Runxin 53520 User manual

Page | 1
Runxin 53520 Filter Valve
Instruction Manual

Page | 2
Table of Contents
Installation Summary Page 3
General Specifications Page 4
Installation Page 5
Service cycles Page 6
Parameter Settings Page 7
Valve Breakdown Page 8
Circuit Board Functions Page 9
Valve Settings Page 10-11
Flow Rate Curve Page 12
Trouble Shooting Page 13-14

Page | 3
Installation Summary
Installation Location: Installation Date:
Installed by: Phone:
Application Type:
Water Source:
Water Test Results
Hardness: Iron: pH:
Other:
Misc:
Tank Size:
Diameter Height:
Resin or Media Type:
Resin or Media Volume: Brine tank Size:
Capacity:
Service Flow Rate:
Min: Max: Backwash:
Inlet Pressure: KPa
Control Valve Configuration
Valve Type: Valve Part No.
Serial Number:
Regenerant Refill Control: Gpm/lpm Injector Type: Gpm/lpm
Drain line flow control: Gpm/lpm

Page | 4
General Specifications
Operating
Minimum/Maximum operating pressures: 20psi (138kPa) –87psi (600kPa)
Minimum/Maximum Operating Temperature: 5°C -50°C
Power Supply: 240V/50Hz DC24V 1.5A
Connections
Inlet: 2” Male BSP
Outlet: 2” Male BSP
Waste: 2” Male BSP
Riser Pipe: 2” D-GB (63mm OD)
Tank Thread: 4”-8UN

Page | 5
Installation
Before Installation, read instructions thoroughly. The installation of the system should be completed
by a professional.
36x72” GS1000 High Absorption micro pollutants, Carbon Media Loading:
160kg 3-6mm #5 Underbed Gravel (Load in tank first)
80kg 8/16 #6 Underbed Gravel (Load in tank second)
210kg GS1000 (8x30) Carbon (Load in tank last)
342LPM Backwash Flow control supplied with valve
Use filling funnel provided:
Do not use Vaseline, oils, or Spray silicone on valve O-rings. 100% Silicone Lubricant must be used
for the O-rings
Locate the system as close as possible to the nearest drain.
The cylinder should be situated on a firm, level surface.
The system should be kept away from boilers, heater and installed inside.
Allow adequate space for pipework and removal of the valve when it is due for servicing equipment.
All pipework should be done in accordance with local plumbing regulation and codes.
Do not use the valve as a support mechanism for pipework use correct supports.
It is recommended to install bypass for the system, to allow for works to be performed on the valve
or cylinder without interruption to production. (Figure 1)
If the installer is soldering pipework, it is important no pipework is connected to the valve as the
heat will damage the system.
When using Teflon tape be careful not to cross thread the fittings.
Allow an air gap when plumbing the waste line to drain.

Page | 6
Riser pipe should be cut off flush with the top of the cylinder and deburred.
Centre the riser in the cylinder and plug to not allow any media to enter riser when filling the
cylinder, fill the media as per suppliers’ recommendations.
Remove plug and fill system slowly with water
Once cylinder is 90% full of water install the valve, making sure not to cross thread the valve.
Connect inlet, outlet and drain line to the valve.
Turn on power to the valve and check system settings are correct
Put system into back wash and then slowly open the inlet valve to allow for air to be removed from
the system.
Once air has been removed and a constant flow of water is running down the backwash line, open
the inlet fully until all fines from the media has flushed out of the system. (This may require 2-3
backwashes)
After backwash make sure to put the valve into flush to settle the media bed.
After backwash is complete check for any leaks within the system and pipework.
Fig.1

Page | 7
System Status
Service Status: Unfiltered water is directed through the media bed and up through the distributor
and riser pipe.
Backwash Status: The flow of water is redirected down the riser and up through the media bed.
lifting the media and removing the sediment down the waste line.
Fast Rinse Status: The Flow of water is directed through the media bed and up through the
distributor and riser pipe and sent to drain. This is to allow the media bed to resettle and remove
any sediment that may be left in the pipework from the backwash.

Page | 8
Display Icons Runxin Controller
Parameter Specifications

Page | 9
Valve Breakdown

Page | 10
Signal Output
There is a signal output connector on the circuit board. It is for controlling
external wiring (Refer to Figure 2 and Figure 3).
There are two kinds of output modes.
b-01: Sends signal start of backwash and stops sending signal at end of
rinse cycle
b-02: Sends signal in between cycles
Interlock Function
The circuit board has an interlock function to send a signal between Runxin
valves in a parallel set up. When one of the units has started a backwash, the
signal will be sent to the other valve and lock it out from performing a
backwash until the first valve has completed its cycles.

Page | 11
Initial Power Up
The valve may need to return to the service position.
The ceramic disc will return to service position and -00- will be displayed when
in motion.
This should be completed within 1 minute (if this takes longer than 2minutes
please contact Dealer)
To initiate a Manual Regeneration
–Unlock Valve –Press Up & Down arrow together for 5 secs until you hear
a beep.
-Press the Manual/Return button
-F-00 will be displayed and Backwash will start
-To skip a cycle, press the Manual/Return button again
To Set Clock
–Unlock Valve –Press Up & Down arrow together for 5 secs until you hear
a beep.
–Press the Menu Button.
–The time will be displayed with the enquiry/setting symbol and clock
symbol illuminated
–Press Menu button again.
–The hour time will flash.
–Change the Hour time to correct time by pressing the up or Down button
& press Menu to save.
–The minutes will then flash.
–Change the minutes time with the up or down arrow and press menu to
confirm changes.
Set Regeneration Time
–From the Set Clock setting press the down arrow.
–Press Menu –The hour will then flash change the Hour time to desired
time by pressing the up or Down button & press Menu to save.
–The minutes will then flash.
–Change the minutes time with the up or down arrow and press menu to
confirm changes.
Leave the next setting at F-00

Page | 12
How to change Regeneration Days Override
–From the F-00 setting press the down arrow
–The hourglass symbol and enquiry/setting symbol will be illuminated,
–Press the Menu Button
–The Digits will then flash change the number to desired number of days by
pressing the up or Down button & press Menu to save.
To Change Regeneration Cycle Minutes
Backwash 2-##
–From the days override setting press the down arrow.
–The backwash symbol and enquiry/setting symbol will be illuminated, press
menu, the time will flash, press the up and down arrows to change to
desired minutes
- Press menu to confirm
Fast Rinse 3-##
–Once backwash is set, Press down
–The Fast Rinse symbol and enquiry/setting symbol will be illuminated, press
menu, the time will flash, press the up and down arrows to change to
desired minutes
–Press menu to confirm

Page | 13
Flow rate Curve

Page | 14
Troubleshooting
Problem
Possible Cause
Solution
Filter Fails to
Backwash
a. Power to controller has
been interrupted
b. Backwash cycle times set
incorrectly
c. Controller Damaged
a. Check power
connection is ok
b. Reset the backwash
cycle times
c. Check or replace
controller
Filter passing
raw water
a. Bypass valve is open
b. Damaged riser pipe
c. Internal Valve Leak
a. Close Bypass Valve
b. Check the riser pipe is
not cracked and O-
ring is ok
c. Check or change valve
body
Water
pressure loss
a. Filter requires a backwash
b. Check no blockage in
Pipework
a. Backwash filter
b. Unblock pipework
Loss of media
material
through drain
line
a. Air in the system
b. Backwash flow control to
high
c. Top screen broken
a. Bleed air from the
system. Check for
leaks
b. Reduce Backwash
flow to suitable size
c. Check and replace top
screen
Control valve
cycle
continuously
a. Wrong size transformer
b. Foreign material stuck in
drive gear
c. Faulty valve
a. Use correct
Transformer
b. Remove Foreign
material from drive
gear
c. Replace valve
Water flowing
through drain
line continually
a. Power outage during
backwash or fast rinse
b. Internal Valve leak
a. Turn on Power, cycle
through to service
b. Check or replace
valve body
All indicators
display on the
controller
a. Wiring between the
display board and control
board failure
b. Control board is faulty
a. Check a replace cable
b. Replace control board
c. Check or replace
transformer

Page | 15
c.
Transformer damaged
d. Incorrect voltage
d. Replace transformer
with correct size
No display on
controller
a. Wiring between the
display board and control
board failure
b. Control board is faulty
c. Display board is faulty
d. Transformer damaged
e. Power outage
a. Check a replace cable
b. Replace control board
c. Replace display board
d. Check or replace
transformer
e. Check power supply
E1 Flash
a. Wiring between the
locating board and display
board failure
b. Locating board damaged
c. Mechanical driver fails
d. Faulty control board
e. Wiring between the
control board and motor
fault
f. Motor damaged
a. Replace the wiring
between display
board and locating
board
b. Replace locating
board
c. Check and repair
mechanical part
d. Replace control board
e. Replace wiring
between control
board and motor
f. Replace motor
E2 Flash
a. Component on locating
board damage
b. Wiring of locating board
fails to work
c. Control board is faulty
a. Replace locating
board
b. Replace locating
board wiring
c. Replace Control board
E3 or E4 Flash
a.
Control board is faulty
a.
Replace Control
Board

Page | 16
Table of contents
Other Runxin Control Unit manuals
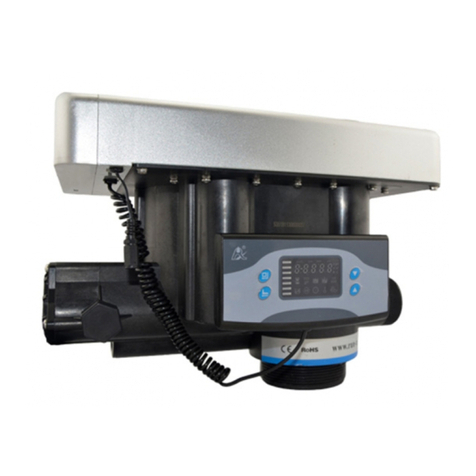
Runxin
Runxin 63518 User manual
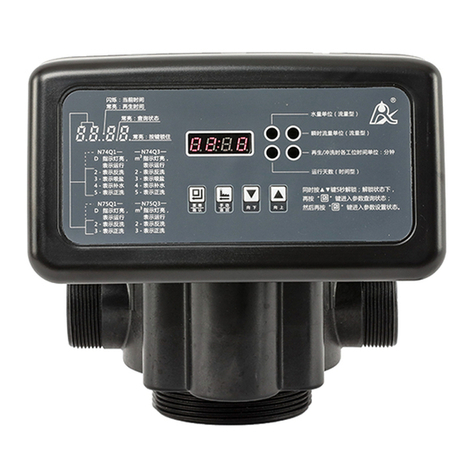
Runxin
Runxin N74Q1 User manual
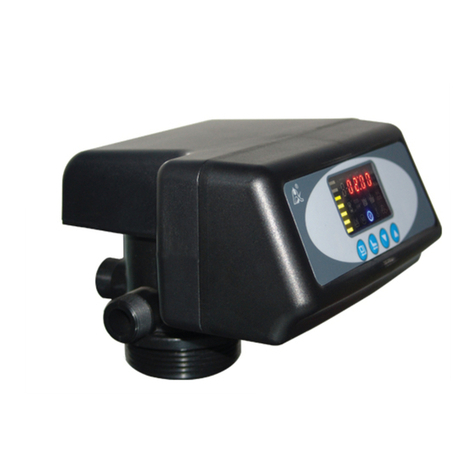
Runxin
Runxin F71B1 User manual
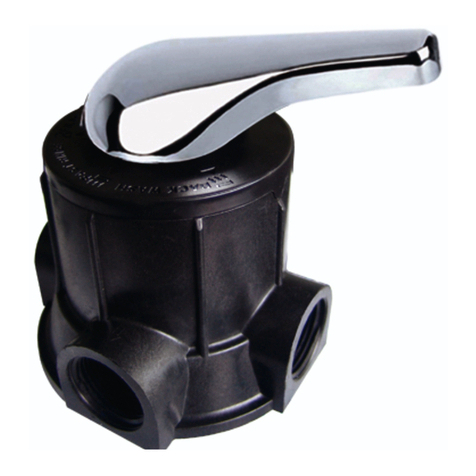
Runxin
Runxin F56A User manual
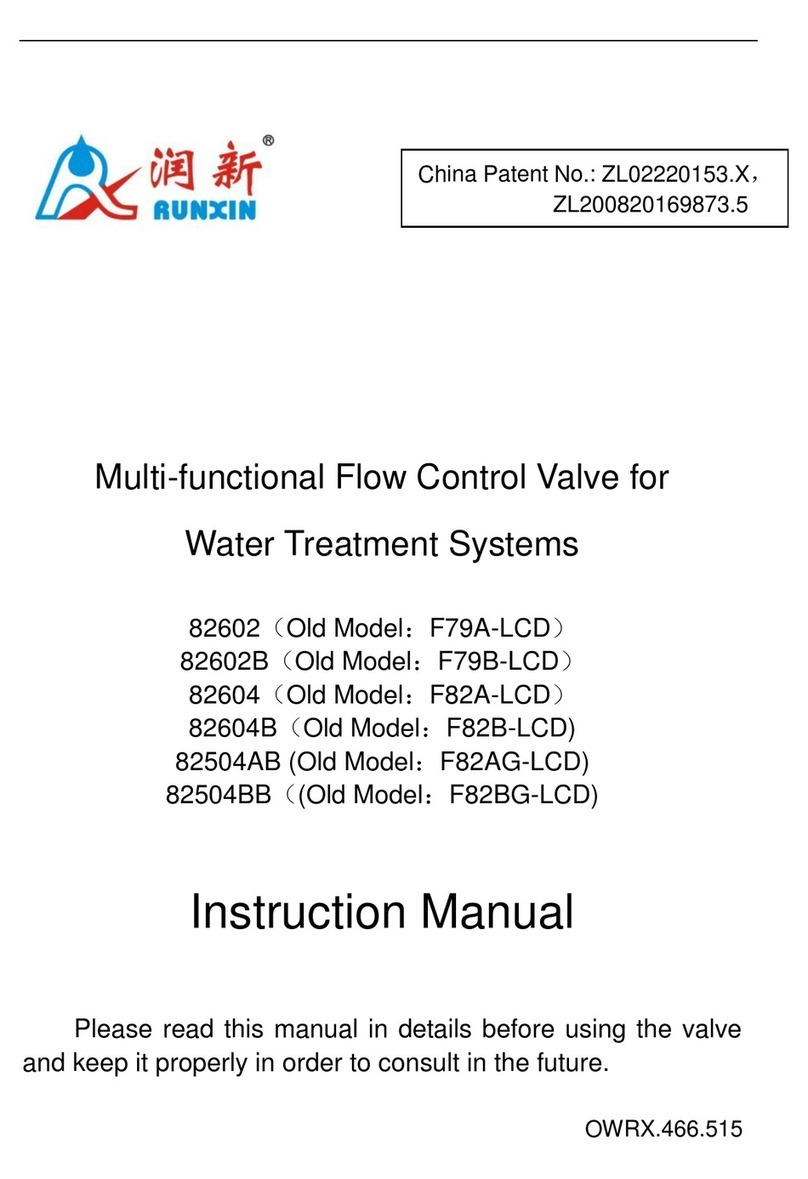
Runxin
Runxin F79A-LCD User manual
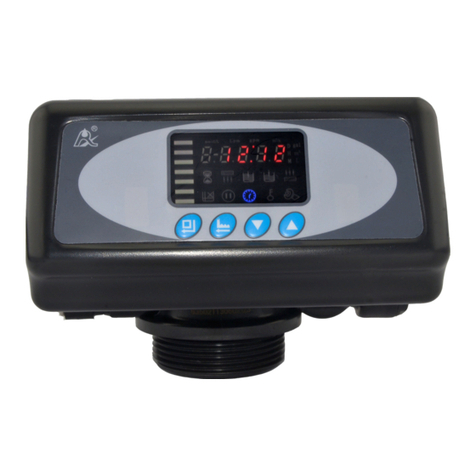
Runxin
Runxin 63504 User manual
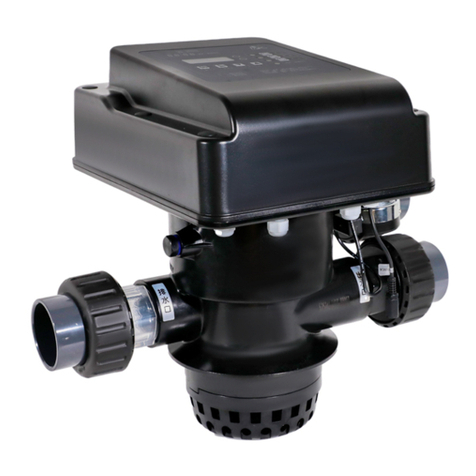
Runxin
Runxin F139 User manual

Runxin
Runxin 51215 User manual
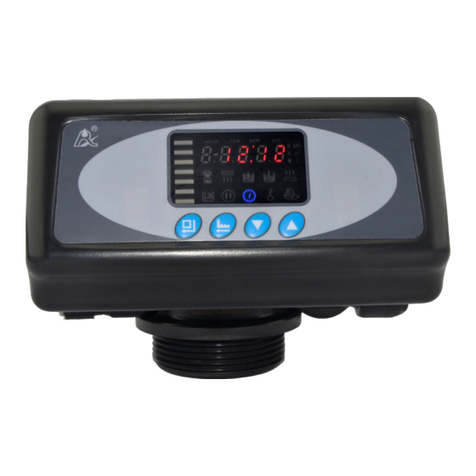
Runxin
Runxin 63504 User manual
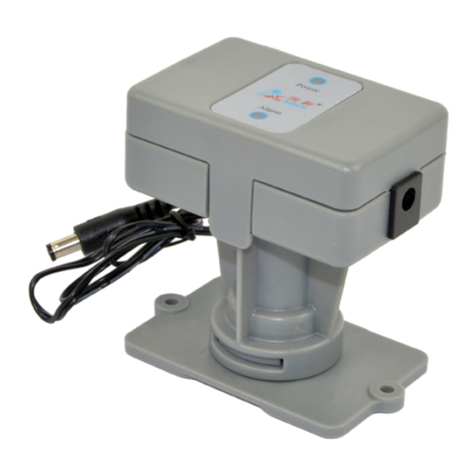
Runxin
Runxin F104 A User manual