SEA GATE 1 DG R1 User manual

International registered trademark n. 2.777.971
SEA USA Inc.
10850 N.W. 21st unit 160 DORAL MIAMI
Florida (FL) 33172 USA
Tel. -
Toll free:
:++1-305.594.1151 ++1-305.594.7325
800.689.4716
web site: www.sea-usa.com
e-mail: [email protected]
CONTROL UNIT FOR SLIDING GATES,
SWING GATES, BARRIERS AND GARAGE DOORS
GATE 1 DG R1
Rev.04 - 06/201467410179
tras

DETAILS
General
An appliance shall be provided with an instruction manual. The instruction manual shall give instructions for the installation,
operation, and user maintenance of the appliance.
The installation instructions shall specify the need for a grounding-type receptacle for connection to the supply and shall stress the
importance of proper grounding.
The installation instructions shall inform the installer that permanent wiring is to be employed as required by local codes, and
instructions for conversion to permanent wiring shall be supplied.
Information shall be supplied with a gate operator for:
a) The required installation and adjustment of all devices and systems to effect the primary and secondary protection against
entrapment (where included with the operator).
b) The intended connections for all devices and systems to effect the primary and secondary protection against entrapment. The
information shall be supplied in the instruction manual, wiring diagrams, separate instructions, or the equivalent.
Vehicular gate operators (or systems)
A vehicular gate operator shall be provided with the information in the instruction manual that defines the different vehicular gate
operator Class categories and give examples of each usage. The manual shall also indicate the use for which the particular unit is
intended as defined in Glossary, Section 3. The installation instructions for vehicular gate operators shall include information on
the Types of gate for which the gate operator is intended.
A gate operator shall be provided with the specific instructions describing all user adjustments required for proper operation of the
gate. Detailed instructions shall be provided regarding user adjustment of any clutch or pressure relief adjustments provided. The
instructions shall also indicate the need for periodic checking and adjustment by a qualified technician of the control mechanism
for force, speed, and sensitivity.
Instructions for the installation, adjustment, and wiring of external controls and devices serving as required protection against
entrapment shall be provided with the operator when such controls are shipped with the operator.
Instructions regarding intended installation of the gate operator shall be supplied as part of the installation instructions or as a
separate document. The following instructions or the equivalent shall be supplied where applicable:
a) Install the gate operator only when:
1) The operator is appropriate for the construction of the gate and the usage Class of the gate,
2) All openings of a horizontal slide gate are guarded or screened from the bottom of the gate to a minimum of 4 feet (1.22
m) above the ground to prevent a 2-1/4 inch (57.2 mm) diameter sphere from passing through the openings anywhere in
the gate, and in that portion of the adjacent fence that the gate covers in the open position,
3)All exposed pinch points are eliminated or guarded, and
4) Guarding is supplied for exposed rollers.
b) The operator is intended for installation only on gates used for vehicles. Pedestrians must be supplied with a separate access
opening. The pedestrian access opening shall be designed to promote pedestrian usage. Locate the gate such that persons will
not come in contact with the vehicular gate during the entire path of travel of the vehicular gate.
c) The gate must be installed in a location so that enough clearance is supplied between the gate and adjacent structures when
opening and closing to reduce the risk of entrapment. Swinging gates shall not open into public access areas.
d) The gate must be properly installed and work freely in both directions prior to the installation of the gate operator. Do not over-
tighten the operator clutch or pressure relief valve to compensate for a damaged gate.
e) (not applicable)
f) Controls intended for user activation must be located at least six feet (6’) away from any moving part of the gate and where the
user is prevented from reaching over, under, around or through the gate to operate the controls. Outdoor or easily accessible
controls shall have a security feature to prevent unauthorized use.
International registered trademark n. 2.777.971
GATE 1 DG R1
67410179 Rev.04 - 06/2014
2

g) The Stop and/or Reset button must be located in the line-of-sight of the gate. Activation of the reset control shall not cause the
operator to start.
h)Aminimum of two (2) WARNING SIGNS shall be installed, one on each side of the gate where easily visible.
i) For gate operators utilizing a non-contact sensor:
1) See instructions on the placement of non-contact sensors for each Type of application,
2) Care shall be exercised to reduce the risk of nuisance tripping, such as when a vehicle, trips the sensor while the gate is
still moving, and
3) One or more non-contact sensors shall be located where the risk of entrapment or obstruction exists, such as the
perimeter reachable by a moving gate or barrier.
j) For a gate operator utilizing a contact sensor:
1) One or more contact sensors shall be located where the risk of entrapment or obstruction exists, such as at the leading
edge, trailing edge, and postmounted both inside and outside of a vehicular horizontal slide gate.
2) One or more contact sensors shall be located at the bottom edge of a vehicular vertical lift gate.
3) One or more contact sensors shall be located at the pinch point of a vehicular vertical pivot gate.
4) Ahardwired contact sensor shall be located and its wiring arranged so that the communication between the sensor and
the gate operator is not subjected to mechanical damage.
5) A wireless contact sensor such as one that transmits radio frequency (RF) signals to the gate operator for entrapment
protection functions shall be located where the transmission of the signals are not obstructed or impeded by building
structures, natural landscaping or similar obstruction. A wireless contact sensor shall function under the intended end-
use conditions.
6) One or more contact sensors shall be located on the inside and outside leading edge of a swing gate.Additionally, if the
bottom edge of a swing gate is greater than 6 inches (152 mm) above the ground at any point in its arc of travel, one or
more contact sensors shall be located on the bottom edge.
7) One or more contact sensors shall be located at the bottom edge of a vertical barrier (arm).
Revised 56.8.4 effective February 21, 2008
Instruction regarding intended operation of the gate operator shall be provided as part of the user instructions or as a separate
document. The following instructions or the equivalent shall be provided:
IMPORTANT SAFETY INSTRUCTIONS
WARNING – To reduce the risk of injury or death:
ATTENTION: pour réduire le risque de dommages ou mort:
1. READAND FOLLOW ALL INSTRUCTIONS.
2. Never let children operate or play with gate controls. Keep the remote control away from children.
3.Always keep people and objects away from the gate. NO ONE SHOULD CROSS THE PATH OF THE MOVING GATE.
4. Test the gate operator monthly. The gate MUST reverse on contact with a rigid object or stop when an object activates the non-
contact sensors. After adjusting the force or the limit of travel, retest the gate operator. Failure to adjust and retest the gate
operator properly can increase the risk of injury or death.
5. Use the emergency release only when the gate is not moving.
6. KEEP GATES PROPERLY MAINTAINED. Read the owner’s manual. Have a qualified service person make repairs to gate
hardware.
7. The entrance is for vehicles only. Pedestrians must use separate entrance.
8. SAVE THESE INSTRUCTIONS.
International registered trademark n. 2.777.971
GATE 1 DG R1
67410179 Rev.04 - 06/2014 3

Rev.04 - 06/2014
CN2CN3
TR1
JOLLY
CN6
CN1
CMS CN5
CN4
CNA
EXP
R1
R2
UP DOWN OK
DS
CNP
F1
F2
T1
CN7
TECHNICAL SPECIFICATIONS
Control unit power supply: 115Vac 50/60 Hz
Absorption in stand by: 30 mA
Environment temperature : -4°F +176°F
Specifications of external enclosure: 183 X 238 X 120 - Ip55
155 mm
85 mm
JOLLY-JOLLY2
RECEIVER RX
CN1 = Input/output connectors
CN2 = Motor and capacitors and
courtesy light connector
CN3 = Power connector
CN4 = 24V~ connector
CN5 = Encoder connector
CN6 = Pre-wired limit switch connector
CN7= Limit switch connector not pre-wired
CNA = RX Receiver connector
CNP = Porgramming connector
EXP = Expansion module connector
JOLLY = Jolly and Jolly 2 connector
DS = Programming display
CMS = MASTER/SLAVE connector
OK = Programming button
DOWN = Programming button
UP = Programming button
T1 = Motor piloting Triac
R1 = Relay C motor command Courtesy light
R2 = Relay motor exchange
F1 = Power supply 10AT fuse
F2 = Accessories 1A fuse
TR1 = Power transformer
COMPONENTS
GATE 1 DG R1
International registered trademark n. 2.777.971
67410179
4

67410179
CONNECTIONS
24Vac
Max 150 mA
CN4
JUMPERS
WARNING: The control unit is designed with the automatic detection of not used N.C. inputs (Photocells, Stop and Limit
switch) except the SAFETY EDGE input. The exclude inputs in self-programming can be restored in the “Check inputs”
menu without need to repeat the programming (page 15).
The herein reported
functions are
available starting
from revision 12.
LIMIT SWITCH
CN7
Limit switch Opening 1 (Green)
Limit switch Closing 1 (Yellow)
123 4 5 6 7 8 910 11 12 13
CN1
Start
Stop
Common
Antenna
START Pedestrian
Common
Photocell 1
Common
ANT COM START
PEDST
STOP COM PH1 PH2
EDGE
24VAUX
COM 24V(FL) (FL)-
Safety edge 1
Flash (-)
+ +
- -
AUX
(24V 500 mA max)
24V 500 mA max
(Accessories)
14 15 16 17 18 19 20
CN2
Flash N
M1
LIGHT
LIGHTN MCL MN MOP CAPACITOR
123 4 5 6 7 8 910 11 12 13
CN1
Flash Light
Motor 1 opening
Motor 1 Neutral
Motor 1 closing
Capacitor
Motor 1
1
CN6
24V (Red)
Common (White)
Limit switch Opening 1 (Green)
Limit switch Closing 1 (Yellow)
Photocell 2
Start
Stop
Common
Antenna
START Pedestrian
Common
Photocell 1
Common
ANT COM START
PEDST
STOP COM PH1 PH2
EDGE
24VAUX
COM 24V(FL) (FL)-
Safety edge 1
Flash (-)
+ +
- -
AUX
(24V 500 mA max)
24V 500 mA max
(Accessories)
Photocell 2
Optional
Obligatory jumper
without accessory
connection.
GATE 1 DG R1
International registered trademark n. 2.777.971
Rev.04 - 06/2014 5

667410179
GATE 1 DG R1
International registered trademark n. 2.777.971
OK
UP DOWN
PROGRAMMING
BUTTONS
QUICK START
Skip this step if you do not want to program a transmitter
MENU
SEA
SET
MENU
SEA
SET
MENU
SEA
SET
MENU
SEA
SET
MENU
SEA
SET
MENU
SEA
SET
MENU
SEA
SET
MENU
SEA
SET
MENU
SEA
SET
MENU
SEA
SET
OK to exit
Menu
or press the
button of
the next
TX to be stored
Choose the type of
motor with
UP or DOWN
With UP or DOWN
choose
the desired logic
To confirm and return
to main menu
With UP or DOWN
choose a delay for
automatic closing
With UP or DOWN
Choose ON
With UP or DOWN choose ON
to start times learning
At the end of the selflearning
the control unit returns automatically
to the main menu
With
UP or DOWN Choose
ON to start test
To confirm and return to
main menu
Skip this step if a TX has already been stored
OK
Press the
button of the
TX to be
stored
To confirm and return
to main menu
To confirm and return
to main menu
OK
OK
OK OK
OK OK
OK OK
OK OK
OK OK
UP
UP
UP
UP
UP
UP
OK To confirm and return
to main menu
Skip this step
if you wna tto work
in half-automatic
logic
1
2
3
4
5
6
7
MENU
SEA
SET
MENU
SEA
SET
OK
UP
LANGUAGE ITALIANO
UP
8
PRESS
BUTTON STORED
TRANSMITTERS
START
MOTOR
LOGIC
PAUSE TIME
START IN
PAUSE
PROGRAM-
MING
TEST START
MENU
SEA
SET
RECEIVER
MISSING
If on the display
appears the item:
Check if a receiver has
been connceted
(see page 4)
(See
page 7)
The gate will execute a CLOSING-OPENING-CLOSING CYCLE
(See
page 7)
UPDOWN
ALL OTHER PARAMETERS HAVE DEFAULT SETTINGS WHICH ARE USEFUL FOR THE 90% OF
THE APPLICATIONS BUT CAN BE HOWEVER SET THROUGH THE SPECIAL MENU. FOR
ENTERING INTO THE SPECIAL MENU MOVE ON ONE OF THE MENU AND PRESS THE UP
AND DOWN BUTTONS AT THE SAME TIME FOR 5 S.
PROGRAMMING
Rev.04 - 06/2014

7
67410179
MENU Default
SET
MENU FUNCTIONS TABLE GATE 1 DG R1
Description Set value
Italian
English
French
Spanish
stop
start
off
1 240
Start
Stop start
off
Ele(trokydravl (
E(kan (
U
Sliding
Reversible sliding gate
Electrohydraulic
off
6 - start n pavse on
Off on
off
off
Off on off
vnlo(k
Storing of a command
for unlocking an
electric brake
U
2 - trans tters
External odvle
U
Pedestr an Start
(Lear e ory
UU
Delete a trans itter
U
Ped Start.
External module
Pedestrian Start
Delete single transmitter
Delete transmitter memory
3 - otor
U
Sl d ng
E(kan (
U
4 - log (
Avto at (
U
open-stop-(lose-stop-open
2 bvttons
safety
Dead an
U
open-stop-(lose-open
Automatic
Step by step type 1
Step by step type 2
Two buttons
Safety
Dead man
Avto at (
U
5 - paVse t e
U
Setting from 1s to 4min.
OFF
(semi-automatic logics)
7 - progra ng
UU
8 - test start
end
Start command
Times learning start
Select END and press OK to exit the menu.The menu
deactivates automatically after 2 minutes
In pause start is not acceped
In pause start is accepted
AGNET ( Sl d ng gate
U
REUERS BLE Sl d ng gate
Sliding gate with magnetic
limit switch
Tripkase - bvll
Three-phase - Bull
seagear
Seagear
Hydraulic motors
Note 1: The * indicates that the default value may change depending on the selected motor type.
1 - langvage
espanol
engl sk
fran(a s
tal ano
tal ano
dut(k Dutch
GATE 1 DG R1
International registered trademark n. 2.777.971
(See page 9)
(See page 8)
Rev.04 - 06/2014

The control unit is pre-set with the default settings, to start the control unit with the
DEFAULT settings just keep pressed the UP and DOWN buttons at the same time power
supplying the control unit the display shows the message init.
The DEFAULT settings are shown in the Menues table.
SELFLERNING OPERATION TIME WITH ENCODER
When an encoder is installed, it is necessary to select On in the En(oder menu, start programming and make sure
that leaf starts as first in closing. The gate will automatically execute the following cycle: CLOSING - OPENING -
CLOSING.
Note: For stop detection sensitivity setting refer to the special menu.
SELFLEARNING OPERATION TIME WITH AMPEROMETRIC SENSOR
(For electromechanical motors only)
The times learning can be done only on electromechanical gates, taking advantage of the automatic detection of the
stops.
Once the programming has been started just make sure that the gate executes the following cycle: CLOSING -
OPENING - CLOSING.
Note: For stop detection sensitivity setting refer to the special menu.
LEARNING WITH LIMIT SWITCH (WITH OR WITHOUT ENCODER)
When limit switches are mounted, the gate executes automatically the following cycle: CLOSING - OPENING -
CLOSING.
Before starting the learning, make sure (through the test menu), that the relative limit switches of every opening are
employed.
WORKING TIMES SELFLEARNING THROUGH IMPULSES
ATTENTION: This procedure is potentially dangerous and should only be performed by qualified people in
safety conditions.
NOTE: The card is preset with the standard working times, therefore the automation can be started even
without the times programming, simply by adjusting the timing on the display (see default times).
1) Turn off electricity, release the motors and manually position the leaves on halfway.
Reset the mechanical lock.
2) Connect the control board to the power supply
3) Select on the on-board display or JOLLY programmer, the type of motor that you are using as indicated in
the dispaly management.
4) If necessary also set the operation logic and the other parameters. If you want to program with a transmitter, store a
transmitter before programming.
5) Select PROGra ing on the display, press OK and than one of the UP or DOWN buttons.
(If the motor starts in opening, remove and re-put power supply, select on the display reuerse otor. And through
the UP and DOWN button put it on ON, or if you have the Jolly programmer, activate the motor exchange function. )
6)At this point the gate will start the following cycle: CLOSING - OPENING - CLOSING.
During cycle, to store the respective stops, press UP or DOWN or START at every point of stop of the leaf.
7) The self-learning is done.
U
UU
67410179
GATE 1 DG R1
International registered trademark n. 2.777.971
WORKING TIMES SELF LEARNING
Rev.04 - 06/2014
8

FUNCTION LOGIC
AUTOMATIC LOGIC
Astart impulse opens the gate.Asecond impluse during the opening will not be accepted.
Astart impulse during closing reverses the movement.
SECURITY LOGIC
Astart impulse opens the gate.Asecond impulse during opening reverses the movement.
Astart impulse during closing reverses the movement.
STEP BY STEP TYPE 1 LOGIC
The start impulse follows the OPEN-STOP-CLOSE-STOP-OPEN logic.
STEP BY STEP TYPE 2 LOGIC
The start impulse follows the OPEN-STOP-CLOSE -OPEN logic.
DEAD MAN LOGIC
The gate opens as long as the START button of opening is pressed; releasing it the gate stops. The gate closes as
long as the button connected to the PEDESTRIAN START is pressed; releasing it the gate stops. To execute
complete opening and/or closing cycles the related pushbuttons must be constantly pressed.
2 PUSHBUTTONS LOGIC
One start opens, one pedestrian start closes. In opening the closing will not be accepted. In closing a start command
reopens, a pedestrian start command (closes) will be ignored.
NOTE 1: To have the automatic closing it is necessary to set a pause time, otherwise all the logic will be semi-
automatic.
NOTE2: It is possible to choose, whether to accept or not, the start in pause, selecting in the MENU the item
Startin pavse and choosing ON or OFF. By default, the parameter is OFF.
NOTE 1: To have the automatic closing it is necessary to set a pause time, otherwise all the logic will be semi-
automatic.
NOTE2: It is possible to choose, whether to accept or not, the start in pause, selecting in the MENU the item
Startin pavse and choosing ON or OFF. By default, the parameter is OFF.
NOTE 1: To have the automatic closing it is necessary to set a pause time, otherwise all the logic will be semi-
automatic.
NOTE2: It is possible to choose, whether to accept or not, the start in pause, selecting in the MENU the item
Startin pavse and choosing ON or OFF. By default, the parameter is OFF.
NOTE 1: To have the automatic closing it is necessary to set a pause time, otherwise all the logic will be semi-
automatic.
NOTE2: It is possible to choose, whether to accept or not, the start in pause, selecting in the MENU the item
Startin pavse and choosing ON or OFF. By default, the parameter is OFF.
GATE 1 DG R1
International registered trademark n. 2.777.971
Rev.04 - 06/201467410179 9

PRESS AT THE SAME TIME FOR 5 SECONDS TO ENTER OR TO EXIT THE SPECIAL MENU
UPDOWN
10 67410179
GATE 1 DG R1
International registered trademark n. 2.777.971
SPECIAL MENU
MENU SP Default
SET
10 100
10 100
0.0 5.0
Pre-flashing only
active before closing
75
Off
75
3 - Pvshouer
Off
Only (los ng
Off
4 - pvsk ng stroke
Off 3
Off 50 20
Off 50 20
bvzzer Buzzer
9 - reuerse otor
U
Off
On
Off
Off
SPECIAL MENU FUNCTIONS TABLE GATE 1 DG R1
UP and DOWN
press END or
UP and DOWN
For entering into the special menu move on one of the menu and press the
buttons at the same time for 5 s. For exiting the special menu move on one of the
menu and press the buttons at the same time for 5 s.
Description Set value
1 - open ng torq 1 *
2 - (los ng torq 1 *
Opening torque
Note: with hydraulic motors
the torque will be on 100%
Closing torque
Note: with hydraulic motors
the torque will be on 100%
Open ng and (los ng
Only open ng
Disabled
Opening an closing
Opening only
Closing only
From OFF to 3 seconds
6 - (los ng sloudoun
5 - open ng sloudoun
From OFF to 50% of
the stroke
From OFF to 50% of
the stroke
7 - preflasx ng
8 - flasx ng l gxt
Only (los ng
Nor al
U
L gxt
aluays
Normal
Control lamp
Always ON
Pre-flashing time
Synchronized right motor
Synchronized left motor
Nor al
U
20
13 - (ourtesy l gxt
N (y(le
Courtesy light setting
from 1s to 4min.
Courtesy light in cycle
Indicates the working times selflearning
in opening and closing.
With UP or DOWN it is possible to increase
or reduce the working times.
OFF
ON
Off
Off
10 - EN(ODER *
xxx.s
Xxx.
xxx.s
Xxx.
11 - opening ti e
u
12 - (losing ti e
u
10 - EN(ODER *
11 - en(oder tot.
12 - en(oder par.
In ON enables the
Encoder, in OFF
it's disabled
In ON enables the
Encoder, in OFF
it's disabled
Encoder impulses stored in programming
Encoder impulses during operation
1 240
Off on Off
14 - traff ( l gxt
reseruat on
When setting this function
the pedestrian input will be
activated to work on the
auxiliary board SEM
(traffic light management).
Note: If the encoder is off, the menus 11and 12 will indicate the "Opening time" and the "Closing Time".
Rev.04 - 06/2014

11
67410179
MENU SP Default
SET
5 100 100
0 10e9 0
1 240
100 10e4
0 100 100%
10e4
= start
Off
= start
22 - EDGE
20 - t er
U
off
off
ONLY (LOS NG
23 - EDGE
8x2
Description Set value
15 - pedestr an open ng
Setting from 20 to 100
16 - pedestr an PAvSE
17 - a((elerat on
18 - a ntenan(e (y(les
U
19 - perfor ed (y(les
U
Pause in pedestrian
opening same as in
total opening
Disabled
Acceleration ramp
Setting from 1s to 4 min.
Setting from 100 to
100000
Reports the executed
cycles. Keep pressed OK
to reset the cycles
ON PXOTO2
ON PEDESTR AN ENTRY
Disabled
Timer function active
on photocell 2
Timer function active on
pedestrian input
OPEN NG AND (LOS NG
ONLY OPEN NG
Active in opening
and closing
Active only in opening
Active only in closing
OPEN NG
AND
(LOS NG
Nor al
U
Edge is active and
protected by a 8k2 resistor
Normal N.C. contact
Nor al
U
ON PKOTO2
ON PEDESTR AN ENTRY
off
21 - f re su t(k
off
Disactivated
Active on Photo 2
Active on pedestrian
stop
24 - PKOTO1
(LOS NG
Stop AND (LOSE
(LOSE
PAUSE RELOAD
Photocell active in closing
Photocell active before
opening
The photocell gives a
command to close during
opening, pause and
closing
The photocell charging
the pausing time
The photocell stops in closing
and closes when released
(LOS NG
OPEN NG
Photocell active in opening
Until occupied, with open
gate, it prevents reclosing.
It is switched off during
closing.
Skadou loop
If the photocell is occupied
during opening, pause or
closing, the gate reopens
completely and closes
without observing the
pause time.
Delay pause ti e
u
GATE 1 DG R1
International registered trademark n. 2.777.971
Rev.04 - 06/2014

12 67410179
25 - PKOTO2
26 - 24u avx *
MENU SP Default
SET
0 20
0.1
28 - OTOR RELEASE
U
Off
0.1 3.0
29 - BRAKE *OFF 100%
1
Description Set value
stop
OPEN NG
(LOS NG
Stop AND (LOSE
(LOSE
PAUSE RELOAD
Photocell active in closing
Photocell active before
opening
The photocell gives a
command to close during
opening, pause and
closing
The photocell charging the
pausing time
The photocell stops in closing
and closes when released
OPEN NG
ALUAYS
N (Y(LE
N pavsE
OPEN NG
(LOS NG
POS T UE BRAKE
ANAGE ENT
UU
NEGAT UE BRAKE
ANAGE ENT
U
U
Positive Electrobrake
Negative Electrobrake
27 - POS T ON RE(OUERY
Retrieves the inertia of the
motor after Stop or
reversing from 0 to 20 s
Disabled
Setting from 1 to 3
Adjusts the braking on the
limit switches
ALUAYS
0
Photocell active in opening
Skadou loop
avtotest
N (Y(LE AND
fototest
Security test
Security test with power
supply only during cycle
Until occupied, with open
gate, it prevents reclosing.
It is switched off during
closing.
off 8
30 - PER OD (AL pvshouer
off
Allows the repetition of the
Pushover functionat a
distance of time adjustable
from 0 to 8 hours at hourly
intervals
If the photocell is occupied
during opening, pause or
closing, the gate reopens
completely and closes
without observing the
pause time.
Delay pause ti e
u
GATE 1 DG R1
International registered trademark n. 2.777.971
AUX output always
power supplied
AUX output power
supplied only during opening
AUX output power
supplied only during closing
AUX output power
supplied only during pause
AUX output active only
during cycle
Rev.04 - 06/2014

13
67410179
GATE 1 DG R1
International registered trademark n. 2.777.971
MENU SP Default
SET
Off
off
Off
On
1 10
34- sloudoun ra p torq *
U
100
Description Set value
31 - ant ntrvs on
ONLY (LOS NG
ONLY OPEN NG
OPEN NG AND (LOS NG
Only on limit switch in opening.
If the limit switch is freed
manually it forces the
reopening of the gate
Only on limit switch in closing.
If the limit switch is freed
manually it forces the
reclosing of the gate
The flashing light remains
ON with active timer and
open gate
The flashing light remains
OFF with the active timer
and open gate
32 - FLASX NG L GXT AND
t er
U
Shows last event
(See alarms table)
33 -d agnost (S
Adjusts the transition
between max. torque
and slowdown
0
0 100
0
0 100
Adjust the tolerance
between stop and
obstacle motor opening.
off
off
off
off
35 - OPEN NG TOLERAN(E
36 - (los ng TOLERAN(E
37 - open ng sens t u ty *
38 - (los ng sens t u ty *
Disabled
Motor sensitivity
adjustment in opening
Disabled
Motor sensitivity
adjustment in closing
Adjust the tolerance
between stop and
obstacle motor closing.
off
off
39 - slou doun
sens t u ty
Reversing sensitivity
adjustment during
slowdown
Disabled
On limit switches in closing
and in opening. If the limit
switch is freed manually it
forces the reopening and the
reclosing of the gate
off Disabled
photo1
photo2
Off Disabled
Autotest only on photo 1
Autotest only on photo 2
40 - AVTOtest
photo1-2
Off
edge
PKOTO1 AND edge
PKOTO2 AND edge
Autotest only on photo 1
and 2
Autotest only on safety edge
Autotest photo 1 and
safety edge
Autotest photo 2 and
safety edge
Autotest photo 1, photo 2
and safety edge
ALL SAFE
0%
100%
10% (max) 99% (min)
10% (max) 99% (min)
10% (max) 99% (min)
Rev.04 - 06/2014

14 67410179
GATE 1 DG R1
International registered trademark n. 2.777.971
MENU SP Default
SET
43 - passuord ---- ----
Description Set value
Allows the entering of a
password blocking the
control unit parameters
modification.
END Select END and press OK to exit the special menu.
The special menu switches off automatically after 20 minutes.
Note 1: The * indicates that the default value may change depending on the selected motor type.
Note 2: After initialization the parameters "motor type" and "limit switch type" remain son the value chosen in the
setup program.
Avto at (
U
ONLY (LOS NG
42 - aster-slaue
U
aster
U
Slaue
off
off
Avto at (
U
41 - sELE(T L T SU T(K
U
ONLY OPEN NG
Limit switch in automatic
recognition
Only limit switch in
opening present
Only limit switch in
closing present
Disabled
For applications with two
motors in master-slave,
you can set the control
unit as slave.
For applications with two
motors in master-slave, it
allows to set the control
unit as master
To be activated if there is
a limit switch that stops
the motor phase.
Otor internal
U
PASSWORD ENTERING MANAGEMENT
With a new control unit all menus can be displayed and set and the password will be disabled.
Selecting one of the Menus and keeping UP and DOWN pressed at the same time for 5 seconds, you will access the SP Menu
containing the Passuord Submenu.
Pressing OK in the Passuord Menu, you will proceed with the entering of the numeric code of the 4-digit PASSWORD.
Use UP and DOWN to increase or decrease the number, press OK to confirm it and you will pass automatically to the entering of
the next number. Pressing OK after the last entered number the word SvRE? appears, confirm the activation of the PASSWORD
and the message Ok appears, pressing UP or DOWN instead you can cancel the operation and NO OPERATION will appear on the
display.
Once entered the PASSWORD, it will be definitively activated, once the display switch off timeout has expired, or by turning off
and on again the control unit. Once the PASSWORD has been activated, the menus of the display can be only displayed but not
set. To unlock them you must enter the correct PASSWORD in the Passuord menu, if the password is wrong the message ERRor
will appear.
At this point, if the password has been entered correctly, the menus will be unlocked and it will be possible to change the
parameters of the control unit again.
If the control unit has been unlocked through Passuord Menu, it is possible to enter a new and different password, using the
same entering process as for the first one; at this point, the old password will no longer be valid.
If the password has been forgotten, the only way to unlock the control unit is to contact the SEA technical assistance, which will
assess whether to provide the procedure to unlock the control unit or not.
Note: The password cannot be set through the Jolly or Jolly 2 terminal.
Rev.04 - 06/2014

MENU
SEA
SET
---
--
---
DISPLAY INPUT STATUS
When the segment
is ON during self-
learning, the input
status is closed or
OFF.
Start
Start
pedestrian
Stop
Limit
Switch
opening
motor
Photocell 1
Photocell 2
Edge
Limit
Switch
closing
motor
u.001
seage
UP
OK
UP
UP
UP
DOWN
DOWN
DOWN
OK
OK
OK
DOWN
otOR
U
Initial system
Software Version
Programming example
Sl d
TR pk
67410179
L T SU T(H
(LOS NG
U
L T SU T(H
OPEN NG
U
MENU
start
Description Description
EDGE
PHOTO1
PHOTO2
PedESTR AN Start
END
Start test
Stop test
Pedestrian
start test
Safety edge
test
Photocell 1
test
Photocell 2
test
Opening
limit switch
test
Closing
limit switch
test
The contact must be a N.O. Contact . When activating the related command
on the display SET lights up, the input works.
If SET is always on, check the wirings.
The contact must be a N.C. Contact. When activating the related command
on the display SET lights up, the input works.
If SET is always on, make sure that the contact is a N.C. Contact
The contact must be a N.C. Contact. When activating the related command
on the display SET lights up, the input works. If SET is always on, make
sure that the contact is a N.C. contact or that the related limit switch is not occupied.
The contact must be a N.O. Contact. When activating the related command
on the display SET lights up, the input works.
If SET is always on, check the wirings.
The contact must be a N.C. Contact. When activating the related command
on the display SET lights up, the input works.
If SET is always on, make sure that the contact is a N.C. Contact
IThe contact must be a N.C. Contact. When activating the related command
on the display SET lights up, the input works.
If SET is always on, make sure that the contact is a N.C. Contact
The contact must be a N.C. Contact. When activating the related command
on the display SET lights up, the input works.
If SET is always on, make sure that the contact is a N.C. Contact
The contact must be a N.C. Contact. When activating the related command
on the display SET lights up, the input works. If SET is always on, make
sure that the contact is a N.C. Contact or that the related limit switch is not occupied.
Exit menu
stop OK
OK
OK
MENU FUNCTION TABLE CHECK GATE 1 DG R1 INPUTS
To access the Menu for input check keep pressed OK for about 5 seconds.
enabled
blo(ked
enabled
blo(ked
enabled
blo(ked
OK
enabled
blo(ked
Note: If the Stop, Photocell 1 and Photocell 2 contacts are not bridged in self-learning, they will be
deactivated and can be reactivated through this menu, without repeating times self-learning.
The settings of the control unit are made through the UP, DOWN and OK buttons. The UP and DOWN buttons to scroll
through the MENUS and SUBMENUS. By pressing OK you enter from MENU into SUBMENU and confirm the choice.
Moving in the language menu pressing the UP and DOWN buttons at the same time you access the SP MENU for special
settings.
Moving in the language menu pressing the OK button for 5 seconds, you enter the CHECK MENU, where you can check
the operating status of all inputs.
GATE 1 DG R1
International registered trademark n. 2.777.971
MENU FOR INPUT CHECK
Rev.04 - 06/2014 15

67410179
GATE 1 DG R1
International registered trademark n. 2.777.971
RADIO TRANSMITTER SELF LEARNING
WITH RECEIVER ON BOARD OF CONTROL UNIT
!!
ROLLING CODE:
press twice
1 2 3 4
0
1
2
3
4
5
TABLE EXAMPLE
Transmitter
button
Memory
location Serial number Customer
WARNING: Make the radio transmitters programming before you connect the antenna and insert the receiver into the
special CMR connector (if available) with turned off control unit.
With RF UNI module it will be possible to use both Coccinella Roll Plus transmitters, max. 800 codes (buttons), and radio
transmitters with fixed code, max. 100 codes (buttons). The first memorized radio transmitter will determine the type of the
remaining radio transmitters.
If the receiver is a Rolling Code, press twice the button of the radio transmitter that you want to program to memorize the first TX.
Notes:
- Enter radio transmitters learning only when the working cycle stops and the gate is closed.
- You can store max. 2 of the available 4 functions. If the control unit receives a code which was already associated to another function it will be
updated with the new function.
In the case of transmitters with fixed code it is necessary to press 1 time the button of the transmitter you want to program to store the first
remote control
FIXED CODE:
press once
MENU
SEA
SET
MENU
SEA
SET
MENU
SEA
SET
UP
MENU
SEA
SET
MENU
SEA
SET
MENU
SEA
SET
MENU
SEA
SET
UP
MENU
SEA
SET
MENU
SEA
SET
UP
MENU
SEA
SET
MENU
SEA
SET
MENU
SEA
SET
UP
MENU
SEA
SET
MENU
SEA
SET
UP
MENU
SEA
MENU
SEA
SET
MENU
SEA
SET
MENU
SEA
SET
SET
START
PEDESTRIAN
START
EXTERNAL
MODULE
STOP
DELETE A
TRANSMITTER
0OK? OK
CLEAR
MEMORY OK
PRESS
BUTTON STORED
STORED
STORED
STORED
PRESS
BUTTON
PRESS
BUTTON
PRESS
BUTTON
If you want to program
the pedestrian
start as second
channel.
If you want to
delete a single
transmitter.
If you want to delete
the whole memory
If you want to program
the activation
of the LIGHT
output
as second channel.
Press the
button of the
transmitter
to be stored
Press the
button of the
transmitter
to be stored
Press the
button of the
transmitter
to be stored
Select with
UP or DOWN
the memory
location
to be deleted
and press OK
Press the
button of the
transmitter
to be stored
If you do not want to execute the cancellation,
press UP or DOWN to return to the
TRANSMITTER menu.
Confirm the cancellation.
If you want to
program the
UNLOCH as
second channel.
MENU
SEA
SET
MENU
SEA
SET
UP
MENU
SEA
SET
UNLOCH STORED
PRESS
BUTTON
Press the
button of the
transmitter
to be stored
If you want to
program the
STOP as
second channel.
OK
OK
OK
OK
OK
OK
OK
for 10 s.
MENU
SEA
SET
OK
TRANSMITTERS
OK
Rev.04 - 06/2014
16

TIMER
TX1
TX2
1 2 3 4 5 6 7 8
RX1
RX2
START
START PED.
STOP
-C
CN1
9 10 11 12 13
CN1
11
12
9 10 11 12 13
CN1
-
-
11
11
12
12
11
12
+
3
4
6
5
6
6
7
6
8
START (N.O.) The
An impulse given to this contact opens and closes the automation depending on the selected logic, it can be given by a keyswitch, a keypad, etc.
To connect the other devices refer to the related instructions leaflets. (ie. loop detectors and proximity switches).
Note1: In DEADMAN logic keep pressed the Start for the opening of the automation.
Note2:
START is connected between connector 2 and 3 of the CN 1 terminal.
In the case of triggering a safety device the
timer will automatically reset after 6 seconds.
Holding
START starts the TIMER function, releasing the start, the operator repeats the pause and then performs the closing.
In 2 BUTTONS logic this button performs the opening.
STOP (N.C.) The STOP is connected between the clamps 2 and 5 of the CN1 terminal .
When pressing this button the motor immediately stops in any condition/position. To re-start the movement give a start command.
After a stop the motor always re-starts in closing.
Can be activated through the on-board display or through the Jolly programmer. In both cases it’s a N.O. contact which provoques the
opening of the automation keeping it open as long as it is activated. When it’s released, after having paused for the set pausing time the
gate recloses. The TIMER can be activated on the inputs FOTO2, PEDESTRIAN START or keeping busy the START input.
Note1: When activated on the pedestrian entry, the pedestrian will be OFF also on the radio transmitter.
Note2: In the event of an intervention of a security device during the timer (Stop, amperometric, Edge), a start impulse restors the
movement.
Note3: In case of no power supply with open gate and active Timer the control unit will restore its function, otherwise if during restoring of
the power supply the TIMER is not activated it will be necessary to give a start impulse for the reclosing.
N.B: If you want the autotest just
connect the positive of the devices to
be tested on the input 10 (AUX) and
choose the device on which to
execute the test through the
avtotest or in (y(le and
fototest function.
PEDESTRIAN START (N.O.) The pedestrian start can be connected
between the conectors 2 and 4 of the CN1 terminal .
This input allows a partial opening, the opening space can be set through
the on-board display or through the JOLLY device.
Note1: The contact for partial opening is a N.O. Contact (Normally open).
Holding START starts the TIMER function, releasing the pedestrian start,
the operator repeats the pause and then performs the closing. In the case
of triggering a safety device the timer will automatically reset after 6
seconds.
Note2:In 2 BUTTONS logic it is necessary to keep pressed the Start Ped. to
re-close the automation.
Note3: In deadman logic this button executes the re-closing if you keep it
pressed.
Note4: When closed during pause, the gate will reclose only after this input
has been reopened.
TIMER activation: This input can be transformed into TIMER (See TIMER).
Nota5: When using the Sem card, the pedestrian input can be used as
priority in closing through the traffi( ligkt reseruation function.
+
67410179
OPTIONS ON FOTO1 and FOTO2 adjustable on on- board display or with JOLLY terminal.
FOTO CLOSE activation ((losing): if occupied, reverses the movement in closing, during pause it
prevent the closing.
Activation repeat pause (pavse RELOAD): If occupied, during pause it recharges the timer of pause. In
closing it reverses the movement.
FOTO OPEN activation (oPEning): If activated the photocell blocks the movement as long as it’s
busy, when released the opening continues.
FOTO PARK activation (stop and (lose): in opening it is not active; in pause are activated it
commands the closing when released, otherwise it’s not active; in closing it stops the movement as
long as it is busy, when released the closing continues.
FOTO STOP activation (STOP): When activated before the opening the photocell blocks the
automation as long as it is busy, during the opening it will be ignored. In closing the intervention of the
photocell causes the reopening.
Activation PHOTO CLOSE IMMEDIATELY ((lose): The photocell stops the gate as long as it is
occupied in both opening and closing, when released it gives a closing command (Closing one second
after release of the photocell ).
Skadou loop Activation: Photocell aktive only during pause.
Activation delay pause TI E: If the photocell is occupied during opening, pause or closing,
the gate reopens completely and closes without observing the pause time.
u
GATE 1 DG R1
International registered trademark n. 2.777.971
START - STOP - PEDESTRIAN START - ANTENNA -
PHOTOCELL
Photocell 1 and Photocell 2 Connections
Note: If the photocells are not connected, it is not necessary put a jumper between the clamps (6 and 7
and/ou 6 and 8 of the CN1 terminal)
+ = 24V (Accessories) 500 mAmax COM = 0V PH1 = Photocell contact 1
PH2 = Photocell contact 2
Note: For the autotest connect the TX to theAUX clamp and activate the Autotest function.
The default setting of the photocell 1 is FOTO CLOSE and the one of the photocell 2 is FOTO OPEN.
The photocell 2 can also be set as TIMER (see TIMER function).
Options AUX 24V 500mA max can be set with on-board Display or with
Jolly device. It is possible to chose when having tension on the AUX output.
The options are: always, only during opening, only during cycle, only
before opening or only during pause or for the management of the
positive or negative electrobrake, as security test avtotest and as test
for economic securities in (y(le and fototest.
Rev.04 - 06/2014 17

AMPEROMETRIC DEVICE FOR ELECTROMECHANICAL OPERATORS
This control unit comes with an obstacle detection system working only on electromechanical operators
allowing to have the reversing on obstacles and the automatic detection of the stops.
Sensitivity adjustable from off to 99% inside the special menu. The more the percentage is high the more
the obstacle detection will be difficult. On hydraulic unit this parameter will be always OFF.
ENCODER (CN5 Connector)
The Encoder, unlike the amperometric sensor, can be used both on electromechanical and hydraulic
operators.
The Encoder allows the detection of the gate position and its reversing in case of obstacles. To use the
ENCODER it is necessary to enable it inside the special EN(oder Menu. The sensitivity on the obstacle is
adjustable from 0 - 99%. The higher the percentage is the more it will be difficult to detect the obstacle.
NOTE: If the Encoder is activated it is possible to visualize in the special menu the total memorized
impulses and the partial impulses executed by the motor.
ATTENTION: The first operation, after power failure will be for searching the mechanical stops at the
end of the run.
SAFETY EDGE AND FLASHING LAMP
SAFETY EDGE
Safety edges (EDGE) can be connected between the contacts 9 and 11 of CN1.
Pressing EDGE, the contact opens, causing a partial reversing of the gate in closing and opening.
Note1: If the edge contact is not used it must be
briged The EDGE input can be set: only in closing,
only in opening or in both directions.
Note2: It is possible to activate a balanced edge
8K2 through the on board display or through the
Jolly programmer, in such case the edge contact
will be controled by a specific resistance value,
detecting the possible involontary short circuit of
the device. In case of an imbalanced device a
special alarm will show on the on board display or
on the JOLLY programmer.
.
Note: it is possible to perform an Autotest also on
the powered radio edge.
Waring lamp Flash Led 24V (Accessories) 3W Max (Control lamp)
The warning lamp can be connected between the terminals 24V (Accessories) and FL(-) of CN1
It blinks once per second during opening and twice per second during closing, while it remains lit during
pause.
Throught the warning lamp it is also possible to identify alarm signals comming from the STOP,
PHOTOCELL 1, PHOTOCELL2 and EDGE devices. Through the on board display or the Jolly programmer
it is possible to activate the pre -flashing function and/or to modify the flashing light function choosing
between fixed flashing, control lamp or Buzzer.
The pre-flashing can be set from 0 to 5 s. or it is possible to have it only before closing.
18 67410179
GATE 1 DG R1
International registered trademark n. 2.777.971
ENCODER OR AMPEROMETRIC MANAGEMENT
Safety edge
in closing
10 11 12 13
1 2 3 4 5 6 7 8 9
CN1
12
13
11
9
FL (-)
24V (Accessories)
Common
+-
Rev.04 - 06/2014

International registered trademark n. 2.777.971
M
Capacitor
Opening
CN2
N L
CN3
14 15 16 17 18 19 20
Neutral
Closing
COURTESY
LIGHT
Neutral
COURTESY LIGHT, MOTORS, CAPACITY
AND POWER SUPPLY CONNECTIONS
Timing
from 0 to 4 min
(115V~ 100W Max)
Motor
Motor connection
M = Opening /Closing
Com = COMMON
Motor to be connected in case
of single-leaf.
POWER SUPPLY INPUT
NOTE: For power supply connection follow the rules in force
Example
Line
19
67410179
19
20
14
15
16 17 18
GATE 1 DG R1
Rev.04 - 06/2014

DS
EXP
DS1
DS2
RL4 RL3 RL2 RL1
L4 L3 L2
IC2
-M2+
1 CNP
CN1
L1
M1
24V~ / (ac/dc)
or
115V~
1 2 3 4 5 6 7 8
1
2
3
4
MASTER-SLAVE FUNCTION
CN4
SIGB
COM
SIGA
SIGB
COM
SIGA
M1 M1
To set an installation with two motors in MASTER-SLAVE function it is recommended to do as follows:
1) Set the two motors as if they were two independent installations, make sure that the individual motor works
properly and that the limit switches (when present) are read properly.
2) Once sure of the correct functioning connect the control unit MASTER to the control unit SLAVE through the
special clamp (Code SEA23001220).
3) Now set the control unit, which has to manage the commands and motor 1 (photocell, keyswitch, STOP, safety
edge etc.) as MASTER and the other one which will move motor 2 as SLAVE.
4) Follow up the selflearning of the times of the MASTER control unit.
Note 1: The master and slave settings on the control unit are present in the special menu selecting ASter-slaue.
Note 2:All these operations can also be managed through the JOLLY programmer).
Note 3: On the SLAVE it is possible to set the following functions only: torque, speed, motor type, slowdown speed,
acceleration, deceleration, position recovery, AUX and motor inversion. All other parameters will be set only by the
MASTER control unit.
U
Insert on CN4
of the Master control unit
Insert on CN4
of the Slave control unit
Note: respect the polarity of the cables.
It is recommended to use a two twisted pairs shielded
2
cable with less than 0.5 mm section.
TRAFFIC LIGHT CARD CONNECTION
Connect on
EXP terminal
20 67410179
GATE 1 DG R1
International registered trademark n. 2.777.971
Rev.04 - 06/2014
Other manuals for GATE 1 DG R1
2
Table of contents
Other SEA Control Unit manuals
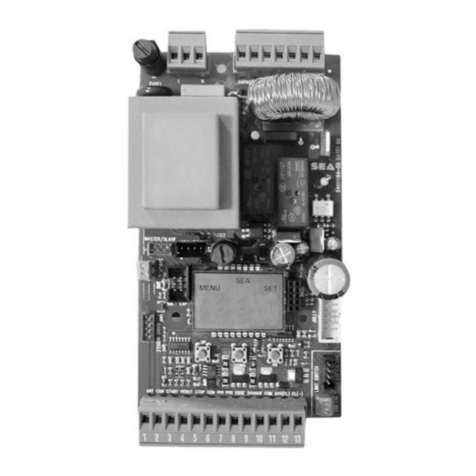
SEA
SEA GATE 1 DG R2BF User manual
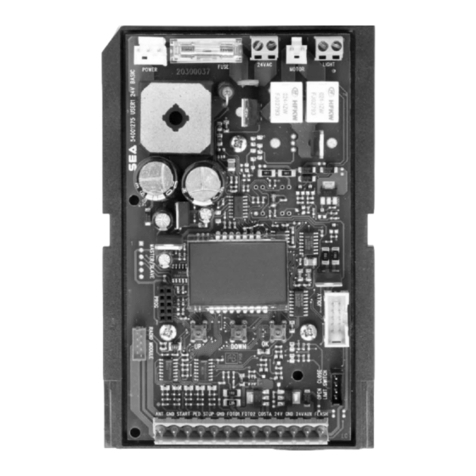
SEA
SEA USER 1 - 24v DG R1 User manual
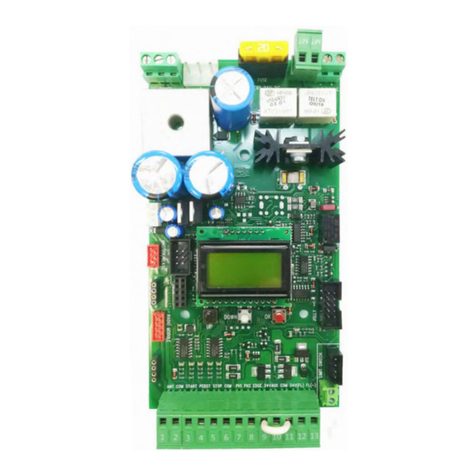
SEA
SEA USER 1 - 24v DG R1 User manual

SEA
SEA GATE 2 DG R1B User manual
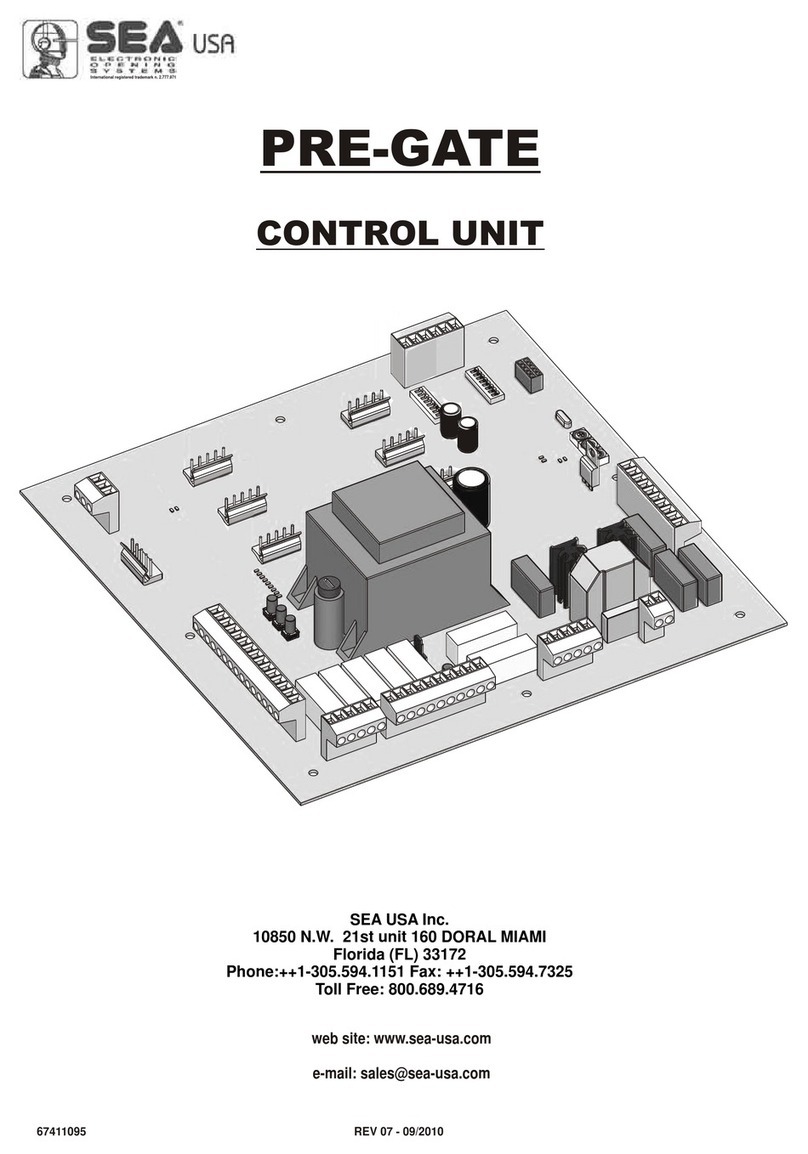
SEA
SEA PRE-GATE User manual
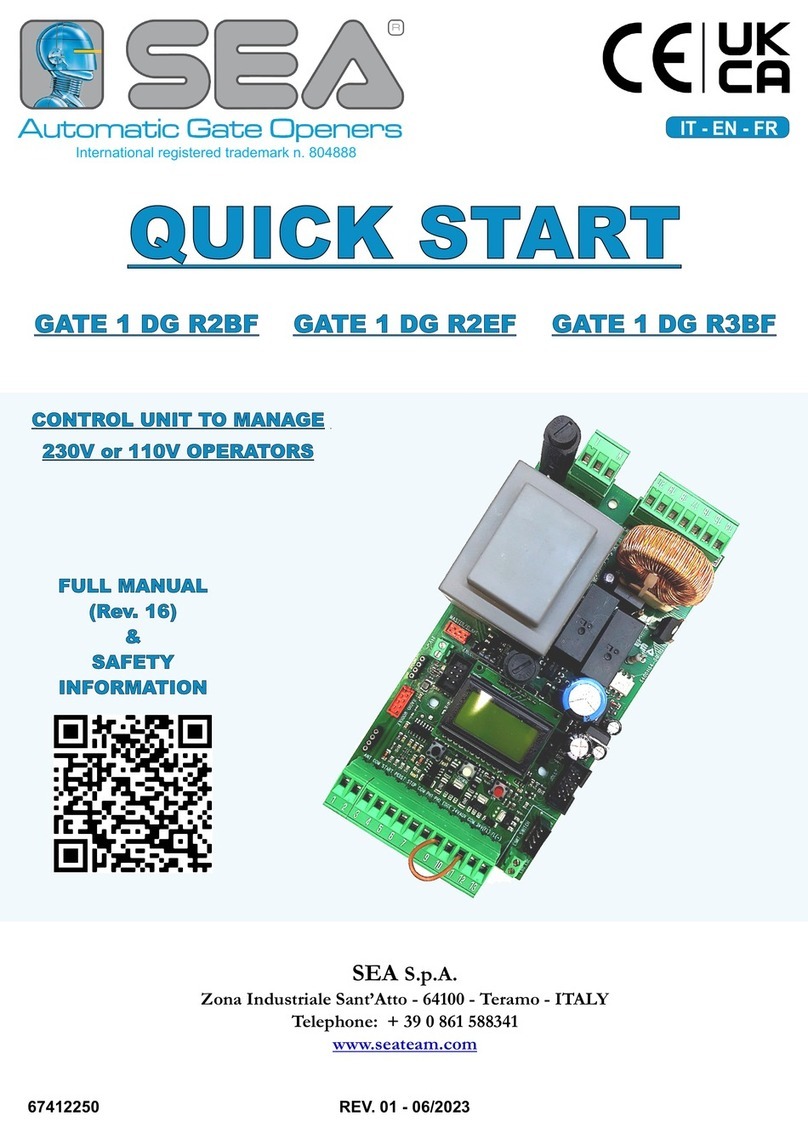
SEA
SEA GATE 1 DG R2BF User manual
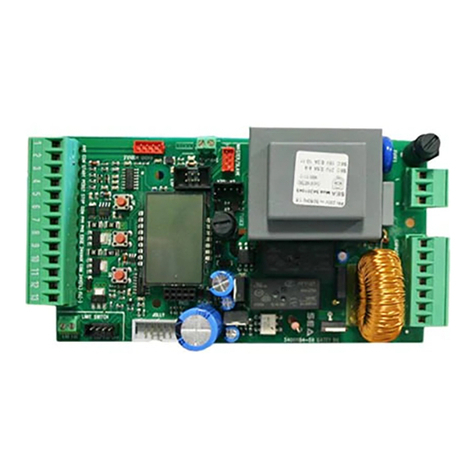
SEA
SEA GATE 1 DG R1 User manual
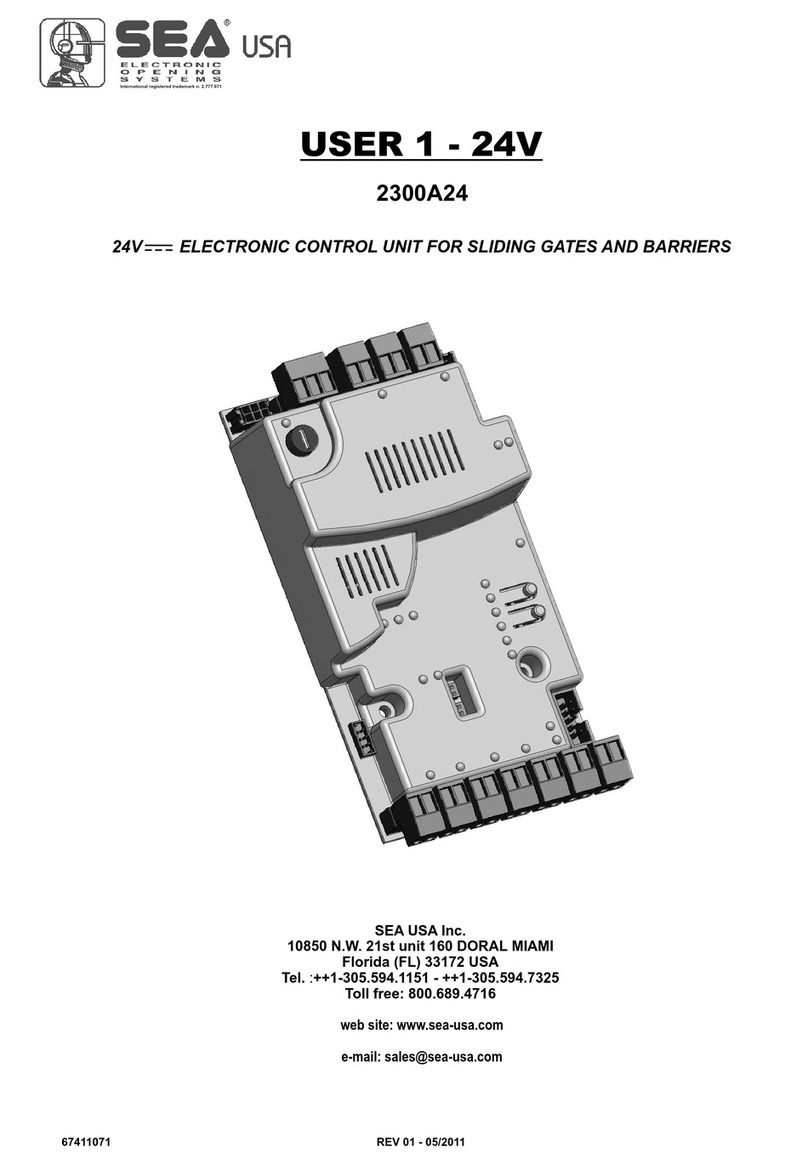
SEA
SEA USER 1-24V User manual

SEA
SEA 23001157 User manual
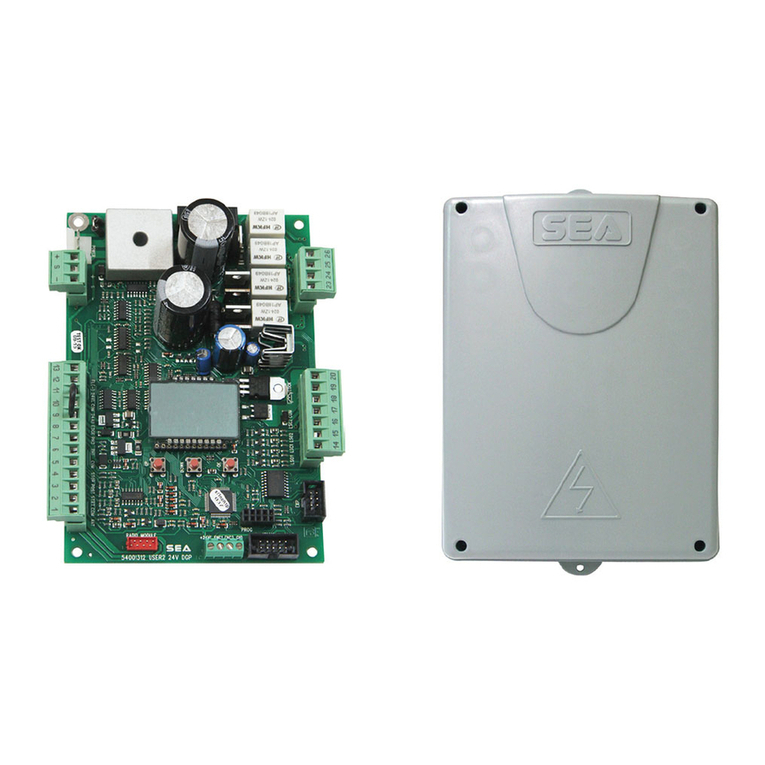
SEA
SEA USER 2 24V DG ALL IN User manual

SEA
SEA USER1-24V User manual

SEA
SEA GATE 1 DG R2BF User manual

SEA
SEA GATE 1 DG R2BF User manual
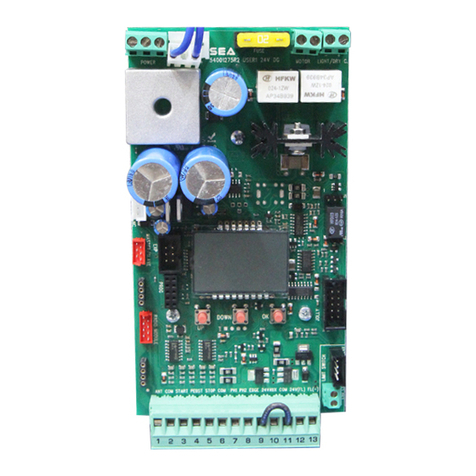
SEA
SEA USER 1 - 24v DG R1 User manual
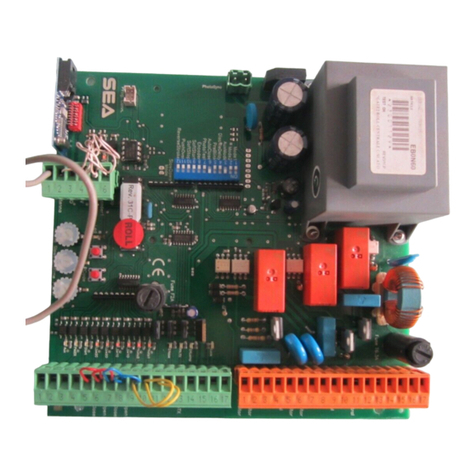
SEA
SEA GATE 2 User manual
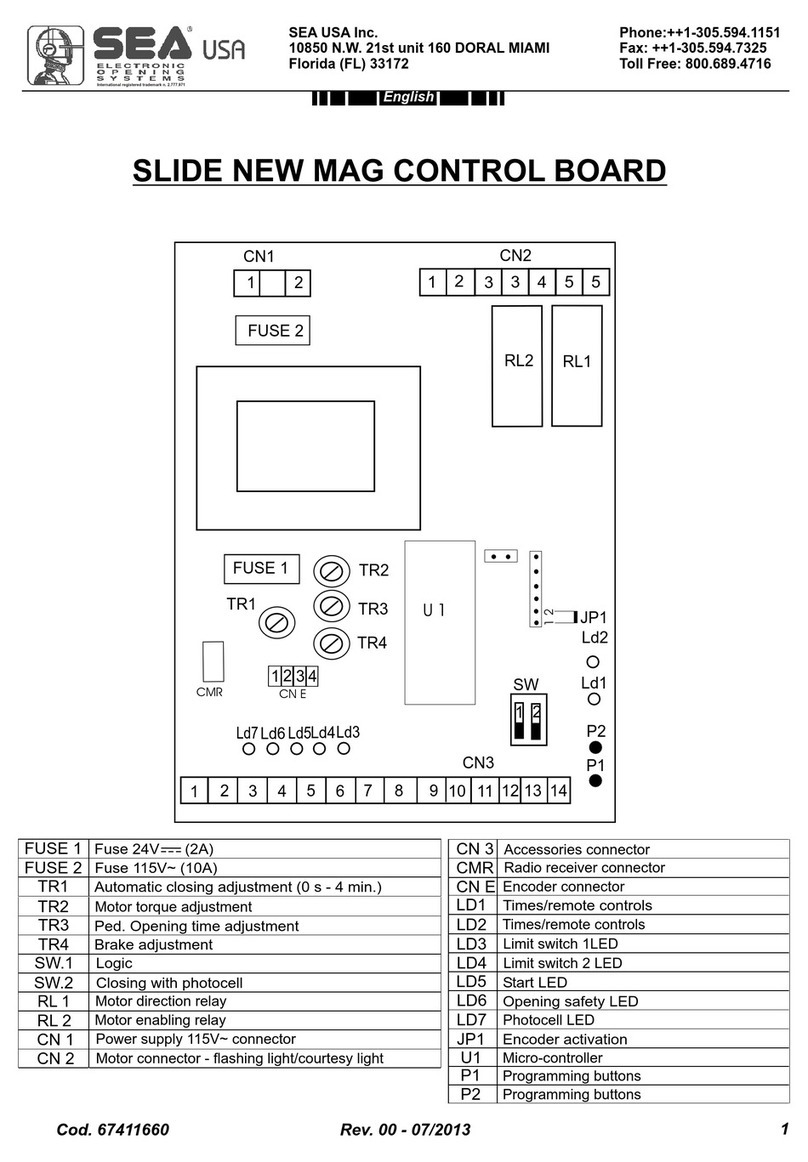
SEA
SEA SLIDE NEW MAG User manual

SEA
SEA CUBE R. NW User manual
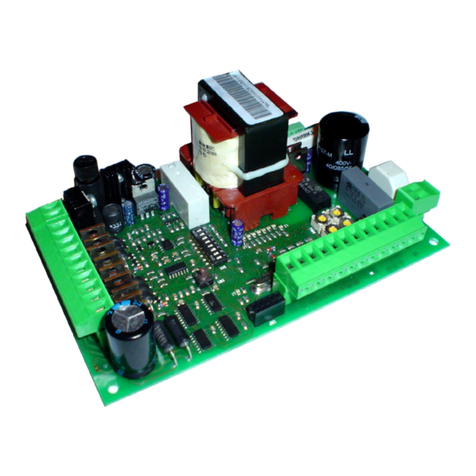
SEA
SEA GATE 2 - 24V PLUS User manual
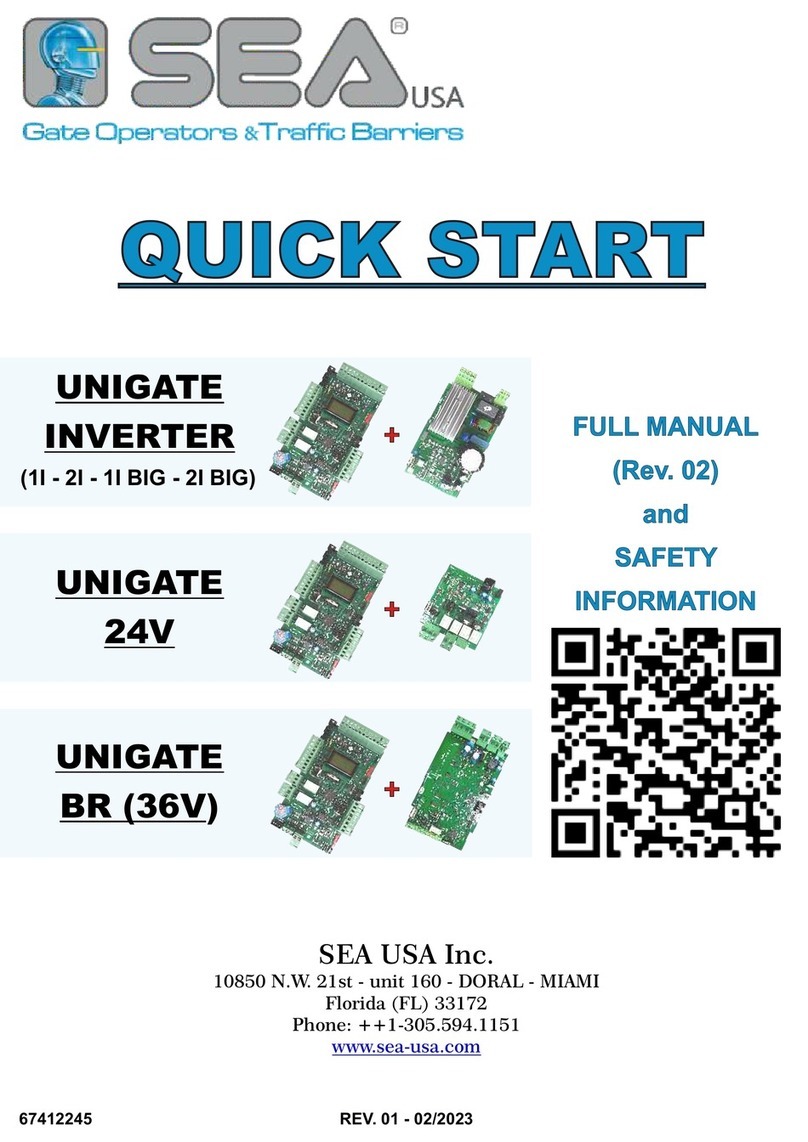
SEA
SEA UNIGATE 1I User manual
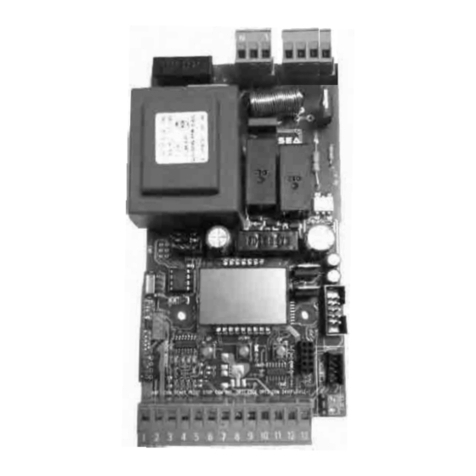
SEA
SEA SLIDE DG R2F User manual