 P/N 1100-TOOLKIT (Set of installation tools)
Part
Number
Description
Quantity
ADH-103
Loctite 271 Thread locker
1
SUP-802
Black Electrical Tape
2
SUP-814
Fiber Tape
2
TLS-100
¼ inch x 4 inch Flat Head Screwdriver
1
TLS-106
#2, 4 inch Phillips Head Screwdriver
1
TLS-205
Log Arm Allen Wrench 3/16 inch
1
TLS-206
9/16 inch Wrench
2
TLS-216
Curved Jaw Vise Grips With Wire Cutter
2
TLS-300
Hacksaw with Blade
1
TLS-301
24 TPI Hacksaw Blades (Gray Stripe)
1
TLS-400
Flat 8 inch File
1
TLS-401
Handel for Hand File
1
TLS-601
Acid Brush (144 count Pack)
12
TLS-619
20 inch Toolbox
1
2.1.2 P/N 1100-RECESSED-TOOLS (Accessories for recessed installations)
Part
Number
Description
Quantity
B4450-49
Setting Tool Wrench
1
HRD-A1663
3/16 inch T-handle Allen wrench, 25 inches Long
1
2.1.3 P/N 1100-GROUT-DOWN (Accessories for inclined downward installations)
Part
Number
Description
Quantity
HRD-A1064
Hose Barb, 5/8 inch x1/2 inch, NPT
1
HRD-A1068
Gate Valve, ½ inch, Bronze, NPT
1
2.1.4 P/N 1100-GROUT-UP (Accessories for overhead/upward installations)
Part
Number
Description
Quantity
A1150-69-5
Down Hole Grout Tube, 36 inches Long
1
A1150-70-1
External Grout Pipe, 24 inches Long
1
HRD-A1065
Hex Reducer Bushing
1
HRD-A1066
Close Nipple, 1/2 inch, Brass
1
HRD-A1067
Tee, 1/2 inch, Female, Brass
1
HRD-A1068
Gate Valve, 1/2 inch, NPT, Bronze
1
SWG-129B
B-400-1-4, Drilled 0.266 Through
1

10
Table 2 - Minimum Borehole Diameter for
Recessed Extensometers.
2.2 Borehole Diameter
Boreholes should be drilled slightly deeper than the deepest anchor and cleared of debris before
use. The mouth of the borehole can be enlarged (over-cored) or left as is, depending on
installation requirements of the extensometer and project.
2.2.1 Extensometers without an Over Core
The minimum borehole diameter for extensometers without an over core is determined by
the number of points included in the head assembly. Use Table 1 to determine the
minimum borehole diameter for protruding head assemblies (Figure 9)and Table 2 to
determine the minimum borehole diameter for recessed head assemblies (Figure 10).
NOTE: When grouting a borehole, the specified diameter may need to be increased to
allow a sufficient amount of grout to be applied around the standpipe (The standpipe may
already be cemented in place, or a standpipe may not be used.)
Figure 9 - Protruding Above the Borehole
Figure 10 - Recessed in the Borehole
# of Points
Min. Borehole
Diameter
1-2
73 mm (2.88 inch)
3-4
89 mm (3.50 inch)
5-6
115 mm (4.50 inch )
# of Points
Min. Borehole
Diameter
1-2
125 mm (4.92 inch)
3-4
141 mm (5.54 inch )
5
176 mm (6.92 inch )
6
184 mm (7.22 inch )
Table 1 - Minimum Borehole Diameter for
Protruding Extensometers
Note: For ease of installation the borehole can
be larger than the minimum diameter shown
above.

11
2.2.2 Extensometers Recessed in an Over Core Borehole
2.2.2.1 Over Core Depth
The over core depth can be determined using Table 3. Table 3 references the length of the
head assembly, which can be determined using the information in Appendix A, Section
A.4 Head Assembly.
NOTE: If the top of the head assembly will be recessed below the ground surface, or if
back fill will be placed above the top of the head assembly, add the distance from the
ground surface to the top of the protective cap to the measurement given in Table 3 to
calculate the total over core depth. If the optional cable exit from the top of head is used,
then the depth should be increased to account for cable. See the Figure 11.
Figure 11 - Over Core Depth
Number of
Points
Transducer Range (VW)
Head Assembly Length
NO FLANGE
Head Assembly Length
WITH FLANGE
1-2
12.5, 25, 50 mm (0.5, 1, 2 inch) 364 mm (14.38 inch)
384 mm (15.13 inch)
100, 150 mm (4, 6 inch) 466 mm (18.38 inch)
485 mm (19.13 inch)
200 mm (8 inch) 625 mm (24.63 inch)
625 mm (24.63 inch)
300 mm (12 inch)
778 mm (30.63 inch)
778 mm (30.63 inch)
3-4
12.5, 25, 50 mm (0.5, 1, 2 inch) 368 mm (14.47 inch)
384 mm (15.13 inch)
100 mm (4 inch) 444 mm (17.47 inch)
485 mm (19.13 inch)
200 mm (8 inch)
608 mm (23.97 inch)
625 mm (24.63 inch)
300 mm (12 inch)
761 mm (29.97 inch)
778 mm (30.63 inch)

12
5-6
12.5, 25, 50 mm (0.5, 1, 2 inch) 378 mm (14.88 inch)
381 mm (15.00 inch)
100 mm (4 inch)
479 mm (18.88 inch)
482 mm (19.00 inch)
200 mm (8 inch)
619 mm (24.38 inch)
622 mm (24.05 inch)
300 mm (12 inch)
772 mm (30.38 inch)
775 mm (30.50 inch)
Table 3 - Head Assembly Length
2.2.2.2 Over Core Diameter
The minimum over core diameter for extensometers protruding above the borehole
(Figure 12) is determined by the number of points included in the head assembly and if a
coupler or flange is used. Use Table 4 below to determine the minimum over core
diameter for using a flange, and Table 2 for a coupler only. Over core diameter should be
larger than the flange diameter.
Figure 12 - Over core Diameter
Number of
Points
Flange Diameter
(overcore should be larger than the flange dimeter)
1-2
178 mm (7 inch)
3-4
191 mm (7.50 inch)
5-6
230 mm (9.06 inch)
Table 4 - Minimum Over Core Diameter

13
2.3 Anchor Spacing
Anchor spacing may be dictated by geologic features or specific zones that need to be monitored.
If possible, the deepest anchor should be installed in stable ground so that it can serve as a
nonmoving reference point for the head and the rest of the anchors. For extensometers installed
from within tunnels, the deepest anchor should be installed at least two tunnel diameters away
from the tunnel wall.
Anchor depths are typically measured from the installation surface to the bottom tip of the
anchor, as illustrated in Figure 13.
Figure 13 - Anchor Depths
2.4 Cable Installation and Splicing
The cable should be routed to minimize the possibility of damage due to moving equipment,
debris or other causes. The cable can be protected using flexible conduit, which can be supplied
by Geokon.
Terminal boxes with sealed cable entries are available from Geokon for all types of applications.
These allow many gauges to be terminated at one location with complete protection of the lead
wires. The interior panel of the terminal box can have built-in jacks or a single connection with a
rotary position selector switch. Contact Geokon for specific application information.
Groutable
Anchors
Bladder
Anchors
Single
Borros
Anchors
Double
Borros
Anchors

14
Because the vibrating wire output signal is a frequency rather than a current or voltage,
variations in cable resistance have little effect on gauge readings; therefore, splicing of cables
has no ill effects, and in some cases may in fact be beneficial. The cable used for making splices
should be a high-quality twisted pair type, with 100% shielding and an integral shield drain wire.
When splicing, it is very important that the shield drain wires be spliced together. Always
maintain polarity by connecting color to color.
Splice kits recommended by Geokon incorporate casts, which are placed around the splice and
are then filled with epoxy to waterproof the connections. When properly made, this type of splice
is equal or superior to the cable in strength and electrical properties. Contact Geokon for splicing
materials and additional cable splicing instructions.
Cables may be terminated by stripping and tinning the individual conductors and then connecting
them to the patch cord of a readout box. Alternatively, a connector may be used which will plug
directly into the readout box or to a receptacle on a special patch cord.
Other Geokon Measuring Instrument manuals
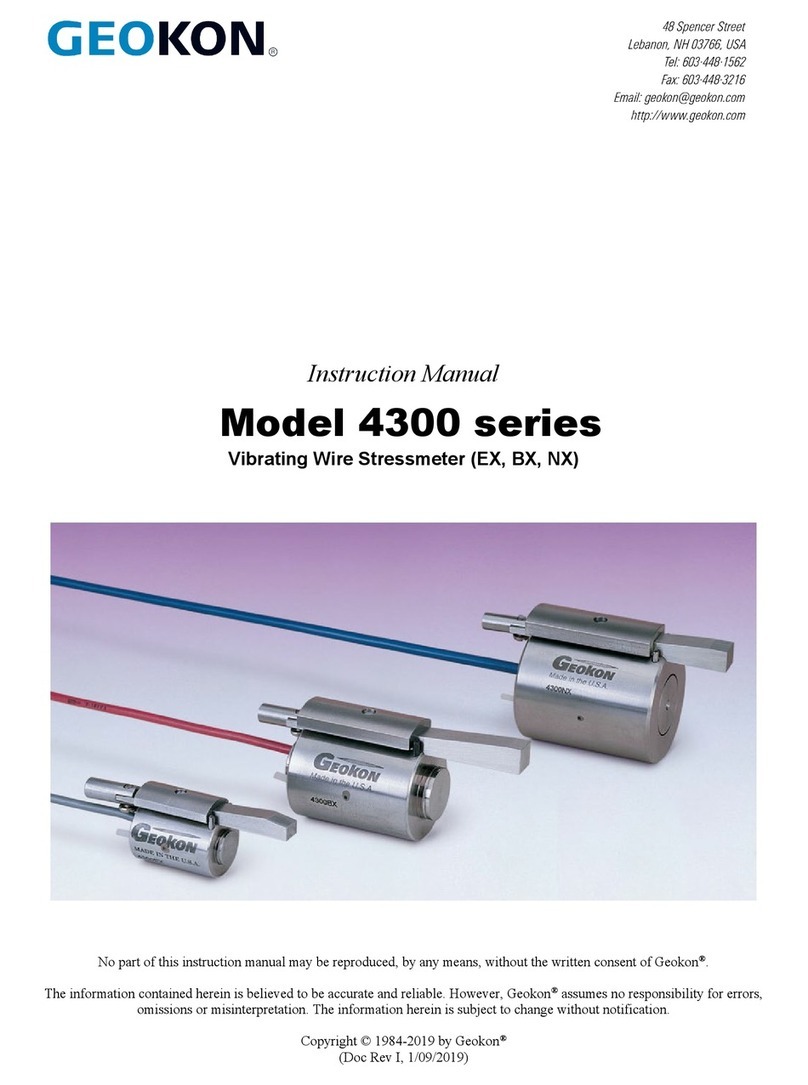
Geokon
Geokon 4300 Series User manual
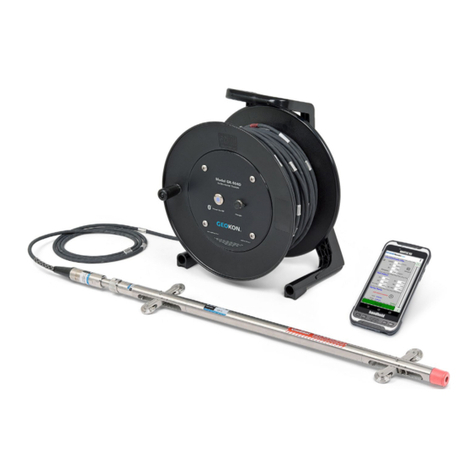
Geokon
Geokon GK-604D User manual
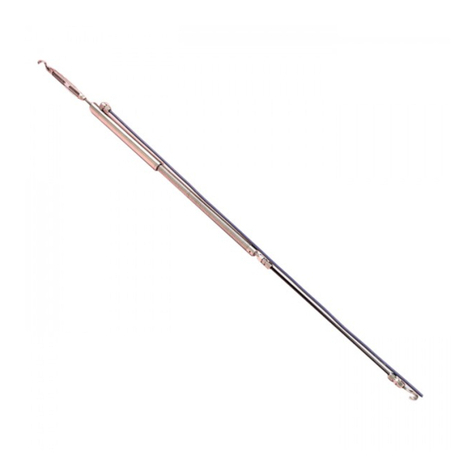
Geokon
Geokon 4425 User manual
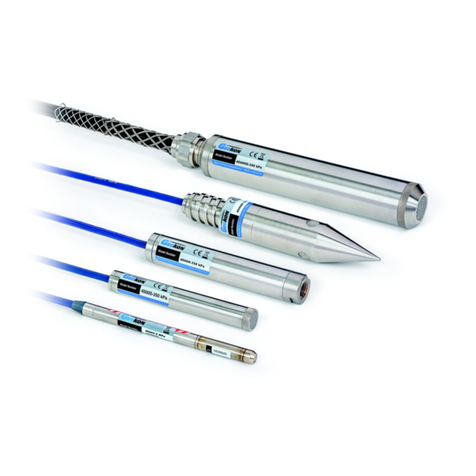
Geokon
Geokon 4500 Series User manual
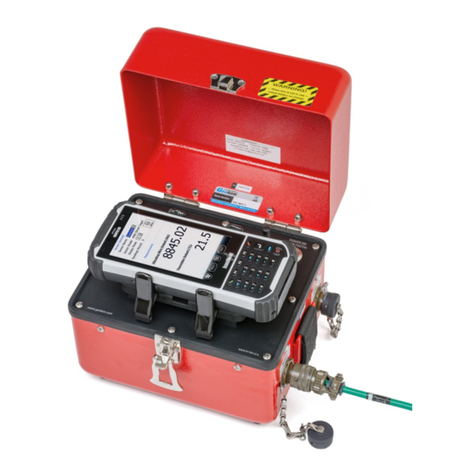
Geokon
Geokon GK-405 User manual

Geokon
Geokon 4420 User manual
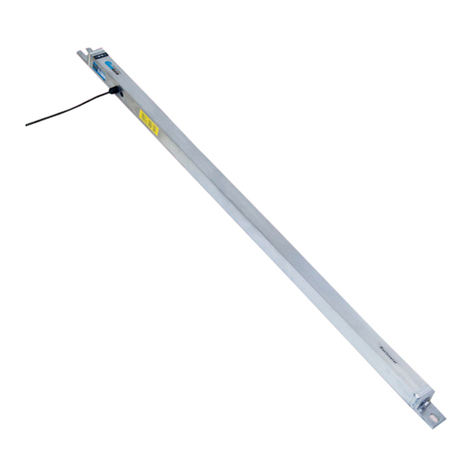
Geokon
Geokon 6165 User manual
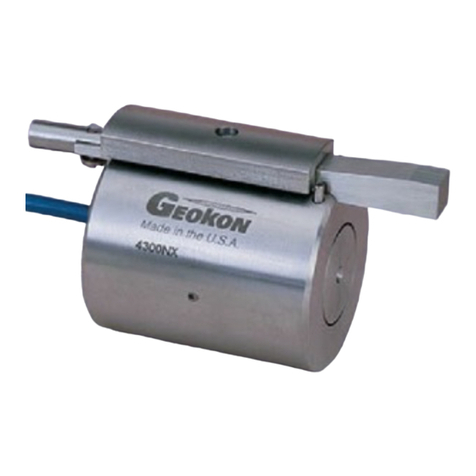
Geokon
Geokon Stressmeter 4300 Series User manual
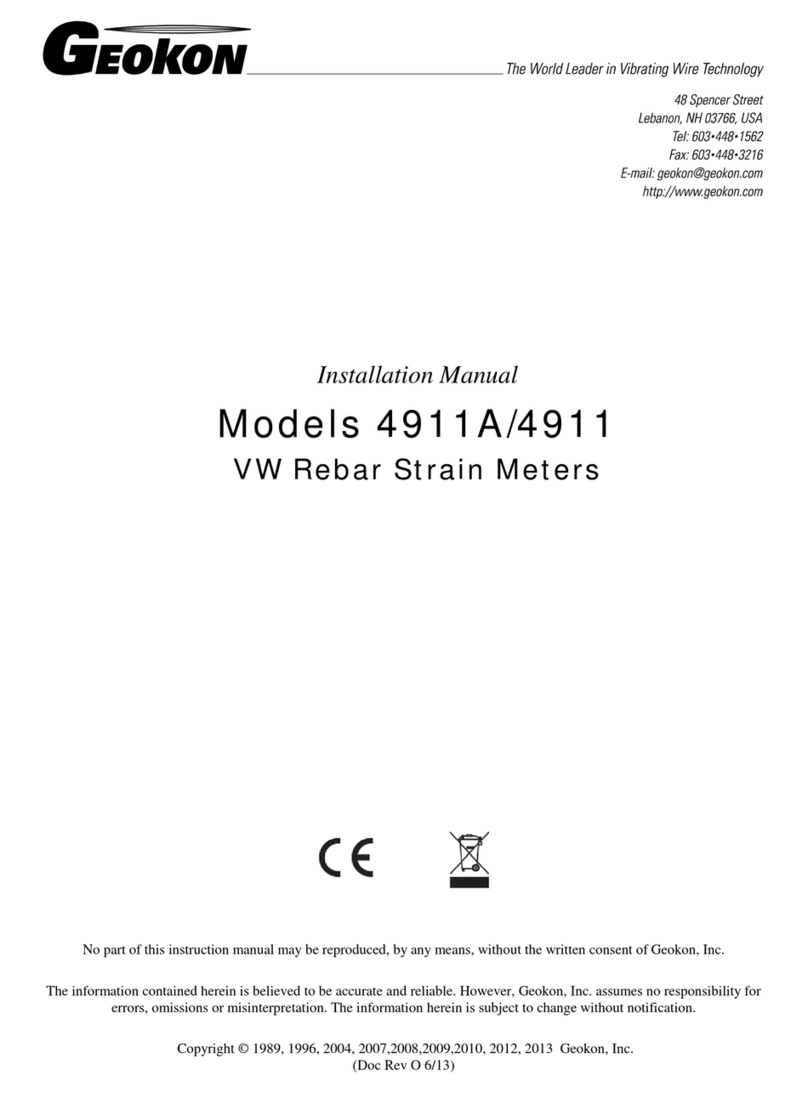
Geokon
Geokon 4911A User manual
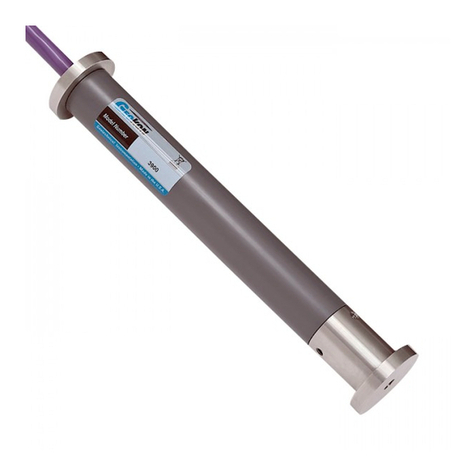
Geokon
Geokon 3900 User manual
Popular Measuring Instrument manuals by other brands
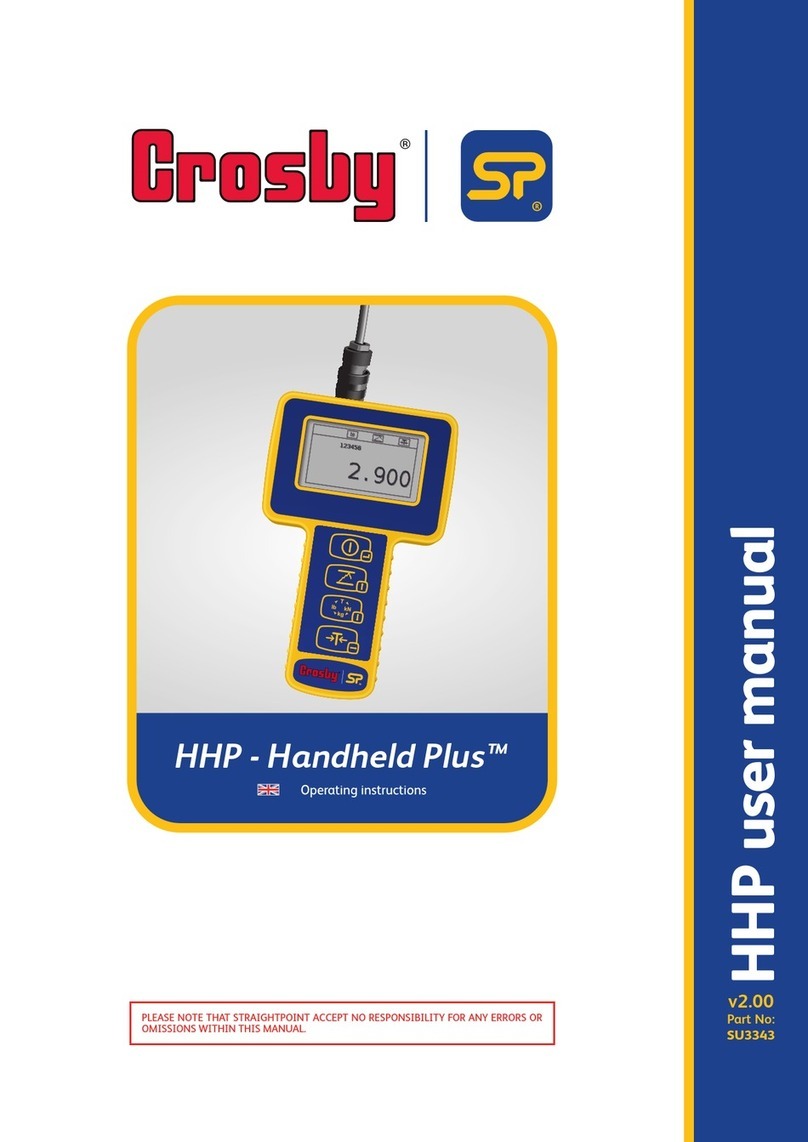
Crosby
Crosby SP Handheld Plus operating instructions

Fluke
Fluke 165X Quick reference guide
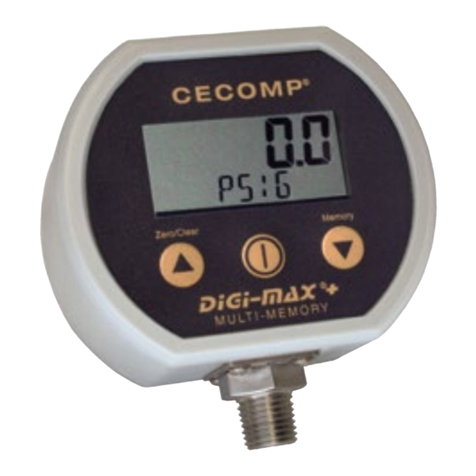
Absolute Process Instruments
Absolute Process Instruments Cecomp F20B quick start guide

Leica
Leica Disto X310 Assembly manual
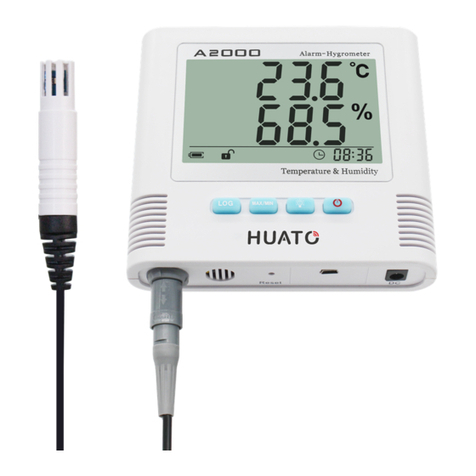
Huato
Huato A2000 Series Operation manual
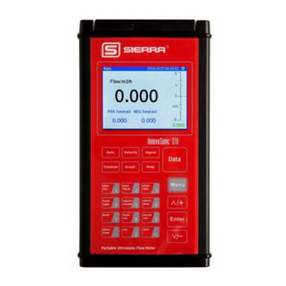
Sierra
Sierra InnovaSonic 210 Quick install guide